注射剂无菌保证工艺介绍
注射剂无菌保证工艺研究及评判的原那么要求
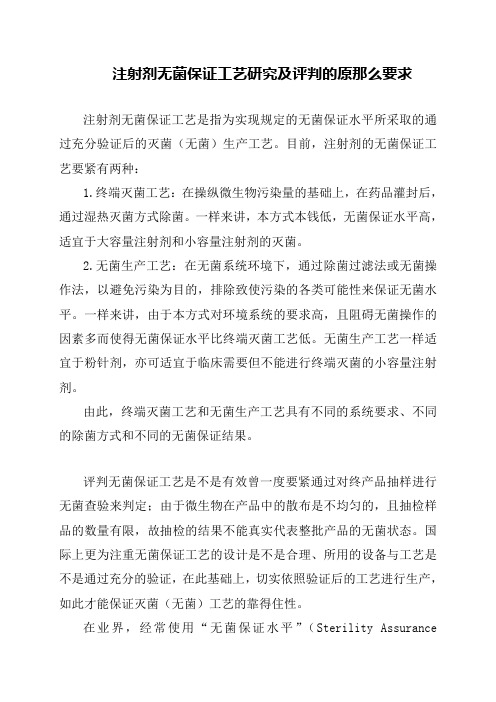
注射剂无菌保证工艺研究及评判的原那么要求注射剂无菌保证工艺是指为实现规定的无菌保证水平所采取的通过充分验证后的灭菌(无菌)生产工艺。
目前,注射剂的无菌保证工艺要紧有两种:1.终端灭菌工艺:在操纵微生物污染量的基础上,在药品灌封后,通过湿热灭菌方式除菌。
一样来讲,本方式本钱低,无菌保证水平高,适宜于大容量注射剂和小容量注射剂的灭菌。
2.无菌生产工艺:在无菌系统环境下,通过除菌过滤法或无菌操作法,以避免污染为目的,排除致使污染的各类可能性来保证无菌水平。
一样来讲,由于本方式对环境系统的要求高,且阻碍无菌操作的因素多而使得无菌保证水平比终端灭菌工艺低。
无菌生产工艺一样适宜于粉针剂,亦可适宜于临床需要但不能进行终端灭菌的小容量注射剂。
由此,终端灭菌工艺和无菌生产工艺具有不同的系统要求、不同的除菌方式和不同的无菌保证结果。
评判无菌保证工艺是不是有效曾一度要紧通过对终产品抽样进行无菌查验来判定;由于微生物在产品中的散布是不均匀的,且抽检样品的数量有限,故抽检的结果不能真实代表整批产品的无菌状态。
国际上更为注重无菌保证工艺的设计是不是合理、所用的设备与工艺是不是通过充分的验证,在此基础上,切实依照验证后的工艺进行生产,如此才能保证灭菌(无菌)工艺的靠得住性。
在业界,经常使用“无菌保证水平”(Sterility AssuranceLevel,SAL)概念来评判灭菌(无菌)工艺的成效,SAL的概念为产品经灭菌/除菌后微生物残余的概率。
该值越小,说明产品中微生物存在的概率越小。
为了保证注射剂的无菌平安性,国际上一致规定,采纳湿热灭菌法的SAL不得大于10-6,即灭菌后微生物存活的概率不得大于百万分之一;而采纳无菌生产工艺的产品,其SAL一样只能达到10-3,故仅限于临床必需注射给药而确实无法耐受终端灭菌的产品。
无菌生产工艺只适用于粉针剂或部份小容量注射剂。
一、注射剂剂型选择的原那么注射剂包括大容量注射剂(50ml以上)、小容量注射剂(20ml以下)和粉针剂三种剂型。
小容量注射剂无菌保证控制措施(最终灭菌)

响产 品 的质 量 。相应 的行业 标准规 定应小 于 lOOC ̄U/g,且原 辅料 行 为 的规 范性 。对 既有 的员 工进 行定 期培训 ,从 而帮助员 工养成
d.制定相应的无菌保证的管理体系对 日常管理进行有效制 果 。对设备状态的 日常管理应制定相应的措施,从而有效控制设
约 。
备 的状态。可适当的采用计算机技术进行 日常灭菌程序的执行、
5 微生 物的负荷
控 制和相 应参数 的 自动 记录等 。
5.1产品灭 菌前微 生物负荷
5.1.4人 员与生 产操作 。风险 :工作人员 日常活动 产生 的污染
十六 条 、第 六 十一条 。
5.1.2生 产环境 。风险 :生产环境 中的 微生 物污染产 品
保证 注射剂 的无 菌水平 ,即是指 通过相 应 的灭菌 工艺使 产 品 在进 行产 品 的生 产 时 ,应保 障生 产 区环境 的干净 整洁 ,从而
的无菌程度达到标准,并通过产品中非无菌品部分的概率进行表 保 障产 品免受环 境 中微 生物 的污 染 。如在生产 区配置相应 的空调
对 清洁效果 产生 影响 的水 温 、时间 、使 用 的清 洁剂 的浓 度 、蒸汽温
a.灭 菌前 微生 物负 荷 ,包 括 :原料 、生 产环 境 、生 产设备 、人员 度等参数,并将这部分参数进行详细的记录 ,做到有据可查。还应
与生产操作 、生产 时限 、灭 菌前微 生物 限度 、微 生物耐 热性 。
示 。如 当 SAL=10r6即是指灭 菌产 品数量为 l06时 ,其 中仅具 有小 净 化 系统 ,且该 系 统 的设 计应 具有 合理 性 和可行性 ,且 符合 相应
于 1个 的活 菌产 品数量 。
化学药品注射剂灭菌和灭菌工艺研究及验证指导原则

化学药品注射剂灭菌和灭菌工艺研究及验证指导原则灭菌工艺的研究与验证是确保注射剂灭菌的有效性和稳定性的关键。
下文将介绍化学药品注射剂灭菌和灭菌工艺的研究及验证指导原则。
一、灭菌方法硫酸化法是一种常见的化学药品注射剂灭菌方法,其原理是在一定的温度和时间条件下,通过硫酸的浓度和反应时间达到灭菌的目的。
硫酸化法的灭菌效果通常良好,且内部流体与过量气体都可以通过使用缓冲盐来被中和。
另一种常用的方法是辐照灭菌,其原理是利用辐射对微生物进行杀灭。
辐照灭菌要求灭菌剂的材料必须与放射物隔离,且需要进行辐射剂量的检测。
二、灭菌工艺的研究1. 灭菌剂选择灭菌剂的选择应该考虑以下因素:(1)药品的特殊性质,例如特殊化学成分、PH值、温度等。
(2)灭菌剂的生物学效应。
(3)灭菌剂的可靠性和性能。
2. 灭菌参数灭菌参数是指灭菌的具体操作条件。
在制定灭菌参数时研究人员应该考虑到一些因素,如:(1)温度。
温度是影响灭菌的主要因素之一。
一般下,灭菌温度降低时,灭菌时间会相应地延长。
(2)压力。
在高温、水蒸气和其他灭菌方法中,压力是保证灭菌效果的重要条件。
一般来说,在不同的药品生产领域中,压力的极限值是不一样的,需要根据不同药品在实践中的表现进行确定。
(3)通气量。
通气量是否合适直接关系到产品中菌落的灭亡情况。
三、灭菌工艺验证灭菌工艺的验证是指通过实验方法验证所制定的灭菌工艺是否能够达到有效的灭菌效果。
灭菌工艺验证应该包括以下步骤:1. 工艺确认工艺确认是指通过实验测试验证所制定的工艺是否能达到预期的灭菌效果,并且符合要求的工艺参数。
工艺确认还包括对制定工艺的初步调试,对灭菌剂的选择及其对生产环境的适应性的验证。
2. 确定最小灭菌剂量最小灭菌剂量是指在给定的灭菌条件下,使无菌品转化为有菌品所需的最小灭菌剂量。
灭菌剂量的确定可以通过针对特定灭菌剂,在不同条件下的生物指标进行实验来完成。
3. 灭菌验证灭菌验证是指在已确立的灭菌工艺参数下,通过实验测试验证所生产出的产品是否能够满足灭菌要求,从而评估具体灭菌方法的效果和稳定性。
注射剂无菌保证工艺
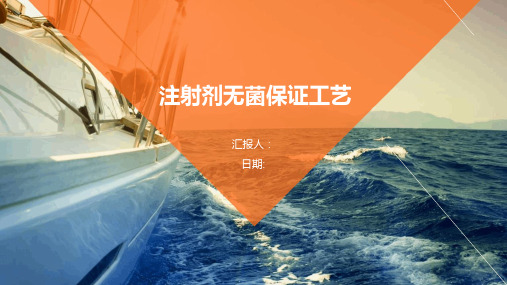
原材料准备与处理设备
01
02
03
原料清洗设备
用于清洗和去除原材料中 的杂质和污染物。
切割和粉碎设备
