不锈钢零件机加工工艺
不锈钢薄壁螺母零件加工工艺设计

合精度要求 。通过对该薄壁零件的加工 , 为进一步研 究类似零件 的/ - 制定更加合理的加工工艺 , j r,  ̄ 积累
宝贵 的实 践 经验 。
图 Байду номын сангаас 零 件 工 装 图
工装设计 的思路为用零件 18 m的外 圆和 参 考 文 献 : 2 m
两端 面 定 位 , 以左 端 面 为定 位 基 准 , 以右端 面作 为受 力 面 , 样安 排 , 这 受力 得 到 了很 大 的改 善 。 做 工装 1时 , 内 台阶端 面 和 ①18mm 内孔要 其 2
证 总长 。
在 试制 过程 中 , 现 以下 问题 : 发
’
( )由于使用 C 2 车床 , 以钻头直径不能太 1 60 所 大, 采用先钻后镗 的方法 , 这样 车削余量较大 。不锈 钢材料具有本身切削力大 、 切削温度高、 切屑不易折
断、 易粘 刀 、 刀具 易 磨损 的特点 。因刀具 易磨 损 , 以 所 效 率不 高 。 ( )车 内 螺 纹 时 采 用 三 爪 卡 盘 夹 持 18ml 2 2 i l
收稿 日期:0 1 0 — 2 2 1— 5 1
刀具的磨损。
作者 简介 : 淑叶(98 )女 , 鲁 17一 , 讲师 , 学士学位 , 主要从事数控 加工 与数控工 艺研究 。
15 3
E u p n Ma u a t n e h oo y No8, 01 q i me t n f e r gT c n lg . 2 i 1
图 1 薄壁螺母零件
的外圆 , 以工件 的左端面定位在卡爪的台阶面上 , 由 于 车螺 纹 切 削力 较 大 , 如果 在 卡 盘 上夹 紧 过 大 , 零件 就会产生变形 ,从而影响工件 的尺寸精度和形状精 度。如果在卡盘上夹得不紧 , 在车削时有可能使零件 松 动而 无法 完成 车 削 。
不锈钢车削加工特点及加工工艺
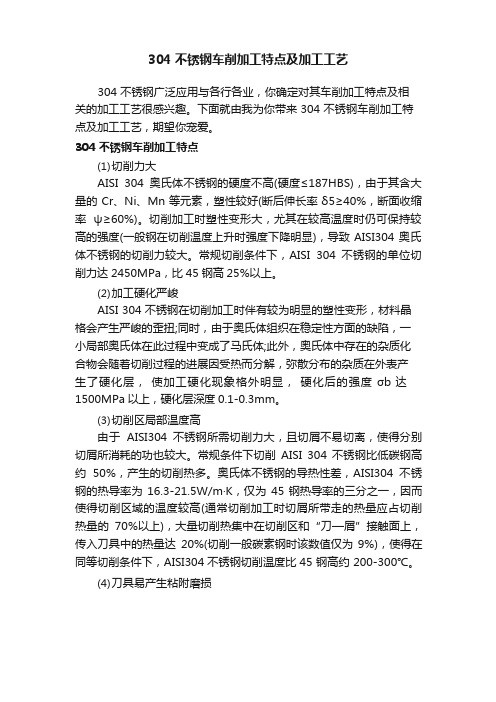
304 不锈钢车削加工特点及加工工艺304 不锈钢广泛应用与各行各业,你确定对其车削加工特点及相关的加工工艺很感兴趣。
下面就由我为你带来 304 不锈钢车削加工特点及加工工艺,期望你宠爱。
304 不锈钢车削加工特点(1)切削力大AISI 304 奥氏体不锈钢的硬度不高(硬度≤187HBS),由于其含大量的 Cr、Ni、Mn 等元素,塑性较好(断后伸长率δ5≥40%,断面收缩率ψ≥60%)。
切削加工时塑性变形大,尤其在较高温度时仍可保持较高的强度(一般钢在切削温度上升时强度下降明显),导致 AISI304 奥氏体不锈钢的切削力较大。
常规切削条件下,AISI 304 不锈钢的单位切削力达 2450MPa,比 45 钢高 25%以上。
(2)加工硬化严峻AISI 304 不锈钢在切削加工时伴有较为明显的塑性变形,材料晶格会产生严峻的歪扭;同时,由于奥氏体组织在稳定性方面的缺陷,一小局部奥氏体在此过程中变成了马氏体;此外,奥氏体中存在的杂质化合物会随着切削过程的进展因受热而分解,弥散分布的杂质在外表产生了硬化层,使加工硬化现象格外明显,硬化后的强度σb达1500MPa 以上,硬化层深度 0.1-0.3mm。
(3)切削区局部温度高由于AISI304 不锈钢所需切削力大,且切屑不易切离,使得分别切屑所消耗的功也较大。
常规条件下切削AISI 304 不锈钢比低碳钢高约50%,产生的切削热多。
奥氏体不锈钢的导热性差,AISI304 不锈钢的热导率为 16.3-21.5W/m·K,仅为 45 钢热导率的三分之一,因而使得切削区域的温度较高(通常切削加工时切屑所带走的热量应占切削热量的70%以上),大量切削热集中在切削区和“刀—屑”接触面上,传入刀具中的热量达20%(切削一般碳素钢时该数值仅为9%),使得在同等切削条件下,AISI304 不锈钢切削温度比 45 钢高约 200-300℃。
(4)刀具易产生粘附磨损由于奥氏体不锈钢的高温强度高,加工硬化倾向大,因此,切削负荷重,奥氏体不锈钢与刀具和切屑之间会由于切削过程中其与刀具之间的亲合趋势显著增加,从而不行避开地产生粘结、集中等现象,并生成“切屑瘤”,造成刀具粘附磨损。
关于不锈钢的工艺

关于不锈钢的工艺不锈钢是一种具有抗腐蚀性能的合金材料,被广泛应用于工业制造、建筑装饰和家居用品等领域。
不锈钢的工艺是指在不锈钢制造过程中所采用的加工方法和工艺技术。
本文将介绍不锈钢的常见工艺及其特点。
1. 冷拔工艺冷拔是不锈钢加工中常用的一种工艺方法。
它是通过将不锈钢坯料加热至一定温度后,利用冷拔机将坯料拉伸成所需的形状和尺寸。
冷拔工艺可以提高不锈钢的硬度和强度,同时改善其表面光洁度和机械性能。
2. 热处理工艺热处理是指将不锈钢加热至一定温度,经过一定时间的保温后进行冷却的工艺方法。
热处理可以改善不锈钢的晶体结构,消除内部应力,提高材料的强度和韧性。
常见的热处理工艺包括退火、淬火、回火等。
3. 焊接工艺不锈钢的焊接是不锈钢加工中的重要环节。
常见的不锈钢焊接方法包括TIG焊、MIG焊、电弧焊等。
不锈钢的焊接工艺要求严格,需要控制焊接温度、焊接速度和焊接气氛等参数,以确保焊接接头的质量和性能。
4. 表面处理工艺不锈钢的表面处理可以改善其外观和耐腐蚀性能。
常见的表面处理方法包括抛光、酸洗、电镀等。
抛光可以提高不锈钢的光洁度和亮度,使其具有更好的装饰效果;酸洗可以去除不锈钢表面的氧化物和污染物,提高其耐腐蚀性能;电镀可以在不锈钢表面形成一层保护性的金属涂层,提高其耐磨性和耐腐蚀性。
5. 冷轧工艺冷轧是指将不锈钢坯料在常温下进行轧制的工艺方法。
冷轧可以使不锈钢材料变薄,同时提高其硬度和强度。
冷轧工艺可以生产出尺寸精度高、表面光洁度好的不锈钢板材和钢带,广泛应用于建筑装饰和汽车制造等领域。
