工厂合理化布局概述
工厂有哪些合理化建议

工厂有哪些合理化建议
工厂是生产企业的重要组成部分,合理化建议可以帮助工厂提高生产效率、降低成本,并且改善工作环境,提高员工的工作满意度。
下面是一些建议:
1、优化生产线布局:合理布置生产设备和工作人员,减少物
料和人员的移动距离,提高生产效率。
2、引入自动化设备:采用先进的生产设备和自动化技术,可
以降低人工成本,提高生产效率和产品质量。
3、改善物料管理:建立科学的物料管理体系,包括物料采购、仓储配送等环节,减少物料浪费和库存过多的情况。
4、培训员工技能:提供必要的培训和技能提升机会,让员工
掌握新的技能和知识,提高工作效率和质量。
5、设立绩效考核机制:建立绩效考核制度,对员工的工作表
现进行评估和奖励,激励员工发挥自己的潜力。
6、完善设备维护保养:定期对生产设备进行检查和维护保养,延长设备的使用寿命,减少设备故障和停机时间。
7、提高产品质量管控:建立科学的质量管理体系,严把产品
质量关,确保产品符合国家标准和客户需求。
8、优化供应链管理:与供应商和客户建立良好的合作关系,
优化供应链管理,降低物流成本和交货时间。
9、节约能源和资源:提倡节能减排和资源回收利用,减少对环境的影响,降低生产成本。
10、关注员工健康和安全:提供良好的工作环境和工作条件,加强安全教育和培训,减少事故发生的风险。
总之,合理化建议不仅可以提高工厂的生产效率和经济效益,还可以改善员工的工作环境和生活质量。
工厂应该不断创新和改进,以适应市场的变化和发展的需要。
对工厂的合理化建议(精简版)

对工厂的合理化建议对工厂的合理化建议对工厂的合理化建议:对工厂的合理化建议1.总则1.1 技术改进与合理化建议和推行工厂现代化管理,是企业革新挖潜、降低成本、提高产品质量、提高劳动生产率、增加经济效益的重要途径,对工厂的合理化建议。
1.2合理化建议包括生产采用新技术、新工艺、新材料、新结构、新配方,提高产品质量,改善产品性能及开发新产品,节约原材料等。
1.3合理化建议也包括对设备、工艺过程、操作技术、工、夹、量具、试验方法、计算技术、安全技术、环境保护、劳动保护、运输及存储等方面的改进或建议。
1.4合理化建议也包括对企业现代化管理方法、手段的创新和应用,促进企业素质全面提高等方面的建议或改进。
2.组织领导和职责范围2.1技术建议与现代管理优秀成果评审小组成员由:厂长祖国-军、人事部主任田春禄、其他各部门负责人和其他有关人员组成。
2.2在评审小组的领导下,日常工作由工会和人事部门负责。
组织、宣传与发动工作由工会负责;具体审查工作由人事部门负责。
人事部每周对职工群众提出的合理化建议进行整理、分类、转达、上报。
2.3采纳、实施等过程由人事部做好建议人、实施部门和创造价值等方面的记录,同时填奖励申报表,报评审领导小组进行鉴定、审核、归档。
2.4评审领导小组进行半年进行一次综合评审,每年度进行一次表彰、奖励。
3.合理化建议、技术改进的范围3.1合理化建议,是指有关改进和完善企业生产技术和经营管理方面的办法和措施及精神文明建设方面的新举措;技术改进是对机器设备、工具、工艺技术等方面所作的改进和革新,,对工厂的合理化建议。
结合本企业的特点,合理化建议和技术改进,划分为以下几个方面:生产技术、生产工艺、生产工具的改进;安全技术、劳动保护技术的改进;节约材料、能源的措施和办法;企业现代管理方法、手段的创新和应用,经营管理的建议;企业精神文明建设、企业文化建设和企业职业道德建设方面的建议。
3.2合理化建议和技术改进的内容是相对于工厂目前技术水平、经营管理水平、精神文明建设有所提高和改进而言,所提建议应具有超前性、可行性和效益性,经过建议人的努力,促使其实现的,均属于本范围。
工厂的合理化建议范文(4篇)
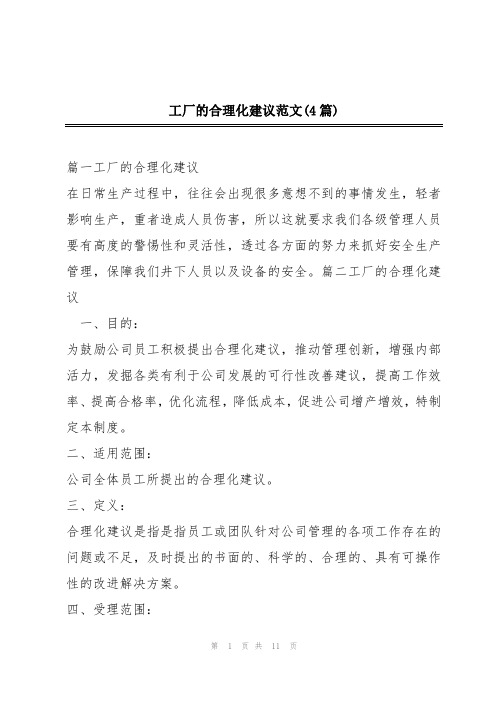
工厂的合理化建议范文(4篇)篇一工厂的合理化建议在日常生产过程中,往往会出现很多意想不到的事情发生,轻者影响生产,重者造成人员伤害,所以这就要求我们各级管理人员要有高度的警惕性和灵活性,透过各方面的努力来抓好安全生产管理,保障我们井下人员以及设备的安全。
篇二工厂的合理化建议一、目的:为鼓励公司员工积极提出合理化建议,推动管理创新,增强内部活力,发掘各类有利于公司发展的可行性改善建议,提高工作效率、提高合格率,优化流程,降低成本,促进公司增产增效,特制定本制度。
二、适用范围:公司全体员工所提出的合理化建议。
三、定义:合理化建议是指是指员工或团队针对公司管理的各项工作存在的问题或不足,及时提出的书面的、科学的、合理的、具有可操作性的改进解决方案。
四、受理范围:1、管理制度、管理方法的改善;2、工作方法、工作流程、工作标准及安全措施的改进。
3、技术创新、作业方式的改进。
4、工具、设备、仪器的改进。
5、原辅材料、能源节约和三废利用的建议。
6、与其他有关降低成本与费用、提高效率和工作合理化等事项。
7、市场开拓及营销的项目和建议。
8、企业文化建设、团队精神、凝聚力和工作绩效的合理化建议等;9、美化公司环境,提高公司内外部形象的建议。
