生产运作管理指导书
BZ-QP-13生产运作管理程序-A1
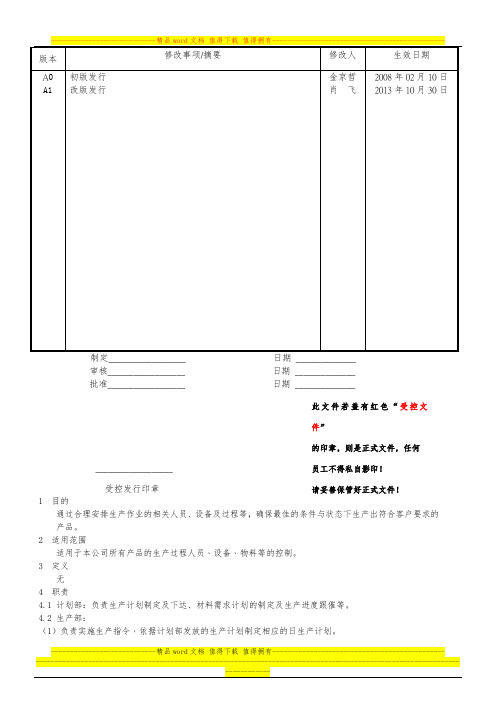
审核__________________ 日期______________批准__________________ 日期______________此文件若盖有红色“受控文件”的印章,则是正式文件,任何__________________ 员工不得私自影印!受控发行印章请妥善保管好正式文件!1 目的通过合理安排生产作业的相关人员、设备及过程等,确保最佳的条件与状态下生产出符合客户要求的产品。
2 适用范围适用于本公司所有产品的生产过程人员﹑设备﹑物料等的控制。
3 定义无4 职责4.1 计划部:负责生产计划制定及下达、材料需求计划的制定及生产进度跟催等。
4.2 生产部:(1)负责实施生产指令﹐依据计划部发放的生产计划制定相应的日生产计划。
(2)负责生产过程中所需人员、物料、设备等需求的评估和准备。
(3)负责生产现场的合理管理,确保生产的正常、有序的开展。
(4)负责执行首件检查、自主检查。
4.3 品管部:负责材料﹑半成品、成品的过程检验﹑巡回检查以及产品功能检查的品质控制。
4.4 工程部:负责生产过程条件设定的指导、现场生产实施工艺条件的确认、跟踪;监督生产成品可靠度试验的实施及产品不良品的分析,并拟定对策监督实施。
5 流程及作业5.1 流程图见4页5.2 作业说明5.2.1前期准备5.2.1.1计划部接到市场部的业务订单,制作《生产通知单》,然后将《生产通知单》交各个部门审核,经总经理批准以后,转化成《生产计划单》,生产部按照计划部下达的《生产计划单》后进行生产计划安排;5.2.1.2各生产车间根据生产计划,工程部提供各工艺文件要求,确认生产所需的工装夹具、人员、场地是否可满足生产需要。
5.2.1.3确认作业员工对相关的工艺条件及使用的设备操作已接受培训,并具备相应的工作能力。
5.2.1.4 确保生产所需的设备处于完好状态,生产设备的控制详见《生产设备管理程序》5.2.2 过程控制5.2.2.1 领料生产线依据日计划安排人员领取物料,若按计划领料后,发现生产过程欠料情况,该线及时上报部门负责人,部门负责人安排人员进行物料的跟进。
教学大纲
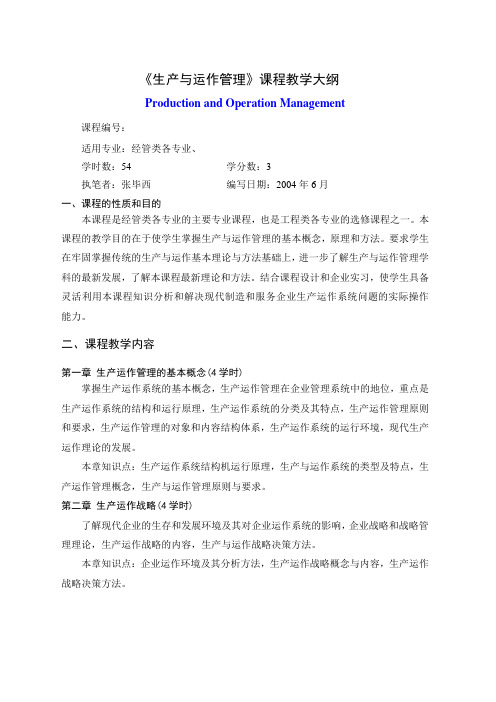
《生产与运作管理》课程教学大纲Production and Operation Management课程编号:适用专业:经管类各专业、学时数:54 学分数:3执笔者:张毕西编写日期:2004年6月一、课程的性质和目的本课程是经管类各专业的主要专业课程,也是工程类各专业的选修课程之一。
本课程的教学目的在于使学生掌握生产与运作管理的基本概念,原理和方法。
要求学生在牢固掌握传统的生产与运作基本理论与方法基础上,进一步了解生产与运作管理学科的最新发展,了解本课程最新理论和方法。
结合课程设计和企业实习,使学生具备灵活利用本课程知识分析和解决现代制造和服务企业生产运作系统问题的实际操作能力。
二、课程教学内容第一章生产运作管理的基本概念(4学时)掌握生产运作系统的基本概念,生产运作管理在企业管理系统中的地位,重点是生产运作系统的结构和运行原理,生产运作系统的分类及其特点,生产运作管理原则和要求,生产运作管理的对象和内容结构体系,生产运作系统的运行环境,现代生产运作理论的发展。
本章知识点:生产运作系统结构机运行原理,生产与运作系统的类型及特点,生产运作管理概念,生产与运作管理原则与要求。
第二章生产运作战略(4学时)了解现代企业的生存和发展环境及其对企业运作系统的影响,企业战略和战略管理理论,生产运作战略的内容,生产与运作战略决策方法。
本章知识点:企业运作环境及其分析方法,生产运作战略概念与内容,生产运作战略决策方法。
第三章生产运作系统设计(4学时)了解和掌握生产运作系统涉及的内容和要求,产品开发与企业R&D管理理论和方法,生产流程设计与选择,并行工程在产品开发组织中的应用,计算机技术在产品研发中的运用与管理,生产类型、设施和模式的选择。
本章知识点:生产系统构建的内容和要求,产品和技术研发内容及其在生产运作系统中的地位,现代先进组织和运作理论在产品技术研发中的应用。
生产运作系统构建决策理论和方法。
第四章生产运作过程组织(4)本章要求掌握生产运作过程的结构,生产运作过程分类及其特点,合理组织生产过程的要求,生产运作过程的时间结构及生产周期,生产运作过程三种移动方式及其周期计算方法,生产运作过程排序原理与方法。
-Unlicensed-《生产与运作管理》自学指导书
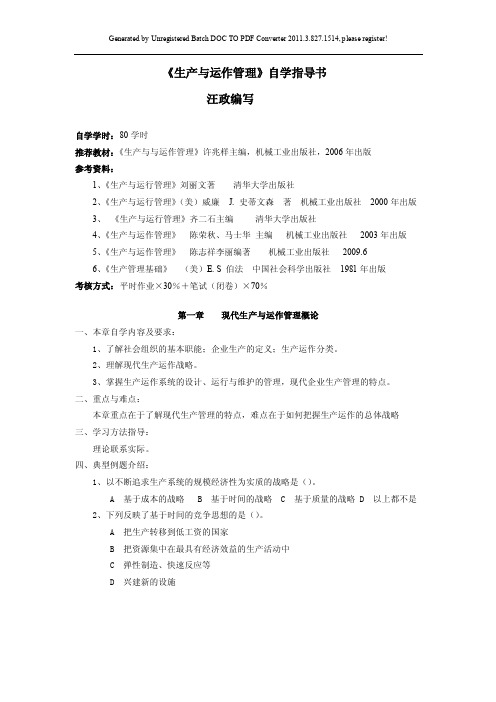
Generated by Unregistered Batch DOC TO PDF Converter 2011.3.827.1514, please register!
