连铸工艺与设备连铸连轧的匹配XXXX
炼钢-连铸流程的炉机匹配
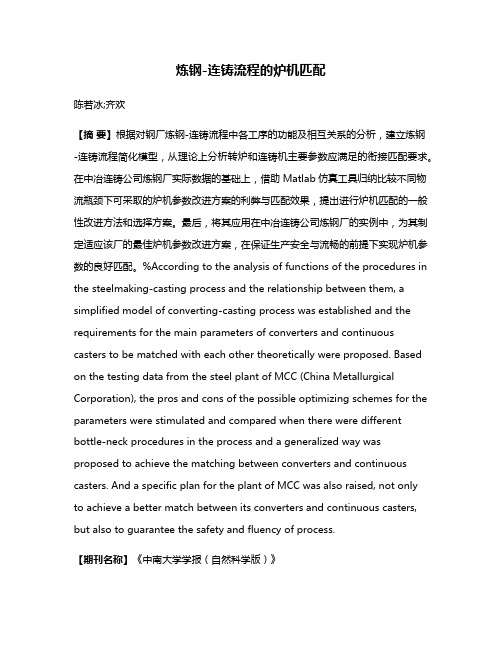
炼钢-连铸流程的炉机匹配陈若冰;齐欢【摘要】根据对钢厂炼钢-连铸流程中各工序的功能及相互关系的分析,建立炼钢-连铸流程简化模型,从理论上分析转炉和连铸机主要参数应满足的衔接匹配要求。
在中冶连铸公司炼钢厂实际数据的基础上,借助Matlab仿真工具归纳比较不同物流瓶颈下可采取的炉机参数改进方案的利弊与匹配效果,提出进行炉机匹配的一般性改进方法和选择方案。
最后,将其应用在中冶连铸公司炼钢厂的实例中,为其制定适应该厂的最佳炉机参数改进方案,在保证生产安全与流畅的前提下实现炉机参数的良好匹配。
%According to the analysis of functions of the procedures in the steelmaking-casting process and the relationship between them, a simplified model of converting-casting process was established and the requirements for the main parameters of converters and continuous casters to be matched with each other theoretically were proposed. Based on the testing data from the steel plant of MCC (China Metallurgical Corporation), the pros and cons of the possible optimizing schemes for the parameters were stimulated and compared when there were different bottle-neck procedures in the process and a generalized way was proposed to achieve the matching between converters and continuous casters. And a specific plan for the plant of MCC was also raised, not onlyto achieve a better match between its converters and continuous casters, but also to guarantee the safety and fluency of process.【期刊名称】《中南大学学报(自然科学版)》【年(卷),期】2011(042)006【总页数】7页(P1650-1656)【关键词】炼钢-连铸系统;炉机匹配;参数优化【作者】陈若冰;齐欢【作者单位】华中科技大学控制科学与工程系,湖北武汉,430074;华中科技大学控制科学与工程系,湖北武汉,430074【正文语种】中文【中图分类】TF758随着钢铁技术的快速发展,钢铁生产的设备与技术都发生了显著变化,在这样动态更新的过程中,工序的匹配程度已成为影响系统运行效率的重要基础。
《连铸工艺与设备》讲稿1

另外,还可以按铸坯断面形状分为方坯连铸机、圆坯连铸机、板坯连铸机、异形坯连铸机、方/板坯兼用型连铸机等。
按钢水的静压头可分为高头型、低头型和超低头型连铸机等。
3.1立式连铸机
立式连铸机是20世纪50年代至60年代初的主要机型。立式连铸机,从中间罐到切割装置等主要设备均布置在垂直中心线上,整个机身矗立在车间地平面以上。采用立式连铸机
图0-2 1972年以来我国连铸坯产量和连铸比的增长
1-钢总产量;2-连铸比;3-连铸坯产量
3连铸机的机型及其特点
连铸机的分类方式很多。按结晶器是否移动可以分为两类:
1)固定式结晶器:包括固定振动结晶器的各种连铸机,如立式连铸机、立弯式连铸机、弧形连铸机、椭圆形连铸机、水平式连铸机等。这些机型已成为现代化连铸机的基本机型,如图3所示。
