Costcontrol成本控制外文翻译
毕业论文--成本控制(cost--control)外文原文及译文【范本模板】
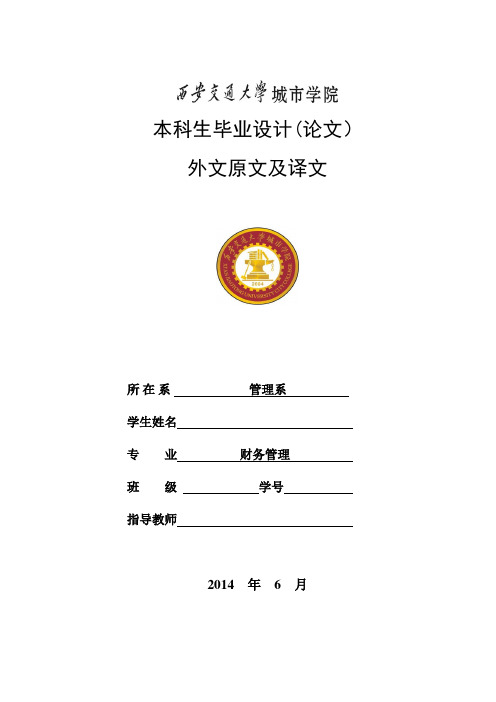
本科生毕业设计(论文)外文原文及译文所在系管理系学生姓名专业财务管理班级学号指导教师2014 年 6 月外文原文及译文Cost ControlRoger J. AbiNaderReference for Business,Encyclopedia of Business, 2nd ed。
Cost control,also known as cost management or cost containment,is a broad set of cost accounting methods and management techniques with the common goal of improving business cost-efficiency by reducing costs, or at least restricting their rate of growth. Businesses use cost control methods to monitor, evaluate, and ultimately enhance the efficiency of specific areas,such as departments,divisions, or product lines, within their operations.Cooper and Kaplan in 1987 in an article entitled "how cost accounting systematically distorts product costs” article for the first time put forward the theory of "cost drivers" (cost driver, cost of driving factor)of that cost, in essence,is a function of a variety of independent or interaction of factors (independent variable) work together to drive the results. So what exactly is what factors drive the cost or the cost of motive which? Traditionally, the volume of business (such as yield)as the only cost driver (independent variable),at least that its cost allocation plays a decisive role in restricting aside,regardless of other factors (motivation). In accordance with the full cost of this cost driver, the enterprise is divided into variable costs and fixed costs of the two categories。
2020年成本管理外文文献及翻译.doc
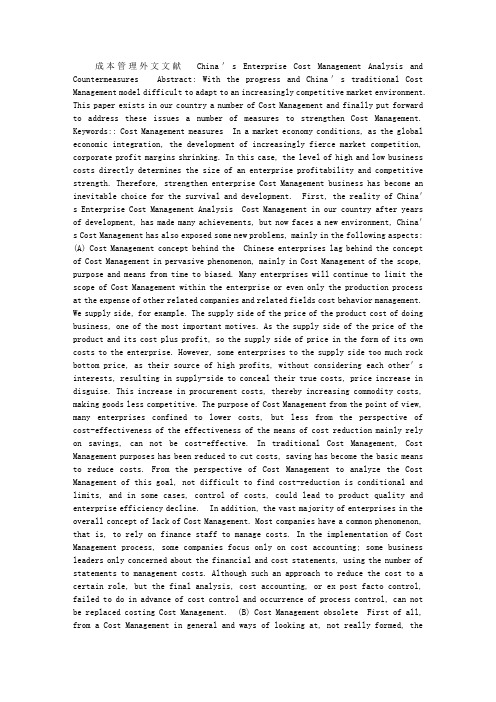
成本管理外文文献China's Enterprise Cost Management Analysis and Countermeasures Abstract: With the progress and China's traditional Cost Management model difficult to adapt to an increasingly competitive market environment. This paper exists in our country a number of Cost Management and finally put forward to address these issues a number of measures to strengthen Cost Management. Keywords:: Cost Management measures In a market economy conditions, as the global economic integration, the development of increasingly fierce market competition, corporate profit margins shrinking. In this case, the level of high and low business costs directly determines the size of an enterprise profitability and competitive strength. Therefore, strengthen enterprise Cost Management business has become an inevitable choice for the survival and development. First, the reality of China's Enterprise Cost Management Analysis Cost Management in our country after years of development, has made many achievements, but now faces a new environment, China's Cost Management has also exposed some new problems, mainly in the following aspects: (A) Cost Management concept behind the Chinese enterprises lag behind the concept of Cost Management in pervasive phenomenon, mainly in Cost Management of the scope, purpose and means from time to biased. Many enterprises will continue to limit the scope of Cost Management within the enterprise or even only the production process at the expense of other related companies and related fields cost behavior management. We supply side, for example. The supply side of the price of the product cost of doing business, one of the most important motives. As the supply side of the price of the product and its cost plus profit, so the supply side of price in the form of its own costs to the enterprise. However, some enterprises to the supply side too much rock bottom price, as their source of high profits, without considering each other's interests, resulting in supply-side to conceal their true costs, price increase in disguise. This increase in procurement costs, thereby increasing commodity costs, making goods less competitive. The purpose of Cost Management from the point of view, many enterprises confined to lower costs, but less from the perspective of cost-effectiveness of the effectiveness of the means of cost reduction mainly rely on savings, can not be cost-effective. In traditional Cost Management, Cost Management purposes has been reduced to cut costs, saving has become the basic means to reduce costs. From the perspective of Cost Management to analyze the Cost Management of this goal, not difficult to find cost-reduction is conditional and limits, and in some cases, control of costs, could lead to product quality and enterprise efficiency decline. In addition, the vast majority of enterprises in the overall concept of lack of Cost Management. Most companies have a common phenomenon, that is, to rely on finance staff to manage costs. In the implementation of Cost Management process, some companies focus only on cost accounting; some business leaders only concerned about the financial and cost statements, using the number of statements to management costs. Although such an approach to reduce the cost to a certain role, but the final analysis, cost accounting, or ex post facto control, failed to do in advance of cost control and occurrence of process control, can not be replaced costing Cost Management. (B) Cost Management obsolete First of all, from a Cost Management in general and ways of looking at, not really formed, thesystem's Cost Management methodology, from speaking, we have proposed the establishment of including cost projections, the cost of decision-making, cost planning, cost accounting, cost control, cost analysis, etc. In the within the new Cost Management system, but how to make this methodology in a scientific, systematic, forming an organic links there are many problems. Secondly, the specific method of Cost Management perspective, According to the survey, 57% of the enterprises use varieties of France, 48% of companies use sub-step. The development trend of current world production of many varieties of small batch production mode, this mode of production batches law applies to product cost. Currently, only 2% of China's enterprises to adopt this method to calculate, which indicates that the organization of production in China is still relatively extensive, paid insufficient attention to the consumer's personality. Finally, from a Cost Management tool to see, even though some enterprises to enter the computerized stage, but the cost of application management module level is not high, and many enterprises are still the manual accounting, in a modern way of technology, Information, and this is bound to constrain business further enhance the level of Cost Management, it is difficult to meet the modern Cost Management of cost Information provided by the timeliness, comprehensiveness, accuracy requirements. (C) the cost Information, a serious distortion of In China, there are a considerable number of enterprises there is the cost of the case Information is untrue, and this situation is getting worse. Cost Information distortion is mainly caused by the following reasons: First, costing only a focus on materials, labor, manufacturing overhead, ignoring the growing increase in the modern enterprise product development, the middle of testing and trial-and after-sales service on a small group of input costs associated with the content of the product was incomplete, does not correctly evaluate the products in the the whole process of life-cycle cost-effectiveness. The second is distortion caused by improper costing methods. A high degree of labor-intensive enterprises in the past years, the accounting of the simple assumption (that is, the number of direct labor hours or production basis for the allocation of indirect costs), usually do not cause serious distortions in product costs. But in a modern manufacturing environment, the proportion of direct labor costs declined significantly, a substantial increase in the proportion of manufacturing costs, and then use the traditional method of cost computation will produce irrational behavior, the use of traditional costing will lead to serious distortions in product cost information to enable enterprises to operate the mistake of choosing the direction of products. Third, to achieve the purpose of artificially adjust the cost of a number of hidden losses caused by a serious, corporate virtual surplus real loss. In China, some enterprises do not increase because of Cost Management, but in order to achieve improper goals or interest to do so at the cost of the external disclosure of false information. Study its causes and performance: business