内孔磨削加工与滚压加工的比较
磨削加工中的磨削方式

磨削加工中的磨削方式磨削加工是一种精密的金属加工方法,不仅可以用于加工金属材料,还可以用于加工陶瓷、玻璃等非金属材料。
它的基本原理是在切削工具与工件之间施加外力,并且在介质中进行磨磨擦削,以达到加工的目的。
磨削加工中的磨削方式有很多种,下面将对其进行一一介绍。
1. 平面磨削平面磨削是一种磨削工艺,主要用于加工平面及其上的孔和槽。
这种加工方式通过旋转磨削轮,使其与工件表面接触,施加相应的压力和剪切力来进行磨削。
平面磨削的加工精度高,工件表面质量好,适用于加工超精密配件。
2. 内圆磨削内圆磨削是一种在工作件内部进行磨削的加工方式,主要用于加工内径大小不同的圆柱体。
这种加工方式的主要设备是内圆磨床,通过不断旋转工作件和磨削轮,结合适当的压力、速度等参数,来进行磨削加工。
3. 外圆磨削外圆磨削是一种在工作件外部进行磨削的加工方式,主要用于加工外径大小不同的圆柱体。
这种加工方式的主要设备是外圆磨床,通过不断旋转工作件和磨削轮,结合适当的压力、速度等参数,来进行磨削加工。
4. 中心磨削中心磨削是一种在两个中心点之间进行磨削加工的方式,主要用于加工圆锥体、圆柱锥体等形状的工件。
这种加工方式的主要设备是中心磨床,在加工过程中,需要较高的精度控制及对磨削力的稳定性要求。
5. 轮廓磨削轮廓磨削是一种根据工件轮廓进行磨削的加工方式,主要用于加工各种不规则形状的工件。
这种加工方式的主要设备是数控磨床,通过对工件进行高精度的三维扫描和轮廓学习,来得到工件的三维形状。
随后,根据得到的轮廓数据进行加工。
6. 微型磨削微型磨削是一种在微米尺度下进行磨削的加工方式,主要用于加工高精度、超细的微件。
这种加工方式的设备应具有高精度、高速度、低摩擦等特点,常用于制造高端光学元件、半导体芯片等高端应用领域。
总之,磨削加工中的磨削方式有很多种,不同的加工方式适用于不同的工件加工需求,需要精确控制加工参数,以保证加工效果。
随着技术的不断进步,相信未来还会涌现更多更精密的磨削加工方式,为各行各业的高精度加工需求提供更多的选择。
齿轮加工加工方法
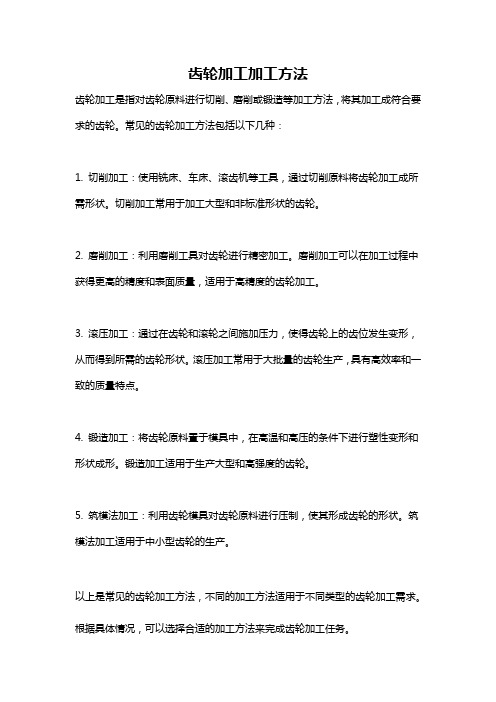
齿轮加工加工方法
齿轮加工是指对齿轮原料进行切削、磨削或锻造等加工方法,将其加工成符合要求的齿轮。
常见的齿轮加工方法包括以下几种:
1. 切削加工:使用铣床、车床、滚齿机等工具,通过切削原料将齿轮加工成所需形状。
切削加工常用于加工大型和非标准形状的齿轮。
2. 磨削加工:利用磨削工具对齿轮进行精密加工。
磨削加工可以在加工过程中获得更高的精度和表面质量,适用于高精度的齿轮加工。
3. 滚压加工:通过在齿轮和滚轮之间施加压力,使得齿轮上的齿位发生变形,从而得到所需的齿轮形状。
滚压加工常用于大批量的齿轮生产,具有高效率和一致的质量特点。
4. 锻造加工:将齿轮原料置于模具中,在高温和高压的条件下进行塑性变形和形状成形。
锻造加工适用于生产大型和高强度的齿轮。
5. 筑模法加工:利用齿轮模具对齿轮原料进行压制,使其形成齿轮的形状。
筑模法加工适用于中小型齿轮的生产。
以上是常见的齿轮加工方法,不同的加工方法适用于不同类型的齿轮加工需求。
根据具体情况,可以选择合适的加工方法来完成齿轮加工任务。
深孔的滚压加工——滚压头滚压刀基础知识
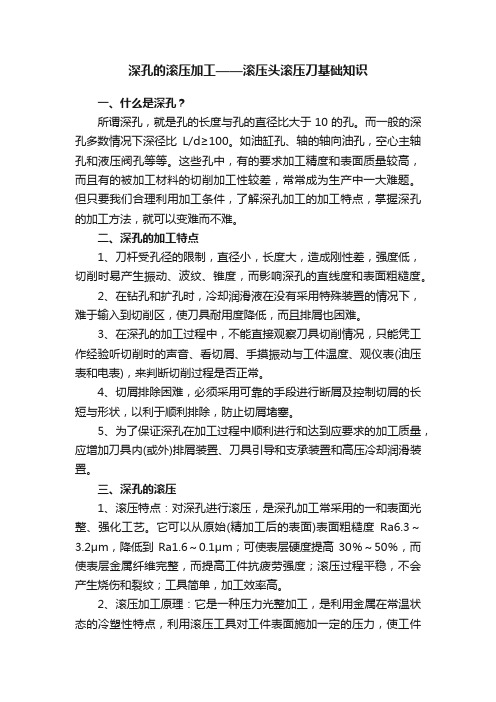
深孔的滚压加工——滚压头滚压刀基础知识一、什么是深孔?所谓深孔,就是孔的长度与孔的直径比大于10的孔。
而一般的深孔多数情况下深径比L/d≥100。
如油缸孔、轴的轴向油孔,空心主轴孔和液压阀孔等等。
这些孔中,有的要求加工精度和表面质量较高,而且有的被加工材料的切削加工性较差,常常成为生产中一大难题。
但只要我们合理利用加工条件,了解深孔加工的加工特点,掌握深孔的加工方法,就可以变难而不难。
二、深孔的加工特点1、刀杆受孔径的限制,直径小,长度大,造成刚性差,强度低,切削时易产生振动、波纹、锥度,而影响深孔的直线度和表面粗糙度。
2、在钻孔和扩孔时,冷却润滑液在没有采用特殊装置的情况下,难于输入到切削区,使刀具耐用度降低,而且排屑也困难。
3、在深孔的加工过程中,不能直接观察刀具切削情况,只能凭工作经验听切削时的声音、看切屑、手摸振动与工件温度、观仪表(油压表和电表),来判断切削过程是否正常。
4、切屑排除困难,必须采用可靠的手段进行断屑及控制切屑的长短与形状,以利于顺利排除,防止切屑堵塞。
5、为了保证深孔在加工过程中顺利进行和达到应要求的加工质量,应增加刀具内(或外)排屑装置、刀具引导和支承装置和高压冷却润滑装置。
三、深孔的滚压1、滚压特点:对深孔进行滚压,是深孔加工常采用的一和表面光整、强化工艺。
