铝合金挤压生产知识
铝合金挤出成型工艺
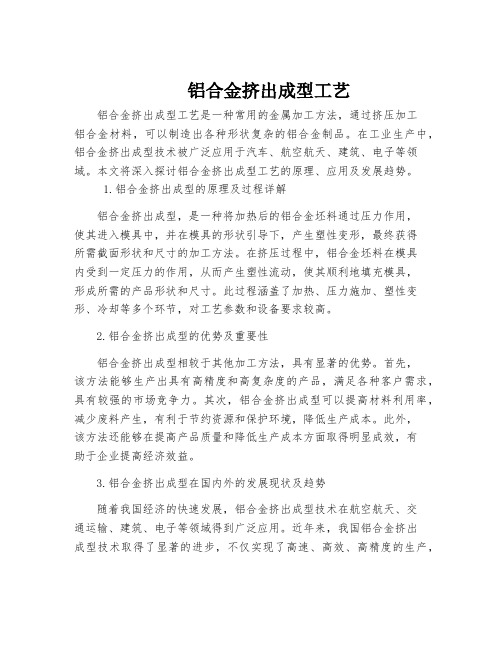
铝合金挤出成型工艺铝合金挤出成型工艺是一种常用的金属加工方法,通过挤压加工铝合金材料,可以制造出各种形状复杂的铝合金制品。
在工业生产中,铝合金挤出成型技术被广泛应用于汽车、航空航天、建筑、电子等领域。
本文将深入探讨铝合金挤出成型工艺的原理、应用及发展趋势。
1.铝合金挤出成型的原理及过程详解铝合金挤出成型,是一种将加热后的铝合金坯料通过压力作用,使其进入模具中,并在模具的形状引导下,产生塑性变形,最终获得所需截面形状和尺寸的加工方法。
在挤压过程中,铝合金坯料在模具内受到一定压力的作用,从而产生塑性流动,使其顺利地填充模具,形成所需的产品形状和尺寸。
此过程涵盖了加热、压力施加、塑性变形、冷却等多个环节,对工艺参数和设备要求较高。
2.铝合金挤出成型的优势及重要性铝合金挤出成型相较于其他加工方法,具有显著的优势。
首先,该方法能够生产出具有高精度和高复杂度的产品,满足各种客户需求,具有较强的市场竞争力。
其次,铝合金挤出成型可以提高材料利用率,减少废料产生,有利于节约资源和保护环境,降低生产成本。
此外,该方法还能够在提高产品质量和降低生产成本方面取得明显成效,有助于企业提高经济效益。
3.铝合金挤出成型在国内外的发展现状及趋势随着我国经济的快速发展,铝合金挤出成型技术在航空航天、交通运输、建筑、电子等领域得到广泛应用。
近年来,我国铝合金挤出成型技术取得了显著的进步,不仅实现了高速、高效、高精度的生产,还大幅提高了材料利用率。
在国际市场上,铝合金挤出成型技术也备受关注,各国纷纷加大研发力度,以期在激烈的市场竞争中占得先机。
4.铝合金挤出成型技术的发展方向及挑战未来,铝合金挤出成型技术的发展方向将主要包括以下几个方面:提高生产效率,降低能耗;提高产品精度,实现精细化生产;研发新型模具材料,提高模具寿命;发展绿色制造,减少废弃物产生。
然而,在技术发展过程中,铝合金挤出成型面临着一系列挑战,如设备研发、工艺优化、环保要求等。
铝合金挤压成型工艺

铝合金挤压成型工艺铝合金挤压成型工艺是一种常见的金属加工方法,通过将铝合金材料加热至一定温度,然后通过挤压机将其挤压成所需形状的工件。
该工艺具有高效、精准、重复性好等优点,在许多工业领域得到广泛应用。
本文将对铝合金挤压成型工艺进行详细介绍。
一、工艺流程铝合金挤压成型工艺的一般流程包括材料准备、加热、模具设计、挤压加工、冷却和后续处理等环节。
1.材料准备铝合金挤压成型的首要工作是选取合适的铝合金材料。
通常选择具有良好塑性和可挤压性的铝合金,如6063、6061等。
在选取材料时,还需要考虑工件的用途、强度要求和耐腐蚀性等因素。
2.加热选取好的铝合金材料后,需要将其加热至一定温度。
加热的目的是使铝合金材料变软和可塑性增加,便于进行挤压加工。
加热温度一般控制在材料的连续搬运温区。
3.模具设计模具设计是铝合金挤压成型工艺中非常关键的一环。
模具的设计需要考虑工件的形状、尺寸、挤压比和冷却方式等因素。
合理的模具设计可以确保工件的质量和尺寸精度。
4.挤压加工在加热和模具设计完成后,将铝合金材料放入挤压机中进行挤压加工。
挤压机通过给定的冲程和行程将铝合金材料挤压入模具中,并形成所需形状的工件。
挤压过程需要控制好挤压速度和压力,以保证工件的质量和形状。
5.冷却挤压完成后,将工件进行冷却以增加其强度和硬度。
冷却可以通过自然冷却或水冷方式进行。
6.后续处理部分工件需要进行后续处理,如修整、打磨、抛光等工序,以进一步提高工件的表面质量和光洁度。
二、工艺参数及影响因素铝合金挤压成型工艺中的一些关键参数包括挤压温度、挤压速度、挤压比和模具温度等。
1.挤压温度挤压温度是指将铝合金材料加热至一定温度后进行挤压加工的温度。
挤压温度的选择需要考虑材料的可塑性和粘度,一般在材料的连续搬运温区进行挤压。
2.挤压速度挤压速度是指铝合金材料在挤压机中的运动速度。
挤压速度的选择需要平衡生产效率和工件质量的要求,过快的挤压速度可能导致工件表面粗糙,过慢的挤压速度可能影响生产效率。
铝挤型材生产工艺

铝挤型材生产工艺
铝挤型材是一种常用的铝合金型材,其生产工艺通常包括以下几个步骤:
1. 原材料准备:首先需要准备适量的铝合金坯料,根据产品的要求选择合适的铝合金牌号和规格。
2. 型材挤压:将铝合金坯料放入铝合金挤压机的料斗中,通过深度挤压的方式将铝坯料挤压成型。
挤压过程中需要注意控制挤压温度和速度,以保证挤压出的型材具有良好的形状和尺寸。
3. 型材退火:挤压后的型材通常需要进行退火处理,以消除挤压过程中产生的内应力和改善结晶组织。
退火过程中需要根据材料的性质确定合适的温度和时间。
4. 型材切割:在挤压出的型材经过退火处理后,需要进行切割。
切割方法可以有锯切、拉切等不同的方式。
切割时需要注意保持型材的精度和表面质量。
5. 型材表面处理:挤压出的型材通常需要进行表面处理,以提高其耐腐蚀性和装饰性。
常见的表面处理方法包括阳极氧化、电泳涂装、喷涂等。
6. 型材检测:对生产出的型材进行质量检测,包括尺寸检测、表面质量检查等,以保证产品符合相关标准要求。
7. 型材包装:将通过质检合格的型材进行包装,通常采用木箱、
纸箱等适当的包装方式,以防止型材在运输过程中的受损。
以上是铝挤型材的一般生产工艺,具体的工艺参数和工艺流程可能会因产品的特殊要求而有所不同。
铝挤型材作为一种常用的建筑材料,广泛应用于建筑、汽车、航空航天等各个领域。
其生产工艺的合理控制将对产品的质量和性能产生重要影响。
大型铝合金型材的热挤压方法
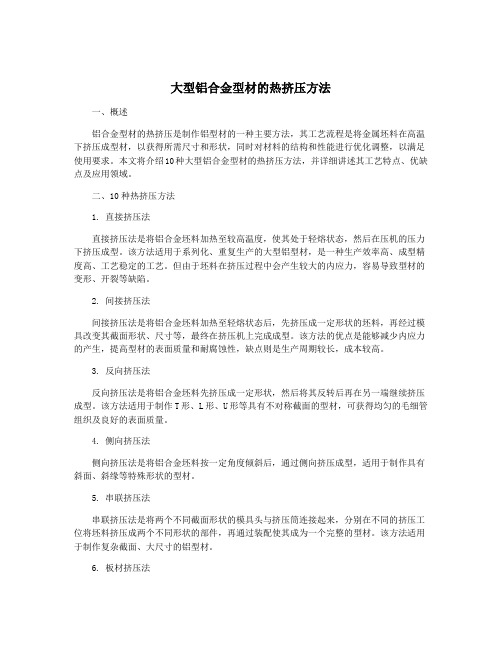
大型铝合金型材的热挤压方法一、概述铝合金型材的热挤压是制作铝型材的一种主要方法,其工艺流程是将金属坯料在高温下挤压成型材,以获得所需尺寸和形状,同时对材料的结构和性能进行优化调整,以满足使用要求。
本文将介绍10种大型铝合金型材的热挤压方法,并详细讲述其工艺特点、优缺点及应用领域。
二、10种热挤压方法1. 直接挤压法直接挤压法是将铝合金坯料加热至较高温度,使其处于轻熔状态,然后在压机的压力下挤压成型。
该方法适用于系列化、重复生产的大型铝型材,是一种生产效率高、成型精度高、工艺稳定的工艺。
