点焊工艺基础知识
点焊生产工艺培训
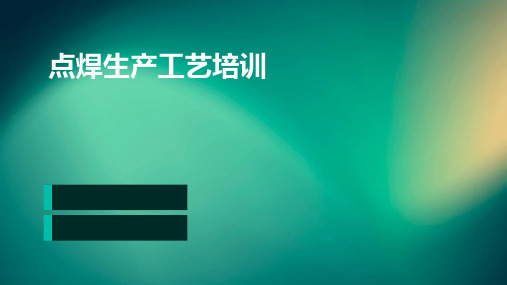
05 点焊缺陷及预防措施
焊接不牢的预防措施
总结词
焊接不牢是点焊生产中常见的问题,主要原因是焊接参数不当或操作不规范。
详细描述
为预防焊接不牢,应确保电极压力足够,焊接电流稳定且符合工艺要求,同时 保持电极头清洁,避免夹杂物影响焊接质量。在生产过程中应定期检查电极压 力和焊接电流,确保其处于最佳状态。
点焊生产工艺培训
目录
• 点焊工艺简介 • 点焊设备与工具 • 点焊工艺流程 • 点焊质量影响因素 • 点焊缺陷及预防措施 • 安全操作规程与环保要求
01 点焊工艺简介
点焊的定义与特点
总结词
点焊是一种将两个金属板通过局部加热熔化连接在一起的焊 接工艺。
详细描述
点焊是一种常见的焊接工艺,通过在两个金属板之间施加电 流,利用电阻热熔化接触点,从而实现连接。点焊具有操作 简单、成本低、生产效率高等特点,广泛应用于汽车、电器 、建筑等制造业领域。
其他点焊缺陷及预防措施
总结词
点焊生产中还可能出现其他缺陷,如焊点表面质量差、 电极头磨损过度等。
详细描述
为避免焊点表面质量差,应保持电极头清洁并定期修磨 。对于电极头磨损过度的情况,应及时更换或修整电极 头,确保其符合工艺要求。此外,还应加强生产过程中 的质量检查,及时发现并处理各种缺陷。
06 安全操作规程与环保要求
有害气体
点焊过程中会产生一些有害气体,如 一氧化碳、氮氧化物等,应通过通风 设施排出室外。
烟尘
点焊过程中会产生烟尘,应通过除尘 器进行收集和处理。
噪音
点焊设备运行时会产生噪音,应采取 消音措施降低噪音。
废弃物
点焊过程中产生的废弃物应按照相关 规定进行分类处理。
点焊设备的环保要求与改进方向
第一章 点焊

点焊的热源及加热特点
1、点焊热源
Q 0.24 i 2 (t ) r (t ) dt
(1)焊件本身电阻Rw 通常电阻率高的金属材料其导热性差,如不锈钢,点焊 时产热容易而散热难,因此可以用较小的焊接电流(几千 安培); 电阻率低的金属一般导热性好,如铝合金,点焊时 产热难而散热易,故须用很大的焊接电流,高达几万安培。 金属的电阻率不仅取决于金属的成分,还取决于金 属表面状态及温度,随着温度的升高电阻率增大,并且金 属熔化时电阻率比熔化前高1~2倍。 在焊接时,随着温度的升高,除电阻率升高使焊件 本身电阻Rw升高外,同时金属的压溃强度降低,使焊件 与焊件之间、焊件与电极之间的接触面积增大,电流线分 布分散,因而引起焊件电阻Rw减小。点焊低碳钢时,在 上述两种相互矛盾的因素下,加热开始时焊件的电阻Rw 逐渐增加,当熔核形成时又逐渐降低。
F>0,I>0 2)作用: 在热和机械力联合作用下,形成塑性环和 熔核,直到熔核长到所要求尺寸.
3.冷却结晶阶段
1)机电特点:
F>0,I=0
2)作用:
保证熔核在压力状态下进行冷却结晶,冷 却结晶时间很短(一般1~2周波),但是 结晶凝固过程符合金属学的凝固理论
维持阶段的作用 1. 保证熔核在压力状态下结晶,减少出现 缩孔裂纹等组织缺陷的几率; 2.避免电极与工件“打火”
(一)、点焊接头形成过程
点焊接头形成的三个阶段
a) 预压 b) 、c)通电加热 d)冷却结晶
点焊过程
加压 通电加热、形成熔核 断电、熔核结晶
卸压 1、焊件装配成搭接接头,并压紧在两柱状电极之间, 加压、加紧。 2、通电加热,接头接触表面,金属局部熔化,形成熔 核,熔核周围金属 处于塑性状态 3、切断电流,融合金属在压力下结晶,形成焊点。 4、卸压
点焊工艺知识培训

选择合适的电极制造材料,确保具 有良好的导电性和导热性,同时具 备耐磨性和耐腐蚀性。
对电极进行必要的热处理和表面处 理,以提高电极的性能和使用寿命 。
04
点焊焊接质量与控制
点焊焊接缺陷的类型和原因分析
飞溅类缺陷 飞溅是由于电极端面不平整或电 极与工件接触不良而引起的。飞 溅会导致焊接处不连续,影响焊 接质量。
点焊的适用范围和局限性
适用范围
点焊适用于金属薄板、管件、线材等材料的连接,广泛应用于汽车、航空、电子 等领域。
局限性
点焊不适合连接不同材料、厚度差异较大的金属,以及一些高熔点的金属材料。 同时,点焊的焊接质量受电极材料、表面质量、电流稳定性等因素影响。
02
点焊工艺参数
