现场改善及案例分析
现场IE改善案例分析--生产线平衡分析改善案例
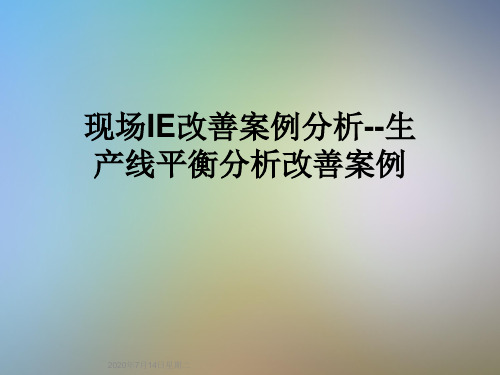
生产线平衡定义
对生产的全部工序进行均衡,调整作业 负荷和工作方式,消除工序不平衡和工 时浪费,实现“一个流”。
出料
入料
平衡生产线的意义
通过平衡生产线可以综合应用到程序分析、动作分析 、layout分析,搬动分析、时间分析等全部IE手法,提 高全员综合素质
在平衡的生产线基础上实现单元生产,提高生产应变 能力,对应市场变化实现柔性生产系统
(4) 4种增值的工作
站在客户的立场上,有四种增值的工作
1、使物料变形 2、组装 3、改变性能 4、部分包装
物料从进厂到出厂,只有不到 10% 的时间是增值的!
工序
符 号
内容
作业内容
分类
加工 作业
○
加工 作业
■产生附加价值的工序及作 业
卖得掉
检查
□
数量检查 ■虽然有必要,但需要进行 品质检查 改善的工序及作业
现场IE改善案例分析--生 产线平衡分析改善案例
2020年7月14日星期二
内容安排
一、线平衡定义 二、生产线平衡分析方法 三、B值、F值的定义与计算 四、线平衡案例分析
一、线平衡定义
生产线平衡定义
什么是生产线平衡
生产线平衡是指构成生产线各道工序所需的 时间处于平衡状态,作业人员的作业时间尽 可能的保持一致,从而消除各道工序间的时 间浪费,进而取得生产线平衡。
减少人手(1)
將工序3里的工作时 间分配至工序2﹑4 及5之內﹐从而工序 3里的人手可调配其 它生产线去
可行性﹕須工序 2﹐4及5內均有足夠 时间接受额外工作。
ቤተ መጻሕፍቲ ባይዱ
生产线平衡-例3﹕减少人手(2人)
降低线体速度,减少生产产量
工作時間
现场管理培训系列之现场改善篇
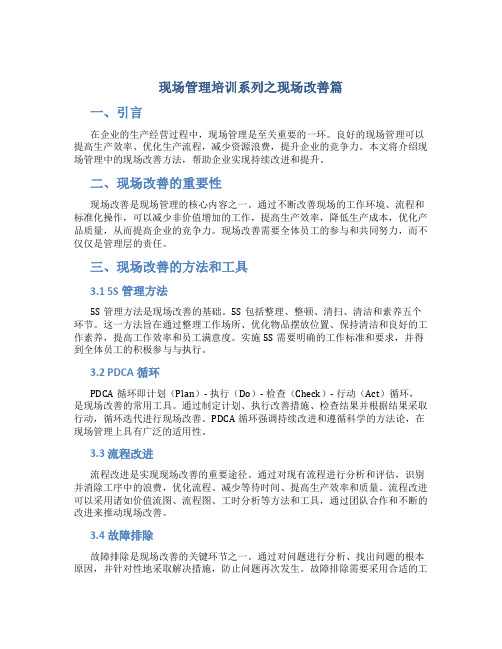
现场管理培训系列之现场改善篇一、引言在企业的生产经营过程中,现场管理是至关重要的一环。
良好的现场管理可以提高生产效率、优化生产流程,减少资源浪费,提升企业的竞争力。
本文将介绍现场管理中的现场改善方法,帮助企业实现持续改进和提升。
二、现场改善的重要性现场改善是现场管理的核心内容之一。
通过不断改善现场的工作环境、流程和标准化操作,可以减少非价值增加的工作,提高生产效率,降低生产成本,优化产品质量,从而提高企业的竞争力。
现场改善需要全体员工的参与和共同努力,而不仅仅是管理层的责任。
三、现场改善的方法和工具3.1 5S管理方法5S管理方法是现场改善的基础。
5S包括整理、整顿、清扫、清洁和素养五个环节。
这一方法旨在通过整理工作场所、优化物品摆放位置、保持清洁和良好的工作素养,提高工作效率和员工满意度。
实施5S需要明确的工作标准和要求,并得到全体员工的积极参与与执行。
3.2 PDCA循环PDCA循环即计划(Plan)- 执行(Do)- 检查(Check)- 行动(Act)循环,是现场改善的常用工具。
通过制定计划、执行改善措施、检查结果并根据结果采取行动,循环迭代进行现场改善。
PDCA循环强调持续改进和遵循科学的方法论,在现场管理上具有广泛的适用性。
3.3 流程改进流程改进是实现现场改善的重要途径。
通过对现有流程进行分析和评估,识别并消除工序中的浪费,优化流程、减少等待时间、提高生产效率和质量。
流程改进可以采用诸如价值流图、流程图、工时分析等方法和工具,通过团队合作和不断的改进来推动现场改善。
3.4 故障排除故障排除是现场改善的关键环节之一。
通过对问题进行分析、找出问题的根本原因,并针对性地采取解决措施,防止问题再次发生。
故障排除需要采用合适的工具和方法,如5W1H(What、When、Where、Who、Why、How)分析、鱼骨图(Ishikawa Diagram)等,帮助确定问题的全貌并解决问题。
四、现场改善的关键要素实施现场改善需要关注以下关键要素:4.1 领导力和员工参与现场改善需要企业领导的关键决策和支持,并鼓励员工积极参与。
生产现场管理与改善

生产现场管理的重要性
未来发展趋势
生产现场管理将更加智能化
智能化
技术成为推动力量
信息化
不断学习新技术、新模式
学习与适应
维持竞争力,可持续发展
竞争力
创新
企业需要不断优化、创新
高效运作
引入新技术、培养人才持续改进生产流程
市场竞争优势
实现高效、高质量的生产运作赢得市场竞争优势
展望未来
基石
生产现场管理与改善是企业发展的基石
什么是生产现场管理与改善?
