粉末涂料
粉末涂料原材料
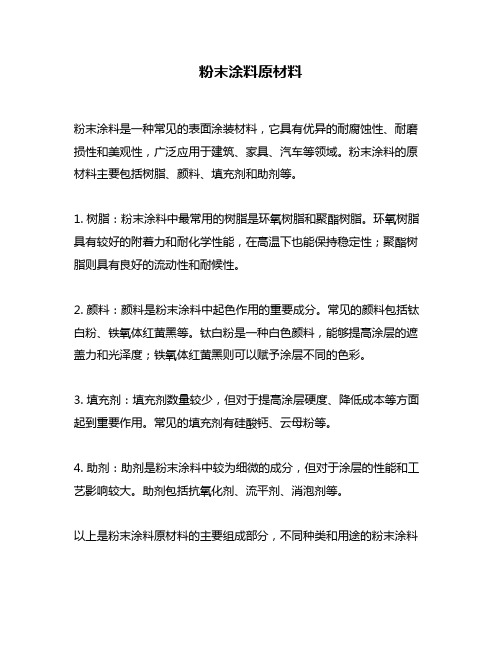
粉末涂料原材料
粉末涂料是一种常见的表面涂装材料,它具有优异的耐腐蚀性、耐磨损性和美观性,广泛应用于建筑、家具、汽车等领域。
粉末涂料的原材料主要包括树脂、颜料、填充剂和助剂等。
1. 树脂:粉末涂料中最常用的树脂是环氧树脂和聚酯树脂。
环氧树脂具有较好的附着力和耐化学性能,在高温下也能保持稳定性;聚酯树脂则具有良好的流动性和耐候性。
2. 颜料:颜料是粉末涂料中起色作用的重要成分。
常见的颜料包括钛白粉、铁氧体红黄黑等。
钛白粉是一种白色颜料,能够提高涂层的遮盖力和光泽度;铁氧体红黄黑则可以赋予涂层不同的色彩。
3. 填充剂:填充剂数量较少,但对于提高涂层硬度、降低成本等方面起到重要作用。
常见的填充剂有硅酸钙、云母粉等。
4. 助剂:助剂是粉末涂料中较为细微的成分,但对于涂层的性能和工艺影响较大。
助剂包括抗氧化剂、流平剂、消泡剂等。
以上是粉末涂料原材料的主要组成部分,不同种类和用途的粉末涂料
原材料比例和配方也有所不同。
在生产过程中,需要根据具体情况进行调整和控制,以保证涂层质量和稳定性。
粉末涂料的用途

粉末涂料的用途粉末涂料是一种常用的涂料,广泛应用于工业生产和个人家居装修中。
它是一种以固态粉末为基础的涂料,具有诸多优点,如环保、耐用、易于清洁等,因此越来越受到人们的青睐。
本文将详细介绍粉末涂料的用途。
一、工业应用1. 金属制品粉末涂料在金属制品上的应用非常广泛,例如汽车、机械、电器、建筑等。
在汽车制造中,粉末涂料可以用于车身、底盘、轮毂等部分的涂装,具有良好的防腐、耐磨、耐高温等特点,可以有效延长汽车的使用寿命。
在机械制造中,粉末涂料可以用于机器壳体、零部件等的涂装,可以有效保护机器不受外界环境的影响。
在电器制造中,粉末涂料可以用于电器外壳、散热器等部分的涂装,可以提高电器的绝缘性能和耐腐蚀性能。
在建筑领域中,粉末涂料可以用于钢结构、铝合金、玻璃幕墙等部分的涂装,可以使建筑更加美观、耐久、环保。
2. 木制品粉末涂料在木制品上的应用也越来越广泛,例如家具、地板、门窗等。
在家具制造中,粉末涂料可以用于框架、脚架、扶手等部分的涂装,可以使家具更加美观、耐用、易于清洁。
在地板制造中,粉末涂料可以用于地板支撑和地板表面的涂装,可以提高地板的耐磨性和防水性。
在门窗制造中,粉末涂料可以用于门窗框架、门扇、窗框等部分的涂装,可以使门窗更加美观、耐用、易于清洁。
二、个人家居装修1. 家庭装修粉末涂料在家庭装修中的应用非常广泛,例如墙面、天花板、地面等。
在墙面装修中,粉末涂料可以用于墙面涂装,可以提高墙面的耐久性、防水性和易于清洁性。
在天花板装修中,粉末涂料可以用于天花板涂装,可以提高天花板的防水性和耐久性。
在地面装修中,粉末涂料可以用于地面涂装,可以提高地面的耐磨性和防水性。
2. 家居用品粉末涂料在家居用品中的应用也越来越广泛,例如厨房用具、卫生间用品、家用电器等。
在厨房用具中,粉末涂料可以用于锅、碗、盘等部分的涂装,可以提高厨具的耐磨性、防水性和易于清洁性。
在卫生间用品中,粉末涂料可以用于淋浴房、马桶、水龙头等部分的涂装,可以提高卫浴用品的防水性、耐腐蚀性和易于清洁性。
粉末涂料的配方设计
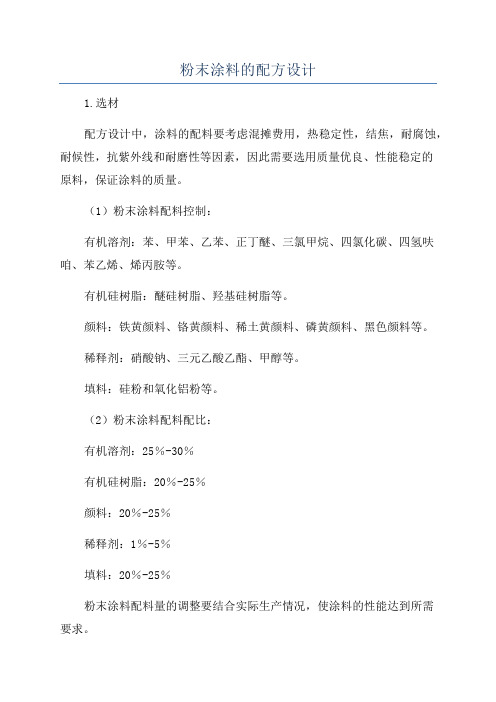
粉末涂料的配方设计
1.选材
配方设计中,涂料的配料要考虑混摊费用,热稳定性,结焦,耐腐蚀,耐候性,抗紫外线和耐磨性等因素,因此需要选用质量优良、性能稳定的
原料,保证涂料的质量。
(1)粉末涂料配料控制:
有机溶剂:苯、甲苯、乙苯、正丁醚、三氯甲烷、四氯化碳、四氢呋咱、苯乙烯、烯丙胺等。
有机硅树脂:醚硅树脂、羟基硅树脂等。
颜料:铁黄颜料、铬黄颜料、稀土黄颜料、磷黄颜料、黑色颜料等。
稀释剂:硝酸钠、三元乙酸乙酯、甲醇等。
填料:硅粉和氧化铝粉等。
(2)粉末涂料配料配比:
有机溶剂:25%-30%
有机硅树脂:20%-25%
颜料:20%-25%
稀释剂:1%-5%
填料:20%-25%
粉末涂料配料量的调整要结合实际生产情况,使涂料的性能达到所需
要求。
二、涂料配方设计
1.首先要明确涂料性质的要求,如涂料的气味挥发量、耐候性、耐腐蚀性、抗紫外线性能、施涂平整度、涂膜厚度等;
