催化裂化操作指南(分馏与稳定)教材
催化裂化—催化裂化工艺(石油加工课件)

吸收塔、解吸塔、稳定塔。完成C2以下组分与C3、C4组分的分离。
四、烟气能量回收系统
一、反应-再生系统
高低并列式提升管催化裂化装置的反应再生和分馏系统的工艺流程
一、反应-再生系统
关键控制手段
1. 沉降器顶部压力:由吸收稳定系统的气压机入口压力调节汽轮机转速控制富气流 量,以维持沉降器顶部压力恒定。 2. 再生器顶部压力:以反应器和再生器压差(通常为0.02~0.04MPa)作为调节信号, 由双动滑阀控制。 3. 催化剂循环量:由提升管反应器出口温度控制再生滑阀开度来调节;根据系统压 力平衡要求由待生滑阀开度控制汽提段料位高度。 4. 烟气中的氧含量:根据再生器稀密相温差调节主风放空量(称为微调放空),来 控制(通常要求小于0.5%),防止发生二次燃烧。
请回答
催化裂化工艺流程的四个系统分别是什么?
反应-再生系统的关键控制因素有哪些?
反应器、沉降器、再生器
提升管反应器
提升管反应器是进行催化裂化化学反应的场所,是催化裂化装置的关键设备。
折叠式提升管反应器
直管式提升管反应器
两段提升管反应器
折叠式提升管反应器:多用于同轴式和由床层反应器改为提升管的装置。 直管式提升管反应器:多用于高低并列式提升管催化裂化装置。 两段式提升管反应器:有两根短提升管串联连接而成,用于两段式提升管催化裂化装置。
双塔流程
吸收稳定系统的工艺流程
四、烟气能量回收系统
目的:最大限度地回收能量,降低装置能耗。下图为催化裂化装置烟气轮机动 力回收系统的典型工艺流程。
烟气轮机动力回收系统的典型工艺流程
思政小课堂
实现绿色生产一直是石油化工人的理想追求,在催化裂化工艺中就蕴含 着很多的绿色理念。
催化裂化装置分馏单元开工操作法
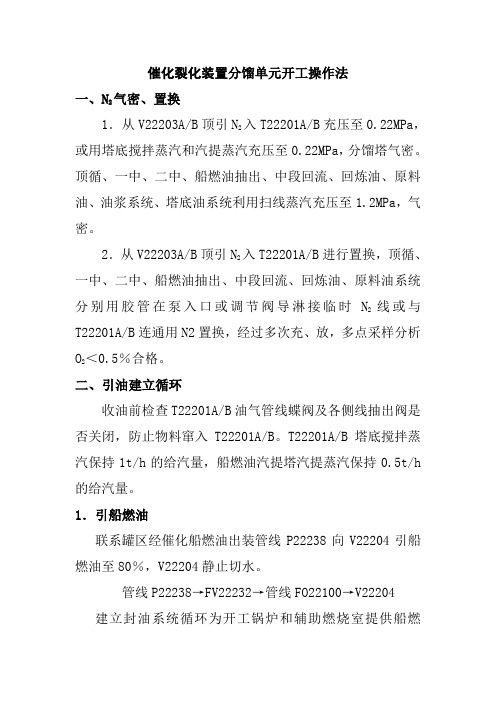
催化裂化装置分馏单元开工操作法一、N2气密、置换1.从V22203A/B顶引N2入T22201A/B充压至0.22MPa,或用塔底搅拌蒸汽和汽提蒸汽充压至0.22MPa,分馏塔气密。
顶循、一中、二中、船燃油抽出、中段回流、回炼油、原料油、油浆系统、塔底油系统利用扫线蒸汽充压至1.2MPa,气密。
2.从V22203A/B顶引N2入T22201A/B进行置换,顶循、一中、二中、船燃油抽出、中段回流、回炼油、原料油系统分别用胶管在泵入口或调节阀导淋接临时N2线或与T22201A/B连通用N2置换,经过多次充、放,多点采样分析O2<0.5%合格。
二、引油建立循环收油前检查T22201A/B油气管线蝶阀及各侧线抽出阀是否关闭,防止物料窜入T22201A/B。
T22201A/B塔底搅拌蒸汽保持1t/h的给汽量,船燃油汽提塔汽提蒸汽保持0.5t/h 的给汽量。
1.引船燃油联系罐区经催化船燃油出装管线P22238向V22204引船燃油至80%,V22204静止切水。
管线P22238→FV22232→管线FO22100→V22204 建立封油系统循环为开工锅炉和辅助燃烧室提供船燃油,控制封油压力2.45MPa。
V22204→P22214A/B→PV22401→V222042.引轻燃油(1).联系罐区经轻燃油不合格线向V22203A/B引轻燃油建立60%液位,静置脱水。
管线P22222→管线P22222/2→管线P22221→V22203A管线P22222→管线P22209→管线P22209/2→管线P22202/2→V22203B(2).重油分馏塔顶冷回流充轻燃油至FV22204阀前静置排水见油;轻燃油分馏塔顶冷回流充轻燃油至FV22212阀前静置排水见油。
(3).重油分馏塔顶循环系统关闭抽出阀,通过重油集合管开工补顶循管线P22225充轻燃油至FV22205阀前排水见油;轻燃油分馏塔顶循环系统关闭抽出阀,通过集合管开工补顶循管线P22203充轻燃油至FV22213阀前排水见油。
催化裂化工艺流程及主要设备教学内容

从流化域来看,单段再生和两
段再生都属于鼓泡床和湍流床 的范畴,传递阻力和返混对烧 碳速率都有重要的影响。
你知道吗?
