QSA品质系统评鉴
QSA质量体系评审

3.最终考查和实验(1.4.1考查和实验?
――包管法度榜样文件中规定的所有项目均美满完成后方可发运产品?
4.顾客要求时,供方是否采取被承认的实验室举措措施?(1.4.10.1,2..1)
6.每台考查、测量和实验用设备是否用特有的标记进行了标识(包含雇员自有设备)?(1.4.11.3)
7.是否按规定的周期在进行精确的情形前提下对每台设备进行了校准(包含雇员自有设备)?(1.4.11.2.b)
8.在从新校准之前,是否记录了量具的状况及实际读数?(1.4.11.2.e)
9.当发明考查、测量或实验设备掉准时,是否在产品和过程方面采取了包含通知顾客等方法在内的恰当方法?(1.4.11.2.f)
――相对过程流程图的关键点?
――零件名称和编号?
――指导书的更换日期?
――目视操纵?
2.职员是否按指导书进行操作/考查?
3.是否相符过程操纵要求?
――是否知足顾客对初始过程才能的要求?(1.4.9.2)
――是否知足顾客对现行过程才能的要求?(1.4.9.3)
――是否查询拜望变差产生的专门缘故并采取恰当的处理方法?(1.4.9.3)
8.假如供方临盆顾客指定为“外不雅项目”的产品:
――在剖断区域内是否有合适的照明?
――是否可获得所有标准辅具?
――标准样件及剖断设备是否进行了足够的保养?
――是否能证实进行外不雅考查的人员是有资格的?(1.4.9.7)
是否有其他质量体系要求须要在现场进行验证?
考查和实验
4.10
问题
审核员看法
结果
1.进货零件和材料及购买的办事(1.4.10.2)
质量体系评定

质量体系评定评定说明和指南目的实质量体系评定(QSA)用以确定体系能否契合QS—9000质量体系要求。
正确运用QSA可以确保一切要求均被说明,并有助于确定QS—9000契合性的部门与人员分歧性。
适用范围QSA可以依据顾客和供方需求,在以下几种状况下运用:——第一方一供方对质量体系停止自我评定,至少运用带(*)和(**)的效果。
——第二方一顾客对供方质量体系停止评定(包括第一层次供方对分供方的评定),应运用一切的效果和子效果。
某些顾客至少会运用标有双星号(**)的效果。
——第三方一由质量体系认证/注册机构用采作为编制审核反省表的输入,至少运用带(*)和(**)的效果。
评定顺序在QS—9000附录A中规则了QSA顺序。
QSA中效果的顺序并不意味着审核的顺序。
评定方法评定方法由三个主要阶段组成:阶段I——质量体系文件审核确定质量手册(包括所要求的支持性文件)是署契合QS—9000的一切要求。
运用QSA的效果0.1文件审核。
阶段Ⅱ——现场审核这一阶段是确定供方现场及外部场所质量体系实施的水平和有效性。
阶段Ⅲ——剖析和报告对上述两阶段的结果停止评审,以确定供方能否契合QS—9000要求。
审核总结的方式审核员/顾客可采用以下两种方法之一对审核做出结论:—引荐/不引荐—计分法每一个要素都可以按顾客的要求选用下述两种方法之一停止评定:—合格/普通不合格/严重不合格;—每个要素可得0~l0分,见〝运用计分法的评定进程〞。
定义严重不合格是指出现下述状况之一:—质量体系缺项或完全不契合QS—9000要求。
假定关于某项要求出现多个普通不合格,而使整集体系无法运转,那么异样视为严重不合格;—任何有能够使不合格产品装运的不合格。
任何能够招致产品或效劳失效或预期的运用功用严重降低的不合格;—审核员依据阅历和判别说明很能够招致质量体系失效或严重降低对产品和进程控制才干的不合格。
普通不合格是指不契合QS—9000要求,但依据阅历和判别不太能够招致出现以下结果的不合格:—质量体系失效;—降低对进程的控制才干;—不合格产品能够被装运。
QS9000QSA质量系统评鉴表(doc 44页)
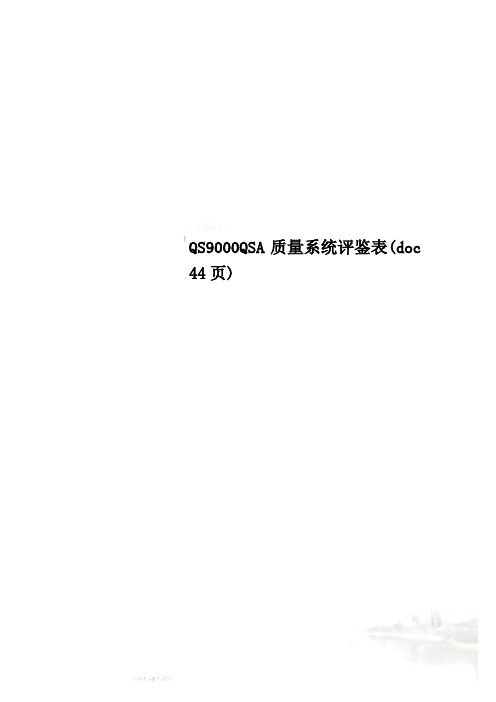
QS9000QSA质量系统评鉴表(doc 44页)QS 9000质量系统评鉴1.6 供货商是否已鉴定资源的需求,提供充分的资源,包括指派训练的人员以从事管理,执行,及验证工作.如:内部质量稽核人员.(4.1.2.2)1.7 是否具备一名职能明确的管理代表,他有权力和责任保证QS-9000的执行,并且对该质量系统的实施成效做出报告?(4.1.2.3)1.8 供货商于概念研发直到生产等阶段,是否建立系统确保对各项活动适当的管理?(4.1.2.4)1.9 供货商是否采用多元化决策模式?(4.1.2.4)问题评审摘记1.10 供货商是否有能力使用顾客规定的格式沟通必要的信息和数据?(4.1.2.4)1.11 当产品或制程无法符合特定要求时,该项信息是否迅即通知负责与授权矫正行动的管理阶层?(4.1.2.5)4.1.3 管理审查1.12**供货商担负经营责任之管理阶层,是否在规定期间审查其质量系统,各要项以确保其持续适切及有效?(4.1.3)4.1.4 经营计划1.13**供货商是否采用一个正式的,明文的,完整的经营计划,并在该计划里提出短期和长期的目标和计划呢?(4.1.4)1.14 该经营计划是否有列为管制文件(4.1.4)1.15 目标和计划拟订是否依据竞争产品的分析,汽车工业内部及外部的标竿,以及供货商自身的商品?(4.1.4)1.16*是否建立衡量目前和未来的顾客期望与需求方法?(4.1.4)1.17 是否采用客观而有效的过程来定义范围及收集信息(包含收集信息的频率与方式)?(4.1.4) 1.18 是否明定追踪,检讨,更新及修订计划的方法,以确保该计划在整体组织中被适当的贯彻与沟通?(4.1.4)4.1.5 公司层级数据分析使用1.19 供货商针对质量,作业绩效(生产的效率,效果)及产品和服务主要特性目前的各种质量水平是否明文记载其趋势?(4.1.5)问题评审摘记1.20**数据和信息的来源是否与以下几个方面相比较:‧竞争者‧适当企业标竿‧与整体经营目标的进度相比较,并转换成据以行动的信息以支持‧顾客相关问题解决方案优先级‧决定与顾客相关的重要趋势(4.1.5)4.1.6 顾客满意度1.21*是否制定一套顾客满意度的书面程序,其中包含测定的频率以及如何确保其客观性和有效性?(4.1.6)1.22 顾客满意的趋势以及顾客不满意的主要指针,是否书面记载且以客观的信息予以证实,并经管理阶层审查?(4.1.6)1.23*当顾客指出QS-9000的任何状态时,供货商是否能在5个工作日之内书面通知认证团体.(4.1.6)有无任何额外的供货商质量系统要求,经证实已在现场实施4.2 质量系统问题评审摘记4.2.2 质量系统程序2.1**质量手册的每一个要项,是否有适当支持的Ⅱ阶程序书?(4.2.2)4.2.3 质量计划2.2**品管计划是否与质量系统的所有其它要求一致,并以适合作业方法的格式将其文书化例如:‧鉴定与取得所有检验及生产/服务之资源‧引导设计与制程可行性研究‧更新质量管理,检验与测试技术‧各适当阶段鉴定其适切的验证‧直接影响质量的生产,安装和服务程序‧管制计划与FMEA的准备‧标准和规格书审查2.3*是否有证据显示已执行先期产品质量规划程序?(4.2.3.1,4.2.3.2)2.4 供货商是否召集内部的跨功能小组,以从事新产品或变产品的生产,且该小组采用规定在先期产品质量规划和管制计划参考手册的各种适当的技术?(4.2.3.1)2.5 当顾客有要求时,各项制程管制指导书及类似的文件是否使用顾客指定的管制特性符号以指明那些制程步骤会影响到管制特性?(4.2.3.2)2.6**是否在签订合约以生产产品之前,对规划的产品探讨及确认制造的可行性?(4.2.3.3)2.7 供货商的设计管制及制程管制其政策与实务是否考虑关注产品的安全性?(4.2.3.4)问题评审摘记2.8*供货商是否在内部推广对其产品安全性考虑的认知?(4.2.3.4)2.9*制程的失效模式与效应分析是否考虑所有的管制特性?(4.2.3.5)2.10 是否致力于改善制程,以做到预防不良甚于找出不良?(4.2.3.5)2.11**是否于制程,设施,仪器,工模具及间题解决过程中,使用适当的错误防止方法论?