现场IE改善案例分析.pptx
合集下载
现场IE改善(PPT47张)
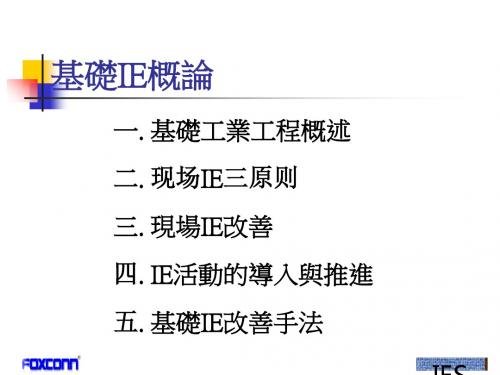
5、改善瓶颈岗位
(1)改善的4大原則
1)减少动作次数 2)同时使用双手 3)缩短移动距离 4)使动作变得轻松
(2) IE动作改善的4原则
ECRS原则 1、Eliminate 2、Combine 3、Rearrange 4、Simplify
——取消 ——合并 ——重排 ——简化
(3)ECRS法运用图示简介
四.基礎IE改善手法 1﹒何謂基礎IE手法
“基礎IE手法是以人的活動為中心 ﹐以事實為依據﹐用科學的分析方法對 生產系統進行觀察﹑記錄﹑分析﹐並對 系統問題進行合理化改善﹐最后對結果 進行標準化的方法”
IE手法一﹕動作改善法(作業標準化)
作業員須每隔28秒轉 身一次﹐取身后的膠 帶﹐這樣每小時須做 150次轉身無效轉身取 膠帶動作
3600<H> 节拍<TT>= 目标产量
二. 现场IE改善<3>
2.现场IE三原则 a、划节距线<25-30cm>,根据标准工时 调整拉速节拍<TT>。 b、保证每个节距有一个产品。 c、每个岗位不准堆积。
生产线平衡计算
平衡率=
(各工序的作业时间总和) * 100% 瓶颈岗位时间*人数<工位数>
改变观念
1、观念改变 2、行动改变 则 则 行动改变 习惯改变
3、习惯改变
则
命运改变
团队与集团的区别
集体
目标不一致
团队
目标一致
Q&A time
本課程到此告一段落﹐請大家就有疑問 的部分踴躍提問﹐謝謝﹗
• • • • • • • • • • • • • • • • • • • • • • • • • • • • • • • • • • • • • • • • • • • • • • • • • • • • • • • • • • • • • • • • • • • • • • • • • • • • • • • • • • • • • • • • • • • • • • • • • • • •
IE改善实战技法ppt课件
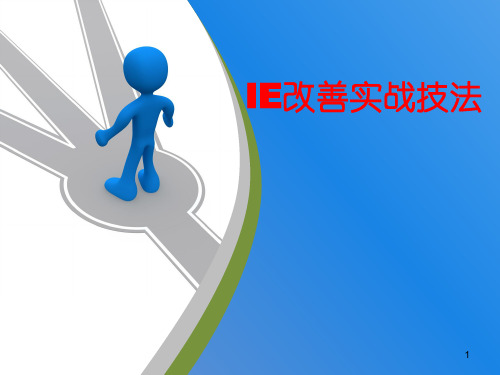
距離或節省操作時間?
• 能否使用不同的肌肉群?如 手指、腕部、前臂、上臂、 軀幹等?。
• 能否使用較強的肌肉組?如 用大腿肌肉擔負重荷,以 腳操從台鉗。
• 能否消除或縮短用手握緊 的時間。
31
31
查檢表應用示例
能否消除“握緊”?能否使用工具和設備?
• 答:可以在工作台上安裝六角形夾具,以保持六角 螺母的牢固、直立,從而消除用手握緊的動作。
能否改變作業次?能否採用槓桿原原理?
• 答:將拉桿旋到螺栓上,比螺栓旋到桿上容易,因 為前者可利用槓桿的作用,使操作變得容易。
能否降低對視力的要求?
• 答:將小零件放在操作者面前,尋找方便。
32
32
问题讨论
我司现场的作业那些地方可以改善,应如何 改善?