2.依据涂料性能的要求,确定配料功能,选择满足要求的原料,如有机液体树脂作为连续体,有机硅树脂作为粘结剂,溶剂作为涂料的低温。
粉末涂料讲义ppt课件
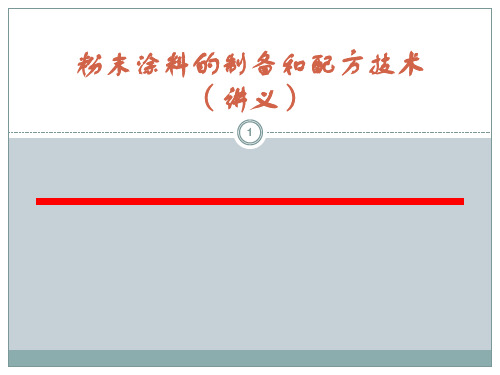
三、工艺原理及其控制方法和原则
21
2、混炼、挤出工序 粉末涂料树脂等材料的相互溶解以及树脂对颜填
料的润湿和分散就是在这个过程进行的。料斗内的物 料被螺旋进料器送入螺筒,螺杆的螺旋进料器将物料 送进加有一定温度的螺筒后,树脂开始熔融,进而树 脂间开始溶解并对颜填料进行润湿。螺杆上的捏合块 在螺筒内的转动对物料产生的剪切力强化了溶解和润 湿过程。
的排布结构、长短、间隙等则决定机器的混炼效果
的好坏。ቤተ መጻሕፍቲ ባይዱ
11
二 热固性粉末涂料的制备工艺 ⅲ 冷却破碎设备:压片破碎机
12
结构:由机架、压辊、输送带、冷风机和破碎辊等组成。 用途:该机对熔融状物料可轧成厚度1.5mm左右的片状, 在输送过程中经护罩上方的冷风机风冷后,破碎成片状。
二 热固性粉末涂料的制备工艺 ⅳ磨粉筛分设备
粉末涂料的制备和配方技术 (讲义)
1
一 粉末涂料的定义、组成和分类
1. 涂料的定义:是能涂敷于底材表面并形2成坚韧连续涂膜的液体或固体高分子材料 (摘自于中国大百科全书-化工卷)。粉末涂料顾名思义就是固体粉末状的涂料, 或叫粉体涂料。由于其性能和加工过程与塑料相似,又称之为塑粉(塑料粉末)。
2. 粉末涂料的组成: 成膜物质:树脂,是涂料成膜的基础,是粘结颜填料形成坚韧连续膜的主要组分。 颜料:赋予粉末涂料遮盖性和颜色。 填料:增加粉末涂料涂膜的耐久性和耐磨性,降低涂膜的收缩率和降低成本。 助剂:增加粉末涂料的成模性,改善或消除涂膜的缺陷,或使涂膜形成纹理。 功能组分:赋予涂膜某种特殊功能,如:导电、阻燃等等。
度
、 料规 流定
过 器定 值时
实
转 参记
,
速 数录
,
螺
二 热固性粉末涂料的制备工艺
粉末涂料定义与分类
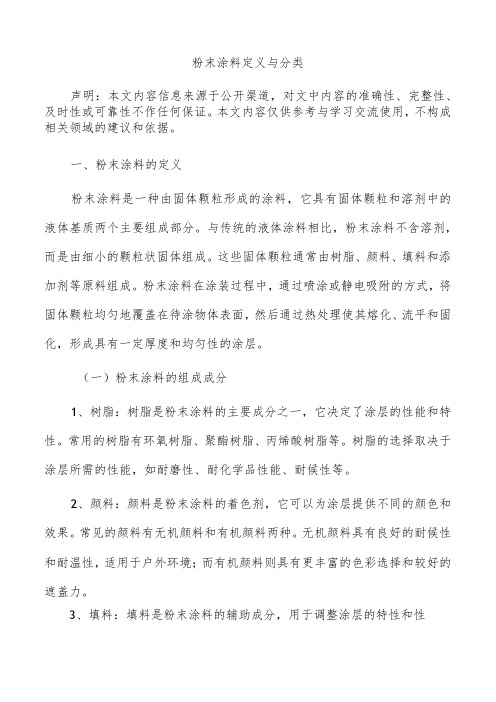
粉末涂料定义与分类声明:本文内容信息来源于公开渠道,对文中内容的准确性、完整性、及时性或可靠性不作任何保证。
本文内容仅供参考与学习交流使用,不构成相关领域的建议和依据。
一、粉末涂料的定义粉末涂料是一种由固体颗粒形成的涂料,它具有固体颗粒和溶剂中的液体基质两个主要组成部分。
与传统的液体涂料相比,粉末涂料不含溶剂,而是由细小的颗粒状固体组成。
这些固体颗粒通常由树脂、颜料、填料和添加剂等原料组成。
粉末涂料在涂装过程中,通过喷涂或静电吸附的方式,将固体颗粒均匀地覆盖在待涂物体表面,然后通过热处理使其熔化、流平和固化,形成具有一定厚度和均匀性的涂层。
(一)粉末涂料的组成成分1、树脂:树脂是粉末涂料的主要成分之一,它决定了涂层的性能和特性。
常用的树脂有环氧树脂、聚酯树脂、丙烯酸树脂等。
树脂的选择取决于涂层所需的性能,如耐磨性、耐化学品性能、耐候性等。
2、颜料:颜料是粉末涂料的着色剂,它可以为涂层提供不同的颜色和效果。
常见的颜料有无机颜料和有机颜料两种。
无机颜料具有良好的耐候性和耐温性,适用于户外环境;而有机颜料则具有更丰富的色彩选择和较好的遮盖力。
3、填料:填料是粉末涂料的辅助成分,用于调整涂层的特性和性能。
常见的填料有滑石粉、硅酸钙、氧化铝等。
填料的添加可以改善涂层的硬度、抗刮擦性和耐磨性。
4、添加剂:添加剂主要用于调整涂料的流动性、干燥速度和附着力等特性。
常见的添加剂有流平剂、增稠剂、固化剂等。
这些添加剂可以使粉末涂料适应不同的涂装工艺和需求,提高涂层的质量和性能。
(二)粉末涂料的分类根据不同的分类标准,粉末涂料可以分为多种类型。
1、按树脂类型分类:按照粉末涂料所使用的主要树脂类型,可以将其分为环氧粉末涂料、聚酯粉末涂料、丙烯酸粉末涂料等。
不同类型的树脂具有不同的特性和适用范围,可以满足各种不同的涂装需求。
2、按应用领域分类:按照粉末涂料在不同领域中的应用,可以将其分为建筑用粉末涂料、汽车用粉末涂料、电器用粉末涂料等。
粉末涂料用途有哪些
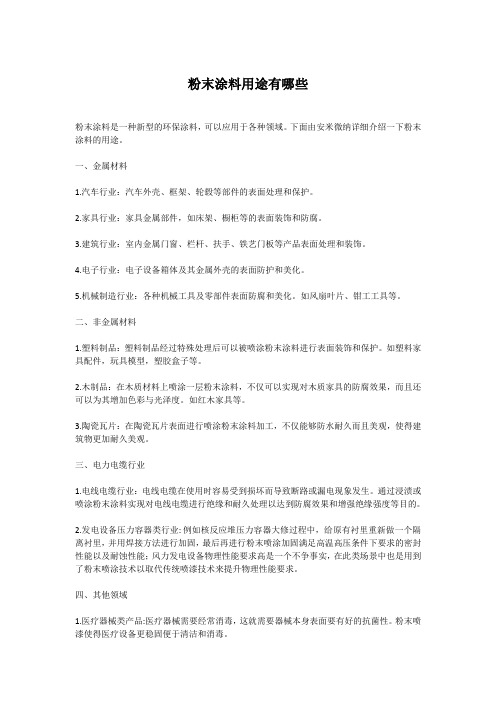
粉末涂料用途有哪些粉末涂料是一种新型的环保涂料,可以应用于各种领域。
下面由安米微纳详细介绍一下粉末涂料的用途。
一、金属材料1.汽车行业:汽车外壳、框架、轮毂等部件的表面处理和保护。
