电镀Cr3+与Cr6+外壳区分管理规程
表面镀铬工艺

1、铁件镀铬工艺流程:除蜡→ 热浸除油→ 阴极→ 阳极→ 电解除油→ 弱酸浸蚀→ 预镀碱铜→ 酸性光亮铜(选择)→ 光亮镍→ 镀铬或其它除蜡→ 热浸除油→ 阴极→ 阳极→ 电解除油→ 弱酸浸蚀→ 半光亮镍→ 高硫镍→ 光亮镍→ 镍封(选择)→ 镀铬2、锌合金镀铬工艺流程除蜡→ 热浸除油→ 阴极电解除油→ 浸酸→ 碱性光亮铜→ 焦磷酸铜(选择性)→ 酸性光亮铜(选择性)→ 光亮镍→镀铬3、不锈钢直接镀铬工艺1) 电化学除油→热水洗→冷水洗→浸酸活化(1ml/L HCL、10ml/L H2SO4,室温,半分钟;适用于自动线上不锈钢镀铬,不宜镀铜或镍)→水洗→镀铬。
2) 阴极电化学除油→清洗→阳极活化(10A/dm2)→直接镀铬。
3) 化学除油→清洗→阳极电化学除油(0.5A/dm2)→清洗→浸酸活化(1ml/L HCL、10ml/L H2SO4,室温,45S)→清洗→镀铬注:镀铬时,应先用是正常电镀时电流密度的1.5~2倍镀3~5分钟,然后再正常电流密度电镀,要尽量缩短各工序之间的过渡引起的停留时@@@@@@@@@@@@@@@@@@@@@@@@@@@@@@@@@@@@@@@@@@@@@@@@@@镀后处理知识1、前言镀后处理和镀前处理在金属的表面镀工艺中占有极其重要的地位,许多采用表面镀技术制造的产品出现缺陷往往都是由前处理或后处理不当造成的,有关前处理的知识在一般的电镀书中都有比较详细的叙述,但对镀后处理还没有文章进行过系统的论述,镀后处理的目的主要是为了提高镀层的耐腐蚀性能或者保持镀层原有的特性,其中最主要的镀后处理是除氢处理和钝化处理[1]。
为了提高镀层的抗腐蚀性能,一般都要同时进行除氢和钝化处理,有些还需要涂有机膜,如镀锌件目前一般要经过除氢和化学钝化处理,仿金电镀要经过化学钝化和涂有机膜处理[2]等。
2、镀后处理2.2钝化处理钝化处理是指在一定的溶液中进行化学或电化学处理,在镀层上形成一层坚实致密的、稳定性高的薄膜的表面处理方法,钝化使镀层的耐腐蚀性能进一步的提高并增加表面光泽和抗污染的能力。
rohs对镀层的要求

rohs对镀层的要求
RoHS指令(Restriction of Hazardous Substances Directive)是欧盟针对电子电气设备和电子电气设备零部件的限制
使用有害物质的指令。
对于镀层的要求,RoHS指令限制了电子电气
设备中所使用的镀层材料中的有害物质含量,主要包括铅(Pb)、
汞(Hg)、镉(Cd)、六价铬(Cr6+)、多溴联苯(PBB)和多溴二
苯醚(PBDE)等物质的含量。
这些有害物质在镀层材料中的含量必
须符合RoHS指令规定的限制要求。
从材料角度来看,RoHS指令要求镀层材料中不得含有上述有害
物质超过规定的限量,因此制造商需要选择符合RoHS要求的环保材
料作为镀层材料,以确保产品的合规性。
同时,镀层生产过程中所
使用的化学药剂和处理工艺也必须符合RoHS指令的要求,以确保镀
层材料在生产过程中不受到有害物质的污染。
此外,从产品设计和生产管理角度来看,制造商需要建立健全
的供应链管理体系,确保从原材料采购到生产加工再到最终产品的
出厂都符合RoHS指令的要求。
这需要严格控制原材料的选择和采购,加强对生产过程的监控和管理,以及建立完善的产品合规性检测体系,确保产品的镀层材料符合RoHS指令的要求。
总的来说,RoHS指令对镀层的要求主要包括材料选择、生产工艺和产品管理等多个方面,制造商需要从多个角度全面考虑,确保镀层材料符合RoHS指令的限制要求,以满足环保和产品合规性的要求。
焊锡技术之有害物质限用指令

焊锡技术之有害物质限用指令(RoHS)无铅锡线无铅焊锡膏无铅锡膏有害物质限用指令(Directiveon Restrictionoftheuse of certain Hazardous Substances in electrical and electronicequipment,简称RoHS)RoHS与WEEE同时间发布,可视为WEEE精神的延伸,规范产品除了WEEE中「医疗设备」与「监控设备」尚未纳入之外,其余八类电子电机产品皆属其限制范畴。
RoHS以六项有害化学物质-铅(Pb)、汞(Hg)、镉(Cd)、六价铬(Cr6+)、多溴联苯(PBB)与多溴联苯醚(PBDE)之限用禁用为其内容大纲,其中前四项化学物质的规范曾出现在过去「包装废弃物管理指令」与「废弃车辆指令」中,此次乃是限用范围的再扩大。
欧盟各国同样必须在2004/8/13前完成立法程序,但正式生效日则略有不同,订于2006/7/1。
RoHS限用物质之应用范围与危害物质应用对人体之危害物质铅(Pb)焊料、电缆、电线、塑料件及组件抛光贫血、腹部剧痛、麻痹汞(Hg)开关、液晶显示器、继电器与灯泡微量即可引发中毒,长期滞留体内可损伤内脏和神经系统镉(Cd)自动贩卖机电源线、电线与开关触点毒性强,引发神经性障碍六价铬(Cr6+)外壳的表面处理毒性强,直接接触即可引发皮肤炎,可能造成遗传性基因缺陷,吸入可能致癌多溴联苯(PBB)塑料与印刷电路板之耐燃剂被怀疑具有扰乱内分泌作用的化学物质(环境荷尔蒙)多溴联苯醚(PBDE)塑料、橡胶与印刷电路板之耐燃剂被怀疑具有扰乱内分泌作用的化学物质(环境荷尔蒙)注:三价铬(Cr3+)、四价铬(Cr4+)与金属铬(Cr)并不具有上述毒性分析此六种化学材料,对台湾制造业来说,影响最大应是「铅」的限用政策。
我国电子零组件产业结构完整,其中包括印刷电路板、连接器、铜箔厂、被动组件等业者都将因RoHS对于「铅」在电子电器产品中的限用禁用受到影响:传统连接器产业在电镀制程中使用锡铅(90/10)电镀液与焊接时所用的锡铅(63/37)焊料,锡铅合金具有低成本、焊接性与抗腐蚀性强以及回焊(reflow)温度(注4)低之特性,而业者为了因应「无铅制程」(注5)的风潮,目前连接器已开发出多种替代品如纯锡、镍锡、铜锡.等多种电镀液,但由于无铅制程回焊温度远高于含铅制程,除了回焊设备需另行购置之外,连接器外壳材质亦需重新调整,基本上「热变形温度」愈高的塑料材质,价格也愈高;印刷电路板、被动组件、铜箔基板甚至是半导体业者皆同样面临「无铅制程」工作温度较高的难题。
金属电镀件检验标准

