注塑成型—TPU成型工艺
TPU成型工艺指导

TPU注塑成型TPU模塑成型工艺有多种方法:包括有注塑、吹塑、压缩成型、挤出成型等,其中以注塑最为常用。
注塑的功能是将TPU加工成所要求的制件,分成预塑、注射和机出三个阶段的不连续过程。
注射击机分柱塞式和螺杆式两种,推荐使用螺杆式注射机,因为它有提供均匀的速度、塑化和熔融。
1、注射机的设计注射机料筒衬以铜铝合金,螺杆镀铬防止磨损。
螺杆长径比L/D=16~20为好,至少15;压缩比2.5/1〜3.0/1。
给料段长度0.5L,压缩段0.3L,计量段0.2L。
应将止逆环装在靠近螺杆顶端的地方,防止反流并保持最大压力。
加工TPU宜用自流喷嘴,出口为倒锥形,喷嘴口径4mm以上,小于主流道套环入口0.68mm,喷嘴应装有可控加热带以防止材料凝固。
从经济角度考虑,注射量应为额定量的40%〜80%。
螺杆转速20〜50r/min。
2、模具设计模具设计就注意以下几点:(1)模塑TPU制件的收缩率收缩受原料的硬度、制件的厚度、形状、成型温度和模具温度等模塑条件的影响。
通常收缩率范围为0.005〜0.020cm/cm。
例如,100X10X2mm的长方形试片,在长度方向浇口,流动方向上收缩,硬度75A比60D 大2〜3倍。
TPU硬度、制作厚度对收缩率的影响见图1。
可见TPU硬度在78A〜90A之间时,制件收缩率随厚度增加而下降;硬度在95A〜74D时制件收缩率随厚度增加而略有增加。
(2)流道和冷料穴主流道是模具中连接注射机喷嘴至分流道或型腔的一段通道,直径应向内扩大,呈2。
以上的角度,以便于流道赘物脱模。
分流道是多槽模中连接主流道和各个型腔的通道,在塑模上的排列应呈对称和等距分布。
流道可为圆形、半圆形、长方形,直径以6~9mm为宜。
流道表面必须像模腔一样抛光,以减少流动阻力,并提供较快的充模速度。
冷料穴是设在主流道末端的一个空穴,用以捕集喷嘴端部两次注射之间所产生的冷料,从而防止分流道或浇口堵塞。
冷料混入型腔,制品容易产生内应力。
热塑性聚氨酯(TPU)注塑加工

热塑性聚氨酯(TPU)注塑加工摘要:本文对热塑性聚氨酯(Polyurethane Thermoplastic)的化学结构与性能之间的关系进行了较系统的论述,在此基础上,介绍了TPU注塑模具的设计及注塑成型工艺方面的注意事项,供相关技术人员参考。
关键词:热塑性聚氨酯(TPU)、软链段、硬链段、虚交联、缩水率、浇铸系统、加工温度。
何为聚氨酯?所谓的聚氨酯是聚氨基甲酸酯的简称,它是由多异氰酸酯与多元醇反应而成,在分子链上含有许多重复的氨基甲酸酯基团(—NH—CO—O—)。
在实际合成的聚氨酯树脂中,除了氨基甲酸酯基团外,还有脲、缩二脲等基团。
大分子多元醇与二异氰酸酯反应生成的链段称为“软链段”,它赋予聚氨酯较好的软顺性;多异氰酸酯与扩链剂生成的链段称为“硬链段”,它赋予聚氨酯较好的刚性与硬度。
软硬链段组成的聚氨酯树脂中,氨基甲酸酯只占少数,所以称为聚氨酯未必恰当,从广义上讲,聚氨酯乃至异氰酸酯的加聚物。
不同类型的异氰酸酯与多羟基化合物反应后,生成各种结构的聚氨酯,从而获得不同性质的高分子材料,如塑料、橡胶、涂料、纤维、粘合剂等。
聚氨酯橡胶聚氨酯橡胶于1940年首先在德国研制成功,1952年后开始投入工业生产,而我国是从60年代中期开始研制并投入生产的。
聚氨酯橡胶属于一种特种橡胶,由聚醚或聚酯与异氰酸酯反应而制得。
因原料种类、反应条件及交联方法的不同而有许多品种。
从化学结构上看,有聚醚型与聚酯型,从加工方法上看,有混炼型、浇注型、和热塑型三种。
合成聚氨酯橡胶,一般先由线型聚酯或聚醚与二异氰酯酯反应,制成低分子量的预聚体,经扩链反应生成高分子聚合物,然后添加适当的交联剂,加热使其固化,成为硫化橡胶,这种方法称为预聚法或二步法。
也可以用一步法——将线型聚酯或聚醚直接与二异氰酸酯、扩链剂、交联剂混合,使反应发生,生成聚氨酯橡胶。
热塑性聚氨酯橡胶(TPU)热塑性聚氨酯橡胶(TPU)是一种(AB)n型嵌段线性聚合物,A代表高分子量的聚酯或聚醚(分子量为1000~6000),称为长链,B代表含2~12个直链碳原子二醇为短链,AB链段间化学结合是用二异氰酸酯。
TPU注塑成型加工工艺指南