它可以从原始(精加工后的表面)表面粗糙度Ra6.3~3.2μm,降低到Ra1.6~0.1μm;可使表层硬度提高30%~50%,而使表层金属纤维完整,而提高工件抗疲劳强度;滚压过程平稳,不会产生烧伤和裂纹;工具简单,加工效率高。
2、滚压加工原理:它是一种压力光整加工,是利用金属在常温状态的冷塑性特点,利用滚压工具对工件表面施加一定的压力,使工件表层金属产生塑性流动,填入到原始残留的低凹波谷中,而达到工件表面粗糙值降低。
由于被滚压的表层金属塑性变形,使表层组织冷硬化和晶粒变细,形成致密的纤维状,使表层金属塑性降低,硬度和强度提高,从而改善了工件表面的耐磨性、耐蚀性和配合性。
内孔的加工讲解
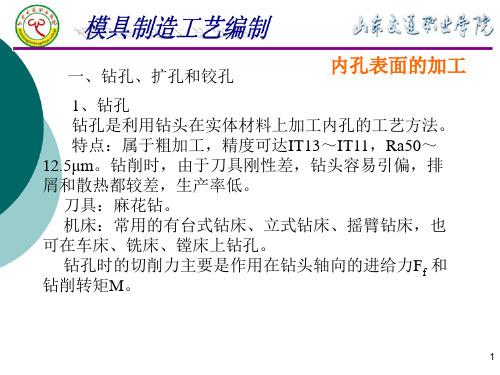
15
11
四、磨孔与孔的精密加工 1 磨孔工艺特点:属于孔的精加方法。精度可达IT7, Ra1.6~0.4 μm。 磨孔不仅能获得较高的尺寸精度和表面质量,而且 还可以提高孔的位置精度和孔的轴线的直线度。与外圆 磨削相比,工作条件较差:砂轮直径小,刚性差,排屑 和散热困难,生产率低。对于淬硬零件中的孔加工,磨 孔是主要的加工方法。 内孔为断续圆周表面(如有键槽或花键的孔)、阶 梯孔及盲孔时,常采用磨孔作为精加工。
研磨孔是一种光整加工方法。精度可达IT7~IT6, Ra0.4~0.025μm,形状精度也有相应的提高,但不能提 高位置精度。
16
珩磨头对孔施加一定压力,结构如图;切除极小的 加工余量。
17
②研磨孔是一种光整加工方法。精度可达IT7~IT6, Ra0.4~0.025μm,形状精度也有相应的提高,但不能提 高位置精度。需要在精镗、精铰或精磨之后进行。
18
固定式研磨棒多用于单件生产。带槽研磨棒便于存 贮研磨剂,用于粗研,光滑研磨棒,一般用于精研。如 图所示 。所有研具采用比工件软的材料制成,这些材料 为铸铁、铜、青铜、巴氏合金及硬木等。有时也可用钢 做研具。研磨时,部分磨粒悬浮于工件与研具之间,部 分磨粒则嵌入研具的表面层,工件与研具作相对运动, 磨料就在工件表面上切除很薄的一层金属 ( 主要是上工 序在工件表面上留下的凸峰 ) 。
12
磨孔时砂轮的尺寸受被加工孔径尺寸的限制,一般 砂轮直径为工件孔径的 0.5—0.9 倍,磨头轴的直径和 长度也取决于被加工孔的直径和深度。故磨削速度低, 磨头的刚度差,磨削质量和生产率均受到影响。
内孔磨削加工与滚压加工的比较

<title>内孔磨削加工与滚压加工的比较</title>
实际生产中,对于表面粗糙度Ra0.04μm~Ra1.6μm的内孔加工,常用加工工艺是磨削、滚压、拉削、珩磨等。拉削加工刀具费用大,生产效率高,适应大批量生产;珩磨用于光整加工表面粗糙度Ra0.04μm以上。所以一般最常用的是磨削和滚压加工。下面通过分析一零件的加工工艺,对磨削加工、滚压加工进行比较。
<P> 生产效率提高几倍; </P>
<P> 工艺简单; </P>
<P> 零件使用性能有提高; </P>
<P> 减少转运次数有利防止磕碰。 </P><!--content-->
<P> 2 工艺比较</P>
<P> 内孔磨削加工工艺和滚压加工工艺都可以提高零件尺寸精度、降低表面粗糙度。但有以下区别:</P>
<P> 内孔磨削加工对上道工序要求不高,能达到比滚压加工更高的精度。实际生产中内孔磨削加工过程降低磨削区温度较困难,加工表面层产生的残余拉应力、磨削裂纹、烧伤等,影响零件使用性能,生产效率低。</P>
<P> 滚压加工对上道工序要求高,不能提高零件形状精度。因加工过程无发热现象,尺寸容易控制;零件加工表面层产生的残余压应力和冷硬化有利于提高零件使用性能;生产效率高。</P>
<P> 4 结语</P>
<P> 通过上面分析、比较可知:在内孔粗糙度Ra0.08μm~Ra1.6μm范围、定型产品、批量生产时,采用滚压加工工艺与磨削加工相比有如下优点:</P>
轴类零部件内孔加工方法

轴类零部件内孔加工是机械加工中常见的一项工艺,确保内孔的精度和表面质量对零部件的功能和性能至关重要。
以下是一些常见的轴类零部件内孔加工方法:
1. 钻削:
- 钻削是最基本的内孔加工方法之一。
通过使用钻头,可在工件上创建孔。
对于较小直径和较短深度的内孔,钻削是一种经济有效的方法。
2. 铰削:
- 铰削是通过使用铰刀,将内孔表面进行切削,以提高其精度和表面质量。
铰刀可以调整,使内孔具有所需的直径和形状。
3. 车削:
- 车削是通过使用车刀在工件上旋转的情况下,切削内孔的一种方法。
车削通常用于制作较大直径和较深的内孔,可以实现较高的加工效率。
4. 镗削:
- 镗削是通过使用镗刀,以旋转或振动的方式切削内孔。
这种方法可以实现较高的精度和表面质量,特别适用于对内孔直径和圆度有严格要求的情况。
