废塑料催化裂解制取燃料油的研究进展
塑料炼油的研究现状
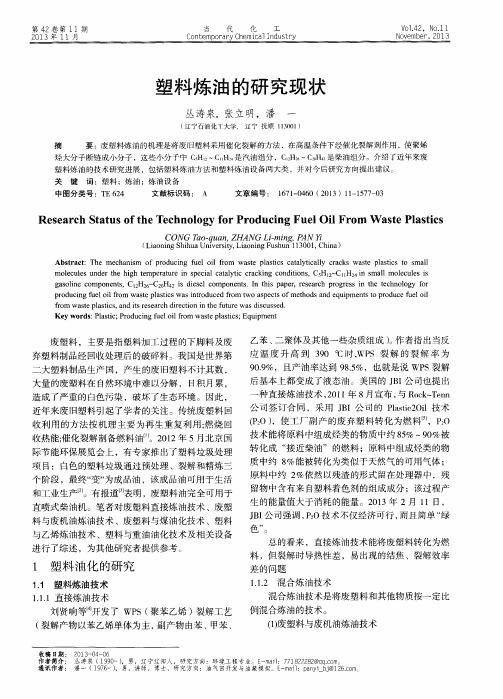
塑 料 炼 油 的研 究 现 状
丛 涛泉,张立 明,潘 一
( 辽 宁石 油 化1: 大学 , 辽 宁 抚 顺 1 1 3 0 0 1 )
摘
要 :废塑料炼 油的机理 是将 废旧塑料采用催化 裂解 的方法 ,在 高温条件下经催 化裂解剂作用 ,使 聚烯
烃大分子断链成小分子 ,这些小分子 中 c H : ~c . H 是 汽油 组分 ,c : H ~c 。 。 H 是柴油组分 。介绍了近年来废
Ke y wo r d s : P l a s t i c ; P r o d u c i n g f u e 1 o i l ro f m wa s t e p l a s t i c s ; E q u i p me n t
废塑 料 ,主要 是指 塑 料加 工 过程 的下 脚料 及废 弃 塑料 制 品经 回收处理 后 的破 碎料 。我 国是世 界第
第4 2卷 第 1 1期 2 0 1 3年 1 1月
当
代
化
工
C o n t e m p o r a r y C h e mi c a l I n d u s t r y
V o 1 . 42 ,N o . 1 l N o v e m b e r .2 0 1 3
塑料 炼油的技术研究进展 ,包括 塑料炼 油方法和塑料炼油设备两 大类 ,并对今后研究方 向提 出建议 。 关 键 词 :塑料 ;炼油 ;炼油设 备 文献标识码 : A 文章编号 : 1 6 7 1 — 0 4 6 0( 2 0 1 3)1 1 - 1 5 7 7 — 0 3 中图分类号 :T E 6 2 4
( L i a o n i n g S h i h u a Un i v e r s i t y , Li a o n i n g F u s h u r  ̄ 1 1 3 0 01 . Ch i n a )
城市废塑料裂解制汽油的研究(译文)

关 键词 : 塑料 ; 废 塑料 裂 解 ; 油 ; 炼 ; 市 汽 精 城
近些年来 , 人们对塑料的需求 日 益增加 , 因此 废塑料的有效处理问题 已成为严材和金属, 纸、 表 1 为城市固体废弃物的成分和含量。
表 1 城市 固体废 弃物 ( 重量 分数 . ) %
以避 免大气 污 染 。在许 多工业 化 国家废塑 料 已经 产生 了越 来越 多 的问题 , 引起 了人 们 的广 泛关 注 ,
政府制定了许多新的法规来 回收废塑料使之成为 种可 用 资源 。 传 统 的 回收 方 法 主要 是 将 废 塑 料 填 埋 或 焚 烧 。热裂 解则 是 第 三 种方 法 , 它可 以提供 三 种 产
有机废物转换为合成燃料主要有以下几种方 法 :1加氢反应 ,2高温裂解反应 , ) () () ( 催化裂解 3 反应 ,4气化 ,5生物转化反应。 () () 文献报道了几篇关于废塑料 高温裂解 的文 章。其中对 H_ W一 催化剂和磷酸改性 H_W T S 5 T S
5 催化剂( z M 一 ) P S 5 应用于废塑料裂解的研究 较多。与在相同反应 温度下没有催化 剂作用相
聚 苯 乙烯 ( S 、 乙烯 (E)聚 丙烯 (P) P )聚 P 、 P 。废 塑料 可 以裂解 为三种馏 分 : 气体 、 体 以及 固态残 渣 。 液
液体产品通常由一些具有较高沸点的碳氢化合物组成。为 了从裂解油 中获得有用的汽油组分 , 可 以对裂 解油进 行分 馏 。许 多化 工原 材料 包括苯 、 甲苯和 其 它芳香 族碳 氢化合 物 也 可通 过提 纯 裂解 油来获得。结果表 明, P 可产生较 多的液体 , 废 S 主要是苯 乙烯 , 而废 P E和 P P则会产 生较 多的气
废塑料制取液体燃料试验研究