2.家具行业:家具金属部件,如床架、橱柜等的表面装饰和防腐。
3.建筑行业:室内金属门窗、栏杆、扶手、铁艺门板等产品表面处理和装饰。
4.电子行业:电子设备箱体及其金属外壳的表面防护和美化。
5.机械制造行业:各种机械工具及零部件表面防腐和美化。
如风扇叶片、钳工工具等。
二、非金属材料1.塑料制品:塑料制品经过特殊处理后可以被喷涂粉末涂料进行表面装饰和保护。
如塑料家具配件,玩具模型,塑胶盒子等。
2.木制品:在木质材料上喷涂一层粉末涂料,不仅可以实现对木质家具的防腐效果,而且还可以为其增加色彩与光泽度。
如红木家具等。
3.陶瓷瓦片:在陶瓷瓦片表面进行喷涂粉末涂料加工,不仅能够防水耐久而且美观,使得建筑物更加耐久美观。
三、电力电缆行业1.电线电缆行业:电线电缆在使用时容易受到损坏而导致断路或漏电现象发生。
通过浸渍或喷涂粉末涂料实现对电线电缆进行绝缘和耐久处理以达到防腐效果和增强绝缘强度等目的。
2.发电设备压力容器类行业: 例如核反应堆压力容器大修过程中,给原有衬里重新做一个隔离衬里,并用焊接方法进行加固,最后再进行粉末喷涂加固满足高温高压条件下要求的密封性能以及耐蚀性能;风力发电设备物理性能要求高是一个不争事实,在此类场景中也是用到了粉末喷涂技术以取代传统喷漆技术来提升物理性能要求。
四、其他领域1.医疗器械类产品:医疗器械需要经常消毒,这就需要器械本身表面要有好的抗菌性。
粉末喷漆使得医疗设备更稳固便于清洁和消毒。
2.道路交通标识牌:道路标识牌上多数采用反光复合材质。
喷有反光剂后再进行喷漆处理。
可以精确控制每个道路标示牌上反光度值并达到长久、稳定的反光效果。
3.管道类产品:管道每年都会遭受较为恶劣的自然因素及氧气氯离子流动刮伤等威胁。
粉末涂料基础知识-精品文档
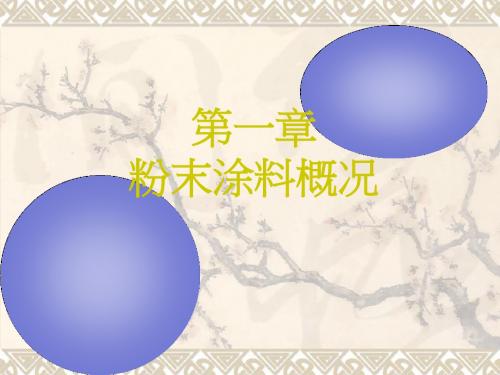
净化。
3. 受 灰 尘 或 其 它 杂 质 污 染 。 3. 彻 底 清 理 环 境 、更 换 合 格 粉来。
现象
产生原因
预防方法
1. 工件表面粗糙。 1. 提高工件光洁度。
2. 粉末粒子粗或受 2. 选择粒度分布均匀的高质量
潮。
粉末及严防粉末受潮。
涂膜 3. 固化温度偏高或 3. 调整适宜的固化条件。
第一章 粉末涂料概况
一、粉末涂料和溶剂型涂料的区别
1.定义:
粉末涂料为100%固体分。以粉 末形态进行涂装并在工件上形成保 护膜的涂料,它和溶剂涂料不同, 它不使用溶剂作为分散介质,而是 借助空气作为分散介质。
2.粉末涂料的优缺点:
a.无溶剂,所以低公害。目前全世界每年向大气排 放的挥发性有机物(VOC)日益增长已达2000万 吨/年,影响环境和人体健康,而涂料(溶剂型) 是第二排放源头,粉末涂料发展如此迅速和无溶制粉末厚度在 60-80μm。
桔皮 4. 涂 膜 太 薄 或 太 5. 定期清理挂具。
厚。
6. 施工前严格清理喷粉系统及
5. 工件接地不良。 场地,避免不同类型或不同
6. 不同粉末混杂。 厂家的粉末混用。
现象
产生原因
预防方法
1.底材前处理质量差。 1. 选 择 合 适 的 前 处 理 工
2.烘 烤 时 间 过 长 或 温 度 艺。
过高。
2. 调整适宜的固化条件。
涂膜 3.炉内有挥发性气体。 3. 净化烤炉。
表面 4.回 收 粉 使 用 比 例 过 4. 回收粉过滤后与新粉混
失光 大。
合 用 , 以 < 30% 为 宜 。
5.两 种 不 同 性 质 的 粉 末 5. 换粉前彻底清理喷粉系
第四讲 水性涂料、粉末涂料
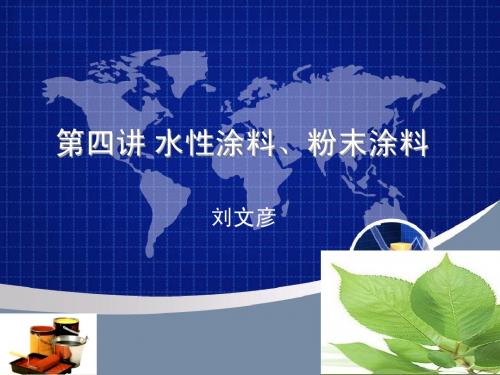
•
3、制作工艺 • 涂料由特制树脂、颜填料、固化剂及其 它助剂,以一定的比例混合,再通过热 挤塑和粉碎过筛等工艺制备而成。它们 在常温下,贮存稳定,经静电喷涂、摩 擦喷涂(热固方法)或流化床浸涂(热 塑方法),再加热烘烤熔融固化,使形 成平整光亮的永久性涂膜,达到装饰和 防腐蚀的目的。
4、特性
• 1、该产品不含毒性,不含溶剂和不含挥发有毒性的物 质,故无中毒、无火灾、无“三废”的排放等公害的问 题,完全符合国家环保法的要求。 • 2、原材料利用率高,一些知名品牌的粉末供应商生产 的粉末,其过喷的粉末可回收利用,最高的利用率甚至 能达99%以上。 • 3、被涂物前处理后,一次性施工,无需底涂,即可得 到足够厚度的涂膜,易实现自动化操作,生产效率高, 可降低成本。 • 4、涂层致密、附着力、抗冲击强度和韧性均好,边角 覆盖率高,具有优良的耐化学药品腐蚀性能和电气绝缘 性能。 • 5、粉末涂料存贮、运输安全和方便。