生产现场管理的重要性
直接影响企业的竞争力和盈利能力
影响企业竞争力
有效管理提高生产效率、减少浪费
提高生产效率
生产管理能改善产品质量
改善产品质量
为企业创造更大的价值
创造更大价值
生产现场管理的挑战
需要面对复杂多变的生产环境
复杂生产环境
需要有效管理人员
人员管理问题
需要维护设备保证生产正常进行
减少设备停机时间
精益生产
消除浪费
01
03
优化生产流程
02
提高价值流动
生产进度
帮助企业实现生产过程的可视化管理
库存情况
帮助企业实现生产过程的可视化管理
提高生产计划的准确性
有效减少库存积压降低生产过程中的拥挤
Kanban制度
管理生产计划
帮助企业实现生产过程的可视化管理
总结
生产现场管理方法是企业提高效率、降低成本、优化流程的重要手段。通过5S管理法、TPM全员生产维护、精益生产和Kanban制度等方法,企业可以实现生产现场的精细化管理,从而提高竞争力。
工业物联网、大数据分析和人工智能对比
工业物联网
精益生产现场改善培训案例

精益生产现场改善培训案例近年来,精益生产成为了企业提高效率和降低成本的重要手段。
为了帮助员工更好地理解和应用精益生产的原则和工具,某公司决定开展精益生产现场改善培训。
以下是培训中的一些案例,展示了精益生产在实际生产现场中的应用。
1. 5S整理工作站在一家制造公司的生产线上,工作人员经常因为工具和物料摆放混乱而浪费时间。
通过培训,员工学习了5S整理原则,并开始整理工作站。
他们将工具、物料和文件按照使用频率和使用顺序进行了布置,使得操作更加流畅和高效。
2. 平衡生产线在一家汽车装配厂,生产线上的工作站之间存在明显的瓶颈,导致生产效率低下。
通过培训,员工学习了平衡生产线的方法,重新安排了工作站的任务分配,使得生产线上的工作负载更加均衡,提高了整体生产效率。
3. 精益布局设计一家仓库经常出现货物堆积、拣选错误等问题,影响了物流运转的效率。
通过培训,仓库管理人员学习了精益布局设计的原则,并重新规划了货物存放和拣选区域。
优化后的布局使得货物的流动更加顺畅,减少了物料处理时间和错误率。
4. 消除浪费在一家食品加工厂,员工经常因为物料不足、工具失效等原因停止工作,造成了生产线的停滞和浪费。
通过培训,员工学习了消除浪费的方法,如及时补充物料、定期检修和维护工具等。
这些措施使得生产线的运转更加稳定,减少了停机时间和浪费。
5. 持续改进一家电子产品制造公司发现产品的良品率低,经常出现质量问题。
通过培训,员工学习了持续改进的方法,如设立质量检查点、建立问题解决小组等。
员工积极参与改进活动,通过不断的问题分析和改进措施,最终提高了产品的质量和良品率。
6. 价值流映射在一家纺织厂,生产线上的流程繁杂,导致生产周期长和库存积压。
通过培训,员工学习了价值流映射的方法,绘制了整个生产过程的价值流图,并找出了各个环节中的浪费和瓶颈。
根据分析结果,他们采取了相应的改进措施,缩短了生产周期和库存周转时间。
7. 一次性设备准备在一家医药公司的生产车间,设备准备时间过长,影响了生产效率。
如何指导生产现场做提案改善

8、现场问题点举例
✓ 有没有浪费的部分存在? ✓ 去取材料时,是否出现浪费的情况? ✓ 形状是否有浪费发生? ✓ 在装卸、移动时是否出现浪费? ✓ 在搬运途中,是否有将物品弄破、弄坏的浪费? ✓ 有没有随意浪费地保管物品? ✓ 是否有浪费不需用的电灯? ✓ 寻找所放置的物品是否是很浪费时间? ✓ 对于不合理的公务出差,是否精算度还不够严格?
✓ 设备
设备是否安全 设备故障是否重复出现、设备是否存在故障隐患 操作是否方便等
✓ 材料(原材料、采购部件等)
材料取用是否方便 材料使用是否存在浪费 材料的使用是否可以替换 ✓ 方法 流程之变更 作业方法之变更 工具、夹具不当
如何指导生产现场做提案改善
✓
环境
电源稳定度、水质稳定度、温度、湿度
空气粉尘、照明度
如何指导生产现场做提案改善
作业操作; 过程搬运; 产品检验; 等待分析;
5、改善的基本原则
✓ 尽可能取消不必要的工序; ✓ 合并工序,减少搬运; ✓ 安排最佳的顺序; ✓ 使各工序尽可以能经济化; ✓ 找出最经济的移动方法; ✓ 尽可能地减少在制品的贮存。
如何指导生产现场做提案改善
6、改善提案全过程六大步骤
✓ Who 由谁做的? 为什么要此人做?有无其它更合适的人?
✓ Why 为什么? 为什么要这样做?有无其它更合适的方法?
✓ How 如何做? 如何做,需要花费多少,能带来什么好处?