10、非职务范围内,有利于公司发展的各项合理化建议;五、不受理范围:1、抱怨、投诉;2、对于工资、福利方面的要求;3、关于人事任免方面的建议;4、公认的事实或正在改善的;5、已被采用过或前已有的重复建议;6、在正常工作渠道被指令执行的(本职岗位职责范围);7、无具体实施方案的建议。
六、管理职责:1、为确保工作质量及有效性,对合理化建议能正确评估、合理奖励,公司设置“合理化建议评审小组”,由总经理任组长,各部门主管任组员。
其工作职责如下:①研究制定合理化建议的管理制度;②对重大建议进行评议,根据标准初审奖励方案;③对已采纳的建议进行过程跟踪,以防范决策失误,并及时予以调整,避免风险;④对实施后产生的效率进行效益评估;2、各部门主管负责动员本部门下属员工积极参与公司合理化建议活动,并做好合理化建议收集、申报工作。
工厂合理化布局简介

工厂合理化布局简介工厂合理化布局简介工厂是生产商品和提供服务的场所,其布局合理与否直接关系到生产效率和运营成本。
工厂合理化布局是指在保证生产流程顺畅和生产设备安全的前提下,通过优化工作空间和流动环境,使生产过程更加高效和经济的一种作业规范。
工厂合理化布局的目的是为了提高生产效率和效益,减少不必要的生产浪费和物流成本。
一个合理的布局可以使生产过程更加流畅,减少生产设备互相干扰和交叉作业带来的时间浪费。
同时,合理的布局还可以减少人员和物料的移动距离,提高生产人员的工作效率,降低物料搬运和仓储成本。
工厂合理化布局的要点是根据生产工艺流程和产品特性,确定最佳生产线和工作区域的组合方式,使得物料的流动路径最短,工作人员之间的交流更加便捷。
一般来说,合理化布局需要考虑以下几个方面的因素:1. 生产工艺流程:合理的布局必须充分考虑生产工艺流程的特点,按照生产所需的顺序排列各个工作站点和设备。
这样可以缩短物料的运输距离,减少工作人员的移动时间和等待时间,提高生产效率。
2. 物料流动:合理的布局要求将物料的流动路径设计得尽量简短和直接。
这可以通过合理安排产品接收区、物料配送区和成品仓储区的位置来实现。
同时,可以采用自动化设备和输送线来实现物料的自动运输,减少人工操作和物料搬运。
3. 人员安排:合理的布局要求将工作人员的工作岗位合理安排在生产线上,减少人员之间的移动距离和交叉作业,提高工作效率。
同时,要合理安排工作区域的大小和设备的布局,以便人员能够自由地移动和操作。
4. 安全环境:合理的布局要考虑生产设备和安全设施的设置,确保工作区域的安全和生产流程的连续。
必要时,可以采用防护设备和安全标识来减少安全风险,并提供必要的培训和指导。
5. 管理和监控:合理的布局可以提高生产过程的可控性和透明度,便于管理人员对生产情况进行监控和调整。
可以通过安装监控设备和使用生产管理系统来实现对生产过程的实时监控和数据分析,以便及时发现和解决生产中的问题。
新厂区合理性规划与布局

新厂区合理性规划与布局摘要本文阐述了新厂区厂房合理性布局所坚持的原则、布局方法以及后续生产物流的规划。
关键词厂房布局物流规划系统布局设计模式1前言新厂区前期规划布局设计应该以制造出质量好的产品为目标,这就要求新厂区的厂房具有一定的发展功能,并拥有合理化的布局规划。
新厂区布局时,首先要考虑到产品设备的利用率、制造成本。
在此前提下,加工设备选择合理、设备布局优化、各生产单位协调组织,尽可能的提高生产效率、降低产品的制造成本。
2新厂区设计的基本原则新厂区厂房设计包括很多因素,将新厂区所涉及到的外部条件、内部条件相互结合,权衡整体利益与局部利益,结合当前利益和长远利益,并结合公司现有产品的产量做定性与定量分析,总结一下四条原则:1.厂房规划以及设备布局过程中要严格按照“安全第一”的原则,必须保证工人的操作安全,为员工提供安全舒适的工作环境是极其必要的;2.厂房前期的规划过程中,需要考虑设备与生产计划、工艺的关系,设备布局时要保证工艺流程的合理性,同时也要保证物流,人流,信息流的相互结合的方便性,在保证物料进出车间不发生拥堵的情况下,尽可能将物料运输距离降低,更要避免交叉往返运输,从而增加设备利用情况也减少物流费用[1];3.增加对产品的监控,加速物料周转,减少库存。
现场调度通过平衡物流和生产能力的办法,调节生产节拍和物流节拍,极小化制品库存;4.厂房的规划充分考虑公司长远发展,在满足现阶段生产的同时也要使厂房具有备速响应能力,能随着生产发展的需要,留下以后的发展空间。
3现代化布局设计方法厂房信息化管理、工艺过程是现阶段大部分厂房布局设计基础。
生产需要工艺过程,工艺过程是任何阶段的厂房设计都需要克服的关键问题[2]。
随着生产率的提高、产品优势利润在信息化管理上的逐渐显现。
公司的目的是市场竞争力的提高,因此公司要有能力进行产品的快速变化,按市场需求变化进行;特别是当产品需求产生变动,公司要能以较高生产率、较大柔性、较低改造费用实现产品改造。
关于工厂的合理化建议

关于工厂的合理化建议工厂合理化是指通过改善工作流程、提高生产效率、降低成本等手段,使工厂的运营更加高效、经济和可持续。
