注塑成型制品常见缺陷及预防措施-注塑件常见缺陷及原因
注塑件常见缺陷及原因分析【详解】
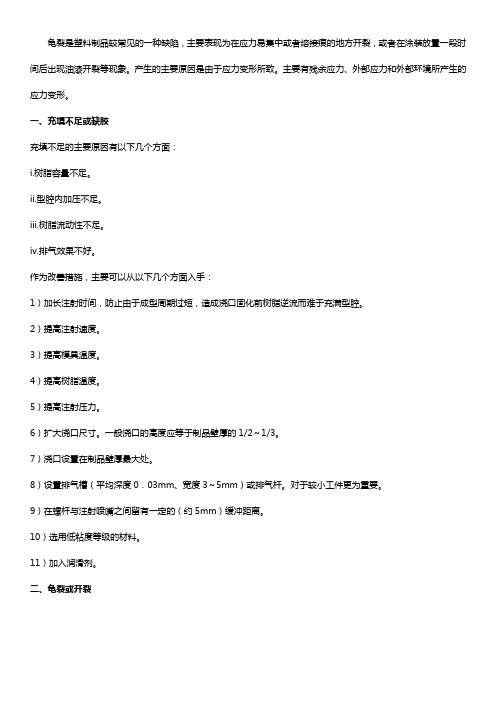
龟裂是塑料制品较常见的一种缺陷,主要表现为在应力易集中或者熔接痕的地方开裂,或者在涂装放置一段时间后出现油漆开裂等现象。
产生的主要原因是由于应力变形所致。
主要有残余应力、外部应力和外部环境所产生的应力变形。
一、充填不足或缺胶充填不足的主要原因有以下几个方面:i.树脂容量不足。
ii.型腔内加压不足。
iii.树脂流动性不足。
iv.排气效果不好。
作为改善措施,主要可以从以下几个方面入手:1)加长注射时间,防止由于成型周期过短,造成浇口固化前树脂逆流而难于充满型腔。
2)提高注射速度。
3)提高模具温度。
4)提高树脂温度。
5)提高注射压力。
6)扩大浇口尺寸。
一般浇口的高度应等于制品壁厚的1/2~1/3。
7)浇口设置在制品壁厚最大处。
8)设置排气槽(平均深度0.03mm、宽度3~5mm)或排气杆。
对于较小工件更为重要。
9)在螺杆与注射喷嘴之间留有一定的(约5mm)缓冲距离。
10)选用低粘度等级的材料。
11)加入润滑剂。
二、龟裂或开裂龟裂是塑料制品较常见的一种缺陷,主要表现为在应力易集中或者熔接痕的地方开裂,或者在涂装放置一段时间后出现油漆开裂等现象。
产生的主要原因是由于应力变形所致。
主要有残余应力、外部应力和外部环境所产生的应力变形。
(一)残余应力引起的龟裂残余应力主要由于以下三种情况,即充填过剩、脱模推出和金属镶嵌件造成的。
作为在充填过剩的情况下产生的龟裂,其解决方法主要可从以下几方面入手:1)由于直浇口压力损失最小,所以,如果龟裂最主要产生在直浇口附近,则可考虑改用多点分布点浇口、侧浇口及柄形浇口方式。
2)在保证树脂不分解、不劣化的前提下,适当提高树脂温度可以降低熔融粘度,提高流动性,同时也可以降低注射压力,以减小应力。
3)一般情况下,模温较低时容易产生应力,应适当提高温度。
但当注射速度较高时,即使模温低一些,也可减低应力的产生。
4)注射和保压时间过长也会产生应力,将其适当缩短或进行Th次保压切换效果较好。
注塑缺陷原因分析与解决方案

注塑缺陷原因分析与解决方案注塑是一种常见的塑料加工方法,广泛应用于各个行业。
然而,在注塑过程中,可能会出现各种缺陷,如气泡、翘曲、短射等问题,影响产品的质量和性能。
为了解决这些问题,我们需要进行缺陷原因分析,并提出相应的解决方案。
一、缺陷原因分析1. 气泡缺陷气泡是注塑过程中常见的缺陷之一。
其主要原因可能包括以下几个方面:- 塑料材料中含有挥发性物质,如水分、溶剂等,这些物质在高温下蒸发产生气泡。
- 注塑机温度设置不当,过高的温度会使塑料材料中的气体膨胀形成气泡。
- 注塑模具设计不合理,存在气孔或死角,导致塑料充填不均匀,形成气泡。
2. 翘曲缺陷翘曲是注塑产品常见的缺陷之一,其主要原因可能包括以下几个方面:- 注塑机温度不均匀,导致塑料材料在冷却过程中收缩不均匀,引起产品翘曲。
- 注塑模具设计不合理,存在过于薄弱的部位,无法承受注塑过程中的压力,导致产品变形。
- 注塑过程中冷却时间不足,使得产品在脱模后还未完全固化,导致变形。
3. 短射缺陷短射是指注塑产品未能充填满模具而产生的缺陷,其主要原因可能包括以下几个方面:- 注塑机温度设置不当,导致塑料材料粘度过高,无法充填满模具。
- 注塑模具设计不合理,存在过于狭窄的充填道或浇口,导致塑料流动受阻,无法充填满模具。
- 注塑过程中注射速度过快,导致塑料材料无法充填满模具。
二、解决方案1. 气泡缺陷的解决方案- 检查塑料材料的质量,确保其含水量和挥发性物质含量符合要求。
- 调整注塑机的温度,确保塑料材料在注塑过程中不会过热。
- 优化注塑模具的设计,避免气孔和死角的存在,确保塑料充填均匀。
2. 翘曲缺陷的解决方案- 调整注塑机的温度分布,确保塑料材料在冷却过程中收缩均匀。
- 优化注塑模具的设计,增加产品的结构强度,避免过于薄弱的部位。
- 增加注塑过程中的冷却时间,确保产品完全固化后再进行脱模。
3. 短射缺陷的解决方案- 调整注塑机的温度,降低塑料材料的粘度,促进充填。
注塑成型制品不良现象及解决办法

注塑成型制品不良现象及解决办法一、塑料制品充填不满1、成因:主要是缺料和注射压力与速度不妥(包括阻力造成压力过于耗损)。
2、解决措施:(1)机台方面:机台的塑化量或加热功率不定,应选用塑化量与加热功率大的机台;螺杆与料筒或过胶头等的磨损造成回料而出现实际充模量不中;热电偶或发热圈等加热系统故障造成料筒的实际温度过低;注射油缸的密封元件磨损造成漏油或回流,而不能达到所需的注射压力;射嘴内孔过小或射嘴中心度调节不当造成阻力过大而使压力消耗。
(2)模具方面:①模具局部或整体的温度过低造成入料困难,应适当提高模温;②模具的型腔的分布不平衡。
制件壁厚过薄造成压力消耗过磊而且充模不力。
应增加整个制件或局部的壁厚或可在填充不足处的附近,设置辅助流或浇口解决。
③模具的流道过小造成压力损耗;过大时会出现射胶无力;过于粗糙都会造成制件不满。
应适当设置流道的大小,主流道与分流道,浇口之间的过渡或本身的转弯处应用适当的圆弧过渡。
④模具的排气不良。
进入型腔的料受到来不及排走的气体压力的阻挡而造成充填不满。
可以充分利用螺杆的缝隙排气或降低锁模力利用分型面排气,必要时要开设排气沟道或气孔。
(3)制件不满反复出现的原因:①塑料原料粒度大小悬殊不均时会使加料份量不定。
②螺杆的过胶头、过胶圈及过胶垫圈的磨损过大,使熔料可能在螺杆处经与料筒内之间滑行及回流造成不满。
③入流口的冷却系统失效,使下料量不稳定。
④料筒调定的注料量不足,即缓冲垫过小会使射料时多时少而出现制件不满。
二、飞边1、成因:又称溢边、披锋、毛刺等,大多发生在模具的分合位置上,如动模和静模的分型面,滑块的滑配部位、镶件的绝隙、顶杆孔隙等处,飞边在很大程度上是由于模具或机台锁模力失效造成。
2、解决措施:(1)机台的最高锁模力不够应选用锁模力够的机台。
锁模机铰磨损或锁模油缸密封元件磨损出现滴油或回流而造成锁模力下降。
加温系统失控造成实际温度过高应检查热电偶、加热圈等是否有问题。
注塑缺陷原因分析与解决方案
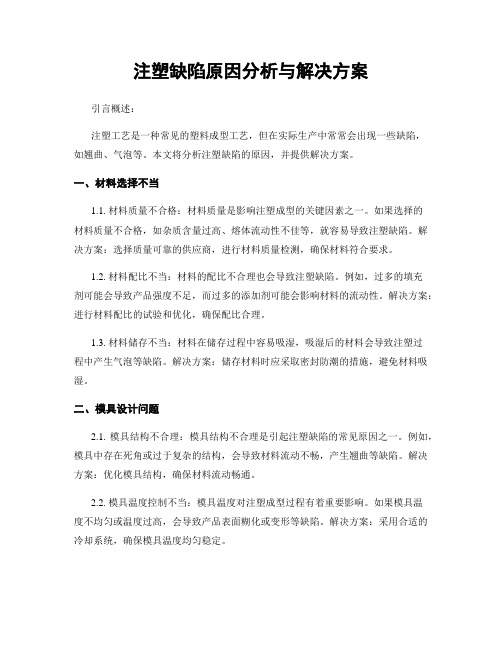
注塑缺陷原因分析与解决方案引言概述:注塑工艺是一种常见的塑料成型工艺,但在实际生产中常常会出现一些缺陷,如翘曲、气泡等。
