精脱硫资料
精脱硫施工方案

精脱硫施工方案一、前言精脱硫是工业生产中常见的清洁技术,通过去除燃料中的硫化物来减少环境污染。
本文将从施工方案方面介绍精脱硫的具体操作步骤。
二、准备工作在进行精脱硫施工前,需要做好以下准备工作: - 确定施工计划和方案; - 准备所需的施工设备和工具; - 对施工人员进行培训,保证他们熟知施工流程和安全操作规范; - 检查施工区域的安全性。
三、施工步骤1. 清洁施工区域在进行精脱硫施工前,需要将施工区域进行清洁,确保没有固体杂质和积污物。
2. 安装设备将所需的精脱硫设备按照设计要求安装到指定位置,确保设备连接牢固,管道通畅。
3. 调试设备在安装完成后,需要对设备进行调试,检查设备运行是否正常,消除可能存在的故障。
4. 开始施工按照施工方案的要求,启动精脱硫设备,开始进行硫化物的去除操作。
5. 监控操作在施工过程中需要不断对设备进行监控,确保操作正常,及时处理可能出现的问题。
6. 收尾工作在完成精脱硫操作后,对设备和施工区域进行清理,保持现场整洁。
四、注意事项在进行精脱硫施工时,需要注意以下事项: - 确保施工人员穿戴好个人防护装备,保障施工安全; - 严格按照施工方案进行操作,不得擅自更改; - 定期对设备进行维护保养,延长设备使用寿命。
五、结语精脱硫作为一项重要的环保技术,在工业生产中发挥着重要作用。
通过本文的介绍,相信大家已经对精脱硫施工方案有了更深入的了解。
希望在今后的施工实践中,能够更好地应用和推广精脱硫技术,共同保护环境、实现可持续发展。
以上为精脱硫施工方案的介绍,谢谢阅读。
常温精脱硫工艺技术

常温精脱硫工艺技术氮肥循环经济支撑技术简介技术名称:常温精脱硫工艺技术技术拥有单位:湖北省化学研究所生产基地一、基本原理、技术特点及技术水平1、基本原理合成氨原料气中一般含有H2S、COS及CS2等硫化物,有的还含有RSH、RSR等,这些硫化物对甲醇催化剂、甲烷化催化剂、铜系低变催化剂都有毒性,常温精脱硫工艺技术是将这些硫化物脱至各种催化剂所要求的精度(总硫<0.1ppm)。
常温精脱硫剂有特种氧化铁、特种活性炭两个系列。
2、技术特点(1)精脱硫在常温下进行(有水解时温度<100℃);(2)脱硫精度高,经精脱硫后气体中总硫化物可<0.1ppm;(3)脱硫剂空速高,达≥1000h-1 ;(4)硫容高,穿透硫容(即出口气中总硫<0.1ppm时)达15%以上;(5)节能,此工艺基本不耗能。
3、技术水平本精脱硫工艺技术达到国际先进水平;在国内处于领先地位,具有自主知识产权的全套技术。
已有7种精脱硫剂出口至英、美等国家。
二、适用范围适用于以煤、天然气、油等为原料的煤气、变换气、脱碳气、高浓度CO2气的精脱硫。
使用领域涉及合成氨、甲醇、精细化工、石油化工、食品CO2,……等。
三、总投资一个年总氨12万吨/的厂(其中NH310万吨,CH3OH 2万吨),精脱硫装置操作压力1.6MPa(G),脱碳气中H2S≤5mg/Nm3,COS+CS2≤2mg/Nm3的条件下,设计采用JTL-4精脱硫工艺,总投资147万元(只含设备及精脱硫剂费用)。
其中,主要设备投资84 万元。
四、应用效果1、经济效益目前多家生产厂实践证明,不上精脱硫甲醇催化剂寿命3~6个月;采用精脱硫工艺技术后催化剂寿命高达3年。
即催化剂使用寿命延长了5~10倍,根据计算,上精脱硫与不上精脱硫甲醇催化剂一个更换周期(三年)相比,经济效益达1970万元(含更换催化剂影响生产损失的利润、催化剂费、开车费等)。
2、社会效益气体精脱硫后,催化剂寿命大大延长,减少了催化剂原料、材料(Cu、Ni等)的消耗,节省了国家资源。
高炉煤气精脱硫技术介绍
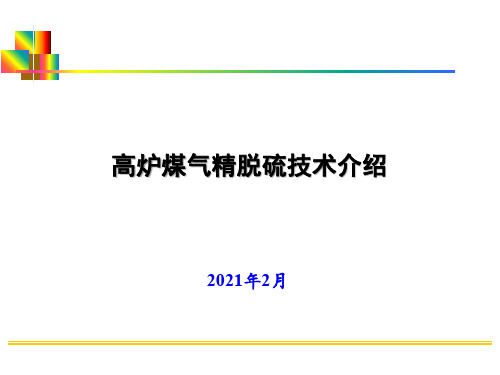
3.高炉煤气精脱硫难点及工艺选择
工艺缺点: 采用“水解+湿法脱硫工艺” ,其可以满足煤气中硫分从150
mg/Nm3降至20mg/Nm3的技术要求;但从目前的效果看: ① 催化剂的稳定性不足、寿命过短、系统阻损较大且存在上 升的隐患,再生困难、成本高。 ② 煤气温度会降低较多,对TRT或BPRT系统及热风炉系统的 运行成本影响较大。 ③ 增加了煤气的水份含量,管网存在腐蚀的可能。 ④ 碱液在脱除H2S的同时,也与部分CO2发生反应,碱液消耗 量大,且会引起高炉煤气热值变化。
解后的煤气温度都比较高,在进入湿法脱硫之前,要设置降温 塔对煤气进行降温。
3.高炉煤气精脱硫典型工艺简介
—工艺(一)
H2S的脱除:高炉煤气经水解,煤气中的有机硫绝大部分转化 为H2S后,进入湿法脱硫装置。 湿法脱硫采用湿式氧化法脱硫。 湿法脱硫的碱源只有氨源与碱源两种。由于高炉煤气中没 有氨的存在,因此,用Na2CO3做为碱源为首选。 根据高炉煤气的工艺状况,选择酞菁钴系列的ZT高效脱硫 催化剂。 吸收塔采用填料脱硫塔,填料采用聚丙烯阶梯环。 再生选择采用喷射氧化再生工艺。
单独脱除一种形态的硫化物, 当进气硫含量甚低时, 可用吸收 型脱硫剂(单脱H2S)或转化吸收型脱硫剂(脱COS和CS2) 一次达到精脱硫的要求。
进气H2S 含量足够低 , COS、CS2稍高时 , 可采用水解吸收两 段精脱硫工艺。
进气H2S、COS、CS2含量均较高时, 可采用吸收-水解- 吸收或 吸收- 水解-转化吸收工艺。
1.高炉煤气精脱硫背景简介
现有高炉煤气净化及后续应用主要是采用袋式除尘去除颗粒物,再 经过TRT余压发电后,送往高炉热风炉、轧钢加热炉、煤气发电等用户 单元作为燃料使用,但高炉煤气中仍然含有硫、氯等有害物质。
JTS-3型精脱硫剂应用总结

甲醇脱 硫 塔 为两 段 式 结构 , 段 高 35 0mm, 每 0 直径 30 0mm; 填 量 5 , 0 装 0m。 设计 压力 2 3 a . 7MP , 设 计 温度 5 C, 采作 压力 2 1 a 操 作温 度 < 0_ 操 . 5MP , 4 0℃ ; 壳体 材料 为 1 Mn 内件 材 料 为 碳 钢 。装 填 6 R,
使用 情况 和企业 实 际 。2 0 0 3年 经 多方 考察 , 用 了 采 河南 省长 葛市龙 基 实业 有 限公 司 生产 的 J S一3型 T 精脱 硫剂 , 用 效果 很好 。 使
1 JS T 一3型 精脱硫 剂 介绍
1 】 活 性 炭 脱 硫 原 理 .