用于将大块的原材料切割 和粉碎成适当的大小和形 状,以利于后续处理。
混合和均质设备
用于将原材料混合和均质 化,以确保原料的均匀性 和稳定性。
配制与过滤设备
配制设备
用于将原材料按照规定的配方和比例进行配制,形成所需的注射剂成分。
注射剂无菌保证工艺流程
02
原材料准备与处理
01
原材料质量把控
对原材料进行严格的质量把控,确保原材料质量符合规 定标准。
02
原材料清洗与消毒
对原材料进行清洗和消毒,以去除杂质和有害微生物。
03
原材料切割与研磨
根据生产工艺需求,对原材料进行切割和研磨,以获得 合适的粒度和浓度。
配制与过滤
配制
根据配方和工艺要求,将原材料 按照比例混合,并加入适量的溶 剂进行配制。
人员培训与资质管理
培训计划
应制定详细的培训计划,包括无菌知识和技 能培训,以确保所有相关员工都了解并遵循 无菌操作规程。
资质认证
所有从事注射剂无菌生产的人员应经过专业 培训并取得相应的资质认证,确保他们具备 足够的理论知识和实践技能。
工艺验证与持续改进
验证流程
每一批注射剂产品在生产前都应进行无菌保 证工艺的验证,确保生产过程符合无菌要求 。同时,应定期对整个工艺流程进行系统性 的验证。
进行检测
在产品生产过程中及成品入库前,按照检测标准进行全面检测,确 保产品质量符合要求。
产品放行管理
建立严格的产品放行管理制度,对检测合格的产品进行放行,对不 合格产品进行处理并分析原因,防止问题再次发生。
小容量注射剂(聚丙烯安瓿)产品无菌保证措施描述

小容量注射剂(聚丙烯安瓿)产品无菌保证措施描述按照《无菌药品》的要求,无菌药品的生产须满足其质量合预定用途的要求,应当最大限度地降低微生物、各种微粒和热原的污染。
生产人员的技能、所接受的培训及其工作态度是达到上述目标的关键因素,无菌药品的生产必须严格按照精心设计并经验证的方法及规程进行,产品的无菌或其它质量特性绝不能只依赖于任何形式的最终处理或成品检验。
按照上述要求,现将我公司小容量注射剂(聚丙烯安瓿)生产过程中无菌保证措施描述如下:1.人员(生产人员的技能、所接受的培训及其工作态度)小容量注射剂(聚丙烯安瓿)车间共有员工25名(不包括质量管理部人员);其中高中及以上人员17名;11名有制药企业生产经验,其中6名有无菌药品生产的实践经验。
按照公司2018年培训方案,该车间员工均接受GMP及其附录无菌药品的理论和实践培训、药品管理法、岗位职责及相应岗位的SOP培训,培训次数达到246人次,其中包括洁净室消毒、清场清洁、人员更衣规程、无菌操作法及岗位操作SOP;同时对员工还进行了《员工守则》和《员工日常行为规范》教育培训,端正了员工工作态度,使员工真正掌握无菌药品生产人员应具备的基本素质;通过三批(注射用水)模拟生产和三批氯化钾的实际生产现场考核,该车间生产人员已熟练掌握了无菌药品生产的基础知识、基本技能和基本要求。
2.厂房洁净室厂房按照《洁净室施工及验收规范》(GB50591-2010)进行设计、建设;本着尽量减少尘埃聚集及便于清洁的原则,墙面、地面连接处均采用R30的圆弧装修,以降低微生物污染,水池、地漏均安装有空气阻断器防止倒灌,地漏用碘伏和新洁尔灭轮换消毒,且同外部排水系统的连接方式能有效防止微生物的侵入;更衣室按照气锁方式设计、建设,两侧们同时打开时,有报警装置,有效防止了工作服被微生物和微粒污染;洁净区的送风能够确保对周围低级别区域的正压,洁净室与室外压差≥12Pa,不同洁净度的洁净室之间的压差≥12Pa,同一级别的相邻房间之间压差≥3Pa,上述相邻区域之间均安装有压差计,压差数据定时记录,有效地维持了良好的气流方向,保证有效的净化能力;C级区域共有5个百级层流保护装置,分布在灭菌后室、整衣间、聚丙烯颗粒上料间、活性炭称量室、原料称量室及吹灌封的暴露等环节,有效保护了已清洁及灭菌的工衣,与器具及产品直接暴露的操作区域,有效的降低了生产环境对生产过程的微生物污染。
《化学药品注射剂灭菌无菌工艺研究及验证指导原则》

化学药品注射剂灭菌/无菌工艺研究及验证指导原则目录一、概述 (3)二、注射剂湿热灭菌工艺 (4)(一)湿热灭菌工艺的研究 (4)1.湿热灭菌工艺的确定依据 (4)2.微生物污染的监控 (7)(二)湿热灭菌工艺的验证 (9)1.物理确认 (9)2.生物学确认 (13)3.基于风险评估的验证方案设计 (16)三、注射剂无菌生产工艺 (16)(一)无菌生产工艺的研究 (16)1.除菌过滤工艺的研究 (16)2.无菌分装工艺的研究 (18)(二)无菌生产工艺的验证 (18)1.除菌过滤工艺验证 (19)2.无菌工艺模拟试验 (21)1/ 29四、附件 (24)五、参考文献 (27)2/ 291一、概述2无菌药品是指法定药品标准中列有无菌检查项目的制3剂和原料药,一般包括注射剂、无菌原料药及滴眼剂等。
4从严格意义上讲,无菌药品应不含任何活的微生物,但由5于目前检验手段的局限性,绝对无菌的概念不能适用于对6整批产品的无菌性评价,因此目前所使用的“无菌”概念,7是概率意义上的“无菌”。
特定批次药品的无菌特性只能通8过该批药品中活微生物存在的概率低至某个可接受的水平,即无菌保证水平(Sterility Assurance Level, SAL)来表征,910而这种概率意义上的无菌需通过合理设计和全面验证的灭11菌/除菌工艺过程、良好的无菌保证体系以及在生产过程中12执行严格的药品生产质量管理规范(GMP)予以保证。
13本指导原则主要参考国内外相关技术指导原则和标准14起草制订,重点对注射剂常用的灭菌/无菌工艺,即湿热灭15菌为主的终端灭菌工艺(terminal sterilizing process)和无16菌生产工艺(aseptic processing)的研究和验证进行阐述,17旨在促进现阶段化学药品注射剂的研究和评价工作的开展。
18本指导原则主要适用于无菌注射剂申请上市以及上市后变19更等注册申报过程中对灭菌/无菌工艺进行的研究和验证工作,相关仪器设备等的验证及常规再验证不包括在本指2021导原则的范围内。
2020版《化学药品注射剂灭菌无菌工艺研究及验证指导原则》