以下是关于工厂合理化的一些建议:1. 流程优化:通过重新设计生产流程,消除繁琐的环节和重复工作,提高生产效率。
可以运用价值流图和时间研究等工具,识别出工作流程中的瓶颈和浪费,从而制定优化措施。
2. 自动化设备:引进先进的自动化设备,将一些简单重复性的工作交给机器完成,提高生产效率和产品质量。
这样可以减少人力资源的投入,提高生产效益。
3. 优化物料管理:建立科学的物料管理制度,确保原材料的及时供应。
可以采用先进的物流管理系统,实现物料的准确跟踪和有效管理,避免出现因物料短缺或过量而导致的生产停顿或库存积压的情况。
4. 培训和技能提升:通过培训和技能提升,提高员工的专业素质和技术水平。
为员工提供定期的培训机会,使其了解最新的生产技术和管理方法,提高他们的工作效率和稳定性。
5. 建立质量管理体系:“质量是企业的生命”,建立完善的质量管理体系,从源头抓起,保证产品的质量稳定。
可以采用ISO9000质量管理体系,确保生产过程的标准化和规范化。
6. 环境保护意识:加强员工的环境保护意识,采取有效措施减少对环境的污染。
可以推广使用清洁能源、节能设备,降低能耗和废物排放,减轻对环境的负担,提升企业形象。
7. 制定绩效考核制度:建立科学合理的绩效考核制度,激发员工积极性和创造力。
可以采用KPI绩效考核模式,设定明确的产量、质量、效率等指标,并给予适当的奖励和激励,促使员工不断进取。
8. 优化设备配置:评估现有设备的使用情况,及时淘汰老化设备,引进新的高效设备。
通过设备的优化配置,提高生产效率和品质,降低故障率和维修成本。
9. 加强团队协作:建立良好的团队协作机制,促进员工之间的沟通和合作。
可以建立跨部门协同工作的机制,减少信息滞后和误传,提高工作效率和沟通效果。
10. 持续改进:通过设立改进小组等方式,鼓励员工提出改进建议,并及时采纳和落实。
对工厂的合理化建议
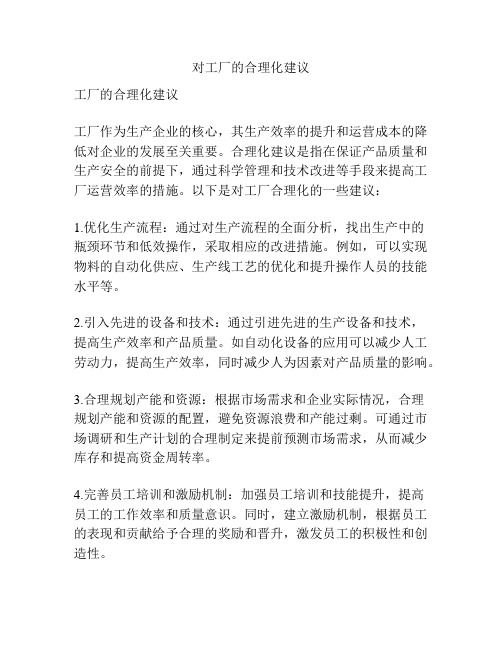
对工厂的合理化建议工厂的合理化建议工厂作为生产企业的核心,其生产效率的提升和运营成本的降低对企业的发展至关重要。
合理化建议是指在保证产品质量和生产安全的前提下,通过科学管理和技术改进等手段来提高工厂运营效率的措施。
以下是对工厂合理化的一些建议:1.优化生产流程:通过对生产流程的全面分析,找出生产中的瓶颈环节和低效操作,采取相应的改进措施。
例如,可以实现物料的自动化供应、生产线工艺的优化和提升操作人员的技能水平等。
2.引入先进的设备和技术:通过引进先进的生产设备和技术,提高生产效率和产品质量。
如自动化设备的应用可以减少人工劳动力,提高生产效率,同时减少人为因素对产品质量的影响。
3.合理规划产能和资源:根据市场需求和企业实际情况,合理规划产能和资源的配置,避免资源浪费和产能过剩。
可通过市场调研和生产计划的合理制定来提前预测市场需求,从而减少库存和提高资金周转率。
4.完善员工培训和激励机制:加强员工培训和技能提升,提高员工的工作效率和质量意识。
同时,建立激励机制,根据员工的表现和贡献给予合理的奖励和晋升,激发员工的积极性和创造性。
5.节约能源和资源:通过合理利用能源和资源,减少浪费和环境污染,达到节能减排的目的。
例如,选择节能设备和绿色材料,优化生产工艺,减少废水、废气和废弃物的排放等。
6.推行精益生产管理:精益生产管理是一种全面优化生产流程的思想和方法,通过消除浪费和提高价值创造能力,实现生产过程的高效、灵活和高质量。
精益生产管理包括价值流映射、流程改进、快速响应、员工参与等一系列的管理措施,可以极大地提高工厂的效率和竞争力。
7.建立良好的沟通和协作机制:建立和完善生产、质量和供应链等部门之间的沟通和协作机制,促进信息的流通和效率的提升。
如通过建立跨部门的沟通渠道、推行信息化管理系统等方式,实现各个部门之间的协作和配合。
以上是对工厂合理化的一些建议。
每家工厂的情况不同,应根据实际情况和具体需求来选择合适的措施。
工厂车间现场管理合理化建议
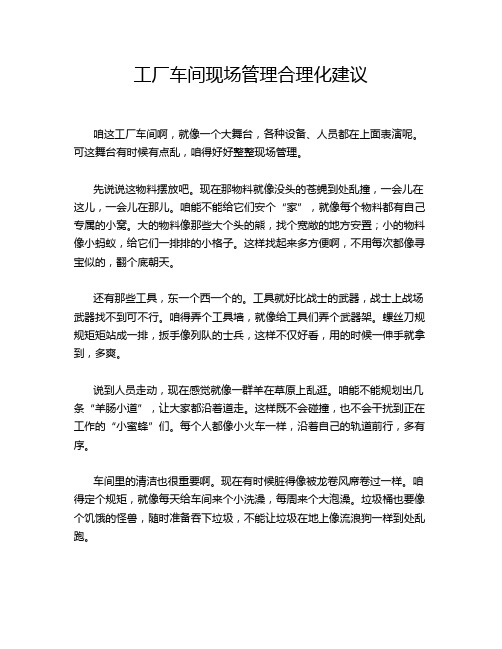
工厂车间现场管理合理化建议咱这工厂车间啊,就像一个大舞台,各种设备、人员都在上面表演呢。
可这舞台有时候有点乱,咱得好好整整现场管理。
先说说这物料摆放吧。
现在那物料就像没头的苍蝇到处乱撞,一会儿在这儿,一会儿在那儿。
咱能不能给它们安个“家”,就像每个物料都有自己专属的小窝。
大的物料像那些大个头的熊,找个宽敞的地方安置;小的物料像小蚂蚁,给它们一排排的小格子。
这样找起来多方便啊,不用每次都像寻宝似的,翻个底朝天。
还有那些工具,东一个西一个的。
工具就好比战士的武器,战士上战场武器找不到可不行。
咱得弄个工具墙,就像给工具们弄个武器架。
螺丝刀规规矩矩站成一排,扳手像列队的士兵,这样不仅好看,用的时候一伸手就拿到,多爽。
说到人员走动,现在感觉就像一群羊在草原上乱逛。
咱能不能规划出几条“羊肠小道”,让大家都沿着道走。
这样既不会碰撞,也不会干扰到正在工作的“小蜜蜂”们。
每个人都像小火车一样,沿着自己的轨道前行,多有序。
车间里的清洁也很重要啊。
现在有时候脏得像被龙卷风席卷过一样。
