重油催化裂化基础知识
重油催化裂化

重油催化裂化(residue fluid catalytIC cracking,即RFCC)工艺的产品是市场极需的高辛烷值汽油馏分,轻柴油馏分和石油化学工业需要的气体原料。
由于该工艺采用了分子筛催化剂、提升管反应器和钝化剂等,使产品分布接近一般流化催化裂化工艺。
但是重油原料中一般有30%~50%的廉价减压渣油,因此,重油流化催化裂化工艺的经济性明显优于一般流化催化工艺,是近年来得到迅速发展的重油加工技术。
㈠重油催化裂化的原料所谓重油是指常压渣油、减压渣油的脱沥青油以及减压渣油、加氢脱金属或脱硫渣油所组成的混合油。
典型的重油是馏程大于350℃的常压渣油或加氢脱硫常压渣油。
与减压馏分相比,重油催化裂化原料油存在如下特点:①粘度大,沸点高;②多环芳香性物质含量高;③重金属含量高;④含硫、氮化合物较多。
因此,用重油为原料进行催化裂化时会出现焦炭产率高,催化剂重金属污染严重以及产物硫、氮含量较高等问题。
㈡重油催化裂化的操作条件为了尽量降低焦炭产率,重油催化裂化在操作条件上采取如下措施:1、改善原料油的雾化和汽化由于渣油在催化裂化过程中呈气液相混合状态,当液相渣油与热催化剂接触时,被催化剂吸附并进入颗粒内部的微孔,进而裂化成焦炭,会使生焦量上升,催化活性下降。
因此可见,为了减少催化剂上的生焦量,必须尽可能地减少液相部分的比例,所以要强化催化裂化前期过程中的雾化和蒸发过程,提高气化率,减少液固反应。
2、采用较高的反应温度和较短的反应时间当反应温度提高时,原料的裂化反应加快较多,而生焦反应则加快较少。
与此同时,当温度提高时,会促使热裂化反应的加剧,从而使重油催化裂化气体中C1、C2增加,C3、C4 减少。
所以宜采用较高反应温度和较短的反应时间。
㈢重油催化裂化催化剂重油催化裂化要求其催化剂具有较高的热稳定性和水热稳定性,并且有较强的抗重金属污染的能力。
所以,目前主要采用Y型沸石分子筛和超稳Y型沸石分子筛催化剂。
㈣重油催化裂化工艺1、重油催化裂化工艺与一般催化裂化工艺的异同点两工艺既有相同的部分,亦有不同之处,完全是由于原料不同造成的。
催化裂化工艺与工程

催化裂化工艺与工程引言催化裂化工艺与工程是石油炼制领域中的重要技术,其通过催化剂的作用,将重油分子裂解为较轻的产品。
催化裂化工艺在石油化工行业中具有广泛应用,可以生产出汽油、液化气和轻质石脑油等产品,对石油资源的高效利用具有重要意义。
催化裂化反应原理1.催化裂化反应介质:常见的催化剂是硅铝酸盐,其具有高的表面积和一定的酸性。
催化剂通过提供活性中心,促进了重油分子的裂解反应。
2.催化裂化反应机理:重油中的长链烷烃在催化剂的作用下发生裂解,产生较短的烷烃和芳烃。
裂解过程中产生了大量的烯烃和芳烃,这些物质是石油下游加工的重要原料。
催化裂化工艺流程1.原料预处理:重油首先需要进行预处理,包括去除硫、氮等杂质,以减小对催化剂的毒化作用。
2.催化裂化反应:重油在裂化装置中与催化剂接触,发生裂解反应。
在裂化过程中,需要严格控制反应温度、压力和催化剂的用量,以提高产品的收率和质量。
3.分离工序:裂化反应产生的产物包括汽油、液化气、轻质石脑油等组分,这些组分需要经过分离工序进行提取。
主要包括精馏、吸附和深度处理等步骤。
4.催化剂再生:经过一段时间的使用,催化剂表面会产生积炭和失活,需要进行再生。
催化剂再生的过程包括热氧化和酸洗等步骤,以恢复催化剂的活性。
5.产品处理:裂化产物需要进一步进行加工和改性,以获得符合市场需求的成品。
催化裂化工程设计1.反应器设计:反应器是催化裂化装置的核心部分,设计合理的反应器可以提高反应效率和产物质量。
反应器设计考虑因素包括反应器类型、反应器尺寸、反应器温度和压力等。
2.催化剂选择:催化剂的选择是催化裂化工程设计中的重要一环。
催化剂的性能直接影响反应的效果和产物的质量。
选择合适的催化剂需要考虑其活性、稳定性和成本等因素。
3.热力学和动力学模型:对催化裂化反应进行热力学和动力学模拟,可以预测反应过程中的表现和优化操作条件。
4.安全性考虑:催化裂化工程设计需要考虑装置的安全性。
石油化工装置涉及高温、高压和易燃易爆物质,需要进行安全分析和设计,以确保操作的安全性和稳定性。
催化裂化
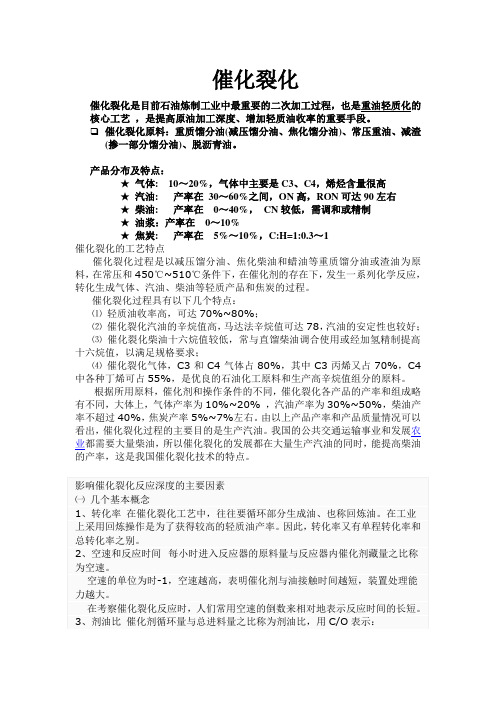
催化裂化催化裂化是目前石油炼制工业中最重要的二次加工过程,也是重油轻质化的核心工艺,是提高原油加工深度、增加轻质油收率的重要手段。
