各家PTA工艺技术对比
国内PTA污水处理及工艺流程

国内PTA污水处理及工艺流程1国内PTA污水处理情况(1)扬子石化PTA污水处理。
采用厌氧+好氧工艺,经过多年改造现已由UASB(上浮厌氧污泥床)改为厌氧复合床。
即向池内添加软性填料,使厌氧池的运行基本保持稳定。
由于软性填料本身不耐用,几年需要更换一次,厌氧污泥易流失等原因致使影响处理效果。
所以,出水达不到国家排放标准,还需排放至下一级污水场继续处理。
(2)仪征化纤PTA污水处理。
采用厌氧+空曝工艺,所采用的厌氧池是带三相分离器的厌氧生物滤池,即UASB+纤维(软性填料)进水经过脉冲发生器间断进水,保持配水系统布水均匀。
其为中温型、敞开式结构,冬天不需保温。
该系统设置了较大容积的调节池,停留时间为3.5天,避免了系统受到冲击。
厌氧+普通空曝之后,出水COD在600mg/L左右,仍需排放到总厂污水处理进行再处理。
(3)乌石化PTA污水处理采用两段普通空曝工艺,虽然处理后的污水可达到国家排放标准,但是停留时间长、占地大、能耗高、污泥产量大、处理成本高。
2 工艺流程通过调研和分析,将聚酯二阶段工程PTA污水处理主体工艺确定为接触氧化+纯氧曝气,加上其他配套工艺,最终确定的工艺和参数。
(1)污水预处理。
PTA、PET装置的生产污水及现有化工污水、涤纶有机污水用泵送至污水场的中和配水池。
中和配水池内设有在线pH计,用以实现根据pH的变化随时加入适量的浓硫酸或弄氢氧化钠,保证进入后续处理系统的污水pH值在6~9。
配水池为水量分配设施,当水量正常时,水经过溢流堰至均质池,水量超标时,经溢流堰至事故调节池。
为使污水充分混合,保证出水水质基本均匀,匀质池设有空气搅拌设备(螺旋曝气器)。
由于PTA生产污水中缺少氮磷等营养成分,故需在均质池内投加尿素(3t/d)和磷酸二氢钾(1t/d),以保证生化处理过程所需营养。
(2)一级生化处理。
PTA等装置产生的高浓度污水经预处理后从均质池进入接触氧化池进行一级生化处理。
接触氧化池采用曝气均匀平稳的蘑菇型中孔曝气器,填料采用不易堵塞、安装使用方便的悬浮梅花型多孔填料。
PTA主流工艺技术

PTA主流工艺技术随着科技的不断进步,PTA主流工艺技术也得到了迅猛的发展。
PTA(聚对苯二甲酸乙二酯)是一种重要的合成纤维原料,广泛应用于纺织、服装、家居、汽车等领域。
在PTA生产过程中,工艺技术对产品质量和生产效率具有重要影响。
在PTA的生产过程中,主流工艺技术有以下几点:首先,原料的选择。
PTA的主要原料是石油中的二甲苯,因此在生产过程中需要选用纯度较高的二甲苯。
高纯度的原料能够保证PTA产品的质量稳定,同时还能减少对环境的污染。
其次,催化剂的选取。
在PTA的合成过程中,需要由对苯二甲酸经过催化剂的作用来进行酯化和醋化反应,最终生成PTA。
选择适合的催化剂能够提高反应效率,缩短反应时间,并且减少废弃物产生。
再次,反应条件的控制。
反应温度、压力和搅拌速度等条件对PTA的合成反应有着重要的影响。
合理控制反应条件能够提高产率,降低成本,并且保证产品的质量稳定。
此外,还需要对产物进行精制处理。
PTA的产物中可能含有杂质,需要通过蒸馏、萃取等方法进行精制处理。
