圆盘剪剪切机理分析及应用探讨
圆盘割刀的工作原理
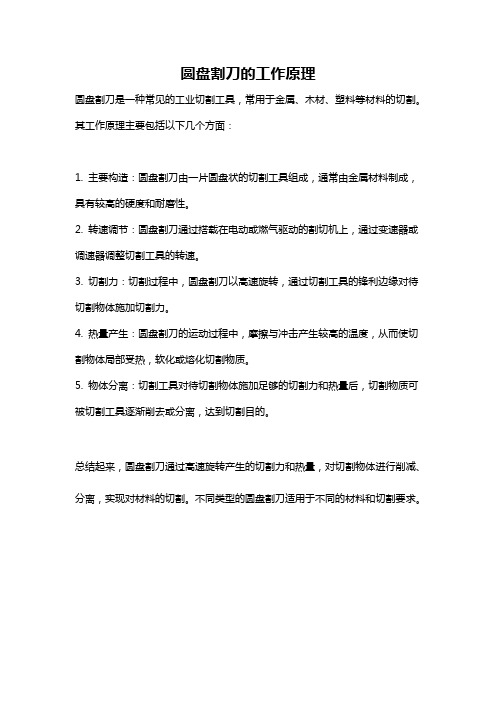
圆盘割刀的工作原理
圆盘割刀是一种常见的工业切割工具,常用于金属、木材、塑料等材料的切割。
其工作原理主要包括以下几个方面:
1. 主要构造:圆盘割刀由一片圆盘状的切割工具组成,通常由金属材料制成,具有较高的硬度和耐磨性。
2. 转速调节:圆盘割刀通过搭载在电动或燃气驱动的割切机上,通过变速器或调速器调整切割工具的转速。
3. 切割力:切割过程中,圆盘割刀以高速旋转,通过切割工具的锋利边缘对待切割物体施加切割力。
4. 热量产生:圆盘割刀的运动过程中,摩擦与冲击产生较高的温度,从而使切割物体局部受热,软化或熔化切割物质。
5. 物体分离:切割工具对待切割物体施加足够的切割力和热量后,切割物质可被切割工具逐渐削去或分离,达到切割目的。
总结起来,圆盘割刀通过高速旋转产生的切割力和热量,对切割物体进行削减、分离,实现对材料的切割。
不同类型的圆盘割刀适用于不同的材料和切割要求。
冷轧连退线圆盘剪自动控制与优化

游
冷 礼迤 退线 园盘剪 自动控 制与 优 丫 匕
河钢唐 钢信 息 自动化 部
冷 轧连 退 生产 线 的 出 口区域都 会 装备 了一 套 圆盘 剪设 备 。连退 生产 线 钢 带切 边是 非 常重 要 的生产 环节 ,它会 直接 决 定连 退线 出 E 1 产 品 的质量 ,如果 设备 运 行不 稳 定或操 作 不 当还会 影 响整 条生 产线 的节奏 及产 量 。本 文着 重 介绍 了连 退线 圆 盘剪 的剪 切 原理 、控 制方 案及 做 的重 要优 化 。
翱姆 糊镣
小时则 降低调整 电机 的速度 以实 现精确 定位 。变频 电机 的控制系 统也 配 有测量 电机转 速的速 度编码器 ,这样作 为调整执 行机构 的 电机 就在 位 置和速度 双闭环的模 式下运行 ,实现精 确定位 。 2_ 2 自动换 边控 制 自动换 刀 功 能 由3 个顺 序 控 制 实现 ,程 序编 译 在 出 口顺 控 P L C 内。当操 作 工给 出换 刀指 令 时 ,圆盘 剪各 个 设备按 以下顺 序执 行 : 首 先将 工作位 的重叠 量 完全 打开 ,然 后 圆盘剪 机 架 向外移 出到最 大 位置 ,到位 后 机架 锁紧 销 打开 ,旋 转 台开 始 做 1 8 0 。 旋 转 ,备用 侧 与 工作 侧转 换 完成 后锁 紧销 关 闭 ,机架 移入 到 设定 宽度 , 到位 后调 整 剪缝 至设 定值 ,生 产 线启 动 。
T Q为 电机 的总转 矩输 出 ; T 为 电机 转矩 的 比例 部分 ; T , 为 电机转 矩 的积分 部分 。 当存 在速 度 偏 差 △时 ,T = AV* P ,T =,AV ( t )d t ,根 据公 式 可 得 出T P 常 量 ,而T , 会 随着 时 间t 的 增加 而 累 计 ,这 就 会 导致 T Q 累计增 大 。从 而 引发 电机 过 电流或 者定 子 温度 过高 。软 化控 制 就是 弱 化 △V 对 电机转 矩 输 出 的影 响。这 就 用 到 了速度 设 定 中 的领 一个 参 数P 1 1 6 0 。参 数编 程如 下 :
圆剪切原理
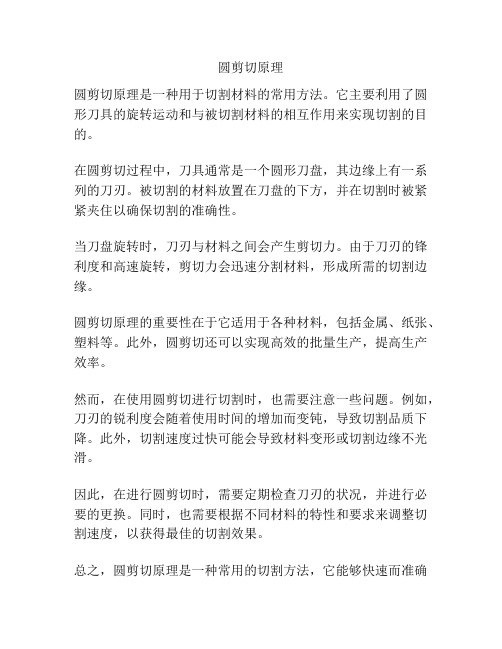
圆剪切原理
圆剪切原理是一种用于切割材料的常用方法。
它主要利用了圆形刀具的旋转运动和与被切割材料的相互作用来实现切割的目的。
在圆剪切过程中,刀具通常是一个圆形刀盘,其边缘上有一系列的刀刃。
被切割的材料放置在刀盘的下方,并在切割时被紧紧夹住以确保切割的准确性。
当刀盘旋转时,刀刃与材料之间会产生剪切力。
由于刀刃的锋利度和高速旋转,剪切力会迅速分割材料,形成所需的切割边缘。
圆剪切原理的重要性在于它适用于各种材料,包括金属、纸张、塑料等。
此外,圆剪切还可以实现高效的批量生产,提高生产效率。
然而,在使用圆剪切进行切割时,也需要注意一些问题。
例如,刀刃的锐利度会随着使用时间的增加而变钝,导致切割品质下降。
此外,切割速度过快可能会导致材料变形或切割边缘不光滑。
因此,在进行圆剪切时,需要定期检查刀刃的状况,并进行必要的更换。
同时,也需要根据不同材料的特性和要求来调整切割速度,以获得最佳的切割效果。
总之,圆剪切原理是一种常用的切割方法,它能够快速而准确
地完成切割任务。
但同时也需要注意刀刃的状况和切割速度的调整,以确保切割质量和效率的提高。