催化裂化原料:重质馏分油(减压馏分油、焦化馏分油)、常压重油、减渣(掺一部分馏分油)、脱沥青油。
产品分布及特点:★气体: 10~20%,气体中主要是C3、C4,烯烃含量很高★汽油: 产率在30~60%之间,ON高,RON可达90左右★柴油: 产率在0~40%,CN较低,需调和或精制★油浆:产率在0~10%★焦炭: 产率在5%~10%,C:H=1:0.3~1催化裂化的工艺特点催化裂化过程是以减压馏分油、焦化柴油和蜡油等重质馏分油或渣油为原料,在常压和450℃~510℃条件下,在催化剂的存在下,发生一系列化学反应,转化生成气体、汽油、柴油等轻质产品和焦炭的过程。
催化裂化过程具有以下几个特点:⑴轻质油收率高,可达70%~80%;⑵催化裂化汽油的辛烷值高,马达法辛烷值可达78,汽油的安定性也较好;⑶催化裂化柴油十六烷值较低,常与直馏柴油调合使用或经加氢精制提高十六烷值,以满足规格要求;⑷催化裂化气体,C3和C4气体占80%,其中C3丙烯又占70%,C4中各种丁烯可占55%,是优良的石油化工原料和生产高辛烷值组分的原料。
根据所用原料,催化剂和操作条件的不同,催化裂化各产品的产率和组成略有不同,大体上,气体产率为10%~20% ,汽油产率为30%~50%,柴油产率不超过40%,焦炭产率5%~7%左右。
由以上产品产率和产品质量情况可以看出,催化裂化过程的主要目的是生产汽油。
我国的公共交通运输事业和发展农业都需要大量柴油,所以催化裂化的发展都在大量生产汽油的同时,能提高柴油的产率,这是我国催化裂化技术的特点。
在同一条件下,剂油比大,表明原料油能与更多的催化剂接触。
㈡影响催化裂化反应深度的主要因素影响催化裂化反应转化率的主要因素有:原料性质、反应温度、反应压力、反应时间。
1、原料油的性质原料油性质主要是其化学组成。
重质油催化裂化化学

• 含硫化合物对于原料油的反应性能也有相 当的影响。硫对催化剂也是暂时的毒物, 会降低其活性和转化为汽油的选择性,同 时使干气产率增大,
•
影响催化裂化过程中硫在产物中分布的 重要因素是含硫化合物的组成结构。研究 表明,在催化裂化条件下,硫醚类化合物 绝大部分裂化生成H2S;而噻吩类化合物中 除有一部分也裂化开环生成H2S外,有些经 侧链断裂反应进入轻质产物,与芳香环并 合的噻吩类化合物则易于缩合进入焦炭。
• 2. 多环的芳香性物质含量高 • 重质油中含有较多的多环芳香烃以及胶质 和沥青质,这些组分易于吸附在催化剂表面 而生焦。 • 对于此类重质原料油,一般是以其残炭值 来衡量它在催化剂上的生焦倾向,有的则 认为应依据其中庚烷沥青质含量。
• 3. 重金属含量高 • 前已述及,原油中的镍、钒等重金属绝大 部分集中在其渣油中。这些金属在催化裂 化反应时绝大部分沉积于催化剂表面,并随 着催化剂的循环而不断积累,使其活性和选 择性逐渐下降。
•
由此可见,单个提升管反应器的高度过高,也 就是反应时间过长是不利的。为此,对于过高的 提升管反应器,有的采用在适当的高度注入诸如 冷态的直馏或催化汽油馏分等难裂解的所谓“中 止剂”,降低反应器上段的温度,以抑制轻质产 物的二次裂化。 为了避免轻质产物的过度裂化和降低汽油的烯 烃含量,近年来出现了许多相关的新技术,包括 用两个提升管反应器以多种方式进行组合,或将 一个提升管分区以不同条件进行反应等各种新工 艺。
三、重油催化裂化原料氢碳比的 影响及杂原子在产物中的分布
• 1.原料氢碳比的影响 • 大庆、胜利、孤岛、大港、华北和辽河 6种 减压渣油的在性质和组成结构上差别很大 的23个抽出油油样的催化裂化产物分布数 据,可以看出汽油的产率基本与原料油的 氢碳比呈线性关系,同时,焦炭产率与原 料油的氢碳比也基本呈线性关系。
催化裂化知识

催化裂化知识催化裂化是一种重要的炼油工艺,通过催化剂的作用将重质石油馏分转化为轻质产品。
在催化裂化过程中,石油馏分经过加热后与催化剂接触,发生裂化反应,生成较轻质的烃类化合物。
催化裂化技术广泛应用于石油炼制行业,使得石油资源得以充分利用。
催化裂化的原理是通过催化剂的作用降低反应的活化能,加快反应速率。
催化剂是一种能够提供活性位点的物质,它能够吸附反应物分子并改变其化学键,从而促进反应的进行。
常用的催化剂有酸性催化剂、碱性催化剂和金属催化剂等。
在催化裂化过程中,石油馏分首先被预热至适宜的温度,然后进入催化剂床层。
