高炉制粉喷煤技术的研究与应用
喷煤自动控制新技术在3#高炉的应用

Li e l ng u W no
( e r n ma i gP a t N w Io - kn ln )
Absr c Afe uz y c n r ltc noo y b i g a pe sd o r vo sp v rz d c a ngn e ig e p re c n he t a t: trf z o to e h l g e n do td ba e n p e iu ule ie o le i e rn x e n e a d t i
铁新厂 3 高炉使用一种新 的控制模式来解决喷煤量 #
波 动的问题 , 高炉稳定顺行 高产低耗创造条件 。 为
待、 喷吹 、 卸压 、 再装 粉 的程序循 环交错 地运 行。当 其 中一个罐在喷吹时另一个罐在进行装粉 、 加压 、 等
2 1 年第 3 01 期
南钢 科技与 管理
6 l
Ke o d :ls f n c ; u z c n o ; ol ne t n r e y w r s bat u ae fzy o t l c a i c o a r r j i t
前 言
高炉喷煤 技术 是 高炉 系 统结 构优 化 的 中心环
1 喷煤工 艺流程
3 高炉煤粉喷吹系统 是 由煤粉仓 、 # 喷吹 罐、 合 混
20k/ , 2 gt设备最大能力 为 20k/。煤粉 喷吹工 艺 5 gt
流 程 如 图 1所 示 。
是维持炉温稳定 、 保证炉况顺 行 , 使得高炉达 到最佳
冶炼状态的重要基础 。 根据高炉喷煤工艺 特点 , 高炉 喷煤量 调节控 制
容 易 受 煤 粉 煤 质 、 动 性 能 、 度 、 度 、 况 的 波 流 湿 粒 炉
高炉矿粉_煤粉复合喷吹研究
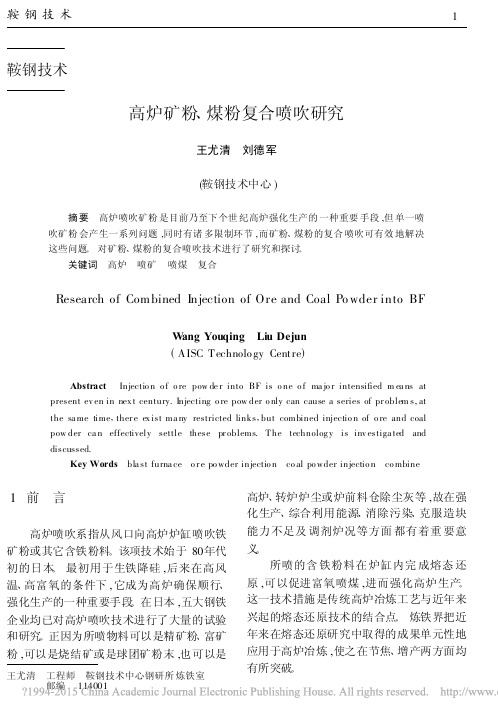
鞍钢技术高炉矿粉、煤粉复合喷吹研究王尤清 刘德军(鞍钢技术中心) 摘要 高炉喷吹矿粉是目前乃至下个世纪高炉强化生产的一种重要手段,但单一喷吹矿粉会产生一系列问题,同时有诸多限制环节,而矿粉、煤粉的复合喷吹可有效地解决这些问题。
对矿粉、煤粉的复合喷吹技术进行了研究和探讨。
关键词 高炉 喷矿 喷煤 复合Research of Combined Injection of Ore and Coal Po wder into BFW ang Youqing Liu Dejun(AISC Technolo gy Centre)Abstract Injectio n o f o re pow de r into BF is o ne o f ma jo r intensified m ea ns at present ev en in nex t century.Injecting o re pow der o nly can cause a series of pr oblem s,atthe sa me time,ther e ex ist ma ny restricted links,but combined injectio n of o re and coalpow der ca n effectively settle these pr oblems.T he technolog y is inv estiga ted anddiscussed.Key Words bla st furna ce o r e po wder injectio n co al po wder injectio n co mbine1 前 言高炉喷吹系指从风口向高炉炉缸喷吹铁矿粉或其它含铁粉料。
该项技术始于80年代初的日本。
最初用于生铁降硅,后来在高风温、高富氧的条件下,它成为高炉确保顺行、强化生产的一种重要手段。
在日本,五大钢铁企业均已对高炉喷吹技术进行了大量的试验和研究。
高炉喷煤系统升级改造及应用

管理及其他M anagement and other 高炉喷煤系统升级改造及应用郭志勇摘要:高炉喷煤系统自建成投产,虽然进行了部分改造,基本能够满足实际生产需要,但是逐渐暴露出制粉系统存在产量低、废料含碳量高、仓顶除尘器经常积粉,喷吹系统自动化控制程度偏低。
喷煤车间及相关单位针对实际生产中存在的问题,通过生产实践、调查,经相关单位论证后,对高炉喷煤系统自动化控制程序进行在线升级;还利用高炉停炉中修的机会对制粉系统设备进行改造。
关键词:喷煤系统;升级改造;自动化控制1 背景1#高炉喷煤系统虽能满足高炉基本喷吹煤粉要求,但实际生产中存在能耗高、可控性差、产能低、劳动强度大等诸多不利因素,制约着高炉冶炼,并形成一定的工艺隐患。
另外,喷煤系统设备实现大型化后、部分自动控制空白,使操作起来掌控性能差。
利用此次高炉停炉中修,提前对喷煤系统各个环节进行论证、实施。
(1)中速磨制粉系统能耗高,高炉煤气、焦炉煤气使用量大。
在高炉对煤粉质量要求持续提高的情况下,1#高炉制粉中速磨台时产量为试点,开展一系列的制粉操作攻关,在经过长期的、大量的对制粉数据进行比对,摸索出了一套新的操作方法,达到即稳定了制粉参数,又降低了高炉煤气、焦炉煤气使用量的目的。
(2)中速磨进风口内部出现积粉,有自燃的重大安全生产隐患。
1#高炉制粉系统中速磨由于进风口在废料口上方,废料堆积成块,导致废料口无法关严,使磨机进口氧含量难以控制在6%以下;其次干燥气温度高于烟煤燃点;还有进风口与磨机连接处的死角,造成煤粉的大量堆积,成为生产中重大的安全隐患。
(3)中速磨磨辊密封风管的磨损导致备件费用高,给磨机造成严重的安全隐患。
1#中速磨磨内 “密封风环管”与三个磨辊连接原为带网金属波纹软管连接,带网金属波纹软管外延部分处在磨机气流上升区域磨损严重。
使用周期不能达到设计标准。
当带网金属波纹软管磨破后,造成磨辊内进入煤粉,导致磨辊内油质变质,磨辊轴承的使用寿命缩短,给磨机带来严重的安全隐患,带网金属波纹软管更换频繁,备件费用居高不下。
高炉喷吹煤粉的预热技术

高炉喷吹煤粉的预热技术浏览:292次评论:0条高炉煤粉喷前预热技术是目前高炉喷煤领域的前沿技术。
该技术是安全的利用原排入大气的热风炉废气的潜热,通过特殊的换热器由热媒传给煤粉再喷入高炉,该技术在某高炉投入工业应用后,生产状况、成本控制都有一定的提高。
1 概述高炉煤粉喷前预热技术是目前高炉喷煤领域的前沿技术。
该技术是安全的利用原排入大气的热风炉废气的潜热,通过特殊的换热器由热媒传给煤粉再喷入高炉,该技术在某高炉投入工业应用后,生产状况、成本控制都有一定的提高。
2 理论依据喷入高炉内有效空间的煤粉,从燃烧学出发,对于煤粉的燃烧过程,燃烧空间和燃烧时间都是非常重要的条件。
燃烧空间不够或燃烧时间不足都将导致煤粉不完全燃烧,以致浪费能源并引起环境污染、高炉操作条件恶化等一系列问题。
高炉煤粉喷枪位于直吹管的前端,离高炉风口回旋区很近,一般大型高炉直吹管的内径为200mm左右,连同风口回旋区在内的煤粉燃烧空间很小。
另外,直吹管内正常的热风速度达100~200m/s,所以煤粉的停留时间有限,一般认为只有10ms左右,以平均粒径为0.074mm(200)的煤粉为例,难以满足其燃烧时间要求。
计算表明,0.074mm的煤粉在高炉条件下,其燃尽时间一般都在几十毫秒范围内。
由于煤粉处在很高的加热速率下,煤粉燃烧的预热、干燥、脱气、挥发、着火、挥发分燃烧以及半焦燃烧等过程交叉进行。
具体而言,高炉喷吹煤粉颗粒的预热、干燥、脱气和挥发过程几乎是同时进行,而挥发物的着火燃烧以及半焦燃烧也几乎是同时进行的。
因此,在有限空间内和有限时间内提高煤粉的燃烧率,是高炉煤粉喷吹的重要课题。
研究表明,提高可燃混合物的初始温度,可显著提高火焰传播速度。
主要原因是可燃混合物的温度提高后,把它预热到着火温度的时间就缩短了。
气体导热系数随温度升高而增加,它也促使燃烧反应速度加快。
因此,现代的喷煤理论认为高喷煤比要有以下特点:(1)煤粉必须在离开喷枪尖部的一瞬间立刻燃烧,燃烧不发生在回旋区内。
新喷煤技术在3200m3高炉中的应用
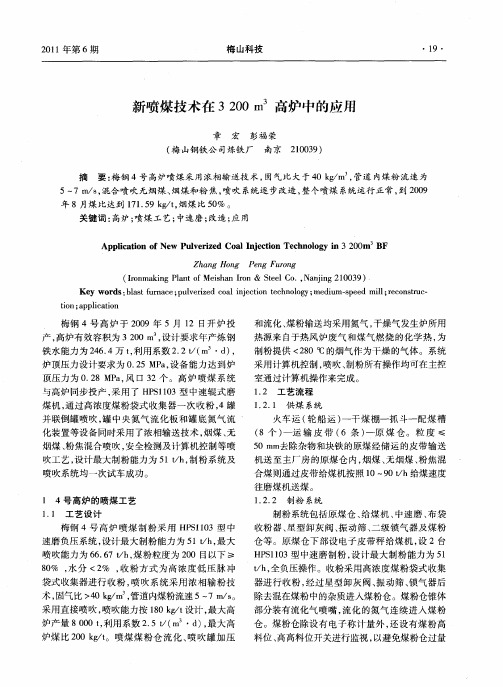
・
2 0・
梅 山科 技
2 1 年第 6期 0 1
装 入煤粉 或 出现空 料 的现象 。
12 3 喷吹 系统 ..