6. 铸造工艺不锈钢的铸造是指将熔融的不锈钢注入铸型,经冷却凝固后得到所需形状的工艺方法。
不锈钢的铸造工艺可以生产出复杂形状的零件和构件,具有设计自由度高、成本低的优点。
常见的不锈钢铸造方法包括砂型铸造、失重铸造和压力铸造等。
不锈钢的工艺是不锈钢制造过程中的关键环节,直接影响着不锈钢材料的性能和质量。
通过合理选择和控制不锈钢的工艺方法,可以获得满足不同需求的不锈钢产品。
大批量生产不锈钢的合金钢等精密小零件的成型工艺方法

大批量生产不锈钢的合金钢等精密小零件的成型工艺方法1.弯曲成型工艺:
在不锈钢制品加工中,弯曲成形是将板料、棒料、管料或型材等弯成一定形状和角度零件的成形方法。
一般430不锈钢厚钢板弯曲成形时容易开裂,而的304不锈钢板则不会有这个现象。
2.拉深成型工艺:
拉深是利用专用模具将冲裁或剪裁后所获得的平板坯料制成开口的空心件的一种冲压工艺方法。
其特点是板料在凸模的带动下,可以向凹模内流动,即依靠材料的流动性和延伸率成形。
3.翻边成型工艺:
翻边成型工艺是济南不锈钢制品加工中,很常用的一种加工方法,翻边是利用模具把坯料上的孔缘或者外缘翻成竖边的冲压加工方法。
在生产不锈钢岗亭的时候,都是采用这种工艺将不锈钢进行成型加工的。
4.胀形成型工艺:
胀形成型工艺是利用模具强迫坯料厚度减薄和表面积增大,以获取零件几何形状的冲压不锈钢制品加工方法。
特点是坯料被压边圈压死,不能向凹模内流动,完全依靠材料本身的延伸成形。
简述不锈钢的加工工艺

简述不锈钢的加工工艺
不锈钢是一种耐腐蚀、抗氧化的金属材料,常用于制造各种产品,包括厨具、建筑材料、化工设备等。
不锈钢的加工工艺通常包括以下几个步骤:
1.切割:针对不同的产品需求,不锈钢通常需要进行切割,以获得所需的形状和尺寸。
常用的切割方法包括机械切割、火焰切割、等离子切割等。
2.弯曲和成形:在制造过程中,需要将不锈钢板材弯曲成特定的形状。
这可以通过机械弯曲、滚轮弯曲或液压弯曲等方法实现。
3.焊接:不锈钢制品通常需要通过焊接来连接零部件。
电弧焊、氩弧焊和激光焊等是常用的不锈钢焊接方法。
焊接后可能需要进行表面处理,以保持不锈钢的耐腐蚀性。
4.表面处理:不锈钢的表面处理可以包括抛光、酸洗、电镀等步骤,以提高其表面光洁度、耐腐蚀性和美观度。
抛光可以使不锈钢表面更光滑,酸洗可以去除氧化层,电镀则可以改变不锈钢的表面颜色和质感。
5.机械加工:不锈钢零部件通常需要进行机械加工,例如车削、铣削、钻孔等,以获得精确的尺寸和表面质量。
6.装配:在加工完成后,不锈钢零部件可能需要进行组装,形成最终的产品。
这可能涉及到螺栓连接、焊接、胶合等方式。
06cr18ni11ti奥氏体不锈钢 加工工艺
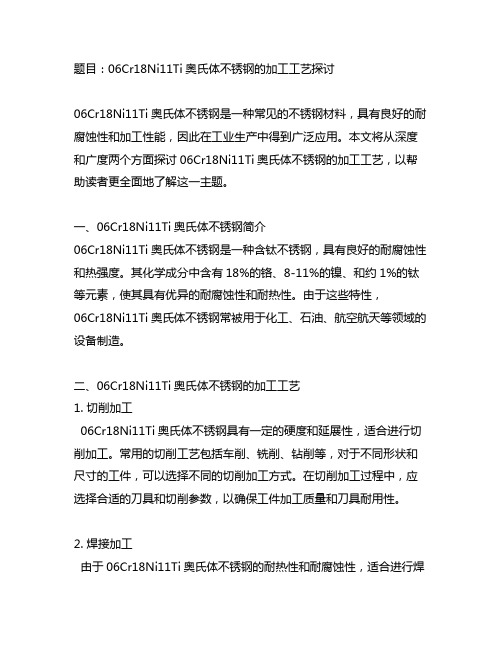
题目:06Cr18Ni11Ti奥氏体不锈钢的加工工艺探讨06Cr18Ni11Ti奥氏体不锈钢是一种常见的不锈钢材料,具有良好的耐腐蚀性和加工性能,因此在工业生产中得到广泛应用。
本文将从深度和广度两个方面探讨06Cr18Ni11Ti奥氏体不锈钢的加工工艺,以帮助读者更全面地了解这一主题。
一、06Cr18Ni11Ti奥氏体不锈钢简介06Cr18Ni11Ti奥氏体不锈钢是一种含钛不锈钢,具有良好的耐腐蚀性和热强度。
其化学成分中含有18%的铬、8-11%的镍、和约1%的钛等元素,使其具有优异的耐腐蚀性和耐热性。
由于这些特性,06Cr18Ni11Ti奥氏体不锈钢常被用于化工、石油、航空航天等领域的设备制造。
二、06Cr18Ni11Ti奥氏体不锈钢的加工工艺1. 切削加工06Cr18Ni11Ti奥氏体不锈钢具有一定的硬度和延展性,适合进行切削加工。
常用的切削工艺包括车削、铣削、钻削等,对于不同形状和尺寸的工件,可以选择不同的切削加工方式。
在切削加工过程中,应选择合适的刀具和切削参数,以确保工件加工质量和刀具耐用性。
2. 焊接加工由于06Cr18Ni11Ti奥氏体不锈钢的耐热性和耐腐蚀性,适合进行焊接加工。
常用的焊接工艺包括氩弧焊、氩气保护焊、电阻焊等,其中氩弧焊是最常用的一种。
在焊接过程中,需要注意控制焊接电流和电压,以避免产生氧化皮和焊缝不良。
3. 热处理工艺06Cr18Ni11Ti奥氏体不锈钢的热处理工艺包括固溶处理和时效处理。
固溶处理可以改善材料的塑性和韧性,时效处理则可以提高材料的硬度和强度。
在热处理过程中,需要控制加热温度和保温时间,以确保材料的组织结构和性能达到设计要求。
4. 表面处理工艺06Cr18Ni11Ti奥氏体不锈钢的表面处理工艺包括抛光、喷丸、酸洗等。
这些工艺可以改善材料表面的光洁度和耐腐蚀性,同时也可以提高涂层的附着力和耐磨性。
在表面处理过程中,应根据具体要求选择合适的工艺流程和化学药剂,以确保材料表面的质量和性能。
不锈钢材料常见成型工艺

不锈钢材料常见成型工艺不锈钢是一种常见的金属材料,具有耐腐蚀、耐高温、强度高等优点,因此在工业生产中得到广泛应用。
不锈钢的成型工艺也是非常重要的,下面将介绍几种常见的不锈钢成型工艺。
一、冷镦成型冷镦成型是一种常见的不锈钢成型工艺,主要用于制造螺栓、螺母等紧固件。
冷镦成型是利用冷镦机将不锈钢棒材强行压制成型,通过镦头和模具的作用,将不锈钢材料冷变形成型。
冷镦成型工艺具有高效、低成本的特点,能够大批量生产符合规格要求的产品。
二、冷拔成型冷拔成型是一种通过拉伸不锈钢材料来实现成型的工艺。
在冷拔过程中,不锈钢材料被放入到冷拔机中,通过连续拉伸的方式,逐渐把材料拉长成所需的形状。
冷拔成型工艺可以制造出形状复杂、尺寸精确的产品,广泛应用于制造轴类零件、弹簧等。
三、冲压成型冲压成型是一种常见的不锈钢成型工艺,通过冲压机将不锈钢板材加工成各种形状的零件。
冲压成型工艺具有生产效率高、成本低的优点,能够批量生产符合要求的产品。
