催化裂化原理
催化裂化原理
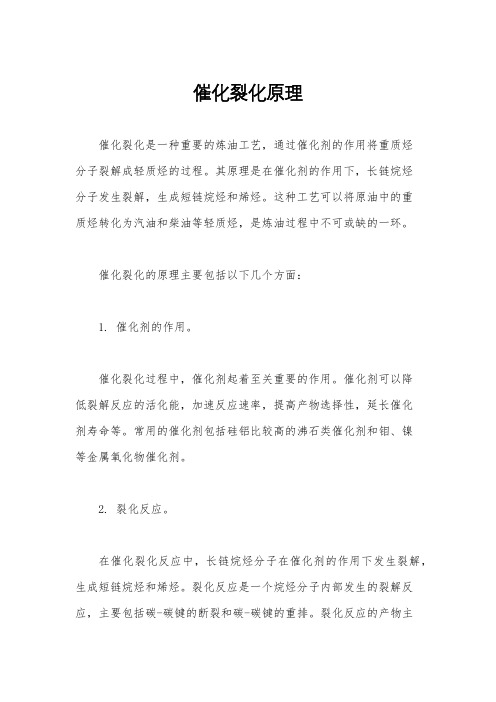
催化裂化原理催化裂化是一种重要的炼油工艺,通过催化剂的作用将重质烃分子裂解成轻质烃的过程。
其原理是在催化剂的作用下,长链烷烃分子发生裂解,生成短链烷烃和烯烃。
这种工艺可以将原油中的重质烃转化为汽油和柴油等轻质烃,是炼油过程中不可或缺的一环。
催化裂化的原理主要包括以下几个方面:1. 催化剂的作用。
催化裂化过程中,催化剂起着至关重要的作用。
催化剂可以降低裂解反应的活化能,加速反应速率,提高产物选择性,延长催化剂寿命等。
常用的催化剂包括硅铝比较高的沸石类催化剂和钼、镍等金属氧化物催化剂。
2. 裂化反应。
在催化裂化反应中,长链烷烃分子在催化剂的作用下发生裂解,生成短链烷烃和烯烃。
裂化反应是一个烷烃分子内部发生的裂解反应,主要包括碳-碳键的断裂和碳-碳键的重排。
裂化反应的产物主要是烷烃、烯烃和芳烃。
3. 反应条件。
催化裂化的反应条件包括温度、压力、催化剂种类和用量等。
通常情况下,催化裂化反应需要在较高的温度下进行,以提高反应速率和产物选择性。
此外,适当的压力和催化剂的选择也对裂化反应的效果有重要影响。
4. 产物分离。
催化裂化反应产生的混合气体需要进行分离和纯化,以得到所需的轻质烃产品。
通常采用的分离技术包括精馏、萃取、吸附等,以获得高纯度的汽油和柴油产品。
5. 催化剂再生。
在催化裂化过程中,催化剂会因受到焦炭和烃类物质的污染而失活,需要进行再生。
催化剂再生是通过热氧化或化学氧化等方法将焦炭烧除,恢复催化剂的活性和选择性,延长催化剂的使用寿命。
总的来说,催化裂化是一种重要的炼油工艺,通过催化剂的作用将重质烃分子裂解成轻质烃,可以提高原油的利用率,生产出更多的汽油和柴油产品。
催化裂化的原理涉及催化剂的作用、裂化反应、反应条件、产物分离和催化剂再生等多个方面,需要综合考虑和控制,以实现高效、稳定的生产过程。
催化裂化工艺与工程

催化裂化工艺与工程引言催化裂化工艺与工程是石油炼制领域中的重要技术,其通过催化剂的作用,将重油分子裂解为较轻的产品。
催化裂化工艺在石油化工行业中具有广泛应用,可以生产出汽油、液化气和轻质石脑油等产品,对石油资源的高效利用具有重要意义。
催化裂化反应原理1.催化裂化反应介质:常见的催化剂是硅铝酸盐,其具有高的表面积和一定的酸性。
催化剂通过提供活性中心,促进了重油分子的裂解反应。
2.催化裂化反应机理:重油中的长链烷烃在催化剂的作用下发生裂解,产生较短的烷烃和芳烃。
裂解过程中产生了大量的烯烃和芳烃,这些物质是石油下游加工的重要原料。
催化裂化工艺流程1.原料预处理:重油首先需要进行预处理,包括去除硫、氮等杂质,以减小对催化剂的毒化作用。
2.催化裂化反应:重油在裂化装置中与催化剂接触,发生裂解反应。
在裂化过程中,需要严格控制反应温度、压力和催化剂的用量,以提高产品的收率和质量。
3.分离工序:裂化反应产生的产物包括汽油、液化气、轻质石脑油等组分,这些组分需要经过分离工序进行提取。
主要包括精馏、吸附和深度处理等步骤。
4.催化剂再生:经过一段时间的使用,催化剂表面会产生积炭和失活,需要进行再生。
催化剂再生的过程包括热氧化和酸洗等步骤,以恢复催化剂的活性。
5.产品处理:裂化产物需要进一步进行加工和改性,以获得符合市场需求的成品。
催化裂化工程设计1.反应器设计:反应器是催化裂化装置的核心部分,设计合理的反应器可以提高反应效率和产物质量。
反应器设计考虑因素包括反应器类型、反应器尺寸、反应器温度和压力等。
2.催化剂选择:催化剂的选择是催化裂化工程设计中的重要一环。
催化剂的性能直接影响反应的效果和产物的质量。
选择合适的催化剂需要考虑其活性、稳定性和成本等因素。
3.热力学和动力学模型:对催化裂化反应进行热力学和动力学模拟,可以预测反应过程中的表现和优化操作条件。
4.安全性考虑:催化裂化工程设计需要考虑装置的安全性。
石油化工装置涉及高温、高压和易燃易爆物质,需要进行安全分析和设计,以确保操作的安全性和稳定性。
催化裂化原理
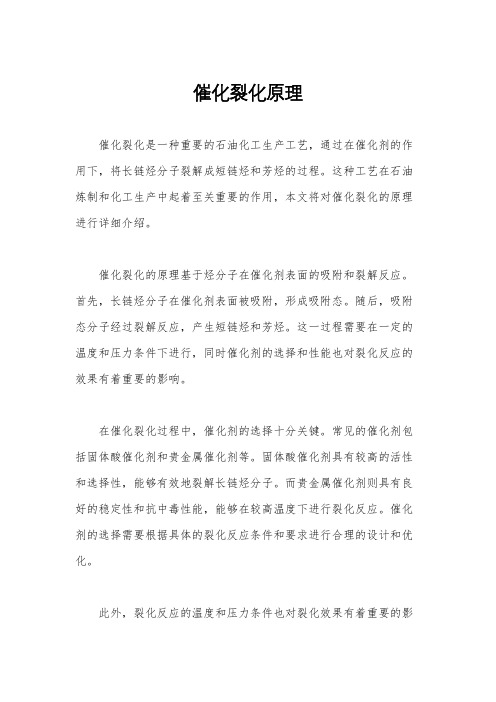
催化裂化原理催化裂化是一种重要的石油化工生产工艺,通过在催化剂的作用下,将长链烃分子裂解成短链烃和芳烃的过程。
这种工艺在石油炼制和化工生产中起着至关重要的作用,本文将对催化裂化的原理进行详细介绍。
催化裂化的原理基于烃分子在催化剂表面的吸附和裂解反应。
首先,长链烃分子在催化剂表面被吸附,形成吸附态。
随后,吸附态分子经过裂解反应,产生短链烃和芳烃。
这一过程需要在一定的温度和压力条件下进行,同时催化剂的选择和性能也对裂化反应的效果有着重要的影响。
在催化裂化过程中,催化剂的选择十分关键。
常见的催化剂包括固体酸催化剂和贵金属催化剂等。
固体酸催化剂具有较高的活性和选择性,能够有效地裂解长链烃分子。
而贵金属催化剂则具有良好的稳定性和抗中毒性能,能够在较高温度下进行裂化反应。
催化剂的选择需要根据具体的裂化反应条件和要求进行合理的设计和优化。
此外,裂化反应的温度和压力条件也对裂化效果有着重要的影响。
一般来说,较高的温度和适当的压力有利于裂化反应的进行。
在一定的温度范围内,裂化反应速率随温度的升高而增加,但过高的温度会导致产物的选择性下降。
因此,裂化反应的温度需要在活性和选择性之间进行平衡。
另外,裂化反应的产物选择性也是一个重要的问题。
在裂化反应中,短链烃和芳烃的选择性对于产品的质量和产率有着重要的影响。
通过调整催化剂的性质和反应条件,可以实现对产物选择性的调控,从而获得理想的产品。
总的来说,催化裂化是一种重要的石油化工生产工艺,通过催化剂的作用,将长链烃分子裂解成短链烃和芳烃。
