刀具磨损PPT课件
合集下载
刀具磨损ppt课件

散和粘结磨损共同造成的。
扩散磨损速度主要与切削温度和刀具的化学成分有关系。
所以YT类硬质合金的抗扩散能力优于YG类。采用TiC 和TiN 的涂层刀片,可提高刀具表面的化学稳定性、减少扩散磨 损。
精选ppt课件2021
17
6.2.4 化学磨损(氧化磨损)
在一定得切削温度下,刀具材料与周围介质的某些成分 (如空气中的氧、切削液中的极压添加剂硫、氯等)会起化 学作用,在刀具表面形成一层硬度较低的化合物被切屑带走,
高速钢刀具的这种磨损比较显著,硬质合金刀具相对较少。 各种切削速度下,刀具都存在硬质点磨损,但它是低速切 削刀具磨损的主要原因。
精选ppt课件2021
12
6.2.2 粘结磨损
粘结是指刀具与工件材料在足够大压力和高温作用下,
所产生的“冷焊”现象,是摩擦面的新鲜表面原子间吸附的 结果。两摩擦表面的粘结点因相对运动将被撕裂而被对方 带走,若粘结点的破裂发生在刀具一方,则造成了刀具磨 损。
精选ppt课件2021
4
前刀面的磨损值常以月牙洼的最大深度KT表示(图 6.2(a))
精选ppt课件2021
5
➢ 2.后(刀)面磨损
当切削脆性材料或以较小进给量、较低切削速度切削塑 性材料时,在后刀面毗邻刃口处很快被磨出α0 =0°的小 棱面都将产生后刀面磨损。
精选ppt课件2021
6
后刀面的磨损往往不均匀,通常分为三个区:靠近刀尖部 分的C区、靠近工件外皮处的N区和中间部分的B区。C区由 于强度较低、散热条件较差,磨损较严重,磨损宽度的最大 值以VC表示;N区磨损属于边界磨损,由于工件毛胚表面 硬皮或上道工序加工硬化层等因素的影响,使得磨损加剧, 会产生较大深沟,该区的磨损宽度以VN表示;B区的磨损 比较均匀,常以平均磨损宽度VB表示,有时也用最大磨损 宽度VBmax表示。
扩散磨损速度主要与切削温度和刀具的化学成分有关系。
所以YT类硬质合金的抗扩散能力优于YG类。采用TiC 和TiN 的涂层刀片,可提高刀具表面的化学稳定性、减少扩散磨 损。
精选ppt课件2021
17
6.2.4 化学磨损(氧化磨损)
在一定得切削温度下,刀具材料与周围介质的某些成分 (如空气中的氧、切削液中的极压添加剂硫、氯等)会起化 学作用,在刀具表面形成一层硬度较低的化合物被切屑带走,
高速钢刀具的这种磨损比较显著,硬质合金刀具相对较少。 各种切削速度下,刀具都存在硬质点磨损,但它是低速切 削刀具磨损的主要原因。
精选ppt课件2021
12
6.2.2 粘结磨损
粘结是指刀具与工件材料在足够大压力和高温作用下,
所产生的“冷焊”现象,是摩擦面的新鲜表面原子间吸附的 结果。两摩擦表面的粘结点因相对运动将被撕裂而被对方 带走,若粘结点的破裂发生在刀具一方,则造成了刀具磨 损。
精选ppt课件2021
4
前刀面的磨损值常以月牙洼的最大深度KT表示(图 6.2(a))
精选ppt课件2021
5
➢ 2.后(刀)面磨损
当切削脆性材料或以较小进给量、较低切削速度切削塑 性材料时,在后刀面毗邻刃口处很快被磨出α0 =0°的小 棱面都将产生后刀面磨损。
精选ppt课件2021
6
后刀面的磨损往往不均匀,通常分为三个区:靠近刀尖部 分的C区、靠近工件外皮处的N区和中间部分的B区。C区由 于强度较低、散热条件较差,磨损较严重,磨损宽度的最大 值以VC表示;N区磨损属于边界磨损,由于工件毛胚表面 硬皮或上道工序加工硬化层等因素的影响,使得磨损加剧, 会产生较大深沟,该区的磨损宽度以VN表示;B区的磨损 比较均匀,常以平均磨损宽度VB表示,有时也用最大磨损 宽度VBmax表示。
第六节刀具磨损与刀具寿命课件

氧化磨损
刀具刚投入使用时,磨损速率较快,随着表面粗糙度逐渐降低,磨损速率逐渐减缓。
初期磨损阶段
刀具经过初期磨损后,进入稳定切削阶段,磨损速率保持较低水平。
正常磨损阶段
随着切削过程的进行,刀具表面的微观结构发生变化,磨损速率突然增加,此时应立即停止使用刀具以避免意外损坏。
急剧磨损阶段
CHAPTER
韧性
刀具材料的硬度、抗弯强度、热导率等性能对刀具磨损有重要影响。
刀具的几何角度、断屑槽型、涂层等结构因素对切削过程中的摩擦、切屑形成和排出有直接影响,进而影响刀具磨损。
结构
材料
CHAPTER
03
刀具寿命概念
刀具寿命是指在正常工作条件下,刀具从开始使用到磨损严重需要更换的时间跨度。
刀具寿命受到多种因素的影响,如切削参数、切削材料、刀具材料和几何形状等。
通过及时发现和更换磨损刀具,减少停机时间,提高生产效率。
