微切片手册
手动微切片法介绍及应用
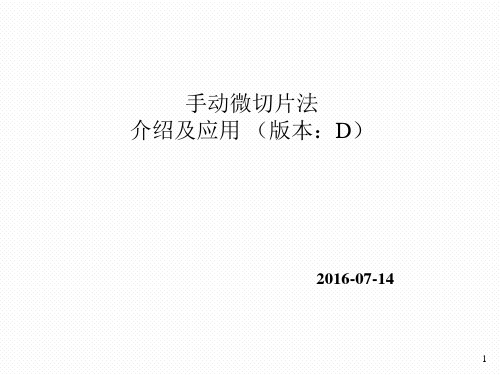
手动微切片法
• 5.3 研磨和抛光
最后抛光使用软织布或中绒毛布、1~0.1μm 钻石抛光剂、0.05氧化铝或其他氧化物
若抛光剂为氧化物或二氧化硅,低到中等压力抛 光10~20s 当使用钻石抛光剂和软织布,可能需要几分钟 通常使用抛光速度为100~150r/min 典型的抛光剂:6μm、1μm、0.04二氧化硅胶或 0.05μm氧化铝 其他的抛光剂:6μm、3μm、0.25μm的钻石研磨 膏
当分离影响少于50%的内层厚度(标识为垂 直切片),这种方法成功率比较低
27
手动微切片法
• 6.0 注意事项 6.3 微蚀液
25ml氨水(25%~30%)、25ml双氧水(体 积比3%~5%) 需要较长时间微蚀时,使用25ml蒸馏水或过 滤水稀释溶液 使用前等待5min,每几小时更换药水 还有其他微蚀液,参考IPC-MS-810等
IMC微蚀液,25ml盐酸/硫酸(5%)、25ml乙醇(95%),可 适当加水稀释,已防止过蚀。
28
手动微切片法
一、谨慎&耐心 切片前要确认清楚;切片操作要有耐心 二、胆大&心细
不关心部分大胆研磨、每道程序间仔细确认
三、创新&延伸 不局限于PTH切片;当做一种工具
29
PTH典型不良
手动微切片法
25
手动微切片法
• 6.0 注意事项 6.2.2 机械/化学同时抛光
使用95%的二氧化硅胶和5%体积比的双氧水 (30%浓度)混合物,和抗化学药水抛光布 ,进行机械和化学同时对样品的研磨 机械抛光过度,将会有很多划痕 化学抛光过度,将会过蚀 要求有最优平衡状态
26
手动微切片法
• 6.0 注意事项 6.3 为获取更多对互连分离的观察,在水 平盘上重新研磨和抛光(垂直于原垂直 平面),检查半圆周表面
微切片制作

具体 1
2
3
4
5
6
7
流程 简介 取样 灌胶 研磨 拋光 微蚀 判读
7.3 胶渣 Smear IPC-A-600H-3.3.12.~ 3.3.13
允收
拒收
拒收
垂 直 切 片
允收
水 平 切 片
拒收
拒收
微切片制作与检验
具体 1
2
3
4
5
6
7
流程 简介 取样 灌胶 研磨 拋光 微蚀 判读
7.4 孔壁粗糙度 Roughness
2
3
4
5
6
7
流程 简介 取样 灌胶 研磨 拋光 微蚀 判读
6. 微蚀
微蚀液的配方是: “氨水+水+双氧水” 配比为:1:1:0.1
观察面上滴微蚀液用棉花棒擦抹后,铜面产生微小 气泡,即表示反应已在进行,来回擦蚀约1~~3秒钟,立刻用 口罩擦干,勿使铜面继续氧化变色. 良好的微蚀将呈现鲜 红铜色,且结晶分界清楚。
7.1 龟裂 Crack IPC-A-600F-3.3.5~3.3.6
允收-孔壁及转角均无裂痕
拒收-镀铜层均有裂痕
微切片制作与检验
具体 1
2
3
4
5
6
7
流程 简介 取样 灌胶 研磨 拋光 微蚀 判读
7.2 芯吸 Wicking IPC-A-600F-3.3.11
允收
拒收: 芯吸≧4mil
微切片制作与检验
具体 1
2
3
4
5
6
7
流程 简介 取样 灌胶 研磨 拋光 微蚀 判读
5. 拋光
拋光粉
拋光
微切片制作与检验
微切片9
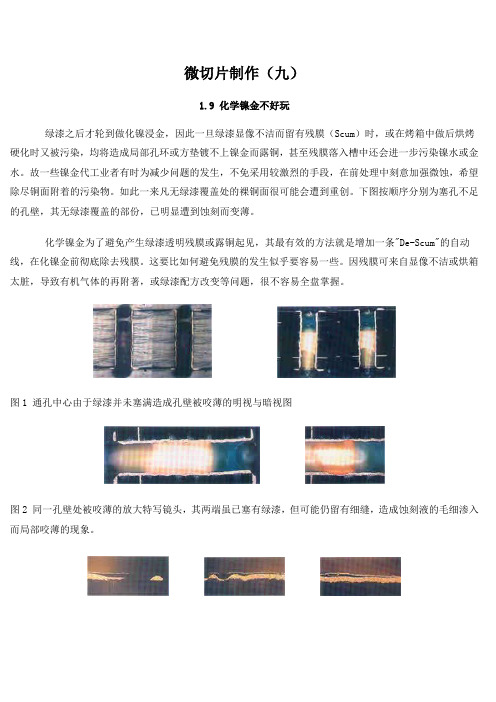
微切片制作(九)1.9 化学镍金不好玩绿漆之后才轮到做化镍浸金,因此一旦绿漆显像不洁而留有残膜(Scum)时,或在烤箱中做后烘烤硬化时又被污染,均将造成局部孔环或方垫镀不上镍金而露铜,甚至残膜落入槽中还会进一步污染镍水或金水。
故一些镍金代工业者有时为减少问题的发生,不免采用较激烈的手段,在前处理中刻意加强微蚀,希望除尽铜面附着的污染物。
如此一来凡无绿漆覆盖处的裸铜面很可能会遭到重创。
下图按顺序分别为塞孔不足的孔壁,其无绿漆覆盖的部份,已明显遭到蚀刻而变薄。
化学镍金为了避免产生绿漆透明残膜或露铜起见,其最有效的方法就是增加一条"De-Scum"的自动线,在化镍金前彻底除去残膜。
这要比如何避免残膜的发生似乎要容易一些。
因残膜可来自显像不洁或烘箱太脏,导致有机气体的再附著,或绿漆配方改变等问题,很不容易全盘掌握。
图1 通孔中心由于绿漆并未塞满造成孔壁被咬薄的明视与暗视图图2 同一孔壁处被咬薄的放大特写镜头,其两端虽已塞有绿漆,但可能仍留有细缝,造成蚀刻液的毛细渗入而局部咬薄的现象。