催化裂化的原理涉及到催化剂的选择、反应条件的控制以及产物选择性的调控等方面。
通过对催化裂化原理的深入理解,可以为工程实践提供理论指导和技术支持,推动石油化工生产的发展和进步。
催化催化裂化技术

催化催化裂化技术催化裂化技术是一种重要的炼油工艺,可以将重质石油馏分转化为高附加值的轻质产品。
本文将从催化裂化技术的原理、应用和发展前景等方面进行探讨,以期为读者提供对该技术的全面了解。
一、催化裂化技术的原理催化裂化技术是通过催化剂的作用将重质石油馏分分解为较轻的产品。
其主要原理是在高温和高压的条件下,将原料油与催化剂接触,使其发生裂化反应。
这种反应可以将长链烃分子裂解成短链烃分子,从而提高汽油和燃料油的产率。
催化裂化反应主要分为两个阶段:热裂化和催化裂化。
在热裂化阶段,原料油在高温下分解成烃气和液体烃。
然后,在催化剂的作用下,烃气和液体烃进一步反应,生成较轻的产品,如汽油、液化气和柴油等。
二、催化裂化技术的应用催化裂化技术在炼油行业中具有广泛的应用。
首先,它可以提高汽油的产率。
由于汽车的普及,对汽油的需求量不断增加。
催化裂化技术可以将重质石油馏分转化为轻质的汽油,从而满足市场需求。
催化裂化技术可以生产出高质量的柴油。
在催化裂化过程中,石油馏分中的硫、氮和金属等杂质可以得到有效去除,从而提高柴油的质量。
这对于减少柴油排放的污染物具有重要意义。
催化裂化技术还可以生产出液化气、石脑油和石化原料等产品。
这些产品在化工、冶金和化肥等行业中具有广泛的应用。
三、催化裂化技术的发展前景随着能源需求的增加和石油资源的日益枯竭,催化裂化技术在未来的发展前景十分广阔。
一方面,随着汽车工业的高速发展,对汽油的需求将持续增加,催化裂化技术将成为满足市场需求的重要手段。
另一方面,随着环境保护意识的提高,对燃料油质量的要求也越来越高。
催化裂化技术可以提高燃料油的质量,减少对环境的污染,因此在未来的发展中具有重要的作用。
随着科技的不断进步,催化剂的研发和改进也将推动催化裂化技术的发展。
新型的催化剂可以提高反应的选择性和活性,从而提高产品的产率和质量。
催化裂化技术作为一种重要的炼油工艺,在提高石油产品产率和质量方面具有重要的作用。
催化裂化的工艺特点及基本原理

催化裂化的工艺特点及基本原理催化裂化是一种重要的石油加工工艺,其开发和应用对于提高石油产业发展水平具有重要的意义。
催化裂化工艺的特点和基本原理如下:一、工艺特点:1.高选择性:催化裂化工艺可以将石油馏分中的大分子烃化合物按照其碳数分解为较低碳数的烃化合物,其中可选择的烃化合物主要是汽油和液化气。
因此,催化裂化可以提高汽油和液化气产率,达到更好的操作经济效益。
2.产物分布广:催化裂化反应不仅可以生成汽油和液化气,还可以生成较低碳数的烃化合物,如乙烯、丙烯等。
因此,催化裂化反应可以提供多种不同碳数的烃化合物,满足不同需求。
3.增塔体积积极:催化裂化工艺采用固定床反应器,反应器内填充了催化剂颗粒,因此反应器体积较大。
大体积的反应器可以增加催化裂化反应的容量,提高石油裂解速率,并且还可以增加反应过程的稳定性和可控性。
4.废气利用:催化裂化反应产生的废气中含有非常丰富的烃化合物和能量,可以通过适当的处理和回收利用,从而得到更好的经济效益,并减少对环境的污染。
二、基本原理:催化裂化反应是通过催化剂的作用来进行的,其基本原理如下:1.裂解反应:石油中的长链烃化合物在催化剂的作用下发生热裂解反应,将大分子烷烃分解成较小分子的烃化合物。
这种反应是一个链状反应过程,会生成一系列的短链烃化合物和碳氢烃中间体。
2.重排反应:短链烃化合物和碳氢烃中间体在催化剂的作用下发生重排反应,重新组合成不同碳数的烃化合物。
3.芳构化反应:在催化裂化过程中,由于催化剂特殊的性质,烃化合物还会发生芳构化反应,生成芳烃类化合物,如苯、甲苯等。
4.积碳反应:由于裂化过程产生的碳元素会在催化剂表面析出,形成碳黑,导致催化剂失活。
因此,催化裂化还需要定期对催化剂进行再生,以保持其活性。
综上所述,催化裂化工艺具有高选择性、广泛的产物分布、增塔体积积极和废气利用等特点。
其基本原理包括裂解反应、重排反应、芳构化反应和积碳反应。
催化裂化工艺的开发和应用有助于提高石油产业的经济效益和环境可持续性。
fcc催化裂化

fcc催化裂化FCC催化裂化技术(Fluid Catalytic Cracking,以下简称FCC)是一种重要的石油炼制工艺,用于将重质石油馏分转化为高附加值的轻质烃类产品。
本文将从FCC技术的原理、工艺流程、催化剂以及应用领域等方面进行介绍。
一、FCC技术的原理FCC技术是利用催化剂在高温条件下对重质石油馏分进行裂化反应,将较长的烷烃链分子裂解为较短的烷烃链分子。
这种裂化反应是在流化床反应器中进行的,床层内的催化剂与石油馏分混合后形成流化床,在催化剂的作用下进行裂化反应。
裂化反应生成的烃类产品经过分离和处理后,可以得到汽油、液化气等高附加值的产品。
二、FCC技术的工艺流程FCC技术的工艺流程主要包括进料预处理、裂化反应、分离和处理等环节。
进料预处理主要是对原料进行加热、脱盐、脱水等操作,以提高裂化反应的效果。
裂化反应是FCC技术的核心环节,通过将预处理过的原料与催化剂混合后送入流化床反应器,经过高温和催化剂的作用,使原料分子发生裂化反应。
分离和处理环节主要是通过一系列的分离设备,如分馏塔、冷凝器等,将裂化反应产生的混合物进行分离和纯化,得到目标产品。
三、FCC技术的催化剂催化剂是FCC技术中起着至关重要作用的物质。
常用的FCC催化剂主要是硅铝酸盐基催化剂,其具有良好的活性和稳定性。
催化剂的选择对于裂化反应的效果具有重要影响,不同的催化剂可以调控反应的产物分布和性质。
此外,催化剂的再生和补充也是FCC技术中必要的工艺环节,通过对催化剂进行再生和补充,可以保持反应的稳定性和持续性。