S u y o x e i n fwa t l si y oy i o r d i i ui u l t d n e p rme to se p a tc p r l ssf r p o ucng lq d f e
D ONG P n Y N S u- r, IGu - ,Z e g , I h i Q ol e i HAI n WAN L g, Mi G i ( .S ho o n ryS i c n n ier g H ri Is tt o eh ooy abn10 0 ,H in j n 1 col f eg ce ea dE gn ei , abn ntue f c n l ,H i 5 0 1 e o g a g E n n i T g r l i
p o u t w r t i e a c r ig t x e me t d t n lss E e g c n u t n a d a q i t n we e a s r d cs e at n d c o d n o e p r n a a a ay i. n r e a i y o s mp i n c u s i r lo o io
收支关 系 , 为废塑料制取 液体燃料 的工业装 置的设计 、 运行提 供 了理论 及试验依据 。 关键词 : ; 燃料 ; 热解 液体 废塑料 ; 能量收支
中图分类号 :K 24 T 2 文献标识码 : A 文章编号 :0 59 5 ( 0 7 0 -0 40 10 - 4 20 )206 - 9 4
维普资讯
第3 卷 第2 5 期
2o 0 7年 2月
化
学
工
程
V0. 5 N . 13 o 2
C E C LE GN E I G C N H MIA N I E R N ( HIA)
含卤废旧塑料回收利用的研究进展

为解聚型 � 随机裂解型和中间型三种类型 � �解聚型 乙烯自由基和聚乙烯反应,而 P P 和 P 的聚合物 是塑料受热裂解时聚合物裂解成单体,生成大量 � 则表现为分子间氢传递反应,同时发现含有 P C 气体, � 如聚 �- 甲基苯乙烯 � 四氟乙烯塑料等; 随机 的 混合塑 料在 不超 过 375 均 可脱 除大 部分 的 � 裂解型是受热后分子间随机性断裂,得到一定数 H C ;脱氯产物在 4 50 以上进行分解和脱烷基反 目的碳氢低分子化合物,气体产物较少,如 P E � 应, 易形成焦炭, 同时提出不同气氛下含卤和无卤 的就可进行分子间链传 P C 等;中间型的裂解反应介于上述两种类型之 � 塑料的热解动力学方程及参数 �P C 和常压渣油 间 � � 的单段热解反应在 1 50 � � 含卤塑料 中含有大量的 C -C � C -H � C - ( : 递的脱 H C 反应, 同时 C � 与渣油中沥青质相互作 � 卤素 ) 键� 主链结构中有 C C 的存在� C -C � C -H � 用使反应中的 H C 生成量明显减少 �国外业内人 � � � C C 键的离解能分别为 3 4 7� 4 14� 61 1 J/ , 而弱 士通 过对 P C � P B 和 P CP 的 热解进 行研究 发 的二级键如偶极力 �感应力和分散力的键能均小 � 现: 由于卤素在分子结构中位置不同以及 C -C 和 于 4 2 J/ � 热降解方式和产品分布在一定程度 C -B 键能的不同导致热解行为的不同, 提出各自 详尽的动力学方程及动力学参数 �国外业内人士 的 H C 对 H D P E 热解过程的影响,提出了对应不 同 H C 浓度 H D P E 热解 动力学方 程和动力 学参 曲线吻合很好� 在热解过程中,添加碱性吸附剂是最常用的 脱卤方法� 碱性吸附剂可以直接加到脱卤反应器 中, 也可以装在固定床中与气相接触进行脱卤� 上与键的解离能 � 聚合物碳链的弱连接位置 � 芳构 子等有关 � 在 P C 的热降解反应过程中应尽量消除 H C 提出, 由于 C-C 键能较低, 在 P C 的热降解中存 在2 0 0 380 380 550 的 C -C 键的断裂的脱 H C 过 程和 的碳链断裂两个明显的失重过程�在脱