图3 由于过度蚀铜而未将铜盐彻底去掉,以致造成化学镍层的浮离,或进一步掏空现象。
图4 铜面前处理不良时,化学镍虽可镀上去,但当镍层之内应力太大时,即会产生浮离现象。
左为100X之清晰垂直切片。
右为200X之水平切片。
图5 上左为100X四图之电脑编辑画面,可见到化镍层顺著基材表面所蔓延长胖的情形。
下为连续焊垫间化镍金常用搭连的俯视图。
上右为化镍为活化不足,漏镀一垫的俯视图。
图6 上四个100X之电脑分割画面,为大哥大板面打线用的电镀镍金也同时镀孔之情形,可清楚看到电镀镍的分布力(Throwing Power)并不好,只见外环上的厚镍与孔中央的薄镍相差几达一倍之多。
下200X大型拼凑画面中为焊接用途的化学镍金所镀之通孔,虽因孔壁中央绿漆残膜不洁而造成部分浮离,但其镍层之厚度内外均匀则是不争的事实,此为化学镍也在其他工业中广为应用的重要原因。
微切片制作(精)

微切片制作一、概述电路板品质的好坏、问题的发生与解决、制程改进的评估,在都需要微切片做为客观检查、研究与判断的根据(Microsectioning此字才是名词,一般人常说的Microsection 是动词,当成名词并不正确)。
微切片做的好不好真不真,与研判的正确与否大有关系焉。
一般生产线为监视(Monitoring)制程的变异,或出货时之品质保证,常需制作多量的切片。
次等常规作品多半是在匆忙几经验不足情况下所赶出来的,故顶多只能看到真相的七、八成而已。
甚至更多缺乏正确指导与客观比较不足下,连一半的实情都看不到。
其等含糊不清的影像中,到底能看出什么来?这样的切片又有什么意义?若只是为了应付公事当然不在话下。
然而若确想改善品质彻底找出症结解决问题者,则必须仔细做好切取、研磨、抛光及微蚀,甚至摄影等功夫,才会有清晰可看的微切片画面,也才不致误导误判。
二、分类电路板解剖式的破坏性微切法,大体上可分为三类:1、微切片系指通孔区或其他板材区,经截取切样灌满封胶后,封垂直于板面方向所做的纵断面切片(Vertical Section),或对通孔做横断面之水平切片(Horizontal section),都是一般常见的微切片。
图1.左为200X之通孔直立纵断面切片,右为100X通孔横断面水平切片。
若以孔与环之对准度而言,纵断面上只能看到一点,但横断面却只可看到全貌的破环。
2、微切孔是小心用钻石锯片将一排待件通孔自正中央直立剖成两半,或用砂纸将一排通孔垂直纵向磨去一般,将此等不封胶直接切到的半壁的通孔,置于20X~40X的立体显微镜下(或称实体显微镜),在全视野下观察剩余半壁的整体情况。
此时若另将通孔的背后板材也磨到很薄时,则其半透明底材的半孔,还可进行背光法(Back Light)检查其最初孔铜层的敷盖情形。
图 2.为求检验与改善行动之效率与迅速全盘了解起见,最方便的方法就是强光之下以性能良好的立体显微镜(40X~60X)直接观察孔壁。
微切片制作(三)

微切片制作(三)
1.3 打底靠抛光
微切片过程需先经粗磨细磨接近孔心之平面后,才可仔细抛光。
之后再经小心微蚀,其整个画面才能看得眉清目秀纤毫毕露。
以下即为笔者的制作经验。
1、研磨过程
将灌胶硬化后的切样,先用120号圆形粗砂纸使平贴在旋转磨盘上,配合细小冲水之动作(可冲掉残粉并能减热),将之削磨接近孔体轴心的平面时,
即换成600号与1200号较细的砂纸再进行修平,最后用2400号尽量将小的砂痕去掉。
在研磨过程中需不断的改换方向及放大观察,以免磨歪或磨过头。
当然也可改用其他方式去研磨,只要到达目的就好。
研磨的要点是:对孔壁而言其截面必须落在孔心平面之附近,必须要两壁平行,必须要消除大多数砂痕。
2、抛光手法
采用专用可吸水的厚毡,以背胶牢贴于圆形转盘上,在滴水打湿的表面涂均抛光膏,一般可用0.5µ或1µ的白色氧化铝专用抛光膏。
在3000rpm的转速下,手执切样不断变换方向进行轻压式抛光。
同时也要用放。
微切片24
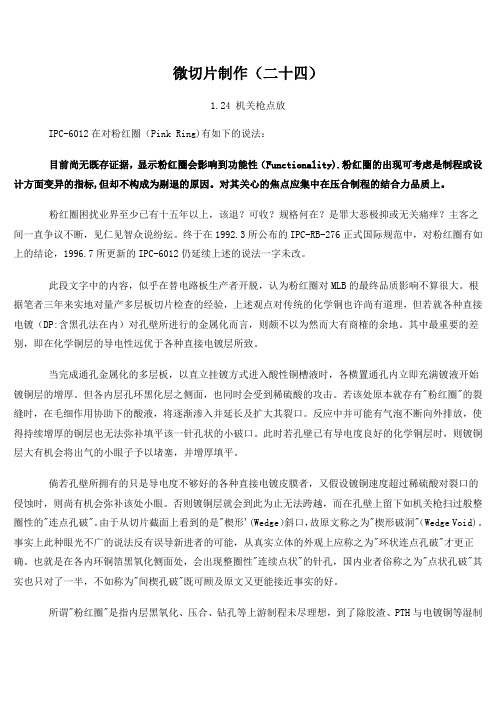
微切片制作(二十四)1.24 机关枪点放IPC-6012在对粉红圈(Pink Ring)有如下的说法:目前尚无既存证据,显示粉红圈会影响到功能性(Functionality).粉红圈的出现可考虑是制程或设计方面变异的指标,但却不构成为剔退的原因。
对其关心的焦点应集中在压合制程的结合力品质上。
