齿轮传动的参数选择
齿轮传动齿轮的选择原则
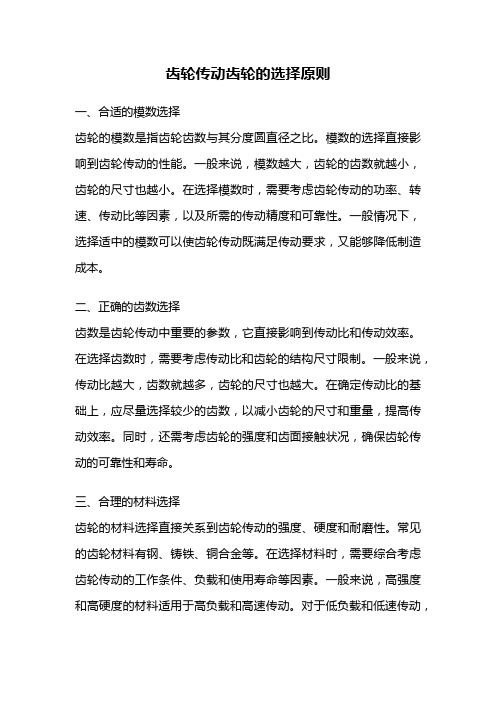
齿轮传动齿轮的选择原则一、合适的模数选择齿轮的模数是指齿轮齿数与其分度圆直径之比。
模数的选择直接影响到齿轮传动的性能。
一般来说,模数越大,齿轮的齿数就越小,齿轮的尺寸也越小。
在选择模数时,需要考虑齿轮传动的功率、转速、传动比等因素,以及所需的传动精度和可靠性。
一般情况下,选择适中的模数可以使齿轮传动既满足传动要求,又能够降低制造成本。
二、正确的齿数选择齿数是齿轮传动中重要的参数,它直接影响到传动比和传动效率。
在选择齿数时,需要考虑传动比和齿轮的结构尺寸限制。
一般来说,传动比越大,齿数就越多,齿轮的尺寸也越大。
在确定传动比的基础上,应尽量选择较少的齿数,以减小齿轮的尺寸和重量,提高传动效率。
同时,还需考虑齿轮的强度和齿面接触状况,确保齿轮传动的可靠性和寿命。
三、合理的材料选择齿轮的材料选择直接关系到齿轮传动的强度、硬度和耐磨性。
常见的齿轮材料有钢、铸铁、铜合金等。
在选择材料时,需要综合考虑齿轮传动的工作条件、负载和使用寿命等因素。
一般来说,高强度和高硬度的材料适用于高负载和高速传动。
对于低负载和低速传动,可以选择强度较低但成本较低的材料。
四、适当的齿形选择齿形是齿轮传动中齿轮的重要特征之一,它直接影响到齿轮传动的噪声、振动和传动效率。
常见的齿形有直齿、斜齿、锥齿等。
在选择齿形时,需要根据具体的传动要求和工作条件,选择合适的齿形。
一般来说,直齿齿轮适用于传动比较小的情况,斜齿齿轮适用于高速传动,锥齿齿轮适用于传动轴的交叉或垂直传动。
齿轮传动齿轮的选择原则包括合适的模数、正确的齿数、合理的材料选择和适当的齿形选择等方面。
在实际应用中,需要根据具体的传动要求和工作条件,综合考虑各种因素,选择合适的齿轮参数,以确保齿轮传动的性能、可靠性和寿命。
齿轮的基本参数和计算公式

齿轮的基本参数和计算公式齿轮是一种常见的机械元件,广泛应用于机械传动系统中。
了解齿轮的基本参数和计算公式对于正确设计和选择齿轮传动具有重要的意义。
下面将详细介绍齿轮的基本参数和计算公式。
一、齿轮的基本参数1.分度圆直径(D):齿轮两侧齿槽最低点所在的圆的直径,是齿轮设计的基本参数。
2.齿数(z):齿轮上的齿的数量。
齿数一般为整数,两个齿轮的齿数比可以决定齿轮传动的速比。
3.法向模数(m):齿轮的模数,是齿轮设计中的重要参数。
可以通过齿轮的公称齿数和分度圆直径来计算。
4.齿廓圆直径(D_a):位于齿槽底部的圆的直径,决定了齿轮传动的拓扑形状。
5.齿顶圆直径(D_f):齿槽的顶部所在的圆的直径,与齿槽的接触和传力能力有关。
6.齿底圆直径(D_b):齿槽底部所在的圆的直径,与齿槽的接触和传力能力有关。
7.齿距(p):相邻齿的中心距离,是齿轮传动中两个齿轮之间的齿距参数。
8.压力角(α):相接触齿廓线与法线之间的夹角,影响着齿轮接触性能和传力能力。
二、齿轮的计算公式1.模数(m)的计算公式:m=D/z2.齿距(p)的计算公式:p=πm3.弧齿高(h_a)和压力角(α)的计算公式:h_a = m(cos(α) + cos(α - φ))其中,φ为齿顶圆角。
4.齿顶高(h_f)和压力角(α)的计算公式:h_f = m(cos(α) + cos(α + φ))其中,φ为齿顶圆角。
5.齿厚(s)的计算公式:s = m(π/2 + tan(α) - α)6.齿廓圆直径(D_a)的计算公式:D_a=D+2m7.齿顶圆直径(D_f)的计算公式:D_f = D + 2m(cos(α) + cos(α + φ))8.齿底圆直径(D_b)的计算公式:D_b = D - 2m(cos(α) + cos(α - φ))需要注意的是,上述公式中齿顶圆角(φ)是一个常量,一般情况下取20°。
三、齿轮的计算过程1.根据传动比确定主动轮的分度圆直径和齿数。
齿轮 参数

齿轮是一种用于传递动力和运动的机械元件,其参数用于描述齿轮的形状、大小和性能。
以下是齿轮的主要参数:
1. 齿数(Z):齿轮的齿数是指齿轮上齿的数量。
齿数的增加会增加齿轮的扭矩输出,但同时也会增加齿轮的体积和重量。
2. 模数(m):模数是齿轮的一个重要参数,用于表示齿轮的大小。
模数越大,齿轮的尺寸越大,传动扭矩越大。
3. 压力角(α):压力角是齿轮齿面与齿轮轴线之间的夹角。
压力角决定了齿轮的齿形,不同的压力角会导致不同的齿形,从而影响齿轮的性能。
4. 齿高(h):齿高是指齿轮齿顶到齿根的距离。
齿高影响齿轮的强度和刚度。
5. 齿宽(b):齿宽是指齿轮齿面的宽度。
齿宽决定了齿轮的承载能力,较宽的齿面可以提高齿轮的强度和耐用性。
6. 齿轮材料:齿轮材料决定了齿轮的强度、硬度和耐磨性。
常用的齿轮材料包括铁、钢、铝、铜等。
7. 齿轮精度:齿轮精度用于描述齿轮的加工和装配误差。
齿轮精度越高,齿轮的传动性能越好,但同时也会增加制造成本。
8. 齿轮类型:根据齿形和用途的不同,齿轮可分为多种类型,如spur gear(直齿轮)、helical gear(螺旋齿轮)、bevel gear(锥齿轮)、worm gear(蜗轮)等。
9. 齿轮传动比:齿轮传动比是指驱动齿轮与被驱动齿轮之间的齿数比。
传动比越大,表示驱动齿轮的转速越高,但输出扭矩也越大。
10. 齿轮噪音:齿轮在传动过程中会产生噪音,噪音大小与齿轮精度、材料、装配质量等因素有关。
降低齿轮噪音可以提高传动系统的性能和稳定性。
齿轮基本参数知识