(4.2.3.6)2.12*是否对所供应产品的系统,子系统,组件及物料等各层次适当地制定管制计划?(4.2.3.7)2.13*管制计划是否包含QS-9000附录J管制计划表格内的所有信息?(4.2.3.7)2.14*管制计划是否包含三个阶段:原型样品和量产前和量产作为客户的要求(4.2.3.7)2.15**当下列任何一项情况开发生时,管制计划是否进行检讨更新:产品或制程变更时,制程不稳定或能力不足时,检验方法或频率等被变更(4.2.3.7)4.2.4 PPAP产品核准程序2.16*供货商是否完全符合PPAP手册里规定的所有要求?(4.2.4.1)2.17*供货商是否对分包商导入单一零件核准程序?(4.2.4.2)2.18*供货商是否负责验证工程变更被适当的确认?(4.2.4.3)4.2.5 持续改善2.19**是否有证据显示为所有顾客持续不断地改善质量,服务及价格?(4.2.5.1)2.20 持续改善是否拓展至那些管制特性中具较高优先的产品特性?(4.2.5.1)2.21 制程显示相当稳定且制程能力合乎要求时,供货商是否研拟具体优先的持续改善计划?(4.2.5.1)2.22*供货商是否明确定出对质量和生产力改进的机会,并执行适当的改进计划?(4.2.5.2)2.23 供货商是否展示具有衡量和方法论的知识,并加以适当应用之?(4.2.5.3)4.2.6 设施与工模具管理2.24 是否采用跨功能小组并结合先期产品质量流程的做法,以制定制程,设施及设备计划?(4.2.6.1) 2.25**工厂布置是否将物料程和流程及搬运程减到最小,以促进同步的物料流程,且将工厂空间的使用附加价值提升到最大?(4.2.6.1)2.26 是否制定和评估目前作业和制程有效性的方法,并考虑下列因素:总体工作计划,适当的自动化,人体工学和人性因素,作业量和生产线的平衡,储存和库存量的多寡及增加工作内容?(4.2.6.1)2.27*供货商是否制订和执行一套工具管理的制度内容包括:保养和修理的设施和人员,储存和修复,设定条件,及损耗件工具有汰换计划,工模具修改包括工模具设计文件?(4.2.6.2)2.28 是否具备适当的技术资源,以从事工模具和量具之设计,制造和全盘的尺寸检查?(4.2.6.2)2.29*如果工模具的这方面工作系属外包者,是否有一套追踪和跟催这些工作的系统?(4.2.6.2)有无任何额外的供货商质量系统要求,经证实已在现场实施4.3 合约审查问题评审摘记4.3.2 审查3.1 供货商是否有审查标单?合约或订单以确保这些要求是被理解和接受的,且任何不清楚或相异的要求均已获得解决了?(4.3.2)3.2*客户特殊的合约要求,包括QS9000第二节涉及功能和充分达成?(4.3.2)4.3.3 合约变更3.3*有无明定合约变更及传达组织相关功能部内之方式?(4.3.3)4.3.4 记录3.4**合约审查的记录是否被保存?(4.3.4)有无任何额外的供货商质量系统要求,经证实已在现场实施4.4 设计管制问题评审摘记4.4.1 概述4.1 是否有一套流程将先前设计项目所获得的信息展开至目前或未来类似性质的项目?(4.4.1.1)4.4.2 设计与开发规划4.2*是否对每一项设计与开发活动拟订计划,并界定其执行责任?(4.4.2)4.3 计划是否随设计的进展加以更新?(4.4.2)4.4*设计开发各项作业人员是否具备所需技能并提供适切的资源?(4.4.3)4.4.3 组织与技术之联系接口4.5 设计过程中提供输入的不同群组间其组织与技术的接口是否予以界定,并将必要的信息书面化,互相传递与定期检讨?(4.4.3)4.4.4 设计输入4.6*供货商是否鉴定,书面记载与产品有关的各项设计输入需求,含适用法规要求,并审核其选用的适切性?(4.4.4)4.7 凡不完备,混淆不清或相互扺触之需求事项是否与提出需求者共同加以解决?(4.4.4)4.8**如果顾客不声明免除的话,是否具备:‧适当的资源和设施,以利用计算机辅助产品设计,工程和分析‧如果这些工作由分包商承担时,应提供技术指导.‧C AD/CAE系统应能跟顾客的计算机系统做变向沟通(4.4.4.1)4.4.5 设计输出问题评审摘记4.9*设计输出是否予以书面化,且其表达方式能相衬设计输入的需求予以验证及确认:‧符合设计输入需求‧包含或引述对应之允收标准‧鉴定那些对产品安全与适当功能的重要设计特性‧设计输出文件在分发前应经审查(4.4.5)4.10*设计输出是否包括下列过程的结果:‧致力于简化,最佳化,创新及减少浪费‧适当的采用几何尺寸和公差技术‧成本/性能/风险的权衡分析‧从测试,生产及市场回馈信息的应用‧设计失效模式与效应分析的应用(4.4.5) 4.4.6 设计审查4.11**是否于设的适当阶段中规划,举行正式的设计结果的审查并将书面记载?(4.4.6)4.4.7 设计验证4.12 是否在设计的适当阶段实施验证.以确保设计各阶段的输出符合设计输入的要求,并予以记录?(4.4.7)4.4.8 设计验收4.13 是否执行设计验收以确保产品符合界定的使用者需求或要求?(4.4.8)4.14*设计验收的执行是否配合顾客项目计划的时程要求?(4.4.8.1)4.15 设计失败的情形是否书写于设计验收记录中?(4.4.8.1)4.16*针对设计失败是否有程序追踪其矫正与预防措施?(4.4.8.1)4.4.9 设计变更4.17*所有设计变更和修改是否在实施以前.均予以鉴定,书面化,并经权责人员审查与核准?(4.4.9)问题评审摘记4.18*在量产实施前设阗变更是否获得顾客书面的核准或同意免除此项要求?(4.4.9.1)4.19 对于具有专利权的设计,设计变更对于外形,装配,性能,功能及耐久性的影响,是否与客户共同商议,以便适当评估变更的影响程度?(4.4.9.1)4.20*供货商是否考虑设计变更对使用该产品的系统之影响?(4.4.9.2)4.4.10 顾客原型样品维持4.21**当顾客要求时,供货商是否有一个完整的原型样品计划?(4.4.9.2)4.22 供货商是否尽可能采用与将来量产相同的分包商,工模具及制程.(4.4.10)4.23**性能测试是否考虑及包括适当的产品寿命,可靠度与耐久性,并追踪所有性能试验的各项活动,以监督试验是否及时完成?(4.4.10)4.24 如果性能测试外包时,供货商是否提供技术指导?(4.4.10)4.1.11 保密性4.25 供货商与顾客合约发展中的产品及其相关产品信息是否确保机密性?有无任何额外的供货商质量系统要求,经证实已在现场实施4.5 文件及数据管制问题评审摘记4.5.1 概述5.1 外来的原始的文件是否列入文件管制?4.5.2 文件及数据核发5.2**文件与资料在分发之前是否经权责人员审查及核准其适切性?(4.5.2)5.3**是否建立文件总览表或相当的文件管制程序,以鉴别文件最新版次,且该总览表或程序书易于取得?(4.5.2)5.4*供货商是否建立程序以保证对质量系统运作极为重要场所均具有适切版本的适当文件?(4.5.2.a)5.5 供货商是否建立一种程序来保证无效的和/或废弃的文件能迅速地从分发或使用地点撤除,或其它确保避免误用的方式?(4.5.2.b)5.6 无效的文件因法律和/或知识保留目的而保留下来的是否能得到适当的鉴别?(4.5.1.c) 5.7*关于顾客工程的规格/标准和变更是否有及时的审查,分发和执行?(4.5.2.1)5.8*供货商是否保存一份记载每次生产变更生效日期的记录?(4.5.2.1)5.9 实施该变更作业程序时是否包含所有相关文件之更新?(4.5.2.1)4.5.3 文件及数据变更5.10 文件和数据的变化是否由原始审查文件数据的组织或部门来审查(除非别外指定)?5.11 指定的部门或组织是否可以获得相当的背景数据,并据此来审查与核准?(4.5.3)5.12 文件中的所有变更是否能在文件或其附件中加以识别?(4.5.3)有无任何额外的供货商质量系统要求,经证实已在现场实施4.6 采购问题评审摘记4.6.1 概述6.1 如果有顾客核准的外包商的名单,供货商是否从这份名单所列之外包采购相关的物料?(4.6.1.1)6.2 所有用于零组件制造的物料,凡涉及管制性,危险性,有毒性的物料,是否符合目前政府和安全法规的规定?