按照设定的时间间隔,定期拆卸刀具进行检测,了解其磨损情况。
定期检测刀具磨损
离线检测需要对刀具进行精确测量,以确保检测结果的准确性。
精度要求高
离线检测适用于一些无法安装在线监控系统的加工场合。
适用特定场合
根据检测结果,对磨损严重的刀具进行修复或更换,并调整切削参数,延长刀具使用寿命。
清洗作用
CHAPTER
05
刀具磨损检测与监控
实时监测刀具磨损
数据处理与分析
预警与提示
提高生产效率
01
02
03
04
系统通过传感器实时监测刀具的振动、声音、温度等参数,及时发现刀具磨损。
系统对采集的数据进行实时处理和分析,生成刀具磨损趋势图和报警信息。
当刀具磨损达到一定程度时,系统自动发出预警和提示,以便及时更换或修复刀具。
(优秀)机械制造技术课件5刀具磨损与刀具耐用度PPT资料

•
l
氧刀化具磨寿损命、及扩其散磨影损响--因---素-硬质合金刀具
金
磨钝标准:通常指刀具后刀面允许的最大 磨损量。
属
刀具寿命T:刀具开始切削到到达磨钝标准
切 中切削时间。
削
影响刀具寿命的因素:切削用量;工件材
过 程
料;刀具材料及几何角度;其它因素。 切削用量中采用尽可能大的背吃刀量,采
用能满足已加工外表粗糙度要求的尽可能大的进
相对加工性Kr 〉3.0 2.5~3.0 1.6~2.5 1.0~1.6
0.65~1.0 0.5~0.65 0.15~0.5
<0.15
3.3.2 影响切削加工性的因素及其改善措施
影响因素
材料硬度;材料塑性和韧性;材料强度; 适用于切削紫铜、不锈钢等高塑性材料。
〔1〕选用切削性好材料及外表状态好的材料
切屑的折断
金属切削过程中产生的切屑是否易折断,与工件材 料的性能及切屑变形有密切关系。工件材料的强度越 高、延伸率越大、韧性越高,切屑越不易折断。如合 金钢、不锈钢等就较难断屑。而铸铁、铸钢等就较易 断屑。
在前刀面上磨出或压制出卷屑槽,迫使切屑流入 槽内经受卷曲变形。经附加变形后的切屑进一步硬化, 当它再受到弯曲和冲击就很容易被折断。
材 弹性模量E;导热系数;其它因素。 工件材料的强度越高、延伸率越大、韧性越高,切屑越不易折断。
〔3〕选用合理的刀具材料及刀具角度
料 刀具几何参数对断屑的影响
切削速度提高,断屑效果下降。
改善措施 切削用量对刀具寿命的影响程度与切削用量对切削温度θ的影响程度是一致的,切削速度对刀具寿命的影响最大,其次是进给量,背吃 切 刀量的影响很小。 削 〔1〕选用切削性好材料及外表状态好的材 刃倾角为+λs时,切屑流向待加工外表折断
刀具磨损与耐用度课件

深入研究刀具磨损机理和 影响因素,为优化切削参 数和提高加工效率提供理 论支持。
开展多因素耦合作用下的 刀具磨损研究,以更全面 地揭示刀具磨损规律。
ABCD
探索新型刀具材料和涂层 技术,提高刀具的耐磨性 和使用寿命。
加强实际生产中刀具磨损 监测与控制技术的研究与 应用,提高生产效率和加 工质量。
感谢观看
切削参数
切削速度、进给量、背吃刀量等切削参数的 选择对刀具磨损具有重要影响。
刀具材料
刀具材料的硬度、韧性、耐磨性等性能对刀 具磨损有直接影响。
切削材料
不同材料的切削特性不同,对刀具的磨损也 有所不同。
刀具构
刀具的几何形状、角度、断屑槽等结构因素 对刀具磨损也有重要影响。
02
刀具磨损过程
初期磨损阶段
06
结论与展望
研究结论
01
刀具磨损程度与切削参 数、刀具材料和工件材 料等因素密切相关。
02
刀具磨损对切削加工质 量和效率具有显著影响, 需要采取有效措施进行 控制。
03
刀具材料和涂层技术是 提高刀具耐磨性和延长 使用寿命的重要手段。
04
合理的刀具维护和保养 对于保持刀具性能至关 重要。
研究展望
硬质合金、陶瓷等。
优化切削参数
合理调整切削速度、进给量、 背吃刀量等切削参数,以降低 切削力和切削热,减轻刀具磨损。
使用切削液
选用合适的切削液,保持充分 的冷却和润滑,有助于降低刀 具温度,减少磨损。
强化刀具热处理
通过合理的热处理工艺,提高 刀具材料的硬度和抗弯强度,
增强刀具的耐磨性。
04
刀具磨损检测与控制
案例二:切削液对刀具磨损的影响
切削液的种类选择
刀具磨损和刀具耐用度课件
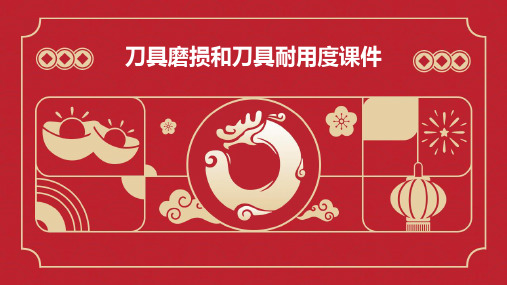
热处理状态
工件材料的不同热处理状 态对刀具磨损也有影响, 如淬火后的工件材料硬度 高,切削时刀具磨损快。
刀具材料
硬度
刀具材料的硬度越高,耐磨性越好, 刀具磨损越慢。
韧性
热处理状态