一种利用废塑料生产燃料油方法
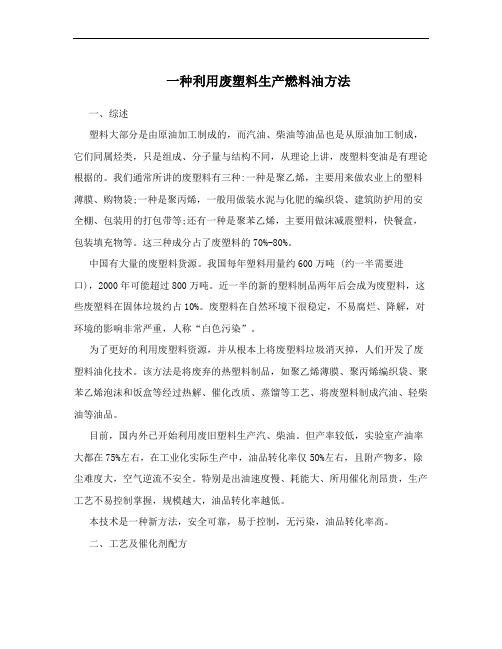
一种利用废塑料生产燃料油方法一、综述塑料大部分是由原油加工制成的,而汽油、柴油等油品也是从原油加工制成,它们同属烃类,只是组成、分子量与结构不同,从理论上讲,废塑料变油是有理论根据的。
我们通常所讲的废塑料有三种:一种是聚乙烯,主要用来做农业上的塑料薄膜、购物袋;一种是聚丙烯,一般用做装水泥与化肥的编织袋、建筑防护用的安全棚、包装用的打包带等;还有一种是聚苯乙烯,主要用做沫减震塑料,快餐盒,包装填充物等。
这三种成分占了废塑料的70%-80%。
中国有大量的废塑料货源。
我国每年塑料用量约600万吨 (约一半需要进口),2000年可能超过800万吨。
近一半的新的塑料制品两年后会成为废塑料,这些废塑料在固体垃圾约占10%。
废塑料在自然环境下很稳定,不易腐烂、降解,对环境的影响非常严重,人称“白色污染”。
为了更好的利用废塑料资源,并从根本上将废塑料垃圾消灭掉,人们开发了废塑料油化技术。
该方法是将废弃的热塑料制品,如聚乙烯薄膜、聚丙烯编织袋、聚苯乙烯泡沫和饭盒等经过热解、催化改质、蒸馏等工艺、将废塑料制成汽油、轻柴油等油品。
目前,国内外已开始利用废旧塑料生产汽、柴油。
但产率较低,实验室产油率大都在75%左右,在工业化实际生产中,油品转化率仅5O%左右,且附产物多,除尘难度大,空气逆流不安全。
特别是出油速度慢、耗能大、所用催化剂昂贵,生产工艺不易控制掌握,规模越大,油品转化率越低。
本技术是一种新方法,安全可靠,易于控制,无污染,油品转化率高。
二、工艺及催化剂配方将废塑料置于气热裂解炉内,炉温控制在180-500?,同时将水蒸汽送入气热裂解炉内;将气热裂解炉内生成的石蜡蒸汽和燃料油混合汽引入催化裂解炉,炉温180-480?,经炉内AL203分子筛进一步裂解重整;将催化裂解炉内充分裂解重整后的燃油汽引入精馏塔蒸馏出汽油和柴油。
将废塑料置于气热裂解炉内裂解时,是通过伸入气热裂解炉底部的蒸汽管将水蒸汽送入气热裂解炉内,还通过从气热裂解炉上部引出而与上述蒸汽管相通,且带控制阀的气管在停止蒸汽管送汽的情况下,使水蒸汽在气热裂解炉内循环。
废旧塑料催化裂解制备汽油
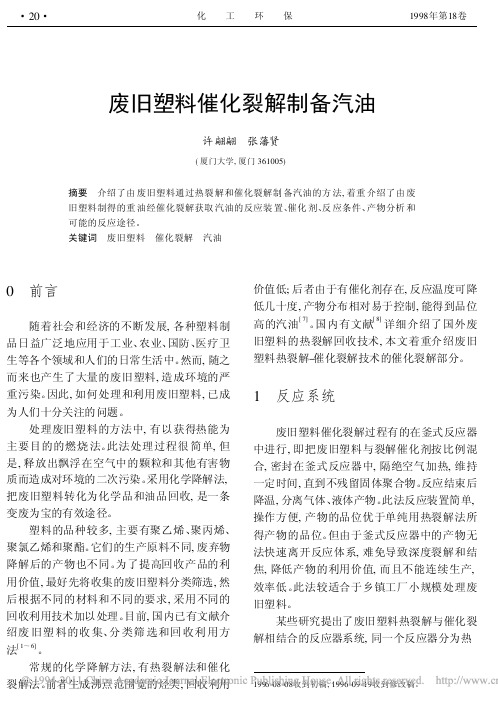
废旧塑料催化裂解制备汽油许翩翩 张藩贤(厦门大学,厦门361005)摘要 介绍了由废旧塑料通过热裂解和催化裂解制备汽油的方法,着重介绍了由废旧塑料制得的重油经催化裂解获取汽油的反应装置、催化剂、反应条件、产物分析和可能的反应途径。
关键词 废旧塑料 催化裂解 汽油0 前言随着社会和经济的不断发展,各种塑料制品日益广泛地应用于工业、农业、国防、医疗卫生等各个领域和人们的日常生活中。
然而,随之而来也产生了大量的废旧塑料,造成环境的严重污染。
因此,如何处理和利用废旧塑料,已成为人们十分关注的问题。
处理废旧塑料的方法中,有以获得热能为主要目的的燃烧法。
此法处理过程很简单,但是,释放出飘浮在空气中的颗粒和其他有害物质而造成对环境的二次污染。
采用化学降解法,把废旧塑料转化为化学品和油品回收,是一条变废为宝的有效途径。
塑料的品种较多,主要有聚乙烯、聚丙烯、聚氯乙烯和聚酯。
它们的生产原料不同,废弃物降解后的产物也不同。
为了提高回收产品的利用价值,最好先将收集的废旧塑料分类筛选,然后根据不同的材料和不同的要求,采用不同的回收利用技术加以处理。
目前,国内已有文献介绍废旧塑料的收集、分类筛选和回收利用方法[1~6]。