(4.6.1.2)4.6.2 分包商评估6.3**外包商的评估和远择是否基于对质量系统和质量保证的要求能力而定?(4.6.2.a)6.4**供货商是否明定对外包商管制方式与程度?(4.6.2.b)6.5**是否建立和维持了对可接受的外包商的质量记录?(4.6.2.c)6.6*为了使外包商符合QS-9000,是否以QS-9000的第一节部分作为基本的质量保证系统要求来指导外包商质量保证系统的发展?(4.6.2.1)6.7**是否对外包商也要求100%如期交货绩效?(4.6.2.2)6.8*供销商是否能提供适当规划信息和采购承诺使外包商能达到100%交货的要求?(4.6.2.2)6.9*是否执行一项系统藉以监测外包商的交货绩效,及实行必要的矫正行动(包括追踪额外费用或过多运费)?(4.6.2.2)4.6.3 采购数据6.10*采购文件包含之资料是否能明确说明所订购产品之要求?(4.6.3)6.11 采购文件及资料在发出前,是否经权责人员审查及核准其适切性?(4.6.3)问题评审摘记4.6.4 采购产品之验证6.12 供货商要在分包商处验证所采购的产品时,是否在采购文件上明定验证安排及产品放行方式?(4.b.4.1)6.13 有无明定合约,有要求顾客或其代表有权在外包商或供货商处,验证外包商所提供的产品是否符合规定要求之权利?(4.6.4.2)有无任何额外的供货商质量系统要求,经证实已在现场实施4.7 客户供应品之管制问题评审摘记7.1 客户供应品若有遗失,损坏或不适用时,是否予以记录,并通告给顾客?(4.7)4.7.1 客户提供工模具7.2*顾客的工具和设备是否赋予永久性标记,以便其所有权一目了然?(4.7.1)有无任何额外的供货商质量系统要求,经证实已在现场实施4.8 产品之鉴别与追溯性问题评审摘记8.1*产品的识别是否贯彻从生产,交货到安装的每一个阶段?(4.8)8.2**当顾客有所求时,是否维持和记录追溯性?(4.8)有无任何额外的供货商,质量系统要求经证实已在现场实施4.9 制程管制问题评审摘记9.1*是否以书面程序界定生产,安装与服务的诸方式,缺乏此等程序书将对质量造成不利影响?(4.9.a)9.2**是否使用适当的生产,安装与服务设备,及适宜的工作环境,并维持与修护作业场所的整齐与清洁?(4.9.b,4.9.b.1)9.3*供货商是否准备各项紧急应变计划,以在紧急状况下合理保护产品对顾客之供应?(4.9.b.2)9.4 是否符合所参照的标准/法规,质量计划或书面程序?(4.9.c)9.5*是否对合适的制程参数与产品特性,加以监控与管制?(4.9.d)包括管制特性的确定与文件化(4.9.d.1)9.6 是否在适当时对于各项制程及设备加以核准?(4.9.e)9.7 工作技艺准则是否以最清楚实用之方式予以规定?(4.9.f)9.8 是否适当地维护设备,以确保制程的持续能力?(4.9.g)9.9**是否鉴别主要的制程设备,并且提供适切的资源以维护这些设备,同时制订一套有效的,规划的全面预防保养制度,该项制度至少包括:‧一套描述计划性保养作业的程序书‧定期的保养活动‧预测保养的方法‧一项提供设备,工模具与治具的包装及防护的程序‧主要制程设备的替换零件的维持‧记载,评估与改善预防保养的目标(4.9.g.1)问题评审摘记9.10*凡制程其结果无法以后续的产品检验或测试完全验证时,此等制程是否由合格操作人员操作且要求持续地监测与管制制程参数?(4.9)9.11 对于已认可之特殊制程,设备及人员的记录是否适当的维持?(4.9)4.9.1 制程监测与作业员指导书9.12**供货商是否为所有负责制程操作的员工准备书面的制程监测和作业指导书,这些指导书面须取材自先期产品质量规划与管制计划参考手册所列之资料,且在工作场所容易取得?(4.9.1)有无任何额外的供货商质量系统要求,经证实已在现场实施问题评审摘记9.13**制程监测和作业指导书是否适当包括或参考以下内容:‧制程流程图主要的作业名称和编号‧零组件名称和编号‧目前的工程等级(版次)/日期‧所需的工具,量具和其它设备?‧材料识别和处置指导书‧顾客指定和供货商设定的管制特性‧统计制程管制的要求‧相关的工程和制造标准‧检验和测试指导书‧异常处置计划‧文件版次和核准‧目视检查辅助工具更换周期及作业设定的指导(4.9.1)4.9.2 制程管制维持9.14**是否维持或超越PPAP所核准制程力或绩效,供货商必须确保管制计划与制造流程图被执行,严守规定的量测技术,抽样计划及当不合准则发生时的异常处置计划?(4.9.2)9.15**重要的制程事件是否摘记于管制图上?(4.9.2)9.16*管制计划所指定的管制特性呈现不稳定或能力不足时,供货商是否依据管制计划提出适当的反应行动?(4.9.2)9.17*矫正行动计划是否包含:‧制程不良的遏止及100%全检‧矫正行动具体的时间‧指派权责人员‧客户核准?(4.9.2)问题评审摘记4.9.3 制程管制需求设定9.18 当顾客要求较高或较低的制程能力或绩效要求,管制计划是不适切地诠释?(4.9.3)4.9.4 作业条件设定验证9.19*作业条件设定验证当适用时,是否使用统计技术方法之验证(4.9.4)4.9.5 制程变更9.20*供货商是否维持制程变更生效日期之记录?(4.9.5)4.9.6 外观项目9.21*当顾客认定属于外观项目时,是否提供:․产品评价区域有合适的照明․颜色,纹理及织物结构有适当的比对标准件․外观比对标准件和评价设备的维护保养․验证从事外观评价作业人员的资格(4.9.b)有无何额外的供货商质量系统要求,经证实已在现场实施4.10 检验与测试问题评审摘记4.10.1 概述10.1*计数值数据的允收准则为零缺点,供货商是否以书面适当的规定,并取得顾客核准?(4.10.1.1)4.10.2 进料检验与测试10.2*供货商是否确保产品在未检验或验证与质量量计划和/或书面程序中规定的要求相符之前,不致被使用或加工(除非为紧急的生产需要)?(4.10.2.1)10.3 于决定接收检验之程度与性质时,是否考虑在分包商处所施行管制程度及已往品管合格记录之证据(4.10.2.2)10.4**为紧急生产目的而在未经验证前先放行之产品是否明确地加以标识与记录?(4.10.2.3)10.5*供货商的质量系统应采用下列一项或多项的方法:․供货商取得并评估统计数据?․进料检验或测试?․在分包商处所执行的第二者或第三者,评鉴或稽核,且记录显示可被接受的品质绩效․要由认证合格实验室实施零组件评估(4.10.2.4)4.10.3 制程检验与测试10.6*供货商是否按照质量计划(管制计划)和/或书面程序规定的要求对产品进行检验与测试?(4.10.3a)10.7**产品是否直到所需检验与测试皆完成,或所需报告已接到并验证,除非产品系依能被明确召回程序的规范下所放行(4.10.3.b)问题评审摘记10.8 所用制程活动是否采用譬如:统计制程管制,防误措施,目视管理等直接导向缺点预防的方法,而非缺点的检查?(4.10.3a)4.10.4 最终检验与测试10.9**供货商是否依据质量计划(管制计划)和/或书面程序要求来执行最终的检验及测试?(4.10.4)10.10 最终检验与测试之质量计划或书面程序是否要求所有规定的检验与测试(包括接收制程中)均已实施且其结果符合规定的要求?(4.10.4)10.11**产品是否在质量计划或书面程序所规定之各项工作未圆满完成及相关数据与文件核准之前,不得进行分发?(4.10.4)10.12*是否按照顾客规定的频率对所有产品实施全盘尺寸检验及机功测试,且顾客有要求时,检查结果应提供顾客审查?(4.10.4.1) 10.13*供货商是否对已包装的产品每隔适当的期间导入稽核,以验证符合所有规定的要求?(4.10.4.2)4.10.5 检验与测试记录10.14*供货商是否建立并保存记录,以证明产品已经被检验或测试,且记录应请楚显示产品检验或测试已按既定之允收标准通过或不通过?(4.10.5)10.15 产品未通过任何检验与测试时,是否按不合格产品管制程序处理?