B. 依据事先确定的目标和标准进行评价 C. 从节省人力的角度进行评价 D. 从节省设备、工具以及材料的角度进行评价 3、工作设计,它是根据组织需要并兼顾个人需要,规定某个工作岗位的任务、责任、权利 以及在组织中与其他工作岗位关系的过程。 工作设计的结果通常也体现在工作说明书上。 从 企业的整个生产经营过程来看,工作设计应当满足:企业劳动分工与协作的需要;企业不断 提高生产效率、增加产出的需要;劳动者在健康、安全、舒适的条件下从事劳动过程中生理 心理的需要。 工作设计的内容主要包括:⑴ 明确生产任务的作业过程;⑵ 通过分工确定工作内容; ⑶ 明确每个操作者的工作责任;⑷ 以组织形式规定分工后的协调,保证任务的完成。
D 、宽裕时间最多的路线
)
B. 单一时间估计法 D. 平均估计法
A、活动数量最多的路线
C、时间最长的路线
3、以下哪一条是项目的特点?( A A、一次性
) E、风险小
B、重复 C、产出是标准的 D、重复性工作多
Generated by Unregistered Batch DOC TO PDF Converter 2011.3.827.1514, please register!
0 10 10 产品 X 的物料清单(BOM)如下:
B(2)
C
D(3)
E(2) F(3) G(2) E(2) H(4) E(2) ⑴ 如果组装 20 个 X,则还需要 E 多少个? ⑵ 根据进度安排,第 11 周开始时有一份发送 X 的订单。该订单最迟应该什么时候开 始才能按时发货?(无须做 MRP 计划)
制造业生产流程管理作业指导书
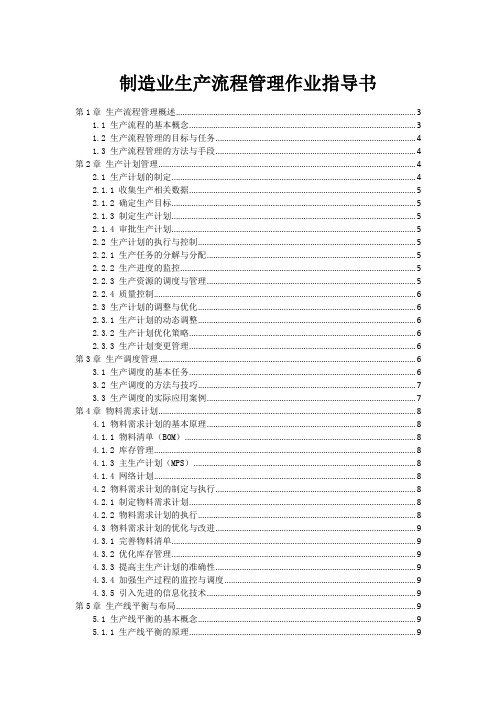
制造业生产流程管理作业指导书第1章生产流程管理概述 (3)1.1 生产流程的基本概念 (3)1.2 生产流程管理的目标与任务 (4)1.3 生产流程管理的方法与手段 (4)第2章生产计划管理 (4)2.1 生产计划的制定 (4)2.1.1 收集生产相关数据 (5)2.1.2 确定生产目标 (5)2.1.3 制定生产计划 (5)2.1.4 审批生产计划 (5)2.2 生产计划的执行与控制 (5)2.2.1 生产任务的分解与分配 (5)2.2.2 生产进度的监控 (5)2.2.3 生产资源的调度与管理 (5)2.2.4 质量控制 (6)2.3 生产计划的调整与优化 (6)2.3.1 生产计划的动态调整 (6)2.3.2 生产计划优化策略 (6)2.3.3 生产计划变更管理 (6)第3章生产调度管理 (6)3.1 生产调度的基本任务 (6)3.2 生产调度的方法与技巧 (7)3.3 生产调度的实际应用案例 (7)第4章物料需求计划 (8)4.1 物料需求计划的基本原理 (8)4.1.1 物料清单(BOM) (8)4.1.2 库存管理 (8)4.1.3 主生产计划(MPS) (8)4.1.4 网络计划 (8)4.2 物料需求计划的制定与执行 (8)4.2.1 制定物料需求计划 (8)4.2.2 物料需求计划的执行 (8)4.3 物料需求计划的优化与改进 (9)4.3.1 完善物料清单 (9)4.3.2 优化库存管理 (9)4.3.3 提高主生产计划的准确性 (9)4.3.4 加强生产过程的监控与调度 (9)4.3.5 引入先进的信息化技术 (9)第5章生产线平衡与布局 (9)5.1 生产线平衡的基本概念 (9)5.1.1 生产线平衡的原理 (9)5.2 生产线平衡的方法与技巧 (10)5.2.1 生产线平衡方法 (10)5.2.2 生产线平衡技巧 (10)5.3 生产线布局的设计与优化 (10)5.3.1 生产线布局设计原则 (10)5.3.2 生产线布局优化方法 (11)5.3.3 生产线布局优化技巧 (11)第6章质量管理 (11)6.1 质量管理的基本原则与方法 (11)6.1.1 质量管理原则 (11)6.1.2 质量管理方法 (11)6.2 质量控制工具与技术 (11)6.2.1 质量控制工具 (11)6.2.2 质量控制技术 (12)6.3 质量改进案例与实践 (12)6.3.1 案例一:降低某产品的不良率 (12)6.3.2 案例二:缩短某产品生产周期 (12)6.3.3 案例三:提高供应商质量水平 (12)第7章设备管理与维护 (12)7.1 设备管理的基本任务与策略 (12)7.1.1 设备管理的基本任务 (12)7.1.2 设备管理的策略 (13)7.2 设备维护的方法与技巧 (13)7.2.1 设备维护的方法 (13)7.2.2 设备维护的技巧 (13)7.3 设备管理在实际生产中的应用 (13)7.3.1 设备选型与配置 (13)7.3.2 设备运行监控 (13)7.3.3 设备维护与保养 (13)7.3.4 设备更新与改造 (14)7.3.5 设备安全管理 (14)7.3.6 设备信息管理 (14)第8章人力资源管理 (14)8.1 生产现场人员配置与管理 (14)8.1.1 人员配置原则 (14)8.1.2 岗位职责明确 (14)8.1.3 人员招聘与选拔 (14)8.1.4 人员培训与调配 (14)8.1.5 绩效考核与激励 (14)8.2 员工培训与技能提升 (14)8.2.1 培训需求分析 (14)8.2.2 培训计划制定 (15)8.2.3 培训实施与评估 (15)8.3 生产团队建设与激励 (15)8.3.1 团队建设 (15)8.3.2 沟通与协作 (15)8.3.3 激励机制 (15)8.3.4 企业文化建设 (15)8.3.5 员工关怀 (15)第9章环境与安全管理 (15)9.1 生产现场环境管理 (15)9.1.1 环境管理原则 (15)9.1.2 环境管理措施 (15)9.2 安全生产管理的基本要求 (16)9.2.1 安全生产责任制 (16)9.2.2 安全生产规章制度 (16)9.2.3 安全生产培训与教育 (16)9.2.4 安全生产投入 (16)9.2.5 安全生产检查与隐患整改 (16)9.3 环境与安全管理的实际应用 (16)9.3.1 环境管理实际应用 (16)9.3.2 安全管理实际应用 (16)第10章生产流程优化与持续改进 (17)10.1 生产流程优化的方法与手段 (17)10.1.1 流程分析与评估 (17)10.1.2 流程建模与仿真 (17)10.1.3 优化方法选择与应用 (17)10.1.4 优化方案实施与监控 (17)10.2 持续改进的体系建设与实践 (17)10.2.1 持续改进理念普及与推广 (17)10.2.2 持续改进组织架构与职责 (17)10.2.3 持续改进机制与流程 (17)10.2.4 持续改进工具与方法 (17)10.3 生产流程优化与持续改进案例分享 (17)第1章生产流程管理概述1.1 生产流程的基本概念生产流程是指将原材料、零部件、能源等通过一系列有序的加工、组装、检测等工序,转化为成品的全过程。