但由于坯料在挤压过程中会产生较大的内应力,容易导致型材的变形、开裂等缺陷。
2. 间接挤压法间接挤压法是将铝合金坯料加热至轻熔状态后,先挤压成一定形状的坯料,再经过模具改变其截面形状、尺寸等,最终在挤压机上完成成型。
该方法的优点是能够减少内应力的产生,提高型材的表面质量和耐腐蚀性,缺点则是生产周期较长,成本较高。
3. 反向挤压法反向挤压法是将铝合金坯料先挤压成一定形状,然后将其反转后再在另一端继续挤压成型。
该方法适用于制作T形、L形、U形等具有不对称截面的型材,可获得均匀的毛细管组织及良好的表面质量。
4. 侧向挤压法侧向挤压法是将铝合金坯料按一定角度倾斜后,通过侧向挤压成型,适用于制作具有斜面、斜缘等特殊形状的型材。
5. 串联挤压法串联挤压法是将两个不同截面形状的模具头与挤压筒连接起来,分别在不同的挤压工位将坯料挤压成两个不同形状的部件,再通过装配使其成为一个完整的型材。
该方法适用于制作复杂截面、大尺寸的铝型材。
6. 板材挤压法板材挤压法是将板材加热后,在挤压机中通过辊式挤压成型,该方法适用于制作厚壁型材,具有成型精度高、产品密度均匀、机械性能优良等优点。
7. 双挤压法双挤压法是将两个不同截面形状的模具头安装在同一挤压机内,同时对坯料进行两次挤压成型。
该方法适用于制作较复杂的型材,如圆形、方形、六边形等复杂几何形状的铝型材。
铝合金挤压生产知识及注意要点
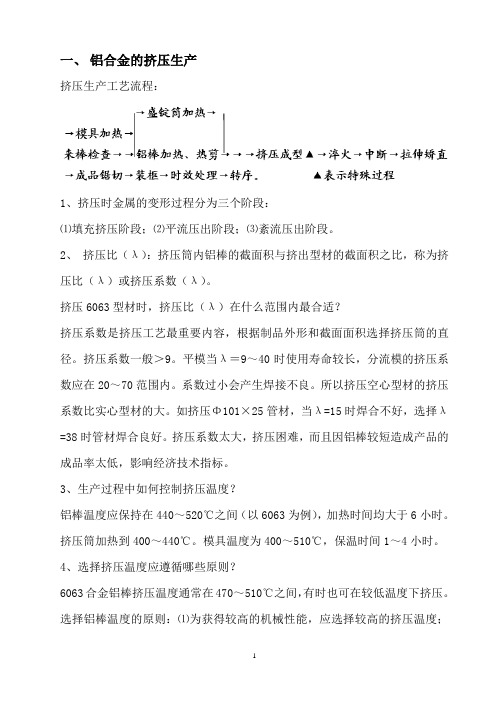
一、铝合金的挤压生产挤压生产工艺流程:1、挤压时金属的变形过程分为三个阶段:⑴填充挤压阶段;⑵平流压出阶段;⑶紊流压出阶段。
2、挤压比(λ):挤压筒内铝棒的截面积与挤出型材的截面积之比,称为挤压比(λ)或挤压系数(λ)。
挤压6063型材时,挤压比(λ)在什么范围内最合适?挤压系数是挤压工艺最重要内容,根据制品外形和截面面积选择挤压筒的直径。
挤压系数一般>9。
平模当λ=9~40时使用寿命较长,分流模的挤压系数应在20~70范围内。
系数过小会产生焊接不良。
所以挤压空心型材的挤压系数比实心型材的大。
如挤压Φ101×25管材,当λ=15时焊合不好,选择λ=38时管材焊合良好。
挤压系数太大,挤压困难,而且因铝棒较短造成产品的成品率太低,影响经济技术指标。
3、生产过程中如何控制挤压温度?铝棒温度应保持在440~520℃之间(以6063为例),加热时间均大于6小时。
挤压筒加热到400~440℃。
模具温度为400~510℃,保温时间1~4小时。
4、选择挤压温度应遵循哪些原则?6063合金铝棒挤压温度通常在470~510℃之间,有时也可在较低温度下挤压。
选择铝棒温度的原则:⑴为获得较高的机械性能,应选择较高的挤压温度;⑵当挤压机能力不足,可通过提高铝棒温度来提高挤压速度;⑶当模具悬臂过大时,可提高铝棒温度,以减小铝棒对模具的压力及摩擦力;⑷挤压温度过高会使产生气泡、撕裂及由于模具工作带粘铝造成表面划痕严重;⑸为了获得高表面质量的产品,宜在较低温度下挤压模具加热及保温控制:5、如何控制挤压速度?挤压速度是影响生产率的一个重要指标。
挤压速度取决于合金种类、几何形状、尺寸和表面状态,同时也与铸锭质量息息相关。
要提高挤压速度,必需合理控制铝棒温度、模具温度、挤压筒温度。
6063铝合金挤压速度范围为:9~80M/min,其中实心型材为:20~80M/min,空心型材的挤压速度一般为实心型材挤压速度的0.5~0.8倍。
铝合金热挤压的基本工艺

铝合金热挤压的基本工艺
铝合金热挤压是一种常见的金属加工工艺,用于生产各种铝合金型材,如铝合金门窗、铝合金管材、铝合金棒材等。
其基本工艺包括以下几个步骤:
1. 原料准备:选择适宜的铝合金材料,并对其进行预处理,如切割、去毛刺等。
2. 加热:将铝合金材料加热至合适的温度,通常为材料的再结晶温度或略高于该温度。
3. 模具准备:准备好挤压模具,根据产品的形状和尺寸要求进行设计和制造。
4. 挤压:将加热后的铝合金材料放入挤压机的料斗中,通过压力将材料挤压进模具中。
在挤压过程中,铝合金材料会发生塑性变形,使得其截面形状和尺寸得到改变。
5. 切割:将挤压出的铝合金型材按照需要的长度进行切割。
6. 退火处理:对挤压出的铝合金型材进行退火处理,以消除残余应力和改善材料的机械性能。
7. 表面处理:对铝合金型材进行表面处理,如阳极氧化、喷涂、喷砂等,以提高其耐腐蚀性和美观度。
通过以上基本工艺步骤,可以生产出各种形状和尺寸的铝合金型材,满足不同行业的需求。
铝合金挤压生产知识及注意要点
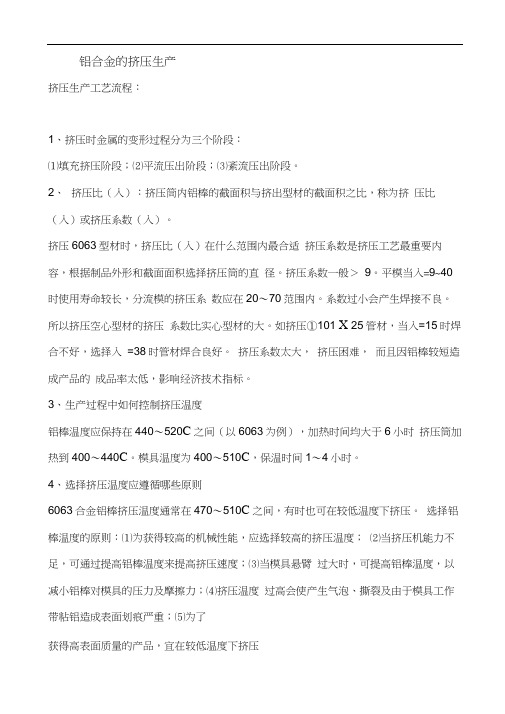
铝合金的挤压生产挤压生产工艺流程:1、挤压时金属的变形过程分为三个阶段:⑴填充挤压阶段;⑵平流压出阶段;⑶紊流压出阶段。
2、挤压比(入):挤压筒内铝棒的截面积与挤出型材的截面积之比,称为挤压比(入)或挤压系数(入)。
挤压6063型材时,挤压比(入)在什么范围内最合适挤压系数是挤压工艺最重要内容,根据制品外形和截面面积选择挤压筒的直径。
挤压系数一般>9。
平模当入=9~40时使用寿命较长,分流模的挤压系数应在20〜70范围内。
系数过小会产生焊接不良。
所以挤压空心型材的挤压系数比实心型材的大。
如挤压①101 X 25管材,当入=15时焊合不好,选择入=38时管材焊合良好。
挤压系数太大,挤压困难,而且因铝棒较短造成产品的成品率太低,影响经济技术指标。
3、生产过程中如何控制挤压温度铝棒温度应保持在440〜520C之间(以6063为例),加热时间均大于6小时挤压筒加热到400〜440C。
模具温度为400〜510C,保温时间1〜4小时。
4、选择挤压温度应遵循哪些原则6063合金铝棒挤压温度通常在470〜510C之间,有时也可在较低温度下挤压。
选择铝棒温度的原则:⑴为获得较高的机械性能,应选择较高的挤压温度;⑵当挤压机能力不足,可通过提高铝棒温度来提高挤压速度;⑶当模具悬臂过大时,可提高铝棒温度,以减小铝棒对模具的压力及摩擦力;⑷挤压温度过高会使产生气泡、撕裂及由于模具工作带粘铝造成表面划痕严重;⑸为了获得高表面质量的产品,宜在较低温度下挤压模具加热及保温控制:5、如何控制挤压速度挤压速度是影响生产率的一个重要指标。
