单元化线体改善方法①中文
改善八步法及课题总结简述课件
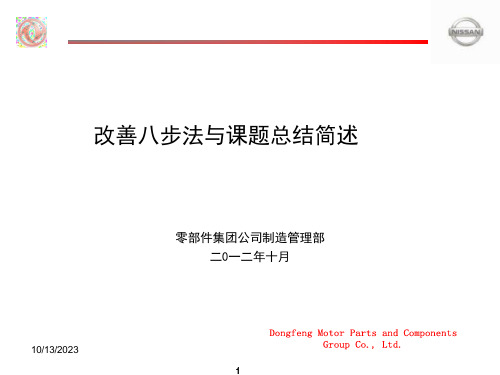
10/13/2023
零部件集团公司制造管理部 二0一二年十月
1
编写说明:
1、为提高改善八步法运用和课题成果总结的水平,进一步促进QCD改善活 动的持续发展进步,特编写此资料,供参考借鉴。
2、本资料依据 “PDCA”管理循环和“改善活动八步法”等法则编
制,是各类改善课题必须开展的步骤,也是对改善活动过程如何展示进行 说明。 3、受认识和水平所限,本资料内容尚有许多不到之处,敬请包涵,欢迎 指正。
10/13/2023 18
步骤四:解析
2、追求原因型课题解析:
1)要因分析 *用掌握的现状(不良现象),以获得的不良程度为特性进行要因分析(影响主导因素的主要原因),特性
用比较具体的事来表达。 *要因分析的方法:对不良现象的构成进行分层,分析手法可采用因果图,按照构成全面罗列所有可能的原
因(是否属于要因需要验证),重要的要因要打上标识。
★ 明确课题的领域和类别,做到特点鲜明。 有的课题可从多个角度进行整理,要考虑改善主要运用的是哪类方法,取得最 主要的效果属于哪一类,再从相应角度进行课题策划和成果总结。
每个课题完成之后,都会形成课题报告。接下来的篇幅,将以课题报告编 制要领说明为切入点,来说明改善八步法实施过程中各环节的思路和关注 点,以及每个环节总结需要注意的方面。
10/13/2023 8
课题名称设定要求
课题名称的设定要简洁、明确,一目了然的针对所要解决的问 题,不可抽象。原则上按以下方式设定:
××
○○○ 的 △△
要解决什么---指质量、效率 成本等方面的管理特性。
所解决问题的对象---指产品、 工序、过程、作业的名称。
如何办---指提高还是降低,增大还是减少。
IE工业工程七大手法的改善方案

IE七大手法之四 — 五五法
1.手法名称: 5 * 5W 1H法;又称5 * 5何法;又称质疑创意法;简称五五 法。
2.目的: 学习本手法的目的在于:
熟悉有系统的质问的技巧,以协助我们发掘 出问题的真正根源所在以及可能的创造改 善途经。
3.1 基本观念:
头脑就像降落伞,○○○只有在开放的情 況下才工作○○○。
工作改善最大的阻碍并不在于技术不足, 而是在于一个人的想法~当他觉得是以最 好的方法在工作着,并且以为满足。
当你认为工作已无法改善了,那就代表你 已落伍了,虽然你是专家,拥有高深的学识.
一个虽然沒有多大学识的人,只要他认为 工作仍有改善的可能,那么他就比您更适 合这工作。
3.2 何处最需要改善 您的時間非常宝贵,应妥善运用;挑最重要的事情
手掌的张 度
三
肘
+前臂
前臂的张 度
四
五
肩
身躯
+上臂
+肩
上臂的张 上臂+身躯
度
弯曲
速度
1
2
3
4
5
体力消耗 最少
少
中
多
最多
动作力量 最弱
弱
中
强
最强
疲劳度
最小
小
中
大
时间(以 25mm为准)
0.0016分
0.0017分
0.0018分
0.0026分
最大
原則5: 物体的“动量”尽可能利用;但如 需用肌力制止时,则应将减至最小度。
1.手法名称 又称动作改善法,简称为“动改法”,是: * 省力动作原則 * 省时动作原則 * 动作舒适原則 * 动作简化原則 此原則以最少的劳力到达最大的工作效果,其原为吉而博斯
标准作业和线平衡改善

等待加走动
产品型号:0110288
生产节拍:
作业人数:2人
时间进度条
操作 步行 等待 总时间 20
40
60
80
100
120
140
160
180
200
220
240
260
280
300
320
340
360
380
400
420
440
460
480
500
520
48################################################################################################################################
21
21
3 24
6
30
2
32
6
38
7
45
5
50
8
58
3
61
4
65
6
71
7
78
30
108
20
128
22
150
28
178
129 307
34 341
103 444
37 481
7
488
9
9
15
24
6
30
10
40
5 45
4
49
8
57
3
60
4
64
6
70
7
77
46
123
2
125
2
127
4
131
线束工程改善方案怎么写

线束工程改善方案怎么写一、引言线束工程是指将汽车各个功能部件之间的电气线路和信号线路捆绑在一起,形成一根完整的线束,以满足汽车各个功能部件之间的电气连接需求。
线束工程是汽车制造过程中非常重要的一环,其质量的好坏直接影响到汽车整车的性能和可靠性。
因此,线束工程的质量控制是汽车制造企业必须重视的工作。
目前,随着汽车制造工艺、技术的发展以及市场对汽车质量和安全性要求的提高,线束工程也面临着更高的要求。
如何提高线束工程的质量和效率,已成为汽车制造企业亟待解决的问题。