33
IE七大手法之二—— 流程法
意义:
泰勒的第一个案例:沙铲
吉尔布雷斯夫妇 砌墙动作不依赖直觉,而以扎实 的资料作根据;影片分析(MTM);
3
如何降低生產成本
廠
址 選 擇 分 析
工 序 分 析
作 業 分 析
動 素 分 析
效益
使用工業工程手法來進行
4
4
IE概论
定义 1: • 工业工程是对人员、物料、设备、能源和信息所组成的集
成系统,进行设计、改善和设置的一门学科.它综合运用数 学、物理学和社会科学方面的专门知识和技术,以及工程 分析和设计的原理与方法,对该系统所取得的成果进行确 定、预测和评价. • ----美国 工业工程师学会(AIIE) 1995年) 定义 2: • 工业工程是对一个组织中人、物料和设备的使用及其费用 作详细分析研究,这种工作由工业工程师完成,目的是使组 织能够提高生产率、利润率和效率. • ----美国 大百科全书 1982年版
• 能否使用不同的肌肉群?如 手指、腕部、前臂、上臂、 軀幹等?。
• 能否使用較強的肌肉組?如 用大腿肌肉擔負重荷,以 腳操從台鉗。
• 能否消除或縮短用手握緊 的時間。
31
31
查檢表應用示例
能否消除“握緊”?能否使用工具和設備?
• 答:可以在工作台上安裝六角形夾具,以保持六角 螺母的牢固、直立,從而消除用手握緊的動作。
能否改變作業次?能否採用槓桿原原理?
• 答:將拉桿旋到螺栓上,比螺栓旋到桿上容易,因 為前者可利用槓桿的作用,使操作變得容易。
能否降低對視力的要求?
• 答:將小零件放在操作者面前,尋找方便。
32
32
问题讨论
我司现场的作业那些地方可以改善,应如何 改善?
33
IE七大手法之二—— 流程法
意义:
泰勒的第一个案例:沙铲
吉尔布雷斯夫妇 砌墙动作不依赖直觉,而以扎实 的资料作根据;影片分析(MTM);
3
如何降低生產成本
廠
址 選 擇 分 析
工 序 分 析
作 業 分 析
動 素 分 析
效益
使用工業工程手法來進行
4
4
IE概论
定义 1: • 工业工程是对人员、物料、设备、能源和信息所组成的集
成系统,进行设计、改善和设置的一门学科.它综合运用数 学、物理学和社会科学方面的专门知识和技术,以及工程 分析和设计的原理与方法,对该系统所取得的成果进行确 定、预测和评价. • ----美国 工业工程师学会(AIIE) 1995年) 定义 2: • 工业工程是对一个组织中人、物料和设备的使用及其费用 作详细分析研究,这种工作由工业工程师完成,目的是使组 织能够提高生产率、利润率和效率. • ----美国 大百科全书 1982年版
《IE现场优化改善》课件

展望
未来企业应进一步拓展IE现场优化改 善的领域,加强与其他管理方法的融 合,实现更高效、更灵活、更智能的 生产模式。
谢谢观看
《IE现场优化改善》PPT课件
目录
• IE现场优化改善概述 • IE现场优化改善方法 • IE现场优化改善案例分析 • IE现场优化改善的未来发展 • 结论与建议
01
IE现场优化改善概述
定义与目标
定义
IE现场优化改善是一种通过系统地分析和改进生产现场的布局、操作流程、设 备及工装夹具等,以提高生产效率、降低成本、提升质量的管理方法。
费,提升产品质量和客户满意度。
动作分析
01
动作分析的定义
通过对作业过程中动作的分析和研究,寻找最优的动作方法和顺序。
02
动作分析的工具
动素分析、动作经济原则。
03
动作分析在IE现场优化中的应用
通过动作分析,消除多余和无效的动作,提高作业效率和生产线的平衡
,降低成本和浪费,提升产品质量和客户满意度。
制定标准、宣传培训、执行落实、检查考 核、持续改进。
通过5S管理,优化现场布局,提高作业效 率和生产线的平衡,减少浪费和不良品, 保障员工安全和健康。
流程优化
流程优化的定义
对现有流程进行分析、改进和优化,提高流程效率和效果。