TPU注塑成型加⼯⼯艺指南1注塑成型机 TPU 材料⽤普通的螺杆注射机就可满⾜成型要求,采⽤柱塞式注射机也可加⼯。
但加⼯较⼤的制件时,建议采⽤往复螺杆式注射成型机。
注射成型机能⼒应⽐成型制品容量⼤ 40%才是最适宜的。
2注塑成型加⼯⼯艺成型温度 TPU 注射成型温度主要由硬度决定,表 1 是参考成型温度,加⼯时必须依据注射成型机种类、螺杆类型、螺杆转速、模具图案设计等稍有差别,需要参考表 1给出的成型温度加以调整。
TPU 与软质 PVC、ABS ⽐较,熔融粘度对温度的依存性⼤。
温度过⾼则粘度降低,树脂易流动,容易产⽣溢料、孔隙、凸凹收缩等不良现象;温度过低则粘度增⾼,流动困难,容易造成充料不⾜,得不到完美的成型品。
加⼯参数除了注射成型温度外,其他加⼯参数参考表 2。
注射速度 ⼀般可采⽤低速注射,注射时间 15~20 秒,⼀次压⼒作⽤ 10 秒左右,⼆次压⼒再增加5~10 秒,是⼀般通⽤树脂 1.5~2 倍,TPU 硬度越低,注射时间越长。
根据模具温度、材质及其图案设计等不同,冷却时间有必要增加 20~40 秒,⽐⼀般通⽤树脂的长1.5~2 倍。
3模具模具温度 模具温度最好控制在 20~40℃,建议采⽤⽔循环⽅式。
对于表⾯积⼤⽽截⾯积⼩的薄⽚型制品,⼀般需要把模具加热⾄ 40~60℃成型。
浇⼝、流道、节流孔 TPU 在浇⼝、流道、节流孔⽅⾯没有特别的限制,⽤长⽅形、圆形、半圆形流道都可以,浇⼝粗、倾⾓⼤的模具在脱模时⼗分⽅便。
⼀般来说,浇⼝、流道、节流孔设计不妨考虑⽐通⽤树脂的⼤些。
但需注意在采⽤点状孔隙节流孔时,孔直径要⼤于 Ф0.7 ㎜,否则树脂填充不好,得不到好的制品。
图 3 为节流孔尺⼨参考图,是以 WHT-1190 的成型品重量与节流孔截⾯积之间关系为例。
脱模器 脱模器可采⽤套筒式,在脱模器上开出排⽓槽是很有效的。
排⽓ 在 TPU 注射成型中,排⽓⼗分重要。
脱⽓不充分的情况下,可能产⽣疤痕、混⼊⽓泡等问题。
TPU注塑成型工艺
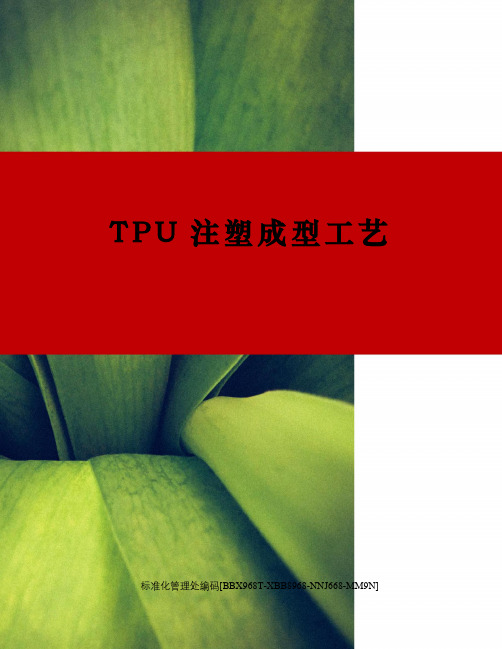
T P U注塑成型工艺标准化管理处编码[BBX968T-XBB8968-NNJ668-MM9N]TPU注塑成型工艺TPU模塑成型工艺有多种方法:包括有注塑、吹塑、压缩成型、挤出成型等,其中以注塑最为常用。
注塑的功能是将TPU加工成所要求的制件,分成预塑、注射和机出三个阶段的不连续过程。
注射击机分柱塞式和螺杆式两种,推荐使用螺杆式注射机,因为它有提供均匀的速度、塑化和熔融。
1、注射机的设计注射机料筒衬以铜铝合金,螺杆镀铬防止磨损。
螺杆长径比L/D=16~20为好,至少15;压缩比1~1。
给料段长度,压缩段,计量段。
应将止逆环装在靠近螺杆顶端的地方,防止反流并保持最大压力。
加工TPU宜用自流喷嘴,出口为倒锥形,喷嘴口径4mm以上,小于主流道套环入口,喷嘴应装有可控加热带以防止材料凝固。
从经济角度考虑,注射量应为额定量的40%~80%。
螺杆转速20~50r/min。
2、模具设计模具设计就注意以下几点:(1)模塑TPU制件的收缩率收缩受原料的硬度、制件的厚度、形状、成型温度和模具温度等模塑条件的影响。
通常收缩率范围为~cm。
例如,100×10×2mm的长方形试片,在长度方向浇口,流动方向上收缩,硬度75A比60D大2~3倍。
TPU硬度、制作厚度对收缩率的影响见图1。
可见TPU 硬度在78A~90A之间时,制件收缩率随厚度增加而下降;硬度在95A~74D时制件收缩率随厚度增加而略有增加。
(2)流道和冷料穴主流道是模具中连接注射机喷嘴至分流道或型腔的一段通道,直径应向内扩大,呈2o以上的角度,以便于流道赘物脱模。
分流道是多槽模中连接主流道和各个型腔的通道,在塑模上的排列应呈对称和等距分布。
流道可为圆形、半圆形、长方形,直径以6~9mm为宜。
流道表面必须像模腔一样抛光,以减少流动阻力,并提供较快的充模速度。
冷料穴是设在主流道末端的一个空穴,用以捕集喷嘴端部两次注射之间所产生的冷料,从而防止分流道或浇口堵塞。
注塑成型—TPU成型工艺
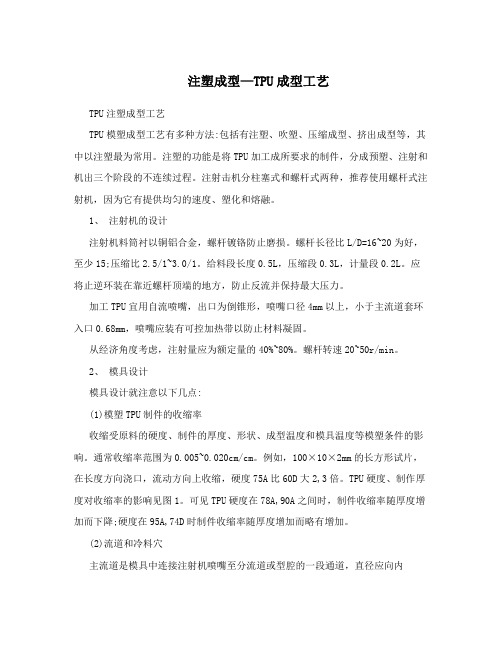
注塑成型—TPU成型工艺TPU注塑成型工艺TPU模塑成型工艺有多种方法:包括有注塑、吹塑、压缩成型、挤出成型等,其中以注塑最为常用。
注塑的功能是将TPU加工成所要求的制件,分成预塑、注射和机出三个阶段的不连续过程。
注射击机分柱塞式和螺杆式两种,推荐使用螺杆式注射机,因为它有提供均匀的速度、塑化和熔融。
1、注射机的设计注射机料筒衬以铜铝合金,螺杆镀铬防止磨损。
螺杆长径比L/D=16~20为好,至少15;压缩比2.5/1~3.0/1。
给料段长度0.5L,压缩段0.3L,计量段0.2L。
应将止逆环装在靠近螺杆顶端的地方,防止反流并保持最大压力。
加工TPU宜用自流喷嘴,出口为倒锥形,喷嘴口径4mm以上,小于主流道套环入口0.68mm,喷嘴应装有可控加热带以防止材料凝固。
从经济角度考虑,注射量应为额定量的40%~80%。
螺杆转速20~50r/min。
2、模具设计模具设计就注意以下几点:(1)模塑TPU制件的收缩率收缩受原料的硬度、制件的厚度、形状、成型温度和模具温度等模塑条件的影响。
通常收缩率范围为0.005~0.020cm/cm。
例如,100×10×2mm的长方形试片,在长度方向浇口,流动方向上收缩,硬度75A比60D大2,3倍。
TPU硬度、制作厚度对收缩率的影响见图1。
可见TPU硬度在78A,90A之间时,制件收缩率随厚度增加而下降;硬度在95A,74D时制件收缩率随厚度增加而略有增加。
(2)流道和冷料穴主流道是模具中连接注射机喷嘴至分流道或型腔的一段通道,直径应向内o扩大,呈2以上的角度,以便于流道赘物脱模。
分流道是多槽模中连接主流道和各个型腔的通道,在塑模上的排列应呈对称和等距分布。
流道可为圆形、半圆形、长方形,直径以6~9mm为宜。
流道表面必须像模腔一样抛光,以减少流动阻力,并提供较快的充模速度。
冷料穴是设在主流道末端的一个空穴,用以捕集喷嘴端部两次注射之间所产生的冷料,从而防止分流道或浇口堵塞。
TPU注塑成型工艺

