amada数控冲床面板及操作指导
数控冲床作业指导书(AMADA)
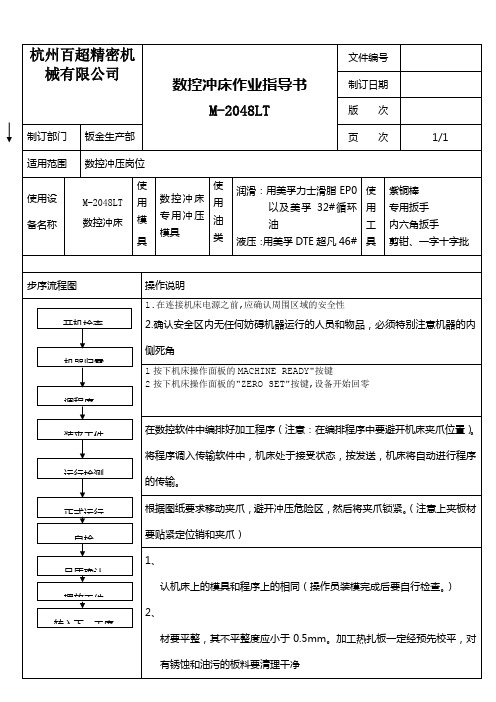
数控冲床作业指导书 M-2048LT
使 数控冲床 用 专用冲压 油 模具 类
文件编号 制订日期 版 次 页 次
1/1
使 润滑:用美孚力士滑脂 EP0 用 以及美孚 32#循环油 工 液压:用美孚 DTE 超凡 46# 具
紫铜棒 专用扳手 内六角扳手 剪钳、一字十字批
步序流程图 开机检查
操作说明
1.在连接机床电源之前,应确认周围区域的安全性
2.确认安全区内无任何妨碍机器运行的人员和物品,必须特别注意机器的内 侧死角
1 按下机床操作面板的 MACHINE READY"按键 2 按下机床操作面板的"ZERO SET"按键,设备开始回零
机器归零
调程序 装夹工件
运行检测
正式运行 自检 品质确认 摆放工件 转入下一工序
在数控软件中编排好加工程序(注意:在编排程序中要避开机床夹爪位置) 。 将程序调入传输软件中,机床处于接受状态,按发送,机床将自动进行程序 的传输。 根据图纸要求移动夹爪,避开冲压危险区,然后将夹爪锁紧。 (注意上夹板材 要贴紧定位销和夹爪) 1、确认机床上的模具和程序上的相同(操作员装模完成后要自行检查。 ) 2、板材要平整,其不平整度应小于 0.5mm。加工热扎板一定经预先校平,对 有锈蚀和油污的板料要清理干净 1、加工过程中操作人员绝对不能离开机床,如确需离开必须先暂停加工。 2、加工过程中,步冲下来的料芯需及时取出,避免事故发生。 3、送进速度要与板料大小相适应。 1、先对冲压出来的工件做外观检查; 2、严格按照图纸尺寸自检工件; 确认合格后通知品检确认 工件要摆放整齐,分好种类,做好标识。 待工件数量完成后即根据工艺流程表顺序转入下一个工序
确认安全区内无任何妨碍机器运行的人员和物品必须特别注意机器的内侧死角按下机床操作面板的machineready按键按下机床操作面板的zeroset按键设备开始回零在数控软件中编排好加工程序注意
数控冲床操作规程

数控冲床操作规程数控冲床是一种以数字程序控制系统为基础的自动化设备,用来进行冲压、切割、冲孔等金属加工操作。
操作数控冲床必须按照相关规程进行,以确保操作安全和加工质量。
以下是数控冲床操作规程的一般要求。
一、操作准备1.操作人员必须熟悉数控冲床的结构、性能、操作方法和安全注意事项。
2.检查数控冲床的各个部位是否有损坏或松动现象,保证设备正常。
3.操作人员应穿戴好工作服,手套、护目镜、防护面罩等安全用品。
二、开机检查1.按照操作手册的要求检查冲床的电源、气源等是否正常接通。
2.检查润滑系统是否正常运转,必要时补充润滑油。
3.检查数控系统是否正常开机,确认数字程序控制系统、工作台、冲头等各部分是否协调工作。
三、设定冲床工作参数1.根据加工产品的要求,设定合适的冲床工作参数,如行程、下降速度、冲击力等。
2.确认加工工艺路线和相应的数控程序。
四、装夹工件1.根据工艺要求选择合适的冲头和模具。
2.将工件正确装夹好,保证工件与冲头、模具的配合关系。
3.紧固好工件,以确保加工过程中工件的稳定性和安全性。
五、调整机床1.根据工件和加工要求,调整冲床的移动速度、冲击力大小等参数。
2.确保工件准确对位,并校正冲床的坐标系统。
六、编制加工控制程序1.根据工艺要求及加工程序,编写合适的数控加工程序。
2.将编写好的程序上传至数控冲床的数控系统中,确保程序的正确性。
七、安全操作1.操作人员必须严格按照操作规程和安全注意事项操作。
2.加工过程中,操作人员必须做好工件、刀具等的定位、监控和观察,确保加工的正确性和安全性。
3.加工过程中,不得随意触碰机床、工件和刀具等,以免发生意外伤害。
八、加工完成后的处理1.加工结束后,关闭数控冲床的电源及气源,并清理工作台和周围环境。
2.检查冲床的各个部位是否正常,如有异常情况应及时报修。
九、记录与整理1.对于每次加工的产品,操作人员应及时记录加工参数、加工程序和产品质量等相关信息。
2.对于冲床的常规维护、保养、故障等情况,也应进行记录和整理,以便日后参考。
Amada数冲操作规程

Amada数冲操作规程一.开机以前做如下检查1.检查并确保以下的机器部件周围无外来的干扰物:X轴导轨,工作台的两端及中间运动轴承, Y轴导轨的前,后部; 转塔上定位销及其安装孔; 上转塔及打击头,下转塔等;2.将以下机器部件涂好润滑油:夹爪、转塔工位、转塔滑块及冲头等;推荐润滑油种类:ESSOTeresso32或MOBILDTEOilLight或SHELLTellusOilC323.检查机器的空气过滤器及空压机是否正常,并排干空气过滤器内的积聚水份;4.检查并确认自动加油钏中的油位应处于刻度线以上,如果油位低于刻度线则需先加油,以确保油位始终处于刻度线以上;5.检查并调节气压阀保证其通过的气压保持在0.49Mpa左右;6.当机器处于停止状态,液压泵开始运行,此时打开停止阀的油压应在19.6±0.49Mpa-9.8±0.49Mpa的范围内,检查完毕后立即关毕停止阀(如果超出该范围则立即停机并申请维修);7.当液压泵开始运行时,应确认机器油箱中的油位应在高低刻度线之间,如果油位低于最低刻度线,则应立即加以补充;8.检查气压管道有无泄露及破损现象;9.检查液压管道及水冷却系统的管道无破损及渗漏现象;10.检查并确认模具已正确安装到位,EMERGENCYSTOP按钮处于工作状态及转塔的塑胶外壳无破损现象;二.开机步骤1.启动车间电源:2.启动空气压缩机并开启气压阀;3.启动水冷却系统;4.将位于机床电器控制柜上的的电路开关切换至ON位置;5.在主控制面板上按下POWERON按钮;6.确认主控制面板上的NCREADY和TOPDEADCENTER灯处于工作状态;7.确认主控制面板上的RETRACT指示灯处于工作状志.如果该指示灯不亮,先将MODECHANGE 开关切换至ON状态,并按下RECRACT按钮,然后再将MODECHANGE开关切换至OFF状态;8.用脚踏开关使夹爪处于关闭状态;9.确认主控制面板上的MACHINESTOP指示灯处于工作状态;10.清理工作区或内的障碍物,并隔离工作区域内的人员;11.按下+X,+Y及T按钮以使工作台,转塔及工作台回至零位;12.确认+X,+Y及T按钮的指示灯处于工作状态;三.关机步骤1.首先按下主控制面板上的POWEROFF按钮;2.将位于机床电器控制柜上的的电路开关切换至OFF位置;3.关闭气压阀并关掉空气机;4.关闭水冷却系统;5.关闭车间电源;四.开机前的预热当机床中液压油温度低于10℃时,在开机之前就必须对机器进行预热,预热时按照以下步聚进行:1.将主控制面板上的MODECHANGE开关切换至ON,并按下MDI按钮并确认其指示灯处于工作状态,然后将MODECHANGE开关切换至OFF状态;2.在主控制面板上按下WARMINGSTART按钮开始预热.冲床打击头会运行5mm约3分钟后机床会自动停止.注意:在机器自动停止运转之前必须停止机器的预热,按下STOP按钮后,机器的运转将会被停止,同时WARMINGSTART按钮的指示灯也将处于关闭状态.按下WARMINGSTART能重新启动机器的预热五.安装模具按以下步骤进行1.确认+X,+Y及T按钮的指示灯处于工作状态;2.将主控制面板上的MODECHANGE开关切换至ON状态,按下MANUAL按钮并确认指示灯处于工作状态,然后将MODECHANGE开关切换至OFF状态;3.将主控制面板上的TOOLCHANGE开关切换至ON状态;4.在子控制面板B上同时按下TURRETJOG和TURRETJOGON按钮以转动转塔至所需更换或安装模具的工位,在转到所需工位后松开按钮;5.打开转塔上的门以安装,拆卸或更换模具;工作完成后关闭此门;6.将主控制面板上的TOOLCHANGE开关切换至OFF状态.注意:1.