进入20世纪60年代,弧形连铸机的问世,使连铸技术出现了一次飞跃。世界第一台弧形连铸机于1964年4月在奥地利百录厂诞生。同年6月由我国自行设计制造的第1台方坯和板坯兼用弧形连铸机在重钢三厂投入生产。此后不久,在前联邦德国又上马了1台宽板弧形连铸机,并开发应用了浸入式水口和保护渣技术。同年英国谢尔顿厂率先实现全连铸生产,共有4台连铸机11流,主要生产低合金钢和低碳钢,浇注断面为140mm×140mm和432mm×632mm的铸坯。也开发应用了浸入式水口和保护渣技术。1967年由美钢联工程咨询公司设计并在格里厂投产1台采用直结晶器、带液心弯曲的弧形连铸机。同一年在胡金根厂相继投产了2台超低头板坯连铸机,浇注断面为(150~250)mm×(1800~2500)mm的铸坯,该铸机至今仍在运行。
11连铸工艺与设备连铸连轧的匹配XXXX

11.1 连铸与轧制的衔接工艺
连铸坯的断面形状和规格受炼钢炉容量及轧材品种规格和质量要求等因素的制约。铸机的生产能力应与炼钢及轧钢的能力相匹配,铸坯的断面和规格应与轧机所需原料及产品规格相匹配(见表2-1及表2-2),并保证一定的压缩比(见表2-3)。为实现连铸与轧制过程的连续化生产,应使连铸机生产能力略大于炼钢能力,而轧钢能力又要略大于连铸能力(例如约大10%),才能保证产量的匹配关系。
连铸坯热送热装和直接轧制工艺的主要优点是:(1)利用连铸坯冶金热能,节约能源消耗。节能效果显著,直接轧制可比常规冷装炉加热轧制工艺节能80%~85%;(2)提高成材率,节约金属消耗。由于加热时间缩短使铸坯烧损减少,例如高温直接热装(DHCR)或直接轧制,可使成材率提高0.5%~1.5%;(3)简化生产工艺流程,减少厂房面积和运输各项设备,节约基建投资和生产费用。
钢铁生产工艺流程发展方向:连续化、紧凑化、自动化。实现钢铁生产连续化的关键之一是实现钢水铸造凝固和变形过程的连续化,亦即实现连铸-连轧过程的连续化。连铸与轧制的连续衔接匹配问题包括产量的匹配、铸坯规格的匹配、生产节奏的匹配、温度与热能的衔接与控制以及钢坯表面质量与组织性能的传递与调控等多方面的技术,其中产量、规格和节奏匹配是基本条件,质量控制是基础,而温度与热能的衔接调控则是技术关键。
11.4 CC-DR工艺
连铸-直接轧制(CC-DR)工艺与采用的关键技术A 保证温度的技术1-钢包输送;2-恒高速浇注;3-板坯测量;4-雾化二次冷却;5-液芯前端位置控制;6-铸机内及辊道周围绝热;7-短运送线及转盘;8-边部温度补偿器(ETC);9-边部质量补偿器(EQC);10-中间坯增厚;11-高速穿带B.保证质量的技术1-转炉出渣孔堵塞;2-成分控制;3-真空处理RH;4-钢包-中间包-结晶器保护;5-加大中间包;6-结晶器液面控制;7-适当的渣粉;8-缩短辊子间距;9-四点矫直;10-压缩铸造;11-利用计算机系统判断质量;12-毛刺清理装置C 保证计划安排的技术1-高速改变结晶器宽度;2-VSB宽度大压下;3-生产制度的计算机控制系统;4-减少分级数D 保证机组可靠性的技术1-辊子在线调整检查;2-辊子冷却;3-加强铸机及辊子强度
连铸工艺与设备1

连铸工艺与设备1连铸工艺与设备1连铸是一种现代钢铁生产工艺,是通过连续浇铸技术将液态钢铁直接铸造成连续坯,进而实现高效率的钢材生产。
连铸工艺与设备是该工艺实施所必需的组成部分,对于钢铁企业的生产效率和质量控制具有重要影响。
连铸工艺的主要步骤包括:浇注、结晶器、凝固、拉伸、切割和冷却等。
首先,通过浇注将液态钢铁注入结晶器中,结晶器中装有冷却剂,使钢水迅速冷却并凝固形成坯料。
然后,通过拉伸机械将坯料进行拉伸,拉伸过程中继续凝固,最终形成长期坯料。
接下来,切割机械将长期坯料切割成合适的长度,并通过冷却设备对坯料进行冷却,使其达到适宜的温度。
连铸工艺与设备应具备以下特点:高效率、高质量和节能环保。
首先,高效率是指连铸工艺与设备能够实现高产量和高利用率。
连铸工艺可以连续生产钢材,大大提高了生产效率。
而连铸设备的设计和制造应该保证设备的稳定性,减少故障和停工时间。
其次,高质量要求连铸工艺与设备能够实现钢材的一致性和均匀性。
结晶器的设计和冷却剂的使用都需要考虑坯料的凝固速度和结晶质量。
同时,拉伸机械的控制能够保证坯料的拉伸速度均匀,从而保证钢材的质量。
最后,节能环保是指连铸工艺与设备应该尽可能减少能源消耗和环境污染。
例如,在冷却过程中可以利用循环水来降低能耗,并且对废水进行处理。
近年来,随着工业技术的不断发展,连铸工艺与设备也得到了提升和改进。
连铸工艺的铸造速度和坯料尺寸得到了提高,可以生产出更大尺寸的钢材。
同时,连铸设备的自动化程度不断提高,减少了人工操作,提高了生产效率和安全性。