TPU注塑成型工艺TPU的硬度通常是用国际认可的邵氏硬度来表示,一般情况下100度以下都用A表示,比如80A,90A,95A,98A等,100度以上都用D表示,比如:50D,60D,64D,71D,74D等。
TPU模塑成型工艺有多种方法:包括有注塑、吹塑、压缩成型、挤出成型等,其中以注塑最为常用。
注塑的功能是将TPU加工成所要求的制件,分成预塑、注射和机出三个阶段的不连续过程。
注射击机分柱塞式和螺杆式两种,推荐使用螺杆式注射机,因为它有提供均匀的速度、塑化和熔融。
1、注射机的设计注射机料筒衬以铜铝合金,螺杆镀铬防止磨损。
螺杆长径比L/D=16~20为好,至少15;压缩比2.5/1~3.0/1。
给料段长度0.5L,压缩段0.3L,计量段0.2L。
应将止逆环装在靠近螺杆顶端的地方,防止反流并保持最大压力。
加工TPU宜用自流喷嘴,出口为倒锥形,喷嘴口径4mm以上,小于主流道套环入口0.68mm,喷嘴应装有可控加热带以防止材料凝固。
从经济角度考虑,注射量应为额定量的40%~80%。
螺杆转速20~50r/min。
2、模具设计模具设计就注意以下几点:(1)模塑TPU制件的收缩率收缩受原料的硬度、制件的厚度、形状、成型温度和模具温度等模塑条件的影响。
通常收缩率范围为0.005~0.020cm/cm。
例如,100×10×2mm的长方形试片,在长度方向浇口,流动方向上收缩,硬度75A比60D大2~3倍。
TPU硬度、制作厚度对收缩率的影响见图1。
可见TPU硬度在78A~90A之间时,制件收缩率随厚度增加而下降;硬度在95A~74D时制件收缩率随厚度增加而略有增加。
(2)流道和冷料穴主流道是模具中连接注射机喷嘴至分流道或型腔的一段通道,直径应向内扩大,呈2o以上的角度,以便于流道赘物脱模。
分流道是多槽模中连接主流道和各个型腔的通道,在塑模上的排列应呈对称和等距分布。
流道可为圆形、半圆形、长方形,直径以6~9mm为宜。
TPU注塑成型工艺

注射速度主要决定于TPU制品的构型。端面厚的制品需要较低的注射速度,端面薄则注射速度较快。
e.螺杆转速
加工TPU制品通常需要低剪切速率,因而以较低的螺杆转速为宜。TPU的螺杆转速一般为20~80r/min,则优选20~40r/min。
(4)停机处理
由于TPU高温下延长时间可能发生降解,故在关机后,应该用PS、PE、丙烯酸酯类塑料或ABS清洗;停机超过1小时,应该关闭加热。
????熔融温度太高或太低????调整熔融温度
注料
量不
足????给料不足????调整给料
????浇口太小????增加浇口尺寸????????过早凝固????提高模具温度
????浇口接合区太长????降低浇口接合区长度????????料筒温度太低????提高料筒温度
????模具温度太低????提高熔融温度????????注射压力太低????增加注射压力
麻孔
气泡或缩Βιβλιοθήκη 皱纹????注射压力太低????增加注射压力????????注射时间短????增加注射时间
????材料过热????降低料筒温度????????喷嘴孔、流道或浇口,尺寸不足????调整喷嘴、流道和浇口尺寸
????模具温度太低????提高模具温度
????给料不足????调整给料????翘曲????注射压力太低????增加注射压力
在剪切速率不变的条件下,粘度随温度增加而下降,但在高剪切速率下,粘度受温度的影响不像低剪切速率那样大。TPU的注射压力一般为20~110MPa。保压压力大约为注射压力的一半,背压应在1。4MPa以下,以使TPU塑化均匀。
c.时间
完成一次注射过程所需的时间称为成型周期。成型周期包括充模时间、保压时间、冷却时间和其他时间(开模、脱模、闭模等),直接影响劳动生产率和设备利用率。TPU的成型周期通常决定于硬度、制件厚度和构型,TPU硬度高周期短,塑件厚周期长,塑件构型复杂周期长,成型周期还与模具温度有关。TPU成型周期一般在20~60s之间。
TPU注塑成型工艺

TPU注塑成型工艺(第1页)TPU模塑成型工艺有多种方法:包括有注塑、吹塑、压缩成型、挤出成型等,其中以注塑最为常用。
注塑的功能是将TPU加工成所要求的制件,分成预塑、注射和机出三个阶段的不连续过程。
注射击机分柱塞式和螺杆式两种,推荐使用螺杆式注射机,因为它有提供均匀的速度、塑化和熔融。
1、注射机的设计注射机料筒衬以铜铝合金,螺杆镀铬防止磨损。
螺杆长径比L/D=16~20为好,至少15;压缩比2.5/1~3.0/1。
给料段长度0.5L,压缩段0.3L,计量段0.2L。
应将止逆环装在靠近螺杆顶端的地方,防止反流并保持最大压力。
加工TPU宜用自流喷嘴,出口为倒锥形,喷嘴口径4m m以上,小于主流道套环入口0.68mm,喷嘴应装有可控加热带以防止材料凝固。
从经济角度考虑,注射量应为额定量的40%~80%。
螺杆转速20~50r/min。
2、模具设计模具设计就注意以下几点:(1)模塑TPU制件的收缩率收缩受原料的硬度、制件的厚度、形状、成型温度和模具温度等模塑条件的影响。
通常收缩率范围为0.005~0.020cm/cm。
例如,100×10×2mm的长方形试片,在长度方向浇口,流动方向上收缩,硬度75A比60D大2~3倍。
TPU硬度、制作厚度对收缩率的影响见图1。
可见TPU硬度在78A~90A之间时,制件收缩率随厚度增加而下降;硬度在95A~74D时制件收缩率随厚度增加而略有增加。
(2)流道和冷料穴主流道是模具中连接注射机喷嘴至分流道或型腔的一段通道,直径应向内扩大,呈2o以上的角度,以便于流道赘物脱模。
分流道是多槽模中连接主流道和各个型腔的通道,在塑模上的排列应呈对称和等距分布。
流道可为圆形、半圆形、长方形,直径以6~9mm为宜。
TPU注塑成型工艺

