如何进行铣削加工的准备
数控铣削加工的对刀操作

数控铣削加工的对刀操作数控铣削加工是一种高效、精密的加工方式。
其中,对刀操作是一项关键步骤,它直接影响到加工质量和效率。
本文将介绍数控铣削加工的对刀操作方法,帮助读者更好地了解和掌握该技巧。
一、对刀操作前的准备工作1. 准备好必要的工具和设备,例如对刀仪、铣刀、卡板、卡钳等。
2. 清洁加工平台和夹具,确保其表面干净、平整。
3. 检查数控铣削机床的零点和坐标系设置是否正确。
4. 安装好铣削主轴和夹具,确认其稳定可靠,没有松动和变形的情况。
二、对刀操作步骤1. 安装对刀仪将对刀仪插入铣削主轴中,使用卡板和卡钳将其固定在主轴上,确保其与夹具垂直,并调整好高度。
2. 定义坐标系使用数控系统的坐标系界面,定义好加工坐标系和工件坐标系,并确定它们之间的转换关系。
3. 加工零点设定将铣刀对准工件的初始切入点,使用数控系统的调试界面,设定加工零点,通常为工件坐标系原点或夹具中心。
4. 对刀点坐标计算根据铣削刀具的半径和加工路径,计算出铣削切入点的坐标位置,在数控系统的坐标系界面中设定对刀点坐标。
5. 夹紧工件将待加工的工件夹紧在夹具上,设计好铣削路径和深度,调整工件位置和夹紧力度。
6. 对刀操作启动数控系统,并按照设定好的路径和深度进行自动对刀操作,观察铣刀和工件的接触情况和相对位置,根据数控系统显示器上的对刀结果信息,调整铣削主轴高度和工件位置,直到达到精确的对刀效果。
7. 对刀结果确认对刀操作完成后,使用数控系统的测量功能,对加工后的工件进行测量和检查,确保其尺寸和形状符合要求。
三、注意事项1. 在对刀操作前,必须先进行加工准备工作,特别是检查加工平台和设备的状态和功能。
2. 在对刀操作中,必须使用专业的对刀仪和铣刀,并遵守安全操作规程,防止发生意外伤害。
3. 对刀操作中,必须准确计算和设定对刀点坐标和夹紧力度,确保加工精度和效率。
4. 对刀操作完成后,必须进行对刀结果确认和工件检查,确保其质量符合要求,避免浪费时间和材料资源。
cnc铣面操作流程

cnc铣面操作流程CNC铣面操作流程是指利用数控铣床进行铣削加工的一系列步骤。
数控铣床是一种通过计算机程序控制工件在三维空间内进行切削加工的机床,具有高精度、高效率和灵活性等优点。
下面将介绍CNC铣面操作流程的具体步骤。
首先,操作人员需要准备好工件和刀具。
工件是需要进行铣削加工的零件,而刀具则是用来切削工件的工具。
在选择刀具时,需要根据工件的材料和加工要求来确定合适的刀具类型和规格。
接下来,操作人员需要将工件夹紧在数控铣床的工作台上,并根据工件的尺寸和形状来确定工件的坐标原点。
通过数控系统的坐标设定功能,可以将工件的坐标原点与数控铣床的坐标系进行对应。
然后,操作人员需要编写加工程序。
加工程序是通过编程软件编写的一系列指令,用来控制数控铣床进行铣削加工。
在编写加工程序时,需要考虑工件的形状、尺寸和表面粗糙度等因素,以确保加工质量和效率。
接下来,操作人员将编写好的加工程序上传到数控铣床的控制系统中,并进行调试和检查。
通过数控系统的仿真功能,可以预先模拟加工过程,以确保程序的准确性和可靠性。
最后,操作人员启动数控铣床进行铣削加工。
在加工过程中,数控系统会根据预先编写的加工程序控制刀具的运动轨迹和切削参数,实现对工件的精确加工。
同时,操作人员需要及时监控加工过程,确保加工质量和安全。
总的来说,CNC铣面操作流程包括准备工件和刀具、确定工件坐标原点、编写加工程序、上传程序和调试、启动数控铣床进行加工等步骤。
通过科学规范的操作流程,可以提高加工效率、保证加工质量,实现数控铣床的高效运行。
金属切削加工基本安全操作规程
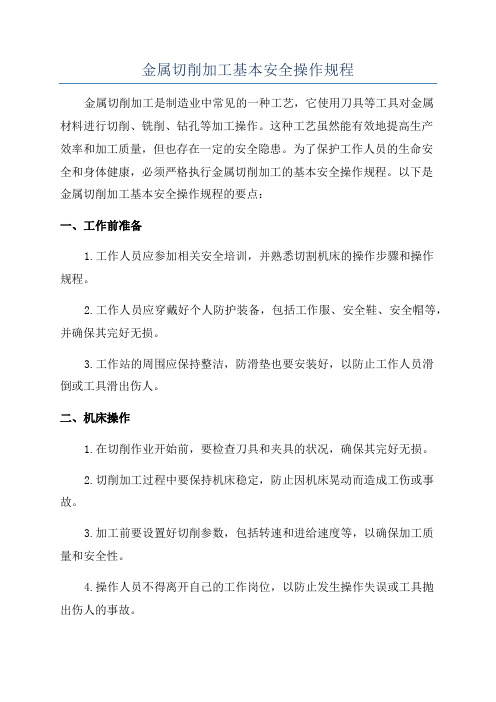
金属切削加工基本安全操作规程金属切削加工是制造业中常见的一种工艺,它使用刀具等工具对金属材料进行切削、铣削、钻孔等加工操作。
这种工艺虽然能有效地提高生产效率和加工质量,但也存在一定的安全隐患。
为了保护工作人员的生命安全和身体健康,必须严格执行金属切削加工的基本安全操作规程。
以下是金属切削加工基本安全操作规程的要点:一、工作前准备1.工作人员应参加相关安全培训,并熟悉切割机床的操作步骤和操作规程。
2.工作人员应穿戴好个人防护装备,包括工作服、安全鞋、安全帽等,并确保其完好无损。
3.工作站的周围应保持整洁,防滑垫也要安装好,以防止工作人员滑倒或工具滑出伤人。
二、机床操作1.在切削作业开始前,要检查刀具和夹具的状况,确保其完好无损。
2.切削加工过程中要保持机床稳定,防止因机床晃动而造成工伤或事故。
3.加工前要设置好切削参数,包括转速和进给速度等,以确保加工质量和安全性。
4.操作人员不得离开自己的工作岗位,以防止发生操作失误或工具抛出伤人的事故。
三、刀具更换和维护1.更换刀具前,必须先关闭机床电源,并确保刀具完全停止运转之后,才能进行更换操作。
2.更换刀具时要佩戴好劳动保护用品,使用适当的工具,并按照正确的步骤进行操作,以防止刀具伤人或滑动摔伤的事故。
3.刀具使用后要进行定期检查和维护,如发现刀具磨损严重或有裂纹等问题,应立即更换或修理。
四、安全防护措施1.切削加工区域应设置明显的安全警示标志和警示标识,以提醒工作人员注意安全。
2.在切削过程中,应使用对眼睛和皮肤有保护作用的护目镜和手套,以防止金属屑或切削油喷溅伤人。
3.尽量减少切削液的使用量,以减少对环境和操作人员的危害。
五、操作人员自身注意事项1.工作时要保持专注和集中注意力,切忌分心和疲劳操作,以免引发事故。
2.操作人员切勿私自进行非法操作或改装机床,以免发生安全事故。
