铸铝转子质量的工艺分析及措施
铸铝转子的常见缺陷及原因分析课件

案例分析与讨论
结合具体案例,对铸铝转子缺陷进行 分析和讨论,加深学员对理论知识的 理解和应用。
02 铸铝转子常见缺 陷类型
气孔
形成原因
影响:降低铸件的致密性,减少有效承 载面积,可能导致铸件在使用过程中提 前失效。
模具预热不足或模具温度过高。
铝液含氢量过高。
浇注系统设计不合理,导致气体不能及 时排出。
促进技术交流
课件可作为企业内部或行 业内的技术交流资料,促 进经验分享和技术进步。
课件内容概述
铸铝转子常见缺陷类型
介绍铸铝转子生产过程中常见的缺陷 类型,如气孔、缩孔、裂纹等。
缺陷原因分析
针对每种缺陷类型,深入分析其产生 的原因,如原材料质量、工艺参数、 操作规范等。
改进措施及预防方法
提出针对性的改进措施和预防方法, 如优化工艺参数、加强原材料质量控 制、提高操作水平等。
选用优质铝锭
确保铝锭成分均匀、无杂质,降低气孔、夹杂等 缺陷的产生。
控制回炉料比例
合理ห้องสมุดไป่ตู้配新料与回炉料,避免过多使用回炉料导 致成分波动和性能下降。
加强原材料检验
对每批次的原材料进行严格检验,确保质量符合 要求。
优化铸造工艺参数
调整熔炼温度
01
控制熔炼温度在合理范围内,避免过高温度导致铝液氧化和吸
应力腐蚀
铸铝转子在受到应力和腐蚀介质的共同作用时,容易发生 应力腐蚀开裂。这种开裂往往从表面开始,逐渐向内部扩 展,对铸件的耐腐蚀性能产生严重影响。
晶间腐蚀
由于晶界处的能量较高,容易成为腐蚀的敏感区域。晶间 腐蚀会导致晶粒间的结合力减弱,从而降低铸件的耐腐蚀 性能。
05 缺陷预防措施与 改进建议
铸铝转子质量的工艺分析及措施

铸铝转子质量的工艺分析及措施转子质量问题专题调查分析如下:铸铝转子质量问题,最突出的表现就是转子内部存在的气孔的问题,其次就是转子内部的笼条细条、断条、夹渣以及端环部分的缩孔、冷裂、热裂、缺肉等。
这些问题的产生,最终导致整机的电气性能下降、转速不够、效率降低。
1、转子片间存油未去除:这是转子产生气孔的一个主要原因,由于转子铸铝是在高温、高压、瞬间形成的一个过程,在铝液刚刚充满转子型腔,高温铝还是液态而与转子片间的油类发生反应时,生成气体,这种气体有些被逸出,有些被铝液包围,然而铝液迅速固化,被包围的气体跑不出去,因此这些气体以气泡的形式残留在转子的笼条和端环中,呈不规则分布状态。
解决的办法为:铸铝前的转子铁芯应进行脱油处理,具体做法为:转子铁芯可用工业清洗剂冷态脱油,自来水冲洗,电炉烘干。
烘干温度以不破坏冲片表面保护膜为准,烘干时间以目测干透为准。
我们在5月19日已经做过96个转子脱油的实验,用拉上同型号转子和实验品转子各10个,装入同型号定子各10台,由抽查室做负载对比检查,结果装有实验品转子的电机比拉上同型号电机的转速平均提高2.5%以上。
2、铝液的清化问题:这个问题也是铸铝转子产生气孔的一个主要问题,铝锭及回炉铝在加热熔解过程中,与空气中的水蒸气接触时(尤其是多雨季节),一方面生成氧化铝沉于铝液底部,另一方面分解出氢气,同时氢气也渗入铝水中。
含有气体的铝水压铸出来的转子质量很差,因为铝水在压铸成型的瞬间,铝水迅速固化,一部分气体还未来得及逸出而被固化的铝包围,从而留在铸件内造成气孔。
另外就是铝液表面上的浮渣、铝液底部的沉渣以及留在铝液中间的其它杂物对转子的质量来说也是一个很大的隐患,一旦将这些渣滓和杂物压入转子内部,它们会使转子造成夹渣、形成冷隔(电阻系数增加)、热裂和冷裂的现象,热裂和冷裂严重时造成转子笼条断路。
为了解决上述问题,加入清化剂(氯盐:一般为NaCl 、ZnCl)可以较好的解决这一问题。
铸铝转子的常见缺陷及原因分析
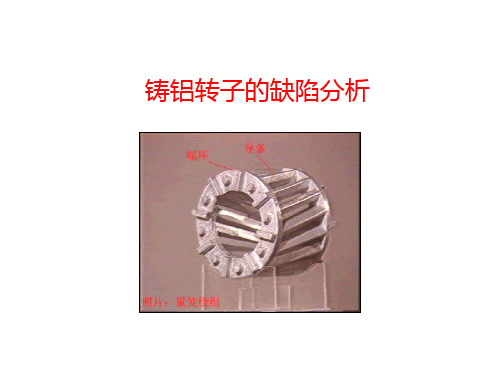
形状为不规则 的封闭或敞露 的孔洞,孔壁 粗糙并带有枝 晶状,常出现 在铸件最后凝 状金属突起 物,常出现 在铸件分型 面和芯头部 位。
毛刺是铸件表面上刺状 金属突起物,常出现在 型和芯的裂缝处,形状 极不规则。
由于金属液未 完全充满型腔 而产生的铸件 缺肉。
产生气孔的主要原因是: 1)铝水清化处理不好,铝水中含气严重,浇注速度太快或排气槽过
小时,模型中气体来不及排出(压力铸铝尤为严重)。
2)铁心预热温度过低,油渍没有烧尽即进行铸铝,油渍挥发在工件 中形成气孔。
3)在低压铸铝时,如果升液管漏气严重,则通入坩埚的压缩空气会
进入升液管,与铝水一齐跑入转子里去而形成气孔。
2)转子槽孔过小,铝水流动困难(遇此情况应适当提高铁心预热温
度)。 3)转子错片,槽斜线不成一直线,阻碍铝水流动。 4)铁心预热温度低,铝水浇入后流动性变差。 转子细条使转子电阻增大,效率降低,温升高,转差率大。
3、气孔
铸件壁内气孔一般呈圆形或椭圆
形,具有光滑的表面,一般是发
亮的氧化皮,有时呈油黄色。表 面气孔、气泡可通过喷砂发现, 内部气孔气泡可通过X光透视或 机械加工发现。
6、裂纹
当铸造应力超过金属的强度极限时,铸件便产生裂纹。 可分为热裂纹和冷裂纹。
热裂纹 在凝固末期高温下形成的裂纹。裂纹表面被氧化而呈氧化色,裂 纹沿晶粒边界产生和发展,外形曲折而不规则;裂纹短,缝隙宽。 产生原因:凝固末期,合金绝大部分已成固体,但强度和塑性很低,当铸 件受到机械阻碍产生很小的铸造应力就能引起热裂。分布在应力集中处或 热节处。 冷裂纹 是铸件处于弹性状态即在低温时形成的裂纹。其表面光滑,具 有金属光泽或呈微氧化色,裂纹穿过晶粒而发生,外形规则,常是圆滑 曲线或直线。
如何分析和判断铸铝转子质量问题