第四讲 水性涂料、粉末涂料
刘文彦
内容提纲
一、水性涂料 二、粉末涂料(概述) 粉末涂料(概述)
一、水性涂料
• • • • • • 1、定义 2、简介 3、分类 4、水性涂料的优缺点 5、水性涂料两个关键问题 6、水性涂料喷涂施工操作技巧
1、定义
• 凡是用水作溶剂或者作分散介质的涂料, 都可称为水性涂料。 • 水性涂料包括水溶性涂料、水稀释性涂料、 水分散性涂料(乳胶涂料)3种。
5、水性涂料存在的问题:
• 1. 水性涂料对施工过程中及材质表面清洁度要求高,因水 的表面张力大,污物易使涂膜产生缩孔; • 2. 水性涂料对抗强机械作用力的分散稳定性差,输送管道 内的流速急剧变化时,分散微粒被压缩成固态微粒,使涂 膜产生麻点。要求输送管道形状良好,管壁无缺陷。 • 3. 水性涂料对涂装设备腐蚀性大,需采用防腐蚀衬里或不 锈钢材料,设备造价高。水性涂料对输送管道的腐蚀,金 属溶解,使分散微粒析出,涂膜产生麻点,也需采用不锈 钢管。 • 4. 烘烤型水性涂料对施工环境条件(温度、湿度)要求较 严格,增加了调温调湿设备的投入,同时也增大了能耗。
粉末涂料的用途
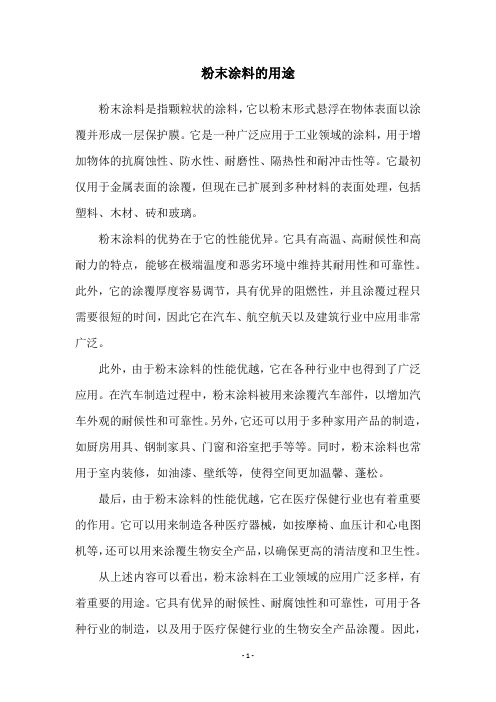
粉末涂料的用途
粉末涂料是指颗粒状的涂料,它以粉末形式悬浮在物体表面以涂覆并形成一层保护膜。
它是一种广泛应用于工业领域的涂料,用于增加物体的抗腐蚀性、防水性、耐磨性、隔热性和耐冲击性等。
它最初仅用于金属表面的涂覆,但现在已扩展到多种材料的表面处理,包括塑料、木材、砖和玻璃。
粉末涂料的优势在于它的性能优异。
它具有高温、高耐候性和高耐力的特点,能够在极端温度和恶劣环境中维持其耐用性和可靠性。
此外,它的涂覆厚度容易调节,具有优异的阻燃性,并且涂覆过程只需要很短的时间,因此它在汽车、航空航天以及建筑行业中应用非常广泛。
此外,由于粉末涂料的性能优越,它在各种行业中也得到了广泛应用。
在汽车制造过程中,粉末涂料被用来涂覆汽车部件,以增加汽车外观的耐候性和可靠性。
另外,它还可以用于多种家用产品的制造,如厨房用具、钢制家具、门窗和浴室把手等等。
同时,粉末涂料也常用于室内装修,如油漆、壁纸等,使得空间更加温馨、蓬松。
最后,由于粉末涂料的性能优越,它在医疗保健行业也有着重要的作用。
它可以用来制造各种医疗器械,如按摩椅、血压计和心电图机等,还可以用来涂覆生物安全产品,以确保更高的清洁度和卫生性。
从上述内容可以看出,粉末涂料在工业领域的应用广泛多样,有着重要的用途。
它具有优异的耐候性、耐腐蚀性和可靠性,可用于各种行业的制造,以及用于医疗保健行业的生物安全产品涂覆。
因此,
它不仅被广泛应用于工业生产领域,而且也为消费者提供了更好的使用体验。
粉末涂料讲义ppt课件

,
保副按 证磨规 磨、定 体进调 内料整 温器好 度的风 正速量 常度以
,及
抽批破随 样次、时
量漏做 为筛筛 单。析 位以样 进每以 行个确 中投定 控料无
工后 混 加
二 热固性粉末涂料的制备工艺
6
2.粉末涂料的生产设备及其结构和工作原理 热固性粉末涂料的生产设备一般分为四个部分:配料 系统、混炼挤出(分散)系统、冷却破碎系统和磨 粉系统。
.
7
二 热固性粉末涂8 料的制备工艺
ⅱ.混练挤出设备:双螺杆挤出机;单螺杆 挤出机。
.
二 热固性粉末涂料的制备工艺
双螺杆挤出机
1.主电机(螺杆 的动力电机)
2.变速齿轮箱 (螺杆的传动装
置) 3.进料电机 4.料斗 5.螺旋进料器 6.螺杆进口料斗 7.操控仪表盘 8. 挤出螺筒
.
9
二 热固性粉末涂料的制备工艺 双螺杆的结构
热固性粉末涂料生产工艺流程及要点
5
破 碎
冷 却 、
压 片 、
筛磨 粉 过
装计 量 包
机启开接开 能片整辊待 动启料启 够在好距挤 挤轧器压 充达钢并出 出辊皿片 分到带协物 机冷、机 冷破速调料 前却粗之 却碎度挤出 启水调前 辊,出来 动阀辊先 处保速后 压、距备 之证度细 片在,好 前料调调
.
件筛按 启次待按 的网要 动启风照 连并求 进动机规 接检装 料其风定 是查好 器它量程 否各规 部稳序 牢管定 分定启 固道目 ,后动
.