常规的化学降解方法,有热裂解法和催化裂解法。
前者生成沸点范围宽的烃类,回收利用价值低;后者由于有催化剂存在,反应温度可降低几十度,产物分布相对易于控制,能得到品位高的汽油[7]。
国内有文献[8]详细介绍了国外废旧塑料的热裂解回收技术,本文着重介绍废旧塑料热裂解-催化裂解技术的催化裂解部分。
1 反应系统废旧塑料催化裂解过程有的在釜式反应器中进行,即把废旧塑料与裂解催化剂按比例混合,密封在釜式反应器中,隔绝空气加热,维持一定时间,直到不残留固体聚合物。
反应结束后降温,分离气体、液体产物。
此法反应装置简单,操作方便,产物的品位优于单纯用热裂解法所得产物的品位。
但由于釜式反应器中的产物无法快速离开反应体系,难免导致深度裂解和结焦,降低产物的利用价值,而且不能连续生产,效率低。
废塑料裂解生产原料油的研究

废塑料裂解生产原料油的研究程水源1 金毓1 郝瑞霞1 F.N g2(1.北京工业大学环境工程系,北京100022;2.加拿大滑铁卢大学化学工程系,安大略N2L3G1)摘 要 本文对聚乙烯和聚丙烯的混合物裂解成原料油进行了研究,在440 条件下,不同比例的聚乙烯和聚丙烯被裂解。
结果发现,聚丙烯有最高的液体回收率。
几种催化剂被应用到聚丙烯的裂解过程中。
裂解产品组分的构成及催化剂的选择是本研究的主要内容。
通过比较几种不同催化剂的催化结果发现,复合催化剂有更好的催化效果。
本研究为将来的废塑料综合利用提供了一种新的有用方法。
关键词 裂解 废塑料 原料油 催化剂 汽油 聚乙烯 聚丙烯A study on thermal pyrolysis of waste plasticsinto fuel oil productsCheng Shuiyuan1 Jin Yuquan1 H ao Ruix ia1 F.Ng2(1.Department of Environm ental Engineeri ng,Beiji ng Polytechnic University,Beiji ng100022;2.Department of Chemical Engineeri ng,University of W aterloo,Canada N2L3G1)Abstract In this study,the methods of decomposing polyethylene(PE)and polypropylene(PP)into fuel oil were studied.After several mixtures w ith different ratios of polyethylene and polypropylene were respectively decomposed at440 ,it was found that the pure polypropylene had highest productivity of both diesel and gasoline.Furthermore,several kinds of catalysts w ere chosen for the catalytic pyrolysis of polypropylene.The components of the decom position products and the choice of catalysts are the main focus of this study.A com parison of the polypropylene decomposition results w ith the different catalysts show ed that composite catalysts had better catalytic results for the pyrolysis of the poly propylene.T he research results prov ide a new useful potential technique for the comprehensive use of w aste plastics.Key words pyrolysis;waste plastics;fuel oil;catalyst;gasoline;polyethylene;polypropylene1 引 言随着石油化工的发展,塑料工业也得到迅速的发展。
