轧机液压压下系统分析
轧机液压AGC系统液压故障分析与诊断

轧机液压AGC系统液压故障分析与诊断作者:王勇来源:《城市建设理论研究》2014年第07期摘要:本文叙述了轧机液压AGC液压系统,对其产生的故障采用的故障树分析方法进行故障分析,能较快的确定故障点,便于及时进行处理。
关键词:热连轧机;液压弯辊;故障;分析;诊断中图分类号:TG332文献标识码: A引言:新型轧机系统是机、电、液、气、仪一体化的大型复杂系统,其结构与功能的复杂性决定了故障机理的复杂性以及故障诊断的困难度。
轧机系统高精度与高可靠性要求使故障诊断任务更加艰巨。
本文主要是概括轧机控制系统中AGC系统的常见故障,整理故障分析的基本思路与程序、列出故障树,并总结出故障症状与原因的关系。
同时,也对轧机液压控制故障与产品质量的关系进行分析。
1、液压压下及AGC故障概述液压压下装置用于作为针对轧制力变化实施厚度调节系统的一种快速精确调节定位系统。
1.1功能投入的条件AGC由液压伺服位置系统实现,通过伺服阀调节保持中心点恒定。
每台轧机由两个压下缸,分别位于操作侧和驱动侧;每个压下缸有两个位置传感器,分别位于入口侧和驱动侧,压下缸的位置是两传感器位置值的平均值。
伺服阀的前后各用一个止回阀,止回阀在调节器正常工作时处于开通状态。
当调节器处于断开,由于伺服阀不能保证完全密封,这时止回阀起作用,关闭油路,短时间维持油缸里的压力不变。
当功能断开时,压下系统的卸荷阀起作用,液压缸回程,把油路的油排回油箱。
液压压下功能的投入与控制系统许多参量有关,必须同时满足以下条件:已通过“工作方式”、“手动”或“电磁阀控制”等选项将功能选定;油源供油正常;阀控制系统正常(软硬件正常,调节钥匙不在手动状态);位置传感器正常,即两侧位置无偏差;油缸位置正常;CPU正常无故障,系统电源、控制柜不在测试状态。
液压系统不在紧急停止状态。
1.2 AGC系统主要故障AGC主要故障有:(1)传感器故障,包括位置、油缸油压、轧制力传感器故障。
冷轧机压下率分配分析

冷轧工艺措施原则1.头几道次尽量多轧,充分利用材料的塑性,并削减头尾几何废料长度,提高成品率;2.最终道次压延率掌握在40~50%范围内,以提高板形质量和厚度精度;3.中间道次压延率尽可能接近,以提高轧制过程的稳定,并承受最大速度轧制,使板卷温度在90~120℃之间,满足轧制硬合金辊形的需要;4.末二道次压延率掌握在40%左右,以掌握板形为主,为终道次供给平直的带材,从而提高终轧道次的速度,以削减断带和波浪;5.通过理论计算,最大轧制力不超过额定轧制力,以满足轧辊强度的需要,但各道次尽量承受大压下量轧制,削减轧制道次,提高劳动生产率;6.前几道次轧制时,由于板带较厚,承受前张力大于后张力轧制,后几道次轧制时,由于板带较薄,承受后张力大于前张力轧制,带材不易拉断,并防止跑偏。
冷轧板带生产(cold rolling of strip and sheet)将热轧板卷在常温下轧制成板带材的生产工艺过程。
冷轧板带产品的厚度为 0.1~3.0mm、宽度为 600~2023mm 外表光滑、平直,尺寸公差和力学性能应符合有关标准规定的要求。
在工业兴旺国家,冷轧板带钢产量占钢材总产量的30%左右。
产品品种有各种有色金属合金板带及一般碳素钢板、合金和低合金钢板、不锈钢板、电工钢板、专用钢板及涂镀层钢板等(表 1)。
冷轧板生产可以追溯到 16 世纪,用于轧制造币用的金板和银板。
19 世纪中叶仅能生产宽度 20~50mm 的冷轧窄带钢。
1920 年在美国第一次冷轧宽带钢成功,很快由单机架不行逆式轧机进展到单机架可逆式轧机。
第一套三机架四辊式冷轧机于 1926 年在美国建成,以后相继消灭 4~6 机架连轧机。
中国冷轧窄带钢(宽度≤600mm)生产始于 20 世纪 40 年月连续冷轧窄带钢的五机架 350 冷连轧机已在上海建成。
冷轧宽带钢(宽度>600mm)生产是从 50 年月末期建成第一台单机架四辊可逆式轧机时开头的。
厚板主轧机液压AGC控制系统浅析
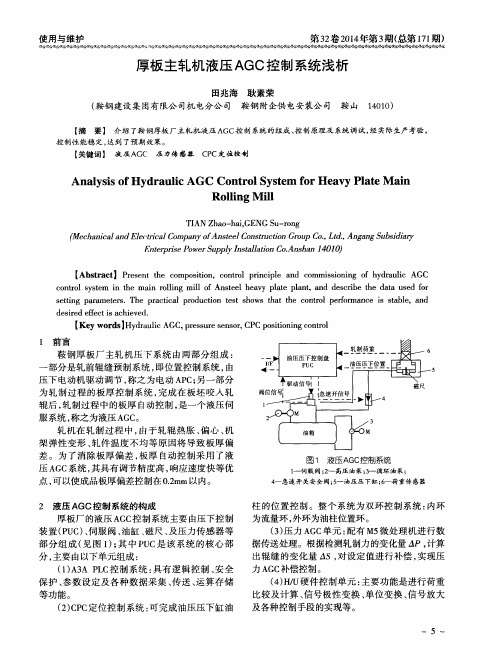
【 A b s t r a c t 】P r e s e n t t h e c o m p o s i t i o n , c o n t r o l p r i n c i p l e a n d c o m m i s s i o n i n g o f h y d r a u l i c A G C
c o n t r o l s y s t e m i n t h e ma i n r o l l i n g mi l l o f An s t e e l h e a v y p l a t e p l a n t ,a n d d e s c r i b e t h e d a t a u s e d f o r s e t t i n g p a r a me t e r s .T h e p r a c t i c a l p r o d u c t i o n t e s t s h o ws t h a t t h e c o n t r o l p e r f o r ma n c e i s s t a b l e ,a n d