≥07 . ≥80 0 ≥ 2 6
活性 炭展 开的 大表 面 活 性点 催 化作 用 , 常温 常 压 在 条件 下发生 下列 氧化 还原 反应 : s / 0 一 H O H。 +1 2 +s 。反应 生成 的单 质 硫被 活 性 炭 发 达 的空 隙 吸
附= 其 中 , 至饱 和 。 F 直
温度 :0 0℃( 佳 温度 3 ~5 2  ̄6 最 2 2℃) 硫化 物与 氧含量 比值 : 2 l:
3 J S一 T 3型精脱 硫 剂在 我 厂的 使 用情 况 我 厂 8 ta甲醇装 置 正 常气 量 为 4 0 / 0k / 00 0m h 温度 为 0 0。 压 力在 2 1 a以下 。该 炉 脱 , ~4 C, . MP
硫 于 20 0 4年 6月 3 0日装 填 , 填 量 为 5 I, 已 装 0I 现 T
3~ 4
比表 面 积 / m ( ・ ) g 硫容 ( S . H2 )
硫 容 ( OS . C )
13 工 艺 条 件 . 空 速 :O ~ 20 0h 5 0 0
高炉精脱硫的原理和方法

高炉精脱硫的原理和方法【摘要】高炉精脱硫是钢铁生产中一项重要的环保措施,具有重要性和必要性。
该技术通过气相脱硫、液相脱硫和固体脱硫等方法,将含硫废气中的有害物质去除,从而减少环境污染。
气相脱硫是指通过在高炉煤气中注入氨水或其他脱硫剂来吸收硫化氢等硫化物。
液相脱硫则是利用化学反应将硫化物转化为不溶于水的硫酸盐来去除。
固体脱硫利用添加含钙、镁等金属离子的材料将硫化物转化为易溶解的硫酸盐,实现脱硫目的。
尽管高炉精脱硫技术仍有一些需要改进的地方,但其发展前景仍然十分广阔。
关键影响因素包括脱硫剂的选择和反应条件的优化等。
高炉精脱硫技术的不断发展将为钢铁行业的绿色可持续发展提供重要支持。
【关键词】高炉精脱硫、重要性、必要性、原理、方法、气相脱硫、液相脱硫、固体脱硫、技术发展前景、关键影响因素。
1. 引言1.1 高炉精脱硫的重要性高炉精脱硫是钢铁生产过程中非常重要的一环,它的主要作用是降低高炉烟气中的硫含量,减少对环境的污染。
硫在燃烧过程中会形成二氧化硫等有害气体,如果直接排放到大气中,会对人体健康和周围的生态环境造成严重影响。
高炉精脱硫可以有效地降低硫排放量,保护环境。
高炉精脱硫还对钢铁生产过程有着重要的影响。
高硫铁矿石在高炉内的使用会导致铁水中硫含量增加,容易影响钢铁的质量。
通过高炉精脱硫,可以有效地减少铁水中的硫含量,提高钢铁的质量,保证产品符合相应的标准要求。
高炉精脱硫的重要性在于减少环境污染,保护生态环境,以及提高钢铁生产的质量和效率。
研究和应用高炉精脱硫技术具有非常重要的意义。
1.2 高炉精脱硫的必要性高炉精脱硫是一项极为重要的环保工作,其必要性主要体现在以下几个方面:高炉精脱硫是为了保护环境和人类健康。
硫化物大量排放会导致酸雨的形成,对大气、水体和土壤造成严重污染,对植物生长和动物生存造成危害。
通过高炉精脱硫技术,可以有效减少硫化物排放,降低环境污染,改善空气质量,保护生态环境,减少人类健康受到的影响。
脱硫剂

T102、T103精脱硫剂已广泛用于合成氨、甲醇、联醇、甲烷化、合成燃料、食品CO2、聚丙烯等生产工艺中精脱硫。
EAC-2或EAC-3型活性炭精脱硫剂97年元月已通过化化工部和湖北省联合主持的专家鉴定,分别被化工部化肥催化剂标准化技术归口单位正式命名为T102和T103型活性炭精脱硫剂,列为国家正式产品。
一、与普通脱硫剂相比,T102及T103精脱硫剂有下列特点:1.脱硫精度高。
普通脱硫剂脱硫精度为出口H2S≤1.0ppm,用于粗脱硫;而EAC精脱硫剂脱硫精度高为出口H2S≤0.03ppm。
2.反应速度快。
研究表明,EAC的穿透空速是普通脱硫剂的2~3倍。
工业使用时,普通脱硫剂的使用空速为200~500h-1,EAC的使用空速为1000~2000h-1左右。
3.精脱硫剂的工作(穿透)硫容高。
研究表明,EAC型精脱硫剂工作硫容为其它常温脱硫剂的3~5倍。
三、反应原理及质量检验标准1. 反应原理原料气中的H2S与残存的O2作用生成硫沉积在微孔中。
其反应式为:H2S+1/2O2=S+H2O △H=-434.0KJ/molDS-1精脱硫剂DS-1精脱硫剂是湖北省化学研究院采用全新配方及工艺研制开发出来的新型、高效耐缺氧型精脱硫剂,可在10~150℃的无氧条件下,用于天然气、油田气、液化气、炼厂气、合成气、变换气等多种气体及石脑油、汽油等液态烃的精脱硫,以保证各类气体及油品的总硫和铜片及银片腐蚀达标,保证蒸气转化、低变、甲烷化、甲醇、联醇、合成氨、聚丙烯和羰基合成等含镍、铜、铁及贵金属催化剂的正常使用和产品质量的提高。
一、性能特点(1)特别适用于无O2的气体或液体,在使用过程中不需向脱硫系统补充空气或氧气。