粉红圈困扰业界至少已有十五年以上,该退?可收?规格何在?是罪大恶极抑或无关痛痒?主客之间一直争议不断,见仁见智众说纷纭。
终于在1992.3所公布的IPC-RB-276正式国际规范中,对粉红圈有如上的结论,1996.7所更新的IPC-6012仍延续上述的说法一字未改。
此段文字中的内容,似乎在替电路板生产者开脱,认为粉红圈对MLB的最终品质影响不算很大。
根据笔者三年来实地对量产多层板切片检查的经验,上述观点对传统的化学铜也许尚有道理,但若就各种直接电镀(DP:含黑孔法在内)对孔壁所进行的金属化而言,则颇不以为然而大有商榷的余地。
其中最重要的差别,即在化学铜层的导电性远优于各种直接电镀层所致。
当完成通孔金属化的多层板,以直立挂镀方式进入酸性铜槽液时,各横置通孔内立即充满镀液开始镀铜层的增厚。
但各内层孔环黑化层之侧面,也同时会受到稀硫酸的攻击。
若该处原本就存有"粉红圈"的裂缝时,在毛细作用协助下的酸液,将逐渐渗入并延长及扩大其裂口。
反应中并可能有气泡不断向外排放,使得持续增厚的铜层也无法弥补填平该一针孔状的小破口。
此时若孔壁已有导电度良好的化学铜层时,则镀铜层大有机会将出气的小眼子予以堵塞,并增厚填平。
倘若孔壁所拥有的只是导电度不够好的各种直接电镀皮膜者,又假设镀铜速度超过稀硫酸对裂口的侵蚀时,则尚有机会弥补该处小眼。
否则镀铜层就会到此为止无法跨越,而在孔壁上留下如机关枪扫过般整圈性的"连点孔破"。
由于从切片截面上看到的是"楔形'(Wedge)斜口,故原文称之为"楔形破洞"(Wedge Void)。
精编微切片之分类图解资料

印制电路板显微剖切技术研究1前言印制电路板制造质量的好坏、使用可靠性的高低、制造过程中问题的发生与解决、制程能力及改进的评估,往往都需要采用显微剖切来作为客观检察、研究和判断的依据。
显微剖切(Microsectioning),又称微切片、金相切片,它的制作有着一套相对专业的制造技术和检测手段。
微切片制作质量的好坏,将直接关系到研究和判断的正确性。
俗话说得好,外行看热闹、内行看门道,各家有各家的高招。
真应了那句名言——条条大路通罗马。
作者长期从事各类印制电路板的制造工艺及品质控制技术的研究,曾专长于金相切片的制作,并有大量第一手金相切片照片在握。
本不该在各位专家面前献丑,但每每翻看这些照片,总有一种与人共研之冲动。
今特将之分类后,陆续登出,望各位不吝赐教,共同为业界之发展贡献些许绵力。
2微切片制作工艺流程2.1取样待检印制电路板试样的采取有以下几种方法:(1)采用机械装置剪切或辊切、锯切;(2)平面冲头之冲切;(3)凹陷冲头之冲切;(4)铣切;(5)带锯切割;上述诸种方法,各有利弊。
从对待检印制电路板部位的损伤来讲,第一种和第二种较为严重;第三种和铣切则适中。
至于带锯切割法,虽然同冲切和铣切一样的快速、便捷,但对操作者来说,存在潜在的伤害危险。
2.2试样续处理2.3试样入模方式用双面胶粘住样品的正截面(较薄的板用订书子夹住样品待检测的侧截边),使样品垂直立于凝胶模中央。
如是试验切片,建议一个模放两个样品,待检测的侧截边分放于切片的两面,以便从两面磨孔均能磨到孔中央,但样品间要保持最少2mm间距,以免固化后影响样品的牢固性。
2.4调胶处理本处理的重点在于各组分混合充分均匀,且尽可能减少搅拌所造成的气泡产生量。
正误搅拌方式对比请参见下左图9。
搅拌方式对比2.5灌胶入模将上述搅拌均匀的胶料,缓慢倒入模内,直至淹没横担试样的铅芯或鱼线(对于待检部位在模具底部之情况除外)。
对于可能粘附于试样上的气泡,可通过轻敲模壁或用牙签将其引出。
微切片手册
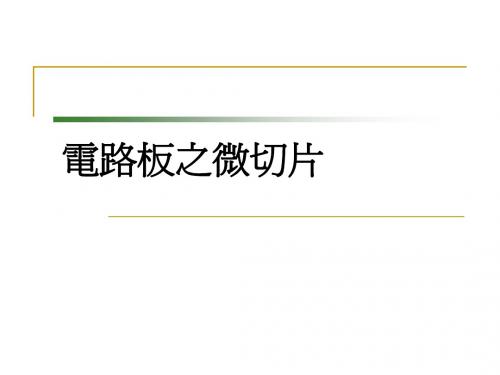
微切片的製作
6.攝影(Photography):
目前顯微攝影有兩類:
其一以光學方式直接照相.透過拍立得式像機而立即取得 證據; 其二是將畫面以電腦先行記憶與編輯,再以Print Out方式 輸出得像.前者每張相片價格昂貴,後者設備價格高.
微切片的製作
注意點及難點:
a. 切樣表面必須極端真平,否則會局部清楚局部模糊,一 般自”拍立得”片盒中所拉出的夾層相片要等一分鐘左右 才能撕開,必要時稍加烘烤以加速其熟化老化. b.曝光所需光量=光強度*時間,要求儘量延長時間與減少 光強度,還須加裝各種濾光片. c. 目視焦距與攝影焦距並不完全相同,不可以目視為準, 可犧牲幾張相片以便找到真正的攝影焦距.