3.发现异常情况或设备故障时,要立即停止加工操作,并向上级报告处理。
通过遵守这些金属切削加工基本安全操作规程,可以有效降低切削加工过程中发生事故的风险,保障工作人员的安全和健康。
典型薄壁零件数控铣削加工工艺

典型薄壁零件数控铣削加工工艺随着制造业的发展,数控加工技术逐渐成为最常用的加工方法之一。
而在数控加工领域中,数控铣削技术是常见的加工方法之一。
本文将介绍典型薄壁零件数控铣削加工工艺,包括工艺准备、加工流程、刀具选择和切削参数等方面的内容。
一、工艺准备1.1 材料选择因为薄壁零件通常是轻型结构件,所以材料一般选择铝合金、镁合金、不锈钢等轻质、高强度的材料。
1.2 工件夹紧在加工薄壁零件时,一定要保证工件夹紧牢固。
否则,易造成加工过程中工件的振动或位移,导致加工精度降低。
1.3 加工精度要求由于薄壁零件的厚度较小,所以在加工过程中要保证加工精度高,以防加工出错或造成损失。
二、加工流程2.1 预处理将所选材料进行预处理,包括去表面氧化层、去毛刺等。
2.2 下刀编制好数控加工程序后,进行下刀和切割。
2.3 清洗清洗零件,以便检查和测试。
2.4 检测检测零件的精度、结构、特性等。
如果不合格,要重新加工。
进行表面处理,包括抛光、喷漆、防锈等。
三、刀具选择在加工薄壁零件时,需要选用比较特殊的刀具。
常用的刀具主要包括切割刀具、削铣刀具、倒角刀具、钻头等。
3.1 切割刀具为了保证零件表面的质量和精度,需要选用切割刀具。
切割刀具的作用是将零件中的材料割离,形成所需的几何形状。
在进行倒角时,需要选用倒角刀具。
倒角刀具能够将薄壁零件边缘处的角进行倒角处理,使其具有更好的平滑度和美观度。
3.4 钻头在加工薄壁零件时,常常需要进行孔加工。
钻头是一种常用的刀具,在加工孔时经常被使用。
四、切削参数在加工薄壁零件时,需要注意切削参数的选择。
切削参数对加工质量起着重要的影响。
4.1 切削速度切削速度是指刀具在切割过程中移动的速度。
切削速度过快,容易导致刀具磨损、表面质量差等问题。
切削速度过慢,加工效率低下。
切削深度是指刀具在一次切削过程中切入材料的深度。
切削深度过大,会导致切屑对切削影响的加重,影响加工质量和效率。
总之,在加工薄壁零件时需要注意工艺准备、加工流程、刀具选择和切削参数等方面的内容。
铣削平面的工艺流程

铣削平面的工艺流程
铣削平面是一种常见的金属加工工艺,用于加工平面零件。
其工艺流程主要包括以下几个步骤:
1. 设计加工方案。
根据零件图纸和要求,确定加工平面的尺寸、精度和表面要求,选择适当的工艺参数和加工工具。
2. 准备工作。
将工件固定在加工平台上,检查加工工具和夹具的磨损和损坏情况,并进行必要的更换和调整。
3. 粗加工。
根据加工方案和工艺参数,进行初次铣削,去除工件表面的毛刺和明显凸起部分,达到初步加工平面。
4. 精加工。
根据加工方案和工艺参数,再次铣削,去除表面的细小凸起和瑕疵,达到高精度的平面加工。
5. 完成加工。
进行表面处理,如打磨、抛光等,使加工平面达到要求的光洁度和表面光滑度。
6. 检查验收。
进行零件尺寸和表面质量的检查,确保加工结果符合要求。
以上是铣削平面的基本工艺流程,不同的工件和加工要求可能会有所差异,需要依据实际情况进行调整和改变。
- 1 -。
铣工安全操作规程
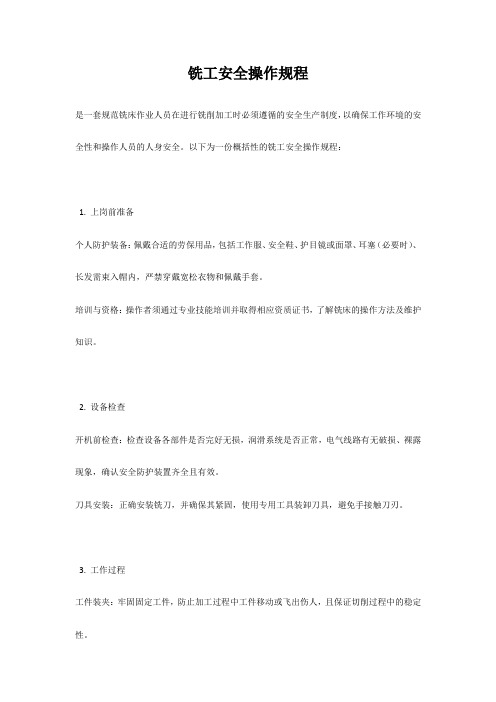
铣工安全操作规程是一套规范铣床作业人员在进行铣削加工时必须遵循的安全生产制度,以确保工作环境的安全性和操作人员的人身安全。
以下为一份概括性的铣工安全操作规程:1. 上岗前准备个人防护装备:佩戴合适的劳保用品,包括工作服、安全鞋、护目镜或面罩、耳塞(必要时)、长发需束入帽内,严禁穿戴宽松衣物和佩戴手套。
培训与资格:操作者须通过专业技能培训并取得相应资质证书,了解铣床的操作方法及维护知识。
2. 设备检查开机前检查:检查设备各部件是否完好无损,润滑系统是否正常,电气线路有无破损、裸露现象,确认安全防护装置齐全且有效。
刀具安装:正确安装铣刀,并确保其紧固,使用专用工具装卸刀具,避免手接触刀刃。
3. 工作过程工件装夹:牢固固定工件,防止加工过程中工件移动或飞出伤人,且保证切削过程中的稳定性。
启动顺序:先开冷却液系统,然后依次启动主轴电动机,待运行平稳后再开始进给运动。
禁止行为:切削过程中严禁身体任何部位进入危险区域,不得戴手套操作或清理铁屑,高速切削时应加设挡板,以防碎屑飞溅。
4. 操作规程速度调整:根据工件材料、硬度和切削深度合理选择切削速度和进给量,遵守机床的最大允许负荷。
紧急停车:熟悉并掌握紧急停止按钮的位置和使用方法,在发生异常情况时立即停机处理。
多人协作:若需多人协同操作,应明确分工,保持良好沟通,确保操作协调一致。
5. 维护保养与清洁停机后操作:加工结束后,及时关闭电源,清理工作台和刀具上的铁屑,恢复设备至初始状态。
定期维护:按照设备维护计划对铣床进行定期保养,更换磨损部件,确保设备处于良好工作状态。
6. 应急预案熟悉应急预案,如火灾、设备故障等突发情况下的应急措施,并定期组织应急演练。
以上仅为简要概括,实际操作中应严格参照详细版《铣工安全操作规程》以及企业内部相关规定执行。
键槽零件的铣削加工
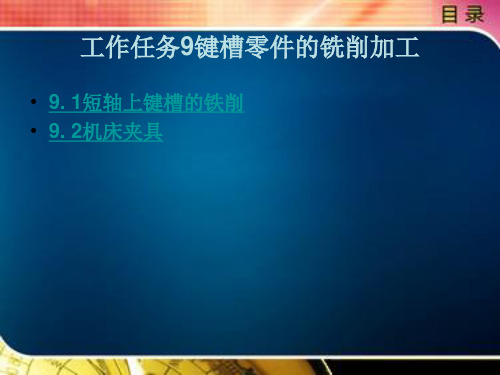
9. 2机床夹具
• (5)连接元件。 • 连接元件是确定夹具在机床上正确位置的元件。图9. 3中夹具体3的