在安装或拆卸模具时必须将TOOLCHANGE开关切换至ON状态;2.在旋转转塔(刀盘)前,注意确认不得有其余人员靠近转塔,3.安装模具时要注意模具间隙,模具间隙因材质,板厚的不同而不同,具体参见下表:Amada机床分为机械式驱动(曲轴式)(指PEGA,COMA,ARIES系列,我司为ARIES系列)及液压式驱动(指VIPROS,APERIO-V系列,我司为VIPROS系列)两种,对于两种机床有着不同的间隙值,详见下表:六.存储器的操作说明1.先将主控制面板上的MODECHANGE开关切换至ON,按下MEMORY按钮并确认其指示灯处于工作状态后,再将MODECHANGE开关切换至OFF状态;2.在主控制面板上按下Program键;并按下右边的箭头和DIR键;3.在显示屏上显示将要生产的程式-----使用键盘输入数字号并按下O-SRH键.再移动指针至显示的程式数字地址后的O;4.使用脚踏开关松开夹爪;5.将板材放于工作台上,并升起X轴定位块;6.推动板材使其对齐夹爪及定位块;7.用脚踏开关合上夹爪夹紧板材并降下定位块;8.确认显示屏上没有任何报警信息.检查并确认以下开关及PHNC参数全部设定为运转状态:·BLOCKSKIP按钮·EDITPROTECT开关(需切换至ON状态)·FEEDATE按钮·MODECHANGE开关(切换至OFF状态)·MULTIPLEPARTMODE按钮·OPTSTOP按钮·OVERRIDEON/OFF按钮·PRESSSELECT开关(切换至CYCLE或OFF状态)·SINGLE按钮·TEST按钮·TOOLCHANGE开关(切换至OFF)·RAM POSITION按钮·RAMSPEED按钮9.清理工作区或内的障碍物,并隔离工作区域内的人员;10. 按下START按钮以执行程式.11. 在加工完一个程式后,工作台及会回至原来的零点,并且+X,+Y按钮的指示灯将会处于工作状态;指针将会回到该程式的开始位置.注意:1.当在危险区域内工作时必须将TOOLCHANGE开关切换至ON状态;2.在机床周边的危险区域里的障碍物未被清理或人员未被隔离出来前,不得启动START按钮;五. MDI模式操作说明:当机床准备工作完毕后可按如下步骤进行MDI模式操作,1.先将主控制面板上的MODECHANGE开关切换至ON,按下MDI按钮并确认其指示灯处于工作状态后,再将MODECHANGE开关切换至OFF状态;2.按下MDI按键;3.使用脚踏开关松开夹爪;4.将板材放于工作台上,并升起X轴定位块;5.推动板材使其对齐夹爪及定位块;6.用脚踏开关合上夹爪夹紧板材并降下定位块;7.按如下步骤在显示屏上创建新程式:a.先将主控制面板上的EDITPROTECT开关切换至OFF;b.按下ABSLT键来指定输入数据的开始;c.在主控制面板上使用地址和数字键输入第一行数据,并在结尾处按下EOB键以输入“;”d.再按Insert键后按同样的方式输入数据;e.在数据输入完毕后,按下REWIND键来移动指针至程式的开始处;f.再将EDITPROTECT开关切换至ON状态8.确认显示屏上没有任何报警信息,检查并确认以下开关及PHNC参数全部设定为运转状态. ·BLOCKSKIP按钮·EDITPROTECT开关(需切换至ON状态)·FEEDRATE 按钮·MODECHANGE开关(需切换至OFF状态)·OPTSTOP按钮·PRESSSELECT开关·SINGLE按钮·TOOLCHANGE开关(需切换至OFF状态)·RAMPOSITION开关·RAMSPEED按钮9.清理工作区或内的障碍物,并隔离工作区域内的人员;10.按下START按钮以确定板材的位置和指定刀位;11. 在加工成型时,按如下步骤设定PHNC内容:a.先将主控制面板上的EDITPROTECT开关切换至OFF;b.再按下主控制面板上的Position按钮;c.按下PHNC键以显示PHNC菜单;d.移动指针至ManualPress并按下Insert键,显示屏上将出现ManualPress选项;e.输入将要使用的M代码命令并按下Insert键输入;f.数据输入完毕后按下REGDATA按钮以存储该程式于内存中;g.再将EDITPROTECT开关切换至ON状态.12.按下RAMSPEED按钮并确认其指示灯处于工作状态;13.将PRESSSELECT开关切换至CYCLE或INCHING状态;14.按下PUNCHING按钮后机床开始加工.。
数控冲床作业指导书

数控冲床作业指导书一、引言数控冲床是一种自动化机床,具有高精度、高效率和灵便性的特点,广泛应用于金属加工领域。
本作业指导书旨在向操作人员提供数控冲床的操作指导,以确保操作的安全性和工作的高效性。
二、数控冲床概述数控冲床是一种通过计算机控制的自动化机床,用于在金属板材上进行冲孔、切割、成形等加工工艺。
它由机床本体、数控系统、液压系统、电气系统等部份组成。
数控系统通过预先编写好的程序,控制机床的运动轨迹和工作参数,实现精确的加工操作。
三、操作前准备1. 确保数控冲床的正常运行状态,检查电源、气源、润滑系统等设备是否正常。
2. 佩戴个人防护装备,如安全帽、防护眼镜、耳塞等。
3. 确认加工工件的尺寸和材质,并选择合适的刀具和夹具。
四、数控冲床操作步骤1. 启动数控冲床,按照系统提示登录数控系统。
2. 导入加工程序,根据工件要求选择相应的程序,并加载到数控系统中。
3. 设置工作坐标系,根据工件的位置和尺寸,在数控系统中设置工作坐标系。
4. 设置刀具和夹具,根据工艺要求选择合适的刀具和夹具,并进行装夹。
5. 进行刀具的长度补偿,根据刀具的实际长度,在数控系统中进行补偿设置。
6. 进行加工参数的设置,根据工艺要求设置加工速度、进给速度、冲床力等参数。
7. 进行手动定位,通过手动操作数控冲床,将刀具位置调整到工件上。
8. 进行自动加工,按下启动按钮,数控冲床将按照预先设定的程序进行自动加工。
9. 监控加工过程,注意观察加工状态,确保加工过程的稳定性和安全性。
10. 加工完成后,关闭数控冲床,清理加工区域,保持机床的整洁。
五、操作注意事项1. 操作人员应熟悉数控冲床的操作规程和安全操作规范。
2. 在操作过程中,严禁随意触摸机床和刀具,以免造成伤害。
3. 注意刀具和夹具的安装和调整,确保其稳固可靠。
4. 定期检查数控冲床的润滑系统和冷却系统,保持其正常工作。
5. 加工过程中,及时清理切屑和废料,防止阻塞和影响加工质量。
数控冲床编程操作程序 AMADA
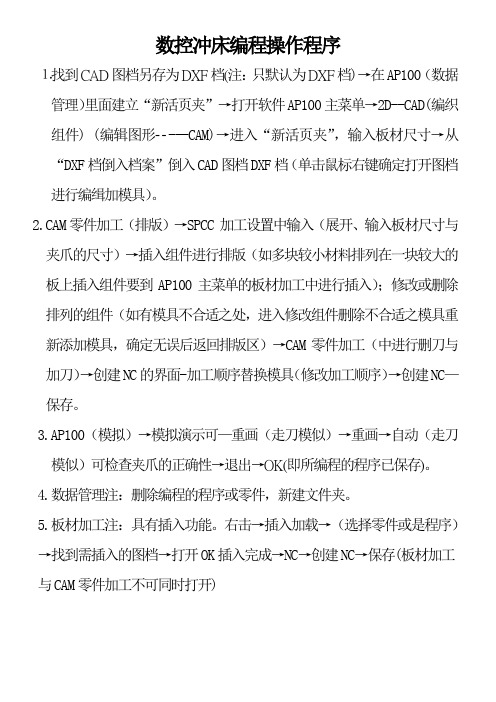
数控冲床编程操作程序
⒈找到CAD图档另存为DXF档(注:只默认为DXF档)→在AP100(数据
管理)里面建立“新活页夹”→打开软件AP100主菜单→2D--CAD(编织组件) (编辑图形---CAM)→进入“新活页夹”,输入板材尺寸→从“DXF档倒入档案”倒入CAD图档DXF档(单击鼠标右键确定打开图档进行编缉加模具)。
2.CAM零件加工(排版)→SPCC 加工设置中输入(展开、输入板材尺寸与夹爪的尺寸)→插入组件进行排版(如多块较小材料排列在一块较大的板上插入组件要到AP100主菜单的板材加工中进行插入);修改或删除排列的组件(如有模具不合适之处,进入修改组件删除不合适之模具重新添加模具,确定无误后返回排版区)→CAM零件加工(中进行删刀与加刀)→创建NC的界面-加工顺序替换模具(修改加工顺序)→创建NC—保存。
3.AP100(模拟)→模拟演示可—重画(走刀模似)→重画→自动(走刀
模似)可检查夹爪的正确性→退出→OK(即所编程的程序已保存)。
4.数据管理注:删除编程的程序或零件,新建文件夹。
5.板材加工注:具有插入功能。
右击→插入加载→(选择零件或是程序)→找到需插入的图档→打开OK插入完成→NC→创建NC→保存(板材加工与CAM零件加工不可同时打开)。
AMADA数控冲床安全操作规程