流程优化的原则
明确目标、关注瓶颈、整体优化、持续改进。
流程优化的方法
流程图绘制、流程分析、流程改进、流程再造。
时间研究
时间研究的定义
通过对作业过程中所需时间的分析和研究,制定标准作业时间。
时间研究的工具
时间测量表、工作抽样。
时间研究在IE现场优化中的应用
通过时间研究,制定合理的生产计划和排程,提高生产效率和产能,降低成本和浪费,提 升产品质量和客户满意度。
未来企业应进一步拓展IE现场优化改 善的领域,加强与其他管理方法的融 合,实现更高效、更灵活、更智能的 生产模式。
谢谢观看
《IE现场优化改善》PPT课件
目录
• IE现场优化改善概述 • IE现场优化改善方法 • IE现场优化改善案例分析 • IE现场优化改善的未来发展 • 结论与建议
01
IE现场优化改善概述
定义与目标
定义
IE现场优化改善是一种通过系统地分析和改进生产现场的布局、操作流程、设 备及工装夹具等,以提高生产效率、降低成本、提升质量的管理方法。
费,提升产品质量和客户满意度。
动作分析
01
动作分析的定义
通过对作业过程中动作的分析和研究,寻找最优的动作方法和顺序。
02
动作分析的工具
动素分析、动作经济原则。
03
动作分析在IE现场优化中的应用
通过动作分析,消除多余和无效的动作,提高作业效率和生产线的平衡
,降低成本和浪费,提升产品质量和客户满意度。
制定标准、宣传培训、执行落实、检查考 核、持续改进。
通过5S管理,优化现场布局,提高作业效 率和生产线的平衡,减少浪费和不良品, 保障员工安全和健康。
流程优化
流程优化的定义
对现有流程进行分析、改进和优化,提高流程效率和效果。
流程优化的原则
明确目标、关注瓶颈、整体优化、持续改进。
流程优化的方法
流程图绘制、流程分析、流程改进、流程再造。
时间研究
时间研究的定义
通过对作业过程中所需时间的分析和研究,制定标准作业时间。
时间研究的工具
时间测量表、工作抽样。
时间研究在IE现场优化中的应用
通过时间研究,制定合理的生产计划和排程,提高生产效率和产能,降低成本和浪费,提 升产品质量和客户满意度。
IE工业工程与现场改善.pptx
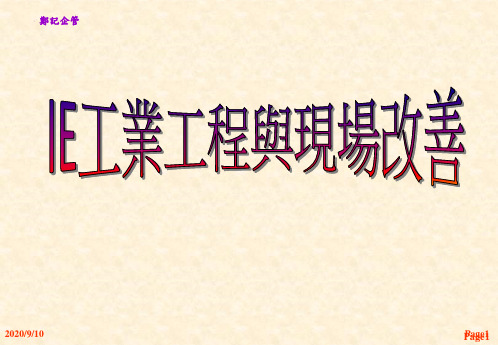
2. 問答:
(1)如此擺放您會放錯嗎?(請在“ □ ”內打“ˇ”作選
擇)
□會
□ 不會
(2) 您不會/會放錯的原因是什麼?
2020/9/10
Page18
鄭記企管 伍.1 IE手法說明 (防錯法/愚巧法)
3.防錯法 之
“三不” 構造原則
2020/9/10
Page19
鄭記企管 伍.1 IE手法說明 (防錯法/愚巧法)
(8)生產線平衡法
2020/9/10
Page10
鄭記企管
名稱
(1)防錯法 (2)動改法 (3)流程法
(4)五五法
2020/9/10
參、 手法之效能
目的
如何避免做錯事情,使工作第一次 就做好的精神能夠具體實現。
改善人體動作的方式,減少疲勞使工作 更為舒適、更有效率,不要蠻幹。 研究探討牽涉到幾個不同工作站或地 點之流動關系,藉以發掘出可資改善 的地方。 藉著質問的技巧來發掘出改善的構想
1 藉“共同”動作必須同時執行來完成。 2 藉“順序”動作來完成。 3 藉“交互”動作來完成。
2020/9/10
Page24
鄭記企管 伍.1 IE手法說明 (防錯法/愚巧法)
適 應性
不 斷
消除浪費降低成本
柔性生產提高競爭力
暴
露
問 題
JIT生產方式
,
不
看板管理
斷
改
善
均衡化生產
良好的外
部協作
2020/9/10
尊 重 人 性 , 發 揮 人 的 作 用
Page3
鄭記企管
IE與精益生產關聯圖
不
斷 暴
質量保證
小批量生產
同步化生產
(1)如此擺放您會放錯嗎?(請在“ □ ”內打“ˇ”作選
擇)
□會
□ 不會
(2) 您不會/會放錯的原因是什麼?