废塑料裂解制液体燃料及废塑料的处理探究解析

白色污染是全球城市都有的环境污染,在各种公共场所到处都能看见
大量废弃的塑料制品,他们从自然界而来,由人类制造,最终归结于大 自然时却不易被自然所消纳,从而影响了大自然的生态环境。从节约资 源的角度出发,由于塑料制品主要来源是面临枯竭的石油资源,应尽可 能回收,但由于现阶段再回收的生产成本远高于直接生产成本,在现行 市场经济条件下难以做到。
塑料是一种很轻的物质,用很低的温度加热就能使它变软,随心所欲地做成各种形状
的东西。塑料制品色彩鲜艳,重量轻,不怕摔,经济耐用,它的问世不仅给人们的生活 带来了诸多方便,也极大地推动了工业的发展。
但是现在工业中,塑料袋从生产到处理,整个过程
都会造成大量资源的耗费,以及地球环境的污染。每 个塑料袋的自然分解需要200年以上,会污染周围的土 地和水质,全国每年耗费掉的塑料包装袋,它在生产 中所消耗的原油超过1000万桶,而处理时要耗费的电 量更是大得惊人啊!白色污染是我国特有的一种环境 污染,在大量公共场所都可以看见许多废弃的塑料制 品,它们从自然界而来,由人类所制造,最终,归结 于大自然时,却的我们的生活环境造成严重的污染, 这些塑料制品埋在地下,100-500年都无法销毁。因 此我们提出此次项目的意义就在于缓解我国目前的白 色污染状况,制定出合适的解决方案,使得资源能够 很好的在利用。
在中国,塑料年产量为300万吨,消费量在600万吨以上。全世界塑料年产量为1亿 吨。如果按每年15%的塑料废弃量计算,全世界年塑料废弃量就是1500万吨,中国的年 塑料废弃量在100万吨以上,废弃塑料在垃圾中的比例占到40%,这样大量的废弃塑料作 为垃圾被埋在地下,无疑给本来就缺乏的可耕种土地带来更大的压力。
查阅相关资料整理并总 结出我们治理白色污染及 其资源回收利用的论文。
分子筛催化剂在废塑料催化裂解中的研究进展

分子筛催化剂在废塑料催化裂解中的研究进展发布时间:2022-07-18T00:54:44.020Z 来源:《科学与技术》2022年第5期第3月作者:李越,蔡尚辰,刘项,乐建材,李传强[导读] 据统计,全球所使用的塑料中仅有不到10 %被回收利用,未被处理的塑料则变为垃圾,在自然界中难以降解,对生态环境产生恶劣影响李越,蔡尚辰,刘项,乐建材,李传强重庆交通大学材料科学与工程学院,重庆 400074[摘要]据统计,全球所使用的塑料中仅有不到10 %被回收利用,未被处理的塑料则变为垃圾,在自然界中难以降解,对生态环境产生恶劣影响。
现阶段,废塑料回收利用方法中催化裂解具有能耗小、选择性高、反应速率快等优势,深受研究者所青睐。
分子筛催化剂应用较为广泛,也是废塑料催化裂解常用催化剂类型之一。
本文主要综述了废塑料催化裂解中常用分子筛催化剂、裂解机理以及研究现状等,并对其未来发展方向做出了展望。
[关键词] 废塑料;热裂解;催化裂解;分子筛催化剂0 前言据统计,2018年全球塑料产量已达到约3.6亿吨,在疫情笼罩下,塑料年产量依旧逐年增加,随之而来的废旧塑料回收处理问题不容忽视。
传统的处理方法主要包括焚烧、填埋或机械回收,全球90 %的废塑料被填埋和焚烧处理,而很少被用于回收生产附加值物品[1]。
近年来,符合可持续发展理念的原料回收利用法与化学回收利用法广泛应用于废塑料处理,其中,化学回收法因具有环境污染性小、能耗低、产品附加值高等优点。