本文将结合目前汽车制造企业在线束工程方面存在的问题,提出一些具体的改善方案,以期为汽车制造企业解决线束工程质量问题提供一些参考。
二、线束工程存在的问题1. 生产效率低下:目前线束工程的制造方式大多仍采用人工手工焊接和组装,导致工艺复杂、生产效率低下。
尤其在汽车行业重工业的发展中,线束工程的手工组装往往成为生产工艺流程中的一个瓶颈,严重影响生产效率。
2. 线束质量难以保证:线束工程需要运用大量的电气连接技术和线缆制造技术,如焊接、搪针、喷锡等,这些工艺技术要求严格,一旦出现问题就可能导致线束的质量不可控,从而影响汽车整车性能和安全性。
3. 成本压力大:随着汽车市场的竞争加剧,汽车制造企业普遍面临着成本压力增大的问题,线束工程的制造成本也成为了汽车制造企业的一大负担。
4. 环保和可持续发展:如何在线束工程制造过程中降低能源消耗和减少排放对环境的影响,是汽车制造企业亟待解决的问题。
以上这些问题使得线束工程成为汽车制造企业亟待解决的一项技术难题。
接下来,本文将从技术改善、流程优化、管理控制等方面,提出对线束工程进行改善的一些具体方案。
三、技术改善方案1. 自动化生产技术在线束工程中的应用:随着科技的发展,自动化生产技术在汽车制造行业中的应用越来越广泛,线束工程的自动化生产技术也逐渐成为了汽车制造企业的新选择。
自动化生产技术可以大大提高线束工程的生产效率,如采用自动化焊接设备、自动化线束组装设备等,能够有效地降低线束工程的生产成本,提高生产效率。
8d8个步骤解决问题改善手法

對小組的效益進行溝通
34
上述各項步驟,不一定必須完全依顺序進行,各 步驟的順序可因個別問題而異.
例如:某一問題于提出報告,並組成小組之時, 負責之領班或作業員可能早已采取臨時措施。
35
8D—问题改善手法
案例说明
36
0. 问题的提出
99年11月4日客户—浙江某机械制造 公司投诉,在其包装车间对“ALT-5 检测器”进行包装时,使用公司的MHT 机用膜时一拉就断裂, 并发现使用的 机用膜端口破裂。
6
ISO 的定義-3
correction
action to eliminate a detected nonconformity (3.6.2)
NOTE 1 A correction can be made in conjunction with a corrective action (3.6.5).
确认临时措施采取后是否 完全有效
←執行後的確認
24
确定并验证根本原因
对问題之何以發生,指出其一切可能形成 的原因.再分別针对每一可能原因予以測 試,以验证真正之根因.然后找出消除该项 根本原因的各项纠正措施。
25
评审所有的 过程,考虑所 有的变异来源
分析最有可能的根 本原因
采用适当的统计 方法对资料进行
29
针对选定的糾正措施
修正衡量指標以及 對現行的質量控制 模式進行工程變更
利用三十天的數據 (如SPC或推移圖)
來進行確認
建立糾正措施 執行計劃
審核改版的 設計FMEA
識別設計或生產過程 中的主要、安全、
關鍵特性
經过推移圖和初次的 測量來停止臨時措施
小学美术单元化教学方法

小学美术单元化教学方法以往美术课程教学中,教师关注教材内容,依托教材进行教学,因此教学相对刻板,较为被动。
在实际教学操作中,教师发现,对美术单元之间主题教学连贯性较差,教学内容之间知识点跳跃性较大,整个教学过程过于凌乱,教师的教学活动不能提高学生学习积极性,甚至对学生学习积极性产生严重打击。
因此教师需要关注单元整合教学形式,促使教师教学“得心应手”,学生学习“学有所得”。
一、小学美术单元化教学概述单元化教学模式是莫里逊倡导的教学模式,主要是指将教学活动与教材相互结合,通过划分的单元内容进行创新教学。
在单元化教学中,需要围绕单元意识,关注教师教学主体、学生学习主体,实现教师与学生之间的互动学习。
同时在单元化教学模式之下,学生接触的美术知识不再是某一节美术课程,而是整个单元的美术课程内容。
教师将单元课程通过系统化的形式呈现在学生眼前,同时在美术课程中形成情境、活动与任务等,并且会呈现多元化的教学特点。
教师也需要在多角度构建单元化教学,充分利用单元化教学有效组织教学过程。
在明确单元化教学的主题内容之后,教师需要收集相关的教学资源,分析教材的内容,同时进行教学资源的整合,最终将单元化教学在课堂教学中呈现。
但是因为现有教学经验不足,笔者发现个别美术教师在单元化教学落实期间,教学效果不好,同时浪费大量的教学时间。
因此,需要将单元化教学进行深度剖析,并结合班级实际学习情况等多个方面进行多角度的思考。
以此为学生提供理想的单元化教学,促使美术课堂教学充满更多的趣味。
二、小学美术单元化教学的作用(一)有利于陶冶学生情操在新课程背景之下,教师关注知识教育的同时还关注素质教育的落实。
因此小学美术课程需要进行素质教育。
教师在实践教学活动中,需要开展美术育人活动,促使学生在单元美术学习过程中感受艺术的特性,强化自身创造性思维发展,提升艺术素养,强化实践学习能力。