在催化剂的作用下,石油馏分中的大分子化合物发生裂化反应,生成烃类产品。
裂化反应主要包括裂解、重排和异构化等过程。
裂解是指将长链烃分子裂解为短链烃分子,重排是指短链烃分子发生位置变化,异构化是指短链烃分子发生结构变化。
催化裂化的反应条件主要包括温度、压力和催化剂的选择等。
温度是影响催化裂化反应速率和产物分布的重要因素。
适宜的温度能够提高反应速率,但过高的温度会导致生成焦炭等副产物。
压力对催化裂化反应的影响相对较小,一般较低的压力即可满足反应的需求。
催化剂的选择对反应的效果有着重要影响,不同的催化剂对产品分布、产率和选择性有不同的影响。
催化裂化技术的应用使得石油炼制过程更加灵活多样,能够根据市场需求灵活调整产品结构。
通过合理的催化剂设计和反应条件控制,可以实现不同产品的选择性裂化。
催化裂化不仅能够提高汽油产率,还能够产生重要的石化原料,如乙烯、丙烯等。
催化裂化技术的发展也为石油炼制行业的绿色转型提供了重要支持。
然而,催化裂化过程中也存在一些问题。
首先,催化剂的失活是一个严重的问题,随着反应的进行,催化剂会逐渐失去活性,需要定期更换。
其次,催化裂化反应的过程较复杂,需要综合考虑反应的热力学和动力学特性,以及催化剂的选择和反应条件的控制。
此外,催化裂化过程中还会产生大量的副产物,如焦炭和烟气,对环境造成一定的污染。
石油化工重油催化裂化工艺技术

石油化工重油催化裂化工艺技术石油化工重油催化裂化工艺技术是一种将重油转化为轻质油和化学品的过程。
该过程主要利用催化剂的作用,在高温高压条件下,使重油的大分子裂解成小分子,同时发生异构化、芳构化和氢转移等反应,以获得更多的轻质油和化学品。
催化剂的选择:催化剂是该技术的核心,其选择对产品的质量和产量有着至关重要的影响。
目前,常用的催化剂包括酸性催化剂、金属催化剂和金属氧化物催化剂等。
工艺条件的控制:工艺条件包括反应温度、压力、空速等,这些因素对产品的质量和产量都有着极大的影响。
因此,精确控制这些工艺条件是重油催化裂化工艺技术成功应用的关键。
产品的质量和性能:重油催化裂化工艺技术生产的产品具有高辛烷值、低硫含量等特点,被广泛应用于汽油、柴油、航空煤油等领域。
在应用方面,石油化工重油催化裂化工艺技术适用于不同类型重油,如减压渣油、催化裂化残渣油、脱沥青油等。
对于不同工业应用,可根据实际需求选择合适的工艺技术。
例如,对于生产高质量汽油和柴油的需求,可以选择更为精细的催化剂和严格的工艺条件;对于生产高附加值化学品的需求,则可以通过调整工艺流程和催化剂类型来增加化学品产量。
虽然石油化工重油催化裂化工艺技术在提高石油利用率、生产高质量石油化工产品方面具有重要作用,但也面临着一些挑战。
催化剂的活性、选择性和稳定性是该技术的关键,而目前催化剂的研究与开发尚存在诸多困难。
重油催化裂化过程中产生的固体废物和废气等对环境造成了严重影响,亟需解决。
由于重油资源的有限性,需要进一步探索和研发更为高效、环保的石油化工技术,以适应未来可持续发展的需要。
石油化工重油催化裂化工艺技术在石油化工产业中具有重要地位。
随着经济的发展和科技的进步,该技术将不断完善和优化,提高石油利用率和生产效率,同时注重环保和可持续发展。
未来,需要加强催化剂的研发与优化,减少环境污染,提高技术的绿色性和可持续性。
应积极探索新的石油化工技术,以应对全球能源危机和环境问题的挑战。
炼油催化裂化理论知识
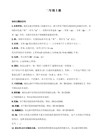
第二部分基础理论知识第二章炼油催化裂化理论知识2.1概述2.1.1催化裂化发展过程1938年4月6日年世界上第一套固定床催化裂化工业化装置问世,这是炼油工艺的重大发展,然而它存在一系列无法克服的缺点:设备结构复杂,操作繁琐,控制困难。
要克服固定床的缺点,需要两项革新,即催化剂在反应和再生操作之间循环和减小催化剂的粒径。
第一项革新结果出现了移动床,两项革新的结合得到了流化床。
本世纪40年代相继出现了移动床催化裂化和流化床催化裂化装置。
60年代中期出现的分子筛型催化剂带来了重大突破,成为催化技术发展的里程碑。
我国第一套移动床催化裂化装置是由前苏联设计并于1958年投产的。
1964年建成第二套,以后我国自己开发了流化催化裂化装置,故以后移动床催化裂化装置就不再建设了,这两套移动床催化裂化装置也于80年代改为流化催化裂化装置。