挤压速度取决于合金种类、几何形状、尺寸和表面状态,同时也与铸锭质量息息相关。
要提高挤压速度,必需合理控制铝棒温度、模具温度、挤压筒温度。
6063铝合金挤压速度范围为:9〜80M/mi n,其中实心型材为:20〜80M/mi n,空心型材的挤压速度一般为实心型材挤压速度的0.5〜0.8 倍。
6、均匀化:通常将6063铝棒在560C保温6〜8小时,使合金的Mg2si相以细小质点均匀分布在整个金属基体中,且消除铸造应力,铸锭出炉后以较高速度冷却(水冷或风冷) ,这种热处理工艺称作均匀化。
铝合金型材挤压模具及挤压生产流程详解

铝合金型材挤压模具及挤压生产流程详解铝合金型材挤压模具是一种用于加工铝合金型材的工具。
铝合金型材挤压生产流程如下:1. 材料准备:首先需要准备好适用于挤压的铝合金材料。
通常情况下,采用的是具有良好延展性和可塑性的铝合金材料。
2. 模具设计:根据产品的形状和尺寸要求,设计合适的挤压模具。
模具的设计需要考虑产品的形状、尺寸、角度和曲率等因素。
3. 模具制造:根据设计好的模具图纸,制造出挤压模具。
通常情况下,模具由高强度的工具钢制成,以确保其耐磨性和寿命。
4. 模具安装:将制造好的挤压模具安装在挤压机上。
挤压机是用于将铝合金材料加热并迫使其通过模具的设备。
5. 加热材料:将铝合金材料加热至所需的挤压温度。
挤压温度可以根据铝合金的特性和产品的要求进行调整。
6. 挤压加工:将加热好的铝合金材料送入挤压机中,通过压力迫使其通过模具。
在挤压过程中,铝合金材料会受到模具的限制,被迫形成与模具相同的形状。
7. 冷却处理:经过挤压后,铝合金型材会以较高的温度存在。
为了增加其强度和硬度,需要对其进行冷却处理。
冷却处理可以通过水冷或空气冷却进行。
8. 切割和加工:经过冷却处理后的铝合金型材需要进行切割和加工。
通常会使用锯床或切割机对其进行切割,并使用机械加工设备对其进行进一步的加工和修整。
9. 表面处理:为了提高铝合金型材的耐腐蚀性和表面光洁度,通常会对其进行表面处理,如阳极氧化、粉末涂装等。
10. 检验和包装:最后,对挤压生产出来的铝合金型材进行检验,确保其质量符合要求。
合格的铝合金型材会进行包装和标识,待发货或存储。
以上是铝合金型材挤压模具及挤压生产流程的详细解释。
各种铝合金型材挤压工艺知识
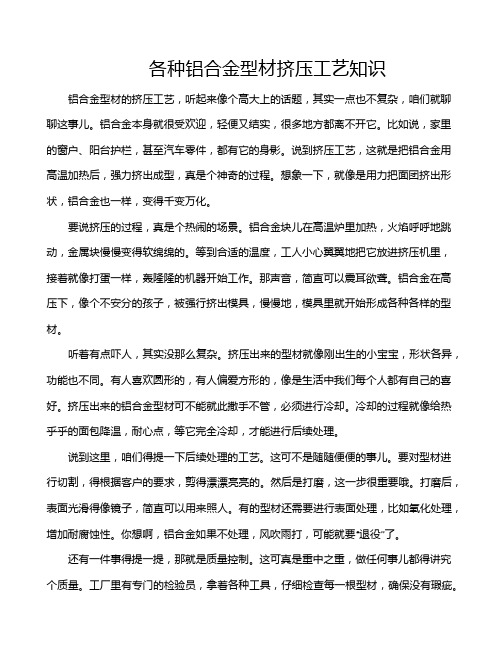
各种铝合金型材挤压工艺知识铝合金型材的挤压工艺,听起来像个高大上的话题,其实一点也不复杂,咱们就聊聊这事儿。
铝合金本身就很受欢迎,轻便又结实,很多地方都离不开它。
比如说,家里的窗户、阳台护栏,甚至汽车零件,都有它的身影。
说到挤压工艺,这就是把铝合金用高温加热后,强力挤出成型,真是个神奇的过程。
想象一下,就像是用力把面团挤出形状,铝合金也一样,变得千变万化。
要说挤压的过程,真是个热闹的场景。
铝合金块儿在高温炉里加热,火焰呼呼地跳动,金属块慢慢变得软绵绵的。
等到合适的温度,工人小心翼翼地把它放进挤压机里,接着就像打蛋一样,轰隆隆的机器开始工作。
那声音,简直可以震耳欲聋。
铝合金在高压下,像个不安分的孩子,被强行挤出模具,慢慢地,模具里就开始形成各种各样的型材。
听着有点吓人,其实没那么复杂。
挤压出来的型材就像刚出生的小宝宝,形状各异,功能也不同。
有人喜欢圆形的,有人偏爱方形的,像是生活中我们每个人都有自己的喜好。
挤压出来的铝合金型材可不能就此撒手不管,必须进行冷却。
冷却的过程就像给热乎乎的面包降温,耐心点,等它完全冷却,才能进行后续处理。
说到这里,咱们得提一下后续处理的工艺。
这可不是随随便便的事儿。
要对型材进行切割,得根据客户的要求,剪得漂漂亮亮的。
然后是打磨,这一步很重要哦。
打磨后,表面光滑得像镜子,简直可以用来照人。
有的型材还需要进行表面处理,比如氧化处理,增加耐腐蚀性。
你想啊,铝合金如果不处理,风吹雨打,可能就要“退役”了。
还有一件事得提一提,那就是质量控制。
这可真是重中之重,做任何事儿都得讲究个质量。
工厂里有专门的检验员,拿着各种工具,仔细检查每一根型材,确保没有瑕疵。
就像妈妈检查孩子的作业一样,严格又细致。
大家都知道,铝合金型材的质量直接影响到后面的使用,出门在外可不能马虎。
说到铝合金型材的应用,简直是无处不在。
建筑、交通、电子、机械……哪个行业不需要铝合金的身影?每当看到这些型材被运用到各种地方,心里总有种成就感,毕竟这背后是无数工人努力的成果。
铝合金及型材的生产原理-挤压

挤压挤压:就是对放在容器(挤压筒)中的锭坯一端施加压力,使之通过模孔以实现成形的一种压力加工方法。
挤压机的主要部件及辅助机构:模座、供锭机构、挤压垫与压余分离及传送机构、坯锭热切断和热剥皮装置、制品牵引机构。
挤压机的技术特征:挤压力、穿孔力、挤压杆的行程与速度、挤压筒的尺寸等。
挤压机的额定能力(最大挤压力)等于工作缸的总面积与工作液体的额定比压的乘积。
在铝及铝合金半成品中,挤压是主要的成型工艺之一,挤压产品占全部半成品的1/3,尤其是生产建筑型材。
挤压方法的基本特点是:(1)具有有利于金属塑性变形的应力状态,即强烈的三向压缩应力状态。
(2)变形金属与工具间存在着较大的外摩擦力,使变形很不均匀。
(3)对生产许多高合金化的铝合金,可获得挤压效应。
(挤压效应是指某些铝合金挤压制品与其它加工制品如轧制、拉伸和锻造等经相同的热处理后,前者的强度比后者高,而塑性比后者低。
这一效应是挤压制品所特有的特征。
)挤压的三个阶段:1.填充挤压阶段———充填、挤压上升。
2.平流挤压阶段———金属流动平稳而不交错,挤压力随锭坯长度的减少而直线下降。
3.紊流挤压阶段———锭坯外层金属及两个难变形区(靠近挤压垫及模子角落处的金属也向模孔流动,形成“挤压缩尾”。
挤压力又开始上升,此时应结束挤压操作。
)一、铝合金挤压成形的几个主要变形参数计算1.挤压系数λ(挤压比):金属变形量的大小λ=F筒/F制F筒、F制——分别为挤压筒和挤压制品的断面积。
2.填充系数在生产中,把挤压筒断面积F筒与铸锭断面积之比K叫做填充系数或墩粗系数,即K= F筒/F锭一般取K=1.02-1.12要考虑铝棒加热的膨胀性,例:20度铝棒加热到520度,其直径是原来的1.0125倍,即直径增大1.25%。