例如,在“漫步建筑世界”这一单元中,教师需要寻找各个主题之间的艺术关联性,整理碎片化的知识点,提升学生整体性学习能力,以此为学生综合性发展做铺垫。
精益生产术语
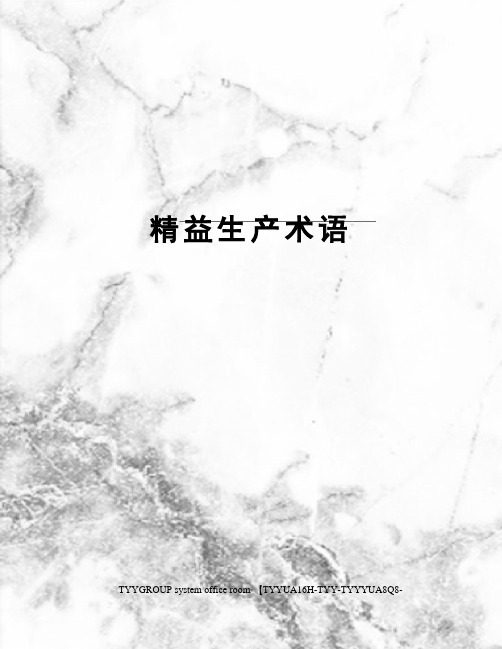
精益生产术语TYYGROUP system office room 【TYYUA16H-TYY-TYYYUA8Q8-精益生产术语为了便于大家进一步学习精益生产,并作为实践的指南,特选用与精益生产有关的术语66条,并加以解释.1.精益生产(Lean Production)含义:精益生产起源于日本的丰田生产方式,美国学者对这种生产方式的理论上加以概括与总结,命名为“Lean Production”,中文翻译为“精益生产”。
“ Lean”的意思是没有脂肪。
这种生产哲学将库存比喻为人体的脂肪,认为动作良好的企业应该是没有库存的,因此命名为“Lean Production”。
2.附加价值(Value Added)含义:附加价值是企业本身创造出的价值。
附加价值愈高则获得能力愈强。
附加价值=销售额-(材料费+委外加工费+折旧费+工资)。
附加价值率的计算方式为:(附加价值/营业收入)*100%。
比率越高则贡献越大,显示获利能力愈强,精益企业应达到30%以上。
3.7种浪费(Seven Wastes)含义:精益生产方式将所有浪费归纳成七种——(1)等待的浪费;(2)搬运的浪费;(3)不良品的浪费;(4)动作的浪费;(5)加工的浪费;(6)库存的浪费;(7)制造过多(早)的浪费。
4.价值流图(Value Stream Mapping)含义:所谓价值流,是指一个产品/服务在流程中所必须要经过的一组特定活动(包括增值活动和非增值活动).识别价值流,是在这组特定活动中识别浪费和寻找改善机会.识别价值流的常用工具,就是价值流图.价值流图把产品或者服务所涉及的所有物流与信息流相关内容用目视图表的方法绘制出来,作为随后即将展开的精益改造的依据.5.丰田生产方式(Toyota Production System)含义:一般认为,丰田生产方式的支柱有两个,一是"自动化",二是“及时生产”。
根据大野耐一的描述,丰田生产方式的现场管理,有两个特点,一是流水化制造,二是拉动式计划方法,也就是看板方式。
精益生产快速改善秘诀
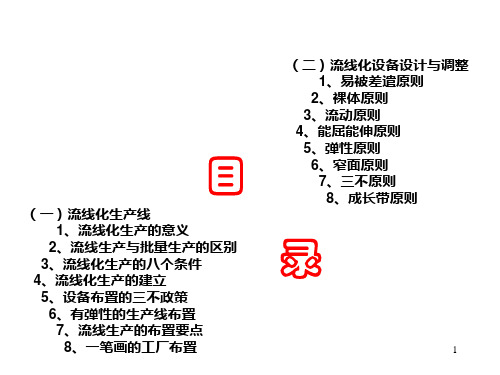
人员配置弹性化 生产品种弹性化 生产数量弹性化
弹性
通过弹性适应化
20
落生不地根
传统观点认为设备越大效率越高,通 常将设备固定在地面而无法移动。设备 不能移动,自然缺乏弹性,也就失去了 改进布置、应对市场变化的能力。
设备小型化 设备可动化
寄篱不人 下
设备“寄居”在固定 的管、线及中央式装置 之下而无法移动。
拒绝“武士道”精神
设备设计(购置)时须考虑市场和产品 的变化,避免产品“死”而设备“徇情”现 象。
“包子换馅”
设备的基本结构一样,通过换模来满足 不同产品的生产需要。
泛用机专用化
将具备基本功能的泛用设备配上专用模 具、刀具等达到专用目的。
44
5、弹性原则
功能 分区
能力 扩充
功能 扩充
基本功能 设备
☆ 逆时针方向操作 ☆ 进行适当的作业组合 ☆ 明确作业循环时间
②.避免物流浪费—— 先进先出,快速流动
☆ 明确在制品数量
☆ 一头一尾存货,
中间均衡快速流动 ☆ 考虑线与线之间的
物流
库存放置、搬运方法 和搬运路径
顺畅
☆ 前后生产线尽量靠拢
26
物留
中间停滞 隐藏问题
物流
顺畅流动 没有停滞
27
③. 信息
(3)便于作业者相互协作,异常时能停线,及时暴
露问题并改善之。
34
(4)步行最短,可单件流动,人员可增可减。
3 Step 将长屋型改为大通铺式
大 通 铺 式 布 置
35
大通铺式 布置
大通铺式布置能有效利用空间,便于线 与线之间相互协作,根据各生产线产距时间 调整作业分配和人员安排,达到少人化目的。
单元式生产详解-精益大本营

建立可以互相协作、没有人员浪费的单元生产。
12
▣ 单元线的优点
▷ 通过工程再编制,可以果断地进行少人化 ▷ 可以一眼看出工程上的异常 ▷ 不良发生时,可以采取快速ACTION ▷ 根据所需要的生产量,可以容易进行工程再编制 ▷ 入口/出口由同一个人担当,所以品质管理及生产管理
▷ 单元生产方式是(在Lean生产方式中效果性已经得到验证的)多技能工体制 和U字型生产LINE的Idea的延伸 (更加提高灵活性)
高
Job Shop
Cell
유灵
생生산产방方식式
생生산产방方식式
연活
Lean
성性
생生산产方방式식
Flow Shop
생生산产방方식式
低
비8费용用우优위位
高
▣ 单元线的必要性 ▷ 转换为不希望有库存的时代 ▷ 转换为由顾客决定价格的时代 ▷ 转换为与顾客的消费速度相对应的生产方式
入/出口的检查同一人担当, 并全部检查
改善 STAFF 小集团活动
现场中心的 2天改善活动
LINE
15
▣ 单元线的目标
▷实现公平的作业分配 (工程Balance) ▷ 工程不良的消除 (工程品质保证) ▷ 省人化的实现 (1人生产性)
16
▣ 单元线七原则