咱得定个规矩,就像每天给车间来个小洗澡,每周来个大泡澡。
垃圾桶也要像个饥饿的怪兽,随时准备吞下垃圾,不能让垃圾在地上像流浪狗一样到处乱跑。
设备维护也不能马虎。
设备就像我们的老伙计,得好好照顾。
不能等到设备“生病”了才去看医生,要定期给它们做“体检”。
就像对待老爷爷老奶奶一样细心,给它们擦擦灰,上上油,让它们一直精神抖擞地干活。
安全标识呢,现在那些标识就像害羞的小姑娘,躲在角落里,不仔细找都看不到。
咱得把安全标识弄得像大明星一样显眼,让人一眼就能看到。
那些危险的地方就像有魔法的禁地,标识就是警示大家不要靠近的魔法符文。
还有工作流程,现在有时候像一团乱麻。
咱得把流程梳理得像梳头发一样顺溜。
每个步骤就像一个个小台阶,一步一步稳稳当当的,不能跳着走,不然容易摔跟头。
咱们要是把车间现场管理好了,那这个大舞台就能上演一出出精彩的好戏,效率像火箭一样飙升,产品质量像钻石一样坚硬又闪亮,咱们也能开开心心地在这个大舞台上继续工作啦。
车间定置要求

车间定置要求引言概述:车间定置是指根据生产工艺和生产需求,对车间进行合理布局和设备配置的过程。
合理的车间定置可以提高生产效率,降低生产成本,保证产品质量。
本文将从四个方面详细阐述车间定置的要求。
一、车间布局要求:1.1 合理划分功能区域:根据生产工艺流程和产品生产流程,将车间划分为原料存放区、加工区、组装区和成品存放区等功能区域。
这样可以实现物料流、信息流和人员流的顺畅,提高生产效率。
1.2 考虑生产安全:合理布局工作区和通道,确保设备之间的距离符合安全要求,避免因工作区域拥挤而导致事故发生。
同时,设置安全出口和应急通道,以便在紧急情况下人员能够迅速疏散。
1.3 充分利用空间:合理利用车间空间,避免堆放杂物和废料,保持车间整洁有序。
同时,考虑设备的布局和排列方式,确保设备之间的距离和通道宽度能够满足操作和维护的需求。
二、设备配置要求:2.1 选择适合的设备:根据产品的生产工艺和质量要求,选择适合的设备。
设备应具备高效、稳定、可靠的特点,能够满足生产需求,并具备一定的扩展性,以适应未来的生产需求变化。
2.2 设备布局合理:根据生产流程和工艺要求,合理布置设备,确保设备之间的协调配合。
同时,考虑设备的维护和保养,保证设备的正常运行。
2.3 设备安全可靠:设备应符合相关的安全标准和要求,具备安全保护装置,防止操作人员受伤。
设备还应具备故障自动检测和报警功能,及时发现并解决故障,保证生产的连续性和稳定性。
三、环境要求:3.1 温度和湿度控制:根据产品的特性和生产工艺的要求,控制车间的温度和湿度。
某些产品对温湿度要求较高,需要在车间内安装空调和湿度控制设备,以保证产品质量。
3.2 通风和排风系统:车间内应设置通风和排风系统,保持空气流通,排除有害气体和粉尘,保护工人的身体健康。
3.3 噪音和振动控制:对于产生较大噪音和振动的设备,应采取相应的控制措施,减少对周围环境和工人的影响。
四、人员要求:4.1 培训和教育:对车间工人进行必要的培训和教育,使其熟悉生产工艺和设备操作,提高工作效率和产品质量。
工厂车间合理化建议及措施
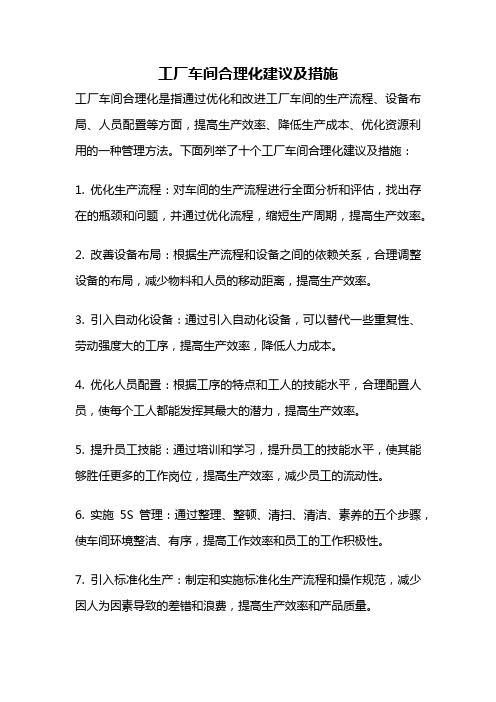
工厂车间合理化建议及措施工厂车间合理化是指通过优化和改进工厂车间的生产流程、设备布局、人员配置等方面,提高生产效率、降低生产成本、优化资源利用的一种管理方法。
下面列举了十个工厂车间合理化建议及措施:1. 优化生产流程:对车间的生产流程进行全面分析和评估,找出存在的瓶颈和问题,并通过优化流程,缩短生产周期,提高生产效率。
2. 改善设备布局:根据生产流程和设备之间的依赖关系,合理调整设备的布局,减少物料和人员的移动距离,提高生产效率。
3. 引入自动化设备:通过引入自动化设备,可以替代一些重复性、劳动强度大的工序,提高生产效率,降低人力成本。
4. 优化人员配置:根据工序的特点和工人的技能水平,合理配置人员,使每个工人都能发挥其最大的潜力,提高生产效率。
5. 提升员工技能:通过培训和学习,提升员工的技能水平,使其能够胜任更多的工作岗位,提高生产效率,减少员工的流动性。
6. 实施5S管理:通过整理、整顿、清扫、清洁、素养的五个步骤,使车间环境整洁、有序,提高工作效率和员工的工作积极性。
7. 引入标准化生产:制定和实施标准化生产流程和操作规范,减少因人为因素导致的差错和浪费,提高生产效率和产品质量。
8. 进行定期维护和保养:定期对设备进行维护和保养,确保设备的正常运行和高效率,减少因设备故障而导致的生产停工。
9. 采用先进的生产管理系统:引入先进的生产管理系统,实现生产过程的实时监控和数据分析,及时掌握生产情况,优化生产计划和资源调配。
10. 鼓励员工提出改进建议:建立员工参与和奖励机制,鼓励员工积极参与车间合理化改进,提出改进建议,共同推动车间的持续改善和创新。
通过以上的建议和措施,工厂车间可以实现生产效率的提升、成本的降低、资源的优化利用,从而提高企业的竞争力和可持续发展能力。
同时,这些建议和措施也需要根据具体的工厂和生产情况进行细化和定制化,以实现最佳效果。