目前,国内各种活性炭与氧化铁(精)脱硫剂的硫容在无O2工况下急聚下降,ZnO虽然可以使用,但在低常温下硫容低、价格高。
对比试验表明在低常温无O2工况中,DS-1精脱硫剂的硫容比国内最好的脱硫剂产品要高3倍。
精脱硫
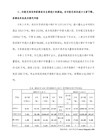
其主要化学反应为:
C4H4S(噻吩)+4H2C4H10+H2S (1)
R-SH(硫醇)+H2RH+H2S (2)
R1-S-R2(硫醚)+2H2R1H+
R2H+H2S (3)
COS+H2CO+H2S (4)
COS+H20 CO2+H2S (5)
利用大量点天灯外排的焦炉煤气,对建设资源节源
型社会,实现经济可持续发展具有重要意义。
1 焦炉煤气的利用途径
① 焦炉煤气的组成与杂质含量
焦炉煤气的主要组分为H2、CO、CH4、CO2等,
随着炼焦配比和操作工艺参数的不同,焦炉煤气的
组成略有变化。一般焦炉煤气的组成见表1,杂质
含量见表2。
近年来,随着钢铁工业对焦炭的巨大需求而高
速发展起来的炼焦产业,在焦炭产能无序扩张、产量
大幅度增长的同时,副产的大量焦炉煤气导致了焦
炭产区的环境急剧恶化,不少单一炼焦的独立焦化
企业“只焦不化”,对大量炼焦剩余的焦炉煤气采取
点天灯方式燃烧排空,既严重污染环境,又造成资源
浪费。作为贫油、缺气的能源需求大国,充分、合理
焦炉煤气中杂质含量高,净化难度大,净化成本
高,制约了其作为化工原料气的用途和经济性。通
常经过焦化厂化产回收预处理的焦炉煤气,仍然含
有微量焦油、苯、萘、氨、HCN、Cl-、不饱和烯烃,以
及H2S、噻吩(C4H4S)、硫醚、硫醇、COS、CS2等杂
质。其中,焦油、苯、萘、不饱和烯烃会在后续的焦炉
硫。
水解法脱除有机硫由于操作温度为中低温,可
甲醇精脱硫知识问答
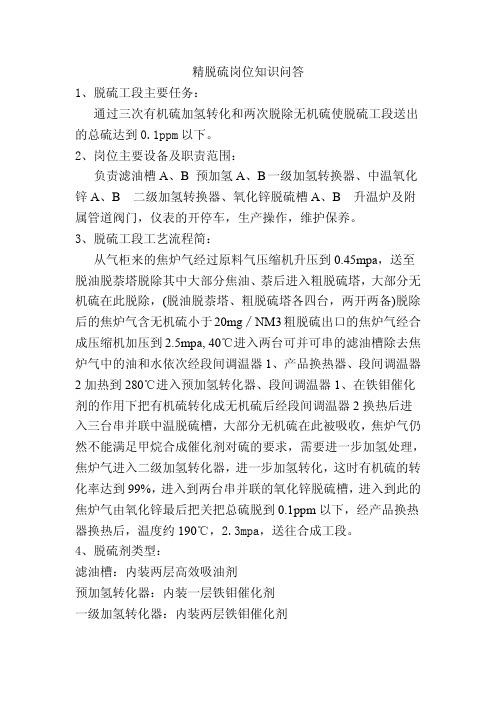
精脱硫岗位知识问答1、脱硫工段主要任务:通过三次有机硫加氢转化和两次脱除无机硫使脱硫工段送出的总硫达到0.1ppm以下。
2、岗位主要设备及职责范围:负责滤油槽A、B预加氢A、B一级加氢转换器、中温氧化锌A、B二级加氢转换器、氧化锌脱硫槽A、B升温炉及附属管道阀门,仪表的开停车,生产操作,维护保养。
3、脱硫工段工艺流程简:从气柜来的焦炉气经过原料气压缩机升压到0.45mpa,送至脱油脱萘塔脱除其中大部分焦油、萘后进入粗脱硫塔,大部分无机硫在此脱除,(脱油脱萘塔、粗脱硫塔各四台,两开两备)脱除后的焦炉气含无机硫小于20mg∕NM3粗脱硫出口的焦炉气经合成压缩机加压到2.5mpa,40℃进入两台可并可串的滤油槽除去焦炉气中的油和水依次经段间调温器1、产品换热器、段间调温器2加热到280℃进入预加氢转化器、段间调温器1、在铁钼催化剂的作用下把有机硫转化成无机硫后经段间调温器2换热后进入三台串并联中温脱硫槽,大部分无机硫在此被吸收,焦炉气仍然不能满足甲烷合成催化剂对硫的要求,需要进一步加氢处理,焦炉气进入二级加氢转化器,进一步加氢转化,这时有机硫的转化率达到99%,进入到两台串并联的氧化锌脱硫槽,进入到此的焦炉气由氧化锌最后把关把总硫脱到0.1ppm以下,经产品换热器换热后,温度约190℃,2.3mpa,送往合成工段。
4、脱硫剂类型:滤油槽:内装两层高效吸油剂预加氢转化器:内装一层铁钼催化剂一级加氢转化器:内装两层铁钼催化剂中温脱硫槽:内装两层中温氧化锌脱硫剂二级加氢转化器:内装两层镍钼催化剂氧化锌脱硫槽:内装两层氧化锌脱硫剂5、在精脱硫工段有很多催化剂,到底何为催化剂?答:催化剂又叫触媒,是一种能改变某一化学反应途径,加快反应速率,但不能改变反应的化学平衡,在反应前后其本身的化学状态不发生变化的物质。
6、在精脱硫整个过程中都是为了脱除硫化氢,在生产中为什么要控制硫化氢,硫化氢高了有什么危害?答:①使催化剂中毒,降低或失去活性。
高炉煤气精脱硫技术
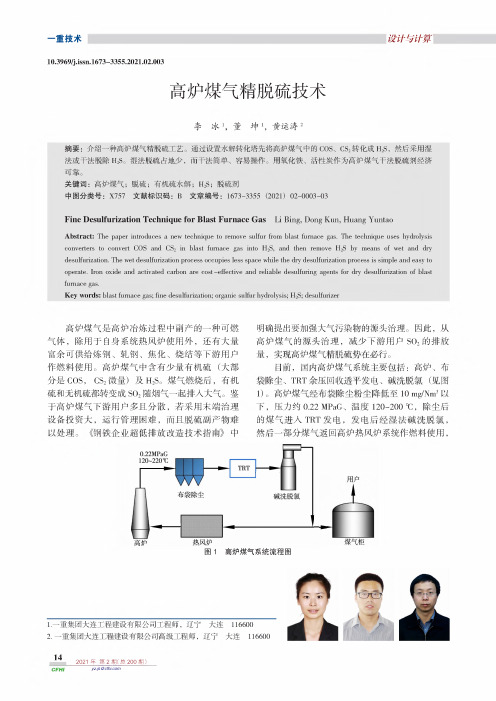
一重技术设计与计算10.3969/j.issn.l673-3355.2021.02.003高炉煤气精脱硫技术李冰董坤黄运涛121. 一重集团大连工程建设有限公司工程师,辽宁大连1166002. 一 大 程设有 高程师,大连11660014摘要:介绍一种高炉煤气精脱硫工艺。
通过设置水解转化塔先将高炉煤气中的COS 、CS 2转化成H $s ,然后采用湿除H $S u硫 少, 、 作。