齿轮基本参数知识1、齿数Z闭式齿轮传动一般转速较高,为了提高传动的平稳性,减小冲击振动,以齿数多一些为好,小一些为好,小齿轮的齿数可取为z1=20~40。
开式(半开式)齿轮传动,由于轮齿主要为磨损失效,为使齿轮不致过小,故小齿轮不亦选用过多的齿数,一般可取z1=17~20。
为使齿轮免于根切,对于α=20o的标准支持圆柱齿轮,应取z1≥17。
Z2=u·z1。
2、压力角αrb=rcosα=1/2mzcosα在两齿轮节圆相切点P处,两齿廓曲线的公法线(即齿廓的受力方向)与两节圆的公切线(即P点处的瞬时运动方向)所夹的锐角称为压力角,也称啮合角。
对单个齿轮即为齿形角。
标准齿轮的压力角一般为20”。
在某些场合也有采用α=14.5° 、15° 、22.50°及25°等情况。
3、模数m=p/ π齿轮的分度圆是设计、计算齿轮各部分尺寸的基准,而齿轮分度圆的周长=πd=z p模数m是决定齿轮尺寸的一个基本参数。
齿数相同的齿轮模数大,则其尺寸也大。
4、齿顶高系数和顶隙系数—h*a 、C*两齿轮啮合时,总是一个齿轮的齿顶进入另一个齿轮的齿根,为了防止热膨胀顶死和具有储成润滑油的空间,要求齿根高大于齿顶高。
为次引入了齿顶高系数和顶隙系数。
正常齿:h*a =1; C*=0.25 短齿:h*a =0.8; C*=0.3一般的直齿圆柱齿轮,啮合的条件是:模数相等,压力角相等齿轮的直径计算方法:齿顶圆直径=(齿数+2)*模数分度圆直径=齿数*模数齿根圆直径=齿顶圆直径-4.5模数比如:M4 32齿齿顶圆直径=(32+2)*4=136mm 分度圆直径=32*4=128mm齿根圆直径=136-4.5*4=118mm 7M 12齿就是(12+2)*7=98mm。
齿轮传动的主要参数

机械设计
表4-1 齿轮传动精度等级的选择与应用
6
一对齿轮
d (节圆直径) d(分度圆直径)
ha、hf 改变了
角度变位
角度变位: x1+x2≠0,
啮合角α’ ≠α,
dd
机械设计
5
精度等级选择
GB/T10095.1-2008规定:共13个等级 0(最高)→12(低)
0~2级:待发展,少数企业目前可以制造2级精度; 3~5级:高精度; 6~8级:中等精度; 9~12级:低精度
机械设计数
机械设计
2
主要参数
1)基本齿廓、模数(GB/T1957-2008) 、中心距、分度圆压力角 2)传动比i、齿数比u
n1 d 2 z 2 (从动轮) i n 2 d 1 z(主动轮) 1
减速传动:i>1
增速传动:i<1
u
z 大齿轮 z 小齿轮
1
减速传动:u=i
增速传动:u=1/i
机械设计 3)变位系数
变位齿轮应用日益广泛,加工方法简单,但通过变位可适应不
3
同要求。 径向变位齿轮:加工时标准刀具从标准位置移动一径向距离xm。 刀具移远
正变位
齿 根 变 厚
刀具移近 负变位
齿 根 变 薄
机械设计 x1+x2=0、 x1= -x2≠0。
高度变位
4
啮合角=α’(α’=分度圆压力角α)
齿轮传动设计参数的选择
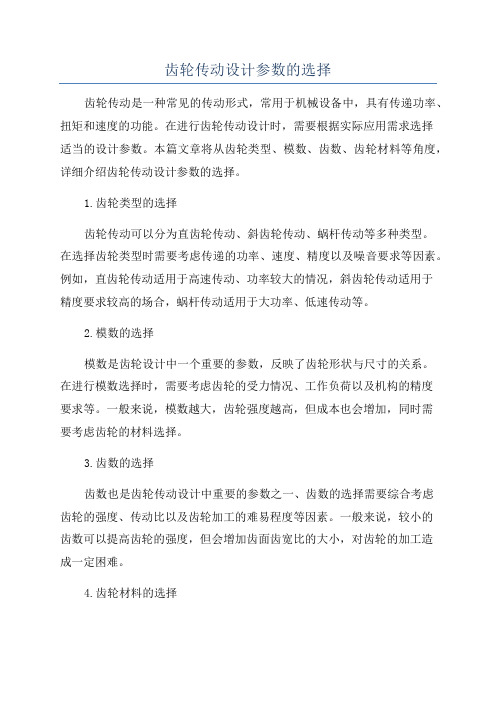
齿轮传动设计参数的选择齿轮传动是一种常见的传动形式,常用于机械设备中,具有传递功率、扭矩和速度的功能。
在进行齿轮传动设计时,需要根据实际应用需求选择适当的设计参数。
本篇文章将从齿轮类型、模数、齿数、齿轮材料等角度,详细介绍齿轮传动设计参数的选择。
1.齿轮类型的选择齿轮传动可以分为直齿轮传动、斜齿轮传动、蜗杆传动等多种类型。
在选择齿轮类型时需要考虑传递的功率、速度、精度以及噪音要求等因素。
例如,直齿轮传动适用于高速传动、功率较大的情况,斜齿轮传动适用于精度要求较高的场合,蜗杆传动适用于大功率、低速传动等。
2.模数的选择模数是齿轮设计中一个重要的参数,反映了齿轮形状与尺寸的关系。
在进行模数选择时,需要考虑齿轮的受力情况、工作负荷以及机构的精度要求等。
一般来说,模数越大,齿轮强度越高,但成本也会增加,同时需要考虑齿轮的材料选择。
3.齿数的选择齿数也是齿轮传动设计中重要的参数之一、齿数的选择需要综合考虑齿轮的强度、传动比以及齿轮加工的难易程度等因素。
一般来说,较小的齿数可以提高齿轮的强度,但会增加齿面齿宽比的大小,对齿轮的加工造成一定困难。
4.齿轮材料的选择齿轮传动中常用的材料有钢、灰铸铁、铜合金等。
在选择齿轮材料时,需要根据齿轮传动的工作环境、负荷以及寿命要求等方面进行综合考虑。
一般来说,钢齿轮可以提供较高的强度和耐磨性能,适用于高功率、高速传动;灰铸铁齿轮成本相对较低,适用于低速传动和负荷较小的情况;铜合金齿轮适用于高速传动和对噪音有一定要求的场合。
5.齿轮副的选择齿轮副是由主动齿轮和从动齿轮组成的。
在选择齿轮副时,需要考虑传动比、精度要求、工作环境等因素。
一般来说,传动比较大的情况下,可以选择斜齿轮传动;精度要求较高的情况下,可以选择硬齿面齿轮。
6.齿轮的配合间隙的选择齿轮的配合间隙是指齿轮齿条之间的间隙。
在选择配合间隙时,需要综合考虑齿轮的加工精度、工作温度、承载能力等因素。
一般来说,配合间隙较小可以提高传动精度,但在高速传动和工作温度较高的情况下,需要适当增加配合间隙以避免因热膨胀引起的紧锁现象。
齿轮传动
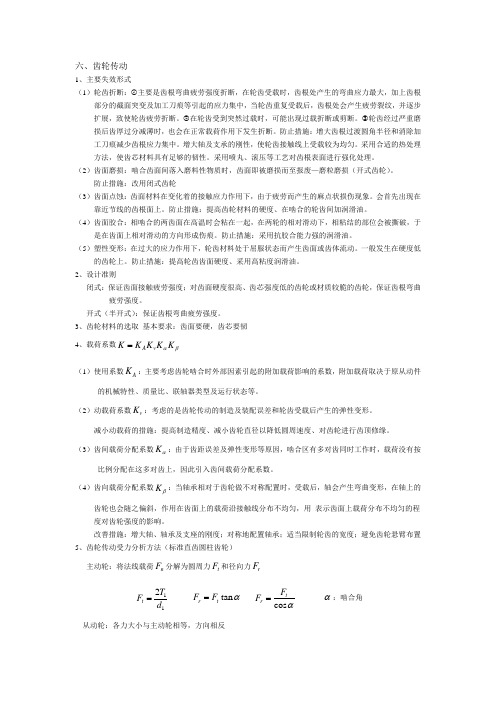
对内凹的凸轮轮廓曲线:工作廓线的曲率半径 a 理论廓线的曲率半径 +工作半径 r
对外凸的凸轮轮廓曲线 当 r 时,工作廓线出现尖点,使尖点磨损 当 r 时,工作廓线出现交叉,会出现失真现象