量精度 ≤1 。喷 吹系统 可按 程序 自动倒 罐 , 可 % 也 由操作 人 员手动控 制 。
13 技术 要求 .
喷 吹 系统位 于收粉 系统 下部 , 由煤 粉仓 、 吹 喷
炉 顶压 力设 计 要求 为 0 2 P , 备 能 力达 到 炉 .5M a设 顶 压力 为 0 2 a 风 口 3 .8MP , 2个 。 高 炉 喷 煤 系 统 与 高 炉 同步投 产 , 采用 了 H S 13型 中速辊 式 磨 P 10
制粉提供 < 8 2 0℃的烟气作为干燥的气体。系统 采用计算机控制, 喷吹、 制粉所有操作均可在主控 室通 过计 算机 操作来 完成 。
( 8个 ) 运 输 皮 带 ( 条 ) 原 煤 仓 。 粒 度 ≤ 一 6 一
烟煤 、 粉焦混合喷吹 , 安全检测及计算机控制等喷 吹工 艺 , 计最 大制 粉 能力 为 5 / , 粉系统 及 设 1th 制
喷 吹系统 均一 次试 车 成功 。 1 4号 高炉 的喷 煤 工艺
1 1 工艺 设计 .
采 用直 接喷 吹 , 喷吹 能力 按 10k/ 设 计 , 8 g t 最大 高
炉产量 8 0 , 0t利用系数 25 ( ・ 、最大高 0 . m d, 炉煤 比 20k/。喷 煤 煤 粉 仓 流 化 、 吹罐 加 压 0 gt 喷
料位 、 高高料位开关进行监视 , 以避免煤粉仓过量
21 0 1年第 6期
梅 山科 技
・ 9・ l
新喷煤技术在 320m 0 。高炉中的应用
章 宏 彭福 荣
高炉喷吹高挥发分烟煤实践

柳 钢 使 用 的 高 挥 发 分 烟 煤 含 挥 发 分 高 ,均
作 者 :林 俊 贤 , 大 学 学历 , 高级 工 程 师 ,现 任 喷 吹
车 间 主任 。
_ √ 0l l 0l 00 l 霉| ≯ 。 0 0
f 7 O 。) ,消除煤 粉堆 积死 角 。
… | :
文 总结 实践 过程 。
在 3 5 % 以上 ,属 于 易燃 强 爆 炸 性 煤 种 。如 果要
安 全 磨 制 和 喷 吹该 烟 煤 ,除必 须 严 格 控 制 喷 煤
系 统 含 氧 量 、温 度 外 ,从 烟煤 喷 吹工 艺 设 计 开 始 就 要 采 取 安 全 措 施 ,以 消 除煤 粉 的着 火 、爆
第 l l
系统 氧 含 量 偏 高 ,粉 尘 污 染严 重 ,不 利 于安 全
( 6 ) 在 制 粉 系 统 中 ,多 处 设 置 自动 充 氮 气
火 花 ,有 利 于安全 。 ( 3 ) 制 粉 的 布 袋 收 尘 器 、煤 粉仓 、喷 吹 罐
设 防爆 孔 ,一 旦发 生爆 炸能 起 到泄爆 作用 。
2 喷吹高挥发分烟煤 的实践
2 . 1 工艺 设计 安全 措施
.
( 4 ) 制 粉 、喷 吹 设 备 系 统 、容 器 、管 道 采 用 防静 电措施 ,避 免产 生静 电火花 。 ( 5 ) 制粉 系统在设 计 时为 防止煤 粉积粉 , 发 生缓 慢 氧 化导 致 温度 升 高 、着 火 ,对 煤 粉 仓 、 喷 吹 罐 、灰 斗 等 角 度 均 大 于 或 等 于 煤 粉 安 全 角
2 0 1 3 每
强
j l
| | 。 一
襁 锻。 。 i 镘
高炉喷煤系统自动控制应用

高炉喷煤系统自动控制的应用摘要高炉喷煤系统的自动化系统控制在高炉生产中已广泛运用,但自动化软件的编程、系统的组态、自控系统的调试在施工单位运用较少。
本文根据蒙丰工程全面阐述了喷煤系统的软件编程、自动化组态及整个喷煤系统的自动控制。
供施工技术人员参考。
关键词自动化软件编程系统组态系统配置1.前言高炉喷煤系统自获得成功以来,很快在国内普遍推广应用,并且高炉喷煤工艺及其相关技术得到了迅速发展。
尤其是近几年发展的富氧大喷煤技术给高炉生产注入新的生机。
高炉喷吹煤粉,是节约焦炭、降低高炉炼铁生产成本的重要措施。
国内炼铁生产规模不断扩大与高炉生产效率的提高,对焦炭需求量也日趋增加,由于国内焦煤资源逐渐减少造成冶金焦价格的不断上涨。
因此,高炉喷吹煤粉是现代高炉炼铁生产降低成本的重要技术之一。
进一步减低生铁成本的途径之一是实现高炉喷煤,对高炉喷吹煤粉代替部分焦炭。
因此高炉设高炉喷吹煤粉工程。
喷煤工程设计指标将达到180kg/t铁喷煤比能力。
喷吹煤种按全烟煤的浓相输送设计。
喷煤工程建成以后,具备可以喷吹单一的无烟煤或烟煤,或喷吹两种不同挥发份、按不同比例组成的混合煤。
并且根据高炉喷煤达到最大喷煤量的需要,应向高炉提供1~3%的富氧率,以及采取各种措施提高高炉热风温度。
随着喷煤系统工艺水平的不断提升,对自动化控制的要求就越来越高。
本文是根据蒙丰特钢工程喷煤系统自动化控制的配置进行分析和阐述。
2.工艺流程蒙丰特钢高炉喷煤工程系统自动控制系统分为三大部分;热烟气系统、制粉系统和喷吹系统。
热烟气系统主要包括烟气升温炉、高炉煤气管道、助燃空气管道、热风炉废气管道、冷空气管道。
制粉系统:包括一个原煤仓,一台密闭式称重皮带给煤机,一台中速磨煤机,,一台热风炉烟气引风机,一台助燃风机,一台布袋收粉器,一台主排烟风机和一个煤粉仓。
喷吹系统:内设两个喷吹罐,两个喷吹罐轮换向一座高炉喷煤。
两个喷吹罐交替向高炉连续喷煤,两根喷煤主管的出口管合并一根主管,在高炉附近的分配器后分成14根支管向所对应高炉风口喷吹煤粉。
高炉喷煤工艺

Kuettner 喷煤系统的分配精度,不是靠分配器后各支管的严格等距离来 获得的,而是靠分配器、以及分配器后的阻流管、再加上设置在总管上 的流量测量和控制装置来保证的。
(3) 使用寿命长
Kuettner 喷煤系统采用的是低速浓相输送,加上独特的内部设计,可以 保证在分配器和管道内几乎没有磨损,实际上根本没有更换的必要。投 产至今的所有喷煤装置,尚无任何一套分配器更换过,甚至从来还没有 维修过。运行时间最长的已超过十五年。从而大大节约了设备的运行成 本,增加了设备的作业率。
沙钢的三座 2600 m3 的高炉和首钢京唐钢铁公司的二座 5500m3 的高炉都采 用了氧煤喷枪技术。
4
2.11 特殊的操作软件 由 Kuettner 公司独立开发的软件,包含了所有制粉系统和喷吹系统的技术 诀窍和工艺诀窍,也是确保上述各项特点得以充分体现的最重要因素。 Kuettner 的软件对计算机硬件没有限制,适用于当今任何计算机系统。