(4.10.5)4.10.6 供货商实验室需求10.16*实验室是否制定范围,并将其政策,系统方案,程序,说明指导与结果予以书面化,以促使实验室能确保其范围内所产生的测试或校正的质量?(4.10.6.1)问题评审摘记10.17 实验室的人员是否具备适当的背景与经验?(4.10.b.2)10.18*实验室被测产品或校正仪器等物品是否在实验室被保存到最终数据完成为止,以让最终数据可追溯到原始数据?(4.10.b.3)10.19*实验室测试与校正的方法是否符合顾客的要求,并恰当的执行所需的测试校正?(4.10.6.5)10.20 当验证活动的结果为数据时,是否采用适当的统计技术?(4.10.6.6)4.10.7 认证合格实验室10.21**供货商是否使用经验证的商业/独立实验设施?(4.10.7)4.11 检验、量测与测试设备之管制问题评审摘记4.11.1 概述11.1 检验,量测与试验设备在使用时,是否确保量测之不确定度已知且与所需的量测能力相符?(4.11.1)11.2 当使用测试软件或比对参考之测试硬件作为适当检验手段时,在生产,安装或服务使用前,是否予以检核,以证明其验证产品允收性的能力?(4.11.1)11.3*供货商是否规定复核的范围和频度,并保存记录以作为管制的证据?(4.11.1) 11.4 当量测设备之技术资料为规定要求时,若顾客或其代表要求此等资料以验证设备的功能是否适切时,供货商是否可提供?(4.11.1)4.11.2 管制程序11.5 供货商是否决定所需的量测工作及其准确度的要求?(4.11.2a)11.6*是否选择所需准确度与精密度之适当检验,量测与试验设备?(4.11.2a)11.7*供货商是否鉴定所有影响产品品管的检验,量测与试验设备?(4.11.2b)11.8**每件设备是否按规定期间或在使用之前予以校正,此项作业应比对经认可的设备且其与国际或国家承认之标准有明确关系,并被置于正确的环境条件?(4.11.2b)11.9 检验量测和试验设备的校正执行是否委由合格实验室(见QS-9000,4.11.2.6.1)或顾客承认的政府机构?(4.11.2b.1)问题评审摘记11.10**是否界定检验,量测与试验设备的校正作业程序包含:‧设备型式‧特定识别‧位置‧检核频率‧检核方法‧允收准则‧矫正措施(4.11.2c)11.11 是否以适当之标识或已核可之鉴定记录来鉴别检验,量测与试验设备,以显示其校正状况?(4.11.2d)11.12 供货商是否维持检验,量测与试验设备之校正记录?(4.11.2e)11.13 当发现检验,量测与试验设备校正失效时,是否评估并记载先前检验与测试结果的有效性?(4.11.2f)11.14 供货商是否确保检验,量测与试验设备在适合的环境条件下实施校正?(4.11.2g) 11.15**供货商是否确保检验,量测与试验设备于搬运,储存与保管均可维持其准确度与适用性?(4.1.2h)11.16*供货商是否有防护检验,量测与试验设备之设施,包含测试用之硬件与软件,免于不当之调整而使原校正之设定失效?(4.11.2I)4.11.3 检验、量测与测试设备记录11.17*所有的检验,量测与试验设备包含员工自有的量具其校正/验证记录,是否包括:‧根据工程变更所修正(如果发生时)‧校正时,发现读值超出规格‧校正完毕符合规格的结论‧可疑的物料可能已被出货,应通知顾客(4.11.3)问题评审摘记4.11.4 量测系统分析11.18**管制计划里所列的每一种型式的量测系统是否实施适当的统计研究藉以分析各种量测及试验设备系统测量结果的变异?(4.11.4)有无任何额外的供货商质量系统要求,经证实已在现场实施12.1*产品检验与测试之状况,是否使用适当的方法鉴别,藉以显示该产品在实施检验与测试后是否合格?(4.12)11.18**产品自生产,安装与服务整个过程中的检验与测试状况之识别,是否依品管计划或书面程序之规定善加维持?(4.12)4.12.1 额外查证12.3 当客户有所要求时,是否对产品进行额外的查证/标识要求?(4.12.1)有无任何额外的供货商质量系统要求,经证实已在现场实施。
QSA质量评估系统标准THD

4
4
建立一套管理业务变更 的正式体系,包括就流 程、模具。设备、材料 A17 或任何分包商表更通知 客户。在变更实施前要 求获得客户批准 (CCP)
4: 工厂有完整的ECN过程,包括客户通知和批准。相关记录可提供; 3:工厂没有有完整的ECN过程,但是在变更实施前通知了客户并得到批准。相关记录可提供; 2: 工厂有完整的ECN过程,但是发现有客户在变更实施前未对变更未进行审核和批准的个别情况; 1: 工厂没有有完整的ECN过程,同时多数变更在变更实施前未由客户审核和批准。 0: Factory does not have a ECN process; does not have ECN records.
主管 当责人
责任人
协助人 员
工作时 数
开始日 期
完成日 每日完成 期 进度
质量目标和责任在公司 内部清晰表述、广泛传 A01 ############################################################################################### 达、计量且公司员工能 够理解
3
4
总分 第2部分:持续改善 要求 审核员指南
15
0
16
4:工厂已制定可测量且充分的质量度量标准以推动和维持质量改善,同时明确了负责部门和计算方法。工厂根据程 序进行度量并将结果传达给相关员工(比如公共区域的测量) 3: 工厂已制定可测量且充分的质量度量标准以推动和维持质量改善,同时明确了负责部门和计算方法。工厂根据程 已建立相关体系推动和 A05 序进行度量,但是未将结果传达给相关员工(比如公共区域的测量); 维持质量改善 2: 工厂已制定可测量且充分的质量度量标准,但是没有明确负责部门和计算方法;只是根据程序进行了简单度量。 1: 工厂建立了质量标准,但是没有进行测量。 0: Factory does not set up quality metrics in system for measurement. 4: 工厂制定了测量生产能力的标准(比如合格率、废品率);按要求程序对生产能力进行了测量。工厂启动持续改 善活动以提高生产力。工厂对持续改善活动进行了恰当记录。 3: 工厂制定了测量生产能力的标准(比如合格率、废品率);按要求程序对生产能力进行了测量。工厂启动持续改 提供和利用推动生产力 A06 改善的工具、资源和管 善活动以提高生产力。但是没有恰当记录持续改善活动。 2: 工厂制定了测量生产能力的标准(比如合格率、废品率);按要求程序对生产能力进行了但是测量。工厂没有启 理支持 动持续改善活动以提高生产力。 1: 工厂没有按程序测量生产效率。 0: Factory does not set up productivity metrics in system. 4: 工厂测量生产周期,制定了切合实际的缩短生产周期F计划,实施了计划并进行了相关记录; 3: 工厂测量生产周期,制定了切合实际的缩短生产周期F计划,但是没有遵守成文的计划; 制定切实计划以缩短产 A07 2: 工厂测量生产周期,制定了缩短生产周期F计划,但是计划不可行 品生产交货周期 1: 工厂测量生产周期,但是没有制定缩短生产周期F计划 0: Factory does not measure production lead time.
供应商体系评估报告(QSA) (2)
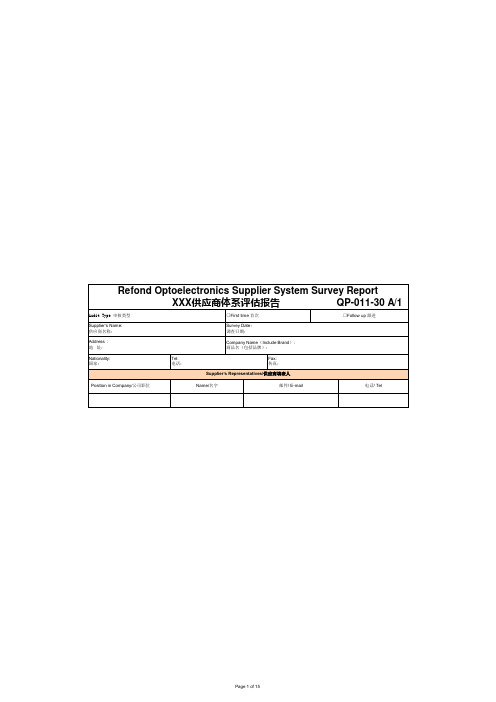
Quality Systems/质量体系部
Grading standards 等级标准
General Comment 总评
91% ~ 100%
□ EXCELLENT / 优秀 Quality system is in place and capable to produce Refond product to spedfications. 品质体系较完善且有能力生产Refond的产品.
