扩散工艺流程
扩散的工艺流程

扩散的工艺流程扩散工艺是集成电路制造中的一项重要工艺,主要用于在半导体材料表面形成掺杂区域,以改变材料的电学性质。
下面将介绍一种典型的扩散工艺流程。
首先是准备工作,包括物料准备、设备检查和工艺参数设置。
物料准备包括半导体晶片、扩散材料和掩膜材料的选择与准备。
设备检查主要是确保扩散炉和扩散源的正常运行状态。
工艺参数设置根据掺杂要求和材料特性,确定扩散温度、时间和气氛等工艺参数。
其次是扩散源的制备,扩散源一般是通过在高温条件下将掺杂材料与半导体材料反应生成的。
按照所需的掺杂浓度和材料属性,可以选择不同的扩散源。
通常情况下,将掺杂材料和半导体材料混合,并加入任何必要的添加剂,形成均匀的混合物。
然后,将混合物放入扩散源槽或坩埚中,在高温条件下进行预热、热分解和扩散源的形成。
形成的扩散源粉末可以直接用于扩散过程,也可以制备成片状等形状。
接下来是掩模制备,掩模是指在扩散过程中所需的模板,用于限制掺杂区域的形成。
一般使用光刻技术将掩模图案转移到掩膜材料上,形成掩模。
然后,将掩模放置在待扩散的半导体晶片表面,并通过光刻和显影等步骤将掩模图案转移到晶片表面。
扩散工艺是在控制的温度条件下进行的,常用的扩散方式有氧化物扩散和固相扩散。
以氧化物扩散为例,首先将掺杂源和半导体片放置在扩散炉中,然后控制炉温使其达到扩散温度。
在扩散温度下,掺杂源释放出掺杂原子,这些原子通过热扩散作用在半导体片中形成掺杂区域。
扩散时间的长短决定了掺杂的深度和浓度。
固相扩散的工艺流程类似,只是没有氧化物参与,直接通过固态反应实现掺杂。
扩散完成后,进行清洗和后续处理。
清洗是为了去除掉表面的杂质和残留的化学物质,以及掩模材料。
清洗可以使用不同的溶液和超声波等方法。
后续处理包括表面加工、封装和测试等步骤,以完成集成电路的制造。
总的来说,扩散工艺是集成电路制造中的一项关键工艺,通过控制温度、时间和掺杂原料,将掺杂原子引入半导体材料中,实现电学性质的改变。
VDMOS工艺流程

VDMOS工艺流程1、原始硅片磨抛:原始硅片磨去40µm,抛光80µm;2、清洗,并且用显微镜检查表面;3、外延生长N-:ρ=20~30Ω·cm,d=45µm;4、清洗;5、氧化:dox=6500±250Å,800℃-1000℃-800℃;6、一次版;7、腐蚀,去胶,清洗;腐蚀:温度25℃;8、P+扩散;预扩:R □=80~100Ω/□,温度:700℃-940℃-700℃;主扩:R □=150~180Ω/□,温度:800℃-1150℃-800℃;9、氧化;10、光刻:二次版反刻P+区,5000pm ;11、腐蚀,(温度25℃),时间t=8.1s ;12、去胶清洗;13、栅氧化;1)dox=1000-1100Å;2)作C-V 检查;3)实测dox=1060-1050Å;此步骤须单独做,主要是为了生长出高质量的氧化层;14、生长多晶硅7000ű200Å;15、清洗;16、三次版:光刻P-区(多晶硅)三次版,留下栅和互连的多晶硅(使多晶硅成为p型);17、腐蚀多晶硅(P-区),干腐:9'50'';18、漂栅氧,(注意不要过漂,留下50~100Å)(P-区内);19、硼注入(带胶);20、正面涂胶(5000pm);21、背面腐蚀多晶硅(干法)和SiO2;干腐4'38''漂2'22、去胶清洗;23、P-推进;dox=1000Å800-1150-800℃;24、漂SiO2,扩磷(N+),同时形成沟道,R□=6~7Ω/□,Xjn=1.1µ,Xjp=5µ,R□poly-Si≤30Ω/□;25、漂磷硅玻璃(PSiO2)(去离子水HF);26、氧化950℃;5'干氧+20'湿氧+5'干氧;dox=2100Å;27、刻边缘多晶硅(即刻场限制环上的多晶硅)5000pm;接触环上dox>1000Å合格;28、腐蚀(先湿腐多晶硅上的SiO2)6'45';29、去胶清洗3-3-1-2;炉口烘800℃20'N2;30、光刻孔(源,栅)(刻引线孔)5000pm;31、蒸铝:2.2µm;32、反刻Al5000rpm(刻电极);33、合金;34、涂聚酰氩胺,氩胺化;35、背面金属化:钒360Å,镍8000Å,金1000Å;36、测试;。
晶体硅太阳能电池生产工艺流程图

晶体硅太阳能电池生产工艺流程图电池片工艺流程说明:(1)清洗、制绒:首先用化学碱(或酸)腐蚀硅片,以去除硅片表面机械损伤层,并进行硅片表面织构化,形成金字塔结构的绒面从而减少光反射。
现在常用的硅片的厚度在 180 μm 左右。
去除硅片表面损伤层是太阳能电池制造的第一道常规工序。
(2)甩干:清洗后的硅片使用离心甩干机进行甩干。
(3)扩散、刻蚀:多数厂家都选用 P型硅片来制作太阳能电池,一般用 POCl3液态源作为扩散源。
扩散设备可用横向石英管或链式扩散炉,进行磷扩散形成 P-N结。
扩散的最高温度可达到 850- 900℃。
这种方法制出的 PN结均匀性好,方块电阻的不均匀性小于 10%,少子寿命大于 10 微秒。
扩散过程遵从如下反应式:4POCl3+3O2(过量)→ 2P2O5+2Cl 2(气) 2P2O5+5Si → 5SiO2 + 4P 腐蚀磷硅玻璃和等离子刻蚀边缘电流通路,用化学方法除去扩散生成的副产物。
SiO2与HF生成可溶于水的 SiF 62-,从而使硅表面的磷硅玻璃(掺 P2O5的SiO2)溶解,化学反应为:SiO2+6HF → H2(SiF 6)+ 2HO(4) 减反射膜沉积:采用等离子体增强型化学气相沉积(PECVD: Plasma Enhanced Chemical Vapor Deposition)技术在电池表面沉积一层氮化硅减反射膜,不仅可以减少光的反射,而且由于在制备SiNx 减反射膜过程中有大量的氢原子进入,因此也起到了很好的表面钝化和体钝化的效果。
这是因为对于具有大量晶界的多晶硅材料而言,晶界的悬挂键被饱和,降低了复合中心的原因。
由于表面钝化和体钝化作用明显,就可以降低对制作太阳能电池材料的要求。
由于增强了对光的吸收,氢原子对太阳能电池起到很好的表面和体内钝化作用,从而提高了电池的短路电流和开路电压。
(5)印刷、烧结:为了从电池上获取电流,一般在电池的正、背两面制作电极。
微电子工艺流程
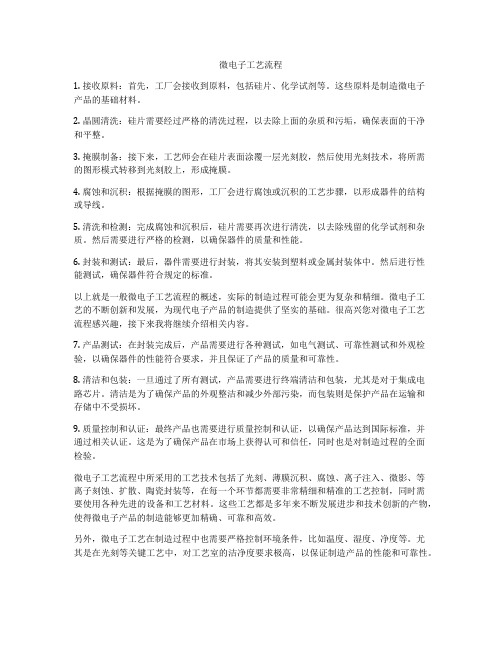
微电子工艺流程1. 接收原料:首先,工厂会接收到原料,包括硅片、化学试剂等。
这些原料是制造微电子产品的基础材料。
2. 晶圆清洗:硅片需要经过严格的清洗过程,以去除上面的杂质和污垢,确保表面的干净和平整。
3. 掩膜制备:接下来,工艺师会在硅片表面涂覆一层光刻胶,然后使用光刻技术,将所需的图形模式转移到光刻胶上,形成掩膜。