如何分析和判断铸铝转子质量问题铸铝转子的质量影响电机的效率、功率因数以及起动、运行等性能。
为全面地提高转子质量,不仅要分析铸铝转子的缺陷,而且还要研究影响铸铝转子质量的各种因素,从而提出改进措施。
本文Ms.参对转子铸铝方法进行一些简要介绍,并针对断条问题进行剖解。
转子铸铝是一个隐密工程,转子的质量控制要靠工艺参数保证,从某种意义上讲,铸铝转子的性能质量比拼焦点就集中在转子的铸铝上。
鼠笼转子由穿铜条改为铸造方法后,使得电机的杂散损耗增加2~6倍。
转子的铸铝方法不同,杂散损耗也不相同。
当采用压力铸铝转子时,电机的杂散损耗最大。
离心铸铝和振动铸铝虽然受各种因素影响,容易产生缺陷,但转子的杂散损耗较小。
进一步研究发现;压铸转子比离心铸铝转子铝笼的密度减少约8%,平均电阻率增高13%,这就使得压铸转子的异步电动机的主要技术经济指标变坏,铁心损耗、转差率、温升均有所上升,而最小力矩和效率下降。
、压铸转子铝的密度减少,电阻增大,是因为压铸时的气体混入铝水呈“针孔”状密布在转子笼条、端环、风叶等各处。
还由于强大的压力使笼条和铁心接触的十分紧密(甚至铁心叠片间亦有铝导体散入),横向电流使得电机的杂散损耗大大增加。
低压铸铝铝水来自坩埚内部,并采取较“缓慢”的低压浇注,排气较好,铸铝转子的质量良好。
以低压铸铝转子质量为最好,离心铸铝次之,最差的是压力铸铝铸铝转子的缺陷是多种多样的,其产生的原因也是错纵复杂的。
国内电机厂多采用离心体铝,下面主要结合离心铸铝转子质量问题进行分析。
其它铸铝方法的一些质量问题将予以简要介绍。
铸铝转子为何会断条?(1)铁心槽口错位或堵塞错位使得槽孔截面减少以致堵塞;个别冲片槽孔漏冲以及预热时带入的夹杂物,均可使槽孔堵塞,以致在浇注时铝水被隔断。
(2)转子笼条被拉断。
当转子铁心叠压过紧,假轴退出后,铁心向外涨开时可能拉断笼条:脱模时若铝水尚未完全凝固,由于过早地敲打模具,笼条也会断裂。
振动铸铝时,由于振动时间过长,往往也会把笼条振断。
铸铝转子的常见缺陷及原因分析优秀课件

6、裂纹
当铸造应力超过金属的强度极限时,铸件便产生裂纹。 可分为热裂纹和冷裂纹。
热裂纹 在凝固末期高温下形成的裂纹。裂纹表面被氧化而呈氧化色,裂 纹沿晶粒边界产生和发展,外形曲折而不规则;裂纹短,缝隙宽。 产生原因:凝固末期,合金绝大部分已成固体,但强度和塑性很低,当铸 件受到机械阻碍产生很小的铸造应力就能引起热裂。分布在应力集中处或 热节处。
披缝是铸件 表面上厚薄 不均匀的片 状金属突起 物,常出现 在铸件分型 面和芯头部 位。
毛刺是铸件表面上刺状 金属突起物,常出现在 型和芯的裂缝处,形状 极不规则。
在铸件清理或搬 运时,损坏了铸 件的完整性。
由于金属液未 完全充满型腔 而产生的铸件 缺肉。
由于收缩应力 或型壁变形、 开裂引起的铸 件外形和尺寸 与图纸不符。
中形成气孔。 3)在低压铸铝时,如果升液管漏气严重,则通入坩埚的压缩空气会
进入升液管,与铝水一齐跑入转子里去而形成气孔。
转子气孔使转子电阻增大,效率降低,温升高,转差率大。
4、浇不满
浇不满的原因主要有: 1)铝水温度过低,铝水流动性差。 2)铁心、模具预热温度过低,铝水浇入后迅速降温,流动性变
差。 3)离心机转速太低,离心力过小,铝水充填不上去。 4)浇入铝水量不够。 5)铸铝模内浇口截面积过小,铝水过早凝固堵住铝水通道。
2)铸铝后脱模过早,铝水未凝固好,铝条由于铁心胀力而断裂。 3)铸铝前,转子铁心槽内有夹杂物。 4)单冲时转子冲片个别槽孔漏冲。 5)铝条中有气孔,或清渣不好,铝水中有夹杂物。 6)浇注时中间停顿。因为铝水极易氧化,先后浇入的铝水因氧化 而结合不到一起,出现“冷隔”。 转子断条对电机性能的影响是: 如果转子断条,则转子电阻很大,所以起动转矩很小; 转子电阻增大,转子损耗增大,效率降低,温升高,转差率大。
影响压铸铝转子质量的工艺因素

摘
要: 压铸 铝 转 子存 在 较 多的质 量 问题 , 造 成 原
比压 两种 。
因是 压 铸 工艺 参 数 ( 压力、 速度 、 温度和时间) 选 用不 当。 文章 从 工艺 参 数之 间 的关 系入手 , 叙 述 了在实 际 生 产 中如何合 理的选用工 艺参数 。
wa s d e s c r i b ed. Ke y w or ds :c a s t a l um i n um r o t o r pr e s s ur e ve l oc i t y
Pv =一 D Pb z
斗
A
式中:P 一 压射力 MN;
一
增压比压 ( 对无 增压 系统 的压铸 机
( b ) 压 力 管道 的压 力损 失 ; ( c ) 蓄 能 器 中 的气 体 与 压 力 油 之 间 的压 力 变化 ;
( d ) 液压 油因温 度变化而 引起 的粘 度变化
对压 力 的影 响 ; ( e ) 压 射 冲 头 与 压 室 之 间 的配 合 状 态 M 3 0 5 文献标识码 : A
DOI 编 码: 1 0 . 3 9 6 9 / j . i s s n l O 0 6 - 2 8 0 7 . 2 0 1 4 . 0 4 . 0 1 6
Ab s t r a c t :Th e c a u s e o f ma n y q u a l i t y p r o b l e ms i n t h e
即为 管道 压 力 ) Mp a ;
D一 压 射 油缸 的直径 m。
谈转子离心铸铝的工艺方法

2 0 1 4
速 农机
AN N O N GJ FUJI I
谈转子 离心铸铝 的工艺方法
陈玉 宇
( 福建 南 电股份 有 限公 司 , 福建 南平 3 5 3 0 0 1 )