如何指导生产现场做提案改善
4、使用“ECRS”原则做改善方案
✓ Eliminate 取消 在经过了“完成什么?”“是否必要”及“为什么?”等 问题的提问后,对于发现的不必要的答案即可以取消,即 取消不必要的工序,操作、动作,取消是改善的最高原则。
现场改善的思路

实施效果:改 善后餐厅客流 量增加员工工 作效率提高顾 客满意度提升。
总结与启示:该 案例展示了现场 改善在餐饮业中 的实际应用为其 他企业提供了借
鉴和启示。
PRT FIVE
数字化技术能够提高生产效率 减少浪费
数字化技术可以实现实时监控 和数据分析为决策提供支持
数字化技术可以优化生产流程 提高产品质量
分析问题:对收 集的数据进行分 析找出存在的问 题和瓶颈确定改 善的重点。
制定改善方案: 根据分析结果制 定具体的改善方 案包括改善的具 体措施、时间安 排和预期效果等。
分析现状:收集数据了解现 状问题分析原因
确定改善目标:明确改善的 目的和期望结果
制定改善计划:提出解决方 案制定实施计划
实施改善:按照计划执行改 善措施确保实施效果
定期评估:对现场改善的效果进行定期评估确保改进措施的有效性。 数据分析:收集相关数据对改善前后的效果进行对比分析了解改进的幅度和潜在问题。 反馈机制:建立有效的反馈机制收集员工意见和建议持续优化改善方案。 持续改进:根据评估结果和反馈意见持续调整和改进现场管理提高生产效率和产品质量。
PRT FOUR
,
汇报人:
CONTENTS
现场改善的概 述
现场改善的思 路
现场改善的实 施步骤
现场改善的案 例分析
现场改善的未 来发展
PRT ONE
现场改善是指在生产现场中通过一系列的方法和手段对生产过程进行优化和改进以提高生产 效率、降低成本、改善质量的过程。
现场改善的目标是实现生产过程的持续改进和优化提高企业的竞争力和盈利能力。
收集数据:对现场 的运作情况进行全 面的数据收集
分析问题:对收集 到的数据进行分析 找出存在的问题和 瓶颈
现场改善

SIPOC分析
--- 供应商 (Suppliers) --- 输 --- 流 --- 输 --- 客 入 程 出 户 (Inputs) (Process) (Outputs) (Customers)
26
3、问题分析与解决
Step1: 主题选定 Step8:残余与潜 在问题 Step7:标准化 与认知 Step2:现状分析
团队 合作
Step3:目标设定
Step6:效果确认 与防止再发
Step5:对策拟定 与实施
Step4:真因分析 与验证
27
3、问题分析与解决
1.目标设定依据
过去资料 -------过去
2.目标的特性
S:Specific-----------特定的
现况数据 -------现在
组织要求 -------未来 客户需求 -------客户 标杆资料 -------其它
三、现场改善的流程和逻辑
1、问题解决的方法
2、问题解决的逻辑 3、问题解决的流程
15
1、问题解决的方法
问题解决的方法
逻辑
工具
Ford 8D
6 Sigma DMAIC
改善 8步法
基本
进阶
高阶
问题 解决型
课题 达成型
2、问题解决的方法-- 逻辑
解决问题的四个基本分析逻辑
PDCA SDCA循环
A C
3、七大浪费
库存 等待 动作
過度加工
4、主要的改善观念
• • • • • 过程导向(8个step) 遵循PDCA循环/SDCA循环 品质保证 改 改善的SDCA与PDCA历程 善 用数据说话 A P 下一流程就是客户 C D
A P C D A S C D
现场改善工具与案例

5、库存掩盖了问题
通过库存维持生产
降低库存暴露问题
缺勤 率高
计划 性差
质量 低劣
机器 故障
销售 问题
生产不均衡
换模 时间长
沟通 不佳
缺勤
质量
率高
低劣
计划
性差
机器 故障
销售 问题
生产不均衡
库存之海
换模 时间长
沟通 不佳
12
6、操作动作不合理
场地布置欠佳 料箱设计不合理 工艺设计不合理 人员安排不当 工具取用不方便
现场改善工具及案例
一 、现场改善基础
1
做好现场改善的四个要素
Comprehension
理解
Competence
能力
承诺
Commitment
持续
Continuance
2
什么是现场
当问题发生时,先去现场 检查现物 找到真正的原因并排除 标准化以防止再发生
现场就是产生 附加值或提供 服务的地方。
24
2S整顿
整顿:定物、定位、定量
• 更快地拿到和返还物品 • 物品放得很整齐,易清点 • 物品的库存更低,但不会短缺 • 空间布局是合理的 • 工作环境是安全的 • 不良品和良品是严格区分的
25
3S清扫
清扫:清扫就是点检