化学药品注射剂灭菌/无菌工艺研究及验证指导原则目录一、概述 (3)二、注射剂湿热灭菌工艺 (4)(一)湿热灭菌工艺的研究 (4)1.湿热灭菌工艺的确定依据 (4)2.微生物污染的监控 (7)(二)湿热灭菌工艺的验证 (9)1.物理确认 (9)2.生物学确认 (13)3.基于风险评估的验证方案设计 (16)三、注射剂无菌生产工艺 (16)(一)无菌生产工艺的研究 (16)1.除菌过滤工艺的研究 (16)2.无菌分装工艺的研究 (18)(二)无菌生产工艺的验证 (18)1.除菌过滤工艺验证 (19)2.无菌工艺模拟试验 (21)1/ 29四、附件 (24)五、参考文献 (27)2/ 291一、概述2无菌药品是指法定药品标准中列有无菌检查项目的制3剂和原料药,一般包括注射剂、无菌原料药及滴眼剂等。
4从严格意义上讲,无菌药品应不含任何活的微生物,但由5于目前检验手段的局限性,绝对无菌的概念不能适用于对6整批产品的无菌性评价,因此目前所使用的“无菌”概念,7是概率意义上的“无菌”。
特定批次药品的无菌特性只能通8过该批药品中活微生物存在的概率低至某个可接受的水平,即无菌保证水平(Sterility Assurance Level, SAL)来表征,910而这种概率意义上的无菌需通过合理设计和全面验证的灭11菌/除菌工艺过程、良好的无菌保证体系以及在生产过程中12执行严格的药品生产质量管理规范(GMP)予以保证。
13本指导原则主要参考国内外相关技术指导原则和标准14起草制订,重点对注射剂常用的灭菌/无菌工艺,即湿热灭15菌为主的终端灭菌工艺(terminal sterilizing process)和无16菌生产工艺(aseptic processing)的研究和验证进行阐述,17旨在促进现阶段化学药品注射剂的研究和评价工作的开展。
18本指导原则主要适用于无菌注射剂申请上市以及上市后变19更等注册申报过程中对灭菌/无菌工艺进行的研究和验证工作,相关仪器设备等的验证及常规再验证不包括在本指2021导原则的范围内。
注射剂灭菌和灭菌工艺研究及验证指导原则

注射剂灭菌和灭菌工艺研究及验证指导原则注射剂是一类常用的药物剂型,在医疗领域中扮演着重要的角色。
为了保证注射剂的质量和安全性,灭菌是必不可少的一个环节。
注射剂灭菌和灭菌工艺的研究及验证是确保注射剂无菌状态的关键。
本文将介绍注射剂灭菌和灭菌工艺的研究内容和验证指导原则。
一、注射剂灭菌研究注射剂灭菌是指将注射剂中的微生物完全去除或杀灭,使其达到无菌状态。
注射剂灭菌研究主要包括灭菌方法的选择、灭菌剂的选用和灭菌条件的确定。
1. 灭菌方法的选择:常用的注射剂灭菌方法有热灭菌、化学灭菌和辐射灭菌。
不同的方法适用于不同的注射剂类型。
热灭菌是最常用的方法,通过高温杀灭微生物。
化学灭菌利用化学物质来灭菌,常见的化学灭菌剂有过氧化氢和乙醛。
辐射灭菌则是利用电离辐射来杀灭微生物。
2. 灭菌剂的选用:灭菌剂需要具有广谱杀菌活性、对人体无毒副作用以及对药物无不良影响。
常用的灭菌剂有热灭菌中的高温、化学灭菌中的过氧化氢和乙醛,以及辐射灭菌中的电离辐射。
3. 灭菌条件的确定:灭菌条件包括温度、压力、时间和湿度等因素。
不同的注射剂类型和灭菌方法需要不同的灭菌条件。
在确定灭菌条件时,需要考虑灭菌效果、药物稳定性和生产效率等因素。
二、灭菌工艺验证指导原则灭菌工艺验证是验证灭菌过程是否能够有效地杀灭注射剂中的微生物的过程。
灭菌工艺验证指导原则主要包括验证目标的确定、验证方法的选择和验证参数的确定。
1. 验证目标的确定:验证目标是指验证灭菌工艺的有效性。
验证目标应该明确,包括灭菌方法、灭菌剂和灭菌条件等方面。
2. 验证方法的选择:验证方法应该能够真实地模拟实际生产过程,并具有可靠的检测灭菌效果的能力。
常用的验证方法包括生物指示剂法、物理化学指标法和微生物学检测法等。
3. 验证参数的确定:验证参数是指验证过程中需要监测的参数。
验证参数应该与灭菌工艺相关,并具有可测量性和可重复性。
常用的验证参数包括温度、压力、时间、湿度和微生物存活率等。
注射剂的无菌保证与工艺研究

中国 GMP(1998 修订)
洁净 级别 尘粒数 / 立方米
≥ 0.5μm ≥ 5μm
微生物最大允许数
浮游菌 CFU /立方米
沉降菌 CFU/皿 (Ф 90 mm 半 小 时 )
100
10 000 100 000 300 000
3 500
350 000 3 500 000 10 500 000
F0=(SAL+lgN0)×D =(6+ lg100)
×1= 8分钟。
换算成115 ℃下的F0
≤1。
/L115=8/0.25=32分钟。
22
• 残存概率法有效的基础: N0≤100, D
2013-11-5
无菌保证水平应用实例2
• 某输液采用110℃,30分钟的灭菌程序,起始
污染微生物仍为100cfu/瓶,D值为0.5分钟, 经计算此时的无菌保证值和残存微生物污染的 概率为: SAL= F0/D - lgN0 = L110×t /D - lg100 = 0.08×30/0.5-2 = 2.8 残存微生物的概率为10-2.8=0.158% 通过无菌检查的概率为(1-0.158%)20=96.9%。
注射剂的无菌保证 与工艺研究
2008.11
2013-11-5
1
药品管理法与药品生产
• 2001年2月28日修订的《药品管理法》第十
条,经修订后明确要求:
“药品必须按照(原法规:工艺规程)国家药品 标准和国务院药品监督管理部门批准的生产工 艺进行生产,…。改变影响药品质量的生产工 艺的,必须报原批准部门审核批准。”
2013-11-5
16
过度杀灭法
– F0不低于12 – 适用于热稳定性好的产品 – 以彻底杀灭任何污染的微生物为实现 无菌的手段 – 无菌保证值不小于6
注射剂无菌保证工艺研究与验证常见技术问题
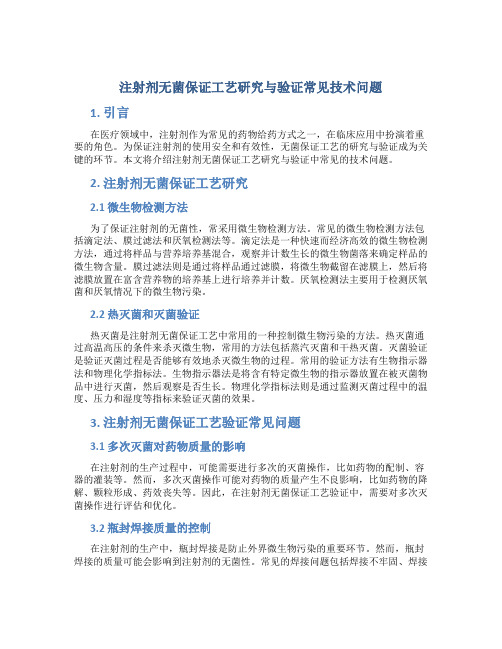
注射剂无菌保证工艺研究与验证常见技术问题1. 引言在医疗领域中,注射剂作为常见的药物给药方式之一,在临床应用中扮演着重要的角色。
为保证注射剂的使用安全和有效性,无菌保证工艺的研究与验证成为关键的环节。
本文将介绍注射剂无菌保证工艺研究与验证中常见的技术问题。
2. 注射剂无菌保证工艺研究2.1 微生物检测方法为了保证注射剂的无菌性,常采用微生物检测方法。
常见的微生物检测方法包括滴定法、膜过滤法和厌氧检测法等。
滴定法是一种快速而经济高效的微生物检测方法,通过将样品与营养培养基混合,观察并计数生长的微生物菌落来确定样品的微生物含量。