焊接电流
焊接电流对熔核形 成和焊接质量有着 直接的影响。
焊接时间过长,会导致热影响 区扩大、晶粒粗大、力学性能 下降等缺陷。
焊接时间过短,会导致熔核形 成不完全、未熔合等缺陷。
焊接压力
焊接压力是指在焊接过程中,电极对工件施加的压力。 焊接压力过大,会导致工件变形、电极寿命降低等缺陷。
焊接压力过小,会导致熔核形成不完全、未熔合等缺陷。
焊接功率
焊接功率是指焊接过程中消耗的 能量。
裂纹类缺陷 裂纹是由于材料内部应力集中、 热膨胀系数差异等原因引起的。 这类缺陷会导致焊接处断裂,严 重影响焊接质量。
熔核偏移类缺陷
熔核偏移是由于电流、电极压力 、电极端面与工件表面贴合不良 等因素引起的。这类缺陷会导致 焊接处强度不足。
缩孔类缺陷
缩孔是由于金属表面氧化膜的熔 化和电极压力不足而引起的。这 类缺陷会导致焊接处承载能力下 降。
有关点焊的焊接工艺参数知识

电阻点焊
1.典型材料的焊接
①碳钢C≤0.15%
焊接性非常好,可调节参数具有很大的调节范围。
焊点直径:5.5•√t[㎜]
电极压力:2000 t[N]
焊接时间:8 t[周波]
焊接电流:9.5•√t[KA]
抗剪强度:6000t[N]注:t—板厚(mm)
1周波=0.02s
②碳钢C>0.15%
焊接性好,但由于碳含量的增大,易产生过热及裂纹
倾向。
因此,常用慢速加热,冷却或加脉冲的方法焊接。
③镀层钢板的点焊
点焊性较好。
焊接时注意的问题:
▲电极易与镀层粘附,缩短电极使用寿命。
▲镀层金属的熔点比低碳钢低,加热时先融化的镀层金属使两板之间的
接触面扩大,电流密度减小,因此焊接电流密度比无镀层时大。
▲电极压力应比无镀层时大。
④不锈钢的点焊
▲奥氏体不锈钢、铁素体不锈钢:由于电阻率高、导热性差、
热敏感性强,可采用较小的焊接电流、较短的焊接时间和较
大的电极压力。
▲马氏体不锈钢由于有淬火倾向,可采用较长焊接时间。
⑤铝合金的点焊
▲电导率和热导率较高,必须采用较大的焊接电流和较短的焊
接时间。
▲塑性温度范围窄线膨胀系数大,必须采用较大的电极压力,
电极随动性要好。
▲工件表面易生成氧化膜,焊前必须严格清理。
⑥铜合金的点焊
铜合金与铝合金相比,无太大的困难。
但纯铜点焊比较困
难。
必须采取一定的措施,如电极与工件之间加垫片等。
2.工艺参数的确定
注: t—板厚(mm) 1周波(per)=0.02s。
电焊工基本知识电焊入门基础知识
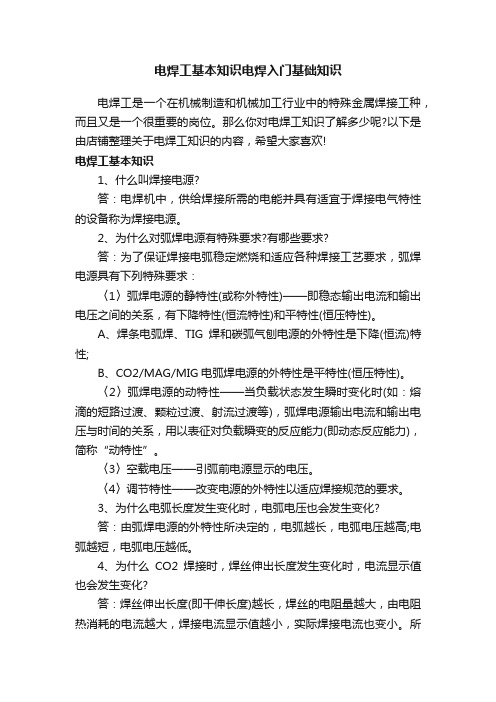
电焊工基本知识电焊入门基础知识电焊工是一个在机械制造和机械加工行业中的特殊金属焊接工种,而且又是一个很重要的岗位。
那么你对电焊工知识了解多少呢?以下是由店铺整理关于电焊工知识的内容,希望大家喜欢!电焊工基本知识1、什么叫焊接电源?答:电焊机中,供给焊接所需的电能并具有适宜于焊接电气特性的设备称为焊接电源。
2、为什么对弧焊电源有特殊要求?有哪些要求?答:为了保证焊接电弧稳定燃烧和适应各种焊接工艺要求,弧焊电源具有下列特殊要求:〈1〉弧焊电源的静特性(或称外特性)——即稳态输出电流和输出电压之间的关系,有下降特性(恒流特性)和平特性(恒压特性)。
A、焊条电弧焊、TIG焊和碳弧气刨电源的外特性是下降(恒流)特性;B、CO2/MAG/MIG电弧焊电源的外特性是平特性(恒压特性)。
〈2〉弧焊电源的动特性——当负载状态发生瞬时变化时(如:熔滴的短路过渡、颗粒过渡、射流过渡等),弧焊电源输出电流和输出电压与时间的关系,用以表征对负载瞬变的反应能力(即动态反应能力),简称“动特性”。
〈3〉空载电压——引弧前电源显示的电压。
〈4〉调节特性——改变电源的外特性以适应焊接规范的要求。
3、为什么电弧长度发生变化时,电弧电压也会发生变化?答:由弧焊电源的外特性所决定的,电弧越长,电弧电压越高;电弧越短,电弧电压越低。
4、为什么CO2焊接时,焊丝伸出长度发生变化时,电流显示值也会发生变化?答:焊丝伸出长度(即干伸长度)越长,焊丝的电阻量越大,由电阻热消耗的电流越大,焊接电流显示值越小,实际焊接电流也变小。
所以焊丝伸出长度一般设定在12--20mm范围内。
5、为什么CO2/MAG/MIG焊接时,焊接电流和电弧电压要严格匹配?答:CO2/MAG/MIG焊接时,调节焊接电流—即调节焊丝的给送速度;调节电弧电压—即调节焊丝的熔化速度;很显然,焊丝的熔化速度和给送速度一定要相等,才能保证电弧稳定焊接。