四、FCC技术的应用领域FCC技术广泛应用于石油炼制工业中,特别是在汽油生产领域有着重要地位。
通过FCC技术可以将重质的石脑油、渣油等转化为高辛烷值的汽油,满足不同地区和需求的汽油标准。
此外,FCC技术还可以生产液化气、煤油、柴油等产品,具有较高的经济效益和社会效益。
总结起来,FCC催化裂化技术是一种重要的石油炼制工艺,通过催化剂在高温条件下对重质石油馏分进行裂化反应,将其转化为高附加值的轻质烃类产品。
简述催化裂化工艺原理
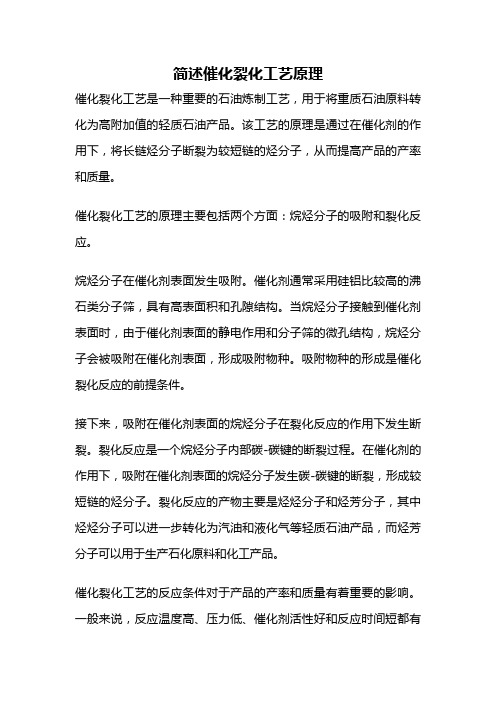
简述催化裂化工艺原理催化裂化工艺是一种重要的石油炼制工艺,用于将重质石油原料转化为高附加值的轻质石油产品。
该工艺的原理是通过在催化剂的作用下,将长链烃分子断裂为较短链的烃分子,从而提高产品的产率和质量。
催化裂化工艺的原理主要包括两个方面:烷烃分子的吸附和裂化反应。
烷烃分子在催化剂表面发生吸附。
催化剂通常采用硅铝比较高的沸石类分子筛,具有高表面积和孔隙结构。
当烷烃分子接触到催化剂表面时,由于催化剂表面的静电作用和分子筛的微孔结构,烷烃分子会被吸附在催化剂表面,形成吸附物种。
吸附物种的形成是催化裂化反应的前提条件。
接下来,吸附在催化剂表面的烷烃分子在裂化反应的作用下发生断裂。
裂化反应是一个烷烃分子内部碳-碳键的断裂过程。
在催化剂的作用下,吸附在催化剂表面的烷烃分子发生碳-碳键的断裂,形成较短链的烃分子。
裂化反应的产物主要是烃烃分子和烃芳分子,其中烃烃分子可以进一步转化为汽油和液化气等轻质石油产品,而烃芳分子可以用于生产石化原料和化工产品。
催化裂化工艺的反应条件对于产品的产率和质量有着重要的影响。
一般来说,反应温度高、压力低、催化剂活性好和反应时间短都有利于提高产品的产率。
此外,催化裂化工艺还需要添加适量的催化剂再生剂,以保证催化剂的活性和稳定性。
催化裂化工艺在石油炼制中具有广泛的应用。
通过该工艺可以将重质石油原料转化为高附加值的轻质石油产品,如汽油、柴油和液化气等。
同时,催化裂化工艺还可以提高石油产品的产率和质量,减少燃料的消耗和环境污染。
催化裂化工艺是一种重要的石油炼制工艺,通过在催化剂的作用下将重质石油原料转化为轻质石油产品。
该工艺的原理是在催化剂表面发生烷烃分子的吸附和裂化反应,从而提高产品的产率和质量。
催化裂化工艺在石油炼制中具有广泛的应用,为能源行业的发展做出了重要的贡献。
催化裂化原理
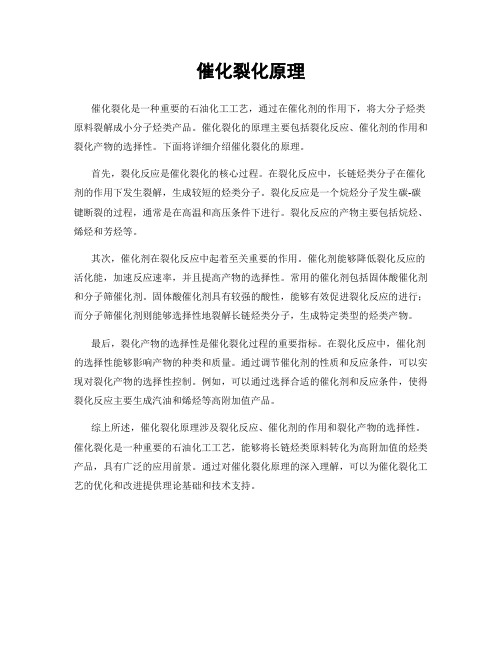
催化裂化原理
催化裂化是一种重要的石油化工工艺,通过在催化剂的作用下,将大分子烃类原料裂解成小分子烃类产品。
催化裂化的原理主要包括裂化反应、催化剂的作用和裂化产物的选择性。
下面将详细介绍催化裂化的原理。
首先,裂化反应是催化裂化的核心过程。
在裂化反应中,长链烃类分子在催化剂的作用下发生裂解,生成较短的烃类分子。
裂化反应是一个烷烃分子发生碳-碳键断裂的过程,通常是在高温和高压条件下进行。
裂化反应的产物主要包括烷烃、烯烃和芳烃等。
其次,催化剂在裂化反应中起着至关重要的作用。
催化剂能够降低裂化反应的活化能,加速反应速率,并且提高产物的选择性。
常用的催化剂包括固体酸催化剂和分子筛催化剂。
固体酸催化剂具有较强的酸性,能够有效促进裂化反应的进行;而分子筛催化剂则能够选择性地裂解长链烃类分子,生成特定类型的烃类产物。
最后,裂化产物的选择性是催化裂化过程的重要指标。
在裂化反应中,催化剂的选择性能够影响产物的种类和质量。
通过调节催化剂的性质和反应条件,可以实现对裂化产物的选择性控制。
例如,可以通过选择合适的催化剂和反应条件,使得裂化反应主要生成汽油和烯烃等高附加值产品。
综上所述,催化裂化原理涉及裂化反应、催化剂的作用和裂化产物的选择性。
催化裂化是一种重要的石油化工工艺,能够将长链烃类原料转化为高附加值的烃类产品,具有广泛的应用前景。
通过对催化裂化原理的深入理解,可以为催化裂化工艺的优化和改进提供理论基础和技术支持。
简述催化裂化工艺原理
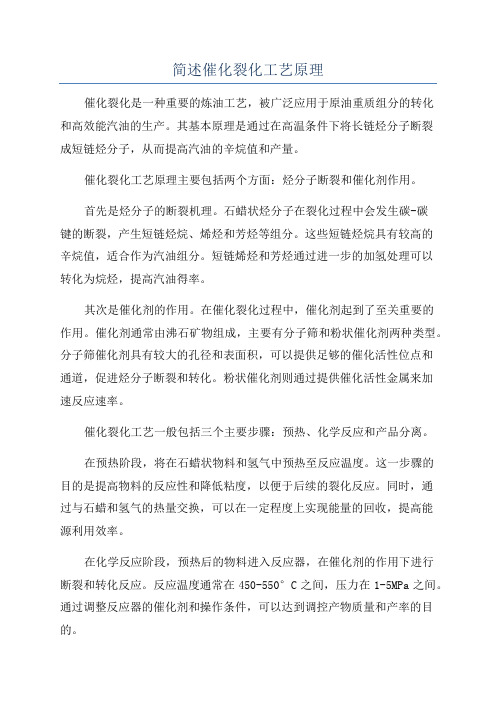
简述催化裂化工艺原理催化裂化是一种重要的炼油工艺,被广泛应用于原油重质组分的转化和高效能汽油的生产。
其基本原理是通过在高温条件下将长链烃分子断裂成短链烃分子,从而提高汽油的辛烷值和产量。
催化裂化工艺原理主要包括两个方面:烃分子断裂和催化剂作用。
首先是烃分子的断裂机理。
石蜡状烃分子在裂化过程中会发生碳-碳键的断裂,产生短链烃烷、烯烃和芳烃等组分。
这些短链烃烷具有较高的辛烷值,适合作为汽油组分。
短链烯烃和芳烃通过进一步的加氢处理可以转化为烷烃,提高汽油得率。
其次是催化剂的作用。
在催化裂化过程中,催化剂起到了至关重要的作用。
催化剂通常由沸石矿物组成,主要有分子筛和粉状催化剂两种类型。
分子筛催化剂具有较大的孔径和表面积,可以提供足够的催化活性位点和通道,促进烃分子断裂和转化。
粉状催化剂则通过提供催化活性金属来加速反应速率。
催化裂化工艺一般包括三个主要步骤:预热、化学反应和产品分离。
在预热阶段,将在石蜡状物料和氢气中预热至反应温度。
这一步骤的目的是提高物料的反应性和降低粘度,以便于后续的裂化反应。
同时,通过与石蜡和氢气的热量交换,可以在一定程度上实现能量的回收,提高能源利用效率。
在化学反应阶段,预热后的物料进入反应器,在催化剂的作用下进行断裂和转化反应。
反应温度通常在450-550°C之间,压力在1-5MPa之间。
通过调整反应器的催化剂和操作条件,可以达到调控产物质量和产率的目的。
最后,在产品分离阶段,通过一系列的分离操作,将裂化产物中的不同组分分离出来。