底面为安装基面,保证了钻套1的轴线垂直于钻床工作台以及圆柱销s 的轴线平行于钻床工作台。因此,夹具体可兼作连接元件。车床夹具 上的过渡盘、铣床夹具上的定位键都是连接元件。 • (6)其他装置或元件。 • 根据加工需要,有些夹具分别采用分度装置、靠模装置、上下料装置、 顶出器和平衡块等。这些元件或装置也需要专门设计。
③刀具相对夹具占有正确位置。 • 显然,工件的定位是其中极为重要的一个环节。 • 1.六点定位原则
上一页 下一页 返回
9. 2机床夹具
• 一个尚未定位的工件,其空间位置是不确定的,这种位置的不确定
• 9.1.2操作过程
• 1.工件的装夹 • 从图9. 1上的标注不难看出,轴上键槽两侧面的表面粗糙度值较小
(Ra = 3. 2μm ),都有极高的宽度尺寸精度要求和对称度要求。因此, 在装夹工件时,不但要保证工件在加工中稳定可靠,还要保证工件的 轴线位置不变,保证键槽的中心平面通过其轴线。轴类工件常用的装 夹方法有用平口钳装夹、用V形垫铁装夹和用分度头定中心装夹等, 由于本零件长度较短,且为单件加工,所以用平口钳装夹较好。
• 用夹具装夹工件的优点包括以下几点。 • (1)能稳定地保证工件的加工精度。用夹具装夹工件时,工件相对于
刀具及机床的位置精度由夹具保证,不受工人技术水平的影响,使一 批工件的加工精度趋于一致。
上一页 下一页 返回
9. 2机床夹具
• (2)能提高劳动生产率。使用夹具装夹工件方便、快速,工件不需要 划线找正,可显著地减少辅助工时,提高劳动生产率;工件在夹具中 装夹后提高了工件的刚性,因此可加大切削用量,提高劳动生产率; 可使用多件、多工位装夹工件的夹具,并可采用高效夹紧机构,进一 步提高劳动生产率。
动态外形铣削的参数设置流程
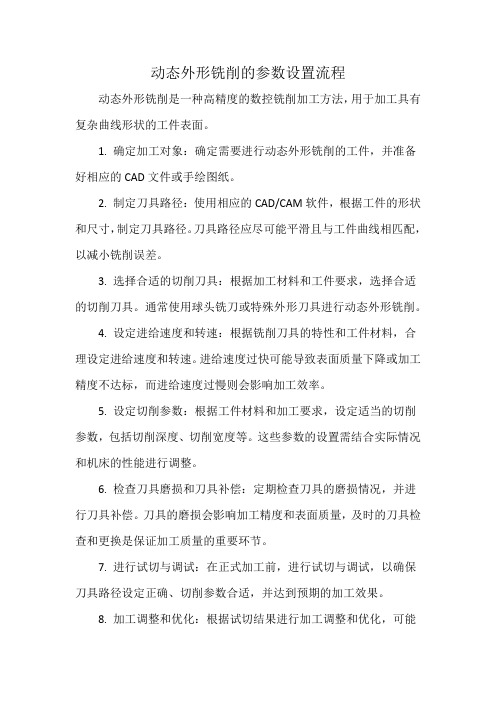
动态外形铣削的参数设置流程
动态外形铣削是一种高精度的数控铣削加工方法,用于加工具有复杂曲线形状的工件表面。
1. 确定加工对象:确定需要进行动态外形铣削的工件,并准备好相应的CAD文件或手绘图纸。
2. 制定刀具路径:使用相应的CAD/CAM软件,根据工件的形状和尺寸,制定刀具路径。
刀具路径应尽可能平滑且与工件曲线相匹配,以减小铣削误差。
3. 选择合适的切削刀具:根据加工材料和工件要求,选择合适的切削刀具。
通常使用球头铣刀或特殊外形刀具进行动态外形铣削。
4. 设定进给速度和转速:根据铣削刀具的特性和工件材料,合理设定进给速度和转速。
进给速度过快可能导致表面质量下降或加工精度不达标,而进给速度过慢则会影响加工效率。
5. 设定切削参数:根据工件材料和加工要求,设定适当的切削参数,包括切削深度、切削宽度等。
这些参数的设置需结合实际情况和机床的性能进行调整。
6. 检查刀具磨损和刀具补偿:定期检查刀具的磨损情况,并进行刀具补偿。
刀具的磨损会影响加工精度和表面质量,及时的刀具检查和更换是保证加工质量的重要环节。
7. 进行试切与调试:在正式加工前,进行试切与调试,以确保刀具路径设定正确、切削参数合适,并达到预期的加工效果。
8. 加工调整和优化:根据试切结果进行加工调整和优化,可能
需要微调刀具路径、进给速度、转速等参数,以获得更精准的加工效果。
铣床的机械加工工艺卡

铣床的机械加工工艺卡铣床是一种常用的金属加工设备,用于加工各类平面、曲线和复杂立体形状的工件。
下面将介绍铣床的机械加工工艺卡。
1. 工件设计与准备在进行铣削加工前,首先需要对工件进行设计与准备。
根据工件的要求和图纸,确定材料、尺寸、形状等参数,并进行合理的切削判断和刀具选择。
2. 设计加工方案根据工件的形状和加工要求,设计出合理的加工方案。
包括切削路径、切削深度、切削速度、进给速度等参数的确定。
3. 选择合适的刀具根据工件的材料和加工要求,选择合适的刀具。
刀具的选择要考虑到材料的切削性能、刀具的耐磨性和刚度等因素。
常用的铣削刀具有平面铣刀、立铣刀、球头铣刀、槽铣刀等。
4. 确定机床参数根据加工方案和刀具要求,确定机床的相关参数。
包括主轴转速、进给速度、切削深度和加工路径等参数。
这些参数的选择要根据材料的硬度、切削性能和刀具的性能等因素进行合理的选取。
5. 加工工序根据加工方案和工件要求,将加工过程分成多个工序。
根据不同的工序,选择合适的切削条件和加工方法。
在每个工序中,要注意加工刀具的刃磨、冷却液的使用和加工表面的检查。
6. 加工过程控制在铣床的加工过程中,要注意切削条件的控制。
保持合理的切削速度和进给速度,避免因切削过度或不足导致加工表面质量下降或刀具损坏。
同时,要合理选择刀具和保持刀具的刃磨状态,避免刀具在加工过程中过早磨损。
7. 加工表面处理在加工过程结束后,要对加工表面进行处理。
包括去除切削残留物、清洁表面和检查表面质量。
使用适量的冷却液和切削油,有助于提高切削效果和加工表面质量。
8. 检查和质量控制在加工完成后,要进行工件表面质量和尺寸的检查。
使用合适的测量工具,检测工件的尺寸偏差和形状误差。
如果存在问题,要及时调整加工参数和重新加工。
9. 加工记录和改进在加工过程中,要做好加工记录和数据统计。
将每个工序的加工参数和质量数据记录下来,以便于后期的分析和改进。
根据加工数据和问题分析,及时调整加工参数和改进加工工艺,以提高加工效率和质量。
铣削主要的加工工艺
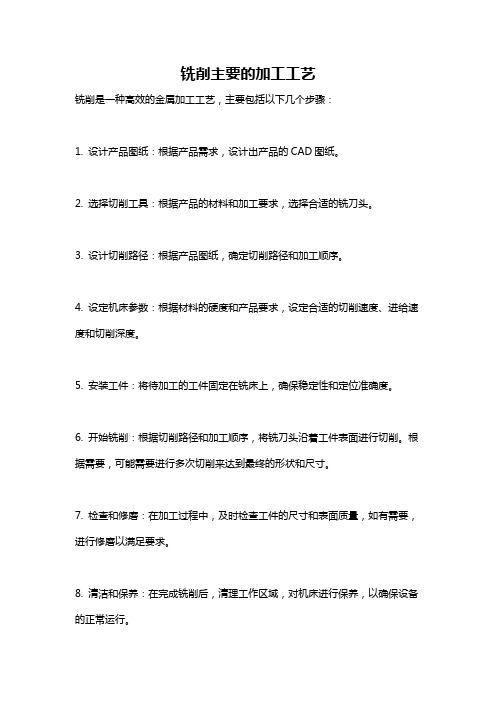
铣削主要的加工工艺
铣削是一种高效的金属加工工艺,主要包括以下几个步骤:
1. 设计产品图纸:根据产品需求,设计出产品的CAD图纸。
2. 选择切削工具:根据产品的材料和加工要求,选择合适的铣刀头。
3. 设计切削路径:根据产品图纸,确定切削路径和加工顺序。
4. 设定机床参数:根据材料的硬度和产品要求,设定合适的切削速度、进给速度和切削深度。