1 范围本标准规定了金属电镀件的缺陷定义、外观判定标准、功能性要求、检验方法、检验规则、运输与贮存。
本标准适用于本公司的3个通用金属电镀功能等级分别为CA级、CE 级、CF级的电镀品。
在ERP系统中物料料号以这3个等级代码体现。
如果客户有严格客户标准,且本标准3个通用等级不适用时,可以为该客户另外制定专用标准和电镀等级代码。
2 参考标准下列文件中的条款通过本标准的引用而成为本标准的条款。
凡是注日期的引用文件,其随后所有的修改单(不包括勘误的内容)或修订版不适用于本标准,然而,鼓励根据本标准达成协议的各方研究是否使用这些文件的最新版本。
凡是不注日期的引用文件,其最新版本适用于本标准。
GB 4955 金属覆盖层厚度测定 阳极溶解库仑方法GB 5933-86 轻工产品金属镀层的结合强度测试方法GB5944-86 轻工产品金属镀层腐蚀试验结果的评价GB6461-86 金属覆盖层对底材为阴极的覆盖层腐蚀试验后的电镀试样的评级 (等效 ISO 4540-80)GB 6462 金属和氧化物覆盖层 横断面厚度显微镜测量方法GB/T 10125-97 人造气氛腐蚀试验 盐雾试验 (等效 ISO 9227-90)ASTM B456-95 铜+镍+铬和镍+铬的电镀层的技术规范EN248-2002 镍、铬电镀通用技术规范ASTM B368-97 铜加速醋酸盐雾实验标准方法ASTM B571-97 金属镀层的结合强度测试方法3 缺陷定义3.1 功能性外观缺陷:功能性表面缺陷是指产品构件的基材在产品使用过程中被腐蚀。
不允许在任何已经表面处理完毕的零件存在任何功能性装饰性外观缺陷。
3.2 装饰性外观缺陷:装饰性外观缺陷导致构件不能象期望的那样外观完好,但它不会造成功能失效。
本规范规定装饰性外观缺陷的种类、部位和可接受的限度。
3.3 常见的表面处理缺陷描述:见表1缺陷名称现象描述附着力(Adhesion)涂层剥落或被擦去。
气泡(Blister)泡状或浮起的区域,在用铅笔尖挤压时能变形电镀烧伤(Burn)电镀过程中局部电流过大引起的镀层发白、发暗,有粗糙感。
螺栓表面氧化处理标准规范

螺栓表面氧化处理标准规范螺栓的表面处理按方法分会有1,氧化发黑。
也有发蓝黑的,一般氧化后涂防锈油使用。
2,磷化。
一般磷化后要涂油。
3,电镀。
主要是电镀锌,还有镀铬,镀镍,镀银等等4,热浸锌。
5,渗锌。
6,非电镀锌片涂层。
广义上的达克罗,又分锌铬涂层,锌铝铬涂层按颜色分,蓝色,银白色,银灰色,铜黄色,黑色,绿色等目前常见的螺栓有银白色,银灰色,黄色,黑色。
这种颜色大多数是为了考虑外观或环保而来,对于是否能提高防腐性,机械财经持保留态度。
机械财经认为提高螺栓防腐性,要通过使用更高级的表面处理方法,如从电镀更改到热浸锌或达克罗。
单纯的更改颜色虽会略微改变防腐效果,但防腐效果仍处于同一数量级之内。
如电镀锌,可以镀黄锌,彩锌,银白锌,但是防腐数量级上还是一样的,市场上的通用电镀锌工艺盐雾试验仍在70小时左右。
再如采用非电解锌片处理方法,可以是银灰色,或特殊处理为黑色,如果涂层厚度一样,其防腐数量级也没有什么特殊的,盐雾试验在900小时200小时的样子。
那么我们再详细聊聊镀锌工艺中各种颜色的些许差别。
一般来讲常见的是银白锌,蓝锌,黄锌,黑锌,如果非要比较出一个耐蚀能力,那么参考镀锌标准,镀白锌c1B、镀彩锌c1C、镀深色铬酸盐(分黑锌c1D(H)和军绿色c1D(J)),其防腐蚀性按上述顺序递增,也就是说白<彩锌(黄或蓝)<黑锌<军绿。
还有可以通过颜色大致区分有害物质Cr6+的存在,一般,彩色是肯定含有Cr6+的,银白色一般是Cr3+,镀黑色的一般都是要求ZnNi合金。
这里的黑色与黑锌以及达克罗黑完全不是一回事,发黑可能是表面处理最简单或者最便宜的方法,大多数是加热氧化发黑,所以也叫煮黑。
发黑就是将螺栓放入溶液槽,溶液槽主要是含有氧化剂的化学溶液,经过加热在螺栓表面形成四氧化三铁(Fe3O4)薄膜,厚度一般为0.6-0.8μm呈黑色或蓝黑色。
不知道大家的家里有没有一些锤头之类的工具,如果是黑色那么基本就是做过氧化发黑处理的。
轧辊镀铬工艺流程

轧辊镀铬工艺流程
在钢铁工业中,轧辊是轧机的主要零件,为了提高表面质量,通常用镀铬处理。
然而在镀铬过程中,由于杂质的存在及溶液本
身的化学作用等原因,往往出现镀层发花、发脆、变色等问题。
因此,提高镀铬质量对提高产品质量具有重要意义。
铬是一种很活泼的金属,在空气中能与氧化合生成四氯化钛(TiCl)和四氯化铁(FeCl)两种化合物。
在锌合金和铜合金中,由于锌的含量较高(一般为22%~25%),因此铬在锌合金和铜合
金中的活动性较大。
镀铬液中的铬主要是以Cr2O3形式存在,当
溶液温度为100~150℃时,铬离子以Cr3+形式存在。
铬层在常温
下具有良好的耐磨性和耐蚀性。
在高温时(高于450℃),铬离
子又转变成Cr3+或Cr6+状态存在。
由于铬层中含有较多的杂质,如铁、钛、铝等金属离子都会降低铬层的耐蚀性。
为了提高镀铬
质量,除控制铬离子浓度外,还应注意以下几点:
1.为保证铬层与基体有良好的结合力,除采用小电流密度外,还应使铬层均匀。
—— 1 —1 —。
电气控制柜设计制作-机柜制作-表面处理-镀后除氢和钝化处理