• 工作环境是明亮的 • 设备上无积灰和油污 • 地面、墙上没有灰尘、积水、油污 • 空气中没有浮尘、异味 • 工作台、办公桌、货架是干净的 • 物品是干净和很好保护的
29
克服消极因素的方法
易学、易懂、 易操作
进行团队活动
领导以 身作则
采取预防措 施,解决根 本问题
重视现场检 查,有错必 纠
生产车间现场改善案例

生产车间现场改善案例一、背景介绍公司是一家制造业企业,主要生产汽车零部件。
生产车间是公司的核心部门之一,但长期以来存在着效率低下、质量不稳定等问题,给企业带来了严重的经济损失和声誉损害。
为了解决这些问题,公司决定对生产车间进行现场改善。
二、问题分析1. 低效率:生产车间的工作流程不够清晰,物料运输和设备调整时间过长,导致工作效率低下。
2. 不稳定的质量:产品质量不稳定,出现了许多次品和废品,给企业带来了严重的经济损失和声誉损害。
3. 安全隐患:由于设备老化和操作人员不规范等原因,生产车间存在安全隐患。
三、现场改善方案1. 优化工作流程:通过对工作流程进行优化,减少物料运输和设备调整时间。
采用“单元生产”模式,在同一区域内设置多个工作单元,并将每个单元之间的距离缩短到最小。
同时,在每个单元内设置标准化作业指导书,并对操作流程进行标准化。
2. 提高质量稳定性:通过引入“6S”管理模式,对生产车间进行整理、整顿、清洁、清理、安全和素养的全面管理。
同时,建立完善的质量控制体系,对每个生产环节进行严格的质量把关,并及时发现和解决问题。
3. 加强安全管理:对老化设备进行更新和维护,并加强操作人员的培训和考核。
同时,建立安全隐患排查机制,定期开展安全检查,并及时处理发现的问题。
四、实施效果通过以上改善方案的实施,生产车间的效率得到了显著提升。
工作流程优化后,物料运输时间缩短了50%,设备调整时间减少了30%。
同时,质量稳定性也得到了明显提高,次品率下降了70%以上。
安全管理方面也取得了很好的效果,事故率下降了50%以上。
五、总结通过现场改善方案的实施,生产车间的工作效率、产品质量和安全管理都得到了显著提升。
企业在此基础上进一步推行精益生产等管理模式,在不断提高效率和质量的同时,也为企业的可持续发展奠定了坚实的基础。
如何指导生产现场做提案改善
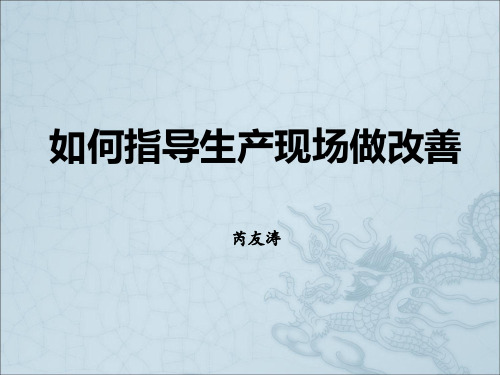
现 状
标 准
目 标
3、什么是提案改善?
在日本又称“提案”或“改善提案”。是指为 了提高产品品质、降低成本、发挥员工的智慧潜 力,发扬主任翁精神,通过征集所有员工的想法 ,对公司的经营作出改善。
改善≠修理
没有最好,只有更好!
4、改善提案活动的目的
作为个人: 为解决问题悉心钻研、提出方案、实施改善、实现目标、得到 奖励、自我成长。 作为公司 1、开发员工个人能力 开拓个人发现问题的意识,改善并提高提案者的能力。 2、创造良好劳动的工作场所 不断发现问题点、通过改善、使劳动场所趋于完美。 3、提高工作场所的活力 提案活动加强上下沟通(上司与下属,提案者之间) 4、使问题表面化 使工作现场的问题能够及时暴露在表面,是问题解决的起点。 5、创造出成果 引导员工从细微处着眼消除各种浪费、损耗、降低成本,提高效率。
不需要的工序或操作; 改变工作顺序; 改变设备或利用新设备; 改变工厂布置或重新编排设备; 改变操作或贮存的位置; 改变订购材料的规格; 作业操作; 过程搬运; 产品检验; 等待分析;
5、改善的基本原则
尽可能取消不必要的工序; 合并工序,减少搬运; 安排最佳的顺序; 使各工序尽可以能经济化; 找出最经济的移动方法; 尽可能地减少在制品的贮存。
—— 【 戴明博士】
公司全员经常要有问题意识,有想打破现状,改 善意识最为重要,只要认为没有问题的职场,进 步就会停止,而开始退步,每天不进步就是退步, 没有问题就是最大问题。
——【石川馨博士】
1、改善就是发现现存问题并采取措施解决问题,通过 “改进→维持→继续改进”,把事情作得越来越好!
2、丰田生产给改善的定义: 一种企业经营理念,用于持续不断的改进工作方法以 及人员的效率等。
精选现场IE改善案例分析

扑克牌游戏规则
1、每个分厂安排4个人(厂长、工艺、作业长、班长) 2、小组内部自己安排4个人的工作 3、要求是将52张扑克牌按同一花色、从大到小的排成一排 4、时间最少的小组获胜 5、开始和结束计时以固定的人员手敲桌子为准 6、游戏开始由工作人员将牌洗好
评分标准
1.2.3.4名分别100.80.60.40分错 一张牌,扣10分
电装7人线标准工时
请 计 算 平 衡 率
6、生产线平衡分析的方法
1、确定对象与范围 2、用作业分析把握现状 3、测定各工程的净时间 4、制作速度图标 5、计算平衡 6、分析结果,制定改善方 案
7、改善瓶颈岗位
(1)改善的4大原则