精制处理能够提高产物的纯度,使得产品更加适合各种应用。
最后,需要进行产品质量的检测。
产品质量检测是PTA工艺技术中必不可少的环节。
通过使用各种分析仪器、设备对产品进行分析,检测其纯度、含水量、分子量等指标。
只有通过产品质量检验,才能保证产品质量的稳定和可靠性。
综上所述,PTA主流工艺技术的发展涉及原料选择、催化剂选取、反应条件控制、产物精制处理和产品质量检测等多个方面。
合理控制这些环节,能够提高PTA的生产效率和产品质量,进一步推动PTA产业的发展。
随着科技的不断创新和进步,相信PTA主流工艺技术将会不断突破,为相关行业带来更多的创新和发展机会。
苯乙烯生产工艺技术对比

苯乙烯生产工艺技术对比苯乙烯是一种重要的化工原料,广泛应用于塑料、橡胶和合成纤维等行业。
目前,苯乙烯的生产工艺技术主要有烟气法和催化裂化法两种。
烟气法是传统的苯乙烯生产工艺技术之一,它的原料是乙苯和空气。
首先,将乙苯和空气混合,并通过燃烧反应生成苯乙烯。
然后,将产生的混合气体通过冷凝器冷却,得到液体苯乙烯。
这个过程的主要优点是简单、成本低,但是也存在一些不足之处。
首先,烟气法的反应温度较高,容易产生副产物和有毒物质,对环境造成污染。
其次,烟气法的乙苯利用率较低,约为70%,对资源的浪费较为严重。
此外,烟气法的产品纯度较低,需要经过进一步的提纯处理。
催化裂化法是目前最常用的苯乙烯生产工艺技术之一。
催化裂化法主要通过在催化剂的作用下,将乙苯分解为苯和乙烯,再将乙烯加氢生成苯乙烯。
催化裂化工艺的优点包括反应温度较低、产品纯度高、乙苯利用率高等。
此外,催化裂化法还可以通过改变催化剂的组成和反应条件,调整产品的比例,满足不同行业的需求。
然而,催化裂化法的成本较高,需要进行催化剂的再生和废气处理等工序,增加了工艺的复杂性。
同时,催化裂化法还面临着催化剂的选择和设计的问题,需要不断改进和优化。
综上所述,烟气法和催化裂化法是目前苯乙烯生产工艺技术的两种主要方法。
烟气法简单、成本低,但对环境造成污染并且乙苯利用率低;催化裂化法反应温度低,产品纯度高,乙苯利用率高,但成本较高并且工艺较为复杂。
随着环保意识的增强和技术的进步,一些新的苯乙烯生产工艺技术也在不断涌现,如光电催化法和电解法等。
未来,随着科学技术的进步和工艺技术的不断改进,苯乙烯的生产工艺将会变得更加环保、高效和经济。
PTA产品技术简介
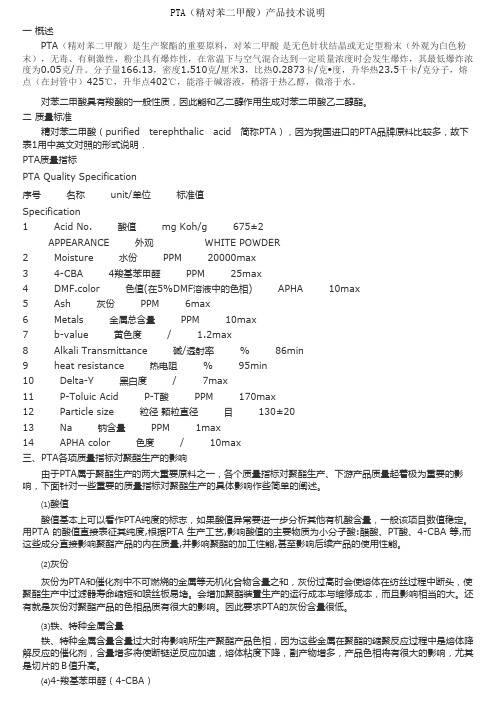
PTA(精对苯二甲酸)产品技术说明一概述 PTA(精对苯二甲酸)是生产聚酯的重要原料,对苯二甲酸是无色针状结晶或无定型粉末(外观为白色粉末),无毒、有刺激性,粉尘具有爆炸性,在常温下与空气混合达到一定质量浓度时会发生爆炸,其最低爆炸浓度为0.05克/升。
分子量166.13,密度1.510克/厘米3,比热0.2873卡/克•度,升华热23.5千卡/克分子,熔点(在封管中)425℃,升华点402℃,能溶于碱溶液,稍溶于热乙醇,微溶于水。
对苯二甲酸具有羧酸的一般性质,因此能和乙二醇作用生成对苯二甲酸乙二醇酯。