在连铸过程中,还可以采用一些先进的监测仪器和控制系统,对铁水的成分、温度和流动情况进行实时监测,从而保证钢材质量的稳定性和一致性。
总之,连铸工艺与设备是实现高效率、高质量和节能环保的钢铁生产的重要组成部分。
随着技术的发展,连铸工艺与设备也在不断改进和完善,为钢铁企业的发展提供了强大的支持。
同时,工艺与设备的优化也促进了钢铁产业的可持续发展。
薄板坯连铸连轧设备及工艺流程
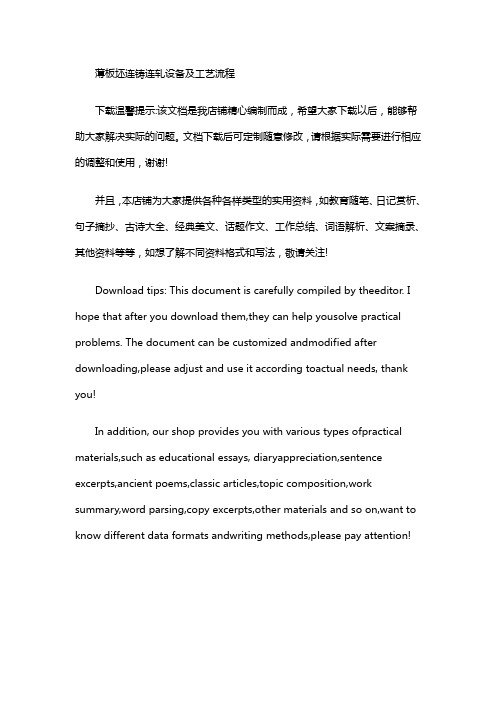
薄板坯连铸连轧设备及工艺流程下载温馨提示:该文档是我店铺精心编制而成,希望大家下载以后,能够帮助大家解决实际的问题。
文档下载后可定制随意修改,请根据实际需要进行相应的调整和使用,谢谢!并且,本店铺为大家提供各种各样类型的实用资料,如教育随笔、日记赏析、句子摘抄、古诗大全、经典美文、话题作文、工作总结、词语解析、文案摘录、其他资料等等,如想了解不同资料格式和写法,敬请关注!Download tips: This document is carefully compiled by theeditor. I hope that after you download them,they can help yousolve practical problems. The document can be customized andmodified after downloading,please adjust and use it according toactual needs, thank you!In addition, our shop provides you with various types ofpractical materials,such as educational essays, diaryappreciation,sentence excerpts,ancient poems,classic articles,topic composition,work summary,word parsing,copy excerpts,other materials and so on,want to know different data formats andwriting methods,please pay attention!薄板坯连铸连轧是一种将连铸薄板坯直接进行热轧的短流程生产方式,具有节能、高效、减少投资等优点。
连铸工艺与设备之连铸连轧的匹配
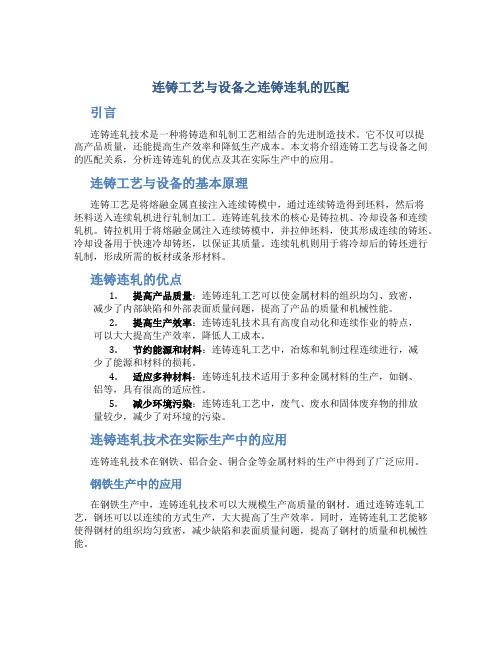
连铸工艺与设备之连铸连轧的匹配引言连铸连轧技术是一种将铸造和轧制工艺相结合的先进制造技术。
它不仅可以提高产品质量,还能提高生产效率和降低生产成本。
本文将介绍连铸工艺与设备之间的匹配关系,分析连铸连轧的优点及其在实际生产中的应用。
连铸工艺与设备的基本原理连铸工艺是将熔融金属直接注入连续铸模中,通过连续铸造得到坯料,然后将坯料送入连续轧机进行轧制加工。
连铸连轧技术的核心是铸拉机、冷却设备和连续轧机。
铸拉机用于将熔融金属注入连续铸模中,并拉伸坯料,使其形成连续的铸坯。
冷却设备用于快速冷却铸坯,以保证其质量。
连续轧机则用于将冷却后的铸坯进行轧制,形成所需的板材或条形材料。
连铸连轧的优点1.提高产品质量:连铸连轧工艺可以使金属材料的组织均匀、致密,减少了内部缺陷和外部表面质量问题,提高了产品的质量和机械性能。
2.提高生产效率:连铸连轧技术具有高度自动化和连续作业的特点,可以大大提高生产效率,降低人工成本。
3.节约能源和材料:连铸连轧工艺中,冶炼和轧制过程连续进行,减少了能源和材料的损耗。
4.适应多种材料:连铸连轧技术适用于多种金属材料的生产,如钢、铝等,具有很高的适应性。
5.减少环境污染:连铸连轧工艺中,废气、废水和固体废弃物的排放量较少,减少了对环境的污染。
连铸连轧技术在实际生产中的应用连铸连轧技术在钢铁、铝合金、铜合金等金属材料的生产中得到了广泛应用。
钢铁生产中的应用在钢铁生产中,连铸连轧技术可以大规模生产高质量的钢材。
通过连铸连轧工艺,钢坯可以以连续的方式生产,大大提高了生产效率。
同时,连铸连轧工艺能够使得钢材的组织均匀致密,减少缺陷和表面质量问题,提高了钢材的质量和机械性能。
铝合金生产中的应用在铝合金生产中,连铸连轧技术可以生产高精度、高品质的铝板和铝带。
通过连续轧制,铝坯可以得到所需的尺寸和厚度,并且具有优良的表面质量。
连铸连轧技术在高速列车、汽车和航空航天等领域的铝合金材料生产中得到了广泛应用。