二 热固性粉末涂料的制备工艺 ⅳ磨粉筛分设备
13
口粗 粉 出
成品出口
分共 离分
四 次 传 输 , 三 次
小片状物料通过料斗下部的进料器送入磨机,在高速转动主磨盘上的击柱冲
粉末涂料配方技术
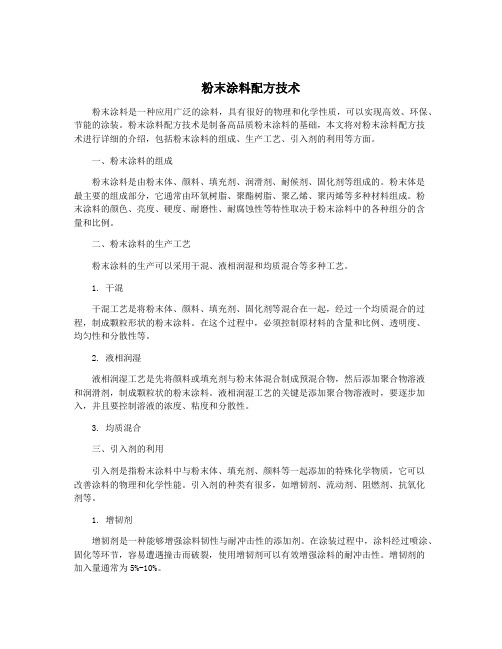
粉末涂料配方技术粉末涂料是一种应用广泛的涂料,具有很好的物理和化学性质,可以实现高效、环保、节能的涂装。
粉末涂料配方技术是制备高品质粉末涂料的基础,本文将对粉末涂料配方技术进行详细的介绍,包括粉末涂料的组成、生产工艺、引入剂的利用等方面。
一、粉末涂料的组成粉末涂料是由粉末体、颜料、填充剂、润滑剂、耐候剂、固化剂等组成的。
粉末体是最主要的组成部分,它通常由环氧树脂、聚酯树脂、聚乙烯、聚丙烯等多种材料组成。
粉末涂料的颜色、亮度、硬度、耐磨性、耐腐蚀性等特性取决于粉末涂料中的各种组分的含量和比例。
二、粉末涂料的生产工艺粉末涂料的生产可以采用干混、液相润湿和均质混合等多种工艺。
1. 干混干混工艺是将粉末体、颜料、填充剂、固化剂等混合在一起,经过一个均质混合的过程,制成颗粒形状的粉末涂料。
在这个过程中,必须控制原材料的含量和比例、透明度、均匀性和分散性等。
2. 液相润湿液相润湿工艺是先将颜料或填充剂与粉末体混合制成预混合物,然后添加聚合物溶液和润滑剂,制成颗粒状的粉末涂料。
液相润湿工艺的关键是添加聚合物溶液时,要逐步加入,并且要控制溶液的浓度、粘度和分散性。
3. 均质混合三、引入剂的利用引入剂是指粉末涂料中与粉末体、填充剂、颜料等一起添加的特殊化学物质,它可以改善涂料的物理和化学性能。
引入剂的种类有很多,如增韧剂、流动剂、阻燃剂、抗氧化剂等。
1. 增韧剂增韧剂是一种能够增强涂料韧性与耐冲击性的添加剂。
在涂装过程中,涂料经过喷涂、固化等环节,容易遭遇撞击而破裂,使用增韧剂可以有效增强涂料的耐冲击性。
增韧剂的加入量通常为5%-10%。
2. 流动剂流动剂是一种能够改善涂料的流动性与涂刷性的添加剂。
在涂装过程中,涂料的流动性和涂刷性会影响到涂层的平整度与光洁度,使用流动剂可以有效改善涂料的流动性和涂刷性。
流动剂的加入量通常为0.5%-2%。
3. 阻燃剂4. 抗氧化剂抗氧化剂是一种能够提高涂料的耐黄变、耐氧化性的添加剂。
粉末涂料

粉末涂料:分类/化学组成
2019/1/12
羟基丙稀酸涂料 也称为丙烯酸聚氨酯,羟基丙稀酸涂料与聚酯型聚 氨酯类似,但具有更好的耐候性。如同聚酯型聚氨 酯涂料,丙烯酸聚氨酯涂料具有非常好的平滑度和 低成膜厚度,但与聚酯不同,其柔韧性和抗冲击强 度通常欠佳。同樣地,羟基丙稀酸涂料在成膜厚度 大于3密耳时,可能释放出气体。
500小时
1,000小时 20分钟,375ºF
11
Flextronics Corporate Presentation
粉末涂料:分类/化学组成
2019/1/12
羧基丙烯酸涂料 羧基丙烯酸涂料又称为丙烯酸复合涂料,或 丙烯酸环氧混合型粉末涂料,羧基丙烯酸涂 料与环氧聚酯混合涂料类似。丙稀酸混合涂 料的耐候性稍好于环氧聚酯混合涂料,但同 样不被认为具有室外耐用性。
热塑型粉末的附着性质不佳,其基板通常必 须进行喷丸或喷砂处理和/或打底漆。这种 涂料通常用作功能性,而非装饰性涂层,且 通常用于流化床工艺。 对加工件进行预热,然后将其浸入粉末涂料 的流化床内,为基板提供一个10密耳或更 厚的完全的包膜。
4
Flextronics Corporate Presentation
8
Flextronics Corporate Presentation
粉末涂料:分类/化学组成
2019/1/12
丙烯酸型 在使用中,最常见的基于丙烯酸的工艺为: 羟基丙稀酸涂料、羧基丙烯酸涂料、以及甲 基丙烯酸缩水甘油酯(GMA)丙烯酸涂料工艺。
9
Flextronics Corporate Presentation
粉末涂料:分类/化学组成
2019/1/12
热固型粉末具有很好的功能性同时又有很好的装饰 性。在現時的市场,制造商同时需要二者,这种粉 末涂料能够以较小的膜厚度(通常为2到3密耳)达 到涂装的要求。热固型粉末具有优良的附着性质, 通常不需要打底。这些粉末涂料通常应用于经过机 械或化学预先处理的基板,并可以进行配制,以提 供多种不同的功能。这一化学分类还可分为两个子 类:抗紫外线 (UV)子类和不抗紫外线子类。(这种 性质通常称为耐候性)。一般说,环氧树脂和基于 环氧树脂的混合型粉末不抗紫外线;而大部分聚酯 、聚氨酯和丙烯酸粉末则可抗紫外线。
粉末涂料

•聚酯树脂-树脂硬而又有韧性,提供优异的机械性能;优异的
热稳定性,耐光性,耐候性;但是耐化学和耐溶剂性差
•丙烯酸树脂-树脂硬而又有韧性,提供优异的机械性能;优异
的热稳定性,耐光性,耐候性
•聚氨酯树脂-树脂硬而又有韧性,提供优异的机械性能;优异
的热稳定性,耐光性,耐候性;具有极佳的耐化学溶剂性能
•氟碳树脂-树脂硬而又有韧性;优异的热稳定性,耐光性,超
聚硫橡胶类固化剂主要有液态聚硫橡胶和多硫化合物两种。
颜料
常用的无机颜料有钛白、铁红、铅铬黄、云母氧化铁、 铝粉、铜金粉、炭黑等。
应具备如下的条件:
a) 颜料的物理、化学稳定性要好,不与树脂、固化剂、填 料、助剂等成分发生化学反应,成膜以后,不容易受酸、碱、 盐、溶剂等化学品的影响。 b) 颜料的着色力要强,遮盖力要强,有利于降低使用量, 节约成本。并在树脂中的分散性要好。 c) 颜料的耐光性(最好是达到7~8级)、耐候性(最好是达到5 级)、耐热性(耐热温度最好是达到粉末涂料的烘烤温度或超 过其温度)要好。 d)颜料应当是无毒。可溶性铅、镉、铬、汞≤50ppm。
环氧树脂合成