〈1〉在焊接电流一定时,调节电弧电压偏高,焊丝的熔化速度增大,电弧长度增加,熔滴无法正常过渡,一般呈大颗粒飞出,飞溅增多。
点焊常识

点焊基本常识(何文章提供)一. 点焊及施焊方法点焊工作原理是根据电流的热效应。
点焊时两个被焊工件首先在焊钳或焊枪气缸的作用下通过上下电极压紧,然后通过焊接电流(一般在几千到几万安培 ),根据焦耳定律Q=0.24I 2Rt,使被焊处金属熔化,达到焊接温度后切断电流,在电极的压力作用下,熔化金属冷却结晶形成焊核。
点焊多数用于薄板焊接,接头形式多采用搭接接头和翻边接头。
点焊的种类很多,我们焊装车间主要有两种。
即:双面单点,单面双点。
双面单点是应用最广的一种点焊形式。
如:悬挂式吊点焊机,座点焊机。
它的特点是一次通电只能焊一个焊点。
单面双点:主要应用在工件同面上,另一面垫有一大块导电性能很好的铜导电板(块),焊接变压器二次线两端与电极连接,工件被压在电极与铜垫块之间。
因此,在装配多点焊机电极块时必须用绝缘材料将电极块与电块支架分离开。
维修时一定要把原有的绝缘垫片装上,防止在施焊时分流。
单面双点(多用与专用多点焊机) 双面单点二.点焊的循环每焊一个焊点必须经过予压.焊接.维持.休止四个过程。
每一个过程都持续一定的时间,分别为予压时间t压,焊接时间t焊,维持时间t维,和休息时间t休,这四个过程对点焊的质量是不可缺少PI予压:予压时间是指电极开始向工件加压到通电开始这段时间。
在这段时间内,电极必须向工件加给焊接时所必须的压力。
保证被焊工件紧密接触,如予压时间太短,没等两工件紧密接触时就开始通电,因接触电阻太大,点焊时就可能出现烧穿现象。
焊接:焊接时间是指在点焊过程中,电极通过的时间,是焊接过程中的重要环节。
焊接时电流通过电极流经焊件,使焊接处产生强烈的电阻热,在热量最集中处的金属首先熔化,同时熔化的金属被周围尚未熔化处与塑性状态的金属环所包围,使熔化的金属不能外溢。
随着时间的增长,熔核不断扩大,焊接时加热的速度是非常快的,低碳钢点焊时可以在0.06~0.1秒内使核心温度达到1800O C以上超过金属熔点200~300度。
点焊工艺基础知识

武汉兴园金属有限责任公司点焊工艺基础知识版本:A/01 主题内容与适用范围2 焊点的形成及对其质量的一般要求焊接是两种或两种以上同种或异种材料通过分子或原子间的结合和扩散而连成一体的工艺加工过程。
焊接包括:熔化焊、压焊、钎焊。
压焊包括:电阻焊、锻焊、摩擦焊、高频焊、超声波焊等等。
电阻焊包括:点焊、凸焊、对焊、缝焊。
电阻焊就是将工件置于两个电极之间加压,通以电流,利用工件的电阻产生热量并形成局部熔化,或达到塑性状态。
断电后,压力继续作用,形成牢固接头。
2.1焊点的形成点焊过程可分为彼此相联的三个阶段:预加压力、通电加热和锻压。
2.1.1预加压力预加电极压力是为了使焊件在焊接处紧密接触。
若压力不足,则接触电阻过大,导致焊件烧穿或将电极工作面烧损。
因此,通电前电极力应达到预定值,以保证电极与焊件、焊件与焊件之间的接触电阻保持稳定。
2.1.2通电加热通电加热是为了供焊件之间形成所需的熔化核心。
在预加电极压力下通电,则在两电极接触表面之间的金属圆柱体内有最大的电流密度,靠焊件之间的接触电阻和焊件自身的电阻,产生相当大的热量,温度也很高。
尤其是在焊件之间的接触面处,首先熔化,形成熔化核心。
电极与焊件之间的接触电阻也产生热量,但大部分被水冷的铜合金电极带走,于是电极与焊件之间接触处的温度远比焊件之间接触处为低。
正常情况下是达不到熔化温度。
在圆柱体周围的金属因电流密度小,温度不高,其中靠近熔化核心的金属温度较高,达到塑性状态,在压力作用下发生焊接,形成一个塑性金属环,紧密地包围着熔化核心,不使熔化金属向外溢出。
在通电加热过程中有两种情况可能引起飞溅:一种是开始时电极预压力过小,熔化核心周围未形成塑性金属环而向外飞溅;另一种是加热结束时,因加热进间过长,熔化核心过大,电极压力下,塑性金属环发生崩溃,熔化金属从焊件之间或焊件表面溢出。
2.1.3锻压锻压是在切断焊接电流后,电极继续对焊点挤压的过程,对焊点起着压实作用。
点焊知识技能培训资料

有动作不通电
焊机内晶闸管不良
控制器内P板不良
谢谢大家!