managers in order to gloss over its management performance, to investors, especially medium and small shareholders have a good explanation to take virtual cut costs, inflated benefits, such as Joan China source event, Guangxia event; some private enterprises do not even pay taxes in order to tax less, false purchase invoices, virtual offset value-addedtax; inflated costs, pay less corporate income tax; a number of enterprise Cost Management is in chaos, infrastructure work is not solid, it is difficult to accurately account for product costs, and thus disclosed the cost of information is not accurate. (D) internal Cost Management of the establishment of the main mistakes Cost of production and operation activities, a comprehensive index covering all aspects of management, but also involves all levels of personnel. However, a long time, people have been the existence of a bias, the Cost Management as a finance officer for a small number of managers patents, that the cost-effectiveness should be handled by business leaders and finance staff and to all workshops, departments, teams and groups of workers only as a producer, resulting in control costs, understand technology, understand technology, understand the financial, the majority of the workers as to which costs should be controlled, how to control problems have no intention also were unable to say in the cost-conscious indifference. Workers that Ganhaoganhuai a sample, feel market pressures, cost control initiative can not be mobilized, serious waste, mainly in energy and materials, the next material without careful planning, the next corner does not make full use of materials, energy and run , risk, dripping, and leak is serious. Cost Management of the main mistakes made to establish the Cost Management business has lost the management of large groups of promise, of course, Cost Management work is not really achieve good results. Second, strengthen enterprise Cost Management measures Cost Management for Chinese Enterprises in the problems, we should start the following efforts to strengthen Cost Management: (A) the introduction of new ideas - the use of strategic Cost Management Strategic management is central to the sustained competitive advantage for businesses, competitive advantage is the core of any Strategy, it ultimately comes from enterprises to create value for customers, this value must exceed the costs of enterprises to create it. An enterprise to gain a competitive advantage need to make a choice, that is, enterprises must strive for what would be an advantage, and to what extent the problem for superiority to make a choice. This requires the introduction of strategic management of Cost Management thinking, to achieve a strategic sense of the extensions to form a strategic Cost Management. Strategic Cost Management refers to management of the specialized approach provides an analysis of the enterprise itself and its competitors information to assist managers and evaluation of the formation of corporate Strategy, thereby creating a competitive advantage in order to meet enterprises to effectively adapt to constantly changing external environment. (B) establish a new concept 1, establish a system management concepts, the implementation of a comprehensive, whole process of Cost Management The content and scope of the cost of doing business should not be confined to areas of production, management needs to be with the change, and as the development of management development. Cost Management should be comprehensive, the whole process, and at the design stage till the development planning stage should begin to reduce the cost of activities. Modern enterprise Cost Management should include the impact on cost changes in all aspects of the projections to penetrate the enterprise, decision-making, technology, sales and other areas in all aspects of the enterprise expansion. 2, establish the concept of cost-effectiveness, cost forecasting anddecision-making levels Enterprises can not succeed in the market for greater profits, they must establish the cost of determining the market concept, give full play to the cost of policy-making functions. Cost Management and enterprise's overall effectiveness should also be linked to the concept of dynamic cost-effective approach to cost and control issues, from the comparative analysis of input and output to look into the necessity and rationality of the enterprise from the perspective of efficiency to determine the increases or decreases in order to conduct a cost benefit as the center of the dynamic management. 3, establish a sense of innovation, technology and insist on combining The vitality lies in its continued innovation, and enterprises should seize the pulse of the market, seeking mechanism innovation, vibrancy, increase scientific and technological input, and the effective use of new technologies, new equipment, new processes and new materials, relying on technology to reduce product cost. Meanwhile, cost accounting should be considered in the scientific and technological content of products, including the cost to go to facilitate enterprises to the correct decision. The formation of the product cost, the technical factors, plays an important role, to improve Cost Management, we must implement the technology-driven economic principle of combining. 4, establish a people-oriented concept, create a cohesive force in enterprise People do not simply a tool for wealth creation, but an enterprise's largest capital, assets, resources and wealth, the main body of the enterprise, is the main Cost Management is to determine the cost of key factors. Therefore, to establish a people-oriented management thinking, and arouse people's intellectual factors, train and develop people's ability to work, so that employees and managers on an equal footing and enjoy the same participation in power, the humanistic, democratic management thinking throughout the enterprise management process from beginning to end, so that enterprises can truly become a democratic, humane organizations, from the human heart in order to stimulate everyone's sense of responsibility and willing to devote themselves masters of the spiritual power. (C) the introduction of advanced Cost Management - activity-based costing and cost-planning method Since the cost of the early 20th century inception, he has appeared 'standard cost', 'budget control', 'difference', 'cost-of-state analysis', 'variable cost method', 'volume-profit analysis', 'responsibility accounting', etc. a series of traditional cost accounting methods. However, in today's increasingly competitive market economy, the traditional cost accounting methods have fatal defects, thus creating an activity-based costing and cost-planning method. 1, Activity-Based Costing Activity-Based Costing is based on 'cost driver' as the fundamental basis of a cost-accounting methods. Its basic principle is that consumption of output operations, operations consume resources. In the product cost, it will be the focus from the traditional 'products' move to 'work' on to work for the accounting object, and the first motivation of resources based on resource allocation of costs to the job, and then tracked by the activity driver products, the final product obtained costs. It is customer-oriented chain, to the value chain as the center of the business 'operational procedures'fundamental and thorough reform, emphasizing the coordination of corporate internal and external customer relations, starting fromthe enterprise as a whole, coordinating the various departments and links the relationship between the ask enterprises to material supply, production and marketing aspects of the operations form a continuous, synchronous's 'workflow', the elimination of all can not increase the value of the operation, so that enterprises in the state continued to improve and promote enterprise-wide optimization, establishing competitive advantage. 