4. 腐蚀和沉积:根据掩膜的图形,工厂会进行腐蚀或沉积的工艺步骤,以形成器件的结构或导线。
5. 清洗和检测:完成腐蚀和沉积后,硅片需要再次进行清洗,以去除残留的化学试剂和杂质。
然后需要进行严格的检测,以确保器件的质量和性能。
6. 封装和测试:最后,器件需要进行封装,将其安装到塑料或金属封装体中。
然后进行性能测试,确保器件符合规定的标准。
以上就是一般微电子工艺流程的概述,实际的制造过程可能会更为复杂和精细。
微电子工艺的不断创新和发展,为现代电子产品的制造提供了坚实的基础。
很高兴您对微电子工艺流程感兴趣,接下来我将继续介绍相关内容。
7. 产品测试:在封装完成后,产品需要进行各种测试,如电气测试、可靠性测试和外观检验,以确保器件的性能符合要求,并且保证了产品的质量和可靠性。
8. 清洁和包装:一旦通过了所有测试,产品需要进行终端清洁和包装,尤其是对于集成电路芯片。
清洁是为了确保产品的外观整洁和减少外部污染,而包装则是保护产品在运输和存储中不受损坏。
9. 质量控制和认证:最终产品也需要进行质量控制和认证,以确保产品达到国际标准,并通过相关认证。
这是为了确保产品在市场上获得认可和信任,同时也是对制造过程的全面检验。
微电子工艺流程中所采用的工艺技术包括了光刻、薄膜沉积、腐蚀、离子注入、微影、等离子刻蚀、扩散、陶瓷封装等,在每一个环节都需要非常精细和精准的工艺控制,同时需要使用各种先进的设备和工艺材料。
这些工艺都是多年来不断发展进步和技术创新的产物,使得微电子产品的制造能够更加精确、可靠和高效。
另外,微电子工艺在制造过程中也需要严格控制环境条件,比如温度、湿度、净度等。
半导体的工艺流程
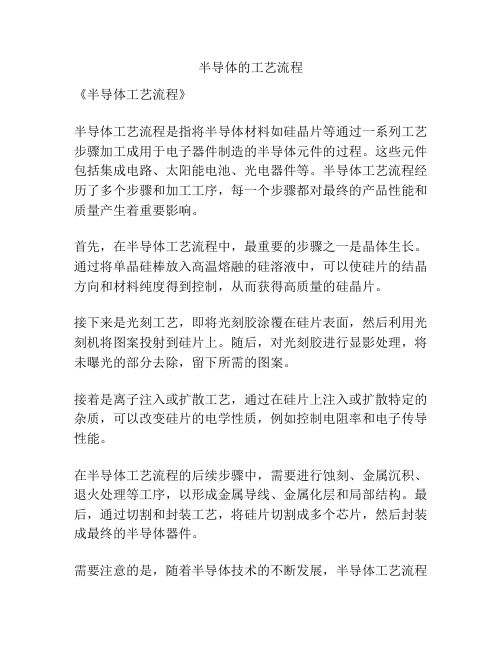
半导体的工艺流程
《半导体工艺流程》
半导体工艺流程是指将半导体材料如硅晶片等通过一系列工艺步骤加工成用于电子器件制造的半导体元件的过程。
这些元件包括集成电路、太阳能电池、光电器件等。
半导体工艺流程经历了多个步骤和加工工序,每一个步骤都对最终的产品性能和质量产生着重要影响。
首先,在半导体工艺流程中,最重要的步骤之一是晶体生长。
通过将单晶硅棒放入高温熔融的硅溶液中,可以使硅片的结晶方向和材料纯度得到控制,从而获得高质量的硅晶片。
接下来是光刻工艺,即将光刻胶涂覆在硅片表面,然后利用光刻机将图案投射到硅片上。
随后,对光刻胶进行显影处理,将未曝光的部分去除,留下所需的图案。
接着是离子注入或扩散工艺,通过在硅片上注入或扩散特定的杂质,可以改变硅片的电学性质,例如控制电阻率和电子传导性能。
在半导体工艺流程的后续步骤中,需要进行蚀刻、金属沉积、退火处理等工序,以形成金属导线、金属化层和局部结构。
最后,通过切割和封装工艺,将硅片切割成多个芯片,然后封装成最终的半导体器件。
需要注意的是,随着半导体技术的不断发展,半导体工艺流程
也在不断创新和改进,以满足新型器件的制造需求。
例如,晶片尺寸的不断缩小、新材料的应用、三维集成等都对工艺流程提出了更高的要求。
总的来说,半导体工艺流程是一个复杂的系统工程,需要多种工艺和技术的协同作用,才能保证最终产品的质量和性能。
随着科学技术的不断进步,相信半导体工艺流程将会不断优化和完善,为半导体产业的发展贡献更多的力量。
扩散的工艺流程

扩散的工艺流程
《扩散的工艺流程》
扩散是一种重要的化工工艺,用于在固体材料之间或在固体和液体之间进行物质交换。
扩散工艺在许多领域都有广泛的应用,包括制造半导体、热处理金属、药物传递等。
扩散的工艺流程通常包括以下几个步骤:
1. 初步准备:在进行扩散之前,首先需要准备好需要进行扩散的材料和介质。
这包括清洗和处理表面,以确保材料表面的纯净度和平整度。
2. 热处理:扩散通常需要高温条件下进行,因此热处理是一个关键的步骤。
材料被置于高温炉中进行加热,以促进扩散的进行。
3. 扩散介质选择:选择合适的介质对于扩散的进行是非常重要的。
一般来说,气体、液体和固体都可以作为扩散介质。
4. 扩散过程:一旦准备好材料和介质,扩散过程就可以进行了。
材料置于介质中,并在一定的时间和温度条件下进行扩散操作。
5. 控制扩散速率:在扩散过程中,需要对扩散速率进行控制。
这可以通过调节温度、压力和介质浓度来实现。
6. 结果分析:一旦扩散完成,需要对扩散结果进行分析。
这包
括检测扩散的深度和速率,以及材料的性能变化情况。
扩散工艺流程需要严格控制各个环节,以确保最终的扩散效果符合预期。
同时,还需要对扩散过程中的安全性进行充分考虑,以确保操作过程稳定可靠。
通过严谨的工艺流程,扩散工艺可以为各种领域提供高质量的材料和产品。
扩散工艺流程

扩散炉开关机作业
• 关机操作 • 2.1 关机前检查确认内容: • 2.1.1 关闭加热。按加热停止按钮前先将温度设定为0时 方可关闭加热停止按钮。 • 2.1.2 关闭扩散炉监控系统。双击屏幕上“扩散炉监控系 统” 图标,输入密码登陆监控系统软件。 • 2.1.3 关闭计算机。按下"计算机关机"按钮。 • 2.1.4 关闭控制电源。按下电控柜面板上的“关机”按钮, 即关闭该炉管的控制电源。 • 2.1.5 关闭BV100恒温水槽。按关机按钮3秒以上。 • 2.1.6 关闭电控柜电源开关。 • 2.1.7 关闭冷却水。当炉温度降至50度以下,方可关闭冷 却水水阀。
• • •
•
进舟标准作业
• 注意事项 • 严禁擅自更改扩散炉各种工艺参数和舟速 • 上下炉内的浆不能同时进出,防止交叉污 染。 • 保持石英叉的洁净,不允许用手触摸石英 管套。上下班均需用沾有异丙醇的干净的 无尘布擦拭。
下片标准作业
下片标准作业
• 扩散结束后,关闭小N2和O2,将石英舟缓缓退至炉口,降温以后,用 舟叉从臂桨上取下石英舟。并立即放上新的石英舟,进行下一轮扩散。 • 出舟时注意浆上有无偏磷酸液体,如有要及时清除,避免污染设备和 危害人员安全。取舟时要等浆停稳了之后再取,先取前舟,再取后舟, 不要将舟靠身体太近避免烫伤和被热气灼伤。挑出的舟要放到相应的 石英凳上,前舟放靠里的石英凳,后舟放靠外的石英凳 • 如没有待扩散的硅片,将臂浆推入扩散炉,尽量缩短臂桨暴露在空气 中的时间。 (小于20分钟)。 • 进出炉在确保安全的基础上尽量提高挑舟进炉和出炉的速度 • 为防止操作台区域的偏磷酸聚集滴落到下方的运行的舟和硅片上,每 班至少清理两次该区域产生的偏磷酸液体。
质检标准作业
质检标准作业
半导体ddpf工艺流程