如果把气速提高到1. 2m/s
以上,而且气体和催化剂向 上同向流动,就会过渡到快 速床区域。
烧焦罐再生(亦称高效再生)就是 循环流化床的一种方式
二密床高度4~6m. 烟气流速 0.1~0.25m/s
①对于全混床反应器,第一段出口的半再生剂的含碳量 高于再生剂的含碳量,从而提高了烧碳速率;
②在第二段再生时可以用新鲜空气和更高的温度,提高 了烧碳速率;
③第二段内的水气分压可以很低,减轻了催化剂的水热 老化;且第二段的催化剂藏量比单段再生器的催化剂藏量低, 停留时间较短。因此,第二段可采用较高的再生温度。
提升管反应器
(1)提升管
➢ 提升管反应器是一根长30~40m的管道,介质是油气和催化剂 ➢ 提升管下端油气速度一般为6 ~l0m/s,出口油气速度为16 ~30m/s, ➢ 操作温度,500~550℃。油气停留时间2~4S。 ➢ 为避免设备内壁受高流速催化剂冲蚀和减少热量损失,管内设有
100~125mm厚的隔热耐磨衬里。 ➢ 伸到汽提段、沉降器内的部分只设耐磨衬里。 ➢ 提升管的上端出口处设有气-固快速分离机构,用于使催化剂与油气
稀相管高度8~15m.
烧焦罐再生 烟气流速7~10m/s
循环管是烧焦罐再生器的独有设备, 它的作用是把热催化剂从二密相返回 烧焦罐,提高烧焦罐底部温度和烧焦 罐密度,以提高烧焦速度并增加烧焦 能力。早期的烧焦罐装置循环比为 I~I.5,循环管直径与再生剂管直径相 当;近年设计的烧焦罐装置循环比为 1.5~2,循环管直径明显大于再生管 直径。
催化裂化工艺流程及主要设备
催化裂化吸收稳定流程说明

催化裂化吸收稳定流程说明一、工艺流程叙述催化装置吸收稳定系统流程模拟流程图如图1 所示。
由分馏塔顶油气分离器来的富气经富气压缩机压缩到 1.6MPa(绝)。
压缩富气与解吸塔顶解吸气混合经气压机出口冷却器冷至55℃,再与吸收塔底油混合,经气压机出口后冷器冷至40℃,进入平衡罐(D-301)分离出气相(富气)及液相(凝缩油)。
吸收塔(C-301)位于脱吸塔(C-302)上部,压力1.4MPa(绝)。
由平衡罐来的富气进入吸收塔的下部,自稳定塔返回的补充吸收剂和分馏塔来的粗汽油均进入吸收塔的顶部,与气体逆流接触。
吸收塔设有两个中段回流,用以取走吸收过程所释放的热量,避免塔内温度上升过高。
中段回流自第14 层及第21 层用泵P3 及P4 抽出,分别经水冷器(E-306,E-307)冷至40℃,返塔第15 层及第22 层上方,吸收塔底釜液饱和吸收油返回到上游与压缩富气混合。
吸收塔顶采出的贫气,进入再吸收塔(C-304)底部,与轻柴油吸收剂逆流接触,吸收贫气中的汽油组分。
塔顶压力为1.3~1.4MPa(绝),塔顶干气为装置的副产品。
塔底富吸收油返回分馏塔。
D-301 底凝缩油经泵P1 加压,与稳定汽油换热(E-304)至70℃进入解吸塔C-302 上部,塔顶压力1.6MPa(绝)。
解吸塔底重沸器E-301 由分馏塔一中回流供热。
解吸塔顶气返回至E-305 前与压缩富气混合。
C-302 塔底脱乙烷汽油经稳定塔进料泵与稳定汽油换热(E-302)至165℃入稳定塔(C-303)。
C-303 塔顶压力1.17MPa(绝),塔底重沸器E-303由分馏二中回流供热。
液化气组分由C-303 顶馏出,经水冷器(E-308)冷却至40℃,入回流罐(D-302)。
液化气经回流泵加压(P-304)后,一部分作为顶回流,另一部分出装置。
稳定塔釜液稳定汽油先与脱乙烷汽油换热(E-302)至161.4℃,再与凝缩油换热(E-304)至130℃,再经除盐水冷却器(E-309)冷至40℃,一部分出装置,一部分用泵P6 打入塔C-301 顶作补充吸收剂。
重油催化裂化吸收稳定单元操作法

重油催化裂化吸收稳定单元操作法催化裂化吸收稳定部分的任务是将来自分馏塔顶油气分离后的粗汽油和富气,通过吸收、解吸分离出干气,通过稳定塔分离出液化气和稳定汽油产品。
为满足汽油产品质量升级的要求,稳定汽油进行轻重汽油分离,分馏后的轻汽油至催化提升管回炼降低烯烃含量,提高液化气产率,重汽油至加氢装置进行脱硫。
稳定汽油和液化气产率的高低,关键取决于催化裂化反应系统的工艺过程,同时也取决于吸收稳定系统的回收程度和操作水平,即分离效果和回收率。
一、正常操作1.干气中C3+含量的控制(≯3%V)干气通常作为炉用燃料。
如果干气中含太多的C3、C4,会造成化工原料的浪费及经济效益的降低,另外干气作乙烯吸附等化工原料对C3+含量控制要求严格。
吸收是以利用压缩富气中各组分在吸收剂中的溶解度的不同达到分离的目的。
影响吸收的因素很多,主要有:油气比、操作温度、操作压力、吸收剂和被吸收气体的性质、塔内气液流动状态、塔板数及塔板结构等。
对具体装置来讲,吸收塔的结构等因素都已确定,吸收效果主要靠适宜的操作条件来保证。
主要影响因素:1)粗汽油与稳定汽油(或重汽油)吸收剂量不足,干气中C3+含量高。
2)吸收剂的温度高,干气中C3+含量高。
3)吸收质(压缩富气)冷后温度高,干气中C3+含量高。
4)吸收塔一、二中段的冷却热量小,干气中C3+含量高。
5)吸收塔操作压力过低,干气中C3+含量高。
6)稳定深度给吸收带来的影响。
深度稳定,稳定汽油蒸汽压小,汽油C含4量少,吸收剂质量提高,吸收效果提高,干气中C3+含量少。
7)粗汽油进料口的位置及流量的影响。
8)操作波动,尤其是操作压力波动给吸收效果带来的影响。
调节方法:1)用补充吸收剂量来控制适宜的油气比,设计值为4.02。
2)尽量降低粗汽油和稳定汽油(或重汽油)冷后温度,从而控制较低的吸收剂入塔温度,设计值为40℃。