5. 滚压:
- 滚压是通过使用滚轮或滚动刀具,将内孔材料进行塑性变形,从而形成所需的内孔形状。
这种方法可以提高内孔的表面质量和硬度。
6. 磨削:
- 磨削是通过使用磨石或磨削刀具,对内孔进行精细磨削,以获得高精度和高表面质量。
磨削通常用于对内孔直径和形状有极高要求的情况。
7. 激光加工:
- 激光加工是通过激光束将内孔材料切割或蒸发,以实现对内孔进行精确加工的方法。
这种方法适用于一些特殊材料或需要非常高精度的内孔加工。
在选择合适的轴类零部件内孔加工方法时,需要考虑材料特性、加工精度、生产效率和成本等因素。
通常,工程师会根据具体的要求和工件特点选择最合适的加工方法。
打孔加工中的滚孔技术
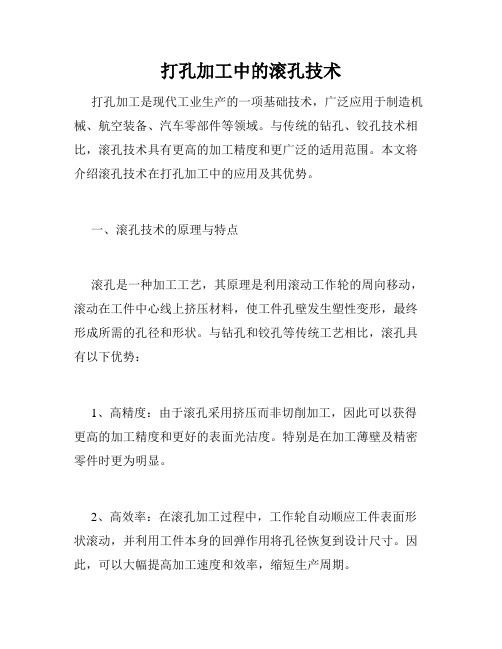
打孔加工中的滚孔技术打孔加工是现代工业生产的一项基础技术,广泛应用于制造机械、航空装备、汽车零部件等领域。
与传统的钻孔、铰孔技术相比,滚孔技术具有更高的加工精度和更广泛的适用范围。
本文将介绍滚孔技术在打孔加工中的应用及其优势。
一、滚孔技术的原理与特点滚孔是一种加工工艺,其原理是利用滚动工作轮的周向移动,滚动在工件中心线上挤压材料,使工件孔壁发生塑性变形,最终形成所需的孔径和形状。
与钻孔和铰孔等传统工艺相比,滚孔具有以下优势:1、高精度:由于滚孔采用挤压而非切削加工,因此可以获得更高的加工精度和更好的表面光洁度。
特别是在加工薄壁及精密零件时更为明显。
2、高效率:在滚孔加工过程中,工作轮自动顺应工件表面形状滚动,并利用工件本身的回弹作用将孔径恢复到设计尺寸。
因此,可以大幅提高加工速度和效率,缩短生产周期。
3、节约成本:从长远角度看,采用滚孔技术可以降低设备和材料消耗,同时减少废品率和后续加工成本。
二、滚孔技术在打孔加工中的应用在机械加工领域中,滚孔技术被广泛应用于打孔加工。
具体包括以下几个方面:1、汽缸孔加工:汽缸是内燃机的重要部件,汽缸孔和活塞配合的精度直接影响到内燃机的性能和寿命。
通过采用滚孔技术,可以获得高精度、高表面质量的汽缸孔,提高内燃机的工作效率和可靠性。
2、发动机气门孔加工:气门是发动机燃烧室的控制门,气门孔的精度和表面质量对发动机的动力性和经济性影响巨大。
采用滚孔技术可以确保气门孔精度,提高发动机的动力性和经济性。
3、齿轮箱孔加工:齿轮箱是重要的传动装置,其孔的精度和表面质量直接影响到整个转动系统的性能。
采用滚孔技术可以确保齿轮箱孔的形状精度和表面质量,提高传动效率和稳定性。
4、轴承座孔加工:轴承座是连接轴承和机体的部件,轴承座孔的精度和表面质量对轴承的寿命和性能影响巨大。
采用滚孔技术可以确保轴承座孔的形状精度和表面质量,提高轴承寿命和运行性能。
三、滚孔技术的改进和发展滚孔技术已经应用多年,并取得显著的效果。
螺纹判定方法

螺纹判定方法螺纹是一种常见的机械零件,广泛应用于各种机械设备中。
螺纹的种类繁多,如公制螺纹、英制螺纹、管螺纹等。
螺纹的加工和检测对于保证机械设备的正常运行具有重要意义。
本文将对螺纹的判定方法进行详细介绍。
一、螺纹的基本概念螺纹是指在圆柱表面上,沿着螺旋线形成的具有规定牙型和螺距的连续凸起。
螺纹的主要参数有:牙型、螺距、直径、导程、角度等。
螺纹的种类主要有:公制螺纹、英制螺纹、管螺纹等。
二、螺纹的判定方法1. 目测法目测法是最简单的一种螺纹判定方法,主要是通过肉眼观察螺纹的形状、尺寸和表面质量等特征来判断其是否符合要求。
目测法适用于对螺纹形状较为简单的场合,如螺栓、螺母等。
2. 比较法比较法是将待判定的螺纹与已知合格的螺纹进行对比,通过对比两者的形状、尺寸和表面质量等特征来判断其是否符合要求。
比较法适用于对螺纹形状较为复杂的场合,如螺杆、丝杠等。
3. 量具测量法量具测量法是通过使用专门的螺纹测量工具(如螺纹规、螺纹千分尺等)来测量螺纹的各项参数,然后与标准值进行比较,从而判断螺纹是否符合要求。
量具测量法具有较高的准确性和可靠性,适用于对螺纹精度要求较高的场合。
4. 光学投影法光学投影法是通过光学投影仪将螺纹放大投影到屏幕上,然后通过观察投影图像来判断螺纹的形状、尺寸和表面质量等特征是否符合要求。
光学投影法适用于对螺纹形状较为复杂的场合,如螺杆、丝杠等。
5. 影像分析法影像分析法是通过使用光学显微镜或扫描电子显微镜等高分辨率成像设备对螺纹进行拍摄,然后通过计算机图像处理技术对拍摄图像进行分析,从而判断螺纹的形状、尺寸和表面质量等特征是否符合要求。
影像分析法具有较高的准确性和可靠性,适用于对螺纹精度要求极高的场合。
三、螺纹的加工方法1. 切削加工法切削加工法是通过车削、铣削、钻削等切削加工方式来加工螺纹。
切削加工法适用于对螺纹精度要求较低的场合。
2. 滚压加工法滚压加工法是通过滚压工具对工件表面进行滚压,使其产生塑性变形,从而形成螺纹。