本文将分析注塑缺陷的原因,并提供解决方案。
一、材料选择不当1.1. 材料质量不合格:材料质量是影响注塑成型的关键因素之一。
如果选择的材料质量不合格,如杂质含量过高、熔体流动性不佳等,就容易导致注塑缺陷。
解决方案:选择质量可靠的供应商,进行材料质量检测,确保材料符合要求。
1.2. 材料配比不当:材料的配比不合理也会导致注塑缺陷。
例如,过多的填充剂可能会导致产品强度不足,而过多的添加剂可能会影响材料的流动性。
解决方案:进行材料配比的试验和优化,确保配比合理。
1.3. 材料储存不当:材料在储存过程中容易吸湿,吸湿后的材料会导致注塑过程中产生气泡等缺陷。
解决方案:储存材料时应采取密封防潮的措施,避免材料吸湿。
二、模具设计问题2.1. 模具结构不合理:模具结构不合理是引起注塑缺陷的常见原因之一。
例如,模具中存在死角或过于复杂的结构,会导致材料流动不畅,产生翘曲等缺陷。
解决方案:优化模具结构,确保材料流动畅通。
2.2. 模具温度控制不当:模具温度对注塑成型过程有着重要影响。
如果模具温度不均匀或温度过高,会导致产品表面糊化或变形等缺陷。
解决方案:采用合适的冷却系统,确保模具温度均匀稳定。
2.3. 模具磨损严重:模具长时间使用后会出现磨损,磨损严重的模具会导致产品尺寸不准确或表面粗糙等缺陷。
解决方案:定期检查和维护模具,及时更换磨损严重的模具部件。
三、注塑工艺参数设置不当3.1. 注射压力过高或过低:注射压力是影响注塑成型的关键参数之一。
如果注射压力过高,会导致产品变形或开裂,而注射压力过低则会导致产品表面光洁度不高。
解决方案:根据产品要求和材料特性,合理设置注射压力。
3.2. 注射速度不合理:注射速度对产品的充填和冷却过程有着重要影响。
如果注射速度过快,会导致产品内部产生气泡或短射,而注射速度过慢则会导致产品表面瑕疵。
注塑制品常见缺陷分析及改善措施

注塑制品常见缺陷分析及改善措施注塑制品是一种常见的塑料制品,它被广泛应用于各个领域。
然而,由于注塑过程中存在很多因素的影响,注塑制品常常会出现一些缺陷。
本文将对常见的注塑制品缺陷进行分析,并提出相应的改善措施。
首先,短斑是指注塑制品表面上出现小块区域与周围区域颜色不一致的现象。
短斑的产生原因主要有以下几点:一是注塑过程中,塑料熔融不均匀,导致注塑制品的物理性能不一致;二是模具构造不合理,导致注射流道中存在死角或交叉断面,使得塑料无法均匀地填充模具。
改善措施包括调整注射温度和速度,提高熔融的均匀性;优化模具结构,避免死角和交叉断面的存在。
其次,气泡是指注塑制品中出现的气体囊泡。
气泡的产生原因主要有以下几点:一是塑料熔融时,吸附在塑料中的气体因温度升高而析出;二是模具内空气被困,形成气泡。
改善措施包括提高注料温度和压力,使气体充分溶解于塑料中;优化模具结构,改善气体的排除。
再次,翘曲是指注塑制品的形状不平整,出现弯曲或变形的现象。
翘曲的产生原因主要有以下几点:一是注塑过程中,注射压力不均匀,导致塑料流动不稳定;二是模具温度不均匀,导致塑料的冷却速度不一致。
改善措施包括提高注射速度和压力,增加注塑壁厚度的控制;优化模具温度控制系统,使模具温度均匀。
此外,色差是指注塑制品表面颜色不均匀的现象。
色差的产生原因主要有以下几点:一是注塑材料质量不均匀,导致色料分散不均匀;二是注塑过程中的温度和压力不稳定,使色料没有充分混合。
改善措施包括选用质量稳定的注塑材料;提高注塑温度和压力的稳定性;增加色料的溶解和混合时间。
最后,露胶是指注塑制品表面出现塑料外露的现象。
露胶的产生原因主要有以下几点:一是模具设计不合理,导致模具分离缺陷;二是注射流道中存在死角或结构不当,使得塑料无法完全填充模具。
改善措施包括优化模具设计,确保模具分离平整;优化注射流道结构,避免死角的存在。
综上所述,注塑制品的常见缺陷主要包括短斑、气泡、翘曲、色差和露胶等。
注塑缺陷原因分析与解决方案
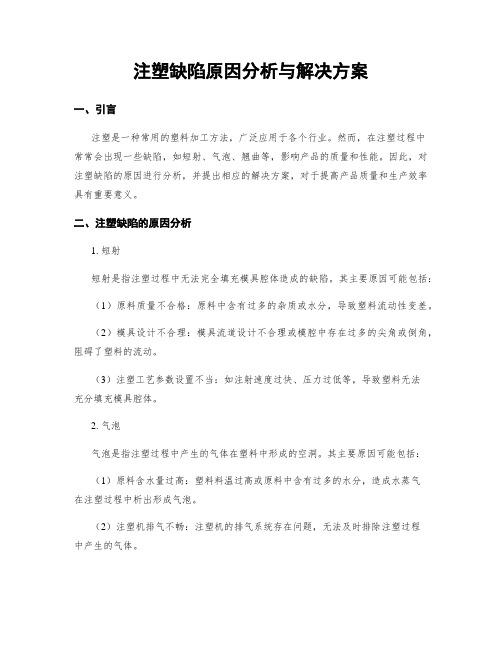
注塑缺陷原因分析与解决方案一、引言注塑是一种常用的塑料加工方法,广泛应用于各个行业。
然而,在注塑过程中常常会出现一些缺陷,如短射、气泡、翘曲等,影响产品的质量和性能。
因此,对注塑缺陷的原因进行分析,并提出相应的解决方案,对于提高产品质量和生产效率具有重要意义。
二、注塑缺陷的原因分析1. 短射短射是指注塑过程中无法完全填充模具腔体造成的缺陷。
其主要原因可能包括:(1)原料质量不合格:原料中含有过多的杂质或水分,导致塑料流动性变差。
(2)模具设计不合理:模具流道设计不合理或模腔中存在过多的尖角或倒角,阻碍了塑料的流动。
(3)注塑工艺参数设置不当:如注射速度过快、压力过低等,导致塑料无法充分填充模具腔体。
2. 气泡气泡是指注塑过程中产生的气体在塑料中形成的空洞。
其主要原因可能包括:(1)原料含水量过高:塑料料温过高或原料中含有过多的水分,造成水蒸气在注塑过程中析出形成气泡。
(2)注塑机排气不畅:注塑机的排气系统存在问题,无法及时排除注塑过程中产生的气体。
(3)注塑工艺参数设置不当:如注射速度过快、压力过高等,造成塑料内部气体无法顺利排出。
3. 翘曲翘曲是指注塑制品在冷却后出现变形的现象。
其主要原因可能包括:(1)模具温度不均匀:模具温度不均匀导致注塑制品冷却不均匀,从而引起翘曲。
(2)注塑过程中的应力积累:注塑过程中,塑料在注射后会受到冷却和收缩的影响,如果释放不及时,会导致应力积累引起翘曲。
(3)注塑工艺参数设置不当:如注射速度过快、冷却时间过短等,造成塑料冷却不充分,引起翘曲。
三、注塑缺陷的解决方案1. 短射的解决方案(1)优化原料质量:选择质量合格的原料,避免杂质和水分的存在。
(2)优化模具设计:合理设计模具流道,避免尖角和倒角的存在,保证塑料的顺畅流动。
(3)优化注塑工艺参数:合理设置注射速度和压力,确保塑料能够充分填充模具腔体。
2. 气泡的解决方案(1)控制原料含水量:确保塑料料温适宜,原料中的水分含量符合要求。
塑胶件常见缺陷产生的原因及避免

注塑件常见成型缺陷及避免摘要列举注塑成型过程的几种典型缺陷,从影响成型制品质量的三大因素分析常见注塑成型制品的质量缺陷产生原因及解决措施,以便在设计阶段防止缺陷,缩短开发周期,节约开发成本。
关键词缺陷,缺胶,毛边,缩水,银纹,流痕,变形,模具1引言随着塑料工业的迅速发展,塑料制品日益普及,现已广泛应用到各个领域。