2, cost planning method The cost of planning the basic ideas: (1) to full life-cycle-based, market-oriented development of target cost. Basic formula is: target cost=expected market price - target profit. (2) product design stage the cost of squeezing. This process can be expressed as the cost of the 'Settings - decomposition - to achieve - (re-setting) - (re-decomposition) - (another achievement) - ... ...', and repeatedly as well as endless, until it reaches target cost. (3) the cost of production at the manufacturing stage decomposition and pressure transmission. The target cost pressures refined to teams and groups, and even individuals and vendors. (4) pre-production phase of the feedback control. Through trial and feedback from the production process and timely leak fill a vacancy, strengthen internal management, improve cost control management through a variety of incentive measures to make the cost of the ideological objectives of planning can be the greatest degree of implementation. (5) The target cost optimization. Product to meet the needs of market competition must be constantly adjusted and optimized so that the cost of setting goals to keep up with the pace of technological and market changes, so that the cost of the entire planning process to form a complete cycle, continuous improvement, and constantly perfect, and always be able to adapt to the changing market. (Iv) computer technology in Enterprise Cost Management At present, the computer is an indispensable tool for economic life, to modern information technology-based Cost Management Cost Management information system has become a symbol of modernization. 1, the software application LOTUS, EXCEL and other spreadsheet software has a powerful form processing, database management and statistical charts processing functions, is commonly used office automation software. They do not have programming, flexible and convenient, the use of low cost, high efficiency, use of these software can be easily and quickly assist management in cost projections, decision-making, and can control the process of implementation of the monitoring analysis, received good results. Businesses can combine their own characteristics, commissioned by software developers for their costs of developing a more professional management software. 2, the application of The network has a strong scalability, enables the sharing of resources, improve efficiency and reduce costs. Internal and external Internet connection of the timely transmission of a variety of cost information, and can interactively communicate with the outside world, learn from each other and promote the application of various Cost Management techniques to achieve Cost Management objectives. (E) to take measures to ensure cost-effective information Companies should establish a sound internal control system, through accounting and other business processes control, help reduce the occurrence of the phenomenon of accounting information Cuobi to a certain extent, the accounting and other information to ensure true and reliable. For example, a good internal control system, required documents must be recorded against previous audit,the certificate of transfer must follow certain procedures, to the reconciliation table cards and checking accounts. Through these means of control, it is possible to reduce the incidence of errors to ensure the accuracy and reliability of accounting information and thus the basis for cost accounting and management information is reliable. Enterprises also need to improve the management and accounting staff of professional ethics. The main body of the implementation of the system is the enterprise managers and decision-making participation in the operation of accounting personnel, in the generation and provision of relevant information, on one hand to enhance the legal awareness, on the one hand to enhance the sense of moral self-discipline, strengthen the moral sense of responsibility and sense of responsibility to maintain professional conscience, economic objectives of enterprises and managers to enhance the double moral standards. In addition to strengthen the market research and information feedback in the Cost Management applications. Information as a business activity is an important factor in the cost management an integral part of. With economic development, enterprise cost management level, with the development of the situation can improve, operation can proceed smoothly, to a large extent also depends on the level of the cost of feedback. Therefore, the enterprise cost management must also adapt to this objective, continually improve the level of information management, seize the opportunity to truly become the strong market competition. 中国企业成本管理的现状分析与对策摘要随着中国所取得的进展,中国传统的成本管理模式已经难以适应竞争日益激烈的市场环境。
成本控制外文文献(Costcontrol,foreignliterature)
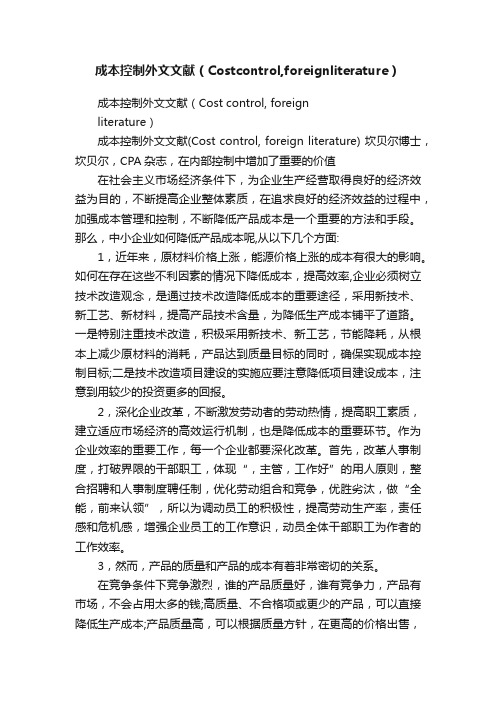
成本控制外文文献(Costcontrol,foreignliterature)成本控制外文文献(Cost control, foreignliterature)成本控制外文文献(Cost control, foreign literature) 坎贝尔博士,坎贝尔,CPA杂志,在内部控制中增加了重要的价值在社会主义市场经济条件下,为企业生产经营取得良好的经济效益为目的,不断提高企业整体素质,在追求良好的经济效益的过程中,加强成本管理和控制,不断降低产品成本是一个重要的方法和手段。
那么,中小企业如何降低产品成本呢,从以下几个方面:1,近年来,原材料价格上涨,能源价格上涨的成本有很大的影响。
如何在存在这些不利因素的情况下降低成本,提高效率,企业必须树立技术改造观念,是通过技术改造降低成本的重要途径,采用新技术、新工艺、新材料,提高产品技术含量,为降低生产成本铺平了道路。
一是特别注重技术改造,积极采用新技术、新工艺,节能降耗,从根本上减少原材料的消耗,产品达到质量目标的同时,确保实现成本控制目标;二是技术改造项目建设的实施应要注意降低项目建设成本,注意到用较少的投资更多的回报。
2,深化企业改革,不断激发劳动者的劳动热情,提高职工素质,建立适应市场经济的高效运行机制,也是降低成本的重要环节。
作为企业效率的重要工作,每一个企业都要深化改革。
首先,改革人事制度,打破界限的干部职工,体现“,主管,工作好”的用人原则,整合招聘和人事制度聘任制,优化劳动组合和竞争,优胜劣汰,做“全能,前来认领”,所以为调动员工的积极性,提高劳动生产率,责任感和危机感,增强企业员工的工作意识,动员全体干部职工为作者的工作效率。
3,然而,产品的质量和产品的成本有着非常密切的关系。
在竞争条件下竞争激烈,谁的产品质量好,谁有竞争力,产品有市场,不会占用太多的钱;高质量、不合格项或更少的产品,可以直接降低生产成本;产品质量高,可以根据质量方针,在更高的价格出售,在销售收入中的比重相对降低成本;高质量的产品,才能赢得更多的客户,增加销售,降低销售成本;产品质量高,实际上也节省了能源和原材料;产品质量高,可节省人工和管理费用,这肯定会降低成本。
工业工程英语第四到7章全文翻译
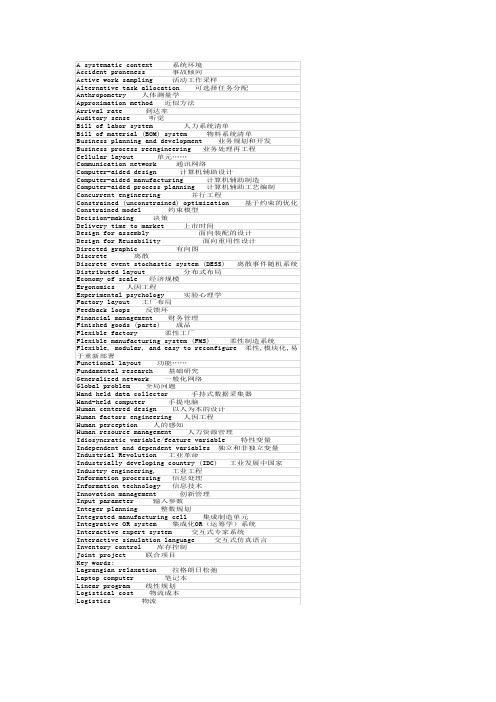
Operations Research 运筹学Some OR accomplishments运筹学的一些成果在 20 世纪 70 年代到 80 年代之间取得了一些十分突出的重大突破,下面讲述他们如何被应用以及其对经济的影响。
Integrative OR systems集成运筹学系统综合的运筹学成果在 1983 和 1984 年,全美最大的石油独立冶炼和销售公司--citgo 石油公司,将 1985 年超过 4 亿的销售额投资在一个独一无二的全面集成系统中,这个系统将运筹学的数学规划、预测及专家系统结合到了统计和组织理论中。
Citgo 将运筹学系统应用到诸如:天然物资的产品开采,冶炼,供应和配送,运作市场规划,应收应付款,存货控制和制定个人执行目标, Citgo 公司由 1984 年 5000 万的营业损失变为到 1985 年高达 7000 万的营业利润要归功于这个运筹学系统。
Network flow problem网络流问题70 年代时出现了一些突破性的网络流建模和解决问题的方法,并初步形成专业化的解决运输问题及其转化问题的原始单纯形算法。
后来广义算法和大型线性网络和嵌入式网络相继出现。
这些算法表现出了前所未有的效率,速度比最好的网络问题通用线性规划系统快了从 10 到 200 倍——效率完全超越任何计算机硬件。
由于现在不可能解决庞大的网络流问题,因此新的应用层出不穷。
目前 Agrico、 Ciba-Geigy、 W.R.Grace、International Paper、Kelly-Springfied、Owens-Corning Fiberglass、Quaker Oats and R.G.Sloan 这些公司已成功地将他们的射频数据采集系统耦合到他们建立的网络流模型上,以改善所做的决定的物流成本效益和服务效益。
比如,Agrico 净减少13%周转资金并在 5 年内节省开支43 万美元;据Kelly-Springfied 报道,他们每年可节省 800 万美元以上,Cahil May Roberts 可减少 20%的运输成本和交货。
中小企业成本管理研究外文翻译中文文献
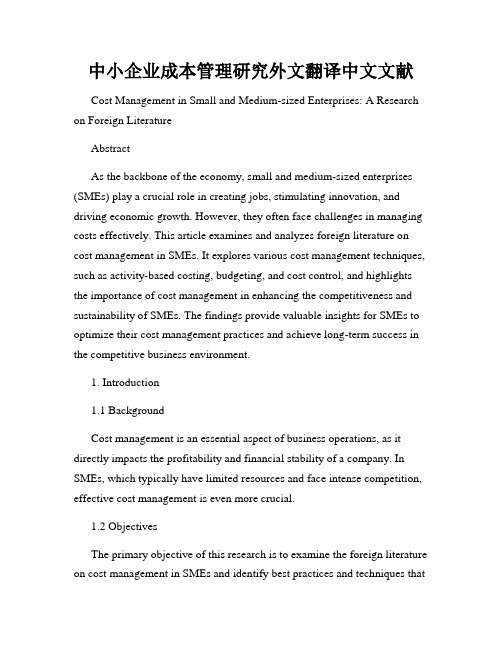
中小企业成本管理研究外文翻译中文文献Cost Management in Small and Medium-sized Enterprises: A Research on Foreign LiteratureAbstractAs the backbone of the economy, small and medium-sized enterprises (SMEs) play a crucial role in creating jobs, stimulating innovation, and driving economic growth. However, they often face challenges in managing costs effectively. This article examines and analyzes foreign literature on cost management in SMEs. It explores various cost management techniques, such as activity-based costing, budgeting, and cost control, and highlights the importance of cost management in enhancing the competitiveness and sustainability of SMEs. The findings provide valuable insights for SMEs to optimize their cost management practices and achieve long-term success in the competitive business environment.1. Introduction1.1 BackgroundCost management is an essential aspect of business operations, as it directly impacts the profitability and financial stability of a company. In SMEs, which typically have limited resources and face intense competition, effective cost management is even more crucial.1.2 ObjectivesThe primary objective of this research is to examine the foreign literature on cost management in SMEs and identify best practices and techniques thatcan be applied in the Chinese context. By understanding the experiences and strategies of SMEs in other countries, Chinese SMEs can learn from their successes and avoid potential pitfalls in cost management.2. Cost Management Techniques2.1 Activity-Based Costing (ABC)Activity-Based Costing is a cost allocation method that assigns costs to specific activities or cost objects based on their utilization of resources. This technique provides a more accurate understanding of the cost drivers in a company, enabling SMEs to allocate resources more effectively and identify areas for cost reduction.2.2 BudgetingBudgeting is a fundamental cost management tool that allows SMEs