生产现场IE改善实例
现场改善IE案例演示文稿

例2
利用镜子减小视线移动角度
作业要求:用视波器检查元件
眼
眼
镜子
视
视
波
波
元件 器
器
改善前 1.将元件放置在检查台上 2.用眼检查事播器屏幕
颈部移动角度大
改善后 1.将元件放置在检查台上 2.用眼检查镜中波形
不用移动眼部
例3 将两个以上动作合并 作业要求:盖日期印和合格印
定位
可完成的动作 ●尽可能将零件、工具放在手
够得着的近处 ●减少屈身、弯腰等躯干动作
例8
眼睛的移动 眼睛→颈部→躯干 ●尽可能将零件、工具 放在看得见的近处
例9 减小移动距离 作业要求:将盖板固定在产品上
产品
传送带
人
改善前 盖板放在一边, 取到盖板后固定在产品上 手移动40cm
人
改善后 盖板放在传送带上, 取到盖板后固定在产品上 手移动15cm
改善后
零件有序、对称放置, 双手同时、按顺序工作
例13
尽量缩小作业区域
传送带 工件 作业台
人
传送带 工件
人
★良好的照明有助于提高作业效率 ★适当的通风、正常的温度和湿度可以减轻疲劳 ★加强清扫和整理、合适的工作服可以避免工伤
例14
容器和器具
方形箱子
漏斗状/托盘状箱子
、、、、、、、、、
零件 过滤网 脏屑
例15
漏斗形容器的利用
加压
轴套 方形容器
改善前 从箱子中取轴套, 移动距离长,不好拿
漏斗形容器出口 改善后 从漏斗形容器出口取轴套 取用方便
例16 辅助工具的应用
小零件
小零件
手指
作业台
现场IE改善案例分析--生产线平衡分析改善案例
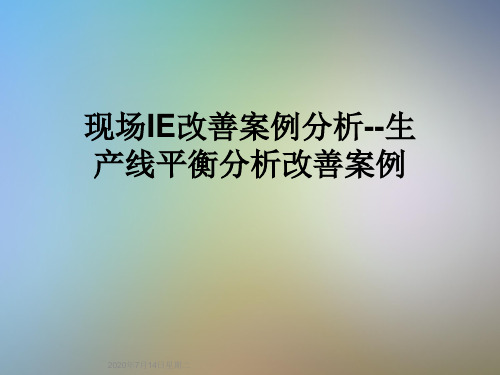
生产线平衡定义
对生产的全部工序进行均衡,调整作业 负荷和工作方式,消除工序不平衡和工 时浪费,实现“一个流”。
出料
入料
平衡生产线的意义
通过平衡生产线可以综合应用到程序分析、动作分析 、layout分析,搬动分析、时间分析等全部IE手法,提 高全员综合素质
在平衡的生产线基础上实现单元生产,提高生产应变 能力,对应市场变化实现柔性生产系统
(4) 4种增值的工作
站在客户的立场上,有四种增值的工作
1、使物料变形 2、组装 3、改变性能 4、部分包装
物料从进厂到出厂,只有不到 10% 的时间是增值的!
工序
符 号
内容
作业内容
分类
加工 作业
○
加工 作业
■产生附加价值的工序及作 业
卖得掉
检查
□
数量检查 ■虽然有必要,但需要进行 品质检查 改善的工序及作业
现场IE改善案例分析--生 产线平衡分析改善案例
2020年7月14日星期二
内容安排
一、线平衡定义 二、生产线平衡分析方法 三、B值、F值的定义与计算 四、线平衡案例分析
一、线平衡定义
生产线平衡定义
什么是生产线平衡
生产线平衡是指构成生产线各道工序所需的 时间处于平衡状态,作业人员的作业时间尽 可能的保持一致,从而消除各道工序间的时 间浪费,进而取得生产线平衡。
减少人手(1)
將工序3里的工作时 间分配至工序2﹑4 及5之內﹐从而工序 3里的人手可调配其 它生产线去
可行性﹕須工序 2﹐4及5內均有足夠 时间接受额外工作。
ቤተ መጻሕፍቲ ባይዱ
生产线平衡-例3﹕减少人手(2人)
降低线体速度,减少生产产量
工作時間
现场IE改善案例分析.pptx
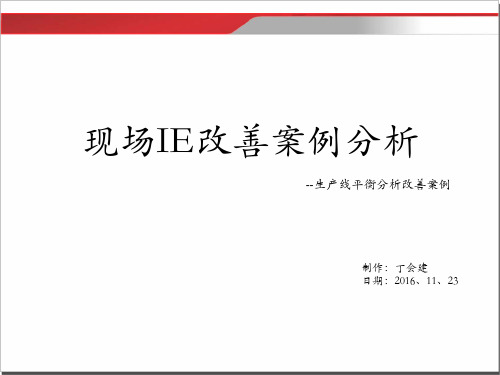
4、工时测定分析(蓝色为作业的时间红色为失去平
衡的时间)
5、生产线平衡的计算
生产平衡率(%)=各工程净时间总计/(时间最长工程*人 员数)*100%
如上图表中,生产线平衡率=1505/(90*19)*100%=88% 不平衡率%=100%-平衡率(%) 对生产线来说,不平衡率越小越好,一般控制5%-13%之间,
有多少岗位是不增值的
扑克牌游戏规则
1、每个分厂安排4个人(厂长、工艺、作业长、班长) 2、小组内部自己安排4个人的工作 3、要求是将52张扑克牌按同一花色、从大到小的排成一排 4、时间最少的小组获胜 5、开始和结束计时以固定的人员手敲桌子为准 6、游戏开始由工作人员将牌洗好