▷ 立式作业的原则 ----- 人类是站立了进步 ▷ 给予步行的原则 ---- 步行能消除疲劳 ▷ 制造1个的原则 ---- 可以看到浪费,可以消除 ▷ 多工程担当的原则 ---现代中解放 ▷ 入口/出口同一人的原则 --- 产线的自律性 ▷ 作业量公平的原则 --- 人性化 ▷ LINE STOP的原则 ------ 由于工程不良的STOP
基于PLC控制的自动化线体保养与维修
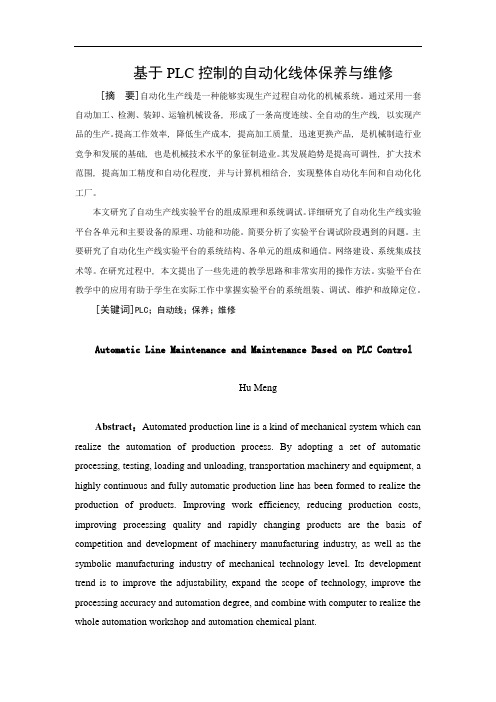
基于PLC控制的自动化线体保养与维修 [摘要]自动化生产线是一种能够实现生产过程自动化的机械系统。
通过采用一套自动加工、检测、装卸、运输机械设备, 形成了一条高度连续、全自动的生产线, 以实现产品的生产。
提高工作效率, 降低生产成本, 提高加工质量, 迅速更换产品, 是机械制造行业竞争和发展的基础, 也是机械技术水平的象征制造业。
其发展趋势是提高可调性, 扩大技术范围, 提高加工精度和自动化程度, 并与计算机相结合, 实现整体自动化车间和自动化化工厂。
本文研究了自动生产线实验平台的组成原理和系统调试。
详细研究了自动化生产线实验平台各单元和主要设备的原理、功能和功能。
简要分析了实验平台调试阶段遇到的问题。
主要研究了自动化生产线实验平台的系统结构、各单元的组成和通信。
网络建设、系统集成技术等。
在研究过程中, 本文提出了一些先进的教学思路和非常实用的操作方法。
实验平台在教学中的应用有助于学生在实际工作中掌握实验平台的系统组装、调试、维护和故障定位。
[关键词]PLC;自动线;保养;维修Automatic Line Maintenance and Maintenance Based on PLC ControlHu MengAbstract:Automated production line is a kind of mechanical system which can realize the automation of production process. By adopting a set of automatic processing, testing, loading and unloading, transportation machinery and equipment, a highly continuous and fully automatic production line has been formed to realize the production of products. Improving work efficiency, reducing production costs, improving processing quality and rapidly changing products are the basis of competition and development of machinery manufacturing industry, as well as the symbolic manufacturing industry of mechanical technology level. Its development trend is to improve the adjustability, expand the scope of technology, improve the processing accuracy and automation degree, and combine with computer to realize the whole automation workshop and automation chemical plant.This paper studies the composition principle and system debugging of the automatic production line experimental platform. The principle, function and function of each unit and main equipment of the automatic production line experimental platform are studied in detail. The problems encountered in the debugging stage of the experimental platform are briefly analyzed. This paper mainly studies the system structure, components and communication of the automatic production line experimental platform. Network construction, system integration