4. 焊接缺陷及常见故障
4.1 焊 点 被 烧 穿 4.2 焊 接 时 飞 溅 大 4.3 焊 点 压 痕 过 大 4.4 焊点太小或强度不够 4.5 焊点有烧痕或划痕 4.6 焊 点 有 裂 纹 4.7 启 动 后 不 动 作 4.8 有 动 作 不 通 电
4.1 焊 点 被 烧 穿
焊接电流过大
电极端面修磨粗糙
4.6 焊 点 有 裂 纹
焊接电流过大
电极压力过小
焊
点
被焊金属本身缺陷
有
工件表面污物过多
裂
纹
上、下电极未对准
焊机调整不当
4.7 启 动 后 不 动 作
气体压力不足
没有压缩空气
焊
机
电磁气阀不良
不
起动 开关不良
动
焊机或控制器 未接通电源。
作
温度继电器动作
4.8 有 动 作 不 通 电
点焊
凸焊
缝焊 对焊(闪光对焊)
1-2.点焊概述
点焊是将被焊工件压紧于两电极之 间,利用电流在工件接触面及邻近区域 的电阻上产生热量,并将其加热到熔化 或塑性状态,使之形成金属结合的一种 焊接方法。
1-3.点焊的特点
适宜大批量生产
生产率高且无噪声及有害气体
操作简单
易于实现机械化和自动化
特点
焊接成本低
单面
单面单点焊
点
点焊
单面双点焊
焊
双面
双面单点焊
点焊
双面双点焊
单面点焊
单面单点焊
单面双点焊 铜垫
双面点焊
+—
点焊基础知识

第一章
1.1 1.2
第二章
2.1 2.2 2.3 2.4
第三章 第四章
4.1 4.2 4.3 4.4 4.5
第五章
概述 目 录
点焊的定义 点焊技术的特点
点焊的工作原理及工艺参数影响
点焊的工作原理 点焊熔核形成过程 点焊工艺参数的影响 影响点焊强度的因素
焊接电流(A)
焊接力(kg)
焊接时间(周波)
6500
200
10
8000
200
13
8500
200
13
9500
200
15
12000
300
18
第三章 电焊的设备
一、点焊设备的组成 电阻焊设备由焊钳、焊接变压器、控制箱三大部分组
成。(如图一(1)、图一(2)所示)
图一(1):焊钳
图一(2):点焊机
其中焊钳是根据焊接设备的形状,尺寸而决定,种 类繁多。它主要由气缸,电极,及启动开关装置组 成。
1.1 点焊的定义 焊接材料在电极压力短时间、大电流的作用下产生的
电阻热使焊接区熔合连接在接头处产生一个熔合点(板厚 0.8mm的材料0.2秒电流8000A)的焊接技术称之为点焊。
1.2 点焊技术的特点
1、焊接时间短,效率高; 2、有助于减轻重量,因为不需要螺栓和焊条; 3、应力小且表面平滑,因为热仅在接头处集中; 4、如果焊接参数已被设定,对焊接操作人员的经
验要求不高; 5、没有合适的无损检测办法对焊接结果进行检测; 6、需要大量的设备投资。
第二章 点一定压力下,给电极与 工件间通以焊接电流,利用电 极与工件间接触电阻产生的热 量将两电极间工件融化,在压 力的作用下进行冷却,形成焊 核。
电焊工作业基础理论知识
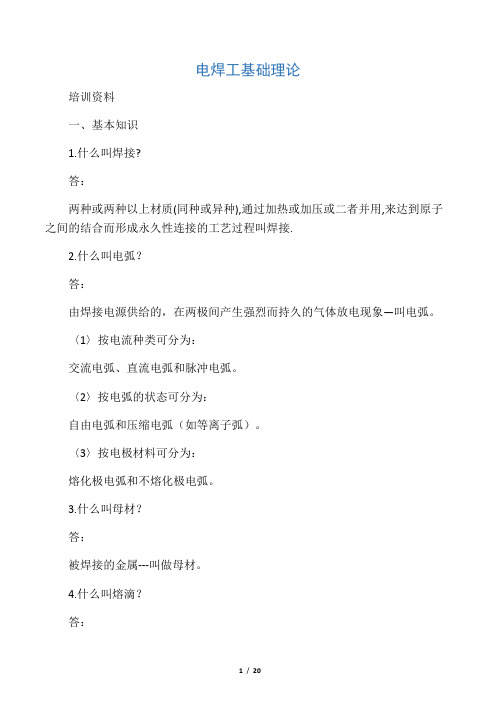
对接、角接、搭接和T型接等。
3.什么叫熔深?
答:
在焊接接头横截面上,母材熔化的xx。
4.什么叫焊接位置?有几种形式?
答:
熔焊时,焊件接缝所处的空间位置。有平焊、立焊、横焊和仰焊等形式。
5.什么叫向下立焊和向上立焊?
答:
〈1〉立焊时,电弧自上向下进行的焊接—叫向下立焊。如:
机—焊接设备的高性能和稳定性
料—焊接材料的高质量
10.什么叫焊机的负载持续率?
答:
负载持续率指焊接电源在一定电流下连续工作的能力。国标规定手工焊额定负载持续率为60%,自动或半自动为60%和100%。如:500KR2焊机在额定负载持续率60%时的额定电流是500A,在实际负载持续率100%(自动焊)时,其最大焊接电流≤387A。
11.什么叫焊枪的负载持续率?
〈2〉降低耗电量
65.4%;
〈3〉设备台班费较焊条电弧焊降低67-80%,降低成本20-40%;
〈4〉减少人工费、工时费,降低成本10-16%;
〈5〉节省辅助工时、辅料消耗及矫正变形费用;
综合五项,CO2焊能使焊接总成本降低
39.6-
78.7%,平均降低59%。
20.为什么CO2焊接有飞溅?
答:
焊丝端部的熔滴与熔池短路接触(短路过渡),由于强烈过热和磁收缩的作用使熔滴爆断,产生飞溅。CO2焊机的输出电抗器和波形控制可以将飞溅降低至最小程度。
9.什么叫CO2电源电弧系统的自身调节特性?为什么CO2焊接用细焊丝?
答:
等速送丝系统下,当弧长变化时引起电流和熔化速度变化,使弧长恢复的作用成为电源电弧系统的自身调节作用。使用的焊丝直径越细,电弧的自身调节作用越强,电弧越稳定,飞溅越少。这就是CO2焊接用细焊丝的原理。唐山松下CO2焊机通过先进的控制技术,电弧的自身调节作用最好,性能最稳定。
点焊的知识
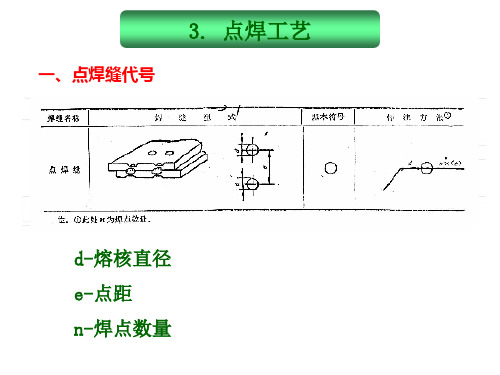
一、点焊缝代号
d-熔核直径 e-点距
n-焊点数量
二、点焊接头设计 点焊通常采用搭接接头和折边接头接头可以由两个
或两个以上等厚度或不等厚度的工件组成。在设计点焊 结构时,必须考虑电极的可达性,即电极必须能方便地 抵达工件的焊接部位。同时还应考虑诸如边距、搭接量、 点距、装作用:恢复到起始状态所必须的工艺时间;
电极提起也必须在电流全部切断之后,否则 电极与焊件之间会引起火花,甚至烧穿工件
为了改善接头的性能,有时会将下列各项中的一项或 多项加于基本循环: 1)加大预压力,以消除厚焊件之间的间隙,Fpr=1.52Fw; 2)用预热脉冲提高金属达到塑性,使焊件之间紧密贴 合,反之飞溅;凸焊时这样做可以使多个凸点在通电前与 电极平衡接触,以保证各点加热的一致性。预热电流 I1=0.25-0.5I。 3)加大锻压力,以使熔核致密,防止产生裂纹和缩孔。 Ff0=2-3Fw; 4)用回火或缓冷脉冲消除合金钢的淬火组织,提高接 头的力学性能。缓冷或回火电流I3=0.5-0.7I。回火时间为 1.5-3.0t(焊接时间)
增大到20-25%。
点焊排数一般不多于3
点焊接头形式
三、点焊的焊前清理
清理方法分机械清理和化学清理两种。常用的
机械清理方法有喷砂、喷丸、抛光以及用纱布或 钢丝刷等。 不同材料采用不同清洗方法,参见P25表1-5.