5. 安装工件:将待加工的工件固定在铣床上,确保稳定性和定位准确度。
6. 开始铣削:根据切削路径和加工顺序,将铣刀头沿着工件表面进行切削。
根据需要,可能需要进行多次切削来达到最终的形状和尺寸。
7. 检查和修磨:在加工过程中,及时检查工件的尺寸和表面质量,如有需要,进行修磨以满足要求。
8. 清洁和保养:在完成铣削后,清理工作区域,对机床进行保养,以确保设备的正常运行。
铣削是一种常见的金属加工工艺,适用于各种形状和尺寸的工件,可以用于加工平面、曲面、凸轮槽等。
铣削广泛应用于机械制造、汽车制造、航空航天等行业,是一项重要的制造工艺。
铣床加工流程

铣床加工流程铣床是一种常见的金属加工设备,广泛应用于机械制造、航空航天、汽车制造等领域。
铣床加工流程是指在铣床上进行金属材料的切削加工过程,下面将详细介绍铣床加工的流程及注意事项。
1. 铣床加工前的准备。
在进行铣床加工之前,首先需要对工件和刀具进行准备。
工件应该进行检查,保证其表面平整、无裂纹和磨损,以确保加工质量。
刀具也需要进行检查和安装,确保刀具的刃部锋利,刀柄固定牢固。
此外,还需要对铣床进行检查和调整,确保设备运转正常。
2. 刀具路径规划。
在进行铣床加工之前,需要根据工件的形状和尺寸,规划刀具的路径。
通过CAD软件或者手工绘制,确定切削路径和切削深度,以确保加工出符合要求的工件。
3. 工件夹紧和定位。
在进行铣床加工之前,需要将工件夹紧在工作台上,并进行定位。
夹紧和定位的准确性直接影响加工质量,因此需要仔细调整夹紧装置和定位装置,确保工件不会移动或者晃动。
4. 铣削加工。
铣削加工是铣床加工的主要过程,通过刀具在工件表面上旋转切削,将工件表面切削成所需的形状和尺寸。
在进行铣削加工时,需要根据刀具路径规划,逐步进行切削,控制切削深度和进给速度,确保加工质量。
5. 清洁和检查。
在完成铣床加工后,需要对工件和铣床进行清洁和检查。
清洁工件表面的切削屑和油污,以便后续的加工或者使用。
同时,需要对工件进行检查,确保加工质量符合要求。
6. 工件卸载。
在完成铣床加工后,需要将工件从工作台上卸载。
在卸载工件时,需要注意操作规范,避免因操作不当导致工件损坏或者人身伤害。
7. 加工记录和总结。
在完成铣床加工后,需要对加工过程进行记录和总结。
记录加工参数、加工时间、加工质量等信息,以便后续的工艺分析和质量控制。
总之,铣床加工流程包括准备、刀具路径规划、工件夹紧和定位、铣削加工、清洁和检查、工件卸载以及加工记录和总结等环节。
在进行铣床加工时,需要严格按照流程进行操作,确保加工质量和安全生产。
薄壁件铣削加工工艺
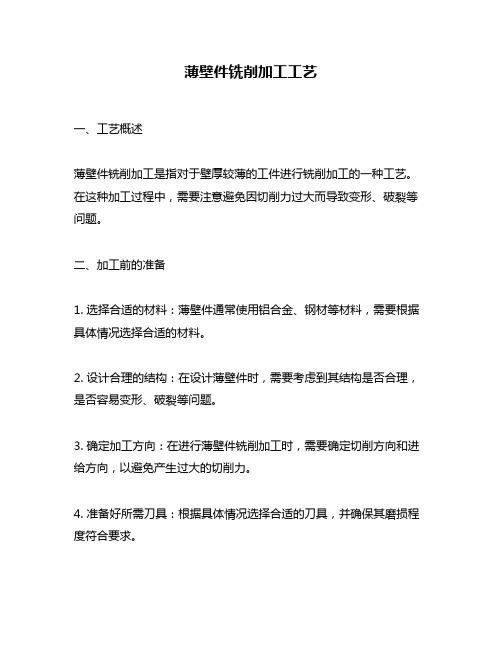
薄壁件铣削加工工艺一、工艺概述薄壁件铣削加工是指对于壁厚较薄的工件进行铣削加工的一种工艺。
在这种加工过程中,需要注意避免因切削力过大而导致变形、破裂等问题。
二、加工前的准备1. 选择合适的材料:薄壁件通常使用铝合金、钢材等材料,需要根据具体情况选择合适的材料。
2. 设计合理的结构:在设计薄壁件时,需要考虑到其结构是否合理,是否容易变形、破裂等问题。
3. 确定加工方向:在进行薄壁件铣削加工时,需要确定切削方向和进给方向,以避免产生过大的切削力。
4. 准备好所需刀具:根据具体情况选择合适的刀具,并确保其磨损程度符合要求。
三、加工过程1. 切割前处理:将薄壁件固定在机床上,并使用夹具固定好位置。
同时检查夹具是否牢固,以避免因夹具不牢导致的误差。
2. 粗铣:根据加工要求选择合适的切削速度和进给速度,并进行粗铣。
在粗铣时,需要注意切削深度和切削宽度的控制,以避免过大的切削力。
3. 半精铣:在粗铣完成后,进行半精铣。
在半精铣时,需要控制好刀具的磨损程度,并根据加工要求选择合适的切削参数。
4. 精铣:最后进行精铣。
在精铣时,需要控制好加工温度和表面质量,并使用合适的冷却液降低温度。
四、加工后处理1. 去毛刺:在加工完成后,需要去除薄壁件表面的毛刺,以保证其表面质量。
2. 洗净清理:将薄壁件洗净并清理干净,在检查其尺寸是否符合要求。
3. 包装运输:将薄壁件包装好,并妥善运输到指定地点。
五、注意事项1. 避免过大的切削力:在进行薄壁件铣削加工时,需要注意避免因切削力过大而导致变形、破裂等问题。
2. 选择合适的刀具:根据加工要求选择合适的刀具,并确保其磨损程度符合要求。
3. 控制好加工温度:在进行薄壁件铣削加工时,需要注意控制好加工温度,以避免因过高的温度导致变形、破裂等问题。
4. 检查夹具是否牢固:在进行薄壁件铣削加工时,需要检查夹具是否牢固,以避免因夹具不牢导致的误差。
电池极柱铣削工艺流程

电池极柱铣削工艺流程1.材料准备电池极柱通常由铝合金或钢材料制成,首先需要对材料进行准备。
根据产品要求,选择适当的材料,并按照预定规格将材料切割成合适的尺寸。
2.铣削前处理在进行铣削之前,需要对材料进行一些预处理。
首先,清洗材料表面的杂质和污垢,确保材料表面干净。
然后,对材料进行酸洗处理,以去除材料表面的氧化物。
最后,进行表面处理,增加材料表面的粗糙度,提高铣削后的精度。
3.设计工艺路线根据产品的要求和规格,设计出适合的工艺路线。
包括工艺方案、机床设备的选择、刀具规格的确定等,确保能够达到产品的要求。
4.刀具选择根据工艺路线和材料的特性,选择适合的刀具。
刀具的选择应考虑到切削力、切削热量和表面质量等因素。
5.铣削加工根据工艺路线,在机床上进行铣削加工。
首先,将材料夹持在机床上,并进行定位和固定。
然后,根据工艺要求,设置好刀具的进给、转速和切削深度等参数。