technology, etc. In the research process, this paper puts forward some advanced teaching ideas and very practical operation methods. The application of the experimental platform in teaching is helpful for students to master the system assembly, debugging, maintenance and fault location of the experimental platform in practical work.Keywords:PLC; automatic line; maintenance; maintenance目录第一章绪论 (4)1.1 自动生产线技术发展概况 (4)1.2 PLC的应用及目前的研究现状 (5)1.3 课题主要研究的内容及意义 (6)第二章PLC控制的自动化线设计 (7)2.1 系统总体设计 (7)2.1.1自动线实验平台的组成 (7)2.1.2 各单元的功能及组成 (7)2.1.3 控制板的设计及系统任务 (8)2.2 控制系统设计 (11)2.2.1 设计思路 (11)2.2.2 电气控制设计 (12)2.2.3 气动控制设计 (13)第三章系统调试与故障分析 (16)3.1 系统调试 (16)3.2 系统运行测试遇到的主要故障和排除方法 (16)3.2.1 系统非正常运行 (17)3.2.2 系统不能启动 (18)第四章总结 (20)4.1 PLC 的日常维护 (20)4.2 PLC 的维修 (21)致谢 (22)参考文献 (23)第一章绪论1.1 自动生产线技术发展概况自动生产线是一种能够实现生产过程自动化的机械系统。
离散化,单元,节点,变形协调条件

离散化,单元,节点,变形协调条件一、离散化(一)概念离散化是将连续的物理系统转化为离散系统的过程。
在数值分析和有限元方法等领域有着广泛的应用。
例如,在对一个连续的结构进行分析时,我们不可能对结构上每一个无穷小的点进行分析,而是将结构划分为有限个小的单元,这个过程就是离散化。
(二)离散化的方法1. 等距划分- 对于一个区间a,b,如果我们要将其离散化,等距划分就是把这个区间分成n 个等长的子区间。
每个子区间的长度h=(b - a)/(n)。
例如,对于区间[0,1],如果n = 5,那么h=(1-0)/(5)=0.2,离散后的节点为0,0.2,0.4,0.6,0.8,1。
2. 非等距划分- 根据问题的特点,有时候需要采用非等距划分。
比如在一些物理量变化剧烈的区域,我们可以将节点划分得更密集,而在变化缓慢的区域节点划分得稀疏一些。
例如在研究热传导问题时,靠近热源的地方温度变化快,就可以在这个区域采用较小的子区间长度进行离散化。
二、单元(一)单元的定义在有限元分析中,单元是离散化后的基本组成部分。
它是将连续体划分后得到的小的、便于分析的子结构。
单元具有一定的形状和特性,常见的单元形状有三角形单元(在二维问题中)、四面体单元(在三维问题中)、矩形单元(二维)、六面体单元(三维)等。
(二)单元的特性1. 几何特性- 单元的形状、尺寸和节点分布决定了它的几何特性。
例如三角形单元由三个节点组成,通过这三个节点的坐标可以确定单元的形状和大小。
不同形状的单元在适应不同几何形状的求解区域方面有各自的优势。
三角形单元可以很好地拟合复杂的二维边界形状,而矩形单元在规则的矩形区域分析中可能更方便。
2. 物理特性- 单元还具有物理特性,如弹性模量、泊松比(对于固体力学问题中的弹性材料)等材料属性。
这些物理特性在单元的力学行为分析中起着关键作用。
例如,在分析结构的应力和应变时,单元的弹性模量决定了它在受到力的作用时的变形特性。
制动单元中文说明书

感谢您选用深圳市四方电气技术有限公司生产的制动单元。 本手册为制动单元的使用手册,它将为您提供制动单元的安装、配线、功能、日 常维护、故障诊断与排除等相关细则及注意事项。 为正确使用本制动单元,充分发挥产品的卓越性能并确保使用者和设备的安全, 在使用制动单元之前,请您务必详细阅读本手册。不正确的使用可能会造成变频器及 制动单元运行异常、发生故障、降低使用寿命,乃至发生设备损坏、人身伤亡等事故! 本使用手册为随机发送的附件,请妥善保管,以备今后对制动单元进行检修和维 护时使用。 由于致力于产品的不断改善,本公司所提供的资料如有变动,恕不另行通知。
故障诊断与对策31常见故障分析故障种类可能原因解决方案1主回路接线错误造成短路1检查接线是否正确过流保护2制动电阻或模块损坏2检查制动电阻是否损坏3制动电阻太小3更换制动电阻或者制动单元1制动单元负载过重1更换功率等级更大的制动单元过热保护2制动比率超过102改善制动单元外部环境3环境温度过高1选择大一级功率等级的制动单元同时更换阻值更小功率更高的制动电1制动电阻制动能力不够变频器过压阻2制动单元没有开始制动2检查制动单元是否发生故障保护3检查制动单元控制线制动时变频器过1制动电阻太小1更换制动电阻流保护2减速时间设置太小2延长减速时间未制动时制动电1接线不正确1检查接线是否正确阻发热严重2制动单元故障2更换制动单元32制动单元的保护及复位1当检测温度高于75?c时制动单元发生过热保护