用化、 作为高炉煤气 硫 济可U关键词:高炉煤气;脱硫;有机硫水解;H $S;脱硫剂中图分类号:X757 文献标识码:B 文章编号:1673-3355(2021) 02-0003-03Fine Desulfurization Technique for Blast Furnace Gas Li Bing, Dong Kun, Huang YuntaoAbstract : The paper introduces a new technique to remove sulfur from blast furnace gas. The technique uses hydrolysis converters to convert COS and CS 2 in blast furnace gas into HS, and then remove HS by means of wet and dry desulfurization. The wet desulfurization process occupies less space while the dry desulfurization process is simple and easy to operate. Iron oxide and activated carbon are cost -effective and reliable desulfuring agents for dry desulfurization of blastfurnace gas.Key words : blast furnace gas; fine desulfurization; organic sulfur hydrolysis; H 2S; desulfurizer高炉煤气是高炉冶炼过程中副产的一种可燃 气体,除用于自身系统热风炉使用外,还有大量富余可供给炼钢、轧钢、焦化、烧结等下游用户 作燃料使用。
精脱硫技术分析

维普资讯
全 国气 体 净化 信 息 站 2 0 技 术 交 流 会 论 文 集 0 6年
哈 尔滨 气 化 厂 的 甲醇 装 置运 行 至 今 , 使用 过 沸
石、 氧化 锌 、 氧化 铁 、 性 炭 4类 精 脱 硫 剂 。其 中 活 活
性炭 使用 了 E AC一3 T1 3 J 一3和 E X 4种 型 、 0 、TS Z
① 脱硫 精 度 高 , 进 口浓 度 H。 当 S为 1 0 00 0×
二硫 化铁 、 硫化铁 或 单质 硫 。其 反应 式 为 : 多
F。 O3 H2 2 + S— F S+ F S + S+ H2 e e O
足 , 而对 甲醇催化 剂 的寿命 造成 很 大危 害 , 响生 因 影
产 长期 、 定 、 稳 高效 地运 行 。
该脱 硫剂 具有 以下 特点 :
其 反应 式为 :
Z O + H n 2 S—
2 ZnO— 卜CS — 2
硫 容高 , 产 品硫容 大 于或 等 于 l . 6 对 COS有 新 8 0 /, 9
Z S H2 n + O
2Zn S+ CO2
一
定 的脱 除作用 。
沸石 脱 硫 剂 的物 理 吸 附 具 有 可逆 性 , 般 将 再 一
l 时 , 口 H2 0 出 S浓 度小 于或 等 于 0 0 ×1 ~ ; . 3 0 ② 反应 速度 快 , 许空 速 l0 0 2 0 ; 工 作 硫 允 0 ~ 0h ③ 0
焦炉煤气精脱硫工艺分析

焦炉煤气精脱硫工艺分析一、工艺原理:焦炉煤气中的H2S主要通过煤气中的Fegl肟羧酸盐、CaS等吸收剂进行吸收。
Fegl肟羧酸盐是一种高效的硫化物吸收剂,可在较低的温度下将煤气中的H2S和COS吸收。
而CaS则可以将煤气中的剩余H2S去除。
二、工艺流程:1.气体预处理:首先对焦炉煤气进行预处理,去除其中的悬浮颗粒物和水分,以净化煤气。
2.前骤吸收:采用Fegl肟羧酸盐作为吸收剂,通过吸收剂床将煤气中的H2S、COS等硫化物吸收。
床层中的吸收剂会与煤气中的硫化氢进行反应,生成硫化铁,并将其捕集。
3.普鲁士蓝阳极液循环:将废液中的硫化铁氧化为硫酸铁,通过循环泵送到反应床顶部,实现循环利用。
4.精脱硫:采用CaS作为吸收剂,通过床层吸收煤气中剩余的硫化氢,并将其转化为CaS。
此过程需要保持一定的温度和压力,以促使吸收反应的进行。
5.再复焦炉:将经过精脱硫的煤气送入焦炉进行再加热,以提高炉内温度。
三、工艺特点:1.高效: 采用Fegl肟羧酸盐和CaS作为吸收剂,可以高效地吸收煤气中的硫化物,使硫化氢的去除率达到90%以上,保证煤气的质量。
2.安全:精脱硫过程中对温度和压力的要求较高,可以有效地防止硫化氢的泄漏,保证了生产环境的安全。
3.循环利用:工艺中的废液通过循环泵送到反应床顶部,实现了废液中的硫化铁的循环利用,减少了废液的排放,具有较好的环保效益。
总结起来,焦炉煤气精脱硫工艺通过床层吸收剂的反应,有效地去除焦炉煤气中的硫化氢等硫化物,以保证煤气的质量达到环保要求。