主要的分离方式包括蒸馏、吸附和萃取等。
其中,蒸馏是最主要的分离手段,可以将产物按烃碳数分为不同的馏分,进一步提纯和精制。
催化裂化工艺具有许多优点。
首先,可以将重质石油产品转化为高辛烷值的汽油,提高产品附加值和经济效益。
其次,可以通过调整催化剂和操作条件,实现灵活生产不同品质和组分的汽油。
再者,催化裂化可以与其他炼油工艺相结合,如加氢裂化、重整和烷基化等,进行综合重整和分子设计,进一步提高汽油产率和质量。
催化裂化原理

催化裂化原理
催化裂化原理是一种常用的石油精炼过程,通过在催化剂的作用下,将较重的石油馏分转化为较轻的馏分。
在催化裂化过程中,石油馏分与催化剂在高温和高压下反应,产生裂化产物。
催化裂化过程的原理基于分子的断裂和重组。
石油馏分中的长链烷烃在催化剂的作用下,经过断开碳碳链和生成烯烃中间体的反应步骤,最终裂解成较短链的烷烃、烯烃以及芳香烃。
催化剂起到了降低反应活化能和调控反应选择性的作用,使得较重的石油馏分得以转化为较轻的馏分。
催化裂化过程的催化剂通常为固体酸,如硅铝酸和氯化铈等。
催化剂的活性主要取决于其酸性和表面活性。
在反应过程中,石油馏分和催化剂通过物理吸附和化学反应作用在一起,催化剂表面的酸性位点可以吸附石油馏分分子,并通过质子传递的方式促进裂解反应的进行。
同时,催化剂表面的活性位点还可以吸附裂解产物分子,并进行一系列的重组反应,使得短链烷烃和烯烃生成较长链的烷烃和芳香烃。
催化裂化过程的优点在于可以将重组分子结构进行优化,得到较高价值的产品。
例如,通过控制反应条件和催化剂配方,可以得到高辛烷值的汽油和较少硫和芳香烃含量的柴油。
此外,催化裂化还能产生丙烯、轻质石蜡和石油醚等重要化工原料。
总结来说,催化裂化原理是通过催化剂的作用,将重的石油馏分转化为轻的馏分。
这个过程涉及到分子的断裂和重组,同时
需要合适的催化剂和反应条件。
催化裂化是一种重要的石油精炼技术,有助于提高石油产品的品质和降低环境影响。
催化裂化装置基本原理
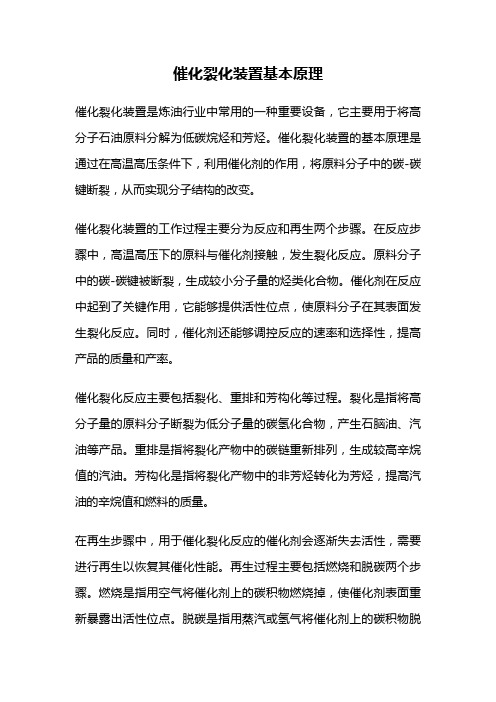
催化裂化装置基本原理催化裂化装置是炼油行业中常用的一种重要设备,它主要用于将高分子石油原料分解为低碳烷烃和芳烃。
催化裂化装置的基本原理是通过在高温高压条件下,利用催化剂的作用,将原料分子中的碳-碳键断裂,从而实现分子结构的改变。
催化裂化装置的工作过程主要分为反应和再生两个步骤。
在反应步骤中,高温高压下的原料与催化剂接触,发生裂化反应。
原料分子中的碳-碳键被断裂,生成较小分子量的烃类化合物。
催化剂在反应中起到了关键作用,它能够提供活性位点,使原料分子在其表面发生裂化反应。
同时,催化剂还能够调控反应的速率和选择性,提高产品的质量和产率。
催化裂化反应主要包括裂化、重排和芳构化等过程。
裂化是指将高分子量的原料分子断裂为低分子量的碳氢化合物,产生石脑油、汽油等产品。
重排是指将裂化产物中的碳链重新排列,生成较高辛烷值的汽油。
芳构化是指将裂化产物中的非芳烃转化为芳烃,提高汽油的辛烷值和燃料的质量。
在再生步骤中,用于催化裂化反应的催化剂会逐渐失去活性,需要进行再生以恢复其催化性能。
再生过程主要包括燃烧和脱碳两个步骤。
燃烧是指用空气将催化剂上的碳积物燃烧掉,使催化剂表面重新暴露出活性位点。
脱碳是指用蒸汽或氢气将催化剂上的碳积物脱除,以保证催化剂的活性和稳定性。
催化裂化装置的设计和操作需要考虑多个因素。
首先是选择合适的催化剂,催化剂的选择应根据原料的性质和产品的要求进行优化。
其次是控制反应的温度、压力和空速等工艺参数,以达到最佳的反应效果。
此外,催化裂化装置还需要考虑原料的预处理、氢气的补充和废热的回收利用等问题,以提高装置的效率和经济性。
催化裂化装置在炼油工业中具有重要的地位和广泛的应用。
通过裂化反应,可以将高分子的重质石油原料转化为轻质燃料和化工原料,满足市场对汽油、柴油和石脑油等产品的需求。
同时,催化裂化装置还可以提高石油产品的质量,减少环境污染物的排放,具有良好的经济和环境效益。
催化裂化装置是一种利用催化剂作用进行石油原料分解的重要设备。
催化裂化的工艺特点及基本原理
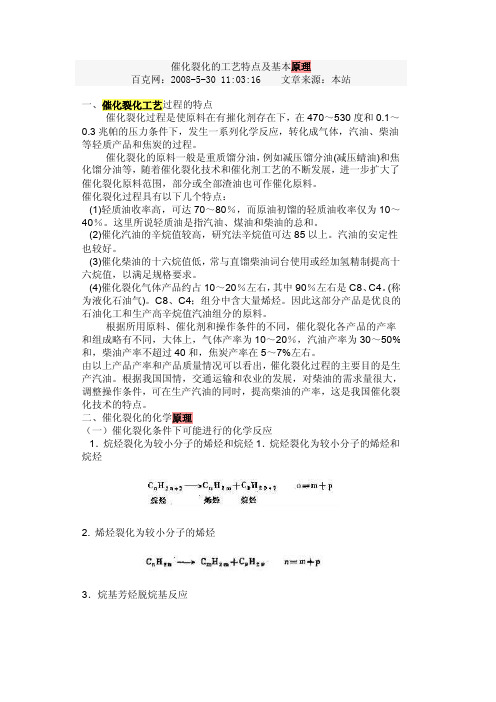
催化裂化的工艺特点及基本原理百克网:2008-5-30 11:03:16 文章来源:本站一、催化裂化工艺过程的特点催化裂化过程是使原料在有摧化剂存在下,在470~530度和0.1~0.3兆帕的压力条件下,发生一系列化学反应,转化成气体,汽油、柴油等轻质产品和焦炭的过程。
催化裂化的原料一般是重质馏分油,例如减压馏分油(减压蜻油)和焦化馏分油等,随着催化裂化技术和催化剂工艺的不断发展,进一步扩大了催化裂化原料范围,部分或全部渣油也可作催化原料。
催化裂化过程具有以下几个特点:(1)轻质油收率高,可达70~80%,而原油初馏的轻质油收率仅为10~40%。
这里所说轻质油是指汽油、煤油和柴油的总和。
(2)催化汽油的辛烷值较高,研究法辛烷值可达85以上。
汽油的安定性也较好。
(3)催化柴油的十六烷值低,常与直馏柴油词台使用或经加氢精制提高十六烷值,以满足规格要求。
(4)催化裂化气体产品约占10~20%左右,其中90%左右是C8、C4。
(称为液化石油气)。
C8、C4;组分中含大量烯烃。
因此这部分产品是优良的石油化工和生产高辛烷值汽油组分的原料。
根据所用原料、催化剂和操作条件的不同,催化裂化各产品的产率和组成略有不同,大体上,气体产率为10~20%,汽油产率为30~50%和,柴油产率不超过40和,焦炭产率在5~7%左右。
由以上产品产率和产品质量情况可以看出,催化裂化过程的主要目的是生产汽油。
根据我国国情,交通运输和农业的发展,对柴油的需求量很大,调整操作条件,可在生产汽油的同时,提高柴油的产率,这是我国催化裂化技术的特点。