我国流化催化裂化的发展始于60年代,1965年5月5日,我国第一套0.6Mt /a同高并列式流化催化裂化装置在抚顺石油二厂建成投产,标志着我国炼油工业进入一个新阶段。
30多年来,我国流化催化裂化在炼油工业中一直处于重要地位,目前仍在发展。
到1993年底统计我国催化裂化装置的能力为5000余万吨/年,仅次于美国,位居世界第二。
随着石油资源的短缺和原油日趋变重,流化催化裂化在加工重质原料方面也取得了进展。
催化裂化掺炼渣油,提高轻质油收率最为显著,我国经过“六五”重大技术攻关,攻克了再生器的内外取热设施,渣油雾化技术,提升管出口快速分离技术,抗重金属污染催化剂等一系列技术难关。
目前,我国渣油催化裂化技术已发展成多种形式,有带内外取热的单段再生,不带取热的两段再生,带外取热的两段再生等。
到1993年底,石化总公司50套催化裂化装置,已有33套掺炼了渣油,掺炼量达到919万吨,渣油掺炼比达到了24.38%,已成为我国重要的渣油转化装置对提高轻质油收率,增加经济效益,起到非常重要的作用。
尽管催化裂化装置具有漫长的历史,但他远非一个完整的技术。
催化裂化技师培训资料

催化剂的装卸和储存过程中,需要注意安全防护,防止催化剂中毒、燃烧和爆炸等事故发 生。
废气、废水和废渣处理
催化裂化过程中产生的废气、废水和废渣,需要进行处理,严禁直接排放,避免对环境造 成污染。
催化裂化装置的环保设施与排放控制
装置密封与泄漏检测
废气处理
催化裂化装置的所有密封点都需要进行泄漏 检测,确保无有毒有害物质泄漏。
催化裂化的工业应用
生产汽油
催化裂化是生产汽油的主要途径之一,约占国内 汽油供应量的30%。
生产柴油
催化裂化也可以生产柴油,约占国内柴油供应量 的20%。
生产烯烃和芳烃
催化裂化还可以生产烯烃和芳烃,这些产品是化 工行业的重要原料。
02
催化裂化装置操作与维护
催化裂化装置的构成和功能
反应-再生系统
包括反应器、再生器、催化剂 输送系统、热量回收系统等。
催化裂化重要性
催化裂化是石油化工的重要组成部分,为我国能源供应和经 济发展做出了重要贡献。
催化裂化的反应原理
1 2
裂化反应
在催化剂作用下,重质油分子发生裂解,生成 轻质油和气体。
异构化反应
重质油中的烷烃在催化剂作用下发生异构化, 生成更轻的烷烃和烯烃。
3
氢转移反应
重质油中的芳烃在催化剂作用下发生氢转移, 生成更简单的芳烃。
多金属催化剂具有高稳定性和抗中毒性能,活性较高 ,寿命较长,但制备成本较高。
单铂催化剂具有高活性和选择性,适用于多种反应, 但稳定性较差。
助催化剂可以增强主催化剂的活性和稳定性,提高产 品质量。
催化裂化催化剂的制备和再生
1
催化裂化催化剂的制备主要包括载体选择、活 性组分浸渍、焙烧、还原等步骤。
石油炼制催化裂化课件
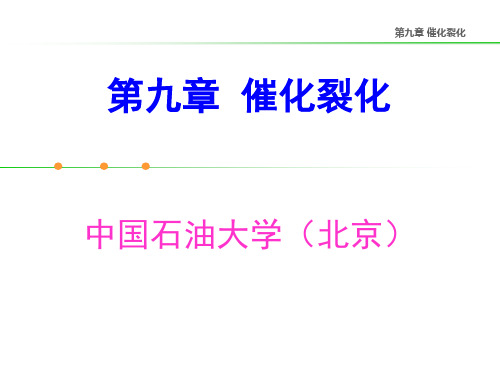
馏分油FCC: 减压馏分油 原料
350~500℃, 焦化馏分油 含芳较多,较难 (焦化汽、柴油) 裂化,不单独使用 C20~C36 含芳更多,更难 溶剂精制抽出 裂化,只能掺兑用 油
第9章 催化裂化
4、催化裂化的原料
类别 重油FCC: 原料来源 常压重油 减压渣油 特点 最重的部分,除 了多环、稠环芳 烃外,含有胶质 与沥青质,必须 使用专门的催化 剂与相应的工艺 设备与条件。
1960
第一套移动床 FCC 第一套流化床 FCC 1930 第一套固定床 FCC 2000
第9章 催化裂化
7、 FCC技术的发展方向 发展重残渣油的FCC技术,拓宽原料来源。
调整产品结构及产品质量 催化剂的发展 (加工重质油,具备专门特性的) 降低能耗 减少环境污染
过程模拟和计算机应用
脱氢
环烷烃
裂化 脱氢
芳烃+H2
断侧链
芳环+烷烃或烯烃(反应同上) 非常困难,只有个别特殊结构的芳烃可裂化 结焦或复杂环芳烃
芳香烃
开环裂化 脱氢
第9章 催化裂化
FCC反应——第一要点
主要反应——分解反应。
特有反应——氢转移反应;
FCC其它反应包括:异构化反应,芳构化 反应,缩合生焦反应。
第9章 催化裂化
第9章 催化裂化
FCC反应热:
强吸热反应——分解、脱氢、环化反应; 弱放热反应——异构化、氢转移及缩合反应。
热效应的计算:
以新鲜原料为基准:300-500 KJ/kg新鲜原料; (P330表9-5)
以反应产物——生成的(汽油+气体)量为基准; (P330,图9-5 ) 以反应生成的焦炭中的碳(催化碳 )为基准