to plan and control their financial resources. By setting realistic and achievable budgets, SMEs can monitor their expenses, forecast future costs, and make informed decisions regarding resource allocation.2.3 Cost ControlCost control involves monitoring and regulating expenses to ensure that they remain within planned limits. SMEs can employ various cost control techniques, such as implementing cost-saving measures, negotiating favorable contracts with suppliers, and leveraging technology to streamline operations and reduce overhead costs.3. Importance of Cost Management in SMEs3.1 Enhanced CompetitivenessCost management enables SMEs to offer competitive prices without compromising on quality. By optimizing their cost structure, SMEs can improve their profit margins and gain a competitive edge in the market.3.2 Resource OptimizationEffective cost management allows SMEs to allocate their limited resources strategically. By identifying unnecessary costs and reallocating funds to key areas, SMEs can optimize their production processes and invest in critical areas such as research and development.3.3 Financial StabilityCost management helps SMEs maintain a stable financial position by minimizing the risk of running into cash flow problems or accumulating excessive debt. By controlling costs and ensuring efficient resource allocation, SMEs can safeguard their financial health and sustain long-term growth.4. ConclusionThis research on foreign literature emphasizes the significance of cost management in SMEs and provides valuable insights into proven techniques and strategies. By implementing effective cost management practices, SMEs can optimize their operational efficiency, enhance competitiveness, and achieve long-term success in an increasingly competitive business environment. This research serves as a guide for Chinese SMEs to improve their cost management practices and overcome challenges effectively. By integrating foreign experiences with localized strategies, SMEs can navigatethe complexities of cost management and position themselves for sustainable growth.。
工程造价专业外文文献翻译(中英文对照

外文文献:Project Cost Control: The Way it WorksBy R. Max WidemanIn a recent consulting assignment we realized that there was some lack of understanding of the whole system of project cost control, how it is setup and applied. So we decided to write up a description of how it works. Project cost control is not that difficult to follow in theory.First you establish a set of reference baselines. Then, as work progresses, you monitor the work, analyze the findings, forecast the end results and compare those with the reference baselines. If the end results are not satisfactory then you make adjustments as necessary to the work in progress, and repeat the cycle at suitable intervals. If the end results get really out of line with the baseline plan, you may have to change the plan. More likely, there will be (or have been) scope changes that change the reference baselines which means that every time that happens you have to change the baseline plan anyway.But project cost control is a lot more difficult to do in practice, as is evidenced by the number of projects that fail to contain costs. It also involves a significant amount of work, as we shall see, and we might as well start at the beginning. So let us follow the thread of project cost control through the entire project life span.And, while we are at it, we will take the opportunity to point out the proper places for several significant documents. These include theBusiness Case, the Request for (a capital) Appropriation (for execution), Work Packages and the Work Breakdown Structure, the Project Charter (or Brief), the Project Budget or Cost Plan, Earned Value and the Cost Baseline. All of these contribute to the organization's ability to effectively control project costs.FootnoteI am indebted to my friend Quentin Fleming, the guru of Earned Value, for checking and correcting my work on this topic.The Business Case and Application for (execution) FundingIt is important to note that project cost control is most effective when the executive management responsible has a good understanding of how projects should unfold through the project life span. This means that they exercise their responsibilities at the key decision points between the major phases. They must also recognize the importance of project risk management for identifying and planning to head off at least the most obvious potential risk events.In the project's Concept Phase• EvEry projEct starts with somEonE idEntifying an opportunity or need. That is usually someone of importance or influence, if the project is to proceed, and that person often becomes the project's sponsor.• to dEtErminE thE suitability of thE potEntial projEct, most organizations call for the preparation of a "Business Case" and its"Order of Magnitude" cost to justify the value of the project so that it can be compared with all the other competing projects. This effort is conducted in the Concept Phase of the project and is done as a part of the organization's management of the entire project portfolio.• thE cost of thE work of preparing the Business Case is usually covered by corporate management overhead, but it may be carried forward as an accounting cost to the eventual project. No doubt because this will provide a tax benefit to the organization. The problem is, how do you then account for all the projects that are not so carried forward?• if thE businEss casE has sufficiEnt mErit, approval will bE givEn to proceed to a Development and Definition phase.In the project's Development or Definition Phase• thE objEctivE of t he Development Phase is to establish a good understanding of the work involved to produce the required product, estimate the cost and seek capital funding for the actual execution of the project.• in a formalizEd sEtting, EspEcially whErE big projEcts arE involved, this application for funding is often referred to as a Request for (a capital) Appropriation (RFA) or Capital Appropriation Request (CAR).• this rEquirEs thE collEction of morE dEtailEd rEquirEmEnts and data to establish what work needsto be done to produce the required product or "deliverable". From this information, a plan is prepared in sufficient detail to give adequate confidence in a dollar figure to be included in the request.• in a lEss formalizEd sEtting, EvEryonE just triEs to muddlE through.Work Packages and the WBSThe Project Management Plan, Project Brief or Project Charter• if thE dElivErablE consists of a numbEr of diffErEnt ElEmEnts, thEsE are identified and assembled into Work Packages (WPs) and presented in the form of a Work Breakdown Structure (WBS).• Each wp involvEs a sEt of activitiEs, thE "work" that is plannEd and scheduled as a part of the Project Management Plan. Note, however, that the planning will still be at a relatively high level,and more detailed planning will be necessary during execution if the project is given the go ahead.• this projEct managEmEnt plan, by thE way, should bEcomE thE "bible" for the execution phase of the project and is sometimes referred to as the "Project Brief" or the "Project Charter".• thE cost of doing thE various activitiEs is thEn EstimatEd and thEsE estimated costs are aggregated to determine the estimated cost of the WP. This approach is known as "detailed estimating" or "bottom up estimating". There are other approaches to estimating that we'll come to in a minute. Either way, the result is an estimated cost of the totalwork of the project.Note: that project risk management planning is an important part of this exercise. This should examine the project's assumptions and environmental conditions to identify any weaknesses in the plan thus far, and identify those potential risk events that warrant attention for mitigation. This might take the form of specific contingency planning, and/or the setting aside of prudent funding reserves.Request for capitalConverting the estimate• howEvEr, an EstimatE of thE work alonE is not sufficiEnt for a capital request. To arrive at a capital request some conversion is necessary, for example, by adding prudent allowances such as overheads, a contingency allowance to cover normal project risks and management reserves to cover unknowns and possible scope changes.