工业生产与运作管理作业指导书
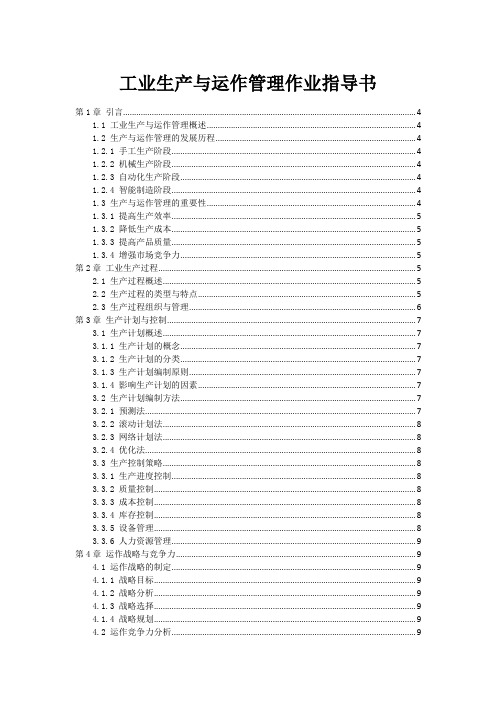
工业生产与运作管理作业指导书第1章引言 (4)1.1 工业生产与运作管理概述 (4)1.2 生产与运作管理的发展历程 (4)1.2.1 手工生产阶段 (4)1.2.2 机械生产阶段 (4)1.2.3 自动化生产阶段 (4)1.2.4 智能制造阶段 (4)1.3 生产与运作管理的重要性 (4)1.3.1 提高生产效率 (5)1.3.2 降低生产成本 (5)1.3.3 提高产品质量 (5)1.3.4 增强市场竞争力 (5)第2章工业生产过程 (5)2.1 生产过程概述 (5)2.2 生产过程的类型与特点 (5)2.3 生产过程组织与管理 (6)第3章生产计划与控制 (7)3.1 生产计划概述 (7)3.1.1 生产计划的概念 (7)3.1.2 生产计划的分类 (7)3.1.3 生产计划编制原则 (7)3.1.4 影响生产计划的因素 (7)3.2 生产计划编制方法 (7)3.2.1 预测法 (7)3.2.2 滚动计划法 (8)3.2.3 网络计划法 (8)3.2.4 优化法 (8)3.3 生产控制策略 (8)3.3.1 生产进度控制 (8)3.3.2 质量控制 (8)3.3.3 成本控制 (8)3.3.4 库存控制 (8)3.3.5 设备管理 (8)3.3.6 人力资源管理 (9)第4章运作战略与竞争力 (9)4.1 运作战略的制定 (9)4.1.1 战略目标 (9)4.1.2 战略分析 (9)4.1.3 战略选择 (9)4.1.4 战略规划 (9)4.2 运作竞争力分析 (9)4.2.2 竞争力分析 (10)4.3 运作战略实施与评估 (10)4.3.1 战略实施 (10)4.3.2 战略评估 (10)第5章设备管理 (10)5.1 设备管理概述 (10)5.2 设备的选择与评价 (10)5.2.1 设备选择原则 (10)5.2.2 设备评价方法 (11)5.3 设备维护与维修 (11)5.3.1 设备维护 (11)5.3.2 设备维修 (11)第6章供应链管理 (12)6.1 供应链概述 (12)6.1.1 供应链的定义 (12)6.1.2 供应链的构成 (12)6.1.3 供应链管理的意义 (12)6.2 供应链管理策略 (12)6.2.1 采购管理 (12)6.2.2 生产管理 (12)6.2.3 库存管理 (12)6.2.4 物流管理 (12)6.2.5 信息管理 (12)6.3 供应链协同与优化 (12)6.3.1 供应链协同 (13)6.3.2 供应链优化 (13)第7章质量管理 (13)7.1 质量管理概述 (13)7.1.1 质量管理的基本概念 (13)7.1.2 质量管理原则 (13)7.1.3 质量管理的目标 (13)7.2 质量管理体系与工具 (13)7.2.1 质量管理体系的基本构成 (13)7.2.2 质量管理工具 (14)7.3 质量改进方法 (14)7.3.1 持续改进 (14)7.3.2 PDCA循环 (14)7.3.3 六西格玛 (14)7.3.4 Kaizen (14)第8章生产现场管理 (14)8.1 现场管理概述 (14)8.1.1 现场管理的目标 (14)8.1.2 现场管理的主要内容 (15)8.2.1 5S管理 (15)8.2.2 精益生产 (15)8.2.3 六西格玛管理 (15)8.3 现场安全管理 (15)8.3.1 安全制度与法规 (15)8.3.2 安全教育与培训 (15)8.3.3 安全检查与整改 (15)8.3.4 应急预案与救援 (15)第9章人际关系与团队协作 (16)9.1 人际关系与沟通 (16)9.1.1 人际关系的重要性 (16)9.1.2 沟通技巧 (16)9.1.3 人际沟通的障碍与应对策略 (16)9.2 团队建设与管理 (16)9.2.1 团队概述 (16)9.2.2 团队建设 (16)9.2.3 团队管理 (16)9.3 团队协作与冲突管理 (17)9.3.1 团队协作的重要性 (17)9.3.2 团队协作技巧 (17)9.3.3 冲突的类型与原因 (17)9.3.4 冲突管理策略 (17)第10章工业生产与运作管理案例分析 (17)10.1 案例分析方法 (17)10.1.1 文献分析法:通过查阅相关文献资料,了解案例背景、企业战略以及生产与运作管理方面的相关信息。
生产运行管理制度(优秀3篇)

生产运行管理制度(优秀3篇)在当今社会生活中,很多场合都离不了制度,制度泛指以规则或运作模式,规范个体行动的一种社会结构。
这些规则蕴含着社会的价值,其运行表彰着一个社会的秩序。
那么制度的格式,你掌握了吗?读书是学习,摘抄是整理,写作是创造,以下是美丽的小编帮助大家找到的生产运行管理制度(优秀3篇),希望对大家有所启发。
生产运行管理制度篇一一、为加强生产成本的控制,不断提高生产效益,特制定本制度。
二、本制度适用范围为涉及生产管理控制的部门。
三、权责分工1、财务部负责对全公司生产成本的预算及统筹核算工作。
2、生产部。
(1)负责对生产原材料及生产产品数量的统筹规划。
(2)负责生产部门的节能管理工作。
(3)负责提交设备检修费用及设备更换费用。
(4)负责统计报送有关经济技术指标,包括《生产月报表》、《生产计划》等。
3、仓储部。
(1)负责各种消耗材料的采购及统计工作。
(2)负责对产品原材料及产品库存情况的统计工作。
4、生产车间。
(1)负责对生产现场的'节能降耗工作。
(2)负责统计生产直接成本。
四、生产成本管理的要求。
1、各职能部门须将生产成本控制工作作为一个长期的工作任务,坚持不懈的开展生产成本管理工作。
2、涉及生产成本管理的各项数据须真实准确,任何部门不得瞒报假报。
3、生产管理工作须贯彻到实际生产工作中,并形成全员参与的局面。
五、生产成本的控制。
1、各部门须制定生产成本控制办法及相关的奖罚标准。
2、各部门须建立健全成本管理体系。
3、各部门须将生产成本控制任务分解到各班组及相关人员,并明确权限及职责。
4、生产车间须将节能降耗工作作为生产成本控制的重点工作来抓。
5、对影响生产成本的工艺环节,生产部及生产车间须及时组织技改攻关。
6、对涉及到生产成本控制的各项费用,各部门须得到公司领导签字审批。
7、在生产过程中,各生产车间须对成本形成的各个环节、成本管理的执行情况、影响成本管理的各种因素坚持检查、监督。
生产运行管理制度篇二一、目的为规范工艺管理,保证生产工艺的正常运作,不断提高工艺布局的合理性,特制定本制度。
