0 熟料烧成系统操作方法14
熟料烧结(一)
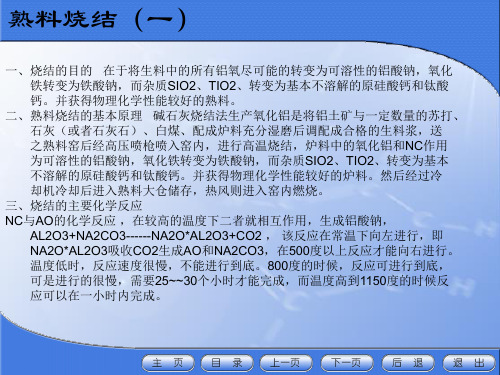
熟料烧结(一)
冷却带 从火焰后部到窑头的一带。高温熟料在冷却带由二次空气和窑头漏风冷却, 逐步冷却到1000以下下落到冷却机。 五、熟料窑结构示意图:
熟料烧结(二)之熟料窑系统
烧结温度范围和液相量控制的意义 液相量的出现和控制 在一定的烧结温度下,液相量很少,在该温度时只能使炉料体现有少许收缩,但尚 不能把粉状炉料粘结成颗粒状(叫黄料)。 提高一定温度,出现液相量较少,在凝结时,虽能把粉状炉料粘结成颗粒状,的温度,液相量达到一定的适当量时,才能出现颗粒度均匀,孔隙度大 并有一定机械强度的熟料,叫正烧结料。 又提高一定的温度,液相量较多时,产生的是致密而少孔的,机械强度很大的熟料, 叫过烧结料。 当液相量过多时,就产生坚硬无孔的,所谓熔融熟料。 生产上把产生以上近烧结熟料,正烧结熟料、过烧结熟料所对应的温度,称为近烧 结温度、正烧结温度、过烧结温度。而炉料从近烧结温度到过烧结温度所经过 的温度区间,叫烧结温度范围。一般来说,在炉料正常配方的情况下,近烧结 时液相量为5~~10%,正烧结时液相量为15~~20%,过烧结时液相量为大于 ~~20%以上。
熟料烧结(二)之熟料窑系统
熟料烧结(二)之熟料窑系统
熟料烧结(二)之熟料窑系统
熟料烧结(二)之熟料窑系统
熟料生产工艺流程图:
熟料烧结(二)之熟料窑系统
几个概念: 烘窑 烘窑的目的是什么? 耐火砖砌好后,在点火开窑前必须烘窑, 使胶泥和耐火砖的水分缓慢的蒸发出来,以加强耐火砖和胶泥之间的结合,同 时可避免耐火砖温度急剧上升和水分剧烈蒸发而引起耐火砖表面爆裂,也防止 机械设备(领圈)因温度急剧升高而涨裂。 挂窑皮 窑皮是物料煅烧后粘附在烧成带耐火砖表面形成的保护层(过烧熟料层)。 它可以防止高温区物料对耐火砖的化学侵蚀和机械磨损,从而可以延长耐火砖 的使用寿命,提高回转窑的运转周期,同时可以增强传热效率,稳定窑的热工 制度,减少散热损失,所以挂好和维护好窑皮是保证优质高产的前提,而挂好 第一层高温窑皮尤为重要。 窑皮形成的机理: ;炉料在回转窑中由窑尾向窑头移动,当进入到分解带前沿时, 在一定温度下开始出现液相,随着温度升高液相量也相应增加,当增加到一定 数量时,炉料有黏结性,物料和耐火砖接触时,由于耐火砖向外散热,液相和 部分炉料就黏结在耐火砖表面而形成第一层窑皮,由于炉料推进,同时形成第 二层窑皮,第二层窑皮黏结后,第一层窑皮因为温度下降而凝固,这个过程继 续下去窑皮愈厚,当厚到一定程度时,由于窑皮的热负荷增加,窑皮表面温度 升高,液相黏度逐渐减小,由于向外冷却困难,液相过热,粘性不足,此时窑 皮就会停止生成。 结圈 炉料烧结过程中,由于液相的出现和凝结,在烧结带前后两端形成了致密而 高于窑皮的结圈称前结圈和后结圈。
水泥生产工艺质量应知应会考试题汇总

水泥生产工艺、质量应知应会考试资料一、填空题1、设备润滑工作的“五定”指的是(定人)、(定点)、(定期)、(定量)和(定质)。
2、空气输送斜槽主要由(槽体)、(透气层)和(多孔板)组成,其中槽体可由数节(标准段)和(非标准段)构成。
3、斗式提升机是水泥厂最常用的(垂直)输送设备,通常用来提升(块状)、(粒状)及(粉状)物料,按牵引构件的形式分为(环链)式、(板链)式和(胶带)式。
其卸料方式可分为(离心式)、(离心—重力式)和(重力式)。
4、胶带输送机由(传动滚筒)、(改向滚筒)、(输送带)、(上下托辊)、(拉紧装臵)、(给料装臵)、(传动装臵)、(卸料装臵)和(清扫装臵)。
5、陕西北元化工集团水泥有限公司的机构设臵为“八科四分厂”指的是(综合管理科)、(生产技术科)、(质量管理科)、(安全环保科)、(设备管理科)(财务管理科)、(物资管理科)、(发运管理科)(原料分厂)、(烧成分厂)、(制成分厂)和(动力检修分厂)。
6、胶带输送机经常出现的不正常现象有(胶带跑偏)、(胶带打滑)、(胶带断裂)、(接头开裂)、(胶带撕裂)。
7、连接胶带输送机接头的方式有(硫化胶接)、(冷粘胶接)和(机械连接)。
8、锤式破碎机的主要零部件有(锤头)、(转子)、(篦条筛)、(内壁衬板)、(机架)等。
9、合格的生料包括(合理而稳定的化学成分)和(合理的细度)。
10、细度的表示方法有(筛析法)、(比表面积法)和(粒径分布法)。
11、生料的主要控制项目有(氧化钙)、(细度)、(三氧化二铁)、(入磨物料粒度)和(水分)。
12、出磨水泥的控制项目包括(物料的配合比)、(细度)、(三氧化硫)、(凝结时间)、(安定性)、(强度)、(烧失量)和(氧化镁)等。
13、普通硅酸盐水泥的强度等级分为(42.5)、(42.5R)、(52.5)、(52,5R)。
14、物料配料的主要形式有(磨头配料)和(库底配料),我厂采用的是(库底配料)。
15、球磨机衬板的安装方式有(螺栓固定法)和(镶砌法)。
日产5000吨水泥熟料新型干法生产线烧成系统窑头工艺设计
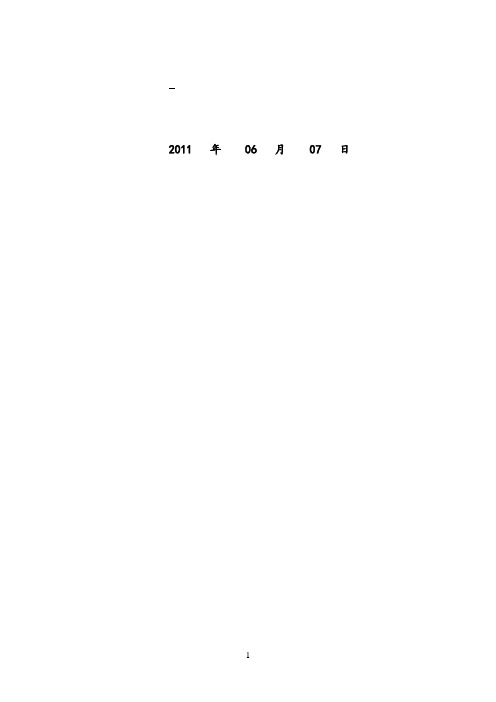
关键词:物料平衡、新型干法生产、篦冷机、电收尘、
ABSTRACT
This designisone 5000tons of cementclinkerproductionlines burningdrykilnsystem ofsome ofthe design.In order todesign morereasonable and perfect,I revieweda lot of information, andcombined with the currentdaily output of5,000 tons ofcement clinkerproduction line ofnew drykilnsystempractical examplesto makehis owndesign results.But has very many Shortcoming existence, therefore looks forgiveness. Under I introduce my design mentality. 1.Kiln choice:in the selection process of Kiln, Icalculate thetheoretical formulausedkiln, and I alsofindthe actualmanufacturerof thesituation, finally, Isetmycombination;2.Mass balance computation:According to the empirical formula(limestone saturation coefficient, silicic acid rate, alumina rate)calculates, obtains the appropriate rate value.Determinethe finalratio of raw materials;3.Material balancecalculationsbased on previousresults, combined withtheoretical formulaand the application ofselectedmodelsderivedinstance;4.Appurtenance shaping: The appurtenance includes,Clinkercrusher,clinkerzippermachines,centrifugal fans,pulverized coal burner.The equipment although is small, but in the production process also is essential.