摘
要: 为 了保证电动机转子铸铝 的质量 , 对转子铸铝熔铝设备、 离心铸铝的工艺参数、 离心铸铝模 的结构
参数、 离心浇注的工艺方法及 离心力大小、 操作程序的具体实施步骤进行剖析介绍, 总结 了一套可用于指导生 产实际的离心铸铝转子生产工艺。
关键词: 转子; 铸铝 ; 坩锅; 涂料 ; 离心力; 温度 ; 速度
由于铸 铝转 子具有结构对称 、 紧凑 , 外形美观 , 易 于达到机械平衡 ; 槽形设计不受 铜条或铝条形 状
铝 过程 中最 容易产 生 的气体 , 在铝 中的溶解 度 随着温 度升高而增加 ( 见图2 ) 。 当铝 温 到 达 8 0 0  ̄ C 时, 由于
3 转子铁芯和铸铝模 的预热炉
预 热炉 必 须保 证 转 子铁 芯 预 热 温度 5 0 0 ℃左右 、
铸铝模预热温度 3 5 0  ̄ C 左右 , 而且温度均匀。 目前大
升随之提高 。所以铸铁坩埚使用前的处理就显得更 为 重要 。新 坩埚 必须 除净 铁锈 , 然后 加 热到 1 5 0 ~
的限制 , 可 以任 意选择能改善 电机性能 的理想槽形 ; 转子风叶、 笼条端环 以及平衡柱可同时铸出 , 槽满率 几乎达 1 0 0 %, 提高了散热效率 ; 生产周期短 、 成本低 、
都 采用反 射 炉或 电阻炉 等 。
4 离心铸铝模
离心铸铝模 由上 、 中、 下模 , 分流器 , 假轴等几部 分组成 。各种铸铝方法所用模具虽有不 同, 但其结构
铸铝转子工艺

铸铝转子工艺(铸铝工序)一、转子铸铝方法我公司所采用的转子铸铝方法主要有离心铸铝和压力铸铝两种。
下面分别来看一下这两种铸铝方法的工作原理和特点。
(一)压力铸铝工作原理是用压力将融化好的金属铝液注入型腔,待冷却凝固成铸件。
其特点有:(1)在压铸过程的始终,压力起着主要作用。
(2)压铸时,金属液在高速冲型过程中,如果型腔中的气体来不及排出,就会被卷入金属内产生气孔。
(3)由于金属液充型过程是在压力作用下进行的,转子铁心可在冷态下压铸。
(4)生产效率高,易实现机械化、自动化,从而可减轻劳动强度。
(二)离心铸铝工作原理是将融化好的金属铝液注入旋转着的铝模中,使之在离心力的作用下充满型腔,并凝固。
其特点有:(1)离心力对铸件的成型和金属结晶过程有重要影响,它有助于金属液中的气体和非金属杂物(比金属轻)的排出。
更重要的是影响到金属结晶过程,起到加强补缩和结晶细化的作用。
(2)转子铁心必须预热。
铁心加热后,在槽型断面上得到氧化,有利于降低电机的杂散损耗。
(3)转子离心铸铝用的设备比较简单。
但在浇铸过程中有不少手工操作,劳动强度较大。
二、离心铸铝和压力铸铝的优缺点及其常见的缺陷和防止措施1.离心铸铝优缺点离心铸铝所得到的铸件,金属组织比较紧密,质量比较好,所用设备不太复杂,操作技术比较简单,与压力铸铝相比较杂散损耗比较小,不过其生产率不高,劳动条件较差,劳动强度较高。
2.压力铸铝优缺点压力铸铝时,铝水压射到转子槽和型腔中的速度极高,其充填速度可达10~25m/s。
压铸时,不象离心铸铝那样铝水有一段流动时间,而是瞬间完成的,因此铁心和模具均可不必预热。
铁心和模具不预热,这就大大减化了操作工艺,改善了劳动条件。
此外由于没有离心铸铝那样复杂的凝固补缩过程,铸铝转子质量稳定,一次合格率达99%以上。
3.压力铸铝的质量,目前存在以下一些问题:(1)由于压力很大,铝水充满型腔的速度很高,原来在型腔中得空气难以排尽,会在铸件中产生气孔。
电机铸铝转子压铸工艺的研究与分析
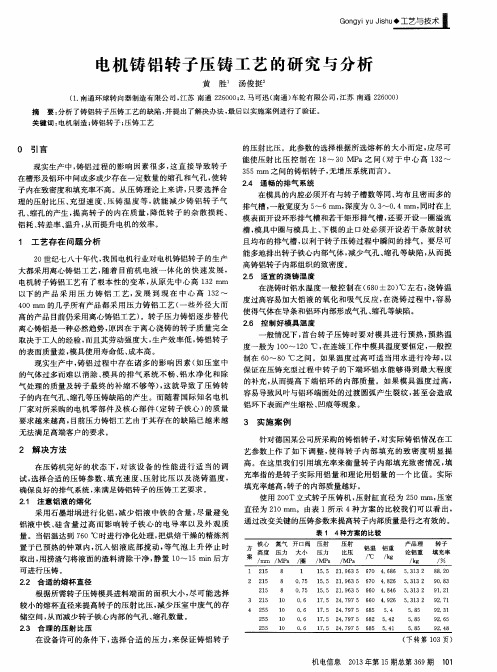
的补充 , 从而提高下端 铝环 的内部质量 。如 果模具 温度 过高 ,
容 易导 致 风 叶与 铝 环 端 面 处 的 过 渡 圆 弧 产 生 裂 纹 , 甚至会造成
铝环下表 面产生缩松 、 凹痕等现象 。
3 实 施 案 例
针对德 国某公 司所采购的铸铝转子 , 对 实际铸铝情况在 工 艺参数上作 了 如下 调整 , 使得 转子 内部 填充 的致 密度 明显 提 高 。在这里我们 引用填充率来衡量转子 内部填充 致密情况 , 填 充率指的是转子实 际用 铝量 和理论用 铝量 的一个 比值 。实际
G 。 n g v t v u 一 一 s n u : 三 兰 量 茎 薯
电机铸 铝 转 子 压铸 工 艺 的研 究 与分析
黄 胜 汤俊挺
( 1 . 南通 环球 转 向器制造 有 限公 司 , 江苏 南 通 2 2 6 0 0 0 ; 2 . 马可 迅 ( 南通) 车轮有 限公 司 , 江 苏 南通 2 2 6 0 0 0 ) 摘 要: 分 析 了铸铝 转子 压铸 工艺 的缺 陷 , 并 提出 了解决 办法 , 最后 以实施 案例 进行 了验 证 。
的气 体 过 多而 难 以 消 除 、 模具 的排气 系统不 畅 、 铝 水 净 化 和 除
在 浇铸 时铝 水 温 度 一 般 控 制 在 ( 6 8 0 i 2 0 ) ℃左右 , 浇 铸 温
度过高容易加大铝液 的氧化 和吸气反应 , 在 浇铸过程 中, 容 易
使得气体在导条和铝环 内部形成气孔 、 缩孔等缺陷。
2 . 5 适 宜 的 浇 铸 温 度
1 工艺存在 问题分析
2 O世纪七八十年代 , 我 国电机行业对 电机铸铝转子 的生产
大都采用离心铸铝工 艺 , 随 着 目前 机 电液 一 体 化 的 快 速 发 展 ,
压铸铝转子气孔质量问题的工艺分析

摘 要 : 气 孔 是压 铸 铸 铝 转 子常 见 的质 量问题 , 它 直接 影响 电机 的效率 、 功 率因数 、 温升 、 起 动和 运行等 性