控制 性能稳定 , 达 到 了预 期 效 果 。
【 关键词 】 液压A G C 压 力传感器
An a l y s i s o f Hy d r a u l i c AGC Co n t r o l S y s t e m f o r He a v y P l a t e Ma i n
使用与维护
第3 2 卷2 0 1 4 年第 3 期( 总第 1 7 1 期)
厚板 主轧机 液压 A GC控 制 系统浅 析
田兆海 耿 紊 ( 鞍钢建设集团有限公 司机 电分公 司 鞍钢 附企供电安装公司 鞍山 1 4 0 1 0 )
轧机液压自动厚度控制系统要素和构成分析
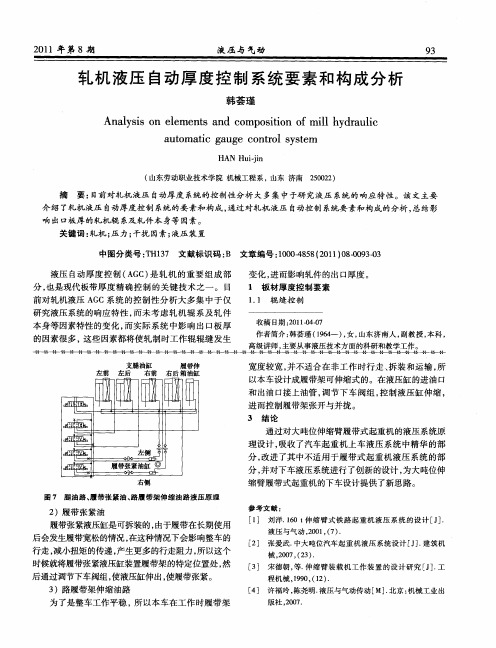
液压与 气动
9 3
轧机 液 压 自动厚 度控 制 系统 要 素 和构 成 分 析
韩荟瑾
An lsso lme t n o o i o fmi y ru i ay i n ee n sa d c mp st n o l h d a l i l c
a t mai a g o to y t m u o tc g u e c n r ls se
1 板 材厚 度控 制 要素
1 1 辊 缝 控 制 . 收稿 日期 :0 10 - 21- 0 47
分, 也是现代板带厚度精 确控制 的关键技术之一。 目 前对轧机液压 A C系统的控制性分析大多集 中于仅 G 研 究 液压 系统 的响 应 特性 , 未 考 虑轧 机 辊 系及 轧 件 而 本身等因素特性 的变化 , 而实际系统 中影 响出 口板厚 的因素很多 , 这些因素都将使轧制时工作辊辊缝发生
I6 秒 流 量 控 制 .
21 0 1年第 8期
辊缝控制是 A C控制的基本内环 , G 它与其他 A C G 模式一起发挥控制作用。辊缝位置的检测有若干种选 择方式及其检测元器件的安装位置 , 位移传感 器可安 装在轧机液压缸上 、 轧机弯辊液压缸 内或专门设计 的 检测支座上 , 还可以将位移传感器安装于缸体中间 , 不
量 和压 力 的调节来 控 制 液压 缸 上 、 移 动 的行 程 来 调 下 节轧辊 辊缝 值 。
压 力控 制是 A C控 制 的第二 个基 本 内环 , G 它也 需 与其他 A C模式一起发挥其控制作用 。具体安装位 G 置在 液压 缸 阀组上 , 压力 传感 器检 测液 压缸 内的压 力 , 经 转 换得 到轧 机轧 制力 反 馈 信 号 , 个 信 号 和压 力 给 这
轧机液压压下故障分析
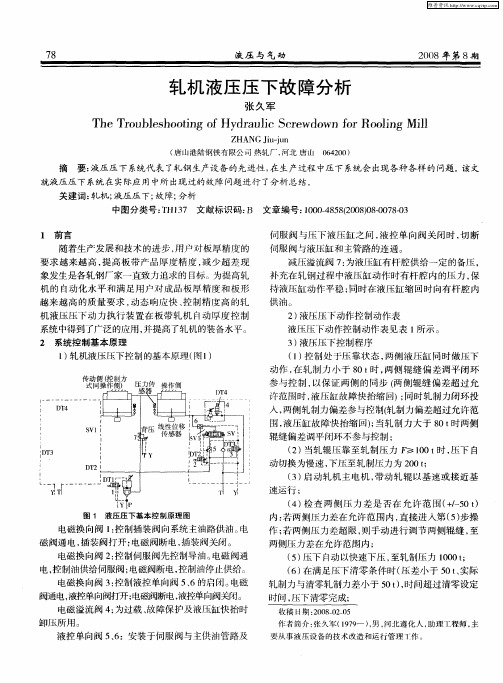
围, 液压缸故障快抬缩 回)当轧制力大于 8 时两侧 ; 0t 辊缝 偏 差调平 闭环 不参 与控 制 ; () 2 当轧 辊 压靠 至轧 制 压力 F 0 时 , 下 自 ≥10t 压 动切换 为慢 速 , 下压 至轧 制压 力 为 2 0t 0 ;
( ) 动 轧 机 主 电机 , 动 轧 辊 以基 速 或 接 近基 3启 带
轧制状态
换辊状 态 事故( ) 态 快抬 状
●
I
j I
+
+ +
+
+ +
+
系统中得到了广泛的应用, 并提高了轧机的装备水平。
2 系统 控制基 本 原理
1 轧机 液压 压下 控制 的基 本原 理 ( 1 ) 图 )
( ) 制 处 于压 靠 状 态 , 1控 两侧 液 压缸 同时 做 压下 动 作 , 轧制 力 小 于 8 时 , 侧 辊 缝 偏 差 调 平 闭环 在 0t 两 参 与控 制 , 以保证 两侧 的 同步 ( 侧 辊缝 偏 差超 过 允 两 许范 围时 , 压 缸故 障快 抬 缩 回) 同B  ̄N 力 闭环 投 液 ;  ̄L 入, 两侧 轧制 力偏 差参 与控 制(L 力 偏差超 过 允许 范 车制
液控单向阀 5 6 、 :安装于伺服阀与主供油管路及
维普资讯
20 0 8年第 8 期
液压 与 气 动
表 1 液 压 压 下 动 作 控 制 动 作 表
7 9
压下控制程序
动作 状态 受 控状态 待机状 态 压靠 ( 清零) 状态
伺服阀 S V
收 稿 日期 :0 80 —5 20 —20 作者简介 : 张久 军 ( 9 9 )男 , 北 遵 化 人 , 理 工程 师 , 1 7一 , 河 助 主 要 从 事 液 压 设 备 的技 术 改造 和运 行 管 理 ] 作 。
轧机液压AGC系统液压故障分析与诊断
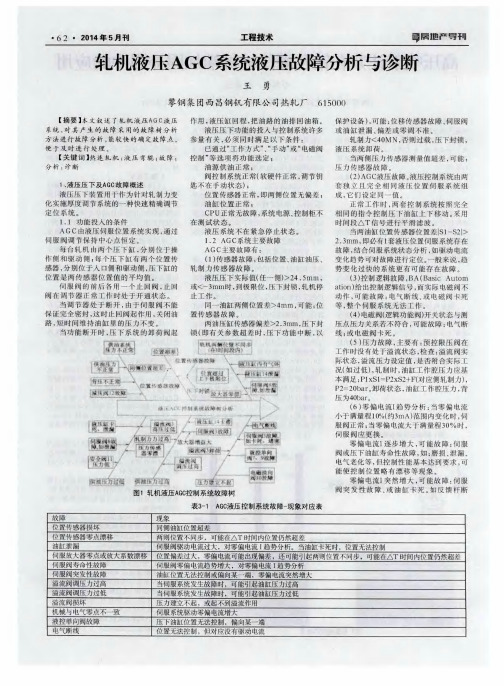
及液压缸工作压力不正常 , 液压 缸的工作