T P U注塑成型工艺TPU模塑成型工艺有多种方法:包括有注塑、吹塑、压缩成型、挤出成型等,其中以注塑最为常用。
注塑的功能是将TPU加工成所要求的制件,分成预塑、注射和机出三个阶段的不连续过程。
注射击机分柱塞式和螺杆式两种,推荐使用螺杆式注射机,因为它有提供均匀的速度、塑化和熔融。
1、?注射机的设计注射机料筒衬以铜铝合金,螺杆镀铬防止磨损。
螺杆长径比L/D=16~20为好,至少15;压缩比2.5/1~3.0/1。
给料段长度0.5L,压缩段0.3L,计量段0.2L。
应将止逆环装在靠近螺杆顶端的地方,防止反流并保持最大压力。
加工TPU宜用自流喷嘴,出口为倒锥形,喷嘴口径4mm以上,小于主流道套环入口0.68mm,喷嘴应装有可控加热带以防止材料凝固。
从经济角度考虑,注射量应为额定量的40%~80%。
螺杆转速20~50r/min。
2、?模具设计模具设计就注意以下几点:(1)模塑TPU制件的收缩率收缩受原料的硬度、制件的厚度、形状、成型温度和模具温度等模塑条件的影响。
通常收缩率范围为0.005~0.020cm/cm。
例如,100×10×2mm的长方形试片,在长度方向浇口,流动方向上收缩,硬度75A比60D大2~3倍。
TPU硬度、制作厚度对收缩率的影响见图1。
可见TPU硬度在78A~90A之间时,制件收缩率随厚度增加而下降;硬度在95A~74D时制件收缩率随厚度增加而略有增加。
(2)流道和冷料穴主流道是模具中连接注射机喷嘴至分流道或型腔的一段通道,直径应向内扩大,呈2o以上的角度,以便于流道赘物脱模。
分流道是多槽模中连接主流道和各个型腔的通道,在塑模上的排列应呈对称和等距分布。
流道可为圆形、半圆形、长方形,直径以6~9mm为宜。
流道表面必须像模腔一样抛光,以减少流动阻力,并提供较快的充模速度。
冷料穴是设在主流道末端的一个空穴,用以捕集喷嘴端部两次注射之间所产生的冷料,从而防止分流道或浇口堵塞。
TPU注塑成型加工工艺指引
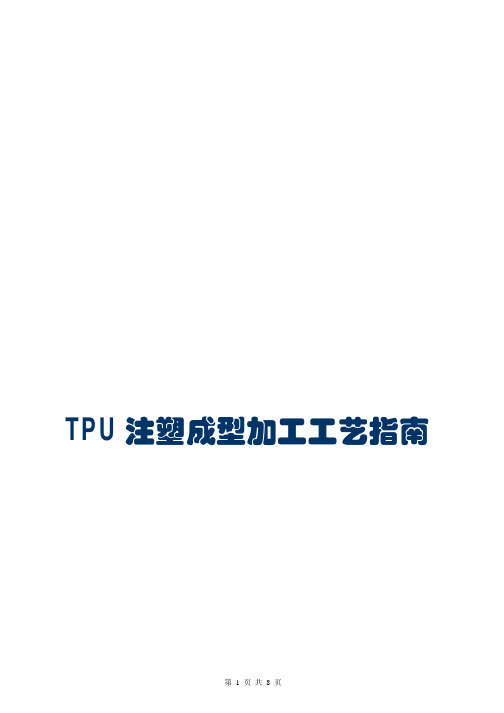
TPU注塑成型加工工艺指南一、注塑成型机TPU材料用普通的螺杆注射机就可满足成型要求,采用柱塞式注射机也可加工。
但加工较大的制件时,建议采用往复螺杆式注射成型机。
注射成型机能力应比成型制品容量大40%才是最适宜的。
二、注塑成型加工工艺成型温度:TPU注射成型温度主要由硬度决定,表1是参考成型温度,客户加工时必须依据注射成型机种类、螺杆类型、螺杆转速、模具图案设计等稍有差别,需要客户参考表1给出的成型温度加以调整。
表1 TPU成型温度参考硬度(邵A)后部中部前部喷嘴70 130℃150℃160℃160℃80 150℃170℃180℃175℃85 160℃175℃180℃180℃90 160℃180℃190℃185℃95 170℃190℃200℃195℃98 180℃195℃210℃200℃TPU与软质PVC、ABS比较,熔融粘度对温度的依存性大。
温度过高则粘度降低,树脂易流动,容易产生溢料、孔隙、凸凹收缩等不良现象;温度过低则粘度增高,流动困难,容易造成充料不足,得不到完美的成型品。
加工参数:除了注射成型温度外,其他加工参数参考表2。
表2 注射加工参数参考项目操作条件注射压力80~120㎏f/c㎡(表压70~110㎏/c㎡)注射速度比一般通用树脂慢螺杆转速50~100 rpm背压6~24㎏f/c㎡(表压5~20㎏/c㎡)保压60~80㎏f/c㎡(表压50~70㎏/c㎡)冷却时间一般通用树脂的1.2~2倍模具温度一般为室温注射速度:一般可采用低速注射,注射时间15~20秒,一次压力作用10秒左右,二次压力再增加5~10秒,是一般通用树脂1.5~2倍,TPU硬度越低,注射时间越长。
根据模具温度、材质及其图案设计等不同,冷却时间有必要增加20~40秒,比一般通用树脂的长1.5~2倍。
三、模具模具温度:模具温度最好控制在20~40℃,建议采用水循环方式。
对于表面积大而截面积小的薄片型制品,一般需要把模具加热至40~60℃成型。
TPU注塑成型工艺29618

TPU注塑成型工艺TPU的硬度通常是用国际认可的邵氏硬度来表示,一般情况下100度以下都用A表示,比如80A,90A,95A,98A等,100度以上都用D表示,比如:50D,60D,64D,71D,74D等。
TPU模塑成型工艺有多种方法:包括有注塑、吹塑、压缩成型、挤出成型等,其中以注塑最为常用。
注塑的功能是将TPU加工成所要求的制件,分成预塑、注射和机出三个阶段的不连续过程。
注射击机分柱塞式和螺杆式两种,推荐使用螺杆式注射机,因为它有提供均匀的速度、塑化和熔融。
1、注射机的设计注射机料筒衬以铜铝合金,螺杆镀铬防止磨损。
螺杆长径比L/D=16~20为好,至少15;压缩比2.5/1~3.0/1。
给料段长度0.5L,压缩段0.3L,计量段0.2L。
应将止逆环装在靠近螺杆顶端的地方,防止反流并保持最大压力。
加工TPU宜用自流喷嘴,出口为倒锥形,喷嘴口径4mm以上,小于主流道套环入口0.68mm,喷嘴应装有可控加热带以防止材料凝固。
从经济角度考虑,注射量应为额定量的40%~80%。
螺杆转速20~50r/min。
2、模具设计模具设计就注意以下几点:(1)模塑TPU制件的收缩率收缩受原料的硬度、制件的厚度、形状、成型温度和模具温度等模塑条件的影响。
通常收缩率范围为0.005~0.020cm/cm。
例如,100×10×2mm的长方形试片,在长度方向浇口,流动方向上收缩,硬度75A比60D大2~3倍。
TPU硬度、制作厚度对收缩率的影响见图1。
可见TPU硬度在78A~90A之间时,制件收缩率随厚度增加而下降;硬度在95A~74D时制件收缩率随厚度增加而略有增加。
(2)流道和冷料穴主流道是模具中连接注射机喷嘴至分流道或型腔的一段通道,直径应向内扩大,呈2o以上的角度,以便于流道赘物脱模。
分流道是多槽模中连接主流道和各个型腔的通道,在塑模上的排列应呈对称和等距分布。
流道可为圆形、半圆形、长方形,直径以6~9mm为宜。
TPU注塑成型工艺