评分标准
1.2.3.4名分别100.80.60.40分错 一张牌,扣10分
(2)IE动作改善的4原则:
• ECRS原则 1.Eliminate —取消 2、Combine —合并 3、Rearrange —重排 4、Simplify —简化
(3)ECRS法运用图示ห้องสมุดไป่ตู้介
生产线平衡—例1:缩短生产节拍
提升生产速度,维持人手不变
缩短生产节拍 将工序2里一部 分可抽离的时间 转至3工序里, 以缩短整体的生 产节拍
降低线体速度,减少生产产量
减少人手(2) 因生产需求量降低而可 降低线体速度
将工序3.4的工作时间 分配至工序1.2.5里,从 而工序3.4工作岗位的 人手可调配至其它生产 线去。
(4)4种增值的工作
站在客户的立场上,有四种增值的工作
1、使物料变形 2、组装 3、改变性能 4、部分包装
现在请大家思考一下…… 我们的生产线上
电装7人线标准工时
请 计 算 平 衡 率
ie工程现场改善方案

ie工程现场改善方案一、引言:随着工程行业的发展,越来越多的企业开始关注工程现场的改善问题。
IE工程作为一种管理和优化工程现场生产的方法,不仅可以提高生产效率,降低成本,还可以改善工作环境,提升员工工作满意度。
本文将以某工程现场为例,提出IE工程现场改善方案,以期为类似的工程现场提供参考。
二、现状分析:某工程现场是一家制造企业的生产基地,主要生产零部件和组件。
然而,该工程现场存在一些问题,例如生产效率低,物料管理混乱,工艺流程不够合理,员工工作负荷过重,工作环境较差等。
这些问题不仅影响了企业的生产和经营,也影响了员工的工作体验和生活质量。
因此,为了解决这些问题,需要对工程现场进行改善。
三、IE工程现场改善方案:1. 进行价值流分析:通过价值流分析,了解生产流程的瓶颈和浪费,找到生产效率低下的原因。
针对分析结果,制定相应的改善计划,优化生产流程。
2. 实施5S管理:建立起规范的物料管理和生产环境,包括整理、整顿、清扫、清洁、素养。
通过5S管理,提高现场的整体效率和安全性。
3. 设计并实施标准化作业程序:为每个工序制定标准化的作业程序,规范生产操作。
通过标准化作业程序,提高生产质量和效率。
4. 应用作业分析技术:通过作业分析,评估员工的工作强度和负荷,合理安排员工的工作任务,避免过重的工作负荷。
5. 实施人机工程学改善:对工作环境进行改善,包括工作高度、工作台面、照明等,提高员工的舒适度和安全性。
6. 建立绩效评价体系:建立合理的绩效评价体系,鼓励员工参与工程现场改善工作,激发员工的工作动力和创造力。
7. 进行员工培训:针对工程现场的改善方案,对员工进行相关的培训,提高员工的技能和素质,增强员工的工程现场管理意识。
8. 建立改善持续改进机制:建立持续改进的机制,定期对工程现场进行检查和评估,及时发现和解决问题,保持工程现场的良好状态。
四、改善效果评估:通过实施上述的IE工程现场改善方案,预计可以取得以下改善效果:1. 生产效率提高:通过价值流分析和优化生产流程,提高生产效率,减少浪费。
现场IE改善案例分析丁会建XX1123
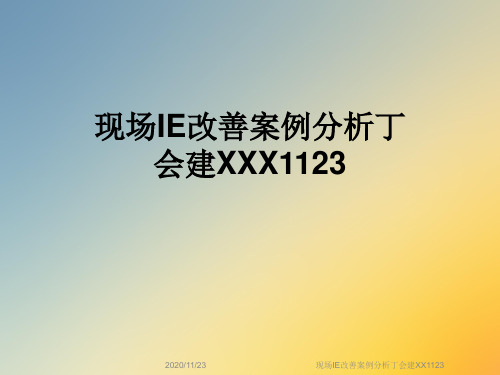
7
24
1
打胶水
2
插变压器线
7
插线
37
1
插线
30
插线
20
功能 功能检验
16
检
拆线
5
45
2
贴断电标贴
4
外观检验
6
外观 检
贴条码
2
14
1
包装
6
改善后
工位 序号
1
4 5
电装7人柔性线(KFR-32G/DY-JN(E3))
岗
位 名
作业内容
动作时 标准工 人员配 间(秒) 时(秒) 置
称
打变压器
10
打电源线
7
打 线
现场IE改善案例分析丁会建XX1123
(4)4种增值的工作
站在客户的立场上,有四种增值的工作
1、使物料变形 2、组装 3、改变性能 4、部分包装
物料从进厂到出厂,只有不到10%的时间是增 值的!