挤压管材时,K值过大,可能增加制品低倍组织和表面上的缺陷,铸锭的对中性差,影响管材的内表面质量和增大管材的壁厚差。
挤压大截面型材时,K值可增至1.5-1.6,有利于提高制品的力学性能,特别是横向性能。
铝合金挤压成型

铝合金挤压成型铝合金挤压成型是一种常见的金属加工方法,它利用挤压机将铝合金坯料在模具中施加高压力,使其通过模孔挤出并形成所需的截面形状。
该方法具有高效、精度高、成本低等优点,被广泛应用于汽车、航空航天、建筑等领域。
一、铝合金挤压成型的原理和过程1.原理铝合金挤压成型是利用挤压机将铝合金坯料在模具中施加高压力,使其通过模孔挤出并形成所需的截面形状。
在此过程中,铝合金坯料受到了强大的剪切力和变形力,其晶粒结构得到了细化和改善。
2.过程(1)选择材料:首先需要根据需要制作的零件要求选择适当的铝合金材料。
(2)设计模具:根据零件要求设计出适当的模具,并进行加工。
(3)准备坯料:将选定的铝合金材料切割成长度与模具相同的坯料条。
(4)预热坯料:将坯料条放入预热炉中进行加热,使其达到挤压温度。
(5)挤压成型:将预热好的坯料条放入挤压机中,在模具的作用下施加高压力,使其通过模孔挤出并形成所需的截面形状。
(6)后处理:将挤出的零件进行切割、冷却、退火等后处理工序,以达到所需的物理性能和表面质量要求。
二、铝合金挤压成型的特点1.高效铝合金挤压成型是一种高效率的生产工艺,可以在较短时间内完成大批量生产。
2.精度高由于铝合金挤压成型过程中施加了高压力,并且采用了先进的数控技术和模具设计,因此可以获得极高的精度和尺寸稳定性。
3.成本低相对于其他加工方法,铝合金挤压成型具有较低的生产成本。
这主要得益于其高效率和自动化程度。
4.适用范围广铝合金挤压成型可以制造各种形状和尺寸的零件,适用于汽车、航空航天、建筑等多个领域。
三、铝合金挤压成型的应用1.汽车行业铝合金挤压成型在汽车行业中得到广泛应用,可以制造车身结构件、发动机部件、悬挂系统等。
2.航空航天行业铝合金挤压成型在航空航天行业中也有重要的应用,可以制造飞机外壳、燃油箱、起落架等。
3.建筑行业铝合金挤压成型还可以制造建筑门窗、幕墙、阳台等零部件,具有轻质化、美观大方的特点。
铝合金挤压过程理论知识已修改

挤压过程的基本理论知识目录1挤压挤压加工挤压就是对放在挤压筒中的铝锭施加以压力,使之通过模孔成型的一种压力加工方法。
最基本的挤压方法有正向挤压与反向挤压,它们的区别在于金属流动的方向与挤压杆的运动方向是否相同,是则为正向挤压,反则为反向挤压。
特点区别在于金属与挤压筒内壁间有无相对运动,或者说有无外摩擦。
除此之外,工业上常用的挤压方法还有:测向挤压、玻璃润滑挤压、静液挤压、连续挤压。
挤压过程可分为三个阶段:首先是填充阶段,在此阶段铝棒受到挤压杆的作用,首先充满挤压筒和模孔,此时压力急剧上升到100Kg/mm 2左右,即从进料到脱气结束。
其次是挤压平流阶段,挤压筒充满铝后,挤压力迅速上升到210Kg/mm2左右,开始出料。
此阶段压力随着铝棒与挤压筒接触长度的缩短,外摩擦力不断减小,挤压力几乎呈直线下降。
再次是挤压终了阶段,即挤:正、反向挤压时典型的挤压力与行程曲线⑷生产灵活性大。
⑸工艺流程简单、设备投资少。
挤压加工的缺点:⑴制品组织性能不均匀。
⑵挤压工模具的工作条件恶劣、工模具损耗大。
⑶生产效率较低。
以下内容将描述挤压加工的原理,在这里面,将简要说明各种加工的不同点和相同点。
在原理上,挤压加工可以分为冷挤压和热挤压两类。
冷挤压意味着挤压的棒在被放入挤压机之前没有预热。
热挤压,更经常被称为“挤压”(因为它是通常的规则),意味着棒在被放入盛锭筒之前需要预热。
冷挤压:棒被装载前没有预热,也就是说,在室温下。
热挤压:棒被预热,也就是说,在高于室温的温度下装载。
图:没有润滑剂和外壳的直接挤压原理这种方法是迄今为止工业上最常见的,一般当一个人说到“挤压”的时候,说的就是直接挤压。
在这样的加工中,棒首先在盛锭筒中镦粗(镦粗=压缩而不弯曲,使其变得短些,粗些)并装满盛锭筒的内部。
然后,被挤压杆挤出穿过模具。
在这个过程中,在棒和盛锭筒之间发生了相对运动。
因此,棒在盛锭筒中的移动必须克服它们之间的摩擦。
直接挤压的典型特征是棒和盛锭筒之间存在摩擦。
铝合金挤压的最新技术和装备
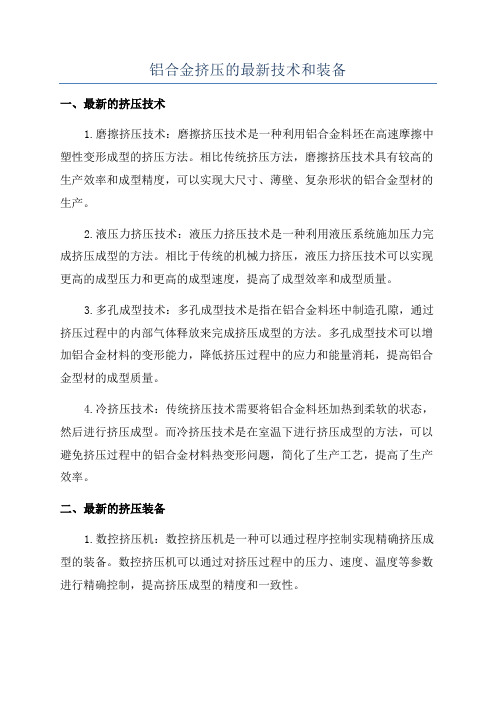
铝合金挤压的最新技术和装备一、最新的挤压技术1.磨擦挤压技术:磨擦挤压技术是一种利用铝合金料坯在高速摩擦中塑性变形成型的挤压方法。
相比传统挤压方法,磨擦挤压技术具有较高的生产效率和成型精度,可以实现大尺寸、薄壁、复杂形状的铝合金型材的生产。
2.液压力挤压技术:液压力挤压技术是一种利用液压系统施加压力完成挤压成型的方法。
相比于传统的机械力挤压,液压力挤压技术可以实现更高的成型压力和更高的成型速度,提高了成型效率和成型质量。
3.多孔成型技术:多孔成型技术是指在铝合金料坯中制造孔隙,通过挤压过程中的内部气体释放来完成挤压成型的方法。
多孔成型技术可以增加铝合金材料的变形能力,降低挤压过程中的应力和能量消耗,提高铝合金型材的成型质量。
4.冷挤压技术:传统挤压技术需要将铝合金料坯加热到柔软的状态,然后进行挤压成型。
而冷挤压技术是在室温下进行挤压成型的方法,可以避免挤压过程中的铝合金材料热变形问题,简化了生产工艺,提高了生产效率。
二、最新的挤压装备1.数控挤压机:数控挤压机是一种可以通过程序控制实现精确挤压成型的装备。
数控挤压机可以通过对挤压过程中的压力、速度、温度等参数进行精确控制,提高挤压成型的精度和一致性。
2.智能挤压模具:智能挤压模具是一种根据工件形状和挤压过程中的力学特性进行优化设计的模具。
智能挤压模具可以通过模具内部的传感器和控制系统实时监测和调整挤压过程中的压力分布,实现均匀的变形和优化的材料利用。
3.真空挤压装备:真空挤压装备是一种在挤压过程中对料坯进行真空处理的装备。
真空挤压可以有效地防止氧化反应和气孔形成,提高挤压成型的表面质量和力学性能。
4.挤压成型模拟仿真装备:挤压成型模拟仿真装备可以通过计算机模拟和分析挤压过程中的力学和热学特性,预测成型过程中的变形情况和应力分布,优化挤压工艺和模具设计,提高挤压成型的效率和质量。
总之,铝合金挤压技术的不断创新和发展,使得铝合金型材的生产更加高效、精确和可靠。
