74工艺尺寸链
加工工艺试卷及答案

填空(1)车刀是一种最常见,最普通,最为典型的刀具.(2)切削运动必须具备主运动和进给运动两种运动.(3)主运动只有一个, 主运动可以是工件的运动,也可以是刀具的运动.(4)在切削加工过程中,工件上始终有三个不断变化的表面:待加工表面,已加工表面,过度表面.(5)切削用量三要素是由切削速度,进给量和背吃刀量组成.(6)切削部分一般由三个刀面,两条切削刃和一个刀尖共六个要素组成.(7)硬度是指材料表面抵抗其他更硬物体压入的能力.(8)工艺性指材料的切削加工性,锻造,焊接,热处理等性能.(9)高速钢是指含较多钨,铬,钼,钒等合金的高合金工具钢,俗称锋钢或白钢. (10)高速钢按其性能可分为通用高速钢和高性能高速钢.(11)金属切削过程的实质是金属切削层在刀具挤压作用下,产生塑性剪切滑移变形的过程.(12)在金属切削中,切屑类型有:带状切屑,节状切屑,粒状切屑,崩碎切屑. (13)切削力是金属切削过程中最重要的物理现象之一.(14)工件材料抵抗刀具切削所产生的阻力,称为切削力.(15)总切削力来源于两个方面:一是三个变形区的变形力;二是切屑与刀具前面,工件与刀具后面之间的摩擦力.(16)切削液具有冷却,润滑,清洁,防锈的作用.(17)切削热使切屑,工件,刀具的温度升高,从而影响工件的质量,刀具的寿命,切削速度的提高等.(18)切削热是由切屑,工件,刀具和周围介质传出扩散.(19)合理的选取切削液,可以减少切削热的产生,降低切削温度,能提高工件的加工质量,刀具寿命和生产率等.(20)切削液的种类有水溶液,乳化液,煤油等.(21)刀具磨损方式可分为前面磨损和后面磨损.(22)在金属切削过程中,机械的,温度的,化学的作用是造成刀具磨损的主要原因.(23)在金属切削过程中化学作用的磨损分为粘结磨损,氧化磨损,扩散磨损和相变磨损.(24)刀具后面磨损的过程一般可分为三个阶段,初期磨损阶段,正常磨损阶段,急剧磨损阶段.(25)影响刀具磨损限度的主要因素有切削用量的影响,几何参数的影响,工件材料的影响.(26)刃倾角的作用有影响排屑方向,影响刀尖强度,影响切削刃锋利特性,影响工件的加工质量.(27)正交平面参考系中由基面,切削平面,正交平面组成.(28)目前常用的刀具材料有高速钢,硬质合金钢,涂层刀具材料,超硬刀具材料. (29)切削用量中对刀具磨损限度的影响由大到小依次是切削速度,进给量和背吃刀量.(30)高的硬度,高的耐磨性,足够的强度和韧性,高的耐热性,良好的工艺性是刀具材料必须具备的性能.(31)车刀是金属切削加工中应用最广泛的一种刀具;(32)焊接式车刀是由硬质合金刀片和普通结构钢或铸铁刀杆通过焊接连接而成;(33)刀片的形状和尺寸用刀片型号来表示;(34)刀片型号由一个字母和一个或两个数字组成;字母表示刀片形状,数字表示刀片的主要尺寸;(35)常用的刀槽形状有开口式,半封闭式,封闭式和切口式四种;(36)刀柄的头部一般有两种形状,分别称为直头和弯头;(37)机夹车刀是将普通的硬质合金刀片用机械方法夹固在刀柄上,刀片磨钝后,卸下刀片,经重新刃磨,可再装上继续使用;(38)可转位车刀的夹紧结构有偏心式,杠杆式,楔块式和上压式四种;(39)成形车刀的特点是加工质量稳定,生产效率高,刀具寿命长,刀具成本较高; (40)麻花钻形似麻花,俗称钻头,是目前孔加工中应用最广泛的一种刀具; (41)标准麻花钻由工作部分,柄部,颈部三部分组成;(42)绞刀的种类很多,通常是按使用方式把绞刀分为手用绞刀和机用绞刀; (43)绞刀是由工作部分,柄部,颈部三部分组成;(44)铣刀的种类很多,圆柱铣刀和面铣刀是较有代表性的铣刀;(45)圆柱铣刀主要用于卧式铣床上加工平面;(46)面铣刀主要用于立式铣床上加工平面,台阶面等;(47)立铣刀主要用于立式铣床上加工凹槽,台阶面,成形面等;(48)模具铣刀按工作部分形状不同,可分为圆柱形球头铣刀,圆锥形球头铣刀和圆锥形立铣刀三种形式;(49)数控机床具有高效率,高精度,高柔性的性能,是现代机械加工的先进工艺装备,也是体现现代化机械加工工艺水平的重要标志;(50)数控刀具有四种常用的快速更换方式更换刀片,更换刀具,更换刀夹和更换刀柄;(51)为实现刀具的快换,一般要求在数控机床外预先调好刀具尺寸,预调刀具尺寸主要是指轴向尺寸、径向尺寸、切削刃的形状、位置等内容;(52)砂轮是由磨料和结合剂经混合、压制、干燥、焙烧而制成的一种特殊刀具; (53)砂轮结构由磨粒、结合剂和气孔组成;(54)砂轮特性的要素由五个要素组成:磨料、粒度、结合剂、硬度和组织; (55)目前制造砂轮用的磨料主要是各种人造磨料,人造磨料分刚玉类、碳化硅类、高硬磨料类三大类;(56)刚玉类磨料的主要成分为氧化硅;(57)碳化硅类磨料的主要成分为碳化硅;(58)常用的结合剂分为有机结合剂和无机结合剂两大类,其中无机结合剂最常用的是陶瓷结合剂;有机结合剂最常用的是树脂结合剂和橡胶结合剂; (59)砂轮特性的各参数一般都以代号的形式在砂轮的端面上;(60)砂轮是由磨粒和结合剂粘固而成的多刃刀具;(61)车刀按结构可分为:整体式车刀,焊接式车刀,机夹车刀,可转位车刀和成形车刀;(62)成形车刀按结构形状可分为平体成形车刀、棱体成形车刀和圆体成形车刀; (63)孔加工刀具有两大类,一类是在实体材料上加工出孔,另一类是在有孔的材料上进行扩孔加工;(64)铰刀是对已有孔进行精加工的一种刀具;(65)铣刀是一种在回转体表面上或端面上分布有多个刀齿的多刃刀具;(66)铣刀按用途大致可分为:圆柱铣刀、面铣刀、立铣刀、键槽铣刀、三面刃铣刀、角度铣刀和磨具铣刀;(67)面铣刀主要用于在立式铣床上加工平面、台阶面等;(68)砂轮结构三要素是:磨粒,结合剂和气孔;(69)砂轮特性五要素中粒度是指磨料颗粒的大小;(70)砂轮特性五要素中组织是指砂轮中磨料、结合剂、气孔三者的体积比例,也就是砂轮内部结构的松紧程度;(71)在机械制造中有许多零件属于轴类零件,而外圆柱面是构成轴类零件的主要表面;(72)外圆表面的加工方法主要有车削和磨削;(73)车削加工是回转类零件外圆表面的主要加工方法;(74)外圆车削的工艺范围很广,一般可划分为粗车、半精车、精车和精细车等各加工阶段;(75)磨削加工是工件外圆表面精加工的主要方法;(76)根据磨削时的工件定位方式的不同,可分为中心磨削和无心磨削两种方式; (77)超精加工过程大致有四个阶段:强烈切削阶段,正常切削阶段,微弱切削阶段和自动停止切削阶段;(78)内孔表面是零件上的主要表面之一;(79)钻孔是采用钻头在实心材料上加工孔的一种方法;(80)钻孔方式有两种,一种是刀具旋转,工件或刀具作轴向进给;另一种是工件旋转,刀具作轴向进给;(81)扩孔是采用扩孔钻对已钻出的孔进行进一步加工的方法;(82)镗床的分类:坐标镗床,金刚镗床和卧式镗床;(83)镗刀可分为单刃镗刀和双刃镗刀;(84)镗孔既可以作为粗加工,也可作为精加工;(85)铰孔是对未淬硬孔进行精加工的一种方法;(86)铰孔时常出现孔径扩大和表面粗糙度不佳等缺陷(87)常用的精密加工方法精细镗孔、珩磨孔和研磨孔;(88)平面常用的加工法有刨削、铣削和磨削,对于大批量生产的零件,也可采用拉削加工;(89)刨床可分为龙门刨床、牛头刨床和插床;(90)在插齿加工中插刀的前角大容易扎刀,前角小容易让刀;(91)升降台式铣床可分为卧式铣床、立式铣床和万能铣床;(92)平面铣削方式有端铣和周铣两种;(93)铣刀切削速度方向与工件进给方向相反时称为逆铣;(94)铣刀切削速度方向与工件进给方向相同时称为顺铣;(95)平面磨削有端面磨削和圆周磨削两种方式;(96)成形面主要加工方法有划线加工、仿形法加工、展成加工以及在数控机床上加工等;(97)展成法主要用于齿轮齿形的加工,它是利用齿轮啮合原理进行加工; (98)用展成法加工齿形的方法,常见的有滚齿、插齿、剃齿和磨齿等;(99)插齿是常用的一种齿轮加工方法;(100)剃齿是精加工齿形的一种方法;(101)磨齿的方法分为两类:一是成形法加工,二是展成法加工;(102)生产过程是指将原材料转变为成品的各有关劳动过程的总和,包括工艺过程与辅助过程;(103)工艺规程是把工艺过程以文字的形式规定下来所形成的工艺文件; (104)工步是工序中一个部分,是指当加工表面、切削刀具和切削用量中的转速与进给量均保持不变时所完成的那部分工序;(105)安装是工序中的一个部分,把工件在夹具或机床中定位与夹紧的过程; (106)生产纲领是指包括成品率和废品率在内的该产品的年产量;(107)精基面是指采用以加工过的表面作为定位基面;(108)基准统一是指选用同一个定位基准加工各表面;(109)制定工艺规程的原则是在现有的生产条件下,能以最少的劳动量,最快的速度,最低的成本,可靠的加工出符合图样要求的零件;(110)毛坯的种类有铸件、锻件、型材和组合件;(111)划分加工阶段的原因是保证加工质量,合理使用设备,便与安排热处理;(112)切削顺序安排的原则是先粗后精,先主后次,先面后孔,基面平行; (113)工艺过程可以分为锻工工艺、车工工艺、磨工工艺、热处理工艺和装配工艺等;(114)机械制造业中的生产可以划分为三个类型单件生产、成批生产和大量生产;(115)衡量零件结构公益性好坏的主要依据是加工量大小、成本高低及材料消耗;(116)零件的技术条件主要包括零件的尺寸精度、形位精度、表面粗糙度值、材料及热处理等要求;(117)锻件是通过对处于固体状态下的材料进行锤击、锻打而改变其尺寸、形状的一种加工方法;(118)按照锻造时是否采用模具,可分为自由锻与模锻;(119)按照锻造时零件是否加热可分为热锻与冷锻;(120)材料的工艺特性首先是指该材料的可铸性、可塑性及可焊性;(121)毛坯的选择应根据零件的结构、形状与外形尺寸大小来确定;(122)在零件图上,用以确定其它点、线、面位置的基准称设计基准; (123)工艺基准按用途可分为定位基准、测量基准、装配基准和工序基准; (124)在工艺路线中按工序性质不同,可以划分为粗加工阶段,半加工阶段,精加工阶段和光整加工阶段四个加工阶段;(125)零件的加工顺序包括切削加工顺序、热处理先后顺序及辅助工序等; (126)常用的热处理有退火、正火、调质、时效、淬火回火、淬碳淬火、渗碳处理等;(127)工序余量的确定方法有查表修正法,经验估算法,分析计算法;(128)尺寸链的计算种类有正计算、反计算、中间计算;(129)工艺装备是指产品在制造过程中采用的各种工具的总称,它包括刀具、夹具、模具量具等,简称为工装;(130)轴类零件在机械设备中主要用于支承传动件,传递转矩;(131)中心孔磨床的顶尖状砂轮有三种运动方式