工厂合理化建议
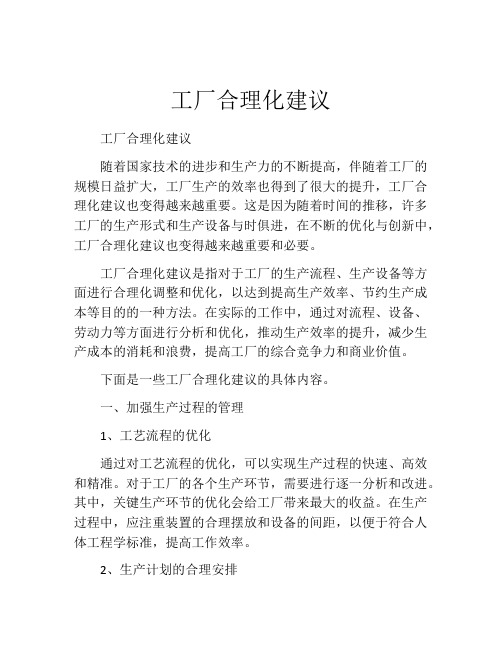
工厂合理化建议工厂合理化建议随着国家技术的进步和生产力的不断提高,伴随着工厂的规模日益扩大,工厂生产的效率也得到了很大的提升,工厂合理化建议也变得越来越重要。
这是因为随着时间的推移,许多工厂的生产形式和生产设备与时俱进,在不断的优化与创新中,工厂合理化建议也变得越来越重要和必要。
工厂合理化建议是指对于工厂的生产流程、生产设备等方面进行合理化调整和优化,以达到提高生产效率、节约生产成本等目的的一种方法。
在实际的工作中,通过对流程、设备、劳动力等方面进行分析和优化,推动生产效率的提升,减少生产成本的消耗和浪费,提高工厂的综合竞争力和商业价值。
下面是一些工厂合理化建议的具体内容。
一、加强生产过程的管理1、工艺流程的优化通过对工艺流程的优化,可以实现生产过程的快速、高效和精准。
对于工厂的各个生产环节,需要进行逐一分析和改进。
其中,关键生产环节的优化会给工厂带来最大的收益。
在生产过程中,应注重装置的合理摆放和设备的间距,以便于符合人体工程学标准,提高工作效率。
2、生产计划的合理安排生产计划是工厂的核心,包括原材料的采购、生产线的安排、流程设计等。
对于此类工作,需要对工厂生产的周期、生产的速度等进行全面的分析和计算,以便确定生产计划的合理性和可行性。
3、生产过程控制和质量管理生产过程需要严格的控制,以确保产品的质量和安全性。
在此过程中,可以实现设备的自动化、智能化和自诊断,帮助工厂自动化监控生产过程的质量,提高库存周转率和产品的生产效率。
同时也需要加强对产品质量的监控,提高质量管理标准,重视客户对产品的反馈,不断推动工厂的改进和优化。
二、提高生产设备的效率1、设备的效率和稳定性一些不稳定的设备往往在使用过程中存在着较高的故障率,极大程度地影响了生产的效率。
对于此类工作,需要对每个生产设备进行全面的检查和维护,及时地更换损坏的零部件和备用物料,以保证各项设备能够正常运转。
2、设备的自动化和数字化在现代工厂生产流程中,设备的自动化程度和数字化程度越高,生产效率就越高,能够达到更高的生产效益。
精益工厂布局

小组方案PK
方案沙盘模拟
最终方案优化
本阶段通过头脑风暴的方式,以工厂布局的骨架为基础 进行设计,关键是找出不同的设计思路。
三. 工厂布局设计
3.1 布局思路确定---①生产区域设计(生产方式的思考)
1)分类产品族,把能连续流动的工序都整合到一起,构建起新的流水线。 2)无法生产线作业的, 将工序靠近,进行同步化生产,形成类似生产线作业方式。
哪些产品适合生产线作业,哪些适合单工序作业,哪些产品适合定位生产?
三. 工厂布局设计
3.1 布局思路确定--- ①生产区域设计(生产方式的思考)
项目
产线生产方式
单工序生产方式
生产性
生产L/T 在制品库存 材料,部品库存 产品库存 作业空间 进度管理 质量不良管理 对应订单
容易排除不必要的作业动作 容易消除lot 待机及停滞 短 少 少 少 不大 看的见的管理 以一单位发生,容易依此检查 多品种,小批量,短期交货及加强 对订单的变化(追加/紧急/变更)
一. 工厂布局概述
1.2 精益生产的概述---演变
阶段三
A
A
工序1
工序2
A
工序3
生产次序同步,无法先进先出,小批量搬运;单工序作业模式(同步生产)
改善:搬运浪费减少,品质隐患得到改善,在制品减少,生产周期加快
阶段四
A
A
工序1
工序2
工序3
生产次序同步,先进先出,以几箱进行搬运,有生产线的概念本质是单工序作业 改善:搬运浪费消除,品质隐患得到控制,在制品少,生产周期加快
1.3 浪费的概述
制造过多 过早浪费
不良品浪费
加工浪费
七大 浪费
库存浪费 等待浪费
工厂生产线布局的六个优化方法

工厂生产线布局的六个优化方法在一个工厂的生产过程中,生产线布局的合理与否直接影响着生产效率和产品质量。
一个优化的生产线布局可以提高产能、降低成本并提高工作效率。
本文将介绍工厂生产线布局的六个优化方法,以帮助工厂管理者提升生产线效益。
一、流程分析与优化流程分析是评估生产线并找出瓶颈的关键步骤之一。
合理的流程分析可以帮助管理者确定每个工序的作业时长和工艺要求。
通过分析生产线上的每个环节,并针对流程中存在的瓶颈进行优化,可以加快生产流程,缩短工期,提高效率。
二、空间布局合理化工厂空间布局是生产线布局的重要组成部分。
通过合理布置设备和工作站,减少物料和人员的移动距离,可以大大提高生产效率。
布局应尽量缩短物料的路径,确保生产线上不同环节的物料流动尽可能顺畅。
可以采用直线型、U型或者分支型的布局,以适应不同的工厂需求。
三、人力资源优化合理配置人力资源是生产线布局优化的另一个关键点。
通过评估每个工序所需的工人数量和技能要求,管理者可以确定合适的员工配备,并进行培训以提高他们的工作效率。
此外,可以考虑引入自动化设备来减少对人力资源的依赖,提高生产线的自动化程度。
四、物料管理与供应链优化物料管理和供应链优化是生产线布局优化中不可忽视的一部分。
通过合理的物料管理,管理者可以避免物料的浪费和丢失,并确保生产线上的物料供应充足。