• in addition, it may bE nEcEssary to convErt thE Estimating data into a financial accounting formatthat satisfies the corporate or sponsor's format for purposes of comparison with other projects and consequent funding approval.• in practicE all thE data for thE typE of "bottom up" approach just described may not be available.In this case alternative estimating approaches are adopted that provide various degrees of reliability in a "top down" fashion. Forexample:Order of Magnitude estimate – a "ball park" estimate, usually reserved for the concept phase onlyAnalogous estimate – an estimate based on previous similar projects Parametric estimate –an estimate based on statistical relationships in historical data• whichEvEr approach is adoptEd, hopEfully thE sum thus arrivEd at will be approved in full and proves to be satisfactory! This is the trigger to start the Execution Phase of the projectNote: Some managements will approve some lesser sum in the mistaken belief that this will help everyone to "sharpen their pencils" and "work smarter" for the benefit of the organization. This is a mistaken belief because management has failed to understand the nature of uncertainty and risk in project work. Consequently, the effect is more likely to result in "corner cutting" with an adverse effect on product quality, or reduced product scope or functionality. This often leads to a "game" in which estimates are inflated so that management can adjust them downwards. But to be fair, management is also well aware that if money is over allocated, it will get spent anyway. The smart thing for managements to do is to set aside contingent reserve funds, varying with the riskiness of the project, and keep that money under careful control.Ownership of approved capital• if sEnior managEmEnt approvEs thE rfa as prEsEntEd, thE sum in question becomes the responsibility of the designated project sponsor. However, if the approved capital request includes allowances such as a "Management Reserve", this may or may not be passed on to the project's sponsor, depending on the policies of the organization.• for thE approvEd rfa, thE projEct sponsor will, in turn, further delegate expenditure authority to the project's project manager and will likely not include any of the allowances. An exception might be the contingency allowances to cover the normal variations in work performance.• thE nEt sum thus arrivEd at constitutes the project manager's Approved Project Budget.Note: If management does not approve the RFA, you should not consider this a project failure. Either the goals, objectives, justification and planning need rethinking to increase the value of the project's deliverables, or senior management simply has higher priorities elsewhere for the available resources and funding.The Project's Execution PhaseThe project manager's Project Budget responsibility• oncE this approvEd projEct budgEt is rElEas ed to the project manager, a reverse process must take place to convert it into a working control document. That is, the money available must be divided amongstthe various WBS WPs that, by the way, have probably by now been upgraded! This results in a project execution Control Budget or Project Baseline Budget, or simply, the Project Budget. In some areas of project management application it is referred to as a Project Cost Plan.• on a largE projEct whErE diffErEnt corporatE production divisions are involved, there may be a further intermediate step of creating "Control Accounts" for the separate divisions, so that each division subdivides their allocated money into their own WBS WPs.• obsErvE that, sincE thE total projEct budgEt rEcEivEd formal approval from Executive Management, you, as project manager, must likewise seek and obtain from Executive Management, via the project's sponsor, formal approval for any changes to the total project budget. Often this is only justified and accepted on the basis of a requested Product Scope Change.• in such a casE thE projEct's sponsor will EithEr draw down on thE management reserve in his or her possession, or submit a supplementary RFA to upper management.• now that wE havE thE projEct budgEt monEy allocatEd to Work Packages we can further distribute it amongst the various activities of each WP so that we know how much money we have as a "Baseline" cost for each activity.• this providEs us with thE basE of rEfErEncE for thE cost controlfunction. Of course, depending on the circumstances the same thing may be done at the WP level but the ability to control is then at a higher and coarser level.Use of the Earned Value technique• if wE havE thE nEcEssary dEtails anothEr control tool that wE can adopt for monitoring ongoing work is the "Earned Value" (EV) technique. This is a considerable art and science that you must learn about from texts dedicated to the subject.• but EssEntially, you takE thE costs of thE schEdulE activitiEs and plot them as a cumulative total on the appropriate time base. Again you can do this at the activity level, WP level or the whole project level. The lower the level the more control information you have available but the more work you get involved in.The Cost Baseline• this plannEd reference S-curve is sometimes referred to as the "Cost Baseline", typically in EVparlance. That is, it is the "Budgeted Cost of Work Scheduled" (BCWS), or more simply the "Planned Value" (PV).• Observe that you need to modify this Cost Baseline every time there is an approved scope change that has cost and/or schedule implications and consequently changes the project's Approved Project Budget.• now, as thE work progrEssEs, you can plot thE "actual cost of workPerformed" (ACWP or simply "Actual Cost" - AC).• you can plot othEr things as wEll, sEE diagram rEfErrEd to abovE, and if you don't like what you see then you need to take "Corrective Action".CommentaryThis whole process is a cyclic, situational operation and is probably the source of the term "cycle" in the popularly misnamed "project life cycle".As an aside, the Earned Value pundits offer various other techniques within the EV process designed to aid in forecasting the final result, that is, the "Estimate At Completion" (EAC). EAC is what you should really be interested in because it is the only constant in a moving project. Therefore, these extended EV techniques must be considered in the same realm of accuracy as top-down estimating. They are useful, but only if you recognize the limitations and know what you are doing!But, as we said at the beginning, it is a lot more difficult to do in practice –and involves a significant amount of work. But, let's face it, that's what project managers are hired for, right?中文译文:项目成本控制:它的工作方式R.马克斯怀德曼我们在最近的咨询任务中意识到,对于整个项目成本控制体系是如何设置和应用的这个问题,我们仍有一些缺乏了解。
成本控制中英文对照外文翻译文献
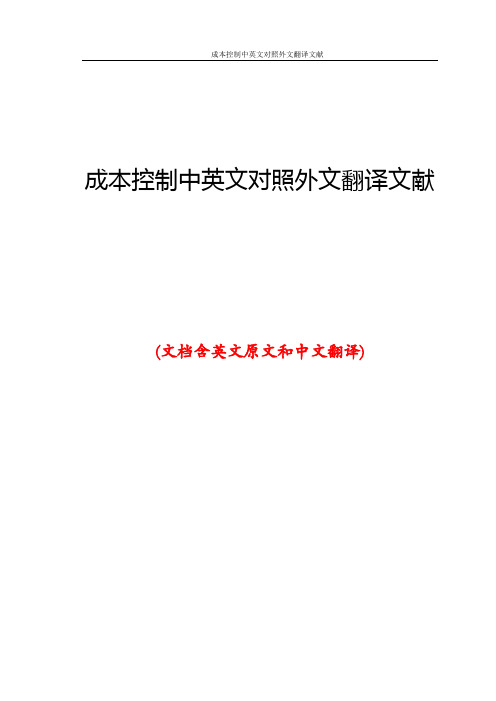
成本控制中英文对照外文翻译文献(文档含英文原文和中文翻译)原文:COST CONTROLRoger J. AbiNaderReference for Business,Encyclopedia of Business, 2nd ed.Cost control, also known as cost management or cost containment, is a broad set of cost accountingmethods and management techniques with the common goal of improving business cost-efficiency by reducing costs, or at least restricting their rate of growth. Businesses use cost control methods to monitor, evaluate, and ultimately enhance the efficiency of specific areas, such as departments, divisions, or product lines, within their operations.Control of the business entity , then, is essentially a managerial and supervisory function .Control consiets of those actions necessary to assur e that the entity’s resources and operations are focused on attaining established objectives , goals and plans. Control, exercised continuously, flags potential problems so that crises may be prevented. It also standardizeds the quantity of output , and provides managers with objective information about employee performance . Management compares actual performance to predetermined standards and takes action when necessary to correct variances from the standards.Keywords : Cost control, Applications, Control reports, Standards, Strategic Cost control, also known as cost management or cost containment, is a broad set of cost accountingmethods and management techniques with the common goal of improving business cost-efficiency by reducing costs, or at least restricting their rate of growth. Businesses use cost control methods to