内孔表面加工方法和加工方案(上中下)

内孔表面加工方法和加工方案(上中下)内孔表面加工方法较多,常用的有钻孔、扩孔、铰孔、镗孔、磨孔、拉孔、研磨孔、珩磨孔、滚压孔等。
一、钻孔用钻头在工件实体部位加工孔称为钻孔。
钻孔属粗加工,可达到的尺寸公差等级为IT13~IT11,表面粗糙度值为Ra50~12.5μm。
由于麻花钻长度较长,钻芯直径小而刚性差,又有横刃的影响,故钻孔有以下工艺特点:1.钻头容易偏斜。
由于横刃的影响定心不准,切入时钻头容易引偏;且钻头的刚性和导向作用较差,切削时钻头容易弯曲。
在钻床上钻孔时,如图7-2a所示,容易引起孔的轴线偏移和不直,但孔径无显著变化;在车床上钻孔时,如图7-2b 所示,容易引起孔径的变化,但孔的轴线仍然是直的。
因此,在钻孔前应先加工端面,并用钻头或中心钻预钻一个锥坑,如图7-3所示,以便钻头定心。
钻小孔和深孔时,为了避免孔的轴线偏移和不直,应尽可能采用工件回转方式进行钻孔。
2.孔径容易扩大。
钻削时钻头两切削刃径向力不等将引起孔径扩大;卧式车床钻孔时的切入引偏也是孔径扩大的重要原因;此外钻头的径向跳动等也是造成孔径扩大的原因。
3.孔的表面质量较差。
钻削切屑较宽,在孔内被迫卷为螺旋状,流出时与孔壁发生摩擦而刮伤已加工表面。
4.钻削时轴向力大。
这主要是由钻头的横刃引起的。
试验表明,钻孔时50%的轴向力和15%的扭矩是由横刃产生的。
因此,当钻孔直径d﹥30mm时,一般分两次进行钻削。
第一次钻出(0.5~0.7)d,第二次钻到所需的孔径。
由于横刃第二次不参加切削,故可采用较大的进给量,使孔的表面质量和生产率均得到提高。
二、扩孔扩孔是用扩孔钻对已钻出的孔做进一步加工,以扩大孔径并提高精度和降低表面粗糙度值。
扩孔可达到的尺寸公差等级为IT11~IT10, 表面粗糙度值为Ra12.5~6.3μm,属于孔的半精加工方法,常作铰削前的预加工,也可作为精度不高的孔的终加工。
扩孔方法如图7-4所示,扩孔余量(D-d),可由表查阅,。
车丝杆加工方法

车丝杆加工方法车丝杆,又称丝杠,是一种旋转变线性运动的机械传动元件,广泛应用于机床、数控机床、自动化设备等领域。
下面介绍车丝杆的加工方法,以供参考。
一、车丝杆的材料与性能车丝杆通常采用优质碳素钢或合金钢材料制作,其性能如下:1.高硬度:车丝杆需要具备较高的硬度,以确保在传递力矩的同时不易产生变形或断裂。
2.高耐磨性:由于车丝杆通常会长时间摩擦运动,因此需具备一定的耐磨性。
3.高精度:车丝杆作为机床等精密设备的传动元件,需要具有较高的平直度和表面粗糙度,保证传动精度。
二、车丝杆加工方法1.车削加工车丝杆可以采用车床进行车削加工,常用的车削方法包括:(1)外圆车削:将车丝杆的外圆表面进行车削加工,采用单刀片或刀架。
(2)内圆车削:对车丝杆的内径进行车削加工,可使用精密缸体车床。
(3)端面车削:对车丝杆的端面进行车削加工,通常采用面铣机或卧式镗床。
2.热处理对车丝杆材料进行热处理可提高其硬度和耐磨性,常用的热处理方法包括淬火、正火、回火等。
(1)淬火:将车丝杆加热至临界点以上,快速冷却后使其达到高硬度。
(2)正火:将车丝杆加热至880-920℃,然后冷却至室温,可以同时提高硬度和韧性。
(3)回火:将经过淬火或正火的车丝杆加热到相应的温度,保持一段时间后冷却,以减少其脆性,提高强度和韧性。
3.滚压加工滚压可以将车丝杆的直径进行加工,在一些高精度的应用场合中,滚压是保证机床高精度眼两定位最重要的加工方法。
4.磨削加工磨削可以在车丝杆加工完成后进行,以达到更高的精度和平直度,通常采用的磨削工艺包括内圆磨削、外圆磨削和圆柱磨削等。
总之,车丝杆在加工前需要进行严格的检查和准备工作,包括材料的选择、车床的选择、刀具的选择等。
加工过程中需要对尺寸和表面质量进行严格控制,以确保产品达到设计要求。
外圆滚压刀,内孔滚压刀,滚压头,滚压工艺,滚压工具,高精度内孔,滚压刀,滚压加工,镜博士滚压头

外圆滚压刀,内孔滚压刀,滚压头,滚压工艺,滚压工具,高精度内孔,滚压刀,滚压加工,锦州滚压头表面粗糙度选用与加工方法表面粗糙度选用序号=1Ra值不大于\μm=100表面状况=明显可见的刀痕加工方法=粗车、镗、刨、钻应用举例=粗加工的表面,如粗车、粗刨、切断等表面,用粗镗刀和粗砂轮等加工的表面,一般很少采用序号=2Ra值不大于\μm=25、50表面状况=明显可见的刀痕加工方法=粗车、镗、刨、钻应用举例=粗加工后的表面,焊接前的焊缝、粗钻孔壁等序号=3Ra值不大于\μm=12.5表面状况=可见刀痕加工方法=粗车、刨、铣、钻应用举例=一般非结合表面,如轴的端面、倒角、齿轮及皮带轮的侧面、键槽的非工作表面,减重孔眼表面序号=4Ra值不大于\μm=6.3表面状况=可见加工痕迹加工方法=车、镗、刨、钻、铣、锉、磨、粗铰、铣齿应用举例=不重要零件的配合表面,如支柱、支架、外壳、衬套、轴、盖等的端面。