压 力 油 可能 过 高 、 国 低或 根 本 无压 力 , 导致 这 些 现象 的 原 因有 机 械方 面 的如 液压 缸卡 死、 泄 漏 以及 伺 服 阀或 溢 流 阀有 故 障 ; 电气 方 面 的有 压 力传 感 器故 障 、 线路 传 输故 障 、 P L C等 控 制故 障 。 位置 故 障有 液 压缸 位 置 超 差 和 两 个 液 压 缸 位 置 不 同步 , 导致 这 些 故 障 的原 因 与前 面 分析 的压 力故 障的 原 因 相类似。 故 障树 分 析 方 法 比较 直 观 了解 故 障原 因, 有 利 于 及 时处 理 。 3 、 A G C 液 压控 制 系统 故 障归 类 AG C 液压 控 制位 置 系统 是精 轧 机组 液 压控制系统的核心 , 故 障 引起 最 终特 征 量 表 现 以下几 个 方 面 : 第一 , 位 置控 制精 度 达 不到要求 , 如 某 一 位 置 传 感 器 测 量 值 大 于 极 限位 , 或 同一压 下 油 缸位 置 值超 差 , 或 两 压 下油 缸 位 置在 △T时 间 内超差 ; 第二, 压 下 油 缸 压 力 过 高 /过 低 , 或 压 力 建 立 不 起 来; 第三 , 伺 服 阀 驱动 零 偏 电 流大 于正 常 范 围, 第四, 压 下油 缸偏 向一 端 , 或 不受 控 。 其 归类 如 表3 —1 与表 3 -2 所示。
4、 结 语
伺服 阀零偏 电流逐渐增大 伺服 阀零偏 电流突然增大 压 下缸位置不受控
裂、 力矩马达卡滞 、 小球脱落 、 节 流 孔 堵 塞 等, 将使伺服系统失控 。 可根 据 电 流I 、 油 缸压 力 P、 伺 服 阀B腔 压力 、 油缸 位置 s等 参量 进 行 故 障定 位 。 其 特征 : 驱 动 电流 I 突 然增 大 ( 幅度 很 大) ; 油 缸 位 置 偏 向一 端 无 法 控 制 。 伺 服 阀 控 制 电流 I 变化 , 而 B腔 压 力 不
轧机插装阀液压平衡系统的分析与应用

4 单 向阀 .
5 减压 阀 .
6 液压泵 .
7 过 滤 器 .
节流 阀 4调 节平 衡缸 的升 降 速 度 , 样 P至 A 间便 形 这
收 稿 日期 :020 —5 20—71 作 者 简 介 : 永 昌 (9 l ) 男 , 龙 江 省 齐 齐 哈 尔 市 人 , 王 15一 , 黑
W a g Yo g c a g , e g B if g n n —h n M n e —a 2 n
,
Wa gZ i og ,h gQ—hn n h- n Z a i eg y n s
110 ) 600
(. 山大学机 械工程学 院, 北 省秦皇岛市 1燕 河
06( 2 中 国 第 一 重 型 机 械 集 团 , 龙 江 省 齐 齐 哈 尔 市 6o o; . 黑
成连 通 器 的主 要 元 件 是 电液 换 向 阀 1 单 向 阀 3和 节 、
流阀 4 。在 轧 机 工 作 过 程 中 , 液换 向 阀 1处 于 图 示 电 位 置 , 控单 向 阀 3靠换 向 阀 2的供 油 处 于开 启 状 态 , 液
I 半衡液压缸 . 2 活 塞 式 蓄能 器 . 3 溢 流 阀 .
维普资讯
20 02年 第 l O期
液 压 与 气动
3 5
轧机 插装 阀液 压平衡 系统 的分析 与应 用
王 永 昌 孟 北 方 王 智 勇 张 齐 生 , , ,
An l ss a d Ap lc to f Ca ti g l e i d a l l n e S se o ls a y i n p ia i n o rrd e Vav n Hy r u i Ba a c y t m f Rol c
新型轧机液压压下系统的研究
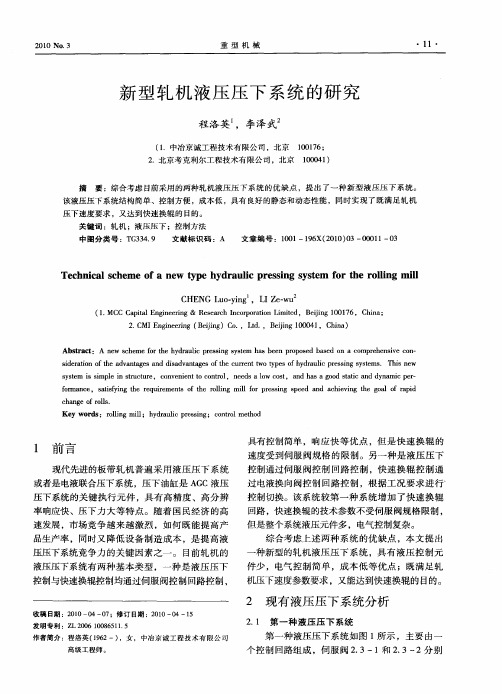
摘
要 :综合考虑 目前采用 的两种轧机液压压 下系统 的优 缺点 ,提 出 了一种新 型液 压压 下系统 。
该液压压下系统结构简单 、控制方便 ,成本低 ,具有 良好 的静态 和动态性 能 ,同时实现 了既满足轧 机 压下速度要求 ,又达到快速换辊 的 目的。
关 键 词 :轧 机 ;液 压压 下 ;控 制 方 法 中图 分 类 号 :T 3 49 G 3. 文 献标 识 码 :A 文 章 编 号 :10 —1 6 2 1 ) 3— 0 1 0 0 1 9 X( 00 0 00 1— 3
1 前 言
现代先进 的板 带 轧机 普遍 采 用液 压 压下 系 统
或者是 电液联 合压下 系统 ,压下 油缸 是 A C液压 G 压下系统 的关 键执 行元 件 ,具 有高 精度 、高 分辨 率响应快 、压 下力 大 等特 点 。随着 国民 经济 的高 速发展 ,市场 竞争 越 来越 激烈 ,如 何 既 能提 高产
A b tac : A e s h me f rt d a lc pr sn yse h sbe n pr p s d b s d o o sr t n w c e o hehy r u i esi g s tm a e o o e a e n a c mpr h n ie c n e e sv o —
Te h i a c m e o e y e h dr u i r s i y t m o he r l n il c n c ls he fa n w t p y a lc p e sng s s e f r t o l g m l i
CH ENG o y n , LIZe WU Lu . i g .