二质量标准 精对苯二甲酸(purified terephthalic acid 简称PTA),因为我国进口的PTA品牌原料比较多,故下表1用中英文对照的形式说明.PTA质量指标PTA Quality Specification序号名称 unit/单位标准值Specification1 Acid No. 酸值 mg Koh/g 675±2APPEARANCE 外观 WHITE POWDER2 Moisture 水份 PPM 20000max3 4-CBA 4羧基苯甲醛 PPM 25max4 DMF.color 色值(在5%DMF溶液中的色相) APHA 10max5 Ash 灰份 PPM 6max6 Metals 金属总含量 PPM 10max7 b-value 黄色度 / 1.2max8 Alkali Transmittance 碱/透射率 % 86min9 heat resistance 热电阻 % 95min10 Delta-Y 黑白度 / 7max11 P-Toluic Acid P-T酸 PPM 170max12 Particle size 粒径颗粒直径目 130±2013 Na 钠含量 PPM 1max14 APHA color 色度 / 10max三、PTA各项质量指标对聚酯生产的影响 由于PTA属于聚酯生产的两大重要原料之一,各个质量指标对聚酯生产、下游产品质量起着极为重要的影响,下面针对一些重要的质量指标对聚酯生产的具体影响作些简单的阐述。
各家PTA工艺技术对比评析

各家PTA工艺技术对比评析精对苯二甲酸(purified terephthalic acid 简称PTA)是生产聚酯的重要原料,对苯二甲酸是无色针状结晶或无定型粉末(外观为白色粉末),无毒、有刺激性,粉尘具有爆炸性,在常温下与空气混合达到一定质量浓度时会发生爆炸,其最低爆炸浓度为0.05克/升。
分子量166.13,密度1.510克/厘米3,比热0.2873卡/克·度,升华热23.5千卡/克分子,熔点(在封管中)425℃,升华点402℃,能溶于碱溶液,稍溶于热乙醇,微溶于水。
我国聚酯工业的超速成长,极大地刺激了PTA投资的快速增长,从而加快了PTA项目的工艺引进,上述成果也不同程度地在新建或改建的PTA装置中得到了应用。
我国从20世纪70年代中期开始引进PTA生产装置,目前已形成相当的生产规模。
但我国PTA装置建设的关键技术仍然依靠进口,基础研究薄弱,能耗水平与国际先进水平比较还有相当大的差距。
我国PTA装置的生产规模已经与国际接轨,在大型化方面取得了长足的进展,但在工艺优化方面,特别是基础研究方面仍然有待开发。
下面将各家PTA生产工艺技术进行对比,来分析各个工艺的优缺点。
工艺技术各专利商都拥有工业化生产PTA的专利技术,拥有近期采用最新技术的专利工厂,并生产出合格的PTA产品。
都采用回收氧化反应副产蒸汽和反应尾气用于空压机驱动等节能措施,并将尾气用于中间产品CTA和成品PTA输送。
溶剂回收:多数厂家为共沸蒸馏,优于常压蒸馏,筛板塔逐渐改为填料塔。
催化剂回收:工艺技术(二)的回收技术较简单,其他几家公司流程较复杂。
精制母液回收:工艺技术(六)无精制母液回收,脱盐水消耗量大, PTA损失量大,其他几家都有。
工艺条件氧化反应温度、压力趋于降低。
工艺技术(一)(二) (三) (五) (六)为高温氧化工艺,工艺技术(四)为中温氧化工艺。