由此可知,对外的凸轮轮廓曲线,应使滚子半径小于理论廓线的最小曲率半径,即出现失真时,增大基 圆半径或适当减小滚子半径
当配对的两齿轮的齿面均属于硬齿面时,分别按齿根弯曲疲劳强度和齿面接触疲劳强度进行计算。 影响齿轮弯曲疲劳强度的主要是模数,模数越大,齿轮的弯曲疲劳强度越高。 影响齿面接触疲劳强度的主要是直径,小齿轮直径越大,齿轮接触疲劳强度越高。
三、凸轮机构 1、分类 (1)按凸轮形状:盘形凸轮、圆柱凸轮 (2)按推杆形状:尖顶推杆,适用于作用力不大和速度较低的场合 滚子推杆,磨损较小,可传递较大的力 平底推杆,凸轮与平底的接触面间易形成油膜,润滑较好,用于高速传动中 (3)按推杆运动形式:直动推杆、摆动推杆 2、推杆常用的运动规律 (1)几个概念:基圆半径:凸轮的最小半径 推程:推杆由最低位置推到最高位置,推杆的运动过程 远(近)休止角:推杆处于最高(低)位置不动,凸轮转过的角度 ④推杆的行程:推杆在推程或回程在推动的距离 (2)常用运动规律的特点 一次多项式运动规律(等速运动规律):推杆在运动开始和终止的瞬时,速度有突变,凸轮机构有 刚性冲击。 二次多项式运动规律(等加速等减速运动规律):加速度有突变,有柔性冲击。 五次多项式运动规律:无刚性也无柔性冲击。 ④余弦加速度运动规律(简谐运动规律):首末两点推杆加速度有突变,有柔性冲击。 ⑤正弦加速度运动规律(摆线运动规律):都无 注:除等速运动规律外,正弦加速度运动规律加速度最大值最大。 为了消除等加速等减速运动规律中的柔性冲击,可由等减速运动规律和余弦减速度运动规律组合 而成的修正梯形运动规律。
直齿圆柱齿轮设计步骤
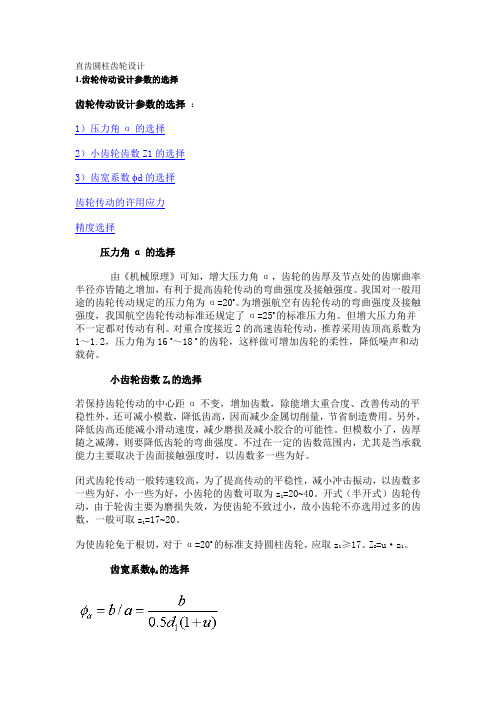
直齿圆柱齿轮设计1.齿轮传动设计参数的选择齿轮传动设计参数的选择:1)压力角α的选择2)小齿轮齿数Z1的选择3)齿宽系数φd的选择齿轮传动的许用应力精度选择压力角α的选择由《机械原理》可知,增大压力角α,齿轮的齿厚及节点处的齿廓曲率半径亦皆随之增加,有利于提高齿轮传动的弯曲强度及接触强度。
我国对一般用途的齿轮传动规定的压力角为α=20o。
为增强航空有齿轮传动的弯曲强度及接触强度,我国航空齿轮传动标准还规定了α=25o的标准压力角。
但增大压力角并不一定都对传动有利。
对重合度接近2的高速齿轮传动,推荐采用齿顶高系数为1~1.2,压力角为16 o~18 o的齿轮,这样做可增加齿轮的柔性,降低噪声和动载荷。
小齿轮齿数Z1的选择若保持齿轮传动的中心距α不变,增加齿数,除能增大重合度、改善传动的平稳性外,还可减小模数,降低齿高,因而减少金属切削量,节省制造费用。
另外,降低齿高还能减小滑动速度,减少磨损及减小胶合的可能性。
但模数小了,齿厚随之减薄,则要降低齿轮的弯曲强度。
不过在一定的齿数范围内,尤其是当承载能力主要取决于齿面接触强度时,以齿数多一些为好。
闭式齿轮传动一般转速较高,为了提高传动的平稳性,减小冲击振动,以齿数多一些为好,小一些为好,小齿轮的齿数可取为z1=20~40。
开式(半开式)齿轮传动,由于轮齿主要为磨损失效,为使齿轮不致过小,故小齿轮不亦选用过多的齿数,一般可取z1=17~20。
为使齿轮免于根切,对于α=20o的标准支持圆柱齿轮,应取z1≥17。
Z2=u·z1。
齿宽系数φd的选择由齿轮的强度公式可知,轮齿越宽,承载能力也愈高,因而轮齿不宜过窄;但增大齿宽又会使齿面上的载荷分布更趋不均匀,故齿宽系数应取得适合。
圆柱齿轮齿宽系数的荐用值列于下表。
对于标准圆柱齿轮减速器,齿宽系数取为所以对于外捏合齿轮传动φa的值规定为0.2,0.25,0.30,0.40,0.50,0.60,0.80,1.0,1.2。
齿轮模数标准值
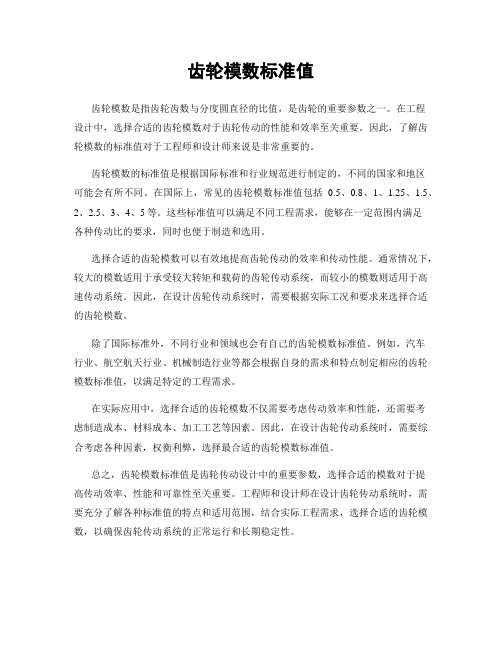
齿轮模数标准值
齿轮模数是指齿轮齿数与分度圆直径的比值,是齿轮的重要参数之一。
在工程
设计中,选择合适的齿轮模数对于齿轮传动的性能和效率至关重要。
因此,了解齿轮模数的标准值对于工程师和设计师来说是非常重要的。
齿轮模数的标准值是根据国际标准和行业规范进行制定的,不同的国家和地区
可能会有所不同。
在国际上,常见的齿轮模数标准值包括0.5、0.8、1、1.25、1.5、2、2.5、3、4、5等。
这些标准值可以满足不同工程需求,能够在一定范围内满足
各种传动比的要求,同时也便于制造和选用。
选择合适的齿轮模数可以有效地提高齿轮传动的效率和传动性能。
通常情况下,较大的模数适用于承受较大转矩和载荷的齿轮传动系统,而较小的模数则适用于高速传动系统。
因此,在设计齿轮传动系统时,需要根据实际工况和要求来选择合适的齿轮模数。
除了国际标准外,不同行业和领域也会有自己的齿轮模数标准值。
例如,汽车
行业、航空航天行业、机械制造行业等都会根据自身的需求和特点制定相应的齿轮模数标准值,以满足特定的工程需求。
在实际应用中,选择合适的齿轮模数不仅需要考虑传动效率和性能,还需要考
虑制造成本、材料成本、加工工艺等因素。
因此,在设计齿轮传动系统时,需要综合考虑各种因素,权衡利弊,选择最合适的齿轮模数标准值。
总之,齿轮模数标准值是齿轮传动设计中的重要参数,选择合适的模数对于提
高传动效率、性能和可靠性至关重要。
工程师和设计师在设计齿轮传动系统时,需要充分了解各种标准值的特点和适用范围,结合实际工程需求,选择合适的齿轮模数,以确保齿轮传动系统的正常运行和长期稳定性。
模数1的齿轮参数