TPU注塑成型工艺TPU的硬度通常是用国际认可的邵氏硬度来表示,一般情况下100度以下都用A表示,比如80A,90A,95A,98A等,100度以上都用D表示,比如:50D,60D,64D,71D,74D等。
TPU模塑成型工艺有多种方法:包括有注塑、吹塑、压缩成型、挤出成型等,其中以注塑最为常用。
注塑的功能是将TPU加工成所要求的制件,分成预塑、注射和机出三个阶段的不连续过程。
注射击机分柱塞式和螺杆式两种,推荐使用螺杆式注射机,因为它有提供均匀的速度、塑化和熔融。
1、注射机的设计注射机料筒衬以铜铝合金,螺杆镀铬防止磨损。
螺杆长径比L/D=16~20为好,至少15;压缩比2.5/1~3.0/1。
给料段长度0.5L,压缩段0.3L,计量段0.2L。
应将止逆环装在靠近螺杆顶端的地方,防止反流并保持最大压力。
加工TPU宜用自流喷嘴,出口为倒锥形,喷嘴口径4mm以上,小于主流道套环入口0.68mm,喷嘴应装有可控加热带以防止材料凝固。
从经济角度考虑,注射量应为额定量的40%~80%。
螺杆转速20~50r/min。
2、模具设计模具设计就注意以下几点:(1)模塑TPU制件的收缩率收缩受原料的硬度、制件的厚度、形状、成型温度和模具温度等模塑条件的影响。
通常收缩率围为0.005~0.020cm/cm。
例如,100×10×2mm的长方形试片,在长度方向浇口,流动方向上收缩,硬度75A比60D大2~3倍。
TPU硬度、制作厚度对收缩率的影响见图1。
可见TPU硬度在78A~90A之间时,制件收缩率随厚度增加而下降;硬度在95A~74D时制件收缩率随厚度增加而略有增加。
(2)流道和冷料穴主流道是模具中连接注射机喷嘴至分流道或型腔的一段通道,直径应向扩大,呈2o以上的角度,以便于流道赘物脱模。
分流道是多槽模中连接主流道和各个型腔的通道,在塑模上的排列应呈对称和等距分布。
流道可为圆形、半圆形、长方形,直径以6~9mm为宜。
tpu注塑碗型的工艺

TPU(热塑性聚氨酯)的注塑成型工艺主要包括以下步骤:
1. 干燥:干燥预热后的TPU粒料从注塑机料斗输送进加热的料筒,此步骤是为了确保成型过程中不会出现不良的成型效果。
2. 塑化:当TPU粒料在加热的料筒中呈熔融状态时,螺杆(或柱塞)的推进作用及料筒前端的喷嘴注射进入温度相对较低的闭合模具中。
3. 注射:熔融状态的TPU在注射到模具的型腔内,充满模腔,并在受压下冷却固化。
4. 冷却:制品在模具内冷却后脱模,获得与模型型腔相同的TPU产品。
需要注意的是,从TPU注塑成型工艺来看,其产品最重要的模塑条件是影响塑化流动和冷却的温度、压力和时间。
因此,注塑机必须具备精确的温度调节和控制系统,否则会因各种因素造成制品缺陷。
tpu注塑成型工艺

tpu注塑成型工艺
TPU注塑成型工艺是利用热塑性聚氨酯材料(TPU)进行注塑成型的生产工艺。
TPU注塑成型工艺主要由以下几个步骤组成:
1.准备原料:将TPU颗粒料按照一定比例混配,通常还会添加一些填充料、增韧剂、分散剂等辅助材料。
2.熔融:将配好的TPU颗粒料放入注塑机的料斗中,通过加热和搅拌使其熔化成为熔融体。
3.注射:将熔融的TPU通过注塑机的注射系统注入到模具腔中,通常需要控制好注射压力、注射速度和注射时间等参数。
4.冷却:在模具中冷却一段时间,使注塑成型的TPU材料快速固化。
5.顶出:打开模具,将已经成型的TPU制品从模具中顶出。
6.修整:对于有些制品,可能需要进行修整和后续加工,如去毛刺、修整边角、打磨光洁等。
7.质检:对注塑成型的TPU制品进行质量检验和检测,确保其达到相关标准和要求。
TPU注塑成型工艺具有制程简单、生产效率高、制品尺寸精
度高、成本相对较低等优点。
它广泛应用于汽车、电子、家电、玩具、鞋材等行业中,制造出各种形状复杂、功能多样的
TPU制品。
tpu成型工艺

tpu成型工艺
TPU(热塑性聚氨酯)是一种高强度、高耐磨、高韧性的聚合物材料,广泛应用于汽车、运动鞋、户外装备等领域。
在制造TPU制品时,需要采用TPU成型工艺。
TPU成型工艺包括以下几个步骤:
1. 原料准备
首先需要准备好TPU颗粒和其他辅助材料(如增塑剂、稳定剂等)。
这些原料需要经过精确的配比和混合,以确保最终制品的质量。
2. 加热和熔融
将原料放入注塑机或挤出机中进行加热和熔融。
注塑机是一种常用的
设备,它可以将TPU颗粒加热到适当的温度,并通过注射器将熔融的材料注入模具中。
3. 模具设计和制造
模具是制造TPU制品的关键部件,它决定了最终产品的形状和尺寸。
模具设计需要考虑到产品的结构特点和功能需求,并采用合适的材料(如钢铁或铝合金)进行制造。
4. 成型
在模具中注入熔融的TPU材料,经过一定的压力和温度控制,使其在模具中快速冷却和凝固。
这个过程需要注意模具的温度和压力控制,以确保最终产品的质量。
5. 后处理
成型后的TPU制品需要进行一些后处理工作,如去除余料、打磨、清洗等。
这些工作可以提高产品的表面光洁度和整体质量。
以上就是TPU成型工艺的基本步骤。
需要注意的是,不同种类的TPU 制品可能会有不同的成型工艺要求,因此在实际生产中需要根据具体情况进行调整和优化。
总之,TPU成型工艺是制造高质量TPU制品必不可少的环节。
通过科学合理地控制每一个步骤,可以生产出外观美观、性能优异、寿命长久的TPU制品。
TPU注塑成型工艺设计
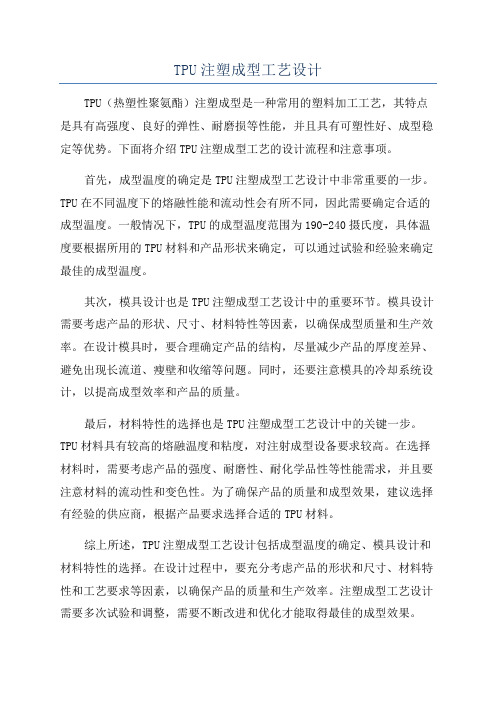
TPU注塑成型工艺设计
TPU(热塑性聚氨酯)注塑成型是一种常用的塑料加工工艺,其特点是具有高强度、良好的弹性、耐磨损等性能,并且具有可塑性好、成型稳定等优势。
下面将介绍TPU注塑成型工艺的设计流程和注意事项。
首先,成型温度的确定是TPU注塑成型工艺设计中非常重要的一步。
TPU在不同温度下的熔融性能和流动性会有所不同,因此需要确定合适的成型温度。
一般情况下,TPU的成型温度范围为190-240摄氏度,具体温度要根据所用的TPU材料和产品形状来确定,可以通过试验和经验来确定最佳的成型温度。
其次,模具设计也是TPU注塑成型工艺设计中的重要环节。
模具设计需要考虑产品的形状、尺寸、材料特性等因素,以确保成型质量和生产效率。
在设计模具时,要合理确定产品的结构,尽量减少产品的厚度差异、避免出现长流道、瘦壁和收缩等问题。
同时,还要注意模具的冷却系统设计,以提高成型效率和产品的质量。
最后,材料特性的选择也是TPU注塑成型工艺设计中的关键一步。
TPU材料具有较高的熔融温度和粘度,对注射成型设备要求较高。
在选择材料时,需要考虑产品的强度、耐磨性、耐化学品性等性能需求,并且要注意材料的流动性和变色性。
为了确保产品的质量和成型效果,建议选择有经验的供应商,根据产品要求选择合适的TPU材料。
综上所述,TPU注塑成型工艺设计包括成型温度的确定、模具设计和材料特性的选择。
在设计过程中,要充分考虑产品的形状和尺寸、材料特性和工艺要求等因素,以确保产品的质量和生产效率。
注塑成型工艺设计需要多次试验和调整,需要不断改进和优化才能取得最佳的成型效果。
tpu成型工艺