膜过滤法则是通过将样品通过滤膜,将微生物截留在滤膜上,然后将滤膜放置在富含营养物的培养基上进行培养并计数。
厌氧检测法主要用于检测厌氧菌和厌氧情况下的微生物污染。
2.2 热灭菌和灭菌验证热灭菌是注射剂无菌保证工艺中常用的一种控制微生物污染的方法。
热灭菌通过高温高压的条件来杀灭微生物,常用的方法包括蒸汽灭菌和干热灭菌。
灭菌验证是验证灭菌过程是否能够有效地杀灭微生物的过程。
常用的验证方法有生物指示器法和物理化学指标法。
生物指示器法是将含有特定微生物的指示器放置在被灭菌物品中进行灭菌,然后观察是否生长。
物理化学指标法则是通过监测灭菌过程中的温度、压力和湿度等指标来验证灭菌的效果。
3. 注射剂无菌保证工艺验证常见问题3.1 多次灭菌对药物质量的影响在注射剂的生产过程中,可能需要进行多次的灭菌操作,比如药物的配制、容器的灌装等。
然而,多次灭菌操作可能对药物的质量产生不良影响,比如药物的降解、颗粒形成、药效丧失等。
因此,在注射剂无菌保证工艺验证中,需要对多次灭菌操作进行评估和优化。
3.2 瓶封焊接质量的控制在注射剂的生产中,瓶封焊接是防止外界微生物污染的重要环节。
然而,瓶封焊接的质量可能会影响到注射剂的无菌性。
常见的焊接问题包括焊接不牢固、焊接不均匀等。
因此,瓶封焊接质量的控制是注射剂无菌保证工艺验证中需要注意的问题之一。
《化学药品注射剂灭菌无菌工艺研究及验证指导原则》

化学药品注射剂灭菌/无菌工艺研究及验证指导原则目录一、概述 (3)二、注射剂湿热灭菌工艺 (4)(一)湿热灭菌工艺的研究 (4)1.湿热灭菌工艺的确定依据 (4)2.微生物污染的监控 (7)(二)湿热灭菌工艺的验证 (9)1.物理确认 (9)2.生物学确认 (13)3.基于风险评估的验证方案设计 (16)三、注射剂无菌生产工艺 (16)(一)无菌生产工艺的研究 (16)1.除菌过滤工艺的研究 (16)2.无菌分装工艺的研究 (18)(二)无菌生产工艺的验证 (18)1.除菌过滤工艺验证 (19)2.无菌工艺模拟试验 (21)1/ 29四、附件 (24)五、参考文献 (27)2/ 291一、概述2无菌药品是指法定药品标准中列有无菌检查项目的制3剂和原料药,一般包括注射剂、无菌原料药及滴眼剂等。
4从严格意义上讲,无菌药品应不含任何活的微生物,但由5于目前检验手段的局限性,绝对无菌的概念不能适用于对6整批产品的无菌性评价,因此目前所使用的“无菌”概念,7是概率意义上的“无菌”。
特定批次药品的无菌特性只能通8过该批药品中活微生物存在的概率低至某个可接受的水平,即无菌保证水平(Sterility Assurance Level, SAL)来表征,910而这种概率意义上的无菌需通过合理设计和全面验证的灭11菌/除菌工艺过程、良好的无菌保证体系以及在生产过程中12执行严格的药品生产质量管理规范(GMP)予以保证。
13本指导原则主要参考国内外相关技术指导原则和标准14起草制订,重点对注射剂常用的灭菌/无菌工艺,即湿热灭15菌为主的终端灭菌工艺(terminal sterilizing process)和无16菌生产工艺(aseptic processing)的研究和验证进行阐述,17旨在促进现阶段化学药品注射剂的研究和评价工作的开展。
18本指导原则主要适用于无菌注射剂申请上市以及上市后变19更等注册申报过程中对灭菌/无菌工艺进行的研究和验证工作,相关仪器设备等的验证及常规再验证不包括在本指2021导原则的范围内。
注射剂无菌保证工艺介绍

注射剂无菌保证工艺介绍注射剂无菌保证工艺是指为实现规定的无菌保证水平所采取的经过充分验证后的灭菌(无菌)生产工艺。
在工业上,无菌保证工艺可分为两类:最终灭菌工艺(terminal sterilization process)和无菌生产工艺(aseptic processing)。
最终灭菌工艺:在控制微生物污染量的基础上将完成最终密封的产品进行适当灭菌的工艺。
一般来说,本方法成本低,无菌保证水平(SAL,Sterility Assurance Level)≤10-6。
无菌生产工艺:在无菌系统环境下通过无菌操作生产无菌产品的方法,以防止污染为目的,消除可能导致污染的各种可能性来保证无菌水平。
目前WHO和欧盟执行的标准是95%可信限度下微生物残存概率不超过0.1%,大概相当于3000瓶产品中不得有1瓶染菌的水平。
本方法对环境系统的要求高,产品存在微生物污染的概率远远高于终端灭菌无菌药品。
1基本原则1.1注射剂剂型选择的原则在遵循剂型选择一般原则的基础上,从无菌保证水平的角度考虑,注射剂剂型选择的一般原则如下:A.首先要考虑被选剂型可采用的灭菌工艺的无菌保证水平的高低。
原则上首选剂型应能采用最终灭菌工艺(F0≥8),以保证SAL≤10-6。
B.对有充分的依据证明不适宜采用终端灭菌工艺(F0≥8)且临床必须注射给药的品种,可考虑选择采用无菌生产工艺的剂型。
通常无菌生产工艺仅限于粉针剂或部分小容量注射剂。
C.注射剂中大容量注射剂、小容量注射剂和粉针剂之间的互改,如无充分的依据,所改剂型的无菌保证水平不得低于原剂型。
1.2无菌工艺的选择原则无菌保证工艺选择原则是:应优先选择无菌保证水平高的最终灭菌工艺,只有在充分的工艺研究证明产品无法耐受各种最终灭菌工艺的前提下,才选择非最终灭菌工艺。
欧洲药品评价局(EMEA)在其规范性文件“选择灭菌方法决策树”(Decision Trees For The Selection of Sterilization Methods (CPMP/QWP/054/98))中将水溶性药品无菌保证工艺分为:①灭菌条件为121℃,15min的湿热灭菌工艺,②灭菌F0值≥8min,SAL≤10-6的湿热灭菌工艺,③采用微生物截留过滤器的除菌过滤工艺,④需要采用无菌原料和预先灭菌的包装材料进行无菌配臵和灌装的工艺;将非水溶性产品,包括非水溶性液体、半固体和干粉的无菌保证工艺分为:①灭菌条件为160℃,120min的干热灭菌工艺,②其他时间和温度组合,SAL≤10-6的干热灭菌工艺,③非干热灭菌方法,如离子辐射吸收剂量≥25KGy的灭菌工艺,④经验证的更低剂量的辐射灭菌工艺,⑤采用微生物截留过滤器的除菌过滤工艺,⑥需要采用无菌原料和预先灭菌的包装材料进行无菌配臵和灌装的工艺。
注射剂的灭菌与无菌技术.

