输送带纵向撕裂检测方法之一
输送带撕裂检测技术浅析

工业技术科技创新导报 Science and Technology Innovation Herald59DOI:10.16660/ki.1674-098X.2019.16.059输送带撕裂检测技术浅析①王伟(秦皇岛港股份有限公司第七港务分公司 河北秦皇岛 066000)摘 要:输送带在码头、矿山以及各类生产企业应用广泛,可实现物料的长距离、大运程、高速度输送。
输送带占皮带机总成本的40%左右,发生撕裂带来的经济损失大,更换、维修费时费力,严重影响生产。
因此,选择适当的防撕裂装置具有重要的现实意义。
本文简要介绍输送带撕裂的原因及目前国内主要输送带撕裂检测所采用的技术方案,分析各方案的技术特点,可供码头、矿山等输送带使用企业参考。
关键词:输送带 撕裂检测 检测方案中图分类号:TD528 文献标识码:A 文章编号:1674-098X(2019)06(a)-0059-02①作者简介:王伟(1984—),男,汉族,天津人,本科,机电工程师,研究方向:港口装卸设备。
1 输送带撕裂的分析导致输送带撕裂的原因主要有以下几种:(1)内置钢丝绳断裂。
由于输送带内置钢丝绳质量缺陷,导致局部抗拉强度较低,当输送带运转期间有大块物料或杂物冲击该位置时内置钢丝绳由于强度不足发生断裂。
一般难以第一时间发现,在继续使用的况下,断裂的钢丝绳可能穿透皮带并罗咯在皮带盖胶外。
当钢丝绳裸露长度较长时,可能在输送带运转过程中卷入托辊、滚筒,造成输送带大范围撕裂。
(2)尖锐物体凿穿输送带。
该情况是导致皮带撕裂的最常见原因。
主要是由于物料中的杂质从溜槽下落后凿穿输送带;或皮带机钢结构变形,导致尖锐部位伸出与输送带运行轨迹重合,划伤皮带。
(3)输送带跑偏。
正常情况下,输送带位于机架中轴部位。
当输送带发生跑偏时,输送带一侧发生堆叠或被托辊架划伤盖胶、划断内置钢丝绳,最终导致内置钢丝绳缠绕在拖轮或滚筒上,造成皮带大范围撕裂。
撕裂分为横向撕裂和纵向撕裂,横向撕裂多由于内置钢丝绳断裂、尖锐物体凿穿输送带等所致,由于钢丝带增加了输送带的抗拉强度,横向撕裂少有发生;纵向撕裂多是由于内置钢丝绳断裂、输送带跑偏、或尖锐物体凿穿输送带后未完全穿过输送带,后又被钢结构等所阻,随着输送带的不断运动持续撕裂输送带等所致。
浅议皮带纵向撕裂压力检测

浅议皮带纵向撕裂压力检测【摘要】在输煤系统中,输煤皮带纵向撕裂事故时有发生,一旦发生撕裂事故,在几分钟内就会全部毁坏,造成巨大的经济损失。
本文分析了皮带纵向撕裂的原因,阐述了皮带纵向撕裂检测原理,并探讨了防皮带纵向撕裂压力检测方法。
【关键词】输煤系统;输煤皮带;纵向撕裂1.皮带纵向撕裂的原因(1)皮带跑偏撕裂。
皮带运行过程中,皮带单侧偏移较多时,在一侧形成褶皱堆积或折叠,受到不均衡拉力或被夹伤及刮伤等,造成撕裂。
(2)抽芯撕裂(只发生于钢绳芯皮带)。
皮带在剧烈的冲击力作用下,有时会造成皮带中的钢丝绳断裂,经过长时间的磨、压、折、拉等外力作用,断裂的钢丝绳头会从皮带接头处、粘口处或磨损比较严重处露出盖胶之外。
(3)物料卡压堵塞撕裂。
这种情况发生在溜槽下部。
由于溜槽前沿和皮带面之间的距离有限,且皮带下缓冲托辊呈间隔分布,自然承载力强度不均匀。
当所运输的物料单侧长度超过这个距离时,在特殊的情况下容易使大块物料卡在溜槽前沿与皮带之间,强力挤压皮带造成撕裂。
(4)异物划伤。
这种损伤也是发生在溜槽下部,有两种情况。
一是长杆状利器压力性划伤。
二是利器穿透性划伤。