镀后处理1.除氢处理有些金属如锌,在电沉积过程中,除自身沉积出来外,还会析出一部分氢,这部分氢渗入镀层中,使镀件产生脆性,甚至断裂,称为氢脆。
为了消除氢脆,往往在电镀后,将镀件在一定的温度下热处理数小时,称为除氢处理。
除氢这个工序一般在钝化之前。
除氢处理的方法比较单一和简单,一般都是采用热处理的方式把原子态的氢驱逐出来。
对于常用的镀锌构件,应在镀后立即或4h内进行去氢处理。
一般在带风机的烘箱中,即在200~215℃温度条件下保温2h,即可达到去氢目的。
如果保温时间过长则容易产生铬脆。
除氢后再进行钝化,这样不会造成由于氢脆而导致钝化层破裂。
2.钝化处理所谓钝化处理是指在一定的溶液中进行化学处理,在镀层上形成一层坚实致密的、稳定性高的薄膜的表面处理方法。
钝化使镀层耐蚀性大大提高,并能增加表面光泽和抗污染能力。
这种方法用途很广,镀锌,铜等后,都可进行钝化处理。
按照钝化膜的化学成分钝化处理可分为无机盐钝化和有机类钝化两类;根据钝化膜组成成分对人体的危害性可分为铬酸钝化和无铬钝化。
铬酸钝化是无机盐钝化的一个分支,目前国内外采用较多的无铬钝化有钼酸盐溶液、钨酸盐溶液、硅酸盐溶液、钛盐钝化、含锆溶液、含钴溶液、稀土金属盐溶液、三价铬溶液、磷酸盐钝化(磷化处理)等无机盐钝化和有机类钝化等。
1)无机盐钝化处理无机盐钝化处理研究比较成熟和应用较早的是铬酸盐钝化。
在含铬钝化膜中,Cr3+起骨骼作用,Cr6+起血肉作用,Cr6+在空气中具有良好的自修复功能,因而对镀层具有很好的保护作用,而且,改变Cr6+和Cr3+的不同配比,还可以得到不同色彩的钝化膜。
这些突出的优点使得铬酸钝化仍然是目前应用最广的钝化工艺。
但是由于Cr6+具有相当高的毒性且易致癌,随着环境保护意识的增强,人们越来越希望寻找可以代替铬酸钝化的新配方和新工艺。
钼和铬是同族元素,因此,它与铬具有相似的化学性质。
钼酸盐已经广泛用于钢铁以及有色金属的缓蚀剂和钝化剂。
电镀生产工艺流程(1)
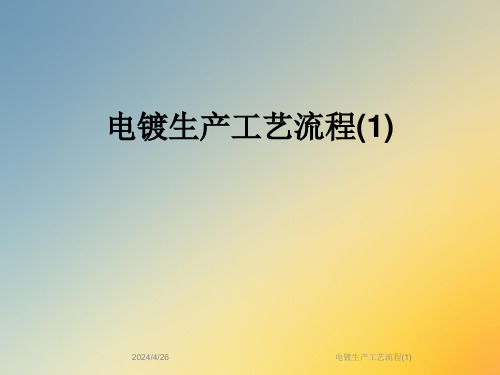
Pd
Pd
Pd
Pd
Pd
Pd
Pd
Pd
Pd
Pd
Pd
Pd
Pd
Pd
Pd
化学镍
电镀部分 electro-plating
焦铜/瓦特镍 2 µm
光铜 10-30 µm
化学镍 0.5 µm
光镍 8-15 µm
光铬 0.1~ 1 µm
电镀生产工艺流程(1)
概述
电镀
五金电镀--在金属基体上直接进行电镀
塑胶电镀--使不导电的塑胶基体覆上一层 导电金属膜后进行电镀 ●前处理 通过化学反应在塑胶表面涂覆一层薄金 属膜层,为之后的电镀提供导电媒介 ●电镀 通过电化学反应使被镀工件表面沉积上致 密而平整的金属层
塑胶电镀 Plastic Electro-Plating
粗化Ⅰ
粗化Ⅱ
整面
亲水
中和
钯水
喷水洗
水洗1#
七 联 水 洗 7# 6# 5# 4# 3# 2# 1#
四 联 水 洗 1# 2# 3# 4#
碱解胶
水洗
水洗
水洗
水洗
三联水洗 1# 2# 3#
化学镍前 水洗
除蜡
除油
水洗
水洗
沙 碳 水 洗
酸 浸
水 洗 2# 3# 4#
Pd
Pd
Pd
Pd
Pd
Pd
Pd
Pd
Pd
Pd
Pd
Pd
Pd
目的:使塑料制品表面金属化。 原理: 化学镀---在无电流通过(无外界动力)时借助还原剂在同一溶液中发生氧化还原作用,从而使金属离子还原沉积在胶件表面上的一种镀覆方法。 Ni2+ Ni
热镀锌层表面黑变机理及其控制

热镀锌层表面黑变机理及其控制摘要: 对含铅镀锌板产生黑变的原因进行了分析;提出了镀层中“杂质元素”是产生黑变的主要原因;钝化产生的不均匀相在表面形成电位差,加速了镀锌板黑变腐蚀。
关键词:镀锌板杂质钝化1.引言黑变现象一直困扰着热镀锌产品的质量,黑变对镀锌板的涂装性能无大的直接影响,但出现黑变预示着镀层到了开始老化的边缘。
而关于黑变膜的变色机理,在国内也一直众说纷纭,各有定论。
作者从镀层表面富集相造成表面电位的不均匀性,阐述了含铅镀锌板黑变产生的原因。
2.镀锌板黑变特征及构成2.1黑变膜表观特征有黑变膜的含铅镀锌板样品,其黑变膜呈不规则、不连续的黑色图案,且面积较大。
黑变膜覆盖了锌花的结晶核,予人感观已粉化。
随着镀锌板裸置时间越长,黑变膜逐渐扩大,变黑的程度也逐渐加深,故称之为镀锌板的黑变现象。
刚收到样品时,镀锌板表面覆盖的黑变膜情况见图1。
图1镀锌板表面的黑变膜2.2黑斑及黑变膜构成为详细了解黑变膜的构成,采用电镜扫描黑变膜的成分组成,并与含铅镀锌板在室温、密封、干燥环境的实验室条件下已存放两年后所产生的小黑斑,以及运输过程中产生的黑斑的成分进行对比分析。
黑斑及黑变区域元素比率见表1。
3.黑变产生原因镀锌板在存放过程中或在高温高湿度环境中使用时,镀层表面会出现发黑现象。
Zn-Al合金镀层板也出现类似现象,特别是含有Mg系列的镀层板尤为显著[1 ]。
同样,含铅镀锌板也存在发黑现象。
图2为在实验室条件下,经硝酸盐溶液及去离子水浸泡后,在高温(49℃)、高湿(R.H≥95% )条件下,镀层的光亮度随试验时间的延长而降低的变化情况。
图2镀锌层在高温高湿度条件下表面光亮度的变化3 .1“杂质”元素影响为保证热镀锌工艺的实现及改善热镀锌板的性能,热镀锌的镀液中有一定量的Al和Pb等元素。
其镀层由多相组织构成,Al、Pb等合金元素在镀层中被均匀合金化了,由于Al的存在。
镀层表面容易形成Pb等的富集相。
图1中亮点为含铅镀锌板Pb的富积区,可见黑膜成分含有较多的Pb。
三价铬与六价铬的区别
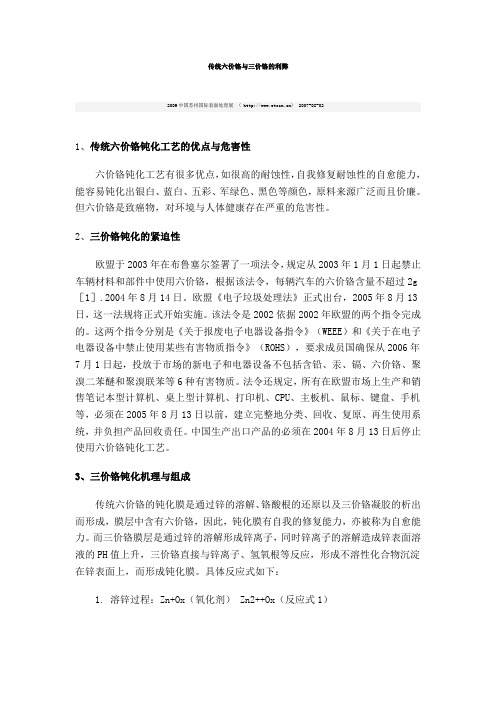
传统六价铬与三价铬的利弊2009中国苏州国际表面处理展 ( ) 2007-08-021、传统六价铬钝化工艺的优点与危害性六价铬钝化工艺有很多优点,如很高的耐蚀性,自我修复耐蚀性的自愈能力,能容易钝化出银白、蓝白、五彩、军绿色、黑色等颜色,原料来源广泛而且价廉。
但六价铬是致癌物,对环境与人体健康存在严重的危害性。
2、三价铬钝化的紧迫性欧盟于2003年在布鲁塞尔签署了一项法令,规定从2003年1月1日起禁止车辆材料和部件中使用六价铬,根据该法令,每辆汽车的六价铬含量不超过2g [1].2004年8月14日。
欧盟《电子垃圾处理法》正式出台,2005年8月13日,这一法规将正式开始实施。
该法令是2002依据2002年欧盟的两个指令完成的。
这两个指令分别是《关于报废电子电器设备指令》(WEEE)和《关于在电子电器设备中禁止使用某些有害物质指令》(ROHS),要求成员国确保从2006年7月1日起,投放于市场的新电子和电器设备不包括含铅、汞、镉、六价铬、聚溴二苯醚和聚溴联苯等6种有害物质。
法令还规定,所有在欧盟市场上生产和销售笔记本型计算机、桌上型计算机、打印机、CPU、主板机、鼠标、键盘、手机等,必须在2005年8月13日以前,建立完整地分类、回收、复原、再生使用系统,并负担产品回收责任。
中国生产出口产品的必须在2004年8月13日后停止使用六价铬钝化工艺。
3、三价铬钝化机理与组成传统六价铬的钝化膜是通过锌的溶解、铬酸根的还原以及三价铬凝胶的析出而形成,膜层中含有六价铬,因此,钝化膜有自我的修复能力,亦被称为自愈能力。
而三价铬膜层是通过锌的溶解形成锌离子,同时锌离子的溶解造成锌表面溶液的PH值上升,三价铬直接与锌离子、氢氧根等反应,形成不溶性化合物沉淀在锌表面上,而形成钝化膜。
具体反应式如下:1. 溶锌过程:Zn+Ox(氧化剂) Zn2++Ox(反应式1)Zn+2H+ Zn2++H2(反应式1a)2. 成膜过程:Zn2++xCr(Ⅲ)+y H2O ZnCrxOy+2YH+(反应式2)3. 溶膜过程:ZnCrxOy+2yH+ Zn2+ xCr(Ⅲ)+ y H2O(反应式3)三价铬钝化剂一般含有以下成份:三价铬Cr(Ⅲ):钝化膜的主要成份来源,三价铬可取硫酸铬、硝酸铬、氯化铬、醋酸铬等。
高耐磨高耐腐蚀镀硬铬技术