s se i i p e i tu t e, c n e intt o to , n e o c s , a d h o d sai nd d na i e - y tm s sm l n sr cur o v ne o c n rl e dsal w o t n asag o ttc a y m c p r fr nc o ma e, s tsy n e e ie e t o h o ln i fr pr si g p e a d c e i g t e o l f r pi aifi g t rqu rm ns f te r li g m l o e sn s e d n a hiv n g a o a d h h c a g frls h n e o o l. Ke y wor ds: r lig m i ; h drulc p e sn oln l l y a i r s ig; co r lmeh d nto to
轧钢机下压机构设计 正文
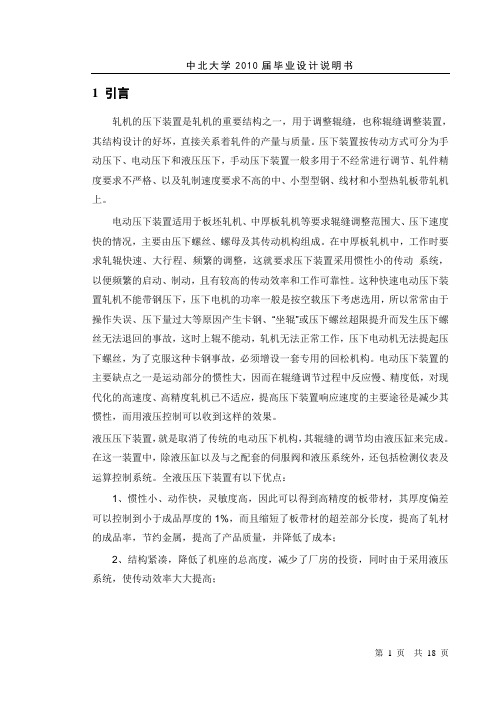
1 引言轧机的压下装置是轧机的重要结构之一,用于调整辊缝,也称辊缝调整装置,其结构设计的好坏,直接关系着轧件的产量与质量。
压下装置按传动方式可分为手动压下、电动压下和液压压下,手动压下装置一般多用于不经常进行调节、轧件精度要求不严格、以及轧制速度要求不高的中、小型型钢、线材和小型热轧板带轧机上。
电动压下装置适用于板坯轧机、中厚板轧机等要求辊缝调整范围大、压下速度快的情况,主要由压下螺丝、螺母及其传动机构组成。
在中厚板轧机中,工作时要求轧辊快速、大行程、频繁的调整,这就要求压下装置采用惯性小的传动系统,以便频繁的启动、制动,且有较高的传动效率和工作可靠性。
这种快速电动压下装置轧机不能带钢压下,压下电机的功率一般是按空载压下考虑选用,所以常常由于操作失误、压下量过大等原因产生卡钢、“坐辊”或压下螺丝超限提升而发生压下螺丝无法退回的事故,这时上辊不能动,轧机无法正常工作,压下电动机无法提起压下螺丝,为了克服这种卡钢事故,必须增设一套专用的回松机构。
电动压下装置的主要缺点之一是运动部分的惯性大,因而在辊缝调节过程中反应慢、精度低,对现代化的高速度、高精度轧机已不适应,提高压下装置响应速度的主要途径是减少其惯性,而用液压控制可以收到这样的效果。
液压压下装置,就是取消了传统的电动压下机构,其辊缝的调节均由液压缸来完成。
在这一装置中,除液压缸以及与之配套的伺服阀和液压系统外,还包括检测仪表及运算控制系统。
全液压压下装置有以下优点:1、惯性小、动作快,灵敏度高,因此可以得到高精度的板带材,其厚度偏差可以控制到小于成品厚度的1%,而且缩短了板带材的超差部分长度,提高了轧材的成品率,节约金属,提高了产品质量,并降低了成本;2、结构紧凑,降低了机座的总高度,减少了厂房的投资,同时由于采用液压系统,使传动效率大大提高;3、采用液压系统可以使卡钢迅速脱开,这样有利于处理卡钢事故,避免了轧件对轧辊的刮伤、烧伤,再启动时为空载启动,降低了主电机启动电流,并有利于油膜轴承工作;4、可以实现轧辊迅速提升,便于快速换辊,提高了轧机的有效作业率,增加了轧机的产量。
轧机的液压压下装置

轧机的液压压下装置轧机的液压压下装置是轧机的重要部件之一,它主要用于轧机在工作过程中对板材进行压下作用。
液压压下装置的设计和性能对轧机的工作效率、产品质量和设备寿命有着重要的影响。
一、液压压下装置的主要功能液压压下装置是轧机的重要部件,主要功能有以下几点:1. 对轧机辊缝中的板材进行压下,保证板材在轧制过程中不会产生变形或者变形较小,从而提高产品的成形精度和表面质量。
2. 通过调整液压压下装置的压下力,可以调节轧机的压下量,满足不同板材的轧制需要。
3. 调整液压压下装置的工作方式和参数,可以适应不同的轧制工艺和板材材质,提高轧机的生产适应性和生产效率。
二、液压压下装置的结构和工作原理液压压下装置通常由液压缸、油缸、阀门、油泵以及压力传感器等部件组成。
其结构如图所示,通过控制阀门的调节,液压系统可以实现对液压缸的压力调节,从而实现对板材的压下作用。
液压压下装置的工作原理如下:当轧机开始工作时,液压系统通过油泵将液压油送入油缸中,使得油缸内的液压缸得以推动,从而对板材进行压下作用。
通过调节液压系统中的阀门,可以控制液压缸的工作压力和压下力的大小,满足不同板材的轧制需要。
通过压力传感器可以实时监测液压系统的工作压力,从而保证轧机的安全运行。
三、液压压下装置的优点液压压下装置相对于机械式压下装置具有以下几个优点:1. 调节性好:液压系统通过调节阀门可以实现对压下力的精确控制,且调节范围大,能够满足不同板材的轧制需求。
2. 压力稳定:液压系统具有压力稳定的特点,能够保证压下力的稳定输出,从而保证产品的成形精度和表面质量。
3. 响应速度快:液压系统的响应速度快,能够满足轧机在工作过程中对压下力的快速调节需求,提高轧机的生产效率。
4. 可靠性好:液压系统的工作过程相对平稳,不易发生振动和冲击,能够保证轧机的稳定运行,延长设备的使用寿命。
四、液压压下装置的应用现状及发展趋势目前,液压压下装置已经在轧机中得到了广泛应用,在改进轧机的生产效率、产品质量和设备可靠性等方面发挥了重要作用。