2.皮带纵向撕裂检测原理2.1皮带撕裂机理针对原因(1)(2),如果我们积极消除现场导致发生撕裂的各种隐患,并完善各方面设施,加强对操作及维修工人的安全教育,落实岗位责任制,就可以杜绝这方面撕裂事故的发生。
而原因(3)(4)一般情况下光靠人力很难杜绝,因为皮带撕裂时基本上没有明显的可视征兆,因此现在很多检测装置也就应运而生了。
2.2皮带纵向撕裂检测原理由上述分析可知,当皮带被异物卡压时,皮带需要一段时间才能造成撕裂,而当皮带被直接扎穿时,皮带就有可能直接造成撕裂。
针对前一种情况,当皮带被撕裂时,由于物料卡压,皮带带速降低的同时,被卡物料给皮带施加的压力会不断增大,且持续一定时间,直至皮带被扎穿,随后压力将会显著减小。
所以,可以通过监测皮带在落料口处所受向下压力的大小及变化情况来诊断皮带纵向撕裂事故。
有关矿用输送带纵向撕裂综合检测技术的研究

有关矿用输送带纵向撕裂综合检测技术的研究带式输送机是广泛应用于矿山井下巷道、矿井地面运输以及露天采矿选矿等生产中的一种设备,由于矿区工作环境相对复杂,加上输送机输送带运行过程中需要承受来自各个方面的外力,因此很容易因输送带跑偏、尖锐器物划伤等原因导致输送带撕裂,不仅给矿区各项业务的正常开展造成了不利影响,而且增加了工作人员的作业安全隐患。
因此,必须要深入分析输送带纵向撕裂的原因,并在此基础上探究撕裂问题的综合检测技术,确保矿用输送带的正常运行。
标签:矿用输送带;纵向撕裂;问题分析;检测技术带式输送机具有伸缩方便、机架轻巧、持续作业、运行可靠等优点,是煤矿作业中较为理想的运输设备之一。
近年来,通过不断的技术革新,矿用输送带的工作性能也有了进一步提升。
纵向撕裂是现阶段影响输送带运行效率的最常见问题之一,文章首先指出了导致输送带出现纵向撕裂问题的常见原因,随后结合国内外实际情况,对纵向撕裂检测技术的发展进行了概述,最后从实际工作经验出发,提出了优化检测技术的几点可行性措施。
1 矿用输送带的技术优势和设计要点1.1 技术优势第一,输送带的安装便捷,运行可靠。
在矿区生产过程中,为了尽可能的提升企业经济效益,往往需要长时间、流水性的进行运输作业。
矿用带式输送机的机架结构相对简单,安装流程非常方便,并且运行稳定性良好,可以适用于多数情况下的矿区矿物输送。
第二是带式输送机的动力消耗低,生产效率高。
带式输送机的主要动力来源于设备两端的滚筒,由于物料与输送带之间没有明显的相位移动,因此输送带运行过程中不会产生较大的运行阻力(运行阻力通常为物体最大静摩擦力的1/5)。
这种技术优势一方面能够减小矿物运输对输送带的磨损,延长了输送带的使用寿命;另一方面也降低了输送带运输所需的功率,起到了很好的节能效果[1]。
1.2 设计要点要想保证矿用输送带的使用效率最大化,必须要保证矿区作业环境的适宜性,总体来说,在进行矿用输送带设计时,需要考虑以下设计要点:首先,要考虑输送带每天的运转时间、服务年限和工作环境,通过营造良好的作业环境,最大限度的延长设备使用寿命;其次,要考虑输送带的运行速度、前后段的水平高度差以及连接尺寸等。
矿用输送带纵撕图像检测和纵撕故障识别方法

矿用输送带纵撕图像检测和纵撕故障识别方法针对矿用输送带运行过程中容易出现纵向撕裂的工程背景,计算纵向长度、横向宽度,计算长宽比等特征参数判定矿用输送带纵撕图像。
矿用输送带纵撕图像的纵向长度、横向宽度超过一定的阈值,自动识别判定发生了纵撕故障。
图像质量识别度高,检测准确,有效解决了解决矿用输送带纵撕图像检测和纵撕故障识别的问题。
