8-增强氮化硅涂层及其在晶体硅铸锭中得应用
多晶硅生产用氮化硅陶瓷材料_概述及解释说明

多晶硅生产用氮化硅陶瓷材料概述及解释说明1. 引言1.1 概述本文主要探讨多晶硅生产过程中使用的氮化硅陶瓷材料。
随着现代科技的快速发展,多晶硅作为一种重要的半导体材料,在光电子、电子信息和太阳能等领域具有广泛应用。
而在多晶硅的生产过程中,氮化硅陶瓷材料被广泛应用,以提高工艺效率和产品质量。
1.2 文章结构文章将按照以下结构展开论述。
首先,在“2. 多晶硅生产用氮化硅陶瓷材料的概述”部分,介绍多晶硅生产的重要性,并详细探讨氮化硅陶瓷材料在多晶硅生产中的应用及其特点与优势。
接着,在“3. 氮化硅陶瓷材料的制备方法和工艺流程”部分,将介绍传统和先进的氮化硅陶瓷制备方法,并简要概述工艺流程。
在“4. 多晶硅生产用氮化硅陶瓷材料的性能考察与分析”部分,将对该材料的物理性能、化学性能和结构性能进行综合考察和分析。
最后,在“5. 结论与展望”部分,将总结研究成果并展望氮化硅陶瓷材料在多晶硅生产中的未来发展前景以及实际应用前景。
1.3 目的通过本文的撰写,旨在全面介绍多晶硅生产过程中所使用的氮化硅陶瓷材料。
通过对其概述、制备方法、工艺流程以及性能考察与分析的探讨,可以更好地了解该材料在多晶硅生产中的重要作用和优势。
同时,通过对未来发展前景和实际应用前景的展望,为相关领域的科研人员提供新思路和参考,促进相关技术和产业的进一步发展。
2. 多晶硅生产用氮化硅陶瓷材料的概述2.1 多晶硅生产的重要性多晶硅是一种重要的半导体材料,广泛应用于太阳能电池、集成电路和光纤等领域。
在多晶硅的生产过程中,需要使用到一种高温耐腐蚀、高强度和高密度的陶瓷材料作为反应容器和保护层。
氮化硅陶瓷材料因其优异的物理性能以及良好的化学稳定性而被广泛选用。
2.2 氮化硅陶瓷材料在多晶硅生产中的应用氮化硅陶瓷材料在多晶硅生产中有多种应用。
首先,它可以作为反应容器,在高温条件下承受精确控制的化学反应过程。
其次,氮化硅陶瓷材料还可以作为衬底或者保护层,提供对多晶硅棒或片子的支撑和防护功能。
氮化硅在半导体的应用

氮化硅:半导体行业的未来之星氮化硅作为一种新型的半导体材料,正逐渐成为半导体行业的未来之星。
首先,氮化硅的硬度比硅高,耐高温、耐腐蚀性能好,可以在极端环境下运行。
其次,氮化硅的载流子迁移率比硅高,能够提高器件的开关速度和能耗效率。
此外,氮化硅还具有高频特性优异的特点,适用于5G通信、雷达和电视等高频应用领域。
目前,氮化硅已经广泛应用于LED芯片、功率器件和射频器件等领域。
尤其在功率器件领域,氮化硅的应用已经取代了传统的硅基功率器件,可以实现更高的功率密度和更低的开关损耗。
同时,在LED 芯片领域,氮化硅的高热传导性能能够提高芯片的发光效率和寿命。
氮化硅的应用前景广阔,但同时也面临着一些挑战。
首先,氮化硅的制造技术还需要不断提高,降低成本。
其次,氮化硅的晶体生长技术和器件制作工艺还需要不断完善。
尽管如此,随着技术的不断发展,氮化硅仍将成为半导体领域的主流材料之一,为行业带来更广阔的前景和发展。
氮化硅陶瓷件的表面涂层与改性研究

氮化硅陶瓷件的表面涂层与改性研究氮化硅陶瓷作为一种新型的高温结构材料,具有出色的力学性能、耐高温性能和耐磨损性能,因此在航空航天、汽车制造和化工等领域得到广泛应用。
然而,氮化硅陶瓷的一些缺点,如易吸湿、低抗裂性和较差的耐热震性能,限制了其进一步应用的发展。
为了克服氮化硅陶瓷的缺点,并提升其性能,研究人员开始关注表面涂层和改性技术。
表面涂层是通过在氮化硅陶瓷表面施加一层特殊涂层来改善其性能。
涂层可以增加氮化硅陶瓷的密封性、防腐蚀性和耐磨损性,同时减小摩擦系数和表面粗糙度。
目前,常用的表面涂层材料有硅酸盐、钛、氮化硅等。
这些涂层可通过化学气相沉积、物理气相沉积、溅射法等技术实现。
同时,改性技术也是改善氮化硅陶瓷性能的重要方法之一。