2020/9/10
Page18
鄭記企管 伍.1 IE手法說明 (防錯法/愚巧法)
3.防錯法 之
“三不” 構造原則
2020/9/10
Page19
鄭記企管 伍.1 IE手法說明 (防錯法/愚巧法)
(8)生產線平衡法
2020/9/10
Page10
鄭記企管
名稱
(1)防錯法 (2)動改法 (3)流程法
(4)五五法
2020/9/10
參、 手法之效能
目的
如何避免做錯事情,使工作第一次 就做好的精神能夠具體實現。
改善人體動作的方式,減少疲勞使工作 更為舒適、更有效率,不要蠻幹。 研究探討牽涉到幾個不同工作站或地 點之流動關系,藉以發掘出可資改善 的地方。 藉著質問的技巧來發掘出改善的構想
1 藉“共同”動作必須同時執行來完成。 2 藉“順序”動作來完成。 3 藉“交互”動作來完成。
2020/9/10
Page24
鄭記企管 伍.1 IE手法說明 (防錯法/愚巧法)
適 應性
不 斷
消除浪費降低成本
柔性生產提高競爭力
暴
露
問 題
JIT生產方式
,
不
看板管理
斷
改
善
均衡化生產
良好的外
部協作
2020/9/10
尊 重 人 性 , 發 揮 人 的 作 用
Page3
鄭記企管
IE與精益生產關聯圖
不
斷 暴
質量保證
小批量生產
同步化生產
IE手法及现场改善手册.pptx

Taylor首創的概念有二:
工作設計(或稱方法研究):主要用於分析一 項操作的工作需求與相關的方法規格。 工作衡量:用於定義該項操作的適當操作時間 。
吉爾布斯夫婦
吉爾布斯夫婦( Frank B.Gilbreth 18681924) 最重要的貢獻是在於將人的基本動作 分析出來,這些基本動作被他稱為「動素」 ,如搜尋、尋找、移動、準備、握取等動作 ,透過將動作加以細微分解之後,他能夠將 工作有效率的改善。
IE 七大手法
為甚麼要有改善(IE)七大手法?
* 以不教而戰,謂之殺. * 徒然要求改善而不講求方法、技巧,於事無補. * 給人一條魚吃,不如教他捕魚的技術. * 要求捕更多的魚,首先必須講求捕魚技術的傳授與使用. * 改善七大手法(IE 7 TOOLS)就是協助我們改善我們工作的技術.
IE改善技術
莉莉廉吉爾布斯 (Lillian M.Gilbreth) 把人因 (human factor)方面帶進許多研究工作中。這後來 造成了組織理論和管理學很大的影響。莉莉廉吉爾布 斯 後來被稱為工程的第一夫人以及管理學的第一特 使。
甘特
甘特(Henry Laurence Gantt 1861-1919)此人最重要的發 明是甘特圖(Gantt Chart)。
出可資改善的地方.
藉著質問的技巧來發掘出改善的構想. 研究探討操作人員與機器工作的過程,藉以發掘出可資改善的地 方. 研究人體雙手在工作時的過程,藉以發掘出可資改善之地方. 藉著抽樣觀察的方法能很迅速有效地了解問題的真象.
防止錯誤法
防止錯誤法
防止錯誤法
防止錯誤法
1>. 斷根原理: 將會造成錯誤的原因從根本上排除掉,使絕不發生錯誤.
2>. 保險原理: 采用二個以上的動作必需共同或依序執行才能完成工作.