半导体ddpf工艺流程Semiconductor DDPF technology, also known as double diffusion process with polycrystalline and field oxide, is a crucial process in the fabrication of integrated circuits. 半导体DDPF技术,也称为双扩散工艺与多晶和场氧化物,在集成电路制造过程中是一个至关重要的工艺。
It involves the formation of both n-type and p-type doped regions ona silicon substrate, which is essential for the creation of various electronic components on the chip. 它涉及在硅衬底上形成n型和p型掺杂区域,这对于在芯片上创建各种电子元件是必不可少的。
The DDPF process consists of several key steps, including oxidation, diffusion, and deposition, which are meticulously controlled to ensure the desired electrical properties and performance of the resulting integrated circuits. DDPF工艺包括几个关键步骤,包括氧化、扩散和沉积,这些步骤都经过精心控制,以确保最终集成电路的所需电气特性和性能。
Understanding the DDPF technology from a manufacturing perspective is essential in order to appreciate the complexities involved in producing high-quality semiconductor devices. 从制造角度了解DDPF技术对于欣赏生产高质量半导体器件所涉及的复杂性至关重要。
多晶硅硅扩散工艺流程

多晶硅硅扩散工艺流程英文回答:Silicon diffusion is a crucial process in the fabrication of multi-crystalline silicon (mc-Si) solar cells. It involves the introduction of impurities into the silicon wafer to create regions with different electrical properties, such as p-type and n-type doping. This allows for the formation of pn junctions, which are essential for the functioning of solar cells.The silicon diffusion process typically consists of several steps, including cleaning, surface passivation, and doping. Let me walk you through each step in more detail.First, the silicon wafer is thoroughly cleaned to remove any contaminants or oxides on the surface. This is usually done using a combination of chemical etching and rinsing with deionized water. The goal is to create a clean and smooth surface for subsequent processing steps.Next, a thin layer of passivation material is deposited on the wafer surface. This passivation layer helps to reduce surface recombination and improve the overall efficiency of the solar cell. Common passivation materials include silicon nitride (SiNx) and aluminum oxide (Al2O3).After passivation, the wafer is ready for the diffusion step. This is where the impurities are introduced into the silicon lattice to create the desired doping profile. The most commonly used dopants for mc-Si solar cells are phosphorus (P) for n-type doping and boron (B) for p-type doping.One technique commonly employed for silicon diffusion is the use of a dopant source, such as a phosphorus or boron-containing gas. The wafer is placed in a diffusion furnace, and the dopant gas is introduced at high temperatures. The dopant atoms diffuse into the silicon lattice, replacing some of the silicon atoms and creating the desired doping profile.The diffusion process is typically carried out at temperatures ranging from 800 to 1100 degrees Celsius, depending on the specific dopant and desired