化学回收法主要分为热裂解与催化裂解。
催化裂解反应具有活化能低、能耗小、反应速率快、选择性可控等优势,是目前提高废塑料裂解产物质量和产量的最佳方法。
制备具有良好活性、选择性及稳定性的废塑料裂解催化剂是环境催化领域中的重要课题。
分子筛因其具有良好的热稳定性,较高的孔隙率、丰富的酸碱中心、可调控的孔径等特性,在工业催化领域中应用广泛。
本文主要综述了国内外在废塑料催化裂解中常用分子筛的裂解机理及应用现状,并展望其未来发展方向。
- 1、下载文档前请自行甄别文档内容的完整性,平台不提供额外的编辑、内容补充、找答案等附加服务。
- 2、"仅部分预览"的文档,不可在线预览部分如存在完整性等问题,可反馈申请退款(可完整预览的文档不适用该条件!)。
- 3、如文档侵犯您的权益,请联系客服反馈,我们会尽快为您处理(人工客服工作时间:9:00-18:30)。
废塑料催化裂解制取燃料油的研究进展来源:环境污染与防治更新时间:08-12-25 11:32 作者: 陈鸿伟摘要:介绍了废塑料催化裂解制取燃料油的基本方法,阐述了废塑料催化裂解的催化剂及催化原理,探讨了废塑料热裂解—催化改质机制,并指出废塑料催化裂解制取燃料油技术是解决废塑料回收的有效手段。
随着现代科学技术特别是化学技术的发展,塑料制品与人们的日常生活密不可分,但随之而来的是每年产生的数千万吨的塑料垃圾。
这些废塑料大多难以自然降解,严重污染环境。
如何正确处理并有效利用这些废塑料已引起人们的广泛重视。
采用廉价且有效的催化剂催化裂解废塑料制取燃料油,不仅可以消除环境污染,而且可以实现废弃物的资源化利用,获得宝贵的资源,既有较大的环境效益、社会效益,又有相当的经济效益。
1 废塑料催化裂解制取燃料油技术的概述废塑料经过热裂解后所得到的液体燃料是沸点范围较宽的烃类物质,其中汽油馏分和柴油馏分不高,但是重油馏分较高,而且汽油馏分和柴油馏分的品质不高。
采用催化剂催化重整的方法可以增加轻质组分、减少重质组分,同时可以提高汽油辛烷值,最终达到提高燃料油品质的目的。
目前,使用催化剂改善油品品质主要有两种方法:一种是将催化剂置于裂解反应器中直接进行催化改质,即一段法;另一种是将热裂解产生的气体导入到催化反应器中进行催化改质,以使产物的碳数分布明显轻质化,并集中于汽油和柴油馏分内,即二段法[1]。
一段法[2]以催化裂解为主,反应速度快,油品中异构化、芳构化产物较热裂解多,工艺较为简单,投资较少。
但是反应过程中有大量焦炭沉积于催化剂表面,使催化剂失活,因此催化剂的再生与剩余催化剂的回收都较为困难。
二段法可克服热裂解制得汽油和柴油品质不高的缺点,操作灵活,运行费用低,催化剂用量少,而且可以多次使用。
所以二段法被认为是一种较为理想的处理废塑料的方法。
热解—催化改质法是成本较低、所得油品的质量较高的废塑料油化工艺技术。
要提高油品的收率和汽油的品味,关键在于开发高性能的改质催化剂。
目前,国内已有十几套废塑料回收生产装置,但多由于种种原因不能正常生产,其中缺少对核心技术—催化剂的实验理论基础研究是其重要原因。
2 废塑料催化裂解的催化剂及催化原理2.1 催化剂的种类目前,国内外常用的废塑料催化剂[3]大致可为金属类、金属氧化物类、金属氧化物-稀土类、分子筛类、沸石矿物类、活性炭催化剂等。
常使用Ni、Cu、A1等5种金属混合物[4]或采用铜粉作为废塑料催化裂解的催化剂。
一些金属氧化物,如硅铝微球、Al2O3、CuO、MgO、ZnO、TiO2、Fe2O3、氧化铈、Co-Mo 氧化物等也常被用来作废塑料裂解的催化剂。
还有大量废弃物,如粉煤灰、炉渣、电石渣等,它们都是金属或者非金属氧化物的混合物,它们对于废塑料的催化裂解有很好的效果。
HY、Ni-REY、NZSM-5等分子筛常用于废塑料催化裂解和催化改质的研究,硫酸铝、硅酸铝、酸性白土、高岭土、铝土矿等沸石矿物也常用来做塑料裂解的催化剂。