水泥烧成系统的调试方法
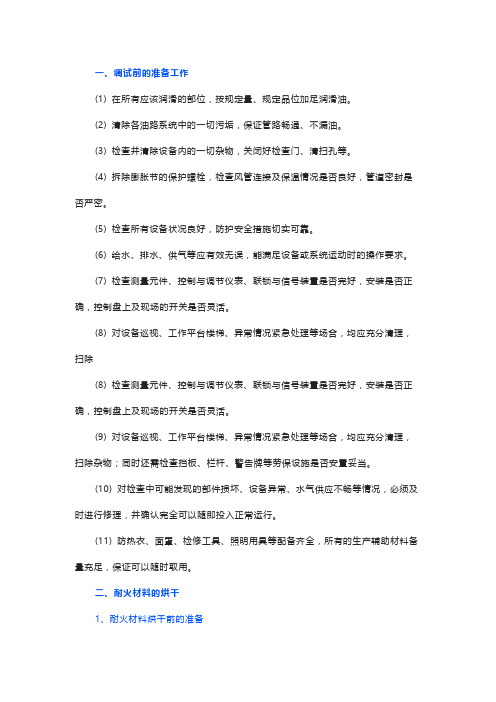
一、调试前的准备工作(1) 在所有应该润滑的部位,按规定量、规定品位加足润滑油。
(2) 清除各油路系统中的一切污垢,保证管路畅通、不漏油。
(3) 检查并清除设备内的一切杂物,关闭好检查门、清扫孔等。
(4) 拆除膨胀节的保护螺栓,检查风管连接及保温情况是否良好,管道密封是否严密。
(5) 检查所有设备状况良好,防护安全措施切实可靠。
(6) 给水、排水、供气等应有效无误,能满足设备或系统运动时的操作要求。
(7) 检查测量元件、控制与调节仪表、联锁与信号装置是否完好,安装是否正确,控制盘上及现场的开关是否灵活。
(8) 对设备巡视、工作平台楼梯、异常情况紧急处理等场合,均应充分清理,扫除(8) 检查测量元件、控制与调节仪表、联锁与信号装置是否完好,安装是否正确,控制盘上及现场的开关是否灵活。
(9) 对设备巡视、工作平台楼梯、异常情况紧急处理等场合,均应充分清理,扫除杂物;同时还需检查挡板、栏杆、警告牌等劳保设施是否安置妥当。
(10) 对检查中可能发现的部件损坏、设备异常、水气供应不畅等情况,必须及时进行修理,并确认完全可以随即投入正常运行。
(11) 防热衣、面罩、检修工具、照明用具等配备齐全,所有的生产辅助材料备量充足,保证可以随时取用。
二、耐火材料的烘干1、耐火材料烘干前的准备(1) 全面检查、排除旋风筒、分解炉、回转窑内的一切杂物,管道畅通无堵。
(2) 打开系统中的烘干排气孔,关闭旋风预热器和分解炉所有的人孔门、清扫孔等。
(3) 打开各级旋风筒的下料翻板阀,并用铅丝固定处于常开状态。
(4) 关闭冷却机至煤磨管道上的热风阀,使烧成系统不受外界因素干扰。
(5) 点火燃油系统准备就绪,柴油备量充足。
(6) 煤粉仓应备有适量煤粉。
(7) 根据衬料材质、砌筑厚度、含水量、砌筑方法等实际情况,制定出切实可行的升温烘干方案。
2、第一次烘窑的升温曲线3、烘窑操作基本方法(1) 通过调节窑尾收尘器排风机进口风门开度来控制窑尾负压约-50 ~-100Pa 。
烧成系统常见故障的中控处理方法

2 煤 粉 计 量 秤 跑 煤
21 窑头煤 粉 计量 秤跑 煤 .
21 1 原 因分 析 ..
() 生紧 急 故障 , 要 维修 时 间 长 时 , 1发 需 则应 止
料停 窑 处理 。
() 生紧 急 故障 , 要 维修 时 间 短 时 , 以减 2发 需 可 少喂 料 量 、 降低 窑速 、 少 风量 ,I 篦床 改为现 场 减 段 启车 , 以防 止 篦床 被 熟 料 压 死 , 链 斗故 障 处 理 完 待 后 , 复 中控 正常操 作 。 恢
槽处) 使熟料往库外排放, , 后用铲车将外排的熟料
图 1 系统 工艺 流 程 图
运走 , 这样 抢 修 时可 以不影 响 正常 生 产 。待 链 斗机 故 障 处 理 完 毕 , 中控 操 作 员 联 系 启 车 , 熟料 通 由 使
过 I段 熟料 链斗机 回到库 内。 I
1 熟 料 链 斗 输 送 机 故 障
片 脱 落 、 斗 变 形 、 螺 栓 、 斗 小轮 脱 落 、 道 不 链 掉 链 轨 平整 等 。 处 理 方法 : 中控 操作 员 在得 到设 备 故 障 的信 息 后 , 先 把 篦 床 上 的料 推 得 薄 一些 , 应 以防 料 多压 住 篦床 , 同时 通 知现 场及 修 理 人 员迅 速抢 修 I段链 斗 输 送 机 。修 理 人 员在 找 准 合 适 的便 于 维 修 的位 置
中控 操作 员 按顺序 启动 设备 。开始 篦 床速度 设 定 比 正 常高 些 , 止料 多压 住 篦床 , 篦床 启动 后 , I 防 待 把 I 段 篦床 的速 度 设 置慢 一 点 , 以避免 进 入链 斗 的 料过
多溢 出链 斗 。
烧结系统操作说明
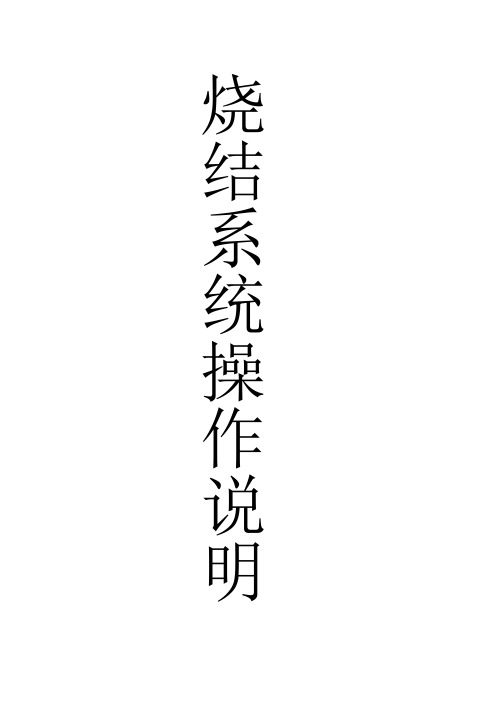
烧结系统操作说明一:系统概括:烧结系统整体分为以下几个分系统:烧制系统;上料系统;成品系统;返料系统。
所有系统中所涉及的设备,必须在现场操作箱选择到自动位置时,设备才能在系统的操作画面中控制其运行。
在各个分系统画面和工艺画面中均可以监控设备的运行情况,及设备的故障信息。
在成品系统,成品系统和返料系统中各皮带机控制方式都是逆启顺停(在以下分系统介绍中会详细提及)。
以下是分画面的详细介绍。
主画面主画面:主画面主要是监控画面,其功能是监控烧制系统所包含的圆棍布料,七棍布料,烧结机,单辊破碎机,热振筛,环冷机等设备的运行情况,以及各个抽风风箱的压力及温度监控,以及点火器所需要的空气,煤气的压力温度,流量等参数。
在烧结画面上按下主画面按钮后,显示出烧结系统的主画面,主要有以下几个内容:一、圆辊布料速度、烧结机速度:是指圆辊布料器和烧结机的速度,单位是赫兹HZ二、煤气、助燃风参数:是指煤气调节阀反馈、煤气压力、煤气流量、煤气温度等参数助燃风参数是助燃风的阀位反馈、助燃风压力、助燃风温度(画面上显示是空气调节阀反馈、空气压力、空气温度)三、风箱参数风箱参数主要是风箱的温度和负压1、风箱温度:是指1#、2#、3#、6#、10#、13#、14#、15#风箱的温度。
单位是摄氏度,并由柱状图显示温度的高低。
柱状图的显示范围是0-600度2、风箱负压:是批1#、2#、3#、6#、10#、13#、14#、15#风箱的压力。
单位是千帕,并由柱状力显示。
柱状图显示的范围是0~-20KPA四、画面切换按钮是进行画面切换,以显示出其它的画面。
五、环冷机参数是显示环冷机各电机的轴承温度、环冷机速度、环冷机废气的画面六、点火炉温度:是点火炉内部温度在主画面上点下工艺画面按钮,则会显示工艺画面内容。