现场IE改善案例分析丁会建XX1123
现场IE改善案例分析丁会建XX1123
现在请大家思考一下…… 我们的生产线上
现场IE改善案例分析丁会建XX1123
实例计算
计算公式 平衡率=(32+37+40)/(40*3) *100%=90.8%
现场IE改善案例分析丁会建XX1123
电装7人线标准工时
请 计 算 平 衡 率
现场IE改善案例分析丁会建XX1123
6、生产线平衡分析的方法
1、确定对象与范围 2、用作业分析把握现状 3、测定各工程的净时间 4、制作速度图标 5、计算平衡 6、分析结果,制定改善方 案
至少要控制在15%以下
IE改善案例展示及学习
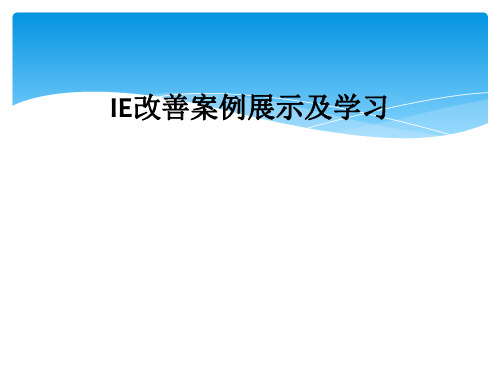
改善对象 改善日期
问题描述
商用公司370型号安装底脚工位员工没有工装,只能用手将底脚安装上,影响员工工作效率
商用公司 2012.07.28
改善措施
根据370底脚样式制作打底脚工装(如图所示),将此工装安在气枪上,把底脚安装好,即省了人力又减少操作时间10s
类别
改善前
改善后
对比照片
差异
员工打底脚时没有工装,用手操作,费时费力
--实验装置之间,而且,试验装 置在另一个房间,从而造成在这 两个房间之间频繁移动现象。
消除一点一滴的浪费是我们追求的目标
1.器皿的配置
作业量减少,操作更简单。简化
2.储水瓶
橡胶软管,橡胶栓种类减少,烧杯减少
3.过滤台(装置的配置台)
作业台减少,有效利用空间
消除一点一滴的浪费是我们追求的目标
改善方案
消除一点一滴的浪费是我们追求的目标
消除一点一滴的浪费是我们追求的目标
消除一点一滴的浪费是我们追求的目标
2.现场改善项目汇总
改善名称 改善部门 问题描述
刷漆工位接漆工装设计 IE办公室
改善类型 改善人
IE改善档案卡
质量改善 管伟琴
生产现场刷漆工位在刷漆过程中油漆经常滴落在压机底板上,影响产品质量
消除一点一滴的浪费是我们追求的目标
1)推进项目汇总表
3.物料模块化进度
项目
第一期 (商用公司)
已完成 7
推进中 0
第二期 (冷柜业务链)
3
4
第二期
(冰箱业务链)
2
5
澳洋
0
8
消除一点一滴的浪费是我们追求的目标
暂不实施 4 0 0 0
现场改善及ie手法

THANK YOU
感谢聆听
时间研究
通过观察和测量作业人员完成某项任务所需的时间,制定合理的时 间标准。
作业标准化
将最优的作业方法和流程标准化,确保所有作业人员都能按照统一 的标准进行操作,提高生产效率和产品质量。
标准作业程序(SOP)制定
编写详细的标准作业程序,明确每一步骤的操作规范和要求,为作 业人员提供明确的指导。
生产线平衡与布局优化
运用各种计划和控制手段,确 保生产系统按照预定目标高效 运行。
IE手法在现场改善中的应用
流程优化
通过分析和改进工作流程,消除浪费、提高效率 。例如,减少不必要的操作步骤、简化工作流程 等。
设备改善
对生产设备进行改进和优化,提高设备效率和可 靠性。例如,采用自动化设备、改进设备维护计 划等。
物料管理
意义
现场改善是企业提高竞争力、实现可持续发展的重要手段之一。 通过现场改善,企业可以不断提高产品质量、降低生产成本、提 高生产效率、增强员工士气,从而赢得更多的市场份额和客户信 任。
现场改善的目标与原则
目标
现场改善的主要目标是提高生产效率、降低生 产成本、提高产品质量、增强员工士气等,以
实现企业的整体经营目标。
现场改善及IE手法
目
CONTENCT
录Hale Waihona Puke • 现场改善概述 • IE手法简介 • 现场改善的步骤与方法 • IE手法在现场改善中的具体应用 • 现场改善的实践案例 • 现场改善的挑战与对策
01
现场改善概述
现场改善的定义与意义
定义
现场改善是一种通过优化工作流程、提高工作效率和质量、降低 成本等方法,对生产现场进行持续改进的管理方法。
IE现场改善指引(非常好)
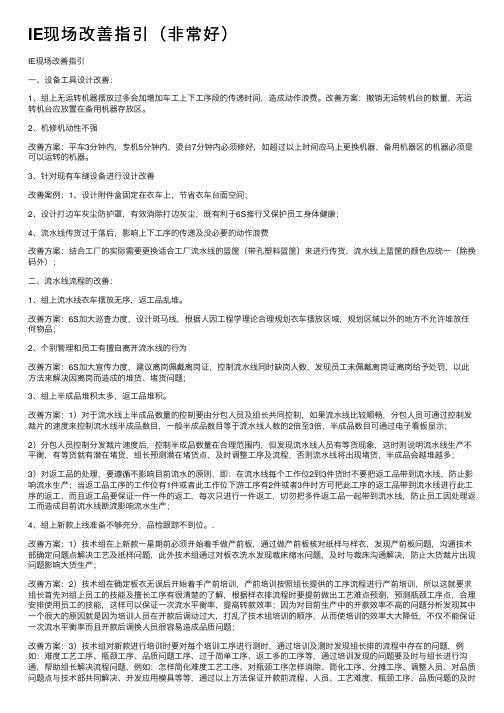
IE现场改善指引(⾮常好)IE现场改善指引⼀、设备⼯具设计改善:1、组上⽆运转机器摆放过多会加增加车⼯上下⼯序段的传递时间,造成动作浪费。
改善⽅案:撤销⽆运转机台的数量,⽆运转机台应放置在备⽤机器存放区。
2、机修机动性不强改善⽅案:平车3分钟内,专机5分钟内,烫台7分钟内必须修好,如超过以上时间应马上更换机器,备⽤机器区的机器必须是可以运转的机器。
3、针对现有车缝设备进⾏设计改善改善案例:1、设计附件盒固定在⾐车上,节省⾐车台⾯空间;2、设计打边车灰尘防护罩,有效消除打边灰尘,既有利于6S推⾏⼜保护员⼯⾝体健康;4、流⽔线传货过于落后,影响上下⼯序的传递及没必要的动作浪费改善⽅案:结合⼯⼚的实际需要更换适合⼯⼚流⽔线的篮筐(带孔塑料篮筐)来进⾏传货,流⽔线上篮筐的颜⾊应统⼀(除换码外);⼆、流⽔线流程的改善:1、组上流⽔线⾐车摆放⽆序,返⼯品乱堆。