连铸设备及工艺
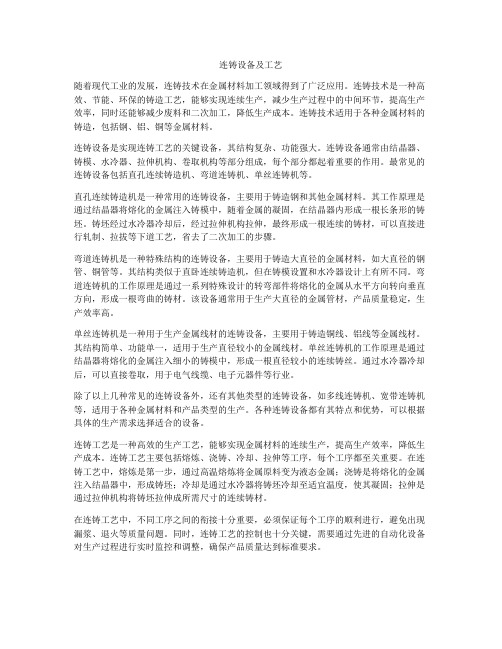
连铸设备及工艺随着现代工业的发展,连铸技术在金属材料加工领域得到了广泛应用。
连铸技术是一种高效、节能、环保的铸造工艺,能够实现连续生产,减少生产过程中的中间环节,提高生产效率,同时还能够减少废料和二次加工,降低生产成本。
连铸技术适用于各种金属材料的铸造,包括钢、铝、铜等金属材料。
连铸设备是实现连铸工艺的关键设备,其结构复杂、功能强大。
连铸设备通常由结晶器、铸模、水冷器、拉伸机构、卷取机构等部分组成,每个部分都起着重要的作用。
最常见的连铸设备包括直孔连续铸造机、弯道连铸机、单丝连铸机等。
直孔连续铸造机是一种常用的连铸设备,主要用于铸造钢和其他金属材料。
其工作原理是通过结晶器将熔化的金属注入铸模中,随着金属的凝固,在结晶器内形成一根长条形的铸坯。
铸坯经过水冷器冷却后,经过拉伸机构拉伸,最终形成一根连续的铸材,可以直接进行轧制、拉拔等下道工艺,省去了二次加工的步骤。
弯道连铸机是一种特殊结构的连铸设备,主要用于铸造大直径的金属材料,如大直径的钢管、铜管等。
其结构类似于直卧连续铸造机,但在铸模设置和水冷器设计上有所不同。
弯道连铸机的工作原理是通过一系列特殊设计的转弯部件将熔化的金属从水平方向转向垂直方向,形成一根弯曲的铸材。
该设备通常用于生产大直径的金属管材,产品质量稳定,生产效率高。
单丝连铸机是一种用于生产金属线材的连铸设备,主要用于铸造铜线、铝线等金属线材。
其结构简单、功能单一,适用于生产直径较小的金属线材。
单丝连铸机的工作原理是通过结晶器将熔化的金属注入细小的铸模中,形成一根直径较小的连续铸丝。
通过水冷器冷却后,可以直接卷取,用于电气线缆、电子元器件等行业。
除了以上几种常见的连铸设备外,还有其他类型的连铸设备,如多线连铸机、宽带连铸机等,适用于各种金属材料和产品类型的生产。
各种连铸设备都有其特点和优势,可以根据具体的生产需求选择适合的设备。
连铸工艺是一种高效的生产工艺,能够实现金属材料的连续生产,提高生产效率,降低生产成本。
薄板坯连铸连轧工艺与设备
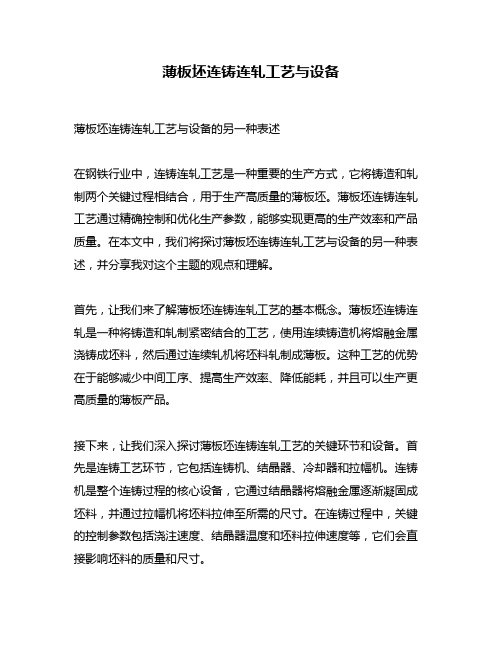
薄板坯连铸连轧工艺与设备薄板坯连铸连轧工艺与设备的另一种表述在钢铁行业中,连铸连轧工艺是一种重要的生产方式,它将铸造和轧制两个关键过程相结合,用于生产高质量的薄板坯。
薄板坯连铸连轧工艺通过精确控制和优化生产参数,能够实现更高的生产效率和产品质量。
在本文中,我们将探讨薄板坯连铸连轧工艺与设备的另一种表述,并分享我对这个主题的观点和理解。
首先,让我们来了解薄板坯连铸连轧工艺的基本概念。
薄板坯连铸连轧是一种将铸造和轧制紧密结合的工艺,使用连续铸造机将熔融金属浇铸成坯料,然后通过连续轧机将坯料轧制成薄板。
这种工艺的优势在于能够减少中间工序、提高生产效率、降低能耗,并且可以生产更高质量的薄板产品。
接下来,让我们深入探讨薄板坯连铸连轧工艺的关键环节和设备。
首先是连铸工艺环节,它包括连铸机、结晶器、冷却器和拉幅机。
连铸机是整个连铸过程的核心设备,它通过结晶器将熔融金属逐渐凝固成坯料,并通过拉幅机将坯料拉伸至所需的尺寸。
在连铸过程中,关键的控制参数包括浇注速度、结晶器温度和坯料拉伸速度等,它们会直接影响坯料的质量和尺寸。
然后是连轧工艺环节,它包括轧机、冷却机和切割机。
轧机是将坯料经过多次轧制,逐渐压制成所需的薄板的关键设备。
在连轧过程中,轧机的参数设置和轧制力的控制是至关重要的,它们会直接影响薄板的厚度均匀性和机械性能。
冷却机则用于降低薄板的温度,并使其达到所需的硬度和强度。
最后,切割机将连续轧制的薄板切割成所需的长度。
综上所述,薄板坯连铸连轧工艺与设备的另一种表述是将铸造和轧制两个关键过程紧密结合,通过连续铸造机和连续轧机实现高效生产高质量的薄板产品。
在这个过程中,关键的控制参数和设备设置会直接影响产品的质量和性能。
对于工艺和设备的优化,需要综合考虑生产效率、质量要求和能源消耗等因素。
在我看来,薄板坯连铸连轧工艺是钢铁行业向高效、高质量生产转型的重要一环。
它通过精确控制和优化生产参数,实现了坯料的连续生产和轧制,大大提高了生产效率和产品质量。
连铸连轧生产工艺
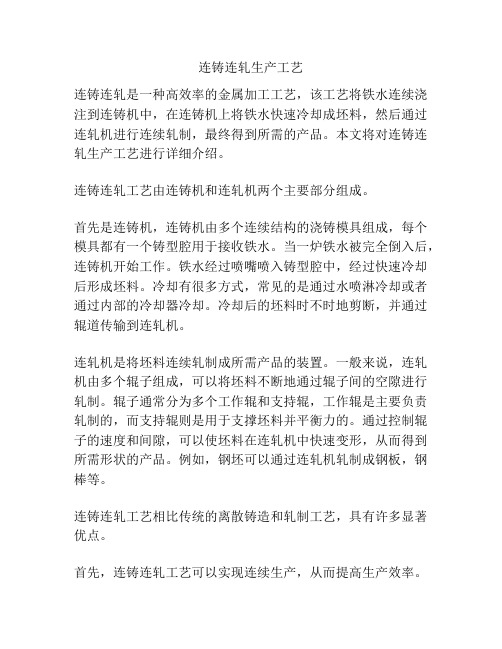
连铸连轧生产工艺连铸连轧是一种高效率的金属加工工艺,该工艺将铁水连续浇注到连铸机中,在连铸机上将铁水快速冷却成坯料,然后通过连轧机进行连续轧制,最终得到所需的产品。