切片室異常匯總,允收標準詳解
1.基板氣泡(Laminalion Void)
多層板在高熱時不但通孔中發生樹脂凹陷,在板中央也 可能在高熱下發生空洞,造成層間空洞. 允收標準:孔徑≦3 mil並且沒有違反應有的介質間距
切片室異常匯總,允收標準詳解
2.樹脂縮陷(Resin Recession)
切片室異常匯總,允收標準詳解
電鍍銅瘤
THANK YOU
微切片的製作
b.鉻酸法:40g氧化鉻,加純水至150ml,全溶加硫酸 4ml,再加0.2-0.4ml乙醇,最後加純水至200ml 方法:用木棒將混合均勻的微蝕液擦抹在切片表面 上,靜置10-15秒種後,立即用水沖洗乾淨,良好的微 蝕效果應該為鮮紅銅色(時間過長將使銅面變色氧 化,出現暗棕色及粗糙的銅面),隨後即可作顯微觀 察.
微切片的製作
5.微蝕(Microetch):
微切片讲解参考PPT
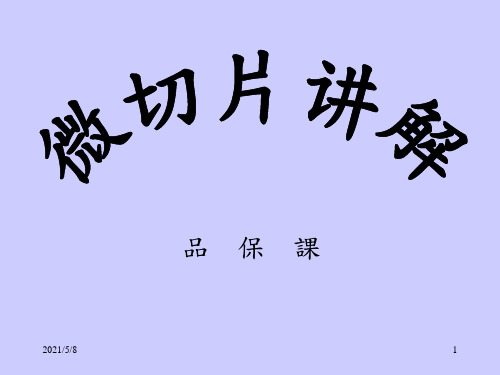
3、斜 切 片
多层板填胶通孔,对其直立方向进行45°或30°的斜剖斜磨,然后以实体显微镜 或高倍断层显微镜,观察其斜切平面上各层导体线路的变异情形。如此可兼顾直 切与横剖的双重特性。(此種切片作起來很困難,也不易觀察)
明视200X之斜切片
暗视200X之斜切片
2021/5/8
9
压 合 空 洞(Lamination Void)
多层板除了在感热之通孔“A区”会产生树脂缩陷外,板子的“B 区”(接受强热通孔以外的板材区)也会在高热后出现空洞,称之为压合 或板材空洞。
焊 环 浮 起(Lifted Land)
由于Z方向的剧烈胀缩,热应力试验后某些板面焊环的外缘,常会发生 浮离,IPC-6012规定不可超过1mil。
4
三、制作技巧
微切片需填胶抛光与微蚀,才能看清各种真实品质.以下为制作过程 的重点:
1、 取 样(Sample culling) 以特殊专用的钻石锯自板上任何位置取样,或用剪床剪掉无用板材而 得切样。注意后者不可太逼近孔边,以防造成通孔受到拉扯变形。此时, 最好先将大样剪下来,再用钻石锯片切出所要的真样,以减少机械应力 造成失真。(本廠是採用金相切片機及沖片機取樣)
品保課
2021/5/8
1
一、概述
电路板品质的好坏、问题的发生与解决、制程改进的评估,在 都需要微切片做为客观检查、研究与判断的根据 (Microsectioning此字才是名词,一般人常说的Microsection是 动词,当成名词并不正确)。微切片做的好不好真不真,与研判 的正确与否大有关系焉。一般生产线为监视(Monitoring)制程的 变异,或出货时之品质保证,常需制作多量的切片。次等常规作 品多半是在匆忙几经验不足情况下所赶出来的,故顶多只能看到 真相的七、八成而已。甚至更多缺乏正确指导与客观比较不足下, 连一半的实情都看不到。其等含糊不清的影像中,到底能看出什 么来?这样的切片又有什么意义?若只是为了应付公事当然不在 话下。然而若确想改善品质彻底找出症结解决问题者,则必须仔 细做好切取、研磨、抛光及微蚀,甚至摄影等功夫,才会有清晰 可看的微切片画面,也才不致误导误判。
微切片之分类图解
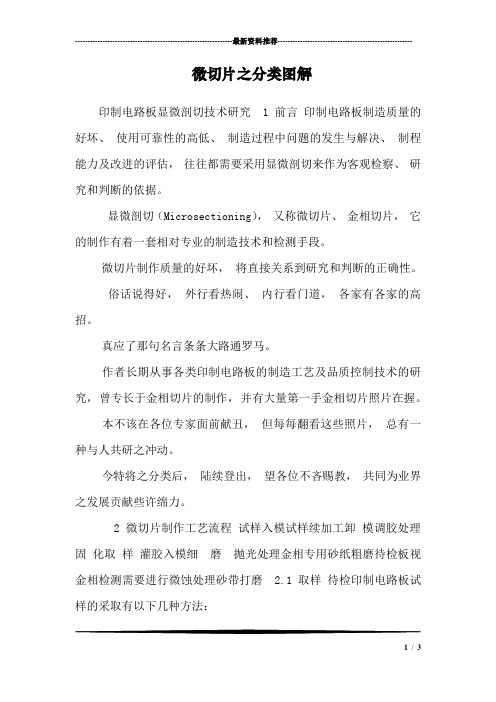
---------------------------------------------------------------最新资料推荐------------------------------------------------------微切片之分类图解印制电路板显微剖切技术研究 1 前言印制电路板制造质量的好坏、使用可靠性的高低、制造过程中问题的发生与解决、制程能力及改进的评估,往往都需要采用显微剖切来作为客观检察、研究和判断的依据。
显微剖切(Microsectioning),又称微切片、金相切片,它的制作有着一套相对专业的制造技术和检测手段。
微切片制作质量的好坏,将直接关系到研究和判断的正确性。
俗话说得好,外行看热闹、内行看门道,各家有各家的高招。
真应了那句名言条条大路通罗马。
作者长期从事各类印制电路板的制造工艺及品质控制技术的研究,曾专长于金相切片的制作,并有大量第一手金相切片照片在握。
本不该在各位专家面前献丑,但每每翻看这些照片,总有一种与人共研之冲动。
今特将之分类后,陆续登出,望各位不吝赐教,共同为业界之发展贡献些许绵力。
2 微切片制作工艺流程试样入模试样续加工卸模调胶处理固化取样灌胶入模细磨抛光处理金相专用砂纸粗磨待检板视金相检测需要进行微蚀处理砂带打磨 2.1 取样待检印制电路板试样的采取有以下几种方法:1 / 3(1)采用机械装置剪切或辊切、锯切;(2)平面冲头之冲切;(3)凹陷冲头之冲切;(4)铣切;(5)带锯切割;上述诸种方法,各有利弊。
从对待检印制电路板部位的损伤来讲,第一种和第二种较为严重;第三种和铣切则适中。