刀具材料经过适当的热处理后,可以 显著提高其硬度和耐磨性,降低刀具 磨损。
刀具材料的韧性越好,抗冲击性能越 强,刀具磨损越慢。
04 刀具耐用度
CHAPTER
刀具耐用度定义
01
刀具耐用度是指刀具在使用过程 中保持其切削性能和几何形状的 能力,通常以刀具寿命来表示。
02
刀具寿命是指刀具从开始使用到 磨损报废所经过的时间,是衡量 刀具耐用度的重要指标。
刀具耐用度的影响因素
01
02
03
04
切削参数
切削速度、进给量、切削深度 等切削参数对刀具的磨损和耐
使用涂层技术
在刀具表面涂覆耐磨涂层,如TiN、TiCN、Al2O3等,提高刀具的耐 磨性和耐热性,延长刀具使用寿命。
刀具磨损的预防措施
定期检查刀具磨损状况
操作人员应定期检查刀具的切 削刃状况,发现磨损及时更换 或修复。
保持刀具清洁和存放环境 干燥
避免刀具在潮湿或污染的环境 中存放,保持刀具清洁和干燥 ,防止锈蚀和损伤。
VS
详细描述
某机械厂发现其生产的刀具耐用度较低, 频繁更换刀具增加了生产成本。经过研究 ,采取了优化切削参数的方案,包括降低 切削速度、增加切削深度和进给量,同时 选用更合适的刀具材料和涂层。这些措施 显著提高了刀具的耐用度,减少了更换次 数。
案例三:某汽车制造企业刀具管理优化
总结词
建立刀具管理系统,实现高效管理
的磨损。
第六节刀具磨损和刀具寿命课件

第六节刀具磨损和刀具寿命课件
$number {01}
目
• 刀具磨损 • 刀具寿命
01 刀具磨损
刀具磨损的定义
01
刀具磨损:在切削过程中,由于 切削刃与切削材料之间的摩擦, 导致刀具表面的材料逐渐损失或 变薄的现象。
02
刀具磨损不仅会导致切削力增大、 切削温度升高,还会影响工件的 加工精度和表面质量。
优化切削参数,如切削速度、进 给量、切削深度等,以降低切削 力和切削热。
采用合适的冷却液和润滑剂,减 少切削热和摩擦力对刀具的影响。
04
刀具磨损的监测与控制
刀具磨损的监测方法
直接观察法
通过直接观察刀具的切削刃、后刀面 和前刀面磨损情况,判断刀具磨损程 度。
切削力监测法
通过监测切削过程中的切削温度变化, 判断刀具磨损状况。
案例二:某机械厂的刀具寿命管理
总结词
实施刀具寿命管理,提高生产效率
详细描述
某机械厂为了提高生产效率,开始实施刀具寿命管理。通过对刀具的跟踪、监测 和维护,合理安排刀具的更换和修磨,有效延长了刀具的使用寿命,减少了生产 过程中的停机时间,提高了整体生产效率。
案例三:某汽车制造企业的刀具磨损控制
总结词
基于经验的预测方法
根据实际加工经验,结合切削参数和 工件材料等因素,对刀具寿命进行预 测。
数学模型预测方法
实验测试方法
通过实验测试不同条件下的刀具磨损 情况,从而确定刀具寿命。
建立数学模型,通过模拟切削过程和 刀具磨损机理,预测刀具寿命。
03
刀具磨损与刀具寿命的关系
刀具磨损对刀具寿命的影响
刀具磨损程度越高,刀具寿命越短。 刀具磨损会导致切削力增大,影响加工精度和表面质量。 刀具磨损会影响切削热和切削温度的分布,加速刀具的损坏。
$number {01}
目
• 刀具磨损 • 刀具寿命
01 刀具磨损
刀具磨损的定义
01
刀具磨损:在切削过程中,由于 切削刃与切削材料之间的摩擦, 导致刀具表面的材料逐渐损失或 变薄的现象。
02
刀具磨损不仅会导致切削力增大、 切削温度升高,还会影响工件的 加工精度和表面质量。
优化切削参数,如切削速度、进 给量、切削深度等,以降低切削 力和切削热。
采用合适的冷却液和润滑剂,减 少切削热和摩擦力对刀具的影响。
04
刀具磨损的监测与控制
刀具磨损的监测方法
直接观察法
通过直接观察刀具的切削刃、后刀面 和前刀面磨损情况,判断刀具磨损程 度。
切削力监测法
通过监测切削过程中的切削温度变化, 判断刀具磨损状况。
案例二:某机械厂的刀具寿命管理
总结词
实施刀具寿命管理,提高生产效率
详细描述
某机械厂为了提高生产效率,开始实施刀具寿命管理。通过对刀具的跟踪、监测 和维护,合理安排刀具的更换和修磨,有效延长了刀具的使用寿命,减少了生产 过程中的停机时间,提高了整体生产效率。
案例三:某汽车制造企业的刀具磨损控制
总结词
基于经验的预测方法
根据实际加工经验,结合切削参数和 工件材料等因素,对刀具寿命进行预 测。
数学模型预测方法
实验测试方法
通过实验测试不同条件下的刀具磨损 情况,从而确定刀具寿命。
建立数学模型,通过模拟切削过程和 刀具磨损机理,预测刀具寿命。
03
刀具磨损与刀具寿命的关系
刀具磨损对刀具寿命的影响