monitor, evaluate, and ultimately enhance the efficiency of specific areas, such as departments, divisions, or product lines, within their operations.During the 1990s cost control initiatives received paramount attention from corporate America. Often taking the form of corporate restructuring, divestmentof peripheral activities, mass layoffs,or outsourcing,cost control strategies were seen as necessary to preserve—or boost—corporate profits and to maintain—or gain—a competitive advantage. The objective was often to be the low-cost producer in a given industry, which would typically allow the company to take a greater profit per unit of sales than its competitors at a given price level.Some cost control proponents believe that such strategic cost-cutting must be planned carefully, as not all cost reduction techniques yield the same benefits. In a notable late 1990s example, chief executive Albert J. Dunlap, nicknamed "Chainsaw Al" because of his penchant for deep cost cutting at the companies he headed, failed to restore the ailing small appliance maker Sunbeam Corporation to profitability despite his drastic cost reduction tactics. Dunlap laid off thousands of workers and sold off business units, but made little contribution to Sunbeam's competitive position or share price in his two years as CEO. Consequently, in 1998 Sunbeam's board fired Dunlap, having lost confidence in his "one-trick" approach to management.COST CONTROL APPLICATIONSA complex business requires frequent information about operations in order to plan for the future, to control present activities, and to evaluate the past performance of managers, employees, and related business segments. To be successful, management guides the activities of its people in the operations of the business according to pre-established goal and objectives. Management’s guidance takestwo forms of control: (1) the management and supervision of behuvior , and (2) the evaluation of performance.Behavioral management deals with the attitudes and actions of employees. While employee behavior ultimately impacts on success, behavioral management involves certain issues and assumptions not applicable to accounting's control function. On the other hand, performance evaluation measures outcomes of employee's actions by comparing the actual results of business outcomes to predetermined standards ofsuccess. In this way management identifies the strengths it needs to maximize, and the weaknesses it seeks to rectify. This process of evaluation and remedy is called cost control.Cost control is a continuous process that begins with the proposed annual budget. The budget helps: (1) to organize and coordinate production, and the selling, distribution, service, and administrative functions; and (2) to take maximum advantage of available opportunities. As the fiscal year progresses, management compares actual results with those projected in the budget and incorporates into the new plan the lessons learned from its evaluation of current operations.Control refers to management's effort to influence the actions of individuals who are responsible for performing tasks, incurring costs, and generating revenues. Management is a two-phased process: planningrefers to the way that management plans and wants people to perform, while controlrefers to the procedures employed to determine whether actual performance complies with these plans. Through the budget process and accounting control, management establishes overall company objectives, defines the centers of responsibility, determines specific objectives for each responsibility center, and designs procedures and standards for reporting and evaluation.A budget segments the business into its components or centers where the responsible party initiates and controls action. Responsibility centersrepresent applicable organizational units, functions, departments, and divisions. Generally a single individual heads the responsibility center exercising substantial, if not complete, control over the activities of people or processes within the center and controlling the results of their activity. Cost centersare accountable only for expenses, that is, they do not generate revenue. Examples include accounting departments, human resources departments, and similar areas of the business that provide internal services. Profit centersaccept responsibility for both revenue and expenses. For example, a product line or an autonomous business unit might be considered profit centers. If the profit center has its own assets, it may also be considered an investment center,for which returns on investment can be determined. The use of responsibility centers allows management todesign control reports to pinpoint accountability, thus aiding in profit planning.A budget also sets standards to indicate the level of activity expected from each responsible person or decision unit, and the amount of resources that a responsible party should use in achieving that level of activity. A budget establishes the responsibility center, delegates the concomitant responsibilities, and determines the decision points within an organization.The planning process provides for two types of control mechanisms:Feedforward: providing a basis for control at the point of action (the decision point); andFeedback: providing a basis for measuring the effectiveness of control after implementation.Management's role is to feedforwarda futuristic vision of where the company is going and how it is to get there, and to make clear decisions coordinating and directing employee activities. Management also oversees the development of procedures to collect, record, and evaluate feedback.Therefore, effective management controls results from leading people by force of personality and through persuasion; providing and maintaining proper training, planning, and resources; and improving quality and results through evaluation and feedback.Control reports are informational reports that tell management about an entity's activities. Management requests control reports only for internal use, and, therefore, directs the accounting department to develop tailor-made reporting formats. Accounting provides management with a format designed to detect variations that need investigating. In addition, management also refers to conventional reports such as the income statement and funds statement, and external reports on the general economy and the specific industry.Control reports, then, need to provide an adequate amount of information so that management may determine the reasons for any cost variances from the original budget.A good control report highlights significant information by focusing management's attention on those items in which actual performance significantly differs from thestandard.Because key success factors shift in type and number, accounting revises control reports when necessary. Accounting also varies the control period covered by the control report toencompass a period in which management can take useful remedial action. In addition, accountingdisseminates control reports in a timely fashion to give management adequate time to act before the issuance of the next report.Managers perform effectively when they attain the goals and objectives set by the budget. With respect to profits, managers succeed by the degree to which revenues continually exceed expenses. In applying the following simple formula, managers, especially those in operations, realize that they exercise more control over expenses than they do over revenue.While they cannot predict the timing and volume of actual sales, they can determine the utilization rate of most of their resources, that is, they can influence the cost side. Hence, the evaluation of management's performance and its operations is cost control.For cost control purposes, a budget provides standard costs. As management constructs budgets, it lays out a road map to guide its efforts. It states a number of assumptions about the relationships and interaction among the economy, market dynamics, the abilities of its sales force, and its capacity to provide the proper quantity and quality of products demanded.Accounting plays a key role in all planning and control. It does this in four key areas: (1) data collection, (2) data analysis, (3) budget control and administration, and (4) consolidation