模数1的齿轮参数齿轮是一种传动装置,由齿与齿两个齿轮进行啮合传动来完成任务。
在齿轮参数的设计中,模数是一个重要的参数,它定义了齿轮的齿数和齿宽之间的关系。
下面将介绍模数1的齿轮参数,并给出相关的参考内容。
1. 齿数:模数1齿轮的齿数是通过模数除以齿距得到的,其中齿距指齿轮齿数和模数的乘积。
例如,模数为1的齿轮的齿数可以是10、20、50、100等等。
齿数的选择会影响齿轮的传动比和传动效率,一般来说,齿数越多,传动比越高,但齿轮的强度和承载能力有限,因此需要根据具体应用场景来选择合适的齿数。
2. 齿宽:齿宽是齿轮轴向上齿宽度的总和,对于模数1的齿轮来说,齿宽一般是模数的整数倍。
例如,模数为1的齿轮的齿宽可以是1、2、3等等。
齿宽的选择主要考虑到齿轮的强度和传递的扭矩,齿宽越大,齿轮的强度越高,但也会增加制造成本和惯性。
3. 压力角:压力角是齿轮齿面与接触线之间的夹角,一般取20°或25°,其中20°是常用的压力角。
压力角的选择会影响齿轮啮合的平稳性和传动效率,较小的压力角能提高齿轮的传动效率,但也会增加制造成本。
4. 齿轮材料:齿轮的材料选择对于齿轮的强度、耐磨性和使用寿命有着重要的影响。
常用的齿轮材料包括碳钢、合金钢、不锈钢等。
碳钢适用于一般载荷和低速传动,合金钢适用于高载荷和高速传动,不锈钢适用于特殊环境。
除了上述参数外,还有一些其他的齿轮参数也需要考虑,例如齿轮的精度等级、齿轮的制造工艺、齿轮的润滑和散热等等。
这些参数的选择需要根据不同的应用要求和实际情况进行综合考虑。
以上是模数1的齿轮参数的相关参考内容,希望能对你有所帮助。
齿轮传动设计参数的选择
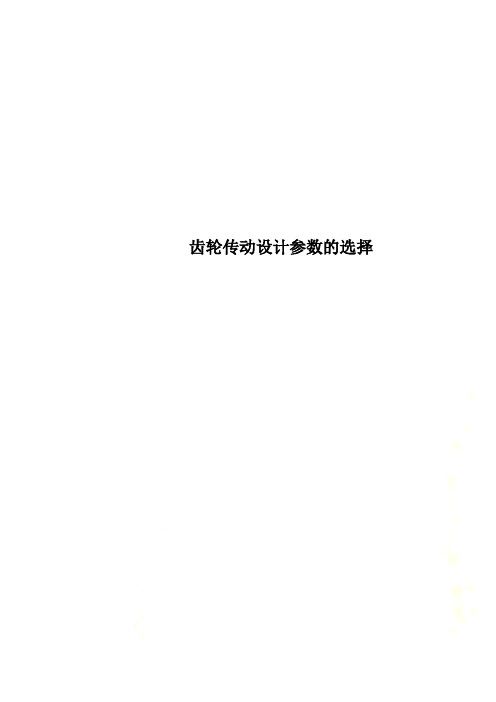
齿轮传动设计参数的选择齿轮传动设计参数的选择:1)压力角α的选择2)小齿轮齿数Z1的选择3)齿宽系数φd的选择齿轮传动的许用应力精度选择压力角α的选择由《机械原理》可知,增大压力角α,齿轮的齿厚及节点处的齿廓曲率半径亦皆随之增加,有利于提高齿轮传动的弯曲强度及接触强度。
我国对一般用途的齿轮传动规定的压力角为α=20o。
为增强航空有齿轮传动的弯曲强度及接触强度,我国航空齿轮传动标准还规定了α=25o的标准压力角。
但增大压力角并不一定都对传动有利。
对重合度接近2的高速齿轮传动,推荐采用齿顶高系数为1~1.2,压力角为16o~18o的齿轮,这样做可增加齿轮的柔性,降低噪声和动载荷。
小齿轮齿数Z1的选择若保持齿轮传动的中心距α不变,增加齿数,除能增大重合度、改善传动的平稳性外,还可减小模数,降低齿高,因而减少金属切削量,节省制造费用。
另外,降低齿高还能减小滑动速度,减少磨损及减小胶合的可能性。
但模数小了,齿厚随之减薄,则要降低齿轮的弯曲强度。
不过在一定的齿数范围内,尤其是当承载能力主要取决于齿面接触强度时,以齿数多一些为好。
闭式齿轮传动一般转速较高,为了提高传动的平稳性,减小冲击振动,以齿数多一些为好,小一些为好,小齿轮的齿数可取为z1=20~40。
开式(半开式)齿轮传动,由于轮齿主要为磨损失效,为使齿轮不致过小,故小齿轮不亦选用过多的齿数,一般可取z1=17~20。
为使齿轮免于根切,对于α=20o的标准支持圆柱齿轮,应取z1≥17。
Z2=u·z1。
齿宽系数φd的选择由齿轮的强度公式可知,轮齿越宽,承载能力也愈高,因而轮齿不宜过窄;但增大齿宽又会使齿面上的载荷分布更趋不均匀,故齿宽系数应取得适合。
圆柱齿轮齿宽系数的荐用值列于下表。
对于标准圆柱齿轮减速器,齿宽系数取为所以对于外捏合齿轮传动φa的值规定为0.2,0.25,0.30,0.40,0.50,0.60,0.80,1.0,1.2。
运用设计计算公式时,对于标准减速器,可先选定再用上式计算出相应的φd值表:圆柱齿轮的齿宽系数φd装置状况两支撑相对小齿轮作对称布置两支撑相对小齿轮作不对称布置小齿轮作悬臂布置φd0.9~1.4(1.2~1.9)0.7~1.15(1.1~1.65)0.4~0.6注:1)大、小齿轮皆为硬齿面时φd应取表中偏下限的数值;若皆为软齿面或仅大齿轮为软齿面时φd可取表中偏上限的数值;2)括号内的数值用于人自齿轮,此时b为人字齿轮的总宽度;3)金属切削机床的齿轮传动,若传递的功率不大时,φd可小到0.2;4)非金属齿轮可取φd≈0.5~1.2。
机械传动课程设计-齿轮传动设计
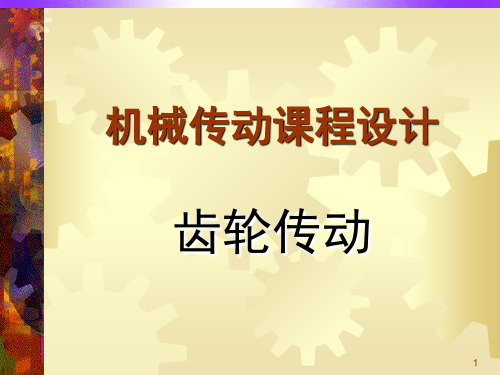
齿轮传动
2.常用齿轮材料 2)表面硬化齿轮用钢 齿面硬度>350HBS的齿轮称为硬齿面齿 轮。轮坯切齿后经表面硬化热处理,形成硬 齿面,再经磨齿后精度可达6级以上。与软 齿面齿轮相比,硬齿面齿轮大大提高齿轮的 承载能力,结构尺寸和重量明显减小,综合 经济效益显著提高。我国齿轮制造业已普遍 采用合金钢及硬齿面、磨齿、高精度、轮齿 修形等工艺方法,生产硬齿面齿轮。常用表 面硬化热处理主要有: 表面淬火;滲碳淬火;滲氮;碳氮共滲。 24
27
三、齿轮的设计准则
设计齿轮传动时,应根据实际工况条件, 分析主要失效形式,确定相应的设计准则, 进行设计计算。
28
三、齿轮的设计准则
开式齿轮传动的主要失效形式是磨损及 弯曲疲劳折断,目前对磨损尚无成熟的设计 计算方法,故通常按齿根弯曲疲劳强度进行 设计计算,并将模数增大10%~20%,以考虑 磨损的影响。
一般取中间MQ偏下值; 硬度超过范围可外插法取值; 对称循环弯曲应力取70%。
正火处理的结构钢 正火处理的铸钢
49
分析中间齿轮接触应力和弯曲应力的特点?