中板轧机液压AGC系统故障分析及处理

的重要 手段。 虽然 中板轧机液压 A GC 系统 自投入使 用以来控制精度 以及可使 用性能都是较稳 定的,但 是仍然存在一 些问题 。文章将针 对 中板 轧 机 液 压 A GC 系统 运 行 中的 故 障原 因 , 提 出一 些判 断和 处理 系统故障的对策 ,希望对 系统运行维护有一 定的帮助 。
3 结 语
主 :检 测 系 统 包 括用 来 补 偿 位 置 闭 环 和 压 力 闭环 控 制 、 保 护 系 统 运
行的压力传感器 ,对 液压 缸进行动态和静态 位移 测量的位移传感器 和辊缝测量仪 2 中板 轧机液压 A G C 系统的故障分析及处理对 策 液压 A G C系统在运行过程 中,由于受到环境、谐波干扰等方面 的影响 ,容 易引起钢 板厚度的波动 ,不利于钢板 厚度 精度的控制, 严重的话甚至会 导致 设备出现故障从而使生产活动 中断,不仅 会影 响钢材成材率和产 品质 量,还会在一定程度上增加维修 成本和生产 成本,因此 ,必须对 故障出现的原因进行分析 ,找 出正确 的处理对 策 ,为系统的稳定、可靠运行提供保 障。 2 . 1伺服 阀 中板轧机液压 A G C系统 为高压 、大流量 的伺 服控制系统,流量 具有非线性特征 ,当控制 系统 向伺 服阀输送信号时 ,若信 号为正电 流 ,液压缸就会呈现进油状态 ,系统运行正常 ,而当信 号为负电流 时 ,液压缸就会呈现漏油状态 ,正是 由于伺服 阀状态不 同,造 成了 液压缸呈现上升或 下降的波 动,通常将输入信号控制在一 4 5 一+ 4 5 I I 1 A 以实现对伺服阀开 口度 的控制 ,对 辊缝厚度实施随机控制 。伺 服阀 的常见故障主要有零偏 电流变 大、卡死、磨损、密封破坏 、动态 响 应变慢等,导致系统失去控制 功能或控制性能明显 下降,这些 故障 产生的原因为系统的清洁度达 不到 目标 精度的要求 ,比如 固体颗粒 污染,造成阀芯卡死 ,密封失 效,系统出现 内外泄漏 :流 量冲 击过 大,造成管路系统的冲击振动 ;系 统的工作压力过高 ,流 量过大 , 环境温度过高且不稳定 ,没有 强有 力的冷却措施 ,造成温度过大 , 大量能量损失 ;电气线路接头 不 良,线圈损坏等 。上述故 障都严 重 影响到系统运行 的稳定性和控 制精 度,必须采取措施对故 障进 行控 制或处理。 针 对 上 述 故 障 ,可 通 过 电 流 给 定 来 观 察 液 压 缸 的响 应 情 况 ,对
全液压压下立辊轧机的结构特点及设计计算
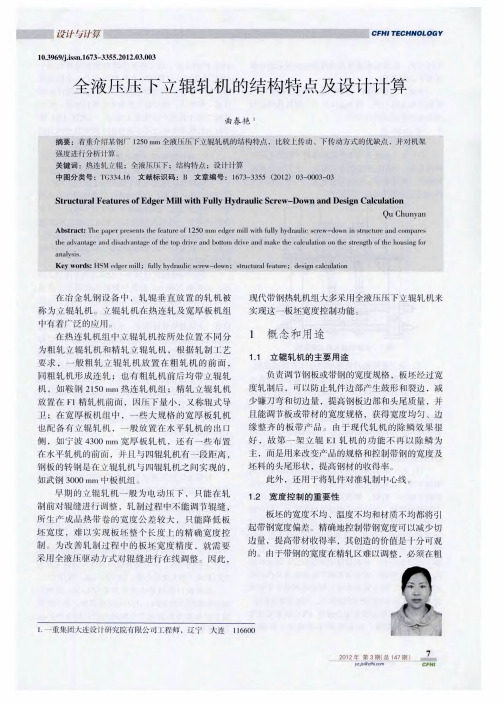
,两 者之 间用 钩子 互相勾 住 ,用楔 子 固定 ,以承受 轧制 板坯时在立辊轧机与水平辊轧机之间所产生的作用力。
() 左 、右对 称 的两个轧 辊轴 承部件 悬挂 在机 3 架 窗 口中 ,轧辊采 用 简支梁结 构 ,轴承 选用 双列 圆
下 ,这样 做 的好 处是 节省 空间 ,但却不 利 于维护 和 检 查 ,无 法避 免氧 化铁皮 、水 和油污 等进 入 圆柱齿 轮 箱 内 ,加剧齿 轮 、传动 轴及轴 承 等磨损 ,而且 将
¨ 吒 f l
守 仁j 耍 囝 皇 L _ _
—
r
r -
图 1 15 2 0热 连 轧 机 立 辊 轧 机
焊接 支架支 承 主减速 机 ,下 部通 过两 个焊接 底座 安
由于上传动式基本上消除了氧化铁皮 、水和油 污对立辊主传动装置的影响,大大减轻移动部分的 重量 ,减 少 了滑 道 的磨 损 ,降低 了侧压 传动 所需 电 机功率 。因此现 代热连 轧 的立辊轧 机大 都采 用这 种
上传 动结 构形式 。
()该 立辊 轧 机 主传 动 采用 电机 上 传 动形 式 , 5 主传 动 箱 的下 方通 过 支 架 支 承 在 立 辊 轧 机 的 牌 坊 上 ,后 面靠预 紧螺 栓与水 平轧机 牌坊联 接 。两 台立 式 交流 变频 电机左 右对 称布置 ,分别 传动 左右 两侧 的一级 圆柱齿 轮 ,通过 两侧大齿 轮互 相 啮合 ,以实 现 机械 同 步 。 电机 分 别 竖直 安 装 在 立 辊 主 减 速 机 上 ,电机轴 下伸 通过 鼓形 齿 联 轴器 与 减 速机 相 连 , 主 电机上各 装有 一 台光 电编码 器 ,用来 控制 两 台电
是 在立柱 的 中央 。所 以机架 纵 向总变 形为 向 上最大
森德威二十辊轧机液压压下故障原因分析
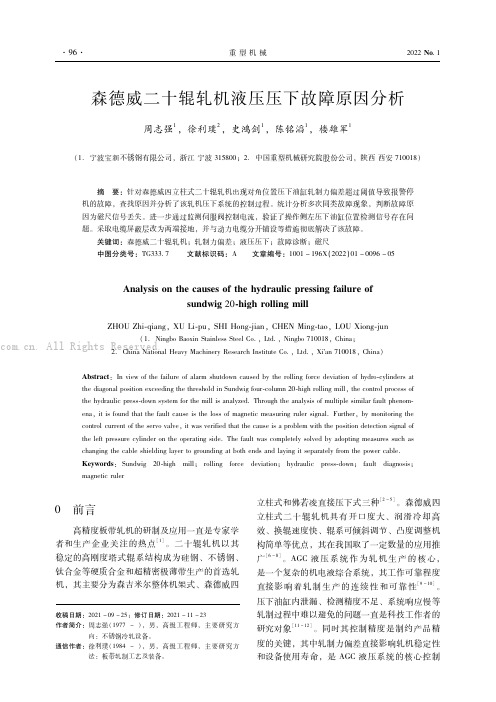
5%'(7+&+,%*$"#':+"+,-*$"$70)':()"++&%< -'&(:)",+:%0.&< &$/$&<$),((&%< 3&((
单轧制力控制模式只在两种情况下使用' !!$ 校平值超过偏差时" 此时位置控制被切断" 需通过 单轧制力控制来纠正位置偏差# !&$在磁尺预设定 时" 设定四个立柱的轧制力相等从而确保四个磁尺 处于同一平面并赋同值& 在该模式下单轧制力通过
"/
重 型 机 械%% %%%%%%%%%%%%%%%%&$&& 8,O!