and review.The accountants play a key role in designing and securing support for the procedural aspects of the planning process. In addition, they design and distribute forms for the collection and booking of detailed data on all aspects of the business.Although operating managers have the main responsibility of planning, accounting compiles and coordinates the elements. Accountants subject proposed budgets to feasibility and profitability analyses to determine conformity to accepted standards andpractices.Management relies on such accounting data and analysis to choose from several cost control alternatives, or management may direct accounting to prepare reports specifically for evaluating such options. As the Chainsaw Al episode indicated, all costs may not be viable targets for cost-cutting measures. For instance, in mass layoffs, the company may lose a significant share of its human capitalby releasing veteran employees who are experts in their fields, not to mention by creating a Decline in morale among those who remain. Thus management must identify which costs have strategic significance and which do not.To determine the strategic impact of cost-cutting, management has to weigh the net effects of the proposed change on all areas of the business. For example, reducing variable costs related directly to manufacturing a product, such as materials and transportation costs, could be the key to greater incremental profits. However, management must also consider whether saving money on production is jeopardizing other strategic interests like quality or time to market. If a cheaper material or transportation system negatively impacts other strategic variables, the nominal cost savings may not benefit the company in the bigger picture, e.g., it may lose sales. In such scenarios, managers require the discipline not to place short-term savings over long-term interests.One trend in cost control has been toward narrowing the focus of corporate responsibility centers, and thereby shifting some of the cost control function to day-to-day managers who have the most knowledge of and influence over how their areas spend money. This practice is intended to promote bottom-up cost control measures and encourage a widespread consensus over cost management strategies.Control of the business entity, then, is essentially a managerial and supervisory function. Control consists of those actions necessary to assure that the entity's resources and operations are focused on attaining established objectives, goals and plans. Control, exercised continuously, flags potential problems so that crises may be prevented. It also standardizes the quality and quantity of output, and provides managers with objectiveinformation about employee performance. Management compares actual performance to predetermined standards and takes action when necessary to correct variances from the standards.译文:成本控制成本控制成本控制,也被称为遏制成本或管理成本,一个广阔的成本管理技术,它的经济增长目标是降低成本提高企业效率。
工程管理专业外文文献翻译(中英文)【精选文档】
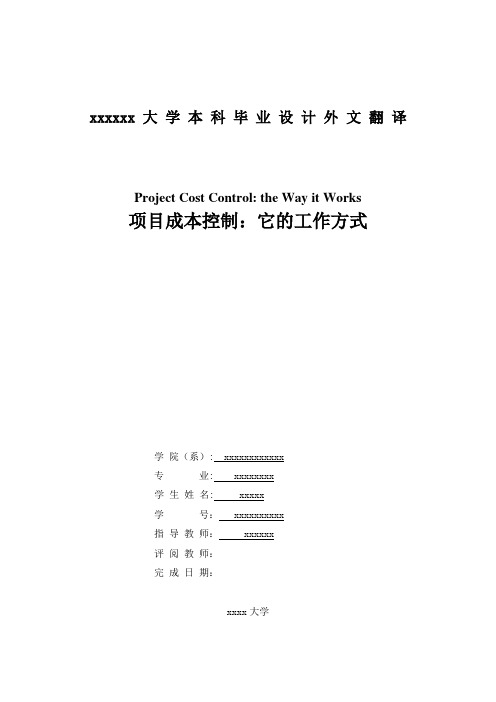
xxxxxx 大学本科毕业设计外文翻译Project Cost Control: the Way it Works项目成本控制:它的工作方式学院(系): xxxxxxxxxxxx专业: xxxxxxxx学生姓名: xxxxx学号: xxxxxxxxxx指导教师: xxxxxx评阅教师:完成日期:xxxx大学项目成本控制:它的工作方式在最近的一次咨询任务中,我们意识到对于整个项目成本控制体系是如何设置和应用的,仍有一些缺乏理解。
所以我们决定描述它是如何工作的.理论上,项目成本控制不是很难跟随。
首先,建立一组参考基线。
然后,随着工作的深入,监控工作,分析研究结果,预测最终结果并比较参考基准。
如果最终的结果不令人满意,那么你要对正在进行的工作进行必要的调整,并在合适的时间间隔重复。
如果最终的结果确实不符合基线计划,你可能不得不改变计划.更有可能的是,会 (或已经) 有范围变更来改变参考基线,这意味着每次出现这种情况你必须改变基线计划。
但在实践中,项目成本控制要困难得多,通过项目数量无法控制成本也证明了这一点。
正如我们将看到的,它还需要大量的工作,我们不妨从一开始启用它。
所以,要跟随项目成本控制在整个项目的生命周期.同时,我们会利用这一机会来指出几个重要文件的适当的地方。
其中包括商业案例,请求(资本)拨款(执行),工作包和工作分解结构,项目章程(或摘要),项目预算或成本计划、挣值和成本基线。
所有这些有助于提高这个组织的有效地控制项目成本的能力。
业务用例和应用程序(执行)的资金重要的是要注意,当负责的管理者对于项目应如何通过项目生命周期展开有很好的理解时,项目成本控制才是最有效的。
这意味着他们在主要阶段的关键决策点之间行使职责。
他们还必须识别项目风险管理的重要性,至少可以确定并计划阻止最明显的潜在风险事件。
在项目的概念阶段•每个项目始于确定的机会或需要的人.通常是有着重要性和影响力的人,如果项目继续,这个人往往成为项目的赞助。
- 1、下载文档前请自行甄别文档内容的完整性,平台不提供额外的编辑、内容补充、找答案等附加服务。
- 2、"仅部分预览"的文档,不可在线预览部分如存在完整性等问题,可反馈申请退款(可完整预览的文档不适用该条件!)。
- 3、如文档侵犯您的权益,请联系客服反馈,我们会尽快为您处理(人工客服工作时间:9:00-18:30)。
Reference for business,Encyclopedia of Business.2nd ed,Cos DesCost controlRoger J. BinderAbstractCost control, also known as cost management or cost containment, is a broad set of cost accounting methods and management techniques with the common goal of improving business cost-efficiency by reducing costs, or at least restricting their rate of growth. Businesses use cost control methods to monitor, evaluate, and ultimately enhance the efficiency of specific areas, such as departments, divisions, or product lines, within their operations.Control of the business entity, then, is essentially a managerial and supervisory function. Control consists of those actions necessary to assure that the entity's resources and operations are focused on attaining established objectives, goals and plans. Control, exercised continuously, flags potential problems so that crises may be prevented. It also standardizes the quality and quantity of output, and provides managers with objective information about employee performance. Management compares actual performance to predetermined standards and takes action when necessary to correct variances from the standards.Keywords: Cost control;Applications;Control reports;Standards;StrategicCost control, also known as cost management or cost containment, is a broad set of cost accounting methods and management techniques with the common goal of improving business cost-efficiency by reducing costs, or at least restricting their rate of growth. Businesses use cost control methods to monitor, evaluate, and ultimately enhance the efficiency of specific areas, such as departments, divisions, or product lines, within their operations.During the 1990s cost control initiatives received paramount attention from corporate America. Often taking the form of corporate restructuring, divestment ofperipheral activities, mass layoffs, or outsourcing, cost control strategies were seen as necessary to preserve—or boost—corporate profits and to maintain—or gain—a competitive advantage. The objective was often to be the low-cost producer in a given industry, which would typically allow the company to take a greater profit per unit of sales than its competitors at a given price level.Some cost control proponents believe that such strategic cost-cutting must be planned carefully, as not all cost reduction techniques yield the same benefits. In a notable late 1990s example, chief executive Albert J. Dunlap, nicknamed "Chainsaw Al" because of his penchant for deep cost cutting at the companies he headed, failed to restore the ailing small appliance maker Sunbeam Corporation to profitability despite his drastic cost reduction tactics. Dunlap laid off thousands of workers and sold off business units, but made little contribution to Sunbeam's competitive position or share price in his two years as CEO. Consequently, in 1998 Sunbeam's board fired Dunlap, having lost confidence in his "one-trick" approach to management.COST CONTROL APPLICATIONSA complex business requires frequent information about operations in order to plan for the future, to control present activities, and to evaluate the past performance of managers, employees, and related business segments. To be successful, management guides the activities of its people in the operations of the business according to pre-established goals and objectives. Management's guidance takes two forms of control: (1) the management and supervision of behavior, and (2) the evaluation of performance.Behavioral management deals with the attitudes and actions of employees. While employee behavior ultimately impacts on success, behavioral management involves certain issues and assumptions not applicable to accounting's control function. On the other hand, performance evaluation measures outcomes of employee's actions by comparing the actual results of business outcomes to predetermined standards of success. In this way management identifies the strengths it needs to maximize, and the weaknesses it seeks to rectify. This process of evaluation and remedy is called cost control.Cost control is a continuous process that begins with the proposed annual budget. The budget helps: (1) to organize and coordinate production, and the selling, distribution, service, and administrative functions; and (2) to take maximum advantage