环氧树脂的种类繁多,不同类型的环氧树脂的合成方法 不同。环氧树脂的合成方法主要有两种: (1) 多元酚、多元醇、多元酸或多元胺等含活泼氢原子的化 合物与环氧氯丙烷等含环氧基的化合物经缩聚而得。
(2) 链状或环状双烯类化合物的双键与过氧酸经环氧化而成。
一、 双酚A型环氧树脂的合成 (1)合成原理
溶解。溶解后,将物料送至反应釜中,在搅拌下于50~55℃,4小时内滴加 完第一份NaOH溶液,在55~60℃下继续维持反应4小时。在85℃、 21.33kPa下减压回收过量的环氧氯丙烷。回收结束后,加苯溶解,搅拌加 热至70℃ 。然后在68~73℃下,于1小时内滴加第二份碱溶液,在68~73℃ 下维持反应3小时。然后冷却静置分层,将上层树脂苯溶液移至回流脱水 釜,下层的水层可加苯萃取一次后放掉。在回流脱水釜中回流至蒸出的苯 清晰无水时止,冷却、静置、过滤后送至脱苯釜脱苯,先常压脱苯至液温 达110℃以上,然后减压脱苯,至液温140~143℃无液体馏出时,出料包装。
粉末涂料
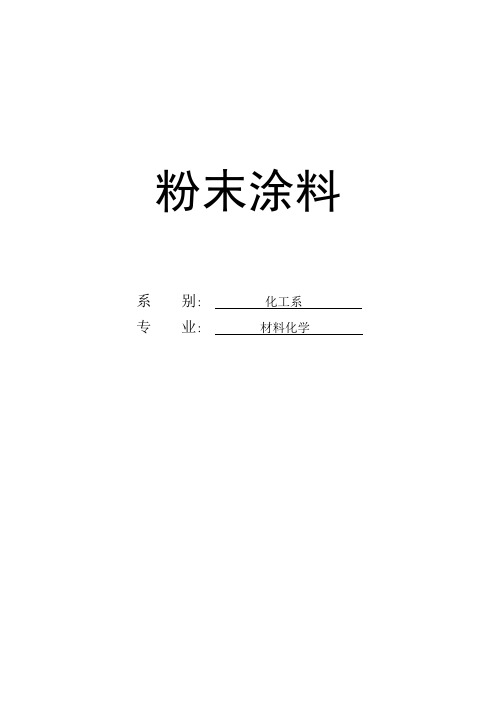
粉末涂料系别:化工系专业:材料化学目录一、前言 (4)1.粉末涂料的概念 (4)2.粉末涂料的特点 (4)2.1 粉末涂料的优点 (4)2.2 粉末涂料的缺点 (4)3 .粉末涂料的分类 (5)3.1 热塑性粉末涂料 (5)3.2 热固性粉末涂料 (6)4、粉末涂料的历史背景、现状及发展方向 (7)4.1粉末涂料的历史背景 (7)4.2粉末涂料的现状 (7)4.2.1粉末涂料生产现状 (7)4.2.2粉末涂料研究现状 (8)4.3 粉末涂料的发展趋势 (11)4.3.1 低温固化型粉末涂料 (11)4.3.2 粉末涂料的薄涂膜化 (11)4.3.3 变换颜色和回收系统简单化 (11)4.3.4功能性粉末涂料 (11)4.3.5 耐侯型粉末涂料 (12)4.3.6 美术型粉末涂料 (12)4.3.7 透明粉末涂料 (12)二、公司简介 (13)三、公司主要产品 (14)1.根据树脂类型分类 (14)2.根据表面状态分类 (14)四、产品的技术特点 (15)五、生产流程 (17)1.原材料的预混合 (17)2、熔融挤出混合 (18)3、冷却 (19)4、细粉碎和分级过筛 (20)5、粉末涂料成膜前的性能试验方法 (20)6、粉末涂料成膜后的性能试验方法 (21)7、出厂粉末涂料常规检测项目表 (21)六、公司的环境保护及发展状况 (22)七、见习感受及对公司的一些建议 (22)八、见习公司意见(签章) (23)九、见习成绩 (23)十、系主任意见 (23)。
粉末涂料
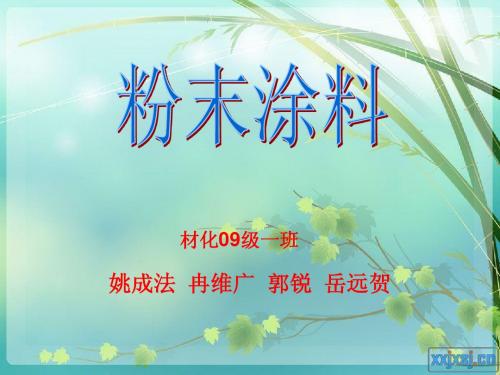
涂膜颜色不正,泛黄 原因:1、粉末涂料耐热性差 2、烘烤温度太高或烘 烤时间太长 解决措施: 1、改换耐热性好的粉末涂料; 2、降 低烘烤温度或者缩短烘烤时间。 涂膜冲击强度差 原因:1、烘烤温度达不到工艺要求温度; 2、烘烤 时间达不到工艺要求时间; 3、粉末涂料质量不好, 包括本身质量和贮存中质量下降。 解决措施: 1、检查烘烤温度,控制到工艺要求的 条件 2、延长烘烤时间,控制到工艺要求的时间; 3、换粉末涂料或改制。
4.应用 应用
1.装饰防护涂装 装饰防护涂装 2.绝缘防潮 绝缘防潮 3.防腐 防腐
5.发展趋势 发展趋势
国内:我国粉末涂料涂装市场的最大增长领域是:船舶工业 和管道工业。目前存在的问题是耐冲击性及吸湿性有待改善 和提高,研究人员把主要精力集中在用各种基料的改性上。 国内生产的管道防腐环氧粉末涂料涂装在贮存稳定性及涂覆 施工性方面,与国外优质产品相比尚有一定差距。 国际:国外汽车粉末涂料制备技术取得的进展,近年来,汽 车罩光、木材和塑料用涂料涂装都是最具活力的潜在市场。 汽车行业将是其消费大户,希腊、土耳其和东欧粉末涂料涂 装市场的增长势头很好亚太地区市场潜力更大已被认为是全 球增长最快的地区。
安全问题
成本高
3)沉淀法
配制溶剂型涂料→研磨 调色 配制溶剂型涂料 研磨→调色 借助 研磨 调色→借助 沉淀剂的作用沉淀造粒→分级 过滤 沉淀剂的作用沉淀造粒 分级→过滤 干 分级 过滤→干 产品。 燥→产品。 产品
特殊高档粉末涂料
4)水分散法
半湿法
全湿法
半湿法
按常用粉末涂料制造法生产的粉末涂 料中,加入水、分散剂、 料中,加入水、分散剂、防腐剂和增稠剂 等助剂,然后一起研磨至一定细度,调节 等助剂,然后一起研磨至一定细度, 粘度和固体分含量至符合产品技术指标要 求。
粉末涂料基础知识

预防方法
1. 被涂工件表面不干净。 1. 改善工件底材质量,加强
涂膜
2. 供 粉 不 均 , 喷 枪 雾 化 不 好。
前处理。 2. 调整空气压力,检查导流
表面 3. 粉 末 太 细 或 粉 末 受 潮 结 器,调至最佳点。
有 团,使喷枪积粉。
3. 控制粉末粒度分布,妥善
颗粒 4. 涂 装 现 场 不 干 净 或 喷 室 保管粉末,严防受潮。
严重 偏低。
4. 控制粉末厚度在 60-80μm。
桔皮 4. 涂 膜 太 薄 或 太 5. 定期清理挂具。
厚。
6. 施工前严格清理喷粉系统及
5. 工件接地不良。 场地,避免不同类型或不同
6. 不同粉末混杂。 厂家的粉末混用。
现象
产生原因
预防方法
1.底材前处理质量差。 1. 选 择 合 适 的 前 处 理 工
3.空 气 中 混 有 油 、 水 。 4.供 粉 器 流 化 不 稳 定 , 供
粉器粉末过少。
1. 清 理 粉 管 的 杂 物 或 结 块,保持粉管畅通。
2. 选 择 合 适 的 空 压 机 。 3. 定 时 排 除 空 压 机 中 的
油、水。 4. 保 持 流 化 床 气 压 稳 定 ,
并定时添加新粉。