刀具磨损程度越高,刀具寿命越短。 刀具磨损会导致切削力增大,影响加工精度和表面质量。 刀具磨损会影响切削热和切削温度的分布,加速刀具的损坏。
刀具磨损破损和刀具耐用度课件

03
刀具耐用度
刀具耐用度定义
刀具耐用度是指刀具在使用过程中保持其切削性能和几何形状的能力,即在一定 切削条件下,刀具能够使用的总切削时间或切削长度。
刀具耐用度是衡量刀具质量和使用寿命的重要指标,也是选择和使用刀具的重要 根据。
刀具耐用度影响因素
切削参数
刀具材料
切削速度、进给量、背吃刀量等切削参数 对刀具耐用度有显著影响。
加强操作人员的技能培训,提高操作水平。
加强设备维护保养
定期对设备进行维护保养,确保设备处于良 好状态。
建立刀具管理制度
建立完善的刀具管理制度,规范刀具使用和 管理。
加强生产监控
加强生产过程中的监控和管理,及时发现和 解决生产中的问题。
THANK YOU
感谢各位观看
刀具磨损破损控制策略
优化切削参数
选择合适的切削速度、进给量和切削深度, 减少刀具磨损。
冷却润滑
采用冷却润滑液,减少切削热和摩擦力,降 低刀具磨损。
选用优质刀具材料
选用耐磨性好的刀具材料,提高刀具使用寿 命。
定期更换刀具
根据刀具磨损情况,定期更换刀具,避免过 度磨损。
刀具磨损破损预防措施
提高操作人员技能水平
05
刀具磨损破损的监测与控制
刀具磨损破损监测方法
直接视察法
通过直接视察刀具表面 磨损情况,判断刀具磨
损程度。
振动监测法
通过监测刀具切削过程 中的振动信号,分析刀
具磨损情况。
切削力监测法
通过监测切削过程中的 切削力变化,判断刀具
磨损程度。
切削温度监测法
通过监测切削过程中的 切削温度变化,判断刀
具磨损程度。
刀具材料质量不好是指刀具材料的显微组织不均匀、含 有杂质等缺陷,导致刀具的力学性能降落;刀具设计不 当是指刀具的几何角度、切削刃强度和排屑槽设计等方 面存在缺陷,导致切削力、切削热和切屑处理等方面的 不公道;加工条件不合适是指切削速度、进给量、背吃 刀量等加工条件设置不合适,导致切削力过大、切削温 度过高或切屑处理不良等;操作不规范是指操作者未按 照规定的操作规程进行加工,导致刀具承受过大的切削 力或热量。
第六节 刀具磨损和刀具寿命
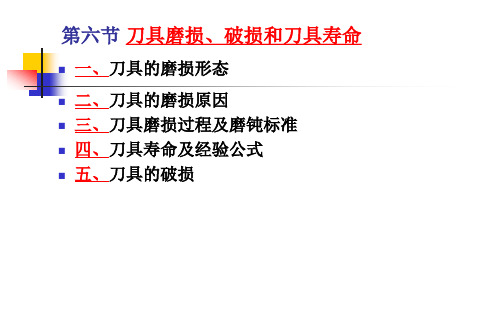
后刀面的磨损带 往往不均匀,可分为:C区、B区、N区。 C区——刀尖部分,(因刀尖部分强度较低,散热条件又差)磨损比较严重,用其最大 值VC表示其磨损程度。
B区——后刀面磨损带中间部位,磨损比较均匀,平均磨损带宽度以 VB表示,而最大磨 损宽度以VBmax表示。 N区——主、副切削刃分别与工件待加工表面和已加工表面接触的地方,通常磨出较深 的沟纹,这个区域的磨损称之为边界磨损(单独介绍)。 后刀面的磨损主要指B区的磨损。 切削铸铁或以较小的切削厚度切削塑性材料时,具磨损原因
刀具磨损不同于一般机械零件的磨损,主要表现为: ① 刀具与切屑、工件间的接触面状态是:刀具表面很洁净,通常表面形成的各种膜已 不存在;切屑和工件表面是活性很高的新鲜表面,不存在氧化膜等的污染。
②刀具与切屑、工件间的接触面上的接触压力很大、接触温度很高。(硬质合金刀, 通常工作温度可达800~1000℃;高速钢刀具,工作温度也可达300~500℃),所以刀具 的正常磨损原因主要是机械、热、化学三种作用的综合结果,表现为:机械磨损(硬质点 磨 损)、粘接磨损、扩散磨损和化学磨损等。 1、硬质点磨损 切削过程中,工件材料中的杂质、材料基体组织中所含的碳、氮化物、氧化物等硬质 点 及积屑瘤碎片等,在刀具表面上划出一条条的沟纹,称为硬质点磨损 在各种切削速度下的刀具都存在硬质点磨损,但它是低速刀具磨损的主要原因。如高 速 钢刀具这种磨损比较明显。 2、粘接磨损 粘接是指刀具与工件材料接触到原子间距离时所产生的结合现象。切削时,刀具与切 屑、工件新鲜表面间实际接触面上,通常存在很大的压力及很高的温度,因而它们之间会形 成冷焊点(粘接),两摩擦表面的粘接点因相对运动将产生破裂。粘接点的破裂通常会发生 在硬度较低的一方即工件材料上,但刀具材料往往有组织不均匀、存在内应力、微裂纹及空 隙、局部软点等缺陷,所以刀具表面也常发生破裂而被工件材料带走,形成了粘接磨损。 粘接磨损一般在中高切削速度下易发生(切削区的温度500~700℃)。
刀具磨损和刀具寿命.ppt
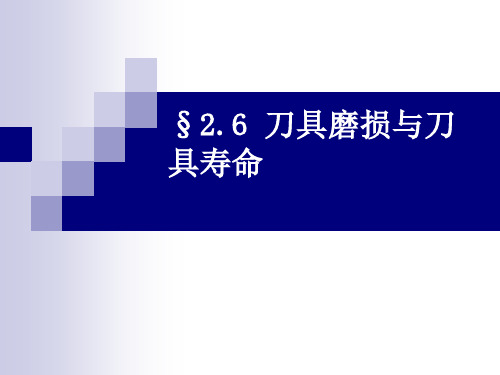