能。 文 章介绍 了如何 预防和解 决这 种缺陷 的一些经验 。 关键词 : 压铸 铸 铝转 子 气孔
气孔 的主要成 因是压室充满度不够, 导致气
面保 护膜 为 准 , 烘干 时 间以 目测干 透 为准 。 曾做 过 1 0 0 个转子脱油的实验, 用 同型 号 转
孔 的特点 , 孔 内表 面 一 般 比较 光 滑 。目前 , 在 我
国电机制造行业中, 采用压铸 工艺生产铸 铝转子
时, 气孔 是 比较常见 的 问题 , 并且 是 难 以根 除的 。
因而铸铝前的转子铁心应进行脱油处理 , 具
体做 法为: 转 子 铁 心用工 业 清 洗 剂 冷态 脱 油 , 自
的孔 , 分布于导体 内部 、 表面或接 近于表面处 ,
形 状有圆的 、 椭 圆 的 及 不规 则 的 , 分 布不 均 是 气
来 水冲洗 , 电炉烘干。 烘干温 度以不破坏冲片表
A bs t r ac t :Bl owho l e wa s t he f r e q ue n t qua l i t y pr o bl e m
1 . 1 转子 片间存油
转子片问存油是铸 铝转子 产生气孔 的一 个 主要成 因。 由于转子压铸 是在 高温 、 高压和瞬间 形成的一个 过程 , 在铝液刚刚充满转子型腔 , 高
体 在 压 室 中占有一定 的空 间 , 在 压 射 时气 体 和 铝 液 同 时 进 入 压 铸 模 型 腔 造 成 的 。采 取 的工 艺 措
施 如下:
中图分类号 : TM3 0 5 文献标 识码 : A DOI 编 码: l 0 . 3 9 6 9  ̄ . i s s n l 0 0 6 - 2 8 0 7 . 2 0 1 3 . 0 6 . 0 1 9
铸铝转子的常见缺陷及原因分析
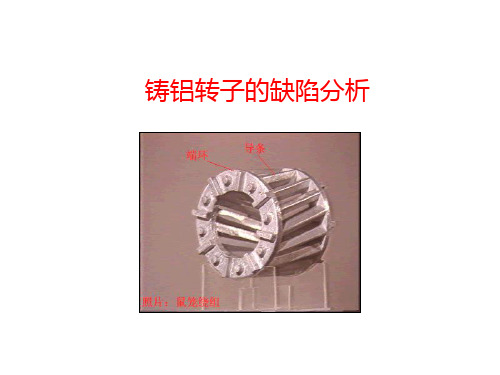
一、铸铝件的常见缺陷
在铸件表面 上、全部或 部分覆盖着 金属与砂的 混合物,或 一层烧结的 型砂,致使 铸件表面粗 糙。
冷隔是铸件上未 完全融合的缝隙 或洼坑,其交接 边缘呈圆角,多 出现在远离浇口 的铸件宽大上表 面和薄壁处、金 属流股汇合处或 激冷部位
铸件表面上 有粗糙不规 则的金属瘤 状物,常位 于浇口附近。 在铸件其它 部位则往往 出现砂眼。
转子气孔使转子电阻增大,效率降低,温升高,转差率大。
4、浇不满
浇不满的原因主要有: 1)铝水温度过低,铝水流动性差。 2)铁心、模具预热温度过低,铝水浇入后迅速降温,流动性变
差。 3)离心机转速太低,离心力过小,铝水充填不上去。 4)浇入铝水量不够。 5)铸铝模内浇口截面积过小,铝水过早凝固堵住铝水通道。
披缝是铸件 表面上厚薄 不均匀的片 状金属突起 物,常出现 在铸件分型 面和芯头部 位。
毛刺是铸件表面上刺状 金属突起物,常出现在 型和芯的裂缝处,形状 极不规则。
在铸件清理或搬 运时,损坏了铸 件的完整性。
由于金属液未 完全充满型腔 而产生的铸件 缺肉。
由于收缩应力 或型壁变形、 开裂引起的铸 件外形和尺寸 与图纸不符。
产生缩孔的原因主要有: 1)铝水、模具、铁心的温度搭配不适当,达不到顺序凝固和合理补缩
的目的。如果上模预热温度过低,铁心预热温度上、下端不均匀,使浇门处 铝水先凝固,上端环铝水凝固时得不到铝水补充,造成上端环缩孔。因为缩 孔总是产生在铝水最后凝固的地方。
2)模具结构不合理,如内浇口截面积过小或分流器过高,使铝水在内 浇口处通道增长,内浇口处铝水先凝固,造成补缩不良,会使上端环出现缩 孔。又如模具密封不好或安装不当造成漏铝,则使得浇门处铝水量过少。无 法起到补缩作用也容易造成缩孔。
铸铝转子的常见缺陷及原因分析
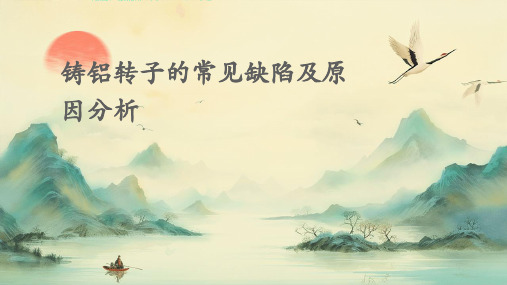
裂纹产生的原因
01
铸件结构设计不合理
铸件结构设计不合理,如壁厚变化大、热节位置不当等,会导致铸件在
冷却过程中产生较大的热应力,从而形成裂纹。
02
铝液成分不合格
铝液中含有的杂质和合金元素比例不合适,如铁含量过高、硅含量过低
等,会导致铸件在凝固过程中产生较大的收缩应力,从而形成裂纹。
03
浇注温度和时间控制不当
铸铝转子的常见缺陷及原 因分析
• 铸铝转子简介 • 铸铝转子的常见缺陷 • 铸铝转子缺陷的原因分析 • 铸铝转子缺陷的预防措施 • 铸铝转子缺陷的检测与修复
01
铸铝转子简介
铸铝转子的应用
01
02
03
汽车工业
铸铝转子广泛应用于汽车 发动机中,具有轻量化、 高强度和耐腐蚀等优点。
家电行业
在空调、冰箱等家电产品 中,铸铝转子也得到了广 泛应用,能够提高产品的 性能和稳定性。
控制浇注温度和浇注速度
总结词
浇注温度和浇注速度是影响铸铝转子质量的 重要因素,通过控制浇注温度和浇注速度可 以有效降低铸铝转子缺陷的发生率。
详细描述
根据模具和铝液的特点,合理控制浇注温度 和浇注速度。避免浇注温度过高或过低,以 及浇注速度过快或过慢,以防止出现气孔、
缩孔、裂纹等缺陷。
05
铸铝转子缺陷的检测与修复
VS
详细描述
根据铸铝转子的结构和要求,合理设计模 具的结构和尺寸。考虑模具的散热性能和 排气性能,避免气孔和缩孔等缺陷的产生 。
加强浇注系统设计
总结词
详细描述
浇注系统设计不合理会导致铝液流动不均匀, 进而引发铸铝转子缺陷,因此加强浇注系统 设计是预防铸铝转子缺陷的重要措施之一。
铸铝转子工艺

首先我们来了解一下交流三相异步电动机的工作原理,可以帮助 我们来理解为什么转子断条、细条等会使电阻增大,要尽量避免,以 及为什么转子两端要用短路环短接等。