该工艺具有高效、安全、循环利用等特点,在焦化行业得到广泛应用。
原料气精脱硫的工艺流程

原料气精脱硫的工艺流程
一、技术简介
焦炉煤气主要组成是甲烷、一氧化碳、二氧化碳、氢、氮及烯烃,同时含有微量硫、焦油、萘、氰化氢、氨、苯等杂质。
焦炉煤气作为化工原料使用时,这些杂质会对后续化工工艺过程中的催化剂造成毒害,导致催化剂部分或完全失活。
采用多级加氢的方法将气体中的有机硫转化,生成易于脱除的硫化氢,然后再采用固体脱硫剂吸收转化后气体中的硫化氢。
这样可使有机硫加氢转化完全,净化度大为提高,而且配套干法脱硫剂的硫容也高,并且可将不饱和烯烃进行加氢饱和、氧气加氢燃烧、并对其它微量杂质(如焦油、萘、氰化氢、氨、苯等)进行脱除,,达到对毒物脱除的目的,开发的精脱硫工艺,使焦炉煤气经加氢转化和吸收后,硫含量降至≤0.1×10-6。
二、技术特点
(1) 无三废产生,工艺简洁、操作简单,运行费用低
(2) 可以脱除无机硫,硫化氢脱除精度高;
(3) 可以脱除有机硫,
(4) 可以脱除苯、萘、氨、氰化氢、焦油等;
(5) 增加了生产的稳定性,减少正常产量的损失,使生产的动力消耗降低,节省的动力费用。
三、应用领域
煤焦化、煤气化、煤液化和电石、精细化工、医药电子、粉末冶
金、林农业品加氢、生物工程、石油炼制、氢燃料清洁汽车等行业。
精脱硫工序操作规程讲解

精脱硫工序操作规程讲解一、工序概述精脱硫工序是指通过一系列的化学反应和物理处理,将燃煤电厂产生的废气中的二氧化硫(SO2)进行脱除的过程。
该工序是燃煤电厂环保设施中的重要组成部分,能够有效减少二氧化硫的排放,保护环境。
二、工序原理精脱硫工序主要通过湿法脱硫的方式进行。
废气经过预处理后,进入脱硫塔,与喷射的石灰乳液进行充分接触和反应。
在反应过程中,二氧化硫与石灰乳液中的氢氧化钙(Ca(OH)2)发生化学反应,生成硫酸钙(CaSO3)和水(H2O)。
最终,废气中的二氧化硫被脱除,净化后的废气排放到大气中。
三、工序步骤1. 脱硫塔准备a. 检查脱硫塔设备的完好性和运行状态,确保各阀门、泵等设备正常工作。
b. 检查石灰乳液的储存罐,确保储存罐内有足够的石灰乳液。
c. 检查脱硫塔的排污系统,确保排污系统正常运行。
2. 废气预处理a. 废气经过除尘器进行初步净化,去除大部分的颗粒物。
b. 废气进入脱硫塔前,通过加热器进行预热,提高反应效果。
3. 脱硫反应a. 废气进入脱硫塔,与喷射的石灰乳液进行充分接触和反应。
b. 废气中的二氧化硫与石灰乳液中的氢氧化钙发生反应,生成硫酸钙和水。
c. 反应过程中,废气中的其他污染物也会被吸附和脱除。
4. 产物处理a. 反应后的废气经过除湿器进行除湿处理,去除水分。
b. 除湿后的废气经过除雾器进行除雾处理,去除细小的颗粒物。
c. 净化后的废气通过排气系统排放到大气中。
四、工序注意事项1. 操作人员必须穿戴好个人防护装备,包括防护眼镜、防护口罩、防护手套等。
2. 定期检查设备的运行状态,确保各部件正常工作。
3. 定期检查石灰乳液的储存情况,及时补充石灰乳液。
4. 定期清洗脱硫塔和相关设备,以保证设备的正常运行和反应效果。
5. 注意废气排放的合规性,确保排放的废气符合环保要求。
五、工序效果评估1. 定期对脱硫塔进行效果评估,检测废气中的二氧化硫浓度,确保达到国家排放标准。
2. 定期对废气进行监测,检测废气中的其他污染物浓度,确保排放的废气符合环保要求。
微晶吸附精脱硫原理

微晶吸附精脱硫原理
微晶吸附是一种新型的脱硫技术,其原理是利用微晶材料具有较大的比表面积和可控的孔隙结构,能够通过吸附作用将气体中的硫化物物质去除。
微晶吸附脱硫的过程如下:
1. 吸附剂选择:选择适合的微晶材料作为吸附剂,常用的微晶材料包括活性炭、分子筛等。
2. 吸附:将含有硫化物的气体通过吸附床,床内的微晶吸附剂能够吸附气体中的硫化物分子。
吸附是通过吸附剂表面的吸附位点吸附硫化物分子来实现的。
3. 饱和:随着吸附过程的进行,吸附剂上的吸附位点逐渐饱和,即吸附剂上的硫化物分子数逐渐增加,直到达到一定的吸附容量。
4. 再生:吸附剂饱和后,需要进行再生操作以将吸附的硫化物分子去除。
常用的再生方法包括热解、蒸汽再生等。
在再生过程中,吸附剂中的硫化物分子会解吸并释放出来。
微晶吸附精脱硫原理是通过吸附作用将气体中的硫化物去除,能够高效地降低气体中硫化物的浓度。
该技术具有结构简单、操作方便、效果显著等优点,是一种应用广泛的脱硫方法。
干法常温精脱硫技术

丙烯腈——合成纤维、树脂、橡胶的重要原料,90% 由丙烯氨氧化生产丙烯腈。 合成丙烯腈所用催化剂 ——钼、铋酸盐催化剂 存在问题 —— 丙烯原料中硫含量较高,硫氯等 杂质易使钼、铋酸盐催化剂中毒失活,使产品质 量下降,增加生产成本!
