汽车零部件疲劳试验讲解共40页
1疲劳基本知识和试验方法f

汽车零件快速疲劳试验方法培训教材目录第一章疲劳的基本知识 21.1概述21.2 变动负荷 21.3 疲劳曲线 31.4 疲劳宏观断口 41.5 S-N曲线与疲劳极限的测定 61.6 疲劳的统计学初步9 第二章S-N曲线的快速测定方法132.1 概述132.2 快速测定方法的假定132.3 虚拟子样法142.4 试验验证152.5 小结18 第三章疲劳极限快速测定方法203.1 概述203.2 疲劳极限快速测定方法研究203.3 国内外同类方法对比243.4 小结25附录-固定射点法的试验验证26 第四章汽车零部件疲劳试验评估方法与试验技巧334.1 概述334.2 试验设计334.3 试验机364.4 夹具设计374.5 试件制备384.6 试件异常失效的处理394.7 若干试验技巧40 第五章汽车零件台架疲劳试验信息的采集、分析及应用435.1 引言435.2 试验信息的获取435.3 试验信息的分析与应用445.4 结束语49第一章疲劳的基本知识1.1 概述许多机械零部件如轴、连杆、齿轮、弹簧等,都是在变动载荷作用下工作的,它们工作时所承受的应力通常都低于材料的屈服强度。
机件在这种变动载荷下,经过较长时间工作而发生断裂的现象叫做金属的疲劳。
疲劳断裂与静载荷下的断裂不同,无论是静载荷下显示脆性或韧性的材料,在疲劳断裂是都不产生明显的塑性变形,断裂是突然发生的,因此,具有很大的危险性,常常造成严重的事故。
据统计,在损坏的机械零件中,大部分是由金属疲劳造成的。
因此,研究疲劳断裂的原因,寻找提高材料疲劳抗力的途径以防止疲劳断裂事故的发生,对于发展国民经济有着重大的实际意义。
金属疲劳有各种不同的分类方法。
根据机件所受应力的大小,应力交变频率的高低,通常可分为两类:一类为应力较低,应力交变频率较高情况下产生的疲劳,即通常所说的疲劳或称高周疲劳。
另一类为应力高(工作应力近于或高于材料的屈服强度),应力交变频率低,断裂时应力交变周次少(小于104~105)的情况下产生的疲劳,称为低周疲劳(或称低循环疲劳),也称应变疲劳。
疲劳分析简介 ppt课件

S1 - 10
Stress Amplitude
S-N 方法 – 相似理论
Unnot ched Shaft Notched Shaft Life in Cycles
snom
s nom
The life of this . . . . . . . . . . . . . . . . is the same as the life of this . . . . . if both are subject to the same nominal stress
S1 - 9
S-N 方法
• 也称为应力-寿命和全寿命方法
• 评估产生严重失效的总疲劳寿命
• 疲劳寿命由对数应力-循环(S-N)曲线计算
• 该方法适合于长寿命疲劳失效问题,因为该
方法是基于名义弹性应力,即使有小的塑性
发生。 PAT318A, Section 1, October 2012
Copyright© 2012 MSC.Software Corporation
Fatigue Line)
Elastic (High Cycle Fatigue Line)