高耐磨高耐腐蚀镀硬铬技术烟台电镀技术研究所2014.3.8目录镀硬铬工艺操作规程。
1 镀硬铬过程中的工艺维护.。
5 代替双层镀铬的高耐蚀镀铬添加剂.。
8超硬耐磨耐腐蚀纳米复合电镀镀铬工艺.。
9不同类型工件储油缸,减震杆,活塞环电镀硬铬的研究.。
15 不含氟镀铬抑雾剂dw-026.。
18DW-032高效镀硬铬添加剂使用指南.。
19dw013镀铬液三价铬处理剂.。
27微裂纹硬铬层的获得?.。
29 油缸轴高耐蚀性镀硬铬工艺.。
30 液压活塞杆高耐蚀镀硬铬工艺操作规程.。
31液压活塞杆镀铬新工艺的研究和开发应用.。
33 液压缸活塞杆高耐蚀镀铬添加剂dw-032.。
34液压缸活塞杆镀铬.。
3538提高活塞杆镀硬铬电镀质量的方法 .。
39 连铸结晶器铜管内腔镀硬铬技术解析.。
42 结晶器铜管高效镀铬添加剂dw-032.。
44 解析液压活塞杆镀铬层的厚度和硬度匹配关系.。
45连铸结晶器铜管内腔镀硬铬新工艺与技术.。
46结晶器铜管镀硬铬故障详解.。
47结晶器铜管镀铬液铁,铜杂质的影响和去除?.。
48结晶器铜管镀铬阳极种类及形状对镀层及通钢量的影响.。
50 结晶器铜管电镀用钛铱钽阳极产品.。
51结晶器铜管镀铬添加剂试验总结.。
52结晶器铜管镀铬的工艺特点.。
53结晶器铜管电镀用钛铱钽阳极产品.。
54 减震器杆镀铬阳极形状及布置.。
55 活塞杆镀铬耐蚀性电镀工艺.。
58 活塞杆电镀无裂纹硬铬层的获得.。
59高速镀硬铬典型工艺流程.。
60高速电镀硬铬镀铬添加剂dw-032.。
62高耐磨结晶器铜管电镀工艺参数的管理.。
63镀硬铬过程中的工艺维护.。
64冷轧工作辊硬镀铬技术研究.。
67国内外液压缸活塞杆镀层的选择依据.。
78 液压缸筒镀铬技术条件.。
84 工程用铬电镀层.。
88镀硬铬工艺操作规程一、工艺介绍镀硬铬是在各种基体表面镀一层较厚的铬镀层,它的厚度一般在20μm以上,利用铬的特性提高零件的硬度、耐磨、耐温和耐蚀等性能。
第7章 电镀铬(完整版本)

图7-5 不同镀液度和电流密度下硫酸根浓度对电流效率的影响 – 45°C;---60 °C 。
当CrO3/SO42-小于100:1时,镀层的光亮性和致密 性有所提高。但镀液的电流效率和分散能力下降。
当CrO3/SO42-小于或等于50:1时,由于催化剂含量 偏高,使阴极胶体膜的溶解速度大于生成速度,阴极极 化也达不到铬的析出电势,导致局部、乃至全部没有铬 的沉积,镀液的电流效率降低,分散能力明显恶化;
图7–2 铬酸浓度与电导率之间的关系
铬酐浓度对阴极电流效率的影响示于图73和图7-4。从图7-3可以看出,在45℃和20 A/dm2的条件下,当镀液中铬酐浓度为250 g/L 时,电流效率最大,达19%。由图7-4可知,电
流效率随着铬酐浓度的降低而有所提高。例如 在55℃ 、45 A/dm2和CrO3/SO42– =100/1的条件 下,铬酐浓度为150 g/L时的电流效率比400g/L 时增大约5%~6%。但温度较低时并不服从上 述关系。
1.4 镀铬过程的特点
与其它单金属相比,镀铬液的成分虽然简单,但镀 铬过程相当复杂,并具有许多特点。
(1) 在镀铬过程中,是由铬的含氧酸即铬酸来提供获得镀层 所需的含铬离子(其它单金属电镀都是由其自身盐来提供 金属离子),属强酸性镀液。在铬酸镀液中,阴极过程相 当复杂,阴极电流大部分都消耗在析出氢气及六价铬还原 为三价铬两个副反应上,故镀铬过程阴极电流效率极低, 一般ŋ=8%~18%。
三价铬取代六价铬电镀的技术研究