主切削运动、行星运动和往复运动;(132)箱体加工的质量会直接影响整台机器的精度及使用寿命;(133)箱体加工的工艺过程安排,包括切削加工安排与热处理工序的安排; (134)箱体加工的加工方法有找正法、镗模法和坐标法;(135)机床夹具按专门化程度可分为通用家具、专用夹具,组合夹具和可调夹具四种;(136)机床夹具按使用机床类型可分为车床夹具、铣床夹具、钻床夹具、镗床夹具、加工中心夹具和其它机床夹具等;(137)外圆定心夹紧机构有三爪卡盘、弹簧夹头等;(138)夹紧力的作用方向应垂直指向主要定位基准;(139)所谓加工余量,是指是加工表面达到所需的精度和表面质量而应切除的金属层的厚度,分为加工总余量和工序余量;(140)定位的实质就是消除工件的自由度;(141)用适当分布的六个支承点限制工件六个自由度的法则,成为六点定位规则;(142)工件的六个自由度都被限制的定位称为完全定位;(143)只限制五个自由度,允许某个自由度不受限制的定位称为不完全定位; (144)工件的定位尺寸应根据加工尺寸要求确定应限制的自由度数; (145)工件以平面作为定位基准时,所用定位元件一般可分为“基本支承”和“辅助支承”两类;(146)内控定位时常用的定位元件有定位销,定位插销和定心轴等(147)要保证工件的加工要求,取决于工件与刀具间的相互位置;(148)在设计加紧装置时,首先要合理的选择夹紧力的作用点,夹紧力的方向和大小,然后选用或设计合适的夹紧机构来保证实现工件正确夹紧; (149)在夹紧时,夹紧力、切削力和工件重力三者方向一致时,所需的夹紧力最小;(150)夹紧力作用点应落在工件刚度较好的方向和部位,防止工件变形; (151)理论上夹紧力的大小只需克服工件重力、切削力、惯性力、离心力等; (152)在实际设计夹紧装置时,往往采用估算法、类比法、实验法来确定所需夹紧力;(153)在夹具中,常以斜楔、螺旋、偏心、铰链等机构来保证工件在加工中有足够的夹紧力;(154)斜楔的特点是自锁性、增力作用、夹紧行程较小;(155)用偏心件直接或间接夹紧工件的机构,称偏心夹紧机构;(156)定心夹紧机构是把中心定位和夹紧结合在一起,两动作同时完成,车床主轴上的三爪自定心卡盘是典型的定心夹紧机构;(157)定心夹紧机构按工作原理可分为两类,一类是以等速移动原理进行定心夹紧,另一类是以匀速弹性形变原理进行定心夹紧;(158)用人的体力,通过各种增力机构对工件进行夹紧,称为手动夹紧; (159)采用动力装置来代替人的体力进行夹紧,称之为机动夹紧;(160)机动夹紧常采用气动、液压、电动以及气液联合等机动夹紧机构作为动力装置;(161)气压装置传动包括三个组成部分气源、控制部分和执行部分;(162)气液联合夹紧装置中能量来源是压缩空气、经增压器后,执行机构是液压缸;(163)气液联合夹紧的主要元件是增压器;(164)国内外已经开发和正式研究的CAPP系统,其基本原理可分为三类:派生法、创成法和混合法;(165)柔性制造系统由加工、物流和信息流三个系统组成;(166)程序编制的方法有手工编程和计算机辅助自动编程两种;(167)要提高生产率可采用的先进工艺方法有特种加工应用,采用毛坯制造工艺和改进加工方法;(168)影响磨削表面粗糙度的主要因素是:砂轮的粒度、砂轮的修整、砂轮速度和磨削深度与工件速度;(169)砂轮的粒度愈细,则砂轮单位面积上的磨粒数愈多,因而在工件上的刻痕也愈密而细,所以表面粗糙度值愈低;(170)磨削表面是砂轮上大量的磨粒刻划出的无数极细的沟槽形成的; (171)影响表面粗糙度的因素主要有几何因素和物理因素两个方面以及机床——刀具——工件系统的振动;(172)在中等切削速度下加工塑性材料时,常常易出现积屑瘤与鳞刺,使加工表面粗糙度值增大;(173)刀具材料与被加工材料分子的亲和力大时,易生成积屑瘤;(174)机械加工表面质量将影响零件或产品的使用性能和使用寿命,主要表现为耐磨性、接触刚度、配合性质、抗疲劳强度、耐腐蚀性等方面; (175)零件的耐磨性与摩擦副的材料、润滑条件和表面质量等因素有关; (176)减少工艺系统热变形的工艺措施有减少切削热或磨削热、加强散热能力、保持工艺系统的热平衡和控制环境温度;(177)提高加工精度的措施有直接减小或消除误差法、误差转移法、补偿或抵消误差法、就地加工法;(178)机械加工误差是由工艺系统的原始误差引起的;(179)引起工艺系统热变形的“热源”大体分为两类,及内部热源和外部热源; (180)内部热源主要指切削热和磨削热;(181)外部热源主要是环境温度和辐射热;(182)车窗类机床的主要热源是主轴箱轴承的摩擦热和主轴箱中油池的发热;(183)切削加工中,工件的热变形主要是由切削热引起的;(184)加工精度在数值上通过加工误差的大小来表示,即精度越高,误差越小;精度越低,误差越大;(185)零件的加工质量,除加工精度外,还包括表面质量,它是指零件加工后的表面层状态;(186)零件加工表面质量应包括:加工表面粗糙度、表面层物理力学性能(187)加工表面层物理力学性能包括表面层冷作硬化、表面层残余应力和表面层金相组织的变化;(188)在机械加工中,机床、夹具、刀具、工件构成了一个完整的工艺系统; (189)原始误差分为两大类,第一类是与工艺系统初始状态有关的原始误差;第二类是与加工工艺过程有关的原始误差;(190)工艺系统的几何误差,就是机床、夹具、刀具和工件本身的原始制造误差以及机床、夹具和刀具在加工过程中的磨损;(191)机床的原始误差是指在工件加工前,由于机床本身制造、磨损和安装误差引起的工件在加工中的误差,因此也称机床的几何误差;(192)机床的成形运动最主要的有两大类,及主轴的回转运动和移动件的直线运动;(193)所谓主轴的回转误差,是指主轴的实际回转轴线相对其理想回转中心的变动量;(194)端面对轴心线的垂直度误差随切削半径的减小而增大;(195)工件表面几何形状误差和位置误差取决于顶尖和中心孔的定位误差,而与主轴回转误差无关;(196)传动元件由于其制造、装配和使用过程中的磨损而产生误差,这些误差就构成了传动链误差,传动元件越多,传动路线越长,则传动误差也越大; (197)在数控加工零件编程时,要确定刀具相对与工件运动的起点,也称为刀点;(198)由于定位不正确而引起的误差称为定位误差;(199)一般来说,物体反抗变形的能力越大,则产生的加工误差越小; (200)减小工艺系统受力变性的主要措施有:提高接触刚度、提高工件或刀具刚度和提高机床部件刚度;a)填空:1、零、部件或机器上若干首尾相接并形成封闭环图形的尺寸系统称为尺寸链;2、尺寸链按应用场合分装配尺寸链零件尺寸链和工艺尺寸链;3、尺寸链由封闭环和组成环构成;4、组成环包含增环和减环;5、封闭环的基本尺寸等于所有增环的基本尺寸之和减去所有减环的基本尺寸之和;6、当所有的增环都是最大极限尺寸,而所有的减环都是最小极限尺寸,封闭环必为最大极限尺寸;7、所有的增环下偏差之和减去所有减环上偏差之和,即为封闭环的下偏差;8、封闭环公差等于所有组成环公差之和 ;9、如图所示,若加工时以Ⅰ面为基准切割A2和A3,则尺寸 A1 为封闭环;若以Ⅰ面为基准切割A1和A2,则尺寸 A3 为封闭环;10、“入体原则”的含义为:当组成环为包容尺寸时取下偏差为零;12-2 选择题:1、一个尺寸链至少由 C 个尺寸组成,有 A 个封闭环;A、1B、2C、3D、42、零件在加工过程中间接获得的尺寸称为 C ;A、增环B、减环C、封闭环D、组成环3、封闭环的精度由尺寸链中 C 的精度确定;A、所有增环B、所有减环C、其他各环4、按“入体原则”确定各组成环极限偏差应 A ;A、向材料内分布B、向材料外分布C、对称分布12-3 判断题:1、当组成尺寸链的尺寸较多时,封闭环可有两个或两个以上; ×2、封闭环的最小极限尺寸等于所有组成环的最小极限尺寸之差; ×3、封闭环的公差值一定大于任何一个组成环的公差值. √4、在装配尺寸链中,封闭环时在装配过程中最后形成的一环, √也即为装配的精度要求; √5、尺寸链增环增大,封闭环增大√ ,减环减小封闭环减小× .6、装配尺寸链每个独立尺寸的偏差都将将影响装配精度√ ;选择1、采用数控机床加工的零件应该是 B ;A. 单一零件B. 中小批量、形状复杂、型号多变C. 大批量D.都行2、数控加工中心的固定循环功能适用于C;A.曲面形状加工 B 平面形状加工 C 孔系加工 D 成型面加工3、刀尖半径左补偿方向的规定是C;A. 沿刀具运动方向看,工件位于刀具左侧B. 沿工件运动方向看,工件位于刀具左侧C. 沿刀具运动方向看,刀具位于工件左侧D. 沿工件运动方向看,刀具位于工件左侧4、数控车床在加工中为了实现对车刀刀尖磨损量的补偿,可沿假设的刀尖方向,在刀尖半径值上,附加一个刀具偏移量,这称为B;A.刀具位置补偿 B.刀具半径补偿 C. 刀具长度补偿 D.刀具精度补偿5、切削热主要是通过切屑和C进行传导的;A.工件 B 刀具 C 周围介质 D.机床6、切削的三要素有进给量、背吃刀量和 B ;A. 切削厚度B. 切削速度C. 进给速度D.进给量7、工件定位时,被消除的自由度少于六个,且不能满足加工要求的定位称为 A ;A、欠定位B、过定位C、完全定位 D.不完全定位8、重复限制自由度的定位现象称之为 C ;A. 完全定位B. 过定位C. 不完全定位D. 欠定位9、工件定位时,仅限制四个或五个自由度,没有限制全部自由度的定位方式称为C ;A.完全定位B. 欠定位C. 不完全定位D. 过定位10、工件定位时,下列哪一种定位是不允许存在的B ;A 完全定位 B. 欠定位 C. 不完全定位 D. 过定位11、切削过程中,工件与刀具的相对运动按其所起的作用可分为 A ;A. 主运动和进给运动B. 主运动和辅助运动C. 辅助运动和进给运动D. 成型运动12、铰孔的切削速度比钻孔的切削速度 B ;A.大 B. 小 C. 相等 D.一样13、夹紧中确定夹紧力大小时,最好状况是力B;A.尽可能的大 B.尽可能的小 C.大小应适应 D.都行14、数控车床加工钢件时希望的切屑是C;A.带状切屑 B.挤裂切屑 C. 单元切屑 D.崩碎切屑15、影响数控加工切屑形状的切削用量三要素中B影响最大;A.切削速度 B.进给量 C.吃刀量 D.切削深度16、在数控机床上使用的夹具最重要的是C;A.夹具的刚性好B.夹具的精度高C. 夹具上有对刀基准D.夹具的塑性好17、数控机床加工零件的程序编制不仅包括零件工艺过程,而且还包括切削用量、走刀路线和C;A.机床工作台尺寸 B. 机床行程尺寸 C.刀具尺寸 D.定位偏差18、机床上的卡盘,中心架等属于A夹具;A.通用 B. 专用 C. 组合 D.万能19、从工作性能上看液压传动的优点有BA.比机械传动准确B.速度、功率、转矩可无级调节C.传动效率高D.生产率高20、从工作性能上看液压传动的缺点有C。