最后,启动机床,进行铣削加工。
6.检验质量在铣削加工完成后,对加工件进行质量检验。
主要包括外观检查、尺寸测量、表面粗糙度检测等。
通过质量检验,确保加工件的质量符合要求。
7.表面处理铣削加工后,需要对加工件进行表面处理。
主要包括去毛刺、除氧化层、抛光等。
表面处理能改善加工件的外观质量和耐蚀性。
8.包装出库经过表面处理后,将加工件进行包装,并按照产品要求进行出库。
以上就是电池极柱铣削的工艺流程。
电池极柱的铣削加工需要确保加工过程的精度和质量,提高工艺效率和产品性能。
数控铣削加工工艺分析
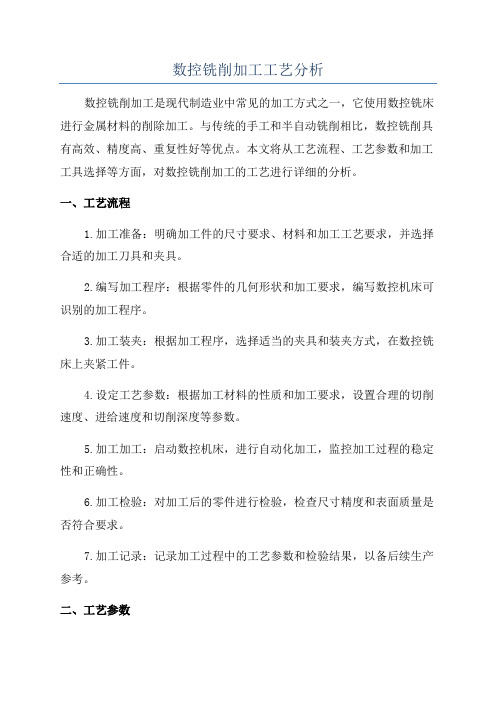
数控铣削加工工艺分析数控铣削加工是现代制造业中常见的加工方式之一,它使用数控铣床进行金属材料的削除加工。
与传统的手工和半自动铣削相比,数控铣削具有高效、精度高、重复性好等优点。
本文将从工艺流程、工艺参数和加工工具选择等方面,对数控铣削加工的工艺进行详细的分析。
一、工艺流程1.加工准备:明确加工件的尺寸要求、材料和加工工艺要求,并选择合适的加工刀具和夹具。
2.编写加工程序:根据零件的几何形状和加工要求,编写数控机床可识别的加工程序。
3.加工装夹:根据加工程序,选择适当的夹具和装夹方式,在数控铣床上夹紧工件。
4.设定工艺参数:根据加工材料的性质和加工要求,设置合理的切削速度、进给速度和切削深度等参数。
5.加工加工:启动数控机床,进行自动化加工,监控加工过程的稳定性和正确性。
6.加工检验:对加工后的零件进行检验,检查尺寸精度和表面质量是否符合要求。
7.加工记录:记录加工过程中的工艺参数和检验结果,以备后续生产参考。
二、工艺参数1.切削速度:是指刀具在单位时间内切削的长度。
根据加工材料的硬度和切削性能,合理选择切削速度,既能保证加工效率,又能保证刀具寿命。
2.进给速度:是指刀具在单位时间内在加工方向上移动的距离。
进给速度的选择应考虑切削力和切削表面的要求。
3.切削深度:是指刀具在一次进给过程中所削除的材料层厚度。
切削深度的选择应使得切削力合理,既能保证加工效率,又能避免切削表面的质量。
4.刀具半径补偿:数控铣床会自动根据刀具半径补偿值进行补偿,使得加工轮廓与设计轮廓一致。
5.加工顺序:根据零件的几何形状和切削力的分布情况,合理选择加工顺序,避免零件变形和加工过程中的切削力过大。
三、加工工具选择1.刀具材料:刀具材料应具有一定的硬度、耐磨性和耐冲击性,常用的刀具材料有硬质合金、高速钢和陶瓷等。
2.刀具形状:根据零件的几何形状和加工要求,选择合适的刀具形状,如平面铣刀、立铣刀、球头铣刀等。
3.切削刃数:根据加工材料的硬度和切削性能,选择合适的刀具刃数,既能保证加工效率,又能保证刀具寿命。
轴加工工艺流程

轴加工工艺流程轴加工是一种常见的机械加工方式,用于制造各种类型的轴类零件。
下面将介绍一种常见的轴加工工艺流程。
1.材料准备:首先需要准备合适的材料,通常选择优质的金属材料,如钢材、铝材等,并根据轴的用途和要求选择合适的材料规格。
2.材料铣削:将准备好的材料放置在铣床上进行铣削加工。
首先进行表面粗铣,将材料的表面切削成一个平整的面,然后进行精铣,将材料的表面进行更加精细的加工。
3.车削加工:将已经铣削好的材料放置在车床上进行车削加工。
根据轴的形状和要求,进行内径和外径的车削加工,使得轴达到所需的形状和尺寸。
4.切削工艺:根据轴的要求,进行各种切削工艺,如齿轮加工、螺纹加工等。
根据轴的用途和要求,选择合适的刀具和切削参数,进行相应的切削操作。
5.热处理:对于一些需要提高轴的硬度和强度的情况,可以进行热处理。
常见的热处理方式有淬火、回火、等等。
通过合适的热处理工艺,提高轴的性能和使用寿命。
6.精密加工:对于一些对轴要求更高的情况,可以进行精密加工。
通过加工中心、磨床等设备进行精密加工,使得轴的尺寸和形状更加精确。
同时,可以进行光洁度处理,使得轴的表面更加光滑。
7.表面处理:根据轴的要求,进行相应的表面处理。
常见的表面处理方式有镀锌、喷涂等。
通过表面处理,提高轴的抗腐蚀性能和美观度。
8.组装和检测:对于一些需要进行组装的轴,进行相应的组装操作。
同时,对于轴的尺寸、形状、质量等进行检测,确保轴的质量达到要求。
以上为一种常见的轴加工工艺流程,根据具体的需求和要求,可能会有所不同。
在轴加工过程中,需要注意选择合适的工艺参数和设备,确保轴的质量和性能达到要求。
铣削操作的方法和顺序

铣削操作的方法和顺序
铣削操作是一种机械加工方法,使用铣床、铣刀等工具对工件进行切削、切削加工。
下面是铣削操作的一般方法和顺序:
1. 准备工作
准备好需要加工的工件和铣床,调整铣床的工作台和工作头的位置和角度,选择合适的铣刀和加工参数。
2. 固定工件
使用夹具将工件固定在铣床的工作台上,以保证工件的稳定和精度。
3. 设定加工参数
将铣刀和铣床按照工艺要求进行调整和设定加工参数,包括铣刀的转速、进给量、进给速度等。
4. 处理工件表面
用铣刀进行表面处理,以便铣削出高质量的表面。
在表面处理前,最好用软布清洁工件表面,以去除存在的污垢。
5. 调整加工深度
根据需要调整铣刀加工深度,控制铣削的宽度和深度。
6. 启动铣床
启动铣床并开始铣削操作,保持切削刃的清洁,确保铣削加工的平稳和精度。
7. 对加工面进行检测
检测铣削加工的加工面是否符合工艺标准和质量要求。
8. 收尾工作
铣削加工完成后,关闭铣床并清理现场,包括清洗铣刀和工作台,存放设备和工具等。
以上是铣削操作的一般方法和顺序,不同工件的铣削加工可能会有所不同。
铣削加工安全操作要点