工作原理:当电动机的定子绕组通以三相对称交流电时,在定子 和转子间便产生以转速ns旋转的旋转磁场(电能生磁),由于转子开始 时是静止的,所以转子导体将被旋转磁场切割,根据相对运动的原 理,我们也可以把磁场看成不动,而转子导体相对磁场旋转切割磁力 线从而产生感生电动势(即1831年法拉第发现的电磁感现象也称“动 磁生电”),由于转子导体两端已被短路环短接,导体已构成闭合回 路,所以转子导体内也相应产生感生电流。有感生电流的转子导体即 为通电导体,通电导体在磁场中就会受到电磁力的作用(电磁生 力),产生电磁力矩最终带动转子旋转,而且我们还可以根据左手定 则判断出转子导体的旋转方向,与旋转磁场的方向是相同的,只不过 是以略小于旋转磁场转速ns的速度运转的,这也是异步电动机名称的 由来。
二、转子铸铝方法
我公司所采用的转子铸铝方法主要有离心铸铝和压力铸铝两种。下面 分别来看一下这两种铸铝方法的工作原理和特点。 (一)压力铸铝
工作原理是用压力将融化好的金属铝液注入型腔,待冷却凝固成铸 件。其特点有: (1)在压铸过程的始终,压力起着主要作用。 (2)压铸时,金属液在高速冲型过程中,如果型腔中的气体来不及排 出,就会被卷入金属内产生气孔。 (3)由于金属液充型过程是在压力作用下进行的,转子铁心可在冷态 下压铸。 (4)生产效率高,易实现机械化、自动化,从而可减轻劳动强度。 (二)离心铸铝
正确进行清化除理; 适当控制浇注速度; 正确控制转子铁心预热温度 和时间; 放大排气孔。
正确控制转子预热温度;
正确控制下模预热温度。
铸铝转子可行性分析方法
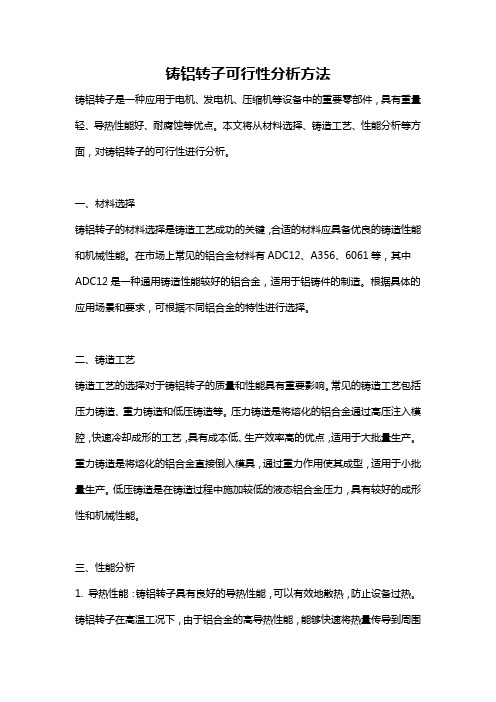
铸铝转子可行性分析方法铸铝转子是一种应用于电机、发电机、压缩机等设备中的重要零部件,具有重量轻、导热性能好、耐腐蚀等优点。
本文将从材料选择、铸造工艺、性能分析等方面,对铸铝转子的可行性进行分析。
一、材料选择铸铝转子的材料选择是铸造工艺成功的关键,合适的材料应具备优良的铸造性能和机械性能。
在市场上常见的铝合金材料有ADC12、A356、6061等,其中ADC12是一种通用铸造性能较好的铝合金,适用于铝铸件的制造。
根据具体的应用场景和要求,可根据不同铝合金的特性进行选择。
二、铸造工艺铸造工艺的选择对于铸铝转子的质量和性能具有重要影响。
常见的铸造工艺包括压力铸造、重力铸造和低压铸造等。
压力铸造是将熔化的铝合金通过高压注入模腔,快速冷却成形的工艺,具有成本低、生产效率高的优点,适用于大批量生产。
重力铸造是将熔化的铝合金直接倒入模具,通过重力作用使其成型,适用于小批量生产。
低压铸造是在铸造过程中施加较低的液态铝合金压力,具有较好的成形性和机械性能。
三、性能分析1. 导热性能:铸铝转子具有良好的导热性能,可以有效地散热,防止设备过热。
铸铝转子在高温工况下,由于铝合金的高导热性能,能够快速将热量传导到周围环境,提高设备的工作效率和稳定性。
2. 强度和硬度:铸铝转子的强度和硬度是其抵抗变形和破损的重要指标。
合适的铝合金材料经过适当的热处理工艺,可以提高转子的强度和硬度。
3. 耐腐蚀性:铸铝转子在使用中需要具备良好的耐腐蚀性能,以保证其长期稳定运行。
选择适当的铝合金材料,并采取防腐措施,可以提高铸铝转子的耐腐蚀性。
4. 重量轻:相比于传统的铸铁转子,铸铝转子具有更轻的重量,可以减轻设备的自重和转子的惯性负荷,提高设备的运行效率和经济性。
综上所述,铸铝转子具有较好的可行性和应用前景。
通过合适的材料选择、铸造工艺以及性能分析,可以生产出质量优良、性能稳定的铸铝转子,满足各类电机、发电机和压缩机等设备对于轻量化、导热性能和耐腐蚀性能的要求。
压铸转子常见质量问题的分析与解决措施

( 6 ) 压铸前应对转子冲片进行去油处理 , 否 则, 在压铸 时由于受热 燃烧也会产生大量气体 ,
且 无 法全 部排 出型 腔 。
l 气 孔
・
5 6・2 0 1 5年 第 1期 《 电机 技术》
毋 #
工 艺与测 试
中图 分 类 号 : T M3 O 7 文献 标 识 码 : A DOI 编 码: 1 0 . 3 9 6 9  ̄. i s s nl 0 0 6 - 2 8 0 7 . 2 0 1 5 . 0 1 . 0 1 8
Ab s t r a c t :Th e r e we r e l o t s o f q u a l i t y p r o b l e ms i n t h e
排除。
而且要求 不应有气孔 、 缩孔 、 冷隔 、 裂纹 及浇注 不足等缺陷的存在, 特别是导条更不得有细条 、 断条和气孔等缺 陷。 另外, 铝液中杂质的含 量特 别是含碳量 , 也不得超过技 术要求 的规定 , 以保
证 转 子用铝 的 电导 率 。
( 5 ) 压室及压铸模 型腔表面的涂料不宜过 多, 涂料过 多会使铝液填充过程中产生较多的气
气孔 的特 征 是 表 面光 滑 、 形 状 为无 规 则 的孔
洞, 一般发生在断环壁较厚处 及其附近 , 为分散
性 的细d , N。 产生气孔的主要原因为压室充满度 不够, 导致气体 在压 室中占有一定的空间 , 在压
射 时气体 和铝 液 同时进 入 压铸 模 型 腔 造成 的 。 一
转 子铁心 的叠压 、 铝 及铝合金 的熔 炼 以及压铸 过程 的操 作等 各种 因素 都有关 。 关键词 : 压铸 转子 质 量问题 工艺参 数
铸铝转子的常见缺陷及原因分析概要

铸件表面上 有粗糙不规 则的金属瘤 状物,常位 于浇口附近。 在铸件其它 部位则往往 出现砂眼。
铸件表面的块 状金属突起物, 其外形与掉落 的砂块很相似。 在铸件其它部 位则往往出现 砂眼或残缺。