doping profile. The duration of the diffusion process also varies, but it can range from a few minutes to several hours.Once the diffusion is complete, the wafer is then subjected to various annealing and activation steps to activate the dopants and repair any defects introduced during the diffusion process. These steps help to improve the electrical properties of the solar cell and optimizeits performance.In summary, the silicon diffusion process in mc-Sisolar cell fabrication involves cleaning, passivation, and doping steps. It is a critical process that determines the electrical properties of the solar cell and its overall performance.中文回答:多晶硅硅扩散是光伏电池制造过程中的关键步骤之一。
晶圆制造流程

晶圆制造过程集成电路的生产从抛光硅片的下料开始。
图4.16的截面图按顺序展示了构成一个简单的MOS栅极硅晶体管结构所需要的基础工艺。
每一步工艺生产的说明如下:第一步:增层工艺。
对晶圆表面的氧化会形成一层保护薄膜,它可作为掺杂的屏障。
这层二氧化硅膜被称为场氧化层。
第二步:光刻工艺。
光刻制程在场氧化层上开凹孔以定义晶体管的源极、栅极和漏极的特定位置。
第三步:增层工艺。
接下来,晶圆将经过二氧化硅氧化反应加工。
晶圆暴露的硅表面会生长一层氧化薄膜。
它可作为栅极氧化层。
第四步:增层工艺。
在第四步,晶圆上沉积一层多晶硅作为栅极构造的。
第五步:光刻工艺。
在氧化层/多晶硅层按电路图形刻蚀的两个开口,它们定义了晶体管的源极和漏极区域。
第六步:掺杂工艺。
掺杂加工用于在源极和漏极区域形成N阱。
第七步:增层工艺。
在源极和漏极区域生长一层氧化膜。
第八步:光刻工艺。
分别在源极、栅极和漏极区域刻蚀形成的孔,称为接触孔。
第九步:增层工艺。
在整个晶圆的表面沉积一层导电金属,该金属通常是铝的合金。
第十步:光刻工艺。
晶圆表面金属镀层在芯片和街区上的部分按照电路图形被除去。
金属膜剩下的部分将芯片的每个元件准确无误地按照设计要求互相连接起来。
第十一步:热处理工艺。
紧随金属刻加工后,晶圆将在氮气环境下经历加热工艺。
此步加工的目的是使金属与源、漏、栅极进一步熔粘以获得更好的电性接触连结。
第十二步:增层工艺。
芯器件上的最后一层是保护层,通常被称为防刮层或钝化层(在图4.5中没有列出)。
它的用途是使芯片表面的元件在电测,封装及使用时得到保护。
第十三步:光刻工艺。
在整个工艺加工序列的最后一步是将钝化层的位于芯片周边金属引线垫上的部分刻蚀去。
这一步被称为引线垫掩膜(在图4.6中没有列出)。
这个十二步的工艺流程举例阐述了这四种最基本的工艺方法是如何应用到制造一个具体的晶体管结构的。
电路所需的其它元件(二极管、电阻器和电容)也同时在电路的不同区域上构成。
晶界扩散表面涂覆工艺流程

晶界扩散表面涂覆工艺流程英文回答:Surface coating is a widely used technique in various industries, including the field of diffusion at grain boundaries. The process involves applying a thin layer of coating material onto the surface of a material to enhance its properties and protect it from corrosion, wear, orother forms of damage. In the context of grain boundary diffusion, the surface coating process plays a crucial role in controlling the diffusion behavior at the grain boundaries.The process of surface coating for grain boundary diffusion typically involves several steps. First, the surface of the material to be coated is cleaned thoroughlyto remove any contaminants or impurities that may hinderthe adhesion of the coating material. This step isessential to ensure a strong bond between the coating and the substrate. Cleaning can be done through various methods,such as chemical cleaning, mechanical cleaning, or a combination of both.Once the surface is clean, a suitable coating material is selected based on the specific requirements of the application. The choice of coating material depends on factors such as the desired properties, the compatibility with the substrate material, and the environmental conditions the coated material will be exposed to. Common