薛福连采用小径木干馏出的具有一定形状具有较高吸附性能的活性炭[5],其孔隙结构十分发达,比表面积大,而且在500~600 ℃的高温下有足够的耐热性,同时耐酸碱性又很好,用作废塑料裂解催化剂载体是十分合适的,并广泛应用于石油化工各类催化反应中。
粉煤灰[6]是一种较典型的硅铝火山灰材料,它主要是由各种金属氧化物构成,它的化学组成主要是SiO2、Al2O3,此外还有Fe2O3、CaO、MgO和K2O等。
它是煤粉燃烧后,由烟气自锅炉炉膛中带出的粉状产物。
粉煤灰玻璃体的外观呈蜂窝状,空穴较多,内部具有较丰富的孔隙,且比表面积大。
炉渣[6]是锅炉炉膛排渣口排出的固体产物,它也是主要由各种金属氧化物构成,其内部空穴也很多,且比表面积也比较大。
炉渣的化学组成主要是CaO(70%以上),此外还有SiO2、Fe2O3、Al2O3和MgO。
电石渣[7]是生产乙炔气、聚氯乙烯和聚乙烯醇等产品排出的废渣,其主要成分为Ca(OH)2和水,其次含有极少量的Al2O3、Fe2O3、MgO、SiO2、S和P等。
这些所谓的废弃物对废塑料的裂解有很好的催化效果。
因此深入研究这些物质对废塑料的催化作用,是非常重要且有实际意义的。
2.2 催化原理一般来说,催化裂解过程既要发生催化裂化反应,也要发生热裂化反应,是碳正离子和自由基两种反应机制共同作用的结果,但具体的裂解反应机制随催化剂的不同和裂解工艺的不同而有所差别。
在Ca-Al系列催化剂上的高温裂解过程中,自由基反应机制占主导地位;在酸性沸石分子筛裂解催化剂上的低温裂解过程中,碳正离子反应机制占主导地位;而在具有双酸性中心的沸石催化剂上的中温裂解过程中,碳正离子机制和自由基机制均发挥着重要的作用。
由于废塑料催化裂解所采用的催化剂大多属于固体酸类催化剂,故反应机制可以用碳正离子理论来解释。
有研究认为废塑料催化改质机制为:先发生热解产生长碳链的烯烃;烯烃进而从催化剂表面上获得H+形成正碳离子;正碳离子先在β位断裂成伯、仲碳离子,然后异构化成更加稳定的叔碳离子;最后,稳定的叔正碳离子将H+还给催化剂,本身变成烯烃[8]。
在催化裂解废塑料PE、PP研究中,部分学者采用的是石油化工中的催化剂,如FCC、择形催化剂和活性炭等。
FCC催化剂的裂解机制和石油催化裂化的机制比较类似,通过此可获得轻质油和气态烃类。
择形催化剂的催化作用依赖于硅铝上的过渡金属,最普遍的是Pt/SiO2-A12O3,Pt只占0.5%(质量分数)。
它的两种活性位起到了不同的作用:金属位进行催化加氢或脱氢反应,酸性位催化异构化反应,两种催化作用相结合,可以产生许多不同的择形反应,其明显的作用就是在不改变分子数的情况下增加汽油的辛烷值。
活性炭也可作为塑料裂解催化剂,但其产品分布与FCC、择形催化剂有不同之处,其产品中直链烷烃较多,异构烷烃较少。
采用分子筛催化剂裂解聚苯乙烯时,由于聚苯乙烯分子大小与催化剂孔径的巨大差异,使得聚苯乙烯分子只能通过热裂解或在催化剂表面及孔口附近裂解为较小的碎片,其中足够小的碎片才能扩散到催化剂内进行催化裂解。
也就是说,聚苯乙烯裂解为小分子和小分子在孔内催化裂解是相对独立的两个过程。
粉煤灰是一种较典型的硅铝火山灰材料,其化学组成主要是SiO2、Al2O3,此外还有Fe2O3、CaO、MgO和K2O等。
由于粉煤灰和沸石在组成上的相似性,且其玻璃体的外观呈蜂窝状,空穴较多,内部具有较丰富的空隙,比表面积大,所以粉煤灰是一种对废塑料裂解有巨大发展前途的催化剂。
3 废塑料热裂解—催化改质机制的讨论废塑料热裂解产物的催化改质取决于催化剂的性能和催化温度。
催化剂中常用的有各种类型的分子筛沸石和硅酸铝沸石,催化剂的成分、酸性、空隙结构和晶粒大小直接影响催化剂活性、裂解产物的分布和所得汽油馏分的品质(辛烷值RON)。