1)减少动作次数 2)同时使用双手 3)缩短移动距离 4)使动作变得轻松
4、工时测定分析(蓝色为作业的时间红色为失去平
衡的时间)
5、生产线平衡的计算
生产平衡率(%)=各工程净时间总计/(时间最长工程*人 员数)*100%
如上图表中,生产线平衡率=1505/(90*19)*100%=88% 不平衡率%=100%-平衡率(%) 对生产线来说,不平衡率越小越好,一般控制5%-13%之间,
(2)IE动作改善的4原则:
• ECRS原则 1.Eliminate —取消 2、Combine —合并 3、Rearrange —重排 4、Simplify —简化
(3)ECRS法运用图示简介
生产线平衡—例1:缩短生产节拍
提升生产速度,维持人手不变
缩短生产节拍 将工序2里一部 分可抽离的时间 转至3工序里, 以缩短整体的生 产节拍
至少要控制在15%以下
• 请大家观看电子分厂电装3人柔性线视频
1、一边看一边测试,最后计算平衡率 2、计算一下线小时理论产量 3、提出提升线平衡的思路方法
生产现场改善案例分析
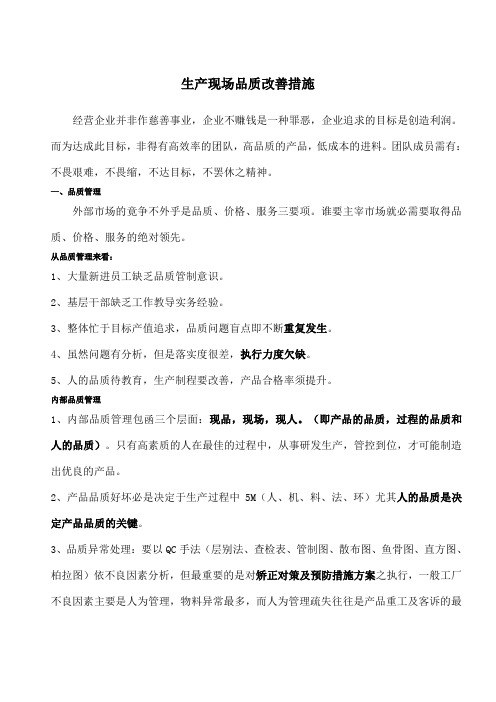
生产现场品质改善措施经营企业并非作慈善事业,企业不赚钱是一种罪恶,企业追求的目标是创造利润。
而为达成此目标,非得有高效率的团队,高品质的产品,低成本的进料。
团队成员需有:不畏艰难,不畏缩,不达目标,不罢休之精神。
—、品质管理外部市场的竟争不外乎是品质、价格、服务三要项。
谁要主宰市场就必需要取得品质、价格、服务的绝对领先。
从品质管理来看:1、大量新进员工缺乏品质管制意识。
2、基层干部缺乏工作教导实务经验。
3、整体忙于目标产值追求,品质问题盲点即不断重复发生。
4、虽然问题有分析,但是落实度很差,执行力度欠缺。
5、人的品质待教育,生产制程要改善,产品合格率须提升。
内部品质管理1、内部品质管理包函三个层面:现品,现场,现人。
(即产品的品质,过程的品质和人的品质)。
只有高素质的人在最佳的过程中,从事研发生产,管控到位,才可能制造出优良的产品。
2、产品品质好坏必是决定于生产过程中5M(人、机、料、法、环)尤其人的品质是决定产品品质的关键。
3、品质异常处理:要以QC手法(层别法、查检表、管制图、散布图、鱼骨图、直方图、柏拉图)依不良因素分析,但最重要的是对矫正对策及预防措施方案之执行,一般工厂不良因素主要是人为管理,物料异常最多,而人为管理疏失往往是产品重工及客诉的最大要因。
4.、对策:以教育训练提升人的品质,并落实改善品质措施。
A:短期(立即执行)用QC手法对问题进行探讨,认真实施对策,依循PDCA时时从不同角度考量如何改善。
B:中期(有效训练措施)实施班QCC活动(每周两小时)针对每个岗位一周以来报表反应出来的品质状况(当然最起码报表必须是真实的)让作业员对品质管理提出看法与问题,使其有参与感,进而加重其责任心,品管圈活动中可运用QC手法,品质改善提案,QCC竟赛等各类管理训练措施。
C:长期(积极教育训练)1、不定期或按计划全面实施职前,在职,重点,机会品质教育。
2、公司举办年度品管圈竟赛,品质征文,征图,品质标语,并品质演讲等意识教育,用来凝聚形成公司全体品质意识,从而提升全员无形中的品质观念。
农村环境整治项目案例分析
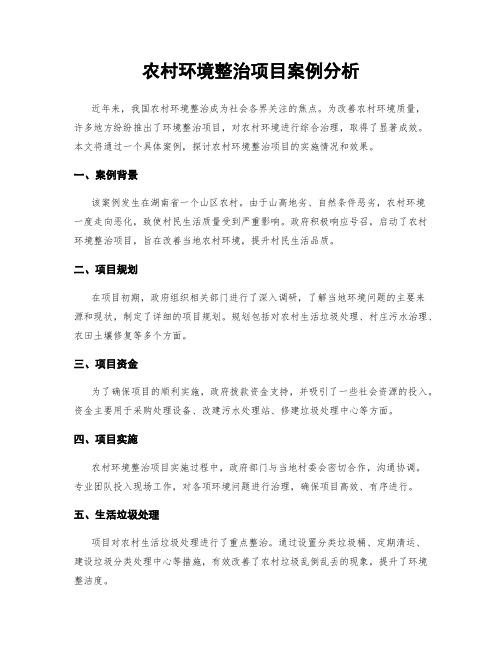
农村环境整治项目案例分析近年来,我国农村环境整治成为社会各界关注的焦点。
为改善农村环境质量,许多地方纷纷推出了环境整治项目,对农村环境进行综合治理,取得了显著成效。
本文将通过一个具体案例,探讨农村环境整治项目的实施情况和效果。
一、案例背景该案例发生在湖南省一个山区农村。
由于山高地劣、自然条件恶劣,农村环境一度走向恶化,致使村民生活质量受到严重影响。
政府积极响应号召,启动了农村环境整治项目,旨在改善当地农村环境,提升村民生活品质。
二、项目规划在项目初期,政府组织相关部门进行了深入调研,了解当地环境问题的主要来源和现状,制定了详细的项目规划。
规划包括对农村生活垃圾处理、村庄污水治理、农田土壤修复等多个方面。
三、项目资金为了确保项目的顺利实施,政府拨款资金支持,并吸引了一些社会资源的投入。
资金主要用于采购处理设备、改建污水处理站、修建垃圾处理中心等方面。
四、项目实施农村环境整治项目实施过程中,政府部门与当地村委会密切合作,沟通协调。
专业团队投入现场工作,对各项环境问题进行治理,确保项目高效、有序进行。
五、生活垃圾处理项目对农村生活垃圾处理进行了重点整治。
通过设置分类垃圾桶、定期清运、建设垃圾分类处理中心等措施,有效改善了农村垃圾乱倒乱丢的现象,提升了环境整洁度。
六、村庄污水治理农村村庄的污水治理一直是一个难题。