§2.6 刀具磨损与刀 具寿命
一、刀具磨损形态和磨损机制
切削过程中,随着切屑的不断产生和切除,刀具本 身也要逐渐磨损或发生破损(如崩刃、碎断、剥落。裂纹等)。
刀具磨损后,使工件加工精度降低,表面粗糙度增 大,并导致切削力和切削温度升高,甚至产生振动使其不能 继续正常工作。因此刀具磨损直接影响加工效率、加工质量 和成本。
损较均匀,其平均磨损宽度以VB表示。
(3)边界磨损 切削钢料时,常在主切削刃 靠近工件外皮处和副切削刃靠近刀尖处, 磨出较深的沟纹,这种磨损称作边界磨损。 沟纹的位置在主切削刃与工件待加工表面、 副切削刃与已加工表面接触的部位
2. 刀具磨损的原因
由于工件材料、刀具材料种类很多,切削条件变化很大,因此刀具 磨损的形式各不相同,其磨损的原因也很复杂。刀具在正常磨损的情况下, 其主要原因包括:
精加工时磨钝标准取较小值,粗加工时取 较大值;工艺系统刚性差时,磨钝标准取 较小值;切削难加工材料时,磨钝标准也 要取较小值。
三、刀具寿命
1.刀具寿命定义
从刀具刃磨后开始切削,到其磨损量达到刀具磨钝标 准所经过的总切削时间。这实际上也是表示刀具切削性能的一 个指标,或刀具耐磨损性能的表示,以下用符号T表示。
刀具寿命T定得低,切削用量可以取得高,切削效率 是提高了,但换刀次数多,刀具消耗变大,调整刀具 位置费工费时,经济效益也未必好。
在生产中,确定刀具寿命有两种不同的原则,按单件 时间最少的原则确定的刀具寿命叫最高生产率刀具寿 命,按单件工艺成本最低的原则确定的刀具寿命叫最 小成本刀具寿命。
一般情况下,应采用最小成本刀具寿命,在生产任务 紧迫或生产中出现节拍不平衡时,可选用最高生产率 刀具寿命。
制订刀具寿命时,还应具体考虑以下几点:
一、刀具磨损形态和磨损机制
切削过程中,随着切屑的不断产生和切除,刀具本 身也要逐渐磨损或发生破损(如崩刃、碎断、剥落。裂纹等)。
刀具磨损后,使工件加工精度降低,表面粗糙度增 大,并导致切削力和切削温度升高,甚至产生振动使其不能 继续正常工作。因此刀具磨损直接影响加工效率、加工质量 和成本。
损较均匀,其平均磨损宽度以VB表示。
(3)边界磨损 切削钢料时,常在主切削刃 靠近工件外皮处和副切削刃靠近刀尖处, 磨出较深的沟纹,这种磨损称作边界磨损。 沟纹的位置在主切削刃与工件待加工表面、 副切削刃与已加工表面接触的部位
2. 刀具磨损的原因
由于工件材料、刀具材料种类很多,切削条件变化很大,因此刀具 磨损的形式各不相同,其磨损的原因也很复杂。刀具在正常磨损的情况下, 其主要原因包括:
精加工时磨钝标准取较小值,粗加工时取 较大值;工艺系统刚性差时,磨钝标准取 较小值;切削难加工材料时,磨钝标准也 要取较小值。
三、刀具寿命
1.刀具寿命定义
从刀具刃磨后开始切削,到其磨损量达到刀具磨钝标 准所经过的总切削时间。这实际上也是表示刀具切削性能的一 个指标,或刀具耐磨损性能的表示,以下用符号T表示。
刀具寿命T定得低,切削用量可以取得高,切削效率 是提高了,但换刀次数多,刀具消耗变大,调整刀具 位置费工费时,经济效益也未必好。
在生产中,确定刀具寿命有两种不同的原则,按单件 时间最少的原则确定的刀具寿命叫最高生产率刀具寿 命,按单件工艺成本最低的原则确定的刀具寿命叫最 小成本刀具寿命。
一般情况下,应采用最小成本刀具寿命,在生产任务 紧迫或生产中出现节拍不平衡时,可选用最高生产率 刀具寿命。
制订刀具寿命时,还应具体考虑以下几点:
最新第四章-刀具磨损及磨钝标准(机械制造技术A)ppt课件

⑵ 产生后刀面磨损的场合 ① 用较低的切削速度和较小的切削厚度切削塑性 材料; ②切削脆性材料。
(3)影响: 切削力↑, 切削温度↑, 产生振动,降低加工质量
⑶前刀面和后刀面同时磨损
4.1 刀具磨损的形式及原因 刀具磨损原因
1)磨料磨损(硬质点磨损) ⑴ 定义:切屑或工件表面的微小硬质点
与刀具表面的相对运动中,在刀具表面划出 沟痕的磨损称为磨料磨损。
⑴新刃磨的刀具表面粗糙不平,接触应力大; ⑵新刀表面有脱碳层、氧化层等表面缺陷。 2.正常磨损 图中BC段 • 特点:磨损量随切削时间缓慢均匀增大,切削过程稳 定 • 该磨损阶段是刀具的有效工作时间。 3.剧烈磨损 图中CD段 • 特点:刀具材料切削性能急剧下降,磨损迅速。 • 机理: 刀具变钝,摩擦过大,切削力与切削温度迅速增长。
第四章-刀具磨损及磨钝标准(机 械制造技术A)
4.1 刀具磨损的形式及原因
◆ 1.非正常磨损: 例如刀具由于受到外力作用造成崩刃、卷刃、 刀头碎裂,硬质合金刀头由于热应力造成的裂 纹等;