PAT318A, Section 1, October 2012 Copyright© 2012 MSC.Software Corporation
N
S1 - 14
S-N和E-N疲劳曲线比较
Low Cycle Region
S1 - 7
Stage II Crack Growth
疲劳寿命计算方法概述
PAT318A, Section 1, October 2012 Copyright© 2012 MSC.Software Corporation
发动机曲轴 疲劳试验
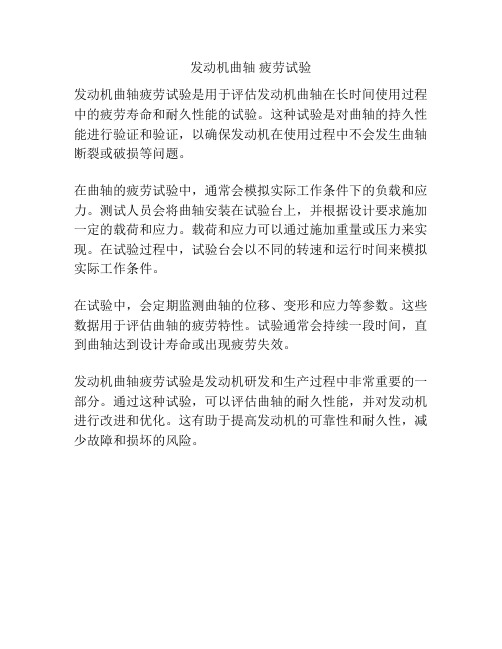
发动机曲轴疲劳试验
发动机曲轴疲劳试验是用于评估发动机曲轴在长时间使用过程中的疲劳寿命和耐久性能的试验。
这种试验是对曲轴的持久性能进行验证和验证,以确保发动机在使用过程中不会发生曲轴断裂或破损等问题。
在曲轴的疲劳试验中,通常会模拟实际工作条件下的负载和应力。
测试人员会将曲轴安装在试验台上,并根据设计要求施加一定的载荷和应力。
载荷和应力可以通过施加重量或压力来实现。
在试验过程中,试验台会以不同的转速和运行时间来模拟实际工作条件。
在试验中,会定期监测曲轴的位移、变形和应力等参数。
这些数据用于评估曲轴的疲劳特性。
试验通常会持续一段时间,直到曲轴达到设计寿命或出现疲劳失效。
发动机曲轴疲劳试验是发动机研发和生产过程中非常重要的一部分。
通过这种试验,可以评估曲轴的耐久性能,并对发动机进行改进和优化。
这有助于提高发动机的可靠性和耐久性,减少故障和损坏的风险。
汽车疲劳耐久性试验道理试验-文档资料

汽车试验认证
认证方法:
样品试制:设计图纸、工艺要求; 道路试验:试验标准和规范、部件\系统\整车技术要求、法规和
限值; 试验室/台架试验:试验标准和规范、部件\系统\整车技术要求、
法规和限值; 数模模拟分析:来自试验规范或设计技术要求的输入载荷、部件
\系统\整车技术要求、法规和限值。
4
汽车试验认证
耐久试验不能完 全反映实际使用
相关:
耐久试验充分 反映实际使用
¥¥¥
不同的认证效率和售后成本
16
车辆使用测量-用途
用户车辆使用
工程设计 技术要求
认证试验规范开发
可靠性(寿命)、 优化设计
耐久、性能预测
发现、消除潜在 失效模式
减少售后索赔和 召回成本
相关
17
车辆使用测量-内容
机构调查 客户投诉
用户需求 开发策略
24
车辆使用测量-结果
承载结构载荷- 循环载荷
10000 1000 100
CyclesCount
10 1
0 40 80 120 160
Strain(ue)
10000 1000 100
CyclesCount
10 1
90%ileEstimate 90%Upperbound 90%Lowerbound
0 40 80 120 160 200
Strain(ue)
25
车辆使用测量-结果
驾驶习惯、装置使用、动力传动系统载荷测量
26
用户车辆使用测量-应用
承载结构载荷-疲劳损伤
局部应力 和应变
雨流统计
材料数据 部件尺寸数据
- 损伤计算 - 线性累积损伤
用户使用/公共道路与试车场试验相对 损伤 百 分 位 用 户 使 用
汽车关键零部件疲劳分析与试验研究

学位论文作者签名:
日期:
年
月
日
指导教师签名:
pdfFactory Pro" 试用版本创建
PDF 文件使用 "pdfFactory Pro" 试用版本创建
北京航空航天大学博士学位论文
摘