冲压成型工艺广泛应用于汽车、航空航天、电子等行业,制造出各种不锈钢零件。
四、热压成型热压成型是一种通过将不锈钢材料加热至一定温度,然后放入模具中进行压制成型的工艺。
热压成型工艺可以制造出尺寸精确、表面光滑的产品,适用于制造各种不锈钢零件,如阀门、管道等。
五、焊接成型焊接是一种将不锈钢材料通过加热至熔化状态,然后通过焊接电弧或者激光束将材料连接在一起的工艺。
焊接成型可以制造出形状复杂的不锈钢零件,广泛应用于建筑、船舶、化工等领域。
六、铸造成型铸造成型是一种通过将熔化的不锈钢注入模具中,冷却后得到所需形状的工艺。
铸造成型具有制造尺寸大、形状复杂的不锈钢零件的优点,广泛应用于制造船舶、汽车、机械等行业。
以上是几种常见的不锈钢成型工艺,每种工艺都有其特点和适用范围。
在实际生产中,根据不同的产品要求和工艺条件,选择合适的成型工艺可以提高生产效率、降低成本,并保证产品质量。
不锈钢轴承生产工艺

不锈钢轴承生产工艺
不锈钢轴承是一种重要的机械零件,广泛应用于机械设备、汽车、电子产品等领域。
其生产工艺是十分繁琐和复杂的,下面我们来了解一下关于不锈钢轴承的生产工艺。
1. 原材料的准备:不锈钢是制造轴承的常用材料之一,所以首先需要准备好不锈钢原材料。
通过熔炼和冶炼等工艺,将不锈钢制成合适的形态和尺寸。
2. 钢材加工:将原材料切割成合适的尺寸,然后利用高速钢切削刀具进行车削。
这个过程需要严格控制尺寸和形状的精度,确保轴承的质量。
3. 理化处理:经过切割和车削后的轴承需要进行理化处理,进一步提高不锈钢的硬度和耐磨性。
常见的处理方法有热处理、冷处理等。
4. 精加工:精加工是指对轴承进行细微的加工和修整。
通过磨床、车床等设备进行研磨和打磨,使轴承表面更加光滑,减少摩擦。
5. 组装:在精加工后,将各个部件按照规定的顺序和方式进行组装。
组装过程需要注意每个部件的配合度和精度,确保轴承的正常运转。
6. 检测和质量控制:对组装完成的轴承进行检测,包括尺寸、硬度、摩擦等方面的检测。
必要时还需要进行质量控制,排除
不合格产品。
7. 表面处理:轴承经过一段时间使用后,表面可能会出现氧化和生锈等问题。
因此需要进行表面处理,包括抛光、镀铬等工艺,使轴承表面更加光滑和耐腐蚀。
通过以上工艺,不锈钢轴承的生产得以完成。
整个过程需要严格按照标准操作,确保产品的质量和性能。
不锈钢轴承的生产工艺虽然繁琐,但却是确保产品质量的关键所在,这也决定了不锈钢轴承的可靠性和持久性。
不锈钢冷镦工艺

不锈钢冷镦工艺一、引言不锈钢是一种具有耐腐蚀性和高强度的材料,广泛应用于制造业中。
冷镦工艺是一种常用的加工方法,用于不锈钢的成型和加工。
本文将详细介绍不锈钢冷镦工艺的原理、步骤和应用。
二、不锈钢冷镦工艺的原理不锈钢冷镦工艺是通过对不锈钢材料进行冷加工,使其在常温下发生塑性变形,从而改变其形状和尺寸的加工方法。
冷镦工艺主要包括以下几个步骤:选材、锻造、切割和精加工。
三、不锈钢冷镦工艺的步骤1. 选材:选择合适的不锈钢材料,根据产品的要求确定材料的成分和性能。
2. 锻造:将不锈钢材料放入冷镦机中,通过压力和冷镦模具的作用,使材料发生塑性变形,达到预定的形状和尺寸。
3. 切割:将经过冷镦加工的不锈钢材料进行切割,得到所需的长度。
4. 精加工:对切割好的不锈钢材料进行精细加工,如修磨、打磨、抛光等,以提高产品的表面质量和精度。
四、不锈钢冷镦工艺的应用不锈钢冷镦工艺广泛应用于制造业中,特别是在汽车、航空航天、家电等领域。
具体应用包括以下几个方面:1. 汽车零部件:不锈钢冷镦工艺可用于制造汽车的各种零部件,如螺栓、螺母、轴承等,提高其强度和耐腐蚀性。
2. 家电产品:不锈钢冷镦工艺可用于制造家电产品的螺丝、连接件等,提高产品的性能和质量。
3. 航空航天领域:不锈钢冷镦工艺可用于制造航空航天领域的紧固件、连接件等,确保飞行器的安全性和可靠性。
4. 其他领域:不锈钢冷镦工艺还可以应用于制造电子产品、建筑材料等领域,满足不同行业的需求。
五、总结不锈钢冷镦工艺是一种常用的加工方法,通过冷加工不锈钢材料,使其获得所需的形状和尺寸。
该工艺具有高效、精度高、成本低等优点,广泛应用于制造业中。
随着科技的不断进步,不锈钢冷镦工艺将会得到更多的应用和发展。
未来,我们可以期待不锈钢冷镦工艺在各个领域的更广泛应用,为制造业的发展做出更大的贡献。
浅谈用直径较小刀具加工不锈钢零件的加工工艺
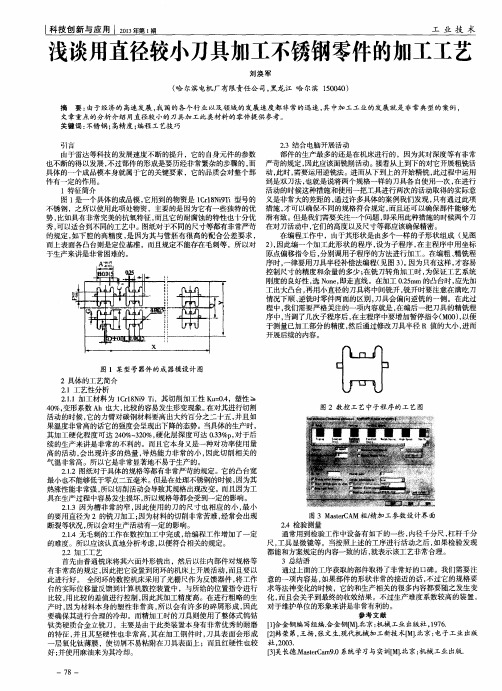
2 . 3结Βιβλιοθήκη 电脑 开展 活动 由于雷达等科技的发展速度不断的提升 ,它的 自身元件的参数 部件的生产最多的还是在机床进行 的,因为其对深度等有非常 因此 应该 面铣 削活 动 。 接 着从 上到 下 的对它 开展 粗铣活 也不断的得 以发展 , 不过部件的形成是要历经非常繁杂 的步骤的 , 而 严 苛 的规定 , 具体的一个成品模本身就属于它的关键要素 ,它的品质会对整个部 动 , 此时, 需要 运用 逆铣 法 。进而 从下 到上 的开始 精铣 , 此 过程 中运用 件 有 一定 的作用 。 到是双刀法 , 也就是说将两个规格一样的刀具各 自使用一次 , 在进行 l特征 简介 活动的时候这种措施和使用一把工具进行两次的活动取得的实际意 图t 是一个具体的成品模 , 它用到的物资是 1 C r l 8 N i 9 T i型号的 义是非常大的差距 的, 通过许多具体的案例我们发现 , 只有通过此项 才可以确保不同的规格符合规定 , 而且还可以确保部件能够光 不锈钢,之所以使用此项处物资,主要的是因为它有一些独特 的优 措施 , 势, 比如具有非常完美的抗氧特征 , 而且它的耐腐蚀的特性也十分优 滑有致 。 