砂
眼
气 孔
缩 孔
披 缝
在铸件表 面或内部 有充塞着 型砂的孔 眼
在铸件内部、表 面或近于表面处 有大小不等的光 滑孔眼。一般为 圆球形或近似于 球形的团球形孔 洞,孔壁光滑。
产生缩孔的原因主要有: 1)铝水、模具、铁心的温度搭配不适当,达不到顺序凝固和合理补缩 的目的。如果上模预热温度过低,铁心预热温度上、下端不均匀,使浇门处 铝水先凝固,上端环铝水凝固时得不到铝水补充,造成上端环缩孔。因为缩 孔总是产生在铝水最后凝固的地方。 2)模具结构不合理,如内浇口截面积过小或分流器过高,使铝水在内 浇口处通道增长,内浇口处铝水先凝固,造成补缩不良,会使上端环出现缩 孔。又如模具密封不好或安装不当造成漏铝,则使得浇门处铝水量过少。无 法起到补缩作用也容易造成缩孔。 缩孔将使转子电阻增大,效率降低,温升高,转差率大。
2)转子槽孔过小,铝水流动困难(遇此情况应适当提高铁心预热温
度)。 3)转子错片,槽斜线不成一直线,阻碍铝水流动。 4)铁心预热温度低,铝水浇入后流动性变差。 转子细条使转子电阻增大,效率降低,温升高,转差率大。
3、气孔
铸件壁内气孔一般呈圆形或椭圆
形,具有光滑的表面,一般是发
亮的氧化皮,有时呈油黄色。表 面气孔、气泡可通过喷砂发现, 内部气孔气泡可通过X光透视或 机械加工发现。
产生裂纹的原因有: 1)工业纯铝中杂质含量不合理。工业纯铝中常有的杂质是铁和硅,大量 实验分析证实、硅铁杂质含量比对裂纹的影响很大,即硅铁比在1.5~10之间
铸铝转子工艺.doc

铸铝转子工艺(铸铝工序)一、转子铸铝方法我公司所采用的转子铸铝方法主要有离心铸铝和压力铸铝两种。
下面分别来看一下这两种铸铝方法的工作原理和特点。
(一)压力铸铝工作原理是用压力将融化好的金属铝液注入型腔,待冷却凝固成铸件。
其特点有:(1)在压铸过程的始终,压力起着主要作用。
(2)压铸时,金属液在高速冲型过程中,如果型腔中的气体来不及排出,就会被卷入金属内产生气孔。
(3)由于金属液充型过程是在压力作用下进行的,转子铁心可在冷态下压铸。
(4)生产效率高,易实现机械化、自动化,从而可减轻劳动强度。
(二)离心铸铝工作原理是将融化好的金属铝液注入旋转着的铝模中,使之在离心力的作用下充满型腔,并凝固。
其特点有:(1)离心力对铸件的成型和金属结晶过程有重要影响,它有助于金属液中的气体和非金属杂物(比金属轻)的排出。
更重要的是影响到金属结晶过程,起到加强补缩和结晶细化的作用。
(2)转子铁心必须预热。
铁心加热后,在槽型断面上得到氧化,有利于降低电机的杂散损耗。
(3)转子离心铸铝用的设备比较简单。
但在浇铸过程中有不少手工操作,劳动强度较大。
二、离心铸铝和压力铸铝的优缺点及其常见的缺陷和防止措施1.离心铸铝优缺点离心铸铝所得到的铸件,金属组织比较紧密,质量比较好,所用设备不太复杂,操作技术比较简单,与压力铸铝相比较杂散损耗比较小,不过其生产率不高,劳动条件较差,劳动强度较高。
2.压力铸铝优缺点压力铸铝时,铝水压射到转子槽和型腔中的速度极高,其充填速度可达10~25m/s。
压铸时,不象离心铸铝那样铝水有一段流动时间,而是瞬间完成的,因此铁心和模具均可不必预热。
铁心和模具不预热,这就大大减化了操作工艺,改善了劳动条件。
此外由于没有离心铸铝那样复杂的凝固补缩过程,铸铝转子质量稳定,一次合格率达99%以上。
3.压力铸铝的质量,目前存在以下一些问题:(1)由于压力很大,铝水充满型腔的速度很高,原来在型腔中得空气难以排尽,会在铸件中产生气孔。
铸铝转子工艺.doc

铸铝转子工艺(铸铝工序)一、转子铸铝方法我公司所采用的转子铸铝方法主要有离心铸铝和压力铸铝两种。
下面分别来看一下这两种铸铝方法的工作原理和特点。
(一)压力铸铝工作原理是用压力将融化好的金属铝液注入型腔,待冷却凝固成铸件。
其特点有:(1)在压铸过程的始终,压力起着主要作用。
(2)压铸时,金属液在高速冲型过程中,如果型腔中的气体来不及排出,就会被卷入金属内产生气孔。
(3)由于金属液充型过程是在压力作用下进行的,转子铁心可在冷态下压铸。
(4)生产效率高,易实现机械化、自动化,从而可减轻劳动强度。
(二)离心铸铝工作原理是将融化好的金属铝液注入旋转着的铝模中,使之在离心力的作用下充满型腔,并凝固。
其特点有:(1)离心力对铸件的成型和金属结晶过程有重要影响,它有助于金属液中的气体和非金属杂物(比金属轻)的排出。
更重要的是影响到金属结晶过程,起到加强补缩和结晶细化的作用。
(2)转子铁心必须预热。
铁心加热后,在槽型断面上得到氧化,有利于降低电机的杂散损耗。
(3)转子离心铸铝用的设备比较简单。
但在浇铸过程中有不少手工操作,劳动强度较大。
二、离心铸铝和压力铸铝的优缺点及其常见的缺陷和防止措施1.离心铸铝优缺点离心铸铝所得到的铸件,金属组织比较紧密,质量比较好,所用设备不太复杂,操作技术比较简单,与压力铸铝相比较杂散损耗比较小,不过其生产率不高,劳动条件较差,劳动强度较高。
2.压力铸铝优缺点压力铸铝时,铝水压射到转子槽和型腔中的速度极高,其充填速度可达10~25m/s。
压铸时,不象离心铸铝那样铝水有一段流动时间,而是瞬间完成的,因此铁心和模具均可不必预热。
铁心和模具不预热,这就大大减化了操作工艺,改善了劳动条件。
此外由于没有离心铸铝那样复杂的凝固补缩过程,铸铝转子质量稳定,一次合格率达99%以上。
3.压力铸铝的质量,目前存在以下一些问题:(1)由于压力很大,铝水充满型腔的速度很高,原来在型腔中得空气难以排尽,会在铸件中产生气孔。
电机转子低压铸铝质量分析

业 甚至同行业 .每年因此而造成的浪费更是惊
.