圆盘剪的剪切原理及剪切缺陷分析

圆盘剪的剪切原理及剪切缺陷分析发布时间:2021-12-10T07:26:58.021Z 来源:《防护工程》2021年25期作者:马斌[导读] 同时,消除了上游原材料的边缘缺陷,避免了产品质量下降,为下游生产线提供了安全保障。
南京钢铁股份有限公司江苏南京 210000摘要:圆盘剪又称切边剪,是带材和板材生产线的关键设备之一。
其主要功能是通过精确控制钢板宽度,满足客户对产品宽度的严格要求。
同时,消除了上游原材料的边缘缺陷,避免了产品质量下降,为下游生产线提供了安全保障。
关键词:圆盘剪;剪切;缺陷圆盘剪是生产板材的主要设备,用于剪切带钢边缘缺陷,保证全带钢宽度的一致性,提高带钢宽度精度,广泛应用于推拉酸洗装置、连续酸洗装置、酸洗-轧机联合装置、精整装置、重卷装置,是生产带材的重要设备。
同时,剪切机是轧机最重要的辅助设备之一,也是金属材料切割的机械设备。
圆盘剪近年来已广泛应用于中厚板剪切生产中,具有划痕小、剪切质量好、磨损小等优点,能保证钢板平整度及断面光滑。
1圆盘剪概述圆盘剪全称是圆盘式剪切机,当圆盘被剪切时,剪刃和轧件以相同速度运动,并经历连续的圆周运动,形成一对无端点剪切。
其一般放置在带材和板材剪切线上,对运动板材或带材两侧边缘进行纵向剪切,使剪后带钢或板材边缘准确、干净、无毛刺。
按用途分为切边剪和分条剪;根据传动形式,有拉剪和动力剪。
拉剪是由后拉力辊或卷取机拉动的无传动圆盘剪。
动力剪有自己的传动装置,其中一些还配有离合器。
使用拉剪时,离合器可根据情况打开。
2圆盘剪的剪切原理圆盘剪由上下两片圆形刀片组成,用于剪切钢板边缘,两片刀片垂直排列,有一定形式的错位,使上下刀片形成一定程度的重叠量及侧间隙。
钢板边缘进入圆盘剪接触剪刃后,刀片向带钢施加剪切力,刀盘旋转,剪刃刃口间距减小,带钢开始逐渐变形,先弹性变形,再塑性变形,当变形量累积到一定程度时,剪裂产生并进一步扩展,废边与整个钢板分离,完成整个剪切过程,基本上包括以下四个连续阶段。
螺旋焊管生产用圆盘剪的剪切质量分析

螺旋焊管生产用圆盘剪的剪切质量分析0 引言圆盘剪是用来进行纵向连续剪切带材的剪断机,也是螺旋焊管机组和纵剪机组中钢带工作宽度定尺的设备。
由于这种剪断机的剪刃是圆盘形的,所以称为圆盘剪。
它除了确定钢带宽度精定尺外,还起到消除或减少钢带轧制过程中所形成的月牙弯(俗称镰刀弯)的作用。
圆盘剪自身不带传动装置,而是靠递送机进行拉力剪切。
圆盘剪的工作部分,是由上剪刃与下剪刃形成的一对剪刃口来完成钢带剪切。
根据剪切需要可采用一对多对剪刃。
螺旋埋弧焊管机组一般采用两对剪刃剪切钢带边缘,纵剪机组则采用一对或多对剪刃进行纵剪钢带。
在制管行业中,虽然圆盘剪的结构、外形、尺寸各有差异,但剪切原理和用途是相同的,影响剪切质量的因素也是相同的。
探讨剪切质量的主要目的,在于提高钢带的剪切质量,提高生产率,降低生产成本。
同时也为日常生产和维修工作中,安装和调试剪刃、分析和判断故障提供依据。
1 螺旋焊管用圆盘剪剪切钢带过程分析螺旋焊管用圆盘剪剪切钢带的过程包括以下四个连续阶段。
(1)挤压阶段(又称弹性变形阶段):钢带在动力机(递送机)张力牵引下,进入上、下剪刃所形成的刃口,剪刃开始挤压钢带,钢带产生弹性压缩弯曲。
这一阶段钢带内的应力还没有超过弹性极限。
(2)滑移阶段(又称塑性变形阶段):剪刃继续挤压钢带,钢带内部产生的应力达到屈服点,晶界移滑。
特别是当剪刃间隙大的时候,钢带纤维的弯曲和拉伸也就越大,在这一阶段的后期,靠近刃口的应力与带钢的剪切应力相等。
(3)剪裂阶段:剪刃继续挤压钢带,刃口处钢带内应力超过了分子间的结合力,这时钢带沿着滑移面方向产生裂纹。
理想的裂纹应是上、下刃口的连线,但由于上、下剪刃有间隙,所以理想的裂纹是很难存在的。
也就是说,剪切的带钢边都存在或大或小的毛刺,而毛刺的大小由裂纹起始点的位置来决定。
(4)分离阶段:剪刃继续挤压带钢,裂纹发展为裂缝。
剪断的板条,由于受到上剪刃外侧摩擦力的作用而向上翘曲脱离钢带。
钢带则在牵引力的作用下,继续向前运行,从而完成剪切全过程。
圆盘剪工作原理

圆盘剪工作原理
圆盘剪是一种常见的金属加工工具,其主要工作原理是通过切削和挤压将金属材料切割成所需要的形状。
下面将详细介绍圆盘剪的工作原理。
圆盘剪主要由一个圆盘刀片和一个转动的平台组成。
在工作时,圆盘刀片会以高速旋转,而平台则用来固定和支撑待加工的金属材料。
当金属材料被放置在平台上后,操作者会通过控制装置将圆盘刀片向下压至金属材料上方。