工作設計(或稱方法研究):主要用於分析一 項操作的工作需求與相關的方法規格。 工作衡量:用於定義該項操作的適當操作時間 。
吉爾布斯夫婦
吉爾布斯夫婦( Frank B.Gilbreth 18681924) 最重要的貢獻是在於將人的基本動作 分析出來,這些基本動作被他稱為「動素」 ,如搜尋、尋找、移動、準備、握取等動作 ,透過將動作加以細微分解之後,他能夠將 工作有效率的改善。
IE 七大手法
為甚麼要有改善(IE)七大手法?
* 以不教而戰,謂之殺. * 徒然要求改善而不講求方法、技巧,於事無補. * 給人一條魚吃,不如教他捕魚的技術. * 要求捕更多的魚,首先必須講求捕魚技術的傳授與使用. * 改善七大手法(IE 7 TOOLS)就是協助我們改善我們工作的技術.
IE改善技術
莉莉廉吉爾布斯 (Lillian M.Gilbreth) 把人因 (human factor)方面帶進許多研究工作中。這後來 造成了組織理論和管理學很大的影響。莉莉廉吉爾布 斯 後來被稱為工程的第一夫人以及管理學的第一特 使。
甘特
甘特(Henry Laurence Gantt 1861-1919)此人最重要的發 明是甘特圖(Gantt Chart)。
出可資改善的地方.
藉著質問的技巧來發掘出改善的構想. 研究探討操作人員與機器工作的過程,藉以發掘出可資改善的地 方. 研究人體雙手在工作時的過程,藉以發掘出可資改善之地方. 藉著抽樣觀察的方法能很迅速有效地了解問題的真象.
防止錯誤法
防止錯誤法
防止錯誤法
防止錯誤法
1>. 斷根原理: 將會造成錯誤的原因從根本上排除掉,使絕不發生錯誤.
2>. 保險原理: 采用二個以上的動作必需共同或依序執行才能完成工作.
现场IE改善方向与方法PPT课件

理由﹔ 10)不要为现状辩解﹐实事求是﹔
.
10
5.传统的工业工程应用(工作研究)
方法 研究
时间 研究
程序 分析
动作 分析
流程经济原则 动作经济原则
客观\公平\准 确地制定工站 标准时间
简化工作并设计更经济的方法和 程序,之后设定标准工作方法. 1:方法,程序 2:材料 3:工具与设备 4:环境与条件
.
23
2﹒IE手法的目的﹕
1) 准确掌握生产活动的实际状态﹔ 2) 尽快地发现浪费﹑不合理﹑不可
靠的地方﹔ 3) 对生产活动的改善和标准化进行
系统的管理﹒
.
24
3﹒IE手法的特征﹕
1) 不同的人能得到同样的分析结果﹔ --客观性﹔
2) 是现状的定量衡量﹐容易检讨﹔ --定量性﹔
3) 相同图表和符号语言﹐信息共享﹔ --通用性﹒
辅助时间
便于操作而发生的时间,例如:翻转产品,移动身体
净时间*
操作动作的时间,例如:安装,锁紧,剪除等时间
.
29
第二章﹕
八大浪费
(Eight waste)
.
30
八大浪费介绍
不良品浪费 ❖ 过生产浪费 过程浪费 动作浪费 库存浪费 移动浪费 不平衡浪费 管理浪费
.
31
一. 不良品浪费
------美国工业工程师学会(AIIE)1995年
.
6
2.IE的定义
我们的定义:“规划/改善/创新/诊断﹐先进制 造生产力﹐标准化﹑高效化﹐提升绩效”
---PCBA IE 2005年
.
7
3.IE的基本意识
1) 成本和效率﹔ 2) 改善和变革﹔ 3) 简化和标准化﹔ 4) 系统和人本意识﹔
.
10
5.传统的工业工程应用(工作研究)
方法 研究
时间 研究
程序 分析
动作 分析
流程经济原则 动作经济原则
客观\公平\准 确地制定工站 标准时间
简化工作并设计更经济的方法和 程序,之后设定标准工作方法. 1:方法,程序 2:材料 3:工具与设备 4:环境与条件
.
23
2﹒IE手法的目的﹕
1) 准确掌握生产活动的实际状态﹔ 2) 尽快地发现浪费﹑不合理﹑不可
靠的地方﹔ 3) 对生产活动的改善和标准化进行
系统的管理﹒
.