重油催化裂化基础知识

重油催化裂化基础知识广州石化总厂炼油厂重油催化裂化车间编一九八八年十二月第一章概述第一节催化裂化在炼油工业生产中的作用催化裂化是炼油工业中使重质原料变成有价值产品的重要加工方法之一。
它不仅能将廉价的重质原料变成高价、优质、市场需要的产品,而且现代化的催化裂化装置具有结构简单,原料广泛(从瓦斯油到常压重油),运转周期长、操作灵活(可按多产汽油、多产柴油,多产气体等多种生产方法操作),催化剂多种多样,(可按原料性质和产品需要选择合适的催化剂),操作简便和操作费用低等优点,因此,它在炼油工业中得到广泛的应用。
第二节催化裂化生产发展概况早在1936年美国纽约美孚真空油公司(SoCony vacu um co)正式建立了工业规模的固定床催化裂化装置。
由于所产汽油的产率及辛烷值均比热裂化高得多,因而一开始就受到人们的重视,并促进了汽车工业发展。
如图所示,片状催化剂放在反应器内不动,反应和再生过程交替地在同一设备中进行、属于间歇式操作,为了使整个装置能连续生产,就需要用几个反应器轮流地进行反应和再生,而且再生时放出大量热量还要有复杂的取热设施。
由于固定床催化裂化的设备结构复杂,钢材用量多、生产连续性差、产品收率及性质不稳定,后为移动床和流化床催化裂化所代替。
第一套移动床催化裂化装置和第一套流化床催化裂化(简称FCC 装置都是1942年在美国投产的固定床反应器移动床催化裂化的优点是使反应连续化。
它们的反应和再生过程分别在不同的两个设备中进行,催化裂化在反应器和再生器之间循环流动,实现了生产连续化。
它使用直径约为3毫米的小球型催化剂。
起初是用机械提升的方法在两器间运送催化剂,后来改为空气提升,生产能力较固定床大为提高、产品质量也得到了改善。
由于催化剂在反应器和再生器内靠重力向下移动、速度很缓慢,所以对设备磨损很小,但移动床的设备仍较复杂,耗钢量仍较大,特别是处理量在80 万吨/年以上的大型装置、移动床远不如流化床优越。
石油炼制过程中的催化裂化技术

石油炼制过程中的催化裂化技术石油作为一种重要的能源资源,在现代工业生产中发挥着重要作用。
然而,原始的石油资源并不直接适用于工业生产,需要经过炼制过程才能得到各种对我们有价值的产品,如汽油、柴油、航空燃料等。
催化裂化技术作为石油炼制中的重要工艺之一,对于提高石油利用率、改善产品质量具有重要意义。
一、催化裂化技术的作用催化裂化技术是指通过催化剂的作用,将大分子石油组分裂解成小分子烃化合物的过程。
在传统炼油工艺中,原油经过蒸馏处理后得到的馏分中,还含有大量的重油和杂质。
这些重油在石油炼制过程中无法直接利用,需要经过催化裂化技术将其裂解成较小分子的轻质油品。
催化裂化技术可以有效提高石油资源的利用率,同时还能改善产品质量。
二、催化裂化技术的原理催化裂化技术的原理基于化学反应中的催化作用以及裂化作用。
催化剂是催化裂化过程中的关键因素,通过调整催化剂的配方和结构,可以控制反应的速率和选择性。
催化裂化过程中,大分子石油组分吸附到催化剂表面,随后经过热裂化作用被裂解成小分子烃化合物。
裂化产物进一步在催化剂的作用下重组成为更加有价值的轻质油品。
三、催化裂化技术的应用催化裂化技术在炼油行业中广泛应用,可以生产出各种油品,如汽油、柴油、液化石油气等。
其中,汽油是对车辆工作性能具有重要影响的燃料,通过催化裂化技术可以有效提高汽油的辛烷值和溢价性能,使得汽车动力性能得到提升。
另外,柴油在农业机械和工程机械中的应用也十分广泛,催化裂化技术可以调整柴油的凝点、减少硫含量,提高其性能。
四、催化裂化技术的发展趋势目前,随着能源需求的增长和环境污染问题的日益凸显,催化裂化技术也在不断发展与完善。
一方面,炼油企业致力于研究更加高效的催化剂和工艺,以提高产品收率和质量;另一方面,催化裂化技术逐渐向更深度和多功能的方向发展,尽可能获取更多高附加值的产品。
此外,随着环保意识的增强,绿色低碳的催化裂化技术也备受关注,以降低碳排放和污染物产生。
催化裂化(分析的很全面)
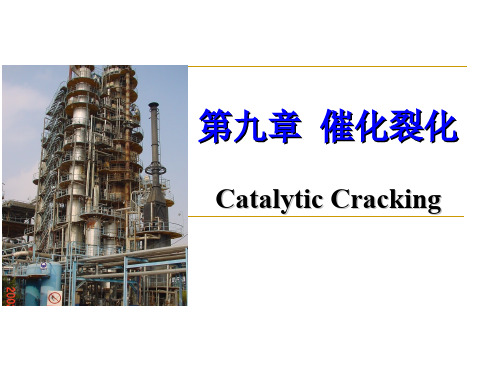
第九章 催化裂化
Catalytic Cracking
第一节 概述
燃料生产中一个重要的问题
如何将原油中的重质馏分油甚至渣油转化成轻
质燃料产品
重质油轻质化
从大分子分解为较小的分子
主要依靠分解反应(热反应和催化反应)
从低 H/C 的组成转化成较高 H/C 的组成