生产运作管理课程设计任务书
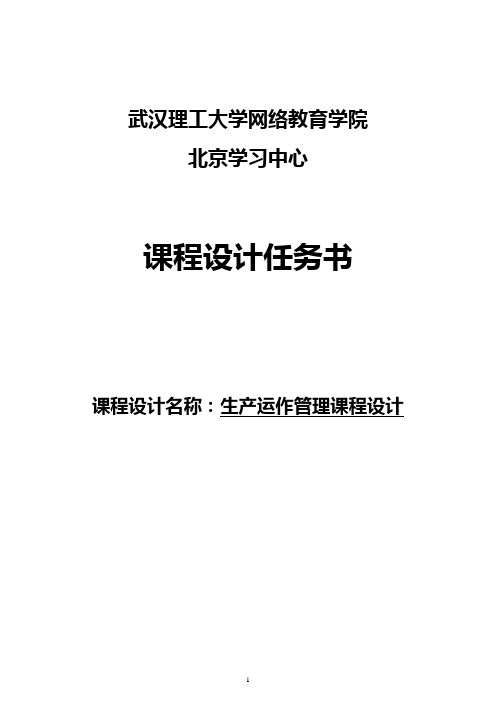
武汉理工大学网络教育学院北京学习中心课程设计任务书课程设计名称:生产运作管理课程设计《生产运作管理》课程设计任务书及指导书一、课程设计的目的《生产运作管理》课程设计是安排在该课程的理论教学之后进行的,是该课程教学活动的一个重要环节。
在完成《生产与运作管理》理论教学基础上,对学生进行一次全面的实际操作性锻炼。
其目的在于为学生提供一次能较为系统地综合运用生产运作管理理论与方法,以及运用电子计算机技术,解决在某种给定的生产条件下企业生产活动实际问题的模拟,通过本环节的设计锻炼,对设计对象的情况、问题和材料有较好的了解,能灵活应用本课程理论知识和方法,分析和解决问题。
二、课程设计总体要求及时间安排(一)总体要求1、每位同学均须完成一个专题的设计,可以选择老师提供的专题,也可以根据自身工作环境,自己拟定专题。
若运用计算机辅助设计(指运用数据库运算或计算机语言编程),均可依其掌握程度给予加分。
2、课程设计报告书内容包括:设计课题名称、命题条件、要求、设计步骤和程序、所采用理论方法的基本原理和运算过程、结果表述、设计心得及存在问题分析。
3、认真编写课程设计报告书,做到数据计算准确、图表清晰完整、文字表达简明扼要,并打印、装订成册。
指导教师电子邮件:******************,4、邮件要写清楚学员的姓名,课题的名称等内容,并以附件的形式发到老师的电子邮箱。
5、课程设计的封面、任务书、指导书在学校网络课堂下面的课程设计中,请学生自己下载。
提交时先交电子版,不要直接提交书面材料。
(二)时间安排8月5日前交课程设计纲要;8月15日以电子邮件形式交初稿,然后修改;8月25日交第二稿,再次修改;8月29日前打印、装订成册,并交到高教部。
(截止收邮件日期为8月28日)9月4日教师到高教部取学员上交材料评阅9月18日教师上交学员成绩三、课程设计的内容根据老师给定的材料,在下面的专题中任选其中一个专题完成设计。
[资料1]液压泵产品品种、结构与零件明细1、产品品种A—1,A—2,A—3;B—1,B—2;C—1,C—2,C—3。
《生产运作计划》课件
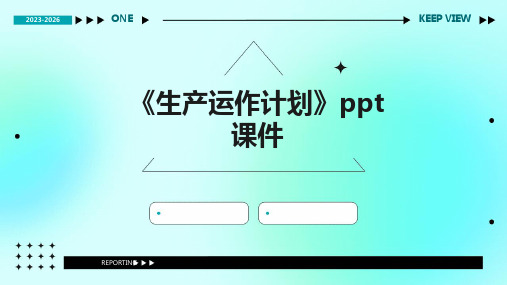
物料需求计划的优化方法
减少库存
通过精确的需求预测和计划,降低库 存水平,减少库存成本。
提高计划灵活性
考虑多种产品和物料的需求,提高计 划对市场变化的适应性。
协同供应链
与供应商和生产部门建立紧密的合作 关系,协同制定物料需求计划,提高 整个供应链的效率。
采用先进的计划工具和技术
利用先进的软件和技术工具,提高物 料需求计划的准确性和效率。
详细描述
生产运作计划是企业管理中一项重要的计划,它是在市场预 测的基础上,通过对企业未来一段时间内的生产任务、生产 进度、生产成本等方面的规划,实现对企业生产活动的有效 控制和协调。
生产运作计划的目的和意义
总结词
生产运作计划旨在提高企业生产效率、降低成本、满足市场需求,从而提升企 业竞争力。
详细描述
动情况,计划在计划期内的生产能力。
生产能力计划的制定
01
02
03
确定市场需求
通过市场调查和预测,了 解市场需求和产品需求, 为制定生产能力计划提供 依据。
分析现有生产能力
评估企业现有设备和工艺 装备的生产能力,了解企 业实际的生产能力水平。
制定生产能力计划
根据市场需求和现有生产 能力,制定合理的生产能 力计划,以满足市场需求 并保持企业的竞争力。
PART 03
物料需求计划
物料需求计划的定义与作用
定义
物料需求计划(MRP)是一种基于产品需求计划,通过物料清单、库存状态和主 生产计划等信息,推算出所需零部件和原材料的需求量和需求时间的计划方法。
作用
确保生产所需的物料在正确的时间、地点可用,以满足生产计划的要求,同时优 化库存水平,降低库存成本。
进度控制
螺杆泵产品生产组织与计划管理设计

《生产与运作管理》课程设计任务书任务发出日期:年月日设计完成日期:年月日指导教师签字:设计题目:螺杆泵产品生产组织与计划管理设计设计依据:1、螺杆泵产品品种,结构与零件明细;2、零件工艺过程,工时定额及设备类型;3、生产能力设计规模(含易损件生产);4、某月订货情况;5、其他参考资料,生产间隔期或设备调整费用等,保管占用量,平行系数,期初重点占用量。
设计任务:1、设置生产单位(职能科室、生产车间、中间库及车间内部组织构成)2、确定生产类型,选择生产组织方式、进行组织设计,画出加工车间平面布置示意图,列出车间设备明细。
3、选择生产作业计划编制方法,编制某月产品进度计划厂级生产作业计划及加工车间内部作业计划(含任务与能力工时平衡)。
4、设计生产进度及在制品控制信息反馈系统。
《生产与运作管理》课程设计指导书设计题目:螺杆泵生产组织与计划管理设计运营管理课程设计是管理类学生的重要教学环节之一,学生学习了《机械制造工艺学》和《运营管理》等课程的基本理论后,通过课程设计可以进一步掌握企业生产组织、计划与控制方面的具体内容和实施方法,增强生产管理的实际工作能力。
一、课程设计的主要工作任务及要求(一)分析课程设计依据中给出的原始资料,领会设计意图(二)按照任务中规定的任务逐项设计并作出必要的分析与说明。
1、设置生产单位根据资料给出的情况,设置与产品生产直接相关的职能科室,生产车间及有关的中间库、生产车间要求进一步设置内部生产单位。
2、对生产车间做出生产组织设计方案采用适当的方法,确定生产车间或生产环节的生产类型,确定各类生产设备需要量,列出车间设备明细,选择合理的生产组织形式(流水线、生产线、设备组)进行组织设计,画出加工车间平面布置示意图。
3、编制作业计划依据资料中给出的某月订货情况,运用所学的加工排序方法对该月排出较优的投产顺序、编制产品进度计划。
选择合理的生产作业计划编制方法:(1)在制品定额法;(2)MRP法;(4)JIT 法。
生产运作与管理课程设计报告

生产运作与管理课程设计报告课程设计报告班级:工业工程11-1班*名:***学号:************指导教师:**日期:2013年12月26日生产计划与操纵课程设计任务书目录第一部分1、课程设计目的2、课程设计思想3、基本原理第二部分4、设计过程5、具体计算分析6、绘制图表及车间平面分布图第三部分7、心得感想报告正文一、设计目的这次课程设计是《生产计划与操纵》这门学科的实践环节,是学习《生产计划与操纵》课本理论知识后的实际操作性锻炼。
通过这次课设,要能够掌握生产与运理的有关理论与方法,同时对设计对象的情况,问题与材料有较好地熟悉,能够灵活应用本课程理论知识与方法,分析与解决问题。