至于带锯切割法,虽然同冲切和铣切一样的快速、便捷,但对操作者来说,存在潜在的伤害危险。
2.2 试样续处理 2.3 试样入模方式用双面胶粘住样品的正截面(较薄的板用订书子夹住样品待检测的侧截边),使样品垂直立于凝胶模中央。
如是试验切片,建议一个模放两个样品,待检测的侧截边分放于切片的两面,以便从两面磨孔均能磨到孔中央,但样品间要保持最少 2mm 间距,以免固化后影响样品的牢固性。
微切片手册新

过度钉头几乎一定会出现较大的挖破,出自钻 孔的纵向玻璃纱束之挖破,除与钻针尖部的"刃 角"损耗有密切关系外,也与钻针的偏转(Run Out)或摇摆(Wobble)有关
网印负片法熔锡后的切片
由圖可以看出二铜镀得特别厚,不但超越油墨 而且还侧爬颇远 ,孔环外缘截面呈现缺口
2 、干 膜 阻 剂
此200X画面的油墨阻剂(如同墙壁)出现异常,致 使二次铜一开始往墙外恻向伸出,有了镀铜层在 非导体表面建立基地,锡铅镀层当然就毫不客气 顺理成章的成长,其结果不免造成板子的报废。
6.蚀 刻 因 子 Etching factor 6.蚀
X V 所谓蚀刻因子(F)系指向下的蚀深V,除 以侧蚀X所得商值F之谓也(F=V/X)。而X 定义是指“从阻剂边缘横量到最细铜腰 之宽距而言”
同一孔壁处被咬薄的放大特写镜头,其两端虽已塞有绿漆, 同一孔壁处被咬薄的放大特写镜头,其两端虽已塞有绿漆,但可能仍留有 细缝,造成蚀刻液的毛细渗入而局部咬薄的现象。 细缝,造成蚀刻液的毛细渗入而局部咬薄的现象。
黑孔孔壁全景(由于孔中央之黑膜太薄,致使皮膜 导电不良,造成孔中央全部镀不上电镀铜层而断孔)
孔壁粗糙
孔壁粗糙是因為钻孔而造成不良, 其中又以钻针情况不佳为主因。说的更仔 细一点,那就是针尖上两个第一面(First Facet)的切削前缘(Cutting Lips)出现崩破(Chipping),无法顺利切削玻璃束所致。或针尖外侧两刃角 (Corner)崩损磨圆,失去原来直角修整孔壁的功能,在破烂刀具的又劈又撞 情形下,经常会把迎面而来的纵向玻织束撞成破裂陷落的坑洞,不过横向撞 折断者则尚可维持平坦。下附各图中读者可清楚的看到其孔壁放大的细部情 形 纵向纱束被劈散成坑
孔壁背后的基材在漂 锡前多半完整无缺,漂锡 后因树脂局部继续硬化聚 合,或挥发份的逸走,造 成局部缩陷而自孔铜背后 退缩之现象即为本词。此 缺点虽然IPC-6012已可允 收,但日本客户仍坚持拒 收.
白容生切片分析说明

关于《电路板微切片手册》一、白蓉生教授自序微切片(Microsectioning)技术应用范围很广,电路板只是其中之一。
对多层板品质监视与工程改善,倒是一种花费不多却收获颇大的传统手艺。
不过由于电路板业扩展迅速人材青黄不接,尤其是纯手艺的技术员更是凤毛麟角。
虽然每家公司也都聊备设施安置人员,也都有模样的切磨抛看,然而若就一般判读标准而言,则多半所得到书面的成绩,虽不至惨不忍睹的地步,多也只停留在不知所云的阶段。
考其原因不外:客户内行者太少、老板们不深入也不重视,工程师好高骛远甚少落宝基本。
是以在欠缺教材乏人指导下,当然只有自我摸索闭门造车了。
至于国外同业的水准,经笔者多年用心观察与比较下,除了设备比我们贵与好之外,手艺方面则不仅乏善可陈,而且还颇为优越自大。
甚至IPC贩售录影带中的讲师,也只是西装笔挺振振有词,根本拿不出几张晶莹剔透眉清目秀的宝物彩照,何况是经年累月众多量产的心血结晶。
国外同业在诸多故障方面的累积经验,也远去国内厂商甚多。
持远来和尚会念经的想法,想要从国外引进微切片技者应只是缘木求鱼竹篮打水罢了。
笔者二十五年前进入PCB业,即对动手微切片发生兴趣,每每找到重点再印证于产品改善时,不仅心情雀跃深获成就感外,且种种经验刻骨铭心至今不忘。
如此亲身实地之经验累积,比诸书本当然大有不同在焉。
多年来共集存了二千多张各式微切片原照,特于投老之际仔细选出730张编辑成书,希望为业界后起留下一些可资比较的样本,盼在无师之下而能自通,抛开包袱减少误导。
由于版面有限许多珍贵照片必须裁剪以利编辑,每在下刀之际就有切肤之痛难以割舍,实乃岁月不居件件辛苦得之不易也。
本书除以全彩印刷极高成本之外,每帧照片也都绝对是费时耗力所有赀,放眼全球业界以如此大手笔成书者应属首见。
本书能顺利编辑,须感谢台湾电路公司切片实验室小姐先生们之鼎力协助,若以简易切片方式而言,从广经阅历的笔者看来,台路的几位老手们应列国内之顶尖。
白蓉生《电路板微切片手册》2

图4 上左100X图中可见到镀铜孔壁与铜箔孔环之间的拉离,完全是出自两次电镀铜本身的内应力,超过对铜箔孔环侧缘之附著力所致,由于尚未进行漂锡,故与热应力无关。
上右200X之正片法镀厚铜孔壁,也由于本身内应力超过对铜环的附著力,而逐步拉离的情形(两图观察前均出现微蚀过度)。