2.2 低速浓相输送 煤粉输送速度低: 2~4 m/s 煤粉输送比高: 60 kg 煤粉 / kg 输送气体 由于煤粉的输送速度低,保证了管道和分配器内几乎没有磨损,对有关设备 的磨损也微乎其微,从而极大地延长了设备的寿命,长期不需要大修。使用 寿命大于 20 年。 此外,由于实现了高输送比,进入高炉的煤粉输送气体只有稀相方式的一 半,甚至是三分之一,由此节约了大量炉内用于将输送气体从 80°C 加热至 2150°C 的焦碳消耗。仅此一项,Kuettner 的喷煤技术将可以为用户每年节 约焦碳消耗几十万美元。这还尚未计算置换焦碳所节约的成本。在蒂森高炉 上使用的 Kuettner 的喷煤系统,其实际输送比已达到 90 kg 煤粉以上。
特殊设计的减震装置,使得振动筛工作时对厂房框架几乎没有任何振动。
天铁高炉混喷技术实践

1 前 言
喷煤
煤 比 工 艺 优化
了 10  ̄t e以上 。 7k . F
天铁集 团炼铁厂 老区现有五座高炉 , 中 7 0I 其 0 1 I 四座 ,8 3 座。高炉喷煤系统采用集 中制粉间接 3 0m 一 喷吹 ,每座高 炉建有 一座喷吹站 。 自 18 年投 产 以 97 来 ,依托 山西优质无 烟煤资源 ,喷煤量逐年 提高 , 到 19 9 5年在不 富氧的条件 下煤 比达到 了 lO g .e 创 O k/F , t 全 国同类行业 先进水 平 。随着高炉喷煤技术 的提高 , 天铁集 团对喷煤 系统 的原有制粉 设备 进行 了工艺 优 化, 并进行 了浓相喷 吹的实验 和改造 ,0 0年高炉 煤 20
为保证混喷投产 的成功 , 首先从距离最远 的 5 高 *
炉开始 , 5 高炉距制粉 8 0多米 ,由于管线 长 、阻损 0 大 , 反复调整后 , 经 确定 出喷吹操作参数 , 实现 了超远 距 离试 喷成功 。随后 , ~ 高炉相 继投产 ,0 0年 1 1 21
( ) 当热风炉废气温度过低 ,或高炉的热风炉废气 3
助燃风机
冷风
压缩空气
补气器
过滤器
图 1 高炉混喷煤粉工艺
2 混喷技 术改造 - 2
同 的受 料斗 , 根据配 料 比例 , 系统 自动调 节定 量配煤
装 置 的给料量 , 到配煤效果 。经过 配料的原煤进入 达 上煤胶带输送机及储 煤仓顶 的带式输送 机 , 送至储煤 仓 完成供煤作业 。
数 /h t / /P ka /m/ /m N3 h r a /m/ N3 h ,P ka
离器体 的衬 板上返 回重磨 , 细度合格 的煤 粉经排 出口
【doc】高炉喷煤粉(PCI)技术

高炉喷煤粉(PCI)技术101998年簟3瑚蒋敏f0~,高炉喷煤粉(PCI)技术译王增勋校鳓.1979年的第二次石油危机造成石油价格猛涨,供应不稳定.迫使日本各钢铁公司进一步加强了节能工作,强化了"脱离石油对策".特别是能源消耗型工序——高炉停用了以往从风口吹八辅助染料重油,向所谓的以全焦操作为主体的"脱离石油化方向转化.与此同时,为长期稳定高炉生产降低成本及适应今后能源变化,作为代替重油的染料,各公司积极推进了煤粉等煤炭系列能源向高炉喷吹的技术开发.喷煤粉(PCI)价格便宜并能使高炉生产稳定.国内以1981年6月开始投产的新日本制铁太分厂1号高炉为起点,十年中合计有26麈高炉采用了PCI技术,占生产中高炉数的70go以上.'术文叙述了高炉PCI技术开发的经过和本技术今后的展望.PCI技术开发的背景1)能源情况的变化.过去在高炉上以引进自熔性烧结矿,高压,高炉,复合送风等技术为背景,积极推进大型化,高生产率化,低燃料比化的操作,?并取得了令人瞩目的进展,见图1.特别是1961年以来使用廉价的重油向高炉喷吹,为提高高炉纳生产率和降低燃料比作出了很大的贡献.随着1973年第一次石油危机,重油价格上涨到几乎和原料煤炭价格相等,进一步推进了高炉低燃料比化的进程,可是1979 年第二次石油危_机以后,石油价格竟涨到原料煤炭的2.5倍,这样从成本上讲停用重油嘴用焦炭更为有利,所以,各公司均向以全通常在吹氧作业中,特g,lI~tg炼超低碳钢的RH处理中,其损伤速度较快有人按热力学原理研究了有关用于吹氧作业的镁铬砖损伤情况,认为随着氧分压的增加,Crz0,形成CrO3,CrO:丽蒸发,CrO.(g)在有Fe(1)存在的低氧分压下发生了Fe(1)+2CrO. (g)=3FeO(1)十Cr2Oa(s)的反应,使CrzO,成分的蒸发和氧化铁向耐火材料中扩散从而降低了耐火材料的耐蚀性.结柬语用于RH脱气罐的直接接合镁铬砖的损伤原因有以下几点,将其综合起来就会造成损伤,且各种损份出现率可田作业条件而变, 1.由于从作业面侵入的CaO,Sio:AIz0.,Fe氧化物等使耐火度下降|并且由于钢流构冲刷造成工作面的熔损.2.CaO,SiOz报侵2,.2E作面下层很深,生成硅酸盐而致密化,在与这部分或更下层的脆弱层界面上产生龟裂而剥落.3.由于温度变化或真空,常压交替进行,引起氧分压改变,而发8-"FeO=Fe2O3 的变化,导致了砖组织脆弱化由于CrO.的蒸发而降低了砖的耐蚀性.4.由于吹八的氧或因漏气而进八罐内的空气与锕液反应产生高温,所生成的氧化铣与砖反应而形成熔流.译自《蔚火物》(日文)1992年4斯●●太钢谭窭?i1?图1高炉生产推移表(日本)霉詈\命,嘉焦操作工艺为主体的"脱离石油操怍"方向转化.2)PCI技术的效果由喷吹重油工艺向全焦操作工艺的转化,给高炉生产带来的变化事例如下.由于高炉炉墙部位易生成呆滞区域,风口前端燃烧温度上升等原因,易使高炉生产不稳定. 采取的对策是降低进风温度,增加送风湿度,力求使高炉生产稳定,但结祟却招致怠比上升,生产量下降,这就提出了采用替代重油燃料的要求.在替代重油的燃料中,从当时的重油和煤炭价格量出发,各公司积极引进了作为"脱离石油技术"的PCI技术,从开始使用非粘结炭粉到今日,不仅在经济性而且在焦炭用强粘结炭资源对第上也取得了重要的效果,此外,由于向全焦操作工艺的转化使焦炉的负荷加大,不可避免地影响了焦炉的寿命.国内各公司的焦炉大部分是在1960年后期到1970年前期建议的,炉龄在20年以上的焦炉已占70嘶,原来被人们认为炉龄在30",~40年的焦炉寿命由于热补技术的发展,预计其寿命可以再延长一些,但;可以预料不久的将来国内的焦炉将逐渐接近炉龄寿命期,因此作为减轻焦炉负荷对策之一的PCI技术在开发延长焦妒寿命技术上其意义十分重大.如上所述,高妒生产|h全焦操工艺向PCI转化,其效果如下:①高炉操作稳定I②能源成本降低,③出铁量增加j④焦炉设备能力的补充完善并延长寿⑤非粘结炭粉的有效利用.PCI技术的.开发1)PCI设备前开发,向高炉喷煤粉早在10世纪中叶法国和比利对就做过这方面昀尝试,但宴际啦用却是进八1960年以后的事.由美国,中国,前并联谣国等国进行实用.