□ YES
Who is in charge of the QA supervisor(List out the person’s position) 2 品保部主管属于谁管(列出此人的职位)
List out the following number of staffs who are under the QA in charge:
Assessed Item/Procedure is included. Planning and execution MEETS requirements. 3 品质体系包含了调查的项目/程序, 计划和实施均符合要求。
Assessed Item/Procedure is included. Planning and execution is thorough and OUTSTANDING. 4 品质体系包含了调查的项目/程序,且计划和实施均都执行得非常好。
Address : 地 址:
Company Name(Include Brand): 商品名(包括品牌):
Nationality: 国家:
Tel: 电话:
Fax: 传真:
Supplier’s Representatives/供应商填表人
Position in Company/公司职位
新供应商评鉴表--QSA

Global Brands Manufacture Ltd.
可获得分 数 0.5 0.5 0.5 0.5 0.5 0.5 1 0.5 可获得总分 得分率 0.00% 4.5 0 无概念 无执行 需改善 已执行 已标准化 NO. Description 1 2 3 4 5 SCORE退回管理
15.1 有无客诉处理的相关程序?有无对各客户抱怨&RMA品做统计? 15.2 是否定义客诉回复时效?有没有系统性的效果确认? 15.3 针对客诉的产品是否能被追溯?是否进行分析,并提出预防对策(临时对策及 永久对策)?
比重因素
15.4 是否有RMA处理程序?是否执行不良分析?改善对策? 15.5 是否有将所有矫正情形和成果文件化,标准化? 15.6 15.7 是否采用Reel ID或Bar code进行批量批号控管?如无,发现环境管理物质异 常时,能否查明料件的批号并进行处理? 是否建立不良发生时的追溯体制?若有,该追溯体制能否追溯至原材料供货 商端?
15.8 矫正预防对策的内容是否向类似产品水平(横向)展开?
实际得分
左证资料
质量体系评定样本

质量体系评定评估阐明和指南目本质量体系评估(QSA)用以拟定体系与否符合QS—9000质量体系规定。
对的使用QSA可以保证所有规定均被阐明,并有助于拟定QS—9000符合性部门与人员一致性。
合用范畴QSA可以依照顾客和供方需要,在下列几种状况下使用:——第一方一供方对质量体系进行自我评估,至少使用带(*)和(**)问题。
——第二方一顾客对供方质量体系进行评估(涉及第一层次供方对分供方评估),应使用所有问题和子问题。
某些顾客至少会使用标有双星号(**)问题。
——第三方一由质量体系认证/注册机构用采作为编制审核检查表输入,至少使用带(*)和(**)问题。
评估程序在QS—9000附录A中规定了QSA程序。
QSA中问题顺序并不意味着审核顺序。
评估办法评估办法由三个重要阶段构成:阶段I——质量体系文献审核拟定质量手册(涉及所规定支持性文献)是署符合QS—9000所有规定。
使用QSA问题0.1文献审核。
阶段Ⅱ——现场审核这一阶段是拟定供方现场及外部场合质量体系实行限度和有效性。
阶段Ⅲ——分析和报告对上述两阶段成果进行评审,以拟定供方与否符合QS—9000规定。
审核总结方式审核员/顾客可采用如下两种办法之一对审核做出结论:—推荐/不推荐—计分法每一种要素都可以按顾客规定选用下述两种办法之一进行评估:—合格/普通不合格/严重不合格;—每个要素可得0~l0分,见“使用计分法评估过程”。
定义严重不合格是指浮现下述状况之一:—质量体系缺项或完全不符合QS—9000规定。
若对于某项规定浮现各种普通不合格,而使整个体系无法运营,则同样视为严重不合格;—任何有也许使不合格产品装运不合格。
任何也许导致产品或服务失效或预期使用性能严重减少不合格;—审核员依照经验和判断表白很也许导致质量体系失效或严重减少对产品和过程控制能力不合格。
普通不合格是指不符合QS—9000规定,但依照经验和判断不太也许导致浮现下列成果不合格:—质量体系失效;—减少对过程控制能力;—不合格产品也许被装运。
qsa评分计算规则

qsa评分计算规则QSA评分计算规则QSA(Quality, Service, and Accessibility)评分计算规则是一种衡量企业质量、服务和可访问性的评分体系。
它通过对企业在这三个方面的表现进行综合评估,为消费者提供参考,帮助他们选择最合适的企业或产品。
本文将介绍QSA评分计算规则的具体内容和应用。
一、质量评分质量评分主要从产品或服务的质量角度考量,包括以下几个方面:1.1. 产品性能:评估产品的性能表现,如耐用性、可靠性、安全性等;1.2. 产品质量控制:考察企业的生产制造过程和产品质量控制体系,如ISO认证等;1.3. 客户满意度:通过客户反馈和调查问卷等方式,评价客户对产品质量的满意程度。
质量评分的计算方式可以采用加权平均法,根据不同指标的重要程度赋予相应的权重,然后计算加权平均值得出最终质量评分。
二、服务评分服务评分主要从企业提供的服务质量和客户体验角度考量,包括以下几个方面:2.1. 响应速度:评估企业在客户提出问题或需求后的响应速度和效率;2.2. 服务态度:考察企业员工的服务态度和专业水平,包括礼貌、耐心、专业知识等;2.3. 问题解决能力:评价企业解决客户问题的能力和效果,包括解答疑问、处理投诉等;2.4. 售后服务:考察企业在售后服务方面的质量,如维修、退换货政策等。
服务评分的计算方式可以采用综合打分法,将每个方面的评分综合计算得出最终的服务评分。
三、可访问性评分可访问性评分主要从产品或服务的可访问性角度考量,包括以下几个方面:3.1. 无障碍设计:评估产品或服务是否符合无障碍设计原则,方便残障人士使用;3.2. 多渠道访问:考察企业提供的多种渠道供客户访问,如网站、手机应用、电话等;3.3. 多语言支持:评价企业是否提供多语言的产品或服务,以满足不同语言的客户需求。
可访问性评分的计算方式可以采用加分法,根据企业在每个方面的表现给予相应的加分,然后计算总分得出最终的可访问性评分。
QSA手册(第二版)--质量体系评定
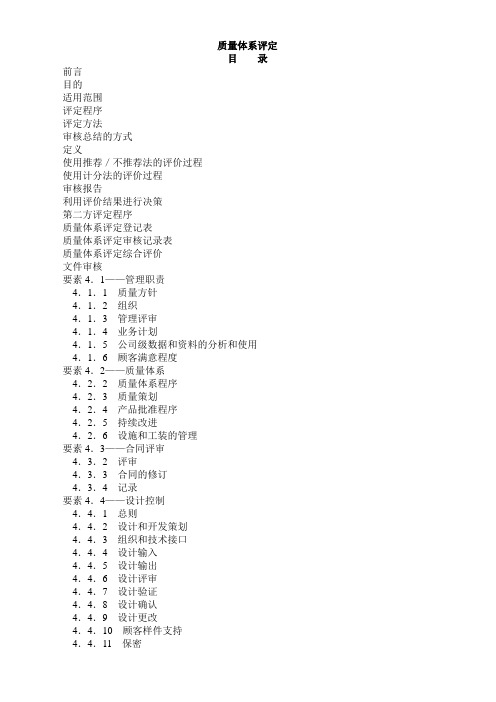