图5 上左500X图示热应力后其铜壁与孔环之间并未完全拉开,而局部拉开所隆起的部分还造成整体铜壁的轻微突出,此罕见之异常现象非常珍贵。
上右为100X漂锡孔在强大热应力的拉扯下,使一铜与二铜之间发生轻微的分离。
IPC-6012在表3-7中指出Class 2与Class 3板类,不能允收此种分离。
图6 上左1000X画面之漂锡孔,转角处之一次镀铜已被拉断,但二次铜则完好如初,也属一种"部分后分离"。
上右200X之漂锡孔,其环与壁互连处似乎已发生后分离,但从背光仔细观察时似乎又未全离。
前图5则恰好切到这种现象。
好奇之下在相同样板上又进行水平切片,以找出更多局部分离的证据。
图7 从许多水平切孔中找到一个样孔可证明上述说法,上左50X"孔环十字桥"(Thernal Pad)之全景,该PTH 是以十字桥与外面大铜面相通,四块无铜的基材区即为预防过度膨胀的"伸缩缝"。
此样左上方图8 孔铜制程后分离的例子很多,有的提早到镀完铜或半镀即呈现"微分",再续镀之下即成了真正的"分离"(开始不久即分离者会形成揩镀)。
上左图为100X,右图为200X之精采水平切片,可看到孔壁自孔环上出现图9 左200X为漂锡试验后"互连分离"之另一实例,不但环壁之间产生沟分,而且连内环黑化皮膜处与铜孔壁上亦均出现"树脂缩陷",热应力之大可见一斑。
右为1000X之环壁分离,其间的虚空不容掩饰,但也并不表示全壁整环已空,也不表示电性断路,只是逮到时就不免挂上问号而已。
化验室微切片手册
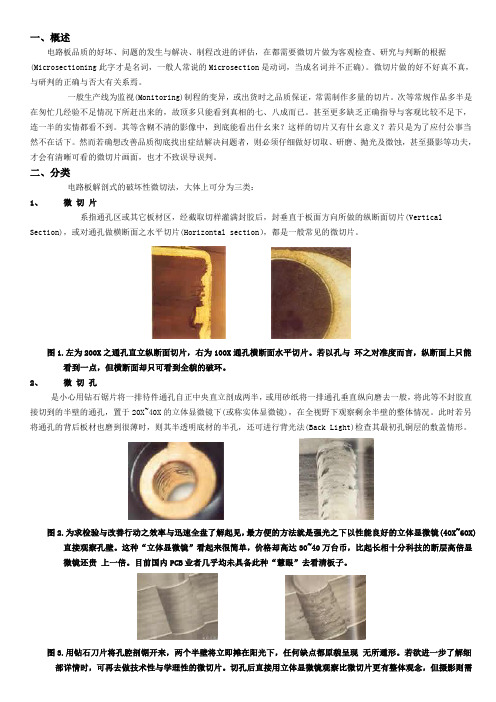
一、概述电路板品质的好坏、问题的发生与解决、制程改进的评估,在都需要微切片做为客观检查、研究与判断的根据(Microsectioning此字才是名词,一般人常说的Microsection是动词,当成名词并不正确)。
微切片做的好不好真不真,与研判的正确与否大有关系焉。
一般生产线为监视(Monitoring)制程的变异,或出货时之品质保证,常需制作多量的切片。
次等常规作品多半是在匆忙几经验不足情况下所赶出来的,故顶多只能看到真相的七、八成而已。
甚至更多缺乏正确指导与客观比较不足下,连一半的实情都看不到。
其等含糊不清的影像中,到底能看出什幺来?这样的切片又有什幺意义?若只是为了应付公事当然不在话下。
然而若确想改善品质彻底找出症结解决问题者,则必须仔细做好切取、研磨、抛光及微蚀,甚至摄影等功夫,才会有清晰可看的微切片画面,也才不致误导误判。
二、分类电路板解剖式的破坏性微切法,大体上可分为三类:1、微切片系指通孔区或其它板材区,经截取切样灌满封胶后,封垂直于板面方向所做的纵断面切片(Vertical Section),或对通孔做横断面之水平切片(Horizontal section),都是一般常见的微切片。
图1.左为200X之通孔直立纵断面切片,右为100X通孔横断面水平切片。
若以孔与环之对准度而言,纵断面上只能看到一点,但横断面却只可看到全貌的破环。
2、微切孔是小心用钻石锯片将一排待件通孔自正中央直立剖成两半,或用砂纸将一排通孔垂直纵向磨去一般,将此等不封胶直接切到的半壁的通孔,置于20X~40X的立体显微镜下(或称实体显微镜),在全视野下观察剩余半壁的整体情况。
此时若另将通孔的背后板材也磨到很薄时,则其半透明底材的半孔,还可进行背光法(Back Light)检查其最初孔铜层的敷盖情形。
图2.为求检验与改善行动之效率与迅速全盘了解起见,最方便的方法就是强光之下以性能良好的立体显微镜(40X~60X)直接观察孔壁。
微切片28
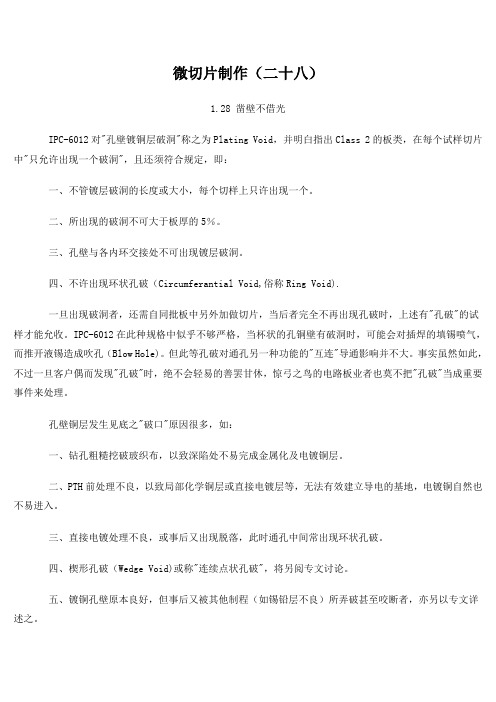
微切片制作(二十八)1.28 凿壁不借光IPC-6012对"孔壁镀铜层破洞"称之为Plating Void,并明白指出Class 2的板类,在每个试样切片中"只允许出现一个破洞",且还须符合规定,即:一、不管镀层破洞的长度或大小,每个切样上只许出现一个。
二、所出现的破洞不可大于板厚的5%。
三、孔壁与各内环交接处不可出现镀层破洞。
四、不许出现环状孔破(Circumferantial Void,俗称Ring Void).一旦出现破洞者,还需自同批板中另外加做切片,当后者完全不再出现孔破时,上述有"孔破"的试样才能允收。
IPC-6012在此种规格中似乎不够严格,当杯状的孔铜壁有破洞时,可能会对插焊的填锡喷气,而推开液锡造成吹孔(Blow Hole)。
但此等孔破对通孔另一种功能的"互连"导通影响并不大。
事实虽然如此,不过一旦客户偶而发现"孔破"时,绝不会轻易的善罢甘休,惊弓之鸟的电路板业者也莫不把"孔破"当成重要事件来处理。
孔壁铜层发生见底之"破口"原因很多,如:一、钻孔粗糙挖破玻织布,以致深陷处不易完成金属化及电镀铜层。
二、PTH前处理不良,以致局部化学铜层或直接电镀层等,无法有效建立导电的基地,电镀铜自然也不易进入。