这以后,以第二次石油危机为契机,世界上PCI设备的开发工作活跃起来,并买现丁多种使用方式.如前所述,自1980年以后各日本公司才开始研究讨论引进PCI设备,在引进Pct设备时国外虽有先例,却设有类似日本高压高温大型高炉的实际经验,因此,从煤炭的莲八到向各风口现在日本国内运行中的PCI设备有26座,占生产中高炉数的70嘶以上i1980年以来,特别是在欧洲,中国,韩国,台湾省也积极从事了这方面的工作.这方面工作落后的美国,由于修改了大气污染净化法,作为改善焦炉环境措施之一,1990年后开始了加快引进的研究,今后PcI技术仍是各国广遵研究的课题之一.PCI高炉的生产和今后的谭曩---最近的高炉考虑到钢铁厂的能源情况与焦炭的生产能力,在制定最低成本韵燃料比和工艺条件下,对喷煤粉效果和经济性等不12199年簟3|If图2神户3高炉PCI系统流程图能一概而论,但是作为发展方向,为了最大限度地发挥前述PCI的效果,近年来各公司均积极引进PCI设备,并致力于增大PC比. 图3为PCI高炉的使用状况.图3PCI高炉的使用状况1)大量喷煤粉工艺如前所述,PCI35艺在降低能源成本,提高高炉生产的稳定性生产性上起了作用.最近,为了最大限度地追求其经济价值,作为延长焦炉寿命的措施正在向大量喷;粉工艺方向转化,但在大量喷吹蝶粉的操作中,随着高炉的大幅度变化,产生了阻碍高炉稳定操作的倾向,各公司都在开发克服这些问题的技术,努力增大喷煤量.关于煤粉比(每1炉吨铁水的煤粉喷八量)的上限现阶段尚难看清.欧洲实现了140—148kg/吨铁水,荷兰,英国等做过2OOkg./吨铁水以上的试生产.从日本1991年平均情况看,神户广3高炉最高为178k~/吨铁水(图4),一般在7o一13okg/吨铁水之间.以前日本制定喷煤粉水平主要是以稳定炉况为主,设计的设备能力低,但随着炉料分布的控制技术号煤粉燃饶控制技术的进步,使得有可能在高PCI下稳定生产.最近,在接近设备能力上限的条件下进行喷煤粉的高炉数增加,进而由于设备*搿-\加羲l991年崖oaO0oO●一l仓2高炉0高炉喜公司乎j目神3高炉●:高PC比高垆攥黔比(/l铁木)图4国内喷煤粉状咒●●'泰翻译文?1S-能力的增强,煤粉比的目标已超过200kg/吨铁术以上.2)大量喷煤粉操作的技术课题经济地充分发挥PCIX果,有必要论述一下它和焦炭的置换率.用煤粉代替焦炭时护内焦炭量减少,矿石量增大.焦炭的重要作用有;①热源,@还原剂,③保证透气性.因此超过限量增大煤粉比会影响高炉的透气性,助长高炉下部边缘气流过剩,增大热损失.另一方面在风口处由于PC燃烧量的增加,使风口内的压力损失增大.进而由于过刺麓气量的减少,未燃烧的煤粉量增大,蓄积在炉内导致透气性恶化,高炉下部焦炭层透气性与液体流动性恶化,并随炉顶废气逸出而降低了对焦炭的置换率.上述这些高炉内现象的主要变化情况见图5和图8.除这些现象之外诸如;由于炉内H2量增加,料下降速度减慢影响铁矿石的还原反应变化以及由于热流地(装入炉料和煤气热容量比)降低使炉顶的热损失增大等,在进行大量喷煤粉操作时应解决的课题毋很多.神户锕公司在1983年开始实施PCI操作以来,以增大煤粉喷八量为目标积极地进行了技术开发,为实现大量喷煤粉操作,神户公图5大量喷煤掰时高炉炉内现象图8大量喷煤粉时炉内的变化情况司已做过的技术课题和措施如表1所示.这些研究所经过基础研究与实际高炉的试生产,已证明实现约20okg/吨铁水是可行的根据这一技术开发的成果,神户厂3高炉现在喷煤粉为180kg/吨铢水,进而以200kg/吨铁水为目标力求增大喷吹量.此外,加古川厂1高炉1992年9月增加了设备的能力, 有可能实现200kg/吨铁水的喷吹量.再有1994年准备点火的加古川广3高炉也设置了同等能力的设备,所有生产中的高炉均向200kg/吨铁水的目标努力.各公司因焦炉能力的关系采用PCI设备的必要性虽肓差14199i年第3期裹1开发大量喷煤粉技术(神户制钢)1)装入高品位矿石/焦炭比的控制技术(即离负荷)①高炉装入原料分布实验②高热态模型实验@焦炭中心装入技术的开发i降低压力损失的炉料分布2)堞粉烧控制技木①煤耕燃烧实验(煤粉品种.粒度,啧^位置,进风条件)@探明未燃烧煤粉在炉内蓄积的机制@择明束燃烧煤粉在炉内消耗的机制高燃烧率,低压力损失的大量喷吹煤粉燃烧技术l0)原料最佳化①从高炉中采集原科试样J!璺堂墨壁4)PCI设备的改善①探明煤粉输送特性大最喷煤设备的开发异,坦相继逐渐增邡喷煤设备,不久的将来国内煤柑比实现150~209kg/吨铁水将成为馨遍现象.进而实现250kg/吨铁水(高炉燃料比:约5O0kg/吨铁水的一半)的超大量喷煤工艺,则必须在煤粉燃烧和装人炉料分布控制方面进行前所未有的革新技术的开发.现在国内外正进行着各种试验,应用这些技术在经济台理的条件下稳定地达到250kg/吨铁水喷煤粉的目标仍需相当长的时间.由1980年开始积极引进的PCI技术在国.内外已逐渐普及,它作为高炉燃料喷吹技术已趋于完善.这期间的技术开发主要侧重于降低成本,稳定高炉操作,提高生产率.今?后为最大限度地追求经济上的价值,井作为延长焦炉寿命的措施,将继续从事增大喷煤粉量的研究,在不久的将来会实现2O0kg/t铁水以上煤粉比的工艺,进而开始对250kg/吨铁水以上的技术进行开发.此外由PCI技术不需要经过焦妒这道工序可直接利用煤炭,所以还会减小COz的排出量,从保护地球环境角度来讲今后仍将是引人注目的课题之一.译自《铁钢界》(日文)1992年IO月■1。
我国高炉喷煤技术的发展和应用
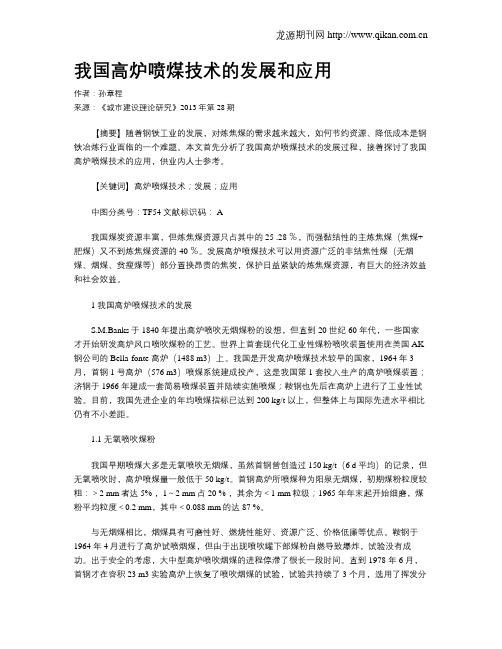
我国高炉喷煤技术的发展和应用作者:孙章程来源:《城市建设理论研究》2013年第28期【摘要】随着钢铁工业的发展,对炼焦煤的需求越来越大,如何节约资源、降低成本是钢铁冶炼行业面临的一个难题。
本文首先分析了我国高炉喷煤技术的发展过程,接着探讨了我国高炉喷煤技术的应用,供业内人士参考。
【关键词】高炉喷煤技术;发展;应用中图分类号:TF54文献标识码: A我国煤炭资源丰富,但炼焦煤资源只占其中的25 .28 %,而强黏结性的主炼焦煤(焦煤+ 肥煤)又不到炼焦煤资源的40 %。
发展高炉喷煤技术可以用资源广泛的非结焦性煤(无烟煤、烟煤、贫瘦煤等)部分置换昂贵的焦炭,保护日益紧缺的炼焦煤资源,有巨大的经济效益和社会效益。
1 我国高炉喷煤技术的发展S.M.Banks于1840 年提出高炉喷吹无烟煤粉的设想,但直到20 世纪60 年代,一些国家才开始研发高炉风口喷吹煤粉的工艺。