3)尽量降低压缩富气冷后温度,设计值为40℃。
4)尽量增加吸收塔一、二中段尤其是二中段的冷却取热量。
6催化裂化工艺技术研讨6.分馏于与吸收稳定ppt

CH-6 分馏、吸收稳定简述
一、分馏部分 1、任务:
将高温油气(含固粒)分割成气体(干气 +LPG)、粗汽油、轻柴油、回炼油(HCO)、 油浆等不同馏分的产品。
2、催化分馏塔结构示意(3#板—塔底) 柴油塔(3#板—17#板) 汽油塔(17#—塔顶)
高温过热油气(含催化剂颗粒)进料
3、原则流程 : 见附图21
吸收剂
含有汽油组分
回
收
补充吸收剂
汽
油
解
组
吸
分
C1
C2
吸 收 C3 C4
使汽油蒸汽压合格 LCO
图21 吸收-稳定系统
4、控制指标: 汽油蒸汽压: 冬季≯88kpa 夏季≯74 kpa LPG 中 : C5+ ≯3%v (C1+C2 ≯1%v )
干气中: C3+ ≯3%v
设脱过热段(洗涤段)
全抽出塔盘 4、控制指标:
粗汽油干点
轻柴油凝点、闪点
5、塔底液面控制 塔底抽出流量控制
露点温度 控制: 塔底液相温度(FCC) 一层板下温度(RFCC)
6、分馏系统原则流程 分馏塔、塔顶油汽分离罐 柴油汽提塔、回炼油罐 原料油缓冲罐
7、防止油浆系统结焦: 塔底温度≯ 350 ℃ 塔底油浆停留时间≯ 5 min 油浆管线速度 ≮1.2 m/s 使用阻垢剂
二、吸收稳定
1、任务 控制汽油蒸汽压、回收LPG和干气
2、名词 ●富气—未经吸收的油气,C3+ >150g/m3
组成: 干气3~4%m/feed LPG14~18%m/feed 汽油10~15%m/feed 烟气 1.0~1.2Nm3/t循环cat
石油催化裂化—分馏系统工艺流程介绍

❖ 回炼比升高,反应所需热量升高,原料预热炉
负荷增大,反应器负荷增大,处理量降低。
工艺流程简述
分馏工艺流程
03 分馏塔
❖提高了侧线产品重柴油和轻柴油的质量 ❖提高了轻组分的收率。
工艺流程简述
分馏工艺流程
04 塔顶
❖产品:粗汽油和富气; ❖粗汽油部分回流控制塔顶温度。
工艺流程简述
分馏工艺流程
05 循环回流
❖剩余热量过多 ❖提高塔处理能力 ❖利用高温位热量,节能。
课程:石油炼制运行与操控 知识点:分馏工艺流程
分馏工艺流程
过热油气
460~480 ℃
回炼油
Hale Waihona Puke 富气粗汽油 轻柴油 重柴油 油浆
工艺流程简述
分馏工艺流程
01 脱过热段
❖ 洗去油气中的粉尘 ❖ 油气呈“饱和状态”
过热油气
工艺流程简述
分馏工艺流程
02 回炼油罐
工业装置上常用回炼操作来提高轻质油的收率”
❖ 降低反应深度,柴油不易二次裂化,柴油产
催化裂化装置技术手册
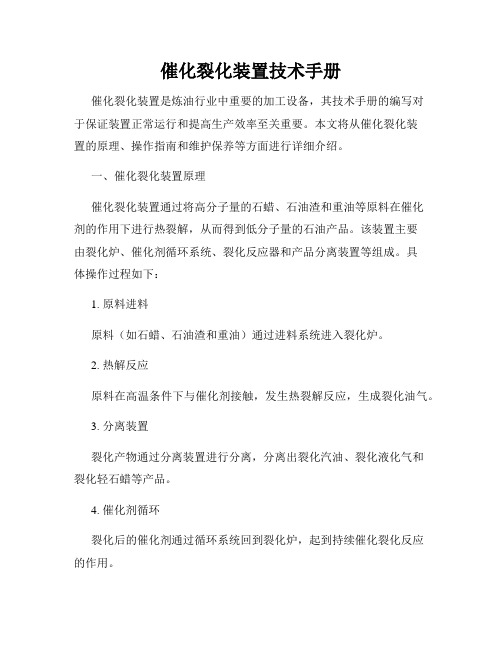
催化裂化装置技术手册催化裂化装置是炼油行业中重要的加工设备,其技术手册的编写对于保证装置正常运行和提高生产效率至关重要。
本文将从催化裂化装置的原理、操作指南和维护保养等方面进行详细介绍。
一、催化裂化装置原理催化裂化装置通过将高分子量的石蜡、石油渣和重油等原料在催化剂的作用下进行热裂解,从而得到低分子量的石油产品。
该装置主要由裂化炉、催化剂循环系统、裂化反应器和产品分离装置等组成。
具体操作过程如下:1. 原料进料原料(如石蜡、石油渣和重油)通过进料系统进入裂化炉。
2. 热解反应原料在高温条件下与催化剂接触,发生热裂解反应,生成裂化油气。
3. 分离装置裂化产物通过分离装置进行分离,分离出裂化汽油、裂化液化气和裂化轻石蜡等产品。
4. 催化剂循环裂化后的催化剂通过循环系统回到裂化炉,起到持续催化裂化反应的作用。
二、催化裂化装置操作指南1. 温度控制裂化炉温度是影响裂化反应效果的关键参数。
在操作中,应根据不同原料的特性和所需产品质量,合理控制催化裂化温度,避免温度过高导致催化剂失活或温度过低影响反应速率。
2. 原料选择不同原料的性质对裂化反应的影响有所差异。
应根据目标产品质量和市场需求,合理选择原料,并进行合适的预处理,如脱蜡、脱硫等,以提高裂化效果和产品品质。
3. 催化剂活性管理催化剂是催化裂化装置中最关键的组成部分。
为保证装置的正常运行,应定期检测催化剂的活性,并进行必要的处理,如焙烧、再生等,以延长催化剂的使用寿命。
4. 安全操作在操作催化裂化装置时,应严格遵守操作规程,保证操作人员的人身安全和设备的正常运行。
同时,应加强对催化裂化装置的检测和维护,及时发现和处理潜在的安全隐患。
三、催化裂化装置维护保养1. 清洗与清理定期对催化裂化装置进行清洗和清理,去除附着物、沉积物和焦炭,以保证装置的畅通和正常运行。
2. 检修和更换定期进行设备的检修和更换,如检修泵、阀门等关键设备,更换老化和磨损的零部件,以确保催化裂化装置的长期稳定运行。
催化裂化操作规程
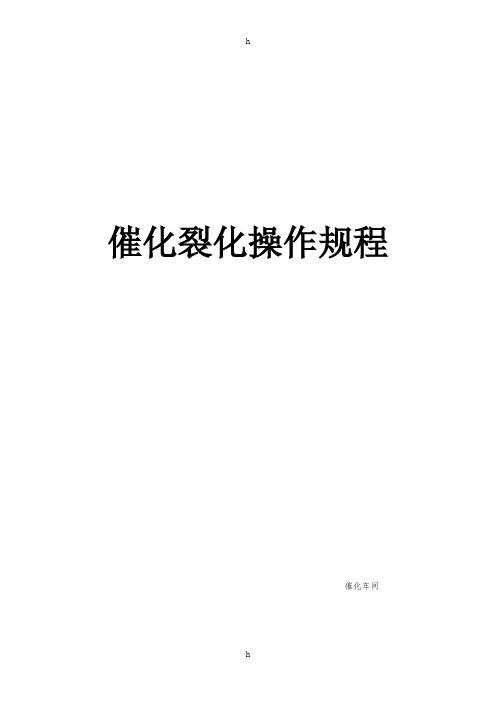
催化裂化操作规程催化车间第一章 装置概况第一节 概况一、本装置设计能力为41014 吨/年(年开工时为8000小时),由反应、分馏、吸收稳定、主风机、气压机等部分组成。
原料由大庆管道原油的常压渣油、通过催化裂化,生产93#汽油,轻柴油、液化汽等目的产品。
二、本装置工艺和设备的主要特点1、两器采用同轴式组合,具有操作弹性大、两端再生。
再生催化剂含碳低。
2、 抗金属污染好、生氢及生焦率较低轻质油收率较高,气体收率较低的系统列分子筛催化剂(具体使用的催化剂类型,根据生产需要选择)。