of available opportunities. As the fiscal year progresses, management compares actual results with those projected in the budget and incorporates into the new plan the lessons learned from its evaluation of current operations.Control refers to management's effort to influence the actions of individuals who are responsible for performing tasks, incurring costs, and generating revenues. Management is a two-phased process: planning refers to the way that management plans and wants people to perform, while control refers to the procedures employed to determine whether actual performance complies with these plans. Through the budget process and accounting control, management establishes overall company objectives, defines the centers of responsibility, determines specific objectives for each responsibility center, and designs procedures and standards for reporting and evaluation.A budget segments the business into its components or centers where the responsible party initiates and controls action. Responsibility centers represent applicable organizational units, functions, departments, and divisions. Generally a single individual heads the responsibility center exercising substantial, if not complete, control over the activities of people or processes within the center and controlling the results of their activity. Cost centers are accountable only for expenses, that is, they do not generate revenue. Examples include accounting departments, human resources departments, and similar areas of the business that provide internal services. Profit centers accept responsibility for both revenue and expenses. For example, a product line or an autonomous business unit might be considered profit centers. If the profit center has its own assets, it may also be considered an investment center, for which returns on investment can be determined. The use of responsibility centers allows management to design control reports to pinpoint accountability, thus aiding in profit planning.A budget also sets standards to indicate the level of activity expected from each responsible person or decision unit, and the amount of resources that a responsible party should use in achieving that level of activity. A budget establishes theresponsibility center, delegates the concomitant responsibilities, and determines the decision points within an organization.CONTROL REPORTSControl reports are informational reports that tell management about an entity's activities. Management requests control reports only for internal use, and, therefore, directs the accounting department to develop tailor-made reporting formats. Accounting provides management with a format designed to detect variations that need investigating. In addition, management also refers to conventional reports such as the income statement and funds statement, and external reports on the general economy and the specific industry.Control reports, then, need to provide an adequate amount of information so that management may determine the reasons for any cost variances from the original budget. A good control report highlights significant information by focusing management's attention on those items in which actual performance significantly differs from the standard.Because key success factors shift in type and number, accounting revises control reports when necessary. Accounting also varies the control period covered by the control report to encompass a period in which management can take useful remedial action. In addition, accounting disseminates control reports in a timely fashion to give management adequate time to act before the issuance of the next report.Managers perform effectively when they attain the goals and objectives set by the budget. With respect to profits, managers succeed by the degree to which revenues continually exceed expenses. In applying the following simple formula, managers, especially those in operations, realize that they exercise more control over expenses than they do over revenue.While they cannot predict the timing and volume of actual sales, they can determine the utilization rate of most of their resources, that is, they can influence the cost side. Hence, the evaluation of management's performance and its operations is cost control.STANDARDSFor cost control purposes, a budget provides standard costs. As management constructs budgets, it lays out a road map to guide its efforts. It states a number of assumptions about the relationships and interaction among the economy, market dynamics, the abilities of its sales force, and its capacity to provide the proper quantity and quality of products demanded.An examination of the details of the budget calculations and assumptions indicates that management expects the sales force to spend only so much in pursuit of the sales forecast. The details also reveal that management expects operations to produce the required amount of units within a certain cost range. Management bases its expectations and projections on the best historical and current information, as well as its best business judgment.THE ROLE OF ACCOUNTINGAccounting plays a key role in all planning and control. It does this in four key areas: (1) data collection, (2) data analysis, (3) budget control and administration, and (4) consolidation and review. The accountants play a key role in designing and securing support for the procedural aspects of the planning process. In addition, they design and distribute forms for the collection and booking of detailed data on all aspects of the business. Although operating managers have the main responsibility of planning, accounting compiles and coordinates the elements. Accountants subject proposed budgets to feasibility and profitability analyses to determine conformity to accepted standards and practices.STRATEGIC COST CONTROLManagement relies on such accounting data and analysis to choose from several cost control alternatives, or management may direct accounting to prepare reports specifically for evaluating such options. As the Chainsaw Al episode indicated, all costs may not be viable targets for cost-cutting measures. For instance, in mass layoffs, the company may lose a significant share of its human capital by releasing veteran employees who are experts in their fields, not to mention by creating a declinein morale among those who remain. Thus management must identify which costs have strategic significance and which do not.To determine the strategic impact of cost-cutting, management has to weigh the net effects of the proposed change on all areas of the business. For example, reducing variable costs related directly to manufacturing a product, such as materials and transportation costs, could be the key to greater incremental profits. However, management must also consider whether saving money on production is jeopardizing other strategic interests like quality or time to market. If a cheaper material or transportation system negatively impacts other strategic variables, the nominal cost savings may not benefit the company in the bigger picture, e.g., it may lose sales. In such scenarios, managers require the discipline not to place short-term savings over long-term interests.One trend in cost control has been toward narrowing the focus of corporate responsibility centers, and thereby shifting some of the cost control function to day-to-day managers who have the most knowledge of and influence over how their areas spend money. This practice is intended to promote bottom-up cost control measures and encourage a widespread consensus over cost management strategies.References:[1] Anthony, Robert N., and Vijay Govindarajan. Management Control Systems.Chicago: Irwin, 1997.[2] Cooper, Robin, and Robert S. Kaplan. The Design of Cost Management Systems.Upper Saddle River, NJ: Prentice Hall, 1998.[3 ] Cooper, Robin, and Regine Slagmulder. "Micro-Profit Centers." ManagementAccounting, June 1998.[4] Hamilton, Martha M. "Who's Chainsawed Now? Dunlap Out as Sunbeam's LossesMount." Washington Post, 16 June 1998. Rotch, William, et al. Cases in Management Accounting and Control Systems. 3rd ed. Englewood Cliffs, NJ: Prentice Hall, 1995.[5] Shank, John K., and Vijay Govindarajan. Strategic Cost Management. New York:Free Press, 1993.Reference for business,Encyclopedia of Business.2nd ed,Cos Des成本控制摘要企业实体的控制,本质上是一种管理和监督职能。