coating materials used in grain boundary diffusion include metals, ceramics, polymers, and composites.After selecting the coating material, it is applied onto the surface using a suitable technique. There are several methods available for surface coating, including spraying, dipping, electroplating, and chemical vapor deposition. The choice of coating technique depends on factors such as the type of coating material, the desired thickness of the coating, and the complexity of the substrate geometry.Once the coating is applied, it is subjected to acuring or drying process to ensure its adhesion and stability. This step may involve heating the coated material to a specific temperature or exposing it to a controlled environment for a certain period. The curing process helps in the formation of strong bonds between the coating material and the substrate, enhancing thedurability and performance of the coated material.In summary, the surface coating process for grain boundary diffusion involves cleaning the surface, selecting a suitable coating material, applying the coating using a suitable technique, and curing the coating to ensure its adhesion and stability. This process is crucial in controlling the diffusion behavior at grain boundaries and enhancing the properties of the coated material.中文回答:晶界扩散表面涂覆工艺是各个行业广泛使用的一种技术,包括晶界扩散领域。
半导体的生产工艺流程

半导体的生产工艺流程,做工艺一、洁净室一般的机械加工是不需要洁净室(clean room)的,因为加工分辨率在数十微米以上,远比日常环境的微尘颗粒为大。
但进入半导体组件或微细加工的世界,空间单位都是以微米计算,因此微尘颗粒沾附在制作半导体组件的晶圆上,便有可能影响到其上精密导线布局的样式,造成电性短路或断路的严重后果。
为此,所有半导体制程设备,都必须安置在隔绝粉尘进入的密闭空间中,这就是洁净室的来由。
洁净室的洁净等级,有一公认的标准,以class 10为例,意谓在单位立方英呎的洁净室空间内,平均只有粒径0.5微米以上的粉尘10粒。
所以class后头数字越小,洁净度越佳,当然其造价也越昂贵(参见图2-1)。
为营造洁净室的环境,有专业的建造厂家,及其相关的技术与使用管理办法如下:1、内部要保持大于一大气压的环境,以确保粉尘只出不进。
所以需要大型鼓风机,将经滤网的空气源源不绝地打入洁净室中。
2、为保持温度与湿度的恒定,大型空调设备须搭配于前述之鼓风加压系统中。
换言之,鼓风机加压多久,冷气空调也开多久。
3、所有气流方向均由上往下为主,尽量减少突兀之室内空间设计或机台摆放调配,使粉尘在洁净室内回旋停滞的机会与时间减至最低程度。
4、所有建材均以不易产生静电吸附的材质为主。
5、所有人事物进出,都必须经过空气吹浴(air shower) 的程序,将表面粉尘先行去除。
6、人体及衣物的毛屑是一项主要粉尘来源,为此务必严格要求进出使用人员穿戴无尘衣,除了眼睛部位外,均需与外界隔绝接触(在次微米制程技术的工厂内,工作人员几乎穿戴得像航天员一样。
) 当然,化妆是在禁绝之内,铅笔等也禁止使用。
7、除了空气外,水的使用也只能限用去离子水(DI water, de-ionized water)。
一则防止水中粉粒污染晶圆,二则防止水中重金属离子,如钾、钠离子污染金氧半(MOS) 晶体管结构之带电载子信道(carrier channel),影响半导体组件的工作特性。
mos晶体管制造工艺流程

mos晶体管制造工艺流程MOS晶体管(Metal-Oxide-Semiconductor Field-Effect Transistor)是一种常见的半导体器件,广泛应用于集成电路中。
它由金属-氧化物-半导体结构组成,其制造工艺流程包括多个步骤。
制造MOS晶体管的第一步是选择合适的硅片作为基底。
硅片通常是由高纯度的单晶硅制成,其表面需要经过清洗和处理,以去除杂质和不均匀性。
接下来,进行掺杂。
掺杂是向硅片中引入杂质,以改变硅片的导电性能。
这一步骤通常包括两个主要的过程:扩散和离子注入。
扩散是通过加热硅片使杂质扩散到硅片中,而离子注入是将杂质离子注入硅片中。
通过控制掺杂过程的条件,可以在硅片上形成不同的导电区域。
然后,进行氧化。
氧化是在硅片表面形成氧化层,以保护硅片和调整硅片表面的性质。
氧化可以通过热氧化或化学气相沉积等方法实现。
氧化层的厚度和性质对MOS晶体管的性能有重要影响。
接下来,进行沉积。
沉积是在硅片表面沉积一层薄膜,用于形成MOS晶体管的栅极、源极和漏极等结构。
常用的沉积方法包括物理气相沉积、化学气相沉积和物理溅射等。
之后,进行光刻。
光刻是通过在硅片上涂覆光刻胶、曝光和显影等步骤,将芯片的图形图案转移到硅片上。
光刻胶光刻胶是一种光敏物质,可以通过曝光和显影来形成所需的图案。
接下来,进行蚀刻。