29
齿轮传动
三、齿轮的设计准则
对于闭式软齿面齿轮传动,主要失效形 式是齿面疲劳点蚀,其次是弯曲疲劳折断。 故先按照齿面接触疲劳强度设计,然后校核 齿根弯曲疲劳强度。 对于闭式硬齿面齿轮传动,主要失效形 式是齿根疲劳折断,其次是齿面疲劳点蚀。 故先按照齿根弯曲疲劳强度设计,然后校核 齿面接触疲劳强度。
40???2?coscos2s66coshbfbshfwmtnf?????????coscos62msmhbmftf???齿轮传动三齿根弯曲疲劳强度计算???coscos62msmhbmftf???41fsafasafatfyymbdktyybmkf?211????78?查表应力修正系数say计入齿根的应力集中考虑单对齿的啮合点位置78?查表变位与齿的形状有关齿数齿形系数fay齿轮传动三齿根弯曲疲劳强度计算fsafasafatfyymbdktyybmkf?211????校核式4278?查表变位与齿的形状有关齿数齿形系数fay78?查表应力修正系数say齿轮传动三齿根弯曲疲劳强度计算1dbd??令代入上式
齿轮传动的参数选择

齿轮传动的参数选择齿轮传动是一种常用的机械传动方式,它通过齿轮的啮合来传递动力和转矩。
在进行齿轮传动设计时,需要选择一些参数来满足传动的要求。
本文将从齿轮的数量、模数、压力角、齿宽等方面详细介绍齿轮传动的参数选择。
1.齿轮的数量:齿轮传动中,齿轮的数量是一个重要的参数。
齿轮传动可分为单级传动和多级传动两种形式。
在选择齿轮的数量时,应根据传递的动力和转矩大小以及可用的空间来确定。
一般情况下,单级传动适用于小功率和低转速的情况,而多级传动适用于大功率和高转速的情况。
2.模数:模数是齿轮的一个重要参数,它表示齿轮的齿数和齿距的比值。
模数选择应满足强度和精度要求。
一般情况下,选择较大的模数可以提高齿轮的强度,但会增加尺寸和重量。
选择较小的模数可以提高齿轮的精度,但可能会降低齿轮的强度。
因此,在进行模数选择时,要综合考虑传动的强度和精度要求,以及齿轮的尺寸和重量。
3.压力角:压力角是指齿轮齿廓与径向线的夹角。
压力角的选择应根据齿轮的工作条件来确定。
一般情况下,选择较小的压力角可以提高齿轮的传动效率和承载能力,但可能会增加齿轮的制造成本。
选择较大的压力角可以降低齿轮的制造成本,但可能会降低齿轮的传动效率和承载能力。
因此,在进行压力角选择时,要综合考虑传动效率、承载能力和制造成本。
4.齿宽:齿宽是齿轮表面上两个相邻齿槽之间的距离。
齿宽的选择应满足齿轮的强度和刚度要求。
一般情况下,选择较大的齿宽可以提高齿轮的强度和刚度,但可能会增加齿轮的尺寸和重量。
选择较小的齿宽可以减小齿轮的尺寸和重量,但可能会降低齿轮的强度和刚度。
因此,在进行齿宽选择时,要综合考虑齿轮的强度、刚度、尺寸和重量。
除了上述参数外,还有一些其他的参数也需要在齿轮传动设计中进行选择,如齿轮材料、齿轮精度等。
在选择齿轮材料时,要考虑齿轮的使用环境和工作条件,选择适合的材料来满足齿轮的强度和耐磨性要求。
在选择齿轮精度时,要根据齿轮的运动要求和传动精度要求,选择适合的精度等级来保证传动的准确性和平稳性。
齿轮的主要基本参数

齿轮的主要基本参数齿轮是机械传动中常用的零件之一,它能够将动力传递到另一个部件,使其转动。
齿轮的主要基本参数包括模数、压力角、齿数、法向模数等,下面将逐一介绍。
一、模数模数是指齿轮齿廓的大小,通常用m表示。
它是指每个齿距离圆心的距离,单位为毫米。
模数越大,齿轮的尺寸越大。
在设计和制造中,模数是一个非常重要的参数。
二、压力角压力角是指啮合时两个相邻齿廓接触点处法线与啮合线所成的夹角。
通常用α表示。
压力角大小直接影响啮合性能和传动效率。
三、齿数齿数是指一个齿轮上的牙数,通常用z表示。
它决定了两个相邻齿之间的距离和整个传动系统的速比。
四、法向模数法向模数是指垂直于啮合面方向上每毫米上牙廓高度与模长之比。
通常用mn表示。
法向模数越大,牙廓高度越高,承载能力越强。
五、顶高系数顶高系数是指齿轮齿廓顶部高度与模长之比。
通常用hf表示。
它决定了齿轮的强度和承载能力。
六、基圆直径基圆直径是指齿轮齿廓中心线上的圆直径,通常用d表示。
基圆直径决定了齿轮的尺寸和传动效率。
七、分度圆直径分度圆直径是指一个齿轮上的牙根与相邻牙顶所在的圆直径,通常用d0表示。
它是设计和制造中一个非常重要的参数。
八、压力角系数压力角系数是指啮合时两个相邻齿廓接触点处法线与啮合线所成夹角的余弦值,通常用cosα表示。
压力角系数越大,啮合性能越好。
九、螺旋角螺旋角是指齿轮齿廓螺旋线与元周线所成的夹角,通常用β表示。
它决定了螺旋锥齿轮的传动性能和制造难度。
十、偏距系数偏距系数是指齿轮齿廓中心线与啮合面法线之间的夹角的正切值,通常用tanψ表示。
偏距系数越大,齿轮的传动效率越高。
总之,以上这些基本参数是设计和制造齿轮时必须了解和掌握的重要内容。
只有深入了解这些参数,才能够设计出满足要求的齿轮传动系统。
齿轮传动参数_512104275
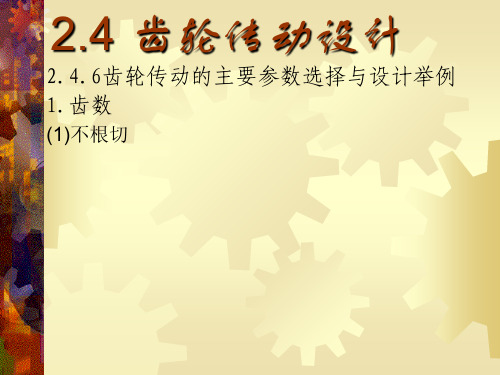
z2
60 72 90 96 120 144 180 240 288 360
b
120 120 120 120 120 120 120 120 120 120
m
6.0 5.0 4.0 3.75 3.0 2.5 2.0 1.5 1.25 1.0
a
240 240 240 240 240 240 240 240 240 240
2.4.6齿轮传动的主要参数选择与设计举例 5.齿数比
a.有利于润滑 b.等强度 c.单级传动比不宜过大(i<8) d.避免干涉 e.齿数互质(以传递动力为目的)
2.4 齿轮传动设计
2.4.6齿轮传动的主要参数选择与设计举例 5.齿数比
a.有利于润滑 b.等强度 c.单级传动比不宜过大(i<8) d.避免干涉 e.齿数互质(以传递动力为目的) f.有利于减小传动误差(以传递运动为目的)
2.4.6齿轮传动的主要参数选择与设计举例 2.齿宽系数
(1)轴的刚度较大宜取较大齿宽系数; (2)对称布置宜取较大齿宽系数; (3)软齿面齿轮传动宜取较大齿宽系数;(不敏感)