机械制造的技术(下)习题(1)

机械制造的技术(下)习题(1)《机械制造技术》习题第⼗四章机械加⼯⼯艺规程的制订1-1 什么是⽣产过程、⼯艺过程和⼯艺规程?1-2 什么是⼯序、⼯位、⼯步和⾛⼑?试举例说明。
1-3 什么是安装?什么是装夹?它们有什么区别?1-4 单件⽣产、成批⽣产、⼤量⽣产各有哪些⼯艺特征?1-5 试为某车床⼚丝杠⽣产线确定⽣产类型,⽣产条件如下:加⼯零件:卧式车床丝杠(长为1617mm,直径为40mm,丝杠精度等级为8级,材料为Y40Mn);年产量:5000台车床;备品率:5%;废品率:0.5%。
1-6 什么是⼯件的定位?什么是⼯件的夹紧?试举例说明。
1-7 什么是⼯件的⽋定位?什么是⼯件的过定位?试举例说明。
1-8 试举例说明什么是设计基准、⼯艺基准、⼯序基准、定位基准、测量基准和装配基准。
1-9 有⼈说:“⼯件在夹具中装夹,只要有6个定位⽀承点,就是⽋定位”,“凡是少于6个定位⽀承点,就不会出现过定位”,上⾯这些说法都对吗?为什么?试举例说明。
1-10 分析图1-8所⽰定位⽅式,并回答以下问题:(1)各定位件所限制的⾃由度;(2)判断有⽆⽋定位或过定位现象,为什么?图1-8 习题1-10图第⼗六章机械加⼯质量及其控制4-1 什么是主轴回转精度?为什么外圆磨床头夹中的顶尖不随⼯件⼀起回转,⽽车床床头箱中中的顶尖则是随⼯件⼀起回转的?4-2 在镗床上镗孔时(⼑具作旋转主运动,⼯件作进给运动),试分析加⼯表⾯产⽣椭圆形误差的原因。
4-3 为什么卧式车床床⾝导轨在⽔平⾯内的直线度要求⾼于垂直⾯内的直线度要求?4-4 某车床导轨在⽔平⾯内的直线度误差为0.015/1000mm ,在垂直⾯内的直线度误差为0.025/1000mm ,欲在此车床上车削直径为φ60mm 、长度为150mm 的⼯件,试计算被加⼯⼯件由导轨⼏何误差引起的圆柱度误差。
4-5 在车床上精车⼀批直径为φ60mm 、长为1200mm 的长轴外圆。
已知:⼯件材料为45钢;切削⽤量为:120=νm/min, p α=0.4mm, f =0.2mm/r; ⼑具材料为YT15。
模具钳工高级题库 DOC 文档
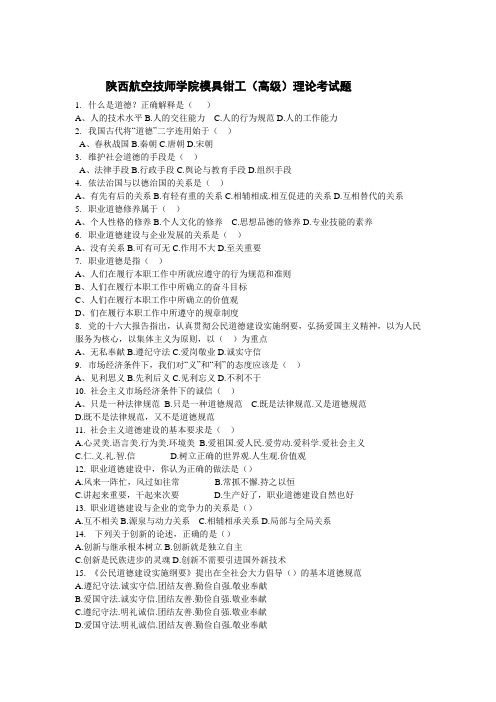
陕西航空技师学院模具钳工(高级)理论考试题1.什么是道德?正确解释是()A、人的技术水平B.人的交往能力 C.人的行为规范D.人的工作能力2.我国古代将“道德”二字连用始于()A、春秋战国B.秦朝C.唐朝D.宋朝3.维护社会道德的手段是()A、法律手段B.行政手段C.舆论与教育手段D.组织手段4.依法治国与以德治国的关系是()A、有先有后的关系B.有轻有重的关系C.相辅相成.相互促进的关系D.互相替代的关系5.职业道德修养属于()A、个人性格的修养B.个人文化的修养 C.思想品德的修养D.专业技能的素养6.职业道德建设与企业发展的关系是()A、没有关系B.可有可无C.作用不大D.至关重要7.职业道德是指()A、人们在履行本职工作中所就应遵守的行为规范和准则B、人们在履行本职工作中所确立的奋斗目标C、人们在履行本职工作中所确立的价值观D、们在履行本职工作中所遵守的规章制度8.党的十六大报告指出,认真贯彻公民道德建设实施纲要,弘扬爱国主义精神,以为人民服务为核心,以集体主义为原则,以()为重点A、无私奉献B.遵纪守法C.爱岗敬业D.诚实守信9.市场经济条件下,我们对“义”和“利”的态度应该是()A、见利思义B.先利后义C.见利忘义D.不利不于10. 社会主义市场经济条件下的诚信()A、只是一种法律规范B.只是一种道德规范 C.既是法律规范.又是道德规范D.既不是法律规范,又不是道德规范11. 社会主义道德建设的基本要求是()A.心灵美.语言美.行为美.环境美B.爱祖国.爱人民.爱劳动.爱科学.爱社会主义C.仁.义.礼.智.信D.树立正确的世界观.人生观.价值观12. 职业道德建设中,你认为正确的做法是()A.风来一阵忙,风过如往常B.常抓不懈.持之以恒C.讲起来重要,干起来次要D.生产好了,职业道德建设自然也好13. 职业道德建设与企业的竞争力的关系是()A.互不相关B.源泉与动力关系C.相辅相承关系D.局部与全局关系14. 下列关于创新的论述,正确的是()A.创新与继承根本树立B.创新就是独立自主C.创新是民族进步的灵魂D.创新不需要引进国外新技术15. 《公民道德建设实施纲要》提出在全社会大力倡导()的基本道德规范A.遵纪守法.诚实守信.团结友善.勤俭自强.敬业奉献B.爱国守法.诚实守信.团结友善.勤俭自强.敬业奉献C.遵纪守法.明礼诚信.团结友善.勤俭自强.敬业奉献D.爱国守法.明礼诚信.团结友善.勤俭自强.敬业奉献16. 尊师爱徒是传统师徒关系的准则,在现实条件下,正确的选择是()A.徒弟尊重师傅,师傅不必尊重徒弟B.徒弟尊重师傅,师傅也尊重徒弟C.徒弟不必尊重师傅,师傅也不必尊重徒弟D.用“哥门”关系取代师徒关系17. 诚实守信是做人的行为准则,在现实生活中正确的观点是()A.诚实守信与市场经济相冲突B.诚实守信是市场经济必须遵守的法则C.是否诚实守信要视具体情况而定D.诚实守信是“呆”.“傻”.“憨”。
互换性题库概要

互换性题库一、判断以下说法是否正确,填写在相应题号下面的空格内。
对的打“√”,错打“×”)1、孔的基本偏差即下偏差,轴的基本偏差即上偏差。
( × )2、基本偏差决定公差带的位置。
( √ )3、实际尺寸就是真实的尺寸,简称真值。
( × )4、某孔要求尺寸为046.0067.020--φ,今测得其实际尺寸为φ19.962mm ,可以判断该孔合格。
( × )5、在ф60H7/f6 代号中,由于轴的精度高于孔,故以轴为基准件。
( × )6、对同一要素既有位置公差要求,又有形状公差要求时,形状公差值应大于位置公差 值。
( × )7、未注公差的尺寸就是没有公差要求的尺寸。
( × )8、Js 和js 的基本偏差可以是上偏差,也可以是下偏差。
( √ )9、零件的实际尺寸越接近其基本尺寸就越好。
( × )10、若φ30f7的基本偏差为-0.02mm ,则φ30F8的基本偏差一定是+0.02mm 。
( √ )11、被测要素采用最大实体要求的零形位公差时,被测要素必须遵守最大实体实效边界。
( √ )12、圆柱度公差是控制圆柱形零件横截面和轴向截面内形状误差的综合性指标。
( √ )13、定位公差带具有确定的位置,但不具有控制被测要素的方向和形状的职能。
( × )14、表面粗糙度的三类特性评定参数中,最常采用的是高度特性参数。
( √ )15、滚动轴承内圈转动,外圈固定,承受方向固定的径向负荷作用,则内圈相对于负荷方向静止。
( × )16、尺寸公差与形位公差采用独立原则时,零件加工的实际尺寸和形位误差中有一项超差,则该零件也有可能合格。
( × )17、配合公差的数值愈小,则相互配合的孔、轴的公差等级愈高。
( √ )18、平键联接中,键宽与轴槽宽的配合采用基轴制。
( √ )19、平键联结中,键宽与键槽宽的配合采用基轴制。
全国职工职业技能鉴定考核机械基础中级-综合题(一)_真题-无答案
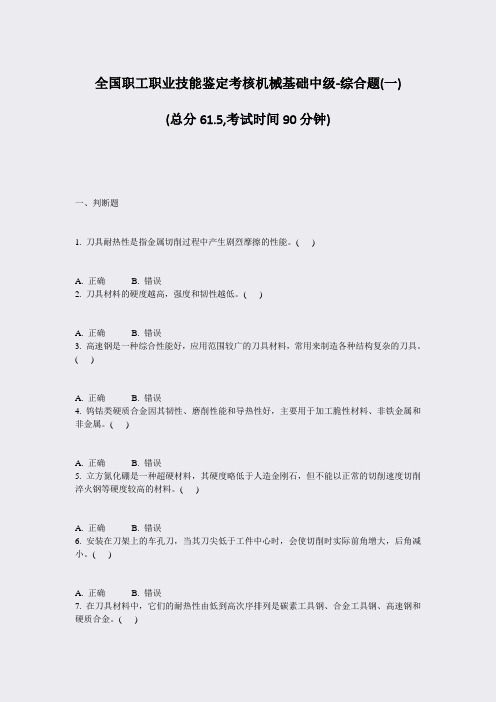
全国职工职业技能鉴定考核机械基础中级-综合题(一)(总分61.5,考试时间90分钟)一、判断题1. 刀具耐热性是指金属切削过程中产生剧烈摩擦的性能。
( )A. 正确B. 错误2. 刀具材料的硬度越高,强度和韧性越低。
( )A. 正确B. 错误3. 高速钢是一种综合性能好,应用范围较广的刀具材料,常用来制造各种结构复杂的刀具。
( )A. 正确B. 错误4. 钨钴类硬质合金因其韧性、磨削性能和导热性好,主要用于加工脆性材料、非铁金属和非金属。
( )A. 正确B. 错误5. 立方氮化硼是一种超硬材料,其硬度略低于人造金刚石,但不能以正常的切削速度切削淬火钢等硬度较高的材料。
( )A. 正确B. 错误6. 安装在刀架上的车孔刀,当其刀尖低于工件中心时,会使切削时实际前角增大,后角减小。
( )A. 正确B. 错误7. 在刀具材料中,它们的耐热性由低到高次序排列是碳素工具钢、合金工具钢、高速钢和硬质合金。
( )A. 正确B. 错误8. 刀具几何参数、刀具材料和刀具结构是研究金属切削刀具的三项基本内容。
( )A. 正确B. 错误9. 由于硬质合金的抗弯强度较低,抗冲击韧性差,所以前角应小于高速钢刀具的合理前角。
( )A. 正确B. 错误10. 当工件材料强度和硬度较高,韧性较差时,可以增大合理前角来减小切屑变形。
( )A. 正确B. 错误11. 在保证切削刃强度和散热条件下,切削中硬钢的合理前角要比切削软钢小,而比切削铸铁来得大。
( )A. 正确B. 错误12. 当粗加工、承受冲击载荷时,若要使刀具寿命延长,则必须减少刀具摩擦,所以后角应取得大些。
( )A. 正确B. 错误13. 主偏角和副偏角减小,能够使加工残留面积高度降低,可以减小表面粗糙度,其中副偏角的减小更明显。
( )A. 正确B. 错误14. 刃倾角的作用是控制切屑的排出方向,精车和半精车时刃倾角选取正值的目的是使切屑流向待加工表面。
( )A. 正确B. 错误15. 粗加工、断续切削和承受冲击载荷时,为了保证切削刃的强度,应取较小的前角,甚至负前角。
机械加工技术基础知识单选题100道及答案

机械加工技术基础知识单选题100道及答案1. 下列哪种刀具材料的硬度最高?()A. 高速钢B. 硬质合金C. 陶瓷D. 金刚石答案:D2. 在车床上加工轴类零件时,常用的装夹方式是()A. 两顶尖装夹B. 一夹一顶装夹C. 三爪卡盘装夹D. 以上都是答案:D3. 钻孔时,钻头的旋转运动是()A. 主运动B. 进给运动C. 辅助运动D. 以上都不是答案:A4. 车削细长轴时,为了减少工件的弯曲变形,应使用()A. 跟刀架B. 中心架C. 顶尖D. 花盘答案:A5. 扩孔加工属于()A. 粗加工B. 半精加工C. 精加工D. 超精加工答案:B6. 磨削加工的精度一般可达()A. IT5 - IT6B. IT7 - IT8C. IT9 - IT10D. IT11 - IT12答案:A7. 下列哪种加工方法主要用于单件小批生产?()A. 模具加工B. 数控加工C. 特种加工D. 钳工加工答案:D8. 在外圆磨床上磨削外圆时,()的运动是进给运动。