蚀刻是利用化学反应或物理方法将不需要的材料从硅片表面去除。
蚀刻可以选择性地去除硅片上的某些区域,以形成所需的结构。
进行后续工艺步骤。
这些步骤包括金属沉积、热处理、封装等。
金属沉积用于形成晶体管的金属连接线,热处理用于改善晶体管的性能,封装用于保护晶体管并提供外部连接。
通过以上步骤,MOS晶体管的制造工艺就完成了。
整个制造过程需要严格控制各个步骤的条件和参数,以确保晶体管的性能和可靠性。
随着技术的不断发展,制造工艺也在不断改进,以实现更高的集成度和性能。
二极管工厂制作工艺流程

二极管工厂制作工艺流程二极管的制作呀,那可是个挺有趣的事儿呢。
一、原材料准备。
做二极管得先有材料呀。
就像盖房子得有砖头水泥一样。
硅片是很关键的原材料,它就像是二极管的身体骨架。
这硅片可得是质量不错的,纯度要高,这样才能保证后面二极管的性能。
除了硅片,还有一些掺杂剂之类的东西。
这些掺杂剂就像是给硅片加调料,让硅片能有不同的电学特性。
比如说,加入硼或者磷这些元素,就可以改变硅片的导电类型。
这些原材料的选择和准备呀,就像是给一场精彩演出挑选演员,每个都得精挑细选才行。
二、芯片制造。
这芯片制造可是二极管制作的核心环节呢。
首先得对硅片进行光刻。
光刻这个词听起来就很高级,其实就像是在硅片上画画一样。
用特殊的光把设计好的电路图案印到硅片上,这图案可精确着呢,一丝一毫都不能差。
然后就是蚀刻啦,蚀刻就像是把光刻好的图案进行雕刻,把不需要的部分去掉,只留下我们想要的电路结构。
这个过程得小心翼翼的,就像雕刻一件艺术品一样。
蚀刻完了之后呢,就是扩散工艺。
扩散就是让那些掺杂剂在硅片里按照我们想要的方式分布,这就像是让调料均匀地分布在食物里,这样做出来的二极管才会有稳定的电学性能。
在芯片制造的过程中,每一个步骤都像是在精心打造一件独一无二的宝贝,每个环节都不能马虎。
三、封装环节。
芯片做好了,可不能就这么光着呀,得给它穿上“衣服”,这就是封装环节。
封装的材料也是很有讲究的。
一般会用塑料或者陶瓷之类的材料。
把芯片放到封装壳里,就像是把一颗珍贵的宝石放到一个精美的盒子里。
在封装的时候,还得把芯片的电极引出来,这就像是给宝石接上链子,让它能和外界连接起来。
封装这个过程呀,不仅要保护好芯片,还得让二极管能方便地在电路板上使用。
封装完了之后,二极管就有了自己的小天地,可以出去闯荡啦。
四、测试阶段。
二极管做好了,可不能就直接出厂呀。
得经过严格的测试呢。
就像学生要考试一样。
测试的时候,会检查二极管的电学性能,比如说正向电压、反向电流之类的参数。
半导体生产工艺流程

半导体的生产工艺流程微机电制作技术,尤其是最大宗以硅半导体为基础的微细加工技术(silicon-basedmicromachining),原本就肇源于半导体组件的制程技术,所以必须先介绍清楚这类制程,以免沦于夏虫语冰的窘态。
一、洁净室一般的机械加工是不需要洁净室(cleanroom)的,因为加工分辨率在数十微米以上,远比日常环境的微尘颗粒为大。
但进入半导体组件或微细加工的世界,空间单位都是以微米计算,因此微尘颗粒沾附在制作半导体组件的晶圆上,便有可能影响到其上精密导线布局的样式,造成电性短路或断路的严重后果。
为此,所有半导体制程设备,都必须安置在隔绝粉尘进入的密闭空间中,这就是洁净室的来由。
洁净室的洁净等级,有一公认的标准,以class10为例,意谓在单位立方英呎的洁净室空间内,平均只有粒径0.5微米以上的粉尘10粒。
所以class后头数字越小,洁净度越佳,当然其造价也越昂贵。
为营造洁净室的环境,有专业的建造厂家,及其相关的技术与使用管理办法如下:1、内部要保持大于一大气压的环境,以确保粉尘只出不进。
所以需要大型鼓风机,将经滤网的空气源源不绝地打入洁净室中。
2、为保持温度与湿度的恒定,大型空调设备须搭配于前述之鼓风加压系统中。
换言之,鼓风机加压多久,冷气空调也开多久。
3、所有气流方向均由上往下为主,尽量减少突兀之室内空间设计或机台摆放调配,使粉尘在洁净室内回旋停滞的机会与时间减至最低程度。
4、所有建材均以不易产生静电吸附的材质为主。
5、所有人事物进出,都必须经过空气吹浴(airshower)的程序,将表面粉尘先行去除。
6、人体及衣物的毛屑是一项主要粉尘来源,为此务必严格要求进出使用人员穿戴无尘衣,除了眼睛部位外,均需与外界隔绝接触(在次微米制程技术的工厂内,工作人员几乎穿戴得像航天员一样。
)当然,化妆是在禁绝之内,铅笔等也禁止使用。
7、除了空气外,水的使用也只能限用去离子水(DIwater,de-ionizedwater)。
太阳能电池制造工艺工艺流程以及工序介绍
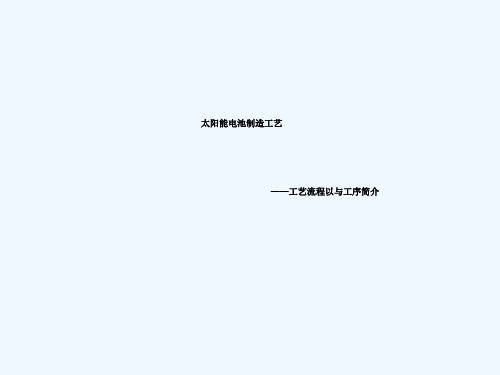
(c). 去磷硅玻璃---PSG 在扩散过程中发生如下反应:
4 P C l 5 O 2 P O 6 C l POCl3分解产生的P2O5淀积在硅片表面, P2O5与Si反应生成SiO2和磷原子:
32
25
2
这样就在硅片表面形成一层含有磷元素的SiO2,称之为磷硅玻璃。 去除磷硅玻璃的目的、作用:
太阳能电池制造工艺 ——工艺流程以与工序简介
硅太阳能电池的结构与其工作原理: 磷扩散层
1.前言
其主要是利用硅半导体p-n结的光生伏打效应。 即当太阳光照射p-n结时,便产生了电子-空穴对, 并在内建电场的作用下,电子驱向n型区,空穴 驱向p型区,从而使n区有过剩的电子,p区有过 剩的空穴,于是在p-n结的附近形成了与内建电 场方向相反的光生电场。在n区与p区间产生了电 动势。当接通外电路时便有了电流输出。
(b). 多晶制绒---RENA InTex
3 S 目i 的 与2 作H 用N :O 3 1 8 H F 3 H 2 S i F 6 0 . 4 5 N O 1 . 3 5 N O 2 0 . 1 N 2 O 4 . 2 5 H 2 2 . 7 5 H 2 O
(1)去除单晶硅片表面的机械损伤层和氧化层。 (2)有效增加硅片对入射太阳光的吸收,从而提高光生电流 密度,提高单晶硅太阳能电池的光电转换效率。
1)、硅太阳能电池的制造工艺流程:
捷佳创单晶制绒
扩 散 工 序
RENA多晶制绒 制绒清洗工序
丝
网
印
工 序
刷 工 序Laser P源自CVD烧 结工工
序
序
测 试 分 选 工 序
去除磷硅玻璃PSG
成品硅太阳能电池
1.原料硅片清洗制绒 12.测试分选
Wafer Process工艺制造流程

介绍:
19
可以淀积多种薄膜。
服务指南
淀积薄膜 类型
淀积材料
工作温度 腔体压力
工作方式
SiN、SiO2、 SiH4、NH3、N2、
SiON、PSG、 N2O、Ar 等