3、为降低装置能耗采用内取热器,回收才生余热付产蒸汽。
4、由于设计原料为大庆管道原油的常压渣油,其残炭和胶质的含量较高,所以裂化后的油浆比重较大,故在生产采用油浆,不回炼或部分回炼的方案以维持再生器的热量平衡和分馏塔底油浆的比重不超标准。
5、由于同常减压装置可以联合操作,以常压热渣油为原料,所以在开工后可以甩掉加热炉。
6、吸收稳定系统采用双塔流程。
第二节设计数据一、原料性质二、汽油馏分性质三、轻柴油馏分性质四、装置物料平衡表五、反应再生部分工艺计算汇总六、装置能耗汇总表设计进料量70000吨/年装置组成:反应再生部分,分馏部分,吸收稳定部分,碱洗部分第三节装置流程简介一、反应再生部分原料油自罐区的原料罐来经泵(P201/1.2)加压后送到至原料一—轻柴油换热器(E205/1.),再进入原料—油浆换热器(E201/1.2.)换热后,进入闪蒸罐(V203/1),经过加热炉后的原料沿管排进入闪蒸(V203/1),进入闪蒸罐内的原料汽相沿顶部汽返线进入分馏塔(T201)第二层塔盘上部,液相自罐底部抽经泵(P201/2.3)加压后进入提升管反应器。
回炼油自分馏塔第一层塔盘自流入回炼油罐(V202),经回炼油泵(P206/1.2)加压后,送到提升管反应器下部与分馏塔底油浆经泵(P207/1.2)加压后送至提升管下部的回炼油浆混合一并进入提升管反应器(R101)。
催化裂化工艺技术手册

催化裂化工艺技术手册第一章催化裂化工艺概述1.1 催化裂化的定义和作用催化裂化是一种重要的炼油工艺,主要用于将重质石油原料分解为轻质燃料和高附加值的化工产品。
通过催化剂的作用,在高温下将长链烃分子裂解成短链烃分子,以提高产品质量和产率。
1.2 催化裂化工艺的发展历程催化裂化工艺的应用可以追溯到20世纪初。
随着石油行业的不断发展,催化裂化技术也得到了广泛应用。
从传统催化裂化到流化床催化裂化,再到现代的超轻质催化裂化,工艺不断创新和改进,以满足市场需求。
1.3 催化裂化的工艺流程和原理催化裂化的工艺流程包括加热炉和裂解器两个主要部分。
在加热炉中,通过加热将石油原料加热至适宜的温度,然后送入裂解器进行裂解反应。
裂解反应在催化剂的作用下进行,在高温和压力下,长链烃被裂解成短链烃。
第二章催化剂的选择和性能2.1 催化剂的种类和特点常用的催化剂包括酸性催化剂和贵金属催化剂。
酸性催化剂主要是用来促进分子内结构重排和骨架碳裂解反应,贵金属催化剂则用于催化氢化反应,减少不饱和化合物。
2.2 催化剂的性能参数选择合适的催化剂对于提高催化裂化的效果至关重要。
催化剂的性能参数包括比表面积、孔径分布、酸性、稳定性等。
这些参数直接影响到催化反应的速率和选择性。
第三章催化裂化装置的设计和运行3.1 催化裂化装置的主要设备催化裂化装置主要包括加热炉、裂解器、分馏塔等组成。
加热炉用于将石油原料加热至裂解温度,裂解器是催化裂化反应的主要场所,分馏塔用于分离裂解产物。
3.2 催化裂化装置的操作注意事项催化裂化装置的正常运行需要注意以下几个方面:保持适宜的反应温度和压力,注意催化剂的再生和投料,控制氢气和催化剂的用量,合理处理废气和废水。
第四章催化裂化产品的特性和应用4.1 轻质燃料的生产和应用催化裂化可以将重质石油原料转化为轻质燃料,如汽油、柴油和液化石油气。
这些轻质燃料在交通运输、工业生产和日常生活中广泛应用。
4.2 高附加值化工产品的生产和应用除了轻质燃料,催化裂化还可以生产一系列高附加值的化工产品,如石蜡、石油焦等。
催化裂化操作规程(2)

1.8.5.2气压机采用气压机+中压背压式透平机二机组组成。
1.8.6工艺流程特点
1.8.6.1 有针对性的采用新型冷换设备。分馏塔顶油气冷却系统采用表面蒸发式空气冷却器,气压机二级出口冷却器、稳定塔顶冷却器、稳定汽油冷却器也采用表面蒸发式空气冷却器,不但节省了水冷器、降低了循环水系统的负荷,而且减小了系统压降,降低气压机的功率消耗,有利于分馏和吸收稳定系统操作。
1.11.1反应温度(TIC2232)
1) 原料预热温度控制原料预热温度控制即提升管进料(主要是混合原料油)的温度控制是通过改变原料油与油浆的换热量来实现的。
2)提升管反应温度(TICSA2101)
反应温度是影响催化裂解装置产率及产品分布的关键参数之一,它受许多工艺参数和制约条件的影响。催化裂解反应是吸热反应,所需热量直接由再生器烧焦的燃烧热(主要的)和进料携带的热量(次要的)提供,在其它因素相对不变的条件下,反应温度在一定范围内可以通过再生催化剂的循环量来控制。
1.8.2.3采用CS型高效雾化喷嘴。改善雾化效果,提高轻质油收率,减少干气及焦炭产率。
1.8.2.4提升管中上部设有注反应终止剂措施。以抑制氢转移等二次反应及减少热裂化反应,增加操作的灵活性和适应性。
1.8.2.5提升管出口快分技术。提升管出口采用粗旋加单旋并采用近似直联技术,使催化剂与反应油气迅速分离,力求减少油气在高温区的停留时间和与催化剂的接触时间,从而减少干气产生。
1 装置概况
1.1装置为新建催化裂化装置。
1.2装置规模
催化裂化分馏和吸收稳定

2.1.4吸收、稳定流程 低温回收C3=流程
•塔顶温度-20C,压力1。7MPa绝 •回收干气中的C3=达93%
•投资回收期1.5-2.5年
2.1.5吸收、稳定流程 轻汽油醚化
•C4=、C5=都可以醚化成为高辛烷值组分,如MTBE、 ETBE、TAME等 •在稳定塔前加一个分离塔就可以分出重汽油。塔顶物流 进入稳定塔,塔顶出液化气,塔底出轻汽油。轻汽油含 C4=、C5=较多,可以醚化,得到高辛烷值组分