近年来由于家电、通讯、视频、医疗等产业对注塑制品需求的日益增长,推动注塑成型技术水平的发展与提高。
目前的工程塑料业中,80%的产品采用注塑成型。
在塑料制品注塑成型过程中,由于成型材料、成型模具、辅助设备、成型环境等多种因素的影响,注塑制品的内在及外观会出现各种各样的问题。
一般来说,制品成型质量主要包括制品外观、制品尺寸精度以及制品的物理性能。
产生缺陷的原因是多方面的,可能塑料材料和成型工艺选择不当,可能是模具设计不合理,也可能是多种因素综合的结果。
本文将对常见的几种的成型缺陷的成因做一分析。
2常见缺陷:2.1、注塑件缺胶、不饱模:指成型过程中料流出现没有完全充满模具型腔而导致的产品不完整,也称不全、缺料等。
主要发生在远离料头或薄壁面的地方。
原因分析:1、与注塑机匹配不当,导致注塑机塑化能力或注射量不足。
2、喷嘴、流道和浇口太小,流程太长,塑胶填充阻力过大。
3、流道设计不良,塑料流动阻力大4、塑料熔化不充分,流动性不好,导致注射压力损失大。
5、流道中冷料井预留不足或不当,冷料头进入型腔而阻碍塑胶之正常流动,增加6、料温、模温太低,塑胶在当前压力下流动困难,射胶速度太慢、保压或保压压力过低。
7、模具排气不良时,空气无法排除。
解决对策:1、改换注塑机台,射出成品含浇道以不超过机台注射量的80%为限。
2、加大喷嘴的射出口尺寸。
3、修改流道以符合实际要求。
4、适当调整背压及螺杆转速,是塑料混合均匀。
5、增加冷料井储存空间。
6、根据实际需要,适当提升模具温度。
7、改善排气,定期清除模垢。
2.2、毛边毛边是指在模具的不连续处(通常是分模面、排气孔、顶针、滑动机构)过量填充造成塑料外溢的瑕疵。
注塑常见不良缺陷原因及解决对策

注塑常见不良缺陷原因及解决对策壹.缺料原因一.材料充填不足.状态1.射出压力未到达最高设定值.解决对策:1.增加射出压力.2.增加射出速度.3.增加模温.4.增加料筒温度.5.检查胶口尺寸.6.检查流道尺寸.7.检查喷嘴温度.8.检查喷嘴大小.状态2.射出压力已到达最高设定值.解决对策:1.延长射出行程.2.增加保持压力.3.增加保持时间.状态3.螺杆已到达最前端.解决对策:1.延长射出行程.2.检查螺杆.原因二.排气不良1.改善排气效果.2.减低射出速度.状态2.缺料位于其它部分.解决对策:1.改善排气效果.2.增加射出压力.3.增加缺料部分厚度原因三.包封现象状态1.于产品中心(不在边缘).解决对策:1.增加排气点.2.增加射出压力.3.改变浇口位置.4.增加溢流区,改变塑料流动方向. 原因四.迟滞现象状态1.浇口附近较薄处肋缺料.解决对策:1.增加厚度.2.增加射出速度.3.增加模温.4.增加料温.5.增加保持压力.6.改变浇口位置.7.增加扰流设计.原因一.过度充填状态1.毛边出现在浇口附近解决对策:1.降低射出速度.(尤其通过浇口时的速度).状态2.毛边出现在分离面(parting)且已饱和. 解决对策:1.降低计量长度.(提高切换到饱压).2.降低射出速度(尤其是切换饱压前之速度).3.减低模温.4.减低料温.5.减低保持压力.状态3.浇口附近凹陷但又发生毛边.解决对策:1.降低计量长度.(提高切换到饱压).2.降低射出速度(尤其是切换饱压前之速度).3.减低模温.4.减低料温.5.尝试以上各对策消除毛边后延长保持时间. 原因二.因流阻太大使模腔状态1.毛边又短射.(或流路末端凹陷)解决对策:1.增加模温. 内压(cavaty pressure)2.增加料温.3.增加射速.5.改善塑料料之流动性.原因三.锁模力(clamping force)不足状态1.无过饱和现象解决对策:1.提高锁模力原因四.吻合面间隙太大状态1.特定位置.解决对策:1.修复模具.原因五.模板变形解决对策:1.提早切换至饱压.2.减低饱压.3.提高模板强度及刚性. 参.凹陷.缩水与真空泡原因一.充填量不足状态1.全面性凹陷.解决对策:1.延长计量行程.2.检查螺杆逆止环3.增加射出速度.4.增加保持压力.5.增加流道或浇口尺寸.6.增加模温.状态2.凹陷出现在流路末端或薄的部位.解决对策:1.增加保持压力(尤其是初期).2.提高料筒(cylinder barrel)温度.3.增加模温.4.增加射出速度.5.检查浇口位置(由厚向薄射出).原因二.有效时间不足.状态1.凹陷出现在浇口或厚的部位.解决对策:1.延长保持时间.2.减低模温.3.减低料温.4.减少浇口断面积.原因三.表面固化太慢状态1.厚的部位出现凹陷或光泽.解决对策:1.减低模温.2.减低料温.3.塑流通过厚肉区时减速使固化层较厚.4.调整肉厚(如肋部减薄.厚薄变缓)5.使用低收缩率之塑料.6.添加发泡剂于塑料.#注:表层未凝固成坚固之固化层时.当中心收缩时会将表面熔解而产生光泽.相反的在厚的部份如果表层足够坚固则中心部的收缩会形成真空泡. #备注:第1.2.3.项会增加真空泡的发生机率#原因四.冷却时间太短状态.1.凹陷或真空泡是在开模取出后才发生.解决对策:1.减低模温.2.减低料温.3.增加冷却时间.肆.喷痕原因:发生在塑料流动断面由小急遽变大的位置;当塑料由小断面进入大断面如速度没有适当降低,则塑料像喷射般向前进.这些塑料温度冷却后与后来流入之塑料无法均匀融和而形成外观之不良.解决对策:1.减低射出速2.增加模温.3.增加料温.4.变更胶口位置.5.增加胶口断面6.避免射料方向由上向下.伍.结合线原因:塑料射出时两股以上的胶流相遇,压力与温度不足.相遇胶流之圆形先端无法融合.而形成表面的沟状痕迹.1.增加射出速度.2.增加模温.3.增加料温.4.增加保持压力.5. 变更胶口位置.6.检查排气效果.陆.波纹原因:当胶流进入较冷的模腔,由于冷却速度快,使得靠近模壁部分之塑料形成固化.这固化层妨碍了后续流动之塑料贴近模壁;但此固化层受流动压力拉伸延展,又受到胶流之压力相互挤压.相互作用一再重演在成品外观上流下一成层层之波浪状.解决对策:1.增加射出速度.2.增加射出压力.3.增加模温.4.增加料温.5.避免流道太小.柒.气泡原因:射出时塑料料包含太多气体或混合了空气.则成品内部或接近表面会有空气之现象.解决对策:1.降低松退速度或检小松退量.2.提高背压.4.检查可塑化机构.5.检查计量长度是否太长.捌.烧焦原因:射出进行中因排气不及.气体受到绝热压缩产生极高温度而将塑料料烧黑.状态1.产生于流路末端解决对策:1.减低射出速度.2.改善排气效果.3.减低锁模力.状态2.产生于包封处解决对策:1.