本文将对连铸连轧生产工艺进行详细介绍。
连铸连轧工艺由连铸机和连轧机两个主要部分组成。
首先是连铸机,连铸机由多个连续结构的浇铸模具组成,每个模具都有一个铸型腔用于接收铁水。
当一炉铁水被完全倒入后,连铸机开始工作。
铁水经过喷嘴喷入铸型腔中,经过快速冷却后形成坯料。
冷却有很多方式,常见的是通过水喷淋冷却或者通过内部的冷却器冷却。
冷却后的坯料时不时地剪断,并通过辊道传输到连轧机。
连轧机是将坯料连续轧制成所需产品的装置。
一般来说,连轧机由多个辊子组成,可以将坯料不断地通过辊子间的空隙进行轧制。
辊子通常分为多个工作辊和支持辊,工作辊是主要负责轧制的,而支持辊则是用于支撑坯料并平衡力的。
通过控制辊子的速度和间隙,可以使坯料在连轧机中快速变形,从而得到所需形状的产品。
例如,钢坯可以通过连轧机轧制成钢板,钢棒等。
连铸连轧工艺相比传统的离散铸造和轧制工艺,具有许多显著优点。
首先,连铸连轧工艺可以实现连续生产,从而提高生产效率。
相比离散铸造和轧制工艺,连铸连轧工艺减少了产品在生产过程中的停留时间,有效减少生产周期,提高了生产效率。
其次,连铸连轧工艺可以减少产品的变形和出现缺陷的可能性。
在连铸连轧过程中,坯料的变形是在连续产生的,产品形状相对稳定,因此可以减少变形和出现缺陷的可能性。
同时,由于坯料在连轧过程中受到很大压力的作用,使其内部结构更加紧密,提高了产品的强度和硬度。
最后,连铸连轧工艺还可以减少能耗并降低生产成本。
连续生产可以减少能耗浪费,同时由于工艺参数的控制更加精准,可以减少废品率,降低了生产成本。
总之,连铸连轧是一种高效率的金属加工工艺,通过连续的铸造和轧制过程,可以快速地生产出所需的产品。
其优点包括高生产效率,减少变形和缺陷的可能性,降低能耗和生产成本等。
连铸工艺与设备之连铸连轧的匹配
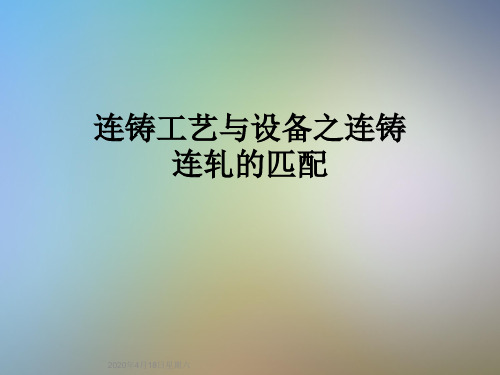
组织性能有更大的提高。
11.3连铸坯热装及直接轧制技术发展概况
连铸连轧技术的起源
•传统轧 钢工序 能源消 耗情况
•加热炉-57.5% •电能-38.6% •其他-3.9%。
•节能的潜 力
20世纪50年代初期,开始实验研究工作,先后 建立了一些连铸连轧试验性机组进行探讨。
连铸-在线同步轧制 •含义
连铸与轧制在同一作业线上,铸坯出连铸机后, 不经切断即直接进行与铸速同步的轧制。
•特点 先轧制后切断,铸与轧同步,铸坯一般要进行在 线加热均温或绝热保温,每流连铸需配置专用轧机( 行星轧机或摆锻机和连锻机),轧机数目1~13架。
可使成材率提高0.5%~1.5%。 3. 简化生产工艺流程 • 减少厂房面积和运输设备,节约基建投资和生产费
用。
•11.2 连铸与连轧衔接工艺类型
4. 生产周期缩短 ➢ 从投料炼钢到轧制出成品仅需几个小时; ➢ 直接轧制时从钢水浇注到轧出成品只需十几分钟
。 5. 产品的质量提高 ➢ 加热时间短,氧化铁皮少,钢材表面质量好; ➢ 无加热炉滑道痕迹,使产品厚度精度也得到提高
•类型3、4为铸坯冷至A3甚至A1线以下温度装炉,称 为低温热装轧制工艺,简称HCR(Hot Charge
Rolling)
•特点:装炉温度一 般在400~700℃之 间。而低温热装工
艺,则常在加热炉
之前还有保温坑或
保温箱等,即采用
双重缓冲工序,以
解决铸、轧节奏匹
配与计划管理问题
。
•类型5为传统的连铸坯冷装炉轧制工艺,简称CCR(Cold Charge Rolling)
•特点:连铸坯 冷至常温后, 再装炉加热后 轧制,一般连 铸坯装炉的温 度在400℃以下 。
短流程连铸连轧成套装备的制造工艺和工程布局

短流程连铸连轧成套装备的制造工艺和工程布局短流程连铸连轧成套装备是一种先进的工艺装备,它能够将铁水直接转化为精细的板材,具有高效、节能、环保等优点。
本文将介绍短流程连铸连轧成套装备的制造工艺和工程布局。
一、制造工艺1. 连铸连铸是将熔化的金属注入连续铸模中,通过快速冷却和凝固,形成连续坯料。
短流程连铸采用的是氧化物冷却剂连续铸模技术,通过喷水冷却,快速凝固,使铸坯变薄、宽度增大,提高了生产效率。
2. 连轧连轧是将连续坯料经过多道次的轧制加工,形成具有一定规格和性能要求的板材。
短流程连铸连轧采用的是快速轧制技术,通过液压控制系统控制辊缝调节,实现轧制速度的快速调整,提高了板材的质量和生产效率。
3. 热处理热处理是对板材进行加热和冷却处理,以改善材料的性能和组织结构。