三、点焊的焊接循环 点焊和凸焊的焊接循环由“预压”、“通 电”、“维持”、“休止”4个基本阶段组成。
(2)焊接电流与电 极压力的配合
焊接过程中不产生喷 溅为主要原则。
五、点焊时的分流
影响分流的因素:
(1)焊点距:连续点焊时,点距愈小,板材愈厚,分流愈大; (2)焊接顺序:已焊点分布在两侧时,分流大;
点焊工艺知识培训课件

目 录
• 点焊工艺基础知识 • 点焊工艺参数及选择 • 点焊质量检查与评定 • 点焊工艺优化与改进 • 点焊工艺实例分析 • 点焊工艺培训总结与展望
01
点焊工艺基础知识
点焊的定义和分类
点焊定义
点焊是一种电阻焊方法,通过电极对工件加压并通电,利用电流通过工件时产 生的电阻热将工件局部加热至熔化状态,形成焊点,实现工件的连接。
点焊分类
根据电极形状和加压方式的不同,点焊可分为单边点焊、双边点焊和多点点焊 等。
点焊的特点及应用
点焊特点
生产效率高、焊接质量好、焊接 变形小、适应性强等。
点焊应用
点焊广泛应用于汽车、航空航天 、电子、家电等制造行业,用于 连接各种金属薄板、线材等。
点焊的安全与卫生
焊接烟尘
点焊过程中会产生焊接烟尘,长 期吸入会对人体健康造成危害。 因此,应佩戴防护口罩,定期通 风换气,保持工作场所空气流通
电极压痕
检查电极压痕的深度和分布,压痕过深或分布不 均可能影响焊接质量。
内部质量评定
焊缝强度
通过拉伸试验、弯曲试验等方法检测焊缝的强度,确保满足设计 要求。
气孔与夹杂
采用X射线探伤、超声波探伤等方法检测焊缝内部的气孔、夹杂等 缺陷,确保焊接质量。
微观组织
观察焊缝金相组织,检查是否存在组织不均匀、晶粒粗大等问题, 以评定焊接质量。
未来点焊工艺将更加注重环保、 高效、智能化发展,提高生产效
率和产品质量。
THANKS
感谢观看
电子元器件引脚焊接
通过点焊工艺将电子元器件引脚与电路板进行连接,确保 电路板的导电性能。
散热器焊接
采用点焊工艺将散热器各部件进行连接,确保散热器的散 热效果。
点焊基础知识

点焊基础知识点焊通常分为双面点焊和单面点焊两大类。
双面点焊时,电极由工件的两侧向焊接处馈电。
典型的双面点焊方式是最常用的方式,这时工件的两侧均有电极压痕。
大焊接面积的导电板做下电极,这样可以消除或减轻下面工件的压痕。
常用于装饰性面板的点焊。
同时焊接两个或多个点焊的双面点焊,使用一个变压器而将各电极并联,这时,所有电流通路的阻抗必须基本相等,而且每一焊接部位的表面状态、材料厚度、电极压力都需相同,才能保证通过各个焊点的电流基本一致采用多个变压器的双面多点点焊,这样可以避免c的不足。
点焊简介点焊是一种高速、经济的连接方法。
它适于制造可以采用搭接、接头不要求气密、厚度小于3mm的冲压、轧制的薄板构件。
是把焊件在接头处接触面上的个别点焊接起来。
点焊要求金属要有较好的塑性。
如图1所示,为最简单的应用点焊的例子。
图1 最简单点焊焊接时,先把焊件表面清理干净,再把被焊的板料搭接装配好,压在两柱状铜电极之间,施加压力P压紧,如图2所示。
当通过足够大的电流时,在板的接触处产生大量的电阻热,将中心最热区域的金属很快加热至高塑性或熔化状态,形成一个透镜形的液态熔池。
继续保持压力P,断开电流,金属冷却后,形成了一个焊点。
如图3所示,是一台点焊机的示意图。
图2点焊过程图3点焊机点焊由于焊点间有一定的间距,所以只用于没有密封性要求的薄板搭接结构和金属网、交叉钢筋结构件等的焊接。
如果把柱状电极换成圆盘状电极,电极紧压焊件并转动,焊件在圆盘状电极只间连续送进,再配合脉冲式通电。
就能形成一个连续并重叠的焊点,形成焊缝,这就是缝焊。
它主要用于有密封要求或接头强度要求较高的薄板搭接结构件的焊接,如油箱、水箱等。
点焊方法单面点焊时,电极由工件的同一侧向焊接处馈电,典型的单面点焊方式,单面单点点焊,不形成焊点的电极采用大直径和大接触面以减小电流密度。
无分流的单面双点点焊,此时焊接电流全部流经焊接区。
有分流的单面双点点焊,流经上面工件的电流不经过焊接区,形成风流。
点焊知识

不
缺少产品定义
合
图示中的焊点
格
补充:工艺参数过大或过小导致的质量缺陷&不良现象:
飞溅、过 烧、焊穿 、粘电极 、电极损 耗快。
过烧、 焊穿、 粘电极、 电极损 耗快。
工作 时间 延长。
未焊透。
未焊透。
电极 寿命 降低。
电
电
焊 接
焊 接
预 压
电 极
极 端
极 修
过大(多)
电 流
时 间
时 间
压 力
面 直
1. 生产效率高; 2. 快速; 3. 简单、可靠; 4. 易用于镀层材料; 5. 成本低; 6. 易于自动化;
焊接最大&最小压力取各组平均值{1900}和{3850}
机器人点焊系统:焊枪选择使压力满足所有板组所有焊接压力要求。
与RSW相比较,PSW一般无参数切换,同一套焊接系统只能输出一种焊接压力和焊接 电流;因此,在焊接参数设定时需要对压力和焊接电流进行修正。