调整肉厚.2.改变浇口位置.3.减低射出速度.4.减低锁模力.5.增加排气点.玖.冷却痕原因:在射出过程中.于喷嘴的先端或浇口部分产生冷却.这些冷却料在被射出时如未被挡在流道系统的冷料井或者是再熔解.则在浇口附近留下长条的流痕.1.增加喷嘴孔径.2.增加喷嘴温度.3.减低松退量.5.降低射出到浇口之速度.拾.浇口周围的雾状原因:在浇口(尤其为小浇口)周围高分子配向的凝固层(强度较弱).如在高速的流动场中.受分子炼被拉开而形成一些小.缺孔.很多小缺孔构成浇口周围的雾状.痕迹.解决对策:1.减低射出速度.2.增加浇口的断面积.3.改变浇口位置4.增加模温5.减低料温.拾壹.表层剥落原因:成品的表面层在塑料料流动和固化速度不同的情形下.一层一层的堆积所形成.如果因塑料料含有不均匀的成份或受过高切段力及过热所破坏则层与层间之熔合就不足而产生剥落.解决对策:1.检查塑料料是否含有太多水份.2.增高模温.3.减低射出速度.4.减低料温.5.检查塑料机的性能及设定条件.6.检查塑料料之色剂或添加物是否兼容.7.检查塑料料之是否混入其它材质.拾贰.黑点原因1.塑料料含有杂质或其它不兼容物质.解决对策:1.检查塑料料是否含有杂质.2.降低回收料的添加比例.3.检查塑料料之色剂或添加物是否兼容.原因2.塑料料在制造过程中受到污染.解决对策:1.检查送料管路及烘料筒.2.清洁螺杆及加热筒.3.清洁热流道及喷嘴.原因3.塑料料在制造过程中受到破坏.解决对策:1.减低料温.2.减低塑料料在加热管内停流时间.拾参.焦纹原因:塑料料因热受损分子量会降低或发生热分解.使成品外观出现银色或棕色的纹状瑕疵.同时也会降低强度.解决对策:1.减低料温.2.减低塑料料在加热管内停流时间.3.减低射出速度.4.增加喷嘴孔径..拾肆.湿纹所形成之水气会受流动推挤到模壁而形成成品表面条状的痕迹.解决对策:1.检查塑料材料的干燥度.2.提高背压.3.检查模壁表面是否含有水份.4.检查材料之包装与储存.拾伍.气痕原因:在射出过程中.气体来不及排出.被推往表面或在进料后松退.吸入空气.而在射出时被推往浇口之附近.状态1.出现在浇口附近.解决对策:1.降低松退速度或行程.2.使用可闭喷嘴.状态2.出现在其它部分.解决对策:1.减低射出速度.2.增加被压.3.改变浇口位置.4.设计时避免尖角及凹凸太深之形状拾陆.光泽与光泽差异原因:塑料成型品之表面,光泽决定于模具表.面加工及射出成形.之冷却速率或收缩差异所产生的表面状态1.模具打光面光泽不足.解决对策:1.模面再打光.2.增加射出速度3.增加模温4.增加料温.状态2.咬花面光泽不足.解决对策:1.调整咬花面.2.减低射出速度.3.减低模温.4.减低料温.状态3.接合线处的光泽差异. 解决对策:1.改变浇口位置.2.增加射出速度.3.增加模温.状态4.孔部周围的光泽差异. 解决对策:1.改变浇口位置.2.调整孔部型状.状态5.肋部或厚驳差异急变处. 解决对策:1.增加保持压力.2.足够的保持时间.3.降低通过问题处之速度.4.调整厚薄变化.使其变化趋缓.状态6.在顶针或滑块处光泽差异. 解决对策:1.检查模温之差异.2.避免模腔内压力过高.。
注塑产品常见的13种质量缺陷原因分析及解决办法
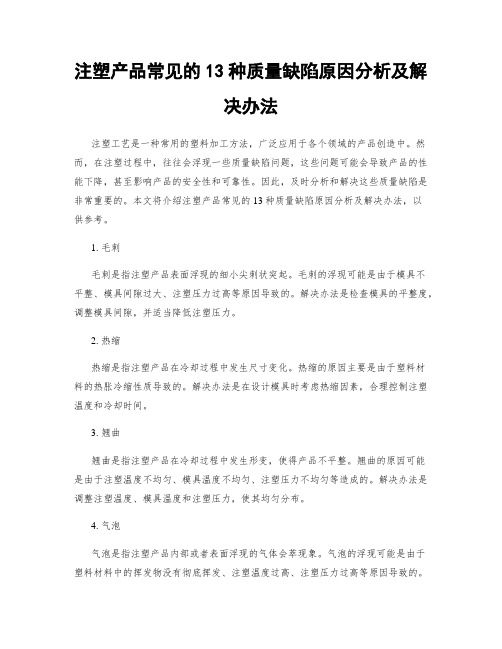
注塑产品常见的13种质量缺陷原因分析及解决办法注塑工艺是一种常用的塑料加工方法,广泛应用于各个领域的产品创造中。
然而,在注塑过程中,往往会浮现一些质量缺陷问题,这些问题可能会导致产品的性能下降,甚至影响产品的安全性和可靠性。
因此,及时分析和解决这些质量缺陷是非常重要的。
本文将介绍注塑产品常见的13种质量缺陷原因分析及解决办法,以供参考。
1. 毛刺毛刺是指注塑产品表面浮现的细小尖刺状突起。
毛刺的浮现可能是由于模具不平整、模具间隙过大、注塑压力过高等原因导致的。
解决办法是检查模具的平整度,调整模具间隙,并适当降低注塑压力。
2. 热缩热缩是指注塑产品在冷却过程中发生尺寸变化。
热缩的原因主要是由于塑料材料的热胀冷缩性质导致的。
解决办法是在设计模具时考虑热缩因素,合理控制注塑温度和冷却时间。
3. 翘曲翘曲是指注塑产品在冷却过程中发生形变,使得产品不平整。
翘曲的原因可能是由于注塑温度不均匀、模具温度不均匀、注塑压力不均匀等造成的。
解决办法是调整注塑温度、模具温度和注塑压力,使其均匀分布。
4. 气泡气泡是指注塑产品内部或者表面浮现的气体会萃现象。
气泡的浮现可能是由于塑料材料中的挥发物没有彻底挥发、注塑温度过高、注塑压力过高等原因导致的。
解决办法是控制注塑温度和压力,选择合适的塑料材料,并进行充分的挤出和干燥处理。
5. 缩孔缩孔是指注塑产品内部浮现的空洞状缺陷。
缩孔的原因可能是由于注塑温度过低、注塑压力不足、模具设计不合理等导致的。
解决办法是提高注塑温度、增加注塑压力,并优化模具设计。
6. 裂纹裂纹是指注塑产品表面或者内部浮现的裂纹状缺陷。
裂纹的浮现可能是由于注塑温度过高、注塑压力过大、冷却时间过短等原因导致的。
解决办法是降低注塑温度、减小注塑压力,并延长冷却时间。
7. 毛边毛边是指注塑产品边缘浮现的不平整现象。
毛边的原因可能是由于模具设计不合理、注塑压力过高、注塑速度过快等导致的。
解决办法是优化模具设计,降低注塑压力,并适当调整注塑速度。
注塑成型制品常见缺陷及预防措施

注塑成型制品常见缺陷及预防措施一、注塑成型加工在制造业中的应用塑料加工工艺一般包括:注塑成型、挤塑成型、压塑成型、吹塑成型。
因为注塑机具有能一次成型外型复杂、尺寸精确或带有金属嵌件的质地密致的塑料制品所以被广泛应用于国防、机电、汽车、交通运输、建材、包装、农业、文教卫生及人们日常生活各个领域。
在塑料工业迅速发展的今天,注塑机不论在数量上或品种上都占有重要地位,其生产总数占整个塑料成型设备20%-30%,从而成为目前塑料机械中增长最快,生产数量最多的机种之一。
从涵盖的行业范围及生产总数已经反映了注塑成型工艺在制造业中的地位举足轻重。
我国注塑机行业的技术在近几年进步十分显著,尤其是注塑机的技术水平与国外名牌产品的差距大大缩小,在控制水平、产品内部质量和外观造型等方面均取得明显进步。
我国注塑成型一般以热固性塑料为主,而热塑性塑料的注塑加工在近年也取得了很大的进步。
但国内由于精密制品比较少,复合制品基本没有,因而很少配置机械手,反映国内整体要求相对比较低,与西方国家差距较大,对制品的质量要求还未提高到相应水平,也反映了我国的生产还处在劳动密集型经济。