SHANGHAI KRUGER VENTILATION CO., LTD.Certificate No. Q16973
版本:A 生效日期:
AMADA数控冲床安全操作规程
1、数控冲床必须有专人操作和维护,操作者必须熟悉机床的结构和性能,严格按照使用说明书和操作规程正确的使用,并严禁超规格使用设备非操作工严禁启动和操作机床。
2、机床周围应保持场地清洁,道路畅通严禁在危险区内堆放产品和其他物品。
3、严禁超负荷冲压,机床核定冲压板厚最大为3毫米,加工时操作工应严格执行此标准,禁止重叠冲切,避免机床超负荷工作。
4、工作前应检查气压数值,达不到规定压力值(0.45-0.55KP)不能开车。
5、使用前应检查各保护装置,主机空车,X?Y进行往复运行,运转正常T轴能正确定位,才能允许正常冲压工作
6、车间应有专人编程,专人核对,程序输入前应检查各控制开关旋钮是否在正确位置。
7、操作箱电脑启动时,不得触碰键盘,以免丢失数据造成程序不可用。
8、加工特大工件时应对机床周围2米以内的危险区进行标示,禁止非操作人员进入危险区。
9、每改变一次程序后,必须进行空车运转,无故障才运行冲活。
10、设备运转时操作人员不准离开机床或干其他工作,更换模具时应关闭电机。
11、严格按润滑部位每班对该机进行润滑保养不进行日保,不准开机。
12、下班后关闭电源,设备各部归位放置原点,整理工作现场及工件。
设备部
生产部
二〇一〇年九月一日。
数控冲床作业指导书
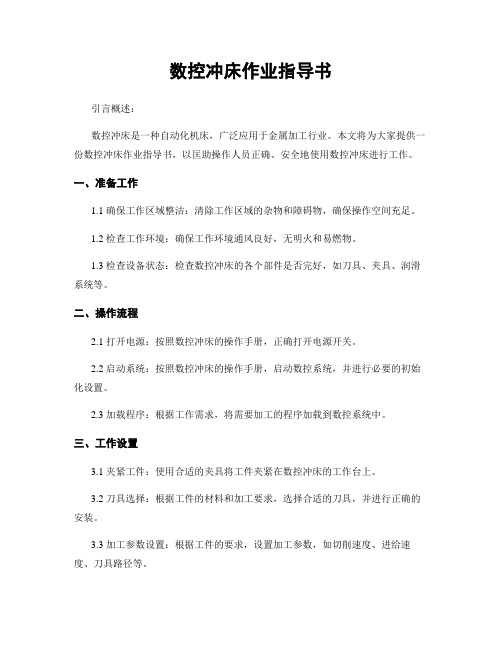
数控冲床作业指导书引言概述:数控冲床是一种自动化机床,广泛应用于金属加工行业。
本文将为大家提供一份数控冲床作业指导书,以匡助操作人员正确、安全地使用数控冲床进行工作。
一、准备工作1.1 确保工作区域整洁:清除工作区域的杂物和障碍物,确保操作空间充足。
1.2 检查工作环境:确保工作环境通风良好,无明火和易燃物。
1.3 检查设备状态:检查数控冲床的各个部件是否完好,如刀具、夹具、润滑系统等。
二、操作流程2.1 打开电源:按照数控冲床的操作手册,正确打开电源开关。
2.2 启动系统:按照数控冲床的操作手册,启动数控系统,并进行必要的初始化设置。
2.3 加载程序:根据工作需求,将需要加工的程序加载到数控系统中。
三、工作设置3.1 夹紧工件:使用合适的夹具将工件夹紧在数控冲床的工作台上。
3.2 刀具选择:根据工件的材料和加工要求,选择合适的刀具,并进行正确的安装。
3.3 加工参数设置:根据工件的要求,设置加工参数,如切削速度、进给速度、刀具路径等。
四、操作步骤4.1 启动加工:按下启动按钮,数控冲床开始进行加工操作。
4.2 监控加工过程:注意观察加工过程中的各个指示灯和数控系统显示屏,确保加工过程正常进行。
4.3 完成加工:加工完成后,及时住手数控冲床,并进行必要的清理工作。
五、安全注意事项5.1 注意个人安全:操作人员必须戴好防护眼镜、手套等个人防护装备,避免意外伤害。
5.2 防止误操作:严禁在加工过程中触摸工件或者刀具,以免发生意外。
5.3 定期维护保养:定期检查数控冲床的各个部件,保持设备的良好状态,减少故障发生的可能性。
结论:本文详细介绍了数控冲床的作业指导,包括准备工作、操作流程、工作设置、操作步骤和安全注意事项。
操作人员应严格按照指导书进行操作,确保工作安全、高效地进行。
同时,定期维护保养数控冲床,延长设备的使用寿命。
AMADA数控冲床操作规程
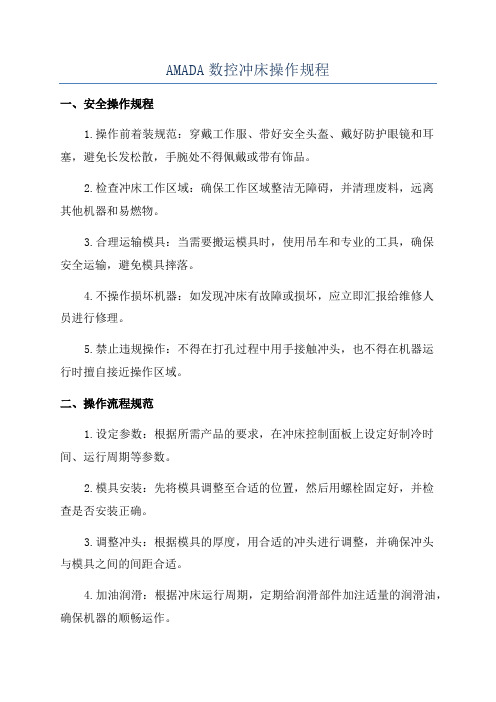
AMADA数控冲床操作规程一、安全操作规程1.操作前着装规范:穿戴工作服、带好安全头盔、戴好防护眼镜和耳塞,避免长发松散,手腕处不得佩戴或带有饰品。
2.检查冲床工作区域:确保工作区域整洁无障碍,并清理废料,远离其他机器和易燃物。
3.合理运输模具:当需要搬运模具时,使用吊车和专业的工具,确保安全运输,避免模具摔落。
4.不操作损坏机器:如发现冲床有故障或损坏,应立即汇报给维修人员进行修理。
5.禁止违规操作:不得在打孔过程中用手接触冲头,也不得在机器运行时擅自接近操作区域。
二、操作流程规范1.设定参数:根据所需产品的要求,在冲床控制面板上设定好制冷时间、运行周期等参数。
2.模具安装:先将模具调整至合适的位置,然后用螺栓固定好,并检查是否安装正确。
3.调整冲头:根据模具的厚度,用合适的冲头进行调整,并确保冲头与模具之间的间距合适。
4.加油润滑:根据冲床运行周期,定期给润滑部件加注适量的润滑油,确保机器的顺畅运作。
5.运行调试:启动冲床,并进行空运行调试,观察是否正常工作。
如发现异常,应立即停机检查排除故障。
6.质量检查:每隔一段时间,应及时检查冲床冲出的零件是否符合质量要求,并及时调整机器参数。
三、故障处理规程1.故障排除步骤:当冲床发生故障时,应立即停机,断开电源,首先观察是否有异样的声音或气味,然后检查机器是否有异物卡住或松动的部件,如有发现应及时处理。
2.维修团队:如故障无法解决,应立即汇报给维修团队进行处理,并配合维修人员的工作。
3.故障记录:发生故障后,需要及时记录故障原因和处理方法,以便今后维护和改进使用。
四、日常维护规程1.清洁保养:定期清理冲床内外的杂物和油污,保持机器的整洁。
2.润滑检查:定期检查冲床上的各润滑点是否处于正常状态,并进行加油维护。
3.零部件更换:根据机器的使用情况,定期检查和更换磨损严重的零部件,保证机器的正常运行。
4.电气检查:定期检查冲床的电气部件,确保线路安全可靠。
数控冲床作业指导书

数控冲床作业指导书概述本作业指导书旨在为操作数控冲床的工作人员提供简明的指导和操作步骤。
请按照以下步骤进行操作,确保安全和高效完成工作。
步骤1. 准备工作:- 检查冲床是否处于正常工作状态,包括电源、控制面板等。
- 检查冲床刀具和模具是否准备就绪,确保其适用于所需的冲孔尺寸和形状。
2. 打开冲床:- 将电源开关打开,使冲床进入待机状态。
- 按照机器设备说明书上的指示进行操作,启动数控系统。
3. 加工准备:- 使用数控系统的控制面板,进入加工准备界面。
- 输入所需加工尺寸和形状等相关参数。
4. 加工操作:- 将待加工的工件放置在冲床工作台上,确保固定牢固。
- 根据加工工艺要求,选择适当的刀具和模具。
- 使用数控系统的控制面板,选择相应的加工程序。
- 根据加工程序的要求,调整切割速度和进给速度等参数。
- 启动加工程序,开始自动加工。
5. 监控加工过程:- 在加工过程中,及时观察加工状态,检查加工质量。
- 注意观察机器运行状态,确保无异常情况出现。
- 如有异常情况或加工质量不合格,立即停止加工并进行必要的调整。
6. 完成加工:- 加工完成后,停止数控系统并关闭电源开关。
- 将加工好的工件从冲床工作台上取下,并进行必要的后续处理。
7. 清洁和维护:- 清理冲床工作台和刀具,确保无残留物。
- 对冲床进行常规的维护和保养,保证设备的正常运行。
注意事项- 在操作冲床时,务必佩戴好个人防护装备,如护目镜、手套等。
- 严禁将手或其他物体靠近冲床刀具和工作台,以免发生意外伤害。
- 在操作数控系统时,要仔细阅读相关的操作手册和安全须知。
- 如遇到无法解决的故障或异常情况,应及时向维修人员报告。
请按照以上指导完成数控冲床的操作,确保安全、高效地完成工作任务。
如有任何疑问或需要进一步的帮助,请及时寻求相关人员的指导和支持。
AMADA数控冲床操作规程
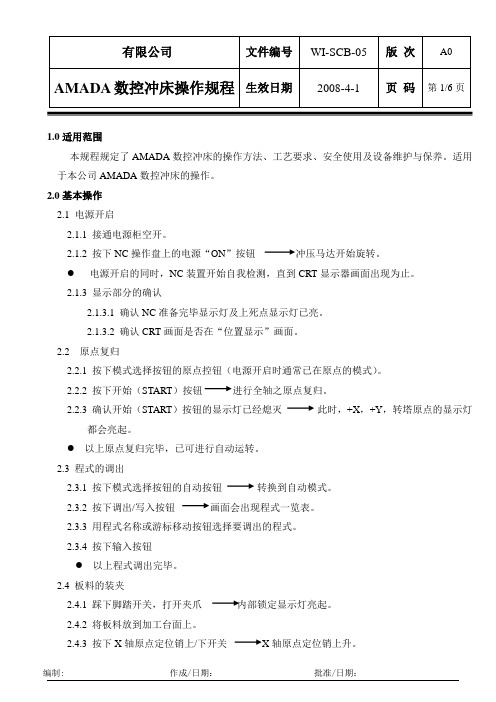
1.0适用范围本规程规定了AMADA数控冲床的操作方法、工艺要求、安全使用及设备维护与保养。
适用于本公司AMADA数控冲床的操作。
2.0基本操作2.1 电源开启2.1.1 接通电源柜空开。
2.1.2 按下NC操作盘上的电源“ON”按钮冲压马达开始旋转。
●电源开启的同时,NC装置开始自我检测,直到CRT显示器画面出现为止。