注射剂的灭菌与无菌技术一、概述1.灭菌法:是指用热力或其他适宜方法将物质中的微生物杀灭或除去的方法。
灭菌是生产灭菌制剂的重要过程之一。
2.灭菌标准:微生物包括细菌(致病与非致病菌)、真菌、病毒,这些微生物无所不在,且繁殖速度惊人。
其中细菌的芽胞具有较强的抗热性,不易杀死,因此灭菌效果以杀死芽胞为灭菌标准。
3.注意区分灭菌、防腐、消毒、概念的区别。
(1)灭菌:是制用物理或化学方法将所有致病或非致病的微生物以及细菌的芽孢全部杀灭。
(2)防腐:是指用低温或化学药品防止和抑制微生物生长和繁殖。
(3)消毒:是指用物理和化学的方法将病原微生物杀死。
4.灭菌方法可分为:(1)物理法a.干热灭菌法c.射线灭菌法d.滤过灭菌法(2)化学灭菌法(环境灭菌)a.化学气体灭菌法b.化学药剂灭菌法(3)无菌操作法灭菌方法的选择:根据灭菌的要求及制剂的稳定性两个方面来选择。
二、物理灭菌法(一)湿热灭菌法本方法特点:由于蒸气潜热大,穿透力强,容易使蛋白质变性或凝固,灭菌效率高。
1.热压灭菌法:是用大于常压的饱和水蒸汽加热杀灭微生物的方法,是最可靠的灭菌方法。
(1)常用的几个压力与温度及时间的对应关系115℃~67 kpa~30min121℃~97 kpa~20min126℃~139 kpa~15min(2)灭菌设备-灭菌柜操作注意事项A.必须使用饱和蒸气B.必须将柜内空气排净C.压力回零后再开启柜门,防止带压操作D.防止过早全部开启柜门造成骤然降温,瓶子破裂(3)影响灭菌效果因素A.细菌的种类与数量B.药物性质与灭菌时间C.蒸气的性质D.介质的性质2.流通蒸气灭菌法:指在常压下100℃流通蒸汽加热杀灭微生物的方法。
杀灭时间为:30~60min。
特点:1)适用于对热不稳定的药品2)不能杀灭所有细菌3)需加入抑菌剂或避菌操作、无菌操作3.煮沸灭菌法:把灭菌物品放入沸水中加热灭菌的方法。
灭菌时间为:30~60min。
灭菌效果差。
4.低温间歇灭菌法:作法:a.温度60~80℃1hr灭菌b.室温或37℃下放置24hr,再进行上述条件下的灭菌c.反复操作3~5次(二)干热灭菌法干热灭菌法分为:火焰灭菌法、干热空气灭菌法※1.细菌对热敏感性:杀灭繁殖型细菌需100℃、干热1hr杀死;芽胞菌:按药典规定:160℃~170℃需2hr以上、170℃~180℃需1hr以上、250℃需45 min。
注射剂灭菌和灭菌工艺研究及验证指导原则

注射剂灭菌和灭菌工艺研究及验证指导原则引言:注射剂是一种常见的药物给药形式,广泛应用于临床治疗。
为了确保注射剂的安全性和有效性,灭菌是一个至关重要的环节。
本文将以注射剂灭菌和灭菌工艺研究及验证指导原则为主题,探讨灭菌的重要性、灭菌工艺研究的方法以及灭菌工艺验证的指导原则。
一、灭菌的重要性灭菌是指通过适当的方法杀灭或去除注射剂中的微生物,以确保药品的无菌状态。
灭菌的重要性主要体现在以下几个方面:1. 防止微生物感染:微生物污染可能导致严重的感染和并发症,对患者的健康造成威胁。
2. 保证药物有效性:某些药物在与微生物接触后可能失去活性,灭菌可以防止这种情况的发生,保证药物的疗效。
3. 维护药品质量:灭菌可以有效延长药品的保质期,保证药品在储存和使用过程中不会受到微生物的污染。
二、灭菌工艺研究的方法灭菌工艺研究是为了确定适合注射剂的灭菌工艺条件,确保灭菌的有效性和可行性。
一般而言,灭菌工艺研究包括以下几个方面的内容:1. 温度和压力条件的确定:通过研究不同温度和压力条件下的灭菌效果,确定最佳的灭菌温度和压力。
2. 灭菌时间的确定:通过不同时间长度的灭菌实验,确定适宜的灭菌时间,以确保灭菌效果。
3. 灭菌剂量的确定:通过不同剂量的灭菌试验,确定适宜的灭菌剂量,保证药物中的微生物被彻底杀灭。
4. 灭菌方法的选择:根据不同药物的特点和要求,选择适合的灭菌方法,如热灭菌、辐射灭菌等。
5. 灭菌工艺参数的优化:通过多次试验和参数调整,优化灭菌工艺参数,提高灭菌效果和工艺可行性。
三、灭菌工艺验证的指导原则灭菌工艺验证是为了验证灭菌工艺的有效性和可行性,确保药物的无菌状态。
以下是灭菌工艺验证的指导原则:1. 选择合适的验证方法:根据灭菌工艺的特点和要求,选择适合的验证方法,如生物指示器法、物理化学指标法等。
2. 设计合理的验证方案:根据验证目标和要求,设计合理的验证方案,包括验证样本的选取、验证参数的确定等。
3. 严格执行验证方案:在验证过程中,按照验证方案的要求,准确执行各项操作,确保验证结果的准确性和可靠性。
化学药品注射剂灭菌无菌工艺研究及验证指导原则
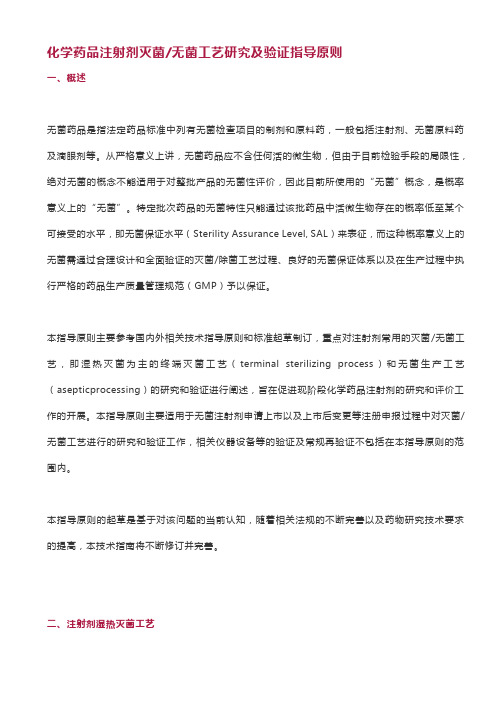
化学药品注射剂灭菌/无菌工艺研究及验证指导原则一、概述无菌药品是指法定药品标准中列有无菌检查项目的制剂和原料药,一般包括注射剂、无菌原料药及滴眼剂等。
从严格意义上讲,无菌药品应不含任何活的微生物,但由于目前检验手段的局限性,绝对无菌的概念不能适用于对整批产品的无菌性评价,因此目前所使用的“无菌”概念,是概率意义上的“无菌”。
特定批次药品的无菌特性只能通过该批药品中活微生物存在的概率低至某个可接受的水平,即无菌保证水平(Sterility Assurance Level, SAL)来表征,而这种概率意义上的无菌需通过合理设计和全面验证的灭菌/除菌工艺过程、良好的无菌保证体系以及在生产过程中执行严格的药品生产质量管理规范(GMP)予以保证。
本指导原则主要参考国内外相关技术指导原则和标准起草制订,重点对注射剂常用的灭菌/无菌工艺,即湿热灭菌为主的终端灭菌工艺(terminal sterilizing process)和无菌生产工艺(asepticprocessing)的研究和验证进行阐述,旨在促进现阶段化学药品注射剂的研究和评价工作的开展。
本指导原则主要适用于无菌注射剂申请上市以及上市后变更等注册申报过程中对灭菌/无菌工艺进行的研究和验证工作,相关仪器设备等的验证及常规再验证不包括在本指导原则的范围内。