工艺画面:在此画面中可以监控及控制烧结系统中所涉及的所有设备,各个设备都有自己的现场控制箱,各个设备在画面中控制时也区分手动自动,当操作人员在画面中选择各个系统单动时,此时需要操作人员在画面中选择该系统所涉及的每一个设备手动点动启动该设备;在选择该系统联动时,再选择系统联动启动,此时该系统中所涉及的设备会自动按程序编辑的顺序启动。
烧成工艺知识

烧成系统工艺知识简介一、预热器的工作原理来自上一级旋风筒收集下来的物料经喂料管落入散料板上冲散折回进入下一级旋风筒的排气管道中均匀冲散悬浮,并随上升气流进入旋风筒进行气固分离。
气流由上而下做旋风运动,最后从锥部随排风机给予的动能沿旋风筒的中心垂直往上运动。
此时,固体的物料沿筒壁落下进入下料溜管。
排出的是相对干净的废气。
二、预热器的功能主要功能是充分利用回转窑和分解炉排出的废气余热加热生料,使生料预热及部分硅酸盐分解。
为了最大限度提高气固间的预热效率,实现整个煅烧系统的优质、高产、低消耗。
必须具备气固分散均匀。
换热迅速和高效分离三个功能,通常换热功能是在连接管道中完成的,高效分离是在旋风筒内完成的。
1、撒料箱的功能特点⑴、利用物料下落的动能冲击撒料箱底板将料流打散;⑵、增大底板面积形成梯形与管道相接,以适应物料分离扩散形状的要求;⑶、底板有一定的倾角,降低物料与底板的摩擦阻力,以利分散的物料向管道内流动;⑷、底板表面一般有顺料流方向的山形筋条,能增强底板刚度以防热变形,同时防止分散后的物料重新汇聚成团。
2、锁风阀的作用及要求主要作用是保持下料均匀畅通,又起密封作用,动作必须灵活自如。
要求:⑴、阀体必须坚固、耐热,避免过热引起变形损坏;⑵、阀板摆动轻巧灵活,重锤易于调整,既要避免阀板开闭动作过大,又要防止物流发生脉冲,做到下料均匀;⑶、阀体具有良好的气密性,杜绝漏风;⑷、支撑阀板的轴承要密封完好,防止灰尘掺入;⑸、阀体各部件易于检修更换。
3、旋风筒的作用⑴、主要作用是气固分离,提高旋风筒的分离效率是减少生料粉内、外循环,降低热损失和加强气固热交换的重要条件;⑵、影响旋风筒分离效率的主要因素:a.旋风筒的直径越小,分离效率越高;b.旋风筒的进风口的形式及尺寸。
气流应以切向进入旋风筒,减少涡流干扰;进风口尺寸应使进口风速在16~22m/s 之间,最好在18~20m/s之间;c.内筒尺寸及插入深度,内筒直径小,插入深,分离效率高。
浅谈新型干法熟料生产线的烧成系统
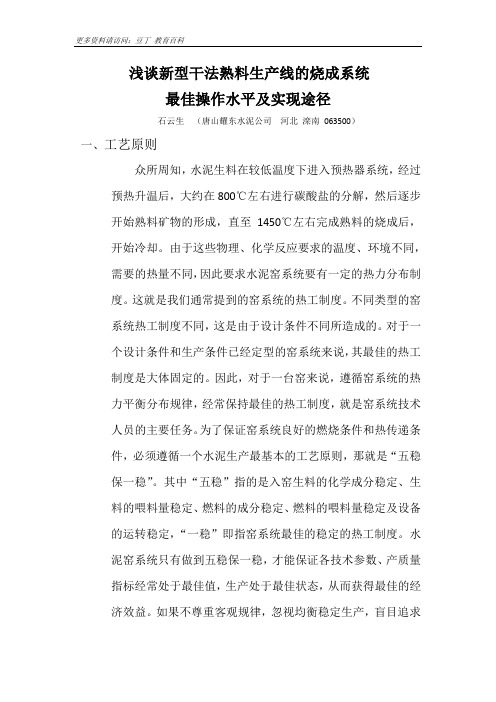
浅谈新型干法熟料生产线的烧成系统最佳操作水平及实现途径石云生(唐山耀东水泥公司河北滦南063500)一、工艺原则众所周知,水泥生料在较低温度下进入预热器系统,经过预热升温后,大约在800℃左右进行碳酸盐的分解,然后逐步开始熟料矿物的形成,直至1450℃左右完成熟料的烧成后,开始冷却。
由于这些物理、化学反应要求的温度、环境不同,需要的热量不同,因此要求水泥窑系统要有一定的热力分布制度。
这就是我们通常提到的窑系统的热工制度。
不同类型的窑系统热工制度不同,这是由于设计条件不同所造成的。
对于一个设计条件和生产条件已经定型的窑系统来说,其最佳的热工制度是大体固定的。
因此,对于一台窑来说,遵循窑系统的热力平衡分布规律,经常保持最佳的热工制度,就是窑系统技术人员的主要任务。
为了保证窑系统良好的燃烧条件和热传递条件,必须遵循一个水泥生产最基本的工艺原则,那就是“五稳保一稳”。
其中“五稳”指的是入窑生料的化学成分稳定、生料的喂料量稳定、燃料的成分稳定、燃料的喂料量稳定及设备的运转稳定,“一稳”即指窑系统最佳的稳定的热工制度。
水泥窑系统只有做到五稳保一稳,才能保证各技术参数、产质量指标经常处于最佳值,生产处于最佳状态,从而获得最佳的经济效益。
如果不尊重客观规律,忽视均衡稳定生产,盲目追求产量,就会人为地造成热工制度的紊乱,结果只能事与愿违、得不偿失。
尤其对于预分解窑,在分解炉内生料与高温气体的传热迅速。
由于窑速的大幅提高,物料在窑系统内的停留时间短,化学反应快,对热工制度的波动更加敏感。
当热工制度不稳时,轻者造成温度、压力的大幅波动,重者直接导致预热器系统的粘结堵塞。
因此,重点强调“均衡稳定”是新型干法工艺最基本、最重要的操作原则,生产过程中需要操作人员运用各种调节手段及时适当的调整,恢复保持或达到新条件下的新的“均衡稳定”。
我们采用的众多新技术,如原料预均化、生料均化、X荧光分析仪、自动控制回路等都是为了达到“均衡稳定”的目的。
水泥熟料的煅烧
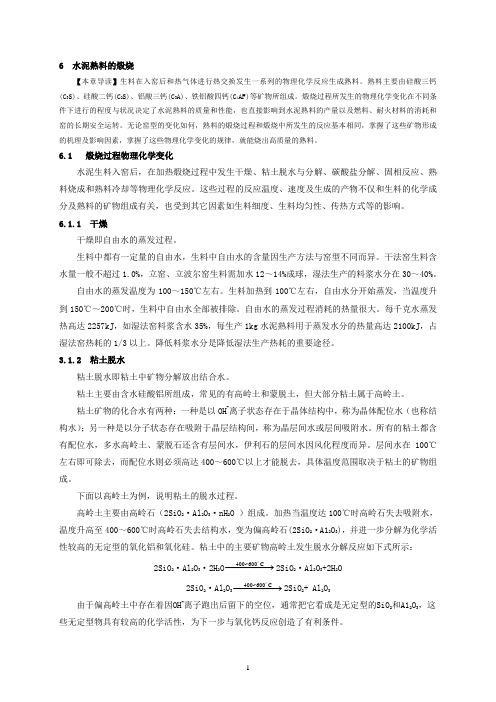
6 水泥熟料的煅烧【本章导读】生料在入窑后和热气体进行热交换发生一系列的物理化学反应生成熟料。
熟料主要由硅酸三钙(C 3S)、硅酸二钙(C 2S)、铝酸三钙(C 3A)、铁铝酸四钙(C 4AF)等矿物所组成。
煅烧过程所发生的物理化学变化在不同条件下进行的程度与状况决定了水泥熟料的质量和性能,也直接影响到水泥熟料的产量以及燃料、耐火材料的消耗和窑的长期安全运转。
无论窑型的变化如何,熟料的煅烧过程和煅烧中所发生的反应基本相同,掌握了这些矿物形成的机理及影响因素,掌握了这些物理化学变化的规律,就能烧出高质量的熟料。
6.1 煅烧过程物理化学变化水泥生料入窑后,在加热煅烧过程中发生干燥、粘土脱水与分解、碳酸盐分解、固相反应、熟料烧成和熟料冷却等物理化学反应。
这些过程的反应温度、速度及生成的产物不仅和生料的化学成分及熟料的矿物组成有关,也受到其它因素如生料细度、生料均匀性、传热方式等的影响。
6.1.1 干燥干燥即自由水的蒸发过程。