要
疲劳寿命是汽车关键零部件的主要设计指标之一。毫无疑问,对疲劳工程师来讲, 最具挑战性的任务就是设计出安全可靠的部件和系统,但又不是过分保守的设计。如果 系统部件不具有足够的疲劳强度,可能会引起永久性破坏和对生命的潜在威胁。另外, 产品召回还会消极影响市场形象。本文以某型商用车后桥壳为研究对象,研究基于虚拟 样机的产品疲劳性能有效计算方法和分析流程,并与产品台架疲劳试验进行关联,成果 对于指导工程产品的疲劳设计和试验具有重要的意义。本文的主要研究内容如下: 建立了综合有限元、 多体动力学和疲劳计算等多学科方法的工程产品虚拟疲劳分析 流程,给出了模型数据在各学科平台上的传递形式和接口关系。使得在产品设计阶段, 便能在产品虚拟样机上进行其最终疲劳性能的估算与优化。增加产品设计的灵活度,降 低产品开发的成本和风险,缩短产品开发的周期。 比较了三种疲劳损伤累积模型,包括线性、非线性和双线性模型。比较了传统疲劳 S-N 曲线和两种计入小循环修正的疲劳损伤计算模型,即 NASA 模型和 Haibach 模型。 通过算例说明各种模型的应用范围及其优劣点,从更方便工程计算且能保证精度的角度 出发,确定了本文中应用线性损伤累积和 Haibach 小循环修正计算疲劳损伤的模型和方 法,为精确计算桥壳疲劳寿命奠定基础。 建立了桥壳整体三维 CAE 模型,通过有限元分析获取其静态应力场;对桥壳匹配 的某型商用车建立了整车动力学模型,通过在不同等级路面上行驶来获取作用在桥壳板 簧座上的随机动载荷。 基于此并调用上述疲劳计算模型进行了整体桥壳多工况下疲劳性 能的计算,并给出了疲劳寿命主要影响因素的敏度分析结果。 建立 了 桥壳 典 型 焊缝特征 的 简 化 疲劳 计 算模 型 , 对 工程 实 践 已经证 明 有 效 的 VOLVO 焊接疲劳计算方法进行消化吸收并对其计算精度进行了修正,修正 VOLVO 方 法则是基于模型中各焊趾节点的挠度比值, 来对焊接刚性和柔性 S-N 曲线进行插值来获 取当前 S-N 曲线,这样能保证计算结果更能符合真实情况。 为了保证上述虚拟计算的准确性,以及为企业后续 CAE 计算积累数据,还针对桥 壳所用材料进行了静强度性能、疲劳性能和焊接疲劳性能的测试工作,对测试结果进行 了数据处理并应用于虚拟计算的相应环节。 通过桥壳台架物理试验,对虚拟计算中的静强度、静刚度和疲劳性能结果进行了对
汽车厂是怎样做疲劳耐久性试验的?

汽车厂是怎样做疲劳耐久性试验的?汽车耐久性试验是为了考核整车、系统、子系统和零部件可靠性的一组试验,疲劳耐久寿命是耐久性试验考核的重点。
在车辆开发领域,耐久性、疲劳、寿命和可靠性这几个概念常常混为一谈,其实他们是有联系又有区别的。
· 汽车的耐久性是指其“保持质量和功能的使用时间”,一般汽车企业对整车耐久性的要求都是XX年或XX万公里,为了达到整车的耐久性,就需要整车、系统、子系统和零件分别满足各自的耐久性要求。
·疲劳是指试件或构件材料在交变应力与交变应变的作用下,裂纹萌生、扩展,直到小片脱落或断裂的过程称为疲劳。
汽车在行驶时不断受到来自路面不平而引起的路面冲击载荷,同时还受到转向侧向力、驱动力和制动力的作用。
这些力一般都随着时间发生变化。
另外,汽车发动机本身也是一个振动源。
因此,汽车在行驶过程中处于一个相当复杂的振动环境中,其各个零部件一般都会受到随着时间发生的应力、应变的作用。