(1)在变频器与制动单元连线时,P+、P-接反将烧毁制动单元并损坏变频器,在变频器上电前 请务必仔细检查。 (2)主回路安装和接线时,必须切断与变频器的连接或断开变频器的电源,并等待 5-10 分钟, 变频器或制动单元电源指示灯熄灭后才可操作。控制回路接线原则上不允许在带电的情况下进 行。 (3)控制回路连线应尽可能远离主功率电路连接线,以防止由于干扰噪声引起误动作。如控制 电路连线必须穿越主回路连接线,则应使之成垂直穿越,如连接线距离较长,则应使用双绞线或 屏蔽线。
单元化线体的改善方法②(中文)

单元化线体的改善方法②(中文)单元化线体的改善方法单元化线体是指在生产过程中通过合理规划和优化生产线上的各个工作岗位,达到提高生产效率和质量的目的。
本文将介绍一些改善单元化线体的方法,以帮助企业提高生产效率和降低成本。
一、优化工艺流程优化工艺流程是改善单元化线体的重要手段。
在优化工艺流程时,需要对生产流程进行详细分析,找出不必要的工序和环节,并进行合理化改进。
通过减少不必要的工序和环节,可以缩短生产周期,提高生产效率。
此外,还可以通过工艺改进来降低生产成本,提高产品质量。
二、提高设备自动化水平设备自动化是实现单元化线体的重要手段之一。
通过提高设备自动化水平,可以有效地提高生产效率,减少人工操作的时间和错误。
采用先进的自动化设备,可以实现自动化生产线的无人化运行,从而大幅度提高生产效率和降低生产成本。
三、培训技术工人技术工人是保证单元化线体正常运行的重要保障。
通过加强技术工人的培训,提高他们的专业技能和操作水平,可以减少生产中的错误和故障,提高生产效率。
此外,还可以通过培训技术工人来推广和传授先进的生产技术和管理经验,进一步提高生产线的整体水平。
四、建立完善的质量管理体系建立完善的质量管理体系是改善单元化线体的重要手段之一。
通过建立完善的质量管理体系,可以对生产过程进行全面监控和控制,减少产品的次品率和生产中的浪费,提高产品质量和生产效率。
同时,还可以通过建立质量管理体系来及时发现和解决生产中的问题,避免延误生产进度和增加成本。
五、引进先进的管理理念引进先进的管理理念是改善单元化线体的重要手段之一。
通过引进先进的管理理念,可以激发员工的积极性和创造力,提高团队的凝聚力和协作能力,推动生产线的持续改进和创新。
在引进先进的管理理念时,企业可以借鉴国内外优秀企业的成功经验,结合自身的实际情况,制定合适的管理策略和措施。
六、实行绩效考核激励机制实行绩效考核激励机制是改善单元化线体的重要手段之一。
通过建立科学的绩效考核体系,可以激励员工的积极性和创造力,推动生产线的高效运行。
精选单元生产线设计和生产性改善方法
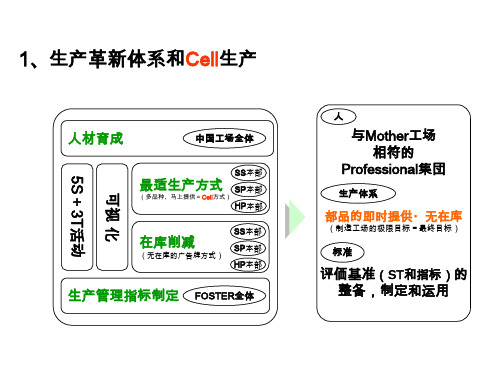
规定1
CELL是后工序向前工序牵拉的方式。所以、「指定席」上如果还有仕挂品,前工序 一定不能超出规定再放入数量、即使是[手等待=空闲]都好,也不能违反规定多放数量。
皮带LINE时代的生产现场(SONY马来西亚工场)
CELL工程作业者日本国SONY工场
26、CELL生产工场的7种浪费
根据不同的生产环境浪费发生的情况有所不同。単一品种大量生产的场合和多品种 少量生产的场合浪费排除的优先顺序有所改变。
7种浪费 过多生产的浪费 过多购入的浪费
経営上的不良影响
SONY的对应方法
8、CELL生产方式的外観(作业台的配置)
CELL生产线的形状如下图所示,使用什么样的形状可以根据 制品、原材料、部品及设备的大小、形状等作出决定。 CELL全体的形状根据下工序的场所、物流、动作、疲労度等 方面作出考虑,选择最有利的摆设方案。动作分析的知识也 活用上去,设计与担当品种最合适的CELL方式。
生产変化幅度
例、1CELL 1500台/日程度
CELL生产能力
一CELL的能力 1500台/日
CELL的数量
顾客要求数 CELL生产能力
个别CELL的设计
人的潜在能力引发, 工程上的分配达到
4:1
11、CELLLINE设计的概略手顺
対象品种的决定
作业标准书、设备仕様收集
CELL的生产能力(P/T)的 确定
U字型CELL
US字型CELL
I字型CELL
L字型CELL
9、CELLLINE的设计手顺
(1)、设计条件的确认 ①、CELL的生产能力 ②、设备能力的把握、其他
企业线条化管理方案

企业线条化管理方案简介随着企业规模的不断扩大,企业管理难度也越来越大,企业线条化管理方案成为了越来越多企业管理者追求的目标。
企业线条化管理方案可以有效地提升企业经营效率,增强企业管理能力,建立科学合理的管理制度,实现企业高质量的发展。
线条化管理的概念线条化管理是指通过科学合理的管理方法,建立起完备系统的管理体系,将企业的各项管理业务分解成为一条条的管理单元,使得管理者可以通过精细化的管理来提高各个管理单元的效率,最终达到提升整个企业管理效率的目的。