α-Si 等
250~350 度
650~ 2000mt
HF power/pulse、 LF power/pulse 等
3.1.7 键合工艺
一般的光刻流程包括前处理、匀胶、前烘、对准曝光、显影、后烘,
可以根据实际情况调整流程中的操作。目前提供单面接触式对准光
刻、双面接触式对准光刻服务。
处理材料:衬底材料直径 100mm,厚度 400-5000um。
(1)单面接触式对准光刻
11
服务指南
光刻胶类型 光刻胶厚度 最小线宽
Shipley 6112 0.5-2.0um
扩散炉
处理面数:双面
片数/批 : 最多 48 片
检 验:方块电阻偏差+/-5%,结深+/-5%
3.1.4 光刻
简 介:光刻工艺是微机械技术里用得最频繁,最关键得技术之一,
光刻工艺将掩膜图形转移到衬底表面的光刻胶图形上,根据曝光方式
可分为接触式、接近式和投影式,根据光刻面数的不同有单面对准光
刻和双面对准光刻,根据光刻胶类型不同,有薄胶光刻和厚胶光刻。
处理面数:双面
片数/批 : 25
14
服务指南
腐蚀槽
(2)干法刻蚀
STS 硅深反应离子刻蚀
配方
选择比
腐蚀速率 腐蚀性质 设备
备注
硅:光刻胶(50:1) 0.5- 标准
硅:氧化硅(150:1) 2um/min
各种水处理工艺流程
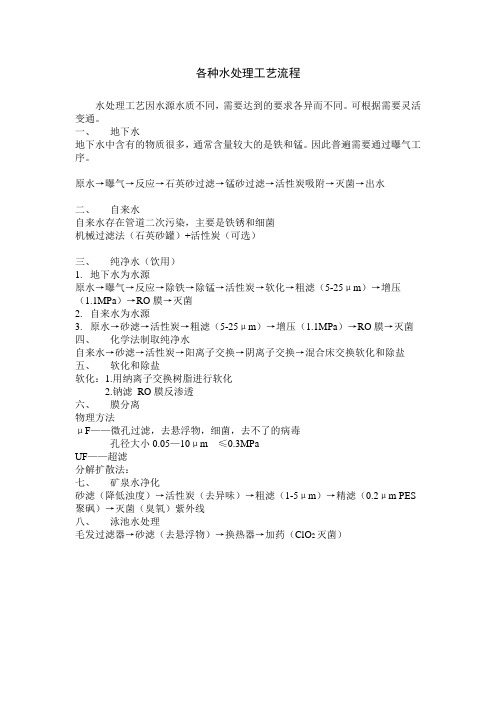
各种水处理工艺流程
水处理工艺因水源水质不同,需要达到的要求各异而不同。
可根据需要灵活变通。
一、地下水
地下水中含有的物质很多,通常含量较大的是铁和锰。
因此普遍需要通过曝气工序。
原水→曝气→反应→石英砂过滤→锰砂过滤→活性炭吸附→灭菌→出水
二、自来水
自来水存在管道二次污染,主要是铁锈和细菌
机械过滤法(石英砂罐)+活性炭(可选)
三、纯净水(饮用)
1.地下水为水源
原水→曝气→反应→除铁→除锰→活性炭→软化→粗滤(5-25μm)→增压(1.1MPa)→RO膜→灭菌
2.自来水为水源
3.原水→砂滤→活性炭→粗滤(5-25μm)→增压(1.1MPa)→RO膜→灭菌
四、化学法制取纯净水
自来水→砂滤→活性炭→阳离子交换→阴离子交换→混合床交换软化和除盐五、软化和除盐
软化:1.用纳离子交换树脂进行软化
2.钠滤RO膜反渗透
六、膜分离
物理方法
μF——微孔过滤,去悬浮物,细菌,去不了的病毒
孔径大小0.05—10μm ≤0.3MPa
UF——超滤
分解扩散法:
七、矿泉水净化
砂滤(降低浊度)→活性炭(去异味)→粗滤(1-5μm)→精滤(0.2μm PES 聚砜)→灭菌(臭氧)紫外线
八、泳池水处理
毛发过滤器→砂滤(去悬浮物)→换热器→加药(ClO2灭菌)。
- 1、下载文档前请自行甄别文档内容的完整性,平台不提供额外的编辑、内容补充、找答案等附加服务。
- 2、"仅部分预览"的文档,不可在线预览部分如存在完整性等问题,可反馈申请退款(可完整预览的文档不适用该条件!)。
- 3、如文档侵犯您的权益,请联系客服反馈,我们会尽快为您处理(人工客服工作时间:9:00-18:30)。
扩散炉开关机作业
• • • • • • • • • • • • • • • • • • • • 1.开机操作 开机操作 1.1开机前检查确认内容: 1.1.1 检查电源。打开电控柜电源开关。确定整机上电正常,电源指示灯亮。 1.1.2 检查气源。确定氧气、压缩空气、氮气的压力为 0.4-0.6MPa。 1.1.3 检查排气系统。检查各风口排风应有风吸出。 1.1.4 检查水源。确定冷却水进出水阀应在打开状态。 1.1.5 检查源瓶。确认源瓶上的进气出气阀门已打开,各接口连接正常。 1.1.6 检查BV100恒温水槽。确定温度正常。如需开关机,按开关机按钮3秒以上。 1.1.7 检查急停按扭。确定按扭正常。 1.2其它检查内容: 1.2.1 检查净化台。应干净,无废液,无其它物品。 1.2.2 检查接液槽。各面应干净,无废液。 1.2.3 检查气源柜。各面应干净,无废液。 1.2.4 检查BV100水槽。水面正常,水中无杂物。 1.3开启监控系统: 1.3.1 启动计算机。按下电控柜面板上的“上电”按钮 。 1.3.2 启动扩散炉监控系统。双击屏幕上“扩散炉监控系统” 图标,输入密码登陆监 控系统软件。 1.3.3 启动加热。按加热按钮前先将温度设定为0才可操作。 1.3.4 当加热按钮按下后加热指示灯亮时,开机完成。
• • •
•
进舟标准作业
• 注意事项 • 严禁擅自更改扩散炉各种工艺参数和舟速 • 上下炉内的浆不能同时进出,防止交叉污 染。 • 保持石英叉的洁净,不允许用手触摸石英 管套。上下班均需用沾有异丙醇的干净的 无尘布擦拭。
下片标准作业
下片标准作业
• 扩散结束后,关闭小N2和O2,将石英舟缓缓退至炉口,降温以后,用 舟叉从臂桨上取下石英舟。并立即放上新的石英舟,进行下一轮扩散。 • 出舟时注意浆上有无偏磷酸液体,如有要及时清除,避免污染设备和 危害人员安全。取舟时要等浆停稳了之后再取,先取前舟,再取后舟, 不要将舟靠身体太近避免烫伤和被热气灼伤。挑出的舟要放到相应的 石英凳上,前舟放靠里的石英凳,后舟放靠外的石英凳 • 如没有待扩散的硅片,将臂浆推入扩散炉,尽量缩短臂桨暴露在空气 中的时间。 (小于20分钟)。 • 进出炉在确保安全的基础上尽量提高挑舟进炉和出炉的速度 • 为防止操作台区域的偏磷酸聚集滴落到下方的运行的舟和硅片上,每 班至少清理两次该区域产生的偏
卸片标准作业
卸片标准作业
卸片标准作业
• 卸片时, 卸舟人员一定要戴PVC手套,袖子也要用皮筋扎住,防止污染硅 片.先把之前质检人员取测试片时留下的6片单片取出,放在最下面, 注意扩散面朝向。在卸片之前要检查片子是否有破裂等异常现象。 • 硅片放在卸片台上要摆放整齐。在卸片过程中如发现烧焦、清洗不净 等异常片要取出放一边,记清片子所处的舟中位置并立即通知工艺人 员。 • 等卸完一舟后,将硅片从卸片台上取下,并整理整齐后,放入到硅片 盒中。 • 将装好、整理好的片夹连同流程单一并通过传递窗传到刻蚀处,流程 单上要填好下传的硅片数目。 • 注意事项 • 卸舟的镊子不能与其它岗位混用,防止交叉污染。不要解触除镊子头。 • 注意挡片不要取。
换源标准作业
换源标准作业
换源标准作业