铣削加工安全操作要点铣削加工是一种常见的金属加工方法,由于其高速旋转的刀具和金属工件的接触,存在一定的安全风险。
为了确保操作人员的安全,以下是铣削加工的安全操作要点,供您参考。
1. 穿戴个人防护装备:操作人员在进行铣削加工时,应穿戴符合标准的个人防护装备,包括安全帽、防护眼镜、防护口罩、耳塞等。
这些装备可以有效地保护头部、眼睛、呼吸系统和听力。
2. 检查设备状态:在进行铣削加工前,要先仔细检查设备的运行状态,确保各零部件正常、无松动或损坏情况。
特别是要检查刀具是否固定牢固,并且清洁干净。
3. 设定合适的加工参数:根据工件的材质和尺寸,选择合适的切削速度、进给速度和切削深度。
设置过高的参数会导致刀具过度磨损和工件损坏,设置过低的参数则可能导致工作效率低下或刃口堵塞而引发安全隐患。
4. 使用合适的夹具和刀具:在进行铣削加工时,要使用合适的夹具将工件固定在加工台上,确保工件在加工过程中保持稳定。
使用刀柄、刀具夹持器等工具时,要根据刀具规格选择合适的夹持方式,并保持夹具清洁,确保刀具牢固。
5. 确定安全工作区域:在进行铣削加工时,要确保操作区域没有其他人员靠近,以免发生意外伤害。
设置明显的警示标志和隔离带,避免他人进入工作区域,并确保工作区域通风良好,防止铣削加工过程中产生的切屑和粉尘积聚导致危险。
6. 遵守操作规程和安全操作流程:操作人员要熟悉和遵守企业或工厂的操作规程和安全操作流程,按照规定的程序进行操作,不得随意更改或省略操作的步骤。
严禁在运行中接触刀具或工件,更不允许用手直接清理切削区域。
7. 定期检查和维护设备:定期检查和维护设备可以及时发现和排除潜在的机械故障和安全隐患。
特别是要定期检查刀具的磨损情况,并及时更换或修复损坏的刀具。
8. 停止操作后的安全措施:在铣削加工完成后,应及时关闭设备电源,清理工作区域内的切削屑和废料,并归位存放刀具和工件。
操作人员离开时,应将设备的防护装置复位和锁定。
轴类零件加工工艺过程
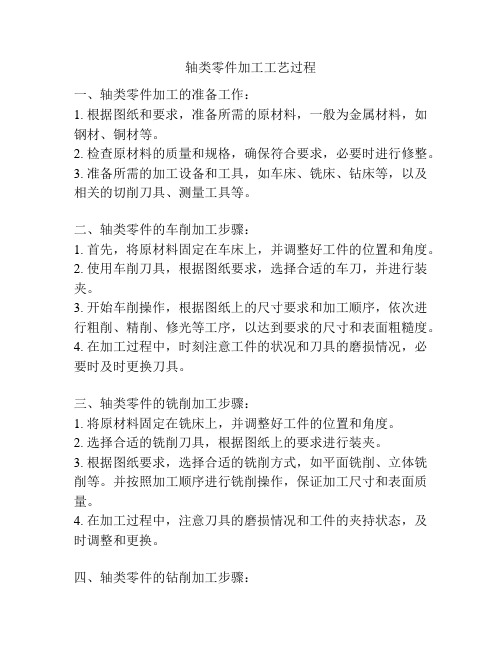
轴类零件加工工艺过程一、轴类零件加工的准备工作:1. 根据图纸和要求,准备所需的原材料,一般为金属材料,如钢材、铜材等。
2. 检查原材料的质量和规格,确保符合要求,必要时进行修整。
3. 准备所需的加工设备和工具,如车床、铣床、钻床等,以及相关的切削刀具、测量工具等。
二、轴类零件的车削加工步骤:1. 首先,将原材料固定在车床上,并调整好工件的位置和角度。
2. 使用车削刀具,根据图纸要求,选择合适的车刀,并进行装夹。
3. 开始车削操作,根据图纸上的尺寸要求和加工顺序,依次进行粗削、精削、修光等工序,以达到要求的尺寸和表面粗糙度。
4. 在加工过程中,时刻注意工件的状况和刀具的磨损情况,必要时及时更换刀具。
三、轴类零件的铣削加工步骤:1. 将原材料固定在铣床上,并调整好工件的位置和角度。
2. 选择合适的铣削刀具,根据图纸上的要求进行装夹。
3. 根据图纸要求,选择合适的铣削方式,如平面铣削、立体铣削等。
并按照加工顺序进行铣削操作,保证加工尺寸和表面质量。
4. 在加工过程中,注意刀具的磨损情况和工件的夹持状态,及时调整和更换。
四、轴类零件的钻削加工步骤:1. 将原材料固定在钻床上,并调整好工件的位置和角度。
2. 选择合适的钻孔刀具,根据图纸要求进行装夹。
3. 根据图纸上的孔径要求,选择合适的钻头,并进行设定,调整钻头的速度和进给量。
4. 开始钻削操作,根据图纸上的孔径位置进行钻孔,保证加工尺寸和孔壁的质量。
5. 在加工过程中,注意刀具的磨损情况和冷却液的使用,及时调整和更换。
五、轴类零件加工的后续工序:1. 进行工件的检验,包括尺寸测量、表面质量等,确保符合要求。
2. 进行必要的热处理、表面处理等工艺,以提高工件的性能和耐用度。
3. 进行最后的整理和打磨工作,使工件达到最终的要求。
4. 进行产品的包装和出库。
以上就是轴类零件加工的基本工艺过程,通过严格按照要求进行加工操作,可以确保加工出高质量的轴类零件。
加工过程中需要密切关注工件的状况和刀具的磨损情况,及时调整和更换,以保证加工质量和工艺效率。
铣削加工加工方法
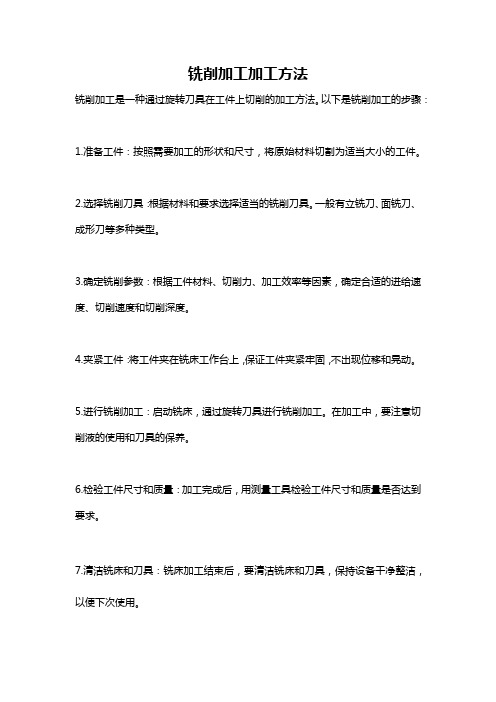
铣削加工加工方法
铣削加工是一种通过旋转刀具在工件上切削的加工方法。
以下是铣削加工的步骤:
1.准备工件:按照需要加工的形状和尺寸,将原始材料切割为适当大小的工件。
2.选择铣削刀具:根据材料和要求选择适当的铣削刀具。
一般有立铣刀、面铣刀、成形刀等多种类型。
3.确定铣削参数:根据工件材料、切削力、加工效率等因素,确定合适的进给速度、切削速度和切削深度。
4.夹紧工件:将工件夹在铣床工作台上,保证工件夹紧牢固,不出现位移和晃动。
5.进行铣削加工:启动铣床,通过旋转刀具进行铣削加工。
在加工中,要注意切削液的使用和刀具的保养。
6.检验工件尺寸和质量:加工完成后,用测量工具检验工件尺寸和质量是否达到要求。
7.清洁铣床和刀具:铣床加工结束后,要清洁铣床和刀具,保持设备干净整洁,以便下次使用。
电池极柱铣削工艺流程

电池极柱铣削工艺流程电池极柱铣削工艺是电池制造过程中的重要环节之一,它主要用于对电池极柱进行加工和修整,以满足电池的性能和质量要求。
本文将介绍电池极柱铣削工艺的流程及其关键步骤。
一、准备工作在进行电池极柱铣削之前,需要进行一系列的准备工作。
首先,确定铣削工艺参数,包括铣削刀具的选择、铣削速度、进给速度等。
其次,准备好所需的设备和工装夹具,确保其正常运行和安全使用。
最后,对电池极柱进行检查,确保其尺寸和形状符合要求。