•分段冷凝时冷凝系统压降增加
1.2.2 分馏系统技术分析 分馏塔温度分布
•分段冷凝使塔顶温度升高约20C •重油催化裂化时,塔底容易结焦,温度减少20C
1.2.3 分馏系统技术分析 热平衡及取热分配
•分馏塔热平衡受回炼比影响很大,回炼比增加0。1全塔剩 余热增加63MJ/t原料 •生产方案的影响:柴油方案回炼比较大,剩余热量较大 •回流取热的经验数据:顶回流15-20%,一中段15-20%, 二中段30-35%,油浆循环回流30-35%
工艺工程师的任务
•日常报表 •分析异常现象
•根据新的情况,制定工艺条件
•通过标定核算发现问题 •通过评估拟定节能和环保方案 •参加先进控制小组制定控制策略
催化裂化分馏、吸收和稳定
第一节 分馏系统 第二节 吸收稳定系统 第三节 干气烃化系统
第一节 分馏系统
•分馏流程
•技术分析
•分馏塔负荷
1.1 分馏流程
39.3 530
填料 66.6 0.114 9.7 629
1.2.8 分馏系统技术分析 结盐及腐蚀
•在轻柴油以上部位析出NH4Cl。可以提高分馏塔温度及原 油深度脱盐,除去NaCl. •腐蚀主要是H2S应力腐蚀
第二节 吸收、稳定系统
催化裂化装置分馏工段使用手册

350万吨/年重油催化裂化装置仿真系统使用手册(分馏工段)北京东方仿真控制技术有限公司目录一.工艺流程简介........................................... 错误!未定义书签。
1.装置简介.................................................错误!未定义书签。
2.工艺流程说明.............................................错误!未定义书签。
二.设备列表............................................... 错误!未定义书签。
三.仪表列表............................................... 错误!未定义书签。
四.装置主要现场阀列表 ..................................... 错误!未定义书签。
五.操作规程............................................... 错误!未定义书签。
冷态开车....................................................错误!未定义书签。
正常停车...................................................错误!未定义书签。
正常调节...................................................错误!未定义书签。
事故处理....................................................错误!未定义书签。
六.复杂控制回路........................................... 错误!未定义书签。
串级控制....................................................错误!未定义书签。
催化裂化工艺流程及主要设备课件

加热炉通常采用燃油、燃气或电加热方式,根据不同的 工艺需求选择合适的加热方式。
加热炉的操作需根据工艺要求控制温度、压力和流量等 参数,以确保原料油和催化剂得到均匀加热。
分馏塔
分馏塔是催化裂化工艺流程中 用于分离不同沸点的烃类的设 备。
反应器内部通常装有高效催化剂,以 促进原料油裂化成小分子烃类,同时 降低生焦率。
反应器通常采用固定床、流化床或移 动床的情势,根据不同的原料和产品 需求选择合适的反应器类型。
反应器的设计需考虑温度、压力、原 料油性质和流量等工艺参数,以确保 较高的转化率和选择性。
再生器
再生器是催化裂化工艺流程中 用于烧焦和再生催化剂的设备
气体净化
分离出的气体中可能含有 硫化氢、一氧化碳等杂质 ,需要进行脱硫、脱碳等 处理,以满足环保要求。
液体产品精制
经过油气分离后的液体产 品需要进行精制,如加氢 处理、脱蜡等,以提高产 品的质量和稳定性。
03
主要设备介绍
反应器
反应器是催化裂化工艺流程中的核心 设备,用于实现原料油在催化剂的作 用下的裂化反应。
活性和寿命。
预热和注水
预处理过程中,原料油需要经过 加热和注水处理,以提高油品的 流动性和降低粘度,有利于油品
的快速加热和反应。
原料的雾化
为了使原料油与催化剂充分接触 和混合,需要对原料油进行雾化 处理,使其形成微小的液滴,增 加油滴在反应器内的停留时间。
反应过程
反应温度与压力
催化裂化反应需要在一定的温度和压力下进行,通常温度在450550℃之间,压力在0.5-1.0 MPa之间。
催化裂化工艺流程及主要设备课 件
催化操作规程