此时,圆盘刀片与金属材料之间会形成一个剪切区域。
在剪切过程中,圆盘刀片以高速旋转,同时向下施加压力。
由于圆盘刀片上有多个锋利的切削齿,它们能够将金属材料切割成所需的形状。
同时,圆盘刀片的旋转也会产生一定的侧向力,将金属材料向两侧挤压,使得切割更加顺利。
在切割过程中,由于金属材料的硬度和厚度不同,圆盘刀片需要不断调整切削角度和施加的压力。
通常情况下,对于较硬的金属材料,需要较大的切削力和较小的切削角度;而对于较薄的金属材料,则需要较小的切削力和较大的切削角度。
此外,为了避免金属材料在切割过程中产生变形或损坏,通常会在金属材料与圆盘刀片之间加入润滑剂。
润滑剂的作用是降低切削力和摩擦,使切削更加顺畅。
总的来说,圆盘剪通过切削和挤压的作用将金属材料切割成所需要的形状。
其工作原理简单而有效,被广泛应用于金属加工行业中。
圆盘剪

酸洗机组圆盘剪调整工艺一、圆盘剪的功能采用一定的剪切工艺对带钢的边部进行剪切,消除热轧钢带的边部缺陷,和满足用户的需求。
二、主要技术性能剪切速度:30~180m/min刀片直径: 350~400 mm刀头开口度: 700~1350 mm刀片厚度: 35~ 40 mm刀片材质: 6CrW2Si刀轴材质: 42CrMo切边量: Min 5mm且大于1.5倍带钢厚度;Max 35mm (单边)剪切带钢厚度: 1.5~ 5mm刀片重叠量调整精度: ±0.2mm刀片侧隙调整精度: ±0.1mm三、圆盘剪的剪切机理圆盘剪由上下错位的、垂直的两片圆形刀片组合而成,调取一定的间隙及重叠量对通过两刀片之间的带钢进行剪切。
带钢通过两刀片之间时,刀片给带钢施以一定的剪切力,使带钢与刀片接触区域产生变形,随着咬入深度的增加,带钢的变形量也随之增加,当变形量达到一定程度时(一般为带钢厚度的1/4~3/4),受压的部分就从原板上断裂。
下刀片装在内侧主要起支撑作用,上刀片装在外侧主要起剪切作用。
上刀片机组中钢带心线边丝下刀片四、剪切不良的常见缺陷及成因分析1. 毛刺1.1原因毛刺的根本原因是刀片自身的平面度、上下刀片的相对平行度及刀片平面与剪切后钢带边缘的平行度存在偏差所至,导致上刀片与带钢边缘进行二次剪切;常见原因为刀片承担剪切面的边缘有缺口、烧伤或粘结、装刀时刀片侧面粘有异物、或者刀片修磨后未作消磁处理,导致刃口部位粘上铁屑。
1.2对策对各规格带钢剪切时按照正确的调整工艺进行调整;为了减少刀片自身的平面度、上下刀片的相对平行度偏差所带来的影响调整时可适当的将刀片的间隙放大,使剪切后钢带的横截面成倒梯形,以减少二次剪切面积;安装时保证刀片平面与机组中心线的平行度,同时使刀片出口侧的间距略大于入口侧的间距(0~1mm);及时更换刀片后作业;保证新刀片及修磨后刀片的精度,对修磨后的刀片作消磁处理。
2. 剪切不断2.1原因剪切不断的根本原因是刀片的间隙过大或重叠量过小;常见原因为刀片崩刃、刀片过钝、刀片的内孔过大导致剪切时重叠量的波动较大、压靠盘的直径与刀片直径的匹配不合理。
圆盘剪剪切原理探讨及剪切力计算分析
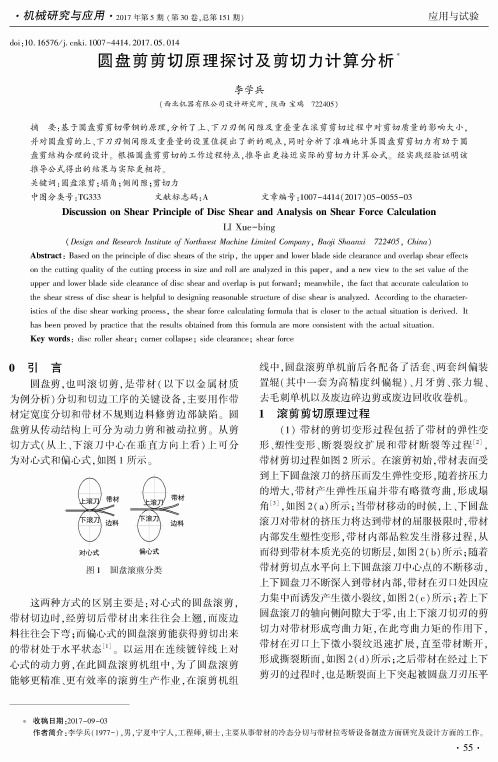
线 中 ,圆盘滚剪单机前后各配备了活套、两套纠偏装 置辊(其 中 一 套为高精度纠偏辊)、月 牙 剪 、张 力 辊 、 去毛刺单机以及废边碎边剪或废边回收收卷机。
1 滚剪剪切原理过程
( 1)带材的剪切变形过程包括了带材的弹性变 形 、塑性变形、断 裂 裂 纹 扩 展 和 带 材 断 裂 等 过 程 [2], 带材剪切过程如图2 所示。在滚剪初始,带材表面受 到上下圆盘滚刀的挤压而发生弹性变形,随着挤压力 的 增 大 ,带 材 产 生 弹 性 压 扁 并 带 有 略 微 弯 曲 ,形成塌 角 [3],如 图 2 (a)所 示 ;当带材移动的时候,上 、下圆盘 滚刀对带材的挤压力将达到带材的屈服极限时,带材 内部发生塑性变形,带材内部晶粒发生滑移过程,从 而得到带材本质光亮的切断层,如 图 2 (b )所 示 ;随着 带材剪切点水平向上下圆盘滚刀中心点的不断移动, 上下圆盘刀不断深入到带材内部,带材在刃口处因应 力集中而诱发产生微小裂纹,如 图 2 (c )所示;若上下 圆盘滚刀的轴向侧间隙大于零,由上下滚刀切刃的剪 切力对带材形成弯曲力矩,在此弯曲力矩的作用下, 带材在刃口上下微小裂纹迅速扩展,直 至 带 材 断 开 , 形成撕裂断面,如 图 2 (d )所示;之后带材在经过上下 剪 刃 的 过 程 时 ,也 是 断 裂 面 上 下 突 起 被 圆 盘 刀 刃 压 平