常用的改性技术包括导入添加剂、增强复合材料和应用纳米技术。
导入添加剂是将适量的其他材料添加到氮化硅陶瓷矩阵中,以改变其晶体结构和力学性能。
常用的添加剂有碳化硅、氮化铝和氧化物等。
增强复合材料是将氮化硅陶瓷与其他增强材料组合,以提高强度、韧性和耐磨性。
纳米技术的应用可以通过纳米颗粒、纳米涂层和纳米复合材料等方式,改善氮化硅陶瓷的性能。
对于氮化硅陶瓷的表面涂层研究,目前的研究主要集中在硅酸盐、钛和氮化硅涂层上。
硅酸盐涂层具有良好的粘附性、高温稳定性和耐磨损性,可提高氮化硅陶瓷的表面硬度和抗裂性能。
钛涂层具有较高的耐磨损性和良好的氧化防护性,可改善氮化硅陶瓷的高温稳定性和耐腐蚀性。
氮化硅涂层可增加氮化硅陶瓷的密封性和防腐蚀性能,同时降低其摩擦系数。
这些涂层的制备方法包括化学气相沉积、物理气相沉积和溅射法等。
对于氮化硅陶瓷的改性研究,导入添加剂是常用的方法之一。
碳化硅作为添加剂可提高氮化硅陶瓷的热震稳定性和抗裂性能。
氮化铝可提高氮化硅陶瓷的力学性能和高温耐磨性能。
氧化物添加剂可以在氮化硅陶瓷中形成稳定的氧化层,提高其耐腐蚀性能。
此外,纳米技术的应用也显示出潜力。
纳米颗粒的添加可以增加氮化硅陶瓷的密实性和硬度。
氮化硅材料在半导体制造中的应用研究

氮化硅材料在半导体制造中的应用研究随着现代科技的发展,半导体行业得到了快速发展,其应用范围越来越广泛。
其中,氮化硅材料在半导体制造中扮演了非常重要的角色。
本文将从氮化硅材料的特性、制备方法和应用等方面进行探讨,以期更好地理解氮化硅材料在半导体制造中的应用研究。
一、氮化硅材料的特性氮化硅具有优异的机械性能、光学性能和电学性能,这些优点使其成为一个非常重要的半导体材料。
首先,氮化硅具有非常高的硬度,这是因为氮化硅的化学结构主要是由氮和硅形成的,其二者之间有很强的键合。
另外,氮化硅具有非常高的熔点,能够在高温环境下工作。
此外,氮化硅具有非常强的耐热性和耐腐蚀性,这意味着它能够在非常恶劣的环境下使用。
除了上述优点之外,氮化硅还具有非常好的光学性能和电学性能。
在光学方面,氮化硅的透过率和反射率非常高,这使得它成为制造反射镜和光学器件的重要材料。
在电学方面,氮化硅有能隙,这使得它能够制造出高速的半导体器件。
此外,它的介电常数也非常高,这意味着它可以用于制造微波集成电路器件。
总体而言,氮化硅是一个功能非常强大的半导体材料,其特点主要包括高硬度、高熔点、耐热性、耐腐蚀性、高透过率、高反射率、有能隙、高介电常数等。
二、氮化硅材料的制备方法氮化硅材料的制备方法有多种,比较常见的有CVD法、PVD法和烧结法。
下面将对这几种方法进行简要介绍。
CVD法:CVD (chemical vapor deposition)是氮化硅制备的一种较常见的方法。
它需要在反应室内制造一定的气压,并通过化学反应的方式在衬底上得到氮化硅。
CVD法主要有低压CVD和等离子CVD两种方法。
相比之下,等离子CVD的产物质量更高,但相应的设备和成本也更高。
PVD法:PVD (physical vapor deposition)是通过加热和蒸发的方式使氮化硅原始物质沉积在衬底上。
与CVD法不同的是,PVD法不需要气体反应室,这意味着其处理的样品尺寸更大,但成本更高。
半导体材料与工艺之多晶硅锭定向凝固生长方法

最大优点是炉子结构简单。
液相
热源
坩埚
固相
液固界面
散热装置
HEM法示意图
保温框 热源 坩埚 液固界面
石墨块
隔热板 (防止不锈钢炉底过热) 炉型1示意图
定向凝固法
与铸锭浇注法相比,定向凝固法具有以下一些优点: 在同一个坩埚中进行熔炼与凝固成形,避免了熔体的
然而,其熔炼与结晶成形在不同的坩埚中进行,容易 造成熔体一次污染,同时受熔炼坩埚及翻转机械的限 制,炉产量较小,目前所生产多晶硅通常为等轴状, 由于晶界、亚晶界的不利影响,电池转换效率较低。
8.5.2 定向凝固法