紧固件的自由表面,紧固件通孔的表面,内、外花键的非定心表面,不作为计量基准的齿轮顶圈圆表面等序号=5Ra值不大于\μm=3.2表面状况=微见加工痕迹加工方法=车、镗、刨、铣、刮1~2点/cm^2、拉、磨、锉、滚压、铣齿应用举例=和其他零件连接不形成配合的表面,如箱体、外壳、端盖等零件的端面。
要求有定心及配合特性的固定支承面如定心的轴间,键和键槽的工作表面。
不重要的紧固螺纹的表面。
需要滚花或氧化处理的表面序号=6Ra值不大于\μm=1.6表面状况=看不清加工痕迹加工方法=车、镗、刨、铣、铰、拉、磨、滚压、刮1~2点/cm^2铣齿应用举例=安装直径超过80mm的G级轴承的外壳孔,普通精度齿轮的齿面,定位销孔,V型带轮的表面,外径定心的内花键外径,轴承盖的定中心凸肩表面序号=7Ra值不大于\μm=0.8表面状况=可辨加工痕迹的方向加工方法=车、镗、拉、磨、立铣、刮3~10点/cm^2、滚压应用举例=要求保证定心及配合特性的表面,如锥销与圆柱销的表面,与G级精度滚动轴承相配合的轴径和外壳孔,中速转动的轴径,直径超过80mm的E、D级滚动轴承配合的轴径及外壳孔,内、外花键的定心内径,外花键键侧及定心外径,过盈配合IT7级的孔(H7),间隙配合IT8~IT9级的孔(H8,H9),磨削的齿轮表面等序号=8Ra值不大于\μm=0.4表面状况=微辨加工痕迹的方向加工方法=铰、磨、镗、拉、刮3~10点/cm^2、滚压应用举例=要求长期保持配合性质稳定的配合表面,IT7级的轴、孔配合表面,精度较高的齿轮表面,受变应力作用的重要零件,与直径小于80mm的E、D 级轴承配合的轴径表面、与橡胶密封件接触的轴的表面,尺寸大于120mm的IT13~IT16级孔和序号=9Ra值不大于\μm=0.2表面状况=不可辨加工痕迹的方向加工方法=布轮磨、磨、研磨、超级加工应用举例=工作时受变应力作用的重要零件的表面。
内孔的加工讲解

研磨孔是一种光整加工方法。精度可达IT7~IT6, Ra0.4~0.025μm,形状精度也有相应的提高,但不能提 高位置精度。
16
珩磨头对孔施加一定压力,结构如图;切除极小的 加工余量。
17
②研磨孔是一种光整加工方法。精度可达IT7~IT6, Ra0.4~0.025μm,形状精度也有相应的提高,但不能提 高位置精度。需要在精镗、精铰或精磨之后进行。
1
钻孔方式: ① 工件旋转,刀具进给(如在车床上钻孔),加工 中如刀具引偏,会造成工件孔径扩大。 ② 工件不动,刀具既旋转又进给(如在钻床上钻 孔),加工中如刀具引偏,会造成工件孔轴线弯曲。
2
麻花钻的组成① 柄部 : ② 颈部 ③ 工作部分:
3
2、扩孔 扩孔是用扩孔钻在已钻出、铸出、锻出或冲出的孔 进行加工的方法。 特点:相当于半精加工,精度可达IT10,Ra 6.3~ 3.2μm。扩孔可以修正孔轴线的歪斜,生产率高。
6
铰刀特点 :刀齿多、刀槽浅、刚度好、定尺寸(一 把刀加工一种孔);精度:H7、H8、H9 。
7
二、镗孔 镗孔是在工件已有的孔上进行扩大孔径的加工方法。 特点:镗孔可分为粗镗(IT13~IT11,Ra50 ~ 12.5μm)、半精镗(IT10~IT9,Ra6.3~3.2 μm)和精 镗(IT8~IT6,Ra1.6~0.8μm)。镗孔除了能提高尺寸 精度和表面质量外,还可以修正孔的轴线的弯曲误差, 且较容易保证各孔的孔距精度和位置精度。 镗孔方式有主轴进给、工作台进给两种,当工件较大、 孔较短时采用主轴进给,反之则采用工作台进给。
11
四、磨孔与孔的精密加工 1 磨孔工艺特点:属于孔的精加方法。精度可达IT7, Ra1.6~0.4 μm。 磨孔不仅能获得较高的尺寸精度和表面质量,而且 还可以提高孔的位置精度和孔的轴线的直线度。与外圆 磨削相比,工作条件较差:砂轮直径小,刚性差,排屑 和散热困难,生产率低。对于淬硬零件中的孔加工,磨 孔是主要的加工方法。 内孔为断续圆周表面(如有键槽或花键的孔)、阶 梯孔及盲孔时,常采用磨孔作为精加工。
油缸内孔的滚压加工
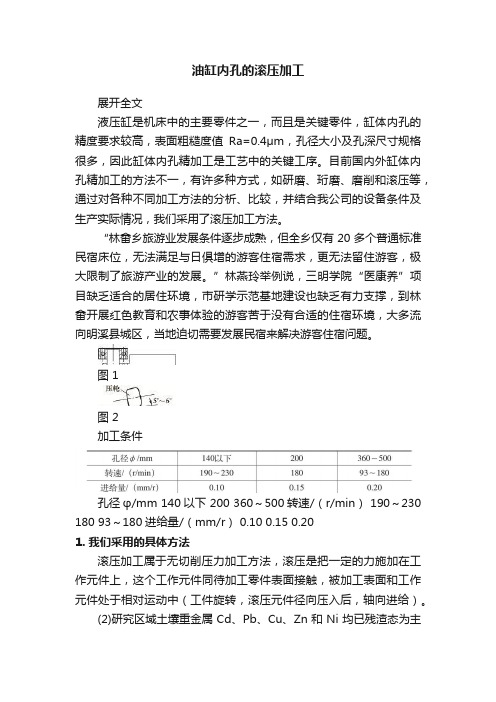
油缸内孔的滚压加工展开全文液压缸是机床中的主要零件之一,而且是关键零件,缸体内孔的精度要求较高,表面粗糙度值Ra=0.4μm,孔径大小及孔深尺寸规格很多,因此缸体内孔精加工是工艺中的关键工序。
目前国内外缸体内孔精加工的方法不一,有许多种方式,如研磨、珩磨、磨削和滚压等,通过对各种不同加工方法的分析、比较,并结合我公司的设备条件及生产实际情况,我们采用了滚压加工方法。
“林畲乡旅游业发展条件逐步成熟,但全乡仅有20多个普通标准民宿床位,无法满足与日俱增的游客住宿需求,更无法留住游客,极大限制了旅游产业的发展。