焊点分割原则: 1、 PSW焊枪 焊接压力设定矫正:同一把焊钳取所有焊点推荐焊接压力平均值。 2、当同一把焊枪所有焊点推荐的最大的焊接压力和最小的焊接压力的差值大于2000N 需要重新分割焊点,将差别大的焊点分出去;
7 、焊点质量缺陷(8种) 7-1、虚焊:无熔核或熔核尺寸小于规定值。 焊点熔着径参考标准:TS66-0034
分流 脱焊原因:1、电流小(分流)、通电时间短、焊接压力偏大;2、电极头研磨不良、焊 接姿态不垂直板件。3、板件搭接不良,间隙太大。 对策:1、调整焊接参数2.研磨好电极头;3.调整好持枪角度。
2-2、常见的手工点焊焊钳有X型、C型及特制型等,X型、C型结构示意图如下:
X型焊钳主要用来焊接水平或基本处于水平位 置的工件; C型焊钳主要用来焊接垂直或近似垂直位置的 工件;
点焊焊接工艺

点焊焊接工艺1.点焊接头形式及焊前准备1)点焊接头形式点焊时,零件采用的接头形式如图10-30所示,分为单剪搭接接头,双剪搭接接头、带垫片对接接头以及弯边搭接接头等,其中单剪搭接接头应用最广。
根据接头的强度要求及零件、组合件的结构特点,焊点可以采用单排、双排或多排的。
2)搭接边的选用点焊接头的搭接边的大小必须选用适当。
搭接边太大,既增加产品质量,又浪费材料;搭接边太小,则点焊过程中,加热金属被挤向一边,给装配带来困难,同时,还会在点焊过程中产生飞溅。
点焊接头的搭接边最小尺寸A可参考表10-6所列的数据。
弯边搭接接头中,当圆角半径r小于两倍板厚时,尺寸A可按表10-6中的值。
若弯边或型材的圆角半径r大于板厚两倍时,则弯边尺寸A应相应增大。
3) 焊点间距的选用点焊接头的强度取决于焊点数目,而焊点数目又取决于焊点中心间距离,焊点间距小,焊点密,接头强度就高。
但是焊点间距不能太小,因为点距越小,电流分流越严重。
对于铝合金,由于电阻系数小。
分流现象比较严重,则焊点间距应比焊黑色金属时大,若须提高接头强度,自能采用双排或多排焊点,点焊时,焊点间的最小间距如表10-7所列。
4)焊件的焊前清理当焊件表面存在油脂、赃物及氧化膜时,使焊件与焊件、电极与焊件间的接触显著增加,甚至出现局部不导电区。
这样,破坏了电流和热量的正常分布,在电流密度特别大的地方,发生金属局部熔化、飞溅和焊件表面过烧,严重者,将烧穿焊件,从而影响焊件质量,如图10-31所示。
所以在焊接之前,必须除去焊件表面进行清理。
焊前对焊件的清理,首先必须用有机溶剂(如丙酮、汽油等)和碱性溶液除去焊件表面的油漆和油脂,然后再除去金属表面的氧化膜。
清理的方法视不同焊件金属及其表面状态而定。
对于无氧化膜的冷轧结构钢,可用金刚砂布、钢丝直径不大于0.2mm的金属刷或带中等粒度的金刚砂毡轮清理,使接头处两面约20mm宽度上露出金属光泽。
当用金刚砂布清理时,砂布号码不宜过小。
点焊常识——精选推荐

点焊常识点焊基本常识(何⽂章提供)⼀. 点焊及施焊⽅法点焊⼯作原理是根据电流的热效应。
点焊时两个被焊⼯件⾸先在焊钳或焊枪⽓缸的作⽤下通过上下电极压紧,然后通过焊接电流(⼀般在⼏千到⼏万安培 ),根据焦⽿定律Q=0.24I 2Rt,使被焊处⾦属熔化,达到焊接温度后切断电流,在电极的压⼒作⽤下,熔化⾦属冷却结晶形成焊核。
点焊多数⽤于薄板焊接,接头形式多采⽤搭接接头和翻边接头。
点焊的种类很多,我们焊装车间主要有两种。
即:双⾯单点,单⾯双点。
双⾯单点是应⽤最⼴的⼀种点焊形式。
如:悬挂式吊点焊机,座点焊机。
它的特点是⼀次通电只能焊⼀个焊点。
单⾯双点:主要应⽤在⼯件同⾯上,另⼀⾯垫有⼀⼤块导电性能很好的铜导电板(块),焊接变压器⼆次线两端与电极连接,⼯件被压在电极与铜垫块之间。
因此,在装配多点焊机电极块时必须⽤绝缘材料将电极块与电块⽀架分离开。
维修时⼀定要把原有的绝缘垫⽚装上,防⽌在施焊时分流。
单⾯双点(多⽤与专⽤多点焊机) 双⾯单点⼆.点焊的循环每焊⼀个焊点必须经过予压.焊接.维持.休⽌四个过程。
每⼀个过程都持续⼀定的时间,分别为予压时间t压,焊接时间t焊,维持时间t维,和休息时间t休,这四个过程对点焊的质量是不可缺少PI予压:予压时间是指电极开始向⼯件加压到通电开始这段时间。
在这段时间内,电极必须向⼯件加给焊接时所必须的压⼒。
保证被焊⼯件紧密接触,如予压时间太短,没等两⼯件紧密接触时就开始通电,因接触电阻太⼤,点焊时就可能出现烧穿现象。
焊接:焊接时间是指在点焊过程中,电极通过的时间,是焊接过程中的重要环节。
焊接时电流通过电极流经焊件,使焊接处产⽣强烈的电阻热,在热量最集中处的⾦属⾸先熔化,同时熔化的⾦属被周围尚未熔化处与塑性状态的⾦属环所包围,使熔化的⾦属不能外溢。
随着时间的增长,熔核不断扩⼤,焊接时加热的速度是⾮常快的,低碳钢点焊时可以在0.06~0.1秒内使核⼼温度达到1800O C以上超过⾦属熔点200~300度。
- 1、下载文档前请自行甄别文档内容的完整性,平台不提供额外的编辑、内容补充、找答案等附加服务。
- 2、"仅部分预览"的文档,不可在线预览部分如存在完整性等问题,可反馈申请退款(可完整预览的文档不适用该条件!)。