二、催化裂化的化学原理(一)催化裂化条件下可能进行的化学反应1.烷烃裂化为较小分子的烯烃和烷烃1.烷烃裂化为较小分子的烯烃和烷烃2. 烯烃裂化为较小分子的烯烃3.烷基芳烃脱烷基反应4.烷基芳烃侧链断裂5.环烷烃裂化为烯烃假如环烷烃中仅有单环,则环不打开:6.氢转移反应如:环烷烃+烯烃→芳香烃+烷烃7.异构化反应:烷烃→异构烷烃烯烃→异构烯烃8.芳构化反应烯烃环化脱氢生成芳香烃,如:9.缩合反应单环芳烃可缩台成稠环芳烃,最后可缩合成焦炭,并放出氢气,使烯烃饱和。
催化裂化化学反应原理及催化剂的选用
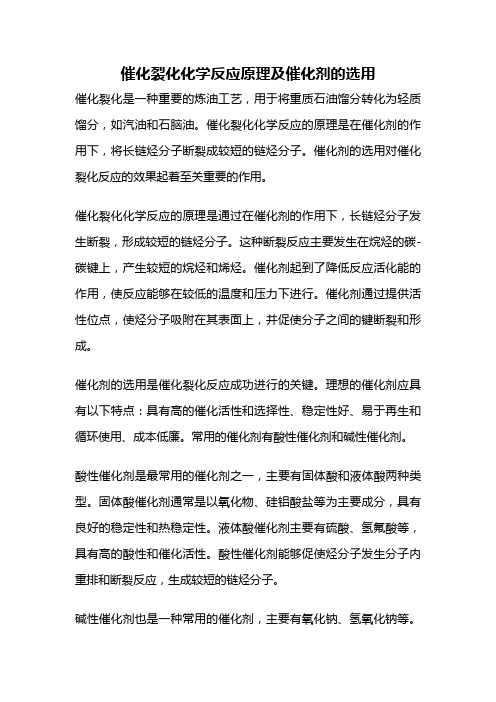
催化裂化化学反应原理及催化剂的选用催化裂化是一种重要的炼油工艺,用于将重质石油馏分转化为轻质馏分,如汽油和石脑油。
催化裂化化学反应的原理是在催化剂的作用下,将长链烃分子断裂成较短的链烃分子。
催化剂的选用对催化裂化反应的效果起着至关重要的作用。
催化裂化化学反应的原理是通过在催化剂的作用下,长链烃分子发生断裂,形成较短的链烃分子。
这种断裂反应主要发生在烷烃的碳-碳键上,产生较短的烷烃和烯烃。
催化剂起到了降低反应活化能的作用,使反应能够在较低的温度和压力下进行。
催化剂通过提供活性位点,使烃分子吸附在其表面上,并促使分子之间的键断裂和形成。
催化剂的选用是催化裂化反应成功进行的关键。
理想的催化剂应具有以下特点:具有高的催化活性和选择性、稳定性好、易于再生和循环使用、成本低廉。
常用的催化剂有酸性催化剂和碱性催化剂。
酸性催化剂是最常用的催化剂之一,主要有固体酸和液体酸两种类型。
固体酸催化剂通常是以氧化物、硅铝酸盐等为主要成分,具有良好的稳定性和热稳定性。
液体酸催化剂主要有硫酸、氢氟酸等,具有高的酸性和催化活性。
酸性催化剂能够促使烃分子发生分子内重排和断裂反应,生成较短的链烃分子。
碱性催化剂也是一种常用的催化剂,主要有氧化钠、氢氧化钠等。
碱性催化剂能够降低反应中的酸性催化剂的副反应,同时还可以促使分子间的碳-碳键断裂,生成较短的链烃分子。
碱性催化剂具有高的催化活性和选择性,但在反应条件下的稳定性较差,容易受到水和杂质等的影响。
除了酸性催化剂和碱性催化剂,还有其他类型的催化剂可供选择,如金属催化剂、复合催化剂等。
金属催化剂通常以贵金属为活性组分,具有高的催化活性和选择性,但成本较高。
复合催化剂由多种催化剂组成,能够充分发挥各种催化剂的优势,提高反应效果。
催化裂化化学反应是一种重要的炼油工艺,通过在催化剂的作用下将重质石油馏分转化为轻质馏分。
催化剂的选用是催化裂化反应成功进行的关键,酸性催化剂和碱性催化剂是常用的催化剂类型。
催化裂化工艺原理
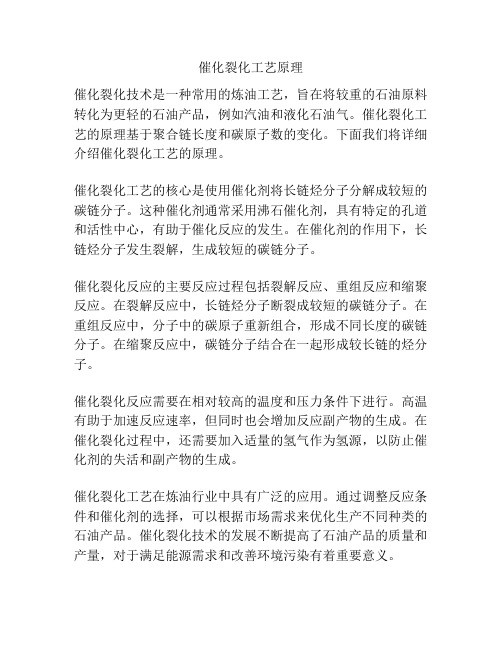
催化裂化工艺原理
催化裂化技术是一种常用的炼油工艺,旨在将较重的石油原料转化为更轻的石油产品,例如汽油和液化石油气。
催化裂化工艺的原理基于聚合链长度和碳原子数的变化。
下面我们将详细介绍催化裂化工艺的原理。
催化裂化工艺的核心是使用催化剂将长链烃分子分解成较短的碳链分子。
这种催化剂通常采用沸石催化剂,具有特定的孔道和活性中心,有助于催化反应的发生。
在催化剂的作用下,长链烃分子发生裂解,生成较短的碳链分子。
催化裂化反应的主要反应过程包括裂解反应、重组反应和缩聚反应。
在裂解反应中,长链烃分子断裂成较短的碳链分子。
在重组反应中,分子中的碳原子重新组合,形成不同长度的碳链分子。
在缩聚反应中,碳链分子结合在一起形成较长链的烃分子。
催化裂化反应需要在相对较高的温度和压力条件下进行。
高温有助于加速反应速率,但同时也会增加反应副产物的生成。
在催化裂化过程中,还需要加入适量的氢气作为氢源,以防止催化剂的失活和副产物的生成。
催化裂化工艺在炼油行业中具有广泛的应用。
通过调整反应条件和催化剂的选择,可以根据市场需求来优化生产不同种类的石油产品。
催化裂化技术的发展不断提高了石油产品的质量和产量,对于满足能源需求和改善环境污染有着重要意义。
催化裂化的工艺特点及基本原理

催化裂化的工艺特点及基本原理催化裂化是一种重要的炼油工艺,主要用于将重质石油馏分裂解为较轻的馏分,以增加汽油和其他高附加值产品的产量。
其工艺特点和基本原理如下:工艺特点:1.选择性:催化裂化能够选择性地将重质石油馏分中的长链烃破裂成较短的烃烷和烃烯。
这种选择性能使得催化裂化工艺可以得到较高品质和较高产率的汽油。
2.灵活性:催化裂化工艺可以通过控制反应条件(如温度、压力、催化剂活性等)来实现不同产品的选择性改变。
这使得生产者可以根据市场需求对产品进行灵活调整。
3.高产率:催化裂化能够将重质石油馏分中的大分子烃分解为较小的分子,从而增加汽油的产率。
此外,催化裂化还能产生其他高附加值产品,如液化石油气(LPG)、石脑油和柴油等。
4.能源效率:催化裂化可以在较低的温度和压力下进行,从而节约能源。
此外,催化裂化还可以利用石油馏分中的热和压力来驱动反应,节约能源成本。
基本原理:催化裂化是通过在催化剂的作用下将石油馏分中的长链烃分子破裂成较短的烃烷和烃烯的过程。
其基本原理包括以下几个方面:1.热裂解和催化裂解:石油馏分中的长链烃在高温条件下会发生热裂解,即分子内部键的断裂,生成较短的碳链。
催化裂化是在催化剂的作用下,将热裂解过程中产生的碳链进行选择性破裂。
2.催化剂的作用:催化剂在催化裂化反应中起到重要作用。
催化剂通常由多孔介质和活性组分组成,活性组分一般为酸性物质,如氧化铝、硅铝酸盐等。
催化剂能够吸附和解离烃分子,使其在催化剂表面发生分解反应,从而实现分子的破裂和选择性转化。
3.反应条件的控制:反应温度、压力、空速和催化剂活性等条件对催化裂化反应的效果具有重要影响。