高温氧化反应温度曾先后采用230 ℃→209 ℃→196 ℃→191 ℃;中温186 ℃。
PTA合成工艺技术

PTA合成工艺技术PTA合成工艺技术是指对金属或金属合金材料进行喷涂处理的一种工艺技术。
PTA(Plasma Transferred Arc)是一种利用直流等离子体电弧喷涂技术,通过高温等离子体电弧的瞬间高热能和高速气流的作用,将喷涂材料熔化并喷射到工件表面,形成一层均匀致密的涂层。
下面将对PTA合成工艺技术进行详细介绍。
PTA合成工艺技术的关键在于掌握好加热源和喷涂源之间的协调配合。
加热源是通过电弧产生高温等离子体,而喷涂源则是通过给予材料足够热能来使其熔化,并将喷射到工件表面。
这两个源的功率和速度需要精确调节,以确保喷涂材料在喷射过程中能够充分熔化,并以适当的速度形成均匀涂层。
PTA合成工艺技术的优点是能够在保持材料组织和化学成分不变的情况下,在工件表面形成一层新的金属涂层。
这些涂层具有很高的附着力和耐磨性,能够提高工件的硬度、耐腐蚀性和耐磨性,从而延长工件的使用寿命。
此外,PTA合成工艺技术还具有喷涂速度快、成形效果好和表面质量高的特点,能够满足不同领域对涂层性能的要求。
PTA合成工艺技术的应用领域广泛。
例如,在制造业中,PTA 合成工艺技术可用于修补或加强零部件的表面,以增强其抗压性和耐磨性,并延长其使用寿命。
在能源领域,PTA合成工艺技术可用于提高发电设备和石油化工设备的耐磨性和耐腐蚀性,减少设备的维修和更换频率。
此外,PTA合成工艺技术还可用于航空、航天和军事等领域,以提高飞机、舰船等载具的耐磨性和抗腐蚀性。
PTA合成工艺技术的发展离不开材料科学和工艺技术的不断进步。
材料科学的发展使得喷涂材料具有更高的熔点和更好的机械性能,从而提高了涂层的质量和耐久性。
而工艺技术的进步则使喷涂操作更加自动化和智能化,提高了工作效率和涂层质量的稳定性。
总之,PTA合成工艺技术是一种先进的喷涂技术,通过瞬间高温等离子体电弧和喷射速度的配合,能够在材料表面形成均匀致密的涂层,提高工件的硬度、耐腐蚀性和耐磨性。
PTA催化剂---醋酸钴、醋酸锰低成本高效无污染生产新工艺

PTA催化剂---醋酸钴、醋酸锰低成本高效无污染生产新工艺1.概述:为适应PTA工业提高产品质量、降低生产成本、提高工作效率需要而研究开发成功的醋酸钴锰生产新工艺技术,生产效率至少比传统工艺提高100倍,具有投资小、建设周期短、可实现直接与PTA及TMA装置的配套,并降低催化剂调制过程成本,改进操作环境;通过利用PTA氧化反应器排出的稀醋酸还可进一步降低PTA或催化剂生产成本,不存在环境污染。
采用此项技术于1997年在济南建成首套工业化生产装置,也是国际上首套此类技术装置,催化剂活性优于晶体催化剂;20XX年4月在仪征化纤集团建成第二套同类装置,至今一直稳定运行。
目前此项技术又获得新进展,全部物料及能源实现全密闭循环,已获得创造专利授权,并于20XX年5月在南京昂扬公司建成第三套同类装置,产品也已应用于多家TMA和扬子石化PTA等装置,此外,新技术更加适合为PTA装置配套,并可与PTA或TMA 催化剂调制部分融合,削减PTA或TMA装置催化剂调制部分投资,催化剂装置投资也大幅削减,催化剂生产能源消耗小于传统工艺的1/20,无环境污染,是目前国际上运行成本最低、原料消耗最少(原料金属钴、锰和醋酸达到或接近理论消耗)、生产产品质量最稳定、杂质含量最低的成熟技术。