二、注塑制品的常见缺陷及预防措施因为制品的质量直接影响到企业的效益,而如果制品中存在缺陷,企业需要派工人进行返工,把制品粉碎后重新加工或者是直接报废,这会提高企业的生产成本。
而产品的质量又直接地影响企业形象与诚信度,要把一切质量问题解决在出厂前。
而一般的一线工人只负责观察塑件是否能正常脱模,面对塑件出现大批量的缺陷,他们无法纠正。
所以为了提高效益,技术人员必须在发现制品缺陷后,及时地进行预防纠正,以及在生产中不断地优化生产工艺、修整模具,以免带来更大的亏损。
下面介绍几种注塑制品常见缺陷及预防措施:1、变形(1)模具温度太高,冷却不足:首先考虑延长冷却时间,检查冷却管道循环水是否正常运作。
如果延长冷却时间无法解决,就应考虑模具冷却系统的设计是否合理。
在塑件横截面积大或在浇注口等温度较高的位置要设计比较集中的冷却管道,而在容易冷却的部位应进行缓慢冷却,尽量使塑件各部位冷却均匀。
常见注塑缺陷及解决方案
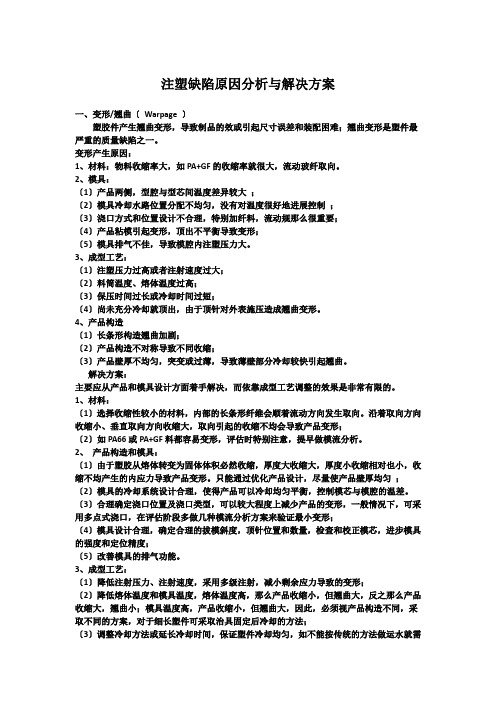
注塑缺陷原因分析与解决方案一、变形/翘曲〔Warpage 〕塑胶件产生翘曲变形,导致制品的效或引起尺寸误差和装配困难;翘曲变形是塑件最严重的质量缺陷之一。
变形产生原因:1、材料:物料收缩率大,如PA+GF的收缩率就很大,流动玻纤取向。
2、模具:〔1〕产品两侧,型腔与型芯间温度差异较大;〔2〕模具冷却水路位置分配不均匀,没有对温度很好地进展控制;〔3〕浇口方式和位置设计不合理,特别加纤料,流动规那么很重要;〔4〕产品粘模引起变形,顶出不平衡导致变形;〔5〕模具排气不佳,导致模腔内注塑压力大。
3、成型工艺:〔1〕注塑压力过高或者注射速度过大;〔2〕料筒温度、熔体温度过高;〔3〕保压时间过长或冷却时间过短;〔4〕尚未充分冷却就顶出,由于顶针对外表施压造成翘曲变形。
4、产品构造〔1〕长条形构造翘曲加剧;〔2〕产品构造不对称导致不同收缩;〔3〕产品壁厚不均匀,突变或过薄,导致薄壁部分冷却较快引起翘曲。
解决方案:主要应从产品和模具设计方面着手解决,而依靠成型工艺调整的效果是非常有限的。
1、材料:〔1〕选择收缩性较小的材料,内部的长条形纤维会顺着流动方向发生取向。
沿着取向方向收缩小、垂直取向方向收缩大,取向引起的收缩不均会导致产品变形;〔2〕如PA66或PA+GF料都容易变形,评估时特别注意,提早做模流分析。
2、产品构造和模具:〔1〕由于塑胶从熔体转变为固体体积必然收缩,厚度大收缩大,厚度小收缩相对也小,收缩不均产生的内应力导致产品变形。
只能通过优化产品设计,尽量使产品壁厚均匀;〔2〕模具的冷却系统设计合理,使得产品可以冷却均匀平衡,控制模芯与模腔的温差。
〔3〕合理确定浇口位置及浇口类型,可以较大程度上减少产品的变形,一般情况下,可采用多点式浇口,在评估阶段多做几种模流分析方案来验证最小变形;〔4〕模具设计合理,确定合理的拔模斜度,顶针位置和数量,检查和校正模芯,进步模具的强度和定位精度;〔5〕改善模具的排气功能。
注塑常见缺陷及解决方法

注塑常见缺陷及解决方法
注塑是一种广泛应用于制造塑料制品的加工方法,但在实际生产中,由于原材料、工艺、设备等多种因素的影响,常常会出现各种缺陷。
下面是注塑常见缺陷及解决方法的详细介绍。
1. 气泡缺陷
气泡缺陷是注塑制品表面或内部存在的空洞或气泡。
一般由于原料过热、注模压力过高、模具进料不足等原因引起。
解决方法:降低原料温度、减小注射速度、增加进料量、调整模型温度、调整模具结构等。
2. 热胀冷缩缺陷
热胀冷缩缺陷是指塑料制品在注塑时由于热胀冷缩现象而导致的尺寸不稳定的现象。
解决方法:合理选择原材料、调整注塑工艺参数、改变模具结构、加入夹层等。
3. 毛刺缺陷
毛刺缺陷是指注塑制品表面出现的刺状物或毛细孔。
可能是由于模具设计不合理、注塑工艺不当、原材料污染等原因引起。
解决方法:调整模具设计、调整注塑工艺参数、更换清洗原材料。
4. 热裂缺陷
热裂缺陷是指塑料制品在注塑过程中由于温度过高而导致的开裂。
通常是由于原材料性能不佳、注塑工艺参数设置不当等原因引起。
解决方法:更换高品质的原材料、调整注塑工艺参数。
5. 毛边缺陷
毛边缺陷是指塑料制品表面出现的毛边或切口。
通常是由于模具设计不合理、注塑工艺参数不当、原材料品质差等原因引起。
解决方法:调整模具设计、调整注塑工艺参数、更换清洗原材料。
注塑制品的质量直接影响到其使用寿命和市场竞争力。
因此,在注塑生产中,应该重视并及时解决各种缺陷问题。
通过合理优化原材料、模具设计和注塑工艺参数等措施,不仅可以提高注塑制品的质量,还可以降低生产成本,提高企业的经济效益。
注塑件常见成型缺陷及解决方案

注塑件常见成型缺陷及解决方案注塑件常见成型缺陷及解决方案前言在注塑成型加式过程中,可能由于原材料处理不好、塑件或模具设计不合理、操作工没有掌握合适的工艺操作条件,或者因机械方面的原因,常常使塑件产品短射、凹痕、飞边、困气、开裂、翘曲变形等成型缺陷。
本文针对塑件在成型过程中出现的各种注塑缺陷,主要是:短射,困气,发脆,烧焦,飞边,分层起皮,喷流痕,流痕,雾斑(浇口晕),银纹(水花纹),凹痕,熔接痕,成型周期过长,翘曲变形,分析了问题产生的可能原因,从原材料、塑件或模具设计、成型工艺等各方面,提出解决方案。
一.短射短射是指模具型腔不能被完全充满的一种现象。
短射形成原因:1、模温、料温或注塑压力和速度过低2、原料塑化不均3、排气不良4、原料流动性不足5、制件太薄或浇口尺寸太小6、聚合物熔体由于结构设计不合理导致过早固化短射解决方案:材料:选用流动性更好的材料模具设计:1、填充薄壁之前先填充厚壁,避免出现滞留现象2、增加浇口数量和流道尺寸,减少流程比及流动阻力3、排气口的位置和尺寸设置适当,避免出现排气不良的现象注塑机:1、检查止逆阀和料筒内壁是否磨损严重2、检查加料口是否有料或是否架桥工艺条件:1、增大注塑压力和注塑速度,增强剪切热2、增大注塑量3、增大料筒温度和模具温度二.困气困气是指空气被困在型腔内而使制件产生气泡。
困气形成原因:它是由于两股熔体前锋交汇时气体无法从分型面、顶杆或排气孔中排出造成的。
困在型腔内气体不能被及时排出,易导致出现表面起泡,制件内部夹气,注塑不满等现象。
困气解决方案:结构设计:减少厚度的不一致,尽量保证壁厚均匀模具设计:1、在最后填充的地方增设排气口2、重新设计浇口和流道系统工艺条件:1、降低最后一级注塑速度.2、增加模温三.发脆塑件发脆是指制件在某些部位出现容易开裂或折断。