- 3、如文档侵犯您的权益,请联系客服反馈,我们会尽快为您处理(人工客服工作时间:9:00-18:30)。
减少分流
选择合适的点距:为了减小分流,通常按焊件材料的电阻率和厚 度规定点距的最小值。材料的电阻率越小,板厚越大,焊件层数 越多,则分流越大,所允许的最小点距也应增大。
► 增加IW、和tW,都使熔核尺寸和焊透率增大,提高焊点的抗剪强度。如果对这两个工艺 参数进行不同的配合调节,就会得出加热速度快慢不同的两种焊接条件,即强条件(规 范)。
► 强条件是焊接电流大、焊接时间短。其效果是加热速度快、焊接区温度分布陡、加热区窄、 接头表面质量好,过热组织少,接头的综合性能好,生产率高。因此,只要焊机功率允许, 各工艺参数控制精确,均应采用。但由于加热速度快,这就要求加大电极力和散热条件与 之配合,否则易的大部分热量
是从上、下电极传导而散失,被焊板件越 薄,其散失的热量就越多。焊接厚度为 1mm的低碳钢,电极散走的热量约占输入 点总热量的70%-80%。
复合电极
▪ 把钨(钼)棒或钨(钼)片镶嵌于铜合金电极的头部构
成复合电极,可提高电极的导电性,改善钨极的 散热效果。此外,可以防止钨极在焊接时受冲击 而碎裂。
❖ 当焊件厚度较大,(铝合金为1.6-2mm,钢板为5-6mm)时, 因熔核周围金属壳较厚,常需增加锻压力。加大压力的时间须 控制好。过早,会把熔化金属挤出来变成飞溅,过晚,熔化 金属已凝固而失去作用。一般断电后在0-0.2秒内加大锻压力。
点焊电极
是点焊机中重要但又易损耗的零 件,它的材质、结构形状直接影 响焊接质量、生产成本和劳动生 产率,也对自身使用寿命有影响
❖ 低碳钢和低合金钢在大气中耐腐蚀能力弱,在运输、存放和加工过程中 常用抗蚀油保护,若涂油表面未被脏物或其他不良导电材料所污染,在 电极压力下,油膜很容易被挤开,不影响接头质量。对未经酸洗过的热 轧钢板,焊前必须用喷砂、喷丸或用化学腐蚀的方法清除氧化皮。有镀 层的钢板,除少数外,一般不用特殊清理就可以进行焊接。镀铝钢板则 需要用钢丝刷或化学腐蚀清理。
点焊工艺参数—焊接时间
焊接时间是指电流脉冲持续时间,它既影响析热又影 响散热。在规定焊接时间内,焊接区析出的热量除部 分散失外,将逐渐积累,用于加热焊接区使熔核逐渐 扩大到所需的尺寸。所以焊接时间对熔核尺寸的影响 也与焊接电流的影响基本相似,焊接时间增加,熔核 尺寸随之扩大,但过长的焊接时间就会引起焊接区过 热、飞溅和搭边压溃等。通常是按焊件材料的物理性 能、厚度、装配精度、焊机容量、焊前表面状态及对 焊接质量的要求等确定通电时间长短。
点焊工艺参数—电极力
电极力对焊点形成有着双重作用。它既影响焊点的接触电阻, 即影响热源的强度与分布;又影响电极散热的效果和焊接区 塑性变形及核心的致密程度。当其它参数不变时,增大电极 力,则接触电阻减小,散热加强,因而总热量减少,熔核尺 寸减小,特别焊透率降低很快,甚至没焊透;若电极力过小, 则板间接触不良,其接触电阻虽大却不稳定,甚至出现飞溅 和烧穿等缺陷。
分流
焊接时不能过焊接区而流经焊件其它部分的电流为分流。 同一焊件上已焊的焊点对正在焊的焊点就能构成分流;焊 接区外焊件间的接触点也能引起分流,见图7。
不希望产生分流现象。因为,分流使焊接区的有效电流减 小,析热不足而使熔核尺寸减少,导致焊点强度下降;分 流电流在电极-焊件接触面一侧集中过密,将因局部过热 造成飞溅、烧伤焊件或电极、熔核偏斜等;由于形成分流 的偶然因素很多,使得焊接电流不稳定,从而焊接质量也 不稳定。
在通电加热过程中有两种情况可能引起飞溅:一种是开始 时电极预压力过小,熔化核心周围未形成塑性金属环而向 外飞溅;另一种是加热结束时,因加热进间过长,熔化核 心过大,电极压力下,塑性金属环发生崩溃,熔化金属从 焊件之间或焊件表面溢出
点焊三个阶段—锻压
❖ 锻压是在切断焊接电流后,电极继续对焊点挤压的过程,对 焊点起着压实作用。断电后,熔化核心是在封闭的金属“壳” 内开始冷却结晶的,收缩不自由。如果此时没有压力作用, 焊点易出现缩孔和裂纹,影响焊点强度。如果有电极挤压, 产生的挤压变形使熔核收缩自由并变得密实。因此,电极压 力必须在断电后继续维持到熔核金属全部凝固之后才能解除
其它特殊措施:分流对单面双点焊影响较大,见图7 b。对于厚度 相等的焊件,因分路阻抗小于焊接区的总电阻,故分流大于焊接 区通过的电流。为了减小分流,通常在焊件下面衬以导电金属板, 见图8 a,使IW=I1+I2≥I1;对于厚度不同或材料不同的焊件,应尽 量将两电极放在分路电阻较大的一侧,即放在较薄板件或导电性 差的材料的一侧。
▪ 由于用纯钨(钼)作电极的镶嵌件,其尺寸受到
限制而不能做得过大,且电极形式有限。因此, 用得较多的是铜-钨和银-钨粉末烧结材料,可加 工成不同形状和尺寸的电极。这些钨(钼)镶嵌 件或烧结材料均用钎焊焊于电极主体的头部。
点焊工艺—前处理