通常情况下,较高的温度和较低的压力利于反应进行,但过高的温度会导致过度裂解和产生过多的烃烯。
因此,在实际生产中,需要综合考虑反应的产率、选择性和经济性,确定合适的反应条件。
4.产物分离和处理:催化裂化反应产生的产物通常是气体、液体和固体混合物,需要通过分离和处理工艺进行产品回收和提纯。
石油化学中的催化裂化
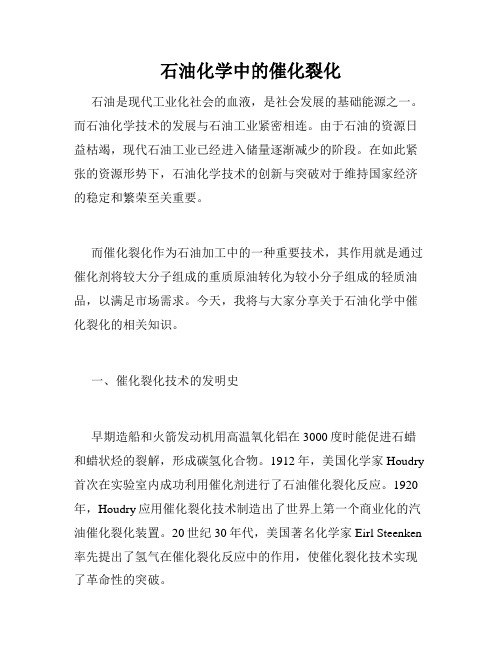
石油化学中的催化裂化石油是现代工业化社会的血液,是社会发展的基础能源之一。
而石油化学技术的发展与石油工业紧密相连。
由于石油的资源日益枯竭,现代石油工业已经进入储量逐渐减少的阶段。
在如此紧张的资源形势下,石油化学技术的创新与突破对于维持国家经济的稳定和繁荣至关重要。
而催化裂化作为石油加工中的一种重要技术,其作用就是通过催化剂将较大分子组成的重质原油转化为较小分子组成的轻质油品,以满足市场需求。
今天,我将与大家分享关于石油化学中催化裂化的相关知识。
一、催化裂化技术的发明史早期造船和火箭发动机用高温氧化铝在3000度时能促进石蜡和蜡状烃的裂解,形成碳氢化合物。
1912年,美国化学家Houdry 首次在实验室内成功利用催化剂进行了石油催化裂化反应。
1920年,Houdry应用催化裂化技术制造出了世界上第一个商业化的汽油催化裂化装置。
20世纪30年代,美国著名化学家Eirl Steenken 率先提出了氢气在催化裂化反应中的作用,使催化裂化技术实现了革命性的突破。
二、催化裂化技术的原理催化裂化技术采用催化剂在高温下进行反应,将重质原油分解成较小分子的烃类气体和液态烃类。
催化剂是指一种能促进原料分子在较低温度下发生化学反应的物质。
通过催化剂可以将化学反应的反应速率大幅提升,使得催化裂化反应能够在相对较低的温度下进行。
在催化裂化反应中,催化剂对原油中的长链碳氢链进行选择性的断裂,将它们转化为较短的链烃、芳烃以及一些氢气。
这些产物中的大部分可以被用作汽油、柴油等液体燃料。
此外,催化裂化还可以提高原油的利用率,减少油价依赖,节省资源等。
三、催化裂化技术的应用催化裂化技术被广泛应用于石油加工过程中,特别是在液态燃料生产部门。
在现代石油工业中,负责处理原油的催化裂化装置也越来越重要。
基于催化裂化技术的装置,被广泛应用于汽油、柴油、煤油以及其他石油化学产品的生产中。
另外,由于催化裂化具有降低原油的含硫量的效果,所以该技术也被用于石油处理的环保领域中。
催化裂化 压差-概述说明以及解释

催化裂化压差-概述说明以及解释1.引言1.1 概述概述:催化裂化是一种重要的炼油工艺,通过在高温和高压条件下将重质石油馏分分解为轻质石油产品。
它被广泛应用于石油化工行业,是产生汽油、柴油和液化石油气等石油产品的关键技术之一。
催化裂化技术的原理是在催化剂的作用下,将长链烃类分子断裂为较短链的烃类分子。
这个过程中产生大量的烃类气体,其中包括汽油和液化石油气等有价值的产品。
通过控制反应条件和催化剂的性质,可以调节产品的比例和质量。
催化裂化广泛应用于炼油厂和石油化工厂,其产品广泛用于交通运输、工农业生产以及家庭生活等领域。
随着世界人口的增长和经济的发展,对石油产品的需求不断增加,催化裂化技术在保障能源供应和满足人民日益增长的需求方面发挥着重要的作用。
然而,催化裂化过程中会出现压力差的问题。
在高温高压环境下进行的催化裂化反应需要对系统进行一定程度的压力控制,以保证反应过程的稳定性和安全性。
压力差控制是催化裂化中一个重要的环节,直接影响着产品质量、生产效率和设备寿命。
本文将重点探讨催化裂化中的压差控制问题,包括压力变化的原因、压力监测的方法和压力调整的技术。
通过深入研究压差控制的相关理论和实践经验,可以为催化裂化生产过程的优化提供有益的参考和指导。
同时,也为今后催化裂化技术的改进和发展提供了新的思路和方向。
1.2 文章结构文章结构部分的内容可以这样来写:本文主要分为三个部分:引言、正文和结论。
首先,在引言部分,我们将对催化裂化和压差进行概述。
我们将介绍催化裂化的基本原理和应用领域,以及本文的目的。
通过这一部分,读者将对催化裂化和压差有一个初步的了解,并明确本文的研究目标。
接下来,在正文部分,我们将详细探讨催化裂化的基本原理和应用领域。
我们将介绍催化裂化的基本概念、反应机制和影响因素,并深入探讨其在石油化工等领域的应用。
同时,我们将重点讨论催化裂化过程中的压差控制问题。
通过对催化裂化中压差的分析和控制方法的介绍,读者将对压差在催化裂化中的作用有一个全面的认识。
催化催化裂化技术
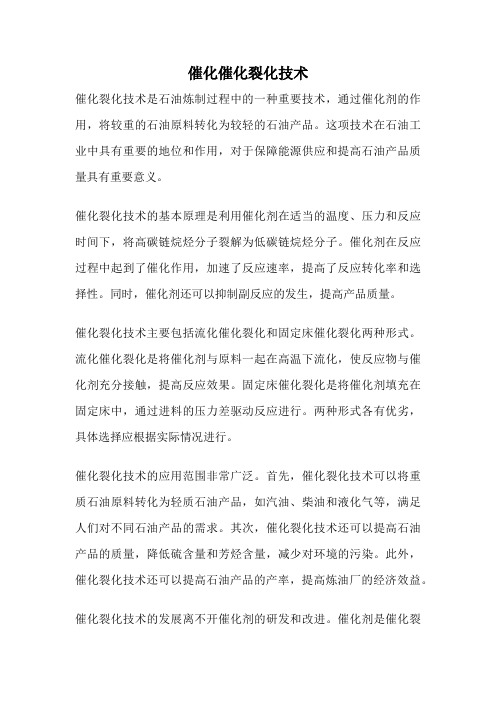
催化催化裂化技术催化裂化技术是石油炼制过程中的一种重要技术,通过催化剂的作用,将较重的石油原料转化为较轻的石油产品。
这项技术在石油工业中具有重要的地位和作用,对于保障能源供应和提高石油产品质量具有重要意义。
催化裂化技术的基本原理是利用催化剂在适当的温度、压力和反应时间下,将高碳链烷烃分子裂解为低碳链烷烃分子。
催化剂在反应过程中起到了催化作用,加速了反应速率,提高了反应转化率和选择性。
同时,催化剂还可以抑制副反应的发生,提高产品质量。
催化裂化技术主要包括流化催化裂化和固定床催化裂化两种形式。
流化催化裂化是将催化剂与原料一起在高温下流化,使反应物与催化剂充分接触,提高反应效果。
固定床催化裂化是将催化剂填充在固定床中,通过进料的压力差驱动反应进行。
两种形式各有优劣,具体选择应根据实际情况进行。
催化裂化技术的应用范围非常广泛。
首先,催化裂化技术可以将重质石油原料转化为轻质石油产品,如汽油、柴油和液化气等,满足人们对不同石油产品的需求。