A. 砂轮的旋转B. 工件的旋转C. 砂轮的横向移动D. 工件的纵向移动答案:C9. 铣削平面时,铣刀的旋转运动是()A. 主运动B. 进给运动C. 复合运动D. 以上都不是答案:A10. 铰孔不能提高孔的()精度。
A. 尺寸B. 形状C. 位置D. 表面粗糙度答案:C11. 电火花加工主要用于加工()A. 导电材料B. 不导电材料C. 陶瓷材料D. 高分子材料答案:A12. 下列哪种量具可以测量内孔的直径?()A. 游标卡尺B. 千分尺C. 内径千分尺D. 以上都是答案:C13. 数控车床的核心部件是()A. 数控系统B. 床身C. 主轴箱D. 刀架答案:A14. 车削螺纹时,螺纹的导程由()决定。
A. 刀具B. 工件转速C. 挂轮D. 丝杠答案:C15. 加工中心与普通数控机床的主要区别是()A. 有刀库和自动换刀装置B. 加工精度高C. 机床刚性好D. 速度快答案:A16. 下列哪种切削液的冷却性能最好?()A. 水溶液B. 乳化液C. 切削油D. 以上都不是答案:A17. 精车时,为了提高表面质量,应选择()的切削速度。
工艺规程设计工艺尺寸链计算
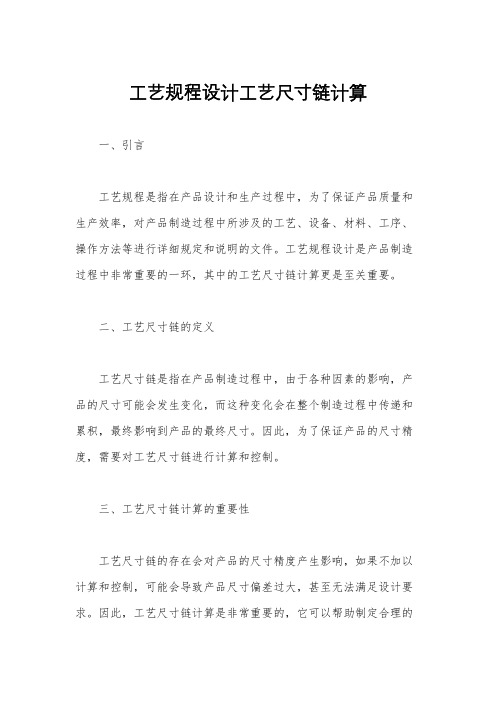
工艺规程设计工艺尺寸链计算一、引言工艺规程是指在产品设计和生产过程中,为了保证产品质量和生产效率,对产品制造过程中所涉及的工艺、设备、材料、工序、操作方法等进行详细规定和说明的文件。
工艺规程设计是产品制造过程中非常重要的一环,其中的工艺尺寸链计算更是至关重要。
二、工艺尺寸链的定义工艺尺寸链是指在产品制造过程中,由于各种因素的影响,产品的尺寸可能会发生变化,而这种变化会在整个制造过程中传递和累积,最终影响到产品的最终尺寸。
因此,为了保证产品的尺寸精度,需要对工艺尺寸链进行计算和控制。
三、工艺尺寸链计算的重要性工艺尺寸链的存在会对产品的尺寸精度产生影响,如果不加以计算和控制,可能会导致产品尺寸偏差过大,甚至无法满足设计要求。
因此,工艺尺寸链计算是非常重要的,它可以帮助制定合理的工艺规程,确保产品尺寸的精度。
四、工艺尺寸链计算的方法1. 确定影响尺寸的因素:在进行工艺尺寸链计算时,首先需要确定影响产品尺寸的因素,包括材料的热胀冷缩、加工工艺的误差、设备精度等。
2. 建立数学模型:根据影响尺寸的因素,建立相应的数学模型,用于描述尺寸变化的规律。
3. 进行计算和分析:利用建立的数学模型,对工艺尺寸链进行计算和分析,得出尺寸变化的规律和程度。
4. 制定控制措施:根据计算和分析的结果,制定相应的控制措施,包括调整工艺参数、优化设备精度、选择合适的材料等,以确保产品尺寸的精度。
五、工艺尺寸链计算的应用工艺尺寸链计算可以应用于各种不同的制造过程中,例如机械加工、注塑成型、铸造等。
通过对工艺尺寸链的计算和控制,可以有效地提高产品的尺寸精度,减少产品的尺寸偏差,提高产品的质量。
六、结论工艺尺寸链计算是工艺规程设计中非常重要的一环,它可以帮助制定合理的工艺规程,确保产品的尺寸精度。
通过对工艺尺寸链的计算和控制,可以有效地提高产品的质量,满足设计要求。
因此,在工艺规程设计过程中,应该重视工艺尺寸链的计算和控制,以确保产品制造过程中尺寸的稳定和精度。
第十章尺寸链

i 1
2、封闭环公差:
T0 L Ti
i 1
m
3、封闭环中间偏差:
0 i
i 1
m
中间偏差:上、下偏差的平均值。
T0 ES 0 0 2 4、封闭环极限偏差: EI T0 0 0 2
5、封闭环的极限尺寸
L0 max L0 ES0 L0 min L0 EI0
由上述公式总结:
1)封闭环公差最大,故工艺中选最不重要的尺寸
作封闭环 2)装配中当封闭环公差确定后,组成环越多则每 一环公差越小,故设计应满足:最短尺寸链原则。
校核计算举例
校核计算的步骤是:根据装配要求确定封闭环;
Hale Waihona Puke 寻找组成环;画尺寸链线图;判别增环和减环; 由各组成环的基本尺寸和极限偏差验算封闭环 的基本尺寸和极限偏差。 例1、如图a所示的结构,已知各零件的尺寸: 0 0 A1=30 0.13 mm,A2=A5=5 0.075 mm, 0 0.18 A3=43 0.02 mm,A4=3 0.04 mm设计要求间隙 A0为0.1~0.45mm,试做校核计算。
2、按几何特征及空间位置分类
1) 长度尺寸链——全部环为长度的尺寸链 2) 角度尺寸链——全部环为角度的尺寸链 3)直线尺寸链—— 全部组成环平行于封闭 环的尺寸链。 4)平面尺寸链—— 全部组成环位于一个或 几个平行平面内,但某些组成环不平行于 封闭环的尺寸链。 5) 空间尺寸链——组成环位于几个不平行 平面内的尺寸链。
校核计算举例
解(l)确定封闭环为要求的间隙 A0;寻找组成环并画尺寸链
线图(上图b);判断A3为增环,A1、A2、A4和A5为减环。 (2)封闭环的基本尺寸 A0=A3—(A1+A2+A4+A5)=43 —(30+5+3+5)=0 0.45 即要求封闭环的尺寸为0 0.10 mm 。 (3)计算封闭环的极限偏差 ES。=ES3—(EI1+EI2+EI4+EI5) = +0 . 18— ( —0 . 13—0 . 075—0 . 04—0 . 075 ) =+0.50 EI。=EI3—(ES1+ES2+ES4+ES5) =+0.02mm—(0+0+0+0)mm=+0.02mm (4)计算封闭环的公差 T。=T1+T1+ T2+T3+T4 +T5 =0.13+0.075十0.16+0.075十0.04=0.48mm 校核结果表明,封闭环的上、下偏差及公差均已超过规定范 围。
《数控编程及操作》习题及答案

《数控编程及操作》习题及答案数控综合试题库一填空题1.数控系统的发展方向将紧紧围绕着性能、价格和可靠性三大因素进行。
2.加工中心按主轴在空间所处的状态可以分为立式、卧式和复合式。
3.数控机床的导轨主要有滑动、滚动、静压三种。
4.数控机床的类别大致有开环、闭环、半闭环。
5.按车床主轴位置分为立式和卧式。
6.世界上第一台数控机床是 1952 年 PARSONS公司与麻省理工学院合作研究的三坐标数控铣床。
7.数控电加工机床主要类型有点火花成型和线切割机床。
8.铣削各种允许条件下,应尽量选择直径较大的铣刀,尽量选择刀刃较短的铣刀。
9.合适加工中心的零件形状有平面、曲面、孔、槽等。
10.数控加工程序的定义是按规定格式描述零件几何形状和加工工艺的数控指令集。
11.常用夹具类型有通用、专用、组合。
13.基点是构成轮廓的不同几何素线的交点或切点。
14.加工程序单主要由程序体和注释两大部分构成。
15.自动编程又称为计算机辅助编程。
其定义是:利用计算机和相应的前置、后置处理程序对零件进行处理,以得到加工程序单和数控穿孔的一种编程方法。
16.按铣刀形状分有盘铣刀、圆柱铣刀、成形铣刀、鼓形刀铣17.按走丝快慢,数控线切割机床可以分为快走丝和慢走丝。
18.数控机床实现插补运算较为成熟并得到广泛应用的是直线插补和圆弧插补。
18.穿孔带是数控机床的一种控制介质,国际上通用标准是ISO 和EIA 两种,我国采用的标准是I SO。
19.自动编程根据编程信息的输入与计算机对信息的处理方式不同,分为以自动编程语言为基础的自动编程方法和以计算机绘图语言为基础的自动编程方法。
20.数控机床按控制运动轨迹可分为点位控制、直线控制和轮廓控制等几种。
按控制方式又可分为开环、闭环和半闭环控制等21.对刀点既是程序的起点,也是程序的终点。
为了提高零件的加工精度,对刀点应尽量选在零件的设计基准或工艺基准上。
22.在数控加工中,刀具刀位点相对于工件运动的轨迹称为加工路线。
《钳工》(四级)考核要素细目表

《钳工》(四级)理论知识考核要素细目表职业(工种)名称钳工等级四级职业代码考核点代序号码分数系名称·内容数重要系数备注章节目点1基础知识45 11机械制图8 111制图基础知识1 11111标注尺寸的基本原则21112尺寸数字的标注112机件形状的表达方法1 31121基本视图的表达方法41122剖视图的表达方法51123断剖面图的表达方法61124其他表达方法113零件图4 71131零件图的基本内容81132典型零件的视图表达方法91133零件图的尺寸标注101134尺寸基准的选择111135合理标注尺寸的原则121136常见尺寸标注方法131137零件图的技术要求141138极限与配合的基本术语151139极限与配合标准的基本规定1611310形位误差和形位公差的概念1711311表面粗糙度概念1811312测绘零件图114常用零件的画法1 191141螺纹的画法201142螺纹代号的标注211143单个直齿圆柱齿轮的规定画法221144齿轮啮合的规定画法职业(工种)名称钳工等级四级职业代码考核点代序号码分数系名称·内容数重要系数备注章节目点115装配图1 231151装配图的表达方法241152拆画零件图12液压传动5 121液压传动的工作原理1 251211液压传动的工作原理122液压传动系统的组成1 261221液压传动系统的动力元件271222液压传动系统的执行元件281223液压传动系统的控制调节元件291224液压传动系统的辅助元件123液压传动的优缺点1 301231液压传动的优点311232液压传动的缺点124液压油的性质与选用1 321241密度的概念331242粘度的概念341243温度、压力对粘度的影响351244液体的可压缩性361245液压油的选用125液体压力、流量、功率1 371251液体压力的概念381252液体流量的概念391253液体功率的概念13切削原理和刀具11 131刀具材料1 401311刀具材料的基本要求411312刀具材料的种类421313刀具材料的主要成分431314刀具材料的用途132刀具角度的合理选择2 441321前角的选择职业(工种)名称钳工等级四级职业代码考核点代序号码分数系名称·内容数重要系数备注章节目点451322后角的选择461323主偏角的选择471324刃倾角的选择133金属切削过程3 481331切屑的类型491332积屑瘤对切削加工的影响501333积屑瘤形成的因素511334切削力的概念531335影响切削力的因素531336切削热的传出541337影响切削温度的因素551338切削液的作用561339切削液的选用134刀具磨损及磨钝标准1 571341刀具磨损的形式581342刀具磨损的原因591343刀具磨损的过程601344刀具的磨钝标准135刀具寿命及影响刀具寿命的因素1 611351刀具寿命621352影响刀具寿命的因素631353刀具寿命的确定原则136刀具的刃磨1 641361成形车刀的刃磨方法651362铰刀的刃磨方法137磨削原理及砂轮的选择2 