定向凝固法通常指的是在同一个坩埚中熔炼,而后通 过控制熔体热流方向,以使坩埚中熔体达到一定的温 度梯度,从而进行定向凝固得到柱状晶的过程。
对于熔体热流方向的控制,主要有: 以一定的速度向上移动坩埚侧壁、向下移动坩埚底板
、在坩埚底板上通水强制冷却或是感应熔炼时将坩埚 连同熔体一起以一定的速度向下移出感应区域、从下 向上陆续降低感应线圈功率等。 实际应用的定向凝固基本方法卞要有:热交换法(HEM) 、Bridgman等
晶体生 长方向
布里曼法(Bridgeman Method) 这是一种经典的较早的定向凝固方法。 特点: 坩埚和热源在凝固开始时作相对位移,分液相区和凝固区,
液相区和凝固区用隔热板隔开。 液固界面交界处的温度梯度必须>0,即dT/dx>0,温度梯
度接近于常数。
长晶速度受工作台下移速度及冷却水流量控制,长晶 速度接近于常数,长晶速度可以调节。
硅锭高度主要受设备及坩埚高度限制。 生长速度约0.8-1.0mm/分。 缺点:炉子结构比热交换法复杂,坩埚需升降且下降
氮化硅应用分析报告

氮化硅应用分析报告氮化硅(Si3N4)是一种重要的功能陶瓷材料,具有优良的热、化学和机械性能,因此在多个领域得到广泛的应用。
本报告将对氮化硅的应用进行分析和评估。
首先,氮化硅在电子行业中具有重要的应用价值。
由于其具有优良的绝缘性能和高温稳定性,氮化硅被广泛应用于集成电路、电子元件和高温电子器件制造中。
其高温稳定性使其能够承受高达2000℃的温度,同时具有较低的热膨胀系数,使其成为在高温环境下可靠工作的理想选择。
其次,氮化硅在光电领域也具备广阔的应用前景。
氮化硅具有优异的光学性能,其透明度与玻璃相当,而其折射率较低,因此被广泛用于太阳能电池、光纤通信、LED照明等领域。
氮化硅作为一种透明材料,能够提供高效的光传输和较低的能量损耗,对光学设备的性能提升起到了重要作用。
此外,氮化硅还在化工工业中起到了重要作用。
由于其优良的耐酸碱性和热稳定性,氮化硅常被应用于高温、高压和腐蚀性环境下的化工设备制造。
例如,在石油化工工业中,氮化硅被广泛应用于催化剂的载体和反应器的内衬,能够提高催化活性和延长设备使用寿命。
除此之外,氮化硅在航空航天领域也具有广泛的应用。
氮化硅具有优异的机械性能,如高硬度、高强度和耐磨性,使其成为制造发动机零部件、导弹和航空器零件的理想材料。
通过使用氮化硅,可以提高零部件的耐磨性和抗疲劳性,从而提高航空航天设备的可靠性和使用寿命。
在医疗领域,氮化硅也有广泛的应用。
由于其生物惰性和高生物相容性,氮化硅被广泛应用于医疗器械和人工器官的制造中。
同时,氮化硅具有优异的抗菌和抑制炎症等特性,可用于制造抗菌和医药输送器等医疗器械。
综上所述,氮化硅作为一种功能陶瓷材料,在电子、光电、化工、航空航天和医疗领域具有广泛的应用前景。
随着科技的不断进步,氮化硅的应用领域还将进一步扩大。
然而,需要指出的是,氮化硅材料的制造和加工仍然面临一些挑战,包括高成本和技术难题。
因此,在未来的研究和应用中,需要进一步提高氮化硅的制备技术和降低制造成本,以促进其在各个领域的应用综上所述,氮化硅作为一种功能陶瓷材料,在电子、光电、化工、航空航天和医疗领域具有广泛的应用前景。
晶体硅太阳电池中的氮化硅的刻蚀方法及应用
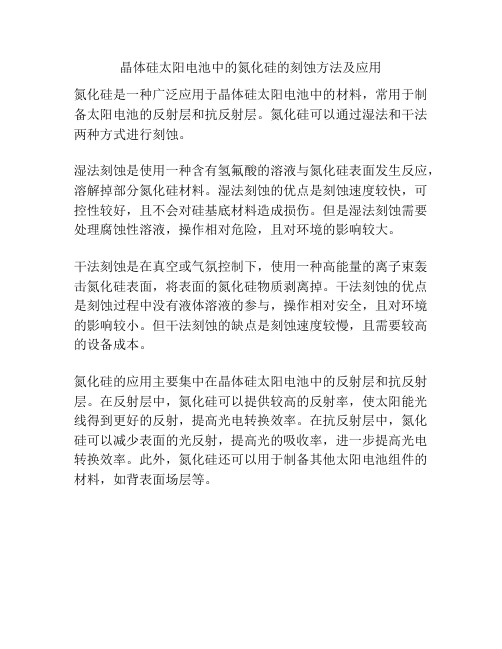
晶体硅太阳电池中的氮化硅的刻蚀方法及应用
氮化硅是一种广泛应用于晶体硅太阳电池中的材料,常用于制备太阳电池的反射层和抗反射层。
氮化硅可以通过湿法和干法两种方式进行刻蚀。
湿法刻蚀是使用一种含有氢氟酸的溶液与氮化硅表面发生反应,溶解掉部分氮化硅材料。
湿法刻蚀的优点是刻蚀速度较快,可控性较好,且不会对硅基底材料造成损伤。
但是湿法刻蚀需要处理腐蚀性溶液,操作相对危险,且对环境的影响较大。
干法刻蚀是在真空或气氛控制下,使用一种高能量的离子束轰击氮化硅表面,将表面的氮化硅物质剥离掉。