24
3﹒IE手法的特征﹕
1) 不同的人能得到同样的分析结果﹔ --客观性﹔
2) 是现状的定量衡量﹐容易检讨﹔ --定量性﹔
3) 相同图表和符号语言﹐信息共享﹔ --通用性﹒
辅助时间
便于操作而发生的时间,例如:翻转产品,移动身体
净时间*
操作动作的时间,例如:安装,锁紧,剪除等时间
.
29
第二章﹕
八大浪费
(Eight waste)
.
30
八大浪费介绍
不良品浪费 ❖ 过生产浪费 过程浪费 动作浪费 库存浪费 移动浪费 不平衡浪费 管理浪费
.
31
一. 不良品浪费
------美国工业工程师学会(AIIE)1995年
.
6
2.IE的定义
我们的定义:“规划/改善/创新/诊断﹐先进制 造生产力﹐标准化﹑高效化﹐提升绩效”
---PCBA IE 2005年
.
7
3.IE的基本意识
1) 成本和效率﹔ 2) 改善和变革﹔ 3) 简化和标准化﹔ 4) 系统和人本意识﹔
IE与提案改善.pptx
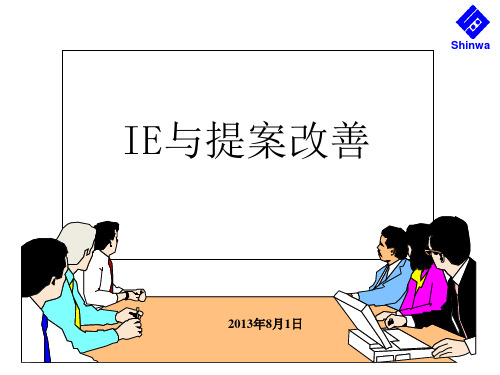
2.8 小时
我们的人力成本是美国的30分之一,生产成本
是美国的3倍
开源
靠策略,靠技术
节流
靠持续改善
改善的基本知识
• 对“改善量变与质变”的正确理解小步阶梯式Sh改inwa
常识性的工具, 进,逐次累积 技巧,不花钱或 而发生质变
全员参与, 少花钱
轻松工作
超越目 前水平
质变
量变
改善的基本知识
改善的目标及改善的主要指针
Shinwa
其实提案活动等类似的由下往上的管理运动,是为了能让这中间的 六成人,也能加入其中。在近年来,企业文化受到重视,这是由于这些 能左右这六成人的行动形式。企业的实力,也是受到这些占有六成的人 之水平来决定的。
这些二成的优秀而积极的人,不管在任何组织或公司之中,他们都 会表现出其个人的意愿开发能力,而显露出其头角。但是,中间的这六 成人,却不是如此。要开发其能力、发挥其能力,即需要有一套策动的 办法或系统。其中之一就是 改善提案制度。
Shinwa
Safer (更安全)
Accurate (更准确)
Better/Best (更好/最好)
Faster (交期更短)
Continuously Consistently (持续,稳定)
Cheaper (成本更低)
Easier
Delightful
(作业更容易) (工作更愉快)
• Productivity ✓ 制造更多的产品 • Quality ✓ 制造更受欢迎的品质 • Cost ✓ 更低廉的成本 • Delivery ✓ 更短的周期 • Safety ✓ 安全的工作环境 • Morale ✓ 高昂的士气
将大多数的员工加以策动,使改善固定化,这是塑造出改善成为企 业文化的一种方法。因此,改善提案活动并不是只有一部分有意愿的人 做就可以了。最理想的就是100% 的全部都来参与。最少也要有二成的人, 加上六成的人,合计八成的人来参加。
现场IE改善讲义(PPT 144页)

生产过程中的改善点
瓶颈环节或工序 成本高昂的工序 质量不稳定的工序 劳动强度大、劳动条件恶的工序 容易发生事故的工序
19.12.2019
现场工业工程
23
主要分析技术
类别
程序 分析
作业 分析
动作 分析
分析方法
工艺程序图 流程程序图
线路图 人机作业分析 联合作业分析 双手作业分析
动素分析
影像分析
现场工业工程
方法 (如何做)
加工内容、 次序
依次搬运的 人数、装货 、卸货的方
法等 检查方法、 判定标准、 不良品的处
理方法
容器的放置 方法、产品 的摆放方式
等。
37
作 业 流 程 分 析 实 例
4.对测定结果进行整理
整理表(表7.9)
项 目 工程数量 时间(分) 距离(M) 人数(人)