标签:纵向撕裂;故障识别;图像质量1 引言输送带作为现代化大生产的重要运输设备已经广泛应用于我国的电力、化工、、港口、煤炭、矿山、冶金等领域。
由于矿用输送带在使用过程中经常出现纵向撕裂、断带等故障,从而造成设备损坏、材料损耗、人员伤亡、停产等事故严重制约了企业的安全生产。
所以非常有必要对输送带纵撕图像进行检测、识别出纵撕故障以保障输送带的运行安全。
对矿用输送带纵撕图像的检测,目前除人工检测外,研究者们还提出了激光发射器检测、差影法检测和面积法检测等方法。
目前应用的基于机器视觉的纵撕故障检测方法主要还是停留在实验室研究阶段距离广泛应用还有好长的一段路要走。
由于各个企业的现场具体应用条件千差万别,所以还没有统一、可靠的纵撕检测技术和方法,国内外在这个领域的研究还处于探索研究阶段。
魏涛等人提出的检测输送带裂纹的算法的数学形态学方法还处于试验研究阶段,无法广泛地应用现场实际。
2 输送带图像分割通常我们把具有相同性质的区域和有意义的部分从图像中提取出来称为图像分割。
这种方法通常是作为高层计算机视觉处理例如图像理解和图像识别等活动的基础来应用的。
它具有以下特点:(1)以明显差异的性质作为相邻区域分割的依据;(2)以相似性作为分割出来的各区域的某种特性(如灰度和纹理),必须保持内部的连通性并且没有过多的小孔作为区域的主要特征;(3)以明确的边界作为区域划分的标准。
作为计算机视觉、图像分析、图像理解研究的经典难题图像分割目前可以分为三大类型:即阈值分割、区域分割、边缘分割。
边缘分割首先探测局部不连续性,然后形成边界;基于区域的分割将具有同类属性的区域连接起来形成边界;而基于阈值的分割通过设置阈值来区分物体与背景。
带式输送机胶带撕裂检测技术综述

带式输送机胶带撕裂检测技术综述摘要:作为一种运输速度快、运输量大、运输距离长的运输设备,带式输送机广泛用于港口装卸煤炭、矿山运输矿石等大宗物料运输中。
作为带式输送机牵引和运载的关键部件,胶带主要由橡胶组成,为了提升胶带的耐磨能力和承载能力,生产胶带时会依据用途在其中贯穿不同材质的芯绳,如纤维芯、帆布芯或钢绳芯等。
其中,钢绳芯胶带横向抗拉强度及承载能力优异,能够显著提高胶带传输机的传送速度和传输距离,广泛应用于工业领域,但其纵向抗撕裂强度并未显著提高,纵向撕裂较易发生,一直是胶带面临的关键问题。
关键词:胶带;纵向撕裂;撕裂检测;机器视觉引言带式输送机是煤矿采掘工作面重要运输设备,具有结构简单、操作方便以及运输能力大、实用性强等优点,它主要通过滚筒与输送带摩擦提供动力源,带动环形输送带运动,达到运输物料的目的;在实际运行过程中若对带式输送机管理维护不当,很容易造成输送机故障,常见故障现象主要为输送机跑偏、撕带、电机烧毁、倒架等。
长距离带式输送机一旦出现故障后,易导致输送机运行稳定性失调,输送机运输效率降低,而且很可能出现伤人事故。
本文巷道前期掘进过程中带式输送机主要存在的问题进行分析,并根据掘进现状采取了若干项安全管理技术措施。
1运行状态智能监控体系结构根据输送机各部件的实际情况及异常分析,本文所提出的运行状态智能监控系统主要是以非接触式检测为核心,以不影响输送机系统的正常运行为基础,采用了模块化的结构设计原则,实现对输送机运行时的输送带损伤检测、关键部件故障检测与预警、煤量监测及人员安全监测等。
该系统主要包括五个部分,分别用于对输送机钢丝绳芯及输送带的损伤检测、托辊及滚筒故障监测、输送机煤流运行状态监测等。
2胶带撕裂原因分析及特征表现胶带纵向撕裂发生的原因主要包括胶带跑偏、抽芯、异物划伤和物料卡压等。