5 . 2
《 电机 技 术 》 2 0 2 0 2()
维普资讯
() a 铸铝前, 调整铝液中的铣硅 比, 使其比值
大 于 25 .:
()缩孔 的防 止措 施 2 ()严格 控制 工艺参数 . a 掌握应 用 “ 三温 ” 的 配 合 。使 转 子铝 液在 型腔 内既能 得N t ,YI , l  ̄ -I 达到 顺序 凝 固 : ()按 电机 中心 高及转子铁 心槽 宽 窄的不 同 , b 调整好最 大充型压 力 , 在此 压力 下结晶 , 防止缩孔 。
() 1 产生裂纹的主要原因 ()铅 液 中铁 硅 比不 当 , F/i .时 . a 在 eS ≤25 容
易 出现 裂纹 : ()铝液温 度 过高时铝 的晶粒 变 粗 , b 延伸 率降 低 ,受不住在冷 凝过 程产 生的收缩 力 而形成 裂纹 :
袅 3 铝锭 化学 成份 (B 1 6 8 ) G 1 — 3 和铝 液的温 度 9
()正确 地 控 制铁心 温 度 ; a
() C 首台转 子铁心预热温度低和上模温度偏
低 而充型 速度 和 压 力不足 ,铝液 在型腔 中 过早 凝 固 使 风叶 豉 平衡 柱 型腔 不满 。 ()防 Ⅱ缺 陷 的措施 2 :
() b 采用台理 的最大充型参数 ;
断条
低 压 铸 铅 转 子常 见 的 缺 陷 是 裂纹 、转 子 风
1 概 述
使用 电动 机转 子低 压铸铝 工艺在 我厂 已有 1 5
叶 、平衡柱残缺或注不满 、缩孔 、气孔 、 断条和
细 条等 。现 对 以上 低压铸 铝转 子 的 常见缺 陷所 产
生的原因加以分析 , 并针对性地制定 出防止措施 。
- 1、下载文档前请自行甄别文档内容的完整性,平台不提供额外的编辑、内容补充、找答案等附加服务。
- 2、"仅部分预览"的文档,不可在线预览部分如存在完整性等问题,可反馈申请退款(可完整预览的文档不适用该条件!)。
- 3、如文档侵犯您的权益,请联系客服反馈,我们会尽快为您处理(人工客服工作时间:9:00-18:30)。
铸铝转子质量的工艺分析及措施
转子质量问题专题调查分析如下:
铸铝转子质量问题,最突出的表现就是转子内部存在的气孔的问题,其次就是转子内部的笼条细条、断条、夹渣以及端环部分的缩孔、冷裂、热裂、缺肉等。
这些问题的产生,最终导致整机的电气性能下降、转速不够、效率降低。
1、转子片间存油未去除:
这是转子产生气孔的一个主要原因,由于转子铸铝是在高温、高压、瞬间形成的一个过程,在铝液刚刚充满转子型腔,高温铝还是液态而与转子片间的油类发生反应时,生成气体,这种气体有些被逸出,有些被铝液包围,然而铝液迅速固化,被包围的气体跑不出去,因此这些气体以气泡的形式残留在转子的笼条和端环中,呈不规则分布状态。
解决的办法为:铸铝前的转子铁芯应进行脱油处理,具体做法为:转子铁芯可用工业清洗剂冷态脱油,自来水冲洗,电炉烘干。
烘干温度以不破坏冲片表面保护膜为准,烘干时间以目测干透为准。
我们在5月19日已经做过96个转子脱油的实验,用拉上同型号转子和实验品转子各10个,装入同型号定子各10台,由抽查室做负载对比检查,结果装有实验品转子的电机比拉上同型号电机的转速平均提高2.5%以上。
2、铝液的清化问题:
这个问题也是铸铝转子产生气孔的一个主要问题,铝锭及回炉铝在加热熔解过程中,与空气中的水蒸气接触时(尤其是多雨季节),一方面生成氧化铝沉于铝液底部,另一方面分解出氢气,同时氢气也渗入铝水中。
含有气体的铝水压铸出来的转子质量很差,因为铝水在压铸成型的瞬间,铝水迅速固化,一部分气体还未来得及逸出而被固化的铝包围,从而留在铸件内造成气孔。
另外就是铝液表面上的浮渣、铝液底部的沉渣以及留在铝液中间的其它杂物对转子的质量来说也是一个很大的隐患,一旦将这些渣滓和杂物压入转子内部,它们会使转子造成夹渣、形成冷隔(电阻系数增加)、热裂和冷裂的现象,热裂和冷裂严重时造成转子笼条断路。
为了解决上述问题,加入清化剂(氯盐:一般为NaCl 、ZnCl)可以较好的解决这一问题。
清化处理的原理,主要就是将氯化物烘干,利用钟罩将其沉于铝液底部搅动,通过置换反应,生成氯化铝,氯化铝的沸点是183度,在铝水中以升华的形式逸出,同时伴随气泡发生。
由于气泡的作用,铝水中的氢会自动扩散到氯化铝中去,并随着气泡的上升而逸出液面,从而达到除气的作用。
另一方面氯盐与氧化铝发生作用生成氯化铝,氯化铝的升华使这些氧化物得以借翻腾的气泡而浮于液面,从而易于除渣。
目前,车间铸铝的操作员工在加入清化剂时应该怎么加、何时加、加多少,这是一个关键问题,否则达不到除气的效果。
目前的操作过程是这样的:
熔新铝锭---加入部分余料------至熔化(采用目测温度、温控不准确)约700多度--------加入半包精炼剂(约0.5kg)----清化、除渣-------保温待铸-----压铸-----
投入余料------压铸-----投入余料----- -- 压铸------(反复循环)(产生气体)(产生气体)
从以上过程可以看出,压铸前一次性清化并不能使铝液的纯洁“永保平安”,投入余料过程中产生的气体实质上是最大隐患。
随着余料的不断投入,铝液中的气体越积越多,铝液的质量就越来越差,然而将这些含有气体的铝液压入到转子中去,转子的质量当然就得不到保证。