经过一定的工作时间,一些零部件就会发生疲劳损坏,出现裂纹或断裂。
据统计,汽车90%以上的零部件损坏都属于疲劳损坏。
· 可靠性是指产品在规定条件和规定时间内产品可能完成规定功能(可靠的/存活),可能完不成规定功能(不可靠的/失效)。
因此,可靠度是产品在规定条件,规定时间内,完成规定功能的概率。
· 汽车及其零部件的失效寿命是个随机变量,具有统计性质,一般而言,符合2参数威布尔分布,或者高斯分布。
一般采用B10寿命来评估汽车及其零部件的寿命,即要求汽车零部件达到这个寿命时发生失效的概率为10%,或者说可靠度为90%。
目前,轿车的设计寿命一般是16万公里。
很多汽车零部件的设计寿命(B10寿命)就是16万公里。
也可以这样理解,一大批汽车零部件中,达到设计寿命(B10寿命)时要求有90%的产品还能够正常工作。
所以现代可靠性的概念已经包括了汽车耐久性的概念。
为了使汽车产品具有需要的工作寿命和可靠性,行业内已经广泛采用了一套设计、分析和试验的流程。
汽车疲劳耐久性试验道理试验ppt课件
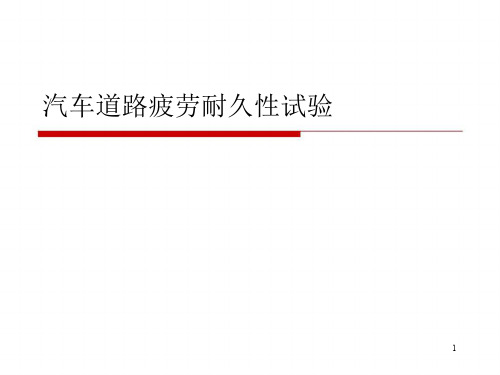
14
汽车疲劳耐久试验
用户使用测量
用户使用分析
耐久性试验规范
耐久性道路试验
失效统计分析
疲劳耐久性评价
15
车辆使用测量-目的
失效模式
用户 车辆使用
认证试验
不相关:
耐久试验完全不 能反映实际使用
弱相关:
Vehiclespeed(km/h)
0
50
100
150
200
Distances (km)
22
车辆使用测量-结果
承载结构载荷-载荷分布
Le v e l-Crossing of LF WFT Force
1.E+05
1.E+05
8.E+04
s
Conut
6.E+04
4.E+04
2.E+04
0.E+00
-4.0
认证要求:
客观、合理:设计、认证条件应充分反映用户需求和产品的实际使 用。(基于用户需求的QFD技术和基于用户产品真实使用产品使用 测量);
全面、完整:基于用户需求和产品的实际使用测量的技术要求和试 验规范的开发;提供用户充分满意的产品同时降低产品本身和售后 服务成本。
准确、有效:严格按照实验规范对产品进行试验,合理的认证策略。 快速、及时:满足产品开发流程计划要求,在保证准确有效的前提
-3.5
-3.0
承载结构 载荷测量
试车场道路载荷 数据采集
各种试车场道路
各地公共道路载荷
典型公共道路数据采集: 非随机- 试验人员 随机-当地司机
零部件疲劳试验
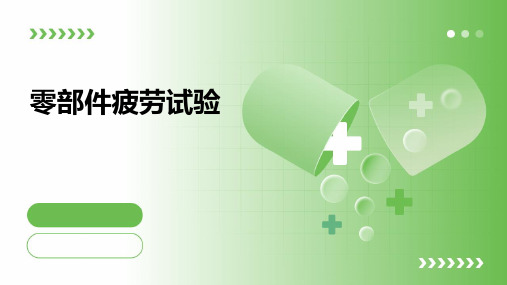
断裂力学试验
基于断裂力学原理,通过 控制裂纹扩展速率或测量 临界应力强度因子来评估 零部件的疲劳性能。
02
零部件疲劳试验方法
应力疲劳试验
总结词
通过在试样上施加交变应力来模拟实际工作状态,以检测试样在交变应力作用下 的疲劳性能。
详细描述
应力疲劳试验是在试样上施加交变应力,使试样在一定周期内反复承受拉伸和压 缩,以模拟实际工作状态。该试验方法适用于各种材料和零部件,如金属、塑料 、橡胶等,是评估材料和零部件疲劳性能的重要手段。
使用和维护建议
根据试验结果和失效分析,提出合 理的使用和维护建议,降低使用过 程中对零部件的损伤和失效风险。
06
零部件疲劳试验的应用与 发展趋势
应用领域
汽车工业