1)胶带上运输的物料分布不均匀或者电机施力不均衡,会使得胶带向运输机一侧偏移,长时间的胶带跑偏,会导致一侧出现严重损耗,受力不均衡,从而导致胶带撕裂,其撕裂部位通常在胶带的边缘。
输送带纵向撕裂检测方法之一
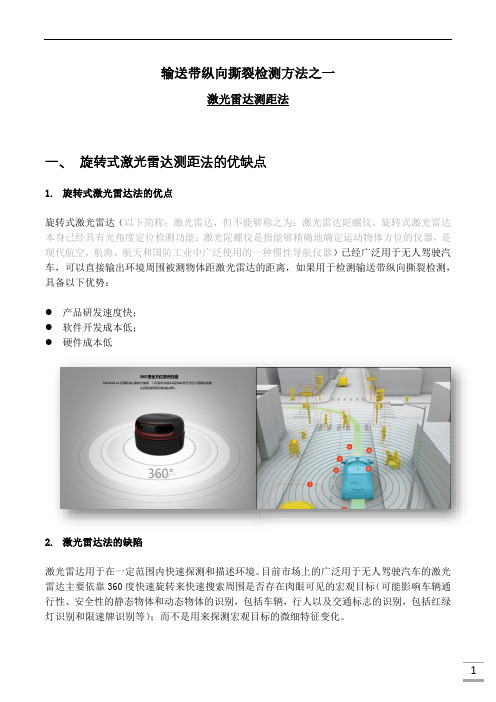
输送带纵向撕裂检测方法之一激光雷达测距法一、旋转式激光雷达测距法的优缺点1.旋转式激光雷达法的优点旋转式激光雷达(以下简称:激光雷达,但不能够称之为:激光雷达陀螺仪。
旋转式激光雷达本身已经具有光角度定位检测功能;激光陀螺仪是指能够精确地确定运动物体方位的仪器,是现代航空,航海,航天和国防工业中广泛使用的一种惯性导航仪器)已经广泛用于无人驾驶汽车,可以直接输出环境周围被测物体距激光雷达的距离,如果用于检测输送带纵向撕裂检测,具备以下优势:●产品研发速度快;●软件开发成本低;●硬件成本低2.激光雷达法的缺陷激光雷达用于在一定范围内快速探测和描述环境。
目前市场上的广泛用于无人驾驶汽车的激光雷达主要依靠360度快速旋转来快速搜索周围是否存在肉眼可见的宏观目标(可能影响车辆通行性、安全性的静态物体和动态物体的识别,包括车辆,行人以及交通标志的识别,包括红绿灯识别和限速牌识别等);而不是用来探测宏观目标的微细特征变化。
下图为世界领先的Velodyne公司的激光雷达产品及主要参数。
因此使用激光雷达来探测输送带撕裂产生的细微裂缝时,就存在许多缺陷:1)探测精度严重不足激光雷达产品参数包括四方面:测量距离、测量精度、角度分辨率以及激光单点发射的速度,使用激光雷达来探测输送带撕裂主要涉及:纵向分辨率和横向分辨率。
目前国内激光雷达厂商的产品如果应用于一条1200mm 宽的输送带上,横向分辨率≥2mm, 纵向分辨率≥200mm,无法探测出宽度细达1mm的输送带撕裂裂缝。
2)无法消除输送带抖动的影响激光雷达每次只能检测一个点,依靠其高速旋转来实现对360度范围内物体的检测。
运动的输送带无时无刻不在抖动(从毫米级/厘米级角度);激光雷达从输送带一端扫描到另一端的时间内,输送带横向上千个点的抖动方向、幅度不可能完全一致,这样就造成至少几毫米的误差,无法精确地探测出各点的距离。
3)无法消除输送带跑偏的影响运动的输送带无时无刻不在跑偏(从毫米级/厘米级角度);激光雷达从输送带一端扫描到另一端的时间内,输送带横向上千个点的位置都在不停变化中,无法精确定位各点。
基于红外热成像技术的输送带纵向撕裂检测方法

1 输 送 带 纵 向撕 裂 原 因
1) 异物 穿卡 异 物穿 卡是 纵 向 撕 裂 事 故 最 常 见 的 原 因 ,多 发 生于 卸 料 点 溜 槽 下 部 。物 料 输 送 过 程 中 ,混 入 有 尖锐棱 角 的物体 (如槽 钢 、角 钢 、矸 石 等 ),或 大块物料 卡在输送带与结构件之 间,导致输送带 被划 伤穿 透 。 2)抽 芯撕 裂 钢丝绳芯带 由于疲 劳磨损 ,折断钢 丝绳芯从 橡胶 层 中伸 出后 被 抽 出来 而 导 致 撕 带 ,多 发 生 在 硫化接头处。 目前主要靠人员重点检查硫化接头 ,
ging technology,the paper puts forward a new monitoring method,better providing in-time and accurate for m ation. Keywords:belt conveyer;longitudinal tear;infra red ther m al imag ing