TPU成型工艺一、概述TPU(Thermoplastic Polyurethane)是一种热塑性聚氨酯弹性体材料,具有优异的弹性、耐磨、耐油、耐化学品等性能,广泛应用于鞋类、汽车零部件、运动器材等领域。
TPU成型工艺是将TPU颗粒通过热熔、注塑等方式成型为各种产品的过程,本文将对TPU成型工艺进行全面、详细、完整的探讨。
二、TPU成型工艺流程TPU成型工艺一般包括以下几个基本步骤:2.1 原料准备首先需要准备好TPU颗粒,根据产品要求选择合适的TPU材料,并严格控制颗粒的湿度和杂质含量,以确保成品质量。
2.2 热熔将TPU颗粒通过加热的方式熔化成为熔融状态,一般采用高温熔融设备进行加热,熔化温度通常在180℃到250℃之间,具体温度取决于TPU材料的种类和要求。
2.3 成型熔化后的TPU熔融物通过注塑、挤出等方式进行成型,根据不同产品的形状和尺寸,选择合适的成型工艺进行操作。
2.4 冷却成型后的TPU产品需要经过冷却过程,使其固化并保持所需形状。
一般采用水冷或气冷的方式进行冷却,冷却时间和温度需根据产品特性进行调整。
2.5 后处理成型后的TPU产品还需要进行一些后处理,如切割、打磨、清洗等工序,以使其达到最终的使用要求。
三、TPU成型工艺参数控制为了获得高质量的TPU成型产品,需要对成型工艺参数进行严格的控制。
以下是一些常见的参数控制要点:3.1 温度控制TPU成型过程中的温度是一个非常重要的参数。
熔融温度应控制在适当的范围内,过低可能导致无法充分熔化,过高可能导致材料退化。
同时,成型温度和冷却温度的控制也会对产品的物理性能产生影响,需要根据产品的要求进行调整。
3.2 压力控制成型过程中的压力对产品的密实度、强度等性能有直接影响。
过高的压力可能导致产品变形、开裂,过低则可能导致产品成型不完全。
需要根据不同的成型方式和产品要求进行合理的压力控制。
3.3 速度控制成型速度也是一个重要的参数,过快的速度可能导致部分产品位置填充不均匀,过慢则可能导致产能低下。
TPU注塑成型工艺

TPU注塑成型工艺TPU的硬度通常就是用国际认可的邵氏硬度来表示,一般情况下100度以下都用A表示,比如80A,90A,95A,98A等,100度以上都用D表示,比如:50D,60D,64D,71D,74D 等。
TPU模塑成型工艺有多种方法:包括有注塑、吹塑、压缩成型、挤出成型等,其中以注塑最为常用。
注塑的功能就是将TPU加工成所要求的制件,分成预塑、注射与机出三个阶段的不连续过程。
注射击机分柱塞式与螺杆式两种,推荐使用螺杆式注射机,因为它有提供均匀的速度、塑化与熔融。
1、注射机的设计注射机料筒衬以铜铝合金,螺杆镀铭防止磨损。
螺杆长径比L/D=16~20为好,至少15;压缩比2、5/1~3、0/1。
给料段长度0.5L,压缩段0.3L,计量段0.2L。
应将止逆环装在靠近螺杆顶端的地方,防止反流并保持最大压力。
加工TPU宜用自流喷嘴,出口为倒锥形,喷嘴口径4mm以上,小于主流道套环入口0.68mm,喷嘴应装有可控加热带以防止材料凝固。
从经济角度考虑,注射量应为额定量的40%~80%。
螺杆转速20~50r/min 。
2、模具设计模具设计就注意以下几点:⑴模塑TPU制件的收缩率收缩受原料的硬度、制件的厚度、形状、成型温度与模具温度等模塑条件的影响。
通常收缩率范围为0、005~0.020cm/cm 。
例如,100 X 10X 2m耐长方形试片,在长度方向浇口,流动方向上收缩,硬度75A比60D大2〜3倍。
TPU硬度、制作厚度对收缩率的影响见图1。
可见TPU硬度在78A〜90A之间时,制件收缩率随厚度增加而下降;硬度在95A〜74D时制件收缩率随厚度增加而略有增加(2)流道与冷料穴主流道就是模具中连接注射机喷嘴至分流道或型腔的一段通道,直径应向内扩大,呈2o以上的角度,以便丁流道赘物脱模。
分流道就是多槽模中连接主流道与各个型腔的通道,在塑模上的排列应呈对称与等距分布。
流道可为圆形、半圆形、长方形,直径以6~9mm为宜。
聚氨酯