质量体系评定目录前言目的适用范围评定程序评定方法审核总结的方式定义使用推荐/不推荐法的评价过程使用计分法的评价过程审核报告利用评价结果进行决策第二方评定程序质量体系评定登记表质量体系评定审核记录表质量体系评定综合评价文件审核要素4.1——管理职责4.1.1 质量方针4.1.2 组织4.1.3 管理评审4.1.4 业务计划4.1.5 公司级数据和资料的分析和使用4.1.6 顾客满意程度要素4.2——质量体系4.2.2 质量体系程序4.2.3 质量策划4.2.4 产品批准程序4.2.5 持续改进4.2.6 设施和工装的管理要素4.3——合同评审4.3.2 评审4.3.3 合同的修订4.3.4 记录要素4.4——设计控制4.4.1 总则4.4.2 设计和开发策划4.4.3 组织和技术接口4.4.4 设计输入4.4.5 设计输出4.4.6 设计评审4.4.7 设计验证4.4.8 设计确认4.4.9 设计更改4.4.10 顾客样件支持要素4.5——文件和资料控制4.5.1 总则4.5.2 文件和资料的批准和发布4.5.3 文件和资料的更改要素4.6——采购4.6.1 总则4.6.2 分承包方的评价4.6.3 采购资料4.6.4 采购产品的验证要素4.7——顾客提供产品的控制4.7.1 顾客所有的工装要素4.8——产品标识和可追溯性要素4.9——过程控制4.9.1 过程监视和作业指导书4.9.2 维护过程的控制4.9.3 更改的过程控制要求4.9.4 作业准备的验证4.9.5 过程更改4.9.6 外观项目要素4.10——检验和试验4.10.1 总则4.10.2 进货检验和试验4.10.3 过程检验和试验4.10.4 最终检验和试验4.10.5 检验和试验记录4.10.6 供方试验室要求4.10.7 认可的试验室要素4.11——检验、测量和试验设备4.11.1 总则4.11.2 控制程序4.11.3 检验、测量和试验设备记录4.11.4 测量系统分析要素4.12——检验和试验状态4.12.1 补充验证要素4.13——不合格品的控制4.13.1 总则4.13.2 不合格品的评审和处置4.13.3 返工产品的控制4.13.4 经工程批准的产品的授权要素4.14——纠正和预防措施4.14.1 总则4.14.2 纠正措施4.14.3 预防措施要素4.15——搬运、储存、包装、防护和交付4.15.2 搬运4.15.3 储存4.15.5 防护4.15.6 交付要素4.16——质量记录的控制4.16.1 记录的保存要素4.17——内部质量审核4.17.1 内部审核计划要素4.18——培训4.18.1 培训的有效性要素4.19——服务4.19.1 服务信息反馈要素4.20——统计技术4.20.1 确定需求4.20.2 程序.4.20.3 统计工具的选择4.20.4 基础统计概念知识克莱斯勒特殊要求福特特殊要求通用特殊要求质量体系评定评定说明和指南目的本质量体系评定(QSA)用以确定体系是否符合QS-9000质量体系要求。
QSA

质量体系评定Quality System AssessmentQSA第二版质量体系评定评定说明和指南目的本质量体系评定(QSA)用以确定体系是否符合QS—9000质量体系要求。
正确使用QSA可以确保所有要求均被说明,并有助于确定QS—9000符合性的部门与人员一致性。
适用范围——第一方—供方对质量体系进行自我评定,至少使用带(*)和(* *)的问题。
——第二方—顾客对供方质量体系进行评定(包括第一层次供方对分供方的评定),应使用所有的问题和子问题。
某些顾客至少会使用标有双星号(* *)的问题。
——第三方—由质量体系认证/注册机构用来作为编制审核检查表的输入,至少使用带(*)和(* *)的问题。
评定程序在QS—9000附录A中规定了QSA程序。
QSA中问题的顺序并不意味着审核的顺序。
评定方法评定方法由三个主要阶段组成:阶段I ——质量体系文件审核确定质量手册(包括所要求的支持性文件)是否符合QS—9000的所有要求。
使用QSA的问题0.1文件审核。
阶段II ——现场审核这一阶段是确定供方现场及外部场所质量体系实施的程度和有效性。
阶段III ——分析和报告对上述两阶段的结果进行评审,以确定供方是否符合QS—9000要求。
审核总结的方式审核员/顾客可采用以下两种方法之一对审核做出结论:—推荐/不推荐—计分法每一个要素都可以按顾客的要求选用下述两种方法之一进行评定:—合格/一般不合格/严重不合格;—每个要素可得0 ~ 10分,见“使用计分法的评定过程”。
定义严重不合格是指出现下述情况之一:—质量体系缺项或完全不符合QS—9000要求。
若对于某项要求出现多个一般不合格,而使整个体系无法运行,则同样视为严重不合格;—任何有可能使不合格产品装运的不合格。
任何可能导致产品或服务失效或预期的使用性能严重降低的不合格;—审核员根据经验和判断表明很可能导致质量体系失效或严重降低对产品和过程控制能力的不合格。
一般不合格是指不符合QS—9000要求,但根据经验和判断不太可能导致出现下列结果的不合格:—质量体系失效;—降低对过程的控制能力;—不合格产品可能被装运。
QSA质量评估系统标准THD
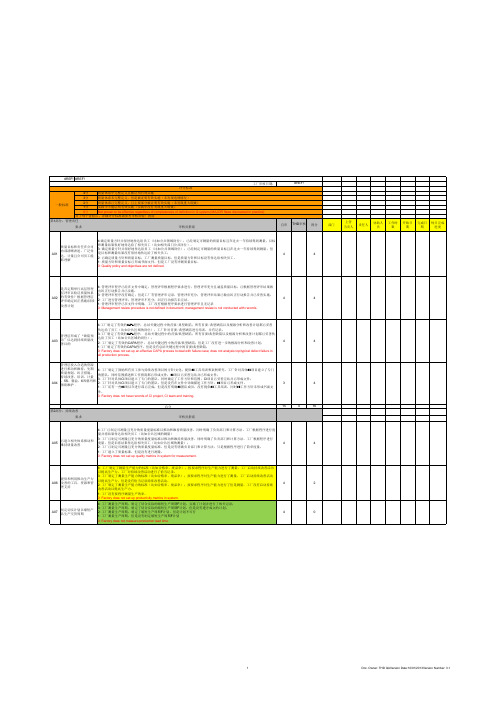
A12 、过程、检验和试验程 (比如ECN);但是没有编辑一套完整的质量规划以审核设计、流程、检验和试验程序的兼容性。
序与适用文件匹配
2: 工厂已制定多数程序,但一些程序没有充分编制;
4
4
1: 工厂缺失一些必要过程(比如ECN)。
0: Factory miss most quality assurance processes.
4
1: 工厂制定了培训过程并用适用范围对培训项目进行了规划。工厂没按照计划进行培训。
0: Factory does not set up training process nor plan training program; no training is performed with records.
提供和利用推动生产力
A06 改善的工具、资源和管 理支持
3: 工厂制定了测量生产能力的标准(比如合格率、废品率);按要求程序对生产能力进行了测量。工厂启动持续改善活动 以提高生产力。但是没有恰当记录持续改善活动。 2: 工厂制定了测量生产能力的标准(比如合格率、废品率);按要求程序对生产能力进行了但是测量。工厂没有启动持续 改善活动以提高生产力。
第3部分:质量体系 要求
总分 审核员指南
24
0
18
A11
质量体系已清楚地记录 在质量手册中,质量体 系应符合ISO9000或 ISO14000或其它国际质
4: 工厂有符合国际质量标准(比如ISO9000/ISO14000)的成文质量手册;质量手册包括最新的程序/文件; 3: 工厂有符合国际质量标准(比如ISO9000/ISO14000)的成文质量手册;质量手册中个别文件/程序过期; 2: 工厂有符合国际质量标准(比如ISO9000/ISO14000)的成文质量手册,但一些重要流程丢失(比如ECN); 1: 工厂有成文的质量手册,但是不完全符合国际质量标准(比如ISO9000/ISO14000),一些元素缺失(比如不合格品控制
品质体系稽核表(QSA)汇总.