其次,催化裂化技术还可以提高石油产品的质量,降低硫含量和芳烃含量,减少对环境的污染。
此外,催化裂化技术还可以提高石油产品的产率,提高炼油厂的经济效益。
催化裂化技术的发展离不开催化剂的研发和改进。
催化剂是催化裂化反应的核心,直接影响着反应的效果和产品的质量。
目前,石油工业中主要采用的催化剂是沸石型催化剂和金属催化剂。
沸石型催化剂具有较高的活性和选择性,能够有效地促进裂化反应的进行。
金属催化剂具有良好的抗中毒性能和稳定性,能够提高催化剂的使用寿命。
催化裂化技术的研究和应用还存在一些挑战和问题。
首先,催化剂的选择和制备是关键问题,需要探索新的催化剂材料和合成方法。
其次,催化剂的失活和再生问题也需要解决,以延长催化剂的使用寿命和降低生产成本。
此外,催化裂化技术的节能、环保和安全性问题也需要重视和解决。
催化裂化技术是石油工业中一项重要的技术,对于提高石油产品质量、增加产能和保障能源供应具有重要意义。
催化裂化名词解释
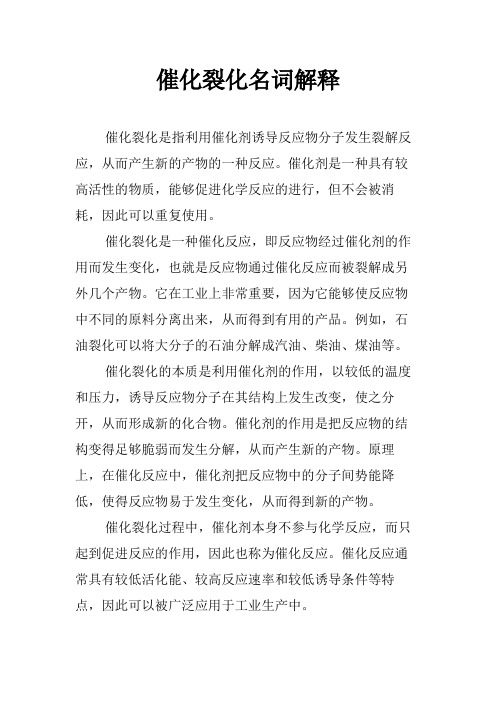
催化裂化名词解释
催化裂化是指利用催化剂诱导反应物分子发生裂解反应,从而产生新的产物的一种反应。
催化剂是一种具有较高活性的物质,能够促进化学反应的进行,但不会被消耗,因此可以重复使用。
催化裂化是一种催化反应,即反应物经过催化剂的作用而发生变化,也就是反应物通过催化反应而被裂解成另外几个产物。
它在工业上非常重要,因为它能够使反应物中不同的原料分离出来,从而得到有用的产品。
例如,石油裂化可以将大分子的石油分解成汽油、柴油、煤油等。
催化裂化的本质是利用催化剂的作用,以较低的温度和压力,诱导反应物分子在其结构上发生改变,使之分开,从而形成新的化合物。
催化剂的作用是把反应物的结构变得足够脆弱而发生分解,从而产生新的产物。
原理上,在催化反应中,催化剂把反应物中的分子间势能降低,使得反应物易于发生变化,从而得到新的产物。
催化裂化过程中,催化剂本身不参与化学反应,而只起到促进反应的作用,因此也称为催化反应。
催化反应通常具有较低活化能、较高反应速率和较低诱导条件等特点,因此可以被广泛应用于工业生产中。
催化裂化是一种重要的化学反应,可以使反应物分解成不同的产物,提高化学反应的效率,并有助于节省能源。
然而,由于催化裂化反应的本质是利用催化剂的作用,因此在催化裂化过程中,需要选择适当的催化剂,以及设定合适的工艺参数,才能使反应达到预期的效果。
- 1、下载文档前请自行甄别文档内容的完整性,平台不提供额外的编辑、内容补充、找答案等附加服务。
- 2、"仅部分预览"的文档,不可在线预览部分如存在完整性等问题,可反馈申请退款(可完整预览的文档不适用该条件!)。
- 3、如文档侵犯您的权益,请联系客服反馈,我们会尽快为您处理(人工客服工作时间:9:00-18:30)。
4
4.1 概述
二、催化裂化的发展历程 催化裂化自1936年实现工业化至今经历了四个阶段: 固定床、移动床、流化床和提升管。
Fixed Bed
Moving Bed
5
4.1 概述
Fluid Bed
Lift Pipe
在全世界催化裂化装置的总加工能力中,提升管催化 裂化已占绝大多数。
6
4.1 概述
三、催化裂化主要发展方向 1、加工重质原料
我国车用汽油70--80%是
产量, Mt/a
800 700 600 500 400 300 200 100 0 1991 1993 1995 1997 1999 2001 时间,年份
来自催化裂化汽油;
柴油产量的30%以上来自
催化裂化; 炼油企业中一半以上的效
全世界 中国 美国 日本 西欧
益依靠催化裂化。
18
C
4.3 烃类的催化裂化反应
二、反应机理(Reaction Mechanism) 正碳离子(carbonium ion)机理。 1、正碳离子 烃分子中有一个碳原子的外围缺少一对电子,而形成 带正电的离子,如:
H ¨ CH R C +
特点:不能在溶液中离解出来自由存在; 只能吸附在催化剂表面上参加化学反应。
23
4.3 烃类的催化裂化反应
CH3 CH3 C CH3 + + CH2 CH3 CH2 + C CH2 CH3 H2C H2C CH2 CH2
CH3 CH3 CH CH3 +
较小正碳离子与烯烃、烷烃、环烷烃间发生氢转移反 应,使小正碳离子变成小分子烷烃。
中性烃分子变成新正碳离子,再进行各种反应,使原
19
4.3 烃类的催化裂化反应
正碳离子形成:烯烃的双键中一个键断开,并在含H多的C 上加上一个H+,使含H少的另一个C缺少一对电子。 2、形成碳离子条件 (1)存在烯烃 来源:原料本身、热反应产生。
(2)存在质子H+
来源:由催化剂的酸性中心提供。 H+不称氢离子,存在于Cat.的活性中心,不能离开Cat.表面。
15
4.3 烃类的催化裂化反应
(2)双键位置异构
C C C C C C
C C C C C C
C H C C H C
(3)几何异构
C C H C C H
3、氢转移反应(hydrogen transfer reaction) 某烃分子上的氢脱下来加到另一烯烃分子上使之饱和 的反应。
氢转移是催化裂化特有的反应。
1、化学反应方向和化学平衡
反应条件:400~500℃、接近常压,反应可分三类: (1)平衡时基本进行完全的反应:分解反应、氢转移
平衡常数很大、可看作不可逆反应; 反应深度不受平衡限制,由反应速率和反应时间决定。
32
4.3 烃类的催化裂化反应
(2)平衡时进行不完全的反应:异构化、开环
化学平衡常数值不大,一般反应条件下要受平衡限制; 反应速率不高、反应时间不长,反应很难达到平衡,
烷烃进行氢转移反应而生成稳定的烷烃和芳烃。
烯烃与高分子芳烃缩合生成焦碳。
31
4.3 烃类的催化裂化反应
思考3:在催化裂化反应中,需要控制二次反应么?