聚氨酯(TPU)注塑成型工艺TPU模塑成型工艺有多种方法:包括有注塑、吹塑、压缩成型、挤出成型等,其中以注塑最为常用。
注塑的功能是将TPU加工成所要求的制件,分成预塑、注射和机出三个阶段的不连续过程。
注射击机分柱塞式和螺杆式两种,推荐使用螺杆式注射机,因为它有提供均匀的速度、塑化和熔融。
1、注射机的设计注射机料筒衬以铜铝合金,螺杆镀铬防止磨损。
螺杆长径比L/D=16~20为好,至少15;压缩比2.5/1~3.0/1。
给料段长度0.5L,压缩段0.3L,计量段0.2L。
应将止逆环装在靠近螺杆顶端的地方,防止反流并保持最大压力。
加工TPU宜用自流喷嘴,出口为倒锥形,喷嘴口径4mm以上,小于主流道套环入口0.68mm,喷嘴应装有可控加热带以防止材料凝固。
从经济角度考虑,注射量应为额定量的40%~80%。
螺杆转速20~50r/min。
模具设计就注意以下几点:(1)模塑TPU制件的收缩率收缩受原料的硬度、制件的厚度、形状、成型温度和模具温度等模塑条件的影响。
通常收缩率范围为0.005~0.020cm/cm。
例如,100×10×2mm的长方形试片,在长度方向浇口,流动方向上收缩,硬度75A比60D大2~3倍。
TPU硬度、制作厚度对收缩率的影响见图1。
可见TPU硬度在78A~90A之间时,制件收缩率随厚度增加而下降;硬度在95A~74D时制件收缩率随厚度增加而略有增加。
(2)流道和冷料穴主流道是模具中连接注射机喷嘴至分流道或型腔的一段通道,直径应向内扩大,呈2o以上的角度,以便于流道赘物脱模。
分流道是多槽模中连接主流道和各个型腔的通道,在塑模上的排列应呈对称和等距分布。
流道可为圆形、半圆形、长方形,直径以6~9mm为宜。
流道表面必须像模腔一样抛光,以减少流动阻力,并提供较快的充模速度。
冷料穴是设在主流道末端的一个空穴,用以捕集喷嘴端部两次注射之间所产生的冷料,从而防止分流道或浇口堵塞。
冷料混入型腔,制品容易产生内应力。
- 1、下载文档前请自行甄别文档内容的完整性,平台不提供额外的编辑、内容补充、找答案等附加服务。
- 2、"仅部分预览"的文档,不可在线预览部分如存在完整性等问题,可反馈申请退款(可完整预览的文档不适用该条件!)。
- 3、如文档侵犯您的权益,请联系客服反馈,我们会尽快为您处理(人工客服工作时间:9:00-18:30)。
注塑成型—TPU成型工艺TPU注塑成型工艺TPU模塑成型工艺有多种方法:包括有注塑、吹塑、压缩成型、挤出成型等,其中以注塑最为常用。
注塑的功能是将TPU加工成所要求的制件,分成预塑、注射和机出三个阶段的不连续过程。
注射击机分柱塞式和螺杆式两种,推荐使用螺杆式注射机,因为它有提供均匀的速度、塑化和熔融。
1、注射机的设计注射机料筒衬以铜铝合金,螺杆镀铬防止磨损。
螺杆长径比L/D=16~20为好,至少15;压缩比2.5/1~3.0/1。
给料段长度0.5L,压缩段0.3L,计量段0.2L。
应将止逆环装在靠近螺杆顶端的地方,防止反流并保持最大压力。
加工TPU宜用自流喷嘴,出口为倒锥形,喷嘴口径4mm以上,小于主流道套环入口0.68mm,喷嘴应装有可控加热带以防止材料凝固。
从经济角度考虑,注射量应为额定量的40%~80%。
螺杆转速20~50r/min。
2、模具设计模具设计就注意以下几点:(1)模塑TPU制件的收缩率收缩受原料的硬度、制件的厚度、形状、成型温度和模具温度等模塑条件的影响。
通常收缩率范围为0.005~0.020cm/cm。
例如,100×10×2mm的长方形试片,在长度方向浇口,流动方向上收缩,硬度75A比60D大2,3倍。
TPU硬度、制作厚度对收缩率的影响见图1。
可见TPU硬度在78A,90A之间时,制件收缩率随厚度增加而下降;硬度在95A,74D时制件收缩率随厚度增加而略有增加。
(2)流道和冷料穴主流道是模具中连接注射机喷嘴至分流道或型腔的一段通道,直径应向内o扩大,呈2以上的角度,以便于流道赘物脱模。
分流道是多槽模中连接主流道和各个型腔的通道,在塑模上的排列应呈对称和等距分布。
流道可为圆形、半圆形、长方形,直径以6~9mm为宜。
流道表面必须像模腔一样抛光,以减少流动阻力,并提供较快的充模速度。
冷料穴是设在主流道末端的一个空穴,用以捕集喷嘴端部两次注射之间所产生的冷料,从而防止分流道或浇口堵塞。
冷料混入型腔,制品容易产生内应力。
冷料穴直径8~10mm,深度约6mm。
(3)浇口和排气口浇口是接通主流道或分流道与型腔的通道。
其截面积通常小于流道,是流道系统中最小的部分,长度宜短。
浇口形状为矩形或圆形,尺寸随制品厚度增中,制品厚度4mm以下,直径1mm;厚度4~8mm,直径1.4mm;厚度8mm以上,直径为2.0~2.7mm。
浇口位置一般选在制品最厚的而又不影响外观和使用的地方,与模具壁成直角,以防止缩孔,避免旋纹。
排气口是在模具中开设的一种槽形出气口,用以防止进入模具的熔料卷入气体,将型腔的气体排出模具。
否则将会使制品带有气孔、熔接不良、充模不满,甚至因空气受压缩产生高温而将制品烧伤,制件产生内应力等。
排气口可设在型腔内熔料流动的尽头或在塑模分型面上,为0.15mm深、6mm宽的浇槽。
必须注意模具温度尽量控制均匀,以免制件翘曲和扭变。
3 模塑条件TPU最重要的模塑条件是影响塑化流动和冷却的温度、压力和时间。
这些参数将影响TPU制件的外观和性能。
良好的加工条件应能获得均匀的白色至米色的制件。
(1)温度模塑TPU过程需要控制的温度有料筒温度、喷嘴温度和模具温度。
前两种温度主要影响TPU的塑化和流动,后一种温度影响TPU的流动和冷却。
a(料筒温度料筒温度的选择与TPU的硬度有关。
硬度高的TPU熔融温度高,料筒末端的最高温度亦高。
加工TPU所用料筒温度范围是177~232?。
料筒温度的分布一般是从料斗一侧(后端)至喷嘴(前端)止,逐渐升高,以使TPU温度平稳地上升达到均匀塑化的目的。
b(喷嘴温度喷嘴温度通常略低于料筒的最高温度,以防止熔料在直通式喷嘴可能发生的流涎现象。
如果为杜绝流涎而采用自锁式的喷嘴,则喷嘴温度亦可控制在料筒的最高温度范围内。
c(模具温度模具温度对TPU制品内在性能和表观质量影响很大。
它的高低决定于TPU的结晶性和制品的尺寸等许多因素。
模具温度通常通过恒温的冷却介质如水来控制,TPU硬度高,结晶度高,模具温度亦高。
例如Texin,硬度480A,模具温度20,30?;硬度591A,模具温度30,50?;硬度355D,模具温度40,65?。
TPU制品模具温度一般在10,60?。