改善⽅案:6S加⼤巡查⼒度,设计斑马线,根据⼈因⼯程学理论合理规划⾐车摆放区域,规划区域以外的地⽅不允许堆放任何物品;2、个别管理和员⼯有擅⾃离开流⽔线的⾏为改善⽅案:6S加⼤宣传⼒度,建议离岗佩戴离岗证,控制流⽔线同时缺岗⼈数,发现员⼯未佩戴离岗证离岗给予处罚,以此⽅法来解决因离岗⽽造成的堆货、堵货问题;3、组上半成品堆积太多,返⼯品堆积。
改善⽅案:1)对于流⽔线上半成品数量的控制要由分包⼈员及组长共同控制,如果流⽔线⽐较顺畅,分包⼈员可通过控制发裁⽚的速度来控制流⽔线半成品数⽬,⼀般半成品数⽬等于流⽔线⼈数的2倍⾄3倍,半成品数⽬可通过电⼦看板显⽰;2)分包⼈员控制分发裁⽚速度后,控制半成品数量在合理范围内,但发现流⽔线⼈员有等货现象,这时则说明流⽔线⽣产不平衡,有等货就有潜在堵货,组长预测潜在堵货点,及时调整⼯序及流程,否则流⽔线将出现堵货,半成品会越堆越多;3)对返⼯品的处理,要遵循不影响⽬前流⽔的原则,即:在流⽔线每个⼯作位2到3件货时不要把返⼯品带到流⽔线,防⽌影响流⽔⽣产;当返⼯品⼯序的⼯作位有1件或者此⼯作位下游⼯序有2件或者3件时⽅可把此⼯序的返⼯品带到流⽔线进⾏此⼯序的返⼯,⽽且返⼯品要保证⼀件⼀件的返⼯,每次只进⾏⼀件返⼯,切勿把多件返⼯品⼀起带到流⽔线,防⽌员⼯因处理返⼯⽽造成⽬前流⽔线断流影响流⽔⽣产;4、组上新款上线准备不够充分,品检跟踪不到位。
现场IE改善案例分析生产线平衡分析改善案例
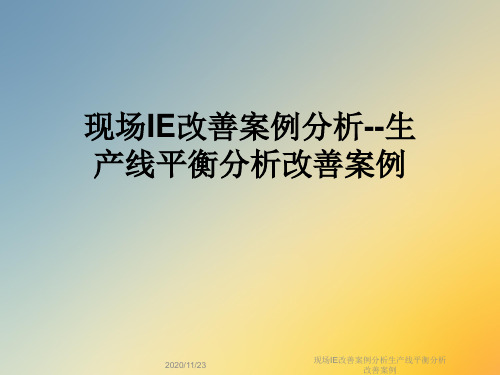
不平衡率(%)= 100% —平衡率(%)
对生产线来说,不平衡率越小越好,一般控 制5%-13%之间,至少要控制在15%以下。
现场IE改善案例分析生产线平衡分析 改善案例
案例:工时测定和线平衡计算
请大家观看电子分厂电装3人柔性线视频
1、一边看一边测试,最后计算平衡率 2、计算一下线小时理论产量 3、提出提升线平衡的思路方法
(1)改善的4大原則
1)减少动作次数 2)同时使用双手 3)缩短移动距离 4)使动作变得轻松
现场IE改善案例分析生产线平衡分析 改善案例
(2) IE动作改善的4原则:
ECRS原则 1、Eliminate ——取消 2、Combine ——合并 3、Rearrange ——重排 4、Simplify ——简化
现场IE改善案例分析生产线平衡分析 改善案例
生产线平衡的改善实例
电子电装7人柔性线,改善前各工位的作业时间如下所示:
现场IE改善案例分析生产线平衡分析 改善案例
生产线平衡的改善实例
电子电装7人柔性线,改善前各工位的作业时间如下所示:
现场IE改善案例分析生产线平衡分析 改善案例
生产线各工位的分析如下:
生产线改善前后各管理指标比较
1、生产线平衡率方面
生产线平衡效 率提高了52%
2、工人人数方面
工人人数由原 来的7人减少至 于3人
3、生产效率方面
生产效率提升 了12.1%
现场IE改善案例分析生产线平衡分析 改善案例
全员参与的思想准备
• 给予和获取信息 • 接受非寻常的工作方法和解决方案 • 对目前的方法提出疑问 • 不允许找借口 • 马上改正错误 • 问五个“为什么”,发掘出问题的真正原因 • 每个人意见都是有价值的 • 不追求完美,一个60%的解决方案,比一个几乎
IE改善案例之一如何解决生产线堆积(doc 15页)
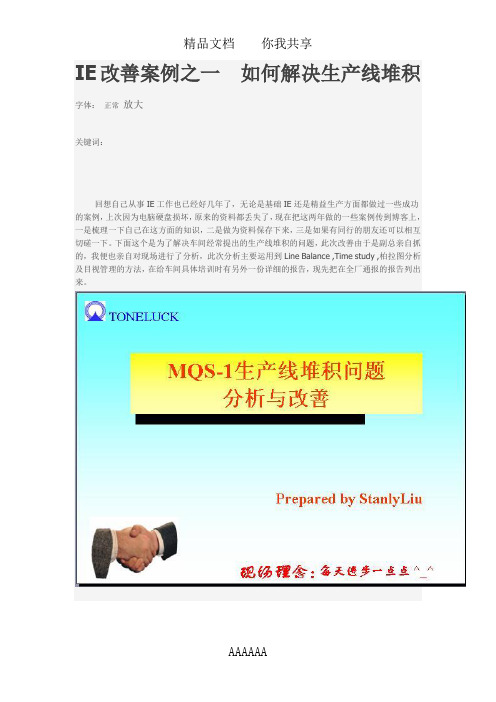
IE改善案例之一如何解决生产线堆积字体:正常放大
关键词:
回想自己从事IE工作也已经好几年了,无论是基础IE还是精益生产方面都做过一些成功的案例,上次因为电脑硬盘损坏,原来的资料都丢失了,现在把这两年做的一些案例传到博客上,一是梳理一下自己在这方面的知识,二是做为资料保存下来,三是如果有同行的朋友还可以相互切磋一下。
下面这个是为了解决车间经常提出的生产线堆积的问题,此次改善由于是副总亲自抓的,我便也亲自对现场进行了分析,此次分析主要运用到Line Balance ,Time study ,柏拉图分析及目视管理的方法,在给车间具体培训时有另外一份详细的报告,现先把在全厂通报的报告列出来。
沁园春·雪
北国风光,千里冰封,万里雪飘。
望长城内外,惟余莽莽;大河上下,顿失滔滔。
山舞银蛇,原驰蜡象,欲与天公试比高。
须晴日,看红装素裹,分外妖娆。
江山如此多娇,引无数英雄竞折腰。
惜秦皇汉武,略输文采;唐宗宋祖,稍逊风骚。
一代天骄,成吉思汗,只识弯弓射大雕。
俱往矣,数风流人物,还看今朝。
IE改善实战技法ppt课件
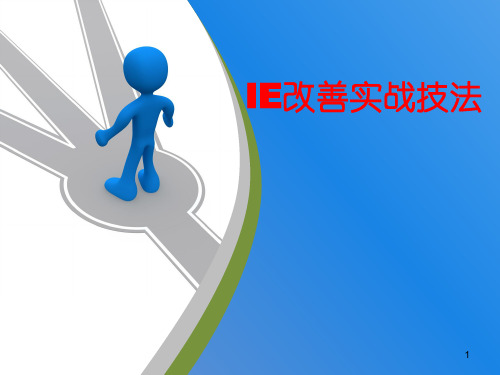
• 能否使用不同的肌肉群?如 手指、腕部、前臂、上臂、 軀幹等?。
• 能否使用較強的肌肉組?如 用大腿肌肉擔負重荷,以 腳操從台鉗。
• 能否消除或縮短用手握緊 的時間。
31
31
查檢表應用示例
能否消除“握緊”?能否使用工具和設備?