2.1.3 显示部分的确认2.1.3.1 确认NC准备完毕显示灯及上死点显示灯已亮。
2.1.3.2 确认CRT画面是否在“位置显示”画面。
2.2 原点复归2.2.1 按下模式选择按钮的原点控钮(电源开启时通常已在原点的模式)。
2.2.2 按下开始(START)按钮进行全轴之原点复归。
2.2.3 确认开始(START)按钮的显示灯已经熄灭此时,+X,+Y,转塔原点的显示灯都会亮起。
●以上原点复归完毕,已可进行自动运转。
2.3 程式的调出2.3.1 按下模式选择按钮的自动按钮转换到自动模式。
2.3.2 按下调出/写入按钮画面会出现程式一览表。
2.3.3 用程式名称或游标移动按钮选择要调出的程式。
2.3.4 按下输入按钮●以上程式调出完毕。
2.4 板料的装夹2.4.1 踩下脚踏开关,打开夹爪内部锁定显示灯亮起。
2.4.2 将板料放到加工台面上。
2.4.3 按下X轴原点定位销上/下开关X轴原点定位销上升。
编制: 作成/日期:批准/日期:2.4.4 把板料靠到夹爪和X轴定位销上来做定位。
2.4.5 踩下脚踏开关,开闭夹爪,固定材料。
2.4.6 再按一次X轴原点定位销上/下开关X轴原点定位销下降到加工台面以下,内部锁定显示灯熄灭。
2.5 自动运转开始2.5.1各显示灯的亮灯,熄灯状态,请做如下的确认。
2.5.1.1 亮灯:NC准备完毕,上死点,模具脱跳2.5.1.2 熄灯:内部锁定,警告,NC警示,紧急停止2.5.2 确认CRT画面2.5.2.1 确认是否显示出所要执行程式的加工资料。
2.5.2.2 要确认程式内容时,可按下软体键中的“列示”(LIST)。
AP100软件AMADA数控冲床M代码运用

3. 上模 长 度〔 0.0 0 ~ 267 .0 0 ㎜ 〕 上模 全 长 。设定 冲 模 头 开 始 到 尖 输入 上 模 全 长 的 测 定 值 。 端冲 头 为 止 的 长 度 (㎜ )。
4. 下模 高 〔 0.0 0 ~ 99. 00 ㎜〕 下模 高 。 设 定 模 高 (㎜ ) 。
输入 下 模 高 测 定 值 。
“ M69 6 ”:冲 切 模 式 ( N E X 模 具 用 ) 上 模 尖 端 与 导 轨 尖 端 一 致 时 使 用 的 M 编码 。 为了 高 速 连 续 进 行 冲 切 运 行 , 冲 切 没 有 速 度 的 切 换 。
置)。
“ M12 ”:步 冲 模 式 为了 高 速 连 续 进 行 冲 切 操 作 , 冲 切 没 有 速 度 的 切 换 ( 减 速 位
1
1
㎜
C:切 入 量
2. 5
5
㎜
材料 的 板 厚 由 程 序 的 “ G06 ” 指令 来 设 定 。(参 照 编 程 手 册 )。
范围
3.0 0 ~ 99. 00 0.0 0 ~ 99. 00 0.0 0 ~ 99. 00
备注
● 根据 计 算 的 冲 击 力 度 , 按 高 速 /中速 /低速 切 换 剪 切 速 度 。
模具 信 息
在转 塔 模 具 台 上 输 入 冲 切 尺 寸 、 形 状 ( 上 模 高 度 、 ASS Y 高度 、 切 面 周 长 、 剪 切 角 ) 的 参 数 后, 即 可 按 适 合 此 尺 寸 的 冲 切 速 度 进 行 加 工 , 简 化 冲 切 模 式 指 令 的 编 程 操 作 。 此外 , 可 以 补 正 经 过 再 研 磨 的 冲 切 位 置 。
AMADA数控冲床操作规程
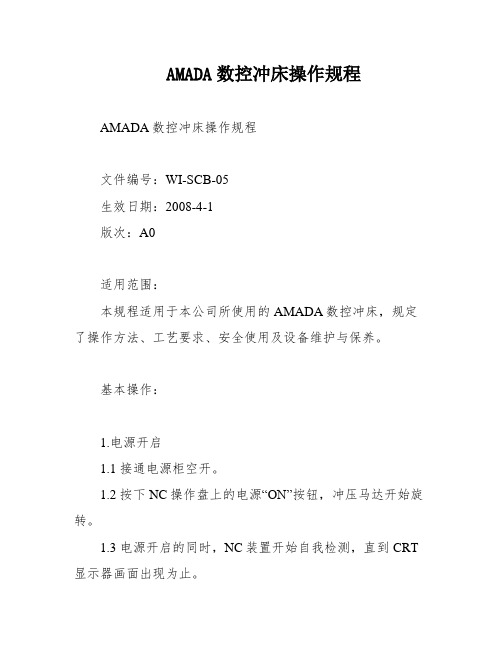
AMADA数控冲床操作规程AMADA数控冲床操作规程文件编号:WI-SCB-05生效日期:2008-4-1版次:A0适用范围:本规程适用于本公司所使用的AMADA数控冲床,规定了操作方法、工艺要求、安全使用及设备维护与保养。
基本操作:1.电源开启1.1 接通电源柜空开。
1.2 按下NC操作盘上的电源“ON”按钮,冲压马达开始旋转。
1.3 电源开启的同时,NC装置开始自我检测,直到CRT 显示器画面出现为止。
1.4 确认NC准备完毕显示灯及上死点显示灯已亮。
1.5 确认CRT画面是否在“位置显示”画面。
2.原点复归2.1 按下模式选择按钮的原点控钮(电源开启时通常已在原点的模式)。
2.2 按下开始(START)按钮进行全轴之原点复归。
2.3 确认开始(START)按钮的显示灯已经熄灭。
此时,+X,+Y,转塔原点的显示灯都会亮起。
3.程式的调出3.1 按下模式选择按钮的自动按钮,转换到自动模式。
3.2 按下调出/写入按钮,画面会出现程式一览表。
3.3 用程式名称或游标移动按钮选择要调出的程式。
3.4 按下输入按钮。
4.板料的装夹4.1 踩下脚踏开关,打开夹爪内部锁定显示灯亮起。
4.2 将板料放到加工台面上。
4.3 按下X轴原点定位销上/下开关,X轴原点定位销上升。
4.4 把板料靠到夹爪和X轴定位销上来做定位。
4.5 踩下脚踏开关,开闭夹爪,固定材料。
4.6 再按一次X轴原点定位销上/下开关,X轴原点定位销下降到加工台面以下,内部锁定显示灯熄灭。
5.自动运转开始5.1 确认各显示灯的亮灯、熄灯状态。
5.2 确认CRT画面是否显示出所要执行程式的加工资料。
5.3 依需要设定各种按钮。
4.3 屏幕操作(仅限主操作人员)4.3.1 操作人员必须按规定操作,不能随意按按钮,以免造成设备或人身事故。
4.3.2 在“EDIT”编辑状态下,不得随意修改参数,只能按规定修正“NC SETUP”下方四行黄字中的前运行参数,并记录修改前后的情况。
AMADA数控冲床指令介绍

以下适合AMADA数控冲床参考NCT指令介绍NCT程序是由基本指令以一定的格式组成的数码信息文件.程序写作固定格式,NCT程序的一行(一个BLOCK)如下所示:N___ G___ G___ X___Y___ T___ C___ M其中针对单个命令不要的指令不必记入.现对NCT程序中常见的指令的基本格式及基应用介绍如下.1. G92 坐标设定(原点设定)格式G92 X___ Y___材料自原点到冲头位置的距离,记忆于NC装置内,原点依据NCT机种不同而有差异.现场使用的机床是VIP357,其原点坐标为X 1830,Y1270.2. G90 绝对坐标指令格式G90 X___ Y___G90绝对坐标指令使用时,必须在坐标值前记上G90.在绝对坐标指令读取时,若开头记入G90,则以后的BLOCK,直到G91之前可省略不写.程序上若无G90或G91时,一律视为与G90相同.3. G91 相对坐标指令G91指令指定的坐标不是从原点算起,而是自前一个孔位算起的增加值,使用此指令时必须在坐标值前记入G91.相对坐标指令读取时,最初以G91记入,以后的BLOCK一直到G90出现之前,G91均可省略不写.4. G50 回归原点指令使用G50指令,材料依G92指定的位置回归的同时,回复到NC初期状态,程序最后必须作G50单一行之输入.5. G70 不冲孔指令格式G70 X___ Y___材料仅位移,不冲孔.G70与G90或G91可以同时使用,且位置先后不影响其指定.G70的指令只在所属BLOCK内有效.例:G90 X100.00 Y100.00 (有冲孔)G70 G91 X200.00 (无冲孔)G90 Y300.00 (有冲孔)6. G27?G25 自动移爪格式G27(或G25) X___(移动量)G27?G25指令是用来换板及加工范围不够宽时所使用的换板功能.通常使用G27,当材料在夹爪夹住的边上有突出不平等的情形时,则使用G25.7. G04 暂停(滞留状态)格式G04 X___ (时间)在轴移动时,作预定时间内暂停的机能.AMADA(315990100) 13:02:16G66后面的X和Y代表什么?