须将检测油缸位置的磁尺进行调零 且调零时当 达 -O/ KK 对磁尺在平台上重新赋值后 四磁
四个油缸都到达机械限位平台 用于标定四油缸 尺同一值再运行即可恢复正常 而对没有压差
位置处于同一高度 每侧加 &W$ L0的单轧制力 故障的调零同类偏差不会超过 $O! KK 由于测量
故障处理过程
手动移动 eJ^磁尺位置 显示高度跟随变化 磁尺 无问题 将四磁尺停电复位 位置控制下调零后正 常&W$ L0时 eJ^比其它低 !O!W KK
& 轧制约 !! K6< 对角线压力成喇叭口 先位置控制后单轧制力控制下打开 单轧制力下位
浅析热轧厂精轧液压AGC控制系统

2 液压AGC系统的组成及控制原理
2 . 1 系 统 组成
好的轧件板形 ,要在最后 的精轧机上采用恒 轧制力控制 。 而其他精 轧机 的AP C 系统 则可 由操 作人员选择恒 辊缝控制 或恒轧制力控制。液压 A P C 的控制原理图如图1 所示 :
p啦 譬僚锺 I 嚣 O S t 赶 鬣传爆 潞
表1 T DC的 硬 件 配 置 及 其 用途 说 明
1 概述
精轧机控 制作为轧线 上的 主要 控制 内容 ,它包括 了板
型 、厚度 、活套 和 主速 度 四个 方面 的控 制 。厚 度 控制 又
是其重点 控制 内容 ,厚度控制好 坏将直接关 系到产 品质量 的好坏 ,它主要包括 了监 控 、偏 心补偿 、反 馈和前馈 的 自
关键 词 :精 轧机 ;液Y  ̄ . A GC;厚 度控 制 ;热轧 厂 中图分类号 :T G3 3 3 文 献标识码 :A 文章 编号 :1 0 0 9 - 2 3 7 4( 2 0 1 3 )1 4 — 0 0 3 7 — 0 3 数 据交换快 速响应 、数 量庞大 的要 求 ,在各精 轧机 的T DC 之间使用了光纤 网 ( 1 0 0 M) 进行 连接 。T D C 的硬件配置及 其用途 如表1 所示 :
于9 9 %。
式中 :
通过调整板 厚偏差 以获得 标准板厚是AG C 控制的最终 目的 。液压 A P C 是液压 A G C 系统 的执 行机构 ,它主要用于 辊缝调节量 的确定 。然后 在轧钢过程 中 ,利用液压AG C 对
因为A G C 系统 在液 压压 下具 有 调节 精 度高 、抗 干扰性 能
好 、截 止频率高 、反应快 、惯 性小 的优 点 ,它是提 高带钢
轧机压下大型伺服液压缸测试系统加载机架有限元模态分析

连杆小头衬套过盈联接 的有 限元计算和试验测试表 明 , 本 文所述 的连杆小头衬套孔位置综合误差纠正方法可行。 按这种纠 正方法 已完成 2 0余件连杆的修理 ,装机使用未发现异常情况 。 0 实际应用情况表明 , 该纠正方法对恢复连杆小头衬套孔位置综合 精度简单 、 有效 , 可在其它内燃机连杆修理中推广应用 。
★ 来稿 日期 :00 0— 1 ★基金项 目: 21—53 科技部科技人员服务企业行动项 目(Q 09 J002 , S 20GE 02 )湖北省教育厅青年科 学基金 (2O 103 , Q 06 10 ) 武汉科技大学冶金装备及其控制教育部 重点实验室开放基金重点资助项 目(09 0 ) 20B 1
有限元模 态分析 木
黄 富碹 陈新元 陈奎 生 陈 忱 。 (武 汉科技 大学 冶 金装备 及其控 制省部 共建教育 部重点 实验室 , ’ 武汉 40 8 ) 30 1
(武钢集团国际经济贸易总公司, 武汉 4 0 8 ) 30 1
F nt l me tmo a a y i ft e r ln i h d a l e v — yid r ii ee e n d I an lss o ol g m l y r u i s r o c l e h i l c n
a dcnrlWu a 3 0 C ia n ot , h n4 0 8 , hn ) o 1 ( nen t n l cn mi & Ta igC roai , gn ru , h n4 0 8 , hn ) 2 t ai a E oo c I r 0 rdn op rt n Wu agG op Wu a 3 0 C ia o 1
微 电子 以及计算 机辅助测试技术 , 能对缸直径 1 0 r 以下 的 60 m a 各类 伺服液压缸进行检验 , 其系统原理图如 图 1 所示 。
粗轧机AWC液压控制系统故障原因分析与改进

( P l a t e H o t R o l l i n g C o m p a n y L i mi t e d , T i a n j i n T i a n t i e M e t a l l u r g y G r o u p , S h e C o u n t y , H e b e i P r o v i n c e 0 5 6 4 0 4 , C h i n a )
的一组重要 的设备 ,它为精轧机提供合格 的中间
坯, 由立 辊 轧 机 和平 辊 轧 机组 成 , 其 中 立辊 轧 机 的 主要作 用是 控制板 材 的宽度 , 主要 由作 用在立 辊 轧 机 上 的 自动 宽 度 控 制 ( a u t o m a t i c w i d t h c o n t r o l , A WC ) 液 压 控制 系统 来 完 成 , 其主要功能为 : 在 生 产 的过 程 中 ,对 立辊 轧机 的工 作辊 进行 精 确定位 , 控 制 中间坯 的宽 度 ,为 精 轧机 组 提 供合 格 的 中间 坯 。 良好 的宽 度 精度 不 仅 可 以降 低 带 钢 的切 边 损 耗, 提 高产 品的 成材 率 , 而 且将 给热 轧 钢卷 的用 户 c o 及 后部 工序 创造 更好 的生 产条 件 。在实 际生 产 中 ,