• 答:可以在工作台上安裝六角形夾具,以保持六角 螺母的牢固、直立,從而消除用手握緊的動作。
能否改變作業次?能否採用槓桿原原理?
• 答:將拉桿旋到螺栓上,比螺栓旋到桿上容易,因 為前者可利用槓桿的作用,使操作變得容易。
能否降低對視力的要求?
• 答:將小零件放在操作者面前,尋找方便。
32
32
问题讨论
我司现场的作业那些地方可以改善,应如何 改善?
33
IE七大手法之二—— 流程法
意义:
泰勒的第一个案例:沙铲
吉尔布雷斯夫妇 砌墙动作不依赖直觉,而以扎实 的资料作根据;影片分析(MTM);
3
如何降低生產成本
廠
址 選 擇 分 析
工 序 分 析
作 業 分 析
動 素 分 析
效益
使用工業工程手法來進行
4
4
IE概论
定义 1: • 工业工程是对人员、物料、设备、能源和信息所组成的集
成系统,进行设计、改善和设置的一门学科.它综合运用数 学、物理学和社会科学方面的专门知识和技术,以及工程 分析和设计的原理与方法,对该系统所取得的成果进行确 定、预测和评价. • ----美国 工业工程师学会(AIIE) 1995年) 定义 2: • 工业工程是对一个组织中人、物料和设备的使用及其费用 作详细分析研究,这种工作由工业工程师完成,目的是使组 织能够提高生产率、利润率和效率. • ----美国 大百科全书 1982年版
IE改善案例

容
果
示意
工装上限位,可放入十个
1.速度:350PCS/H400PCS/H
2.工作效率提升: UP15% 3.管理费用节约:约840元/年
以上为对工装夹具的改善举例,通过一系列的改进后,生产已明显好转, 部分工装夹具已水平展开至所有工序,目前仍在进一步对工装夹具进行改进。
2.2、生产方式的革新
个人计件(单元式) 生产改善方案 (以306A为例)
圆 刀
角
1人 1人 1人 2人
8人
弹 1人
簧
问题点:
2人
新生产方式
1.制作零部件放置盒 2.培训多能工 3.分组单元式生产 4.个人计件
传递式
零部件放置盒
1014 三个单元
前 壳 附 件 组 装
8人
利点
焊焊焊 擦贴 电插电 线胶 池脚机 路带
板
1人 1人 1人 1组1人
加多能工2人/共6人
装 盖 打 装磨 前 后 螺 防油 壳 盖 丝 尘装
善 2.工作效率提升: UP15%
效 果 3.劳度强度:易疲劳省力
4> 通用测电机
生产改善方案
工程名:电机音质测试
人员:1人/每工位7/14
班 组:二车间机头组/装配组 材料:机头/电机
改善前
劳作 动业 强速 度度 大慢
用两个夹子夹
取电机 夹正极 夹负极 判定
初回改善-个别工位 再次改善-各工位均可使用 使用可
2.1、工装夹具革新
1> 316卷发器生产
改善方案
4/14 工程名:电池盖与铁片组立 人员:3人
班 组:外贸组
材料:电池盖/铁片
改善前
人员手工+螺丝刀操作
IE改善实际案例-产能提升
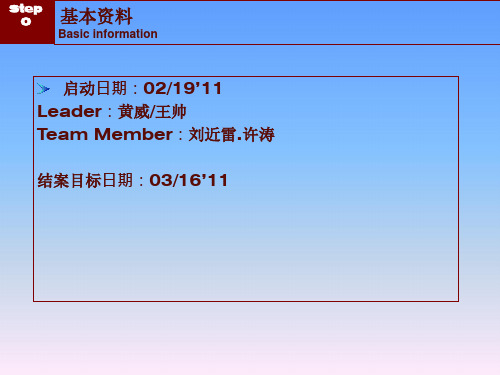
Step 对策拟定与实施
4 Permanent corrective action
物流路线改善
改善前
工序名稱
到栈板放置处取一箱灯管 抬一箱灯管
将周转箱抬回工作台 周转箱产品移入作业完区
合计
時間 min s
7.00 7.00 4.00 26.00 0.04 50.04
改善后
工序名稱
到栈板放置处取一箱灯管 抬一箱灯管
Capping
Capping后 FI
包装
自动 Capping
手动 Capping
P2-Capping
W-Capping P2-Capping
1.自动Capping机台只能生产P2-Capping类产品,当客户需求量超过生产能力时,使用手动配合生产。 机种只能由手动机台生产。
综上,因人力成本远大于自动机台成本,所以提升手工工站效率对成本控制影响巨大!