2.4 齿轮传动设计
2.4.6齿轮传动的主要参数选择与设计举例 2.齿宽系数
(1)轴的刚度较大宜取较大齿宽系数; (2)对称布置宜取较大齿宽系数; (3)软齿面齿轮传动宜取较大齿宽系数; (4)固定传动比传动宜取较大齿宽系数; (具体数值参考教材有关章节)
接触强度
弯曲强度
2T1 F YFaYSaYε K [ ]F bd1m
H ZE ZH
2 KT1 u 1 [ ]H 2 bd1 u
硬齿面
接触强度
弯曲强度
2T1 F YFaYSaYε K [ ]F bd1m
说一说齿轮参数及其特点。

说一说齿轮参数及其特点。
齿轮是一种常见的机械传动元件,广泛应用于各种机械设备中,起到传递动力和运动的作用。
齿轮的性能与设计参数密切相关,下面将对一些常见的齿轮参数及其特点进行详细介绍。
一、齿轮的基本参数:1.模数(Module):–定义:模数是齿轮齿廓曲线上齿数与分度圆直径之比。
–特点:模数越大,齿轮的齿数相对较少,但齿轮的强度相对较高。
2.齿数(Number of Teeth):–定义:齿轮上的齿的数量。
–特点:齿数的多少直接影响到齿轮的传动比。
3.分度圆直径(Pitch Diameter):–定义:分度圆是一个圆,其直径等于齿轮齿数除以模数。
–特点:分度圆直径是齿轮的基本尺寸,用于计算齿轮的其他几何参数。
二、齿轮副的参数:1.中心距(Center Distance):–定义:两个相互啮合的齿轮齿廓上两个齿轮的分度圆直径之和的一半。
–特点:中心距的选择影响齿轮副的传动比和齿轮的强度。
2.啮合角(Pressure Angle):–定义:齿轮齿廓上与齿轮轴线的夹角。
–特点:常见的啮合角有20°和25°,选择合适的啮合角有助于提高齿轮传动的效率。
三、齿轮的特性参数:1.螺旋角(Helix Angle):–定义:齿轮齿廓线与齿轴线间的夹角。
–特点:螺旋齿轮常用于高速传动,能够减小齿轮噪音和振动。
2.顶隙(Backlash):–定义:两个啮合的齿轮齿面之间的间隙。
–特点:顶隙的大小会影响齿轮传动的精密度和反向运动的稳定性。
四、齿轮的材料和热处理:1.材料选择:–特点:齿轮的材料应具备高强度、硬度和耐磨性,常见的材料有钢、铸铁、铜合金等。
2.热处理:–特点:热处理可提高齿轮的硬度和强度,减小变形,常用的热处理方式包括淬火、渗碳等。
五、齿轮的制造和检测:1.制造工艺:–特点:齿轮的制造工艺包括铣削、滚齿、锻造等,制造精度和表面质量对齿轮的性能有显著影响。
2.检测方法:–特点:齿轮的检测主要包括几何尺寸、齿形、齿距等,常用的检测方法有测量工具、光学检测、影像测量等。
齿轮传动设计中压力角、齿顶高系数及齿根圆角半径的选择

齿轮传 动设计 中压 力角 、 齿顶高 系数 及 齿 电职业 技术 学 院 , 辽宁
摘
丹东
1 1 8 0 0 0 )
要 :齿轮压 力角和齿顶 高系数及齿根 圆角半径也是齿轮设计 中的重要参数 ,本文 以渐开线直齿 圆柱齿轮 为研 究对
( 2 ) 能降低 齿轮 的振动 和噪声 ( 齿轮精 ( 3 ) 不根切 的最少齿 数减少
度要有保证 ) , 增加运转 的平 稳性
( 4 ) 增 加齿根 圆角 半径 , 减 小齿
根 应力集中系数
( 4 ) 齿根过 渡 曲线 的长度 和曲率半径减 主要应用 于透 平机 ( 1 4 . 5 0 、 1 5 0 小, 应力集中系数增大 1 5 . 5 、 1 6 0 ) 、 汽车 ( 1 4 . 5~2 0 0 )
收 稿 日期 : 2 0 1 5 - 0 3 — 1 5
2 齿顶高 系数 的选择
目前 , 国内外 标 准都 毫 无 例外 地 规 定 齿 轮 的齿 顶高 h a = l m, 即齿 顶高 系数 h a * = 1 。一般 的齿 轮设 计取 此标 准值 即可 , 但 是 要 了解 , 这也 是 一 个折 中值 。因
为如果能根据不 同齿轮 的使用条件 和其他要求 , 适
在齿 轮 设 计 中 , 齿轮 的压力 角 、 齿 顶 高 系 数及 齿 根 圆 角半 径 的选 择 对齿 轮 轮 齿 的接 触 轻度 、齿根 强
性( 噪声 和 动 载荷 ) , 因此 o  ̄ p = 2 0 。 的标 准值 其 实 是 一 个 强 度 和动 态 特 性 的折 中值 .因此 , 根 据 各 种 齿 轮 使 用条 件 、 加工条件等 , 选 用 更 合 理 的压 力 角 、 齿 顶
标准直齿圆柱齿轮参数

标准直齿圆柱齿轮参数标题:标准直齿圆柱齿轮参数——完整的参数列表及解释引言:标准直齿圆柱齿轮是一种常见的机械传动元件,广泛应用于各个领域的机械设备中。
了解和掌握标准直齿圆柱齿轮的参数对于正确选择和设计齿轮传动系统至关重要。
本文将详细介绍标准直齿圆柱齿轮的各项参数,包括齿轮模数、齿数、齿轮宽度、齿距系数、压力角、齿顶高、齿根高等。
一、齿轮模数:齿轮模数是指每公厘的模齿的数量,通常用"M"表示。
它是齿轮传动中的一个重要参数,决定了齿轮齿数和齿轮尺寸的大小。
齿轮模数的选择应根据传动功率、转速、齿轮类型、材料强度等因素进行合理的计算和选择。
二、齿数:齿数是指齿轮上的齿的数量,通常用"Z"表示。
齿数是齿轮传动中一个关键参数,决定了齿轮的传动比和运动形式。
齿数的选择应根据齿轮传动的要求和实际应用进行计算和选择。
三、齿轮宽度:齿轮宽度是指齿轮齿面宽度的大小,通常用"b"表示。
齿轮宽度的选择应根据传动扭矩和转速、齿轮材料强度等因素进行计算和选择,以确保齿轮传动的稳定性和可靠性。
四、齿距系数:齿距系数是指齿轮齿距与模数的比值,通常用"x"表示。
齿距系数直接关系到齿轮传动的运动平稳性和噪声水平。
其选择应根据实际应用需求和齿轮类型进行合理的计算和选择。
五、压力角:压力角是指齿轮齿面上与法线方向的夹角,通常用"α"表示。
压力角的选择应根据齿轮材料强度、齿轮传动形式等因素进行计算和选择,以确保齿轮传动的可靠性和效率。
六、齿顶高:齿顶高是指齿轮齿顶到齿距上沿的距离,通常用"ha"表示。
齿顶高的选择应根据齿轮传动的承载能力、齿轮材料强度等因素进行计算和选择,以确保齿轮传动的稳定性和可靠性。