世界上首套现代化工业性煤粉喷吹装置使用在美国AK 钢公司的Bella-fonte 高炉(1488 m3)上。
我国是开发高炉喷煤技术较早的国家,1964 年3 月,首钢1 号高炉(576 m3)喷煤系统建成投产,这是我国第1 套投入生产的高炉喷煤装置;济钢于1966 年建成一套简易喷煤装置并陆续实施喷煤;鞍钢也先后在高炉上进行了工业性试验。
目前,我国先进企业的年均喷煤指标已达到200 kg/t 以上,但整体上与国际先进水平相比仍有不小差距。
1.1 无氧喷吹煤粉我国早期喷煤大多是无氧喷吹无烟煤,虽然首钢曾创造过150 kg/t(6 d 平均)的记录,但无氧喷吹时,高炉喷煤量一般低于50 kg/t。
首钢高炉所喷煤种为阳泉无烟煤,初期煤粉粒度较粗:>2 mm者达5% ,1~2 mm占20 % ,其余为<1 mm粒级;1965 年年末起开始细磨,煤粉平均粒度<0.2 mm,其中<0.088 mm的达87 %。
与无烟煤相比,烟煤具有可磨性好、燃烧性能好、资源广泛、价格低廉等优点。
钢铁厂高炉喷煤系统原理详细介绍(一)
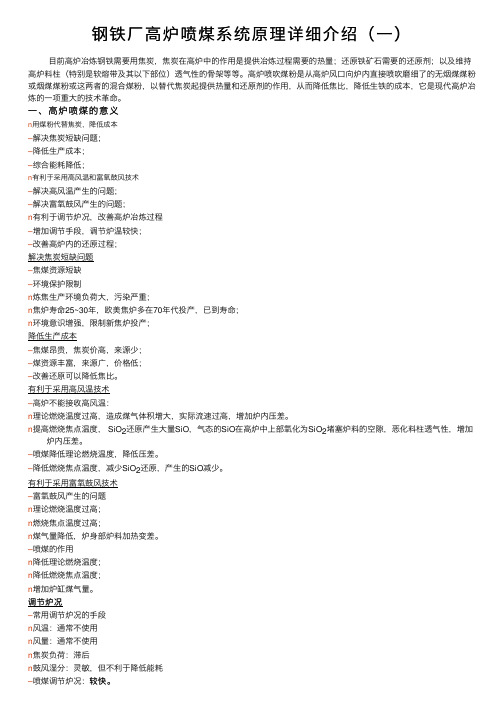
请您及时更换请请请您正在使用的模版将于2周后被下线请您及时更换
钢铁厂高炉喷煤系统原理详细介绍(一)
目前高炉冶炼钢铁需要用焦炭,焦炭在高炉中的作用是提供冶炼过程需要的热量;还原铁矿石需要的还原剂;以及维持 高炉料柱(特别是软熔带及其以下部位)透气性的骨架等等。高炉喷吹煤粉是从高炉风口向炉内直接喷吹磨细了的无烟煤煤粉 或烟煤煤粉或这两者的混合煤粉,以替代焦炭起提供热量和还原剂的作用,从而降低焦比,降低生铁的成本,它是现代高炉冶 炼的一项重大的技术革命。
制,烟煤一般不超过120~130℃,褐煤一般不超过100℃。 –磨煤设备:球磨机或中速磨 n球磨机: –优点:对煤种适应性强,安全可靠,维护工作量少; –缺点:噪声大,电耗高,外形尺寸大。 n中速磨: –优点:电耗低,噪音小,防爆性好,调节性和均匀性好。 –缺点:对煤种变化敏感。 n喷吹罐 n双罐并列式: –上为贮煤罐,下为喷煤罐。 –优点:高度低,称量准确,可靠性高。 –缺点:占地面积大,设备多,投资略高。 n三罐单列式: –上为收集罐,中为贮煤罐,下为喷吹罐。 –优点:占地面积小,装置简单设备少,投资低。 –缺点:贮煤罐和喷吹罐之间硬连接,影响称量的准确性。 n供煤方式和煤粉分配器 –各风口单独供粉: –向高炉集中供粉,采用煤粉分配器将煤粉分配到各个风口。
一、高炉喷煤的意义
浅谈高炉经济喷煤比

浅谈高炉经济喷煤比王立杰尹焕岭赵杨(唐钢不锈钢)摘要:高炉喷煤是降低铁水成本,增加利润的重要手段;同时,直接喷吹煤粉,不经过焦化工艺,减少了环境污染。
提高喷煤比应具备的条件是:稳定的原燃料质量、合适的理论燃烧温度、精细的操作和合理煤气分布。
高炉提高喷煤比是冶炼技术发展的必然趋势,然而各单位能满足的条件不同,因此各单位的经济煤比也应根据自身条件确定。
关键词:高炉经济喷煤比理论燃烧温度未燃煤粉置换比0 前言高炉喷吹煤粉则是部分替代焦炭的“提供热量”及“还原剂和渗碳剂”,即以价格低廉的煤粉部分替代价格日趋昂贵的冶金焦炭,以缓解因炼焦用主焦煤匮乏所造成的冶金焦炭产量渐显不足的矛盾,最终降低高炉炼铁焦比和生铁成本。
当前高炉生产的一些习惯性认识和操作,直接影响到高炉喷煤的科学性,且给高炉喷煤效益乃至生铁成本带来不良影响,因此选择合理的喷煤比就是实现企业效益最大化的重要一项。
1 经济喷煤比的概念所谓经济喷煤比,是在一定的生产条件下(产量、原燃料质量、炉料结构、煤和焦炭的市场价格等),喷煤比最高且稳定、焦比和燃料比最低的操作煤比。
可见,经济喷煤比的大小取决于喷煤量水平、煤交置换比和能量消耗利用程度,最终有总燃料消耗、工序成本来确定。
喷煤对高炉工序降低值的影响可按下式计算:△J=PCR(P k×R—P m)/1000(1)式中△J——高炉工序成本降低值,元/t;PCR——喷煤比,kg/t;R——未校正煤焦置换比;P k——焦炭价格,元/t;P m——煤粉工序成本,元/t。
从图1曲线可见,喷煤生产操作中存在经济喷煤比。
由于原燃料质量、炉况参数在一定范围内波动,因此经济喷煤比是一个操作范围。
2 提高喷煤比的关键技术2.1稳定原燃料条件2.1.1提高焦炭质量,特别是焦炭的热性能,保证高炉必要炉料柱透气性。
图1 高炉工序成本降低值与喷煤比的关系焦炭在高炉内的骨架作用是煤粉不可替代的,随着煤比的提高,焦炭的负荷随之加重,以及焦炭在炉内停留的时间越长,焦炭的骨架作用更显的重要。
安钢7号高炉大喷煤技术分析
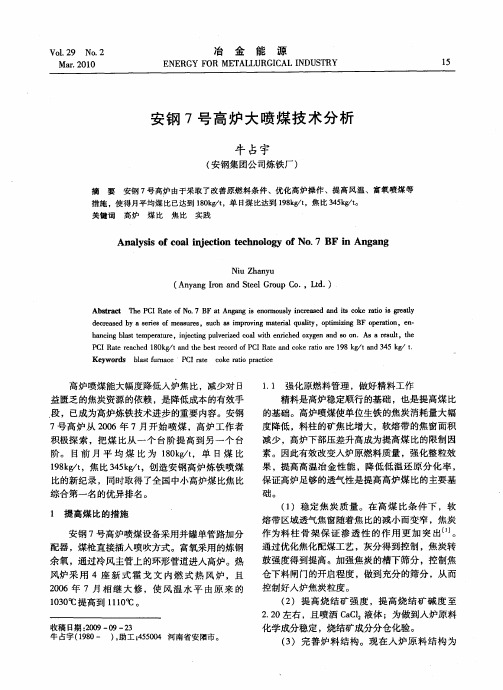
熔 带 区域 透气 焦窗 随着焦 比的减 小而 变窄 ,焦 炭 作 为料 柱 骨 架 保 证 渗 透 性 的 作 用 更 加 突 出… 。 通 过优化 焦化 配煤工 艺 ,灰 分得 到控 制 ,焦 炭 转
余氧 ,通过冷风主管上 的环形管道进入高炉。热
风炉 采 用 4座 新 式 霍 戈 文 内 燃 式 热 风 炉 ,且 20 06年 7月 相 继 大 修 ,使 风 温 水 平 由原 来 的 13 o 00C提高到 11o 10C。
收稿 1期 :09—0 2 3 20 9— 3 牛 占宇( 90一 ) 助工 ;5 04 河南省安阳市。 18 , 45 0
鼓强度得到提高。加强焦炭的槽下筛分 ,控制焦 仓下料闸门的开启程度 ,做到充分的筛分 ,从而 控 制好人 炉焦 炭粒度 。 ( ) 提 高 烧 结 矿 强 度 ,提 高 烧 结 矿 碱 度 至 2 22 右 ,且 喷洒 CC: .0左 a1液体 ;为做到 人炉 原料 化 学成分 稳定 ,烧结 矿成 分分 仓化验 。 ( )完 善炉 料 结 构 。现 在 人 炉 原 料 结 构 为 3
高炉 煤比 焦比 实践
措施 ,使得月平均煤 比已达到 10 gt 8k/ ,单 1煤 比达到 18 s t 3 9 k ,焦 比 35 s t / 4k 。 /
关键词
A ay i o o l net n tc n lg fN . F i n a g n ls f a jci h oo yo o 7 B A g n s c i o e n
Ni a y u Zh n u
( na gI na dSel ru o , t. A y n o n te G opC . Ld ) r