干法刻蚀的优点是刻蚀过程中没有液体溶液的参与,操作相对安全,且对环境的影响较小。
但干法刻蚀的缺点是刻蚀速度较慢,且需要较高的设备成本。
氮化硅的应用主要集中在晶体硅太阳电池中的反射层和抗反射层。
在反射层中,氮化硅可以提供较高的反射率,使太阳能光线得到更好的反射,提高光电转换效率。
在抗反射层中,氮化硅可以减少表面的光反射,提高光的吸收率,进一步提高光电转换效率。
此外,氮化硅还可以用于制备其他太阳电池组件的材料,如背表面场层等。
管式PECVD_法沉积的SiyNx
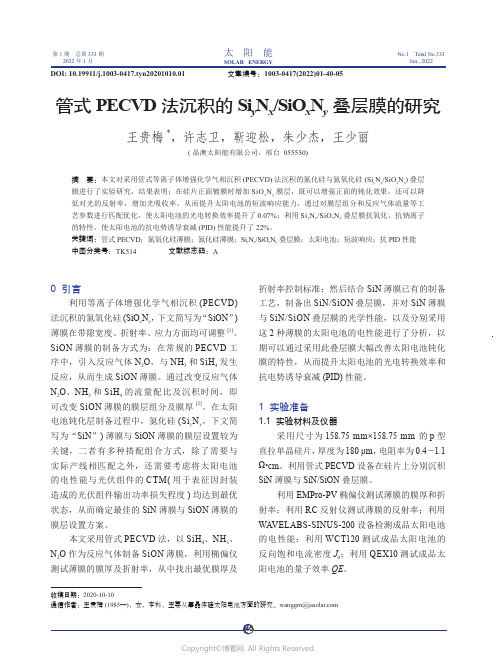
太 阳 能第1期 总第333期2022年1月No.1 Total No.333Jan., 2022SOLAR ENERGY0 引言利用等离子体增强化学气相沉积(PECVD)法沉积的氮氧化硅(SiO x N y,下文简写为“SiON”)薄膜在带隙宽度、折射率、应力方面均可调整[1]。
SiON薄膜的制备方式为:在常规的PECVD工序中,引入反应气体N2O,与NH3和SiH4发生反应,从而生成SiON薄膜。
通过改变反应气体N2O、NH3和SiH4的流量配比及沉积时间,即可改变SiON薄膜的膜层组分及膜厚[2]。
在太阳电池钝化层制备过程中,氮化硅(Si y N x,下文简写为“SiN”)薄膜与SiON薄膜的膜层设置较为关键,二者有多种搭配组合方式,除了需要与实际产线相匹配之外,还需要考虑将太阳电池的电性能与光伏组件的CTM(用于表征因封装造成的光伏组件输出功率损失程度)均达到最优状态,从而确定最佳的SiN薄膜与SiON薄膜的膜层设置方案。
本文采用管式PECVD法,以SiH4、NH3、N2O作为反应气体制备SiON薄膜,利用椭偏仪测试薄膜的膜厚及折射率,从中找出最优膜厚及折射率控制标准;然后结合SiN薄膜已有的制备工艺,制备出SiN/SiON叠层膜,并对SiN薄膜与SiN/SiON叠层膜的光学性能,以及分别采用这2种薄膜的太阳电池的电性能进行了分析,以期可以通过采用此叠层膜大幅改善太阳电池钝化膜的特性,从而提升太阳电池的光电转换效率和抗电势诱导衰减(PID)性能。
1 实验准备1.1 实验材料及仪器采用尺寸为158.75 mm×158.75 mm 的p型直拉单晶硅片,厚度为180 μm,电阻率为0.4~1.1 Ω•cm。
利用管式PECVD设备在硅片上分别沉积SiN薄膜与SiN/SiON叠层膜。
利用EMPro-PV椭偏仪测试薄膜的膜厚和折射率;利用RC反射仪测试薄膜的反射率;利用WAVELABS-SINUS-200设备检测成品太阳电池的电性能;利用WCT120测试成品太阳电池的反向饱和电流密度J0;利用QEX10测试成品太阳电池的量子效率QE。
氮化硅应用及专利

氮化硅应用及专利氮化硅是一种具有广泛应用前景的半导体材料,具有优异的电学、光学和热学性质,被广泛应用于电子、光电和高温器件领域。
以下将详细介绍氮化硅的应用领域以及相关的专利。
1. 电子器件领域:氮化硅具有优异的电学特性,例如高电子迁移率、较高的电击穿电场强度和低漏电流密度等,因此在电子器件领域有广泛应用。
其中最重要的应用之一是在功率电子器件领域,如大功率开关、逆变器和整流器等,其高击穿电压和高电流密度使其成为高效率、高频率和高电压的理想材料。
此外,氮化硅还广泛应用于高频微波器件、光纤通信器件、高速集成电路和传感器等。
2. 光电器件领域:氮化硅具有广谱透明性,具有在紫外(UV)至红外(IR)波段的宽光吸收范围,并且具有较高的光学质量,使其成为光电器件领域的理想材料。
例如,氮化硅可以用于制备高性能的光电二极管、光电探测器和太阳能电池等。
此外,由于氮化硅具有热稳定性和较大的带隙宽度,可以在高温环境下使用,因此特别适用于需在高温环境下工作的光学器件。
3. 高温器件领域:氮化硅具有出色的热学性能,包括较高的热导率和热稳定性,使其在高温器件领域具有重要应用价值。