产能提升:
品名 P2-Capping
产能提升:17.04%,满负荷生产时白夜班可精简2人。
改善前
改善后
全负荷生产时人力/天
22
20
人力成本(RMB/h) 节约工时(h/天) 年节约工时 年节约RMB
10
2.2
5500
55000
Step 水平展开
6 Spread Out 此流程的优化只适用于P2-capping镭射工站,无法水平展开.
起身 走到栈板放置处 左手抓住周转箱边缘凹处
将周转箱抬起 抬起周转箱,向工作台移动
拿取1pcs灯管
镭射作业
2 Invalue
将灯管放置在机台相应位置
3 Invalue
感应器感应后镭射
产品入周转箱
电子厂IE改善案例分享
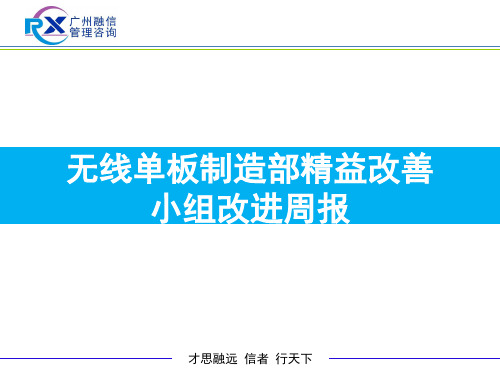
才思融远 信者 行天下
项目背景概要
课题:无线双密度模块全流程一个流 目标: 1、双密度模块综合直通率提升46%,由88%提升到93.5%; 2、双密度模块综合加工周期降低63%,由13.5天降低到5天; 3、模块产出能力由400块/天提升到600块/天,提升50%。
直通率改善目标 94% 92% 90% 88% 86% 84% 现状 目标 88% 93.50%
天 15 10 5 0
加工周期改善目标
13.5
5
现状
目标
才思融远 信者 行天下
无线双密度价值流程图(现状)
Question(问题点) 1、单板用原材料的物流现状:自动物流中心-生产中心二级库-电装生产现场 2、模块/整机用原材料的物流现状:自动物流中心-生产中心二级库-生产现场 3、单板发料周期长 4、发料及备料环节等待时间长 5、SMT工序不能分开备料,双面加工机时长焊接不能跟线一个流运作 6、插件与SMT工序CT相差大,中间存在堆板,不能做到一个流 7、装配工位贴条码,中间转运距离长,且批量作业等待时间长 8、单板FT环节无标准作业,堆板严重,在制量大
才思融远 信者 行天下
内容提要
改善目标 本周完成的主要改善工作 改善前后对比 存在的主要问题 下一步工作思路及计划
才思融远 信者 行天下
本周完成的主要改善工作
• •
1、GM52DPAU产能提升; 2、 DTRU操作质量问题改善;
•
• •
3、 CDMA2000送检周期缩短;
4、软件加工车间加工周期改善; 5、无线ICT TS设备产出率提升项目;
改 善 后(After)
问题点.着眼点(problem) :补焊第一工位需去除辅助边及 锉平毛刺
IE七大手法改善案例

五. 防錯法 案例3:SMT空焊降低改善1/3
改善前 1.1 新機種Raptor量產初期,SMT BSide目檢工站發現SD Conn空焊(浮高)與掉件不良,達0.78%,占總不良比重:22%, 居不良首位.
五. 防錯法 案例3:SMT空焊降低改善2/3
改善后 在BSide Reflow前增加一個夾具(如圖),能彈性的支撑SD
改善前
改善后
設計制作測試自動拔插治具,減少誤操作,減少劃傷
五. 防錯法 案例2:SMT上料防混料改善1/3
上料防混料---防錯料台車支架的使用
改善前
改善後
HITACHI台車
軌道 號條
碼
自製防錯料 台車支架
物料
料帶易重疊交叉,且不易發現 掃描軌道號太遠,不易判斷對應軌道
以上缺陷使上料員不能及時發現
上料
2
2
5 爐前目檢
1
1
6
AOI
1
1
7 爐后比對
1
1
8 爐后目檢
2
1
合計
10人 8人
精簡 1
1 2
B side
改善前 改善后
NO 工站
人數
1
線長
1
1
2 全技員
1
0
3
印刷
1
1
4
上料
2
2
5 爐前目檢 1
1
6
AOI
1
1
7 爐后比對 1
1
8 爐后目檢 3
1
合計
11人 9人
精簡 1
2 2
五. 防錯法 案例1:L10測試治具改善1/1
Conn,防止焊點重熔時受重力等影響產生不良.