the shear stress of disc shear is helpful to designing reasonable structure of disc shear is analyzed. According to the character
isticshe shear force calculating formula that is closer to the actual situation is derived. It
变宽度圆盘剪切机的研究与分析
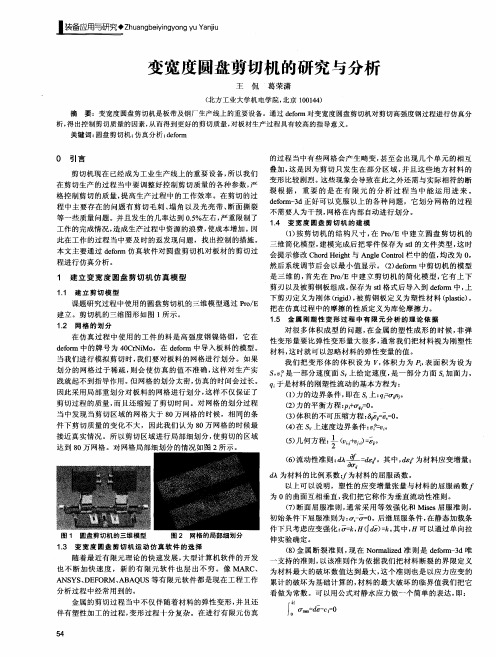
O 引 言
剪 切 机 现 在 已经 成 为 工 业 生 产 线 上 的重 要 设 备 , 以 我 们 所
的过程 当中有 些网格会产 生畸变 , 甚至会 出现 几个单元 的相互 叠 加 , 是 因 为 剪 切 只 发 生 在 部 分 区域 , 且 这 些 地 方 材 料 的 这 并 变形 比较剧烈 。 这些现象会 导致在此之外还需 与实际相符的断
() 3 体积 的不可压缩方程 : s= 。 跏 0 () . 上速度边界条件 : 。 4在 s 口
1
接近真 实情况 。所 以剪 切区域进行局 部细划分 , 使剪切 的区域 达到 8 O万网格 。对 网格局 部细划分的情况如图 2所示 。
() 何 方 程 : 返发现 问题 ,找 出控制 的措施 。
本 文 主 要 通 过 dfr 仿 真 软 件 对 圆 盘 剪 切机 对 板 材 的 剪 切 过 e om
() 1 按剪切 机 的结构 尺寸 , Po E中建立 圆盘 剪切 机 的 在 r/ 三 维 简 化 模 型 , 模 完 成 后 把 零 件 保 存 为 s 的 文 件 类 型 , 时 建 t l 这 会提示修 改 C odH i t A geC nrl 中的值 , 改为 0 h r eg 与 n l o t 栏 h o 均 , 然后系统调 节后会 以最 小值显示 。 () eo 中剪切机 的模型 2 dfr m
摘
要 :变 宽度 圆盘 剪切 机是 板带 及钢 厂 生产 线上 的重 要 设备 。通 过 df m 对 变 宽度 圆盘 剪切 机对 剪 切 高强度 钢 过程 进 行仿 真分 eo r
析 , 出控制 剪切 质量 的因素 , 而得 到更 好 的剪切 质 量 , 板材 生 产过 程具 有较 高 的指 导意 义 。 得 从 对 关键 词 : 圆盘 剪切 机 ; 仿真 分析 ;eo dfr m
圆盘剪机组及滚切剪工作原理-杨春雨

圆盘剪机组工作原理
综上所述,圆盘剪机组的工作流程可以概述如 下:钢板经1#冷床被送到出口辊道,然后经出口 辊道被送到圆盘剪剪前辊道,在进入圆盘剪前钢 板停止前行,由推钢机根据激光划线仪划出的线 将钢板对中,然后由剪前辊道将钢板送入圆盘剪 进行剪切。在圆盘剪开始启动的同时,碎边剪也 同时启动,圆盘剪剪下的板边经导卫装置进入碎 边剪,然后碎边剪将其剪断,剪断后的板边经由 漏斗进入废料斗。在剪切的同时,操作人员根据 钢板的宽度与实际情况启动剪后导尺,由剪后导 尺将钢板对中,防止钢板在剪切过程中跑偏,导 致钢板出现毛边、切口不齐甚至形成浪形钢板, 以及卡钢等事故。之后钢板由剪后辊道送到滚切 剪剪前辊道,准备进行对其切头切尾工序。
二、规格与性能 1、剪切钢板规格 剪切钢板母板长度:~33m 厚度: 4 ~33mm 宽度: 1300 ~2400mm 定尺长度: 4m 2、剪切力:最大4800KN 3、剪刃长度:2700mm 4、理论剪切次数:最大20次/min 5、剪刃水平间隙调整量:0.25 ~0.5mm 6、剪刃重叠量: ~5mm
三、结构特点
滚切式定尺剪的主要组成部分包括:机架,主传动
箱,上刀架及连杆,下刀座,剪刃侧隙调整装置, 前后测长辊,面板等。 主要辅机有:换刀装置,废料及试样收集装置, 摆动辊道,机架辊,夹送辊等。 四、设备的润滑 1、稀油循环润滑 滚切式定尺剪有一套稀油润滑系统。油泵装置装 在剪机的主电机平台上,剪机的主传动箱做为储油 箱。润滑系统由两台齿轮油泵(一台工作,一台备 用):RBZ—63型、 流量Q=63 L/min、 公称压力 P=0.63MPa、 泵电机功率2.2KW、 转数940r/min、
提高圆盘剪剪切质量探讨
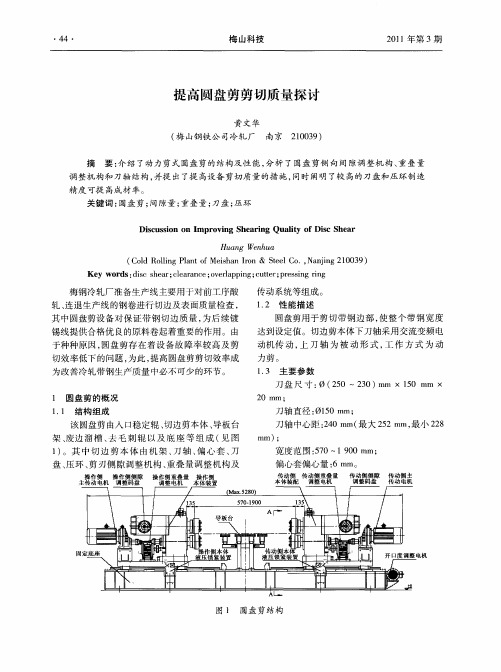
取 偏心 套在 最 高位置 ( = 。 和最 低 位置 (r 0) O .