脱 碳(溶剂脱沥青、催化裂化、焦炭化等) 加 氢(加氢裂化)
变)
提高催化剂的活性还有利于促进氢转移反应和异
构化反应,对提高产品质量有利。
催化剂的活性取决于它的结构和组成。
② 活性和催化剂表面上的积炭有关
催化剂表面积炭量↗,活性↙ 。 单位催化剂上焦炭沉积量主要与催化剂在反应器内
的停留时间有关。
催化剂上的焦炭含量还与剂油比有关
③ 剂油比, C/O
一、催化裂化的原料和产品
催化裂化是目前石油炼制工业中最重要的二次加工过
程,也是重油轻质化的核心工艺 ,是提高原油加工深 度、增加轻质油收率的重要手段。
催化裂化原料:重质馏分油 ( 减压馏分油、焦化馏分
油 ) 、常压重油、减渣 ( 掺一部分馏分油 ) 、脱沥青 油。 主要控制指标:金属含量和残碳值
催化裂化技术今后的发展方向: ① 加工重质原料 ② 降低能耗 ③ 减少环境污染 ④ 适应多种生产需要的催化剂和工艺 ⑤ 过程模拟和计算机应用
第二节 石油烃类的催化裂化反应
一、单体烃的催化裂化反应
1 .各类单体烃的裂化反应
(1). 烷 烃
烷烃主要发生分解反应,例如 :
C16H34
+ C8H16 C8H18
催化裂化基础知识

提升管在流化过程中,当气速高于带出速度,固体颗粒便被带出。
把带出的颗粒沿一根垂直管道向上运动,这根管道称为提升管。
提升管主要有两种用途。
一是用于固体颗粒输送;一是作为反应器,亦称为提升管反应器,催化剂和气相原料在提升管中停留时进行反应,在出口处反应产物与催化剂分离。
催化剂经再生后又重新进入提升管,构成一循环流化床反应系统。
提升管反应器的主要优点是返混较小,效率高,结构简单。
目前的催化裂化装置都采用提升管反应器。
提升管反应器的基本结构形式如图1所示。
提升管反应器的直径由进料量确提升管反应器的作用定。
工业上一般采用的线速是入口处为4-7m/s,出口处为12-18m/s。
随着反应深度的增大,油气体积流量增大,因此有的提升管反应器由不同直径的两段(上粗下细)组成二提升管反应器的高度由反应所需时间确定,工业设计时多采用2-4s的反应时间。
近年来由于进入反应器的再生催化剂温度多已提高到650-720C,提升管下段进料油与再生催化剂接触处的混合温度较高,当以生产汽油、柴油为上要目标时,反应只需2s左右的时间就已基本完成,过长的反应时间使二次裂化反应增多,反而使口的产物的收率下降。
为了优化反应深度,有的装置采用终止反应技术,即在提升管的中上部某个适当位置注人冷却介质以降低终中部的反应温度,从而抑制二次反应。
有的还在注人反应终止剂的问时相应地提高或控制混合段的温度,称为混合温度控制技术(MTC。
此项技术的关键是如何确定注入冷却介质的适宜位置、种类和数量。
国内有些炼油厂采用了注入终止剂技术,但是仅是凭经验来确定有关的参数,可靠性差。
中国石油大学提出的提升管反应器流动一反应模型可以对提升管内的反应过程进行三维模拟,初步解决了科学确定上述有关参数的问题。
图2是在某催化裂化装置的提升管的适当位置注入反应终止剂前后提升管沿高的温度及反应产二物产率变化情况的模拟计算结果。
由此可见,注入终止剂后,汽油和柴油的产率都有所提高。
注入终止剂的效果与原工况及注入的条件有关。
催化裂化技师培训资料

催化裂化技师培训资料xx年xx月xx日CATALOGUE目录•催化裂化基础知识•催化裂化装置操作与维护•催化裂化生产安全管理•催化裂化工艺流程优化•催化裂化节能减排技术•催化裂化技师培训计划与实施01催化裂化基础知识催化裂化是一种石油加工技术,通过催化剂的作用,将重质油转化为轻质油的过程。
催化裂化定义具有较高的转化率和良好的产品质量,同时能够实现重质油的轻质化,提高石油资源的利用率。
催化裂化特点催化裂化的定义与特点裂化反应在热和催化剂的作用下,重质油发生裂化反应,分解成更小的分子,如烷烃、烯烃等。
异构化反应在催化剂的作用下,小分子发生异构化反应,转化为更优质的石油产品。
催化裂化的反应原理催化裂化的工业应用生产高质量汽油催化裂化是生产高质量汽油的重要手段之一,具有较高的辛烷值和良好的燃烧性能。
提高石油资源利用率催化裂化技术能够将重质油转化为轻质油,提高石油资源的利用率,降低能源消耗。
生产柴油和燃料油催化裂化技术也能够生产柴油和燃料油等重油产品,满足工业和交通运输的需求。
02催化裂化装置操作与维护催化裂化装置的构成与功能催化裂化反应在反应器中进行,包括提升管、沉降器等主要部件。