三、直接电镀处理不良,或事后又出现脱落,此时通孔中间常出现环状孔破。
四、楔形孔破(Wedge Void)或称"连续点状孔破",将另阅专文讨论。
五、镀铜孔壁原本良好,但事后又被其他制程(如锡铅层不良)所弄破甚至咬断者,亦另以专文详述之。
除了环状孔破可从电性连通测试(Continuity Test,即俗称之Open-Short Pest)中逮到外,其余大小孔破均需以"九孔镜"或微切片做目视检查。
通常业者内部管理的工程与品管人员,每天都严格把关,希望尽早发现问题所在,及时解决烦恼故障,以免落到客户手中才东窗事发则噬脐莫及也。
- 1、下载文档前请自行甄别文档内容的完整性,平台不提供额外的编辑、内容补充、找答案等附加服务。
- 2、"仅部分预览"的文档,不可在线预览部分如存在完整性等问题,可反馈申请退款(可完整预览的文档不适用该条件!)。
- 3、如文档侵犯您的权益,请联系客服反馈,我们会尽快为您处理(人工客服工作时间:9:00-18:30)。
第二部分:切片的制作程序
&研磨:
1.打开研磨机电源,并调节转速钮 2.在研磨过程中需加入适当之水量帮助研磨。 3.用150目砂纸,将观察孔研磨至孔邊。 4.用600目砂纸,将观察孔研磨至约1/4处。 5.用1200目砂纸,将观察孔研磨至约1/3处。 6.用2000目砂纸,将观察孔研磨至约1/2处。 7.研磨方向应与切片成45角,并不断以90旋转,以确保切片表面完全 研磨。 8.研磨时用力应均匀,防止磨偏。禁止用力过度,导致切片与压克力 胶分裂。 9.在接近孔中心时,应注意防止过磨,检查有无喇叭孔、磨偏及研磨不 够等缺陷
第四部分:導同孔常見異常及允收標准 &.除胶渣不良
圖示一 圖示二 不允收/钻孔时钻针与板材强力摩擦所产生的温度甚高,故所累积的热量常使得 孔壁瞬间温度高达200℃以上,如此一来不免使得部份树脂被软化而成为胶糊, 随着钻针的旋转而涂满孔壁,各内孔环的內層铜面也自不能幸免,冷却后变成胶 渣導致PTH后殘膠不能除盡
自動取樣機
手動取樣機
第二部分:切片的制作程序 &封胶:
1.将沖切下來的切片试样用吹风机吹干,并卡于灌胶模内(或以双面胶将 切片研磨边固定于塑料灌胶模内),竖直固定。 2.将压克力粉与硬化剂(约1:1)调和均匀,缓慢注入灌胶模,并检视无气 泡后,自然固化约15分钟。 注意事项: 1.若切片孔内存有气泡,则用棉花棒沿切片边缘来回移动,直至赶出气 泡为止。 2.固化时间必须充足,否则研磨时,会导致切片与压克力胶分裂。
B
第七部分:切孔的判讀
項目 允收規格及說明 圖片說明
粗糙度
≦1.2mil
回蝕
0.2-3 mil
第七部分:切孔的判讀
項目 允收規格及說明 圖片說明
反回蝕
<1mil
燈芯效應
≦3.15mil
第八部分:總結 微切片對于PCB板來講于同醫生看病照X光一 樣﹐切片做的好不好真不真﹐直接將影響到制 程改善方向與問題解決之時效性﹐為有效及时 管控制程产品品质及從切面去分析產品不良原 因﹐准確的找出問題產生源頭﹐以提升制程改 善空間﹐故必須做好切片分析﹐即﹕切取﹑鑲 嵌﹑灌膠﹑研磨﹑拋光﹑微蝕﹑拍照﹑量測等 功夫。
C F D 1 3 E 2 4 B E
>70% T/P [(A+B+C+D+E+F)/6]/ [(1+2+3+4)/4]
A
B
C
F
第七部分:切孔的判讀
項目 允收規格及說明 min 0.4 mil 綠油厚 圖片說明
(基板上﹑線路上﹑拐角處)
寬度不可超過該處銅箔厚 釘頭 度的1.5倍(a/b≦1.5)
A
理想狀態如圖示一﹐允收如圖示二﹐不允收如圖三﹐回蝕深度允收標准﹕ 0.2~3mil。
第三部分:切片的用途 &.反回蝕
&.反回蝕
圖示一 圖示二 圖示三
反回蝕的有利面是在介面處不會產生應力集中點﹐且經過電鍍后仍可得到均勻平滑的孔壁﹐但 過度的反回蝕因其在惡劣的環境下儲存而造成內層自孔壁分離的缺點﹔
理想狀態如圖示一﹐允收如圖示二﹐不允收如圖三﹐反回蝕長度不可大于1mil
第二部分:切片的制作程序
&拋光﹕
1.将转盘转速设定为200~300RPM。 2〃细磨完毕后再以抛光布加抛光粉将切片表面抛光至光滑,抛光方式与研 磨方式相同。 3.使用專業可吸水拋光布與0.5~1.0U”之氧化鋁拋光粉。
注意事项:
1.抛光时间不可太久,一般要求应 30秒,以免造成表面“发黑”。 2〃抛光时,应使较小的力,才能保证抛光效果。
研磨至孔邊
研磨邊
第二部分:切片的制作程序
&研磨:
1.用150#砂紙研磨至孔邊
研磨邊
孔邊
2.用600#砂紙研磨至孔1/4處
孔中心線
研磨邊
1/4處
第二部分:切片的制作程序
&研磨:
3.用1200#砂紙研磨至孔1/3處
孔中心線
研磨邊
1/3處
4.用2000#砂紙研磨至孔1/2處(孔中心不可磨過)
研磨邊
1/2處
第五部分:熱應力填錫切片允收標准 &.樹脂內縮