=
10 ) 可 以 推 算 出 新 刀 片 重 叠 量 的 调 整 范 8。 ,
S = L +2R O O — D C St
=
围为 :
2 40+2 ×6 X C S / 5 O O 一2 0
=
(一 2 m 2~ ) m
梅 钢冷 轧厂 准备 生产 线 主要用 于对 前 工序 酸 轧、 连退 生产 线 的钢卷 进 行切 边及 表 面质量 检查 ,
传 动系 统等 组成 。
12 性能描 述 .
其 中 圆盘剪 设 备对 保 证 带 钢 切 边 质 量 , 后 续 镀 为 锡 线提 供合 格优 良的原 料卷起 着 重要 的作 用 。 由 于 种种 原 因 , 圆盘 剪 存 在 着 设 备故 障率 较 高 及 剪 切 效 率低 下 的问题 , 此 , 高 圆盘 剪剪切 效 率成 为 提
构 。侧 向间隙调 整装 置 安 装 在 上 刀轴 箱 体 上 , 采 用 高刚 性 的直线 导 轨 作 为 导 向元 件 , 带有 锁 紧装
置的手轮通过滚珠丝杠付驱动楔形块在直线导轨 上运 动 , 而斜 楔 块将 直 线 导 轨 滑 块 的 直线 运 动 改
变 9 。 动 方 向 , 用 双 向 推 力 圆 柱 滚 子 轴 承 作 0运 采
为改 善冷 轧带 钢生 产质 量 中必不 可少 的环 节 。 1 圆盘 剪的 概况
1 1 结构 组 成 .
圆盘剪 用 于剪 切 带 钢 边 部 , 整 个带 钢 宽度 使 达到设 定值 。切 边 剪本体 下 刀轴 采用 交流 变频 电
圆盘剪工作原理

圆盘剪工作原理
圆盘剪是一种常见的剪切工具,通过将材料夹持在两个圆盘之间进行剪切。
其工作原理如下:
1. 放置材料:将需要剪切的材料放置在圆盘剪的夹持部分,确保材料平稳固定,不会滑动或移动。
2. 启动机械装置:通过启动机械装置,驱动两个圆盘同时旋转。
3. 压力施加:当圆盘旋转时,材料被夹持在圆盘之间,同时受到一定的压力。
4. 剪切过程:由于受到夹持和压力的作用,圆盘与材料之间形成的剪切力会逐渐切断或剪断材料。
这个过程可以重复进行,直到材料完全被切断或剪断。
5. 完成剪切:当材料被切断或剪断后,剪切就完成了。
剪切后的材料可以取出,供后续加工或使用。
需要注意的是,圆盘剪在剪切过程中需要提供足够的压力和稳定的夹持,以确保剪切的准确性和效率。
同时,操作人员也需要具备一定的安全意识和技巧,以避免意外伤害。
关于圆盘剪剪切工艺的探讨

1 29 ・
科技 与创 新 I S c i e n c e a n d T e c h n o l o g y &I n n o v a t i o n
当重合量大于合理值时 , 可能会导致毛刺增加 , 如图 4所 示 ,并且剪刃磨损 加大 ;当重合量小 于合理值 时 ,不能进行切 边工作 。当间隙量大于合理值时 , 可能会导致剪切 面板形不 良, 不能实现剪切或带 钢划伤 ;当间 隙量小 于合理值 时 ,无法进行 剪切工作 。当剪 刃磨损较大时 ,剪切 面板形不 良;当剪刃掉齿
时 ,会周期性 出现板形不 良的剪切 面 ,比如 啃边 , 如图 流 程
本钢浦项 1 j f i } 重卷机组的圆盘剪位于质量检查 台后 , 设 计它 就是为 了剪 切带钢边部 ,保证 带钢的宽度符合相关要求 ,消除 冷轧钢带边部存 在的缺陷 , 从 而取 得优质冷轧或镀锌 产品。通 过伺服 电机带 动偏心 圆传动轴传 动来调节 圆盘剪剪 刃的间隙和 重合量 ,使 圆盘剪具有较高 的剪切力和精确 的剪 刃调整 。圆盘 懒 , 跏 图 4 毛刺 图 5 啃边 剪要做 到精 确安装 、调整 和标 定 ,使剪切后 的带 钢边部没有缺 3 圆盘剪主要工艺参数的选择 陷 ,进而达到标 准和合 同所要求的边部质量 。 圆盘 剪的主要 工艺参数包括上下剪刃重合量和间隙量 。 1 . 2 圆盘剪 的剪切 机理 3 . 1 剪刃 间隙量 的选择 圆盘剪是 由上下错位 、垂直 的两 片圆形刀片组合而成 的。 在设 定合理 的圆盘剪上下 剪刃间隙时 ,应 当保证带 钢的剪 在工作时 , 调 出一定的间隙和重合量 ,剪切通过两刀片之间的带 切断面光洁无毛刺 ,圆盘剪所需要 的剪切力最小 。对 于需要剪 钢 。带钢通过两刀片之 间时 ,刀片给带钢施 以一定的剪切力 , 使 切边 部的钢带 ,调整 圆盘剪 上下剪刃 间隙量主要是根据 带钢的 带钢与刀片接触 区域发生变形 。随着咬人深度 的增加 ,带钢 的变 形量也会 随之增加 。当变形量达到一定程度 时 ( 一般为带钢厚度 厚度 和力学性能确定 的。一 般变形抗力较小 的带钢调整 圆盘剪 上下剪刃 间隙量 时 ,要 比变形抗力较大 的带钢小一 些 ;薄带钢 调整圆盘剪上下剪刃 间隙量 时,要厚带钢 的间隙量小一些 。 圆盘剪 的间隙量经验值 为带钢厚度 的 1 / 1 0~1 / 9 . 3 . 2 剪 刃重合量 的选择 圆盘剪上下剪 刃重合量取决于带钢 的厚度 和力 学性能 。带 钢厚度越薄 ,其重合量相对越大 ;带钢厚 度较大时 ,可用相对 厚度较小 的重 合量 。在实 际生产过程 中 ,剪刃的重合量装配不 带钢的剪切面如 图 3所示 。图 3中,挤压 面为 出现剪切 变 宜过大 。当重合量装配过大 时 ,则会 增加剪刃的磨损 ,特别 当 刀片瓢 曲不平 时 ,很容易造成上下剪 刃互 相啃伤 。同时 ,如果 形之前 被挤压 的部分 ;剪切面为被剪 刃剪切的部分 ,有光泽 ; 磨擦 面则是剪刃 和剪 切面磨擦而形成 的 ,它是剪切面 中被延 伸 重合量过 大 ,在剪切时 ,带钢会往下 弯 ,毛边往上翘 ,容易造 率 推下来 的部分 ;断裂面是拉伸 断裂 的部分 ,凹凸较严 重的部 成边丝跑 出 ,引发事故 。 分 ;毛刺则是带钢断裂 时拉长 的部 分。 ’ 圆盘剪 的重合量 经验值 为带钢厚 度的 1 / 3~1 / 2 .