铝合金挤压成型工艺

铝合金挤压成型工艺铝合金挤压成型工艺是一种常用的金属成型工艺,广泛应用于航空航天、汽车制造、建筑等领域。
本文将从工艺原理、设备和应用等方面进行介绍。
一、工艺原理铝合金挤压成型是指将加热至柔软状态的铝合金坯料放入挤压机的料斗中,通过挤压机的压力和模具的作用,使铝合金坯料在一定的温度和变形条件下,通过模具的缝隙挤压成型,从而得到所需形状的铝合金材料。
铝合金挤压成型的工艺原理主要包括以下几个方面:1. 坯料预热:铝合金坯料通过加热炉进行预热,使其达到适宜的挤压温度,提高材料的塑性和变形能力。
2. 挤压过程:将预热后的铝合金坯料放入挤压机的料斗中,通过挤压机的运动和模具的作用,使材料在一定的温度和变形条件下,通过模具的缝隙挤压成型。
3. 冷却处理:挤压成型后的铝合金材料需要进行冷却处理,以使其达到所需的力学性能和物理性能。
二、设备铝合金挤压成型的设备主要包括挤压机、加热炉和模具等。
挤压机是铝合金挤压成型的核心设备,其主要由机架、油缸、传动机构和控制系统等组成。
加热炉用于对铝合金坯料进行预热处理,以提高材料的塑性和变形能力。
模具是铝合金挤压成型的重要工具,其形状和结构决定了最终产品的形状和尺寸。
三、应用铝合金挤压成型工艺在各个领域都有广泛的应用,主要体现在以下几个方面:1. 航空航天领域:铝合金挤压成型可以制造轻量化的航空航天结构件,如飞机翼梁、机身外壳等。
铝合金材料具有高强度、高刚度和良好的耐腐蚀性能,适合用于航空航天领域的要求。
2. 汽车制造领域:铝合金挤压成型可以制造汽车车身结构件,如车门、车顶等。
铝合金材料具有优良的耐腐蚀性能和轻质化特点,可以减轻汽车重量,提高燃油效率。
3. 建筑领域:铝合金挤压成型可以制造建筑结构件,如窗框、门框等。
铝合金材料具有良好的耐候性和装饰性能,可以满足建筑领域对于外观和环境要求。
4. 电子电器领域:铝合金挤压成型可以制造电子电器外壳,如手机壳、笔记本电脑外壳等。
铝合金材料具有良好的导热性能和抗电磁干扰能力,可以保护电子元器件的安全运行。
铝合金挤压生产知识

一、铝合金的挤压生产1.挤压时金属的变形过程分为几个阶段?分为:⑴填充挤压阶段;⑵平流压由阶段;⑶紊流压由阶段。
2、什么是挤压比(入)?挤压6063型材时,挤压比(入)在什么范围内最合适?挤压筒内铝棒的截面积与挤由型材的截面积之比,称为挤压比(入)或挤压系数(入)。
挤压系数是挤压工艺最重要的内容,根据制品外形和截面面积选择挤压筒的直径。
挤压系数一般〉9。
平模当入=9〜40时使用寿命较长,分流模的挤压系数应在20〜70范围内。
系数过小会产生焊接不良。
所以挤压空心型材的挤压系数比实心型材的大。
如挤压①101X25管材,当入=15时焊合不好,选择入=38时管材焊合良好。
挤压系数太大,挤压困难,而且因铝棒较短造成产品的成品率太低,影响经济技术指标。
3.生产过程中如何控制挤压温度?铝棒温度应保持在440〜520c之间(以6063为例),加热时间均在6小时以上。
挤压筒加热到400〜440C。
模具温度为400〜510C,保温时间1〜4小时。
4、选择挤压温度应遵循哪些原则?6063合金铝棒的挤压温度通常在470〜510之间,有时也可在较低温度下挤压。
选择铝棒温度的原则:⑴为获得较高的机械性能,应选择较高的挤压温度;⑵当挤压机能力不足,可通过提高铝棒温度来提高挤压速度;⑶当模具悬臂过大时,可提高铝棒温度,以减小铝棒对模具的压力及摩擦力;⑷挤压温度过高会使产生气泡、撕裂及由于模具工作带粘铝造成表面划痕严重;⑸为了获得高表面质量的产品,宜在较低温度下挤压5、如何控制挤压速度?挤压速度是影响生产率的一个重要指标。
挤压速度取决于合金种类、几何形状、尺寸和表面状态,同时也与铸锭质量息息相关。
要提高挤压速度,必需合理控制铝棒温度、模具温度、挤压筒温度。
6063铝合金挤压速度范围为:9〜80M/min,其中实心型材为:20〜80M/min,空心型材的挤压速度一般为实心型材挤压速度的0.5〜0.8倍。
6、什么是均匀化?通常将6063铝棒在560c保温6〜8小时,使合金的Mg2si相以细小质点均匀分布在整个金属基体中,且消除铸造应力,铸锭由炉后以较高速度冷却(水冷或风冷),这种热处理工艺称作均匀化。
一般工业用铝及铝合金挤压型材

一般工业用铝及铝合金挤压型材一、引言二、铝及铝合金的挤压加工技术三、一般工业用铝及铝合金挤压型材的特点四、一般工业用铝及铝合金挤压型材的应用五、未来一般工业用铝及铝合金挤压型材的发展趋势六、结论一、引言随着工业化的发展,铝及铝合金被广泛应用于不同领域,成为工业生产的重要材料之一、铝及铝合金挤压型材作为铝及铝合金的一种常见形式,在工业生产中具有重要的地位。
本文将对一般工业用铝及铝合金挤压型材进行详细的介绍,包括挤压加工技术、特点、应用及未来发展趋势等方面。
二、铝及铝合金的挤压加工技术挤压是一种常用的金属加工方法,通过将金属材料加热至适当温度后,通过挤压机将其挤出成型。
对于铝及铝合金来说,挤压加工技术具有以下特点:1.铝及铝合金具有较好的可挤压性,容易进行挤压加工。
2.挤压加工过程中,铝及铝合金的晶粒细化,提高了材料的强度和塑性。
3.挤压加工可以实现多种复杂截面形状的制造,满足不同领域的需求。
4.挤压加工是一种高效、节能的加工方式,能够提高材料的利用率。
三、一般工业用铝及铝合金挤压型材的特点1.良好的力学性能:铝及铝合金挤压型材具有较高的强度和较好的塑性,能够承受一定的负荷。
2.良好的耐腐蚀性:铝及铝合金挤压型材具有良好的耐腐蚀性能,适用于各种环境条件下的使用。
3. 轻质化:铝及铝合金挤压型材具有轻质化的特点,比重约为2.7g/cm³,是钢材的1/34.易加工:铝及铝合金挤压型材容易进行切割、打孔、焊接等加工,便于使用和安装。
四、一般工业用铝及铝合金挤压型材的应用1.建筑领域:铝及铝合金挤压型材常用于建筑门窗、幕墙、装饰材料等的制造,具有轻质、坚固、美观的特点。
2.交通领域:铝及铝合金挤压型材常用于汽车、火车、飞机等交通工具的制造,具有减轻重量、提高燃油效率的优势。
3.电子领域:铝及铝合金挤压型材常用于电子设备的外壳、散热器等零部件的制造,具有散热性能好、导电性好的特点。
4.机械领域:铝及铝合金挤压型材常用于机械设备的结构支架、传动零部件等的制造,具有高强度、抗疲劳的特点。