零部件疲劳试验在汽车工业中应用广泛,主要用 于测试发动机、传动系统、悬挂系统等关键部件 的疲劳性能,以确保车辆的安全性和可靠性。
轨道交通
03
零部件疲劳试验设备与材 料
试验设备
疲劳试验机
用于施加循环载荷,模 拟零部件在实际使用中
的受力情况。
数据采集系统
用于实时监测和记录试 验过程中的应变、位移
等数据。
环境箱
用于模拟不同温度、湿度等 环境条件,以评估零部件在
不同环境下的疲劳性能。
振动台
用于模拟实际使用中的 振动情况,加速疲劳裂
纹的萌生和扩展。
应力分析
分析试验过程中零部件所承受的应力分布和变化情况,评估应力 对疲劳寿命的影响。
损伤累积
评估零部件在循环载荷下的损伤累积情况,分析损伤累积与疲劳 失效的关系。
失效分析
失效模式
分析试验中观察到的失效模式,如裂纹、断裂、磨损等,了解失效 的具体表现形式。
疲劳试验 ppt课件
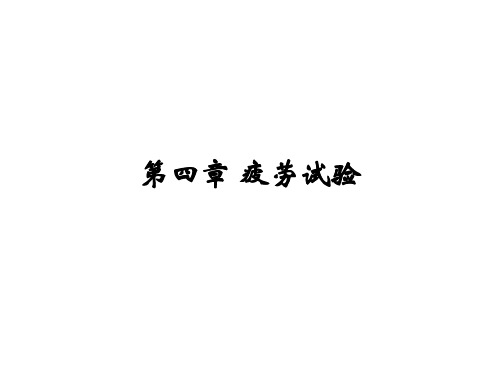
第四章 疲劳试验
引言
材料构件在变动应力和应变的长期作用下, 由于累积损伤而引起的断裂的现象——疲劳。
疲劳属低应力循环延时断裂。 不产生明显的塑性变形,呈现突然的脆断。 ∴疲劳断裂是一种非常危险的断裂。 ∴工程中研究疲劳的规律、机理、力学性能指 标、影响因素等,就具有重要的意义。
(二)疲劳极限
1、对称疲劳极限 97 循环载荷,r=-1。 σ-1,τ-1,σ-1p(对称拉压)Leabharlann 2、不对称循环疲劳极限(σr)
利用已知的对称循环疲劳极限,用工程作图法求得各 种不对称循环疲劳极限。
或者采用回归的公式求得。 (1)应力幅σa~平均应力σm图
y轴上的边界点为0和σ-1 x轴上的边界点为0和σb
铜及轻合金:τ-1=0.55σ-1,铸铁τ-1=0.8σ-1 σ-1>σ-1p>τ-1
三、疲劳极限与静强度之间的关系
钢:σ-1p=0.23(σs+σb) σ-1=0.27(σs+σb)
铸铁:σ-1p=0.4σb σ-1=0.45σb
铝合金:σ-1p=σb/6 +7.5(MPa) σ-1p=σb/6 -7.5(MPa)
第二节 疲劳抗力指标及其测定
一、疲劳极限的测定
第一步 采用升降法测定条件疲劳极限, 第二步 用成组法测定σ一N曲线有限寿命段上各 点的数据, 第三步 绘制σ一N曲线。
二、不同应力状态下的疲劳极限 根据大量的实验结果,弯曲与拉压、扭转疲劳
极限之间的关系: 钢:σ-1p=0.85σ-1,铸铁σ-1p=0.65σ-1
汽车零部件疲劳失效分析

汽车零部件的疲劳失效分析主要内容疲劳失效分析基础Ø金属材料疲劳断裂的定义、特点Ø金属疲劳的分类疲劳失效的过程Ø汽车零部件疲劳失效特点Ø引起汽车零件疲劳失效的原因Ø疲劳失效的过程Ø疲劳失效的特征:载荷的影响汽车零部件疲劳失效案例Ø轴类零件Ø杆类零件Ø管件类零件Ø弹簧类零件Ø齿轮类零件Ø螺栓类零件案例01案例-EQ6102增压喷射泵联结轴01案例-EQ6102增压喷射泵联结轴03案例-连通轴04案例-横拉杆05案例-转向垂臂销子06案例-高压油泵柱塞套失效分析07案例-增压器回油管失效分析与改进08案例-客车钢板弹簧09案例-调整臂弹簧10案例-无声链条11案例-六档齿轮12案例-后桥主减主动轮13案例-变速箱太阳轮14案例-变速箱中间轴常啮合齿轮15案例-42CrMo螺栓16案例-减振器螺栓疲劳失效分析基础金属材料疲劳断裂的定义、特点定义:许多机械零件和工程构件,是承受交变载荷工作的。