2.项目背景醋酸钴及醋酸锰是由对二甲苯经液相氧化制备对苯二甲酸时的最主要催化剂,对于醋酸钴,国内外早期的工艺一般采用硝酸法生产,其主要特点是:首先将金属钴用硝酸溶解,再加入碳酸钠使之转化为碳酸钴,生成的碳酸钴经水洗脱盐后,用醋酸中和使之成为醋酸钴,再经浓缩、结晶、提纯、分别、干燥等得到成品,在用作催化剂时,还要经过溶解等,此工艺所需设备多、流程长、设备腐蚀严重,存在严重环境污染、生产中钴(依靠进口)消耗量大,需重复回收处理,生产成本高。
为了降低成本,人们又改进了硝酸法,即采用硝酸醋酸混酸工艺,通过掌握混酸中硝酸浓度、降低产品浓度和结晶除杂等合成醋酸钴,目前国内多采用此工艺,但此工艺仍存在环境污染、反应生产效率低、能源消耗大、反应后期钴活性降低、钴消耗大、镍铜简单进入产品、产品中硝酸盐高等缺陷。
国内PTA生产技术的应用及新一代工艺介绍

国内PTA生产技术的应用及新一代工艺介绍PTA是生产聚酯的主要原料,全称精对苯二甲酸,据公开资料统计目前国内产量总和已达到全球总产能的56%左右,截止2018年1月嘉兴石化二期投产后国内产能总和达到了5131.5萬吨/年。
本文对目前国内已投产主流专利进行简单介绍,并对新一代PTA技术进行介绍和解析。
标签:PTA生产技术;PTA新工艺1 国内已投产PTA生产技术简介我国投产的PTA应用的技术包括BP、INVISTA、昆仑、日立、三菱+东帝士、EASTMAN、早期BP+AMOCO工艺、三井工艺等,产能市场份额从打到小依次是INVISTA、日立、三菱+东帝士、昆仑、BP,截止2018年8月各占37.45%、26.11%、13.15%、12.08%、7.79%。
从上世纪五十年代开始,BP-Amoco(简称BP)公司和DuPont-ICI(后转让给INVISTA)公司几乎同时对PTA生产工艺进行研发,不断完善逐步发展和形成氧化、精制专利技术,其他的生产工艺都是这两家工艺技术的基础上,通过进行研发而形成的具有自身特点的专有工艺技术。
因BP专利在2015年开始出售专利授权,之前国内除了珠海BP以外并没有其他使用其专利的工厂,其国内技术应用比例并不大。
而INVISTA专利在1995年、1996年开始对辽阳石化、乌鲁木齐石化出售其专利技术,截止2018年8月国内有20套采用INVISAT的装置已建设完成。
国产工艺为中国昆仑工程公司(原来的中国纺织工业设计院)的专利技术,其专利技术以三井工艺技术为基础进行工艺改进优化,重庆市涪陵蓬威石化有限责任公司是第一个采用该技术的PTA装置,之后海伦石化120万吨/年、浙江远东石化(现已被华杉集团收购)140万吨/年、虹港石化150万吨/年PTA装置也均采用该技术,但其能耗、物耗与同期的BP、INVISTA工艺仍有差距。
2 PTA新工艺介绍目前PTA新技术开发提供技术转让的主要有BP、INVISTA、昆仑三家,其中BP最新工艺技术于2015年7月在珠海BP三期投产,INVISTA最新P8技术2018年1月在嘉兴桐昆二期投产,虽然在试运行阶段设备故障和工艺稳定方面存在一定的问题,但经过相关改造,装置运行已趋于平稳,技术已接近成熟。