但是我们需要关注一个问题 , 即采用此种措施的时候两个刀 秀, 可以适合到不同的工艺中。图纸对于不同的尺寸等都有非常严苛 在对刀活动中, 它们的高度以及尺寸等都应该确保精密。 在编 程工 作 中 ,由于 其形 状是 由多 个一 样 的子 形状 组 成 ( 见 图 的规定 , 如下腔的高精度 , 是因为其与管胚有很高 的配合公差要求 , ) , 因此 编一 个 加工 此 形 状 的程 序 , 设 为 子程 序 , 在 主 程 序 中用 坐 标 而上表面各凸台则是定位基准 ,而且规定不能存在毛刺等 ,所 以对 2 于生产来讲是非常困难的。 原点偏移指令后 , 分别调用子程序的方法进行加工。在编粗 、 精铣程 A 序时, 一律要用刀具半径补偿法编程( 见图 3 ) 。 因为只有这样 , 才容易 控制尺寸的精度和余量的多少; 在铣刀转角加工时 , 为保证工艺 系统 刚度的 良好性 , 选N o n e , 即走直线。在加工 0 . 2 5 a r m的凸台时, 应先加
浅谈用直径较小刀具加工一不锈钢零件的加工工艺
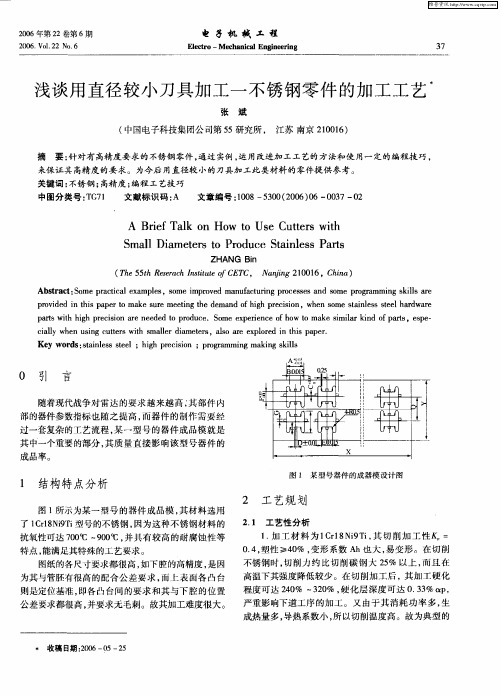
图纸的各尺寸要求都很高 , 如下腔的高精度 , 因 是
不锈钢时 , 切削力约 比切 削碳 钢大 2 % 以上 , 5 而且在
为其与管胚:很高 的配合公差要求 , 有 而上表面各 凸台 则是定位基准 , 即各凸 台问的要求 和其与下腔的位置
高温下其强度降低较少。在切 削加工后 , 加工硬化 其 程度 可达 2 0 ~30 , 化 层 深 度 可 达 0 3 % e , 4% 2% 硬 .3 t p
维普资讯
20 0 6年第 2 2卷第 6期
2 o . 12 o 6 o 6 Vo. 2 N .
电 子 机 械 工 程
E eto—Me h nc l n ie rn l r c c a ia E gn e i g 3 7
浅谈 用 直 径 较 小 刀 具 加 工一 不 锈 钢 零 件 的加 工 工 艺
—
、_ L i
.
一
I ; :
X
I J ± . 旦
1 结构特 点分析
图1 所示为某一型号的器件 成品模 , 其材料选用
了 1 r8 iF 型号的不锈钢 , ClN9 i 因为这种不锈钢材料的 抗氧性可达 70C一 0 o 并具有较高的耐腐蚀性等 0 c 9 0C,
严重影 响下道工序的加工。又由于其 消耗功率 多 , 生 成热量多 , 导热系数小 , 以切削温度高。故为典型 的 所
公差要求都;高 , 限 并要求无毛刺。故其加工难度很大。
} 收 稿 日期 :0 6— 5— 5 20 0 2
维普资讯
3 8
电 子 机 械 工 程
Ab t a t S me p a t a x mp e ,s me i r v d ma u a t r g p o e s sa d s me p o r mmi g s i s a e s r c : o r ci le a l s o mp o e n fc u i r c s e n o r g a c n n k l r l p o i e n t i a e k u e me t gt e d ma d o ih p e iin,w e o t i ls te a d r r v d d i h sp p rt ma e s r e i e n fh g r c s o n h o h n s me sa ne s s l r wa e e h
不锈钢T型长条形零件制造技术
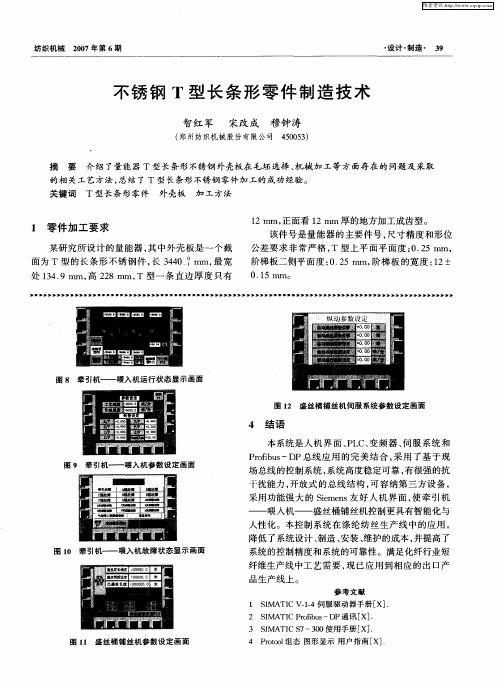
4 Poo l rto组态 图形显示 用户指南 [ . x]
维普资讯
4 ・ 计 ・ 造 ・ 0 设 制
纺 织 机械
20 0 7年 第 6期
外壳 板 中心线 与 阶梯 板 中 心线 并 不 垂 直 , 是 而
在 6 . ±0 1r 处相交 , 角为 19 ±2 。设 计尺 2 1 . m n 夹  ̄
人性 化 。本 控 制 系统 在 涤 纶 纺 丝 生产 线 中的应 用 ,
降低 了 系统 设 计 、 制造 、 安装 、 维护 的成 本 , 提高 了 并
图 1 牵 引机 — — 喂入 机故 障状 态显 示 画 面 0
系统 的控制 精度 和 系统 的可靠 性 。满足 化纤行 业短 纤维 生 产线 中工 艺 需 要 , 已应 用 到相 应 的 出 口产 现
工装 垫块保 证 角 度误 差 。 为便 于检 测 角 度 , 采用 样
板对 刀 和测量 。
图 1
3 3 5 铣 齿工 艺安排 在加 工 中心加 工 , 了尽 量少 .. 为
占用 加 工 中心 时 间 , 7 1 6个 M6螺 孔 在加 工 中心 点
2 工 艺分 析
2 1 量能 器外壳 板 , 质 为 0 r8 9不锈 钢 , 加 . 材 C lNi 属
图 9 牵引机—— 喂入 机参 数设 定画面
一
图 1 盛 丝桶 铺 丝 机伺 服 系 统 参 数 设 定 画 面 2
4 结 语
本系统 是 人 机 界 面 、L 变 频 器 、 服 系 统 和 P C、 伺
Poiu —DP总线 应 用 的完 美 结 合 , 用 了基 于 现 rf s b 采
来 , 不产 生大 的变形 。 又
不锈钢圆环加工工艺

不锈钢圆环加工工艺一、引言不锈钢圆环是一种常用的零部件,广泛应用于机械制造、船舶、电力、化工等领域。
不锈钢圆环的加工工艺对产品的质量和性能起着至关重要的作用。
本文将介绍不锈钢圆环的加工工艺流程及相关注意事项。
二、加工工艺流程1. 材料准备选择合适的不锈钢材料是保证产品质量的重要步骤。
常用的不锈钢材料有304、316等。
在选择材料时,需要根据实际使用环境和要求来确定。
2. 切割不锈钢材料经过切割成合适尺寸的圆环形状。
常用的切割方法有剪切、火焰切割等。