心灵鸡汤(361781127) 13:02:308. G72 模式基准点指令格式G72 X___ Y___欲使用模式基准点时,坐标值之前要加上G72.l G72与G90或G91同时使用,且那一个先写都相同l G72仅有指示坐标的作用,而无决定位置或实行冲孔的动作.l G72的下一行必需是实行冲孔的指令.l 与G72在同一行内不可存在M?T等功能的指令.9. T指令定义刀具T为三位数字所组成,用来指令所使用模具的STATION,位于X?Y的位置之后.若为相同之模具继续使用时,一直到另一模具使用前,不须再另行指定模具.10. C指令设置刀具角度C指令位于X?Y(位置)与T(使用模具)之指令之后.自动转角可于±360°的范围内指定,同角度的加工时,C指令为必重复指定.11. G26 BLOT HOLE CIRCLE (BHC)以现在的位置或G72指定的位置为中心,在半径为r的圆周上,与X轴夹θ角的点开始,将圆周分成n等分,作n个点的冲孔指令.格式G26 I r J±θK n T___ (C___ )I=圆的半径r.输入正值J=冲孔起始点与X轴之夹±θ.反时针方向为正(+),顺时针方向为负(-)K=冲孔个数,反时针方向加工为正(+),顺时针方向为负(-)12. G28 LINE AT ANGLE (LAA)以现在的位置或G72指令的位置算起,与X轴夹θ角的方向,间隔d的距离,冲n个孔的指令.格式G28 I d J±θK n T___ (C___ )I=间隔±d.d为负时,以模式基准点作为中心,于对称方向冲孔J=角度±θ,反时针方向为正(+),顺时针方向为负(-)K=冲孔个数n.不包括模式基准点13. G29 圆弧(ARC)以现在的位置或G72所指定的基准点为中心,半径为r的圆周上,与X轴夹角为θ的开始点,角度间隔Δθ,排列n个点的冲孔指令.格式G28 I r J±θP±ΔθK n T___ (C___ )I=圆的半径r,为正数J=最初冲孔起始点,角度±θ,反时针方向为正(+),顺时针方向为负(-)P=角度间隔为±Δθ,为正时,以反时针方向冲孔,为负时,以顺时针方向冲孔K=冲孔的个数14. G36?G37 格状孔此模式从G72指定的位置开始,X轴方向以d1为间隔.做n个,Y轴方向以d2为间隔,做n2个格子状冲孔的指令.G36是以X轴方向为优先加工指令,G37是以Y轴方向为优先加工指令,考虑到板料在运动中的稳定性,一般选用G36.格式G36 I±d1 P n1 J±d2 K n2 T___ (C___ )G36 I±d1 P n1 J±d2 K n2 T___ (C___ )I=间隔±d1,正(+)时为X轴方向,负(-)时为-X方向取间隔P=X轴方向的冲孔数n1(不含基准点)J=间隔±d2,正(+)时为Y轴方向,负(-)时为-Y方向取间隔K=Y轴方向的冲孔数n2(不含基准点)15. G66 切边(SHP)此模式是由G72所指定之基准点开始,在与X轴夹角为θ°的方向上,以W1×W2之模具,作长度为±d的连续冲孔指令.格式G66 I e J±θP±W1 Q±W2 D±d T___I=连续冲孔加工之长度eJ=角度±θ.反时针为(+)时针为(-)P=模具边长±W1(J方向的模具尺寸)Q=模具边±W2(与J成90°方向的模具尺寸)W1与W2必需同号,若W1=W2时Q可省略不写.D=对加工长度作补正之值±d(d=0时,D项可省略)l D若为负时连续冲也的长度比I短少2倍D的长,为正时则比I长2 倍D.l 连续冲孔的长度I,至少需为P(W1)之1.5倍以上方可.16. G67 矩形(SQR)此模式是由G72所指定的基准点开始,平行X轴方向长度e1,Y轴方向长e2的矩形,以长W1W2的模具连续冲孔的指令.格式G67 I±e1 J±e2 P W1 Q W2 T___I=X轴方向冲孔长度±e1.正为X方向.负为X轴负方向J=Y轴方向冲孔长度±e1.正为Y方向.负为Y轴负方向P=X方向模具长度W1,为正值Q=Y方向模具长度W2,为正值.若W1=W2时,Q可省略因通常使用正方形模,帮Q不使用.17. G68 蚕食圆弧(NBL-A)此模式是以G72所指定的基准点为中心,半径为r的圆周上,与X轴夹角为θ1的点开始,增加θ2的角度,以直径为ψ的模具,间隔为d来作蚕食加工之指令.格式G68 I r J±θ1 K±θ2 P±ψQ d T___I=圆的半径r,输入正值(但I<5700mm)J=加工起始点自X轴算起之角度±θ1,反时针方向为正,顺时针方向为负K=蚕食加工的角度±θ2,(+)时为逆时针加工,(-)时为顺时针加工P=模具直径±ψ,正时在圆的外侧加工,负时在圆的内侧加工Q=蚕食的间隔为d,输入正数(最大d值为8mm)l 板厚3.2mm以上场合,或是间隔超过8mm时,以G78代替G68使用之.l 蚕食所使用之模具,必须小于所蚕食之圆的半径.18. G69 I e J±θ P±ψ Q d T___此模式是从G72指定的基准点开始,与X轴成θ角方向,长度e,以直径ψ模具,间隔d来蚕食的加工模式.格式G69 I e J±θP±ψQ d T___I=蚕食执行的长度,为模式起点至模式终点的长度J=角度±θ,反时针为正,顺时针为负P=模具直径±ψ,正时加工方向在直线之左侧,负时加工于直线右侧Q=蚕食间隔d,正值输入,最大值为8mm19. G78 冲孔圆弧(PNC-A)此模式是以G72所指定之基准点为中心,半径为r的圆周上,与X轴夹角为θ1的点开始,增加θ2之角度,以直径ψ的模具,间隔为d来作蚕食加工之指令.格式G78 I r J±θ1 K±θ2 P±ψQ d D t T___I=圆的半径r.输入正值J=加工起始点自X轴算起之角度±θ1.反时针方向为正,顺时针方向为负K=蚕食加工的角度±θ2.(+)时逆时针加工,(-)时顺时针加工P=模具直径±ψ.(+)时在圆的外侧加工,(-)时在圆的内侧加工Q=蚕食的间隔为dD=使用板厚t,(d≧t)20. G79 冲孔长圆(PNC-L)此模式是从G72指令的基准点开始,与X轴成θ1角方向,长度e,直径ψ的模具,间隔d来蚕食的加工模式.格式G79 I e J±θ1 P±ψQ d D t T____I=蚕食执行的长度,为模式起点至模式终点的长度J=角度±θ1,反时针为正,顺时针为负P=模具直径±ψ.正时加工方向在直线之左侧,负时加工于直线右侧Q=蚕食间隔dD=使用板厚t.(d≧t)21. G98 多数取的基准点与排列间隔之设定多数取加工时,制品对于材料作何种排列的指令格式G98 Xx0 Yy0 Ixp Jyp Pnx Knyx0……排列在左下方制品的左下角点的X坐标y0……排列在左下方制品的左下角点的Y坐标xp……X方向上制品排列的间隔yp……Y方向上制品排列的间隔nx……X方向上排列的间隔数ny……Y方向上排列的间隔数22. G7576 多数取执行指令除多数取程序外,UOO~VOO为止,为一个制品的子程序,此编号的MACRO对应WOO,根据G98所设定之排列,令材料全部执行的指令.格式G75 W___ Q___ ……以X方向为优先级执行G76 W___ Q ___……以Y方向为优先级执行W=为MACRO编号,与程序中的UOO~VOO对应Q=为加工开始的角落.Q1—左下角;Q2—右下角;Q3—左上角;Q4—右上角23. MACRO机能(U)MACRO记忆机能,UOO与VOO为程序中数个BLOCK之记忆OO则为不限次数之记忆呼出时使用,这时U所对应读取之数值,需为相同格式UOO...VOOWOO注:一个U…V对应一个W.U~V之间不可有M02M03及50之指令存在.24. M13 加工结束指令加工结束之后单一行输入25. M510~M559 冲凸台形强筋前之指令.在冲凸台形强筋前单一行输入.指令可在M510~M559中任选一个,但在同一程序中,不同模具前不能用同一M指令.26. M560~M563 打标记沙拉孔前之指令在打标记沙拉孔前单一行输入,可在M560~M505中任选一个,但在同一程序中,不同的模具前不能使用同一M指令.27. M502~M505 冲敲落孔前之指令在冲敲落孔前单一行输入,可在M502~M505中任选一个,但在同一程序中不同模具前不能使用同一M指令.