二、设计思想生产作业计划能够分为大量流水生产,成批生产与单件小批量生产三种类型,本次课程设计为大量间断流水线设计。
其特点是专业化程度高;工艺过程封闭;工作地按工艺过程的顺序排列,生产对象在工作地间单向移动;各工序生产能力平衡;生产具有节奏性;各工作地间有传送装置连接。
流水线具有高度的连续性、比例性、平行性。
生产作业计划的设计要在工厂、车间布置满足生产过程需要的情况下,尽可能的提高资源、设备与人员的利用率,车间作业系统方便人与机器的操作,缩小设备与人员的占地面积,避免相互交叉与迂回运输,缩短生产周期,节约生产开支。
三、基本原理根据设计内容,我需要对四个不一致型号的零件进行车间作业系统的设计设计合理的大量流水线要紧按下列步骤进行:(1)确定流水线的节拍;(2)计算工作地数、设备负荷系数、流水线负荷系数等,确定生产类型;(3)绘制间断流水线标准计划工作指示图表;(4)绘制车间设计图;(5)绘制在制品周转占用量变化图表。
四、分析过程根据选题要求,我所选的四种零件情况如下表:备注:设备工作制度规定为两班制,一年为250天,看管周期为120分钟。
每个零件机械加工的计划废品率为6%,设备时间利用率为96%。
下列将以零件前轮轴为例,写出全面计算过程,其他三个零件的过程省去,结果直接以表格形式呈现。
生产运作管理指导书

生产运作管理实验指导书实验模块1:微型工厂实验微型工厂实验是一个连贯的综合设计性实验,包括了以下四个实验,每个实验相对独立但又有严格的先后顺序,上一个实验的数据和成果作为下一个实验的输入。
实验一产品结构分析实验一、实验目的1.熟悉物料编码的各种类型,掌握物料编码的基本原则;2.学会根据具体的编码方法进行编码;3.理解编码的作用;4.了解物料清单的定义和作用;5.学会绘制产品结构树和编制 BOM 表。
二、实验任务1.对玩具小车所涉及的各个零部件和原材料进行物料编码;2.画出玩具小车的产品结构树和产品结构 BOM 表三、实验器具1、拆卸工具:十字和一字改锥、镊子等;2、秒表;3、自备数码相机或摄像机;4、纸和笔的影响,指出装配注意事项,确保产品装配后能实现其功能,达到一定性能指标。
2、对产品进行拆卸分解,直至最底层零件与部件(对电机、线路板等功能部件一般不再拆分)。
3、从视线功能和装配关系的角度描述产品结构,建立产品功能结构树。
以树状图形方式描述产品结构,为了便于后面计算物料需求量,树状图应按照最低层级规则(Lower Lever coding)绘制,即将构成产品的各种物料按其隶属关系分为不同的层级,这样上下层级的物料为母子项关系。
最终产品定成0级,与它相临的下一层物料定位1级,依次类推。
要求同一种物料只能出现在同一层级上,即将其集中在它们所处的各层级中最低的层级上。
产品结构树的形式如下中:P 表示产品,A~E 表示零部件,LT=1 表示提前期为1,字母前的数字表示零部件的个数。
4、产品结构图为依据,建立 BOM。
产品B OM 表物料清单(BOM)是生产制造进行物料需求规划的基础,同时也是编制生产与采购计划、配套领料、跟踪物流、把握生产、计算成本、投资报价、改变产品设计都需要的重要文件。
它表明了组装成最终成品的各分装件、组件、零部件和原材料之间的结构关系以及每一组组装件的用量。
物料清单(BOM)在M RPII 系统中起非常重要的作用。
《生产与运作管理》实验指导手册(doc 31页)

《生产与运作管理》实验指导手册(doc 31页)当前文档修改密码:8362839《生产与运作管理》实验指导书《生产与运作管理》实验的学时划分和评分方法(1)本课程实验由2个实验组成,每个实验的学时划分如下实验内容学时划分实验一装配流水线控制实验5实验二APS生产排程实验 5(2)本课程实验综合成绩由2个实验综合计算,每个小实验单独给分,各小实验在实验综合成绩中的比例设定如下实验内容占综合成绩的比例实验一装配流水线控制实验50%实验二APS生产排程实验50%(3)每个实验的给分原则如下:给分项目分值备注预习实验报告10通过实验前提问及实验预习报告的质量给定实验态度10 实验前后对仪器摆放和操作标准实验到课情况实验环境的维护等操作技能10 实验记录10创新能力10 对实验系统的问题和见解实验报告50实验一、装配流水线控制实验1.实验目的本实验旨在加强学生对流水线生产的深刻理解,尤其是节拍的概念、生产负荷、生产瓶颈的理解,提高学生应用知识的能力,主要是节拍变换和负荷平衡的运用。
2.实验原理和任务流水线生产方式是企业里一种较为普遍的生产形式,对流水线的生产控制方法主要是设置节拍,根据节拍设置工位。
=⨯各工位实际操作需要的总时间生产线平衡率节拍工序数为了保证流水线获得较高的生产线平衡率,各个工位安排的实际操作工作时间须尽量接近节拍时间,并趋于一致。
控制节拍有两种方式:自由节拍和强制节拍。
本次实验任务:(1)将实验用的产品拆开分解,计算组装时各个零部件所用的时间,设计一个包含14个工位的流水线。
以获得最高的生产线平衡率为目标,计算其节拍并分配各工位的加工工序及加工时间。
(2)在进行强制节拍,在控制台进行各个工位的曲线绘制。
并保存打印。
(3)进行自由节拍训练,在控制台进行各个工位的曲线绘制。
并保存打印。
并分析整个流水线的负荷情况,给出负荷平衡方法,计算出最后的生产线平衡率。
以报告形式提交。
3.实验方式每次15人一组。
生产运作管理1~40完整版

⽣产运作管理1~40完整版第⼀章1.请描述⽣产与运作活动的过程⽣产与运作活动的过程是⼀个“输⼊转换输出”的过程,即把输⼊的⼀定资源按照社会需要,经过⼀系列或多种形式的转换,实现价值增值,最后以某种形式的输出提供给社会的过程。
2.请简述企业最基本的⽣产经营活动企业的经营具有五⼤基本职能:财务、技术、⽣产与运作、营销和⼈⼒资源管理。
企业的经营活动是这五⼤职能有机联系的⼀个循环往复的过程。
企业为了实现⾃⼰的经营⽬的,⾸先要制定⼀个经营⽅针,决定经营什么,⽣产什么;决定之后,⾸先需要准备资⾦——进⾏财务活动,这是企业的财务职能;其次需要设计产品和运作流程——统称为进⾏技术活动;之后需要购买物料、加⼯制造——即进⾏⽣产与运作活动,⽣产出产品或服务;销售产品与服务,得到的收⼊进⾏分配,其中⼀部分作为下⼀轮的⽣产资⾦,⼜⼀个循环开始。
⽽使得这⼀切运转的是⼈——企业的⼈⼒资源管理活动。