本指导原则的起草是基于对该问题的当前认知,随着相关法规的不断完善以及药物研究技术要求的提高,本技术指南将不断修订并完善。
二、注射剂湿热灭菌工艺(一)湿热灭菌工艺的研究1. 湿热灭菌工艺的确定依据灭菌工艺的选择一般按照灭菌工艺选择的决策树(详见附件1)进行,湿热灭菌工艺是决策树中首先考虑的灭菌方法。
湿热灭菌法是利用饱和蒸汽、过热水喷淋等手段使微生物菌体中的蛋白质、核酸发生变性从而杀灭微生物的方法。
注射剂的湿热灭菌工艺应首选过度杀灭法,即F0(标准灭菌时间)值大于12的灭菌工艺;对热不稳定的药物,可以选择残存概率法,即F0值大于8的灭菌工艺。
无菌工艺概述

无菌工艺概述
注射剂可分为溶液型、注射用无菌粉末、注射用浓溶液以及乳剂、混悬剂、注射用油溶液、注射用微球、胶束、纳米粒、脂质体等特殊类型载药系统的注射剂
无菌药品质量保证的重点在于微生物、细菌内毒素和微粒的污染控制,同时也需要关注混淆和交叉污染。
采用最终灭菌工艺的为最终灭菌产品;部分或全部工序采用无菌生产工艺的为非最终灭菌产品
灭菌方法通常包括湿热、干热、辐射、气体、过滤灭菌法采用湿热灭菌方法进行最终灭菌的,通常标准灭菌时间FO值应当大于8分钟,流通蒸汽处理不属于最终灭菌。
最终灭菌产品中的微生物存活概率(即无菌保证水平,SAL)不得高于10-6。
采用无菌生产工艺生产的产品比最终灭菌工艺生产的产品微生物污染风险高,影响因素多。
在无菌灌装工艺中,产品、直接接触药品的包装材料分别灭菌后,在A级洁净区下灌装或分装,以降低微生物污染的风险。
空调系统的停机问题,因故障停机再次开启空气净化系统,应当进行必要的测试以确认仍能达到规定的洁净度级别要求,必要的测试,在文件中应有规定,开机后需做的项目,建议保持每周开机运行维护。
无菌粉针剂生产工艺特点
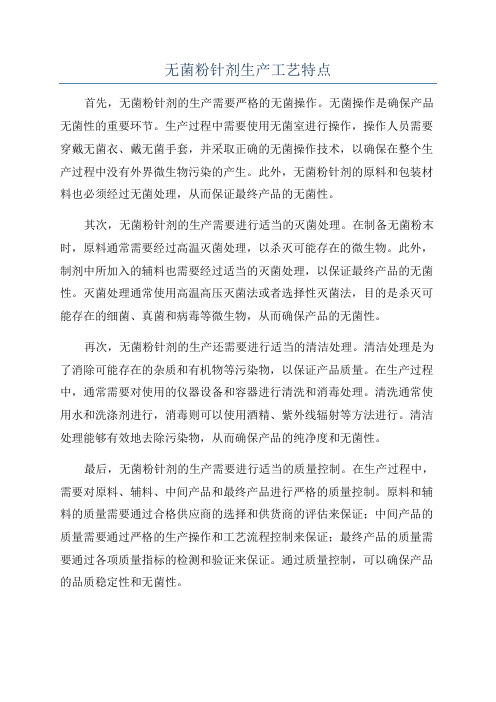
无菌粉针剂生产工艺特点首先,无菌粉针剂的生产需要严格的无菌操作。
无菌操作是确保产品无菌性的重要环节。
生产过程中需要使用无菌室进行操作,操作人员需要穿戴无菌衣、戴无菌手套,并采取正确的无菌操作技术,以确保在整个生产过程中没有外界微生物污染的产生。
此外,无菌粉针剂的原料和包装材料也必须经过无菌处理,从而保证最终产品的无菌性。
其次,无菌粉针剂的生产需要进行适当的灭菌处理。
在制备无菌粉末时,原料通常需要经过高温灭菌处理,以杀灭可能存在的微生物。
此外,制剂中所加入的辅料也需要经过适当的灭菌处理,以保证最终产品的无菌性。
灭菌处理通常使用高温高压灭菌法或者选择性灭菌法,目的是杀灭可能存在的细菌、真菌和病毒等微生物,从而确保产品的无菌性。
再次,无菌粉针剂的生产还需要进行适当的清洁处理。
清洁处理是为了消除可能存在的杂质和有机物等污染物,以保证产品质量。
在生产过程中,通常需要对使用的仪器设备和容器进行清洗和消毒处理。
清洗通常使用水和洗涤剂进行,消毒则可以使用酒精、紫外线辐射等方法进行。
清洁处理能够有效地去除污染物,从而确保产品的纯净度和无菌性。
最后,无菌粉针剂的生产需要进行适当的质量控制。
在生产过程中,需要对原料、辅料、中间产品和最终产品进行严格的质量控制。
原料和辅料的质量需要通过合格供应商的选择和供货商的评估来保证;中间产品的质量需要通过严格的生产操作和工艺流程控制来保证;最终产品的质量需要通过各项质量指标的检测和验证来保证。
通过质量控制,可以确保产品的品质稳定性和无菌性。
总之,无菌粉针剂的生产工艺具有无菌操作、灭菌处理、清洁处理和质量控制等特点。
通过严格的无菌操作、适当的灭菌处理、适当的清洁处理和严格的质量控制,可以保证产品的无菌性和质量稳定性,从而满足临床使用的要求。
为了确保无菌粉针剂的安全性和有效性,生产企业需要严格遵守相关法律法规和规范要求,并进行相应的质量控制和管理。
针剂无菌操作方法有哪些

针剂无菌操作方法有哪些针剂无菌操作方法主要包括以下几个步骤:1. 必要的准备工作:戴上无菌手套,并将所需的针头、针筒等器械放在刮刀上,进行高压蒸汽灭菌处理。
2. 准备工作台面:用无尘纸覆盖操作台面,然后用70%的乙醇擦拭操作区域,保持清洁无菌。
3. 维持无菌操作区域:在操作前,先拉上手术袍,佩戴口罩,头套,将无尘帽提高到合适位置,面罩或者护目镜遮盖住视线.4. 打开包装:将药品与所需的针头、针筒等器械放置在操作台上,用洁净的无菌毛巾合理掩盖。
打开需要应用的针剂包装的若干便。
5. 明白剂量:读懂了药品使用说明中的用量,最后量取所需要的剂量。
6. 准备药品:戴好无菌手套,保持干净手指在容器外壁。
在容器内自有培养菌物质时,可第一次用局灭菌的无菌空心针吸液量,告诉你的配制药物,再注射到刚准备好的无菌容器中,供应液药物最高容量不能超过内壁1/2, 以防药液撒在容器盖筋上分解氧化。
7. 抽取针剂:用洁净的无菌针头,抽取所需的药液。
注意必须插入容器中,以避免气体进入针筒,导致露点吸音。
用皖水泵或贝尔针套液抽摆放胰岛素。
8. 准备针头:将药液注入到无菌注射器中(使用拐轮/旋钮注射器时,用拧紧拧紧药液盖,在注射器上,注射器壁厚度-厚度来算方便调节需要的药液注射速度)。
9. 准备病人:确定病人的身份和接受治疗的部位。
准备要求用察找方式核对标签上的数字、科室、床号等信息。
10. 注射针剂:用无菌针头,刺入病人的皮肤,然后缓慢注射药液。
结束后,轻轻拉出。
最后,将所有已使用过的器材以及其它垃圾物品,放入封闭好的医疗垃圾桶中,即可完成针剂无菌操作。
注意在整个过程中保持无菌环境的稳定,并且严格按照操作规范进行操作,以确保针剂的无菌性。
无菌保证工艺

无菌保证工艺
无菌生产工艺的验证要求 无菌生产工艺: 过滤除菌+无菌生产工艺 无菌组装工艺
无菌保证工艺
选择无菌生产工艺的前提:
➢ 同品种均未采用最终灭菌工艺 ➢ 经过深入的研究(化学反应机理、穷尽方法并
证明在合理的技术条件下无法有效阻止化学反 应的发生) ➢ 临床需要注射剂型
无菌保证工艺
小容量注射剂和冻干粉针剂验证项目差异
不同剂型 验证项目
小容量注射剂
冻干粉针剂
过滤系统验证 培养基灌装验证
需要 验证至灌装结束
需要