博兴县永鑫化工有限公司15万吨/年重油催化裂化操作规程二零零五年十月目录第一章催化裂化工艺流程------------------------------------------------------3 § 1正常操作流程----------------------------------------------------------------3 § 2开停工流程-------------------------------------------------------------------4 § 3事故处理流程----------------------------------------------------------------5 § 4催化剂流程-------------------------------------------------------------------6 § 5工艺操作指标----------------------------------------------------------------6 § 6质量指标---------------------------------------------------------------------9 第二章催化裂化装置主要设备-----------------------------------------------10 § 1设备明细表------------------------------------------------------------------10 § 2主要设备简介---------------------------------------------------------------10 第三章催化裂化装置开工、停工--------------------------------------------14 § 1 装置开工--------------------------------------------------------------------14一、开工前的准备------------------------------------------------------------141 原则和要求------------------------------------------------------------------142 准备和检查------------------------------------------------------------------14二、吹扫试压------------------------------------------------------------------141 目的和要求------------------------------------------------------------------142 吹扫和试压------------------------------------------------------------------143 试压标准---------------------------------------------------------------------15三、升温烘器、系统引油---------------------------------------------------161 目的和要求------------------------------------------------------------------162 升温烘两器------------------------------------------------------------------163 系统引油---------------------------------------------------------------------16四、反应进料前准备---------------------------------------------------------171 装转催化剂、平衡剂------------------------------------------------------172 反应、沉降赶空气和两器流化------------------------------------------173 原料升温脱水、切换汽封------------------------------------------------18五、反应进料开工------------------------------------------------------------18六、精制准备、开工----------------------------------------------------------19 § 2装置停工---------------------------------------------------------------------19一、装置正常停工------------------------------------------------------------191 停工原则---------------------------------------------------------------------192 停工要求---------------------------------------------------------------------193 岗位停工操作---------------------------------------------------------------20二、装置异常停工------------------------------------------------------------221 原则和要求------------------------------------------------------------------222 