切割时需要注意尺寸的准确性和切割面的光洁度。
3. 折弯经过切割的不锈钢材料进一步进行折弯,使其呈现出圆环形状。
折弯时需要使用专用的折弯机械设备,确保折弯角度的准确性。
4. 焊接将折弯好的不锈钢圆环进行焊接。
焊接时需要保证焊接接头的质量和焊缝的牢固性。
常用的焊接方法有氩弧焊、电阻焊等。
5. 修磨焊接完成后,需要对焊接接头进行修磨,使其表面平整光滑。
修磨时需要使用砂轮等工具,注意修磨的力度和角度,避免对产品造成损坏。
6. 表面处理经过修磨的不锈钢圆环需要进行表面处理,以提高其耐腐蚀性。
常用的表面处理方法有酸洗、喷砂、抛光等。
表面处理时需要注意操作方法和处理时间,避免对产品造成损坏。
7. 检验加工完成的不锈钢圆环需要进行质量检验,确保产品符合相关标准和要求。
常用的检验方法有外观检查、尺寸测量、力学性能测试等。
检验时需要使用合适的测量工具和设备,严格按照检验标准来进行。
8. 包装通过检验合格的不锈钢圆环需要进行包装,以保护产品免受外界环境的影响。
常用的包装方法有纸箱包装、木箱包装等。
包装时需要注意包装材料的选择和包装方式的合理性。
三、注意事项1. 加工过程中要严格控制温度,避免对不锈钢材料造成变形或损伤。
2. 加工设备和工具要保持清洁,避免杂质对产品质量的影响。
3. 每个加工步骤都要进行记录,以便追溯工艺和问题排查。
4. 操作人员要经过专业培训,熟练掌握加工工艺和操作规程。
430不锈钢加工工艺

430不锈钢加工工艺一、引言430不锈钢是一种常见的不锈钢材料,具有良好的耐腐蚀性和机械性能。
在工业领域中,430不锈钢被广泛应用于制造各种零部件和设备。
为了充分发挥430不锈钢的优势,需要进行适当的加工工艺。
二、材料准备在进行430不锈钢加工之前,需要准备好所需的材料和工具。
首先是430不锈钢板材,通常采用常规规格的板材。
此外,还需要钢锯、切割机、磨床、电焊机等加工工具。
三、切割切割是对430不锈钢进行加工的第一步。
可以使用钢锯或切割机进行切割,根据需要将板材切割成所需的尺寸和形状。
在进行切割之前,需要测量好尺寸,并在430不锈钢板上做好标记,以确保精确切割。
四、折弯在某些情况下,需要将430不锈钢板折弯成特定的形状。
为了实现精确的折弯,可以使用折弯机或者手工折弯工具。
在进行折弯之前,需要根据设计要求计算好折弯角度和弯曲半径,并在430不锈钢板上做好标记。
五、钻孔钻孔是在430不锈钢板上制作孔洞的常用加工方法。
可以使用钻床或者手持电钻进行钻孔操作。
在进行钻孔之前,需要选择合适的钻头,并根据设计要求确定孔洞的位置和尺寸。
在钻孔过程中,需要注意保持稳定的加工速度和适当的冷却润滑。
六、磨削磨削是对430不锈钢表面进行光洁度提升和尺寸修整的加工方法。
可以使用磨床或者手持磨削工具进行磨削操作。
在进行磨削之前,需要选择合适的磨削工具和磨粒,并根据要求确定磨削路径和磨削压力。
在磨削过程中,需要保持适当的冷却润滑和加工速度。
七、焊接在某些情况下,需要对430不锈钢进行焊接。
可以使用电焊机进行焊接操作。
在进行焊接之前,需要选择合适的焊接材料和焊接方法,并根据设计要求确定焊接位置和焊接顺序。
在焊接过程中,需要注意保持合适的焊接温度和焊接速度,以避免产生焊接缺陷。
八、表面处理为了提高430不锈钢的表面光洁度和耐腐蚀性,可以进行表面处理。
常见的表面处理方法包括抛光、酸洗和电镀等。
抛光可以使430不锈钢表面变得光滑亮丽,酸洗可以去除表面的氧化层和污垢,电镀可以在表面形成一层保护膜。
不锈钢加工之工艺流程

不锈钢钣金加工之工艺流程1、下料:下料方式有各种,主要有以下几种方式①.剪床:是利用剪床剪切条料简单料件,它主要是为模具落料成形准备加工,成本低,精度低于0.2,但只能加工无孔无切角的条料或块料。
②.冲床:是利用冲床分一步或多步在板材上将零件展开后的平板件冲裁成形各种形状料件,其优点是耗费工时短,效率高,精度高,成本低,适用大批量生产,但要设计模具。
③.NC数控下料,NC下料时首先要编写数控加工程式,利用编程软件,将绘制的展开图编写成NC数拉加工机床可识别的程式,让其根据这些程式一步一刀在平板上冲裁各构形状平板件,但其结构受刀具结构所至,成本低,精度于0.15。
④.镭射下料,是利用激光切割方式,在大平板上将其平板的结构形状切割出来,同NC 下料一样需编写镭射程式,它可下各种复杂形状的平板件,成本高,精度于0.1.⑤.锯床:主要用下铝型材、方管、图管、圆棒料之类,成本低,精度低。
1.钳工:沉孔、攻丝、扩孔、钻孔沉孔角度一般120℃,用于拉铆钉,90℃用于沉头螺钉,攻丝英制底孔。
2.翻边:又叫抽孔、翻孔,就是在一个较小的基孔上抽成一个稍大的孔,再攻丝,主要用板厚比较薄的钣金加工,增加其强度和螺纹圈数,避免滑牙,一般用于板厚比较薄,其孔周正常的浅翻边,厚度基本没有变化,允许有厚度的变薄30-40%时,可得到比正常翻边高度大高40-60%的高度,用挤薄50%时,可得最大的翻边高度,当板厚较大时,如2.0、2.5等以上的板厚,便可直接攻丝。
3.冲床:是利用模具成形的加工工序,一般冲床加工的有冲孔、切角、落料、冲凸包(凸点),冲撕裂、抽孔、成形等加工方式,其加工需要有相应的模具来完成操作,如冲孔落料模、凸包模、撕裂模、抽孔模、成型模等,操作主要注意位置,方向性。
4.压铆:压铆就本公司而言,主要有压铆螺母、螺钉、松不脱等,其是通过液压压铆机或冲床来完成操作,将其铆接到钣金件上,还有涨铆方式,需注意方向性。
5.折弯;折弯就是将2D的平板件,折成功D的零件。
不锈钢不同的加工工艺

不锈钢不同的加工工艺
不锈钢常见的加工工艺有如下几种:
1. 切割:不锈钢可以通过机械切割、火焰切割、等离子切割、激光切割等方式进行切割,用于制作板材、管件等。
2. 弯曲:通过弯曲机械对不锈钢进行弯曲,可用于制作弯头、弯管等零部件。