模具温度低,熔料过早冻结而产生流线,并且不利于球晶的增长,使制品结晶度低,会出现后期结晶过程,从而引起制品的后收缩和性能的变化。
d.烤料温度一般情况下,烤料温度控制在75—95?,时间控制在2—3小时。
(二)(压力注塑过程是压力包括塑化压力(背压)和注射压力。
螺杆后退时,其顶部熔料所受到的压力即为背压,通过溢流阀来调节。
增加背压会提高熔体温度,减低塑化速度,使熔体温度均匀,色料混合均匀,并排出熔体气体,但会延长成型周期。
TPU 的背压通常在0。
3,4MPa。
注射压力是螺杆顶部对TPU所施的压力,它的作用是克服TPU从料筒流向型腔的流动阻力,给熔料充模的速率,并对熔料压实。
TPU流动阻力和充模速率与熔料粘度密切相关,而熔料粘度又与TPU硬度和熔料温度直接相关,即熔料粘度不仅决定于温度和压力,还决定于TPU硬度和形变速率。
剪切速率越高粘度越低;剪切速率不变,TPU硬度越高粘度越大。
在剪切速率不变的条件下,粘度随温度增加而下降,但在高剪切速率下,粘度受温度的影响不像低剪切速率那样大。
TPU的注射压力一般为20~110MPa。
保压压力大约为注射压力的一半,背压应在1。
4MPa以下,以使TPU塑化均匀。
(三)(时间完成一次注射过程所需的时间称为成型周期。
成型周期包括充模时间、保压时间、冷却时间和其他时间(开模、脱模、闭模等),直接影响劳动生产率和设备利用率。
TPU的成型周期通常决定于硬度、制件厚度和构型,TPU硬度高周期短,塑件厚周期长,塑件构型复杂周期长,成型周期还与模具温度有关。
TPU成型周期一般在20~60s之间。
(四)(注射速度注射速度主要决定于TPU制品的构型。
端面厚的制品需要较低的注射速度,端面薄则注射速度较快。
螺杆转速加工TPU制品通常需要低剪切速率,因而以较低的螺杆转速为宜。
TPU的螺杆转速一般为20~80r/min,则优选20~40r/min。
(五)停机处理由于TPU高温下延长时间可能发生降解,故在关机后,应该用PS、PE、丙烯酸酯类塑料或ABS清洗;停机超过1小时,应该关闭加热。
(六)制品后处理TPU由于在料筒内塑化不均匀或在模腔内冷却速率不同,常会产生不均匀的结晶、取向和收缩,因此致使制品存在内应力,这在厚壁制品或带有金属嵌件的制品中更为突出。
存在内应力的制品在贮存和使用中常会发生力学性能下降,表面有银纹甚至变形开裂。
生产中解决这些问题的方法是对制品进行退火处理。
退火温度视TPU制品的硬度而定,硬度高的制品退火温度亦较高,硬度低温度亦低;温度过高可能使制品发生翘曲或变形,过低达不到消除内应力的目的。
TPU的退火宜用低温长时间,硬度较低的制品室温放置数周即可达到最佳性能。
硬度在邵尔A85以下退火80?×20h,A85以上者100?×20h即可。
退火可在热风烘箱中进行,注意放置位置不要局部过热而使制品变形。
退火不仅可以消除内应力,还可提高力学性能。
由于TPU是两相形态,TPU热加工期间发生相的混合,在迅速冷却时,由于TPU粘度高,相分离很慢,必须有足够的时间使其分离,形成微区,从而获得最佳性能。
(七)镶嵌注塑为了满足装配和使用强度的需要,TPU制件内需嵌入金属嵌件。
金属嵌件先放入模具内的预定位置,然后注射成一个整体的制品。
有嵌件的TPU制品由于金属嵌件与TPU热性能和收缩率差别较大,导致嵌件与TPU粘接不牢。
解决的办法是对金属嵌件进行预热处理,因为预热后嵌件减少了熔料的温度差,从而在注射过程中可使嵌件周围的熔料冷却较慢,收缩比较均匀,发生一定的热料补缩作用,防止嵌件周围产生过大的内应力。
TPU镶嵌成型比较容易,嵌物形状不受限制,只要在嵌件脱脂后,将其在200,230?加热处理1。
5,2min,剥离强度可达6,9kg/25mm。
欲获得更牢的粘接,可在嵌件上涂粘合剂,然后于120?加热,再行注射。
此外,应该注意所用的TPU不能含润滑剂。
(八)回收料的再利用在TPU加工过程中,主流道、分流道、不合格的制品等废料,可以回收再利用。
从实验结果看,100%回收料不掺合新料,力学性能下降也不太严重,完全可以利用,但为保持物理力学性能和注射条件在最佳水平,推荐回收料比例在25%~30%为好。
应该注意的是回收料与新料的品种规格最好相同,已污染的或已退火的回收料避免使用,回收料不要贮存太久,最好马上造粒,干燥使用。
回收料的熔融粘度一般要下降,成型条件要进行调整。
(九)注射缺陷原因及处理缺产生原因解决办法缺产生原因解决办法陷陷背压低增加背压材料过热降低料筒温度毛材料潮湿彻底干燥注射压力太降低注射压边高力气螺杆转速太高降低螺杆转速模具紧固压提高紧固压泡力低力材料过热降低料筒温度注射压力太降低注射压高力注射速度过快降低注射速度保压时间太减少保压时长间制注射压力太高降低注射压力冷却不充分增加冷却时品间或循环时粘焦间模斑注射速度太快降低注射速度模温太高或调整模温太低材料过热降低料筒温度注射时间太降低注射时长间模具排气不当增加排气口模具表面镀改变模具表铬或高面材料潮湿彻底干燥度抛光韧回收料比率太降低回收料比熔融温度过降低熔料温性大率高度降熔融温度太高调整熔融温度给料不足调整给料低或太低注浇口太小增加浇口尺寸过早凝固提高模具温料度量浇口接合区太降低浇口接合料筒温度太提高料筒温不长区长度低度模具温度太低提高熔融温度足注射压力太增加注射压低力麻注射压力太低增加注射压力注射时间短增加注射时孔间气材料过热降低料筒温度喷嘴孔、流道调整喷嘴、流泡或浇口道和浇口尺模具温度太低提高模具温度或尺寸不足寸缩给料不足调整给料注射压力太增加注射压皱低力翘纹浇口定位不当调整浇口位置材料过热降低料筒温曲度注射速度快降低注射速度模具温度太降低模具温高度注射时间短增加注射时间树脂缓冲过降低树脂缓度冲制背压过高降低背压接注射压力、时增加注射压品合间不足力、时间凹线注射压力低提高注射压力熔料温度低提高料筒温陷度合模压力不足提高合模压力浇口尺寸小、增加浇口尺位置不当寸,改变位置熔料温度高降低料筒温度表熔料温度太降低料筒温面高度线凹陷部位排气凹陷部位设排注射速度快降低注射速纹不良气口度料斗进料部位排除进料部位浇口尺寸过加大浇口尺故障障碍小寸料筒后部温度降低该处温度材料干燥不彻底干燥材过高足料螺螺杆退后速度降低退后速度螺熔料温度低提高料筒温杆过快杆度打无料筒没有清洗用其他树脂清背压过高降低背压滑法净洗料筒转材料干燥不充再行干燥材料材料欠润滑添加适当润动分滑剂材料颗粒过大降低颗粒尺寸材熔料温度低提高料筒温料度未喷熔料温度过高降低料筒温度背压过低增加背压熔嘴喷嘴温度过高降低喷嘴温度料斗下部过关闭料斗下尽流冷部冷却系统料背压过大降低背压成型周期太增加成型周短期主流道冷料断延迟冷料断脱材料干燥不彻底干燥材脱时间早时间足料。