”林燕玲举例说,三明学院“医康养”项目缺乏适合的居住环境,市研学示范基地建设也缺乏有力支撑,到林畲开展红色教育和农事体验的游客苦于没有合适的住宿环境,大多流向明溪县城区,当地迫切需要发展民宿来解决游客住宿问题。
图 1图 2加工条件孔径φ/mm 140以下 200 360~500转速/(r/min) 190~230 180 93~180进给量/(mm/r) 0.10 0.15 0.201. 我们采用的具体方法滚压加工属于无切削压力加工方法,滚压是把一定的力施加在工作元件上,这个工作元件同待加工零件表面接触,被加工表面和工作元件处于相对运动中(工件旋转,滚压元件径向压入后,轴向进给)。
(2)研究区域土壤重金属Cd、Pb、Cu、Zn和Ni均已残渣态为主要存在形态,除Cu元素外,其余4种元素的3种活性组分之和比例均较高,尤其是Cd元素,其有效态略高于稳定态,生物活性最强,生物有效性大小顺序为Cd>Pb>Ni>Zn>Cu。
工作元件可以是滚压球和硬质合金嵌入物。
这种相对运动与切削加工一样是通过速度值和进给量表征的。
我们采用以202或204单列向心球轴承为主要元件的滚压工具,如图1所示。
在加工较小孔径的缸体时,我们采用了整体滚压工具。
例如,在加工CK61160数控重型卧式车床床头箱内的变速液压缸时(孔径为φ80+0.05 +0.03mm),使用的是深孔弹性滚压工具。
常见加工方法
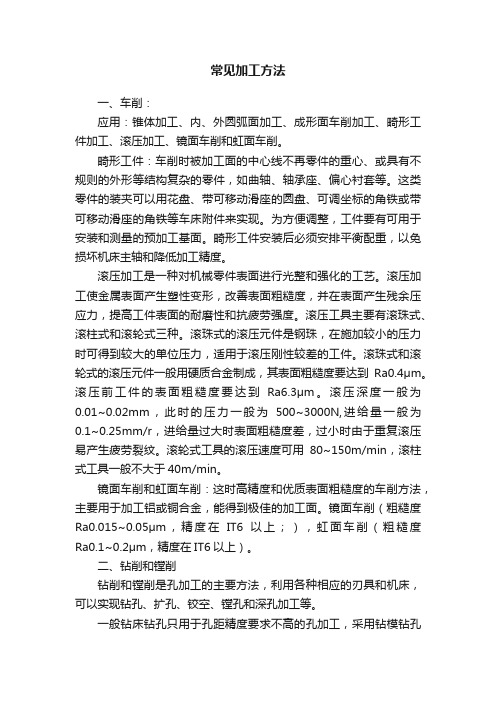
常见加工方法一、车削:应用:锥体加工、内、外圆弧面加工、成形面车削加工、畸形工件加工、滚压加工、镜面车削和虹面车削。
畸形工件:车削时被加工面的中心线不再零件的重心、或具有不规则的外形等结构复杂的零件,如曲轴、轴承座、偏心衬套等。
这类零件的装夹可以用花盘、带可移动滑座的圆盘、可调坐标的角铁或带可移动滑座的角铁等车床附件来实现。
为方便调整,工件要有可用于安装和测量的预加工基面。
畸形工件安装后必须安排平衡配重,以免损坏机床主轴和降低加工精度。
滚压加工是一种对机械零件表面进行光整和强化的工艺。
滚压加工使金属表面产生塑性变形,改善表面粗糙度,并在表面产生残余压应力,提高工件表面的耐磨性和抗疲劳强度。
滚压工具主要有滚珠式、滚柱式和滚轮式三种。
滚珠式的滚压元件是钢珠,在施加较小的压力时可得到较大的单位压力,适用于滚压刚性较差的工件。
滚珠式和滚轮式的滚压元件一般用硬质合金制成,其表面粗糙度要达到Ra0.4μm。
滚压前工件的表面粗糙度要达到Ra6.3μm。
滚压深度一般为0.01~0.02mm,此时的压力一般为500~3000N,进给量一般为0.1~0.25mm/r,进给量过大时表面粗糙度差,过小时由于重复滚压易产生疲劳裂纹。
滚轮式工具的滚压速度可用80~150m/min,滚柱式工具一般不大于40m/min。
镜面车削和虹面车削:这时高精度和优质表面粗糙度的车削方法,主要用于加工铝或铜合金,能得到极佳的加工面。
镜面车削(粗糙度Ra0.015~0.05μm,精度在IT6以上;),虹面车削(粗糙度Ra0.1~0.2μm,精度在IT6以上)。
二、钻削和镗削钻削和镗削是孔加工的主要方法,利用各种相应的刃具和机床,可以实现钻孔、扩孔、铰空、镗孔和深孔加工等。
一般钻床钻孔只用于孔距精度要求不高的孔加工,采用钻模钻孔孔距精度能达到±0.1mm。
镗削不仅可以加工直径很大的孔,而且能够保证孔系有较高的孔距精度。
镗床上使用相应的刀具后还可以加工有较高精度要求的端面、内孔肩面和内孔圆槽等。
数控车床加工件内孔表面加工方法怎么选择
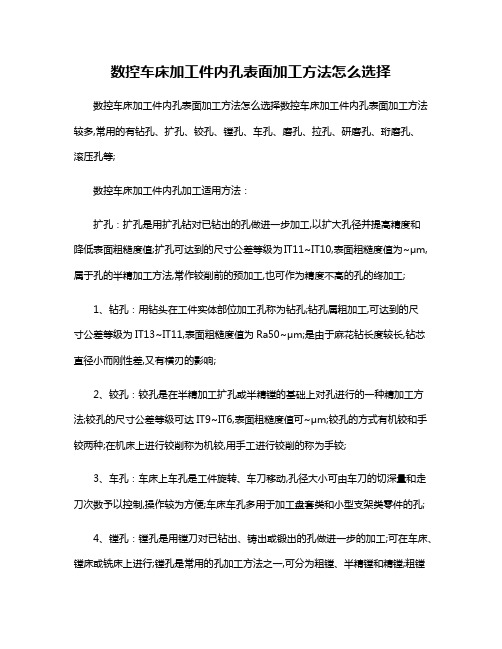
数控车床加工件内孔表面加工方法怎么选择数控车床加工件内孔表面加工方法怎么选择数控车床加工件内孔表面加工方法较多,常用的有钻孔、扩孔、铰孔、镗孔、车孔、磨孔、拉孔、研磨孔、珩磨孔、滚压孔等;数控车床加工件内孔加工适用方法:扩孔:扩孔是用扩孔钻对已钻出的孔做进一步加工,以扩大孔径并提高精度和降低表面粗糙度值;扩孔可达到的尺寸公差等级为IT11~IT10,表面粗糙度值为~μm,属于孔的半精加工方法,常作铰削前的预加工,也可作为精度不高的孔的终加工;1、钻孔:用钻头在工件实体部位加工孔称为钻孔;钻孔属粗加工,可达到的尺寸公差等级为IT13~IT11,表面粗糙度值为Ra50~μm;是由于麻花钻长度较长,钻芯直径小而刚性差,又有横刃的影响;2、铰孔:铰孔是在半精加工扩孔或半精镗的基础上对孔进行的一种精加工方法;铰孔的尺寸公差等级可达IT9~IT6,表面粗糙度值可~μm;铰孔的方式有机铰和手铰两种;在机床上进行铰削称为机铰,用手工进行铰削的称为手铰;3、车孔:车床上车孔是工件旋