3.简述⽣产过程的组织形式及其优缺点(论述)(1)⼯艺专业化(Process-Oriented Specialization)按⼯艺特征建⽴⽣产单位集中了相同类型的设备和相同⼯种的⼯⼈,对不同种类的⼯件进⾏相同⼯艺⽅式的加⼯(2)对象专业化(Product-Oriented Specialization)按加⼯对象建⽴⽣产单位集中了为加⼯某种产品 (零件)所需的全套设备、⼯艺装备和各有关⼯种的⼯⼈,对同种或相似的产品(零件)进⾏该产品(零件)的全部(或⼤部分)⼯艺加⼯(3)⼯艺专业化的优点(对象专业化的缺点):制造顺序有⼀定的弹性,品种变换的适应性较好,能充分利⽤设备⼈员的⼯作时间;有利于同类技术⼈员的交流与⽀援,便于⼯艺管理。
(4)⼯艺专业化的缺点(对象专业化的优点):在实际⽣产中,可能在某些⼯序上形成“瓶颈”,连续性差;运输时间和费⽤较⾼;在制品库存量⼤;不同单位之间的⽣产联系复杂,管理难度⼤。
第⼆章4.简述⽣产管理发展的历史,并针对每个阶段例举⾄少两个代表性研究成果(论)(1)科学⽣产管理雏形形成的时代作业计划图(⽢特图)、通⽤⽣产管理模式(2)复杂数学⽅法的应⽤时代运筹学的的诞⽣与完善、⾏为学派的发展(3)计算机开始应⽤的时代物料需求计划(MRP) 、服务业中的⼤量⽣产(4)现代理论普及的时代供应链管理、Internet与电⼦商务5.简述丰⽥⽣产模式(TPS)丰⽥⽣产⽅式(Toyota Production System, TPS)可以简单概括为:通过⽣产过程整体优化,改进技术,理顺物流,杜绝超量⽣产,消除⽆效劳动与浪费,有效利⽤资源,降低成本,改善质量,达到⽤最少的投⼊实现最⼤产出的⽬的。
《生产与运作管理》章节笔记

《生产与运作管理》章节笔记第一章生产与运作管理概述一、生产与运作管理的基本概念1. 定义:生产与运作管理(Production and Operations Management, POM)是指对企业生产与运作活动进行系统的计划、组织、指挥、协调和控制,以有效地利用资源,实现产品和服务的高效、低成本、高质量生产,满足市场需求,提升企业竞争力的管理活动。
2. 范围:生产与运作管理涵盖了从原材料采购、生产加工、产品装配、质量控制、库存管理、物流配送直至产品售后服务的一系列过程。
具体包括以下方面:- 设计管理:包括产品设计和工艺设计的管理。
- 生产规划:确定生产规模、工厂布局、生产能力等。
- 生产控制:监控生产进度,调整生产计划,确保生产目标的实现。
- 设备管理:设备的选购、使用、维护和更新。
- 物料管理:原材料的采购、储存、配送和使用。
- 质量管理:确保产品和服务满足既定的质量标准。
- 人力资源管理:生产员工的招聘、培训、绩效评估等。
- 成本管理:控制生产成本,提高成本效益。
- 环境与安全管理:确保生产活动符合环保法规,预防安全事故。
3. 重要性:生产与运作管理是企业运营的核心环节,其重要性体现在:- 效率提升:通过优化生产流程,提高生产效率,缩短生产周期。
- 成本控制:降低生产成本,提高产品价格竞争力。
- 质量保障:确保产品和服务质量,增强客户满意度。
- 市场响应:快速响应市场变化,满足客户需求。
- 竞争优势:通过有效的生产与运作管理,建立企业的竞争优势。
二、生产与运作管理的任务和目标1. 任务:- 确保生产资源的有效配置:包括人力、物料、设备、资金等。
- 制定和实施生产计划:根据市场需求,制定生产计划并确保执行。
- 优化生产流程:通过精益生产、持续改进等方法,提高生产效率。
- 控制生产成本:通过成本分析和成本控制,降低不必要的开支。
- 管理生产质量:建立质量管理体系,实施质量控制和质量改进。
- 管理生产安全:确保生产过程中的员工安全和环境保护。
《生产与运作管理》课程设计任务

《生产与运作管理》课程设计指导书一、性质和目的本课程设计是与《生产与运作管理》配套的实践环节之一。
在完成《生产与运作管理》理论教学基础上,对学生进行一次全面的实际操作性锻炼。
通过本环节的设计锻炼,让学生较好地掌握生产与运作管理的相关理论与方法,对设计对象的情况、问题和材料有较好的了解,能灵活应用本课程理论知识和方法,分析和解决问题。
二、设计任务及选题要求本课程设计选题围绕《生产与运营管理》的教学目的和任务,面向工业企业和服务企业,充分体现本课程的特点,密切联系企业实际,并具有较强的理论和实践意义。
设计任务分为以下几类:(详细设计内容附后)题目一、企业生产现场优化设计题目二、采用MRPⅡ/ERP软件编制物料需求计划(或不用软件,做理论计算)题目三、服务业设施规划设计选题要求:可在题目一、二、三中自行选取设计题目。
三、课程设计完成形式1、一份完整的课程设计报告,字数不少于3千。
(必须);2、课程设计图表或图纸(可选);五、具体要求及注意事项1、每位学生应严格按任务书要求选题。
2、课程设计报告项目要齐全。
一般应包括:设计任务,目的、设计思想、基本原理、分析与设计过程、结果分析,有关说明等。
报告应说明设计思路、依据、计算过程和计算结果。
课程设计报告应做到理论联系实际,具有一定的针对性。
设计方案应有一定的可操作性,选用的资料、数据必须真实。
3、课程设计报告统一用A4纸打印,按统一格式、统一顺序装订(教务处的统一格式)。
4、课程设计报告严禁出现雷同,凡有雷同者一经发现,相关学生课程设计成绩均按不及格处理。
附:课程设计任务题目一、企业生产现场优化设计目的:理解生产现场的空间组织方式,掌握生产现场的设施布置方式,包括:物料运量图和物料相关图的具体使用技巧,能对现有生产现场进行优化设计。
具体内容:1.通过对某一企业进行现场考察,熟悉企业的产品特点,车间布置,工艺流程,工作地人员配置以及劳动定额执行等情况;2.以企业的主导产品为依据,根据其工艺流程,绘制车间之间或车间内部设备之间的物料运量图或作业相关图;3.按照物料运量图或作业相关图确定车间之间或车间部分设备之间的相对位置,进行生产现场的优化设计。
生产运作管理第4讲 流程
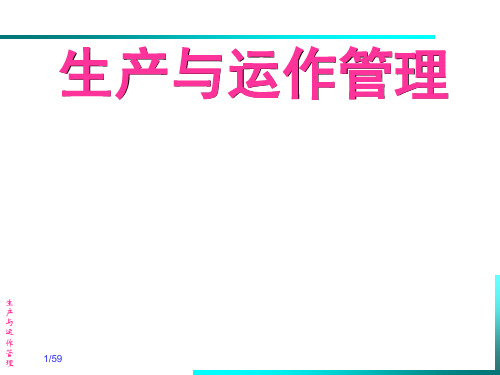
生
产
与
运
作
管 理
18/59
1、影响流程设计的主要因素
产品/服务的特征与需求性质 自制/外购决策 生产柔性:从品种柔性和产量柔性 产品/服务质量水平 接触顾客的程度 技术、人力资源、可靠性…
对决策影响最大的是品种数的多少和每种产品产量的大小。
生
产
与
运
作
管 理
19/59
产品/服务的特征与需求性质(最主要因素):需求数量、品种、季节 波动性等
少品种、大批量
高设备利用率 (70%-90%) 专用设备
MC——精益生产与敏捷制造的结合
生
产
与
运
作
管 理
14/59
产品导向型流程与MC流程的比较
比较内容
大批量生产
MC
核心
通过稳定性和控制取得效率 通过柔性和快速反应实现产 品变型和客户化
目标
以几乎每个客户都能承受的 低成本和低价格开发、生产 、销售、运送商品和提供服 务
➢ 产品生命周期短
三类不同生产流程特征比较