三价铬取代六价铬电镀的技术研究首先,我们来了解一下三价铬电镀的原理。
传统的六价铬电镀主要是通过将铬酸根离子(CrO3)转化为六价铬阳离子(Cr6+),而在三价铬电镀中,则是通过将三价铬(Cr3+)溶解在电镀液中,并在阳极处进行氧化反应,最终生成耐腐蚀的三价铬膜。
与六价铬电镀相比,三价铬电镀的原理更加环保,不会产生有害物质。
其次,我们来看看目前对三价铬电镀技术的研究进展。
近年来,许多研究机构和企业开始致力于三价铬电镀技术的研究与开发。
研究者通过改变电镀液配方、优化电镀工艺以及引入新的添加剂等方法,不断提高三价铬电镀的电镀速率、电镀质量和耐腐蚀性能。
此外,还有一些新型的三价铬电镀技术得到了广泛关注,如化学镀铬、电化学沉积、反应沉积等。
这些新技术在改善传统三价铬电镀存在的问题和弊端的同时,也为工业界提供了更多选择。
最后,我们来讨论一下三价铬电镀技术的应用前景。
随着全球环境保护意识的提升和环境法规的更加严格,对传统六价铬电镀的限制将越来越多。
而三价铬电镀正是作为一种环保、低污染的替代技术而被广泛研究和应用。
三价铬电镀可以应用于多个领域,如汽车制造、电子设备、航空航天等。
它能够提供与六价铬电镀相媲美的电镀性能,同时减少环境污染和对操作员的健康风险。
因此,未来三价铬电镀技术有望取得更大的突破,并逐渐替代传统的六价铬电镀。
综上所述,三价铬电镀技术的研究是十分重要的,它能够解决六价铬电镀中存在的环境污染和健康风险问题。
通过不断改进电镀液配方、优化电镀工艺以及引入新的添加剂等方法,三价铬电镀技术在电镀速率、电镀质量和耐腐蚀性能方面取得了显著进展。
未来,三价铬电镀技术有望广泛应用于汽车制造、电子设备、航空航天等领域,并逐渐取代传统的六价铬电镀。
这将为我们提供更环保、更可持续的电镀解决方案。
电镀铬的工艺及应用

2 镀铬的分类及应用
镀铬可按其工艺及溶液不同来分类,所得到的铬层可应用于不 同的场合。 1)按工艺: (1) 防护装饰性镀铬 利用铬镀层的钝化能力、良好的化学稳定性 和反射能力,铬层与铜、镍及铜锡合金等组成防护装饰性体系,广 泛用于汽车、自行车、缝纫机、钟表(历史上聘礼三大件)、仪器 仪表、日用五金等零部件,既保持产品表面的光亮和美观,又达到 防护目的。 这类铬层的厚度一般为0.25µm~1µm。
0.54 0.19 淬火钢与青铜
0.30 0.20 淬火钢与巴比特合金
静 摩 擦 滑动摩擦
系数
系数
0.06 0.05 0.08 0.22 0.11 0.19
• 三一是中国最大、全球第五的工程机械制造商“创建一流企业 ,造就一流人才,做出一流贡献”(挖掘机录像)
(4)光学性能
铬镀层具有良好的化学稳定性,碱、硫化物、硝酸和大多数 有机酸对其均不发生作用,但能溶于氢卤酸(如盐酸)和热的硫酸中。
(5) 黑铬 与其它上黑色镀层(如黑镍镀层)相比,有较高的硬度,
耐磨损及耐热性能好,而且有极好的消光性能。常用于光学仪器、 航空仪表等零件的镀覆。此外,黑铬镀层也可用于装饰。
2) 按镀铬溶液组成及性能
((1)普通镀铬液 以硫酸根作催化剂的镀铬溶液。铬酐和硫
酸的比例一般控制在CrO3/H2SO4:100/1,铬酐浓度在150g/L~ 450g/L之间变化。根据铬酐浓度的不同,可分成高浓度、中等浓 度和低浓度镀铬液。习惯上把CrO3 250g/L和H2SO4 2.5g/L的中 等浓度镀液称之谓“标准镀铬液”。低浓度镀液的电流效率较高, 铬层的硬度也较高,但覆盖能力较差;高浓度镀液稳定,导电性好, 电镀时槽电压较低,覆盖能力较稀溶液好,但电流效率较低;标准 镀铬液的性能介于两者之间。
电镀六价铬讲议