❖ 当焊件表面有油污、水分、油漆、氧化膜及其它脏物时,使表面接触电 阻急剧增大,且在很大范围内波动,直接影响到焊接质量的稳定。为保 证接头质量稳定,点焊(也包括凸焊)前必须对工件表面进行清理。清 理方法分机械清理和化学清理两种,前者有喷砂、喷丸、刷光、抛光、 磨光等,后者常用的是酸洗或其它化学药品。主要是将金属表面的锈皮、 油污、氧化膜、脏物溶解和剥蚀掉。这两种清理方法一般是根据焊件材 料、供应状态、结构形状与尺寸、生产规模、生产条件及对焊接质量要 求等因素选定。
点焊工艺基础知识
点焊的形成
点焊过程可分为彼此相联的三个 阶段:预加压力、通电加热和锻 压。
点焊的定义
►焊接是两种或两种以上同种或异种材料通过 分子或原子间的结合和扩散而连成一体的工 艺加工过程。
►电阻焊就是将工件置于两个电极之间加压, 通以电流,利用工件的电阻产生热量并形成 局部熔化,或达到塑性状态。断电后,压力 继续作用,形成牢固接头。
焊前清理焊件表面:表面上存在有氧化膜、油垢等脏物时,焊接 区总电阻增大,使分流增大。
提高装配质量:待焊处装配间隙大,其电阻增加,使分流增大。 因此,结构刚性较大或多层板进行组装时,应提高装配质量,尽 量减小装配间隙。
适当增大焊接电流,以补偿分流的影响:由于结构设计需要或其 它原因,分流不可避免时。为了保证熔核具有足够几何尺寸,应 加大焊接电流。以补偿分流的损失。例如,焊接不锈钢与高温合 金连续点焊时,采用比正常点焊的焊接电流高40%-60%。
❖ 不锈钢、高温合金点焊时,需保持焊件表面高度清洁,若有油、尘土、 油漆物存在,有增加硫脆化可能,需用抛光、喷丸或化学腐蚀方法清理。 对重要焊件有时用电解抛光,但其工艺较复杂,生产率低。
点焊工艺参数
点焊的工艺参数主要有焊接电流I、 焊接时间t、电极力F 和电极工作 面尺寸d等。
它们之间密切相关,而且可在相 当大的范围内变化来控制焊点的 质量。
点焊的三个阶段—预压
预加电极压力是为了使焊件在焊接处紧密 接触。若压力不足,则接触电阻过大,导 致焊件烧穿或将电极工作面烧损。因此, 通电前电极力应达到预定值,以保证电极 与焊件、焊件与焊件之间的接触电阻保持 稳定。
点焊三个阶段—通电加热
通电加热是为了供焊件之间形成所需的熔化核心。在预加 电极压力下通电,则在两电极接触表面之间的金属圆柱体 内有最大的电流密度,靠焊件之间的接触电阻和焊件自身 的电阻,产生相当大的热量,温度也很高。尤其是在焊件 之间的接触面处,首先熔化,形成熔化核心。电极与焊件 之间的接触电阻也产生热量,但大部分被水冷的铜合金电 极带走,于是电极与焊件之间接触处的温度远比焊件之间 接触处为低。正常情况下是达不到熔化温度。在圆柱体周 围的金属因电流密度小,温度不高,其中靠近熔化核心的 金属温度较高,达到塑性状态,在压力作用下发生焊接, 形成一个塑性金属环,紧密地包围着熔化核心,不使熔化 金属向外溢出。
各工艺参数之间的关系
► 实际上点焊过程上述各工艺参数间并非孤立变化,常常变动其中一个参数会引起另一个参 数的改变,彼此相互制约。改变焊接电流IW、、焊接时间tW、电极力FW、电极工作面直 径de都会影响散热,而tW和FW与焊点塑性区大小有密切关系。增加IW、和tW,降低FW, 使析热增多,可以增大熔核尺寸,这时若散热不良(de小)就可能发生飞溅、过热等现象; 反之,则熔核尺寸小,甚至出现未焊透。
不同厚度焊接
当材料相同而厚度不等的焊件点焊时, 若用相同尺寸的电极,则由于接合面 与强烈散热的两电极距离不同,使上、 下两焊件散热条件不同,所以其温度 场分布不对称,熔核偏向厚板侧
偏移结果使接合面上熔核尺寸小于核 心最大尺寸,降低了焊点强度,严重 时会造成未焊合。产生熔核偏移现象, 随两焊件厚度比增大而加剧,焊接条 件(规范)越软,其散热作用越强, 偏移也越大。
如何保证强度
提高接触面上的电流密度,增强发热,在薄件或零件上预 制凸点,或在接触面上放工艺垫片,使接触面上电流密度 增大,析热集中于接触面附近,从而使熔核形成在接合面 上。垫片材料、厚度由薄件厚度和材质而定,一般用厚为 0.2-0.3mm的箔片。导热性差而熔点较高的不锈钢箔可用 于焊接铜或铝合金;坡莫合金箔片可用于焊耐热合金。
► 弱条件是焊接电流小而焊接时间长。其效果是加热速度慢、焊接区温度分布平缓、塑性区 宽,在压力作用下易变形。因此,对于焊机功率不足,工件厚度大,变形困难或易淬火的 材料,采用弱条件焊接是有利的。
► 根据不同金属材料或结构对焊接质量的要求,工艺参数的调节是多种多样的。在点焊所有 工艺参数中,焊接电流和通电时间是影响焊接区温度的主要参数,通过改变焊接电流的脉 冲次数、幅值大小和通断时间的长短,就可以在焊接区获得不同温度变化过程,以达到顺 利焊接不同材质和不同厚度的焊件的目的。
电极功能:传输电流、传递压力 和迅速散热
点焊电极功能
a.传输电流:点焊时焊接电流靠电极传输,流 过电极工作面的电流密度很大。
点焊时的电流密度是常用导线电流密度的数十 到数百倍,已超过一般导线所能承受能力。