◆ 2.正常磨损的三种形式: ⑴前刀面磨损 ⑵后刀面磨损 ⑶前刀面和后刀面同时磨损
1.前刀面磨损
⑴ 后刀面磨损的特征
⑴ 磨损过程:
空气中的氧与刀具硬质合金中的钴和碳化钨等
发生氧化作用,产生疏松脆弱的氧化物。切削时这 些氧化物被切屑和工件带走,形成刀具的氧化磨损。
⑵ 发生场合:
硬质合金中的碳化钛含量较低时,则氧化较快, 易发生氧化磨损。
5)相变磨损
切削温度超过相变温度时,刀具金相组织发生 变化,使表层的硬度下降造成刀具的相变磨损。
后刀面磨损量VB
刀具磨损曲线
4.2 刀具耐用度及切削量的选择
刀具耐用度标准
相关主题
- 1、下载文档前请自行甄别文档内容的完整性,平台不提供额外的编辑、内容补充、找答案等附加服务。
- 2、"仅部分预览"的文档,不可在线预览部分如存在完整性等问题,可反馈申请退款(可完整预览的文档不适用该条件!)。
- 3、如文档侵犯您的权益,请联系客服反馈,我们会尽快为您处理(人工客服工作时间:9:00-18:30)。
高速钢刀具的这种磨损比较显著,硬质合金刀具相对较少。 各种切削速度下,刀具都存在硬质点磨损,但它是低速切 削刀具磨损的主要原因。
.
12
6.2.2 粘结磨损
粘结是指刀具与工件材料在足够大压力和高温作用下,
所产生的“冷焊”现象,是摩擦面的新鲜表面原子间吸附的 结果。两摩擦表面的粘结点因相对运动将被撕裂而被对方 带走,若粘结点的破裂发生在刀具一方,则造成了刀具磨 损。
.
6
后刀面的磨损往往不均匀,通常分为三个区:靠近刀尖部 分的C区、靠近工件外皮处的N区和中间部分的B区。C区由 于强度较低、散热条件较差,磨损较严重,磨损宽度的最大 值以VC表示;N区磨损属于边界磨损,由于工件毛胚表面 硬皮或上道工序加工硬化层等因素的影响,使得磨损加剧, 会产生较大深沟,该区的磨损宽度以VN表示;B区的磨损 比较均匀,常以平均磨损宽度VB表示,有时也用最大磨损 宽度VBmax表示。
一般来说,粘结点的破裂往往发生在工件或切屑上。
但刀具材料也可能有组织不均,存在内应力、微裂纹、
空穴及局部软点等缺陷,所以刀具材料表面也会发生
被工件材料带走造成的磨损。
各种刀具材料包括立方氮化硼和金刚石刀具都有可能发生 粘结磨损。
切削温度是影响粘结磨损的主要因素。切削温度越高,
粘结磨损越严重。
.
13
图6.4是不同硬质合金与钢的粘结温度曲线。由图可知, YT类硬质合金与钢的粘结温度比YG类高,说明YT类硬质合金
第六章 刀具磨损与刀具使用寿命
6.1 刀具磨损形态 6.2 刀具磨损的原因 6.3 刀具磨损过程与磨钝标准 6.4 刀具使用寿命及与切削用量的关系 6.5 刀具合理使用寿命的制定
.
1
切削过程中,刀具切削部分在前、后刀面上的接触压力 很大,温度很高。同时,还与切屑及加工表面产生强烈的摩 擦,结果使刀具逐渐磨钝,以致失效。
抗粘结性能好于YG类。故切削钢件时宜选用YT类硬质合金。
.
14
6.2.3 扩散磨损
由于切削时处于高温,当两摩擦表面化学元素的浓度相差 较大时,它们就可能在固态下相互扩散到对方去,改变了 刀具材料和工件材料的化学成分,使刀具材料变得脆弱而 造成刀具磨损,这种磨损称为扩散磨损。
例如,当切削温度达800℃以上时,一方面硬质合金中的
所以YT类硬质合金的抗扩散能力优于YG类。采用TiC 和TiN 的涂层刀片,可提高刀具表面的化学稳定性、减少扩散磨 损。
.
17
6.2.4 化学磨损(氧化磨损)
在一定得切削温度下,刀具材料与周围介质的某些成分 (如空气中的氧、切削液中的极压添加剂硫、氯等)会起化 学作用,在刀具表面形成一层硬度较低的化合物被切屑带走,
C、W、Co 等元素扩散到切屑中去而被带走(图6.5),切
屑中的Fe元素扩散到硬质合金表层,形成新的脆性低硬度
复合碳化物;另一方面,硬质合金中的C扩散出去造成贫
碳,使硬度降低,Co的扩散使其含量减小,降低了WC、
TiC等碳化物与基体的粘结强度,这些都使刀具磨损加工加
剧。但TiC 的扩散能力不如WC,高温下反而会在表层生成
加速了刀具的磨损,这种磨损称为化学磨损。 如用金刚石刀具切削黑色金属时,当切削温度高区700℃ 时,刀具表面的碳原子将与空气中的氧发生强烈的化学反 应,生成C0或CO2 气体,加剧了刀具的磨损,这是金刚石 刀具在空气中不能切削黑色金属的一个主要原因。
由于工件材料、刀具材料和切削条件的不同变化很 大,刀具的磨损形态各不相同,磨损原因也复杂得很, 刀具磨损的主要原因分述如下:
.