在交变载荷的作用下,虽然应力水平低于材料的屈服极限,但经过长时间的应力反复循环作用以后,也会发生突然脆性断裂,这种现象叫做金属材料的疲劳。
特点:1)载荷应力是交变的;2)载荷的作用时间较长;3)断裂是瞬时发生的;4)无论是塑性材料还是脆性材料,在疲劳断裂区都是脆性的。
所以,疲劳断裂是工程上最常见、最危险的断裂形式。
金属疲劳的分类金属材料的疲劳现象,按条件不同可分为下列几种:1)高周疲劳:指在低应力(工作应力低于材料的屈服极限,甚至低于弹性极限)条件下,应力循环周数在100000以上的疲劳。
它是最常见的一种疲劳破坏。
高周疲劳一般简称为疲劳。
2)低周疲劳:指在高应力(工作应力接近材料的屈服极限)或高应变条件下,应力循环周数在10000~100000以下的疲劳。
由于交变的塑性应变在这种疲劳破坏中起主要作用,因而,也称为塑性疲劳或应变疲劳。
疲劳分析介绍PPT学习教案

会计学
1
内容提要
1.概述 2.交变应力 3.S-N曲线 4.影响因素 5.疲劳寿命计算方法 6.SN方法介绍
第1页/共42页
1.概述-疲劳失效危害
19世纪30-40年代,英国铁路车辆轮轴在轴 肩处多次发生破坏;
1954年, 英国慧星号喷气客机坠入地中海 (机身舱门拐角处开裂);
Kt
max 0
σmax为最大应力,σ0为载荷除以缺口处 净截面积所的得平均应力(名义应力)
。
第23页/共42页
4.3缺口形状效应-疲劳缺口系数
除非是高强度材料,零件的疲劳极限 并非随 Kt降低 想象中 那样大 ,即应 力集中 使零件 疲劳强 度降低 的倍数 和它使 零件应 力提高 的倍数 并不相 同。此 时应力 集中系 数就无 法真实 地反映 缺口对 疲劳强 度的影 响。因 此常用 疲劳缺 口系数Kf(fatigue notch factor,又被称为有效应力集中系数) 来更直 接地反 映疲劳 强度的 真实的 降低程 度。
4.疲劳寿命的影响因素
Factors Influencing Fatigue Life 平均应力
Mean stress
尺寸效应
Component size
缺口与不连续形状
Notches and discontinuities
表面处理及粗糙度
Surface treatment & finish
电镜照片-铝合金疲劳辉纹图
第7页/共42页
1.概述-疲劳研究发展简史
19世纪40年代,铁路机车车轴的疲劳破坏问 题。德国A.沃勒通过旋转弯曲试验获得车轴 疲劳结果,把疲劳和应力联系起来,提出 疲劳极限的概念,奠定了常规疲劳分析的 基础。
汽车疲劳耐久性试验道理试验63页PPT

相关:
耐久试验充分 反映实际使用
¥¥¥
不同的认证效率和售后成本
16
车辆使用测量-用途
用户车辆使用
工程设计 技术要求
认证试验规范开发
可靠性(寿命)、 优化设计
耐久、性能预测
发现、消除潜在 失效模式
减少售后索赔和 召回成本
相关
17
车辆使用测量-内容
机构调查 客户投诉
用户需求 开发策略
➢ 能够: 客观地反映并识别和判断设计问题; 提供全面、广泛的工作载荷/输入; 基于实际的用户车辆使用(试验输入反映实际的的运行 工况); 反映典型的使用环境(热、冷环境和腐蚀)工况; 同时兼顾司机/技师/检查人员对车辆的主观评价; 尽可能在产品开发早期获得改进的机会。
13