圆盘剪剪切质量分析和调整步骤

圆盘剪剪切质量分析及调整步骤一、剪切变形的过程剪切变形包含了钢板的弹性变形、塑性变形、裂纹扩展、材料断裂等过程。
在弹性变形阶段,上下刀刃挤压钢板,使钢板产生弹性压扁并略有弯曲;而后随着刃口距离的不断靠近,钢板达到屈服极限,金属内部发生塑性变形,得到光亮的切断层断面;剪切继续进行,在刃口处产生应力集中并诱发微小裂纹产生,上下裂纹迅速扩展、重合,钢板断开,剪切过程完成。
剪切后的断面见图1。
图1 剪切断面其中a为塌肩(或塌角),b为切断层(或叫做光亮带),c为撕断层(或断裂带),d为毛刺。
正常情况下塌肩和毛刺都比较小,切断层和撕断层占据了剪切断面的绝大部分。
二、剪刃间隙和切边质量的关系1.切边质量的判定标准:切断面约占钢板厚度的1/5~1/3;切断面与撕断面分界线连续、平直;整个剪切面平整光滑、无缺口、无大的毛刺。
2.侧间隙和切边质量的关系:剪刃的侧向间隙是影响钢板剪切质量的最重要因素,实践表明,侧隙大小对剪切质量的影响比重叠量的影响要敏感得多,因而设定出合理的侧隙值是圆盘剪间隙调整的关键。
从钢板的剪切断面来看,随着侧隙的增加,切断层比例会随之显著减小,塌肩、毛刺则基本上没有变化。
当侧隙增加到一定程度后,切断层减小趋势不再明显,而塌肩、毛刺会有显著地增加。
剪刃侧隙调整过小,会导致剪刃磨损严重,设备超载,切断面所占比例较大,部分断面还会出现沾肉或二次剪切现象;侧隙太大时,裂缝无法合上,中心部分被强行拉断,毛刺、塌肩严重。
3.重叠量和切边质量的关系:剪刃重叠量应根据钢板厚度及剪切情况进行调整,一般来说重叠量太大时,会造成剪切力太大,边丝弯曲产生扣头现象;重叠量过小时则可能会造成钢板无法剪断。
重叠量主要通过影响钢板的咬入角进而影响剪切力,关系式如下:D sh+-=1cosα,其中h为钢板厚度;D为圆盘剪刀片直径,980 mm左右;s为重叠量。
可以验证,若钢板厚度为10 mm,当重叠量从-1mm增加到0mm时,咬入角α几乎没有多大变化。
新钢酸轧线中圆盘剪的应用分析
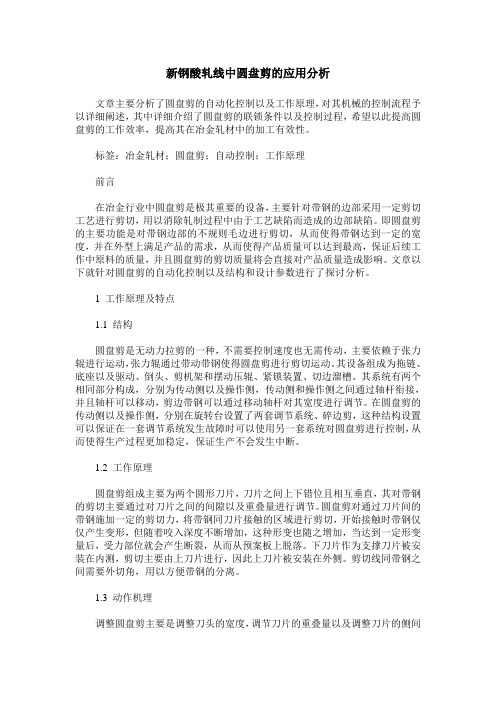
新钢酸轧线中圆盘剪的应用分析文章主要分析了圆盘剪的自动化控制以及工作原理,对其机械的控制流程予以详细阐述,其中详细介绍了圆盘剪的联锁条件以及控制过程,希望以此提高圆盘剪的工作效率,提高其在冶金轧材中的加工有效性。
标签:冶金轧材;圆盘剪;自动控制;工作原理前言在冶金行业中圆盘剪是极其重要的设备,主要针对带钢的边部采用一定剪切工艺进行剪切,用以消除轧制过程中由于工艺缺陷而造成的边部缺陷。
即圆盘剪的主要功能是对带钢边部的不规则毛边进行剪切,从而使得带钢达到一定的宽度,并在外型上满足产品的需求,从而使得产品质量可以达到最高,保证后续工作中原料的质量,并且圆盘剪的剪切质量将会直接对产品质量造成影响。
文章以下就针对圆盘剪的自动化控制以及结构和设计参数进行了探讨分析。
1 工作原理及特点1.1 结构圆盘剪是无动力拉剪的一种,不需要控制速度也无需传动,主要依赖于张力辊进行运动,张力辊通过带动带钢使得圆盘剪进行剪切运动。
其设备组成为拖链、底座以及驱动、倒头、剪机架和摆动压辊、紧锁装置、切边溜槽。
其系统有两个相同部分构成,分别为传动侧以及操作侧,传动侧和操作侧之间通过轴杆衔接,并且轴杆可以移动,剪边带钢可以通过移动轴杆对其宽度进行调节。
在圆盘剪的传动侧以及操作侧,分别在旋转台设置了两套调节系统、碎边剪,这种结构设置可以保证在一套调节系统发生故障时可以使用另一套系统对圆盘剪进行控制,从而使得生产过程更加稳定,保证生产不会发生中断。
1.2 工作原理圆盘剪组成主要为两个圆形刀片,刀片之间上下错位且相互垂直,其对带钢的剪切主要通过对刀片之间的间隙以及重叠量进行调节。
圆盘剪对通过刀片间的带钢施加一定的剪切力,将带钢同刀片接触的区域进行剪切,开始接触时带钢仅仅产生变形,但随着咬入深度不断增加,这种形变也随之增加,当达到一定形变量后,受力部位就会产生断裂,从而从预案板上脱落。
下刀片作为支撑刀片被安装在内测,剪切主要由上刀片进行,因此上刀片被安装在外侧。
圆盘剪切机工作原理

圆盘剪切机工作原理
圆盘剪切机是一种常见的金属切割设备,主要用于将金属材料切割成所需形状和尺寸。