生料中都有一定量的自由水,生料中自由水的含量因生产方法与窑型不同而异。
干法窑生料含水量一般不超过1.0%,立窑、立波尔窑生料需加水12~14%成球,湿法生产的料浆水分在30~40%。
自由水的蒸发温度为100~150℃左右。
生料加热到100℃左右,自由水分开始蒸发,当温度升到150℃~200℃时,生料中自由水全部被排除。
自由水的蒸发过程消耗的热量很大。
每千克水蒸发热高达2257kJ ,如湿法窑料浆含水35%,每生产1kg 水泥熟料用于蒸发水分的热量高达2100kJ ,占湿法窑热耗的1/3以上。
降低料浆水分是降低湿法生产热耗的重要途径。
3.1.2 粘土脱水粘土脱水即粘土中矿物分解放出结合水。
粘土主要由含水硅酸铝所组成,常见的有高岭土和蒙脱土,但大部分粘土属于高岭土。
粘土矿物的化合水有两种:一种是以OH -离子状态存在于晶体结构中,称为晶体配位水(也称结构水);另一种是以分子状态存在吸附于晶层结构间,称为晶层间水或层间吸附水。
(ppt版)熟料的冷却及设备

〔1〕开发新型高效、低阻的旋风筒 〔2〕开发新型换热管道
〔3〕开发新型锁风阀 〔4〕开发新型撒料装置
第十六页,共八十七页。
各级旋风(xuànfēng)预热器性能的配合〔以5级为例〕
〔1〕各级旋风(xuànfēng)筒的气固别离效率 〔2〕各级旋风(xuànfēng)筒的外表散热损失
• 〔3〕分解炉的温度
• 〔4〕燃料燃烧条件
• 〔5〕粉料与气体的停留时间
第二十九页,共八十七页。
(1)、NSF型和 CSF型 NSF型炉: 结构:
上部:圆柱+圆锥体, 为反响室
下部:旋转涡壳——涡旋室
特点:
气体: 窑气、预热空气经涡旋 室混合后
形成喷旋叠加的湍流运动 (yùndòng)混合,
盘旋进入反响室
mr--生产每千克熟料所需要的燃料量〔kg煤/kg熟料〕
2〕水泥熟料(shú liào)的实际烧成热耗
〔kJ/kg熟料〕
第四页,共八十七页。
3〕回转窑内燃烧带的截面热力强度〔燃烧带的截面热负荷〕:燃烧带 单位截面面积(miàn jī)、单位时间内所承受的热量
4〕回转窑内燃烧带的外表热力强度〔燃烧带的外表热负荷) 燃烧带单位外表面积(miàn jī)、单位时间内所承受的热量
燃料:通过几个喷煤嘴从漩涡室 顶优侧点向:下气固之间的混合(hùnhé)得到了改善,燃料燃烧完全,碳酸盐的 斜分喷解入程三度次高风,热的耗空低气。流中,
第三十页,共八十七页。
CSF型〔在NSF上改进〕
主要改进: 1〕在分解炉上部设置 了一个涡流室, 使炉 气呈螺旋形出炉。
2〕将分解炉与预热器之 间的联接管道延长(yáncháng)--相当于增加了分解炉的 容积),其效果是延长 (yáncháng)了生料在分解炉内 的停留时间,使得碳酸盐
水泥熟料煅烧工技能与知识(一)

水泥熟料煅烧工技能与知识(一)编码:25—005工种名称:水泥熟料煅烧工工种定义:利用窑炉将生料煅烧成水泥熟料适用范围:回转窑、机立窑等级线:初、中、高培训期:二年初级水泥熟料煅烧工知识要求:1.水泥生产工艺流程。
2.本岗位操作(工作)标准及各项规程制度。
3.本岗位各项经济技术指标及计算方法。
4.本岗位各种设备、仪表、配件、工具的名称、规格、材质、性能、结构、使用维护方法及更换周期。
5.本岗位所用润滑剂的种类、名称、性能和使用方法。
6.生料、燃烧成份、细度(粒度)变化对窑产质量和操作影响的一般知识。
7.立窑生料球的水份、粒度、孔隙率、强度和配煤量对煅烧的影响。
8.立窑煅烧方法的基本知识。
9.熟料率值、燃料质量、风煤(油)配合、喷煤管(油枪)对火焰形状、燃烧速度、温度、窑皮结构和熟料产质量影响的一般知识。
10.窑内各带的划分及物料在各带内发生的物理—化学变化的一般知识。
11.预分解窑的分解炉、预热器的作用、各测点工艺参数的一般知识。
12.稳定立窑底火的一般知识。
13.各指示仪表参数发生变化时,反映的窑内热工制度变化的一般知识。
14.钳工、电气的一般知识。
15.全面质量管理的基本知识。
16.全面质量管理的基本知识。
技能要求:1.独立操作本岗位设备,在指导下点火开窑的熄火停窑。
2.维护本岗位设备,正确处理常见一般故障。
3.担负本岗位设备小修工作。
4.根据熟料在烧成带的结粒、色泽、粒度翻动情况、外观组织、黑影远近等因素控制熟料升重、质量。
5.根据立窑出窑熟料的色泽、外观状况,判断熟料质量和窑面煅烧情况,判断烧成温度和底火位置。
6.一般机械零件图的识图。
7.正确填写岗位记录。
中级水泥熟料煅烧工知识要求:1.本工种各项经济技术指标及计算方法。
2.本工种各种设备、仪表、配件、工具的名称、规格、材质、性能、结构、使用维护方法及更换周期。
3.本工种设备各种轴承、齿轮公差与配合。
4.燃料燃烧与传热的一般知识。
5.物料在窑内各带发生物理—化学反应的理论知识,加速各带物理—化学反应的途径。
新型干法水泥第四节熟料烧成系统的调试
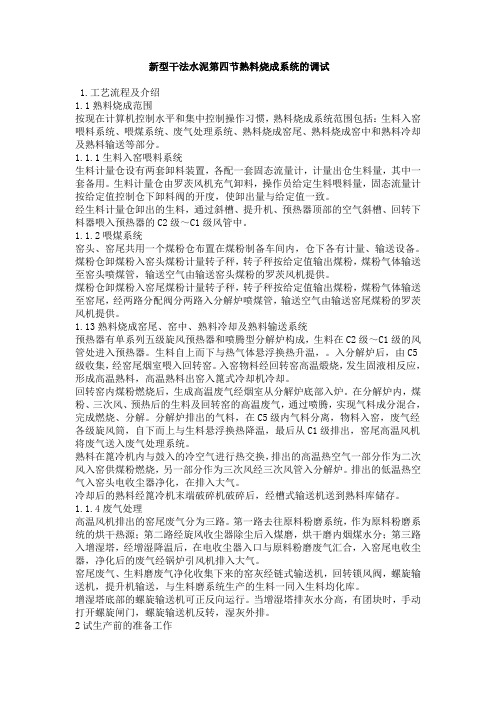
新型干法水泥第四节熟料烧成系统的调试1.工艺流程及介绍1.1熟料烧成范围按现在计算机控制水平和集中控制操作习惯,熟料烧成系统范围包括:生料入窑喂料系统、喂煤系统、废气处理系统、熟料烧成窑尾、熟料烧成窑中和熟料冷却及熟料输送等部分。
1.1.1生料入窑喂料系统生料计量仓设有两套卸料装置,各配一套固态流量计,计量出仓生料量,其中一套备用。
生料计量仓由罗茨风机充气卸料,操作员给定生料喂料量,固态流量计按给定值控制仓下卸料阀的开度,使卸出量与给定值一致。
经生料计量仓卸出的生料,通过斜槽、提升机、预热器顶部的空气斜槽、回转下料器喂入预热器的C2级~C1级风管中。