3. 焊接:不锈钢可使用TIG氩弧焊、MIG氩弧焊、电阻焊、激光焊接等方式进行焊接,用于制作大型容器、管道等。
4. 打孔:通过冲孔机、数控钻床等工艺对不锈钢进行打孔,常用于制作过滤器、网板等。
5. 抛光:通过机械研磨、化学抛光等方式对不锈钢表面进行抛光处理,提高光洁度和美观度。
6. 铣削:通过数控铣床对不锈钢进行铣削加工,用于制作各种形状和尺寸的零部件。
7. 钻孔:通过数控钻床或钻床对不锈钢进行钻孔,常用于制作管道支架、连接件等。
8. 镶嵌:将不锈钢与其他材料(如木材、玻璃等)进行镶嵌,用于制作家具、装饰品等。
这只是不锈钢加工的一部分常见工艺,具体加工方式还会根据不同的产品要求和加工工艺设备而有所差异。
不锈钢薄壁零件的加工工艺分析

使满足学生愿望 , 是培养足球骨干的最好途 径。 2改变组 队模式 , . 增加训练 时间 , 高运动员训 练 提 热情。高校足球队伍不 同于职业球 队和专业球 队, 应根 据高校队伍 的特点 , 教练员要注 重全年训练计划 、 阶段 训练计划和课训练计划 的制订 , 改变组 队模式 , 增加训 练次数与 时间, 给予球 队更多 的空间提高竞技水平 。同 时利用学生课余时 间训练是一般 高校所采取 的基 本训 练手段 , 课余训练工作 的JN实施是运动员竞技水平逐 l b  ̄ , 步提高 的重要保证 , 只有 遵循训练 的客观 规律 , 才能取 得和提高运动水平和运动成绩 , 从而达到预期 的目标 。 3 要积极营造 良好的青少年校园足球活动社会氛 .
-
围。各地要加强与新闻媒体的合作 , 广泛宣传开展青少 年校 园足球 活动 的重要 意义 ,大力宣传开展青少 年校 园足球活动 的典型 和所取 得 的成效 ,形成 正确 的舆论 导 向和 良好 的社会氛 围 ,为开展青少年校 园足球 活动 创造有利 的社会环境和舆论环境 。 4增加体 验式培训在高校足球教学 中的应用 。 . 足球 是学 生最 为喜欢 的项 目之一 , 生很早就接触 了足球 , 学 对 足球技术 有 了初步 的了解 。体验式训练创造 了一种 非 常态 的情 景 , 高校足球训 练增 加体验式训练课 , 以 可 让学 生在学 习技能 和增 强体能 的同时 ,增 强 自身 的社
都体育学院学报 ,9 7 ( ) 19 ,3 .
2 5 0-
【 专题研讨 】
0 0m . 3 m以内。经过切 削比较发现 , O 超硬 车削加工工 艺
比一般磨削加 工工艺 的生产效率要高4  ̄L 6 3 ] 。
机械加工的工艺流程
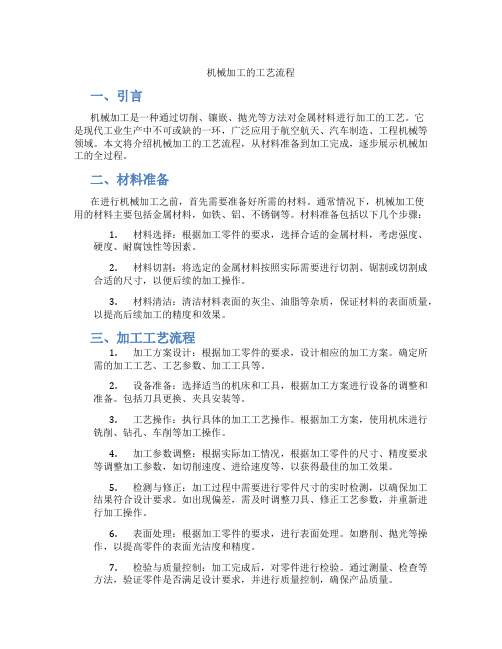
机械加工的工艺流程一、引言机械加工是一种通过切削、镶嵌、抛光等方法对金属材料进行加工的工艺。
它是现代工业生产中不可或缺的一环,广泛应用于航空航天、汽车制造、工程机械等领域。
本文将介绍机械加工的工艺流程,从材料准备到加工完成,逐步展示机械加工的全过程。
二、材料准备在进行机械加工之前,首先需要准备好所需的材料。
通常情况下,机械加工使用的材料主要包括金属材料,如铁、铝、不锈钢等。
材料准备包括以下几个步骤:1.材料选择:根据加工零件的要求,选择合适的金属材料,考虑强度、硬度、耐腐蚀性等因素。
2.材料切割:将选定的金属材料按照实际需要进行切割、锯割或切割成合适的尺寸,以便后续的加工操作。
3.材料清洁:清洁材料表面的灰尘、油脂等杂质,保证材料的表面质量,以提高后续加工的精度和效果。
三、加工工艺流程1.加工方案设计:根据加工零件的要求,设计相应的加工方案。
确定所需的加工工艺、工艺参数、加工工具等。
2.设备准备:选择适当的机床和工具,根据加工方案进行设备的调整和准备。
包括刀具更换、夹具安装等。
3.工艺操作:执行具体的加工工艺操作。
根据加工方案,使用机床进行铣削、钻孔、车削等加工操作。
4.加工参数调整:根据实际加工情况,根据加工零件的尺寸、精度要求等调整加工参数,如切削速度、进给速度等,以获得最佳的加工效果。
5.检测与修正:加工过程中需要进行零件尺寸的实时检测,以确保加工结果符合设计要求。
如出现偏差,需及时调整刀具、修正工艺参数,并重新进行加工操作。
6.表面处理:根据加工零件的要求,进行表面处理。
如磨削、抛光等操作,以提高零件的表面光洁度和精度。
7.检验与质量控制:加工完成后,对零件进行检验。
通过测量、检查等方法,验证零件是否满足设计要求,并进行质量控制,确保产品质量。
8.清洁和防护:完成加工的零件需要进行清洁和防护处理,以防止零件因铁锈、腐蚀等原因影响质量。
通常采用喷油、涂覆等方式进行处理。
四、加工后处理1.部件组装:根据设计要求,将加工好的零件进行组装。
不锈钢产品加工制造工艺规程规范

不锈钢产品制造工艺规程1范围本标准规定了一般不锈钢产品的制造工艺原则,当产品使用在耐腐蚀要求很高的工况特殊时,在相应的产品制造工艺过程卡上再另行明确要求。
本标准适用于我公司制造的奥氏体不锈钢和不锈复合钢零部件等产品的制造。
2 引用标准下列标准所包含的条文,通过在本标准中引用而构成本标准的条文。
本标准出版时所示版本均为有效,使用本标准的各方应使用下列标准的最新版本。
GB150 钢制压力容器GB151管壳式换热器HG20584 钢制化工容器制造技术要求压力容器安全技术监察规程Q/AXL J 3013铆工管工通用工艺守则Q/AXL J5010钢制压力容器检验规程Q/AXL J0801压力试验和致密性试验工艺规程3一般要求3.1 不锈钢产品的制造应具备制造场地通风、清洁、文明生产条件。
不锈钢材料及零部件应防止长期露天存放、混料保管。
要求按时投料、集中使用、及时回收、指定区域存放保管。
3.2 工件存放制造场地应铺设防铁离子污染的专用地板或橡胶板。
滚轮架上配挂胶轮。