圖示一 圖示二 允收/熱應力后孔樹脂內縮寬度不可超過3mil﹐長度不可大于孔深的40%
如圖示二
第五部分:熱應力填錫切片允收標准 &.分層
圖示一
圖示二
不允收/因板材質過期﹑壓合后未完全固化或PCB板充分吸濕熱后經高溫
膨脹導致分層﹐分層有壓合分層﹑基材分層兩種﹐如圖示二
取 樣 封 膠 研 磨 拋 光 微 蝕 拍 照 量 測
提供書 面報表
書面 存檔
判 定
填寫報 表
第二部分:切片的制作程序 &.取样:
用手动冲床或切割机,将板边测试孔(或要觀察的部分)冲切下来。 冲切时,一般以板边深入至过测试孔(或要觀察的部分)2-3mm为宜。 注意事项 冲切时不可太靠近孔边(或要觀察的部分),以防通孔受外力而变形。 冲切时亦不可过于接近成型线,以防因冲切入成型线内致使PCS报废。
平面圖 切面圖 不允收/钻孔时钻针与板材强力摩擦所产生的温度甚高,故所累积的热量常使得 孔壁瞬间温度高达200℃以上,如此一来不免使得部份树脂被软化而成为胶糊, 随着钻针的旋转而涂满孔壁,各内孔环的內層铜面也自不能幸免,冷却后变成胶 渣導致PTH后殘膠不能除盡
第七部分:切孔的判讀
項目 Ⅰ銅厚度 允收規格及說明 0.2-0.5mil
END
第五部分:熱應力填錫切片允收標准
&.鍍層斷裂
圖示一
圖示二
不允收/因鍍層延展性不好﹐經高溫沖擊拉扯出現鍍層斷裂﹐如圖示一
第六部分:水平切片的判讀 &.粉红圈
平面圖
切面圖
不允收/粉紅圈源自于黑化﹐通常此異常為外觀檢驗出,水平切片﹑垂直切
片均可檢驗其現象由下圖可清楚看出。
第六部分:水平切片的判讀 &.除胶渣不良
第一部分:微切片的定義及類型
PCB板品質的好壞、問題發生的源頭與解決、製程改進, 都需要微切片作為觀(檢)查 ,因此製作切片時必須仔 細做好切取、研磨、 拋光及微蝕﹐甚至拍照等功夫, 才會有清晰可看的微切片畫面,也才不致誤判。 切片大體上可分為三類﹕
&.微切片 &.微切孔 &.斜切片
第二部分:切片的制作程序 &.切片制作流程﹕
客戶料號 廠內料號 SPEC
A
孔銅量測位置
D
MIN:20UM
08G2007F A20V
E018E6033C
AVG:25UM
B
E
MAX:50UM
C F
第三部分:切片的用途 &.燈芯效應
燈芯效應長度需 <3.15mil
第三部分:切片的用途 &.回蝕
圖示一
圖示二
圖示三
回蝕是指針對孔壁內層銅環上下﹐對其介質層加以移除而退回一部份﹔回蝕會形成面包 夾式的結合﹐但也會造成孔壁粗糙﹐使銅壁有斷裂及使內層孔環發生龜裂等問題
不可有刮痕﹑ 銅面發黑等不 良現象
第二部分:切片的制作程序
&微蝕﹕
微蝕液配置方法﹕純水與NH3H2O按體積比1:1配製再加入2-3滴H2O2,微蝕液 需2H更換一次。 注意事项: 研磨完毕之金相切片用微蚀液轻擦10S左右﹐微蚀时间过短过长,均会影响测 试结果的准确性。一般以微蚀至镀层分界线清晰出现时为最佳。 微蚀完毕后必须用棉布将微蚀液擦干净。
锡厚 銅面不可發黑 且鍍層分界線 需清晰 基板銅 IICU ICU
第三部分:切片的用途 • • • • • • • • • 微切片的主要用途﹕ 背光測試 (Backlight) 基板厚度量測 孔壁粗糙度量測 孔銅狀況量測 燈芯效應 回蝕 反回蝕 釘頭
第三部分:切片的用途
&.背光
&.背光測試原理﹕ 光可透過基材﹐但光不能透過銅層. 注意事项: &.背光切片用显微镜观察透光点,并根据(背光等级判断标准大于8級)
以透光点最多的一个孔,来判断该板的背光状况.
單孔亮點<50個
研磨邊
第三部分:切片的用途 &.基板厚度及PP厚度測試
玻璃纖 維 環氧 樹脂
內層 銅箔
第三部分:切片的用途 &.孔壁粗糙度量測
鑽 孔 后
電 鍍 后
孔壁粗糙度IPC規范內定義不影響最小孔徑為原則﹐廠內定義<1.2mil
第三部分:切片的用途 &.孔銅狀況量測
鍍錫
圖片說明
Ⅱ銅
基板銅0.5OZ:0.3740.741mil 總面銅厚度 (基板銅+Ⅰ銅 +Ⅱ銅) 基板銅1 OZ:1.18-3.04 mil 基板銅2 OZ:2.443.04mil 鍍錫厚 0.2-0.6 mil
基板 銅 Ⅰ銅
第七部分:切孔的判讀
項目 允收規格及說明
A
圖片說明
D
min 0.8 mil & avg 1.0 mil 成品孔 銅厚度 (A﹑B﹑C﹑D﹑E﹑F六點)
第五部分:熱應力填錫切片允收標准 &.基材空洞
圖示一
圖示二
允收/基材空洞不可大于3mil,且同一區域不可有多處空洞
第五部分:熱應力填錫切片允收標准 &.孔環浮離
圖示一 圖示二 允收/熱應力后孔環浮離不可超過1mil﹐如圖示二
第五部分:熱應力填錫切片允收標准 &.斷角
圖示一
圖示二
不允收/熱應力后切片不可有斷角現象﹐如圖示二
第四部分:導同孔常見異常及允收標准 &.孔內鍍瘤
圖示一
圖示二
允收/鍍瘤不可影響最小成品孔徑要求
第四部分:導同孔常見異常及允收標准 &.內層接觸不良