生产现场IE改善实例

∮6长4700mm 从表层挖掘影响该车型的质量问题。
方向机、驾驶室后平台支架、七芯线缆原在内饰分装调整到了试制分装
另需加一个三通 底盘管路偶尔有短的
现场问题
空调线与驾驶室线为母母配合,改 空调安装共改两个接头
现场问题
驾驶室方面: 气喇叭管子盘在上面没有顺下来 膨胀水箱软管长(有的长1米多)
深入现场找出长期影响装配作业的实际问题并加以解决,以降低职工劳动强度、减少无效作业。
∮12长1100mm 班组长的权威、团队的协作问题。
25日对生产过程进行了粗放性的测时,当第12台驾驶室装配时生产节拍又恢复到了100余分钟。
∮8长2300mm 方向机、驾驶室后平台支架、七芯线缆原在内饰分装调整到了试制分装
15
落驾驶室
5
装方向机 7
12
安装后踏板 10
加注液压油 起驾驶室
5
连接油门线 5
等待
连接电线
连接变速箱 线
封驾驶室盘
11
20
15
5
连接制动总阀 连接手制动 安装挂车
管路
管路
阀管路
10
20
5
等待
连接方向机 转向油管
固定管路
10
30
10
连接上水 管(跨工
位)
15 装隔热板 (跨工位)
10
装保险杠 灯(跨工
公司要求本批广州订单23日上线、25日下线完成,生 产任务量远超当前实际产能。
以上海参展车辆为标准,全面提升码头车外观质量与装 调质量,进一步提升特种车公司码头车在港口市场的竞争 力与影响力。
改善过程与效果
本批订单自22日开始上线,由于车架总成改进后考虑不周,造成过板接头无法 装配,影响4小时,故22日基本未生产。
IE生产效率改善与流程优化案例
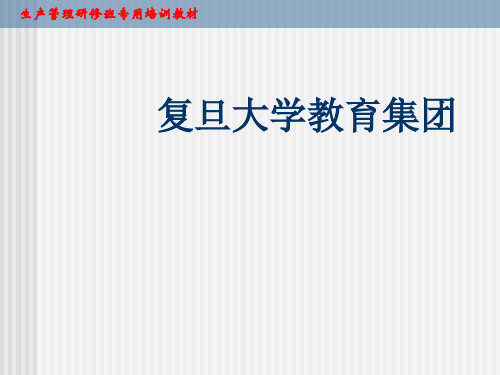
生产管理研修班专用培训教材
生产管理研修班专用培训教材
6大防错案例分析
生产管理研修班专用培训教材
案例应用:
1.鸡蛋之隔层装运盒减少搬运途中的损伤.(缓和原理)
2.设立多层之检查方法,考试后检查一次看看,有没有犯错的地方.(保险原理)
3.自动消防洒水系统,火灾发生了开始自动洒水灭火.(警告原理)
4.汽车之安全带,骑机车戴安全帽.(保险原理)
程式时间
6
2
F5 开机
7
2 .9 7
取出M /B
8
4 .9 7
拆治具(C P U )
9
4 .2 2
目檢,SFIS
10
2 .5 5
盖测试章
11
1.3 7
放M /B 于输送帶
C ycle tim e(秒) (A ) 15 1.76
O P 时间(秒)
(B )
3 6 .9 2
人机比例
C = A /B
4 .11
假效率
真效率
生产管理研修班专用培训教材
线平衡改善的方法
分担转移
作业改善
增加人员
拆解去除
重新分配
改善合并
生产管理研修班专用培训教材
实战训练:电器生产线人员排班
民生电器厂A2生产线有10个工位,主管依据生产流程和IE给定的标准工时,在结合作业员 的实际状态后制定的工序排拉表如下:
工位 下机 加工 安装 配置 组装 目检 调试 检查 组合 包装
2、作业员责任很小,已够努力 如厕/休息仅各占5%左右 已是世界性宽放水准范围内
3、停工待料占11%,为何?
生产管理研修班专用培训教材
IE十大手法之七 — 搬运法
最新IE改善案例之一如何解决生产线堆积
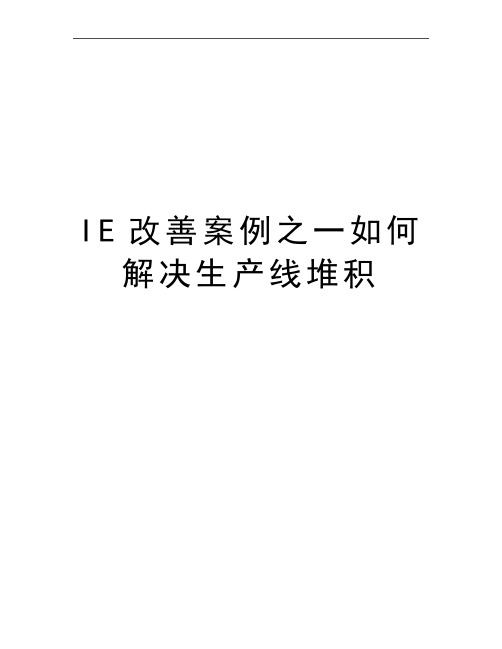
关键词:
回想自己从事IE工作也已经好几年了,无论是基础IE还是精益生产方面都做过一些成功的案例,上次因为电脑硬盘损坏,原来的资料都丢失了,现在把这两年做的知识,二是做为资料保存下来,三是如果有同行的朋友还可以相互切磋一下。下面这个是为了解决车间经常提出的生产线堆积的问题,此次改善由于是副总亲自抓的,我便也亲自对现场进行了分析,此次分析主要运用到Line Balance ,Time study ,柏拉图分析及目视管理的方法,在给车间具体培训时有另外一份详细的报告,现先把在全厂通报的报告列出来。
回想自己从事ie工作也已经好几年了无论是基础ie还是精益生产方面都做过一些成功的案例上次因为电脑硬盘损坏原来的资料都丢失了现在把这两年做的一些案例传到博客上一是梳理一下自己在这方面的知识二是做为资料保存下来三是如果有同行的朋友还可以相互切磋一下
IE改善案例之一如何解决生产线堆积
IE改善案例之一 如何解决生产线堆积
- 1、下载文档前请自行甄别文档内容的完整性,平台不提供额外的编辑、内容补充、找答案等附加服务。
- 2、"仅部分预览"的文档,不可在线预览部分如存在完整性等问题,可反馈申请退款(可完整预览的文档不适用该条件!)。
- 3、如文档侵犯您的权益,请联系客服反馈,我们会尽快为您处理(人工客服工作时间:9:00-18:30)。
a
16
试制车间七工位问题与作业改善
现场问题
空调线与驾驶室线为母母配合,改
空调安装a 共改两个接头
17
试制车间七工位问题与作业改善
现场问题
驾驶室方面: 气喇叭管子盘在上面没有顺下来 膨胀水箱软管长(有的长1米多)
线路走的靠后,须剪开重走 方向机、驾驶室后平台支架、七芯线缆原在内饰分
试制车间七工位问题与改善
制造部 2011·10·28
a
1
试制车间七工位问题与作业改善
目录
1. 现场改善背景 2. 现场改善过程与效果 3. 头脑风暴会 4. 现场反馈的问题
a
2
试制车间七工位问题与作业改善