注:在实际运用中,为配合NCT现场的操作,使NCT程序转换与NCT现场对M指令的添加达到共识,对常用的特殊刀具指定了固定的M指令,具体运用参考第三章.风轻云淡05.29 17:1815. G66 切边(SHP)此模式是由G72所指定之基准点开始,在与X轴夹角为θ°的方向上,以W1×W2之模具,作长度为±d的连续冲孔指令.格式G66 I e J±θP±W1 Q±W2 D±d T___I=连续冲孔加工之长度eJ=角度±θ.反时针为(+)时针为(-)P=模具边长±W1(J方向的模具尺寸)Q=模具边±W2(与J成90°方向的模具尺寸)W1与W2必需同号,若W1=W2时Q可省略不写.D=对加工长度作补正之值±d(d=0时,D项可省略)l D若为负时连续冲也的长度比I短少2倍D的长,为正时则比I长2 倍D.l 连续冲孔的长度I,至少需为P(W1)之1.5倍以上方可.16. G67 矩形(SQR)此模式是由G72所指定的基准点开始,平行X轴方向长度e1,Y轴方向长e2的矩形,以长W1W2的模具连续冲孔的指令.格式G67 I±e1 J±e2 P W1 Q W2 T___I=X轴方向冲孔长度±e1.正为X方向.负为X轴负方向J=Y轴方向冲孔长度±e1.正为Y方向.负为Y轴负方向P=X方向模具长度W1,为正值Q=Y方向模具长度W2,为正值.若W1=W2时,Q可省略因通常使用正方形模,帮Q不使用.17. G68 蚕食圆弧(NBL-A)此模式是以G72所指定的基准点为中心,半径为r的圆周上,与X轴夹角为θ1的点开始,增加θ2的角度,以直径为ψ的模具,间隔为d来作蚕食加工之指令.格式G68 I r J±θ1 K±θ2 P±ψQ d T___I=圆的半径r,输入正值(但I<5700mm)J=加工起始点自X轴算起之角度±θ1,反时针方向为正,顺时针方向为负K=蚕食加工的角度±θ2,(+)时为逆时针加工,(-)时为顺时针加工P=模具直径±ψ,正时在圆的外侧加工,负时在圆的内侧加工Q=蚕食的间隔为d,输入正数(最大d值为8mm)l 板厚3.2mm以上场合,或是间隔超过8mm时,以G78代替G68使用之.l 蚕食所使用之模具,必须小于所蚕食之圆的半径.18. G69 I e J±θ P±ψ Q d T___此模式是从G72指定的基准点开始,与X轴成θ角方向,长度e,以直径ψ模具,间隔d来蚕食的加工模式.格式G69 I e J±θP±ψQ d T___I=蚕食执行的长度,为模式起点至模式终点的长度J=角度±θ,反时针为正,顺时针为负P=模具直径±ψ,正时加工方向在直线之左侧,负时加工于直线右侧Q=蚕食间隔d,正值输入,最大值为8mm19. G78 冲孔圆弧(PNC-A)此模式是以G72所指定之基准点为中心,半径为r的圆周上,与X轴夹角为θ1的点开始,增加θ2之角度,以直径ψ的模具,间隔为d来作蚕食加工之指令.格式G78 I r J±θ1 K±θ2 P±ψQ d D t T___I=圆的半径r.输入正值J=加工起始点自X轴算起之角度±θ1.反时针方向为正,顺时针方向为负K=蚕食加工的角度±θ2.(+)时逆时针加工,(-)时顺时针加工P=模具直径±ψ.(+)时在圆的外侧加工,(-)时在圆的内侧加工Q=蚕食的间隔为dD=使用板厚t,(d≧t)20. G79 冲孔长圆(PNC-L)此模式是从G72指令的基准点开始,与X轴成θ1角方向,长度e,直径ψ的模具,间隔d来蚕食的加工模式.格式G79 I e J±θ1 P±ψQ d D t T____I=蚕食执行的长度,为模式起点至模式终点的长度J=角度±θ1,反时针为正,顺时针为负P=模具直径±ψ.正时加工方向在直线之左侧,负时加工于直线右侧Q=蚕食间隔dD=使用板厚t.(d≧t)21. G98 多数取的基准点与排列间隔之设定多数取加工时,制品对于材料作何种排列的指令格式G98 Xx0 Yy0 Ixp Jyp Pnx Knyx0……排列在左下方制品的左下角点的X坐标y0……排列在左下方制品的左下角点的Y坐标xp……X方向上制品排列的间隔yp……Y方向上制品排列的间隔nx……X方向上排列的间隔数ny……Y方向上排列的间隔数22. G7576 多数取执行指令除多数取程序外,UOO~VOO为止,为一个制品的子程序,此编号的MACRO对应WOO,根据G98所设定之排列,令材料全部执行的指令.格式G75 W___ Q___ ……以X方向为优先级执行G76 W___ Q ___……以Y方向为优先级执行W=为MACRO编号,与程序中的UOO~VOO对应Q=为加工开始的角落.Q1—左下角;Q2—右下角;Q3—左上角;Q4—右上角23. MACRO机能(U)MACRO记忆机能,UOO与VOO为程序中数个BLOCK之记忆OO则为不限次数之记忆呼出时使用,这时U所对应读取之数值,需为相同格式UOO...VOOWOO注:一个U…V对应一个W.U~V之间不可有M02M03及50之指令存在.24. M13 加工结束指令加工结束之后单一行输入25. M510~M559 冲凸台形强筋前之指令.在冲凸台形强筋前单一行输入.指令可在M510~M559中任选一个,但在同一程序中,不同模具前不能用同一M指令.26. M560~M563 打标记沙拉孔前之指令在打标记沙拉孔前单一行输入,可在M560~M505中任选一个,但在同一程序中,不同的模具前不能使用同一M指令.27. M502~M505 冲敲落孔前之指令在冲敲落孔前单一行输入,可在M502~M505中任选一个,但在同一程序中不同模。
amada数控冲床操作规程

amada数控冲床操作规程操作规程是指操作者在使用工作设备时应遵循的一系列规定。
Amada数控冲床操作规程1. 安全注意事项1.1 操作前,必须带好工作牌,在设备周围设置明显的安全标识,确保没有无关人员进入操作区域。
1.2 检查冲床的安全保护装置,确保正常工作并能保护操作者的安全。
1.3 在操作前,应检查冲床的主要运动部件是否润滑良好,并且无异常声响。
1.4 在操作过程中,应避免穿着松散的衣物和饰品,并且戴好安全帽、手套和护目镜。
1.5 在操作开始前,操作者必须熟悉和理解冲床的操作原理和紧急停机装置的使用方法。
2. 开机操作流程2.1 启动冲床前,确认主电源开关处于关闭状态,确保所有紧急停机装置已复位。
2.2 按下主电源开关,然后按下机床电源开关,启动电机。
2.3 确认控制面板上各项指示灯正常亮起。
2.4 按下机床准备按钮,检查床台和模具的位置是否正确。
2.5 按下手动运动按钮,逐步移动床台到所需位置,并检查各轴的运动是否正常。
3. 加工操作流程3.1 在机床准备完毕后,将工件固定在床台上,并根据加工图纸上的要求调整模具。
3.2 设定好加工参数,包括工作速度、冲压深度和停顿时间等。
3.3 在控制面板上输入加工程序,并进行程序编辑。
3.4 在程序编辑完毕后,进行程序的检查和校正。
3.5 将模具保护装置关闭,并按下开始按钮,开始自动加工。
3.6 在加工过程中,及时观察加工情况,确保工件加工质量符合要求。
3.7 如果发现加工中出现异常情况或问题,应立即按下紧急停机按钮,停止机床的运行。
4. 关机操作流程4.1 在加工结束后,按下暂停按钮,让床台停在安全位置。
4.2 关闭冲床电机,然后按下冷却系统的停止按钮。
4.3 将机床电源开关和主电源开关关闭。
4.4 清理加工现场,将冲床周围的杂物和废料清理干净。
4.5 对冲床进行定期保养和维护,确保设备的正常运行和寿命。
5. 操作注意事项5.1 在操作过程中,严禁将手、头或其他身体部位靠近冲床的运动部件,以免造成伤害。
amada数控冲床面板及操作指导
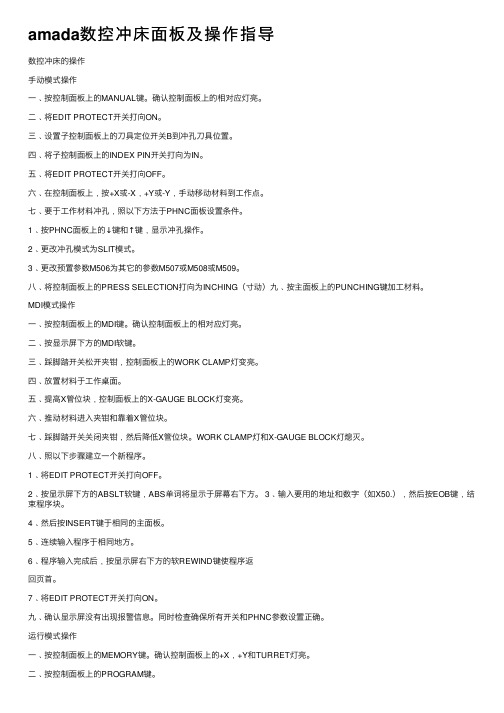
amada数控冲床⾯板及操作指导数控冲床的操作⼿动模式操作⼀﹑按控制⾯板上的MANUAL键。