反应器再生器分馏塔其他辅助设备烧焦催化剂以恢复其活性,包括燃烧室、再生器等主要部件。
将反应产物分离成不同沸点的产品,包括分馏塔、回流罐等主要部件。
如输送泵、压缩机、阀门等,控制和调节装置的运行。
催化裂化装置的操作规程检查设备状况、催化剂准备、工艺流程等,确保装置满足开车条件。
开车前准备按照规定的步骤和顺序启动装置,确保各部位运行正常。
开车操作控制适宜的反应温度、压力等参数,保持装置稳定运行。
正常操作按照规定的步骤和顺序停车装置,确保安全、环保。
停车操作定期对装置进行巡检,发现异常及时处理。
巡检维护检查设备部件、管道、阀门等是否正常,及时更换损坏部件。
定期检查根据催化剂活性情况,及时补充或更换催化剂。
催化剂补充根据产品需求和市场变化,优化工艺流程,提高装置效率。
催化裂化讲义

催化裂化讲义单位:姓名:目录1.催化裂化基本知识 (1)1.1基本催化裂化工艺 (1)1.2装置主要指标 (1)1.3产品质量控制 (3)1.4各种基本计算 (5)2.中油催化装置基本情况 (6)2.1平面布置 (6)2.2主要设备型号 (9)2.3主要控制回路 (11)2.4三大平衡 (14)3.自动保护系统(ESD) (15)4.基本开停工过程 (19)4.1开工步骤 (19)4.2停工步骤 (19)5.基本事故处理 (19)5.1紧急停工的条件: (19)5.2紧急停电 (20)5.3全厂性停电: (21)5.4仪表电全停时装置应急处理方案 (22)5.5火灾事故 (22)5.6增压机自停事故处理预案 (22)1.催化裂化基本知识1.1基本催化裂化工艺FCC(流化催化裂化)的各种工艺,基本上没有多大的区别,较大的区别在产品分布,从而对各部分的设计产生影响。
以重质油为原料多产丙烯的催化裂解技术(DCC)、多产液化气和汽油的催化裂化技术(MGG和ARGG)、多产异构烯烃的催化裂化技术(MIO)、多产丙烯和乙烯的催化热裂解技术(CPP),全大庆减压渣油催化裂化工艺(VRFCC),焦化蜡油吸附转化DNCC催化裂化技术。
MIP 多产异构烷烃DCC 深度催化裂化MGD 最大量生产液化气和柴油工艺FDFCC 灵活双效催化裂化MSR(Multi Stage Reaction)多段提升管MSR-PL 最大量丙稀、液化气MSR-LG 最大量液化气、汽油MSR-DG 最大量柴油、汽油MSR-OLD 最大量降低汽油稀烃催化裂化装置主要任务是将常压重油(渣油、蜡油)等经过反应生成高辛烷值汽油、轻柴油、液化石油气、干气、油浆,并将生成的焦炭在再生器燃烧,产生蒸汽,另外还提供近100℃的低温热源。
1.2装置主要指标1.加工能力同类装置,相同条件下(装置类型、原料和催化剂性质、加工工艺、生产方案等)一般加工量越大,综合能耗越低。
重油催化裂化工艺
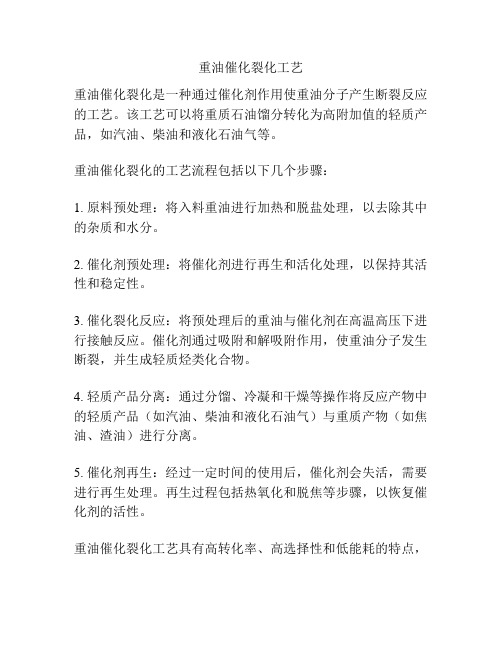
重油催化裂化工艺
重油催化裂化是一种通过催化剂作用使重油分子产生断裂反应的工艺。
该工艺可以将重质石油馏分转化为高附加值的轻质产品,如汽油、柴油和液化石油气等。
重油催化裂化的工艺流程包括以下几个步骤:
1. 原料预处理:将入料重油进行加热和脱盐处理,以去除其中的杂质和水分。
2. 催化剂预处理:将催化剂进行再生和活化处理,以保持其活性和稳定性。
3. 催化裂化反应:将预处理后的重油与催化剂在高温高压下进行接触反应。
催化剂通过吸附和解吸附作用,使重油分子发生断裂,并生成轻质烃类化合物。
4. 轻质产品分离:通过分馏、冷凝和干燥等操作将反应产物中的轻质产品(如汽油、柴油和液化石油气)与重质产物(如焦油、渣油)进行分离。
5. 催化剂再生:经过一定时间的使用后,催化剂会失活,需要进行再生处理。
再生过程包括热氧化和脱焦等步骤,以恢复催化剂的活性。
重油催化裂化工艺具有高转化率、高选择性和低能耗的特点,
可以有效地利用重油资源,提高石油产品的附加值。
这一工艺在石油炼制行业中得到广泛应用。
催化裂化技师培训资料

在启动催化裂化装置前,需检查各种设备、管道和阀门等设施是否正常,确保没有安全隐患。启动过程中,需要按照操作规程依次开启设备,控制适宜的工艺参数,如温度、压力和流速等。在装置运行稳定后,可进行停机操作,先逐渐降低工艺参数至安全范围,再关闭设备。
详细描述
总结词
掌握装置正常操作与优化是提高催化裂化过程效率和经济效益的关键。
催化裂化事故处理与安全
03
事故处理原则
遵循“安全第一,预防为主”的原则,确保人员安全,减少事故损失。