电镀六价铬讲议下面我将从电镀六价铬的工艺范围,开缸配槽顺序及注意事项,电镀槽及其辅助配制,各组份作用及电镀机理,不良现象的原因分析,镀液维护管理,六大方面进行讲解:一六价铬的工艺参数:CrO3 : 270—300 g/l 控制点: 290 g/lCS-2 : CrO3重量的1%.H2SO4:0.8-1.2g/l.Cr3+ :0.8-1.2 g/l. (这一项我司没控制)阳极采用铅锡合金.一定量的抑雾剂.温度:38-42O C.阴极电流密度6-12A/dm2.阴阳极面积比:阴极:阳极=1:1.5-2.二电镀槽及其辅助配制:1> 不锈钢内衬PVC(PVC不能有破损现象).2> 温控系统:温度自动控制仪,电笔,冷水系统.3> 带软起动的电源(波纹系数7以下):4> 抽风系统.(侧抽和顶抽是防止生产环境恶化,化学镍漏镀以及焦铜漏镀的保证)5> 打气管.三开缸配槽顺序及注意事项:1> 先用砂碳水将电镀槽清洗干净,若制作过程中有油污,可用洗衣粉清洗干净.并用干抹布抹干.2> 往电镀槽中注入70%体积的纯水.3> 打开抽风,开启打气的情况下,慢慢加入计算好的铬酐,继续打气,直到铬酐完全溶解.并将水补充至标准水位.4> 加入铬酐重量1%的CS-2,并搅拌均匀.5> 加入计算量的CP级硫酸.并搅拦均匀.6> 用大阴极,小阳级电解(阴极电流密度约3A/dm2)6-8小时,调整温度即可试镀.也可用添加无水乙醇来产生三价铬. 无水乙醇的体积相当于镀液体积的0.11%.注意事项:操作时必须穿戴好防护用具,如:围裙,手套,胶鞋,防护面具等到.因铬酐具有挥发性,酸性,强氧化性和腐蚀性.若粘上皮肤要水清洗干净.四各组份作用及反应机理:1> 铬酐:是导电盐和主盐,在水常水溶液中以重铬酸(H2Cr2O7)形式存在.它可电离成: H2Cr2O7------2H++Cr2O72-具有导电作用,其中Cr2O72-是电镀铬时的主盐.电镀时其在SO42-催化作用化学反应方程式如下:Cr2O72-+8H++6e---- Cr2O3+4H2O <1>2H++2e----H2 <2>Cr2O72-+H2O===2 CrO42-+2H+ <3>CrO42-+8H++6e---- Cr +4H2O <4>阴极电流密度(A/dm2)阴阴电位/V通电开始时,电压较低(小于φ1),这时阴极电流会随电压升高而升高,主要发生以上<1>反应.即电解产生三价铬.因此配制新槽,或旧槽电镀液三价铬偏低,要升高三介铬时,可采用此法提升三价铬,并最好开启打气.再随着电压升高,达到氢离子析出电位,则<1>和<2>反应同时进行.在bcd 段落,会出现随着电压升高,电流下降的怪现象.这是什么原因呢?原来<1>和<2>的电化学反应都要消耗大量的H+.而电镀铬时是不打气搅拌的,在阴电极界面上PH值会升高,形成一层碱式铬酸铬胶体膜(Cr(OH)3.Cr(OH)CrO4)覆盖在阴极表面.电阻增加,故电流会下降.另当阴极表面附近PH值升高时,重铬酸阴离子会发生如<3>可逆化学反应: 阴极表面附近CrO42-迅速增加.当电位达到铬离子析出电位φ2时,即d点,电化学反应<4>也开始起进行,镀铬开始.在de段:4个反应同时进行,并随着电位负移,并随电流升高,镀铬速度加快.铬酸酐的浓度控制在270—300 g/l,理论上随着铬酸酐的浓度增加,镀液的导电性会提高,镀液的覆盖能力也会提高,两阴极的电流效率会降低.但带出消耗增加,增加电镀成本,污染加重,更不利于环保,且随着镀铬添加剂的开发,它的浓度有下降盐趋势.2> 硫酸根(SO42-)的作用:覆盖在阴极表面的碱式胶体膜,在硫酸的催化作用下发生溶解:(HO)2==Cr—CrO4—Cr==(OH)2+2SO42-→SO4==Cr--- CrO4---Cr== SO4 (可溶性)→CrO42-以上反应只会在局部发生,并慢慢扩展,因此露出的通电面积小,真时的电流密度大,<4>反应才得以顺利进行.在新生的铬镀层上同时以会有<1>反应,产生三价铬膜,如此反复.铬层起来越厚.H2SO4的含量控制在0.8-1.2g/l.若H2SO4的含量偏高,镀层的光亮度和致密性要好,但电流效率和覆盖能力变差,若H2SO4的含量偏低,镀层发花,粗糙和致密性要差,覆盖能力变好.3> 三价铬的影响:铬酸酐和硫酸根是电镀铬的必要条件,但一定量的三价铬存在有利于电镀出优良的铬镀层,提高镀铬的电流效率:这一项我公司没有控制,建议控制在:Cr3+ :0.8-1.2 g/l.三价铬低:沉积速度慢,镀层软,覆盖能力差:三价铬高:镀层发暗,粗糙,光亮电流密度范围变小,电镀时易发白,调小电流又易发黄.这就是我们平时说的又黄又烧.4> 稀土(CS-2)的作用:它实际上是一种催化剂的作用,能降低极化曲线,提高镀液的覆盖能力.提高电流效率,降低铬酐的浓度.减少带出消耗和污染.降低能耗.增加镀层的硬度.镀铬的阴极极化示意图:1为没加稀土;2为加了稀土.加入稀土后,阴极的极化曲线形状没变化,但相应的峰电流和谷电流都降低,图中峰电流对应的电位φ1是Cr6+还原成Cr3+的电位.峰电位下降,表明需使用的电流咸少,因而电流效率升高;谷电流下降,意味着析铬的临界电流密度下降,相应提高电流效率,分散能力和覆盖能力.另:加入稀土后,也改变了碱式胶体膜的结果,导致膜的电阻增加,有利于放电离子CrO42-在阴极的富集和放电,增加了析氢的过电位,使析氢减少,提高了电流效率.加入稀土后,镀层结晶结构也会发生变化,结晶更细腻,光亮度,硬度都会提高.5> 阴极电流密度的影响:我司体系的六价光铬的阴极电流密度控制在6-12A/dm2.最佳值为8A/dm2,除太高会烧铬,太低工件会发黄外,还会有以下影响.太高或太低产品的硬度,耐磨性,铬层的韧性,和镀层的结合力都会降低.但电流效率和覆盖能力会随电流密度增加而升高.6> 温度的影响:我司体系的六价光铬的温度控制在38-42O C.最佳质为40O C.除太高镀铬覆盖能力不好,太低镀铬易发白外,还会有以下影响.太高或太低产品的硬度,耐磨性,铬层的韧性,和镀层的结合力都会降低.但电流效率会随电流密度增加而升高.7> 空气搅抖:电镀铬时不需空气搅拌,搅拌时镀铬的覆盖能力差,甚至镀不上铬,这是因为空气功搅拌不利于在阴极附近形成局部碱性条件,也就不利于胶体三价铬膜的形成.空气搅拌只在加料时使用.8> 阳极:电镀铬时不能用铬条作阳极,而必须用铅或其合金的不溶性物质作阳极,这是由镀铬有别于电镀铜,镍的特殊性决非定的.<1> 镀铬时若用铬作阳极,阳极的电流效率可高达100%;而由于电极电位的原因,电镀铬时会伴随大量的析氢反应,电流效率只有15%左右.这样会造成电镀液中铬的浓度不断升高.<2> 铬有多个价态:(0,2+,3+,6+),电镀铬时,阴板是由多个反应后,六价铬转变成铬.而阳极的铬单质既会转变成六价铬,也可转变成三价铬,且以三价铬为主.这会造成三价铬不断升高,无法镀铬.<3> 若用铅或其合金作阳极:则电镀生产时阴极产生的三价铬的速度和阳极三价铬还原成六价铬的速度相差不多,可保持镀液中三价铬的稳定性.因阳极还伴随水电解析氧的反应.反应方程式式如下:2Cr3+--6e+7H2O→Cr2O72-+14H+2H2O--4e→O2+4 H+9> 阴阳极面积比:电镀生产时阴阳极比率的控制对稳定镀液的三价铬含量非常重要.一般要求:阴极:阳极=1:1.5-2.若比例偏小,三价铬会降低;若比率偏大,三价铬会升高.五不良现象的分析:1> 镀铬发白:生产时产生镀铬发白有许多原因:以下逐个分析:<1> 整流机的波纹系数不稳定,检测整流机的波纹系数是否在8以下.(这种情况不易发生).<2> 检查镀槽的加热电笔是否有漏电现象,若漏电会干扰镀铬的电力线造成镀铬发白.<3> 镀槽的PVC衬板是否有破损现象,若有会产生双极性电镀现象,镀铬时也会有发白现象.<4> 电镀生产过程式中是否有断电,若断电会产生二次镀铬,也会有发白现象.<5> 光镍光剂是否偏多,若光镍光剂多,则镍层的活性不好,电镀量也会发白.<6> 镀镍后到镀铬的时间不宜太久,否则镍层表面会被氧化成一层较厚的氧化膜,镀铬易发白.<7> 电镀镍后要用PH=3左右的稀硫酸水溶液活化镍层表面的氧化层,否则也易发白.<8> 镍层经硫酸活化后,要用含铬酐10g/l的稀铬水钝化,可避免发白.<9> 镀液的温度是否偏低,否则电镀铬时也易发白.<10>生产环境:若生产环境差,有许多酸,碱雾,油烟也会产生发白现象.2> 镀铬发黄:<1> 使用的阴极电流密度是否太小,计算电流密度是否在6-12A/dm2.<2> 挂具是否导电良好,电镀生产时,有些飞巴或挂具导电不良,而整流机显示的电流则是4臂的总电流.<3> 生产时是否有电流产生,整流机是否有问题.<4> 电镀铬时,使用的电流密度大,挂具是否导电良好,挂具的铜排是否导电足够.检查挂具是否发热严重.<5> 挂具和工件的导电接触是否足够,否则塑胶电镀时,接触点会被击穿,造成工件不通电,镀铬发黄.<6> 工件在挂具上是否固定良好,若工件固定不好,受打气和镀液浮力影响而摇动,镀铬也会发黄.<7> 镀液的温度是否太高,检测温度.<8> 生产时是否开有打气.镀铬时不能开启打气.<9> 镀铬溶液是否正常:如铬酐是否太低和硫酸是否太高, 进行化学分析: 3> 产品既黄又烧:<1> 产品的结构是否过于复杂,整个产品电镀所需的电流密度分布过广.<2> 生产用挂具的设计是否合理,如产品排布过密.不利于镀铬走位.<3> 镀液的硫酸太高,铬缸的走位能力很差.<4> 镀液的三价铬太高.怎样区别产生既黄又烧的原因是<3>还是<4>呢?若平时电镀使用的电流是500A/臂.现用500A电流电镀时,产品会发黄,再调高电流时,产品出现既黄又烧现象,则可断定:可能是镀液的硫酸含量太高:若用500A电流电镀时,产品会发白,再用400A电流电镀时, 产品出现既黄又发白现象,则镀液的三价铬太高.六镀液的维护和管理:1> 平时生产时只需将温度自动控制即可,若镀缸没有电镀,则温度会低于工艺要求的38-420C.这时铬缸配备的电笔(石英,不锈钢,钛,铁氟笼材质都行)就会自动加热:若在生产时,因镀铬的电流大,镀液温度会升高,则铬缸配备的钛管冷水系统就会工作.确保镀液温度维持在工艺范围.2> 连续生产时,镀液每天分析和加料两次即可:一般需添加的有:铬酐,硫酸,CS-2(铬酐重量的1%)以及少量的铬抑雾剂.3> 若阴阳极面积比率合理的话,镀液中三价铬含量变化不会太大,因此一周分析两次即可.但目前我们使用的一些分析方法误差都较大:如氧化滴定法,比色法等.若三价铬太高,可用大阳极,小阴极,大电流密度扯低:若三价铬太低,可用小阳极,大阴极,开启打气,小电流密度扯高.4> 平时生产时,不需循环过滤,打气,摇摆.5> 加料时必须在铬缸没生产时,因加料需开打气.6> 每10天左右,最好用10U的棉芯过一次缸滤,除去阳极泥,掉落的工件等.并分析加料才能生产.7> 清缸或不生产时,要将阳极“铬条”取出,并用钢丝刷将其表面的黄色氧化铅除去,保证生产时阳极导电良好.8> 生产时要经常检查阳极导电是否良好,若生产时阳极附近有汽泡冒出,则表明阳极导电,否则就是导电不良.9> 电镀镍后,工件要清洗干净,避免将镍杂质,光剂过多带入铬缸.10>及时打捞掉缸的工件.。
【镀铬标准】电镀工艺的规范--镀铬工艺镀铬标准