例如,氮化硅可用于制备高温传感器、高温电子器件和高温电子封装材料等。
在高温环境下,传统的硅基材料往往无法满足需求,而氮化硅的特性使其成为一种理想的高温材料。
除了以上提到的应用领域,氮化硅还具有其他一些潜在的应用,例如压电器件、微机械系统、生物传感器等。
随着对氮化硅性能的深入研究,其应用领域还将不断扩展。
在氮化硅领域,相关的专利研究和发明也正在不断进行。
以下是一些氮化硅相关的专利研究方向和技术创新:1. 氮化硅发光二极管技术:该技术利用氮化硅材料的优良光学性质,通过改变材料的掺杂方式和结构,研究发展氮化硅纳米结构发光二极管。
这种发光二极管具有高效率、低功耗和长寿命等优点,有望应用于照明、显示和生物传感器等领域。
2. 氮化硅太阳能电池技术:该技术通过研究氮化硅材料的能带结构和光学性质,设计和制备高效率的氮化硅太阳能电池。
铸造多晶硅锭常见异常问题浅析_王建立

高新技术产业发展ECHNOLOGY DEVELOPMENTT铸造多晶硅锭常见异常问题浅析王建立,张呈沛,张华利,颜颉颃(晶海洋半导体材料(东海)有限公司,江苏东海 222300)摘 要 介绍多晶硅锭在铸造生产过程中遇到的各类异常问题,分析产生各种异常的原因。
关键词 多晶硅;铸造;异常中图分类号:TM911 文献标识码:A 文章编号:1671-7597(2014)06-0014-02光伏太阳能行业作为一种绿色无污染的新能源产业,近年来发展迅猛。
通过定向凝固方法生产的铸造多晶硅晶体(硅锭),因其低廉的成本和较高的产出,已经成为光伏电池制造行业重要的基体材料。
多晶硅定向凝固系统(Directional Solidification System),简称为DS炉,是生产硅锭的主要设备,从2005年左右开始,经过不断升级,多晶硅锭的发展经历了G4、G5到G6的历程,投料重量也分别从240 kg、450 kg发展到800 kg,2013年,有厂家推出了G7铸锭炉和投料量达1200 kg的硅锭。
不论哪一代的多晶硅锭,其品质受热场设计和工艺影响重大,还会受原料、辅料、操作等诸多因素影响,硅锭检测也会各种异常或缺陷问题。
本文介绍了多晶硅锭生产过程中遇到的各种异常情况,分析这些异常产生的原因,提出了一些相关的预防及改善措施。
1 硅液溢流多晶硅铸锭包括加热、熔化、长晶、退火、冷却五个工艺步骤,其中硅料在熔化过程中或熔化完以后可能会因其盛放的石英陶瓷坩埚破裂,从坩埚内流出,常简称硅液溢流。
高温硅液体流到溢流丝上面,使溢流丝熔断,触发溢流报警,系统进入紧急冷却。
一般溢流发生在熔化阶段及长晶阶段,特别是在熔化后期及长晶初期发生的溢流最为常见。
溢流以后不但意味着该炉次没有硅锭产出,而且轻则损失几公斤硅料,重则造成热场部件的重大损失甚至安全事故,因此溢流是多晶硅铸造最严重也是较为常见的生产异常。
造成硅液溢流的可能原因大概有以下几点。
氮化硅的作用

氮化硅的作用嘿,朋友们!今天咱来聊聊氮化硅这玩意儿,可别小瞧它,它的作用那可真是杠杠的!氮化硅就像是一个默默无闻的超级英雄,在很多领域都有着出色的表现。
你想想看,陶瓷,这大家都熟悉吧,氮化硅可是陶瓷中的佼佼者呢!它能让陶瓷变得更加坚固耐用,就好比给陶瓷穿上了一层坚不可摧的铠甲。
咱家里用的那些陶瓷餐具啥的,如果加入了氮化硅,那可就不容易摔坏啦,这得省多少买新餐具的钱呀!再说说在工业领域,氮化硅简直就是个宝贝。
它能在高温环境下依然稳稳当当的工作,这可不是一般材料能做到的哟!就好像一个不怕热的勇士,不管多高的温度都能坚守岗位。
一些制造工厂里的那些重要设备,有了氮化硅的加持,就能更好地运行,生产效率也能大大提高呢!还有啊,在一些高科技产品中,氮化硅也有着重要的地位。
它就像是一个智慧的小精灵,为这些产品注入神奇的力量。
比如一些精密的电子元件,氮化硅能让它们更稳定地工作,减少出错的几率。