转、车刀移动,孔径大小可由车刀的切深量和走刀次数予以控制,操作较为方便;车床车孔多用于加工盘套类和小型支架类零件的孔;4、镗孔:镗孔是用镗刀对已钻出、铸出或锻出的孔做进一步的加工;可在车床、镗床或铣床上进行;镗孔是常用的孔加工方法之一,可分为粗镗、半精镗和精镗;粗镗的尺寸公差等级为IT13~IT12,表面粗糙度值为~μm;半精镗的尺寸公差等级为IT10~IT9,表面粗糙度值为~μm;精镗的尺寸公差等级为IT8~IT7,表面粗糙度值为~μm;上海市松江丰远是在原松江县骏马五金厂1995年成立的基础上成立的,位于国际大都市上海的西郊;工厂是由三线建设大型军工企业回沪人员创建;二十多年来先后成为几十家内外资企业的配套厂家;以合理的价格、可靠的质量多次成为年度先锋供应商;配套产品远销十多个国家和地区;“合作共赢”是我厂宗旨;我厂主要业务:机械零配件制作,工装夹具制作,铝制吸塑模设计制作,液压阀块制作,橡胶辊制作,工业滚筒制作以及上海地区的机械加工;。
内圆磨削的工艺特点

内圆磨削的工艺特点内圆磨削是一种将金属、非金属材料的内孔进行加工的技术。
相比其他加工方法,内圆磨削具有以下几个工艺特点:1.加工精度高:内圆磨削可以实现高精度的加工,其精度可以达到μm级别。
这对于一些对孔径、圆度等精度要求较高的零件来说尤为重要。
2.加工效率高:内圆磨削的加工效率较高,可以一次加工出理想的孔径和圆度,在一定程度上提高生产效率。
3.加工质量好:内圆磨削的表面质量较好,能够实现光洁度较高的加工效果,提高零件的使用寿命。
4.适应性强:内圆磨削适用于各种材料的内孔加工,包括金属材料和非金属材料,如钢、铸铁、不锈钢、铝、铜、陶瓷等。
5.加工范围广:内圆磨削可以加工各种形状的内孔,例如圆孔、椭圆孔、扇形孔、多孔等。
6.加工工艺简单:内圆磨削的操作相对简单,只需要通过磨削机床上的夹具和磨削工具,调整参数后即可进行加工。
同时,由于磨削时工件不与磨削工具直接接触,因此对工件的损伤较小。
7.易于实现自动化:内圆磨削可以通过自动化设备进行加工,减少了人力操作,提高了生产效率和一致性。
8.加工后余量小:由于内圆磨削是通过磨削工具进行材料的削除,因此加工后的余量相比其他加工方法较小。
9.工艺性能可调节:内圆磨削可以根据加工要求调整磨削参数,如磨削速度、进给速度、磨削液的喷射压力等,以实现所需的表面光洁度、尺寸精度和加工效率。
10.灵活性强:内圆磨削可根据不同需要选择不同磨削方法,如内经磨削、内圆磨削和内外圆磨削等方法。
总之,内圆磨削是一种高效、高精度的内孔加工方法,具有适应性强、操作简单、加工质量好等工艺特点,被广泛应用于制造业中。
丝杆螺母的加工方式

丝杆螺母的加工方式
丝杆螺母的加工方式是一项精密的工艺,需要经过多道工序和严格的质量控制。
下面是一些常见的丝杆螺母加工方式:
1.切削加工:通过车床或铣床等切削设备,对丝杆螺母进行切削加工,以获得所需的形状和尺寸。
这种方式适用于批量生产,加工精度高,但生产效率相对较低。
2.磨削加工:通过磨床对丝杆螺母进行磨削加工,以获得更高的精度和更光滑的表面。
这种方式适用于高精度丝杆螺母的加工,但生产效率较低,且需要消耗大量的砂轮和磨料。
3.滚压加工:通过滚压机对丝杆螺母进行滚压加工,以获得更精确的尺寸和更光滑的表面。
这种方式适用于长丝杆螺母的加工,但需要使用特殊的滚压工具和材料。
4.热处理加工:通过热处理工艺对丝杆螺母进行处理,以提高其硬度和耐磨性。
这种方式适用于高强度和高耐磨性要求的丝杆螺母,但需要严格控制热处理工艺和材料的质量。
总之,丝杆螺母的加工方式需要根据具体的应用场景和要求选择合适的加工工艺和技术,以保证其质量和性能的可靠性。
齿轮内孔特殊车削与磨削的对比研究

齿轮内孔特殊车削与磨削的对比研究【摘要】齿轮内孔精加工目前常用的方法是磨孔,但磨孔效率比较低,孔径大小控制完全依靠操作者水平保证,工序加工能力指数(CPK)值不高,通过特殊的车削工艺来加工齿轮内孔完全可以满足其设计要求,而且各个方面都超越了磨孔工艺。
论文通过研究、对比,说明了内孔采用特殊车削工艺可以获得比磨孔更佳的综合效果,从而为生产实际中齿轮内孔精加工提供了更好的选择。
【关键词】齿轮内孔加工;特殊车孔;磨孔;综合成本前言齿轮是传动件的核心,其加工精度和加工效率直接反映生产厂家的制造水平。
齿轮除了齿形加工非常重要以外,其内孔加工也同等重要,孔的加工精度直接影响到齿轮的啮合精度。
佛山市星光传动机械有限公司目前齿轮内孔精加工一般都是采用磨孔方法,加工精度可以满足其设计要求,但加工效率相当低,对操作者水平依耐较大,工序能力指数CPK不高、且不稳定;当产能扩大时,采用磨孔的方法无法满足生产要求。
公司采用的齿轮材料为20CrMnTi,热处理后硬度为58-60HRC,精加工余量为0.1mm。