二、粗铣削粗铣削是电池极柱铣削的第一步,其目的是将电池极柱的表面切削至一定的粗糙度,为后续的加工步骤提供良好的加工基准。
在粗铣削过程中,需要注意切削刀具与电池极柱表面的接触状态,确保刀具与工件之间的切削力得到合理分配。
三、精铣削精铣削是电池极柱铣削的关键步骤,其目的是将电池极柱的表面进行进一步的修整和光洁处理,提高其表面质量和精度。
在精铣削过程中,需要采用合适的切削刀具和加工参数,确保电池极柱的尺寸和形状符合要求,并且表面光洁度达到要求。
四、尺寸检测在电池极柱铣削完成后,需要对加工后的电池极柱进行尺寸检测。
尺寸检测可以利用专用的测量仪器和设备进行,以确保电池极柱的尺寸和形状与设计要求相符。
同时,还需对电池极柱的表面质量和光洁度进行检查,以确保其满足质量要求。
五、表面处理电池极柱铣削完成后,还需要进行表面处理,以提高其耐腐蚀性和电导率。
常见的表面处理方法包括喷涂、电镀、热处理等,根据不同的要求选择合适的表面处理方式,确保电池极柱的性能和质量得到进一步提升。
六、质量控制在整个电池极柱铣削工艺流程中,质量控制是非常重要的环节。
通过对每个工艺步骤进行严格的质量控制,可以确保电池极柱的加工质量和性能稳定可靠。
质量控制可以包括工艺参数的监控、加工过程的实时检测以及最终产品的检验等环节。
总结起来,电池极柱铣削工艺流程包括准备工作、粗铣削、精铣削、尺寸检测、表面处理和质量控制等关键步骤。
通过科学合理地执行这些步骤,可以保证电池极柱的加工质量和性能达到设计要求,从而提高电池的整体性能和可靠性。
- 1、下载文档前请自行甄别文档内容的完整性,平台不提供额外的编辑、内容补充、找答案等附加服务。
- 2、"仅部分预览"的文档,不可在线预览部分如存在完整性等问题,可反馈申请退款(可完整预览的文档不适用该条件!)。
- 3、如文档侵犯您的权益,请联系客服反馈,我们会尽快为您处理(人工客服工作时间:9:00-18:30)。
如何进行铣削加工的准备1、加工工艺1.1常用刀具用于加工平面的刀具很多,这里只介绍几种在数控机床上常用的铣刀。
(1) 立铣刀:立铣刀是数控机床上用得最多的一种铣刀,其结构如图1-1-2所示。
立铣刀的圆柱表面和端面上都有切削刃,它们可同时进行切削,也可单独进行切削。
立铣刀圆柱表面的切削刃为主切削刃,端面上的切削刃为副切削刃。
主切削刃一般为螺旋齿,这样可以增加切削平稳性,提高加工精度。
由于普通立铣刀端面中心处无切削刃,所以立铣刀不能做轴向进给,端面刃主要用来加工与侧面相垂直的底平面。
直径较小的立铣刀,一般制成带柄形式。
Φ2~Φ71mm的立铣刀制成直柄;Φ6~Φ63mm的立铣刀制成莫氏锥柄;Φ25~Φ80mm的立铣刀做成7:24锥柄,内有螺孔用来拉紧刀具。
但是由于数控机床要求铣刀能快速自动装卸,所以立铣刀柄部形式也有很大不同,一般是图1-1-2由专业厂家按照一定的规范设计制造成统一形式、统一尺寸的刀柄。
直径大于Φ40~Φ160mm的立铣刀可做成套式结构。
(2) 面铣刀:如图1-1-3所示,面铣刀的圆周表面和端面上都有切削刃,端部切削刃为副切削刃。
面铣刀多制成套式镶齿结构,刀齿为高速钢或硬质合金,刀体为40Cr。
高速钢面铣刀按国家标准规定,直径为80 ~250mm,螺旋角β为10°,刀齿数为10 ~26。
硬质合金面铣刀与高速钢铣刀相比,铣削速度较高、加工效率高,加工表面质量也比较好,并可加工带有硬皮和淬硬层的工件,所以得到了广泛应用。
硬质合金面铣刀按刀片和刀齿的安装方式不同,可分为整体焊接式、机夹—焊接式和可转位式3种。
图1-1-3数控加工中广泛使用可转位式面铣刀。
目前先进的可转位式数控面铣刀的刀体趋向于用轻质高强度铝、镁合金制造,切削刃采用大前角、负刃倾角,可转位刀片带有三维断屑槽形,便于排屑。
1.2平面铣削加工走刀路线的确定数控铣削加工中进给路线的确定对零件的加工精度和表面质量有直接的影响,因此,缺确定好进给路线是保证铣削加工精度和表面这里的工艺措施之一。
进给路线的确定与工件表面状况、要求的零件表面质量、机床进给机构的间隙、刀具耐用度以及零件轮廓形状等有关。
在平面加工中,能使用的进给路线也是多种多样的,比较常用的有两种。
如图1-1-4(a)和图1-1-4(b)所示分别为平行加工和环绕加工。
图1-4(a) 1-4(b)1.3铣削参数选择铣削参数一般包括切削速度V、进给量F、铣削宽度a e、铣削深度a p四个要素。
参数的选用由工艺条件决定。
铣削时采用的切削用量,应在保证工件加工精度和刀具耐用度、不超过铣床允许的动力和扭矩前提下,获得最高的生产率和最低的成本。
铣削过程中,如果能在一定的时间内切除较多的金属,就有较高的生产率,从刀具耐用度的角度考虑,切削用量选择的次序是:根据侧吃刀量a e先选大的背吃刀量a p(见图1-5),再选大的进给速度F,最后再选大的铣削速度V(最后转换为主轴转速S)。
对于高速铣床(主轴转速在10000r/min以上),为发挥其高速旋转的特性、减少主轴的重载磨损,其切削用量选择的次序应是:V→F→a p(a e)。
(1)铣削深度a p,铣削宽度a e的选择铣削宽度a e<d/2(d为铣刀直径)时,取a p=(1/3~1/2)d;铣削宽度d/2≤a e<d时,取a p=(1/4~1/3)d;铣削宽度a e=d(即全径切削)时,取a p=(1/5~1/4)d。
当机床的刚性较好,且刀具的直径较大时,a p可取得更大。
图1-5立铣刀的铣削深度与铣削宽度(2)进给量F的选择粗铣时铣削力大,进给量的提高主要受刀具强度、机床、夹具等工艺系统刚性的限制,根据刀具形状、材料以及被加工工件材质的不同,在强度刚度许可的条件下,进给量应尽量取大;精铣时限制进给量的主要因素是加工表面的粗糙度,为了减小工艺系统的弹性变形,减小已加工表面的粗糙度,一般采用较小的进给量,具体参见表1-1。