特征标记
对象专业化
订货类型
批量较大
产品 产品流程
流水型
产品变化速度 低
市场类型
大批量
产量
高
劳动 技能要求
低
者 任务类型
重复性
工资
低
投资
高
资本
库存 设备
低 专用设备
柔性
低
目标
成本 质量
低 均匀一致
生
按期交货程度 高
产 与
计划 生产控制
容易
运 控制 质量控制
容易
作 管 理
库存控制
【实验报告】生产运作管理实验报告范文

生产运作管理实验报告范文篇一:生产与运作管理实训报告前言:教学实习促进人才计划的完善和课程的设置的调整,教学实习促进了学生自身的发展,实习活动使学生初步接触社会,培养他们的环境适应能力及发现问题,分析问题,解决问题的实际工作能力,为他们今后的发展打下了良好的基础。
近年来,各大高校为适应学生的实践需要陆续增设与调整了一系列课程,受到同学的欢迎。
所以,组织学生到校外实训是很有必要的。
一、实训目的:通过连续几个不同工厂,企业(康菱动力技术有限公司、佳居乐有限公司、广东唯美集团有限公司、金威啤酒有限公司和沃尔玛连锁超市)的参观,实地的了解到工厂生产的基本程序,流程,工序,让我们所学的东西在实训中体现,强化学过的知识,扎根现实中,将理论从实际中得到体现。
二、实训时间:6月7日―6月17日三实训地点:康菱动力科技有限公司、佳居乐有限公司、广东唯美集团有限公司、金威啤酒有限公司和沃尔玛连锁超市。
四、实训内容:6月7日,我们去参观了康菱动力科技有限公司,进入康菱公司的前台,向右望去就是一个小小的文化展厅,为我们展示了康菱的前身,发展史,成就以及骨干人员等等。
然后就是展示了他们工厂的生产车间,一系列的发动机让我们震惊,最后就是做一个详尽的讲座,为我们讲诉企业的文化,宗旨。
让我们对工厂的了解由无到有,有少增多,由表面到更深层。
6月8日-6月9日,我们的实训目的地都是佳居乐有限公司,一个打造橱柜的企业,当我踏进佳居乐的橱柜展厅时,让我看了橱柜的装饰也可以很漂亮的,这是最初的印象,佳居乐给了我一个很好的印象,让我对它产生了浓厚的兴趣。
然后我带着好奇的心情去参观佳居乐的生产工厂,让我知道了一个精美的橱柜是怎么由一块普通的木头而成的。
经过6月9日的讲座,我了解到佳居乐的企业文化包括了以下的方面:企业核心价值观:厚德感恩?求真务实,企业愿景:我为企业创品牌,企业使我做主人。
战略目标: 专心、专注、专业打造行业第一品牌。
企业使命:专心橱柜事业,使员工价值最大化,使客户价值最大化。
- 1、下载文档前请自行甄别文档内容的完整性,平台不提供额外的编辑、内容补充、找答案等附加服务。
- 2、"仅部分预览"的文档,不可在线预览部分如存在完整性等问题,可反馈申请退款(可完整预览的文档不适用该条件!)。
- 3、如文档侵犯您的权益,请联系客服反馈,我们会尽快为您处理(人工客服工作时间:9:00-18:30)。
生产运作管理实验指导书实验模块1:微型工厂实验微型工厂实验是一个连贯的综合设计性实验,包括了以下四个实验,每个实验相对独立但又有严格的先后顺序,上一个实验的数据和成果作为下一个实验的输入。
实验一产品结构分析实验一、实验目的1.熟悉物料编码的各种类型,掌握物料编码的基本原则;2.学会根据具体的编码方法进行编码;3.理解编码的作用;4.了解物料清单的定义和作用;5.学会绘制产品结构树和编制 BOM 表。
二、实验任务1.对玩具小车所涉及的各个零部件和原材料进行物料编码;2.画出玩具小车的产品结构树和产品结构 BOM 表三、实验器具1、拆卸工具:十字和一字改锥、镊子等;2、秒表;3、自备数码相机或摄像机;4、纸和笔的影响,指出装配注意事项,确保产品装配后能实现其功能,达到一定性能指标。
2、对产品进行拆卸分解,直至最底层零件与部件(对电机、线路板等功能部件一般不再拆分)。
3、从视线功能和装配关系的角度描述产品结构,建立产品功能结构树。
以树状图形方式描述产品结构,为了便于后面计算物料需求量,树状图应按照最低层级规则(Lower Lever coding)绘制,即将构成产品的各种物料按其隶属关系分为不同的层级,这样上下层级的物料为母子项关系。
最终产品定成0级,与它相临的下一层物料定位1级,依次类推。
要求同一种物料只能出现在同一层级上,即将其集中在它们所处的各层级中最低的层级上。
产品结构树的形式如下中:P 表示产品,A~E 表示零部件,LT=1 表示提前期为1,字母前的数字表示零部件的个数。
4、产品结构图为依据,建立 BOM。
产品B OM 表物料清单(BOM)是生产制造进行物料需求规划的基础,同时也是编制生产与采购计划、配套领料、跟踪物流、把握生产、计算成本、投资报价、改变产品设计都需要的重要文件。
它表明了组装成最终成品的各分装件、组件、零部件和原材料之间的结构关系以及每一组组装件的用量。
物料清单(BOM)在M RPII 系统中起非常重要的作用。
五、实验报告要求实验报告应包括以下内容:1、产品的功能与性能描述,以及装配作业注意事项;2、产品功能结构树与装配结构树、BOM 表。
六、思考题1.为什么要进行物料编码?2.本实验所用的物料编码方法合理吗?请你自己想一套编码方法进行编码,并对两者进行对比。
说明两者的优点和缺点。
实验二装配工艺设计实验一、实验目的1、通过装配工艺设计实验,掌握装配流程程序分析的方法,掌握绘制流程图的方法;2、通过流程分析,掌握紧前工序的处理方法;3、学会用“5W1H”方法提问技术发掘问题,用“ECRS“原则改进流程。
二、实验任务1、依据上一实验的产品结构,确定装配顺序,分解装配作业任务,确定紧前紧后关系,建立装配流程图;2、通过动作研究确定标准作业方法3、通过时间研究确定标准作业时间三、实验器具1、拆卸工具:十字和一字改锥、镊子等;2、秒表;3、自备数码相机或摄像机;4、纸和笔四、实验步骤1、根据玩具小车的组装流程,确定玩具小车装配流程;2、分解装配作业任务,确定紧前关系;3、用“5W1H”方法发掘装配流程中存在的问题,用“ECRS“原则改进装配流程;4、通过秒表发进行装配工艺时间研究,确定标准作业时间。
五、实验报告要求实验报告应包括以下内容:1、产品组装的工艺程序分析和流程分析,以及如何确定标准作业;2、装配作业任务及操作时间、紧前关系表、紧前关系图。
六、思考题在实验中每一个装配任务的作业时间是如何确定的?都考虑到了什么影响因素?经过实验检验,所确定的时间是否合理?是否对实验结果造成了影响?实验三装配线平衡实验一、实验目的1、掌握装配线节拍和效率的计算2、通过对玩具小车生产工位的分配,掌握生产线平衡的方法;3、学会根据实际装配操作优化生产线装配效率的方法。