齐鲁分公司腈纶厂决定增设一套丙烯精制工艺,为 确保丙烯质量满足丙烯腈装置的生产需求,使用中 国石油大学(北京)开发的精脱硫工艺技术。
3.7 常温精脱硫工艺流程
C-301:固碱塔;C-302:COS水解塔;C-303:氧化锌脱硫塔;F-101:过滤器 图2 干法精脱硫工艺主流程
3 常温精脱硫技术在丙烯制丙烯腈中的应用
3.7 常温精脱硫工艺流程
来自上游的液体丙烯自下部侧面进入固碱塔,丙烯与固碱床层接触,丙烯中含有 的微量水分被床层吸收,丙烯自塔顶排出进入COS水解塔。固碱床层不断吸收水分后 形成液体,并在塔底部积累。塔底部设有液面计,通过巡检时检查液面计中碱水与丙 烯间的界面可观察塔底部所积累碱水液位高度。当碱水液面超过液面计量程一半时即 可排放废水,通过手动阀并观察界面变动情况,将塔底部形成的含碱水层排放至桶外 送。 当固碱床层消耗以后,脱水效果将降低。根据固碱塔下游丙烯中水分的定期分析 结果,可切换至备用塔,并根据固碱床层消耗情况需要补充固碱。 来自固碱塔顶部的液体丙烯自底部进入水解塔,水解塔内设有由脱羰基硫剂构成 的催化剂床层,流经床层与催化剂充分接触,丙烯中的羰基硫等杂质被吸附、转换。 丙烯物流自塔顶部排出,送入氧化锌脱硫塔。 来自COS水解塔的丙烯依次自塔底部进入精脱硫塔。丙烯流经床层与脱硫剂接 触,丙烯中的无机硫等杂质被吸附、吸收。净化后丙烯物流自塔顶部排出,送入过滤 器。 液体丙烯经过滤器脱除微量催化剂固体颗粒,防止带入下游。设置两台过滤器, 一开一备。
原料气的精脱硫

焦炉煤气铁锰脱硫剂(主要活性组分Mn+Fe+Zn(%)≥35%)
外观:
黑褐色条形
几何尺寸:
Φ4x8-15mm
侧压抗破碎强度:N/cm:≥40
堆积密度,kg/l:1.0-1.1
磨耗率(%): ≤10
脱硫活性:
≤0.1ppm
操作工作硫容;
≥18%
2021/3/11
ZnO与硫化物进一
2 原步料反应气,精除去脱有硫机 的工艺流程
ZnO+H2S→ZnS+H2O ZnO+C2H5SH→ZnS+C2H5OH ZnO+C2H5SH→ZnS+C2H4+H2O
2021/3/11
同时,硫氧化碳和二硫化碳先加氢反应生成硫化氢 ,然后再被氧化锌所吸收。其反应式为:
COS+H2→H2S+CO CS2+4H2→2H2S+CH4
工业生产中,氧化锌脱硫的操作温度较高,一般在 200-400℃左右。这主要是由于普通氧化锌脱硫剂在 常温下反应速度慢,吸收硫化氢的效果较差。
2021/3/11
氧化铁法脱
硫基本上可
以除净H2S, 当煤气中的
H2S含量高 时,流程将
变成湿法脱
硫与氧化铁
法脱硫串联
使用。
•铁(钴)钼加氢-氧化锌法
有机硫化物脱除一般比较困难,但将其加氢转化成硫 化氢就可以容易脱除。其反应为:
COS+H2→CO+H2S CS2+4H2→2H2S+CH4 RCH2SH+H2→RCH3+H2S C4H4S+4H2→C4H10+H2S 当原料气中有碳的氧化物和氧存在时,钴钼催化剂上 会发生甲烷化反应和脱氧反应,即: CO+3H2→CH4+H2O O2+2H2→2H2O
精脱硫工序操作规程讲解

精脱硫工序操作规程讲解一、引言精脱硫是一种重要的工序,用于去除燃煤电厂等工业过程中产生的二氧化硫(SO2)等有害气体。
本文将详细介绍精脱硫工序的操作规程,包括工序概述、操作步骤、设备使用和维护等方面的内容。
二、工序概述精脱硫是一种通过吸收和氧化的过程,将燃煤电厂的废气中的SO2转化为硫酸盐或硫酸。
该工序通常在烟囱底部设置石灰石浆液喷淋装置,通过喷淋石灰石浆液,使废气中的SO2与石灰石反应生成硫酸钙或石膏,并通过后续处理将其分离。
三、操作步骤1. 准备工作a. 确保操作人员佩戴适当的个人防护设备,如手套、护目镜和呼吸器等。
b. 检查设备的运行状况,确保其正常工作。
c. 检查石灰石浆液的供应是否充足。
2. 启动设备a. 打开石灰石浆液喷淋装置的进水阀门,确保石灰石浆液供应畅通。
b. 启动废气处理设备,确保其正常运行。
3. 调节操作参数a. 根据废气流量和SO2浓度的监测结果,调节石灰石浆液的喷淋量,以确保最佳的脱硫效果。
b. 监测并调节废气温度,保持在适宜的范围内,以提高脱硫效率。
4. 监测和记录数据a. 定期监测废气中的SO2浓度,记录并分析数据,以评估脱硫效果。
b. 记录石灰石浆液的消耗量和供应情况,以便及时补充。
5. 停机和维护a. 按照设备的操作手册和维护计划,定期停机进行设备检修和维护。
b. 清洗和更换喷淋装置中的堵塞物,以确保其正常工作。
c. 定期检查和更换石灰石供应系统中的阀门和管道,以防止泄漏和堵塞。
四、设备使用和维护1. 石灰石浆液喷淋装置a. 确保喷嘴的通畅,定期清洗和更换堵塞的喷嘴。
b. 检查喷淋装置的压力和流量,确保其正常工作。
c. 定期检查和更换喷淋装置中的密封件,以防止泄漏。
2. 废气处理设备a. 定期检查和更换废气处理设备中的滤网和过滤介质,以确保其有效工作。
b. 清洗和维护废气处理设备中的泵和管道,以防止堵塞和泄漏。
3. 石灰石供应系统a. 定期检查和更换石灰石供应系统中的阀门和管道,以防止泄漏和堵塞。
- 1、下载文档前请自行甄别文档内容的完整性,平台不提供额外的编辑、内容补充、找答案等附加服务。
- 2、"仅部分预览"的文档,不可在线预览部分如存在完整性等问题,可反馈申请退款(可完整预览的文档不适用该条件!)。