同时,加强供应链的管理和协调,减少物料交付时间,可以提高生产线的灵活性和响应能力。
五、质量控制与改进质量控制是生产线布局优化中必不可少的一环。
通过建立有效的质量控制体系,管理者可以实时监测产品的质量,并及时发现并解决质量问题。
同时,工厂应积极倡导员工参与质量改进活动,以不断优化生产线的工艺流程和产品质量。
六、数据分析与迭代改进数据分析和迭代改进是实现持续优化的重要手段。
管理者应定期收集和分析生产线运行数据,如产能、质量问题和生产效率等,并根据数据结果制定相应的改进策略。
通过不断的迭代改进,工厂可以实现生产线的持续优化和提高。
工厂车间的合理化建议

工厂车间的合理化建议一、优化车间布局1. 合理规划车间内各个区域的位置,确保生产流程顺畅,减少物料和人员的移动距离,提高生产效率。
2. 将常用的设备和工具放置在易于取用的位置,避免频繁的移动和搜索,节约时间和人力成本。
3. 设置合理的通道和安全出口,确保车间的安全性和紧急情况下的疏散能力。
二、优化生产流程1. 对车间的生产流程进行分析和改进,消除不必要的环节和瓶颈,提高生产效率。
2. 引入自动化设备和智能化系统,减少人力投入,提高生产效率和质量稳定性。
3. 优化物料供应链管理,确保物料的及时供应和减少库存积压的风险。
4. 实施精益生产和质量管理,不断优化生产过程,减少浪费和次品率。
三、提高员工工作环境和效率1. 优化车间的照明和通风系统,提供良好的工作环境,减少员工的疲劳和错误率。
2. 提供合适的工作工具和设备,减轻员工的体力劳动,提高工作效率。
3. 提供员工培训和技能提升机会,提高员工的专业素质和工作效率。
4. 设置合理的工作时间和休息制度,避免员工的过度劳累和工作失误。
四、优化设备维护和保养1. 制定设备维护计划和标准操作规程,保证设备的正常运行和延长使用寿命。
2. 建立设备故障预警和维修反馈机制,及时发现和解决设备问题,减少停机时间和生产损失。
3. 加强设备保养和清洁工作,保持设备的良好状态,提高生产效率和产品质量。
五、加强车间安全管理1. 建立完善的安全管理制度和操作规程,确保员工的人身安全和车间的安全生产。
2. 提供员工个人防护用品和培训,提高员工的安全意识和应急能力。
3. 定期进行安全隐患排查和检查,及时消除潜在的安全风险。
六、推行节能减排和环保措施1. 优化设备的能源利用和生产流程,降低能耗和排放,提高资源利用效率。
2. 推行循环经济理念,减少废弃物的产生和对环境的影响。
3. 加强车间噪音和污染的治理,提供良好的工作环境和保护员工的身体健康。
七、加强信息化与管理1. 引入车间信息化管理系统,实现生产数据的实时监测和分析,提高生产效率和质量控制能力。
工厂车间合理化建议

工厂车间合理化建议一、优化车间布局1. 合理规划车间内的设备和工作区域,使生产流程更加高效和顺畅。
2. 将常用的设备和工具放置在离工人最近的位置,减少工人的移动时间。
3. 将不同工序的设备和工作区域进行合理划分,避免相互干扰和混乱。
二、改进设备和工具1. 更新老旧设备,采用新技术和自动化设备,提高生产效率和质量。
2. 选择符合工作需求的工具,减轻工人的劳动强度,提高工作效率。
3. 引入智能设备和机器人,减少人力成本,提高生产精度和一致性。
三、优化物料管理1. 建立物料供应链管理系统,确保物料的及时供应和准确配送。
2. 对物料进行分类和标识,便于查找和使用,减少物料搜索时间。
3. 引入物料管理软件,实现物料的自动化管理,避免人为错误和延误。
四、提升员工技能1. 组织培训课程,提升员工的专业知识和技能水平,适应新技术和工作需求。
2. 建立员工轮岗制度,使员工能够掌握多个工序的操作技能,提高工作的灵活性和效率。
3. 鼓励员工提出改进意见和创新思路,激发员工的工作积极性和创造力。
五、改进生产计划和排程1. 制定合理的生产计划,考虑设备利用率、工人的工作强度和物料供应等因素。
2. 使用排程软件,优化生产顺序和时间,减少等待时间和生产周期。
3. 定期评估和调整生产计划,根据市场需求和生产能力的变化进行合理调整。
六、优化质量管理1. 建立完善的质量管理体系,包括质量检测和质量控制措施,确保产品质量达到标准要求。
2. 引入自动化检测设备,提高检测的准确性和效率,减少人为因素对质量的影响。
3. 建立反馈机制,及时处理质量问题,避免不良品的产生和扩散。
七、改善工作环境1. 提供良好的工作环境和设施,包括通风、照明、温度和噪音控制等方面,提高工人的工作舒适度和安全性。
2. 给予员工足够的休息时间和休假制度,减少工人的疲劳和心理压力。
3. 建立员工关怀机制,关注员工的身心健康,提供必要的支持和帮助。
八、推行精益生产1. 引入精益生产理念,优化生产流程,消除浪费,提高生产效率和质量。
关于工厂的合理化建议
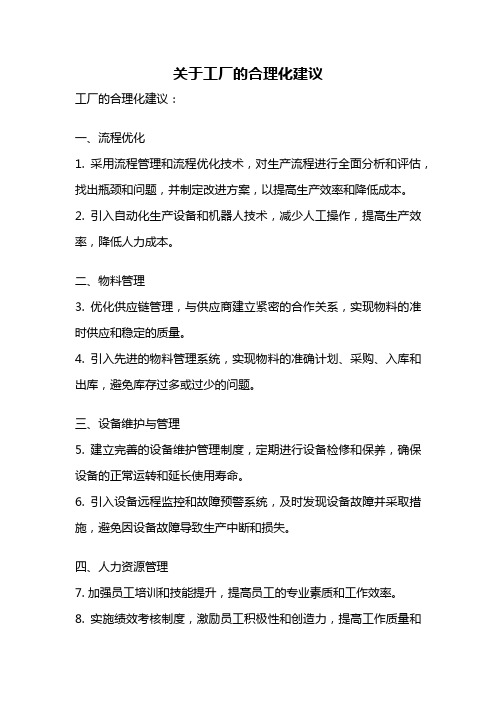
关于工厂的合理化建议工厂的合理化建议:一、流程优化1. 采用流程管理和流程优化技术,对生产流程进行全面分析和评估,找出瓶颈和问题,并制定改进方案,以提高生产效率和降低成本。