这不就像给这些元件找了个可靠的保镖嘛!氮化硅在航空航天领域也有它的一席之地呢!在那广阔的天空中,对材料的要求可是非常高的呀。
氮化硅能承受住各种极端的条件,为飞行器的安全保驾护航。
难道这不神奇吗?它就像是给飞行器装上了一双有力的翅膀,带着我们飞向更遥远的地方。
你说,氮化硅是不是很厉害?它在我们生活中的各个角落都发挥着重要的作用,虽然我们可能平时不太注意到它,但它却一直在默默地奉献着。
如果没有氮化硅,我们的生活说不定会变得没那么方便和精彩呢!所以呀,我们真应该好好感谢这个神奇的氮化硅,不是吗?它真的就像是一个低调的幕后英雄,虽然不被大众所熟知,但却为我们的生活带来了实实在在的好处。
总之,氮化硅的作用可太多啦,说也说不完。
它在不同的领域都绽放着属于自己的光芒,让我们的生活变得更加美好。
我们真的应该好好珍惜这个了不起的氮化硅呀!。
- 1、下载文档前请自行甄别文档内容的完整性,平台不提供额外的编辑、内容补充、找答案等附加服务。
- 2、"仅部分预览"的文档,不可在线预览部分如存在完整性等问题,可反馈申请退款(可完整预览的文档不适用该条件!)。
- 3、如文档侵犯您的权益,请联系客服反馈,我们会尽快为您处理(人工客服工作时间:9:00-18:30)。
第12届中国光伏大会暨国际光伏展览会论文增强氮化硅涂层及其在晶体硅铸锭中的应用尹长浩1,钟根香1,黄新明1,21.东海晶澳太阳能科技有限公司;2. 南京工业大学材料科学与工程学院摘要:本文采用改进溶胶凝胶法(sol-gel)制备增强氮化硅涂层(SG涂层),并将其应用于准单晶硅铸锭及普通多晶硅铸锭。
实验结果显示:1)采用溶胶凝胶法制备的氮化硅涂层,早期强度较常规喷涂法制备的涂层有显著的提高;2)氮化硅涂层中有机物的添加会降低硅熔体与涂层间的非浸润性,涂层中有机物在加热过程中的碳化可能是其主要原因。
铸锭应用结果显示:完整的SG工艺制备的氮化硅涂层可以满足准单晶硅铸锭脱模需要,同时,免烧结SG涂层可直接应用于普通多晶硅铸锭生产。
关键词:氮化硅涂层;溶胶凝胶法;准单晶硅;多晶硅Reinforced Si3N4 coatings and its application in silicon demouldingChanghao Yin1, Genxiang Zhong1, Xinming Huang1,2,1)Donghai JA Solar Technology Co. Ltd.2)College of Materials Sci. & Engineering, Nanjing Univ. Tech.Abstract: In this paper, the silicon nitride coatings used in silicon casting were prepared by improved sol-gel method (SG), which had been used in quasi-mono crystalline silicon casting and multicrystalline silicon casting successfully. The experiments showed significant reinforcement in hardness of the coatings prepared by SG method compared with the coatings prepared by spraying-sintering method (SS). The remnants of the sol added in the coatings increased the wettability in the interface between silicon melt and coating, and carbonization of the organic contents in the coating during