Ab t a t T e P I R t fN . F a n a g i e o mo sy i c e s d a d i o e rt s s t sr c h C ae o o 7 B tA g n s n r u l n r a e n t c k ai i  ̄al s o y d c e s d b e is o a u e ,s c s i r vn t r l q a t e r a e y a s r fme s r s u h a mp o ig mae a u l y,o t zn F o e ai n n e i i pi i g B p r t ,e — mi o
高炉喷煤概论
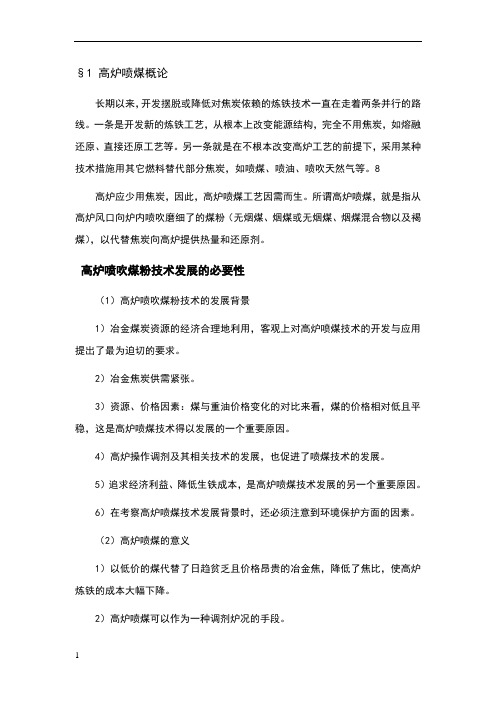
§1高炉喷煤概论长期以来,开发摆脱或降低对焦炭依赖的炼铁技术一直在走着两条并行的路线。
一条是开发新的炼铁工艺,从根本上改变能源结构,完全不用焦炭,如熔融还原、直接还原工艺等。
另一条就是在不根本改变高炉工艺的前提下,采用某种技术措施用其它燃料替代部分焦炭,如喷煤、喷油、喷吹天然气等。
8高炉应少用焦炭,因此,高炉喷煤工艺因需而生。
所谓高炉喷煤,就是指从高炉风口向炉内喷吹磨细了的煤粉(无烟煤、烟煤或无烟煤、烟煤混合物以及褐煤),以代替焦炭向高炉提供热量和还原剂。
高炉喷吹煤粉技术发展的必要性(1)高炉喷吹煤粉技术的发展背景1)冶金煤炭资源的经济合理地利用,客观上对高炉喷煤技术的开发与应用提出了最为迫切的要求。
2)冶金焦炭供需紧张。
3)资源、价格因素:煤与重油价格变化的对比来看,煤的价格相对低且平稳,这是高炉喷煤技术得以发展的一个重要原因。
4)高炉操作调剂及其相关技术的发展,也促进了喷煤技术的发展。
5)追求经济利益、降低生铁成本,是高炉喷煤技术发展的另一个重要原因。
6)在考察高炉喷煤技术发展背景时,还必须注意到环境保护方面的因素。
(2)高炉喷煤的意义1)以低价的煤代替了日趋贫乏且价格昂贵的冶金焦,降低了焦比,使高炉炼铁的成本大幅下降。
2)高炉喷煤可以作为一种调剂炉况的手段。
v1.0 可编辑可修改3)高炉喷煤可以改善炉缸工作状态,使高炉稳定顺行。
4)为高炉提高风温和富氧鼓风创造条件。
因为喷吹煤粉会使风口前理论燃烧温度降低,导致理论燃烧温度降低的原因主要有:高炉喷吹煤粉后煤气量增加,加热煤气需要消耗热量;高炉煤粉带入的热量少,而焦炭进入到风口区时已加热到1450~1500℃,而喷吹煤粉的温度不超过100℃;煤粉中碳氢化合物分解吸热。
5)喷吹煤粉中的氢含量比焦炭带入的多,氢气提高了煤气的还原能力和穿透扩散能力,有利于矿石的还原和高炉操作指标的改善。
6)喷吹煤粉代替了部分焦炭,不仅缓解了焦煤的供需紧张状况,也减少了对炼焦设施的投资和建设,降低了炼焦生产对环境的污染。
高炉喷吹煤比的关键技术
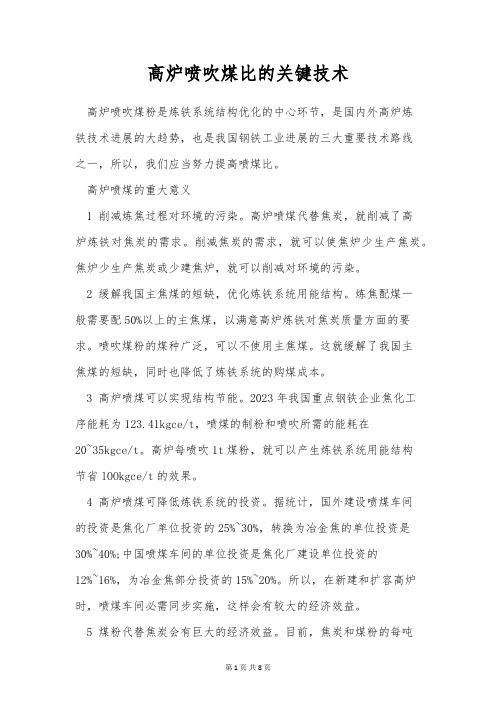
高炉喷吹煤比的关键技术高炉喷吹煤粉是炼铁系统结构优化的中心环节,是国内外高炉炼铁技术进展的大趋势,也是我国钢铁工业进展的三大重要技术路线之一,所以,我们应当努力提高喷煤比。
高炉喷煤的重大意义1 削减炼焦过程对环境的污染。
高炉喷煤代替焦炭,就削减了高炉炼铁对焦炭的需求。
削减焦炭的需求,就可以使焦炉少生产焦炭。
焦炉少生产焦炭或少建焦炉,就可以削减对环境的污染。
2 缓解我国主焦煤的短缺,优化炼铁系统用能结构。
炼焦配煤一般需要配50%以上的主焦煤,以满意高炉炼铁对焦炭质量方面的要求。
喷吹煤粉的煤种广泛,可以不使用主焦煤。
这就缓解了我国主焦煤的短缺,同时也降低了炼铁系统的购煤成本。
3 高炉喷煤可以实现结构节能。
2023年我国重点钢铁企业焦化工序能耗为123.41kgce/t,喷煤的制粉和喷吹所需的能耗在20~35kgce/t。
高炉每喷吹1t煤粉,就可以产生炼铁系统用能结构节省lOOkgce/t的效果。
4 高炉喷煤可降低炼铁系统的投资。
据统计,国外建设喷煤车间的投资是焦化厂单位投资的25%~30%,转换为冶金焦的单位投资是30%~40%;中国喷煤车间的单位投资是焦化厂建设单位投资的12%~16%,为冶金焦部分投资的15%~20%。
所以,在新建和扩容高炉时,喷煤车间必需同步实施,这样会有较大的经济效益。
5 煤粉代替焦炭会有巨大的经济效益。
目前,焦炭和煤粉的每吨价差在400~500元。
一个年产400万t的炼铁企业,假如喷煤比在130kg/t,就可以年喷吹52万t煤粉,代替的等量的焦炭,可以产生年降低208~260万元的炼铁成本。
6 提高企业劳动生产率,降低生产运行费。
喷煤车间的员工人数和生产运行费用要比焦化厂少,这样就可以产生因高炉喷煤而提高钢铁企业劳动生产率、障低生产运行费用的效果。
我国喷煤水平进展不平衡,与国际先进水平尚有差距据统计,2023年我国大中型钢铁企业高炉喷煤比135kg/t,比上年度提高llkg/t,全年重点钢铁企业喷煤总量为4046万t,创出我国历史最好水平。
高炉喷煤的应用

可燃成分 碳、氢、氧、氮、硫
水分
游离水、化合水
3、煤的物理性质
1. 煤的孔隙率
煤的孔隙率也是决定煤层瓦斯容量的主要因素之一,是 计算煤层中游离瓦斯含量的重要依据。根据煤的视(相 对)密度和煤的真(相对)密度可以计算出煤的孔隙率
混合器
混合器是将压缩空气与 煤粉混合并使煤粉启动 的设备,由壳体和喷嘴 组成,如图6所示 混合器的工作原理是利 用从喷嘴喷射出的高速 气流所产生的相对负压 将煤粉吸附、混匀和启 动的
图6 沸腾式混合器 l一压缩空气阀门;2—气室;3一壳 体;4一喷嘴;5一调节帽
分配器
单管路喷吹必须设置分配器 (图7) 煤粉由设在喷吹罐下部的混 合器供给,经喷吹总管送入 分配器,在分配器四周均匀 布置了若干个喷吹支管,喷 吹支管数目与高炉风口数相 同,煤粉经喷吹支管和喷枪 喷入高炉 目前使用效果较好的分配器 有瓶式、盘式和锥形分配器
四
高炉喷煤系统主体设备
1、原煤仓
原煤仓的个数和磨煤机的台数相对应,最好采用圆筒形直 段、双曲线锥段结构 为了满足喷煤系统设备检修时间要求,原煤仓必须有相应 的存煤容积 为了满足高炉变料时间,要求储煤容积加上用煤和加煤之 间的不平衡所需的容积即所需的原煤仓的几何容积
2、给料机
给煤机位于原煤仓下面,用于向磨煤机提供原煤,目前常用埋刮板给
我国高炉喷煤始于20世纪60年代初,起步最早的是鞍钢、 首钢。 鞍钢1964年开始试验至19966年实现5座高炉全部喷煤。 首钢也与1964年开始试验至1965年正式喷煤。因此我国是 世界上最早实现喷煤的国家之一。 之后一段时间发展缓慢,直至80年代末90年代初,特别是 近几十年我国的高炉喷煤技术得到迅速发展。如图2所示.