除灌装外,尚包括部 分冻干程序,目的是 尚要考察冻干区域的 装载和卸载过程
无菌保证工艺
无菌组装工艺
➢ 严格执行药品生产质量管理规范(GMP)是无菌 粉针剂生产的重要质量保证 ➢ 生产工艺的控制和验证要求对不同的无菌组装 产品是一致的
无菌保证工艺
➢ 热穿透试验-测定产品实际温度和F0值
以热分布(空载、满载)试验结果为基础,进一步 确定实际样品(或模拟样品)的冷点(与平均温度 差超过1.5度为冷点)
重要标准 产品中F0 MEAN± 3SD 符合注册F0值标准
无菌保证工艺
注意:
同品种不同浓度 — 考察不同浓度对热穿透的影响 不同包装规格 — 进行最大和最小包装规格的试验 不同装载量 — 进行最小和最大装载量的试验 不同灭菌温度 —进行最高温度条件下的试验
明确要求进行制备工艺研究 包括:制备工艺的选择
工艺参数的确定 工艺的验证 注射剂灭菌工艺及其验证
无菌保证工艺
一、前言
➢ 现行法规要求
《药品注册管理办法》(局令第28号) 附件2 申报资料项目8 制剂处方及工艺的研究资料及文献资料: 应包括起始物料、处方筛选、生产工艺及验证资料
- 1、下载文档前请自行甄别文档内容的完整性,平台不提供额外的编辑、内容补充、找答案等附加服务。
- 2、"仅部分预览"的文档,不可在线预览部分如存在完整性等问题,可反馈申请退款(可完整预览的文档不适用该条件!)。
- 3、如文档侵犯您的权益,请联系客服反馈,我们会尽快为您处理(人工客服工作时间:9:00-18:30)。
注射剂无菌保证工艺介绍注射剂无菌保证工艺是指为实现规定的无菌保证水平所采取的经过充分验证后的灭菌(无菌)生产工艺。
在工业上,无菌保证工艺可分为两类:最终灭菌工艺(terminal sterilization process)和无菌生产工艺(aseptic processing)。
最终灭菌工艺:在控制微生物污染量的基础上将完成最终密封的产品进行适当灭菌的工艺。
一般来说,本方法成本低,无菌保证水平(SAL,Sterility Assurance Level)≤10-6。
无菌生产工艺:在无菌系统环境下通过无菌操作生产无菌产品的方法,以防止污染为目的,消除可能导致污染的各种可能性来保证无菌水平。
目前WHO和欧盟执行的标准是95%可信限度下微生物残存概率不超过0.1%,大概相当于3000瓶产品中不得有1瓶染菌的水平。
本方法对环境系统的要求高,产品存在微生物污染的概率远远高于终端灭菌无菌药品。
1基本原则1.1注射剂剂型选择的原则在遵循剂型选择一般原则的基础上,从无菌保证水平的角度考虑,注射剂剂型选择的一般原则如下:A.首先要考虑被选剂型可采用的灭菌工艺的无菌保证水平的高低。
原则上首选剂型应能采用最终灭菌工艺(F0≥8),以保证SAL≤10-6。
B.对有充分的依据证明不适宜采用终端灭菌工艺(F0≥8)且临床必须注射给药的品种,可考虑选择采用无菌生产工艺的剂型。
通常无菌生产工艺仅限于粉针剂或部分小容量注射剂。
C.注射剂中大容量注射剂、小容量注射剂和粉针剂之间的互改,如无充分的依据,所改剂型的无菌保证水平不得低于原剂型。
1.2无菌工艺的选择原则无菌保证工艺选择原则是:应优先选择无菌保证水平高的最终灭菌工艺,只有在充分的工艺研究证明产品无法耐受各种最终灭菌工艺的前提下,才选择非最终灭菌工艺。
欧洲药品评价局(EMEA)在其规范性文件“选择灭菌方法决策树”(Decision Trees For The Selection of Sterilization Methods (CPMP/QWP/054/98))中将水溶性药品无菌保证工艺分为:①灭菌条件为121℃,15min的湿热灭菌工艺,②灭菌F0值≥8min,SAL≤10-6的湿热灭菌工艺,③采用微生物截留过滤器的除菌过滤工艺,④需要采用无菌原料和预先灭菌的包装材料进行无菌配臵和灌装的工艺;将非水溶性产品,包括非水溶性液体、半固体和干粉的无菌保证工艺分为:①灭菌条件为160℃,120min的干热灭菌工艺,②其他时间和温度组合,SAL≤10-6的干热灭菌工艺,③非干热灭菌方法,如离子辐射吸收剂量≥25KGy的灭菌工艺,④经验证的更低剂量的辐射灭菌工艺,⑤采用微生物截留过滤器的除菌过滤工艺,⑥需要采用无菌原料和预先灭菌的包装材料进行无菌配臵和灌装的工艺。
文件指出,无菌制剂应采用最终灭菌的工艺。
只有当产品稳定性问题不可能采用最终灭菌工艺时,才能选择替代灭菌工艺、除菌过滤及无菌生产工艺。
药品是否能耐受最终灭菌工艺,除了取决于药物活性成分本身的化学性质以外,很大程度还与活性成分存在的环境,如药品溶剂、辅料、氧气、原料药中的杂志等密切相关。
只有理论和实践都证明即使采用了各种可行的技术方法如除氧、选择合适的溶剂或辅料等之后,活性成分依然无法耐受最终灭菌工艺,才能选择无菌保证水平较低的除菌过滤等无菌生产工艺。
对于注射剂,如果已经证明活性成分可耐受适当的最终灭菌工艺,则不应选择质量风险相对更大的低于药典标准的灭菌工艺或无菌生产工艺。
2注射剂无菌保证工艺的技术要求2.1大容量注射剂应采取最终灭菌工艺,建议首选过度杀灭法(F0≥12),如产品不能耐受过度杀灭的条件,可考虑采用残存概率法(8≤F0≤12),但均应保证产品灭菌后的SAL不大于10-6。
采用其他F0值小于8的终端灭菌条件的工艺,原则上不予认可。
如产品不能耐受最终灭菌工艺条件,首先应优化处方工艺,以改善制剂的耐热性。
如果确实无法耐受,则应考虑其他剂型。
2.2粉针剂采用无菌生产工艺的粉针剂,应能保证SAL≤10-3。
这主要依赖于无菌生产工艺是否严格按照GMP要求进行生产和验证。
2.3小容量注射剂应首选最终灭菌工艺,相关技术要求同大容量注射剂。
如有充分的依据证明不能采用最终灭菌工艺的品种,且为临床必须注射给药的品种,可考虑采用无菌生产工艺,相关技术要求同粉针剂。
对于过滤除菌工艺同时采用了流通蒸汽辅助灭菌的品种,建议修改为最终灭菌工艺,技术要求同大容量注射剂;对确实无法采用最终灭菌工艺的品种,应修改为无菌生产工艺,技术要求同粉针剂。