发脆原因:1、干燥条件不适合;使用过多回收料2、注塑温度设置不对3、浇口和流道系统设置不恰当4、熔解痕强度不高发脆解决方案:材料:1、注塑前设置适当的干燥条件2、减少使用回收料,增加原生料的比例.3、选用高强度的塑胶.模具设计:增大主流道、分流道和浇口尺寸注塑机:选择设计良好的螺杆,使塑化时温度分配更加均匀工艺条件:1、降低料筒和喷嘴的温度2、降低背压、螺杆转速和注塑速度3、通过增加料温,加大注塑压力,提高熔解痕强度四.烧焦焦痕是指型腔内气体不能及时排走,导致在流动最末断产生烧黑现象。
注塑件常见品质缺陷分析及解决方法
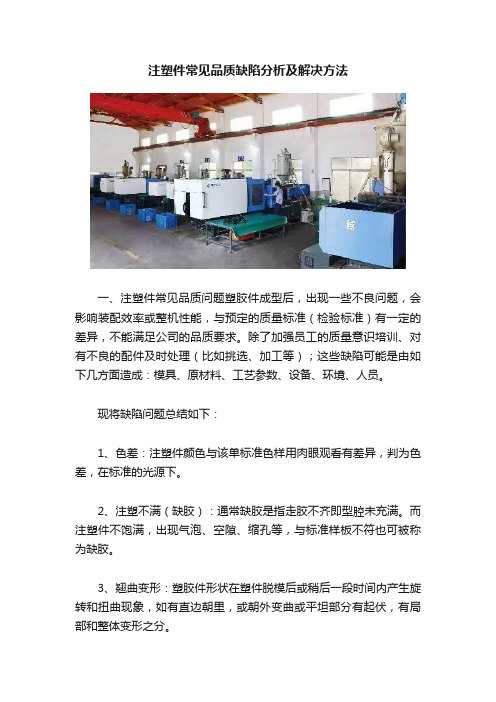
注塑件常见品质缺陷分析及解决方法一、注塑件常见品质问题塑胶件成型后,出现一些不良问题,会影响装配效率或整机性能,与预定的质量标准(检验标准)有一定的差异,不能满足公司的品质要求。
除了加强员工的质量意识培训、对有不良的配件及时处理(比如挑选、加工等);这些缺陷可能是由如下几方面造成:模具、原材料、工艺参数、设备、环境、人员。
现将缺陷问题总结如下:1、色差:注塑件颜色与该单标准色样用肉眼观看有差异,判为色差,在标准的光源下。
2、注塑不满(缺胶):通常缺胶是指走胶不齐即型腔未充满。
而注塑件不饱满,出现气泡、空隙、缩孔等,与标准样板不符也可被称为缺胶。
3、翘曲变形:塑胶件形状在塑件脱模后或稍后一段时间内产生旋转和扭曲现象,如有直边朝里,或朝外变曲或平坦部分有起伏,有局部和整体变形之分。
4、熔接痕(纹):在塑胶件表面的线状痕迹,由塑胶在模具内汇合在一起所形成,而熔体在其交汇处未完全熔合在一起,彼此不能熔为一体即产生熔接纹,多表现为一直线,由深向浅发展,此现象对外观和力学性能有一定影响。
如勾盘底部的熔接痕。
5、波纹:注塑件表面有螺旋状或云雾状的波形凹凸不平的表征现象,或透明产品的里面有波状纹,称为波纹。
6、溢边(飞边、披锋):在注塑件四周沿分型线的地方或模具密封面出现薄薄的(飞边)胶料,称为溢边。
7、银丝纹:注塑件表面的很长的、针状银白色如霜一般的细纹,开口方向沿着料流方向,在塑件未完全充满的地方,流体前端较粗糙,称为银丝纹(银纹)。
8、色泽不均(混色):注塑件表面的色泽不是均一的,有深浅和不同色相,称为混色。
9、光泽不良(暗色):注塑件表面为灰暗无光或光泽不均匀称为暗色或光泽不良。
10、脱模不良(脱模变形):与翘曲变形相似,注塑件成型后不能顺利的从模具中脱出,有变形、顶白、拉裂、拉伤等、称为脱模不良。
11、裂纹及破裂:塑胶件表面出现空隙的裂纹和由此形成的破损现象。
12、糊斑(烧焦):在塑件的表面或内部出现许多暗黑色的条纹或黑点,称为糊斑或烧焦。
TPR.TPR注塑成型制品易出现缺陷,原因,解决全方案

TPR/TPE注塑成型制品易出现缺陷,原因,解决方案1. TPR/TPE等注塑成型的制品易出现飞边注塑零件飞边又称溢边或者披锋,大多发生在模具上模块相结合的位置。
如:分型面、顶针的孔隙、滑块的配合部位、镶件的缝隙、顶针的孔隙等处。
飞边不及时修正可能会影响产品外观或影响充模过程中的排气;若飞边过大,脱模过程中产生的碎屑可能会残留在模具内部,导致产品出现冷料,严重的还会使模具产生永久性压痕,如果碎屑残留在运动部件,如滑块、顶针等处,还可能导致模具运动不畅。
第一、设备方面(1)成型机合模力不足。
如果成型机的额定合模力小与成型过程中制品从像投影面积上的张力,将会导致分型面间隙,造成飞边。
TPR/TPE注塑缺陷问题解决方案:增大锁模力(2)成型机合模形成不足。
如果成型机合模的最小间隙大于模具的厚度,制品的投影面积超过了注压机的最大注射面积,注压机模板安装调节不正确,模具安装不正确,锁模力不能保持恒定,注压机模板不平行,拉杆变形不均将会导致模具合模不紧密造成飞边。
TPR/TPE注塑缺陷问题解决方案:改进注塑机缺陷第二、模具方面(1)模具本身精度差,如分型面配合不严密;分型面有压痕或疲劳塌陷;分型面间隙过大;TPR/TPE注塑缺陷问题解决方案:改进模具设计(2) 设计不合理,如型腔分布不对称,导致成型时张力不均容易产生分型面飞边;顶出机构不对称,导致顶出时顶针受到扭力,也会产生飞边;排气间隙过大;型腔和型芯对插结构过多;型腔和型芯偏移;模板不平行;模板变形;模子平面落入异物;排气不足;排气孔太大;第三、工艺方面(1) 注射压力过高或速度过快,产生高速高压熔体,导致模具接合部位出现弹性变形,从而产生飞边。
TPR/TPE注塑缺陷问题解决方案:降低注塑速度(2) 温度过高:无论是料筒温度、喷嘴温度还使模具温度过高,都将使塑料熔体黏度下降,流动性增强从而在模块接合部位产生飞边。
TPR/TPE注塑缺陷问题解决方案:降低温度(3)计量过大,会使模具内产生局部高压,如果发生在模块接合部位,将产生飞边。
注塑制品易出现的缺陷、原因和解决方法 Mold flow

1、欠注欠注(short)也可以称为填充不足或短射,是指聚合物不能完全充满模具型腔的各个角落现象,从(Fill Time)。
产生欠注现象的原因及相关解决方案如下:1、注塑设备选择不合理在选择注射机时,注射机的最大注塑量应该大于产品重量(包括制品、流道、飞边等),要得到较好的效果,注塑总量应保证在最大注塑量的85%以下。
2、聚合物流动性能较差针对这种情况,应该在原料中增加适量的助剂,改善树脂的流动性能,同时,检查原料中的再生料的比例,适当减少用量。
或者考虑改进模具的浇注系统,倒是设置浇道位置、扩大浇口、流道和浇口尺寸以及采用较大的喷嘴等,从而改善模具浇注系统的滞流缺陷。
3、浇注系统实际不合理合理的浇注系统考虑到浇口、流道的平衡,各个型腔内的空腔体积要与浇口大小成正比,从而能够使聚合物同时充满各个型腔,同时浇口位置要选择在厚壁处,也可采用分流道平衡布置的设计方案。
对于浇口或流道小、薄、长的情况,熔料在流动过程中压力损失太大,流动受阻,容易产生欠注现象,针对这种情况应该扩大流道截面和浇口面积,必要时可采取多点进料的方法。
4、料温、模温太低通常情况下,料温与充模长度接近于正比例关系,较低的料温会使熔体的流动性能下降,使得充模长度缩短。
当确认料温较低时,应检查料筒加热器是否完好并设法提高料筒温度。
如果为了防止熔料分解,而不得不采取低温注射时,可适当提高料筒前部区段的温度,或者加快注塑的速度,减少聚合物冷却的时间,但是同时应该注意,注射速度过快可能引起熔体破裂而形成皱纹缺陷。