heating process was probably responsible for the result. The silicon casting applications showed that the coatings prepared by SG could be used in quasi-mono crystalline silicon casting, and the coatings prepared by SG without sintering could be used in multicrystalline silicon casting as well.Keywords:silicon nitride coating, sol-gel, quasi-mono silicon, multi-crystalline silicon1.引言多晶硅铸锭是目前光伏晶体硅主要的生产方法:将多晶硅料置于石英坩埚内通过定向凝固铸造而成。
通过改良热场结构并调整相应的长晶工艺可获得电池转化效率更高的准单晶硅锭。
无论常规多晶铸锭还是准单晶铸锭,坩埚内壁的氮化硅涂层都是必不可少的脱模剂。
该脱模剂具备两大功能:一、在铸锭过程中,阻止坩埚中杂质向硅料中扩散;二、在铸锭完成后,确保硅锭与坩埚的顺利分离。
常规多晶铸锭生产中通常采用先喷涂后烧结的方法在坩埚内壁上制备氮化硅涂层,称为喷涂烧结法(spraying-sintering method, SS);其改进方法是在氮化硅浆料中添加硅溶胶等具有粘合能力的物质,免去烧结过程,因而这种涂层制备方法称为免烧结法(Spraying Method, SM)。
对于常规多晶铸锭而言,SS涂层及SM涂层基本可以满足生产需求。
但对于长晶条件更为苛刻的准单晶铸锭而言,上述涂层由于强度较低等因素易导致较高的粘埚率,难以直接使用。
如何提高氮化硅涂层的强度成为重要课题。
目前氮化硅涂层的作用机理已得到广泛研究。
普遍认为氮化硅涂层与硅熔体之间的浸润特性与粘埚现象关系密切。
而氮化硅涂层与硅熔体之间的浸润性受众多因素的影响,包括影响三相界面接触角(γS–L, γS–G, γL–G)的诸多因素[1],如:氮化硅涂层的完整性、氮化硅涂层的氧化程度[2]以及氮化硅涂层与坩埚基体、硅熔体所处的氧分压[3,4]等。
必须强调的是,纯净的氮化硅与硅熔体之间是相互浸润的[4-6],因而无法直接制作涂层。
大量研究表明[7-10],氮化硅涂层中氧的存在(氮化硅颗粒表面的氧化层、自坩埚中氧的扩散)及其在界面处的释放很可能是维持氮化硅涂层与硅熔体非浸润性的主要因素。
因而调节涂层中氧含量及其释放速率是控制涂层性能的重要手段。
本文主要通过调节氮化硅涂层中的氧化物含量、烧结条件等因素控制涂层中的氧含量,另外,鉴于喷涂方法制备的涂层质地疏松,引入改进溶胶凝胶法(sol-gel,SG)用于制备增强氮化硅涂层,并就涂层中残余有机物引入的碳素对硅熔体与氮化硅涂层界面间浸润性的影响进行了探讨。
2.实验本文分别采用SS法、SM法及SG法在坩埚碎片制备实验涂层样品,对比不同制备方法中氧化物添加量及是否烧结处理对涂层性能的影响,采用划痕测试法检验烧结前后涂层强度的变化,采用小尺度铸锭观察涂层与硅熔体间的浸润性,并在实际铸锭生产中验证涂层的脱模性能。
3.实验结果与分析3.1 早期强度表1为不同制备工艺下制备的涂层的铅笔硬度测试结果。
其中所有样品在烧结前表1涂层样品参数。
Table 1 Parameters of the coating samples.编号成膜方法氧含量烧结前烧结后SS spray-sinter <3% <4B 2B-HB SM spray <1% 3B-2B -SG1sol-gel 5% 3B-2B HB-2H SG2sol-gel 10% 2B-HB HB-2H SG3sol-gel 15% 2B-HB >4H SG4sol-gel 20% 2B-HB >4H均在空气气氛下80℃晾干2h,以去除多余的游离水。