岗位停工操作---------------------------------------------------------------23三、装置事故停工------------------------------------------------------------241 原则和要求----------------------------------------------------------------242 岗位停工操作-------------------------------------------------------------24 第四章岗位操作法----------------------------------------------------------25 § 1 反应――再生岗位操作法-----------------------------------------------25 § 2 分馏岗位操作法----------------------------------------------------------42 §3 吸收稳定岗位操作法----------------------------------------------------49 §4 精制脱硫岗位操作法----------------------------------------------------55 § 5 气压机岗位操作法-------------------------------------------------------56 § 6 司泵岗位操作法-----------------------------------------------------------61 第五章安全生产规定-------------------------------------------------------66 § 1安全规定--------------------------------------------------------------------66 § 2安全检查制度-------------------------------------------------------------68第一章催化裂化工艺流程工艺流程简述催化裂化装置主要流程由反应——再生、分馏、吸收稳定、产品精制、主风机、气压机、空压机、余热锅炉八部分,其中主风机、气压机、空压机单独设操作规程。
重油催化裂化分馏单元操作法

重油催化裂化分馏单元操作法催化裂化分馏系统的任务主要是把反应器送来的油气混合物,按沸点的差异分割为富气、粗汽油、轻柴油、回炼油和油浆等馏份,并保证各个馏份的质量符合规定要求,为气压机和吸收稳定提供合格进料;此外,还要将反应油气携带的热能,通过回流热和馏份余热回收利用,用来发生中压蒸汽或预热原料、提供脱吸和稳定热源、加热除盐水、低温热至气分作热源等。
一、正常操作1.分馏塔底液相温度的控制由于油浆中含有较多的重质芳烃,在较高的温度下极易结焦,造成油浆泵排量减小,油浆所流经的管线、换热器等以较低的流速通过,导致固体颗粒沉积,进一步加剧油浆在管内结焦,严重时导致被迫停工。
为防止塔底结焦,应控制最大的油浆循环总量(还应控制油浆上返塔量不低);油浆固体含量不大于6g/l;严格控制分馏塔底温度不大于350℃。
主要影响因素:1)反应温度升高,塔底温度上升。
2)反应加工量增大,塔底温度上升。
3)内回流量减少,塔底温度升高。
4)油浆上返塔量(8FIC220)增大,塔底温度升高。
5)回炼比增大,塔底温度升高。
6)分馏塔底注汽量增大,塔底温度下降。
7)油浆下返塔量(8FIC204)增大,塔底温度下降。
8)油浆返塔温度(8TI249)降低,塔底温度下降。
9)油浆蒸汽发生器内漏,塔底温度下降。
调节方法:1)正常情况下,为减少油浆系统结焦,油浆循环下返塔实施最大流量控制,这样可以使塔底温度8TI232最低、油浆线速最大、停留时间最短。
(因为油浆循环下返塔不与油气接触,塔底油属过冷液体、非平衡液相,所以油浆中不会含有过多轻馏分)。
2)随着油浆停止回炼,塔底油冷凝量减少,油浆取热量也随之减少,为确保循环油浆对油气中催化剂的洗涤效果(洗涤效果不好容易造成分馏塔下部塔板结焦),油浆上返塔流量不宜过小。
为此可采取塔底热油浆直接进入油浆上返塔,提高返塔温度(设计值275℃),增加油浆上返塔流量。
2.分馏塔底液面(8LI202、8LI202B)就分馏自身而言,塔底液面的变化反映了全塔物料平衡的变化,物料平衡又取决于温度、流量和压力的平衡及回炼油与油浆量的平衡。
- 1、下载文档前请自行甄别文档内容的完整性,平台不提供额外的编辑、内容补充、找答案等附加服务。
- 2、"仅部分预览"的文档,不可在线预览部分如存在完整性等问题,可反馈申请退款(可完整预览的文档不适用该条件!)。
- 3、如文档侵犯您的权益,请联系客服反馈,我们会尽快为您处理(人工客服工作时间:9:00-18:30)。
第一节 第二节 第三节 第四节 第五节 主要设备 开工准备 开工过程 停工与事故处理
产品精制
气体精制
分馏过程
第一节 概 述
分馏系统的任务是把反应油气按沸点范围分割成富气、粗汽油、轻 柴油、重柴油、回炼油、油浆等馏分,并保证各个馏分质量符合规定要 求。富气和粗汽油送到吸收稳定系统,柴油经精制后送出装置,回炼油 和油浆送回提升管反应器。