较低的模温会导致熔融聚合物过早地冷却,从而无法填充整个型腔。
针对这种情况,应该将模具加热到满足工艺要求的温度,并且在注塑初期,应减少冷却介质的流量。
如果模具温度始终较低,应该改变冷却系统的设计方案。
5、注塑喷嘴温度低在注射过程中,喷嘴与模具直接接触,由于模具温度一般低于喷嘴温度,且温差较大,两者频繁接触后使喷嘴温度下降,导致熔料在喷嘴处冷凝(又称干尖)。
注塑成型常见产品缺陷的原因及解决方案
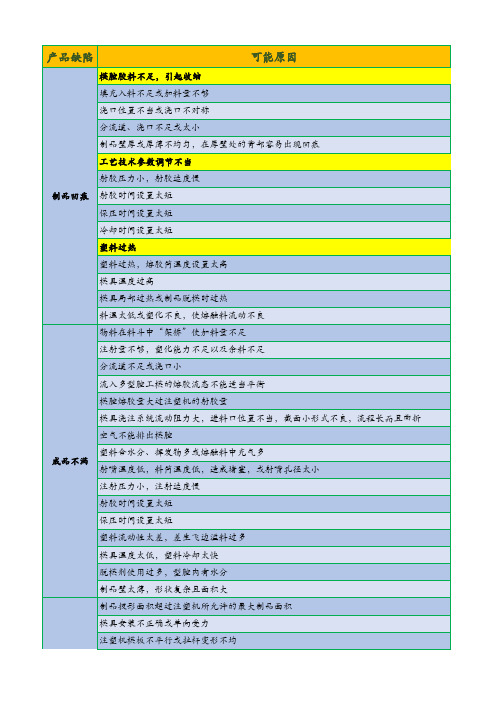
模具局部过热或制品脱模时过热
料温太低或塑化不良,使熔融料流动不良
物料在料斗中“架桥”使加料量不足
注射量不够,塑化能力不足以及余料不足
分流道不足或浇口小
流入多型腔工模的熔胶流态不能适当平衡
模腔熔胶量大过注塑机的射胶量
模具浇注系统流动阻力大,进料口位置不当,截面小形式不良,流程长而且曲折
空气不能排出模腔
模具安装不正确或单受力
注塑机模板不平行或拉杆变形不均
制品披锋
模具平行度不良或模边有阻碍 制品披锋 模具分型面密合不良,型腔和型芯偏移或滑动零件的间隙过大
塑料流动性太大且加料量太大 型腔料温高,模温过高 注射压力过大,注射速度过快 锁模力不恒定或锁模力不均匀 浇口系统形式不当,浇口小,分流道小,流程长,流料阻力大,料温下降快 料温太低或模温太低 塑料流动性差,有冷料掺入,冷却速度快 模具内有水分或润滑剂熔融料充气过多,脱模剂过多 熔接不良 注射压力太小或注射速度慢 制品形状不良,壁厚薄不均匀,使熔融料在壁薄处汇合 模具冷却系统不当或排气不良 塑料内掺有不相溶的料、油质或脱模剂不当 塑料污染,干燥不良或有挥发物 塑料及回料混合比例大,使塑料收缩方向性过大或填料分布不均 不适当的脱模设计,制品壁薄,脱模斜度小,有尖角及缺口,容易产生应力集中 顶针或环定位不当,或成型条件不当,应力过大,顶出不良 制品裂纹 工模温度太低或温度不均 注射压力太低,注射速度过慢 射胶时间和保压时间太短 冷却时间设置不当,太长或太短 制品脱模后或后冷却不均匀,或脱模剂使用不当
塑料含水分、挥发物多或熔融料中充气多 成品不满
射嘴温度低,料筒温度低,造成堵塞,或射嘴孔径太小
注射压力小,注射速度慢
射胶时间设置太短
保压时间设置太短
塑料流动性太差,差生飞边溢料过多
注塑成型缺陷之原因分析及对策
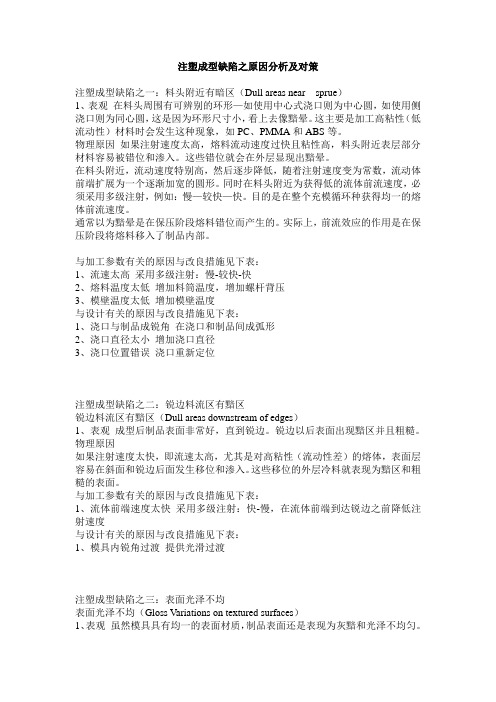
注塑成型缺陷之原因分析及对策注塑成型缺陷之一:料头附近有暗区(Dull areas near sprue)1、表观在料头周围有可辨别的环形—如使用中心式浇口则为中心圆,如使用侧浇口则为同心圆,这是因为环形尺寸小,看上去像黯晕。
这主要是加工高粘性(低流动性)材料时会发生这种现象,如PC、PMMA和ABS等。
物理原因如果注射速度太高,熔料流动速度过快且粘性高,料头附近表层部分材料容易被错位和渗入。
这些错位就会在外层显现出黯晕。
在料头附近,流动速度特别高,然后逐步降低,随着注射速度变为常数,流动体前端扩展为一个逐渐加宽的圆形。
同时在料头附近为获得低的流体前流速度,必须采用多级注射,例如:慢—较快—快。
目的是在整个充模循环种获得均一的熔体前流速度。
通常以为黯晕是在保压阶段熔料错位而产生的。
实际上,前流效应的作用是在保压阶段将熔料移入了制品内部。
与加工参数有关的原因与改良措施见下表:1、流速太高采用多级注射:慢-较快-快2、熔料温度太低增加料筒温度,增加螺杆背压3、模壁温度太低增加模壁温度与设计有关的原因与改良措施见下表:1、浇口与制品成锐角在浇口和制品间成弧形2、浇口直径太小增加浇口直径3、浇口位置错误浇口重新定位注塑成型缺陷之二:锐边料流区有黯区锐边料流区有黯区(Dull areas downstream of edges)1、表观成型后制品表面非常好,直到锐边。
锐边以后表面出现黯区并且粗糙。
物理原因如果注射速度太快,即流速太高,尤其是对高粘性(流动性差)的熔体,表面层容易在斜面和锐边后面发生移位和渗入。
这些移位的外层冷料就表现为黯区和粗糙的表面。
与加工参数有关的原因与改良措施见下表:1、流体前端速度太快采用多级注射:快-慢,在流体前端到达锐边之前降低注射速度与设计有关的原因与改良措施见下表:1、模具内锐角过渡提供光滑过渡注塑成型缺陷之三:表面光泽不均表面光泽不均(Gloss Variations on textured surfaces)1、表观虽然模具具有均一的表面材质,制品表面还是表现为灰黯和光泽不均匀。
- 1、下载文档前请自行甄别文档内容的完整性,平台不提供额外的编辑、内容补充、找答案等附加服务。
- 2、"仅部分预览"的文档,不可在线预览部分如存在完整性等问题,可反馈申请退款(可完整预览的文档不适用该条件!)。
- 3、如文档侵犯您的权益,请联系客服反馈,我们会尽快为您处理(人工客服工作时间:9:00-18:30)。
注塑成型制品常见缺陷及预防措施
作者:徐丽瑜
来源:《知识文库》2016年第04期
一、注塑成型加工在制造业中的应用
塑料加工工艺一般包括:注塑成型、挤塑成型、压塑成型、吹塑成型。
因为注塑机具有能一次成型外型复杂、尺寸精确或带有金属嵌件的质地密致的塑料制品所以被广泛应用于国防、机电、汽车、交通运输、建材、包装、农业、文教卫生及人们日常生活各个领域。
在塑料工业迅速发展的今天,注塑机不论在数量上或品种上都占有重要地位,其生产总数占整个塑料成型设备20%-30%,从而成为目前塑料机械中增长最快,生产数量最多的机种之一。
从涵盖的行业范围及生产总数已经反映了注塑成型工艺在制造业中的地位举足轻重。
我国注塑机行业的技术在近几年进步十分显著,尤其是注塑机的技术水平与国外名牌产品的差距大大缩小,在控制水平、产品内部质量和外观造型等方面均取得明显进步。
我国注塑成型一般以热固性塑料为主,而热塑性塑料的注塑加工在近年也取得了很大的进步。
但国内由于精密制品比较少,复合制品基本没有,因而很少配置机械手,反映国内整体要求相对比较低,与西方国家差距较大,对制品的质量要求还未提高到相应水平,也反映了我国的生产还处在劳动密集型经济。
二、注塑制品的常见缺陷及预防措施
因为制品的质量直接影响到企业的效益,而如果制品中存在缺陷,企业需要派工人进行返工,把制品粉碎后重新加工或者是直接报废,这会提高企业的生产成本。