661371磨削加工的特点671372磨削加工的应用681373砂轮的结构691374砂轮磨料的选择701375砂轮粒度的选择711376砂轮结合剂的选择职业(工种)名称钳工等级四级职业代码考核点代序号码分数系名称·内容数重要系数备注章节目点721377砂轮硬度的选择14机械制造工艺11 141基本概念2 731411工艺过程的概念741412工序的概念751413安装的概念761414工位的概念771415工步的概念781416生产的类型791417各种生产类型的工艺特征142机械加工精度的概念1 801421加工精度的定义811422加工精度的主要内容821423获得尺寸精度的方法831424获得形状精度的方法143工件的装夹和基准2 841431工件常用的装夹方法851432基准的分类863定位基准面的概念871434粗基准的选择881435精基准的选择144工艺尺寸链1 891441工艺尺寸链的基本概念901442工艺尺寸链极值法的计算公式145产生误差的原因4 911451工艺系统的概念921452机床主轴的回转误差931453机床导轨的误差941454误差的敏感方向951455机床传动链的误差961456工艺系统的刚度971457工艺系统受力变形产生的误差职业(工种)名称钳工等级四级职业代码考核点代序号码分数系名称·内容数重要系数备注章节目点981458切削中的“误差复映”规律991459工艺系统受热变形引起的误差10014510工件残余应力引起的误差10114511磨损引起的误差10214512加工原理误差146机械加工的表面质量1 1031461机械加工的表面质量的含义1041462表面质量对零件使用性能的影响1051463影响机械加工表面粗糙度的因素1061464影响加工表面物理力学性能的工艺因素15机床夹具10 151基本概念1071511夹具的定义2 1081512夹具的组成1091513定位元件的作用1101514对刀或导向元件的作用1111515夹具的作用1121516夹具的分类152工件的定位5 1131521六点定位原理1141522完全定位的概念1151523不完全定的概念1161524过定位的概念1171525欠定位的概念1181526支承板的定位方式1191527圆柱定位销(心轴)的定位方式1201528V形块的定位方式1211529定位套的定位方式12215210圆锥销的定位方式12315211定位元件的组合使用12415212辅助支承的概念12515213产生定位误差的原因职业(工种)名称钳工等级四级职业代码考核点代序号码分数系名称·内容数重要系数备注章节目点12615214常见定位方式的定位误差计算153工件的夹紧2 1271531夹紧装置的基本要求1281532夹紧力方向的确定1291533夹紧力作用点的确定1301534基本夹紧机构的特点1311535自动定心夹紧机构的特点1321536联动夹紧机构的特点154钻夹具1 1331541钻夹具的类型1341542翻转式钻模的特点1351543钻套的选择1361544钻模板联接的方式2专业知识50 21复杂工件的划线3 211复杂工件的划线方法1 1372111箱体工件划线基准的选择1382112畸形工件划线的特点1392113凸轮划线的方法212大型工件的划线1 1402121平板接长的划线法1412122工件位移的划线法1422123拉线吊线的划线法213回转体和多面体的展开1 1432131可展表面的定义1442132不可展表面的定义22群钻和钻削特殊孔9 221群钻4 1452211麻花钻的缺点1462212标准群钻的特点1472213标准群钻的优点1482214标准群钻的应用职业(工种)名称钳工等级四级职业代码考核点代序号码分数系名称·内容数重要系数备注章节目点1492215铸铁群钻的特点1502216钻黄铜群钻的特点1512217钻纯铜群钻的特点1522218钻铝合金群钻的特点1532219钻薄板群钻的特点15422110钻胶木群钻的特点15522111钻有机玻璃群钻的特点15622112钻橡胶群钻的特点222各种特殊孔的钻削4 1572221钻小孔常出现的问题1582222钻小孔的注意点1592223在斜面上钻孔常出现的问题1602224在斜面上钻孔的一般方法1612225接长钻钻深孔常出现的问题1622226接长钻钻深孔的注意点1632227钻精孔的概念1642228钻精孔的方法1652229钻精孔的注意点16622210孔距精度要求较高的孔系的加工方法16722211钻相交孔的方法223立式钻床常见故障1 1682231保险离合器失效的原因1692232主轴上下移动出现轻重现象的原因1702233钻孔轴线倾斜的原因23旋转件的平衡2 231旋转件平衡的基本知识1 1712311离心力对机器运行的影响1722312静不平衡1732313动不平衡232动、静平衡1 1742321静平衡的概念1752322静平衡的调整方法职业(工种)名称钳工等级四级职业代码考核点代序号码分数系名称·内容数重要系数备注章节目点1762323动平衡的的概念24机床导轨5 241机床导轨的结构类型和精度要求3 1772411三角形导轨的特点1782412燕尾形导轨的特点1792413滚动导轨的特点1802414对机床导轨的基本要求1812415机床导轨材料的性能1822416机床导轨的精度1832417机床导轨直线度的要求1842418刮研导轨接触精度的要求1852419导轨直线度误差的计算18624110光学平直仪测量导轨的特点242机床导轨的刮削和检查1 1872421刮削导轨的基本原则1882422卧式车床床身导轨的刮削1892423外圆磨床床身导轨的刮削243机床导轨的修整1 1902431机床导轨面修整的一般要求1912432机床导轨面的修整方法25联接件与轴承的装配7 251螺纹联接的装配1 1922511螺纹联接的预紧1932512螺纹联接的防松1942513成组螺钉、螺栓、螺母的装配方法252键、销联接的装配1 1952521平键联接的装配1962522花键联接的装配1972523圆柱销的装配252圆柱面过盈联接的装配1 1982521圆柱面过盈联接的压装法1992522圆柱面过盈联接的热装法职业(工种)名称钳工等级四级职业代码考核点代序号码分数系名称·内容数重要系数备注章节目点2002523圆柱面过盈联接的冷装法253滑动轴承的特点1 2012531动压轴承的工作原理2022532多瓦式动压轴承的特点2032533静压轴承的优点254滑动轴承的装配要点1 2042541多瓦式动压轴承的刮研2052542轴套装配后轴套孔的修整2062543锥形表面滑动轴承的装配要点2072544剖分式滑动轴承的配刮要点255滚动轴承的装配2 2082551滚动轴承的配合制度2092552滚动轴承配合的选择2102553滚动轴承装配前的准备工作2112554滚动轴承的预加负荷2122555圆柱孔轴承的装配2132556推力球轴承的装配2142557滚动轴承的定向装配26传动机构的装配调整6 261带传动机构的装配调整1 2152611V带传动机构的装配要求2162612传动带张紧力的调整2172613带轮与轴的装配262链传动机构的装配调整1 2182621链传动机构的装配要求2192622链传动机构的装配263齿轮传动机构的装配调整1 2202631齿轮传动机构的装配的技术要求2212632圆柱齿轮副接触斑点的检查2222633锥齿轮接触斑点的检查264蜗杆传动机构的装配1职业(工种)名称钳工等级四级职业代码考核点代序号码分数系名称·内容数重要系数备注章节目点2232641对蜗杆、蜗轮轴线的要求2242642蜗杆副接触斑点的检验2252643蜗杆副齿侧间隙的检查265联轴器和离合器的装配1 2262651联轴器和离合器的作用2272652联轴器的类型2282653联轴器装配的技术要求266螺旋机构的装配1 2292661螺旋机构配合间隙的调整2302662单螺母结构消隙力的方向2312663螺旋机构的校正27装配工艺规程4 271装配工艺规程基础知识1 2322711部件装配的概念2332712总装配的概念2342713装配单元的概念272制订装配工艺规程的步骤1 2352721装配的组织形式2362722装配顺序的确定2372723装配单元系统图的特点273装配尺寸链的基本知识2 2382731装配尺寸链封闭环的特点2392732完全互换法的特点2402733选配法的特点2412734修配法的特点2422735可动调整法的特点2432736固定调整法的特点28卧式车床装配6 281CA6140型卧式车床4 2442811车床主要部件的功能2452812主轴转速的级数2462813车螺纹传动链的机构职业(工种)名称钳工等级四级职业代码考核点代序号码分数系名称·内容数重要系数备注章节目点2472814变换螺距机构的特点2482815主轴部件的结构及调整2492816主轴结构的特点2502817多片式摩擦离合器的作用2512818多片式摩擦离合器的调整2522819制动装置的特点25328110溜板箱的主要机构25428111互锁机构的作用25528112安全离合器和超越离合器的作用282卧式车床的装配工艺2 2562821检验棒的主要用途2572822水平仪与检验桥板的结合使用2582823安装齿条的要点2592824溜板箱左右位置的确定2602825安装丝杠的要点2612826安装主轴箱的要求29卧式车床的装配质量检验3 291卧式车床的试车和验收2 2622911试车和验收的程序2632912车床空转试验的方法2642913空运转时对轴承温度的要求2652914机床负荷试验的目的2662915工作精度检验的目的2672916切槽试验的目的292几何精度的检验1 2682921车床溜板用导轨精度的要求2692922主轴锥孔轴线径向圆跳动的检验方法2702923安装尾座精度的要求210泵、制冷机及压缩机3 2101离心泵2 27121011泵的定义27221012泵的种类职业(工种)名称钳工等级四级职业代码考核点代序号码分数系名称·内容数重要系数备注章节目点27321013泵的主要参数27421014离心泵的工作原理27521015离心泵的运行27621016离心泵常见的故障2102制冷机1 27721021制冷机的蒸发过程27821022制冷机的压缩过程27921023制冷机的冷凝过程28021024制冷机的膨胀过程211机械运行时工作参数的测定22111机械工作时温度、转速和功率的测定1 