七、齿根高:齿根高是指齿轮齿根到齿距下沿的距离,通常用"hf"表示。
齿根高的选择应根据齿轮传动的承载能力、齿轮材料强度等因素进行计算和选择,以确保齿轮传动的稳定性和可靠性。
齿轮尺寸设计
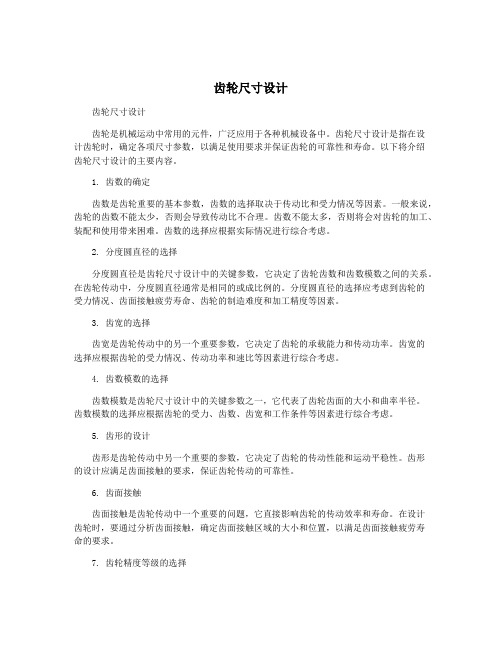
齿轮尺寸设计齿轮尺寸设计齿轮是机械运动中常用的元件,广泛应用于各种机械设备中。
齿轮尺寸设计是指在设计齿轮时,确定各项尺寸参数,以满足使用要求并保证齿轮的可靠性和寿命。
以下将介绍齿轮尺寸设计的主要内容。
1. 齿数的确定齿数是齿轮重要的基本参数,齿数的选择取决于传动比和受力情况等因素。
一般来说,齿轮的齿数不能太少,否则会导致传动比不合理。
齿数不能太多,否则将会对齿轮的加工、装配和使用带来困难。
齿数的选择应根据实际情况进行综合考虑。
2. 分度圆直径的选择分度圆直径是齿轮尺寸设计中的关键参数,它决定了齿轮齿数和齿数模数之间的关系。
在齿轮传动中,分度圆直径通常是相同的或成比例的。
分度圆直径的选择应考虑到齿轮的受力情况、齿面接触疲劳寿命、齿轮的制造难度和加工精度等因素。
3. 齿宽的选择齿宽是齿轮传动中的另一个重要参数,它决定了齿轮的承载能力和传动功率。
齿宽的选择应根据齿轮的受力情况、传动功率和速比等因素进行综合考虑。
4. 齿数模数的选择齿数模数是齿轮尺寸设计中的关键参数之一,它代表了齿轮齿面的大小和曲率半径。
齿数模数的选择应根据齿轮的受力、齿数、齿宽和工作条件等因素进行综合考虑。
5. 齿形的设计齿形是齿轮传动中另一个重要的参数,它决定了齿轮的传动性能和运动平稳性。
齿形的设计应满足齿面接触的要求,保证齿轮传动的可靠性。
6. 齿面接触齿面接触是齿轮传动中一个重要的问题,它直接影响齿轮的传动效率和寿命。
在设计齿轮时,要通过分析齿面接触,确定齿面接触区域的大小和位置,以满足齿面接触疲劳寿命的要求。
7. 齿轮精度等级的选择齿轮精度等级是齿轮制造过程中的一个重要参数,它决定了齿轮的制造难度和精度要求。
齿轮精度等级的选择应根据齿轮的使用要求和制造条件等因素进行综合考虑。
齿轮尺寸设计是齿轮传动中的一个重要步骤,它决定了齿轮的传动效率、寿命和可靠性。
在进行齿轮尺寸设计时,应综合考虑齿数、分度圆直径、齿宽、齿数模数、齿形、齿面接触和齿轮精度等级等因素,满足使用要求,并保证齿轮的正常工作。
- 1、下载文档前请自行甄别文档内容的完整性,平台不提供额外的编辑、内容补充、找答案等附加服务。
- 2、"仅部分预览"的文档,不可在线预览部分如存在完整性等问题,可反馈申请退款(可完整预览的文档不适用该条件!)。
- 3、如文档侵犯您的权益,请联系客服反馈,我们会尽快为您处理(人工客服工作时间:9:00-18:30)。
齿轮传动的参数选择(一)齿轮传动设计参数的选择压力角α的选择由机械原理可知,增大压力角α,轮齿的齿厚及节点处的齿廓曲率半径亦皆随之增加,有利于提高齿轮传动的弯曲强度及接触强度。
我国对一般用途的齿轮传动规定的标准压力角为α=20°。
为增强航空用齿轮传动的弯曲强度及接触强度,我国航空齿轮传动标准还规定了α=25°的标准压力角。
但增大压力角并不一定都对传动有利。
对重合度接近2的高速齿轮传动,推荐采用齿顶高系数为1~1.2 ,压力角为16°~18°的齿轮,这样做可增加轮齿的柔性,降低噪声和动载荷。
小齿轮齿数z1的选择若保持齿轮传动的中心距 a 不变,增加齿数,除能增大重合度、改善传动的平稳性外,还可减小模数,降低齿高,因而减少金属切削量,节省制造费用。
另外,降低齿高还能减小滑动速度,减少磨损及减小胶合的可能性。
但模数小了,齿厚随之减薄,则要降低轮齿的弯曲强度。
不过在一定的齿数范围内,尤其是当承载能力主要取决于齿面接触强度时,以齿数多一些为好。
闭式齿轮传动一般转速较高,为了提高传动的平稳性,减小冲击振动,以齿数多一些为好。
小齿轮的齿数可取为z1=20~40。
开式(半开式)齿轮传动,由于轮齿主要为磨损失效,为使轮齿不至过小,故小齿轮不宜选用过多的齿数,一般可取z1=17~20。
为使轮齿免于根切,对于α=20°的标准直齿圆柱齿轮,应取z1≥17。
齿宽系数φd的选择由齿轮的强度计算公式可知,轮齿愈宽,承载能力愈高;但增大齿宽又会使齿面上的载荷分布趋不均匀,故齿宽系数应取得适当。
圆柱齿轮齿宽系数的荐用值见下表。
对于标准圆柱齿轮减速器,齿宽系数取为,所以对于外啮合齿轮传动:。
φa的值规定为0.2,0.25,0.30,0.40,0.50,0.60,0.80,1.0,1.2。
运用设计计算公式时,对于标准减速器,可先选定φa后再用上式计算出相应的φd值。
装置状况两支承相对小齿轮作对称布置两支承相对小齿轮作不对称布置小齿轮作悬臂布置φd0.9~1.4(1.2~1.9)0.7~1.15(1.1~1.65)0.4~0.6注: 1)大、小齿轮皆为硬齿面时,φd取偏下限的数值;若皆为软齿面或仅大齿轮为软齿面时,φd取偏上限的数值;2)括号内的数值用于人字齿轮,此时b为人字齿轮的总宽度;3)金属切削机床的齿轮传动,若传递的功率不大时,φd可小到0.2;4)非金属齿轮可取φd≈0.5~1.2。
圆柱齿轮的计算齿宽b=φd d1,并加以圆整。
为了防止两齿轮因装配后轴向稍有错位而导致啮合齿宽减小,常把小齿轮的齿宽在计算齿宽b的基础上人为地加宽约5~lOmm。
(二)齿轮传动的许用应力本书荐用的齿轮的疲劳极限是用m=3~5mm、α=20°、b=10~50mm、v=10m/s、R a约为0.8 的直齿圆柱齿轮副试件,按失效概率为1%,经持久疲劳试验确定的。
对一般的齿轮传动,因绝对尺寸、齿面粗糙度、圆周速度及润滑等对实际所用齿轮的疲劳极限的影响不大,通常都不予考虑,故只要考虑应力循环次数对疲劳极限的影响即可。
齿轮的许用应力[σ]按下式计算:式中:S—疲劳强度安全系数。
对接触疲劳强度计算,由于点蚀破坏发生后引起噪声、振动增大,并不立即导致不能继续工作的后果,故可取S=S H=1。
但是,如果一旦发生断齿,就会引起严重的故事,因此在进行齿根弯曲疲劳强度计算时取S=S F=1.25~1.5。
K N—考虑应力循环次数影响的系数,称为寿命系数。
弯曲疲劳寿命系数和接触疲劳寿命系数分别见下图。