挤压成型技术

4)挤压速度的影响。
5)摩擦条件的影响 挤压筒内表面的状态、润滑条件影响锭坯 与筒壁间的摩擦状况,从而会影响挤压力 大小。 6)挤压筒温度的影响 挤压筒预热适当们可以降低锭坯的冷却速 率,减小挤压力。 7)挤压温度的影响 金属在挤压时必须考虑适宜的挤压温度。
6.挤压时金属的流动
I为定径区 II为变形区 III区位未变形区 IV为死区
主要内容
• 挤压成型基础知识
• 铝型材挤压
1定义 挤压成型(Press Forming)是对放在模具模腔 (或挤压筒)内的的金属坯料施加强大的压力, 迫使金属坯料产生定向塑性变形,从挤压模的模 孔中挤出而获得所需断面形状、尺寸并具有一定 力学性能的零件或半成品的塑性加工方法。
金属挤压示意图
2.挤压分类方法 2.1按金属塑变流动方向可以分为:
正挤压:挤压时,金属流动方向与凸模运动方向相同 反挤压:挤压时,金属流动方向与凸模运动方向相反 复合挤压:挤压时,坯料一部分金属流动方向与凸模运动方向相同, 另一部分则相反 径向挤压:挤压时,金属流动方向与凸模运动方向成90°
2.2按金属坯料的温度分类:
•
•
5.影响挤压力大小的因素
1)变形抗力(金属的屈服限)越大,所需挤压力
越高,高温时,变形抗力降低,挤压力随之降低。
2)加工率的影响。加工率越大,所需挤压力 越大。
3)锭坯长度的影响
长度越长,挤压过程越长,挤压终了时温度变化大,变形抗 力变大。正挤压时,要克服锭坯与挤压筒壁的摩擦力,故 挤压力增加,反挤压时,挤压力与锭坯长无关。
模具材料
表面处理及 零件质量影 润滑 响因素
1.设备的刚性 2.温度升高 3.模具弹性变形 1.温度 2.润滑 3.模具弹性变形
铝合金挤压成型工艺研究
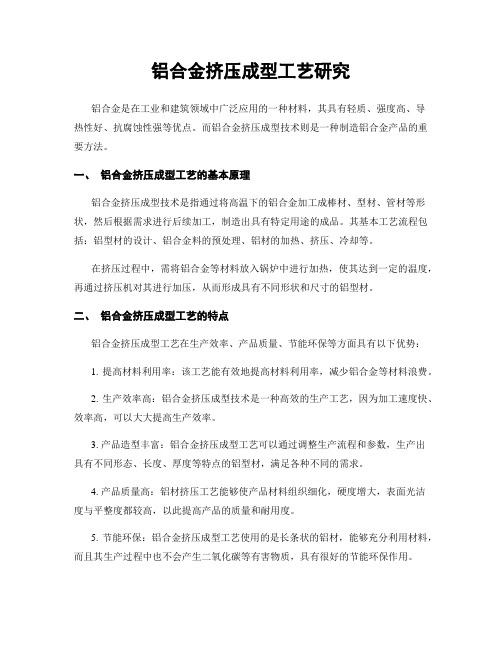
铝合金挤压成型工艺研究铝合金是在工业和建筑领域中广泛应用的一种材料,其具有轻质、强度高、导热性好、抗腐蚀性强等优点。
而铝合金挤压成型技术则是一种制造铝合金产品的重要方法。
一、铝合金挤压成型工艺的基本原理铝合金挤压成型技术是指通过将高温下的铝合金加工成棒材、型材、管材等形状,然后根据需求进行后续加工,制造出具有特定用途的成品。
其基本工艺流程包括:铝型材的设计、铝合金料的预处理、铝材的加热、挤压、冷却等。
在挤压过程中,需将铝合金等材料放入锅炉中进行加热,使其达到一定的温度,再通过挤压机对其进行加压,从而形成具有不同形状和尺寸的铝型材。
二、铝合金挤压成型工艺的特点铝合金挤压成型工艺在生产效率、产品质量、节能环保等方面具有以下优势:1. 提高材料利用率:该工艺能有效地提高材料利用率,减少铝合金等材料浪费。
2. 生产效率高:铝合金挤压成型技术是一种高效的生产工艺,因为加工速度快、效率高,可以大大提高生产效率。
3. 产品造型丰富:铝合金挤压成型工艺可以通过调整生产流程和参数,生产出具有不同形态、长度、厚度等特点的铝型材,满足各种不同的需求。
4. 产品质量高:铝材挤压工艺能够使产品材料组织细化,硬度增大,表面光洁度与平整度都较高,以此提高产品的质量和耐用度。
5. 节能环保:铝合金挤压成型工艺使用的是长条状的铝材,能够充分利用材料,而且其生产过程中也不会产生二氧化碳等有害物质,具有很好的节能环保作用。
三、铝合金挤压成型工艺的应用领域铝合金挤压成型技术被广泛应用在机械、汽车、建筑、船舶、轨道交通等领域。
包括机械制造、电子电器、建筑装饰、广告、家居、通讯、铁路运输等各个方向。
这些领域常用的铝合金挤压产品有:铝合金门窗、铝合金线管、铝合金太阳能板材、铝合金压铸件等等。
结束语:总之,铝合金挤压成型工艺是一种高效、节能、环保的铝材加工方法,其应用范围广泛,性能优越。
因此,学习研究铝合金挤压成型技术,对于提高制品质量、降低制造成本等方面都具有非常重要的意义。
铝合金挤压生产知识及注意要点分析

一、铝合金的挤压生产挤压生产工艺流程:1、挤压时金属的变形过程分为三个阶段:⑴填充挤压阶段;⑵平流压出阶段;⑶紊流压出阶段。
2、挤压比(λ):挤压筒内铝棒的截面积与挤出型材的截面积之比,称为挤压比(λ)或挤压系数(λ)。
挤压6063型材时,挤压比(λ)在什么范围内最合适?挤压系数是挤压工艺最重要内容,根据制品外形和截面面积选择挤压筒的直径。
挤压系数一般>9。
平模当λ=9~40时使用寿命较长,分流模的挤压系数应在20~70范围内。
系数过小会产生焊接不良。
所以挤压空心型材的挤压系数比实心型材的大。
如挤压Φ101×25管材,当λ=15时焊合不好,选择λ=38时管材焊合良好。
挤压系数太大,挤压困难,而且因铝棒较短造成产品的成品率太低,影响经济技术指标。
3、生产过程中如何控制挤压温度?铝棒温度应保持在440~520℃之间(以6063为例),加热时间均大于6小时。
挤压筒加热到400~440℃。
模具温度为400~510℃,保温时间1~4小时。
4、选择挤压温度应遵循哪些原则?6063合金铝棒挤压温度通常在470~510℃之间,有时也可在较低温度下挤压。
选择铝棒温度的原则:⑴为获得较高的机械性能,应选择较高的挤压温度;⑵当挤压机能力不足,可通过提高铝棒温度来提高挤压速度;⑶当模具悬臂过大时,可提高铝棒温度,以减小铝棒对模具的压力及摩擦力;⑷挤压温度过高会使产生气泡、撕裂及由于模具工作带粘铝造成表面划痕严重;⑸为了获得高表面质量的产品,宜在较低温度下挤压模具加热及保温控制:5、如何控制挤压速度?挤压速度是影响生产率的一个重要指标。
挤压速度取决于合金种类、几何形状、尺寸和表面状态,同时也与铸锭质量息息相关。
要提高挤压速度,必需合理控制铝棒温度、模具温度、挤压筒温度。
6063铝合金挤压速度范围为:9~80M/min,其中实心型材为:20~80M/min,空心型材的挤压速度一般为实心型材挤压速度的0.5~0.8倍。
铝合金挤压过程理论知识已修改

挤压过程的基本理论知识目录1挤压挤压加工挤压就是对放在挤压筒中的铝锭施加以压力,使之通过模孔成型的一种压力加工方法。
最基本的挤压方法有正向挤压与反向挤压,它们的区别在于金属流动的方向与挤压杆的运动方向是否相同,是则为正向挤压,反则为反向挤压。
特点区别在于金属与挤压筒内壁间有无相对运动,或者说有无外摩擦。