28121111测量温度的仪器28221112转速的测定28321113功率的测定2112机械运行时流体的压力和流量的测定1 28421121压力的测量28521122流量的测量3相关知识531生产管理和专业技术管理基本内容3311生产管理21 2863111车间生产过程的组成2873112车间内生产单位的组成2883113车间布置的要求2893114车间在制品管理的含义2903115车间生产调度的要求2913116车间定置管理的任务312技术管理15 2923121车间技术管理的内容5 2933122车间日常工艺的管理2943123车间技术革新的内容32电气传动基础知识2321机床电力设备11职业(工种)名称钳工等级四级职业代码考核点代序号码分数系名称·内容数重要系数备注章节目点2953211机床电力设备的组成1 2963212手动控制的电器2973213接触控制的电器322常用低压电器15 2983221继电器的作用5 2993222熔断器的作用3003223主令电器的类型《钳工》(四级)操作技能考核要素细目表职业(工种)名称钳工等级四级职业代码考核点代序号码重要系名称·内容数备注项目单元细目1锉配加工11平面和曲面锉削1111尺寸控制2112形状与位置精度控制3113表面粗糙度12螺孔加工4121螺孔尺寸5螺孔轴线与端面垂直度6122孔距13钻孔加工7131孔径尺寸8132表面粗糙度9133孔距14铰孔加工10141孔径尺寸11142孔囗倒角12143表面粗糙度13144孔距15锪孔加工14151锪90°锥坑15152锪90°倒角16153锪孔尺寸17154表面粗糙度2机构拆卸、装配与调整1821V形导轨拆卸与装配1922配合间隙控制2023圆柱销装配2124紧定螺钉装配与调整2225可动零件移动或转动应灵活五卡阻现象2326装配件装配后的外观质量续表职业(工种)名称钳工等级四级职业代码考核点代序号码重要系名称·内容数备注项目单元细目3零件测绘31图形24311视图表达合理25312螺纹的画法与标注26313键槽画法32测量27321普通螺纹、梯形螺纹的主要参数测量28322测量尺寸的圆整29323测量尺寸的标准化33标注30331尺寸及公差标注合理、完整、正确、清晰31332形位公差的标注32333粗糙度的标注33334螺纹的标注34技术要求34341粗糙度的合理选用35342工件材料的选用36343热处理的合理选用37344尺寸公差代号与极限偏差的查表38345技术要求的正确表达4零件工艺编制39411毛坯选择正确140412工序划分、顺序合理、内容正确941413本工种工步划分、顺序合理、内容正确942414热处理工序安排合理543415本工种工艺装备和机床选用合理944416本工种加工的工时定额的估算5(注:将“操作技能考核要素细目表”和“理论知识考核要素细目表”组合成为《考核要素细目表》)。
尺寸链介绍PPT

尺寸链介绍2010年5月目录尺寸链概述 尺寸链计算案例分析内容提要尺寸链计算软件介绍 尺寸链计算软件演示交流尺寸链概述本部分主要介绍尺寸链中的基本概念、名 词定义、基本方法、原理、目的以及相关 的理论基础等。
尺寸链计算目的• • • • • 验证设计是否能达到质量要求 提高产品合格率 预防生产过程中的重复工作和延工现象 降低产品的返修率 实现产品的无修锉、大批量生产降低成本、缩短周期、提高质量尺寸链计算与研发成本关系尺寸链基本概念在零件的加工或机器的装配中决定各个几何要素(点、线、 面)间相互位置的尺寸通常都是彼此相联系的、按一定顺 序排列的、一个封闭的尺寸系统,这个尺寸系统就称为尺 寸链尺寸链主要特征封闭性:尺寸链必须是一组相关尺寸按 顺序首尾相接而形成的封闭轮廓,其中应 包含一个间接保证的尺寸和若干个与之有 关的直接获得的尺寸 关联性:尺寸链内间接保证的尺寸的大 小和变化范围(即精度),是受该链内直接 获得的尺寸大小和变化范围所制约的,彼 此间具有特定的函数关系尺寸链的组成单元——环构成尺寸链的每一个尺寸都称为“环”,一条尺寸链中必包含两种环。
封闭环:尺寸链中最终被间接保证的那个尺寸称为封闭环,它是在加工或装配之后形成的。
组成环:除封闭以外尺寸链中其它所有的环皆称为组成环。
组成环按其对封闭环的影响性质又可划分为增环和减环。
尺寸链的组成单元——闭环对于单个零件的加工而言,封闭环通常是零件设计图上未标注的尺寸即最不重要的尺寸。
对于若干零部件的装配而言,封闭环通常是对有关要素间的联系所提出的技术要求,如位置精度、距离精度、间隙过盈等。
注意,不要错误的认为需要求的环就是闭环。
尺寸工程、尺寸链计算、公差分析关系尺寸工程尺寸链计算数据检测统计分析…公差分析公差分析公差分配公差分配((设计设计))公差分配公差分配((设计设计))尺寸链的分类——各环尺寸所处的空间位置线性尺寸链:尺寸链各环位于同一平面内,且互相平行平面尺寸链:尺寸链各环位于同一平面内,但其中有些环彼此不平行(存在一定的夹角关系)。
高数控车工理论试题附带答案

数控车工高级理论试题1 我国古代将“道德”二字连用始于()A、春秋战国B、秦朝C、唐朝D、宋朝 A2 维护社会道德的手段是()A、法律手段B、行政手段C、舆论及教育手段D、组织手段 C3 职业道德是指()A、人们在履行本职工作中所就应遵守的行为规范和准则B、人们在履行本职工作中所确立的奋斗目标C、人们在履行本职工作中所确立的价值观D、们在履行本职工作中所遵守的规章制度 A4 党的十六大报告指出,认真贯彻公民道德建设实施纲要,弘扬爱国主义精神,以为人民服务为核心,以集体主义为原则,以()为重点。
A、无私奉献B、遵纪守法C、爱岗敬业D、诚实守信 D5 市场经济条件下,我们对“义”和“利”的态度应该是()A、见利思义B 先利后义C、见利忘义D、不利不于 A6 社会主义市场经济条件下的诚信()A、只是一种法律规范B、只是一种道德规范C、既是法律规范、又是道德规范D、既不是法律规范,又不是道德规范 C7 社会主义道德建设的基本要求是()A、心灵美、语言美、行为美、环境美B、爱祖国、爱人民、爱劳动、爱科学、爱社会主义C、仁、义、礼、智、信D、树立正确的世界观、人生观、价值观 B8 职业道德建设中,你认为正确的做法是()A、风来一阵忙,风过如往常B、常抓不懈、持之以恒C、讲起来重要,干起来次要D、生产好了,职业道德建设自然也好B9 职业道德建设及企业的竞争力的关系是()A、互不相关B、源泉及动力关系C、相辅相承关系D、局部及全局关系 B10 在现实条件下,你对“个人修养”的积极选择是()A、竞争激烈、弱肉强食、个人修养难以对待B、贫富悬珠、心理失衡、个人修养难以适应C、物质诱惑、社会风气、个人修养难以抵御D、加强修养、提高品德、促进社会风气好转 D11 强化职业责任是()职业道德观范的具体要求A、团结协作B、诚实守信C、勤劳节俭D、爱岗敬业 D12 树立职业道德,正确的选择是()A、从事自己喜爱的职业,才能树立职业道德B、从事报酬高的职业,才能树立职业道德C、从事社会地位高的职业,才能树立职业道德D、确立正确的择业观,才能树立职业道德 D13 你认为市场经济对职业道德建设带来何种影响()A、带来正面影响B、带来负页影响C、正、负面影响都有D、没有带来影响 C14 在企业中职工及领导的关系应始终保持一种()A、和谐、融洽、默契的关系B、严肃、敬畏、疏远的关系C、佣、主仆、合同的关系D、防范、对立、疏远的关系 A15 企业的竞争力及职业道德建设的关系是()A、互不相关B、相辅相承关系C、源泉及动力关系D、局部及全局关系 C16 下列说法中,符合语言规范具体要求的是()A、多说俏皮话B、用尊称C、可用忌语D、语速要快 B17 下面关于以德治国及依法治国的关系中正确的是()A、依法治国比以德治国更为重要B、以德治国比依法治国更为重要C、德治是目的,法治是手段D、以德治国及依法治国是相辅相成,相互促进 D18 职业道德主要通过调节企业及市场的关系,增强企业的凝聚力。
《机械制造基础》复习题答案

机械制造复习提纲一名词解释:外链传动链:前角:定位:完全定位:切削三要素:零件加工质量:工序:生产纲领:工艺尺寸链:前角、主切削刃:切削用量:铣削用量:生产纲领装配:顺铣:展成法::砂轮的组织:二填空:1工件表面的成形方法有轨迹、成型、展成等。
2工件加工的切削运动有主运动、进给。
3机床由传动装置、执行装置、动力装置组成。
4按照控制方式分,数控机床分为点控制、线控制、轮廓控制。
6刀具的常用材料有高速钢、硬质合金钢。
7切削液的作用有清洗、润滑、冷却。
8按照用途分,车刀分为切断刀、外圆车刀、端面车刀等。
9车刀由前刀面、后刀面、主副后刀面主切削刃等组成。
10铣削用量包括背吃刀量、铣削用量、进给量、切削速度。
11影响切削力的因素材料、进给量、前角等。
12在切削三要素中,对切削热影响最大的是切削速度。
13刀具的磨损形式有前刀面磨削、后刀面磨削、前后刀面同时磨削。
14平面铣削分为周铣和端铣。
15周铣分为顺铣、逆铣。
16孔的加工方法有钻、扩、铰、镗等,其中,在实体上加工孔用钻。
17对于孔径大于φ80mm的孔,常选用镗孔来加工。
18 在孔的加工中,不能修正孔的轴线歪斜的加工方法有铰、拉。
20 砂轮由磨料、结合剂、气孔组成。
21砂轮的五参数是磨料、粒度、结合剂、硬度、组织。
22齿形的加工方法分为成型、展成。
23滚齿可以加工圆柱齿轮、斜柱齿轮、涡轮,不能加工内齿轮和多联齿轮。
24插齿可以加工内齿轮、多联齿轮。
25齿面的精加工方法有剃齿、衔齿、磨齿。
26刨削加工主要用于加工母线是直线的工件的加工,主要特点成本低、直线度好。
27拉削可加工各种形状的孔、平面、沟槽等,不能加工盲孔、阶梯孔、薄壁孔等。
28拉削不能修正孔的轴线的歪斜。
29螺纹的加工方法有车、铣、磨等。
30机械加工精度包括尺寸、形状、位置。
31加工质量包括Ra的值、表面力学物理性能。
32主轴的回转运动误差表现为:轴向窜动、径向跳动、角度摆动三种形式。
33机床导轨的误差分为:导轨在水平面的直线度误差、导轨在垂直平面内的直线度误差、导轨面间的平行度误差。
机械加工工艺习题册答案(1-8)
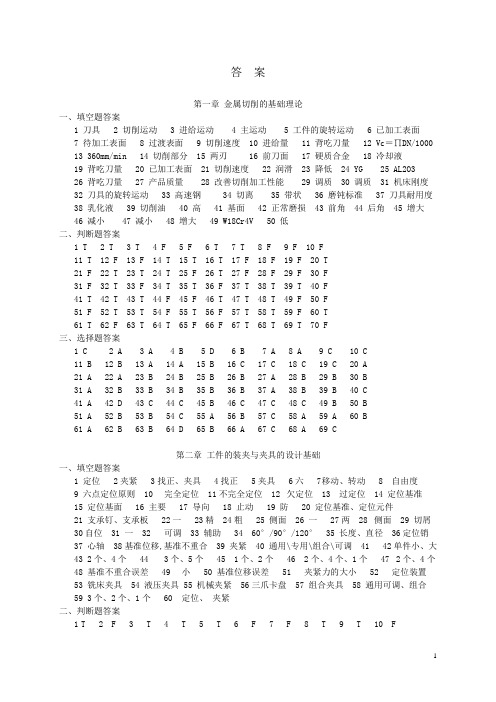