• • 领取源瓶规定实行“五双”的方式,即:双人领取、双人检查、双人运输、双人更换、双人处理的 原则,确保整个换源过程的安全性,领取源瓶时要注意发现源箱上有无经过质检部检查后张贴的红 标签,如有标签则说明该源合格可以使用,如果没有标签则禁止使用。 2、在检查新源瓶以前要对源瓶包装箱的外表面进行彻底打扫,确保进入车间的源箱表面灰尘少不 会对车间洁净度形成太大影响;打开源箱,将源瓶上部的保护垫拿开,将源瓶带外部透明塑料包装 轻轻从箱中拿出,将源瓶放在平稳的地方,拆开源瓶外包装塑料袋;左手托住源瓶底部,右手轻握 源瓶上部,观察源瓶的外表看瓶身是否有外观缺陷,如裂纹等,包装内是否有液滴,如存在以上现 象则源瓶不能使用 3、用PH试纸对源瓶所有的接口和接头螺母、开关阀门进行检测,看是否存在蒸汽泄漏现象,如果 试纸呈红色酸性则为漏源应该把源瓶立刻封箱退回,如正常则继续进行。打开源箱,将源瓶取出平 稳的放在换源操作台上,去掉瓶外包装对源瓶各个螺母、阀门进行外观复检。用PH试纸测试源瓶 各个接头螺母和阀门,对之进行测试性复检,如正常暂时搁置,开始拆卸旧源瓶。 4、旧源的拆卸:按照顺时针方向,先关闭源瓶进气口阀门(接口部分较细),再关闭出气口阀门 (接口部分较粗),拆下源瓶与导气管各个进出气口接头。断开源瓶与气管的接头,将导气管的两 个气管接头暂时用手套包住,防止气管接头污染。将源瓶从恒温槽内慢慢的取出,把瓶身外表的水 用无尘纸擦拭去,然后将瓶放入原来新源包装袋中装入箱子。 5、新源安装:左手握住源瓶接头部分,右手托住源瓶底部,将瓶搬到恒温槽,瓶底暂时放在槽上 右手也握住瓶另一接头部分,将源瓶慢慢放入槽内,将源瓶进出气阀门与炉子导气管阀门对应连接 起来,导气管细管与源瓶进气管连接,导气管粗管与源瓶出气管对应连接。用换源专用扳手将连接 好的接头上紧,同时将源瓶阀门下的螺母按照逆时针方向轻度旋转一圈,注意力度。 6、连接完毕后按照先开出气阀门后开进气阀门的原则依次打开源瓶气体阀门,并用PH试纸对各个 接头阀门、螺母进行检测确认源瓶密封性是否良好,并察看通源工艺运行情况。 7、如通源状况确认正常后对更换的源瓶进行记录,并将装箱后的旧源瓶放入化学通道内作处理。 8、脱去防护用品并将防护用品张挂于专门的区域内,对于出现损坏的用品要做及时的处理,不可 再使用。
扩散工艺操作规范
多晶扩散目的:形成P-N结 制造一个PN结并不是把两块不同类 型(p型和n型)的半导体接触在以 起就能形成的。 必须使一块完整的半导体晶体的一 部分是P型区域,另一部分是N型区 域。 也就是在晶体内部实现P型和N型半 导体的接触 。
扩散间洁净度、温度、 扩散间洁净度、温度、湿度
• • 洁净度: 洁净度:千级净化间,净化插片台(净化度:100级)、净化保护柜(净化度:100级) 温度:23±2℃ 湿度:<50% 温度: ± ℃ 湿度:
进舟标准作业
进舟标准作业
• • 硅片进炉时首先要检查舟内硅片摆放有无错槽现象;然后用舟叉挑舟进炉。 挑石英舟时双手握紧叉柄,轻轻对准舟两端的小孔,注意不要触碰到硅片; 当舟叉三分之二插进舟内时轻轻抬起石英舟,舟的前端(远离身体的一端) 微翘,与地面形成小角度倾角,在挑舟过程中要注意脚下和四周行人,避免 发生碰撞。到达炉边轻轻将是石英舟放在浆上,放稳之后把舟叉缓慢的从小 孔中拔出,不要两个同时拔出,一个舟叉先扶着舟另一个往外拔,然后再拔 第二个。如遇困难不能拔出,切勿硬拔,可以一边轻轻地旋转一边往外拔。 前舟(炉尾)放稳之后再用相同的方法挑后舟(炉口)。两个舟都放稳之后 检查舟是否在恒温区内(前轴尽量靠近匀流板)。 监督扩散炉是否运行正常,包括运行过程中的工艺参数和运行时间是否正常 以及设备有无报警,并在记录本上记录炉管运行工艺时的各个气体流量。 出舟时注意浆上有无偏磷酸液体,如有要及时清除,避免污染设备和危害人 员安全。取舟时要等浆停稳了之后再取,先取后舟(炉口),再取前舟(炉 尾),不要将舟靠身体太近避免烫伤和被热气灼伤。挑出的舟要放到相应的 石英凳上,前舟放靠里的石英凳,后舟放靠外的石英凳。 进出炉在确保安全的基础上尽量提高挑舟进炉和出炉的速度,减少浆在外面 停留时间。为防止操作台区域的偏磷酸聚集滴落到下方的运行的舟和硅片上, 每班至少清理两次该区域产生的偏磷酸液体。
多晶扩散流程图
下料 插片 上片 扩散 下片 质检 卸片 转入镀膜工序 异常处理
下料标准作业
插片标准作业
• • • • • • • • • • 先把空舟上挡片分别放到舟的挡片位置(处于舟的两边的第一个槽)。 双手把载满片子的载片篮搬到舟的下位(舟和操作员之间的空位上)。 用真空吸笔将片子插入石英舟中。装舟时要从左边一直装到右边。 装好一舟后放到相应的空位置,装好的另一舟也要和第一舟一样放到 一起,摆放整齐。等待进炉。 记录流程单,并把相关信息记录到装舟记录单上。 注意事项: 注意事项: 在装片时,注意硅片绒面状况,尽量将绒面好的一面做为扩散面,尽 量将蹦边、缺角和小裂纹片装入石英舟中。 禁止单手搬载片篮,防治因载片篮过重而摔片。 以3°的倾斜角轻轻插入舟槽内,注意要插到舟的底部,尽量防止与 舟杠磕碰;注意任何物体均不可从舟上过,防止污染 装好每一组硅片时都要摆放整齐,注意核对硅片数目。
质检标准作业
质检标准作业
质检标准作业
• 从扩散完毕的两舟硅片中从炉尾方向向炉口方向按第5片、中间片、第3片(前舟), 第3片、中间片、第五片(后舟)的顺序抽取测试片放入花篮中,六片均匀分布,先取 前舟(炉尾),再取后舟(炉口) 测试片放入篮内注意方向是否正确,硅片的正面(扩散面)朝向花篮的圆孔方向。 四探针方阻测试仪:测量电阻之前要调试仪器(电流为4532mA),测量时要注意取片 的操作方式,一手拿镊子将硅片放在测试台上,另一只手拿镊子固定硅片的位置,测 试硅片时注意探针压硅片的程度要适中,读完数据后将硅片的一角滑出测试台,以免 压碎。 少子寿命测试仪:测量电阻时要注意取片的操作方式,一手拿镊子将硅片放在测试台 上,另一只手拿镊子固定硅片的位置,测试硅片时注意放置硅片位置要适中,按照 Recorder-Autosetting-Runtime-New的顺序来测试,完成后将硅片的一角滑出测试台, 并记录数据。 各班每天接班时必须用无尘布蘸取乙醇或异丙醇拭擦少子寿命测试仪、四探针方阻测 试仪和电脑。
•
•
•
• • •
扩散炉开关机作业
• 关机操作 • 2.1 关机前检查确认内容: • 2.1.1 关闭加热。按加热停止按钮前先将温度设定为0时 方可关闭加热停止按钮。 • 2.1.2 关闭扩散炉监控系统。双击屏幕上“扩散炉监控系 统” 图标,输入密码登陆监控系统软件。 • 2.1.3 关闭计算机。按下"计算机关机"按钮。 • 2.1.4 关闭控制电源。按下电控柜面板上的“关机”按钮, 即关闭该炉管的控制电源。 • 2.1.5 关闭BV100恒温水槽。按关机按钮3秒以上。 • 2.1.6 关闭电控柜电源开关。 • 2.1.7 关闭冷却水。当炉温度降至50度以下,方可关闭冷 却水水阀。