对于采用无菌生产工艺生产的小容量注射剂,生产线的验证应结合无菌生产工艺进行。
3.最终灭菌工艺3.1无菌检查的局限性数学公式(p+q)n=1定量描述了无菌产品污染率q、取样量即样本数n和受污染批次“通过”无菌检查的概率p之间的关系。
所以,基于抽样检验的无菌检查无法保证产品达到药典规定的无菌保证水平,只有通过证明无菌保证工艺的可靠性来推断产品无菌的无菌保证水平。
3.2灭菌的基本原理各种灭菌方法使微生物死亡的速度都符合一级动力学方程。
以湿热灭菌为例,在特定灭菌温度下,某种微生物孢子的死亡速度仅与这个时刻孢子的浓度有关。
用数学模型可以表示为:lgN=lgN0-ktN 产品内微生物的残存数N0灭菌开始时产品内微生物数t 累计灭菌时间k 常数,与微生物耐热性、灭菌温度相关当N小于1时,其含义为产品存在微生物的概率。
灭菌率(LT)灭菌率是表示不同灭菌温度所对应的灭菌效果的重要函数。
表1给出了以121℃为标准,Z=10℃时不同温度下的灭菌率。
表1 灭菌温度与灭菌率灭菌温度(T,℃)灭菌率(LT)100 0.008110 0.08112 0.13114 0.19116 0.32118 0.50120 0.79121 1122 1.26标准灭菌时间(F0值)标准灭菌时间F0值是指在121℃下的灭菌时间。
它的意义在于将不同灭菌温度条件下、灭菌不同时间的灭菌效果,统一表达成为121℃下灭菌所需的时间。
F0=LT×tF0标准灭菌时间LT 灭菌率t 灭菌时间如118℃下灭菌24分钟的F0值计算:118℃的灭菌率为0.50,F0=0.50×24=12分钟,即表示118℃下灭菌24分钟相当于121℃下灭菌12分钟。
F0值是衡量、区分无菌保证工艺属于最终灭菌工艺还是无菌生产工艺的重要指标。
美国FDA和欧盟习惯上都将灭菌F0值是否≥8分钟视为区别最终灭菌工艺和无菌生产工艺的标志。
微生物耐热参数(D值)D值是指在特定灭菌条件下,使微生物数量下降一个对数单位或杀灭90%所需的时间(分钟)。
无菌保证值将无菌保证水平(SAL)的负对数值定义为无菌保证值。
无菌保证值=F0/D-lgN0无菌保证值与标准灭菌时间(F0),灭菌开始时产品中的污染微生物数量(N0)和污染微生物的耐热参数(D)密切相关。
该公式是确定灭菌工艺最重要的理论基础。
根据灭菌工艺所提供的F0值,还可以将最终灭菌工艺进一步分为过度杀灭灭菌工艺和残存概率灭菌工艺。
3.3残存概率灭菌工艺美国药典定义的残存概率灭菌工艺指F0值小于12分钟的湿热灭菌程序。
适用于热稳定性不是太好的品种,如复方氨基酸注射液、脂肪乳注射液、葡萄糖注射液和含维生素等的小容量注射液。
对建立在污染菌残存概率基础上的灭菌工艺而言,产品灭菌前污染微生物的水平及其耐热性是确定灭菌工艺是否提供足够无菌保证水平的决定性因素。
因此,生产工艺过程应当将避免产品被耐热菌污染放在首位,而不能仅依靠最终灭菌去消除污染。
3.4过度杀灭灭菌工艺过度杀灭是指F0值≥12min的灭菌工艺。
热稳定性好的产品才能采用过度杀灭工艺。
采用过度杀灭灭菌工艺时,即使不考虑产品灭菌前的污染状况,也能保证SAL≤10-6。
当然,这并不意味着生产过程中对污染可以完全不加以控制。
从控制热源的角度,也应当遵循工艺卫生规范,控制产品的微生物污染。
4.无菌生产工艺如果产品的热稳定性不佳,无法耐受达到药典要求的无菌保证水平的最低F0值时,方可采用无菌生产工艺。
无菌生产工艺系指必须在无菌控制条件下生产无菌制剂的方法,无菌分装及无菌冻干是最常见的无菌生产工艺。
后者在工艺过程中需采用过滤除菌法。
无菌生产工艺特别强调维持生产环境的无菌洁净状态并予以监控,以及对药液过滤前微生物污染水平的监控。
国外通常将这两项指标列入注册标准,尽管其在成品检验中无法体现出来。
目前国际上较普遍的非最终灭菌无菌生产的无菌保证标准是在95%臵信限下产品中微生物残存概率不超过0.1%。
无菌生产工艺应定期进行验证,包括对环境空气过滤系统有效性验证及培养基模拟灌装试验。
5. 无菌保证工艺的验证灭菌产品的无菌保证不能依赖于最终产品的无菌检验,而是取决于生产过程中采用合格的灭菌工艺、严格的GMP管理和良好的无菌保证体系。
灭菌程序的验证是无菌保证的必要条件。
灭菌程序经验证后,方可交付正式使用。
验证内容包括:(1)撰写验证方案及制定评估标准;(2)确认灭菌设备技术资料齐全、安装正确,并能处于正常运行(安装确认);(3)确认关键控制设备和仪表能在规定的参数范围内正常运行(运行确认);(4)采用被灭菌物品或模拟物品进行重复试验,确认灭菌效果符合规定(性能确认);(5)汇总并完善各种文件和记录,撰写验证报告。
5.1最终灭菌工艺的验证灭菌工艺验证的前提是生产设备已经完成安装确认和运行确认。
最终灭菌工艺验证主要包括以下4部分试验:①空载热分布试验;②装载(满载)热分布试验;③热穿透试验;④微生物挑战试验。
不同试验的目的不同,最终灭菌工艺验证实际上是通过上述4部分试验过程来确认生产的药品可以达到规定的无菌保证水平。
下面是4部分试验各自的目的、研究内容和评价要点。
5.1.1空载热分布试验空载热分布试验的目的是确定灭菌腔室内温度分布的均匀性。
通过试验证明灭菌设备的均匀性和重现性,应至少连续运行3次同一个完整的灭菌程序。
由于很多情况下该灭菌设备可能运行多种灭菌程序,故可以根据灭菌设备的构造特点,在科学性有保证的前提下,选择一个有代表性的灭菌程序进行空载热分布试验。
若进行的灭菌程序与申报的灭菌参数不同,则应说明理由。
5.1.2装载(满载)热分布试验装载热分布试验的目的是确定有装载的情况下灭菌腔室内温度分布的均匀性,个别位臵的温度与平均温度的差异,是否存在冷点和热点。
应根据空载热分布试验的结果制定装载热分布试验方案,至少应进行满载条件下的热分布试验。
若申报产品有多个装量规格,必要时需分别进行满载各种装量规格产品(通常是模拟产品)的热分布试验。
在规定的灭菌程序运行达到灭菌温度时,个别点的温度与平均温度有显著差异时,该点为冷点或热点,为证明灭菌设备的均匀性和重现性,应至少连续运行3次完整的申报的灭菌程序。