1.1.2喂煤系统窑头、窑尾共用一个煤粉仓布置在煤粉制备车间内,仓下各有计量、输送设备。
煤粉仓卸煤粉入窑头煤粉计量转子秤,转子秤按给定值输出煤粉,煤粉气体输送至窑头喷煤管,输送空气由输送窑头煤粉的罗茨风机提供。
煤粉仓卸煤粉入窑尾煤粉计量转子秤,转子秤按给定值输出煤粉,煤粉气体输送至窑尾,经两路分配阀分两路入分解炉喷煤管,输送空气由输送窑尾煤粉的罗茨风机提供。
1.13熟料烧成窑尾、窑中、熟料冷却及熟料输送系统预热器有单系列五级旋风预热器和喷腾型分解炉构成,生料在C2级~C1级的风管处进入预热器。
生料自上而下与热气体悬浮换热升温,。
入分解炉后,由C5级收集,经窑尾烟室喂入回转窑。
入窑物料经回转窑高温煅烧,发生固液相反应,形成高温熟料,高温熟料出窑入篦式冷却机冷却。
回转窑内煤粉燃烧后,生成高温废气经烟室从分解炉底部入炉。
在分解炉内,煤粉、三次风、预热后的生料及回转窑的高温废气,通过喷腾,实现气料成分混合,完成燃烧、分解。
分解炉排出的气料,在C5级内气料分离,物料入窑,废气经各级旋风筒,自下而上与生料悬浮换热降温,最后从C1级排出,窑尾高温风机将废气送入废气处理系统。
熟料在篦冷机内与鼓入的冷空气进行热交换,排出的高温热空气一部分作为二次风入窑供煤粉燃烧,另一部分作为三次风经三次风管入分解炉。
水泥熟料生产线熟料煅烧的基本知识
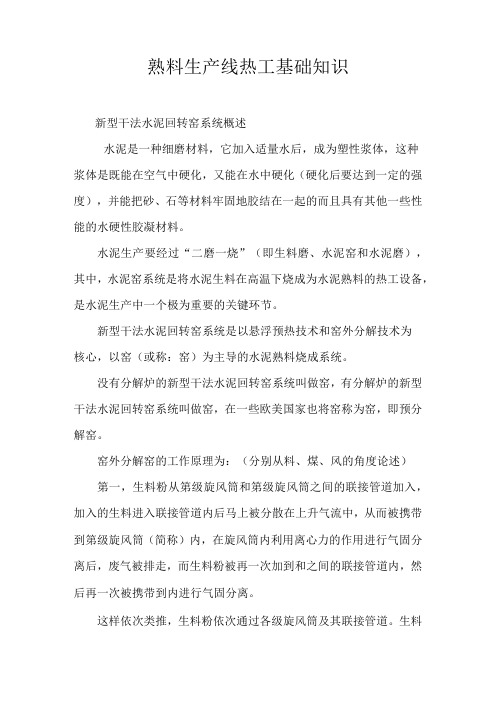
熟料生产线热工基础知识新型干法水泥回转窑系统概述水泥是一种细磨材料,它加入适量水后,成为塑性浆体,这种浆体是既能在空气中硬化,又能在水中硬化(硬化后要达到一定的强度),并能把砂、石等材料牢固地胶结在一起的而且具有其他一些性能的水硬性胶凝材料。
水泥生产要经过“二磨一烧”(即生料磨、水泥窑和水泥磨),其中,水泥窑系统是将水泥生料在高温下烧成为水泥熟料的热工设备,是水泥生产中一个极为重要的关键环节。
新型干法水泥回转窑系统是以悬浮预热技术和窑外分解技术为核心,以窑(或称:窑)为主导的水泥熟料烧成系统。
没有分解炉的新型干法水泥回转窑系统叫做窑,有分解炉的新型干法水泥回转窑系统叫做窑,在一些欧美国家也将窑称为窑,即预分解窑。
窑外分解窑的工作原理为:(分别从料、煤、风的角度论述)第一,生料粉从第级旋风筒和第级旋风筒之间的联接管道加入,加入的生料进入联接管道内后马上被分散在上升气流中,从而被携带到第级旋风筒(简称)内,在旋风筒内利用离心力的作用进行气固分离后,废气被排走,而生料粉被再一次加到和之间的联接管道内,然后再一次被携带到内进行气固分离。
这样依次类推,生料粉依次通过各级旋风筒及其联接管道。
生料粉每与上升的气流接触一次,就经过一次剧烈的热交换,从而生料粉被一次一次地预热升温,废气则被一次一次地冷却降温,从而达到回收废气余热来预热生料。
当生料达到一定温度,会发生一定程度的碳酸盐分解(小部分分解,因为废气的热焓不足以使其发生大量分解)。
出的预热生料进入分解炉,在分解炉内完成大部分碳酸钙的分解,分解反应所需热量来自于分解炉内的燃料燃烧。
分解后的生料与废气再一起进入内,经完成气固分离后,生料入回转窑内煅烧,再经过一系列物理化学反应后,最终烧成为水泥熟料。
出窑后熟料再经过冷却机冷却后被送到熟料库内。
熟料、石膏、混合材按一定比例在水泥磨内混合粉磨后就成为水泥。
第二,来自煤磨的煤粉被分成二部分,小部分煤粉(大约)被送到窑头喷入回转窑内燃烧,燃烧后产生的高温烟气供给回转窑内煅烧水泥熟料所用;大部分煤粉(大约)被气力输送到分解炉内燃烧,以供给预热生料中碳酸钙分解所需的大量热量。
2024年水泥熟料煅烧工(窑操)理论测试题附答案

2024年水泥熟料煅烧工(窑操)理论测试题附答案一.填空题(共10题,每题2分,共20分)1.(KH)是指熟料中全部氧化硅生成硅酸钙所需的氧化钙含量与全部氧化硅生成硅酸三钙所需氧化钙的比值。
2.预分解窑系统是由预热器、分解炉、回转窑、冷却机组成的系统,它主要承担水泥熟料形成过程中最主要的(预热、分解、烧成、冷却)等四个过程。
3.衡量燃烧器性能优劣的重要指标之一是(一次)空气量大小。
4.煤灰的掺入,一般会使熟料的饱和比(降低)、硅率(降低)。
5.原料主要有害成分包括碱、(氯)、(硫),应该限制其含量。
6.燃料燃烧时实际空气量与理论空气量之比值称为(过剩空气系数)。
7.回转窑内物料流量是通过改变回转窑(窑速)来控制的。
8.煤粉越细,燃烧速度越(快)。
9.旋风预热器截面风速范围(4.5~5.5)m/s。
10.旋风筒的主要作用是(气固分离),而不是传热。
二.判断题(共10题,每题2分,共20分,对的打√、错的打×) 1.生料中的液相量随温度升高而增加缓慢,其烧结范围就宽。
(√)2.入窑物料分解率不高,预烧不好,窑尾温度低,窑头煅烧困难,则需要加大头煤用量、提高煅烧能力。
(√)3.预分解窑投料愈少愈好控制。
(×)4.煤的工业分析组成有水分、挥发分、灰分、固定碳和硫五项,总量为100%。
(×)5.煤粉自喷嘴喷出至开始燃烧的这段距离称为黑火头。
黑火头拉长说明煤粉中的水分或灰分含量较低。
(×)6.回转窑运转一段时间后,其中心线不会有变动。
(×)7.分解炉内碳酸盐分解所需能量全部来自于喂入分解炉的燃料。
(×)8.预分解窑窑前温度低是因为窑头喂煤量少。
(×)9.挥发分高、灰分低的煤,其细度可以适当放粗。
(√)10.预分解窑的篦式冷却机工况的好坏对窑的煅烧影响不大。
(×)三.不定项选择题(共20题,每题2分,共40分)1.在采用五级预热器的预分解窑系统中,料粉流程是( C )。
烧成系统

1烧成系统是水泥厂生产的核心,它包含了烧成窑尾、烧成窑中、烧成窑头和熟料输送及储存。