项目背景
试制车间七工位隶属于三工段,主要从事安装举升系统、 落装驾驶室、安装方向机及管路、连接各类管线路、连接上下 水管等作业,现有员工七名:孟光雷(班组长)、李健、井绪 行、黄世堂、马全静(女)、李越、张旺。该工位是码头车装 配的历史瓶颈,生产节拍达100分钟以上,正常班次日产不过 五辆份。
装调整到了试制分装
发动机方面: 发动机分装时方向机油管角度不一,须调整
a
18
试制车间七工位问题与作业改善
现场问题
驾驶室有15个无法正常落下
a
19
试制车间七工位问题与作业改善
现场问题
车架总成少螺母
a
20
试制车间七工位问题与作业改善
现场问题
车架总成焊接螺母掉落
a
21
试制车间七工位问题与作业改善
现场问题
5
15
12
分装液压油管 及驾驶室举升
拉带
安装举升油 缸及管路
5
15
开行车吊驾驶 室
落驾驶室
装方向机
安装后踏板
加注液压油 起驾驶室
连接油门线
6
5
7
10
5
5
等待
连接电线
连接变速箱 线
封驾驶室盘
11
20
15
5
连接制动总阀 连接手制动 安装挂车
管路
管路
阀管路
10
20
5
等待
连接方向机 转向油管
固定管路
10
30
原因分析: • 由于员工的作业内容与标准的模糊或缺失,造成员工在生
产过程中随意性强,当现场有领导监督时或积极性高时则 快,反之则慢。 • 班组长的权威、团队的协作问题。 • 产品质量问题。 • 设计时个别点未能考虑装配舒适性。 • 装配方式的不足。
a
6
试制车间七工位问题与作业改善
改善过程与效果
测时表
a
11
试制车间七工位问题与作业改善
头脑风暴会
a
12
试制车间七工位问题与作业改善
现场问题
穿线困难、护套易扯掉
a
13
试制车间七工位问题与作业改善
现场问题
卡套螺母改快插
a
14
试制车间七工位问题与作业改善
现场问题
卡套螺母改快插
a
15
试制车间七工位问题与作业改善
现场问题
一辆份线束仅在七工 位多余的管子: ∮12长1100mm ∮8长2300mm ∮6长4700mm 另需加一个三通
公司要求本批广州订单23日上线、25日下线完成,生产任 务量远超当前实际产能。
以上海参展车辆为标准,全面提升码头车外观质量与装调 质量,进一步提升特种车公司码头车在港口市场的竞争力与影 响力。
深入现场找出长期影响装配作业的实际问题并加以解决, 以降低职工劳动强度、减少无效作业。
从表层挖掘影响该车型的质量问题。
井绪行
分装水管 连接下水管
5
15
等待 13
连接上水管 15
黄世堂
孟光雷 李健 李越
张旺
马全静
分装液压油管及 安装举升油缸 驾驶室举升拉带 及管路
5
15
开行车吊驾驶室 落驾驶室
装方向机
安装后踏板及 加注液压油起
支架
驾驶室
6
5
7
10
5
等待 30
连接油门 线
装隔热板
5
5
分装制动总阀及 挂车阀
12
等待 21
10
a
连接上水 管(跨工
位) 15 装隔热板 (跨工位) 10
装保险杠 灯(跨工
位) 5
8
试制车间七工位问题与作业改善
改善过程与效果
改善后山积图
a
9
试制车间七工位问题与作业改善
改善过程与效果
a
10
试制车间七工位问题与作业改善
改善过程与效果
效果评价: • 工序调整后未经系统培训,员工熟练程度不一。 • 现场缺件影响测评。 • 六工位慢,导致等待。 • 产品质量问题。
25日对生产过程进行了粗放性的测时,当第12台驾驶室 装配时生产节拍又恢复到了100余分钟。
a
4
试制车间七工位问题与作业改善
改善过程与效果
第12台车生产测时现状图
a
5
试制车间七工位问题与作业改善
改善过程与效果
在现场针对员工协作与等待问题,与邵主任协商,提出了50 分钟完成装配的目标,在第15辆车上进行验证,达成目标 则按50元/人进行奖励,结果36分钟。
等待 63
连接手制动管 连接制动总阀 安装挂车
路
管路
阀管路
20
10
5ห้องสมุดไป่ตู้
连接方向 机转向油 固定管路
管
30
10
等待
连接电线 连接变速箱线 封驾驶室盘 装保险杠灯
11
20
15 a
5
7
试制车间七工位问题与作业改善
改善过程与效果
改善后
井绪行
黄世堂 孟光雷
李健 马全静
李越 张旺
分装水管 连接下水管
分装制动总阀及挂车阀
时以上 空调安装与工位上有时冲突(车间内部解决)
手剪子磨损快 一个工具未修好,临时借用
晚上灯光不好 工资低
80元中餐补助未兑现
a
25
举升缸故障高(本批换3个)、轴座孔可
空穿销子、但装a举升缸时个别困难
22
试制车间七工位问题与作业改善
现场问题
驾驶室拉带与车架碰、个别轴座尺寸大
a
23
试制车间七工位问题与作业改善
现场问题
踏板未经试装便批量使用,再更换
(20+a 13)件
24
试制车间七工位问题与作业改善
现场问题
其它方面: 当工位上出现不良品时,再要件时间长,有的1小
a
3
试制车间七工位问题与作业改善
改善过程与效果
本批订单自22日开始上线,由于车架总成改进后考虑不 周,造成过板接头无法装配,影响4小时,故22日基本未生 产。
23日开始的装配过程中,七工位生产节拍基本维持在 100分钟左右。
自24日开始,公司总经理带领各部门亲自到现场实施改 善,对原有的工序进行了初步调整。在装配第五辆车时已达 到了50分钟左右。