而产品的质量又直接地影响企业形象与诚信度,要把一切质量问题解决在出厂前。
而一般的一线工人只负责观察塑件是否能正常脱模,面对塑件出现大批量的缺陷,他们无法纠正。
所以为了提高效益,技术人员必须在发现制品缺陷后,及时地进行预防纠正,以及在生产中不断地优化生产工艺、修整模具,以免带来更大的亏损。
下面介绍几种注塑制品常见缺陷及预防措施:
1、变形
(1)模具温度太高,冷却不足:首先考虑延长冷却时间,检查冷却管道循环水是否正常运作。
如果延长冷却时间无法解决,就应考虑模具冷却系统的设计是否合理。
在塑件横截面积大或在浇注口等温度较高的位置要设计比较集中的冷却管道,而在容易冷却的部位应进行缓慢冷却,尽量使塑件各部位冷却均匀。
(2)分子取向不均衡:塑化后的塑料被注射进入型腔内,在型腔中流动的过程中,分子取向是不可避免的,但如果分子取向存在方向上的差异就容易导致塑件翘曲变形。
如果在塑件
发生分子取向不均衡后,再通过外力改变其翘曲变形的现状,通常是只有短暂效果,基本是不见成效的。
应降低塑料温度(第三段-均化段的塑化温度)和模具温度,并且结合使用热处理方法,使塑件脱模后置于较高温度保温一段时间后再缓慢冷却至室温(一般采用随炉冷却或空冷),这样就可以极大地降低塑件内的取向应力。
(3)顶出位置、脱模斜度设计不良:如果顶出位置设计不合理,容易导致塑件脱模时受力不均而导致变形。
而脱模斜度不够及容易导致塑件脱模困难,同样容易造成塑件变形。
这种情况往往会伴随塑件在顶针位置会出现表面发白的现象。
所以在塑件设计时较难脱模收缩较大的位置,需要增加顶针的数量及接触面积(可考虑气动推出设备),增加脱模斜度及边缘的光滑度。
(4)塑件制品厚薄差异大:如果塑件制品厚薄差异大,容易导致塑件的内应力较大而造成变形。
所以在设计塑件时,不光要考虑美观和使用性能,还要考虑工业设计的可行性。
2、制品表面有气泡和银纹
(1)原料含有水分超标或者加热存在挥发物容易导致制品出现气泡和银纹。
只需对原料进行干燥处理或者在加热中排气即可解决。
(2)注塑工艺控制问题:首先料筒温度过高或在料筒内停留时间过长,需要降低料筒前段温度或者改用较小规格注塑机,减短原料塑化时间;其次螺杆背压小,保压压力偏低或降温固化时间短,应该适当提高螺杆背压,保压压力和延迟冷却时间;再次模具温度偏低,塑化的塑料在没有完成充型接触到模具塑料表面马上冷却,就容易出现气泡和银纹,这时需要适当提高模具温度;最后注射压力或注射速度偏高,应适当降低注射压力和注射速度。
3、制品外形结构尺寸不完整
(1)供料不足:首先要考虑设备的选用是否合理,机台的熔胶量必须大于制品的熔胶量,注塑制品重量只能占机台总熔胶量的85%。
排除设备问题后,就需要检查加料口是否有“架桥”现象,可适当增加螺杆注射行程,增加供料量。
此外还可以通过提高注射压力,减小注射速度以延长注射时间,目的都是增加进胶量。
(2)原料流动性差:改善模具浇注系统的滞流缺陷,合理设计浇注口位置,扩大浇口、增加浇口数量、分流道和进胶口尺寸以及采用较大的喷嘴,适当提高原料温度、增加模具温度、减小合模力。
(3)模具设计不当:注意浇注系统浇口平衡,各型腔内塑件的重量要与浇口大小成正比,各型腔能同时充满,合理安排分流道平衡分布的设计方案。
同时要考虑模具排气问题。
在
缺料位置增加排气孔和排气沟槽,在合模面上开设深为0.02-0.04mm,宽度为5-11mm的排气槽,在最终填充处增加排气孔。
4、溢料(在珠三角地区及港澳台企业通常称其为“披锋”)
(1)工艺条件控制不当:发生溢料的最常见原因是注塑机锁模力太低,在塑料注入的过程中会产生极大的压力,而合模力不足就容易导致材料在分模线溢出。
这个时候可以考虑提高锁模力解决。
在排除了合模力不足的情况下,就应该考虑其他工艺条件,例如:注射速度太快、注射时间过长、注射压力在模腔中分布不均、充模速度不均衡,以及注射量过多,都会导致溢料。
这时要适当降低第三段注射速度,降低第三段注射压力和第三段保压压力,也可以降低锁模力。
(2)料温太高,原料流动性太大:通常料温越高,塑料的流动性能越好,这就使得塑料更容易充满型腔,也容易溢料。
而且如果材料本身就具有太大的流动性能,会容易溢料,还容易导致在喷嘴处出现“流涎”现象,需要采用锁闭式喷嘴。
适当降低料筒、喷嘴及模具温度,以提高熔体粘度,预防溢料。
(3)模具缺陷:检查模具是否密封严密,合模面和导柱孔内有无杂物或模板是否有弯曲变形。
以上情况容易导致模具未能完全闭合锁紧而发生溢料。
如果锁模面无损伤,导杆无变形,就应检查模腔是否排气不良,检查排气孔排气槽是否太大、太深。
5、制品表面有熔接痕
(1)料筒温度、模具温度过低:普通塑料在温度越高的情况下,材料的粘度会越低、流动性越好,这就促使材料在分流汇合处的融合性能提高。
可适当提高料筒温度,延长注射周期,对模具进行加温,提高注射压力和注射速度。
(2)原料性能与脱模剂的影响:原料本身的流动性欠佳,容易出现熔接缝,尽量选用流动指数为(MI)值较高的塑料。
同时尽量减少脱模剂的使用,脱模剂的性能本身就不利于塑料融合。
(3)塑件结构与模具设计不合理:在设计塑件时应考虑塑件壁厚相差不能太悬殊以及尽量减少嵌件的使用。
在模具设计时,首先要考虑浇口形式和浇口位置,尽量选用分流少的浇口形式,尽量保持进胶速度的平衡;其次需要排除模具排气不良,检查气孔中是否存在异物堵塞,同时降低料温和模具温度缩短注射时间,降低注射压力;最后要保证熔接角度在135°左右。
三、总结
从企业的生产成本和企业信誉的角度考虑,及时对制品缺陷进行纠正是十分有必要的。
在大部分中小型企业中如果材料出现缺陷,基本上只有溢料这种情况可以返工,而出现其他几种缺陷而且缺陷比较明显的情况一般只能选择直接报废。
这就极大地增加了生产成本,降低生产效率。
所有我们必须要在调试和修模过程中不断的优化生产加工工艺,力求把效率与制品质量达到最高。
在质量分析纠正缺陷的过程中,我们一般遵循先尝试控制注塑工艺,通过调试注塑机的相关参数,对注塑机调为手动,注塑几个制品观察是否依然存在缺陷。
如果控制注塑工艺还无法纠正缺陷,再考虑进行修模。
因为从加工成本及时间成本来考虑,调试注塑机只需要几分钟就可以看到效果,但是一旦要进行修模,成本大幅上升。
针对注塑件可能存在的缺陷,在设计阶段需要遵循模具设计和制品结构设计的相关规范和原则,在加工中合理安排工艺参数,不仅可缩短消除制品缺陷的时间,而且可增加产品及格率,有利于提高经济效益。
(作者单位:广州市增城区职业技术学校)。