加工
2
75
19.12.2019
现场工业工程
21
方法研究的改善范围
改善工厂、车间和工作场所的布置,缩短工艺
和运输的路线
改善对原材料、机器设备和劳动力的运用,以
减少资源投入,获得更多产出
减轻劳动强度,避免生产劳动中不必要的体力
消耗,节省人力
改进工作环境, 改善劳动条件
19.12.2019
现场工业工程
22
方法研究
把工作简化并定出 进行此项工作的更 经济的方法和程序
作业测定
确定进行某项工作 所需时间的长短
“工作研究”是改善 生产力的基本技巧之一
提高
生产率
19.12.2019
现场工业工程
16
工作研究的范畴
1 方法研究----用以确定最佳的作业方法的一系列研究 技术,包括: (1)程序分析----对整个生产过程或一项管理工作 的全面分析。 (2)作业分析----对同一工作地上的工作进行分析。 (3)动作分析----将过程分解为基本单元直到手指 的动作分析。
- 1、下载文档前请自行甄别文档内容的完整性,平台不提供额外的编辑、内容补充、找答案等附加服务。
- 2、"仅部分预览"的文档,不可在线预览部分如存在完整性等问题,可反馈申请退款(可完整预览的文档不适用该条件!)。
- 3、如文档侵犯您的权益,请联系客服反馈,我们会尽快为您处理(人工客服工作时间:9:00-18:30)。
4、工时测定分析(蓝色为作业的时间红色为失去平
衡的时间)
5、生产线平衡的计算
生产平衡率(%)=各工程净时间总计/(时间最长工程*人 员数)*100%
如上图表中,生产线平衡率=1505/(90*19)*100%=88% 不平衡率%=100%-平衡率(%) 对生产线来说,不平衡率越小越好,一般控制5%-13%之间,
有多少岗位是不增值的
扑克牌游戏规则
1、每个分厂安排4个人(厂长、工艺、作业长、班长) 2、小组内部自己安排4个人的工作 3、要求是将52张扑克牌按同一花色、从大到小的排成一排 4、时间最少的小组获胜 5、开始和结束计时以固定的人员手敲桌子为准 6、游戏开始由工作人员将牌洗好
评分标准
1.2.3.4名分别100.80.60.40分错 一张牌,扣10分
(2)IE动作改善的4原则:
• ECRS原则 1.Eliminate —取消 2、Combine —合并 3、Rearrange —重排 4、Simplify —简化
(3)ECRS法运用图示ห้องสมุดไป่ตู้介
生产线平衡—例1:缩短生产节拍
提升生产速度,维持人手不变
缩短生产节拍 将工序2里一部 分可抽离的时间 转至3工序里, 以缩短整体的生 产节拍
降低线体速度,减少生产产量
减少人手(2) 因生产需求量降低而可 降低线体速度
将工序3.4的工作时间 分配至工序1.2.5里,从 而工序3.4工作岗位的 人手可调配至其它生产 线去。
(4)4种增值的工作
站在客户的立场上,有四种增值的工作
1、使物料变形 2、组装 3、改变性能 4、部分包装
现在请大家思考一下…… 我们的生产线上
电装7人线标准工时
请 计 算 平 衡 率
6、生产线平衡分析的方法
1、确定对象与范围 2、用作业分析把握现状 3、测定各工程的净时间 4、制作速度图标 5、计算平衡 6、分析结果,制定改善方 案
7、改善瓶颈岗位
(1)改善的4大原则
1)减少动作次数 2)同时使用双手 3)缩短移动距离 4)使动作变得轻松
在熟练度、合理性、工作热情及其他所有方面都相同的标 准作业员以标准的作业方法及一般的努力程度进行作业, 次日不会感到疲劳的作业时间
二、生产平衡分析方法
1、识别瓶颈岗位
2、作业岗位工时测定
A通过1,B前端到达1所需时间
3、建立山积表
将各分解动作时间,以叠加方式直方图表现的一种研 究作业时间结果的手法。