输 送 带跑 偏 达 到 一定 程 度 时可 能 被 托 辊 或 机 架 的棱 角 割 开 ,造 成 撕 带 。此 类 撕 带 事 故 可 能 发 生在 输送 机任 何 一个 位 置 ,具 有 缓 慢 性 和 长期 性 ,
的温 度相 关 。红 外 热 像 仪 利 用 红 外 探 测 器 和 光 学 成像 物镜 ,接 受 被 测 目标 的红 外 辐 射 能 量 分 布 图 形 ,反 映到 红 外 探 测 器 的光 敏 元 件 上 ,获 得 与 物
通 过 图 5可 以看 出 ,在 追 踪 的数 据 中 IB1 1022 (应急链 条 限位 ) 的状 态 在故 障 时发 生 变化 。找 到 这 个开 关 后 ,发 现 该 感 应 式 限 位 开 关 由于 固定 基 座脱落 ,当起 升 机 构 动 作 时 由 于振 动 ,使 限位 器 左右摇晃 ,导致其感应 到周 围的金属 物体 ,瞬间 误 动作 ,从 而造 成起 升机 构急停 。
基于声音的带式输送机输送带纵向撕裂检测方法

在现代化工业生产中,带式输送机在产品运输方面扮演着不可或缺的角色,具有负载量大、运输距离远、性价比高的优势,已被广泛应用于工矿、运输等领域[1-2]。
作为带式输送机的核心部件,输送带承担着运载产品的关键性任务。
在使用过程中,输送带可能会遭受到煤矸石或废钢铁等异物的冲击,亦或者物料运输造成的压力不均,致使输送带长期处于恶劣环境下,纵向撕裂时有发生。
若在纵向撕裂发生时没有得到及时的反馈和处理,会为企业的生产留下巨大的安全隐患,增加发生重大安全事故的风险,不仅危害了企业生产效益,更严重时甚至会威胁到人员的生命安全[3-4]。
输送带纵向撕裂的主要检测方法是通过压力、电磁、激光、红外温度等传感器检测输送带的物料泄露和钢丝绳或橡胶脱落等状态[5],判断纵向撕裂故障,其基于声音的带式输送机输送带纵向撕裂检测方法苗长云,邵琦(天津工业大学电子与信息工程学院,天津300387)摘要:针对带式输送机输送带的纵向撕裂检测存在准确性差等难题,提出了一种基于声音的带式输送机输送带纵向撕裂检测方法。
采用树莓派3B 开发板设计带式输送机声音采集系统以采集声音信号,对声音信号进行预处理,提取梅尔频率倒谱系数和短时能量参数,再经过高斯混合模型(GMM )进行均值估计,形成特征数据作为支持向量机(SVM )的输入进行分类和识别,实现带式输送机的输送带纵向撕裂检测。
实验结果表明:该方法实现了带式输送机声音信号的实时采集、处理、分类与输送带纵向撕裂声音的检测,平均检测准确率达到91.5%,平均耗时2.85s ,解决了输送带纵向撕裂检测精度低、实时性差等问题,满足了输送带纵向撕裂检测的要求。
关键词:带式输送机;纵向撕裂检测;声音信号;高斯混合模型;支持向量机中图分类号:TP216文献标志码:A 文章编号:员远苑员原园圆源载(圆园21)园6原园园70原06收稿日期:2020-11-04基金项目:天津市科技支撑重点资助项目(18YFZCGX00930);天津市成果转化接力支持重点研发计划资助项目(18YFJLCG00060)通信作者:苗长云(1962—),男,教授,博士生导师,主要研究方向为通信技术及系统。
- 1、下载文档前请自行甄别文档内容的完整性,平台不提供额外的编辑、内容补充、找答案等附加服务。
- 2、"仅部分预览"的文档,不可在线预览部分如存在完整性等问题,可反馈申请退款(可完整预览的文档不适用该条件!)。
- 3、如文档侵犯您的权益,请联系客服反馈,我们会尽快为您处理(人工客服工作时间:9:00-18:30)。