从表中可以看出,常规喷涂涂层由于质地疏松,其烧结前强度最低,而SG 法的样品由于有机交联结构的加强,其烧结前强度有显著的提高,这为氮化硅涂层免烧结工艺提供极好的基础。
3.2 非浸润性图1为仅经过80℃2h晾干去除水分而未经过烧结处理涂层样品SS(A)和SG1(B)在空气气氛下的热重分析曲线。
当烧图1经80℃2h晾干除水分而未经过烧结处理涂层样品SS(A)和SG1(B)热重曲线,其中曲线C为温度变化。
Fig. 1 TG-analysis of coating samples (air drying: 80℃,2h) sintered at 1070℃in air. A:SS, B: SG1and C: temperature curve.结温度达到500℃时,SG法样品快速失重约9%左右,而常规喷涂样品失重1%左右,在趋势上与Ingvild Brynjulfsen等[11]报道的结果相一致。
这是由于样品中残余少量的水分及其它杂质的挥发所致。
由于SG法在涂层中添加了有机物,其失重比例远高于不添加有机物的常规喷涂法。
随着烧结温度的增加及烧结时间的延续样品失重趋于减缓,这说明500℃有氧烧结即可有效去除SG法添加的有机粘合剂。
而当烧结温度达970℃后样品即出现增重。
根据Brynjulfsen[11]等的研究,这一增重很可能是烧结过程中氮化硅颗粒氧化所致。
在氧化过程中,很有可能发生如下反应并生成相应氧氮化硅相(Si2N2O)。
其反应式为:2Si3N4(s)+3O2(g)→3Si2N2O(s)+N2(g) (1)根据文献报道[2,4,6,8],基本可以确认的是,无论氮化硅涂层中氧以何种形式存在,氧在氮化硅涂层与硅熔体间的浸润性方面起到至关重要的作用。
其作用机理可以概括为如下反应:Si(l)+SiO2(s)→2SiO(g)(2)上述反应中,可以理解为气体SiO的产生,起到了阻碍硅熔体与涂层进一步接触的作用,但其前提是SiO不易溶解于硅熔体,并且SiO能够形成完美的气膜阻挡在硅熔体和氮化硅颗粒之间。
根据B. Drevet等[2]的研究结果,含氧氮化硅涂层与硅熔体相接触瞬间硅熔体与氮化硅涂层之间表现非浸润特性,但非浸润特性在很短的时间(不超过100s)内消失,具体表现为接触角从稍大于90°快速减小并稳定在40-50°。
这可以理解为在氮化硅涂层与硅熔体接触瞬间,氮化硅涂层表面氧快速消耗,导致浸润性的变化。
3.3 碳素的影响选取SG法和SS法制作涂层的坩埚角进行硅料的熔化及结晶实验,结果如图2所示。
从图中可以看出SG法制备的涂层在铸造后涂层暴露在硅熔体外的表面形成一层黑色的硬壳,这是R. Einhaus 等[12]研究者中所提到的硅次级浸润层。
虽然样品较小而铸造环境中碳含量较高,硅锭表面形成不光泽的杂质层,但与之相对比,不添加有机物的喷涂涂层,在同样的气氛下没有出现硅次级浸润层现象,这恰恰证明气氛中的碳含量显然不是导致硅次级浸润层的主要原因。
实验证实,对于添加有机物的氮化硅涂层,即便在空气(氧化性)气氛下长时间图2 坩埚角涂层铸锭实验。
Fig. 2 Coatings in casting test with crucible corners. (1070℃,4h)烧结也难以完全去除涂层中碳素残余。
而根据热力学数据[13]可以计算出在高温低压条件下,下述反应具有较强反应倾向:Si3N4(s)+3C(s)→3SiC(s)+2N2(g) (3)其中C(s)为在氮化硅涂层中的残余碳,SiC(s)为反应生成的碳化硅。
实验证实通常情况下碳化硅与硅熔体具有较强的相互浸润特性,这可能是碳素残余导致氮化硅涂层与硅熔体浸润性改变的主要原因。
值得注意的是,尽管由于有机物的添加降低了氮化硅涂层与硅熔体之间的非浸润性,但在冷却后的脱模过程中却未发现SG 法的氮化硅涂层与硅锭发生任何粘连。