企业线条化管理的优点提高管理效率通过线条化管理,可以将繁琐的管理工作分解为一个个具体的管理单元,使各个管理单元之间的工作互不干扰,管理者可以针对每个管理单元进行精细化的管理和调整,从而提升管理效率。
建立科学合理的管理制度线条化管理可以帮助企业建立起一整套科学合理的管理体系,通过制定对应的管理规章制度和流程,规范各项管理工作,从而优化企业的运营效率,提高整个企业的绩效水平。
提高管理层决策水平线条化管理可以对企业内部的管理业务进行切割,帮助管理者更加清晰的了解企业运营的各个方面,调整决策方向,使得企业决策更加精准,有效。
鼓励员工创新和积极性线条化管理可以将企业管理工作分解为具体的管理单元,并将责任明确到每个员工,让员工主动承担各自的工作,提高员工对工作的责任感,鼓励员工创新和积极性。
实施企业线条化管理的几个关键步骤初期准备企业实施线条化管理,需要在初期做好诸多的准备工作,包括调查、研究和规划等,全面了解和掌握企业内部运营状况,对企业体系进行有序优化改善,制定出符合企业实际情况的管理制度和流程。
制定标准化管理规范制定标准化管理规范是企业实施线条化管理的重要步骤之一,企业需要根据自身的业务特点和管理需求,建立起满足实际需要的管理规范,包括各个管理单元的任务和责任,管理流程和标准化的操作方法等。
明确标准化流程企业线条化管理需要明确具体的标准化流程,同时要对各流程进行详细的分析和评估,找出流程中的漏洞和不足,及时进行改进和优化。
电力电缆圆整度的影响因素及改进措施

高C-13电力电缆圆整度的影响因素及改进措施摘要:塑力缆和硅烷交联绝缘低压电力电缆作为公司的重要产品,近年来在市场上所占份额越来越大,特别是硅烷交联低压电力电缆更是未来的主导产品。
产品质量的好坏将直接影响公司产品在市场上的竞争力以及企业形象。
电缆圆整度是产品外观质量的重要考核项目,提高电缆圆整度是提高产品市场竞争力的关键部分。
由于电缆成缆的圆整度又是影响电缆整体圆整度的重要因素,因此,本文主要分析了影响电缆成缆时圆整度的各种因素,并提出了相应的改进措施。
主题词:电力电缆圆整度、成缆圆整度、影响因素、改进措施前言:将二芯、三芯,甚至是几十芯绞合在一起,组成多芯电缆。
这种将绝缘线芯按一定的规则绞合在一起,包括绞合时线芯间空隙的填充和在成缆上的包带过程,叫做成缆。
我公司在实际生产制造中,主要有两芯,三芯等截面圆形电缆,三芯等截面扇形电缆,四芯、五芯等截面扇形电缆,3 大1小扇形电缆, 4大1小芯电缆,以及2芯到37芯的控制电缆等成缆结构。
影响成缆圆整度的因素很多,而且不同型号的电缆线芯潜在的影响因素又不一样,采取相应的措施也不一样,本文主要对圆型线芯电力电缆和扇型线芯电力电缆进行了分析,找出影响成缆圆整度的主要因素,并针对不同因素提出了不同的改进和解决办法。
还针对扇型硅烷交联电缆成缆出现的问题进行分析,并找出加以解决改进。
一.影响电缆成缆圆整度的主要因素影响成缆圆整度的主要因素如图一,图1.影响电缆圆整度的主要因素下面根据实际生产中发现问题的解剖和分析,简要阐述主要影响因素。
1.1.填充填充是电缆成缆圆整度的主要影响因素,电缆线芯在成缆时,其线芯与线芯之间均有一些较大空隙,如果不正确地使用填充材料加以填充,很难保证线芯的圆整度,特别是二芯、三大一小、三大二小、四大一小电缆成缆时填充要求的更高。
因此,填充不合理也是影响电缆圆整度的主要因素之一。
1.2.扇形绝缘线芯排线质量不好,线芯翻身,预扭角度不够或过大扇型绝缘线芯排线不好,容易造成线芯“拉刹”拉断,并且造成线芯在模具中擦伤等问题出现,而且线芯容易翻身形成油条型,从而影响电缆圆整度。
- 1、下载文档前请自行甄别文档内容的完整性,平台不提供额外的编辑、内容补充、找答案等附加服务。
- 2、"仅部分预览"的文档,不可在线预览部分如存在完整性等问题,可反馈申请退款(可完整预览的文档不适用该条件!)。
- 3、如文档侵犯您的权益,请联系客服反馈,我们会尽快为您处理(人工客服工作时间:9:00-18:30)。
第11页/共22页
四、导入单元化线体的步骤
----2)制定改善方案
ⅵ.零件从前面取料,物料架要放到伸手就能拿到的 地方
ⅶ.工序排布设计 ・在地上画上与实物相等的图进行确认 ・记录零件容器、供应位置 ・对每个工序进行作业分配 ・步行最少化 ⅷ.设计与作业点相吻合的工装夹具 ⅸ.工作台(线体)、配电、管道可以随时移动。
生产线以手工作业为主
6)1个流制作与标准作业WF=100 7)动作改善使零件、工装夹具达到最佳配置(手
头配置) 8)通过防呆、防错减少需要注意的地方 9)培养多能力工,通过独立全部组装1台来培训 10)减少零件数量、螺钉种类与按同一方向装
配的设计改善。
第5页/共22页
四、导入单元化线体的步骤
1)掌握实际情况(现状)…用IE的手法调查现状 ①P-Q分析、工程表(含部件组装工序・外协 工序)、工时表 ②制造不良的发生情况与分析 ③目前的排布
除了线上的人员外,如果有需要可以让物料管 理、配送、部装线、部装车间的员工参加