确认控制⾯板上的相对应灯亮。
⼆﹑将EDIT PROTECT开关打向ON。
三﹑设置⼦控制⾯板上的⼑具定位开关B到冲孔⼑具位置。
四﹑将⼦控制⾯板上的INDEX PIN开关打向为IN。
五﹑将EDIT PROTECT开关打向OFF。
六﹑在控制⾯板上﹐按+X或-X﹐+Y或-Y﹐⼿动移动材料到⼯作点。
七﹑要于⼯作材料冲孔﹐照以下⽅法于PHNC⾯板设置条件。
1﹑按PHNC⾯板上的↓键和↑键﹐显⽰冲孔操作。
2﹑更改冲孔模式为SLIT模式。
3﹑更改预置参数M506为其它的参数M507或M508或M509。
⼋﹑将控制⾯板上的PRESS SELECTION打向为INCHING(⼨动)九﹑按主⾯板上的PUNCHING键加⼯材料。
MDI模式操作⼀﹑按控制⾯板上的MDI键。
确认控制⾯板上的相对应灯亮。
⼆﹑按显⽰屏下⽅的MDI软键。
三﹑踩脚踏开关松开夹钳﹐控制⾯板上的WORK CLAMP灯变亮。
四﹑放置材料于⼯作桌⾯。
五﹑提⾼X管位块﹐控制⾯板上的X-GAUGE BLOCK灯变亮。
六﹑推动材料进⼊夹钳和靠着X管位块。
七﹑踩脚踏开关关闭夹钳﹐然后降低X管位块。
WORK CLAMP灯和X-GAUGE BLOCK灯熄灭。
⼋﹑照以下步骤建⽴⼀个新程序。
1﹑将EDIT PROTECT开关打向OFF。
2﹑按显⽰屏下⽅的ABSLT软键﹐ABS单词将显⽰于屏幕右下⽅。
3﹑输⼊要⽤的地址和数字(如X50.)﹐然后按EOB键﹐结束程序块。
4﹑然后按INSERT键于相同的主⾯板。
5﹑连续输⼊程序于相同地⽅。
6﹑程序输⼊完成后﹐按显⽰屏右下⽅的软REWIND键使程序返回页⾸。
7﹑将EDIT PROTECT开关打向ON。
九﹑确认显⽰屏没有出现报警信息。
同时检查确保所有开关和PHNC参数设置正确。
运⾏模式操作⼀﹑按控制⾯板上的MEMORY键。
确认控制⾯板上的+X﹐+Y和TURRET灯亮。
AMADA 数控冲床操作规程

1.0适用范围`本规程规定了AMADA数控冲床的操作方法、工艺要求、安全使用及设备维护与保养。
适用于本公司AMADA数控冲床的操作。
2.0基本操作2.1 电源开启2.1.1 接通电源柜空开。
2.1.2 按下NC操作盘上的电源“ON”按钮冲压马达开始旋转。
●电源开启的同时,NC装置开始自我检测,直到CRT显示器画面出现为止。
2.1.3 显示部分的确认2.1.3.1 确认NC准备完毕显示灯及上死点显示灯已亮。
2.1.3.2 确认CRT画面是否在“位置显示”画面。
2.2 原点复归2.2.1 按下模式选择按钮的原点控钮(电源开启时通常已在原点的模式)。
2.2.2 按下开始(START)按钮进行全轴之原点复归。
2.2.3 确认开始(START)按钮的显示灯已经熄灭此时,+X,+Y,转塔原点的显示灯都会亮起。
●以上原点复归完毕,已可进行自动运转。
2.3 程式的调出2.3.1 按下模式选择按钮的自动按钮转换到自动模式。
2.3.2 按下调出/写入按钮画面会出现程式一览表。
2.3.3 用程式名称或游标移动按钮选择要调出的程式。
2.3.4 按下输入按钮●以上程式调出完毕。
2.4 板料的装夹2.4.1 踩下脚踏开关,打开夹爪内部锁定显示灯亮起。
2.4.2 将板料放到加工台面上。
2.4.3 按下X轴原点定位销上/下开关X轴原点定位销上升。
2.4.4 把板料靠到夹爪和X轴定位销上来做定位。
2.4.5 踩下脚踏开关,开闭夹爪,固定材料。
2.4.6 再按一次X轴原点定位销上/下开关X轴原点定位销下降到加工台面以下,内部锁定显示灯熄灭。
2.5 自动运转开始2.5.1各显示灯的亮灯,熄灯状态,请做如下的确认。
2.5.1.1 亮灯:NC准备完毕,上死点,模具脱跳2.5.1.2 熄灯:内部锁定,警告,NC警示,紧急停止2.5.2 确认CRT画面2.5.2.1 确认是否显示出所要执行程式的加工资料。
2.5.2.2 要确认程式内容时,可按下软体键中的“列示”(LIST)。
数控冲床操作指导书

数控冲床操作指导书1000字数控冲床是一种高精度、高自动化的机床,广泛应用于制造业。
为了使数控冲床能够正常运行,需要对其进行正确的操作和维护。
本文将对数控冲床的操作进行指导,以确保操作者的安全和机床的正常运行。
一、操作前的准备:1. 确定所要加工的零件和加工工艺;2. 检查工装夹紧状态是否正确,夹具上的工件是否固定可靠;3. 检查刀具,刀具是否固定牢固;4. 保证冲床的润滑系统和供气系统运转正常,保持机床的清洁。
二、操作步骤:1. 打开电源,将系统开关设为“ON”,然后按下“复位”键,待机床回到初始状态后按下“自动”键;2. 输入加工程序,包括工件尺寸、材料、加工速度、冲头型号等参数;3. 按下“启动”键,机床按加工程序进行操作,同时进行自动检测和报警监视;4. 冲床加工中,要严格按照程序要求进行操作,不得随意中途停机或更改程序;5. 当加工结束后,按下“停止”键,关闭电源。
三、安全操作:1. 在操作前,要了解机床的相关安全规定和操作程序;2. 在加工过程中,操作者要保持清醒,注意保护好双手和身体,避免发生伤害事故;3. 加工过程中,如有异常声音或异味,要及时停止机床,检查并排除故障。
四、保养维护:1. 经常清洗机床表面和工作平台,保持干净;2. 定期检查液压油、润滑油等油品的状态和量,及时进行添加或更换;3. 定期检查加工程序和冲头的使用状况,及时更换或修复;4. 定期检查机床基础、联轴器、传动结构等部件的紧固度和使用状况,及时进行调整和维修。
总之,正确的操作和维护可以有效地提高数控冲床的加工效率和精度,减少故障发生,保证操作者的安全。
在操作过程中,需要严格遵守机床的相关安全规定,保持操作者的警惕性,及时发现并解决故障。
AMADA数控冲床指令介绍

AMADA数控冲床指令介绍1.程序格式:AMADA数控冲床的程序由多个指令组成,每个指令占据一行。
程序的格式要求严格,每行指令都必须以字母N开头,后面紧跟一个整数作为指令号。
指令号用于标识和排序指令,方便机床进行程序的读取和执行。
2.运动指令:AMADA数控冲床提供了多种运动指令,用于控制机床在加工过程中的运动方式。
常见的运动指令包括直线插补(G01)、圆弧插补(G02和G03)、快速定位(G00)等。
这些指令可以通过设定坐标轴的位置、速度和加速度等参数来实现机床的精确定位和移动。
3.辅助功能指令:除了运动指令,AMADA数控冲床还提供了一系列辅助功能指令,用于控制机床在加工过程中的其他操作。
这些指令包括刀具补偿(G41和G42)、刀具半径补偿(G40)、暂停(M00和M01)、循环(M08和M09)等。
这些指令可以根据具体的加工要求来控制机床的工作方式和生产效率。
4.变量和参数:AMADA数控冲床的指令中可以使用变量和参数,用于存储和传递数据。
变量可以在程序中定义,并在程序的不同位置进行读取和修改。
参数可以在运动指令中使用,用于设定机床在加工过程中的参数,例如速度、加速度、旋转半径等。
通过合理使用变量和参数,可以实现程序的灵活性和可复用性。
5.流程控制指令:为了实现更加复杂的加工任务,AMADA数控冲床还提供了一些流程控制指令,用于实现程序的条件执行和循环控制。
常用的流程控制指令包括条件判断(IF和ELSEIF)、循环(FOR和WHILE)、跳转(GOTO)等。
这些指令可以根据程序中的条件来决定下一步的操作,实现程序的灵活性和逻辑性。
总之,AMADA数控冲床的指令是通过编程来控制机床运动和加工过程的指令。
这些指令通过特定的格式和语法来书写,包括程序格式、运动指令、辅助功能指令、变量和参数、流程控制指令等。
合理使用这些指令,可以实现机床的高效加工和精度控制,提高生产效率和产品质量。
AMADA数控冲床操作规程

1.0适用范围`本规程规定了AMADA数控冲床的操作方法、工艺要求、安全使用及设备维护与保养。
适用于本公司AMADA数控冲床的操作。