高炉喷吹煤粉技术
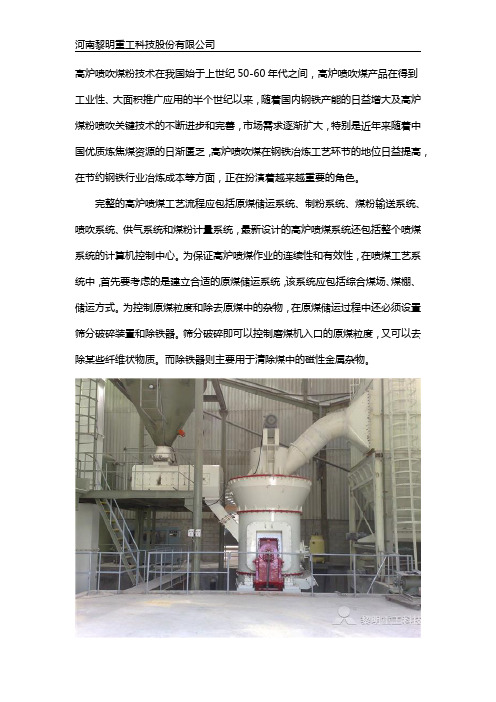
高炉喷吹煤粉技术在我国始于上世纪50-60年代之间,高炉喷吹煤产品在得到工业性、大面积推广应用的半个世纪以来,随着国内钢铁产能的日益增大及高炉煤粉喷吹关键技术的不断进步和完善,市场需求逐渐扩大,特别是近年来随着中国优质炼焦煤资源的日渐匮乏,高炉喷吹煤在钢铁冶炼工艺环节的地位日益提高,在节约钢铁行业冶炼成本等方面,正在扮演着越来越重要的角色。
完整的高炉喷煤工艺流程应包括原煤储运系统、制粉系统、煤粉输送系统、喷吹系统、供气系统和煤粉计量系统,最新设计的高炉喷煤系统还包括整个喷煤系统的计算机控制中心。
为保证高炉喷煤作业的连续性和有效性,在喷煤工艺系统中,首先要考虑的是建立合适的原煤储运系统,该系统应包括综合煤场、煤棚、储运方式。
为控制原煤粒度和除去原煤中的杂物,在原煤储运过程中还必须设置筛分破碎装置和除铁器。
筛分破碎即可以控制磨煤机入口的原煤粒度,又可以去除某些纤维状物质。
而除铁器则主要用于清除煤中的磁性金属杂物。
河南黎明重工科技股份有限公司是我国著名矿山机械破碎机,磨粉机和制砂机研发制造商,公司在市场需求中带动磨粉机制造业经济增长的同时,更促进了整个行业的技术进步,涌现了一批具有自主知识产权的重大新产品,生产的雷蒙磨粉机、三环中速磨粉机、立式磨粉机、超压梯形磨粉机、高压悬辊磨粉机、高压微分磨粉机等,其中生产LM系列磨煤机以其占地面积小、低电耗、检修方便、最新型、高效节能等优点,全面支持高炉喷吹煤粉技术应用,常与颚式破碎机等设备搭配使用,实现制粉系统中的干燥与研磨、收粉与除尘,填补了国内超大型磨粉机市场的空白,开创了国际工业磨粉高效、低能耗的新纪元。
- 1、下载文档前请自行甄别文档内容的完整性,平台不提供额外的编辑、内容补充、找答案等附加服务。
- 2、"仅部分预览"的文档,不可在线预览部分如存在完整性等问题,可反馈申请退款(可完整预览的文档不适用该条件!)。
- 3、如文档侵犯您的权益,请联系客服反馈,我们会尽快为您处理(人工客服工作时间:9:00-18:30)。
高炉制粉喷煤技术的研究与应用作者:王维乔1. 技术研发历程高炉喷吹煤粉可以降低焦炭消耗,减少炼焦污染,调节炉况,促进高炉稳定顺行,强化高炉冶炼。
首钢作为我国高炉喷煤技术的开创者和先行者,早在196 3年,就进行了系统的研究与试验,并于1964年在国内率先将其在高炉上进行工业化试验。
1966年,首钢在全公司的高炉上进行推广应用,当时的年平均喷煤量达159kg/tHM,最高月平均喷煤量达到279kg/tHM,创造了当时的世界纪录。
1994年,在首钢1726-2536m3四座高炉上应用,采用集中制粉,间接喷吹,串联罐多管路喷煤。
2000年,首钢进行重大技术改进,采用中速磨煤机制粉,布袋一级收粉,双系列串联罐直接喷吹,在首钢两座(1780m3、2536m3)高炉上应用,达到国际先进水平。
2004年,首钢国际工程公司设计的湘钢1800m3高炉,采用中速磨制粉,并列罐间接喷吹。
2007年,首钢国际工程公司设计的迁钢2号2650m3高炉,采用并列罐直接喷吹,并实现全自动喷煤操作。
2009年,首钢国际工程公司设计的京唐1号5500m3高炉,采用并列罐直接喷吹,全自动喷煤操作,并实现浓相输送。
2010年,首钢国际工程公司设计的迁钢3号4000m3高炉,采用并列罐直接喷吹,全自动喷煤。
2010年,首钢国际工程公司设计的京唐2号5500m3高炉,采用并列罐直接喷吹,浓相输送,全自动喷煤。
经过几十年的发展,首钢国际工程公司不断完善和优化设计,掌握了从原煤料场到煤粉制备和喷吹的全套高炉喷煤工艺设计。
近年来,首钢国际工程公司还参与编制了国家标准GB 50607-2010《高炉喷吹煤粉工程设计规范》。
2. 高炉喷吹煤粉技术的主要技术特点2.1 长距离直接喷吹,紧凑型布局由首钢国际工程公司设计的首钢2号、3号高炉喷煤工程,完全采用国产化技术和设备,采用紧凑型短流程工艺,实现了煤粉长距离直接喷吹。
2号高炉喷煤总管长度达到452m,已被列入第九批《中国企业新记录》。
该项工程经有关专家鉴定,达到国际先进水平。
2.2 浓相输送煤粉喷吹一般按输送浓度可分为稀相输送和浓相输送。
稀相输送工艺相对简单,运行比较稳定;而随着煤粉输送浓度的提高,虽然增加了运行不稳定的可能性,但其可以节约大量输送气体的消耗,并且减少了管道磨损,因此其降低了维护和运行费用。
为消除输送过程中的不稳定因素,可通过改善喷煤罐底部的流化状态,以及改善输送管道的补气系统和输送管路的布置,来达稳定运行的目的。
另外首钢国际工程公司通过吸收国内外先进技术,开发完善了浓相喷煤技术的设计,并将其成功应用于实施项目中。
从实际运行效果看,其输送连续,系统运行平稳,固气比可达到大于40kg/kg。
2.3 均匀喷吹煤粉分配方式现在主要以单管加分配器方式为主,分配器后各支管的煤粉均匀分配有利于高炉运行稳定顺行。
目前首钢国际工程公司的设计通常采用支管等阻损布置,通过计算机三维辅助设计软件,喷煤量常规偏差小于4%。
2.4 喷煤的全自动化操作和实时监控随着设备的大型化和操作的精度等要求的提高,高炉喷煤操作对于自动化控制要求也越来越高。
1) 全自动化操作提高了生产效率全自动喷吹可使储煤场,制粉系统,喷吹系统等过程实现PLC自动控制,不但减少人为主观不确定性和不完全准确性的影响,缓和手工计算与操作和喷煤对炉况影响的滞后性之间的矛盾,还可以大大减少误操作造成的损失,更能进一步减少在岗人员的数量,使得喷煤系统在时间和空间上都大幅度提高了生产效率。
2) 喷煤控制精度得到提高全自动喷吹以中速磨为核心,进行连锁控制,同时实现了对下煤量、煤温、喷煤量、充压稳压自动调节及自动倒罐。
在自动控制及计量和调节精度方面,按照高炉要求自动调节,喷煤量计量精度可以控制在1%误差范围内,各风口喷吹煤粉的均匀性控制在4%的误差范围内。
与以往手工计算调节控制相比,更加精确合理。
3) 实时监测在线检测系统内的气体成分和温度检测,一旦超过安全范围,自动报警,并进行相应的联锁吹扫或停机等操作。
2.5 三维软件辅助设计在普通的二维平面设计条件下,由于喷煤系统的管线繁多且错综复杂,管线与管线间或管线与电缆槽间现场发现相互干涉的问题再所难免,这样在现场安装施工时,不但需要返工增加费用,而且延误了施工工期。