2. 引入自动化生产设备和机器人技术,减少人工操作,提高生产效率,降低人力成本。
二、物料管理3. 优化供应链管理,与供应商建立紧密的合作关系,实现物料的准时供应和稳定的质量。
4. 引入先进的物料管理系统,实现物料的准确计划、采购、入库和出库,避免库存过多或过少的问题。
三、设备维护与管理5. 建立完善的设备维护管理制度,定期进行设备检修和保养,确保设备的正常运转和延长使用寿命。
6. 引入设备远程监控和故障预警系统,及时发现设备故障并采取措施,避免因设备故障导致生产中断和损失。
四、人力资源管理7. 加强员工培训和技能提升,提高员工的专业素质和工作效率。
8. 实施绩效考核制度,激励员工积极性和创造力,提高工作质量和效率。
五、质量管理9. 引入全面质量管理体系,从源头上控制产品质量,减少不良品率和退货率。
10. 加强产品检验和测试,确保产品符合质量标准和客户要求。
六、环境保护和安全管理11. 优化生产工艺,减少废气、废水和废物的产生,实现循环利用和资源节约。
12. 加强安全管理,建立完善的安全生产制度和应急预案,确保员工安全和生产设备的正常运行。
七、信息化管理13. 引入企业资源计划(ERP)系统,实现生产、采购、销售等各个环节的信息共享和快速响应。
14. 建立数据分析和决策支持系统,通过数据分析和预测,优化生产计划和资源配置。
八、持续改进15. 建立持续改进机制,定期评估和审查生产流程和管理制度,不断寻找改进的空间和机会,提高工厂的综合竞争力。
总结起来,工厂的合理化建议主要包括流程优化、物料管理、设备维护与管理、人力资源管理、质量管理、环境保护和安全管理、信息化管理以及持续改进等方面。
通过优化各个环节的管理和流程,可以提高生产效率、降低成本、提升产品质量和企业竞争力。
工厂合理化建议例子
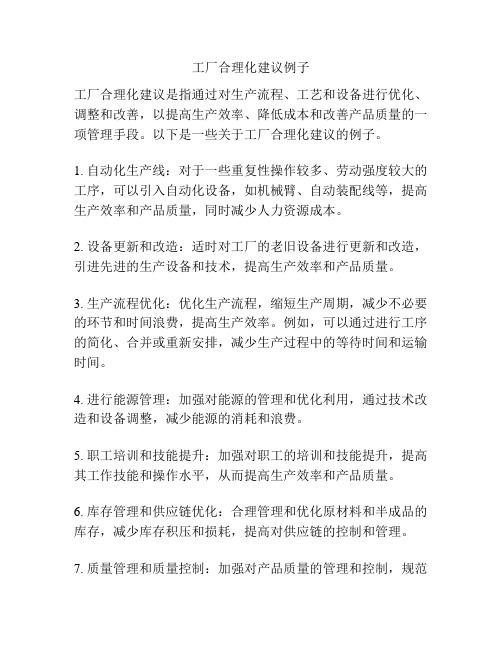
工厂合理化建议例子工厂合理化建议是指通过对生产流程、工艺和设备进行优化、调整和改善,以提高生产效率、降低成本和改善产品质量的一项管理手段。
以下是一些关于工厂合理化建议的例子。
1. 自动化生产线:对于一些重复性操作较多、劳动强度较大的工序,可以引入自动化设备,如机械臂、自动装配线等,提高生产效率和产品质量,同时减少人力资源成本。
2. 设备更新和改造:适时对工厂的老旧设备进行更新和改造,引进先进的生产设备和技术,提高生产效率和产品质量。
3. 生产流程优化:优化生产流程,缩短生产周期,减少不必要的环节和时间浪费,提高生产效率。
例如,可以通过进行工序的简化、合并或重新安排,减少生产过程中的等待时间和运输时间。
4. 进行能源管理:加强对能源的管理和优化利用,通过技术改造和设备调整,减少能源的消耗和浪费。
5. 职工培训和技能提升:加强对职工的培训和技能提升,提高其工作技能和操作水平,从而提高生产效率和产品质量。
6. 库存管理和供应链优化:合理管理和优化原材料和半成品的库存,减少库存积压和损耗,提高对供应链的控制和管理。
7. 质量管理和质量控制:加强对产品质量的管理和控制,规范生产过程和操作流程,提高产品的合格率和一致性。
8. 信息化建设:加强信息化建设,引入先进的信息管理系统和工业互联网技术,实现对工厂生产数据的实时监测和分析,为管理决策提供准确的数据支持。
9. 制定奖惩制度:建立合理的奖惩制度,激励职工积极努力和创新,提高工作效率和质量,同时惩罚违规行为和低效率行为,推动全员参与合理化建议的落实。
10. 绿色生产和环保措施:注重环保意识和环保责任,采取有效的环保措施,减少对环境的污染和破坏,推动工厂向绿色生产方向发展。
以上是一些关于工厂合理化建议的例子,希望能对工厂提高生产效率、降低成本和改善产品质量有所帮助。
- 1、下载文档前请自行甄别文档内容的完整性,平台不提供额外的编辑、内容补充、找答案等附加服务。
- 2、"仅部分预览"的文档,不可在线预览部分如存在完整性等问题,可反馈申请退款(可完整预览的文档不适用该条件!)。
- 3、如文档侵犯您的权益,请联系客服反馈,我们会尽快为您处理(人工客服工作时间:9:00-18:30)。
1993年,康佳进军东北牡丹江(康佳1800万资金+对方 1200万实物),兼并原牡丹江电视机厂,成立牡康公司。
1995年,康佳进军西北,接管陕西如意电视机厂,成立陕 康公司。
1997年,康佳将第3个工厂选在安徽滁州,兼并滁州电视机 厂,成立安康公司。
二.影响选址的因素—自然
(四)自然因素——气候条件、水资源
✓ 气候条件:影响职工健康、工作效率 气温过高/低:工作效率低、厂房设计、空调费用
✓ 水资源 • 耗水量大的企业应靠近水资源:造纸厂、发电厂 • 污染:环保要求,加处理设施
三.案例分析:康佳北上抢滩—背景
1.背景:1992年,位于深圳的康佳集团彩电产量过百万,
三.案例分析:康佳北上抢滩—分析1
2.1993年,康佳进军东北牡丹江,兼并原牡丹江电视机厂( 康佳1800万资金+对方1200实物),成立牡康公司。
选址——制造网络的选址问题
喷油装置
引擎
南威尔士 喷油生产厂