激光雷达每次只能检测一个点,依靠其高速旋转来实现对360度范围内物体的检测。运动的输 送带无时无刻不在抖动(从亳米级/厘米级角度);激光雷达从输送带一端扫描到另一端的时间 内,输送带横向上千个点的抖动方向、幅度不可能完全一致,这样就造成至少儿毫米的误差, 无法精确地探测出各点的距离。
•软件开发成本低;
•硬件成本低
2.激光雷达法的缺陷
激光雷达用于在一定范围内快速探测和描述环境。U前市场上的广泛用于无人驾驶汽车的激光 雷达主要依靠360度快速旋转来快速搜索周围是否存在肉眼可见的宏观LI标(可能影响车辆通 行性、安全性的静态物体和动态物体的识别,包括车辆,行人以及交通标志的识别,包括红绿 灯识别和限速牌识别等);而不是用来探测宏观目标的微细特征变化。
5)无法长年7天24小时连续运行
没有一种汽车设计用来7天24小时长年连续行驶,激光雷达也不能7天24小时长年连续360 度高速运转。
3)无法消除输送带跑偏的影响
运动的输送带无时无刻不在跑偏(从毫米级/厘米级角度);激光雷达从输送带一端扫描到另一 端的时间内,输送带横向上千个点的位置都在不停变化中,无法精确定位各点。
4)激光强度低,无法保证在高风尘、高泥灰环境内正常工作
激光雷达设计用来扫描人体,功率很小,无法在矿山高风尘、高泥灰环境内正常工作。激光线 可能变得非常弱,无法完成基本检测功能。
1)探测精度严重不足
激光雷达产品参数包括四方面:测量距离、测量精度、角度分辨率以及激光单点发射的速度, 使用激光雷达来探测输送带撕裂主要涉及:纵向分辨率和横向分辨率。
目前国内激光雷达厂商的产品如果应用于一条1200mm宽的输送带上,横向分辨率$2mm,纵 向分辨率$200mm,无法探测出宽度细达1mm的输送带撕裂裂缝。
104mm x 72mm
13.2KG
1.3KG
0.83KG/0.53KG
0.8KG~L3KG
漱光波长
905nm
905nm
9O5nm
905nm
水平视野
360°
360°
360°
360*
垂宜视野
26.8e(令2。一24.6。)
41.34・
(•10・677・30・67。)
30・ (+15•—15°)
28・
距离精度
下图为世界领先的Velodyne公司的激光雷达产品及主要参数。
Velodyrw
■价
50-100万
10・30万元
7999美元
500美元的目标价格(大规横H产)
特点
性能佳,价瞬
体积更小,更轻
适用于无人机
汽车专用
漱光器数
64
32
16
32
尺寸
203mm x 284mm
86mmx 145mm
104 mmx 72mm
<2cm
、w
<2cm
<3cm
<2cm5HzΒιβλιοθήκη 0.08°5HeO.O8°
5Hz 0.1°
水平分辨率
10Hz0.17°
10Hz0.17a
10Hz 0.2°
20Hz 0.35°
20Hz: 0.35。
20Hz0.4°
垂直分辨率
0.4°
1.33°
2.0°
IP67
ff>67
IP67
IP67
因此使用激光雷达来探测输送带撕裂产生的细微裂缝时,就存在许多缺陷:
输送带纵向撕裂检测方法之一
激光雷达测距法
一、旋转式激光雷达测距法的优缺点
1.旋转式激光雷达法的优点
旋转式激光雷达(以下简称:激比宙达,但不能够称之为:激光雷达陀螺仪。旋转式激光需达 本身已经具有光角度定位检测功能:激光陀螺仪是指能够精确地确定运动物体方位的仪器,是 现代航空,航海,航夭和国防I〕业中广泛使用的--种惯性导航仁)已经广泛用于无人驾驶汽 车,可以直接输岀环境周圉被测物体距激光雷达的距离,如果用于检测输送带纵向撕裂检测, 具备以下优势:•产品研发速度快;