本系统采用了高吸低阻5级旋风预热器带管道式在线分解炉系统;熟料冷却采用第三代控制流推动篦式冷却机,熟料烧成设计热耗不超过度小于正个系统的操作均由中央控制室集中操作控制。
由于本系统的工艺参数多,工况复杂且变化多端,因此要求中控操作员必须十分熟悉本系统的生产工艺操作,对操作终端上的显示信号、操作功能及方法均十分熟悉。
2烧成系统包括从生料喂入一级旋风筒进风管道开始,经预热、分解后入回转窑烧成水泥熟料,通过水平推动篦式冷却机的冷却、破碎并卸到链斗输送机输送入熟料库为止。
本系统可分为生料预热与分解、三次风管、熟料煅烧、熟料冷却破碎及熟料输送四大部分。
1)生料预热与分解(烧成窑尾)窑尾系统由五级旋风筒和链接旋风筒的气体管道、料管及分解炉构成,生料经计量后由空气输送斜槽、提升机送入二级旋风筒出口管道,在气流作用下立即分散、悬浮在气流中,并进入一级旋风筒。
经一级旋风筒气料分离后,料粉通过重锤翻板阀转到三级旋风筒出口管道,并随气流进入二级旋风筒。
这样经过四级热交换后,生料粉得到充分预热,随之入分解炉内与来自窑头罩的三次风及喂入的煤粉在喷腾状态下进行煅烧分解。
预分解的物料,随气流进入五级旋风筒,经过第五级旋风筒分离后喂入窑内;而废气沿着逐级旋风筒及其出口管道上升,最后由第一级旋风筒出风管道排出,经增湿塔由高温风机送往原料磨和废气处理系统。
为防止气流沿下料管反串而影响分离效率,在各级旋风筒下料管上均设有带重锤平衡的翻板阀。
正常生产中应检查各翻板阀动作是否灵活,必要时应调整重锤位置,控制翻板动作幅度小而频繁,以保证物料流畅、物料连续均匀,避免大幅度的脉冲下料。
预热器系统中,各级旋风筒依其所处的地位和作用侧重之不同,采用不同的高径比和内部结构型式。
一级旋风筒采用高柱长内筒型式以提高分离效率,减少废气带走飞灰量;各级旋风筒均采用大蜗壳式进口方式,减小旋风筒直径,使进入旋风筒气流通道逐渐变窄,有利于减少颗粒向桶壁移动的距离,增加气流通向出风口的距离,将内同缩短并加粗,以降低阻力损失,各级旋风筒间链接风管均采用方圆变换形式,增强局部涡流,使气料得打冲锋的混合与热交换。
烧成系统操作规程

烧成系统操作规程一操作目的本规程旨在达到树立安全第一的观点,统一操作思想,生产合格熟料,实现环保设备稳定达标排放,力求达到优质、稳定、高产、低耗的目的。
二范围本规程适用于烧成中控操作,即从窑尾排风机至熟料库顶。
三工艺设备简介及工艺流程1.设备简介2. 工艺流程简介1、生料入窑部分:均化库内生料分两路分别经手动闸板阀、气动开关阀及电动流量调节阀进入生料计量仓,计量仓中生料再经手动闸板阀、气动开关阀及电动流量调节阀,由固体流量计计量后经空气输送斜槽入胶带斗式提升机提至预热器顶,这时通过电动推杆闸阀控制来实现:a、生料循环回库,b、生料入预热器;计量仓、斜槽、斗提等处扬尘由袋式收尘器净化后排入大气。
2、预热器部分:生料在预热器进行热交换,在四级筒收集后入分解炉进行预分解,分解过的生料经五级旋风筒收集后入窑煅烧。
3、分解炉部分:出窑废气由轴向入炉,三次风由切向入炉,煤粉由两侧直接喷入的在线型分解炉。
4、回转窑部分:窑规格:4×60m,能力:2500t/d,斜度:4%,主传转速:0.4—4.0rpm,功率:315Kw,辅传转速:7.73rph,功率22 Kw。
5、篦冷机部分:型号:推动篦式冷却机,驱动采用二段链条传动方式,速度调节范围:11.11 次/分钟,篦床面积:71 m2,出料温度高出环境温度65℃;冷却后的熟料与窑头电收尘收集下来的粉料一起入输送机入库;冷却熟料的废气一部分作为二次风入窑,一部分作为三次风入炉,一部分作为煤粉制备系统的烘干热源,若余热发电项目运行后,将有一部分废气被余热发电系统所利用,剩余部分由窑头电收尘除尘净化后排入大气。
5、废气处理部分:出预热器的高温废气一部分作为原料粉磨系统的烘干热源被利用,一部分经增湿塔增湿降温后共同入窑尾袋收尘除尘净化后排入大气,若余热发电运行后还将被余热发电系统利用。
四. 开机前的准备工作1、确认系统是否处于备妥、开机准备状态。
2、确认各处的阀门动作是否灵活、准确、可靠,检查好阀门位置。
水泥烧成系统工艺简介
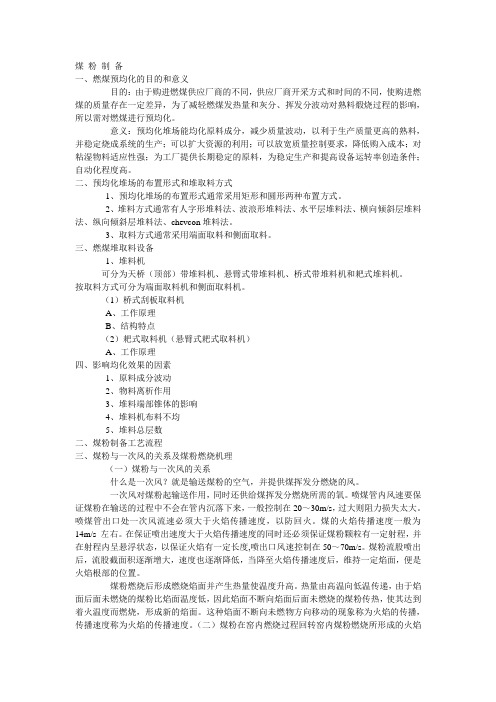
2、旋流分解室结构特点
3、混合室结构特点
三、回转窑
回转窑是水泥熟料煅烧的关键设备,它的功能主要表现在四个方面:①作为燃料燃烧装置(预分解窑中加入40%~50%的燃料),具有广阔的燃烧空间和热力场,保证燃料充分燃烧;②作为热交换装置,具有均匀的温度场,可满足熟料煅烧的要求;③作为化学反应器,满足熟料矿物形成对热量、温度及时间的不同要求;④作为输送设备,具有更大的潜力。
旋风筒工作原理:当气流携带料粉进入旋风筒后,被迫在旋风筒筒体与内筒(排气管)之间的环状空间内做旋转流动,并且一边旋转一边向下运动,由筒体到锥体,一直可以延伸到锥体的端部,然后转而向上旋转上升,由排气管排出。由于物料密度大于气体密度,受离心力作用,物料向边部移动的速度远大于气体,致使靠近边壁处浓度增大;同时,由于粘滞阻力作用,边壁处流体速度降低,使得悬浮阻力大大减小,物料沉降而与气体分离。旋风筒内向下旋转运动的流体称为外涡旋,向上旋转运动的流体称为内涡旋。
随着过滤的进行滤袋外侧的积尘逐渐增多使收尘器的运行阻力也逐渐增高当阻力达到预先设定值12451470pa时清灰控制器发出信号首先控制提升阀将阀板孔关闭以切断过滤烟气流停止过滤过程然后电磁脉冲阀打开以极短的时间01015s向箱体内喷入压力为0507mpa的空气脉冲空气快速向下进入滤袋同时产生一股使室内所有滤袋褶曲的冲击波使滤袋产生变形震动加上逆气流的作用滤袋外部的粉尘被清除下来掉入灰斗收集下来的粉尘通过排灰阀卸出