答案第一章金属切削的基础理论一、填空题答案1 刀具2 切削运动3 进给运动4 主运动5 工件的旋转运动6 已加工表面7 待加工表面 8 过渡表面 9 切削速度 10 进给量 11 背吃刀量 12 Vc=∏DN/100013 360mm/min 14 切削部分 15 两刃 16 前刀面 17 硬质合金 18 冷却液19 背吃刀量 20 已加工表面 21 切削速度 22 润滑 23 降低 24 YG 25 AL2O326 背吃刀量 27 产品质量 28 改善切削加工性能 29 调质 30 调质 31 机床刚度32 刀具的旋转运动 33 高速钢 34 切离 35 带状 36 磨钝标准 37 刀具耐用度38 乳化液 39 切削油 40 高 41 基面 42 正常磨损 43 前角 44 后角 45 增大46 减小 47 减小 48 增大 49 W18Cr4V 50 低二、判断题答案1 T2 T3 T4 F5 F6 T7 T8 F9 F 10 F11 T 12 F 13 F 14 T 15 T 16 T 17 F 18 F 19 F 20 T21 F 22 T 23 T 24 T 25 F 26 T 27 F 28 F 29 F 30 F31 F 32 T 33 F 34 T 35 T 36 F 37 T 38 T 39 T 40 F41 T 42 T 43 T 44 F 45 F 46 T 47 T 48 T 49 F 50 F51 F 52 T 53 T 54 F 55 T 56 F 57 T 58 T 59 F 60 T61 T 62 F 63 T 64 T 65 F 66 F 67 T 68 T 69 T 70 F三、选择题答案1 C2 A3 A4 B5 D6 B7 A8 A9 C 10 C11 B 12 B 13 A 14 A 15 B 16 C 17 C 18 C 19 C 20 A21 A 22 A 23 B 24 B 25 B 26 B 27 A 28 B 29 B 30 B31 A 32 B 33 B 34 B 35 B 36 B 37 A 38 B 39 B 40 C41 A 42 D 43 C 44 C 45 B 46 C 47 C 48 C 49 B 50 B51 A 52 B 53 B 54 C 55 A 56 B 57 C 58 A 59 A 60 B61 A 62 B 63 B 64 D 65 B 66 A 67 C 68 A 69 C第二章工件的装夹与夹具的设计基础一、填空题答案1 定位 2夹紧 3找正、夹具 4找正 5夹具 6六 7 移动、转动 8 自由度9 六点定位原则 10 完全定位 11不完全定位 12 欠定位 13 过定位 14 定位基准15 定位基面 16 主要 17 导向 18 止动 19 防 20 定位基准、定位元件21 支承钉、支承板 22一 23精 24 粗 25 侧面 26 一 27两 28 侧面 29 切屑30自位 31 一 32 可调 33 辅助 34 60°/90°/120° 35 长度、直径 36定位销37 心轴 38基准位移,基准不重合 39 夹紧 40 通用\专用\组合\可调 41 42单件小、大43 2个、4个 44 3个、5个 45 1个、2个 46 2个、4个、1个 47 2个、4个48 基准不重合误差 49 小 50 基准位移误差 51 夹紧力的大小 52 定位装置53 铣床夹具 54 液压夹具 55 机械夹紧 56 三爪卡盘 57 组合夹具 58 通用可调、组合59 3个、2个、1个 60 定位、夹紧二、判断题答案1 T2 F3 T4 T5 T6 F7 F8 T9 T 10 F11 T 12 T 13 T 14 T 15 F 16 T 17 F 18 T 19 T 20 F21 T 22 T 23 T 24 F 25 T 26 F 27 F 28 F 29 F 30 T31 T 32 F 33 F 34 F 35 T 36 F 37 F 38 F 39 T 40 F41 F 42 T 43 F 44 F 45 F 46 F 47 F 48 T 49 F 50 F51 F 52 F 53 T 54 F 55 T 56 T 57 F 58 T 59 F 60 F61 T 62 T 63 F 64 F 65 T 66 T 67 T 68 T 69 F 70 T71 T 72 F 73 T 74 F 75 T 76 F 77 T 78 F 79 T 80 F81 T 82 F 83 T 84 T 85 T 86 F 87 F 88 F 89 F 90 F三、简答题答案1根据工件被限制的自由度的情况,定位分为哪些情况?完全定位。
车工(数控)高级操作职业技能考核复习题二

车工(数控)高级操作职业技能考核复习题二判断题:1、表面粗糙度符号,表面粗糙度符号表示表面是用去除材料的方法获得.×2、剖视图可分为全剖视图、半剖视图和局部剖视图三种.3、孔、轴公差代号由基本偏差与标准公差数值组成.4、配合可分为间隙配合和过盈配合两种.×5、国际规定公差共有十四项,其中形状公差六项,位置公差八项.6、按加热温度不同回火可分为低温、常温和高温回火。
7、铸造碳钢ZG270—500的抗拉强度为500N/mm2。
8、工艺尺寸链中,组成环可分为增环和减环。
9、数控机床适用于单品种,大批量的生产。
10、加工工件时,进给量太大,会造成工件表面质量差。
11、再同一次安装中进行多工序加工,应先完成对工件刚性破坏较大的工序。
12工件以圆内孔作为定位基面时,常用圆柱定位销、圆锥定位销、定位心轴等定位元件。
13、V形块定位的优点是对中性好。
14、粗基准即为零件粗加工中所用基准,精基准即为零件精加工中所用基准。
15、使用千分尺时,用等温方法将千分尺和被测件保持同温,这样可以减少温度对测量结果的影响。
16、硬质合金切断刀切断中碳钢,不许用切削液以免刀片破裂。
17、刀具耐热性是指金属切削过程中产生剧烈摩擦的性能。
18、外圆车刀切削部分一般由四个面、两条刀刃和一个刀尖组成。
19、引入三个相互垂直的参考平面,目的是为了确定和测量车刀的几何角度。
20、当时用半径补偿时,编程按工件实际尺寸加上刀具半径来计算。
21、顺序选刀方式具有无需刀具识别装置,驱动控制简单的特点。
22、如果实际刀具与编程刀具长度不符时,可用长度补偿来进行修正,不必改变所编程序。
23刀具长度补偿值表示目标刀具与标准零号刀具的长度差值。
24、使用刀具半径补偿的工作是通过执行含有G41(G42)指令来实现的。
25、当用端面铣刀加工工件的端面时则须长度补偿,也须刀具半径补偿。
26中央处理器通常由运算器和控制器两部分组成,简称CPU。
工艺尺寸链的概念 -回复

工艺尺寸链的概念-回复什么是工艺尺寸链?工艺尺寸链是指在产品开发和生产过程中,涉及到的各个工艺环节的尺寸链条。
它描述了产品从设计到制造的每个阶段,各环节之间的尺寸关系。
工艺尺寸链的目的是确保产品各部件之间的尺寸精度,以便实现产品的功能和性能要求。
在产品制造过程中,每一个工艺步骤都会对产品的尺寸产生影响。
因此,如果不合理地设计和控制工艺尺寸链,可能会导致产品尺寸不匹配、功能失效或者无法组装等问题。
为此,需要对工艺尺寸链进行全面的分析和优化。
工艺尺寸链的构成一个完整的工艺尺寸链通常包含以下几个主要的环节:1. 设计阶段:在产品设计阶段,工程师会根据产品的功能和性能要求进行尺寸设计。
这些尺寸要与其他部件相匹配,以确保产品能够正常工作。
设计阶段的尺寸决策会影响后续工艺环节。
2. 材料准备:在选择材料和准备材料阶段,尺寸链开始发生变化。
不同材料的性质和收缩率都会对产品尺寸产生影响。
因此,在此阶段需要进行材料的尺寸调整和优化。
3. 制造工艺:制造工艺包括材料加工、装配、焊接、喷涂等环节。
每个工序都有自己的尺寸要求和容差范围。
在制造过程中,需要严格控制每个工序的尺寸,避免尺寸误差的累积。
4. 检验与测试:为了确保产品质量,需要进行检验与测试。
这些过程涉及到对产品尺寸的测量和验证。
通过测量和验证,可以发现和修复尺寸不准确之处,并进行调整。
5. 最终组装:在最终组装过程中,各个部件需要精确地配合。
如果尺寸不匹配,可能会导致装配困难或者装配不成功。
因此,在最终组装前需要对各个部件的尺寸进行检查和调整。
工艺尺寸链的优化为了优化工艺尺寸链,可以采取以下措施:1. 设计阶段优化:在产品设计阶段,要考虑到尺寸链的重要性。
工程师应该根据产品的功能和性能要求,合理确定尺寸和容差范围。
同时,要与其他工艺环节的相关人员进行充分的沟通和协调。
2. 材料准备优化:在选择材料和准备材料过程中,要考虑材料的性质和收缩率。
选择合适的材料和调整材料的尺寸,以适应后续工艺环节的要求。
机械制造名词解释

1. 工艺系统:由机床、夹具、刀具和工件组成的系统。
2. 强度:金属材料在外载荷的作用下抵抗塑性变形和断裂的能力。
3. 硬度:金属材料抵抗比它更硬的物体压入其表面的能力,即抵抗局部塑性变形的能力。
4. 冲击韧性:金属抵抗冲击载荷作用而不被破坏的能力。
5. 疲劳强度:金属材料经受无数次交变载荷作用而不引起断裂的最大应力值。
6. 蠕变强度:在长期高温载荷的作用下,金属材料对塑性变形的抵抗能力。
7. 渗碳:零件表面渗入碳原子的过程。
8. 氮化:向钢的表面渗入碳原子的过程。
9. 碳钢:含碳量小于2.11%的铁碳合金。
10. 铸铁:含碳量大于2.11%的铁碳合金。
11. 有色金属:除钢、铁、猛以外的其他金属。
12. 高分子材料:以高分子化合物为主要组成物的材料。
13. 塑料:以合成树脂为主要成分的高分子材料,它由合成树脂和添加剂组成。
14. 铸造:制造铸型,并将熔融的金属浇入铸型,凝固后获得一定形状和性能的铸件的成行方法。
15. 锻压:属于金属塑性加工的范畴。
16. 焊接:指通过加热、加压或两者并用,使连接达到原子结合的一种加工方法。
17. 尺寸:以特定单位表示线性尺寸的数值。
18. 进给运动:不断地把切削层投入切削,以逐渐切出整个工件表面的运动19. 车削:在车床上,工件旋转,车刀在屏幕,平面内作直线或曲线移动的切削。
20. 铣削:在铣床上,用旋转的铣刀切削工件上各种表面或沟槽的加工方法。
21. 刨削:在刨床上用刨刀加工工件的方法22. 钻销:用钻头在实体材料上加工出孔的方法。
23. 磨销:用砂轮或其他模具对工件表面进行切削加工的方法。
24. 夹具:在机械加工,为了保证工件加工精度,使之占有确实位置以接受加工或检测的工艺装备统称为机床夹具。
25. 加工精度:零件加工后的实际几何参数与理想参数的符合程度。
26. 加工误差:零件加工后的实际几何参数与理想参数的偏差程度。
27. 加工表面质量:机器零件在加工后的表面状态。
电切削工技能鉴定试卷(中A)
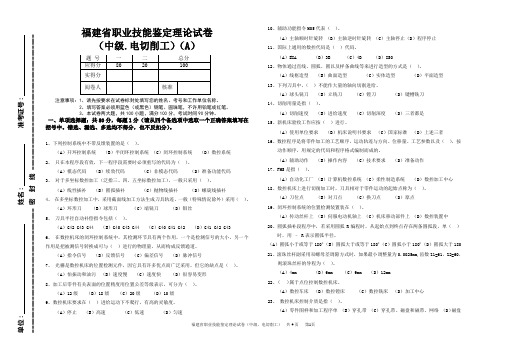
福建省职业技能鉴定理论试卷 (中级.电切削工)(A )注意事项:1、请先按要求在试卷标封处填写您的姓名、考号和工作单位名称。