净化。
3. 受 灰 尘 或 其 它 杂 质 污 染 。 3. 彻 底 清 理 环 境 、更 换 合 格 粉来。
现象
产生原因
预防方法
1. 工件表面粗糙。 1. 提高工件光洁度。
2. 粉末粒子粗或受 2. 选择粒度分布均匀的高质量
潮。
粉末及严防粉末受潮。
涂膜 3. 固化温度偏高或 3. 调整适宜的固化条件。
2.烘 烤 时 间 过 长 或 温 度 艺。
- 1、下载文档前请自行甄别文档内容的完整性,平台不提供额外的编辑、内容补充、找答案等附加服务。
- 2、"仅部分预览"的文档,不可在线预览部分如存在完整性等问题,可反馈申请退款(可完整预览的文档不适用该条件!)。
- 3、如文档侵犯您的权益,请联系客服反馈,我们会尽快为您处理(人工客服工作时间:9:00-18:30)。
粉末涂料的生产工艺一、粉末涂料的生产工艺过程与质量控制粉末涂料生产过程更接近塑料加工工艺,而不同于一般涂料的制作工艺。
热固性粉末涂料的生产要经过以下四到五个工序,即配混料工序、混炼挤出工序、冷却破碎工序、磨粉筛分工序,有的产品还需要加上拼混或邦定工序。
1、配混料工序:该工序是粉末涂料生产的基础,是粉末涂料生产最重要的工序。
目前该工序大都使用两种混料设备1.1固定高速混料罐这种混料罐下部装有水平转动的并有一定斜面的桨叶,桨叶将物料水平搅动,并在离心力的作用下物料趋向罐体内壁。
同时,桨叶的斜面将物料向上推抛,物料再顺着罐体侧壁的斜面向内翻动。
与此同时,侧面的破碎刀片高速旋转,将树脂打碎。
该混料罐混料强度大、效率高、设备结构和维修比较简单,其价格低,是目前最常用的混料设备。
此种混料罐可做成卧式结构,通过皮带轮传动和变速,这样可做成较大容量的混料罐。
这类设备的一个主要缺点是有混料和出料死角。
1.2翻转式高速配料翻转式高速混料机是目前比较新型的设备,有了翻转的动作,增大混料投料量效果很好,一次投料量和生产效率大大提高。
混料机罐体可进行多次的翻转操作。
混料机罐体罐机可分离,可一机多罐,以提高工作效率。
这种设备几乎没有混料和出料死角。
此外,一些低速混合器,如:滚筒式混合器、卧式混合器、锥式以及现在还在应用的翻转混合器(双锥、V型等)这里就不一一介绍了。
混料均匀(包括调整补料后的均匀)是该工序的关键,其工艺关键点:—物料的计量:称量的偏差量不会影响产品质量。
—物料的粒径:块状物料粒径的控制,小则影响挤出的压缩比;大则不均匀。
—投料量是否合适——投料的料容比,物料的堆积密度是罐体容积的30~80%。
—混料时间和搅拌次数——跑色的问题。
—补料的方法该工序对设备的要求是不能有混料和下料死角。
该工序的质量标准:物料均匀;同品种产品一致。
一旦混合不均匀,靠后面的混炼挤出工序是解决不了问题的!粉末涂料的颜色和涂膜性能的调整就在此工序完成。
2、混炼挤出工序2、1单螺杆挤出机:目前粉末涂料混炼挤出一般使用两种设备来完成,即单螺杆挤出机或双螺杆挤出机。
单螺杆挤出机的螺杆结构见下图单螺杆挤出机的结构为螺筒的内壁与螺杆的外缘以及螺筒内的三排阻尼销钉和螺杆上的凹槽,在螺杆转动时形成对物料的剪切和混炼,进口设备的螺杆还同时具有明显的往复运动(冲程在5cm以上),增强了物料的混炼效果。
单螺杆挤出机的螺杆扭矩相对较小,螺杆可以做得较长,使挤出物料在螺筒内的存留时间较长,单螺杆挤出机螺杆的转动和往复运动可使物料形成较多的湍流,可以增加树脂对颜填料浸润时间和增大物料的剪切流动方式,使物料的混炼更加充分。
单螺杆的螺筒内部结构间隙相对较大,挤出物料的胶化粒子较少。
单螺杆的混炼长度、间隙及往复地幅度决定其混炼效果。
进口单螺杆挤出机价格昂贵,国产单螺杆设备在许多方面达不到进口设备的条件,国内使用这类设备的粉末涂料生产厂家和数量不多。
单螺杆挤出机清机换色较困难。
以下表格列出BUSS公司不同的单螺杆挤出机的性能另外,掺有细粉的物料不适合在单螺杆挤出机生产。
2、2双螺杆挤出机:双螺杆挤出机的传动结构比较复杂,两只螺杆的转动方向相同,剪切程度加大。
双螺杆挤出机的螺杆结构见图双螺杆的螺杆结构1送料段(即螺旋进料器)2塑化段3混炼捏合段4加强混炼段对于单螺杆挤出机来说,双螺杆挤出机具有更好的分散效果,可加工加有细粉的物料,对填料填充较大的物料有较好的加工性能,自清洗性能好,螺杆更换、清理、换色容易。
缺点是温度稳定性较低,易产生胶化颗粒。
由于双螺杆间隙小,物料在螺筒中有更强的剪切分散。
双螺杆挤出机的螺杆可随意调节塑化段和捏合混炼段的比列,可对物料的分散效果进行调整,因而对粉末涂料产品的加工范围更宽,从高光平面粉到砂纹粉等等。
2、3该工序对物料温度的要求:粉末涂料的树脂部分在一定温度塑化后对颜料和填料以及其他材料形成一定程度的分散,下图就是挤出机各个区域的温度分布图。
一旦物料超出这个区域就容易发生分散差、堵料、预胶化等问题。
2、4该工序物料在螺筒内留存时间:挤出机的挤出量越接近其最大生产量时,物料在螺筒内留存的时间越短,反之则反。
或者说在保证一定喂料的情况下,螺杆转速越高,物料在螺筒内留存的时间越短,反之亦反。
物料在螺筒内滞留时间长则利于树脂对颜填料的浸润分散;螺杆的转速高则剪切分散效果好。
一些浸润分散性差而更需通过加强剪切分散而达到一定分散效果的的产品,如:羟烷基酰胺/聚酯体系和PT910/聚酯体系,则最好使用长径比较大、螺杆转速较高的双螺杆挤出机来生产。
3、压片破碎工序:该工序就是把塑化的物料进行冷却和粗破碎,以利于后面细磨粉工序的进行。
该工序的关键就是把物料快速冷却到最低温度,是磨粉工序保证磨粉质量的基础。
4、磨粉筛分工序:下图是磨粉工序设备系统图这套设备即完成了磨粉、也完成了筛分过程。
磨粉、筛分工序在生产过程有四个可调整的参数——进料速度、分级器(副磨)转速、引风量和主磨转速。