第14页/共22页
四、导入单元化线体的步骤
---- 3)试运行与改善
ⅵ.把改善的记录、小组会议的结果通报给 小组成员、相关的全体人员,让他们明白。 用大的纸、可以手写的,无论是谁无论何时 都可以自由的制度的制定
ⅶ.披露每天的生产实际数量、品质数据(要记 录目标值)
第3页/共22页
三、单元化线体具备的条件
生产线以手工作业为主 1)多用轻型设备,人手作业与设备/装置的稼动同
时作业的自动化 2)组装~打包的顺畅流动F值=1 3)手送岗位间距最佳为75cm 4)多机型的混合生产线。转产不需要2分钟 5)多频次的生产指示与有序的物料配送。
第4页/共22页
三、单元化线体具备的条件
2)制定改善方案 ①改善目标…提高生产效率、减少在制品数量、提高
空间利用率、减少管理要点、及时性(交货期) 第6页/共22页
四、导入单元化线体的步骤
----2)制定改善方案 [效果(经验值)] 生产力提高:150% (线平衡:25%、动作浪费:减少25%的人) 在制品:1/2~1/5 管理要点:岗位连接数量 品质提高:不良率1/5~1/10
ⅷ.员工轮岗,训练员工能做每一个岗位。 确认作业指导书的内容,修订
ⅸ.公开演示试运行,听取相关人员的意见
第15页/共22页
四、导单元化线体的步骤
---- 4)稳定产量
第2页/共22页
二、单元化线体应具备的特征
6)作业点的高度为站立作业时肘关节的高度。 7)零件有序地JIT投入。 8)定位置定作业零件从前面拿取。 9)生产多种机型。 10)单元化排布线体,工序间的设置轻型化。 11)“3直线”有节奏地运动。
流动直线化。作业点在水平面直线。物料/材料 的移动也是直线。
四、导入单元化线体的步骤
----2)制定改善方案
ⅱ.生产节拍的推荐范围
12 ~ 23秒 : 可能范围
24 ~ 259秒 : 推荐范围
260 ~ 369秒 : 可能范围
零件数量的标准是10个左右
ⅲ.人数的推荐范围
最少人数 1人
容易管理的人数 极限人数
4~5人
7~8人
ⅳ.U线的开口:100~150cm(不影响员工的作业) ⅴ.工作台(线体)带脚轮,最好是自制
进行调整,确认作业指导书等必需的技术指导 资料是 否齐备 第13页/共22页
四、导入单元化线体的步骤
---- 3)试运行与改善
②试运行 ⅰ.挑选优秀的员工 ⅱ.对员工说明作业顺序、注意事项、管理要点等。 ⅲ.首先让其反复按指示作业,学习作业内容。 ⅳ.单元化线体整体开线作业
不妥当的时候停线,及时改善 ⅴ.每天下班前停线开小组会议。
电气布线、压缩空气管道、气体管道、排气/吸气 管道在线体上方铺设,互相独立。
第12页/共22页
四、导入单元化线体的步骤
---- 3)试运行与改善
3)试运行与改善 ①试运行的准备 ⅰ.确认各工序的作业台、工装夹具、零件容器等。 ⅱ.为了试运行进行生产调整与物料的准备 ⅲ.多能工的培训 ⅳ.由高手1人作业对全工序的作业进行确认 ⅴ.根据1人作业的结果为基础,对各工序作业顺序
第7页/共22页
四、导入单元化线体的步骤
----2)制定改善方案
②U线的原则 ⅰ.站立作业
坐着作业会使手的动作变长、产生肩膀转动/扭腰 的动作,难以形成互助。 ⅱ.1个流制作 使手头持有量的浪费可视化。排除制作过多浪费。 ⅲ.一人做多工序
具备1个流生产与流水化生产的条件。 ⅳ.作业量公平
站在员工的立场分配作业及设置岗位。
第8页/共22页
四、导入单元化线体的步骤
----2)制定改善方案
ⅴ.做完1台→投1台的料 为了能够实现1个流生产,以及发生不良→停线 →品质塑造改善。
ⅵ.步行最小化 步行虽然可恢复疲劳,但要禁止不必要的步行。
ⅶ.停线的原则 出现问题时停线解决,不让不良流到下一工序
第9页/共22页
四、导入单元化线体的步骤
----2)制定改善方案
③ 单元化线体工序设计的原则 ⅰ.根据正确的现状数据进行设计 ⅱ.根据一定的原理原则设计 ⅲ.对现状“改善”后的设计
④U线设计规范 ⅰ.节拍与生产线人员: 生产节拍=稼动时间/生产计划台数(台/日) 理论人员=合计作业时间/生产节拍 (现状分析理论与第实10页际/共的22页人数差就是改善目标)
第1页/共22页
二、单元化线体应具备的特征
1)作业分配平均、加工品(产品)以稳定的节拍 以手动的方式流动。
2)组装~测试~打包的贯通化作业。 (零件从材料投入到制成产品)
3)“站立作业”的作业方式…可以“互助”。 4)1个流制作工序间没有缓冲件,B值近似于1。
零件(物料)上线时间以成品制成时间为准。 5)作业区域为0.75m/岗位(工程)。
一、单元化线体的定义
1)能够根据产量的变化配置(增减)人手。 2)能高效率地进行多机型混合生产。 3)以人的稼动为主的生产方式。 4)完成1台(个)→投1台(个)的物料、零件,
工序间的在制品数量最小化,不变化。 5)标准作业:手头保持的数量、作业顺序、生产
节拍…都是确定的 6)配备了辅助作业/动作的简易工装夹具。 7)不良品不会流到下一个工序的体系=有防呆措施。 8)单元化线体→入口与出口同源管理。 9)品质与生产数量稳定