汽车疲劳耐久试验
8
汽车疲劳耐久试验
依据
➢ 开发策略; ➢ 用户特殊需求; ➢ 市场反馈(售后失效模式、用户抱怨、机构评价)。
要求
➢ 客观:试验方法以用户产品使用为目标(合理的试 验、合理的评价 );
➢ 有效:降低售后产品故障率,减少售后成本; ➢ 快速:适应产品开发流程需求。
9
汽车疲劳耐久试验
耐久试验内容和设施
一般耐久性试验 质量评估试验/短期可靠性 耐候试验:冷/热气候暴露 加速腐蚀
➢ 结构耐久性开发试验- 构架/主要承载结构和接口评价
试验室耐久性模拟和数模分析计算 加速结构耐久性
➢ 传动系统耐久性评价
有限耐久性 简化的(短期)传动系统耐久性-质量评估
12
汽车疲劳耐久试验
耐久性道路试验的角色
3
汽车试验认证
认证方法:
样品试制:设计图纸、工艺要求; 道路试验:试验标准和规范、部件\系统\整车技术要求、法规和
汽车疲劳耐久性试验-道理试验PPT文档63页

39、勿问成功的秘诀为何,且尽全力做你应该做的事吧。——美华纳
40、学而不思则罔,思而不学则殆。——孔子
谢谢!
36、自己的鞋子,弱。——拉罗什福科
xiexie! 38、我这个人走得很慢,但是我从不后退。——亚伯拉罕·林肯
汽车疲劳耐久性试验-道理试验
11、获得的成功越大,就越令人高兴 。野心 是使人 勤奋的 原因, 节制使 人枯萎 。 12、不问收获,只问耕耘。如同种树 ,先有 根茎, 再有枝 叶,尔 后花实 ,好好 劳动, 不要想 太多, 那样只 会使人 胆孝懒 惰,因 为不实 践,甚 至不接 触社会 ,难道 你是野 人。(名 言网) 13、不怕,不悔(虽然只有四个字,但 常看常 新。 14、我在心里默默地为每一个人祝福 。我爱 自己, 我用清 洁与节 制来珍 惜我的 身体, 我用智 慧和知 识充实 我的头 脑。 15、这世上的一切都借希望而完成。 农夫不 会播下 一粒玉 米,如 果他不 曾希望 它长成 种籽; 单身汉 不会娶 妻,如 果他不 曾希望 有小孩 ;商人 或手艺 人不会 工作, 如果他 不曾希 望因此 而有收 益。-- 马钉路 德。
汽车零部件疲劳试验

20
1.236E‐02
200
3.683E+02
200
1.633E‐01
200
2.241E‐02
2200
1.526E+02
250
2.389E+00
100
2.810E‐01
累计总损伤强度:1.339E+3
累计百分比损伤强度
44.4% 0.0% 16.2% 0.1%
0.2% 0.0%
27.5%
0.0%
0.0% 11.4%
悬架压缩时侧向载荷:
FI [
W
a R
2
悬架伸张时侧向载荷:
F
[ W R
O
2
WH
R
)]
T
a
W
H
R
]
T
技术参数
W
WR H
T r
加速度 amax
摩擦系数 µ
FI
量值
2562 1280
640
1590 341 0.8
0.8
0.7
8249
单位
kg kg
mm
mm mm
g
N
FO
1563
N
整车满载载重 满载后桥轴荷 中心到地面高度
员
重
根据寿命数据判断其符合的概率分布规律;
量 分
布
零 件
寿 命 分 布
歪斜/长尾
用数理统计的方法计算分布参数,并给出寿命-概率结果。
对汽车结构疲劳寿命试验结果分析,最常用的是 2 参数威
布尔分布:
(T )
F (t ) 1 e
根据分布规律和试验数据获取分布参数得过程称为参数估