短流程连铸连轧装备中的热处理设备,采用先进的间歇加热技术和快速冷却技术,保证了板材的机械性能和物理性能。
4. 轧机调整轧机调整是针对不同规格和性能要求的板材,对连铸连轧装备进行参数调整和设备配置的过程。
短流程连铸连轧装备采用智能化的控制系统,可以根据板材的要求自动调整轧机的参数,提高了生产的灵活性和效率。
二、工程布局1. 轧机生产线轧机生产线是短流程连铸连轧装备的核心部分,包括轧机、连铸机、热处理设备等。
轧机生产线的布局应尽量紧凑,以确保连续生产的流程顺畅和效率高。
同时,还需要考虑轧机生产线与其他生产线的协调和配合,提高整体生产效率。
2. 辅助设备辅助设备包括钢水净化设备、除渣设备、冷却设备等,用于辅助轧机生产线工作。
辅助设备的布局应与轧机生产线结合紧密,确保各个设备之间的协调和衔接,提高生产效率和产品质量。
3. 能源控制能源控制是短流程连铸连轧装备的重要方面,包括电力、水、气等能源的供应和控制。
在工程布局中,应合理设置能源控制中心,实现对各个能源的集中控制和监测,提高能源的利用效率和生产的可持续发展。
4. 安全环保安全环保是短流程连铸连轧装备的基本要求,应在工程布局中考虑相关的设备和措施。
连铸工艺设备连铸设备及主要工艺参数
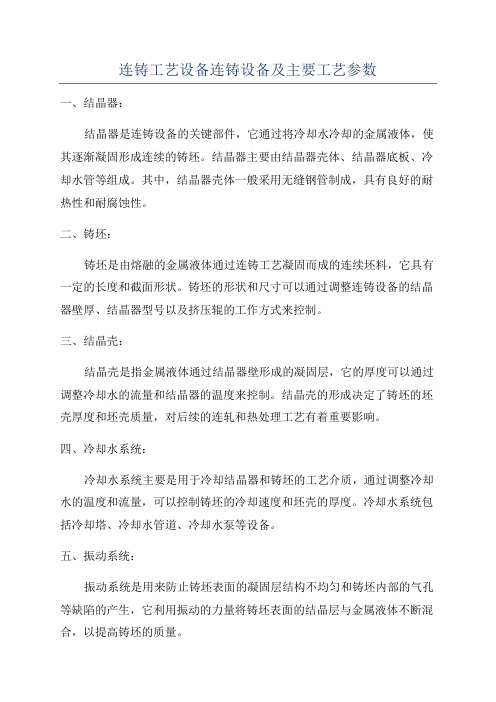
连铸工艺设备连铸设备及主要工艺参数一、结晶器:结晶器是连铸设备的关键部件,它通过将冷却水冷却的金属液体,使其逐渐凝固形成连续的铸坯。
结晶器主要由结晶器壳体、结晶器底板、冷却水管等组成。
其中,结晶器壳体一般采用无缝钢管制成,具有良好的耐热性和耐腐蚀性。
二、铸坯:铸坯是由熔融的金属液体通过连铸工艺凝固而成的连续坯料,它具有一定的长度和截面形状。
铸坯的形状和尺寸可以通过调整连铸设备的结晶器壁厚、结晶器型号以及挤压辊的工作方式来控制。
三、结晶壳:结晶壳是指金属液体通过结晶器壁形成的凝固层,它的厚度可以通过调整冷却水的流量和结晶器的温度来控制。
结晶壳的形成决定了铸坯的坯壳厚度和坯壳质量,对后续的连轧和热处理工艺有着重要影响。
四、冷却水系统:冷却水系统主要是用于冷却结晶器和铸坯的工艺介质,通过调整冷却水的温度和流量,可以控制铸坯的冷却速度和坯壳的厚度。
冷却水系统包括冷却塔、冷却水管道、冷却水泵等设备。
五、振动系统:振动系统是用来防止铸坯表面的凝固层结构不均匀和铸坯内部的气孔等缺陷的产生,它利用振动的力量将铸坯表面的结晶层与金属液体不断混合,以提高铸坯的质量。
六、铸坯切割系统:铸坯切割系统是将连铸的整坯切割成所需长度的小块铸件,以便后续的加工和使用。
铸坯切割系统包括切割机、切割刀具等设备。
七、传动系统:传动系统主要是将连铸工艺设备的动力传递给各个部件,以确保连铸过程的连续和稳定。
传动系统包括电机、减速机、联轴器等设备。
八、电气控制系统:电气控制系统是连铸设备各个部件之间的信息交流和工艺参数调整的重要手段,它通过传感器、PLC控制器等设备实现对连铸过程的自动控制。
与连铸设备相关的主要工艺参数包括:1.结晶器温度:结晶器温度决定了铸坯的凝固速度和结晶壳的厚度,通常在1000℃-1500℃之间。
2. 冷却水流量:冷却水的流量决定了铸坯的冷却速度和坯壳的厚度,通常在20-100L/min之间。
3. 振动频率和振幅:振动频率和振幅的调节可以改善铸坯的结晶层结构,通常在50-150Hz和0.2-0.5mm之间。
连铸连轧工艺及设备
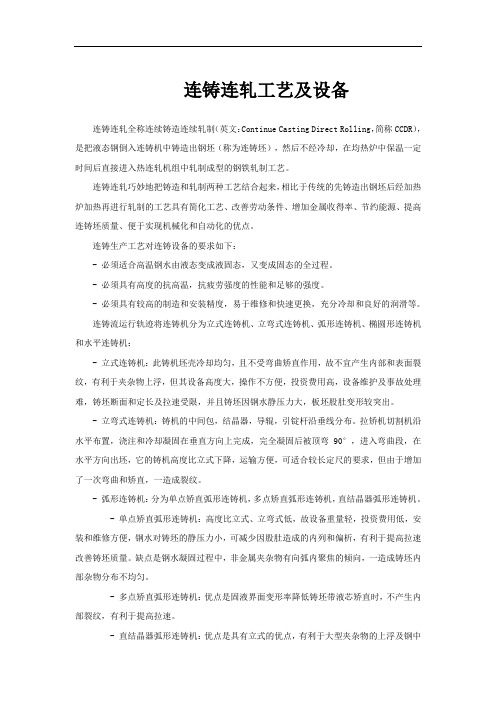
连铸连轧工艺及设备连铸连轧全称连续铸造连续轧制(英文:Continue Casting Direct Rolling,简称CCDR),是把液态钢倒入连铸机中铸造出钢坯(称为连铸坯),然后不经冷却,在均热炉中保温一定时间后直接进入热连轧机组中轧制成型的钢铁轧制工艺。
连铸连轧巧妙地把铸造和轧制两种工艺结合起来,相比于传统的先铸造出钢坯后经加热炉加热再进行轧制的工艺具有简化工艺、改善劳动条件、增加金属收得率、节约能源、提高连铸坯质量、便于实现机械化和自动化的优点。
连铸生产工艺对连铸设备的要求如下:- 必须适合高温钢水由液态变成液固态,又变成固态的全过程。
- 必须具有高度的抗高温,抗疲劳强度的性能和足够的强度。
- 必须具有较高的制造和安装精度,易于维修和快速更换,充分冷却和良好的润滑等。