设n为齿轮的转速,r/min;j为齿轮每转一圈时,同一齿面啮合的次数;L h为齿轮的工作寿命,h,则齿轮的工作应力循环次数N按下式计算:N=60njL h。
σlim—齿轮的疲劳极限。
弯曲疲劳强度极限值用σFE带入,查图<齿轮的弯曲疲劳强度极限>,图中的σFE=σFlim·Y ST,Y ST为试验齿轮的应力校正系数;接触疲劳强度极限值σHlim查图<齿轮的接触疲劳强度极限>。
1—调质钢;球墨铸铁(珠光体、贝氏体);珠光体可锻铸铁2—渗碳淬火的渗碳钢;全齿廓火焰或感应淬火的钢、球墨铸铁3—渗氮的渗氮钢;球墨铸铁(铁素体);灰铸铁;结构钢。
4—氮碳共渗的调质钢、渗碳钢。
弯曲疲劳寿命系数(当N>Nc 时,可根据经验在网纹区内取值)1— 允许一定点蚀时的结构钢;调质钢;球墨铸铁(珠光体、贝氏体);珠光体可锻铸铁;渗碳淬火的渗碳钢2— 结构钢;调质钢;渗碳淬火钢;火焰或感应淬火的钢、球墨铸铁;球墨铸铁(珠光体、贝氏体);珠光体可锻铸铁; 3— 灰铸铁;球墨铸铁(铁素体);渗氮的渗氮钢;调质钢、渗碳钢 4— 氮碳共渗的调质钢、渗碳钢接触疲劳寿命系数(当N>Nc 时,可根据经验在网纹区内取值)图<齿轮的弯曲疲劳强度极限>、图<齿轮的接触疲劳强度极限>所示极限应力值,一般选取其中间偏下值,即在MQ 及ML 中间选值。
使用图<齿轮的弯曲疲劳强度极限>及图<齿轮的接触疲劳强度极限>时,若齿面硬度超出图中荐用的范围,可大体按外插法查取相应的极限应力值。
图<齿轮的弯曲疲劳强度极限>所示为脉动循环应力的极限应力。
对称循环应力的极限应力值仅为脉动循环应力的70%。
夹布塑料的弯曲疲劳许用应力=50MPa,接触疲劳许用应力=110MPa 。
(三)齿轮精度的选择各类机器所用齿轮传动的精度等级范围列于下表中,按载荷及速度推荐的齿轮传动精度等级如下图所示。
各类机器所用齿轮传动的精度等级范围机器名称精度等级机器名称精度等级汽轮机 3~6拖拉机 6~8金属切削机床 3~8通用减速器 6~8航空发动机 4~8锻压机床 6~9轻型汽车 5~8起重机 7~10载重汽车 7~9农业机器 8~11注:主传动齿轮或重要的齿轮传动,偏上限选择;辅助传动齿轮或一般齿轮传动,居中或偏下限选择。
例题如图所示,试设计此带式输送机减速器的高速级齿轮传动。
已知输入功率P1=40kW,小齿轮转速n1=960r/min,齿数比u=3.2,由电动机驱动,工作寿命15年(设每年工作300天),两班制,带式输送机工作平稳,转向不变。
[解]1.选定齿轮类型、精度等级、材料及齿数1)按图所示的传动方案,选用直齿圆柱齿轮传动。
2)考虑此减速器的功率较大,故大、小齿轮都选用硬齿面。
由表<常用齿轮材料及其力学特性>选得大、小齿轮的材料均为40Cr,并经调质及表面淬火,齿面硬度为48~55HRC。
3)选取精度等级。
因采用表面淬火,轮齿的变形不大,不需要磨削,故初选7级精度(GB10095-1988)。
4)选小齿轮齿数z1=24,大齿轮齿数z2=uz1=77。
2.按齿面接触强度设计由设计计算公式(10-9a)进行试算,即1)确定公式内的各计算数值(1)试选载荷系数Kt=1.3;(2)计算小齿轮传递的转矩(3)由表<圆柱齿轮的齿宽系数φd>选取齿宽系数φd=0.9;(4)由表<弹性影响系数Z E>查得材料的弹性影响系数Z E=189.8;(5)由图<齿轮的接触疲劳强度极限>e按齿面硬度中间值52HRC查得大、小齿轮得接触疲劳强度极限σHlim1=σHlim2=1170MPa;(6)计算应力循环次数(7)由图<接触疲劳寿命系数>查得接触疲劳寿命系数1=0.88;2=0.90;(8)计算接触疲劳许用应力取失效概率为1%,安全系数S=1,得2)计算(1)试算小齿轮分度圆直径d1t,代入中较小的值(2)计算圆周速度v(3)计算齿宽b(4)计算齿宽与齿高之比b/h模数齿高b/h=61.55/6.413=9.6(5)计算载荷系数根据v=3.44m/s,7级精度,由动载系数图查得动载系数=1.12;直齿轮,假设F t/b≥100N/mm,由表<齿间载荷分配系数>查得==1.1;由表<使用系数>查得使用系数=1;由表<接触疲劳强度计算用齿向载荷分布系数K H 的简化计算公式>查得=1.43;(由表中6级精度硬齿面齿轮查得,适当加大)由图弯曲疲劳强度计算用齿向载荷分布系数查得=1.37;(由b/h=9.6,=1.43)故载荷系数K==1×1.12×1.1×1.43=1.72 (6)按实际的载荷系数校正所得的分度圆直径,由式(10-10a)得(7)计算模数mm=d1/z1=75.08/24=3.128mm3.按齿根弯曲强度设计弯曲强度的设计公式为mm1)确定公式内的各计算数值(1)由图<齿轮的弯曲疲劳强度极限>d查得大、小齿轮的弯曲疲劳强度极限σFE1=σFE2=680MPa;(2)由图<弯曲疲劳寿命系数>查得弯曲疲劳寿命系数1=0.88;2=0.9;(3)计算弯曲疲劳许用应力取弯曲疲劳安全系数S=1.4,得(4)计算载荷系数KK==1×1.12×1.1×1.37=1.69(5)查取齿形系数由表<齿形系数及应力校正系数>查得Y Fa1=2.65;Y Fa2=2.226 (6)查取应力校正系数由表<齿形系数及应力校正系数>可查得Y Sa1=1.58;Y Sa2=1.764。
(7)计算大小齿轮的并加以比较小齿轮的数值大。
2)设计计算对比计算结果,由齿面接触疲劳强度计算的模数m略大于由齿根疲劳强度计算的模数,由于齿轮模数m的大小主要取决于弯曲强度所决定的承载能力,而齿面接触疲劳强度所决定的承载能力,仅与齿轮直径(即模数与齿数的乘积)有关,可取由弯曲强度算得得模数2.94,并就近圆整为标准值m=3mm,按接触强度算得的分度圆直径d1=75.08mm,由z1=d1/m=75.08/3=25.03,取在z1=25z2=uz1=804.几何尺寸计算1)计算分度圆直径d1=z1m=25×3=75mmd2=z2m=80×3=240mm2)计算中心距a=(d1+d2)/2=(75+240)/2=157.5mm3)计算齿轮宽度b=φd d1=0.9×75=67.5mm圆整,取B2=68mm,B1=73mm。
5.验算合适。