3.3 防止在不锈钢表面踩踏。
如果不可避免应穿没有铁钉的软底鞋并带脚套,过后应将表面擦扫干净。
3.4 使用工具,如铜锤、木锤、不锈钢铲或淬火工具钢铲等,尽量使工件不和铁器接触。
磨削磨轮用纯氧化物制成。
3.5 材料标记用墨水或记号笔应不含金属颜料、硫、氯含量要≤25PPm.3.6 防止磕碰划伤钢板或零部件在吊运制作过程中应始终保持钢板表面、设备及胎具的清洁,防止将焊豆、熔渣、氧化皮压入工件表面。
3.6.1 吊具应加铜垫,吊带首选尼龙吊带且为不锈钢产品零部件专用,绝不允许与其它碳素钢混淆,如用钢丝绳外套必须套胶管或用麻绳。
3.6.2 钢管切割应在锯床上铺垫木板或橡胶板,采用专用锯条。
3.7 除切割线外其余标记线不应使用“划针”划线及“冲子”冲孔。
可使用硬色笔或记号笔。
也可以使用不含金属颜料及硫氯含量小于25PPm的墨水划线作标记。
3.8 不锈钢零部件应尽量采用冷成形。
宇联不锈钢开平工段工艺流程图
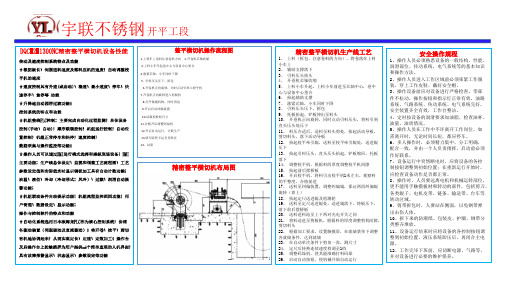
精密整平横切机布局图
Hale Waihona Puke 安全操作规程1、操作人员必须熟悉设备的一般结构、性能、 润滑部位、传动系统、电气系统等的基本知识 和操作方法。 2、操作人员进入工作区域前必须束紧工作服 装、穿上工作皮鞋、戴好安全帽。 3、操作设备前应对设备进行严格检查,零部 件不松动,操作按钮和指示灯正常有效,油路 系统、气路系统、传动系统、电气系统完好, 安全装置齐全有效,工作台整洁。 4、定时按设备的润滑要求加油脂,检查油杯、 油量、油质情况。 5、操作人员在工作中不许离开工作岗位,如 需离开时,无论时间长短,都应停车。 6、多人操作时,必须精力集中,分工明确, 配合一致,并由一个人负责指挥,启动前必须 作好联系。 7、设备运行中突然断电时,应将设备的各控 制按钮调整到初始位置;在重新运行开始时, 应检查设备动作是否都正常。 8、操作时,人员要远离电机和机械运转部位, 更不能用手触摸板材和转动的部件,包括剪刀、 各类辊子、电机皮带、链条、输送带、台车等 转动区域。 9、剪带拆包时,人要站在侧面,以免钢带弹 出击伤人体。 10、拆下来的防潮纸、包装皮、护圈、钢带分 类整齐堆放。 11、设备运行结束时应将设备的各控制按钮调 整到初始位置,液压系统卸压后,再闭合主电 源。 12、工作完毕下班前,应切断电源、气路等, 并对设备进行必要的维护保养。
宇联不锈钢 开平工段
整平横切机操作流程图
1.上料车上卷料注意卷料方向 2.开卷机芯轴收缩 3.上料小车升起卷中心与设备中心重合 4.涨紧芯轴,小车同时下降 5. 引料压头压下,拆包 6.开卷机正向旋转,同时点动引料入校平机 7.开卷机正向旋转进入剪板机 8.打开储能机构,同时剪边 9.开启自动纠偏装置 10.试裁剪检验尺寸 11.合格开启调整码垛机 12.开启自动运行,计数生产 13.填写流程卡运至待转区 14、结束
- 1、下载文档前请自行甄别文档内容的完整性,平台不提供额外的编辑、内容补充、找答案等附加服务。
- 2、"仅部分预览"的文档,不可在线预览部分如存在完整性等问题,可反馈申请退款(可完整预览的文档不适用该条件!)。
- 3、如文档侵犯您的权益,请联系客服反馈,我们会尽快为您处理(人工客服工作时间:9:00-18:30)。
不锈钢零件机加工工艺
1不锈钢材料加工难点
1.1切削力大,切削温度高
该类型材料强度大,切削时切向应力大、塑性变形大,因而切削力大。
此外材料导热性极差,造成切削温度升高,且高温往往集中在刀具刃口附近的狭长区域内,从而加快了刀具的磨损。
1.2加工硬化严重
奥氏体不锈钢以及一些高温合金不锈钢均为奥氏体组织,切削时加工硬化倾向大,通常是普通碳素钢的数倍,刀具在加工硬化区域内切削,使刀具寿命缩短。
1.3容易粘刀
论是奥氏体不锈钢还是马氏体不锈钢均存在加工时切屑强韧、切削温度很高的特点。
当强韧的切屑流经前刀面时,将产生粘结、熔焊等粘刀现象,影响加工零件表面粗糙度。
1.4刀具磨损加快
上述材料一般含高熔点元素、塑性大,切削温度高,使刀具磨损加快,磨刀、换刀频繁,从而影响了生产效率,提高了刀具使用成本。
2不锈钢零件加工工艺
通过上述加工难点分析,不锈钢的加工工艺及相关刀具参数设计与普通结构钢材料应具有较大的不同,其具体加工工艺如下:
2.1钻孔加工
在钻孔加工时,由于不锈钢材料导热性能差,弹性模量小,孔加工起来也比较困难。
解决此类材料的孔加工难题,主要是选用合适的刀具材料,确定合理的刀具的几何参数以及刀具的切削用量。
钻削上述材料时,钻头一般应选用W6Mo5Cr4V2Al、W2Mo9Cr4Co8等材质的钻头,这些材质钻头缺点是价格比较昂贵,而且难以采购。
而采用常用的W18Cr4V普通标准高速钢钻头钻孔时,由于存在顶角较小、切屑太宽而不能及时排出孔外、切削液不能及时冷却钻头等缺点,再加上不锈钢材料导热性差,造成集中在刀刃上的切削温度升高,容易导致两个后刀面和主刃烧伤及崩刃,使钻头的使用寿命降低。
(1)刀具几何参数设计在采用W18Cr4V普通高速钢钻头钻孔时,切削力及切削温度均集中在钻尖上,为提高钻头切削部位的耐用度,可以适当增大顶角角度,顶角一般选135°~140°,顶角增大也将使外缘前角减小,钻屑变窄,以利于排屑。
但是加大顶角后,钻头的横刃变宽,造成切削阻力增大,因而必须对钻头横刃进行修磨,修磨后横刃的斜角为47°~55°,横刃前角为3°~5°,修磨横刃时,应将切削刃与圆柱面转角处修磨成圆角,以增加横刃强度。
由于不锈钢材料弹性模量较小,切屑层下的金属弹性恢复大,加之加工过程中加工硬化严重,后角太小会加快钻头后刀面的磨损,而且增加了切削温度,降低钻头的寿命。
因此须适当加大后角,但后角太大,将使钻头的主刃变得单薄,减小了主刃的刚性,所以后角应以12°~15°为宜。