连铸流运行轨迹将连铸机分为立式连铸机、立弯式连铸机、弧形连铸机、椭圆形连铸机和水平连铸机:- 立式连铸机:此铸机坯壳冷却均匀,且不受弯曲矫直作用,故不宜产生内部和表面裂纹,有利于夹杂物上浮,但其设备高度大,操作不方便,投资费用高,设备维护及事故处理难,铸坯断面和定长及拉速受限,并且铸坯因钢水静压力大,板坯股肚变形较突出。
- 立弯式连铸机:铸机的中间包,结晶器,导辊,引锭杆沿垂线分布。
拉矫机切割机沿水平布置,浇注和冷却凝固在垂直方向上完成,完全凝固后被顶弯90°,进入弯曲段,在水平方向出坯,它的铸机高度比立式下降,运输方便,可适合较长定尺的要求,但由于增加了一次弯曲和矫直,一造成裂纹。
- 弧形连铸机:分为单点矫直弧形连铸机,多点矫直弧形连铸机,直结晶器弧形连铸机。
- 单点矫直弧形连铸机:高度比立式、立弯式低,故设备重量轻,投资费用低,安装和维修方便,钢水对铸坯的静压力小,可减少因股肚造成的内列和偏析,有利于提高拉速改善铸坯质量。
缺点是钢水凝固过程中,非金属夹杂物有向弧内聚焦的倾向,一造成铸坯内部杂物分布不均匀。
- 多点矫直弧形连铸机:优点是固液界面变形率降低铸坯带液芯矫直时,不产生内部裂纹,有利于提高拉速。
薄板坯连铸连轧工艺与设备

薄板坯连铸连轧工艺与设备薄板坯连铸连轧是一种用于生产薄板钢的高效工艺。
它以连续铸造和连续轧制钢材为主要特征,利用自动控制技术实现高效生产。
以下是薄板坯连铸连轧的工艺与设备分析。
工艺原理:薄板坯连铸连轧的工艺原理是先将钢液通过连铸机连续铸造成板坯,再通过热连轧机将板坯不断地轧制成薄板材,最终冷却成为薄板钢。
其中,连铸机采用高温流体力学模拟和液相结构模拟理论,通过模拟和优化连铸过程中的各项参数(如冷却水量、铸模间隙等)实现自动控制。
而热连轧机则采用高速旋转轧辊,通过实时纠偏技术保证铸坯能够保持恒定的厚度和宽度,以便连轧出高质量的薄板。
设备组成:薄板坯连铸连轧工艺涉及到许多关键设备,包括连铸机、热连轧机、辊道、处理设备等。
其中,连铸机是整个工艺中的核心设备,其性能直接影响到钢材质量和生产效率。
连铸机主要由铸机构、冷却装置、支撑架和电气控制系统等组成。
它通过先将钢液浇注到冷却结构中铸造成坯料,然后通过一系列的冷却器进行冷却,最终将坯料不断地冷却成固体。
热连轧机则采用四辊式卷板机,通过热连轧将铸坯压制成所需的薄板。
应用前景:薄板坯连铸连轧是一项高效率、高品质、节能环保的生产技术,结合了连铸和连轧两种现代化生产工艺的优点,具有广泛的应用前景。
在现代工业制造领域,它已成为生产高品质钢材的主要手段。
同时,薄板钢材也是许多工业领域所必需的,如汽车工业、建筑工程、船舶航运、家电制造等。
薄板坯连铸连轧工艺正不断地发展和完善,无论是在国内还是国际市场上,都有着广泛的应用前景。
综上所述,薄板坯连铸连轧工艺是一项高效率、高品质的生产技术,它通过优化工艺和改进设备,使钢材的生产效率和质量得到了显著提高。
该工艺在各行各业中都有着广泛的应用前景,将为现代工业制造提供更为可靠的质量保障和生产保障。
《连铸工艺与设备》课件
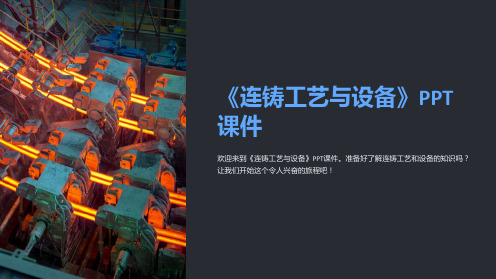
模具
模具形状决定了连铸坯的形状和 尺寸。
冷却系统
通过冷却水冷却铸件,控制连铸 坯的温度。
移动系统
控制模具和冷却系统的移动,实 现连续铸造。
连铸设备结构
分机构
包括机架、传动装置、支撑系统等。
冷却系统
包括水冷却系统和气冷却系统。
控制系统
用于控制整个铸造过程,确保连续铸造的顺利进行。
数据采集和监测系统
监测和记录连铸过程中的数据,以确保产品质量。
连铸设备操作要点
1. 保持设备的清洁和润滑。 2. 定期检查和更换易损件。 3. 严格控制冷却水和熔化金属的温度。 4. 合理调整模具和冷却系统的位置和角度。
常见问题解答ห้องสมุดไป่ตู้
Q: 连铸过程中出现坯料结 疤怎么办?
A: 调整模具和冷却系统的位置和 参数,避免热裂。
Q: 连铸坯的内部缺陷如何 排除?
A: 加强熔化金属的净化和过滤作 业。
连铸产品
生产铜、铝、钢等金属的连铸坯、 板、棒、管等铸造产品。
设备分类
1 立式连铸机
通过重力作用,使熔化金属自上而下流入模具。
2 卧式连铸机
通过压力或真空力,使熔化金属从侧面进入模具。
3 多流连铸机
同时浇注多份熔化金属,提高生产效率。
连铸设备原理
连铸设备利用模具和冷却系统实现连续铸造。熔化金属通过模具,在冷却水的作用下凝固成连铸坯。
《连铸工艺与设备》PPT 课件
欢迎来到《连铸工艺与设备》PPT课件。准备好了解连铸工艺和设备的知识吗? 让我们开始这个令人兴奋的旅程吧!