【镀铬标准】电镀工艺的规范--镀铬工艺镀铬标准【镀铬标准】电镀工艺的规范--镀铬工艺镀铬标准话题:镀铬标准休闲阅读催化剂的作用协同作用镀铬四、规范镀铬工艺铬面是凹版制版公司的一张脸面,可以直接为公司赢得客户的信赖。
光洁的铬面,超凡的耐印力,令人满意的刮刀消耗,无不对客户产生着巨大的吸引力。
镀铬层印刷时直接与承印材料接触,要能有效地保护铜层不被刮伤、刮坏,因此,要求铬层要达到一定的硬度。
铬层的高硬度和表面硬度均匀是提高凹版滚筒耐印力的关键,如果印数达到50万印,则铬层硬度在HV750,HV950、耐印力在80万,100万次为佳。
目前业内普遍采用镀硬铬工艺,有的公司还采用瑞士镀铬工艺,以保证铬层有很高的硬度、很好的耐磨性及化学稳定性,从而提高印版滚筒的耐印力,使其能够承受刮墨刀及油墨中颜料的频繁摩擦。
当前全国各地凹版制版公司都深深感受到镀铬质量是个永远的问题,是造成返工的一个主要因素。
影响镀铬质量的因素很多,也很复杂,铬层硬度与温度、电流密度、铬酐及硫酸的含量有着密切关系。
归纳一下,笔者认为主要有三大影响因素:一是导电性不良,二是镀铬液不稳定,三是清洗不干净,还有些公司虽然制定了质量标准和控制数据,但员工在执行时不认真,不严格,造成返工。
因此,必须强化管理,严格管理。
(一)镀铬工艺流程雕刻好滚筒?检查(合格)?装配?滚筒清洗?镀铬?抛光?自检(合格)?交总检(不合格退铬)。
(二)镀铬的基本原理镀铬液中铬酸一般以重铬酸形式存在(H2Cr2O7),在浓度很高的镀铬液中可以三铬酸(H2Cr3O10)和四铬酸(H2Cr4O13)的形式存在。
当镀液中只有铬酸而无硫酸等催化剂存在时,通入直流电,阴极上只有氢气析出,没有铬层沉积,相当于电解水。
加入适当的硫酸催化剂后(CrO3?H2SO4=100?1),在阴极上依次发生下列反应:Cr2O72-,8H+ +6e ? Cr2O3+4H2O ?2H,,2e ? H2? ?Cr2O72-+ H2O2CrO42-+2H+ ?CrO42-+ 8H+ +6e ? Cr?+4H2O ?由以上反应可知,镀铬的阴极反应是很复杂的。
镀铬工艺流程