i n c r e a s e d a n d b i g e c o n o my b e n e i f t o b t a i n e d . Ke y wo r d s r o u g h i n g mi l l ; h y d r a u l i c c o n t r o l s y s t e m; v i b r a t i o n ;n o i s e
轧机液压压下系统的特性分析
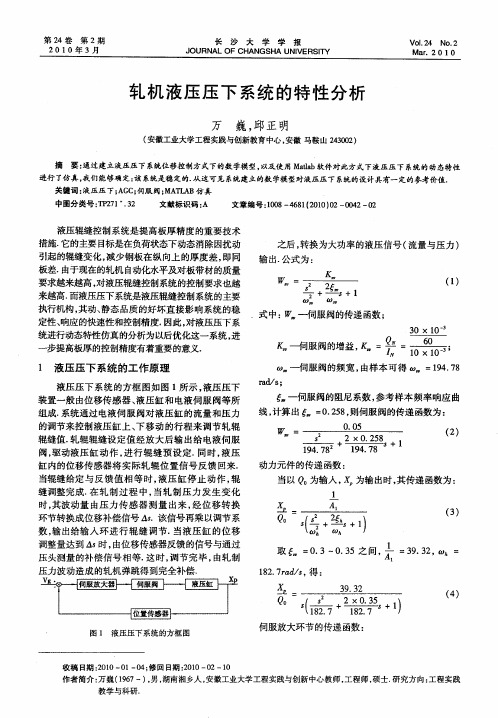
动 力元件 的传递 函数 : 当以 Q 为输 入 , 为输 出时 , 。 其传 递 函数 为 :
生 一
Qs+ 1 0( + 妄 )
取
.
( 3 )
=o 3—0 3 . . 5之 间 , I =3 3 9 2,∞^ :
12 7 a / , : 8 . rd s 得
G() 校 正环节 的传 递 函数 . s 一
位移传感器 : 由于系统 中选 用高精 度、 高响应 的位 置传 感
器, 因此 :
=
图 4 液压压下系统仿 真结果
() 6
2 结论
由液压压 下系 统 Bd oe图可 知 , 系统 的幅值 裕量
式中: 一位移传感器的传递函数 ;
一
伺 服 阀 的增益 ,
=
=
;
1 液 压 压 下 系统 的工 作 原 理
液压 压下 系统 的方 框 图如 图 1所示 , 液压 压下
∞ — 伺 服 阀的频宽 , 由样本 可 得 ∞ =14 7 9 .8
rd ; a /s
一
装置 一般 由位移传 感 器 、 压缸 和 电液伺 服 阀等所 液 组成 . 系统 通过 电液 伺 服 阀对 液压 缸 的 流量 和压 力 的调 节来控 制液 压缸 上 、 移 动 的行 程来 调 节 轧辊 下 辊缝 值. 辊辊缝 设 定值 经 放 大后 输 出给 电液伺 服 轧 阀, 驱动液 压 缸 动 作 , 行 辊 缝 预设 定 . 时 , 压 进 同 液
执行机构 , 动、 其 静态 品质 的好 坏直 接影 响系 统 的稳
之后 , 转换 为大功 率 的液压 信号 ( 流量 与压 力 )
输 出. 式为 : 公
万能轧机液压AGC系统动特性研究

dr u i ys e . a lc s t m
Ke r s: ni r a il hy r u i a t m a i y wo d u ve s lm l; d a lc u o tc
1 1 万 能 轧 机 压 下 系统 的 组 成 .
收 稿 日期 : 0 0—0 —2 21 4 8
图 2 液压 压下 控制 系统
-
《 械 与 电子  ̄ 0 0 9 机 2 1 ()
7 ・ 5
12 液压 A C系统动态方 框 图及 技术参数 . G
响应 的谐波输 入信 号 频 率 范 围。频 宽大 , 统对 于 系 频率 较高 的谐 波输 人 , 稳 态下 仍 有输 出。频 宽不 在 仅表 明系统 的稳态 性 能 , 也是 一个 直 接影 响 动 态 响
A b ta t By s u i g t e a l r un ilA G C s r c : t dy n h l — o d m l s t m oli g m il , idi g m a he a i a o yse ofr ln ls bu l n t m tc lm d— e s o h s t m b t d au i p e s e s s l f t e yse a ou a hy r lc r s ur y —
万 能 轧 机液 压 AGC系 统动 特 性 研 究
袁带 英
M o l nd S m u a i n o y r u i dei a i l to f H d a lc AGC y t m f Un v r a il ng S s e o i e s lM l
应快 慢 的指 标 。频宽 大 , 系统 的上 升时 间短 , 过渡过
- 1、下载文档前请自行甄别文档内容的完整性,平台不提供额外的编辑、内容补充、找答案等附加服务。
- 2、"仅部分预览"的文档,不可在线预览部分如存在完整性等问题,可反馈申请退款(可完整预览的文档不适用该条件!)。
- 3、如文档侵犯您的权益,请联系客服反馈,我们会尽快为您处理(人工客服工作时间:9:00-18:30)。
轧机液压压下系统分析
摘要:本文通过对带钢冷轧机液压压下装置的相关性能特征和工作原理,以及轧
机液压轧制控制分析,以及相关的材料工艺选用,得到轧机液压压下系统的高指
标性能的依赖于系统的各个环节优良,还需要相关技术工作人员轧制工艺精湛,
更需要液压、电气和机械上相互配合,做到各方面优秀,积极运用高技术,保证
高专业,配套高综合知识水平,才能保证我们整个轧机液压压下系统的稳定高效
运行。
关键词:带钢冷轧机液压压下系统轧制控制
一、前言
目前我们所说的轧辊压下通常包括液压压下以及电动压下两个主要组成方式。
当下社会,伺服控制液压压下装置的产生和发展较为迅速,与之相配合的液
压压下系统也得到了广泛的应用和推广[1]。
此装置克服了传统电动压下装置的一
些弊端,并且能极大提高相关精度的调节以及提升了相应的速度,对之前装置存
在的系统惯性大也起到了较好的降低作用,较为有效的控制了轧机基座的当量刚
度和恒辊缝轧制,这些改善保证了装置能较好的实现恒压力的功能,恒辊缝轧制
得到有效控制后能产生过载保护的功能,在出现过载事故时,辊缝能迅速打开并
及时卸压,不仅有效的保护了机械设备,还促进了机械传动效率和机组作业率,
较好的实现了快速换辊的环节,正是因为该装置存在众多优点,所以在我们现代
化冷、热轧和平整机中得以广泛的使用。