除此之外,工业上常用的挤压方法还有:测向挤压、玻璃润滑挤压、静液挤压、连续挤压。
挤压过程可分为三个阶段:首先是填充阶段,在此阶段铝棒受到挤压杆的作用,首先充满挤压筒和模孔,此时压力急剧上升到100Kg/mm 2左右,即从进料到脱气结束。
其次是挤压平流阶段,挤压筒充满铝后,挤压力迅速上升到210Kg/mm2左右,开始出料。
此阶段压力随着铝棒与挤压筒接触长度的缩短,外摩擦力不断减小,挤压力几乎呈直线下降。
再次是挤压终了阶段,即挤:正、反向挤压时典型的挤压力与行程曲线⑷生产灵活性大。
⑸工艺流程简单、设备投资少。
挤压加工的缺点:⑴制品组织性能不均匀。
⑵挤压工模具的工作条件恶劣、工模具损耗大。
⑶生产效率较低。
以下内容将描述挤压加工的原理,在这里面,将简要说明各种加工的不同点和相同点。
在原理上,挤压加工可以分为冷挤压和热挤压两类。
冷挤压意味着挤压的棒在被放入挤压机之前没有预热。
热挤压,更经常被称为“挤压”(因为它是通常的规则),意味着棒在被放入盛锭筒之前需要预热。
冷挤压:棒被装载前没有预热,也就是说,在室温下。
热挤压:棒被预热,也就是说,在高于室温的温度下装载。
图:没有润滑剂和外壳的直接挤压原理这种方法是迄今为止工业上最常见的,一般当一个人说到“挤压”的时候,说的就是直接挤压。
在这样的加工中,棒首先在盛锭筒中镦粗(镦粗=压缩而不弯曲,使其变得短些,粗些)并装满盛锭筒的内部。
然后,被挤压杆挤出穿过模具。
在这个过程中,在棒和盛锭筒之间发生了相对运动。
因此,棒在盛锭筒中的移动必须克服它们之间的摩擦。
直接挤压的典型特征是棒和盛锭筒之间存在摩擦。
- 1、下载文档前请自行甄别文档内容的完整性,平台不提供额外的编辑、内容补充、找答案等附加服务。
- 2、"仅部分预览"的文档,不可在线预览部分如存在完整性等问题,可反馈申请退款(可完整预览的文档不适用该条件!)。
- 3、如文档侵犯您的权益,请联系客服反馈,我们会尽快为您处理(人工客服工作时间:9:00-18:30)。
一、铝合金的挤压生产1.挤压时金属的变形过程分为几个阶段?分为:⑴填充挤压阶段;⑵平流压出阶段;⑶紊流压出阶段。
2、什么是挤压比(λ)?挤压6063型材时,挤压比(λ)在什么范围内最合适?挤压筒内铝棒的截面积与挤出型材的截面积之比,称为挤压比(λ)或挤压系数(λ)。
挤压系数是挤压工艺最重要的内容,根据制品外形和截面面积选择挤压筒的直径。
挤压系数一般>9。
平模当λ=9~40时使用寿命较长,分流模的挤压系数应在20~70范围内。
系数过小会产生焊接不良。
所以挤压空心型材的挤压系数比实心型材的大。
如挤压Φ101×25管材,当λ=15时焊合不好,选择λ=38时管材焊合良好。
挤压系数太大,挤压困难,而且因铝棒较短造成产品的成品率太低,影响经济技术指标。
3.生产过程中如何控制挤压温度?铝棒温度应保持在440~520℃之间(以6063为例),加热时间均在6小时以上。
挤压筒加热到400~440℃。
模具温度为400~510℃,保温时间1~4小时。
4、选择挤压温度应遵循哪些原则?6063合金铝棒的挤压温度通常在470~510之间,有时也可在较低温度下挤压。
选择铝棒温度的原则:⑴为获得较高的机械性能,应选择较高的挤压温度;⑵当挤压机能力不足,可通过提高铝棒温度来提高挤压速度;⑶当模具悬臂过大时,可提高铝棒温度,以减小铝棒对模具的压力及摩擦力;⑷挤压温度过高会使产生气泡、撕裂及由于模具工作带粘铝造成表面划痕严重;⑸为了获得高表面质量的产品,宜在较低温度下挤压5、如何控制挤压速度?挤压速度是影响生产率的一个重要指标。
挤压速度取决于合金种类、几何形状、尺寸和表面状态,同时也与铸锭质量息息相关。
要提高挤压速度,必需合理控制铝棒温度、模具温度、挤压筒温度。
6063铝合金挤压速度范围为:9~80M/min,其中实心型材为:20~80M/min,空心型材的挤压速度一般为实心型材挤压速度的0.5~0.8倍。
6、什么是均匀化?通常将6063铝棒在560℃保温6~8小时,使合金的Mg2si相以细小质点均匀分布在整个金属基体中,且消除铸造应力,铸锭出炉后以较高速度冷却(水冷或风冷),这种热处理工艺称作均匀化。
7、在挤压生产中,均匀化有什么作用?⑴能提高型材的机械性能;⑵降低挤压力约10~15%;⑶大大提高挤压速度;⑷降低合金的挤压摩擦,提高模具寿命;⑸减少型材的挤压痕,改善型材的氧化着色质量。
8、怎样计算挤压机每小时产量?挤压机每小时产量按下面公式计算:As=3600×F×P[1Vi÷tf/(Ld-1)]其中:As-挤压机每小时产能(t/h)F-铸锭截面积(㎡)P-铸锭密度(m3)tf-辅助机构空程和工作行程时间(秒)Ld-铸锭长度(m)1-压余长度(m)Vi-平均挤压速度(m)9、如何实现6063合金的快速挤压?⑴严格控制铸锭的化学成分,如采用铝含量99.7%以上的铝锭作为基体,Mg+Si总量在1.0 %左右,Mg:Si控制在1.5~1.7,Fe含量要在0.20%以下;⑵用Ti-B细化铸锭晶粒,对铸锭均匀化处理;⑶挤压出口处型材温度控制在515~525℃左右;⑷模具工作带应光洁,并生产一定量型材后就要氮化处理重新抛光。
10.型材在挤压过程中,如何消除弯曲、扭拧、尺寸不合格等缺陷?除了正确设计模具和认真修理模具外,可采取以下措施消除上述缺陷:⑴设置导路:让温度高具有可塑性的型材沿着规定路线移动,从而消除缺陷;⑵使用牵引机:通过牵引型材,起到导路作用,从而克服各模孔流速不均匀而引起的各类缺陷。
11.什么是淬火处理?淬火是为了使模子出口处的型材快速冷却到室温,将在淬火温度下固溶于基体金属中的强化项Mg2Si保留在基体内。
6063合金的淬火敏感性较低,可以实现风冷淬火;而6061合金则必需采用水冷淬火。
12.张力矫直有什么作用?张力矫直是使型材在张力作用下产生塑性变形而实现矫直,从而消除型材的弯曲、扭拧、波浪等缺陷。
6063-T5合金型材的拉伸量为0.5%~1.5%。
13.什么是人工时效处理?人工时效是合金过饱和固溶体在固溶温度以下析出Mg2Si强化相而使合金强化的过程,人工时效处理是铝合金最重要的热处理,是改善合金组织构造和性能的重要手段,经过人工时效处理后强度可提高50%以上,消除了挤压残余应力,合金元素在时效中变得更均匀,固溶化更好,为氧化着色提供了一个组织均匀的表面,可获得色差小色调均匀的优质型材。