为使钻屑变窄,利于排屑,还需要在钻头两个后刀面上开交错分布的分屑槽。
(2)切削用量选择钻削时,切削用量的选择应从降低切削温度的基本点出发,因为高速切削将会使切削温度升高,而高的切削温度将加剧刀具磨损,因而切削用量中最重要的是选择切削速度。
一般情况下,切削速度以12~15m/min较为合适。
进给量对刀具寿命影响较小,但进给量选择太小将会使刀具在硬化层内切削,加剧磨损;而进给量如果太大,又会使表面粗糙度变差。
综合上述两个因素,进给量选择为0.32~0.50mm/r为宜。
(3)切削液选择钻削时,为降低切削温度,可采用乳化液作为冷却介质。
2.2铰孔加工
(1)刀具几何参数设计不锈钢材料的铰削加工大部分使用硬质合金铰刀。
铰刀的结构和几何参数与普通铰刀有所不同。
为增强刀齿强度并防止铰削时产生切屑堵塞现象,铰刀齿数一般比较少。
铰刀前角一般为8°~12°,但在某些特定情况,为了实现高速铰削,也可采用0°~
5°前角;后角一般为8°~12°;主偏角的选择视孔的不同而异,一般情况下通孔为15°~30°,不通孔为45°;铰孔时为了使切屑向前排出,也可适当增加刃倾角角度,刃倾角角度一般为10°~20°;刃带宽度为0.1~0.15mm;铰刀上倒锥应较普通铰刀大,硬质合金铰刀一般为0.25~0.5mm/100mm,高速钢铰刀为0.1~0.25mm/100mm;铰刀校正部分长度一般为普通铰刀的65%~80%,其中圆柱部分长度为普通铰刀的40%~50%。
(2)切削用量选择铰孔时进给量为0.08~0.4mm/r,切削速度为10~20m/min,粗铰余量一般为0.2~0.3mm,精铰余量为0.1~0.2mm。
粗铰时应采用硬质合金刀具,精铰时可采用高速钢刀具。
(3)切削液选择不锈钢材料铰孔时,可采用全损耗系统用油或二硫化钼作为冷却介质。
2.3镗孔加工
(1)刀具材料选择因加工不锈钢零件时切削力大、切削温度高,刀具材料应尽量选择强度高、导热性好的YW或YG类硬质合金。
精加工时也可使用YT14及YT15硬质合金刀片。
批量加工上述材料零件时,可采用陶瓷材料刀具,由于此类材料的特点主要是韧性大,加工硬化严重,切削这些材料的切屑以单元切屑形式产生,将使刀具产生振动,容易造成刀刃产生微崩现象,因此选择陶瓷刀具切削此类材料零件时首先应考虑的是微观韧性。
目前Sialon是一种比较好的选择,特别是α/βSialon材料,因其优异的抗高温变形的性能以及扩散磨损的性能而引人注目,并成功应用于切削镍基合金,其寿命远远超过Al2O3基陶瓷。
此外,SiC晶须加强陶瓷也是切削不锈钢或镍基合金的一种很有效的刀具材料。
对于此类材料淬火零件的加工,可以采用CBN(立方氮化硼)刀片,CBN硬度仅次于金刚石,硬度可达7000~8000HV,因此耐磨性很高,与金刚石相比,CBN突出优点是耐热性比金刚石高得多,可达1200℃,可承受很高的切削温度。
此外其化学惰性很大,与铁族金属在1200~1300℃时也不起化学作用,因此非常适合加工不锈钢材料。
其刀具寿命是硬质合金或陶瓷刀具的几十倍。
(2)刀具几何参数设计刀具几何参数对其切削性能起重要的作用,为使切削轻快、顺利,硬质合金刀具宜采用较大的前角,以提高刀具寿命。
一般粗加工时,前角取10°~20°,半精加工时取15°~20°;精加工时取20°~30°。
主偏角的选择依据是,当工艺系统刚性良好时,可取30°~45°;如工艺系统刚性差时,则取60~75°,当工件长度与直径之比超过10倍时,可取90°。
用陶瓷刀具镗削不锈钢材料时,绝大多数情况下,陶瓷刀具均采用负前角进行切削。
前角大小一般选应-5°~-12°。
这样有利于加强刀刃,充分发挥陶瓷刀具抗压强度较高的优越性。
后角大小直接影响刀具磨损,对刀刃强度也有影响,一般选用5°~12°。
主偏角的改变会影响径向切削分力与轴向切削分力的变化以及切削宽度和切削厚度的大小。
因为工艺系统的振动对陶瓷刀具极为不利,所以主偏角的选择要有利于减少这种振动,一般选取30°~75°。
选用CBN作为刀具材料时,刀具几何参数为前角0°~10°,后角12°~20°,主偏角45°~90°。
(3)前刀面刃磨时粗糙度值要小为避免出现切屑粘刀现象,刀具的前、后刀面应仔细刃磨以保证具有较小的粗糙度值,从而减少切屑流出阻力,避免切屑粘刀。
(4)刀具刃口应保持锋利刀具刃口应保持锋利,以减少加工硬化,进给量和背吃刀量不宜过小,以防止刀具在硬化层中切削,影响刀具使用寿命。
(5)注意断屑槽的磨削由于不锈钢切屑具有强韧的特点,刀具前刀面上断屑槽修磨应合适,从而使切削过程中断屑、容屑、排屑方便。
(6)切削用量的选择根据不锈钢材料特点,加工时宜选用低速和较大进给量进行切削。
采用陶瓷刀具进行镗削时,切削用量的合理选择是充分发挥陶瓷刀具性能的关键之一。
陶瓷刀具连续切削时可以按照磨损耐用度与切削用量之间的关系选择切削用量;断续切削则应按照刀具破损规律确定合理切削用量。
由于陶瓷刀具有优越的耐热性和耐磨性,切削用量对刀具磨损寿命的影响比硬质合金刀具要小。
一般情况下,用陶瓷刀具加工时,进给量对刀具的破损影响最为敏感。
因而,根据工件材料的性质,在机床功率、工艺系统刚度和刀片强度
许可的前提下,在镗削不锈钢零件时,尽可能选择高的切削速度、较大的背吃刀量和比较小的进给量。
(7)切削液选择要合适由于不锈钢具有极易产生粘结和散热性差的特点,因此在镗削中选用抗粘结和散热性好的切削液相当重要,如选用含氯较高的切削液,以及具有良好冷却、清洗、防锈和润滑作用的不含矿物油、不含亚酸盐的水溶液,如H1L-2合成切削液。
采用上述工艺方法,可以克服不锈钢的加工难点,使不锈钢在进行钻、铰、镗孔时刀具寿命得到极大的提高,减少操作中磨刀、换刀次数,在提高生产效率和孔加工质量、降低工人劳动强度和生产成本方面,能取得令人满意的效果。