论文研究采用特殊的车孔工艺:超硬立方氮化硼(CBN)刀具,高强度抗震刀杆和高精度斜导轨数控车床及合适的工艺参数。
研究结果表明,不仅加工精度可以达到设计要求,而且加工效率远高于磨孔工艺;论文研究成果已应用于公司的生产中。
1 设备使用设备车床:高精密斜导轨数控车:长城CK7150B;刀杆:高强度抗震刀杆:山特系列;刀片:立方氮化硼CBN:山特系列;2 相关参数的计算2.1 工序能力指数(CPK值)CPK= min〔﹙USL-A VG〕/3σ﹙A VG-LSL﹚/3σ〕Min:取最小值USL:规格上限;LSL:规格下限A VG:样品平均值;σ:样品标准偏差2.2 单件加工时间单件加工时间=装夹时间+校正时间+机动时间+检测时间+刀具修正时间+取件时间。
2.3 单件成本加工的单件成本=单件人工费+刀具成本折算费+水电折算费+设备折旧费+场地折算费。
- 1、下载文档前请自行甄别文档内容的完整性,平台不提供额外的编辑、内容补充、找答案等附加服务。
- 2、"仅部分预览"的文档,不可在线预览部分如存在完整性等问题,可反馈申请退款(可完整预览的文档不适用该条件!)。
- 3、如文档侵犯您的权益,请联系客服反馈,我们会尽快为您处理(人工客服工作时间:9:00-18:30)。
内孔磨削加工与滚压加工的比较
文章来源:互联网 文章作者:浦沅集团起重机公司 娄恬 发布时间:2006-12-29 字体: [大 中 小] 今 一种新型数控系统的研制与开发
M1432A 型外圆磨床工作台故障诊断 CNC 数控加工优化控制系统OMAT-Pro 凸轮轴仿形加工的恒速磨削
凸轮轴磨床电气设计
数控凸轮轴磨床加工过程的仿真软件 M6420B 滚刀磨床分度故障及对策 开放式数控系统在超精密加工中的应 日 导 读
1 概述
实际生产中,对于表面粗糙度Ra0.04μm ~Ra1.6μm 的内孔加工,常用加工工艺是磨削、滚压、拉削、珩磨等。
拉削加工刀具费用大,生产效率高,适应大批量生产;珩磨用于光整加工表面粗糙度Ra0.04μm 以上。
所以一般最常用的是磨削和滚压加工。
下面通过分析一零件的加工工艺,对磨削加工、滚压加工进行比较。
2 工艺分析
该零件如图,内径φ140 0.0630、粗糙度Ra0.08μm 圆度公差0.045mm 。
原加工工艺:车-粗磨-精磨,车削加工留磨量0.2mm ~0.4mm 。
该工艺能保证零件技术要求。
现场测试结果:表面粗糙度Ra0.08μm,尺寸在公差φ140~φ140.063mm 范围内,圆度公差分布在0~0.025mm 范围内。
磨削加工是高速切削能呈分散状态,降低零件表面粗糙度,还能提高零件的尺寸精度和几何精度。
但是磨削过程中由于磨削速度高产生大量磨削热传给零件,使得零件温升几十度,工件冷却(受环境温度
影响)后收缩、孔径缩小,为保证尺寸精度需人为调整完工尺寸,所以出现加工尺寸分散现象。
磨削区温度很高(表面局部温度可达1000℃)产生对零件使用性能危害甚大的表面层残余拉应力、磨削裂纹、烧伤等;而实际生产中内孔磨削降低磨削热较困难;磨削加工效率低。
现加工工艺:粗车-半精车-精车-滚压,零件在车床上即可加工完毕,此工艺同样能完全保证零件技术要求。
现场实测结果:表面粗糙度Ra0.08μm;尺寸分布在φ140.02mm~φ140.04mm之间,加工尺寸相对集中;圆度公差分布在0.01~0.03mm范围内。
工艺执行过程为保证零件质量对车削要求很高,精车零件为表面粗糙度Ra3.2μm、尺寸φ140-0.01 0.02。
因为滚压加工零件实际压入量很小,且是靠零件加工表面自身定位进行加工,故能降低零件的表面粗糙度、提高尺寸精度,但零件的形状偏差不会有明显改善,所以零件滚压加工后的精度主要决定于零件滚压前预加工(车削)的精度、表面粗糙度。
滚压加工是无屑加工,无发热现象,完工尺寸即成形尺寸,加工尺寸容易控制。
滚压加工零件表面层产生残余压应力和冷硬化,可提高零件疲劳强度,生产效率高。
但需制作滚压工具。
3 工艺比较
内孔磨削加工工艺和滚压加工工艺都可以提高零件尺寸精度、降低表面粗糙度。
但有以下区别:
内孔磨削加工对上道工序要求不高,能达到比滚压加工更高的精度。
实际生产中内孔磨削加工过程降低磨削区温度较困难,加工表面层产生的残余拉应力、磨削裂纹、烧伤等,影响零件使用性能,生产效率低。
滚压加工对上道工序要求高,不能提高零件形状精度。
因加工过程无发热现象,尺寸容易控制;零件加工表面层产生的残余压应力和冷硬化有利于提高零件使用性能;生产效率高。
4 结语
通过上面分析、比较可知:在内孔粗糙度Ra0.08μm~Ra1.6μm范围、定型产品、批量生产时,采用滚压加工工艺与磨削加工相比有如下优点:
生产效率提高几倍;
工艺简单;
零件使用性能有提高;
减少转运次数有利防止磕碰。