二、实验任务1、在装配结构图基础上,按照标准时间分配工作站,进行装配线节拍时间和生产效率计算;2、找出影响装配线效率的关键作业,研究将其进一步分解,并重新进行装配线平衡,得到优化的节拍时间与装配线效率三、实验器具1、微型工厂流水线一套和配套工作台8个;2、拆卸工具:十字和一字改锥、镊子等;3、计算器、纸和笔四、实验步骤1、在给定的技术参数条件下,计算装配线的节拍和效率;2、根据前面实验的作业标准时间以及线节拍计算结果,在装配作业任务列表与紧前关系图的基础上,将装配任务分配到装配生产线的8个工位上;3、找出影响装配线效率的关键作业任务,研究将其进一步分解的方法,并重新进行线平衡,优化节拍时间和装配效率。
1)首先应考虑对瓶颈工序进行作业改善,作业改善的方法,可参照程序分析的改善方法及动作分析、工装自动化等IE方法与手段;2)将瓶颈工序的作业内容分担给其它工序;3)增加各作业员,只要平衡率提高了,人均产量就等于提高了,单位产品成本也随之下降;4)合并相关工序,重新排布生产工序,相对来讲在作业内容较多的情况下容易拉平衡;5)分解作业时间较短的工序,把该工序安排到其它工序当中去。
五、实验报告要求实验报告应包括以下内容:1、装配线平衡计算与优化的过程及结果,装配线节拍与效率;2、组员分工情况说明;3、在装配线平衡时,如果提供的工作站数目不局限于8个,也可以适当增加工作站数目来延长装配线,是否有更好的装配线平衡结果?六、思考题1、在装配线平衡时,可以采用哪些方法将装配作业任务分配到工作站上?2、不同的方法会不会出现不同的分配结果?装配线的效率有什么变化?3、在实验中每一个装配任务的作业时间是如何确定的?都考虑到了什么影响因素?经过实验检验,所确定的时间是否合理?是否对实验结果造成了影响?实验四装配线仿真实验一、实验目的1、建立从物理模型过渡到计算机模型的思维;2、初步了解离散事件系统仿真及仿真建模的基本方法,学会仿真的基本操作3、学会应用系统内模块对现实的生产系统进行建模仿真;4、对仿真系统的参数进行调试,对系统运行结果进行分析、评价,进而进行系统优化二、实验任务1、对以上建立的装配线,利用仿真软件进行仿真建模,参数设计,并利用参数变化调节优化生产线配置方案。
2、对仿真模型方案优化结果,通过现场的装配线重新配置实验,检验方案的可行性,如有需要,进一步调整,生成装配线方案仿真优化实验报告三、实验器具1、微型工厂流水线一套和配套工作台多个;2、仿真软件一套四、实验步骤1、熟悉仿真软件的仿真原理和基本建模步骤;2、应用基本的模块建立简单排队系统;3、根据上一实验的装配线设计成果,应用系统模块仿真生产系统;4、对已建立仿真模型进行调试、参数设置以及输出结果分析;5、将仿真运行结果反馈回来,重新建立装配线,检验仿真方案的可行性,探讨进一步改进的方向及可能性。
五、实验报告要求实验报告应包括以下内容:1、装配线示意图和仿真模型执行文件2、仿真模型的逻辑示意图3、仿真模型的参数设置及仿真运行输出的结果六、思考题1、应用仿真软件建立仿真模型的步骤大体分为几步?2、仿真模型参数的设置有什么依据?对系统会产生什么影响?实验模块2:企业经营模拟实验一、实验目的企业经营模拟实验是通过ERP电子沙盘的形式,亲身模拟参与经营决策过程,几乎涵盖了企业运营的所有关键环节:战略规划、资金筹集、市场营销、产品研发、生产组织、物资采购、设备投资与改造、财务核算与管理等几个部分为设计主线,把企业运营所处的内外环境抽象为一系列的规则,由受训者组成企业经营团队,赋予每人不同的角色和职能范围,模拟企业6年的经营,并与其他五个随机企业展开相互竞争。
通过学生参与-->沙盘载体-->模拟经营-->对抗演练—> 讲师评析--> 学生感悟等一系列的实验环节,其融和理论与实践一体、集角色扮演与岗位体验于一身的设计思想,使受训者在分析市场、制定战略、营销策划、组织生产、财务管理等一系列活动中,参悟科学的管理规律,同时也对企业资源的管理过程有一个实际的体验。
二、实验任务1、在给定的企业经营环境、市场预测、产品研发及市场开拓条件下,分析企业的总体经营战略,建立企业的市场定位,形成企业生产指导大纲;2、根据产品系列的选择和组合,选择生产线配置的数量以及型号,同时选择租赁或者购买的厂房类型,确定投资生产线的时间及生产能力的调整;3、根据订单获取成本以及市场竞争情况,对所涉及的产品类型以及开拓的市场范围,确定每年年初的各产品在各市场的广告费投入,依据当年度规划产能优选订单,实现供需平衡和库存调节,提前发起原材料采购订单,满足当期生产需要4、尝试不同的经营模式,分析各自面临的风险与机会,学会根据年初订单竞争结果,实时调整生产策略、资金筹措方式、生产线能力配置结构,原料订单的获取等;比较不同经营模式和策略下的经营成果,确定最优经营策略。
三、实验器具1、ERP企业经营模拟软件;2、计算机;3、纸和笔四、实验步骤1、企业总体经营战略实验任务:根据不同的目标市场进行详细分析,确定企业市场定位及产品选型。
(1)本地市场分析。
如图2-1所示(左图纵坐标表示数量,横坐标表示年份;右图纵坐标表示价格,横坐标表示年份),本地市场将会持续发展,客户对低端产品的需求可能要下滑。
伴随着需求的减少,低端产品的价格很有可能会逐步走低。
后几年,随着高端产品的成熟,市场对P3、P4产品的需求将会逐渐增大。
同时随着时间的推移,客户的质量意识将不断提高,后几年可能会对厂商是否通过了ISO 9000认证和IS0 14000认证有更多的要求。
图2-1本地市场预测图(2)区域市场分析。
如图2-2所示,区域市场的客户对P系列产品的喜好相对稳定,因此,市场需求量的波动也很有可能会比较平稳。
因其紧邻本地市场,所以产品需求量的走势可能与本地市场相似,价格趋势也应大致一样。
该市场的客户比较乐于接受新的事物,因此对于高端产品也会比较有兴趣。
但由于受到地域的限制,该市场的需求总量非常有限。
并且这个市场上的客户相对比较挑剔,因此,在以后几年,客户会对厂商是否通过了ISO 9000认证和ISO 14000认证有较高的要求。
图2-2区域市场预测图(3)国内市场分析。
如图2-3所示,因为P1产品带有较浓的地域色彩,估计国内市场对Pl产品不会有持久的需求。
但P2产品因为更适合于国内市场,所以估计需求会一直比较平稳。
随着对P系列产品新技术的逐渐认同,估计对P3产品的需求会发展较快,但这个市场上的客户对P4产品却并不是那么认同。
当然,对于高端产品来说,客户一定会更注重产品的质量保证。
图2-3 国内市场预测图(4)亚洲市场分析。
如图2-4所示,这个市场上的客户喜好一向波动较大,不易把握,所以对P1产品的需求可能起伏较大,估计P2产品的需求走势也会与Pl相似。
但该市场对新产品很敏感,因此估计对P3、P4产品的需求会发展较快,价格也可能不菲。