圆盘剪切机的工作原理如下:
1. 材料夹持:将待切割的金属材料通过夹具固定在工作台上,确保材料稳定不动。
2. 刀盘旋转:启动电动机,通过传动装置使刀盘开始旋转。
刀盘通常由高速钢或硬质合金制成,具有锐利的切割刃。
3. 切割过程:将待切割的金属材料通过刃口压下来,同时刀盘不断地旋转,切削材料。
刀盘的旋转运动和切削刃的锋利特性使其能够迅速切断金属材料,形成所需的切割形状。
4. 排屑:切割过程中产生的金属屑会通过切削区域的缝隙排出,以保证切割过程的顺利进行。
5. 完成切割:当刀盘通过金属材料完成整个切割过程后,刀盘会停止旋转。
操作人员可以取出切割好的工件,并进行后续的处理和加工。
需要注意的是,圆盘剪切机在工作过程中会产生较大的噪音和振动,因此需要采取相应的安全措施,如佩戴个人防护装备和确保机器的稳定性。
圆形裁剪机的结构原理

圆形裁剪机的结构原理圆形裁剪机是一种用于裁剪圆形材料的机械设备。
它可以通过自动或手动操作,将圆形材料如纸张、布料、塑料片等切割成所需的尺寸和形状。
圆形裁剪机的结构原理可以分为几个主要部分:底座、上刀和下刀、传动系统、控制系统等。
首先,底座是圆形裁剪机的主要支撑部分,通常由坚固的钢材制成。
底座上通常有一个工作台面,用于放置要裁剪的材料。
工作台面上通常有一个固定装置,可以将材料固定在工作台上,以确保裁剪的准确性和稳定性。
上刀和下刀是圆形裁剪机的核心部分。
上刀通常是一个旋转式的圆形刀片,可以通过电动机驱动,实现快速而准确的旋转。
下刀是上刀的配套部分,一般固定在底座上,用于支撑和定位材料。
上刀和下刀之间可以通过一套精密的导向装置实现刀具的配合运动。
传动系统是圆形裁剪机的另一个重要组成部分,通常包括电动机、减速器、传动轴等。
电动机通常用于驱动上刀的旋转,减速器则用于减速电动机的转速,以满足裁剪的需求。
传动轴则起到连接电动机、减速器和上刀的作用。
控制系统是圆形裁剪机的智能部分,通常由电气元件和电路组成。
控制系统可以根据操作人员的指令,实现圆形裁剪机的自动化控制。
操作人员可以通过按键、触摸屏等方式,向控制系统发送裁剪参数和指令。
控制系统则可以根据接收到的信号,控制电动机的转速和方向,调节刀具的切割深度和速度。
除了以上主要部分,圆形裁剪机还可能包括一些辅助装置,如刀具润滑系统、材料输送装置等。
刀具润滑系统可以通过给刀具提供润滑剂,提高切割的效率和寿命。
材料输送装置可以帮助将材料从材料库存区域转移到裁剪区域,提高生产效率和自动化程度。
总结起来,圆形裁剪机的结构原理主要包括底座、上刀和下刀、传动系统、控制系统等几个主要部分。
通过这些组成部分的配合和协同工作,圆形裁剪机可以实现对圆形材料的快速和准确的裁剪。
它在纸张、布料、塑料片等行业中具有广泛的应用,使裁剪工作更加高效、精确和自动化。
手动圆盘拉剪 为什么这么锋利 是什么原理结构
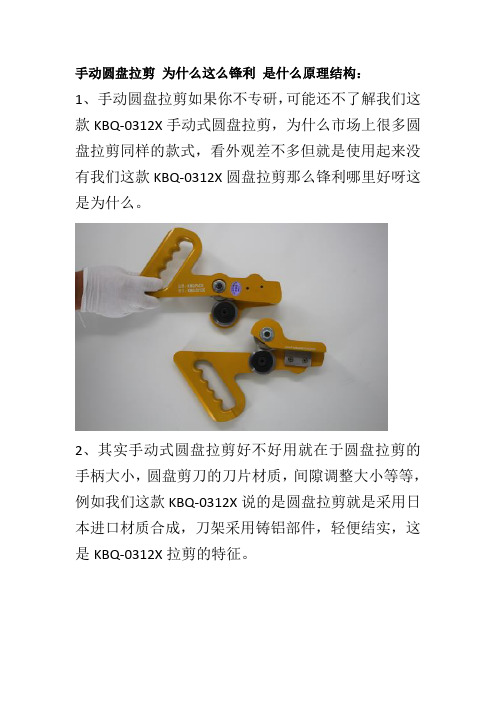
手动圆盘拉剪为什么这么锋利是什么原理结构:
1、手动圆盘拉剪如果你不专研,可能还不了解我们这款KBQ-0312X手动式圆盘拉剪,为什么市场上很多圆盘拉剪同样的款式,看外观差不多但就是使用起来没有我们这款KBQ-0312X圆盘拉剪那么锋利哪里好呀这是为什么。
2、其实手动式圆盘拉剪好不好用就在于圆盘拉剪的手柄大小,圆盘剪刀的刀片材质,间隙调整大小等等,例如我们这款KBQ-0312X说的是圆盘拉剪就是采用日本进口材质合成,刀架采用铸铝部件,轻便结实,这是KBQ-0312X拉剪的特征。
- 1、下载文档前请自行甄别文档内容的完整性,平台不提供额外的编辑、内容补充、找答案等附加服务。
- 2、"仅部分预览"的文档,不可在线预览部分如存在完整性等问题,可反馈申请退款(可完整预览的文档不适用该条件!)。
- 3、如文档侵犯您的权益,请联系客服反馈,我们会尽快为您处理(人工客服工作时间:9:00-18:30)。
圆盘剪剪切机理分析及应用探讨
摘要圆盘剪是酸洗机组上的关键设备之一,其主要作用是通过对带钢设定宽度的精确剪切并控制边部缺陷,为轧机的轧制提供一定的保障。
切边质量的好坏直接影响产品的质量等级、产量,甚至产品的报废。
因此,本文分析了圆盘剪剪切机理及应用。
关键词切边;圆盘剪;边部质量