- 3、如文档侵犯您的权益,请联系客服反馈,我们会尽快为您处理(人工客服工作时间:9:00-18:30)。
要:我国焦化企业每年副产约640 Gm3焦炉煤气,只有约15%得到利用。
焦炉气的洁净化、资源化利用,符合我国保护环境、节约资源和可持续发展的国策。
焦炉煤气化工利用的关键是焦炉煤气的深度净化技术。
西北化工研究院开发两段加氢、两段吸收工艺及其相应的加氢转化催化剂和净化吸收剂已实现工业应用,净化度达到0.05×10-6~0.1×10-6,满足了甲醇生产的净化要求。
我国是炼焦大国,由于世界焦炭市场供不应求,近年来我国炼焦行业发展很快。
据统计,2005年,世界焦炭产量4.7亿吨,我国焦炭产量占全球总产量比重约53%。
2005年底,国内规模以上焦炭生产企业近千家,产量2.43亿吨,其中机焦产量为2.33亿吨,占焦炭总产量的90%以上,土焦产量所占比例降低到10%以下。
2006年底我国焦炭年生产量约2.75亿吨,按每1.33 t干煤生产1 t焦炭和每吨干煤生产320 m3焦炉煤气计算,全国焦炉煤气年总产量约1170亿立方米,除炼焦自身用焦炉煤气外,每年排放的焦炉煤气达640亿立方米。
焦炉煤气未经利用放空,不仅造成资源浪费,而且对环境造成巨大污染。
将焦炉煤气转变为既是化工原料又是清洁燃料的甲醇,成为近年来的热点。
在成熟的甲醇合成方案中,经济性最好的包括焦化(焦炉气)联醇、化肥(合成氨)联醇、利用高硫煤多联供生产甲醇。
按照中、美两国合作进行的“3E”研究成果中对燃料甲醇的几种生产方案进行综合比较后认为,化肥联醇和焦化联醇最为经济。
与以煤为原料相比,焦炉煤气作为合成甲醇、合成氨和制氢的原料,具有装置投资少、资源丰富、原料成本低的特点,经济优势明显。
尤为重要的是,焦炉煤气的资源最大化利用,符合我国建设节约型社会、保护环境、循环经济和资源、环境与社会协调、可持续发展的国策,也是煤基甲醇、煤基合成氨的又一种实现形式。
目前,已开工建设和改造的以焦炉气为原料的甲醇项目能力已经达100万吨以上。
对焦炉气深度净化工艺的需求非常紧迫。
1.焦炉煤气净化技术现状焦炉煤气含有微量硫、烯烃、氧气、焦油、萘、氰化氢、氨、苯等杂质。
焦炉煤气作为化工原料使用时,这些杂质会对后续化工工艺过程中的催化剂造成毒害,导致催化剂部分或完全失活。
尤其是现代高效合成催化剂,要求合成气中硫含量低于0.1×10-6;而焦炉煤气在进入蒸汽转化催化剂之前也要求烯烃等杂质总含量尽可能低于50×10-6。
因此,无论是作为工业原料还是民用燃料,高效脱除焦炉煤气中的硫、烯烃、焦油、萘、氰化氢、氨、苯等杂质,是焦炉煤气资源化利用的关键。
焦炉煤气典型的组成见表1。
表1 焦炉煤气的典型组成(体积分数)由表 1 可见,焦炉煤气虽然是良好的合成甲醇、合成氨及制氢原料,但其所含的杂质如各种形态硫、焦油、萘、氨、氧、不饱和烃类等对后续的转化、合成等催化剂有极大的毒害。
硫化物会与转化催化剂的主要活性组分Ni迅速反应,生成NiS,使催化剂失去活性,而且无法再生。
不饱和烃、焦油、萘、氰化氢、氨、苯会在转化催化剂表面发生析炭及其他副反应,堵塞催化剂的有效孔,遮盖表面活性位,使催化剂活性下降。
甲醇合成催化剂对硫含量及其他杂质更为敏感,对焦炉煤气深度净化的要求更高一些。
目前,国内现有的焦炉煤气净化工艺主要是湿法净化,近十几年,国内设计的焦炉煤气净化工艺中,均设有脱硫、脱氰等湿法净化装置,一方面是为了减轻硫化氢和氰化氢对后续装置的腐蚀,更重要的是减轻焦炉煤气作为燃料气时对大气造成的污染。
焦炉煤气作为化工原料时其净化工艺主要是采用湿法净化再加干法净化的净化工艺以减轻对后续催化剂的毒害。
目前,我国焦炉煤气脱硫、脱氰工艺有Takahax-Hirohax法(简称TH)、索尔菲班法、 Fumarks-Rhodacs-Compacs法(简称 F.R.C.)、真空碳酸盐法、AS 法、ADA法、OMC法、PDS法以及HPF等。
各种脱硫工艺针对不同的工艺流程和装置,各有利弊,其中使用最多的是AS和HPF脱硫、脱氰工艺。
与半水煤气相S含量高得多(一般在6 g/m3),而且HCN、萘、苯、焦油等比,焦炉煤气不但H2含量也高得多,脱硫循环液中的复盐也高出3~10倍,其净化难度更大。
焦炉煤气净化工艺流程分为传统的正压工艺流程和后来发展的全负压工艺流程两种。
正压工艺流程如下:净化焦炉煤气全负压工艺流程如下:净化焦炉煤气比较以上两种流程可以看出,所谓全负压工艺流程,就是将煤气鼓风机设置在洗苯装置后(也就是工艺流程的最后),使煤气净化各装置均在负压状态下工作。
湿法脱硫后,焦炉煤气中的硫化氢含量在20 mg/m3以下。
尽管在此过程中可脱去少量有机硫,但有机硫含量仍然较高,一般有机硫仍在200~300 mg/m3,高的可达500~600 mg/m3,且有机硫形态复杂;每立方米气体中焦油、萘、氰化氢、氨、苯等杂质的含量仍在几十甚至几百毫克。
这样的焦炉煤气若直接送入后续工段,将使有关工序的催化剂很快中毒失活。
因此,必须采用深度净化技术对焦炉煤气中的有机硫及其他杂质进行处理。
2.现有干法净化工艺存在的缺陷焦炉煤气中的HS相对容易脱除,但湿法脱硫后含量高达200~600 mg/m3、2硫的形态较为复杂的有机硫,十分难以脱除。
因此,焦炉煤气干法净化工艺中需要先将形态较为复杂的有机硫催化加氢转化为硫化氢,再通过固体吸收剂予以脱除。