项目投入了资金,对村庄周边的污水排放口进行改造,建设了污水处理站,采用生态处理技术,将污水净化后排放,有效改善了村庄周边的环境质量。
七、农田土壤修复随着农药、化肥的大量使用,农田土壤污染问题日益突出。
项目重点治理了农田土壤的污染情况,采用生物修复、植物修复等技术手段,使土壤得到了一定的恢复,为农产品的安全生产提供了有力保障。
八、宣传教育除了实施整治项目外,政府还开展了大力宣传教育活动,提高了农民的环境保护意识。
定期举办宣传活动、设立宣传栏,使村民了解环境保护的重要性,积极配合项目的实施。
九、项目效果经过一段时间的实施,该项目取得了显著成效。
制造现场改善提案(“改善”文档)共7张
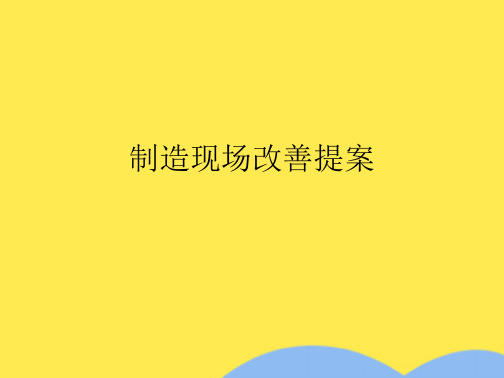
切生换产时 标间准5具化体制5统程S改计善、线内与线外区分、线责 规内任 范区 、转域 稽线的 核外划 小分 组改、 的善区 形域 成内摆放规范&使用
生产标准化制程
1.
6
错料改善
生产换料;炉前缺件手补料;贴片不良 维修换料;
改善活动规范制度&检讨改善项目 调用程序7错误程、序设异备常内无程序、程序内缺调 缺件用 件程 ,,C序C/错T/变T误更变、更设备内无程序、程序内
1.密度化 2.高速化 3.标准化 用户对电子产品多元化的需求,使少量品种的大批量生产转化为多品种、小批量的生产,
这样必然对元器件贴装制程提出更高的标准要求。
目的:
通过全员参与&制造现场改善达成: 短期:
提高生产效率; 提高品质;降低成本;
中长期: 生产标准化制程
制造现场改善提案
改善方向
人员
1.技能培训(项目&计划),
保养项目1、管全理员规参范与改、善稽核小组形成 改善活动规范制度&检讨改善项目 切换时间具体统计、线内与线外区分、线内转线外改善 调用程序2错误作、业设人备员技内能无培程训序、程序内缺人件员训,练C、/T考变核更、等级制定
提高生产3效率日;常保养制度形成
设备日常保养项目,稽核小组形成
定岗定位4(技工能治级具别的保区养分与)管理规范实制定行目视保养化项管目理、管:理规范、稽核小组形成
12 达成率不足
各机种C/T评估,达成率不足调查,分析 、对策,处理与结果比较
制造现场改善提案
快速换线(SMED)案例
不良产品的(重方复法)发生
实行全员参与改善,由被动变主动: 1.提高执行纪律的主动性;
2.具有高品质高效率的意识;
现场动作改善案例-工位作业方式优化

修改,此表要和前面的 踏台高度30MM 基本满足装配高度 数据结论对应,即总 结出来影响作业周期 3种零件6件标准件拿 取件次数较多 时间和导致劳动强度 取 大的原因。
工艺执行情况 符合工艺操作规程
4、工艺
成果改进思路和过程控制
动作经济原则:
以尽可能减少作业人员的疲劳、能发挥作业
人员的最高效率为准則来制定操作方法,再配备 有效的加工工具、机械设备和合理的工作地布置。
序 号 1 2 3 4
实施情况
现场测量次寸,设计 取材制作 协助制作 协助实施,并使用后完善
实施人
陈祥光 杨金发 邵麟 张凤麟
备注
成果改进思路和过程控制
在 该 工 位 铺 设 运 行 轨 道
多来几个角度的照片
成果改进思路和过程控制
随线装配小车的制作:利用控制开关,通过气管使其气缸工 作,将其卡在吊具上
级别
一
指节 运动枢轴 手指 人体运动部份 动力作范围 手指节之长度 1 速度 最少 体力消耗 最弱 动作力量 最小 疲劳度 时 间 0.0016分 以25mm为主
结合P5的作业手顺书, 人体动作等级划分 和下表的等级划分试 二 三 四 着分析下里面的动作 手腕 肘 肩 等级。 + 手掌 + 前臂 + 上臂
精益生产经典案例

精益生产改善案例生产管理追求无库存,就是要彻底改变以超量库存保发货的传统做法,变以造型为中心的推动式生产为以清理为起点的拉动式生产。
实行期量流或一个流生产方式,逐步扩大看板生产品种,造型生产线实行柔性生产,生产作业计划和生产统计应用计算机管理,大幅度地压缩工序、在制品和成品库存,最大限度地降低资金占用,提高生产组织管理水平。
质量管理追求无缺陷,就是要不断提高质量管理和产品质量水平。
质量管理要从“全面质量管理”转向“零缺点管理”,进一步减少不良损失,用精益思想研究和实施质量改进和攻关,提高产品的工艺水平。
落实质量责任制,严格厂内质量评审,严肃工艺纪律,使每个环节、每道工序、每名职工都切实做到精心操作,严格把关,确保产品内在质量和表面质量达到优质品标准。
设备管理追求无停台,就是要提高设备的可动率和开动率,提高工装的工艺水平和使用寿命。
要坚持以生产现场为中心,抓好现场巡检,现场维修,实行设备封闭管理。
工装采取快速换模方法,满足小批量多品种生产的需求。