催化裂化装置操作指南
第二部 (分馏、吸收稳定过程及产品精制)
防城港市信润石化有限公司 培训队
2014年8月14日
分馏与吸收稳定过程
目
录
分馏过程
第一节 概述
第二节 工艺流程及主要控制方案
第三节 主要设备
第四节 开工准备
第五节 开工过程
第六节 操作参数与调节方法
第七节 停工和事故处理
分馏与吸收稳定过程
装置开工首先进行开路大循环。原料油从罐区引进装置,经装置内三 路循环后由油浆冷却水箱外甩口送到罐区。开路大循环的目的是考验装 置外系统设施情况,及脱除外部系统存水。当开路循环完成后改为装置 内循环。
原料油循环:原料罐→原料泵→提升管反应器前→循环阀→原料罐 回炼油循环:回炼油罐→回炼泵→提升管反应器前→循环阀→回炼油罐 油浆循环:回炼油罐→联通阀→油浆泵→返塔线→循环阀→原料罐
(3)汽油、柴油补油流程
开工时为顺利建立分馏塔顶循环回流,从粗汽油出口引一根管线到顶 循环泵入口,当顶循环泵不上量时补入汽油。轻柴油泵出口引一根管线 到中段油泵入口,开工时帮助快速建立中段循环回流,抽空时补轻柴油。
分馏过程
分馏过程
4、开停工辅助流程 (1)引水和除氧水流程
装置第一次试运时要进行水联运。一般在粗汽油泵入口接有新鲜水管线。
从化学水引来的除氧水线到热水器再到各蒸汽发生器,产生蒸汽。
(2)引燃料气流程
开工时辅助燃料炉用的液化气由罐区提供,有专门的液化气线到装置 内的气化器,经蒸汽加热升压后引到辅助燃料炉使用。
在拆油气大盲板前,开工原料不进分馏塔,原料罐和回炼油罐的挥 发油气线也不进分馏塔,而是通过专门设计的油气冷却线排至轻污油罐。
分馏过程
拆除油气大盲板后,将开工原料改进分馏塔,打开塔底进泵阀,关闭回 炼油罐联通阀,关闭循环回炼油罐阀,打开返塔阀,建立油浆正常循环 (塔内循环)同时将挥发线改进分馏塔。拆除油气大盲板前,可将进分 馏塔蒸汽停掉。
分馏过程
③顶循环回流系统。顶循环回流用泵从分馏塔第4层抽出,经热水换热器 (低温热利用)、循环水冷却器(空冷)冷却,返回分馏塔1层塔板。
④轻柴油系统。轻柴油从分馏塔第12-14层塔板流出,进入轻柴油汽提塔 上部,下部进入蒸汽对轻柴油进行汽提,汽提气返回分馏塔11层,汽提 后用泵抽出升压后经与富吸收油换热器、热水换热器、循环水冷却器 (空冷)冷却后,一路去再吸收塔作再吸收剂,另一路作为产品送出装 置。
分馏部分流程含有多个系统,原料油、回炼油系统,顶循环、一中 段、二中段、油浆循环系统,粗汽油、轻重柴油系统等,是一个复杂的 多系统体系。而且上受反应系统制约,下又牵扯富气压缩机和吸收稳定 系统,是起着承上启下的作用。
第二节 工艺流程及主要控制方案
一、工艺流程
1、工艺特点 (1)有脱过热和冼涤段
分馏塔进料是带有催化剂细粉的高温油气。与其他装置分馏塔不同 之处是催化分馏塔专门设有脱过热和冼涤段。脱过热段设有数层人字
尽量降低分馏系统压降(包括分馏塔、塔顶冷凝冷却系统及压缩机入 口系统),提高富气压缩机入口压力,可降低气压机功率消耗,提高气 压处理能力。
2、工艺流程 有几种典型流程:
(1)冷原料流程(早期蜡油催化裂化) (2)热原料流程 ①原料油预热系统。重油催化裂化要求原料进料温度较低,一般为200-
250 ℃ 。可从常压直接来150-200 ℃ 热原料,进入原料罐,用原料泵 升压后与循环油浆换热升到200-250 ℃进入反应器提升管。 ②塔顶系统。粗汽油、富气、水蒸气从分馏塔顶出来,经空冷器(有的装 置用热水回收其低温热)、冷凝冷却器进入分馏塔顶油气分离罐。未冷 凝下来的油气(富气)去压缩机。粗汽油用泵送往吸收塔。
⑤中段循环回流系统。用泵从分馏塔17层抽出后经稳定塔重沸器、解吸塔 重沸器、热水换热器、循环水冷却器(空冷)冷却后返回分馏塔15层。
⑥重柴油系统。重柴油从分馏塔22层流出,进入重柴油汽提塔进行汽提, 然后用泵升压后经热水换热器、循环水冷却器(空冷)冷却后,送出装 置。
⑦回炼油系统。回炼油从分馏塔27-29层自流进入回炼油罐,用泵抽出一 部分返塔最下一层塔板,大部分去提升管反应器回炼。
分馏过程
档板或园盘型档板,进入油气与260-360℃循环油浆逆流接触、换热、 冼涤,油气被冷却,将油气中夹带的催化剂细枌冼涤下来,防止其污染 上部的测线产品,堵塞上部塔盘。
(2)全塔过剩热量大
分馏塔进料是过热度很高的反应油气(480-510 ℃ ),塔顶是低温 (100-130 ℃ )气体,其他产品均以液态形式离开分馏塔。在整个分 馏过程中有大量的过剩热量需要移出。所以系统有大量的冷换设备和热 水器。
分馏过程
⑧油浆系统。油浆从塔底抽出后,少部分去提升管回炼,大部分经原料油 换热器、蒸汽发生器返回分馏塔。油浆外甩从蒸汽发生器后引出,经冷 却水箱将温度降低(不大于95 ℃ )再送出装置。 热原料流程示意图:
分馏过程
分馏过程
3、开工循环流程
设置开工循环流程的目的是负荷试运行阶段为装置内高温管道、设备 预热升温,以脱除系统内存水;预热高温管道,是考验系统(管道、仪 表、设备等)的耐热性能;高温设备热紧等。开工循环有开路循环、闭 路循环;塔内循环、塔外循环之分。装置内循环系统主要有原料油、回 炼油、循环油浆,简称三路循环。
(3)产品分馏要求较容易满足
油品分馏难易程度可用相邻馏分50%馏出温度差值来衡量。差值越大, 馏分间相对挥发度越大,就越容易分离。催化分馏塔除塔顶为粗汽油外 还有轻柴油、重柴油、回炼油三个侧线组分。催化裂化各侧线组分50% 馏出温度值较大,馏分容易分离,所以产品分馏要求容易满足。
分馏过程
(4)要求尽量降低分馏系统压降