镀铬工艺流程1、铁件镀铬工艺流程:除蜡→ 热浸除油→ 阴极→ 阳极→ 电解除油→ 弱酸浸蚀→ 预镀碱铜→ 酸性光亮铜(选择)→ 光亮镍→ 镀铬或其它除蜡→ 热浸除油→ 阴极→ 阳极→ 电解除油→ 弱酸浸蚀→ 半光亮镍→ 高硫镍→ 光亮镍→ 镍封(选择)→ 镀铬2、锌合金镀铬工艺流程除蜡→ 热浸除油→ 阴极电解除油→ 浸酸→ 碱性光亮铜→ 焦磷酸铜(选择性)→ 酸性光亮铜(选择性)→ 光亮镍→镀铬3、不锈钢直接镀铬工艺1) 电化学除油→热水洗→冷水洗→浸酸活化(1ml/L HCL、10ml/L H2SO4,室温,半分钟;适用于自动线上不锈钢镀铬,不宜镀铜或镍)→水洗→镀铬。
2)阴极电化学除油→清洗→阳极活化(10A/dm2)→直接镀铬.3) 化学除油→清洗→阳极电化学除油(0.5A/dm2)→清洗→浸酸活化(1ml/L HCL、10ml/L H2SO4,室温,45S)→清洗→镀铬注:镀铬时,应先用是正常电镀时电流密度的1。
5~2倍镀3~5分钟,然后再正常电流密度电镀,要尽量缩短各工序之间的过渡引起的停留时@@@@@@@@@@@@@@@@@@@@@@@@@@@@@@@@@@@@@@@@@@@@@@@@@@电镀相关基础知识一、基础化学知识1.盐酸有何特征?答:纯净的盐酸是无色透明的液体,一般因含有杂质三氯化铁而呈黄色。
常用浓盐酸中约含37%的氯化氢。
盐酸易挥发,是一种强酸。
在电镀生产中广泛使用盐酸作为浸蚀剂。
2.硫酸有和特征?答:浓度为96%的硫酸溶液,比重为1.84.浓硫酸具有吸水性,吸水过程中放出大量的热量。
在电镀生产中广泛使用硫酸作为浸蚀剂,由于其挥发性低,所以可利用加热提高浸蚀速度。
3.硝酸有何特征?答:硝酸是一种氧化型的强酸,在见光受热时分解放出氧而使别的物质氧化,所以硝酸应盛在棕色瓶内,电镀生产中广泛使用权有作为浸蚀剂。
4.现有浓盐酸、浓硝酸、浓硫酸各一坛,能凭目测将它们分辨出来吗?答:冒白雾的是盐酸,冒黄烟的是硝酸,无烟雾的是硫酸。
三价铬和六价铬的区别
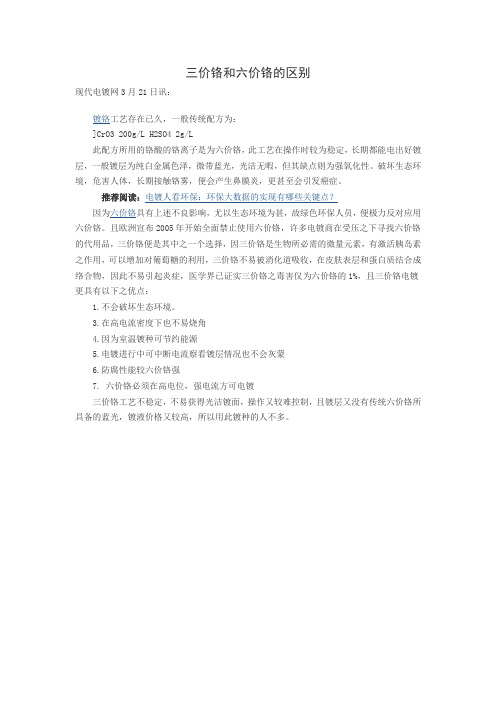
三价铬和六价铬的区别
现代电镀网3月21日讯:
镀铬工艺存在已久,一般传统配方为:
]CrO3 200g/L H2SO4 2g/L
此配方所用的铬酸的铬离子是为六价铬,此工艺在操作时较为稳定,长期都能电出好镀层,一般镀层为纯白金属色泽,微带蓝光,光洁无暇,但其缺点则为强氧化性。
破坏生态环境,危害人体,长期接触铬雾,便会产生鼻膜炎,更甚至会引发癌症。
推荐阅读:电镀人看环保:环保大数据的实现有哪些关键点?
因为六价铬具有上述不良影响,尤以生态环境为甚,故绿色环保人员,便极力反对应用六价铬。
且欧洲宣布2005年开始全面禁止使用六价铬,许多电镀商在受压之下寻找六价铬的代用品,三价铬便是其中之一个选择,因三价铬是生物所必需的微量元素,有激活胰岛素之作用,可以增加对葡萄糖的利用,三价铬不易被消化道吸收,在皮肤表层和蛋白质结合成络合物,因此不易引起炎症,医学界已证实三价铬之毒害仅为六价铬的1%,且三价铬电镀更具有以下之优点:
1.不会破坏生态环境。
3.在高电流密度下也不易烧角
4.因为室温镀种可节约能源
5.电镀进行中可中断电流察看镀层情况也不会灰蒙
6.防腐性能较六价铬强
7. 六价铬必须在高电位,强电流方可电镀
三价铬工艺不稳定,不易获得光洁镀面,操作又较难控制,且镀层又没有传统六价铬所具备的蓝光,镀液价格又较高,所以用此镀种的人不多。
- 1、下载文档前请自行甄别文档内容的完整性,平台不提供额外的编辑、内容补充、找答案等附加服务。
- 2、"仅部分预览"的文档,不可在线预览部分如存在完整性等问题,可反馈申请退款(可完整预览的文档不适用该条件!)。
- 3、如文档侵犯您的权益,请联系客服反馈,我们会尽快为您处理(人工客服工作时间:9:00-18:30)。
1.1为满足不同客户对产品表面电镀处理的不同要求,防止外壳电镀Cr3+与Cr6+的产品混装、混用;
1.2防止因产品表面电镀处理不同的混装,而导致组装不良的流出。
2.适用范围
本规程适用于浙江环方汽车电器有限公司所有电镀Cr3+与Cr6+外壳的区分管理。
3.职责与权限
3.1生产部负责电镀厂家、库存管理及制造过程的标识与管理;
3.2质管部负责入库检查及对电镀产品整个过程的标识和监控管理。
4.一般原则
4.1没有特殊要求的外壳产品电镀Cr3+采用白色、兰白色,电镀Cr6+采用彩色;
4.2特殊客户要求电镀Cr3+彩色的外壳,必须采用特殊的产品标识;
4.3只有质管部下属的检验科才能对从电镀厂电镀完成转至公司司内部的外壳进行内部包装的转换工作;
4.4仓库物流人员将相关外壳件转至电镀厂电镀加工时,必须实行统一的蓝色塑料箱包装,并在开的票据上注明箱数数量与电镀要求;
4.5电镀厂产品防护包装要求:
4.5.1电镀Cr3+与Cr6+采用统一的蓝色塑料包装;
4.6公司内部检验完成后的产品包装要求:
4.6.1电镀Cr3+与Cr6+采用统一的蓝色塑料包装,并在每箱放置检验合格证并注明产品型号及电镀色别或电镀颜色要求;
4.7在任何状态下的产品都必须要有产品标识,对没有产品标识的产品,不得使用,作为不合格品处理;只有通过检验科重新确认或重新检验后按照相关要求进行检验标识包装后方可正常使用;
5区分管理流程
5.1生产部在编制生产派工单时必须在单上注明电镀的颜色要求与电镀状态;
5.2仓库在进行产品转序电镀出库时,必须在出库单上注明产品的箱数及数量,并附上产品流动卡,出库必须按4.4的包装要求严格执行;
5.3电镀加工厂在收到加工指令后,必须严格按照出库单票据或图纸的要求进行电镀加工,并进行有效标识、包装及送货;
5.4仓库在收到电镀厂加工完成后的产品时,必须将对方出示的送货单与本厂出库的单票据进行核对,对电镀处理、包装要求等不相符的产品及时反馈质管部相关人员进行处理;
产品及进反馈质管部相关人员进行处理;
5.5仓库对电镀厂送货产品进行确认无误后,填写产品电镀工序报检单,注明电镀的状态及数量报与检验科检验;
5.6检验科接到报检单后必须按《三价铬与六价铬分辨试验操作规程》对产品Cr3+与Cr6+的状态进行检验确认;并按《外观检验作业要领书》对产品的外观进行检验、转换包装方式;
5.7检验科检验及包装转换完成后将产品与检验结果反馈给仓库,不合格品按《不合格品管理程序》执行,对合格品进行入库记录后方可向组装车间发料进行生产;
5.8组装车间按照生产部生产派工单的生产要求领用外壳,对不符合产品生产要求及包装要求的产品不予领用,对存在异议的产品报与质管部门进行处理;
6.任何部门及科室个人都必须严格遵守本规定,如有违反将依据公司相关制度进行处罚。
7.相关文件
7.1《不合格品管理程序》
7.2《三价铬与六价铬分辨试验操作规程》
7.3《外观检验作业要领书》
8.记录和表格
《外协、外购件入厂报检及检验单》
编制/日期
黄勇干
2011.9.10
审核/日期批准/日期。