11
6.2.1 硬质磨损
硬质点磨损(亦称机械磨损或磨料磨损),是由于工件 材料中含有的硬质点(如碳化物、氮化物和氧化物)以及积 屑瘤的碎片等在刀具表面上划出沟纹而造成的磨损。
刀具磨损与一般机械零件的磨损有明显不同:与前刀面 接触的切屑底层是不存在氧化膜或油膜的新鲜表面。因此, 刀具磨损与机械、热和化学作用密切相关。
刀具磨损决定于刀具材料、工件材料的物理力学性能和 切削条件。
.
2
6.1 刀具磨损形态
刀具磨损失效可分为正常磨损和非正常磨损两种。
6.1.1 正常磨损
所谓正常磨损,是指切削过程中刀具前刀面和后刀面在高 温、高压作用下产生的正常磨钝现象。刀具的磨损形态如 图6.1所示。
正常磨损有三种形态:
.
3
➢ 1. 前(刀)面磨损
加工塑性材料时,切削速度 较高,切削厚度较大时,在 高温高压作用下,切屑将在 刀具前刀面上逐渐磨出一个 月牙形凹窝,常被称为月牙 洼磨损(图6.1)。
.
4
前刀面的磨损值常以月牙洼的最大深度KT表示(图 6.2(a))
.
5
➢ 2.后(刀)面磨损
当切削脆性材料或以较小进给量、较低切削速度切削塑 性材料时,在后刀面毗邻刃口处很快被磨出α0 =0°的小 棱面都将产生后刀面磨损。
TiO2保护层而阻碍扩散进行,故高速切钢宜选用YT类硬质 合金。
.ቤተ መጻሕፍቲ ባይዱ
15
.
16
扩散磨损常常和粘结磨损同时产生。硬质合金刀具的前
刀面上月牙洼最深处的温度最高,故该处的扩散速度也高,
磨损快;月牙洼处又容易发生粘结,因此月牙洼磨损是由扩
散和粘结磨损共同造成的。
扩散磨损速度主要与切削温度和刀具的化学成分有关系。
.
9
➢ 1. 塑性破损
塑性破损是指由于高温高压作用而使前、后刀面发生塑 性流动而丧失切削能力。它直接与刀具材料与工件材料的硬 度比值有关,硬度比值越大,越不容易发生塑性破损。
➢ 2. 脆性破损
硬质合金和陶瓷刀具在机械与热冲击作用下,常产生的 崩刃、碎断、剥落、裂纹等均属脆性破损。
.
10
6.2 刀具磨损的原因
.
7
➢ 3.边界磨损 切削钢材时,常在主切
削刃与工件待加工表面或副 切削刃与工件已加工表面接 触处的后刀面上,磨出较深 沟纹,这种磨损沟纹称为边 界磨损。(图6.3)
.
8
6.1.2 非正常磨损(破损)
刀具破损是刀具失效的另一种形式,刀具的破损按性质 可分为塑性破损和脆性破损,据统计,硬质合金刀具约 有50%-60%的损坏是脆性破损。 按时间又可分为早期破损和后期破损。早期破损是切削 刚开始或经短时间切削后即发生的破损脆性大的刀具材 料切削高硬度材料或断续切削时,常出现这种破损。后 期破损是切削一定时间后,刀具材料因交变机械应力和 热应力所致的疲劳损坏。
.
12
6.2.2 粘结磨损
粘结是指刀具与工件材料在足够大压力和高温作用下,
所产生的“冷焊”现象,是摩擦面的新鲜表面原子间吸附的 结果。两摩擦表面的粘结点因相对运动将被撕裂而被对方 带走,若粘结点的破裂发生在刀具一方,则造成了刀具磨 损。
.
6
后刀面的磨损往往不均匀,通常分为三个区:靠近刀尖部 分的C区、靠近工件外皮处的N区和中间部分的B区。C区由 于强度较低、散热条件较差,磨损较严重,磨损宽度的最大 值以VC表示;N区磨损属于边界磨损,由于工件毛胚表面 硬皮或上道工序加工硬化层等因素的影响,使得磨损加剧, 会产生较大深沟,该区的磨损宽度以VN表示;B区的磨损 比较均匀,常以平均磨损宽度VB表示,有时也用最大磨损 宽度VBmax表示。
一般来说,粘结点的破裂往往发生在工件或切屑上。
但刀具材料也可能有组织不均,存在内应力、微裂纹、
空穴及局部软点等缺陷,所以刀具材料表面也会发生
被工件材料带走造成的磨损。
各种刀具材料包括立方氮化硼和金刚石刀具都有可能发生 粘结磨损。
切削温度是影响粘结磨损的主要因素。切削温度越高,
粘结磨损越严重。
.
13
图6.4是不同硬质合金与钢的粘结温度曲线。由图可知, YT类硬质合金与钢的粘结温度比YG类高,说明YT类硬质合金
第六章 刀具磨损与刀具使用寿命
6.1 刀具磨损形态 6.2 刀具磨损的原因 6.3 刀具磨损过程与磨钝标准 6.4 刀具使用寿命及与切削用量的关系 6.5 刀具合理使用寿命的制定
.