2、填写答案必须用蓝色(或黑色)钢笔、圆珠笔,不许用铅笔或红笔。
3、本试卷两大题,共100小题,满分100分,考试时间90分钟。
一、单项选择题:共80分,每题1分(请从四个备选项中选取一个正确答案填写在括号中。
错选、漏选、多选均不得分,也不反扣分)。
1、下列控制系统中不带反馈装置的是( )。
(A )开环控制系统 (B )半闭环控制系统 (C )闭环控制系统 (D )数控系统2、 只在本程序段有效,下一程序段需要时必须重写的代码为( )。
(A )模态代码 (B )续效代码(C )非模态代码(D )准备功能代码3、 对于多坐标数控加工(泛指三、四、五坐标数控加工),一般只采用( )。
(A )线性插补 (B )圆弧插补(C )抛物线插补(D )螺旋线插补4、 在多坐标数控加工中,采用截面线加工方法生成刀具轨迹,一般(特殊情况除外)采用( )。
(A )环形刀 (B )球形刀(C )端铣刀(D )钼丝5、 刀具半径自动补偿指令包括( )。
(A )G42 G43 G44 (B )G40 G43 G44 (C )G40 G41 G42 (D )G41 G42 G43 6、 在数控机床的闭环控制系统中,其检测环节具有两个作用,一个是检测信号的大小,另一个作用是把被测信号转换成可与( )进行的物理量,从而构成反馈通道。
(A )指令信号 (B )反馈信号 (C )偏差信号 (D )脉冲信号7、 光栅是数控机床的位置检测元件,因它具有许多优点而广泛采用,但它的缺点是( )。
(A )怕振动和油污 (B )速度慢 (C )速度快(D )很容易变形8、加工后零件有关表面的位置精度用位置公差等级表示,可分为( )。
(A )12级 (B )18级 (C )20级(D )10级9、数控机床要求在( )进给运动下不爬行,有高的灵敏度。
- 1、下载文档前请自行甄别文档内容的完整性,平台不提供额外的编辑、内容补充、找答案等附加服务。
- 2、"仅部分预览"的文档,不可在线预览部分如存在完整性等问题,可反馈申请退款(可完整预览的文档不适用该条件!)。
- 3、如文档侵犯您的权益,请联系客服反馈,我们会尽快为您处理(人工客服工作时间:9:00-18:30)。
尺寸链原理是分析和计算工序尺寸很 有效的工具,在制定机械加工工艺过程 和保证装配精度中都有很重要的应用。
一、尺寸链的定义和组成
1.尺寸链的定义:在工件加工和机器装配过程中, 由相互连接的尺寸形成的封闭尺寸组。如图所 示
组成尺寸链的每一个尺寸,称为尺寸链的环。 尺寸链中凡属间接得到的尺寸称为封闭环,在 图所示尺寸链中,A0 是封闭环。 尺寸链中凡属通过加工直接得到的尺寸称为组 A 成环,图示尺寸链中A 、 2 都是尺寸链中的组 1 成环。
m
j m 1
n 1
EI(A )
j
j
n 1
封闭环下偏差
EI(A 0 ) EI(A i )
i 1
m n 1
m
j m 1
ES(A )
n 1 k 1 j k
封闭环的公差
T ( A 0 ) T( A i )
i 1
j m 1
T ( A ) T( A
例4:如图a)所示阶梯轴,A面是轴向的主要 0.1 40 设计基准,从它直接标注的尺寸有 0 mm 和 160 0.15mm 两个设计尺寸。与A、B、C三 个端面加工有关的工序尺寸是:
(1)在车削工序中,以精车过的A面为测量基 准,精车B面,保证工序尺寸L1;以精车过 的B面为基准精车C面,保证工序尺寸L2。 (2)淬火处理后对A面磨削,直接控制尺 0.1 寸 L3 400 mm ,同时间接保证尺 寸 160 0.15mm 。 试确定工序中,A2为增环, A3为减环,用极值法可求出:Z3 0.25 0.07mm 在以Z4为封闭环的尺寸链中,A3为增环, A4为减环,可求出: Z 4 0.15 0.04mm
由上述结果可见,磨削余量偏大,不利于提高 生产率和降低成本。为此,对各工序尺寸进行 适当调整: A 2 30.25 0.05mm, 令 A1 30.8 0.1mm , A 3 30.1 0.02mm ,A4不变。此时用极值法 求得各工序的余量:Z2=0.4~0.7mm, Z3=0.08~0.22mm,Z4=0.06~0.14mm, 按此工序尺寸执行,在生产中获得了满意的结 果。
(3)空间尺寸链:由位于几个不平行平面内的 尺寸组成。
3.尺寸链计算 有正计算、反计算和中间计算三种类型。
正计算:已知组成环求封闭环。 反计算:已知封闭环求组成环。 中间计算:已知封闭环及部分组成环,求其余 的一个或几个组成环。
4.极值法解尺寸链的计算公 式 机械制造中的尺寸及公差 通常用 基本尺 寸 (A) 、 上 偏差 (ES) 、下偏差 (EI) 表 示;还可以用最大极限尺 寸 ( Amax ) 与最小极限尺寸 ( Amin ) 表示;也可以用基 本尺寸 (A), 中间偏差 ( ) 与公差 (T) 表示,它们之 间的关系参见右图。
A 0 25 , A1 60 ,Tα0=0.1, 由已知条件: Tα1=0.05,由极值法的计算公式得: 基本尺寸: A0=A1-A2 得A2=35mm A2的下偏差: ES(A0)=ES(A1)-EI(A2) 得 EI(A2)=-0.25mm A2的上偏差: EI(A0)=EI(A1)-ES(A2)得 ES(A2)=-0.1mm ∴ Tα2的公差 Tα0=Tα1+Tα2 Tα2=0.05mm
A 43.4
3. 一次加工后需要同时保证多个设计尺寸及公差 的计算 在零件图上常常有多个设计尺寸是从某个设计 基准面标注出。由于这种基面的精度及表面粗 糙度要求较高,故常安排在最后阶段作终加工。 因此,只能直接保证其中一个设计尺寸(通常 选用公差要求最严的那个设计尺寸),而其他 以此为设计基准的尺寸,就只能间接保证了。 由此可见,当终加工一个主要设计基准面而又 同时需要保证多个设计尺寸时,就必须对有关 工序的尺寸和公差进行计算。
(4)以A面定位磨B面,保证最终轴向尺 寸A 4 30 0.02mm ,磨削余量为Z4。试对余量 Z2,Z3及Z4进行校核。
解:有关轴向尺寸的工艺尺寸链如图b)所示,由 于余量是加工过程中间接保证的,是尺寸链的封 闭环。 在以Z2为环闭环的尺寸链中,A1为增环,A2为 减环,用极值法可求出: Z 0.6 0.15mm 2
例3: 0.34 槽尺寸为 43.60 。内孔与键槽的加工顺序为: mm 0.1 mm ; (1)精镗内孔至 390 (2)插键槽至尺寸A; (3)热处理(为简化起见不考虑热处理内孔的变形 误差); 0.05 (4)磨内孔至 400 mm。 现要确定工艺过程中的工序尺寸A及其偏差。
0.05 40 如图为一齿轮内孔简图。内孔为 0 mm,键
基本尺寸、极限偏差、 公差与中间偏差
(1)基本尺寸 封闭环的基本尺寸等于各增环的基本尺寸之和 减去各减环的基本尺寸之和。
A0 Ai
i 1
m
j m 1
A
n 1
j
其中Ai表示增环,Aj表示减环。m为增环 的数目,n-1为组成环的数目。
(2)极限尺寸 封闭环的最大尺寸等于各增环的最大尺寸之和 减去各减环的最小尺寸之和。封闭环的最小尺 寸等于各增环的最小尺寸之和减去各减环的最 大尺寸之和。
)
三、工艺尺寸链分析与计算的实例
1.工艺基准与设计基准不重合时工序尺寸的计 算 零件在加工或测量中,有时为了便于定位和测 量,当采用的工艺基准与设计基准不重合时, 则应通过换算来改注有关工序的尺寸与公差。
例:如图a)所示零件,表面A、C已加工好, 0.25 现需加工B面,要求保证尺寸 A 0 250 及 平行度0.1。由于C面定位不方便,现改用A 面定位用调整法加工,试确定工序尺寸A2及 Tα2。
2.尺寸链的分类 按尺寸链在空间分布的位置关系,可分为 直线尺寸链、平面尺寸链和空间尺寸链。 ⑴直线尺寸链:由彼此平行的直线尺寸所组成。 图示尺寸链属直线尺寸链。
⑵平面尺寸链:由位于一个或几个平行平面内但 A1 、 A2 相互间不都平行的尺寸组成。图中 A0 、 三个尺寸就组成了一个平面尺寸链。
(A 0 ) max (A i ) max
i 1
m
j m 1
(A )
n 1
n 1
j min
(A 0 ) min (A i ) min
i 1
m
j m 1
(A )
j max
(3)偏差与公差
封闭环上偏差
ES(A 0 ) ES(A i )
i 1
解:由图a的有关尺寸可建立起图b所示的尺寸 链图。在该尺寸链中键槽的设计尺寸是间接保 证的,是封闭环。镗孔的直径及磨孔的直径是 通过中心线发生联系的,故在尺寸链中应以半 径表示。
由尺寸链计算公式得: A=43.6—20+19.8=43.4mm ES(A)=0.34—0.025+0=0.315mm EI(A)=0—0+0.05=0.05mm 0.315 即 A 43.4 0.050 按单向入体标注为: 0.27 0
组成环按其对封闭环的影响又可分为增环和减 环。 当其它组成环的大小不变,若封闭环随着某组 成环的增大而增大,则该组成环就称为增环; 若封闭环随着某组成环的增大而减小,则此组 A1 是增环, 成环就称为减环。图示尺寸链中, A2 是减环。
尺寸链图作法如图6-11所示: ⑴首先根据工件加工工艺过程,找出间接保证的 尺寸A。,定作封闭环。 ⑵从封闭环开始,按照零件表面之间的联系, A2 ,作为组成 依次画出直接获得的尺寸 A1 、 环,直至尺寸的终端回到封闭环的起点,形成 一个封闭图形。
0.25 0
0 0.1
从计算结果看出,由于基准不重合,使原 C面设计要求的尺寸公差0.25mm及平行度公 差0.1mm提高为0.15mm及0.05mm,即提高 了加工要求。
2. 中间工序的尺寸与公差的计算 在加工过程中,其他工序的尺寸与公差都为已 知,需求中间某一工序的尺寸与公差,称为中 间工序尺寸与公差的计算。
解:由工艺过程可建立如图 b)所示的尺寸链。其中 L0= 160 0.15 mm 为封闭 环,L2、L3为增环。用 极值法的计算公式可求得:
L2 120.05
0 0.2
mm
4. 加工余量的校核 工序余量的变化大小取决于本工序及前面工序 加工误差的大小。在已知工序尺寸及公差的情 况下,可利用工艺尺寸链的计算公式对加工余 量进行校验,以防止余量过大或过小。
例5:图a)所示的零件,有关轴向尺寸 30 0.02 mm 的加工过程如下: (1)精车端面A,自B处切断,保证两端面距离 尺寸 A1 31 0.1mm ; (2)以A面定位,精车B面,保证两端面距离尺 寸 A 2 30.4 0.05mm ,精车余量为Z2;
(3)以B面定位磨A面,保证两端面的距离尺 寸 A3 30.15 0.02mm ,磨削余量为Z3;