得分
备注
是否建立控制采购质量的程序。采购文件是否明确采购的要求,并按规定进行了审批。 是否规定了选择采购分供方(Sub-supplier)的评定方法,并建立分供方的记录。(需包含对有害物质管理的要求) 是否有定义资格及委派熟悉产品专业知识和技术的人员去评鉴分供方。 是否通过质量系统审核(QSA)和质量制程审核(QPA)來评鉴分供方。 是否有针对有害物质风险的高低对分供方进行识别,并分类管理。 是否有制定合格供应商名册(AVL)及定期进行更新。 是否对分供方的品质协议、技术协议和采购协议进行管理。 是否定期评估分供方技术、质量、服务、交期和成本方面的标准。 是否规定采购验证和放行的方法,并切实执行。(有无进料检验管制系统,供应商是否有相应的进料程序来保证购买的材料和所定的要求相符) 进料检验是否按规定进行并做好记录,在进料检验中,是否识别关键和安规原物料,并能检测实施。 进料检验是否识别材料的有害物质风险大小,并制定不同的监测计划,且能贯彻实施。有无有害物质检测设备。 对材料及制程中可能污染的产品/辅料,是否有规定风险等级,并制定有害物质检测频率并贯彻实施。
5 5.1
生产和服务提供
该项得分百分比: 该项得分:
[ [
] ] 该项总分: [ ] A类 V
评鉴类别 B类 V C类 V D类 V
得分
备注
是否确定与服务有关的部门,规定其职责,并明确该部门负责向顾客提供必要的信息,了解顾客要求。
LNT Confidential
Page 2 of 5
LNT QSA 5.2 5.3 5.4 5.5 5.6 5.7 5.8 5.9 5.10 5.11 5.12 5.13 5.14 5.15 5.16 5.17 5.18 5.19 5.20 5.21 5.22 是否建立产品要求的评审程序,评审应在组织向顾客作出提供产品的承诺(如接受合同或订单及接受合同或订单更改)之前,并规定其职责。合同或订单是否进行评 审,并有完整的记录。是否有口头方式接受订货,有无记录和确认。 与顾客有关的产品要求改变时,是否按规定更改相关文件,并及时传递有关部门。产品要求的有关评审记录是否妥善保管。 是否建立产品生产过程控制程序,并明确过程之间的相互作用(需包含有害物质的管理)。 是否制订了生产过程中各工序的工艺要求或作业指导书。作业指导书等品质文件是否有版本控制,且在发布前经权责人员确认;作业指导书是否明确地规定所使用的机 器、装备、工具、治具、材料及程序;作业指导书对作业者是否清楚易懂。是否规定生产方式和每个过程/站别的设立。包装、装货的流程是否符合作业指导书。 是否选用合适生产设备、制订了生产设备维修、保养制度,并切实执行。测试条件、程序和仪器是否足够充分。 是否定义关键工序或特殊工序,并利用 SPC 进行控制,Cp/Cpk值没有达到期望值时,是否采取适当的措施。 是否有程序或計划细分所有需要监视或控制的关键参数和产品特性 (如:PFMEA、QC工程图)。 当制程失控和生产异常,是否有一个停线标准或停止出货标准。 有无品质反馈系统,如制程品质收集分析等,并贯彻执行。 操作人员是否掌握工艺要求或作业指导书,并按其要求进行操作。作业员是否清楚本制程的安全质控点。 客户样品是否进行明确的标识并妥善保存,样品的有效期是否列入管制清册。是否有样品测试流程和项目LIST。 是否对产品生产、安装、服务过程的标识作出明确规定(装配产品时,是否有标识来保证流程中没有步骤被遗漏)。 制程中的材料(含生产中的材料)能否适当地识别和控制。是否有证据表明,原材料供应商零部件是可追溯的(日期码、批号等)。 产品生产过程中是否有检验状态标识,即对合格品、不合格品的检验或测试状况,是否有标识(如标签、检验数据、测试软件、放置场所等);所有等待/通过/未通过测 试的产品有否采取适当的方式区分、标识,以避免混乱。 是否有产品标识和追溯的管理办法,并有效实施,在有可追溯性要求的场合,组织应控制产品的唯一性标识,并保持记录。生管对工单进行控制并可追溯。 改善品是否能进行识别。(如:S/N或Barcode的记录) 现有产能是否与所提报的产能调查表相符,能否满足LNT要求。 是否对可能造成有害物质污染或产生质变的生产过程进行识别并加以管控。如三价铬钝化过程 是否区分HSF产品与非HSF产品(无卤产品与有卤产品)的生产过程,对不同生产过程的原材料、辅料、工治具、设备进行识别区分,避免污染及混用。 是否有定义有害物质检测的第三方机构,及对第三方测试机构资格的识别。 是否有一个明确的计划,以不断对制程自动化进行改进。 V V V V V V V V V V V V V V V V V V V V V V V V V V V V V V V V V V V V V V V V V V V V V V V V V V V V V V V V V V V V V V V V V V V V V V V V V V V V V V V V V
qsa质量管理体系

qsa质量管理体系QSA质量管理体系是一种广泛使用的质量管理方法,旨在确保产品或服务的质量满足客户的需求和期望。
下面是关于QSA质量管理体系的详细介绍:1.质量管理体系的概念QSA质量管理体系是一种结构化的质量管理方法,它涵盖了质量策划、质量控制、质量保证和质量改进等活动。
这个体系的目标是帮助组织实现质量目标,并确保产品或服务的质量符合客户的需求和期望。
2.QSA质量管理体系的构成QSA质量管理体系由四个主要部分组成:(1) 质量策划:该部分涉及确定组织的质量目标、制定实现这些目标所需的计划和策略。
这包括了解客户的需求和期望,并确定如何满足这些需求和期望。
(2) 质量控制:该部分涉及对产品或服务的质量进行监控和检查,以确保其符合组织的质量目标和客户的需求。
这包括对原材料、生产过程、成品等进行检验和测试。
(3) 质量保证:该部分涉及为确保产品或服务的质量而采取的措施,以保证客户对质量的信任。
这包括对员工进行培训、实施内部审核、进行外部审核等。
(4) 质量改进:该部分涉及通过持续改进来提高产品或服务的质量,以满足客户的需求和期望。
这包括采用六西格玛、精益生产等质量管理工具和方法。
3.QSA质量管理体系的实施实施QSA质量管理体系需要以下步骤:(1) 制定质量方针和目标:组织需要明确自己的质量方针和目标,这将成为整个质量管理体系的基础。
(2) 确定组织结构和工作职责:组织需要明确各个部门和岗位的职责和权限,以确保质量管理工作的顺利进行。
(3) 制定质量管理计划:组织需要制定质量管理计划,包括质量策划、质量控制、质量保证和质量改进等方面的计划和策略。
(4) 实施质量管理计划:组织需要按照质量管理计划实施各项质量管理活动,以确保产品或服务的质量符合要求。
(5) 监控和评估质量管理体系:组织需要定期对质量管理体系进行监控和评估,以确保其有效性和适应性。
总之,QSA质量管理体系是一种结构化的质量管理方法,涵盖了质量策划、质量控制、质量保证和质量改进等活动。
QSA质量体系评定

QSA 质量体系评定评定说明和指南目的本质量体系评定(QSA)用以确定体系是否符合QS9000质量体系要求。
正确使用QSA可以确保所有要求均被说明,并有助于确定QS9000符合性的部门与人员一致性。
适用范围QSA可以根据顾客和供方的需要,在下列几种情况下使用:——第一方—供方对质量体系进行自我评定,至少使用带(*)和(**)的问题。
——第二方—顾客对供方质量体系进行评定(包括第一层次供方对分供方的评定),应使用所有问题和子问题。
某些顾客至少会使用标有双星号(**)的问题。
——第三方—由质量体系认证/注册机构用来作为编制审核检查表的输入,至少使用带(*)和(**)的问题。
评定程序在QS9000附录中A中规定了QSA程序。
QSA中问题的顺序并不意味着审核的顺序。
评定方法评定方法由三个主要阶段组成:阶段I——质量体系文件审核确定质量手册(包括所要求的支持性文件)是否符合QS9000的所有要求。