要通过采用一系列有效措施,不断提高设备工装的技术状态,为保证生产顺利进行和生产优质产品提供可靠的必要条件。
成本管理追求无浪费,就是要狠抓投入产出管理,做到少投入,多产出,优质低耗,降低成本。
深入开展三级经济核算,抓好产品收到率、原材料投入、成品产出率、清理合格率等环节的考核。
要整顿库房,对原材料、产成品、备品、备件等重新制定最高最低储备限额,做到用最低的储备满足生产的需要,大幅度地降低消耗,减少浪费,活化资金,降低产品成本。
优化生产,就是全厂每个生产环节都要达到整体优化标准,建立起以车间主任为首,以生产工人为主体,以生产现场为中心的现场“三为”管理机制。
实施生产要素一体化管理,强化现场“5S”管理和定置管理,现场工位器具标准化、改善生产现场环境,提高现场文明生产水平,使生产要素达到最佳状态。
优质服务,就是要强化科室为一线,后方为前方服务。
职能科室要切实转变工作作风,提高工作质量、服务质量和工作效率,充分发挥指导服务的职能。
- 1、下载文档前请自行甄别文档内容的完整性,平台不提供额外的编辑、内容补充、找答案等附加服务。
- 2、"仅部分预览"的文档,不可在线预览部分如存在完整性等问题,可反馈申请退款(可完整预览的文档不适用该条件!)。
- 3、如文档侵犯您的权益,请联系客服反馈,我们会尽快为您处理(人工客服工作时间:9:00-18:30)。
2 改善的着眼点
一、从现场的浪费中发现问题
过量生产的浪费
搬运的浪费
物
库存的浪费
不良品的浪费
现场的七大浪费
等待的浪费
人
动作的浪费
(即:现场中不产生附 加值的活动)
法 加工的浪费
图例:
搬运浪费
动作浪费
不良浪费
二、从现场的管理标准中发现问题 做事情的最佳方法。
现状与已确立的标准之间
必须解决的差距。
பைடு நூலகம்
四、从客户的反馈/需求中发现问题
内部客户服务链:
财务部
采购部
客户
生产部
业务部
质管部 技术部
小故事:
合格率的检查标准
二战期间,美国空军降落伞的合格率为99.9%,这就意味着从概率上来 说,每一千个跳伞的士兵中会有一个因为降落伞不合格而丧命。军方要求厂 家必须让合格率达到100%才行。
厂家负责人说他们竭尽全力了,99.9%已是极限,除非出现奇迹。 于是军方改变检查标准,每次交货前从降落伞中随机挑出几个,让厂家 负责人亲自跳伞检测。 从此,奇迹出现了,降落伞的合格率达到了百分之百。
大批量
一个流
③ 改善要遵循“三现主义”的原则
现地: 1、到问题发生的现场 现物: 2、看异常事物 现认: 3、对问题的产生原因进行
分析,制定对策。
④ 改善没有终点
正确的观点:
还有改善的空 间,现在的方 法一定不是最 好的!
⑤ 全员参与
改善活动的方式有:
改善例会制度 … 主体为各部门主管 改善提案奖励制度… 主体为全体员工 自主研究改善活动… 主管、员工
维持:80% 改进:20%
改善活动中,各级别人员的职能
高层管理者 中层管理者
现场主管 工人
改进 维持
高层管理者 中层管理者
现场主管 工人
对改进功能进行分解
创新 改善 维护
二、现场管理的PDCA法:
A:处置 C:检查
P:策划 D:执行
三、管理者的行动 (1:建立标准)
1、建立标准 2、对员工展开标准的培训教育 3、对标准是否得到遵守进行监督 4、修订标准
思维方式:现在执行的方法是最好的吗?
一是与其他企业比较,找到作业方式与加工方法上存在差距;
二是转变思维,现在的方法可以改得更好。
三、通过改善培养人才
发现问题 分析问题 解决问题 分享成果
通过改善,培养人的判断力、分析力、改善力、表现力。
四、通过改善活动提高团队凝聚力
小小的蚂蚁都懂得抱团的力量
改善活动是为了把大家拧成一股绳
4:为什么吸不上油来? 因为油泵轴磨损松动了。
5:为什么磨损了? 因为没有安装过滤器混进了铁屑。
找到问题根源进行对策
3. 用特性要因图找到真因
料
机
人
烧门
法
环
测
4. 改善方案的制定 所用道具:改善的四原则表(ECRS)
原则 取消
自问
是否可以不做 如果不做会怎样
例子
通过变换布局省略搬运 省略加工
合并
人员配置合理吗/员工之间合作吗
2. 现状分析 现状来自于现场的数据、标准。
如:《品质推移表》、《工时推移表》、《生产计划管理表》
3. 发现问题的重点 (问5个为什么找到真因)
1:为什么机器停了? 因为超负荷保险丝断了。
2:为什么超负荷呢? 因为轴承部分的润滑不够。
3:为什么润滑不够? 因为润滑泵吸不上油来。
因为:有标准才能发现问题。
三、管理者的行动 (2: 制定管理目标) 1、制定管理目标(品质、工时、成本、交期) 2、为实现管理目标开展改善活动
三、管理者的行动 (3:找到客户) 1、找到各自的客户(内部/外部); 2、了解客户的需求; 3、满足客户的需求。
此次培训到此结束! 谢谢!