首先是主磨转速(或粉碎脊柱的线速度),物料是通过在一定速度下形成的撞击而破碎的,脊柱的线速度越高,产生的冲击能量越大,磨粉细度越高。
物料在磨膛内的撞击分为与脊柱和衬瓦的撞击以及物料之间的撞击,与脊柱和衬瓦的撞击更利于物料的破碎,物料之间的撞击粉碎效率较低,进料速度大会增加物料间撞击的机率,使磨粉效率降低,磨粉效果变差。
此外,还有两个控制值——磨粉温度、粒径分布数值。
磨粉、筛分工序是通过冲击粉碎,以气流为动力,粒度分布和磨粉温度为工作标准进行进料量和副磨转速调整配合的过程。
这一过程的核心就是力——冲击力、粉末颗粒旋转产生的离心力与气流形成的吸力。
粉末颗粒的离心力和颗粒的动能有关,颗粒的运动速度越大其动能越大,通过调整分级器转速大小来控制进入成品粉管道粉末颗粒的细或粗,具体的数值可依据粒度分析仪所测的结果来确定。
气流风量的调控则涉及到磨机内部环境的温度、粒径分布和成品率。
对于磨机来说,风量大利于降温;对于旋风分离器来说,风量大则产生的回流风也越大,对细微粉的抽吸率越大,粒径分布较窄,产量较大,但消耗也大;风量小旋风风速低,超细粉的损耗就要小些,产量较低。
调整风量的同时,一定要照顾到磨机的温度。
以上两个参数确定下来后,就可以根据磨机的工作温度来调整进料量了,如果磨机温度高,就应该减少进料量。
由于配方或产品品种的不同,会造成片料的硬度不同,在相同参数条件下,物料被粉碎的粒度不一样。
总之,磨粉过程应该依据粒径分布测试的结果,对磨粉系统的主磨转速、副磨转速、进料转速、引风量(最好通过调整引风电机的转速调整引风量)对磨粉粒径进行调整,生产出适合客户使用的粉末涂料。
5、拼混或邦定工序:有些产品磨粉后还需进一步加工。
5、1低速拼混设备一般为翻转式混合设备,如:V型混料机或双锥混合机5、2高速拼混机和邦定我们使用的高速配料罐也可作为高速拼混机使用。
高速混合机混料强度高,物料的分散性要比低速混合设备强很多,因而在拼混颜料或助剂时,颜料或助剂的聚集团被进一步分散,使产品的拼混效果更好。
如:金属颜料在相同加量的情况下,使用高速混合的产品涂膜表面的金属感更强。
需要注意的是,高低速拼混会造成表面纹理、颜色等不同。
邦定混合:通过一定的加热手段,使粉末涂料粒子与其它材料(金属颜料、珠光颜料等或粉末涂料粒子之间)形成一定熔结的混合工艺。
邦定混合分为低速邦定混合和高速邦定混合。
低速绑定混合使用的是锥形混合器,如下图,目前国内还没有使用经验。
目前国内大部分厂家使用的是高速邦定工艺,高速邦定采用的是高速搅拌摩擦加热的原理,主要邦定的产品是金属粉、珠光粉等。
国产高速邦定设备的温控性能较差,加上原料指标的波动,因此绑定产品的稳定性(主要是上粉率和涂膜外观)还不是很好。
由于邦定过程中部分粉末粒子有一定程度的熔结,因而用于邦定的底粉粒径应细一些;如果不能测定邦定底粉的玻璃转化温度,需进行一些实验来确定邦定温度和邦定时间。
邦定结束前加入白炭黑或氧化铝-C并迅速放料冷却。
邦定的金属粉末涂料解决了电晕枪的极针容易积粉而形成吐粉的缺陷。
完全邦定的金属粉末涂料不会因涂装设备不同而造成涂膜外观不一致。
6、粉末涂料的质量控制粉末涂料的质量水平是由粉末涂料的各种性能指标体现的,它体现在两个方面,即粉末涂料的使用性能和涂膜的装饰、防护性能。
6、1粉末涂料的使用性能6、1、1粉末涂料的储存稳定能粉末涂料在一定温度下,经一定时间储存,不发生粉末结块、不发生涂膜外观和性能的变化。
正常情况下40℃以下,存放一年之内不应发生任何问题。
6、1、2粉末涂料的粒径分布粉末涂料是由无数个不同粒径的粉末粒子组成的,所谓的粒径分布是指某一粒子群中,不同粒径的粒子所占比例。
D50:一个样品的累计粒度分布百分数达到50%时所对应的粒径。
它的物理意义是粒径大于它的颗粒占50%,小于它的颗粒也占50%,D50也叫中位粒径或中值粒径。
D50常用来表示粉体的平均粒度。
粉末涂料的粒径越小,越利于涂层的流平。
但它的粒径小到一定程度时会发生聚集结团现象,使喷涂受到影响,粉末太细,带电性降低,涂装施工效率会下降。
粒径太大,涂膜流平不好,容易产生厚涂现象,影响粉末涂料的单位涂装面积。
粉末涂料的粒径分布情况与粉末涂料生产的磨粉设备有较大关系,粒径分布越窄,磨粉生产的损耗越大。
6、1、3粉末涂料的粉末流动性粉末涂料在供粉桶中的流化性能何在管道中的输送性能,可通过测定粉末涂料流动性指标——粉末流速R值表示。
往试验容器中装入(250±10)g的粉末涂料样品。
通过多孔的底部导入洁净的空气,调整压缩空气流速为(200±10)L/h。
为防止流化过程中出现的流沟和气泡,用直尺搅拌粉末直至粉末流化床的高度在搅拌过程中保持恒定。
测定流化床的高度h,测量精度为2mm,关掉空气让粉料静置下来(可能需要1~2min)。
测定静止粉料的高度h0,测量精度为2mm。
在空气流速相同的情况下再次流化粉料,搅拌以促进流化,等到流化粉料床高度恒定后,打开开口,同时按下计时器,在(30±1)s内收集从开口处流出的粉料。
关闭开口,称量收集到的粉料(m),精确称量至0.1g。
粉料流速6、1、4粉末涂料的密度粉末涂料中颜填料多则密度大,影响粉末涂料涂装的上粉率和喷涂面积。
粉末涂料的密度分实际密度和堆积密度,实际密度用比重瓶法测定。
6、1、5粉末涂料的沉积率粉末涂料的沉积效率是指沉积在目标上的粉末重量与所喷用粉末的重量比,以百分数表示。
粉末涂料的沉积效率不等于上粉率,是能表示上粉率高低的一个指标。
这种测定方法适用于静电枪喷涂和摩擦枪喷涂用粉末涂料,可用于比较相同喷枪不同粉末涂料或相同粉末涂料不同喷枪的性能对比。
粉末的粒径分布、密度、带电性、粉末流动性、涂装设备条件、涂装环境等都会对粉末涂料的沉积率或上粉率有影响。