1 圆盘剪的剪切机理分析
圆盘剪剪切钢板时,刀盘以相等于带钢运动速度做圆周运动,形成一对无端点的剪刃。
板带剪切过程是上下刀的刃口距离随着刀盘不断转动逐渐减小,中间的板带被刀片不断地切入,使板带材料发生变形,最终被完全切断的过程[1]。
板带剪切过程可分为弹性变形、塑性变形和断裂分离3个阶段。
按现代金属物理学的观点,金属内部存在大量的位错,金属塑性变形的实质就是位错的运动,材料的屈服极限就是开动位错使之运动所需的临界应力值。
材料内部的位错数量越多,开动位错就越困难,屈服极限也就越高。
位错运动的结果是使位错数量增加、位错堆积,增加了进一步塑性变形的困难,因而材料的屈服极限提高。
当位错堆积、增加到一定程度时,如果继续加大应力值,则会在位错的堆积处产生裂纹,金属就会断裂分离。
弹性变形阶段,上、下刀盘与板带接触并挤压,板带产生弹性压缩且有穹弯,略有材料挤靠上、下刀盘侧面的趋势,随着刀盘的相互靠近,穹弯愈加严重,侧向间隙越大,穹弯越大,此时应力未超过材料的弹性极限,一旦上、下刀盘分离,则板带可恢复原形。
正是由于穹弯的存在,带钢经后两个阶段时将会有反弹而挤压摩擦刀盘,对其边部造成一定的不利条件,如图1(a)示意。
塑性变形阶段,随着上、下刀盘的靠近,板带变形达到材料的屈服极限,部分材料被刀盘侧面挤压,产生塑性变形,得到光亮的剪切断面,由于侧向间隙的存在,塑性变形的同时还伴有材料的弯曲和拉伸,剪切继续进行,材料内应力不断增大,在刃口处由于应力集中,此处的最大内应力超过材料的断裂极限,开始出现微小裂纹,如图1(b)所示。
断裂分离阶段,随着上、下刀盘切入材料的深入,刃口处的裂纹不断向材料内部扩展,在侧隙合理时,上下裂纹最终将相互对接,材料随即断开,得到带钢的剪切断面。
断裂后的边部在穹弯作用下反弹。
剪切断面如图1(c)所示。
2 剪切质量的探讨及应用
2.1 弹性阶段的穹弯问题
穹弯在切断带钢后将出现一定程度的反弹,原本带钢在塑性变形时由刀盘剪切滑移所得的断面非常光滑,而反弹后的光滑面会出现二次与刀盘接触摩擦,所以在图1(b)、(c)中表示的切断区出现层层竖状条纹,实际切断条纹如图2(b)所示。
图2(a)中所示的横向灰白相间的沟壑纹路为带钢塑性变形硬化后经穹弯作用反弹接触刀盘,二次与刀盘摩擦硬化所致,对于轧制非常不利。
断面条纹和不规则断裂边界组成了轧后的带钢边部效果,如图2(b)所示,超限轧后带钢边部变成坑点状裂边。
此情况也是引起剪刃崩刃的原因之一,为消除二次加工硬化问题,首先将剪刃布置为八字,使剪切后的刀片让出反弹空间。
八字调整方案为单侧约2mm/1000mm左右,视设备安装精度关系略有偏差,剪刃布置如图3所示。
2.2 塑性、断裂阶段的问题
带钢的塑性变形过程是金属内部开动位错的过程。
此过程与刀盘的侧隙有相应的联系,当刀盘侧隙值大时,上下刀盘间的金属内部位错累积偏多,带钢的屈服强度也相应偏高,剪刃对带钢材质的加工硬化程度也偏高,带钢塑性降低,在轧制过程中更容易出现裂边。
故在侧隙允许范围内,侧隙应选偏小值。
2.3 带钢本身软硬程度的影响
由于原材料带钢材质的软硬程度会有偏差,造成其各个阶段的变形程度也不一样,材质偏硬的带钢其剪刃侧隙应适当放大一些,材质偏软则侧隙减小。
大的侧隙可以使撕裂层相对较厚,其强度更接近母材本身,受加工硬化的程度将变小。
2.4 外界条件的影响
除去剪切的因素,还存在外部条件的影响,例纠偏系统、板形等。
带钢本身大的浪边、镰刀弯等,会使纠偏机构的偏转加大,尤其是在纠偏过程中对于带钢的左右偏转会对剪刃施加一个交变的横向作用力,容易使剪刃崩刃。
纠偏系统的灵敏程度也会对带钢剪切造成影响。
正常情况下纠偏机构使得帶钢处于圆盘剪中位进入剪切,当带钢停止运动时,纠偏系统不再有纠偏动作且带钢刚好处于中位。
此时若系统过于灵敏,即使带钢保持中位不动,纠偏系统仍为不停地左右抖动状态,则会造成切断裂纹更加无序扩散、剪刃承受更复杂的交变作用力,其后果就是剪切断面更加不平,存在沟壑,甚至剪刃崩刃。
3 结束语
对剪切过程的机理进行分析,总结了剪切过程中各种不利因素,简述了各因素与剪刃侧隙的变化关系,探讨了应对措施,应用效果良好。
参考文献
[1] 陈东文,黄贞益,郝震宇,等.圆盘剪剪切工艺优化研究[J].轧钢,2015,
32(2):90.。