《转子铸铝工艺手则》中的第四.6.2)E款中提到装料熔化时,先加预热好的新纯铝,再加回炉料,回炉料的加入量小于或等于16kg,并未说明回炉料可以随时加入;在第七条“注意事项”第四款中注明坩埚内液面至锅底不足100-150mm时,停止压铸,重新熔铝。
可见《守则》中并未赞同回炉料可以随时加入。
但车间操作人员在压铸过程中随时加入回炉料却是由来已久了。
我们认为:如果每班在压铸前加入一次性清化剂的话,则该过程中回炉料不允许加入;如果该过程中间非得要加入回炉料的话,也应分批投入并及时加入清化剂。
清化剂的加入量严格按照《守则》规定的参数执行。
3、压铸温度的问题:
铝液温度不够,使铝液的流动性降低,加上铝液在压铸机注入口停留一段时间,又会降低一些液温,铝液在压入型腔时,由于浇道口的尺寸太小,致使铝液的流动性更加变差,铝液虽被压入型腔后,但过低的铝温使之固化速度加快,可是浇道口尺寸太小,本身就限制了铝液的流动,另外浇道口的铝液也会迅速固化从而堵塞了料饼“后续部队”的支援、致使型腔和端环部位得不到铝液的补充,从而形成了气孔。
为解决这一问题,必须提高铝液的压铸温度,使铝液温度控制在720±5˙范围内,确保铸铝转子质量(请公司考虑,购置一些温控仪器)。
4、铝液的保护:
铝液很容易氧化,在铝液表面上生成一层氧化铝薄膜,它具有良好的保护作用,能够防止氧化的继续进行,也能防止气体进入铝液中。
但是当操作工用勺取铝液时一定要注意用勺底轻轻将该层氧化膜拨开,不可将该层薄膜打碎。
因为氧化铝很容易集结成块混入铝水中去,氧化铝的密度约为
3.95~
4.10,大于纯铝的密度(2.7),熔点很高,约2050
度,它们一旦混入铝液中就不再浮出来,也不溶于铝水,而是成颗粒状存在于铝水中,如果采用这样的铝液压铸转子,不仅降低了铝液的流动性,而且增大了铝的电阻率,影响转子性能。
我们认为,铝水保温时,不要随便破坏铝液表面的氧化层,在压铸取铝水时,注意不要把氧化膜打碎渗入到铝水中去。
5、脱模剂的使用:
脱模剂中的水分不宜过多,更不能喷洒在型腔中,只能在模具的分型面上均匀的喷上薄薄的一层,否则在压铸时,铝液很容易与水发生反应,产生气体,使转子中的气孔增加。
6、关于压铸后的保压时间:
较大、较长的一些转子,经过压射以后的铝液,正处于半熔和补缩的阶段,铝液还来不及固化时,浇口部位的铝液还在补充型腔,如果保压时间过短,正处于固化和收缩阶段的铝液就得不到充分的补缩,容易导致浇口部位产生冷缩、缩裂、甚至还会连同“铝肉”随同浇口余料拉去一部分,减少了转子端环截面积。
保压时间不好定性,应靠操作工人从实践中掌握一套经验和办法来确保转子压铸质量。
7、合理的注射系统:
合理的注射系统很重要,它是铝液压射入型腔保证质量的关键,它包括压射室、储料室、浇道、浇口及排气系统及合适的压射速度、比压力等。
一般来说,压射室、储料室、浇道基本上都能满足目前压铸转子的性能要求,但浇口尺寸的大小、排气面的合理设计、压射速度的快慢、比压力的大小等都是不可忽视的。
排气面的设计及分布决定了在压铸瞬间模腔里的气体是否能及时排出,设计合理的排气面应能使气体及时排出而保证铝水不致由排气面喷出。
排气面分布的位置应是气体最后排出的地方,不能使型腔内部存在余气的“死角”,否则转子端环将会产生气孔。
压射速度的快慢同样对压铸转子的质量起到关键作用,压力铸造时,铝水压射到转子铁心槽和型腔中的速度很高,其填充速度可达10~25m/s。
整个压铸过程是在瞬间完成的。
如果铝水充型速度很快,充型速度大于空气排出速度,堵塞排气系统,并形成旋涡及喷雾,型腔内的空气难于排尽,会使气体滞留在型腔内部,产生气孔。
如果铝水充型速度低,铝水固化快,型腔内部可能填充不满,造成转子笼条组织疏松及欠铸现象。
铝水的比压力(铸件型腔内单位面积上所受的静压力)
P=4Q/πD2
P——比压力;
Q——压射压力:N
D——压射活塞直径;m
是铸件获得组织紧密和轮廓清晰的主要因素。
增大铝水的比压力可以提高转子笼条的致密性和端环的光洁,但过高的比压力,易使模具受铝液的强烈冲刷,并增加了粘模的可能性,降低模具的使用寿命,因此,在保证铸件组织致密的情况下,尽量用较低的比压力,一般约在60~100MN/m2。
8、员工的素质要求:
压铸工作在本公司来说是一项关键工序,对员工的文化素质要求应较高一些,对文化素质薄弱的员工应加强培训,以提高其质量意识,另外要对员工加强对设备的保养及对模具的爱护,增强压铸过程中的自我安全保护意识。
9、确保设计参数:
铸铝转子铁心在压假轴的工序中,压装时有丢片现象,转子的净铁长得不到保证,净铁长不够会使电机定、转子铁心平面不在同一平面上。
导致定转子有效磁感应长度减少(线圈切割磁力线的长度),影响电机的整机性能,达不到设计要求。
我们认为,在铸铝转子质量还未稳定之前,暂时不要采取丢片的方法,等转子铸铝质量稳定以后,视情况取舍。
10、机加工过程中转子质量的问题:
在机加工车间,转子外径的粗加工是采用叉式工装带动转子的运转,转子端环被深深的叉出了六道叉痕,痕迹最深可达1毫米左右,实际上减少了端环的截面积,影响了电机的整机性能。
建议:改叉式工装为浅凸台摩擦片式工装,既不影响端环部位的有效截面积,又能起到传动作用,加工速度不受影响。
综上所述,除了温控之外,其余各方面我们都是可以做得到的。
以上是我们对目前转子质量的分析和建议意见,有不妥之处,请予以斧正。
2010-5-27。