西班牙 引擎装配厂
全球制造
比利时 车体生产厂
一.选址重要性与难度
选址重要性:涉及投资、建设速度、服务成本等
➢投资:建新厂是一大笔投资
✓偏僻山区建厂:“靠山、分散、隐蔽”------比平地建厂投资大( 材料运输)、速度慢,但地价便宜
✓市中心:地价很高
➢成本:不同选址影响提供产品/服务的成本-----影响价格 与竞争力
✓若建在远离原材料供应地方:运输成本高 ✓建在城市:易找合作厂家,但职工工资高
一.选址重要性与难度
职工:不同选址影响职工生活和积极性
➢风俗习惯、气候、生活标准、教育等-----职工生活、子女 教育、家庭,如:内迁厂职工不安心
作用长远:一旦建成,难补救
✓ 运输工具:
5)管道运输:适合定点、量大、单向的流体运输(液体、气体、石 油、天然气)
优点:运量大(720mm管道年运易凝高粘原油2000万吨-----一条 铁路的运量)、连续性强、损耗少、运输安全、占地面积少(多 数埋入地下,水下)、运输费用低、无污染、无装卸包装问题
缺点:品种单一、流向固定
二.影响选址的因素—经济
二.影响选址的因素—经济
厂址接近消费市场企业:
a. 运输不便产品:家具、预制板厂 b. 易变化和变质产品:食品厂、制冰厂 c. 多数服务业:商店、消防队、医院等
二.影响选址的因素—经济
2. 劳动力可获得性
✓ 劳动密集型企业:人工费占产品成本的大部分 a.工厂应在劳动力资源丰富、工资低的地区 b.发达国家在不发达国家设厂 c.工人易训练上岗
➢投资无法回收 ➢厂房不便移动 ➢出售:无人问津
一.选址重要性与难度
选址的难度
➢选址因素相互矛盾:利于营业的地方,地价高 ➢不同决策部门利益不同,追求目标不同。采购部门希望接近
原材料供应商,销售部门希望接近消费商场。 ➢判别标准会随时间变化——当前选址合理,将来不一定好
二.影响选址的因素
选址应使供应链成本最低:
二.影响选址的因素—政治及社会
(二)政治因素——特别在国外建厂
✓ 政治因素:政局稳定、法制、税收 ✓ 风险:在政局不稳地国家建厂 ✓ 法制健全:保护投资者利益
(三)社会因素
✓ 生活习惯:国外流行国内不一定适应 ✓ 文化水平:员工水平、吸引人才 ✓ 经济水平:产品/服务的销路 ✓ 生活条件:员工吸引力
高、受气候影响小,污染比公路少。 缺点:受路线货站限制不够灵活、货损较公路高(震动)
二.影响选址的因素—经济
✓ 运输工具:
2)水路运输:最便宜、速度最慢 优点:运量大(56万吨油轮)、航道设施投资省、不 占用农田、运费低(运输成本为铁路的1/25~1/20,公路 的1/100)——适合原材料和大宗物资的运输 缺点:受河道港口限制不灵活、航速慢、易受季节气候限制
目录
生产与服务设施选址 厂房&生产线布置 物流管理系统设计 精益型生产单元布局
生产与服务设施选址
一.选址重要性与难度
设施选址(Facility location):确定在何处建厂或 服务设施
✓人类祖先居住洞穴选址:风水 ✓第一个研究制造活动选址:德国经济学家Weber ✓90年代经济全球化:全球范围选址,不再是单一工厂
理想厂址:选水、路、空都方便的地方;粗大笨重产品应靠 近铁路车站;出口产品应靠近码头。 厂址接近原材料产地企业: a. 原材料笨重而价格低廉的企业:砖瓦厂、水泥厂、玻璃
厂、钢铁冶炼厂、木材厂等 b. 原材料易变质的企业:水果、蔬菜罐头厂 c. 原料笨重,产品由原料中一小部分提炼而成:制糖、金
属选矿 原料运输不便:屠宰厂
二.影响选址的因素—经济
✓运输工具:
3)航空运输:长途运输,贵重物品、精密仪器、鲜活物资 优点:速度最快(800~900km/h,较汽车快5 ~10倍,比船快
20~30倍) 距离越长节约时间越多、不受地形限制、对货物 包装要求低、舒适、安全、基本建设(买飞机、建机场)投资 少周期短(较铁路、公路)、占地少、适用面广(客货、急救、 农、林、鱼) 缺点:成本最高、运量小、受天气影响大
➢服务企业:设施应靠近顾客 ➢水泥厂:靠近原材料
选址约束:供应链上许多企业、顾客已经存在,难以 平衡各实体需求
选址需考虑因素:经济、政治、社会、自然因素
二.影响选址的因素—经济
(一)经济因素
1.运输条件 ✓ 运输工具:
1)铁路运输:长途、大量运输主要方式 优点:运量大、运价低、运距长,速度快、安全、可靠性
二.影响选址的因素—经济
✓ 运输工具:
4)公路运输:适合短途、高价值、限时急需运送的货物 优点:机动灵活(随时调拨、到处停靠)、受地形、气候
(较飞机、船)影响小 缺点:运量小(客运:3-4人或数十人。货运:3-5T或数十T)、效率
低、成本高、安全性差(路况、驾驶员、车种)。
二.影响选址的因素—经济
✓ 需大量专门技术人员的企业:员工技术、业务能力影响产品 质量和产量,必须考虑劳动力可获得性与费用
二.影响选址的因素—经济
3.能源可获得性与费用:
能耗大户:钢铁、火力发电,靠近动力、燃料供应地
4.厂址条件与费用:地理位置
✓ 平地建厂:比山区建厂易施工、造价低 ✓ 地震区:建筑物抗震要求 ✓ 滑坡、流沙地:防范措施 ✓ 尽量不占耕地:投资与资源问题