工作原理:输送机由传动装置、头部罩壳、头部装置、运行部份、尾部装置和进料装置等部份组成。由传动装置驱动头部装置中的链轮,牵引装有物料的输送斗沿轨道运行,物料从头部罩壳卸出,从而达到输送物料的目的。
煤粉制备
一、燃煤预均化的目的和意义
- 1、下载文档前请自行甄别文档内容的完整性,平台不提供额外的编辑、内容补充、找答案等附加服务。
- 2、"仅部分预览"的文档,不可在线预览部分如存在完整性等问题,可反馈申请退款(可完整预览的文档不适用该条件!)。
- 3、如文档侵犯您的权益,请联系客服反馈,我们会尽快为您处理(人工客服工作时间:9:00-18:30)。
精准平衡操作技术简介(水泥熟料烧成操作专利新技术)淄博科邦热工科技有限公司2013前言窑外分解技术在中国出现已经四十多年了。
技术已经很成熟。
以至于如果有人说这个系统还可以进行优化时都很少有人相信。
然而自从窑外分解技术进入到中国以来,至今没有提出一套完整的标准的烧成系统操作的方法。
只有大家在生产实践中基本形成了一定的共识的操作原则:薄料快烧;喷煤管火焰活泼有力,定位在中心线以下;三次风管的阀门开度在35—50%;窑头罩压力控制在-50—0pa;窑皮长度约5D。
按照任何技术都是在发展的观点,虽然窑外分解的基本理论是成熟的,大家也都在按照一些原则进行着操作。
但是日新月异的应用技术的发展,使这种操作技术难一适应。
淄博科邦公司在这些年的生产实践中,在不断为水泥厂解决生产难题的过程中,探讨出了一些新的操作方法。
并组合起来系统的使用,取得了不同于原来操作方法的效果。
在知识产权专家的建议下,这项技术申请了发明专利:《水泥熟料烧成系统控制方法》细细分析起来,这项操作技术的产生应该追溯到1995年我们开始从事中小型旋窑改造的时候。
那时候因为生产线的能力都不大,700t/d的就是大生产线了。
当时很多生产线的熟料冷却都是采用的单筒冷却机。
在生产时,窑头罩都是正压或是微正压。
完全负压的很少。
有些工厂窑头正压到看火都需要拿着像盾牌一样大的看火镜。
当时大家都不明白产生正压的原因,有些工厂甚至将高温风机的风量加大了一倍,祈望将窑头拉成负压,但是没有作用,反而使生产更不稳定了。
当时就有一些文章探讨单筒冷却机的规格和回转窑规格的匹配问题,希望通过匹配来解决窑头正压问题。
也有一些工厂,对窑头罩进行了改造,特别是窑头冷烟室的尺寸。
改造后确实有些效果,但随之带来的是产量和其他方面的影响。
我们在开始从事旋窑改造以后,也研究了这种现象,并在一些在水泥厂工作的专家的启发下,利用组合技术实现了窑头罩的负压工况,同时使旋窑的产量大幅度提高。
在这种情况下逐渐认识了系统空气平衡和烟气平衡的重要性以及其中的一些特殊关系。
真正达到高峰的是利用这方面的技术解决了当时被称为水泥行业老大难问题的河北宣化水泥厂(今张家口金隅)700t/d生产线的达标问题。
在以系统空气平衡为主要指导思想的基础上,没有对系统进行大的改动,只改了一些在他人看来无足轻重的若干细节部位,就使这个建厂10年没有达标的生产线,远远得超过了设计产量而达到了800t/d。
时至今日,科邦公司已经完成了关于分解炉和篦冷机的优化操作的研究,完成了烧煤燃烧器的合理使用的研究,同时完成了在5000t/d以下规模多条生产线应用这项操作技术的工作。
并取得了显著效果。
俗话说,三分技术七分操作(不一定这样区分)。
一个技术设计好的烧成系统,设计者如果不能同时设计出相对应的合理的操作方法,那它就不会充分发挥出设计者期望的性能。
所以科邦公司在推出系统优化技术的同时也推出了这项操作技术(专利)。
希望它与淄博科邦公司推出的其他技术一起,为水泥熟料生产线再次降低热耗,减少有害气体的排放的技术进步做出一些贡献。
以下就是这项专利技术的介绍。
技术简介水泥熟料烧成系统的操作,是直接关系到水泥质量和成本的重要工作。
因此,掌握先进的、正确合理的、精准的、高水平的操作技术是水泥厂中控工作的最重要的任务。
新型干法水泥生产技术的核心是悬浮预热和窑外分解技术。
因此,采用窑外分解技术的烧成系统,首先需要保证窑尾预热器系统特别是分解炉的正常、稳定、高效的工作。
并使其最大限度的发挥预热预分解作用。
而目前正在运行的新型干法熟料烧成生产线,多年以来一直都延续一种基本相同得原则和方法来操作。
这种方法在运行中的表现特点为:三次风管的阀门开度控制在30---50%,以加强窑内通风;喷煤管的火焰调整为活泼有力,把喷煤管定位在第四象限,加强火焰对熟料的直接热交换作用;把窑头罩压力控制在-50----0pa;窑转速达到最高转,实现薄料快烧。
随着新型干法生产技术的进步和社会环境对节能减排和减少氮氧化物等有害气体排放要求的不断提高。
这种旧有的操作方法已经逐渐感到难以适应这些要求。
例如:控制窑内的煤粉在低过剩空气系数的工况下燃烧(α≦1.05),可以减少氮氧化物的生成量,减少系统脱硝的成本,就是一个突出的例子;很多窑如果这样操作,就会出现熟料呈现还原气氛的现象,严重影响熟料质量。
还有,将喷煤管定位在中心以上位置,使火焰的中心落点移动到窑尾,可以使生料入窑后快速通过过渡带,进入烧成带,这样生料升温速度快,CaO的吸收速度也越快,越有利于C3S的形成。
短粗窑的原理就是根据此理论形成的。
并确实实现了降低热耗的好作用。
这种定位同时可以减少煤灰落入熟料的机率,提高熟料的质量。
是将来降低热耗和运行成本的一种的操作方法。
而目前的操作方法都较难做到这一点。
精准平衡操作技术是建立在淄博科邦公司对烧成系统优化理论的基础上。
其中科邦公司创始人郭红军先生《关于分解炉的优化和操作》;《篦冷机的优化和操作》;《烧煤燃烧器的合理使用》等系列讲座中的理论解释和对烧成系统的全面认识和分析,为这种操作方法奠定了基础。