问题
标
现
准
状
没有标准就没有管理。
图例: 没有标准就无法管理
标准的重要性:
◆ 是教训、经验的总和,最优化的制造、管理方法; ◆ 是员工培训、教育的依据; ◆ 是管理者监督、检查的依据; ◆ 使管理可视化,一眼能发现问题。
我们要创建哪些标准?
人:《出勤管理规定》、 《新员工培训管理规定》、《作业要领书》、
品质自働化
工序内控制品质 异常时自动停止 设备有防错功能
以消除七大浪费为着眼点,在生产、管理以及工 作方式上要不断地进行改善与创新。
提纲
1 改善的目的 2 改善的着眼点 3 改善的原则.步骤 4 管理者的行动
相关的概念
一、什么是现场?
• 广义:企业赚取利润活动的主要场所。 (研发、生产、销售)
• 狭义:制造产品或提供服务的地方。
推动进步的一种工作方法。
改善就是发挥人的智慧,让现场改得更好、更 简单、更轻松、更方便。
五、主要的改善工具
精益工厂
TQM
均 衡 生 产
质 量 改 善 方 法
IE 持 续 改 善
TPM
拉 动 看 板
全 员 生 产 维
快 速 切 换
护
单 元 生 产
全员5S活动、全员改善提案活动
1 改善的目的
一、为什么要改善?
• 生产现场是一面镜子,直接反映管理水平的高低。
解决问题唯有
依靠生产现场。
大野耐一
因为:现场展现问题,有事实、有数据。
解决现场问题的两种方法:
一、创新
运用高科技,投入大成本。
二、改善
改善运用常识性工具,不需要花多少钱。
( TQM、TPM、JIT、QC活动、员工提案建议制度)
四、什么是改善?
改善:就是发现问题、动手解决问题,
二、现场改善是谁的事情?
以降低库存的改善为例进行说明: 主责
原材料 采购部
次责 质管部
总库存
在制品 生产部
技术部、质管部
技 术成品 生销产售、部品质 采生购产、部仓、库、、
现场改善与各个部门息息相关。
三、现场改善为什么从生产开始?
• 生产是主线,通过生产过程中发生的问题,拉出 其他版块(采购、技术、人力等)存在的问题。
2个以上的工序是否 2个以上的加工同时作业
可以组合起来
加工与检查同时作业
重排 简化
是否可以调换工序 是否可以改变方法
更换加工顺序提高作业效率
是否可以更简单
(数量、动作)
手动改自动
5. 实施、评价改善方案(与目标对比) 6. 跟踪处理改善方案(标准化)
问题描述:涂装喷漆流水线FD110磁电的挂具现存在以下问题:
《异常处理流程》
机:《安全操作规程》、《设备点检标准》、《换型作业指导书》 料:《检验标准》、《库存管理标准》、 《出入库管理标准》、
《物料消耗管理标准》
环: 《3S管理标准》 其他:《从接单到生产的业务流程》、《模具的开发流程》……
三、从现场的管理目标中发现问题
为什么要求制定品质、工时管理目标?
1.生产效率低(8个/挂)。 2.喷漆时油漆浪费大。
改善对策:重新设计制作一挂12只的挂具。
效果确认: FD110磁电4.1-4.15不良率为22.9%, 4.16-4.30不良率为20.4%,在不影响品质
的前提下,效率提升了50%!
改善前后
问题描述:产品自动喷塑后,两侧的窗口因静电吸附不够,导致窗口位置经常
3 改善的原则.步骤
一、改善的原则
① 改善要有明确的目标或具体需求
如:不良下降多少? 周期缩短多少? 效率提高多少? 成本降低多少?
量化指标
或:改善现场环境 改善现场安全 降低劳动强度
具体需求
② 改善要马上行动
不要找借口(设限):如
我们一直都是这样的,没有办法改! 这个是不可能的! 做这个价值不大!(如果每人一天省1毛钱)
露底,造成不良。
改善对策:将窗口补喷调整到自动喷之前进行。
最低节省成本 2072元/月
效果: 日期 1月份
2月1-15日
改善前
露底数
不良率
3721
1.4%
1454
3.0%
日期 2月16-28日
3月份
改善后 露底数 96 232
不良率 0.06% 0.068%
4 管理者的行动
一、现场管理的两大项工作: 维持:现行技术、管理方法和操作标准。 改进:提升现行标准,包括创新和改善。
二、改善的基本步骤:
1.问题的发生、发现
要改善什么
2.现状分析
现状是怎样的(数据)
3.发现问题的重点
为什么会发生(真因)
4.改善方案的制定
怎样对策
5.实施、评价改善方案 对策是否有效(与目标对比)
6.跟踪处理改善方案
标准化
1. 问题的发生、发现 (要改善什么)
调查项目
调查重点
P:生产率、生产量
产量下降了吗/产量还能提高吗/人员过多或过少/ 设备正常吗
现场改善及案例分析
预计用时:100分钟
精益生产的理论框架
生产准时化
在需要的时间 按需要的数量 提供需要的产品
目 标:
低成本、高品质、短交
期地进行生产,最大限度的满
足客户需求。
准
员工和团队
时
化
●一个流
持续改善
●快速切换 ●后拉生产 ●快速切换
减少浪费
问5个为什么
改 善:
自 働 化
●异常停止 ●自动防错 ●就地解决
Q:质量 C:成本 D:交期
质量指标超标吗/有批量不良发生吗/客户有投诉吗 /哪些不良项目上升了/工艺合理吗
原材料、辅料、燃料消耗上升了吗/库存超标了吗/ 采购成本上升了吗
产品交期延误了吗/生产周期可以缩短了吗/采购周 期可能缩短吗