进给速度F与铣刀每齿进给量f z、铣刀齿数Z及主轴转速S(r/min)的关系为:F=fz(mm/r)或F=S*fz(mm/min)Φ10 S400 0.03 0.05*15=0.09*400=60F=20~60 mm/min表1-1 铣刀每齿进给量f Z推荐值(mm/Z)(3)铣削速度V的选择在背吃刀量和进给量选好后,应在保证合理的刀具耐用度、机床功率等因素的前提下确定,具体参见表1-2。
主轴转速S(r/min)与铣削速度V(m/min)及铣刀直径d(mm)的关系为:S=1000V/(πd)Φ10 V=15 m/min S=1000*15/(3.14*10) =400~500 r/minΦ12 V=15 m/min S=1000*15/(3.14*12) =350~400 r/min铣削参数的选择是一项经验性极强的技术,一般情况下,下述列举的数据只能作为参考。
通常,粗铣时选用较小的数值、精铣是采用较大的数值,具体作业时应该优先考虑采用带班老师建议的数据,再根据实际切削情况进行调整。
这样可保证加工的安全、顺利进行,保证较高的加工效率、较高的加工质量、较高的刀具寿命。
表1-2 铣刀的铣削速度V(m/min)2、指令程序2.1辅助功能指令辅助功能指令又称M指令,其主要是用来控制机床各种辅助动作及开关状态的,用地址字符M及两位数字表示的。
如主轴的转动与停止、冷却液的开与关闭等等,通常是靠继电器的通断来实现控制过程。
程序的每一个程序段中M代码只能出现一次。
常用辅助功能M指令及其说明见表1-1-1所列:表1- 1-1 M功能代码:(1)程序控制M代码。
M00――程序停止指令,运行后自动运行暂停,当程序运行停止时,全部现存的模态信息保持不变。
重新按下循环启动按键,CNC就继续运行后续程序。
此功能便于操作者进行工件的手动测量等操作为模态指令。
M01 ――程序选择性停止,为模态指令。
在运行时如已选定机床的选择性停止功能为开启状态,该指令等同于M00,否则该指令无效。
通常用于关键尺寸的检验或临时暂停。
M30、M02――都是程序结束指令,使主轴、进给停止,冷却液关闭。
在初期的数控系统中,M30会附加一个程序复位(使光标回到程序首)动作,M02则没有,现在的数控系统一般没有这个区别。
(2)其他M代码M03――主轴正转,使主轴以当前指定的主轴转速顺时针(CCW)旋转(逆着Z轴正向观察)。
M04――主轴反转,使主轴以当前指定的主轴转速逆时针(CW)旋转(逆着Z轴正向观察)。
M05――主轴停止。
M08――冷却液开。
M09――冷却液关。
2.2主轴转速功能指令主轴转速功能指令也称S指令,其作用是指定机床主轴的转速,用字母S及后面若干位数字表示,单位为r/min。
主轴转速指令:指令格式:S___ 。
指令主轴转速的大小,单位为r/min用字母S及其后面的若干位数字表示,一般是不能带小数点的。
例如S1000表示1000r./min。
该指令与M04(反转)、M03(正转)结合使用,M05为主轴停止转动。
这四个都为模态指令,其中S及其指令的数值在重新指令后才改变。
2.3进给速度功能指令进给速度功能指令又称F指令,其作用是指定刀具的进给速度,用字母F加后面若干位数字表示。
单位为mm/min(G94有效)或mm/r(G95有效)。
进给量指令:指令格式:F___ 。
指令进给速度的大小。
用字母F及其后面的若干位数字表示,单位为mm/min或mm/r。
为模态指令,F及其指令的数值在重新指令后才改变。
1)进给状态指令G94:设置每分钟进给速度状态,G94可以与其他G功能指令同时存在一个程序段中,其指定F字段设置的切削进给速度的单位是mm/min,即每分钟进给速度。
2)进给状态指令G95:设置每转进给速度状态,G95可以与其他G功能指令同时存在一个程序段中,其指定F字段设置的切削进给速度的单位是mm/r,即每进给速度。
2.4准备功能指令准备功能指令也称G指令,是建立机床工作方式的一种指令。
用字母G加数字构成。
进行零件平面加工所需的G指令见表1-1-2。
表1-1-2 FANUC 0i Mate-MC/ SINUMERIK802D/802S数控铣床/加工中心准备功能指令(部分)带“*”号的G指令表示接通电源时,即为G指令的状态。
G00、G01;G17、G18、G19;G90、G91由参数设定选择。
(1) 编程平面指令(G17、G18、G19)应用数控铣床/加工中心进行零件加工前,只有先指定一个坐标平面,即确定一个两坐标的坐标平面,才能使机床在加工过程中正常执行刀具半径补偿及刀具长度补偿功能,坐标平面选择指令的主要功能就是指定加工时所需的坐标平面。
坐标平面规定如图1-1-5示,分述如下:G17——之后的程序都是以XY平面为切削平面,本指令为模态指令, G17为机床开机后系统默认状态,在编程时G17可省略。
G18——之后的程序都是以XZ平面为切削平面,本指令为模态指令。
G19——之后的程序都是以YZ平面为切削平面,本指令为模态指令。
图1-1-5 编程平面与坐标轴(2) 工件坐标系的设置指令(G54~G59/G92)G54~G59指令所设置加工坐标系为模态指令,其中任意一个坐标系指令作用和效果都是相同的,设定时可任选中一个,但设定后编程时使用的坐标系指令必须跟设定的一致。
例如操作着在对刀设定的工件坐标系为G54,那么编写的加工程序中坐标系指令也应相应地使用G54指令来设置工件坐标系。
一般情况下,机床开机并回零后,G54为系统默认工件坐标系。