提升生产速度,维持人手不变
缩短生产节拍
将工序2里一部分可 抽离的时间转至 工序3里,以缩 短整体生产节拍
生产线平衡—例2:减少人手(1人)
减少人员,维持生产速度不变
减少人手(1) 将工序3里的工作时间分 配至工序2/4及5之内, 从而工序3里的人手可调 配其它生产线去 可行性:需工序2,4及5 内均有足够时间接受额 外工作。
减少人员,维持生产速度不变
减少人手(1) 将工序3里的工作时间分配
至工序2.4及5内,从而工 序3里的人手可调配其它 生产线去 可行性:须工序2.4及5内均 有足够时间接受额外工 作
生产线平衡—例3:减少人手(2人)
降低线体速度,减少生产产量
减少人手(2) 因生产需求量降低而可 降低线体速度
将工序3.4的工作时间分 配至工序1.2.5里,从而 工序3.4工作岗位的人手 可调配至其它生产线去。
开始各小组内部演练一遍
扑克牌游戏结果展示(标准)
三、B值、F值的定义 和计算
B值(缓冲)定义
B值是用来表示某生产线的未完成量的状态的指标
B值=生产线过程中未完工产品(WIP)数量总和/该生产 线作业人数
■B值的最优值为“1”
一个流生产
One world、one dream One piece、one flow One piece flow是指单件的进行生产,即工人 每次只加工一件产品或组件,理想状态下, 任何操作工位间和工位内的多余WIP为零
B值=1
物留
中间停滞 隐藏问题
一、物流
物流
顺畅流动 没有停滞
“一个流”的益处
1.内建品质管理; 2.创造真正的灵活弹性; 3.创造更高的生产力; 4.腾出更多厂房空间 5.改善安全性; 6.改善员工士气;
7.降低存货成本。
B值计算(1)
此生产线B值=9/5=1.6
B值计算(2)
此生产线B值=32/4=8
至少要控制在15%以下
• 请大家观看电子分厂电装3人柔性线视频
1、一边看一边测试,最后计算平衡率 2、计算一下线小时理论产量 3、提出提升线平衡的思路方法
评分标准 1.2.3.4名分别100.80.60.40分 计算公式错不得分 计算公式对,结果错,扣10分
实例计算
计算公式 平衡率=(32+37+40)/(40*3)*100%=90.8%
生产线的平衡计算
节拍—生产周期 最长工序时间(瓶颈岗位时间)决定,生产线的作业时间,等同于节拍 平衡率 平衡率=∑各工序的作业时间/(瓶颈岗位时间*人数)*100% 产品标准工时=每个工位所用时间的总和 生产线平衡损失=1-平衡率
一般要求生产线平衡率要在85%以上
何谓标准工时
标准时间是指,一个熟练工所用规定的作业方法以及标准 速度进行作业所需的作业时间。
现场IE改善案例分析
--生产线平衡分析改善案例
制作:丁会建 日期:2016、11、23
内容安排
一、线平衡定义 二生产线平衡的分析方法 三、B值、F值的定义与计算 四、线平衡案例分析
一、线平衡定义
什么是生产线平衡
◆ 生产线平衡是指构成生产线各道工序所需的时 间处于平衡状态,作业人员的作业时间尽可能保持 一致,从而消除各道工序间的时间浪费,进而取得 生产线平衡
生产线平衡的意义
◆对生产的全部工序进行均衡,调整作业负荷 与工作方式,消除工序不平衡和工时浪费,实 现“一个流”
出 料
入 料
平衡生产线的意义
1)通过平衡生产线可以综合应用到程序分 析,动作分析,layout分析,搬动分析,时 间分析等全部IE手法,提高全员综合素质 2)在平衡的生产线基础上实现单元生产, 提高生产应变能力,对应市场变化实现柔性 生产系统 3)减少单件产品的工时消耗,降低成本 (等同于提高人均产量) 4)减少工序的在制品,真正实现一个流 5)提高设备及工装的工作效率