工艺介绍
连铸工艺是一种高效的铸造工艺,通过连续将熔化金属注入连铸机,实现快速、连续铸造。
连铸工艺优势
铝合金连续铸轧和连铸连轧技术

铝合金连续铸轧和连铸连轧技术
铝合金连续铸轧和连铸连轧技术
铝合金连续铸轧和连铸连轧技术是一种新兴的材料加工技术,它结合
了铸造和轧制的技术,可以实现铝合金材料的连续加工。
连续铸轧工艺,是把铝合金浇液料加热熔融,然后将熔体倒入熔体模,经过一段时间冷却固化后即可得到铸件,并经过轧制加工,从而提高
了铝合金的力学性能和外观质量。
连铸连轧技术,则是将熔体倒入铸轧机中,一次完成浇注和轧制,实
现熔体的连续加工,从而提高了产量和效率,并可以直接改变铸件的
尺寸和形状,并可以提高质量,降低生产成本。
连续铸轧和连铸连轧技术,不仅可以改善铝合金的力学性能,提高外
观质量,而且可以提高产量,降低成本,一定程度上满足大批量生产
的要求。
它已经被广泛应用于车辆制造、航空航天、电力行业等众多
领域,受到了社会的广泛认可。
总之,铝合金连续铸轧和连铸连轧技术是一种新兴的材料加工技术,
它的应用范围广泛,可以改善铝合金的力学性能,提高外观质量,提
高产量,降低成本,有助于提高生产能力和效率,更好地满足社会对
高品质铝合金产品的需求。
- 1、下载文档前请自行甄别文档内容的完整性,平台不提供额外的编辑、内容补充、找答案等附加服务。
- 2、"仅部分预览"的文档,不可在线预览部分如存在完整性等问题,可反馈申请退款(可完整预览的文档不适用该条件!)。
- 3、如文档侵犯您的权益,请联系客服反馈,我们会尽快为您处理(人工客服工作时间:9:00-18:30)。
组织性能有更大的提高。
18
类型5为传统的连铸坯冷装炉轧制工艺,简称CCR(Cold Charge Rolling)
特点:连铸坯 冷至常温后, 再装炉加热后 轧制,一般连 铸坯装炉的温 度在400℃以下。
16
11.2 连铸与连轧衔接工艺类型
CC-DR和HCR工艺的主要优点:
1. 节约能源消耗 ➢ 节能量与热装或补偿加热入炉温度有关,入炉温度越
8
炼钢技术的进步提高了钢的纯净度,近终形连铸对凝 固过程和凝固组织的优化控制,使得保证钢材性能所 需的最小压缩比发生了变化。
除杂质总量外,杂质的种类、粒度和分布也影响压缩 比的选择。当钢中S、P、N、H、O等杂质总量继续下 降时,加上连铸质量的提高,达到钢材基本性能要求 的最小压缩比会继续下降。炼钢-连铸-轧钢三者技术进 步的相互影响,将最终实现铸-轧一体化,即实现所谓 的“极限近终形连铸”加“最小压缩比轧制”的低能 耗、低成本的铸-轧一体化。这不仅对板材生产,而且 也是棒、线、型材生产发展的要求。
连铸工艺与设备
11. 连铸连轧的匹配
课程编号:01014901
课程类型:选修课
学 时: 32
学 分:2
开课对象:材料成型及控制工程专业本科生
先修课程:认识实习、机械设计、金属学、生产实习
2011.5.31
1/68
11.1 连铸与轧制的衔接工艺
钢铁生产工艺流程发展方向:连续化、紧凑化、自 动化。实现钢铁生产连续化的关键之一是实现钢水铸 造凝固和变形过程的连续化,亦即实现连铸-连轧过 程的连续化。 连铸与轧制的连续衔接匹配问题包括产量的匹配、 铸坯规格的匹配、生产节奏的匹配、温度与热能的衔 接与控制以及钢坯表面质量与组织性能的传递与调控 等多方面的技术,其中产量、规格和节奏匹配是基本 条件,质量控制是基础,而温度与热能的衔接调控则 是技术关键。
高,则节能越多; ➢ 直接轧制比常规冷装炉轧制工艺节能80%~85%。 2. 提高成材率,节约金属消耗
加热时间缩短,烧损减少,DHCR或CC-DR工艺,可 使成材率提高0.5%~1.5%。 3. 简化生产工艺流程 减少厂房面积和运输设备,节约基建投资和生产费用。
17
11.2 连铸与连轧衔接工艺类型
无相变工艺。
12
11.2 连铸与连轧衔接工艺类型
类型1为连铸坯直接轧制工艺,简称CC-DR(Continuous Casting-Direct Rolling)或称HDR(Hot Direct Rolling)
特点:铸坯温度在 1100℃以上,铸坯不 需进加热炉加热,只 需在输送过程中进行 补热和均热,即直接 送入轧机进行轧制。 在连铸机与轧机间只 有在线补偿加热而无 正式加热炉缓冲工序。
9
铁碳平衡图
10
11.2 连铸与连轧衔接工艺类型
连铸与轧钢的衔接模式
11
11.2 连铸与连轧衔接工艺类型
类型1’—CR(Cast-Rolling) 类型1—CC-DR 类型2—γ-HCR或DHCR 类型3—(α+ γ)HCR 类型4—CC-αHCR 类型5—CC-CCR冷装炉轧制 钢材生产工艺趋向:连续化,铸轧一体化。 连铸连轧的定义:1及2能实现均衡连续化生产,
11.3连铸坯热装及直接轧制技术发展概况
连铸连轧技术的起源
传统轧 钢工序 能源消 耗情况
加热炉-57.5% 电能-38.6% 其他-3.9%。
节能的潜力
20世纪50年代初期,开始实验研究工作,先后 建立了一些连铸连轧试验性机组进行探讨。
19
11.3连铸坯热装及直接轧制技术发展概况
20世纪60年代后期,出现了工业生产规模的连铸连 轧试验机组。
20世纪70年代中期以前,工业性试验研究和初步应 用阶段。
所采用 的主要 实验研 究方案
在线同步轧制 带液芯轧制 热装炉轧制 直接轧制
主要方式
20
11.3连铸坯热装及直接轧制技术发展概况
连铸-在线同步轧制 含义
14
类型3、4为铸坯冷至A3甚至A1线以下温度装炉,称 为低温热装轧制工艺,简称HCR(Hot Charge Rolling)
特点:装炉温度一 般在400~700℃之 间。而低温热装工 艺,则常在加热炉 之前还有保温坑或 保温箱等,即采用 双重缓冲工序,以 解决铸、轧节奏匹 配与计划管理问题。
15
2
11.1 连铸与轧制的衔接工艺
3
11.1 钢坯断面规格及产量匹配衔接
连铸坯的断面形状和规格受炼钢炉容量及轧材品种 规格和质量要求等因素的制约。铸机的生产能力应与 炼钢及轧钢的能力相匹配,铸坯的断面和规格应与轧 机所需原料及产品规格相匹配(见表2-1及表2-2),并保 证一定的压缩比(见表2-3)。 为实现连铸与轧制过程的连续化生产,应使连铸机 生产能力略大于炼钢能力,而轧钢能力又要略大于连 铸能力(例如约大10%),才能保证产量的匹配关系。
4
表2-1 铸坯的断面和轧机的配合
5
表2-1 铸坯的断面和轧机的配合
6
表2-2 轧钢材横断面积 之比,压缩比是为了保证最终产品的组织结构和机械 性能所需要的最小变形量,是保证内在质量所需的一 个经验数据。高的压缩比可以使变形深透更完全,再 结晶晶粒细化,性能较好。 对一般普碳钢连铸坯,如生产只要求强度性能达标的 钢材产品,压缩比为4~5时就可满足要求。而对于优 质钢、合金钢连铸坯,最小压缩比值不得低于10。
13
类型2为连铸坯直接热装轧制工艺,简称DHCR(Direct Hot Charge Rolling)或称为高温热装炉轧制工艺,简 称γ-HCR(γ-Hot Charge Rolling)
特点:装炉温度在 700~1000℃左右, 即在A3线以上奥氏 体状态直接装炉, 加热到轧制温度后 进行轧制。只有加 热炉缓冲工序且能 保持连续高温装炉 生产节奏的称为直 接(高温)热装轧制 工艺。