在国内现有焦炉煤气的干法净化工艺中,对焦炉煤气中有机硫的加氢转化一般采用铁钼催化剂,在350~450 ℃下使有机硫加氢转化为硫化氢。
固体吸收剂可用便宜但硫容较低的锰矿,或价格较贵但硫容较高的氧化锌脱硫剂。
我国现有的焦炉煤气干法净化工艺,存在着以下缺陷:(1)净化度较差,对含有机硫为200~600 mg/m3的焦炉煤气,其有机硫总转化率在93%~95%左右,导致出口硫指标很难达到甲醇合成催化剂的要求。
对形态复杂的有机硫(硫醇、硫醚及噻吩等)的加氢转化能力更差。
(2)低温活性差,使用温度高达350~450 ℃,操作弹性小,易超温,易结炭。
(3)固体吸收剂硫容较低,用量较大。
(4)堆积密度高,抗压碎强度差,易粉化。
(5)没有完整的净化工艺,并且对焦炉煤气中其他杂质(不饱和烃,焦油,萘,氰化氢,氨,苯)脱除的研究几乎为空白。
浓度的焦炉煤气进行加氢净化时,将遇到以下几个问题:在对高CO 、CO2(1)如何避免如此高浓度的碳氧化物在加氢催化剂上发生甲烷化反应;(2)如何提高对形态复杂有机硫(如硫醇、硫醚及噻吩等)的加氢转化率;(3)如何避免CO 和烯烃的分解析炭;(4)如何避免羰基化合物的产生,使加氢过程安全地进行。
由焦炉煤气制合成气,转化、变换、合成等技术均已比较成熟,技术“瓶颈”是焦炉煤气的深度净化,特别是形态复杂的有机硫(硫醇、硫醚及噻吩等)和不饱和烃等其他杂质的深度净化。
而大多数合成催化剂对合成气中微量杂质的净化要求较高,如甲醇合成过程对杂质的要求比合成氨等更为苛刻,要求将原料气中硫化物脱除至总硫含量<0.1 ppm,而现有焦炉煤气净化工艺最多可将硫化物脱除至总硫含量<3~10 ppm,只能满足合成氨系统的净化要求。
3新型干法净化工艺的开发目前,国内已建成或在建的焦炉煤气制甲醇项目,所采用的干法净化工艺有传统的干法净化工艺和新型干法净化工艺。
3.1 新型干法净化工艺已经开发并正在工业化推广的新型干法净化工艺有:(1)两级加氢工艺,即“一级加氢+粗脱+二级加氢+精脱”。
(2)一级加氢工艺,即“一级加氢+粗吸收+精吸收”。
这两种净化工艺是西北化研究院在最近几年针对焦炉煤气综合利用的需求而开发的。
由于焦炉煤气中有机硫含量高达200~600 mg/m3,且硫的形态较为复杂,并含有不饱和烃等其他杂质,采用传统的干法净化工艺,其净化度难以满足焦炉煤气进一步化工利用的要求。
因此,必须将加氢催化剂、净化剂的开发与净化工艺开发相结合,形成集成化、针对性的工艺技术,才能解决不同来源焦炉煤气化工利用的净化需求。
3.2.适用于煤气、焦炉气加氢催化剂的开发西北化研究院在最近几年针对焦炉煤气综合利用的需求而开发了适用于煤气、焦炉气加氢催化剂,在催化剂的制备技术上,引入新的低温活性组分、抑制甲烷化付反应,采用溶胶-凝胶与有机扩孔法相结合制备载体,采用沉积-沉淀与浸渍相结合方法,并通过活性组分的预处理提高活性组分的分散度,使加氢转化催化剂在活性和稳定性等方面有大的提高,对焦炉煤气中硫形态复杂的硫醇、硫醚及噻吩等有机硫和烯烃等杂质具有深度加氢转化能力,同时具有较强的抑制甲烷化副反应含量0.5%的上限要求,可确能力;突破了传统加氢转化催化剂对原料中CO和CO2保适用于不同来源焦炉煤气的深度净化,特别是对焦炉煤气中形态复杂的硫醇、硫醚及噻吩等有机硫具有深度加氢转化能力。
开发的净化工艺,使焦炉煤气经加氢转化和吸收后,硫含量降至≤0.1 ppm,达到合成气及合成催化剂的净化度要求。
研究开发定型的催化剂为:JT-1;JT-8 。
3.2.1 JT-1型加氢催化剂JT-1型水煤气加氢催化剂,适用于以水煤气、合成气、焦炉气、油田气或天然气等为原料的合成氨厂、甲醇厂等原料气的加氢脱硫。
对合成气或水煤气中高达37%的CO或10%的CO气氛具有较强的抗结碳能力。
2物理性质外观:灰蓝色球状物规格:φ2~4 mm堆积密度: 0.60~0.8 kg/L抗压碎强度:≥50 N/粒磨耗:<3 %正常操作条件对水煤气或合成气、焦炉气压力:常压~5.0 Mpa温度: 200~450 ℃空速: 500~2000 h-13.2.2 JT-8型加氢催化剂JT-8型焦炉气加氢转化催化剂主要用于CO含量在10%以下,烯烃含量在5%左右焦炉气为原料的加氢转化脱除有机硫过程。
在空速500~1500h-1,反应温度300~420℃,压力为0.8~5.0MPa的条件下,对含有机硫为100~500mg/Nm3的焦炉气,有机硫转化率可达97%以上。
物化性能:外观:褐色球状物规格:φ3~φ5 mm堆积密度: 0.60-0.80kg/L抗压碎强度:≥50 N/粒磨耗:≤5 %正常操作条件:压力: 0.8~5.0 MPa温度: 250~450 ℃空速: 500~1500 h-13.3 新型干法净化工艺及催化剂性能评价3.3.1 加氢催化剂串精脱硫试验在温度350 ℃、压力2.0MPa、空速2000 h-1的条件下,对JT-1型加氢催化剂试验室放大样品串氧化锌精脱硫剂进行了原粒度活性评价试验。
试验用原料气为配制的模拟焦炉气,含有机硫化物100×10-6,其中噻吩约50×10-6。
反应后气体中未检出所配入的不饱和烃如乙炔、乙烯和丙烯等,总硫含量<0.1×10-6,评价结果及试验条件见表2。
由表2可见,JT-1型加氢催化剂对不饱和烃及有机硫化物具有较高的转化能力,可满足有机硫化物含量在100×10-6左右原料气的深度净化要求。