在催化裂化生产中应适当控制二次反应的发生
3、渣油催化裂化反应
芳香分中含有较多的多环芳烃和稠环芳烃。我国渣油的特点:胶质含量高(50%),沥 青质含量低。减压渣油的沸点很高,在FCC提升管处与催化剂接触时不会全部气化。所以是 一个气一液一固三相催化反应。采用不同孔径的分子筛催化剂进行渣油的FCC反应。 四、催化裂化反应的热力学特征
16
4.3 烃类的催化裂化反应
C
+C C C C
C
+ C C C C
特点:二烯烃最易接受氢转化为单烯烃,故产品中二
烯烃很少。
4、芳构化反应(aromatization reaction) 所有能生成芳烃的反应。也是催化裂化的主要反应。
C C C C C C C
C C
+ 6H
17
4.3 烃类的催化裂化反应
30
4.3 烃类的催化裂化反应
思考1:为什么有这些变化规律?
因为达到一定反应深度后,再加深反应,中间产物将会进 一步分解成更轻馏分,其分解速度>生成速度。
称初次反应产物再继续反应为二次反应。 思考2:二次反应对产品的产率和质量的影响?
有利方面:烯烃再异构化生成辛烷值更高的异构烃,或环 不利方面:烯烃裂化为干气,丙烯、丁烯由H转移而饱和,
第四章 催化裂化 Chapter 4 Catalytic Cracking
辽宁石油化工大学 石油化工学院 赵德智
1
本章主要内容
概述
催化裂化工艺流程 烃类的催化裂化反应 催化裂化的原料和产品 催化剂的失活与再生 流态化基本原理和流化输送 催化裂化主要设备
反应-再生系统及工艺计算
2
4.1 概述
原油一次加工
35
4.3 烃类的催化裂化反应
催化碳的计算:
催化碳=总碳-附加碳-可汽提碳 式中:总碳——再生时烧去焦碳中的总碳量; 附加碳——原料中残碳转化生成的焦碳中的碳,附
加碳=新鲜原料量×新鲜原料的残碳%×0.6%;
如常压渣油、脱沥青残渣油等,以提高经济效益。
2、尽量提高汽油辛烷值
改善原料质量、重整催化汽油中间馏分、优化操作条件、
使用高辛烷值催化剂。
3、降低能耗
降低焦炭产率、充分利用再生烟气中CO的燃烧热、发展再
生烟气热能利用技术。
7
4.1 概述
4、减少环境污染
再生烟气中的粉尘、CO、SO2和NOx; 含硫污水、产品精制时产生的碱渣; 再生烟气放空、机械设备产生的噪音。 5、过程模拟和计算机应用
H CH3 C CH3 + H+(Cat.) + CH3 CH CH3
思考1:为什么催化裂化产物中少C1、C2,多C3、C4? 正碳离子分解时不生成<C3、C4的更小正碳离子。
思考2:为什么催化裂化产物中多异构烃?
伯、仲正碳离子稳定性差,易转化为叔正碳离子。 思考3:为什么催化裂化产物中多β烯烃? 伯正碳离子易转为仲正碳离子,放出H+形成β烯烃。
5、叠合反应(condensation reaction)
烯烃与烯烃合成大分子烯烃的反应。 随叠合深度不断加深,最终将生成焦炭。与叠合相反的分 解反应占优势,故催化裂化过程叠合反应不显著。
6、烷基化反应(alkylation reaction)
烯烃与芳烃或烷烃的加合反应。
C
+
C C C C
C
C C C
常减压蒸馏:只可得10~40%的汽油、煤油、柴油等
轻质油品,其余为重质馏分和渣油。
原油二次加工
催化裂化:重质油轻质化的过程。 催化重整:生产高辛烷值汽油及轻芳烃。 催化加氢:石油馏分在氢气存在下催化加工的过程。
产品精制:提高产品质量,满足产品规格要求。
3
4.1 概述
一、催化裂化在炼油过程中的地位 催化裂化是现代化炼油厂用来改质重质馏分和渣油的 核心技术。
20
4.3 烃类的催化裂化反应
2、正碳离子机理 以正n-C16H32来说明。 (1)生成正碳离子 正n-C16H32得到一个H+,生成正碳离子。如
H n-C5H11 C C10H20 + H+ H n-C5H11 C C10H21
+
(2)β断裂 大正碳离子不稳定,容易在β位置上断裂,生成一个烯 烃和一个小正碳离子:
外扩散:反应产物分子扩散到主气流中。
27
4.3 烃类的催化裂化反应
速度最慢的步骤对整个催化裂化反应起控制作用。 (1)各类竞争吸附能力 C数相同的各类烃,被吸附的顺序为: 稠环芳烃>稠环环烷烃>烯烃>单烷基侧链的单环芳 烃>环烷烃>烷烃;
同类烃,分子量↗,越容易被吸附。
(2)各类烃的化学反应顺序 烯烃>大分子侧链的单环芳烃>异构烷烃或烷基环烷 烃>小分子侧链的单环芳烃>正构烷烃>稠环芳烃。
26
4.3 烃类的催化裂化反应
三、催化裂化反应的特点 1、气固非均相反应(inhomogeneous reaction) 原料在反应器汽化,然后在Cat.表面上反应。
外扩散:反应物分子向Cat.表面扩散; 内扩散:反应物分子向Cat.内部扩散; 吸附:反应物分子被Cat.内表面吸咐; 表面反应:Cat.内表面上发生化学反应; 脱附:反应产物分子从Cat.内表面脱附; 内扩散:反应产物分子由孔穴向外扩散;
C C C C C C C C C C C+C C C
规律:分子越大越易断裂; C原子数相同时,异构烃比正构烃容易分解。
13
4.3 烃类的催化裂化反应
(2)烯烃(olefin) 烯烃分解反应规律与烷烃相似,分解速度比烷烃快。 (3)环烷烃(cyclane) 开环生成异构烯烃;带侧链时,可能断侧链反应。
料不断变成产品。
24
4.3 烃类的催化裂化反应
(5)叠合反应 正碳离子和烯烃结合在一起,生成大分子正碳离子:
H CH3 C CH3 + H2C CH CH2 CH3 + CH3 H CH3 CH CH2 C CH2 CH3 +
ห้องสมุดไป่ตู้
(6)反应终止 正碳离子放出H+还给Cat.而变成烯烃,反应终止:
25
4.3 烃类的催化裂化反应
22
4.3 烃类的催化裂化反应
CH2 C8H17 + CH3 CH C7H16 + CH3 CH CH2 + CH2 C5H11 +
CH2 C5H11 +