时效处理的温度和时间依合金种类、合金元素含量而变化,如果工艺参数选择不当,同样会造成组织结构和表面状态的差异。
6063铝合金通常采用200℃,保温两小时,决不宜高于210℃。
二、铝合金挤压型材常见缺陷及解决办法⑴划、擦、碰伤:划伤、擦伤、碰伤是当型材从模孔流出以及在随后工序中与工具、设备等相接触时导致的表面损伤。
主要原因1)铸锭表面附着有杂物或铸锭成分偏析,在挤压过程中金属流经工作带时,这些杂物或偏析浮出物附着在工作带表面或对工作带造成损伤,,最终对型材表面造成划伤;2)模具型腔或工作带上有杂物,模具工作带硬度较低,使工作带表面在挤压时受伤而划伤型材;3)出料轨道或摆床上有裸露的金属或石墨条内有较硬的夹杂物,当其与型材接触时对型材表面造成划伤;4)在叉料杆将型材从出料轨道上时,由于速度过快造成型材碰伤;5)在摆床上人为拖动型材造成擦伤;6)在运输过程中型材之间相互摩擦或挤压造成损伤。
解决方法1)加强对铸锭质量的控制;2)提高修模质量,模具定期氮化并严格执行氮化工艺;3)用软质毛毡将型材与辅具隔离,尽量减少型材与辅具的接触损伤;4)生产中要轻拿轻放,尽量避免随意拖动或翻动型材;5)在料框中合理摆放型材,尽量避免相互摩擦。
(二)机械性机能不合格主要原因1)挤压时温度过低,挤压速度太慢,型材在挤压机的出口温度达不到固溶温度,起不到固溶强化作用;2)型材出口处风机少,风量不够,导至冷却速度慢,不能使型材在最短的时间内降到200℃以下,使粗大的Mg2Si过早析出,从而使固溶相减少,影响了型材热处理后的机械性能;3)铸锭成分不合格,铸锭中的Mg、Si含量达不到标准要求;4)铸锭未均匀化处理,使铸锭组织中析出的Mg2Si相无法在较短时间内重新固溶,造成固溶不充分而影响了产品性能;5)时效工艺不当,热风循环不畅或热电偶安装位置不正确,导至时效不充分或过时效。
解决办法1)合理控制挤压温度和挤压速度,使型材在挤压机出口温度保持在最低固溶温度以上;2)强化风冷条件,有条件的工厂可安装雾化冷却装置,以期达到6063合金冷却梯度的最低要求;3)加强铸锭的质量管理;4)对铸锭进行均匀化处理;5)合理确定时效工艺,正确安装热电偶,正确摆放型材以保证热风循环通畅。
(三)几何尺寸超差主要原因1)由于模具设计不合理或制造有误,挤压工艺不当,模具与挤压筒不对中、不合理润滑等,导致金属流动中各点流速相差过大,从而产生内应力致使型材变形;2)由于拉伸矫直量过大导致型材尺寸超差。
解决办法1)合理设计模具,保证模具精度;2)正确执行挤压工艺,合理设定挤压温度和挤压速度;3)保证设备的对中性;4)采用适中的牵引力,严格控制型材的拉伸矫直量。
(四)条纹挤压型材的条纹缺陷种类比较多,形成因素也较复杂,这里仅就一些常见条纹的产生原因及解决方法加以论述。
A.摩擦纹模具每次抛光上机挤压后,纹路都不能一一对应,有轻有重。
主要原因在挤压过程中,型材流出模孔的瞬间与工作带紧紧地靠在一起,构成一对热状态下的干摩擦副,且将工作带分成两个区—粘着区和滑动区。
在粘着区内,金属质点受到至少来自两个方面的力的作用:摩擦力和剪切力。
当粘着区内金属质点所受摩擦力大于剪切力时,金属质点就会粘附在粘着区工作带表面上,并将型材表面擦伤形成摩擦纹。
解决办法1)调整模具工作带出口角 ,使其在-1~-3°范围内,这样可降低工作带粘着区高度,减小该区的摩擦力,增大滑动区;2)保证模具氮化处理质量,使模具表面硬度保持在HV900以上;工作带表面渗硫可降低粘着区摩擦力,减少摩擦纹。
B组织条纹主要原因铸锭铸造组织不均匀,成分偏析,铸锭表皮下存在较严重的缺陷,铸锭的均匀化处理不充分等,在随后的挤压过程中导致型材表面成分不均匀,从而使型材氧化后的着色能力不相同,形成组织条纹。
解决办法1)合理执行铸造工艺,消除或减轻组织条纹;2)铸锭表面车皮;3)严格按工艺对铸锭均匀化处理。
C.金属亮线在氧化白料中表面发亮,大多数情况下为笔直条状且宽度不定,在氧化着色料和表面喷涂料中该条纹呈浅色条纹。
主要原因由于金属流动出现摩擦或变形极其剧烈时,金属局部温度会上升很高,另外金属流动不均匀也会导至晶粒发生剧烈破碎,然后发生再结晶,致使该处组织发生变化,在随后的氧化处理中导致型材表面出现纵向的亮条纹,着色处理和表面喷涂中致使型材呈现浅色条纹。
解决办法1)合理设计模具结构;2)模具加工要注意工作带的过度,工作带要圆滑过渡,防止出现较大落差。
焊合条纹焊合条纹又称焊合线,笔直通长,在氧化白料中多呈现浅色,着色料和表面喷凃料中多呈浅色。
主要原因1)挤压比、分流比过小;2)焊合室深度不够,不能保证有足够的压力;3)挤压工艺不合理,润滑不当。
解决办法1)采用大吨位挤压机,提高挤压比;2)焊合室深度不够,不能保证有足够的压力;3)设计模具时必需考虑有足够的分流比;保证模桥呈水滴形,消除棱角;设计模具时尽量把焊合线避在角部;4)合理控制挤压工艺参数。
(五)挤压波纹挤压波纹是指在挤压型材表面出现的类似于水波纹的情况,一般无手感,在光的作用下表现明显。
主要原因1)牵引机发生周期性上下跳动使型材表面发生局部弯折;2)模具设计不合理,工作带在挤压力作用下发生颤动导致型材出现波纹。
解决办法1)保证牵引机运行平稳;2)合理设计模具结构。
(六)气泡型材表层金属与基体金属出现局部连续或断续的分离,表现为圆形或局部连续凸起。
主要原因1)由于挤压筒经长期使用后尺寸超差,挤压时筒内气体未排除,变型金属表层沿前端弹性区流出而造成气泡;2)铸锭表面有沟槽或铸锭组织中有汽孔,铸锭在墩粗时包进了汽体,挤压时汽体进入金属表层;3)挤压时,铸锭或模具中带有水分和油污,由于水和油污受热挥发成汽体,在高温高压的金属流动中被卷入型材表面型成汽体;4)设备排汽装置工作不正常;5)金属填充过快造成挤压排气不好。
解决办法1)合理选择和配备挤压工具,及时检查、修理或更换;2)加强铸锭的质量管理,严格控制铸锭的表面质量和含气量;3)尽量少涂油或不涂油;4)保证设备的排气系统正常;5)合理控制挤压速度,按要求进行排气。
(七)麻面麻面是指在型材表面出现的密度不等、带有拖尾、非常细小的瘤状物,手感明显,有尖刺的感觉。
主要原因由于铸锭中的夹杂物或模具工作带上粘有金属或杂物,在挤压时被高温高压的铝夹带着脱落,在型材表面形成麻面。