为将喷煤系统的设计做到更高效、更精细,首钢国际工程公司引入了三维工厂设计软件。
该三维工厂设计软件集智能化建模、碰撞检查、出图及报表、全厂漫游等功能于一体,有效提高了设计及施工效率和准确性。
3. 典型工程及应用效果3.1 首钢四制粉首钢国际工程公司用不到一年的时间完成了首钢四制粉整个工程的设计和施工服务工作,并于2000年11月投产。
新的制粉喷煤系统与此前首钢的间接喷吹不同,采用了直接喷煤工艺,即制粉和喷煤同在一所厂房内。
制粉系统以两台中速磨作为主要设备,每台生产能力为40t/h(实际出力),制粉总能力为80t/h。
两套总管—分配器喷吹系统分别对2号高炉(1780m3)、3号高炉(2536m3)进行直接喷吹,喷吹工艺为双系列串联罐组、总管加分配器,分别为2号和3号高炉的喷吹煤粉。
2号高炉喷煤总管总长452m,3号高炉喷煤总管总长358m。
喷煤能力按每个高炉煤比200kg/t设计,喷吹煤种为烟煤。
本项工程采用长距离直接喷吹的新工艺,其主要技术特点如下:1)采用直接喷煤工艺,简化喷煤流程,在喷吹烟煤时更为安全。
厂房布置紧凑,占地面积小,大大节约了投资。
2号高炉喷煤总管总长达到452m,当时是国内最长的;2)大胆采用大倾角胶带机,在现有场地条件下,使利用旧储煤场的煤成为可能,即节省投资,又减少设备;3)采用新型封闭式干燥炉,在满足烟气温度条件下,使整个煤粉输送管道全部处于封闭状态,减少了系统漏风率,降低了氧含量,在喷吹烟煤时更为安全。
而且合理地利用了锅炉废气,节约了能源;4)采用中速磨煤机制粉,降低制粉运行费用,从而减少煤粉生产成本;5)采用高效低压脉冲煤粉收集器一级收粉工艺,简化工艺流程,提高了煤粉收集效率,而且使排尘浓度大大降低,减少了环境污染;6)设计中考虑两个系统之间煤粉的互相补充和分配,其结构简单实用,给生产创造许多方便;7)贮煤罐与喷煤罐之间设置压力平衡式波纹补偿器,提高连续喷煤过程中的计量精度;8)采用自动可调煤粉给料机和高精度煤粉分配器,以流化喷吹为前提,实现时间过程的均匀喷吹,消除了脉动煤流;9)提高自动化控制水平,实现喷煤倒罐自动控制和调节。
该工程经生产实践验证,证实是成功的,采用直接喷煤工艺也是非常合理的,为首钢进一步扩大喷煤量,提高煤比,创造了必要的先决条件。
该工程当时经专家鉴定达到国际先进水平。
另外,设计整体构思非常巧妙,布局合理,尤其是占地面积非常小,对旧厂改造来说值得借鉴,而且该工程总投资也是国内类似同等项目中最少的。
3.2 迁钢4000m3高炉制粉喷煤首钢国际工程公司设计的迁钢3号高炉,有效容积4000m3,设计煤比正常190kg/tHM,设备能力可达250kg/tHM。
在原有煤场基础上进行改造,新建1座配煤间,设置10个圆筒仓,可同时满足厂区内3座高炉24h连续正常喷吹原煤需要;原煤运输本次选用管式皮带机运煤,相比传统皮带机原煤运输,解决了长距离运输时皮带机通廊布置困难和转运站多的问题,同时管式皮带机还具有占地面积小,环保清洁,允许上行或下行皮带同时两个方向输送以及多点物料输入,并可以根据地形位置进行空间曲线布置等优点,而且减少建设费用和时间,此外在厂房东侧还备有一条大倾角皮带机可临时使用汽车进行上煤;新建制粉喷吹厂房,采用直接喷吹工艺,即制粉喷煤同建在一座厂房内,制粉选用弹簧加载的中速磨煤机和一次布袋煤粉收集器收粉,制粉能力可达75t/h;喷吹系统形式为并列喷吹罐布置、单管路加煤粉分配器,其中引进一些先进的设计理念,如采用全自动喷吹控制、喷煤支管煤粉均匀分配等。
另外,为保证喷吹气使用稳定设有单独喷煤空压站,且在厂房内设有压缩空气和氮气缓冲储气罐。
该工程投产三年多来,运行良好,各生产指标达到或超过预期水平。
3.3 京唐2座5500m3高炉制粉喷煤系统首钢国际工程公司自主设计的两座5500m3特大型高炉,是当时国内容积最大的高炉,设计煤比200kg/tHM,设备能力最高可达250kg/tHM。
喷吹煤种为烟煤或混煤。
采用制粉喷吹合建在一所厂房内。
中速磨制粉、一级袋式煤粉收集器、直接喷吹工艺。
每座高炉配备2台中速磨,单台制粉能力为≥75t/h;采用热风炉废气作为煤粉干燥的主要介质。
在制粉系统末端设置2台排粉风机作为整个系统的动力源,风机出口设置消音器,以减小系统的噪声污染,使噪音指标低于85dB;系统排放浓度小于20mg/m3。
喷煤系统每座高炉设置3个并列布置的喷煤罐交替向高炉喷煤,它们共用一个煤粉仓,煤粉仓有效容积1200m3,喷煤罐有效容积为90m3,正常喷吹周期为30min。
每个喷煤罐为2个出煤口,6根喷煤管最终汇入2根喷煤总管中,分别输送至2台煤粉分配器,再由42根喷煤支管喷入高炉风口。
每根总管上都装有煤粉流量计和调节阀,其调节和计量精度小于4%。
采用浓相输送技术,固气比在40kg/kg以上,极大降低了输送气体的消耗量;管道内煤粉流速可达2~4m/s,这对于输送管道和弯头几乎不会产生磨损。
煤粉分配器的出口设有等阻损装置,喷煤支管路采用等长度设计,偏差小于1m,以保证煤粉分配器各出口均匀分配煤粉量,减少各高炉风口煤粉量分配的不均匀。
喷煤罐的充压、煤粉的输送、系统的流化及防爆吹扫全部采用氮气,避免了火灾和爆炸发生的可能性。
系统全自动操作,机旁设手动应急操作。
设有温度、压力、流量、重量和料位等的显示、报警等功能。
喷煤量按设定值自动调节,如果出现紧急情况,可启动紧急停止按钮,全系统可自动地向安全方向运行。
喷煤的倒罐操作、喷吹操作、停止操作、吹扫操作、事故停止操作均为程序自动控制。
首钢京唐钢铁厂高炉喷煤系统的设计和装备达到了国际先进水平,作为国内首座5000m3级以上的高炉,为其他特大型高炉的建设提供了宝贵经验。
4. 结语首钢国际工程公司的制粉喷煤技术源自于百年首钢,但在不断承接国内外项目的同时,也在不断提高和完善。
近年来,首钢国际工程公司与国外公司合作,引进并吸收了诸多先进的喷煤技术和设计理念,将其应用于项目当中,同时也为公司培养了一大批中青年技术专家。
目前,公司的制粉喷煤工程设计和工程总承包业绩遍布国内外。
公司技术团队正按照“引领绿色钢铁未来”追求,以先进的首钢制粉喷煤技术竭诚为社会各界提供最优质的服务,为开创我国冶金技术新的飞跃发展,做出更大的贡献。