1
切削过程中,刀具切削部分在前、后刀面上的接触压力 很大,温度很高。同时,还与切屑及加工表面产生强烈的摩 擦,结果使刀具逐渐磨钝,以致失效。
抗粘结性能好于YG类。故切削钢件时宜选用YT类硬质合金。
.
14
6.2.3 扩散磨损
由于切削时处于高温,当两摩擦表面化学元素的浓度相差 较大时,它们就可能在固态下相互扩散到对方去,改变了 刀具材料和工件材料的化学成分,使刀具材料变得脆弱而 造成刀具磨损,这种磨损称为扩散磨损。
例如,当切削温度达800℃以上时,一方面硬质合金中的
所以YT类硬质合金的抗扩散能力优于YG类。采用TiC 和TiN 的涂层刀片,可提高刀具表面的化学稳定性、减少扩散磨 损。
.
17
6.2.4 化学磨损(氧化磨损)
在一定得切削温度下,刀具材料与周围介质的某些成分 (如空气中的氧、切削液中的极压添加剂硫、氯等)会起化 学作用,在刀具表面形成一层硬度较低的化合物被切屑带走,
C、W、Co 等元素扩散到切屑中去而被带走(图6.5),切
屑中的Fe元素扩散到硬质合金表层,形成新的脆性低硬度
复合碳化物;另一方面,硬质合金中的C扩散出去造成贫
碳,使硬度降低,Co的扩散使其含量减小,降低了WC、
TiC等碳化物与基体的粘结强度,这些都使刀具磨损加工加
剧。但TiC 的扩散能力不如WC,高温下反而会在表层生成
加速了刀具的磨损,这种磨损称为化学磨损。 如用金刚石刀具切削黑色金属时,当切削温度高区700℃ 时,刀具表面的碳原子将与空气中的氧发生强烈的化学反 应,生成C0或CO2 气体,加剧了刀具的磨损,这是金刚石 刀具在空气中不能切削黑色金属的一个主要原因。
由于工件材料、刀具材料和切削条件的不同变化很 大,刀具的磨损形态各不相同,磨损原因也复杂得很, 刀具磨损的主要原因分述如下:
.
11
6.2.1 硬质磨损
硬质点磨损(亦称机械磨损或磨料磨损),是由于工件 材料中含有的硬质点(如碳化物、氮化物和氧化物)以及积 屑瘤的碎片等在刀具表面上划出沟纹而造成的磨损。
刀具磨损与一般机械零件的磨损有明显不同:与前刀面 接触的切屑底层是不存在氧化膜或油膜的新鲜表面。因此, 刀具磨损与机械、热和化学作用密切相关。
刀具磨损决定于刀具材料、工件材料的物理力学性能和 切削条件。
.
2
6.1 刀具磨损形态
刀具磨损失效可分为正常磨损和非正常磨损两种。
6.1.1 正常磨损
所谓正常磨损,是指切削过程中刀具前刀面和后刀面在高 温、高压作用下产生的正常磨钝现象。刀具的磨损形态如 图6.1所示。
正常磨损有三种形态:
.
3
➢ 1. 前(刀)面磨损
加工塑性材料时,切削速度 较高,切削厚度较大时,在 高温高压作用下,切屑将在 刀具前刀面上逐渐磨出一个 月牙形凹窝,常被称为月牙 洼磨损(图6.1)。
.
4
前刀面的磨损值常以月牙洼的最大深度KT表示(图 6.2(a))
.
5
➢ 2.后(刀)面磨损
当切削脆性材料或以较小进给量、较低切削速度切削塑 性材料时,在后刀面毗邻刃口处很快被磨出α0 =0°的小 棱面都将产生后刀面磨损。
TiO2保护层而阻碍扩散进行,故高速切钢宜选用YT类硬质 合金。
.ቤተ መጻሕፍቲ ባይዱ
15
.
16
扩散磨损常常和粘结磨损同时产生。硬质合金刀具的前
刀面上月牙洼最深处的温度最高,故该处的扩散速度也高,
磨损快;月牙洼处又容易发生粘结,因此月牙洼磨损是由扩
散和粘结磨损共同造成的。
扩散磨损速度主要与切削温度和刀具的化学成分有关系。
.
9
➢ 1. 塑性破损
塑性破损是指由于高温高压作用而使前、后刀面发生塑 性流动而丧失切削能力。它直接与刀具材料与工件材料的硬 度比值有关,硬度比值越大,越不容易发生塑性破损。
➢ 2. 脆性破损
硬质合金和陶瓷刀具在机械与热冲击作用下,常产生的 崩刃、碎断、剥落、裂纹等均属脆性破损。
.
10
6.2 刀具磨损的原因
.
7
➢ 3.边界磨损 切削钢材时,常在主切
削刃与工件待加工表面或副 切削刃与工件已加工表面接 触处的后刀面上,磨出较深 沟纹,这种磨损沟纹称为边 界磨损。(图6.3)
.
8
6.1.2 非正常磨损(破损)
刀具破损是刀具失效的另一种形式,刀具的破损按性质 可分为塑性破损和脆性破损,据统计,硬质合金刀具约 有50%-60%的损坏是脆性破损。 按时间又可分为早期破损和后期破损。早期破损是切削 刚开始或经短时间切削后即发生的破损脆性大的刀具材 料切削高硬度材料或断续切削时,常出现这种破损。后 期破损是切削一定时间后,刀具材料因交变机械应力和 热应力所致的疲劳损坏。