事故处理方法
立即报告,迅速采取措施防止事故扩大,保护事故现场,收集证据。
事故处理原则与方法
安全风险识别
识别潜在的事故风险源,如设备故障、操作失误、自然灾害等。
安全风险防范
采取有效的预防措施,如定期检查设备、培训操作人员、建立应急预案等。
催化裂化定义
催化裂化广泛应用于炼油厂和石化工业,是生产高辛烷值汽油、柴油和其他石油产品的关键技术之一。
催化裂化应用范围
催化裂化定义
反应原理概述
催化裂化过程主要涉及裂解和异构化反应,通过催化剂的作用将重质油转化为轻质烃类。
催化裂化反应原理
裂解反应
裂解反应是催化催化剂的作用下,按C-C键裂解成更小的烃类,如汽油、柴油等。
持续学习
职业素养提升方法与途径
在实际工作中积累经验,通过完成各种任务,提高解决问题的能力,培养对工作的敏感性和判断力。
实践积累
参加行业会议、研讨会和论坛,与同行交流,了解行业发展趋势,拓展视野。
参与行业交流
制定学习计划
对催化裂化领域的专业知识进行深入学习,包括反应机理、工艺流程、设备原理等。
深入学习
环保运行管理
催化裂化基础知识培训讲义
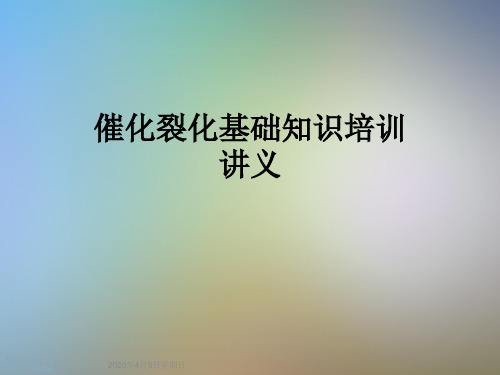
路漫漫其修远兮, 吾将上下而求索
•
二、世界石油资源状况分析
路漫漫其修远兮, 吾将上下而求索
1、石油资源: 世界石油资源分析见表-2: 石油比重指数变化趋势见图-1 石油中的硫含量变化趋势见图-2
2、常规原油各馏分性质 相对密度的变化:见表-3 原油馏分组成:见图-3和表-4
3、世界石油产品需求结构 世界石油产品需求结构变化情况见图-4
催化裂化基础知识培训 讲义
路漫漫其修远兮, 吾将上下而求索
2020年4月5日星期日
路漫漫其修远兮, 吾将上下而求索
催化裂化基础知识
授课内容
第一节 世界石油资源 第二节 催化裂化原料 第三节 催化裂化反应 第四节 流态化原理
•
•第一节 世界石油资源
一、石油的基本性质 •二、世界石油资源状况分
析 •三、重质油加
说明:重质原料油的化学组成很难分析,平时 用相对密度、特性因数和苯胺点等物理性质来间接 判断原料的裂化性能。
路漫漫其修远兮, 吾将上下而求索
•
一、衡量原料性质的指标
3、残炭
残炭值对焦炭生成量和热平衡两个方面有影 响。
原料残炭越高,则生焦量多,再生时燃烧放 出的热量过剩,需要外取热。常规馏分油的残炭较 低,一般在6%左右。
•
三、重质油加工
1、重质油的定义: 定义并不十分明确,一般指适应于:
(1)API重度<20; (2)S%>2%; (3)粘度,硫、氮、氧和重金属含量较 高。 广义地讲,重质油包括所有原油中的沸 点在500℃以上的渣油。
路漫漫其修远兮, 吾将上下而求索
•
三、重质油加工
2、重质油加工的目的
充分利用石油资源,使重油轻质化,提高轻质 油收率,提高经济效益。
- 1、下载文档前请自行甄别文档内容的完整性,平台不提供额外的编辑、内容补充、找答案等附加服务。
- 2、"仅部分预览"的文档,不可在线预览部分如存在完整性等问题,可反馈申请退款(可完整预览的文档不适用该条件!)。
- 3、如文档侵犯您的权益,请联系客服反馈,我们会尽快为您处理(人工客服工作时间:9:00-18:30)。
矿产资源开发利用方案编写内容要求及审查大纲
矿产资源开发利用方案编写内容要求及《矿产资源开发利用方案》审查大纲一、概述
㈠矿区位置、隶属关系和企业性质。
如为改扩建矿山, 应说明矿山现状、
特点及存在的主要问题。
㈡编制依据
(1简述项目前期工作进展情况及与有关方面对项目的意向性协议情况。
(2 列出开发利用方案编制所依据的主要基础性资料的名称。
如经储量管理部门认定的矿区地质勘探报告、选矿试验报告、加工利用试验报告、工程地质初评资料、矿区水文资料和供水资料等。
对改、扩建矿山应有生产实际资料, 如矿山总平面现状图、矿床开拓系统图、采场现状图和主要采选设备清单等。
二、矿产品需求现状和预测
㈠该矿产在国内需求情况和市场供应情况
1、矿产品现状及加工利用趋向。
2、国内近、远期的需求量及主要销向预测。
㈡产品价格分析
1、国内矿产品价格现状。
2、矿产品价格稳定性及变化趋势。
三、矿产资源概况
㈠矿区总体概况
1、矿区总体规划情况。
2、矿区矿产资源概况。
3、该设计与矿区总体开发的关系。
㈡该设计项目的资源概况
1、矿床地质及构造特征。
2、矿床开采技术条件及水文地质条件。