二、系统工作原理
组成液压压下装置系统的相关零件有:伺服放大器、伺服阀、液压缸、位
置传感器等。
在现实情况下液压缸移动的行程受电液伺服阀对液压缸压力和相关
流量调节的影响,在此情况下才能对轧辊辊缝的值进行相关调节,通过对轧辊辊
缝值的放大设置,向电液伺服阀施加输出,从而驱动液压缸工作,使得辊缝达到
预设定。
液压缸内的位置传感器能实时捕捉轧辊的实际位置,这里能产生一个反
馈值,如果反馈值与辊缝相关的预定值实现了统一,这就表明辊缝完成参数调整,则指示液压缸停止动作。
如果在轧制过程中,轧制压力产生了一定的变化,
此时压力传感器可以对轧制压力变化进行相关波动测量,并转换成对应的位移补
偿信号差值,并将信号差值和调节系数进行相乘计算后,重新输入值进行调节辊缝,直至液压缸位移调节量与补偿信号差值相等,这时才表示调节完成,在这种
情况下,因为轧制压力的变化,致使轧机弹跳,从而实现了完全补偿。
三、轧制控制
为了获取轧制力,液压轧制是通过对两个位于轧机机架底部液压缸压力的
捕获,和其相关位置的调整的变化得到,通过提高轧制力的方法,我们能有效改
善带钢产品的屈服强度和其他相关金属性能,还能提高产品的表面平整度。
为了
提高轧机的延伸率和达到所施加轧制力的最终效果,我们应当确保我们的轧辊的
轧制模式优良,产品特性好,还要保证高光洁度。
机器底部的2个液压缸受到液
压阀的调节,从而为机器提供了相应的轧机轧制力。
液压缸中存在杆侧,在受到
电磁阀提供的背压之后,能实现辊缝的打开[2]。
为了使机器更好的工作,在液压
缸的每侧都需要配置相应的压力变送器,以及对应的位移传感器。
压力传感器为
轧机的各侧的轧制力大小提供了相关依据,而液压缸的缩回工作则是由电磁阀的
杆侧施加相关的背压实现。
液压控制有几个主要方式:轧制力差、轧制力和、倾
斜控制、平均位置控制。
闭环控制系统则有其他两组调节器共同构成。
四、相关注意事项
在整个系统中液压缸也有其特定的组成部分,具体由液压缸防护罩、液压
缸压板、液压缸缸盖、液压缸柱塞、液压缸缸筒等一些部件共同组成的,也称之
为柱塞式液压油缸。
为了让液压缸达到更好的工作性能,我们对相关材质要做出
明确的要求,其中,相关的缸筒材质配置如下:材料由42MrMo锻造调制而成,
缸筒的内径硬铬厚度应控制在0.03mm左右,经过精细磨制之后,其内径圆柱度
公差应当控制在0.02mm以内,缸筒表面的粗糙度也有相关规定,应控制在
0.2μm以内,柱塞材料应按规定,用45钢锻造调制而成,缸筒的杆外径硬铬厚度应控制在0.03mm左右,与缸筒表面的粗糙度一样,在精细磨制之后应当控制在0.2μm以内[3]。
对于缸筒的活塞外径也有相关规定,必须在活塞外径上安装达到
耐磨要求的且密封的安装槽。
在整个缸筒中,安装槽与活塞机柱塞杆的同心度公
差不能超过规定的0.03mm。
液压缸缸盖在液压缸的相关配置中也处于举足轻重的位置,应当保证缸盖在
意外事故中或者极限位置的特殊情况下,能有足够顽强的承压能力,这就需要对
缸盖的材料选择做出苛刻的要求,其材料必须具有较高的力学性能。
与缸筒材料
相同,同样通常选用42CrMo材料,或者选择强度更高以及韧性更好的材料,与
缸筒设计一样,也需在内径上安装经久耐磨且密封的安装槽,同样对应的同心度
公差保持在0.03mm以内。
如果在选择活塞外径,及缸盖内径安装的安装槽的时候,对安装槽的密封性
和耐磨性具有极高的要求。
在通常的情况下,25Mpa是冷轧机液压压下装置的相
关额定工作油压,但是试验压力通常取额定油压的一点五倍左右,也就是保持在38Mpa左右,只有通过试验才能确保之后的工作中符合要求,也能满足安全性能。
对于密封性来说,除了严格的保证无串油和漏油现象产生,还有达到其他相关要求,如能将移动面之间可能产生的摩擦力减至最低,因为通常情况下,液压缸的
响应速度与摩擦力成反比例关系,所以减小摩擦力也是提高系统性能的关键之一[4]。
一般而言,冷轧机液压压下装置所规定的静摩擦力应当控制在冷轧机工作压
力的百分之零点五以内,而对于速度与精度要求更高的冷轧机的静摩擦力要求也
更高,应当控制在百分之零点二以内,而这些零件的相关测试值也必须取自液压
缸正常的工作区域范围内[5]。
除了这些要求之外,安装槽的耐磨损性也有相关规定,其耐磨损性要求安装槽能够承受液压装置工作中出现的最高温度,以及满足
装置启动频率和相关零件的移动速速,只有全部满足才能算合格的液压装置,保
证工作顺利有效进行。
五、结语
综上所述,只有个系统的出色才能提高整体的优良效率,每件事每个工作
以及每个设备的效率都服从于木桶效益,只有各个部分都提高才能产生好的效益,所以整个液压压下装置的高性能,不仅仅是说某个设备优良就能满足工作需求了的,其各项高性能指标来自系统的各个环节优良,还需要相关技术工作人员轧制
工艺精湛,更需要液压、电气和机械上相互配合,做到各方面优秀,积极运用高
技术,保证高专业,配套高综合知识水平,才能保证我们整个轧机液压压下系统
的稳定高效运行。
参考文献:
[1]杜巧连, 陈旭辉. 轧机液压压下位置闭环控制系统研究及仿真[J]. 机械制造,
2017(12):39-41.
[2]张瑞成, 马寅洲, 高峥,等. 轧机液压压下垂直系统非线性振动机理研究[J]. 机械强度, 2016(1):6-11.
[3]张震. 液压压下系统在热轧窄带钢精轧机组的应用研究[J]. 山东工业技术,
2016(3):7-7.
[4]卢权观. 在中板轧机上实现液压压下控制的方法与实践[J]. 太钢科技, 2016(3):25-34.
[5]赵玉武, 魏志恒. 液压缸及辊缝控制下辊系非线性垂直振动分析[J]. 设备管理与
维修, 2016(11):72-75.。