3.1 催化剂的组成实用的催化剂一般都是含有多种组分,单一组分的情况很少,根据各成分的功能不同,可分为主要组分、次要组分和载体;催化剂至少含有主组分和载体两部分。
催化剂的催化活性主要由主组分提供。
载体的作用是提供适合的表面积和孔结构,改进催化剂的机械强度和热稳定性。
塑料裂解气的催化改质需要改性催化剂应具有较大的孔径、比表面积及合理的表面酸位分布。
3.2 催化反应温度的影响不同的催化剂在不同的催化裂解温度下,其气体、液体收率不同。
这是因为不同催化剂的酸性分布不同,不同温度下催化剂的活性不同。
湖南大学袁兴中通过实验得出,催化温度对聚丙烯裂解—催化改质的液体收率及组成的影响(见表1)。
表1催化温度对聚丙烯热解-催化改质的液体收率及组成的影响实验发现,对PPA和GOR-C这两种催化剂而言,随催化温度的升高,液体收率减少,油品中汽油馏分含量升高,柴油馏分含量变化不明显,而重油馏分含量则逐渐减少,这说明这两种催化剂对重油馏分催化改质效果明显。
在废塑料裂解过程中,随催化温度的升高,催化剂积炭率减少。
这是因为生成气体、燃料油的反应与生成焦炭的反应互为竞争反应。
一般情况下,生成汽油与气体的反应速率常数的温度系数高于生成焦炭的反应速率常数的温度系数。
催化温度升高时,生成汽油与气体的反应比生成焦炭的反应速度高,有利于反应生成汽油和气体,同时催化剂的积炭率减少。
结果见图1。
图1 物料为PP时催化温度对催化剂积炭率的影响3.3 催化剂颗粒的影响大小的影响Y型分子筛的主要阻力来自于分子筛内部。
有研究比较了不同晶粒的分子筛对催化剂重油裂解的影响,发现小晶粒比大晶粒催化剂的反应速率常数大,生成的汽油量大,而汽油品位几乎没有差别。
所以可认为分子筛催化剂晶粒粒径<0.1 μm为最佳,可降低内扩散阻力。
3.4 催化剂孔径对催化裂解的影响催化剂孔隙结构将影响废塑料的催化裂解,催化剂的孔径大小是决定废塑料裂解产生的大分子能否进入催化剂晶粒内部区接触活性中心的关键因素。
若催化剂的孔径比产物分子的直径小,且缺乏形状选择性,则不利于废塑料的催化裂解。
SONGIP等[8]对废塑料催化裂解常用的固体酸催化剂,如HY沸石、稀土Y沸石、HZSM-5沸石和氧化硅-氧化铝。
研究发现,而HY沸石和稀土Y沸石作催化剂催化改质得到的汽油辛烷值较高、产品收率也较高;氧化硅-氧化铝和普通NZSM-5沸石作为催化剂催化改质得到的汽油辛烷值较低、产品收率也较低。
这是因为NZSM-5沸石的孔径太小,大分子的碳氢化合物不能进入孔隙进行催化反应,而反应主要发生在催化剂的外表面,生成大量的气态低碳烃产物。
氧化硅-氧化铝的催化活性太低。
而HY沸石和稀土Y沸石晶体结构中有较大的孔径和合适的强酸位,允许产物分子有效地渗透进入催化剂的内部,故有较好的催化活性、较强的选择性,汽油收率、辛烷值也高,结焦较少。
有研究发现,聚丙烯树脂热解催化改质用的催化剂,以平均孔径为2.5~4.0 nm为宜,过大的孔径易导致积炭,液体产率下降,催化剂寿命缩短;过小的孔径则不利于气相产物的内扩散[9]。
3.5 催化剂酸位对废塑料催化裂解性能的影响OHKITA等[10]研究了氧化硅-氧化铝催化剂上的酸强度和酸量在聚乙烯裂解过程种的催化作用。
催化剂上的酸有两种:Broensted酸和Lewis酸。
随着催化剂中SiO2/Al2O3质量比不同,酸的强度和数量有所不同。
在673 K下,聚乙烯在这种催化剂的催化作用下的产物主要有裂解气、油和蜡。
随着催化剂上酸的数量增多,产物油中的芳香族化合物的量增多。
催化剂的强酸位是反应的活性中心。
文献报道了稀土金属交换的Y型沸石催化剂上强酸位数量对产物分布的影响(见图2,反应温度为673 ℃)。
随着催化剂强酸位数量的增加,重油的转化率、气体和汽油产率均提高。
但由于汽油是催化裂解反应的中间产物,其产率提高到一定值后又随着强酸位的继续增加而下降。