同时指导着这种种操作技术的合理应用。
“精准平衡操作技术”的核心是:以理论计算、数据分析为依据;以系统空气平衡为前提(包括窑的烟气平衡);以保证分解炉用风(三次风)和烧成带恒温煅烧为重点;以窑头罩的温度、压力两个数据为主要控制参数;通过合理调整窑头喷煤管的四个风速和风量的匹配、合理篦冷机的操作,最终实现熟料烧成的高质、高产、低消耗、低排放的目标。
这项操作技术在系统运行参数中的表现特点为:1三次风管的阀门开度在85--100%;2喷煤管定位在窑口中心线以上(0,10--50);3根据窑头罩的容积合理控制窑头罩压力。
1以理论计算、数据分析为依据,以系统空气平衡为前提(包括窑的烟气平衡)采用这项技术进行操作之前,首先要进行系统分析计算。
弄清楚系统中各部位的空气来源和数量。
弄清楚排出多余空气的数量和能力以及排出烟气的能力。
清楚篦冷机内零压点的位置和对应的风机数量。
制作简单的平衡图(见下)。
然后进行分析。
1.1悬浮预热预分解系统的分解炉有三十几种。
这些分解炉由于结构不同、规格不同或是结构相同参数不同,以及配套的喷煤管不同,其性能是不一样的。
而且运行中需要的空气量也不一样。
以5000t/d的D-D炉窑尾系统为例:这种炉型其过剩空气系数需要1.15。
在产量达到5700吨时,分解炉的用风量为132941m3/h。
进入分解炉时的工况风量为603576m3/h。
按照此平衡数据计算,窑内的烟气量为526683m3/h(工况),窑尾烟室缩口的实际风速为32--33m/s;如果在操作中将三次风管的阀门关到很小,窑内的实际通风就更大了,所以缩口的风速就会更高。
这时如果窑尾烟室缩口的直径是一样的话,分解炉内的气体流场就会因为三次风风速和风量脱离设计时的工况,使分解炉不能按照设计参数来发挥作用,使系统的能力受到了限制。
1.2系统中采用的篦冷机在冷却风机的配套风量上也不一样;一般第三代篦冷机的冷却风量大约是2.3nm3/kgcl。
而第四代篦冷机的冷却风量仅有1.5-1.8nm3/kgcl。
这样余风抽取口和煤磨抽风口的位置设置就应该不一样。
烧成系统用风量和余风排风量的分界线(也即人们常说的篦冷机的“零压点”)就不一样了。
如果“零压点”内设置了取风口,那么在操作时就很难保证系统运行时的燃烧空气量。
即使“零压点”在抽取口之内,如果冷却风机的实际供风量(阀门开度或者转速)不能达到设计要求,则“零压点”就会向后移动到取风口的位置。
而这时仍然不容易保证系统用风。
或者是以高的用煤量来保证系统运行。
仍以5000t/d的烧成系统为例:在产量达到5700吨时,热耗105kgce/tcl时,需要用的空气量为219888m3/h。
一般情况下,篦冷机的一段篦床配套风机有六台,其总风量基本正好满足。
但是在实际运行中,很多风机的进风口阀门开度只有70-90%,或者是变频器的频率调整在45Hz以下,这样一来,一段的供风量就不能满足燃烧用空气的要求了。
在这种情况下,如果再继续提高产量,将会造成用煤量大幅增加的现象(有很多工厂的实际情况已经验证了这一点),使熟料的热耗急剧增加。
形成产量越高,热耗越高的现象。
而且还会因为煤粉不能充分燃烧,容易造成质量不稳定的状况。
所以,操作时就需要考虑如何用二段的风机来提供风量的问题;或者是提高喷煤管的供风量来保证空气量。
但这样做在实际操作时一般的操作人员很难做到。
1.3对于小窑头罩结构的系统来说,由于其窑内用风和分解炉用风是分别从篦冷机的不同位置引风的。
这样就需要多考虑一种因素:如果窑头罩的尺寸范围内的冷却风机供风量不能满足窑内煤粉燃烧的需要,就需要调整三次风管的取风口的位置,或是调整三次风取风口的尺寸。
再或是关小三次风管阀门,控制三次风管在此范围内的抽风量。
这样一来,系统地整体阻力就会增加,高温风机的实际风量就会减少,电机的电流就会增大了;所以,一个设计合理的烧成系统除了预热器、分解炉设计合理之外,还需要窑头罩结构、篦冷机的冷却风机、余风排放口的位置、三次风管直径、送煤管道规格及布置等等细节设计合理。
才能保证系统中各部件的能力充分匹配,才能使操作人员在采用合理的操作方法时,使系统发挥出全部能力。
以理论计算、数据分析为依据,以系统空气平衡为前提(包括窑的烟气平衡)来进行操作,就是让操作者在进行操作之前,就做到心中有数。
可以使系统快速准确的进入到最佳状态。
2以保证分解炉用风(三次风)和烧成带恒温煅烧为重点;新型干法水泥生产技术的核心是悬浮预热和窑外分解技术。
因此,采用窑外分解技术的烧成系统,首先需要保证窑尾预热器系统特别是分解炉的正常稳定工作。
并使其最大限度的发挥作用。
任何一个分解炉都是通过模拟试验和工业试验得出其性能地。
同时在实际应用到生产线中去的时候,都利用放大系数进行了修正。
即使这样,实际应用中也会因为种种原因而与试验数据有些差别。
三次风大多数都是由窑头罩的上方抽取,也有从篦冷机的壳体上抽取的。
当高温的二次风经过窑头罩下部的烟室去往窑内和分解炉的时候,回转窑内的气体流速因为喷煤管的高速射流的作用,其阻力要小于三次风管(窑皮过厚和结构不合理除外)。
因此窑内的通风比较容易保证。
而分解炉就要难一些。
所以为了保证预分解系统的作用,首先要保证分解炉的用风,这样,三次风管的阀门就应该尽可能的打开。
但是,一般的烧成系统,如果打开的幅度超过50--60%,都会出现感觉窑内通风不足的现象。
所以,在操作中就需要有另外的操作来进行相应的配合。
以实现这种首先保证分解炉性能的操作方法。
这样操作的结果与以往相比,增加了分解炉的用风量,保证了分解炉内实际流场更加接近设计的流场,保证并提高了分解炉的性能。