2.0基本操作2.1 电源开启2.1.1 接通电源柜空开。
2.1.2 按下NC操作盘上的电源“ON”按钮冲压马达开始旋转。
● 电源开启的同时,NC装置开始自我检测,直到CRT显示器画面出现为止。
2.1.3 显示部分的确认2.1.3.1 确认NC准备完毕显示灯及上死点显示灯已亮。
2.1.3.2 确认CRT画面是否在“位置显示”画面。
2.2 原点复归2.2.1 按下模式选择按钮的原点控钮(电源开启时通常已在原点的模式)。
2.2.2 按下开始(START)按钮进行全轴之原点复归。
2.2.3 确认开始(START)按钮的显示灯已经熄灭此时,+X,+Y,转塔原点的显示灯都会亮起。
● 以上原点复归完毕,已可进行自动运转。
2.3 程式的调出2.3.1 按下模式选择按钮的自动按钮转换到自动模式。
2.3.2 按下调出/写入按钮画面会出现程式一览表。
2.3.3 用程式名称或游标移动按钮选择要调出的程式。
2.3.4 按下输入按钮● 以上程式调出完毕。
2.4 板料的装夹2.4.1 踩下脚踏开关,打开夹爪内部锁定显示灯亮起。
2.4.2 将板料放到加工台面上。
2.4.3 按下X轴原点定位销上/下开关 X轴原点定位销上升。
2.4.4 把板料靠到夹爪和X轴定位销上来做定位。
2.4.5 踩下脚踏开关,开闭夹爪,固定材料。
2.4.6 再按一次X轴原点定位销上/下开关 X轴原点定位销下降到加工台面以下,内部锁定显示灯熄灭。
2.5 自动运转开始2.5.1各显示灯的亮灯,熄灯状态,请做如下的确认。
2.5.1.1 亮灯:NC准备完毕,上死点,模具脱跳2.5.1.2 熄灯:内部锁定,警告,NC警示,紧急停止2.5.2 确认CRT画面2.5.2.1 确认是否显示出所要执行程式的加工资料。
2.5.2.2 要确认程式内容时,可按下软体键中的“列示”(LIST)。
数控冲床作业指导书

数控冲床作业指导书引言概述:数控冲床是现代制造业中常用的一种机床,它具有高精度、高效率、高自动化程度等特点,广泛应用于各个行业。
为了正确、安全地操作数控冲床,本文将提供一份详细的数控冲床作业指导书,帮助操作人员掌握正确的操作方法和注意事项。
一、准备工作1.1 确认机床状态:检查数控冲床的各个部位是否完好,如导轨、润滑系统等,确保机床处于正常工作状态。
1.2 准备工装夹具:根据工件的尺寸和形状,选择合适的工装夹具,并进行正确的安装和调整。
1.3 载入加工程序:使用数控编程软件将加工程序输入数控冲床的控制系统中,并进行正确的参数设置。
二、操作步骤2.1 启动机床:按照机床的启动顺序,依次打开电源、液压系统和冷却系统,确保机床各个系统正常工作。
2.2 加载工件:将待加工的工件放置在工装夹具中,并进行正确的夹紧操作,确保工件的稳定性和安全性。
2.3 运行加工程序:通过数控系统的操作界面,选择对应的加工程序,并按照提示进行操作,确保数控冲床按照预定的路径和速度进行加工。
三、加工操作3.1 刀具选择:根据工件的材料和加工要求,选择合适的刀具,并进行正确的安装和调整。
3.2 加工参数设置:根据工件的材料和形状,设置合适的加工参数,如切削速度、进给速度等,确保加工质量和效率。
3.3 加工监控:在加工过程中,及时观察加工情况,如切削力、切削温度等,发现异常情况及时停机检查,并进行调整和处理。
四、安全注意事项4.1 安全防护:在操作数控冲床时,必须正确佩戴防护眼镜、手套等个人防护装备,确保工作人员的人身安全。
4.2 紧急停机:在发生紧急情况时,应立即按下紧急停机按钮,切断机床的电源,保证操作人员的安全。
4.3 维护保养:定期对数控冲床进行维护保养,如清洁、润滑等,确保机床的正常运行和寿命。
五、结束操作5.1 停止机床:在完成加工任务后,按照机床的停止顺序,依次关闭电源、液压系统和冷却系统,确保机床处于停止状态。
5.2 清理工作区:清理机床周围的工作区域,清除加工过程中产生的废料和切屑等,保持工作环境整洁。
- 1、下载文档前请自行甄别文档内容的完整性,平台不提供额外的编辑、内容补充、找答案等附加服务。
- 2、"仅部分预览"的文档,不可在线预览部分如存在完整性等问题,可反馈申请退款(可完整预览的文档不适用该条件!)。
- 3、如文档侵犯您的权益,请联系客服反馈,我们会尽快为您处理(人工客服工作时间:9:00-18:30)。
数控冲床的操作
手动模式操作
一﹑按控制面板上的MANUAL键。
确认控制面板上的相对应灯亮。
二﹑将EDIT PROTECT开关打向ON。
三﹑设置子控制面板上的刀具定位开关B到冲孔刀具位置。
四﹑将子控制面板上的INDEX PIN开关打向为IN。
五﹑将EDIT PROTECT开关打向OFF。
六﹑在控制面板上﹐按+X或-X﹐+Y或-Y﹐手动移动材料到工作点。
七﹑要于工作材料冲孔﹐照以下方法于PHNC面板设置条件。
1﹑按PHNC面板上的↓键和↑键﹐显示冲孔操作。
2﹑更改冲孔模式为SLIT模式。
3﹑更改预置参数M506为其它的参数M507或M508或M509。
八﹑将控制面板上的PRESS SELECTION打向为INCHING(寸动)九﹑按主面板上的PUNCHING键加工材料。
MDI模式操作
一﹑按控制面板上的MDI键。
确认控制面板上的相对应灯亮。
二﹑按显示屏下方的MDI软键。
三﹑踩脚踏开关松开夹钳﹐控制面板上的WORK CLAMP灯变亮。
四﹑放置材料于工作桌面。
五﹑提高X管位块﹐控制面板上的X-GAUGE BLOCK灯变亮。
六﹑推动材料进入夹钳和靠着X管位块。
七﹑踩脚踏开关关闭夹钳﹐然后降低X管位块。
WORK CLAMP灯和X-GAUGE BLOCK灯熄灭。
八﹑照以下步骤建立一个新程序。
1﹑将EDIT PROTECT开关打向OFF。
2﹑按显示屏下方的ABSLT软键﹐ABS单词将显示于屏幕右下方。
3﹑输入要用的地址和数字(如X50.)﹐然后按EOB键﹐结束程序块。
4﹑然后按INSERT键于相同的主面板。
5﹑连续输入程序于相同地方。
6﹑程序输入完成后﹐按显示屏右下方的软REWIND键使程序返回页首。
7﹑将EDIT PROTECT开关打向ON。
九﹑确认显示屏没有出现报警信息。
同时检查确保所有开关和PHNC参数设置正确。
运行模式操作
一﹑按控制面板上的MEMORY键。
确认控制面板上的+X﹐+Y和TURRET灯亮。
二﹑按控制面板上的PROGRAM键。
三﹑按显示面板上的?键和DIR键。
四﹑按O-SRH使刀盘转到所需位置需要同时按TURRET JOG键TURRER JOG ON键。
五﹑踩脚踏开关松开夹钳﹐控制面板上的WORK CLAMP灯变亮。
六﹑放置材料于工作桌面。
七﹑提高X管位块﹐控制面板上的X-GAUGE BLOCK灯变亮。
八﹑推动材料进入夹钳和靠着X管位块。
九﹑踩脚踏开关关闭夹钳﹐然后降低X管位块。
WORK CLAMP灯和X-GAUGE BLOCK灯熄灭。
十﹑确认显示屏没有出现报警信息。
同时检查确保所有开关和PHNC参数设置正确。
BLOCK SKIP健(块删除)
EDIT PROTECT开关打向开(程序修改)
FEEDRATE键(进给速度)
MULTI-PART MODE键(多数取模式)
OPT STOP键(选择性停止)
OVERRIDE ON/OFF键(安全区开关)。
PRESS SELECTION开关(压力选择)
SINGLE键(单冲)
TEST键(程序检测)
TOOL CHANGE开关打向为关(刀具更换)
RAM POSITION开关(冲头定位)
RAM SPEED开关(冲头速度)
十一﹑清除机器周围的一切物体。
十二﹑按START键执行程序。
控制面板上的AUTO OPERATION 灯亮。
显示器上的光标按程序块向下跳动。
十三﹑程序结束﹐控制面板上的AUTO OPERATION灯熄灭﹐桌面和货物返回﹐控制面板上的+X﹐+Y灯亮。
程序返回页首并可重新执行。