使用QSA的问题0.1文件审核.阶段Ⅱ----现场审核这一阶段确定供方现场及外部场所质量体系实施的程度和有效性. 阶段Ⅲ----分析和报告对上述两阶段的结果进行评审,以确定供方是否符合QS9000要求.审核总结的方式审核员/顾客可采用以下两种方法之一对审核做出结论:--推荐/不推荐--计分法每一个要不都可以按顾客的要求选用下述两种方法之一进行评定:--合格/一般不合格/严重不合格--每个要素可得0~10分,见“使用计分法的评定过程”.定义严重不合格是指出现下述情况之一:--质量体系缺项或完全不符合QS9000要求.若对于某项要求出现多个一般不合格,而使整个体系无法运行,则同样视为严重不合格;--任何有可能使不合格产品装运的不合格.任何可能导致产品或服务失效或预期的使用性能严重降低的不合格.--审核员根据经验和判断表明很可能导致质量体系失效或严重降低对产品和过程控制能力的不合格.一般不合格是指不符合QS9000要求,但根据经验和判断不大可能导致出现下列结果的不合格: --质量体系失效;--降低对过程的控制能力;--不合格产品可能被装运;一般不合格可能是下列情况之一:--供方文件化的质量体系的某一部分不符合QS9000的要求;--在某公司质量体系中发现的一个或多个轻微错误.改进的机会----观察到的情形尽管不属于严重不合格或一般不合格,但凭审核员的判断和经验未使用最佳方法.为了保证顾客的利益,必须在最终的审核报告中将需改进的内容记录下来.合格----审核中没有发现严重不合格或一般不合格.充分性----本文的充分性是指就供方的作业范围而言,供方特定文件满足QS9000的意图.为了支持持续改进,审核员应指出质量体系的优点和不足,并必须将需改进的内容记录下来.使用推荐/不推荐法的评价过程如果审核中未发现任何不合格,总体评价结论将是“推荐”.在下列情况下评价处于“待定”状态----审核中发现一个严重不合格;----审核中发现一个或多个一般不合格;如果在90天或规定时间期限内能够得到满意的合格证据,“待定”可转为“推荐”.由审核员决定是否进行现场验证.如果审核过程中发现一个以上严重不合格,总的评价结论应是“不推荐”.如果在规定时间内没有完成不合格的处理,也被评定为“不推荐”.每个要素的结果(0~10分)应在审核记录表的相应位臵记录下来.各个要素得分总和除以参与打分的要素总数就是最后得分.每个适用要素的得分至少是7分,才能够被推荐.不适用于特定供方的要素.某些要素,如4.7(顾客提供产品的控制)和4.19(服务)并非适用所有供方,此时应在记分位臵填入“不适用”.审核报告对于被证实符合QS9000要求,但明显有持续改进机会的项目应标识.对于第一方和第二方审核,审核员应指出质量体系的优点和不足.利用评价结果进行决策无论采用哪种评价方法,每个顾客的采购部门应根据自己的情况利用评价结果做出决策.第二方评定程序1.供方向顾客提供所需的材料 (如质量手册/程序文件)为保证审核效果,质量手册和所需其它材料最迟应在现场审核前两周提交给顾客.通常供方还需提交以下材料:----按顾客要求进行自我评定的结果;----第三方质量体系注册计划(如果有);----其它顾客使用QSA进行的审核(如果有).2.文件审核按照QSA中问题0.1,由顾客评审供方提交的材料是否满足QS9000的要求.如果某项规定超出了QS9000的要求,应在审核检查表中记录.如发现不足的地方应明确指出并通知供方.3.文件是否合格?由顾客建议供方对质量体系文件进行修改以满足QS9000的要求.若文件修改未达到满意,现场审核通常会推迟.4.供方进行必要的修改供方对质量体系文件进行必要的修改.5.顾客准备审核检查表现场审核检查表除QSA内容外还应加上文件审核确定的需要补充审核的问题.QSA中为这类问题预留了空间.6.顾客实施现场审核顾客利用审核检查表评价供方体系的运行情况.审核应在供方生产现场及其它适当的外部场所(如工程、采购等部门进行.如果生产厂有多个基本相同的工序(生产线/冲压线等),顾客可抽取其中一个作为样本进行审核,重大发现应立即通知供方. 有些顾客可通过审核带星号(**)的问题对潜在供方进行评价.7.顾客确定不合格所有不合格必须在最终报告中列出.某些顾客还会提供详细的审核检查表.8.供方纠正不合格(并通知顾客)若供方能够在审核过程中纠正一般不合格,应将纠正情况在报告中注明.对于其它不合格项,供方确定纠正措施完成的日期.供方在纠正措施完成后应通知顾客.9.顾客验证根据不合格项的性质,顾客通过现场和/或文件评审来验证纠正措施的有效性.10.顾客通知供方审核结果顾客向供方提供最终审核结果(如推荐/不推荐)质量体系评定登记表供方:_______________________________________________________________________工厂地址:___________________________________________________________________供方代码:___________________________审核日期:_______________________________审核范围:___________________________________________________________________被审核产品/生产线:__________________________________________________________审核目的:___________________________________________________________________审核类型:_________初评 _______跟踪验证 ________监督检查 ________其它审核结果:_________推荐 _______待定 ________不推荐 ________分数(如适用) 是否需要监督检查:_______是 _______否日期:__________________评语:__________________________________________________________________________ 审核员姓名:_____________________________ 电话:_________________________________ ______________________________________________________________________________质量体系评定审核记录表所有不合格项纠正措施拟定完成日期:_________________分数计算(如适用) 各个要素得分总除以参与打分的要素总数就是最后得分.质量体系评定文件审核。
QSA厂商体系审核评分(详细)
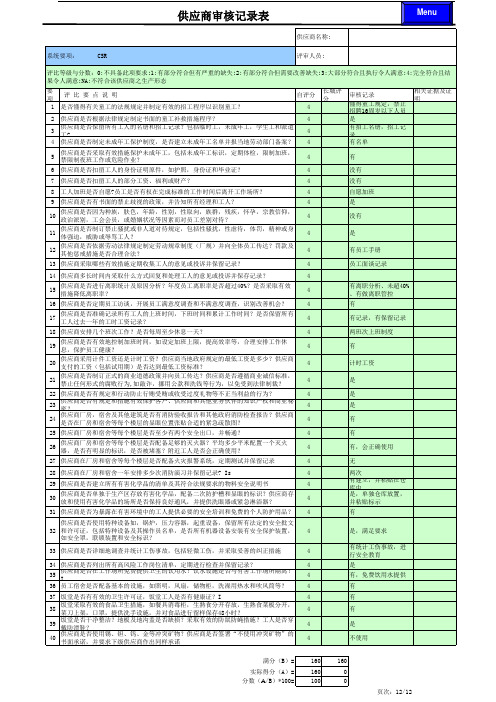
4
有
25 供应商厂房和宿舍等每个楼层是否至少有两个安全出口,并畅通?
4
有
26
供应商厂房和宿舍等每个楼层是否配备足够的灭火器?平均多少平米配置一个灭火 器,是否有明显的标识,是否被堵塞?附近工人是否会正确使用?
4
有,会正确使用
27 供应商在厂房和宿舍等每个楼层是否配备火灾报警系统,定期测试并保留记录
4
4
有 有 是 不使用
满分(B)=
160160实ຫໍສະໝຸດ 得分(A)=1600
分数(A/B)*100=
100
0
页次:12/12
37 饭堂是否有有效的卫生许可证,饭堂工人是否有健康证?I
4
38
饭堂采取有效的食品卫生措施,如餐具消毒柜,生熟食分开存放,生熟食菜板分开, 菜刀上架,口罩,提供洗手设施,并对食品进行留样保存48小时?
4
39
饭堂是否干净整洁?地板及地沟盖是否缺损?采取有效的防鼠防蝇措施?工人是否穿 戴防滑鞋?
4
40
供应商是否使用锡、钽、钨、金等冲突矿物?供应商是否签署“不使用冲突矿物”的 书面承诺,并要求下级供应商作出同样承诺
4
有 计时工资 是
22 供应商是否有规定和行动防止行贿受贿或收受过度礼物等不正当利益的行为?
4
是
23
供应商是否有规定和措施有效保护客户、供应商和其他业务伙伴的知识产权和商业秘 密?
4
是
24
供应商厂房,宿舍及其他建筑是否有消防验收报告和其他政府消防检查报告?供应商 是否在厂房和宿舍等每个楼层的显眼位置张贴合适的紧急疏散图?
4
自愿加班
9 供应商是否有书面的禁止歧视的政策,并告知所有经理和工人?
QSA质量体系评定
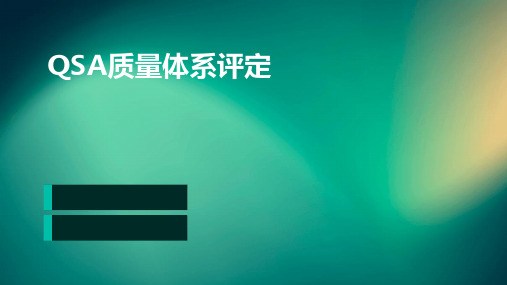
02 QSA质量体系评定的基础
质量管理体系的建立
明确质量方针和目标
制定清晰、可衡量的质量方针和目标,为整个组织提供明确的质 量方向。
组织架构和职责分配
建立合理的组织架构,明确各部门和岗位的职责、权限和相互关系, 确保质量管理的有效实施。
资源管理
合理配置人力、物力、财力等资源,确保质量管理工作的正常开展。
目的
帮助组织识别其质量管理体系的优势 和不足,提出改进建议,促进持续改 进和提升组织绩效。
评定流程与标准
评定流程
通常包括预评估、正式评估和后续评估三个阶段。预评估阶段主要是对组织的质 量管理体系进行初步了解和诊断;正式评估阶段则是对质量管理体系进行全面、 深入的审核;后续评估阶段则是跟踪改进措施的落实情况。
感谢您的观看
质量信息管理
建立有效的质量信息管理系统,收集、整理和分 析质量数据,为质量管理体系的改进提供支持。
培训与意识提升
定期开展质量管理培训和意识提升活动,提高全 员的质量意识和技能水平。
03 QSA质量体系评定的方法 与工具
质量保证工具
01
质量计划
质量手册
02
03
检验与试验
制定详细的质量计划,明确质量 目标、质量标准和质量控制方法。
失败案例反思
案例选择
选择一些QSA质量体系评定失败的案例,如某些组织在 质
分析失败案例中存在的问题和不足,如 管理体系不健全、过程控制不严格、员 工培训不到位等。
02
03
案例反思
深入反思失败案例的教训,提出改进 建议和措施,避免类似问题再次发生。
05 QSA质量体系评定的未来 发展
通过对生产过程能力的评估,识 别出影响产品质量的关键因素, 为改进生产过程提供依据。