pta生产工艺方案比较

pta生产工艺方案比较
本文将比较pta生产工艺中的两种方案,并对其进行评估。
两种方案分别是:
1. 纯氧气法生产工艺:该方案使用纯氧气作为氧化剂,通过氧化反应将二甲醚转化为pta。
2. 空气氧法生产工艺:该方案使用空气中的氧气作为氧化剂,通过氧化反应将二甲醚转化为pta。
以下是两种方案的比较和评估:
纯氧气法生产工艺
- 优点:
- 可以得到高纯度的pta产品。
- 氧化反应速度较快,生产效率高。
- 缺点:
- 需要纯氧气供应,成本较高。
- 氧气的使用增加了安全风险。
空气氧法生产工艺
- 优点:
- 不需要纯氧气供应,成本较低。
- 可以使用环境中的氧气作为氧化剂,更加环保。
- 缺点:
- 得到的pta产品质量相对较低。
- 由于氧化反应速度较慢,生产效率较低。
根据以上比较,两种生产工艺方案各有优缺点。
如果追求高纯度的pta产品和较高的生产效率,纯氧气法生产工艺是一个很好的选择。
然而,如果成本和环保性是更重要的考虑因素,空气氧法生产工艺可能更适合。
请注意,本文所提供的信息仅供参考,具体实施方案需根据实际情况进行评估和决策。
PTA产业及技术发展概况
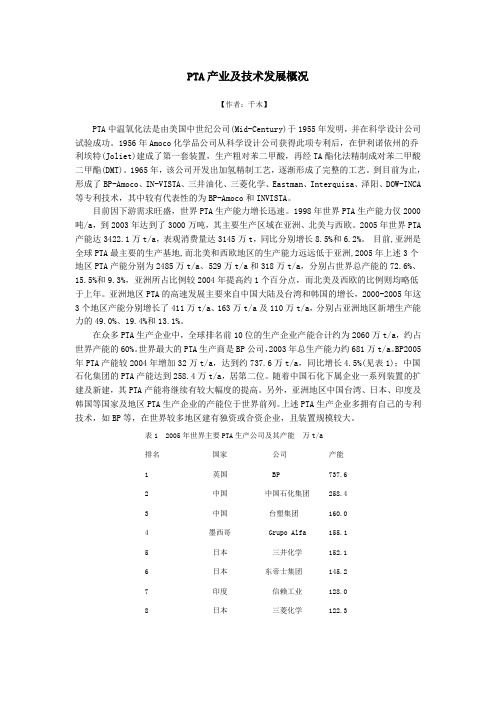
PTA产业及技术发展概况【作者:千木】PTA中温氧化法是由美国中世纪公司(Mid-Century)于1955年发明,并在科学设计公司试验成功。
1956年Amoco化学品公司从科学设计公司获得此项专利后,在伊利诺依州的乔利埃特(Joliet)建成了第一套装置,生产粗对苯二甲酸,再经TA酯化法精制成对苯二甲酸二甲酯(DMT)。
1965年,该公司开发出加氢精制工艺,逐渐形成了完整的工艺。
到目前为止,形成了BP-Amoco、IN-VISTA、三井油化、三菱化学、Eastman、Interquisa、泽阳、DOW-INCA 等专利技术,其中较有代表性的为BP-Amoco和INVISTA。
目前因下游需求旺盛,世界PTA生产能力增长迅速。
1998年世界PTA生产能力仅2000吨/a,到2003年达到了3000万吨,其主要生产区域在亚洲、北美与西欧。
2005年世界PTA 产能达3422.1万t/a,表观消费量达3145万t,同比分别增长8.5%和6.2%。
目前,亚洲是全球PTA最主要的生产基地,而北美和西欧地区的生产能力远远低于亚洲,2005年上述3个地区PTA产能分别为2485万t/a、529万t/a和318万t/a,分别占世界总产能的72.6%、15.5%和9.3%,亚洲所占比例较2004年提高约1个百分点,而北美及西欧的比例则均略低于上年。
亚洲地区PTA的高速发展主要来自中国大陆及台湾和韩国的增长,2000-2005年这3个地区产能分别增长了411万t/a、163万t/a及110万t/a,分别占亚洲地区新增生产能力的49.0%、19.4%和13.1%。
在众多PTA生产企业中,全球排名前10位的生产企业产能合计约为2060万t/a,约占世界产能的60%。
世界最大的PTA生产商是BP公司,2003年总生产能力约681万t/a。
BP2005年PTA产能较2004年增加32万t/a,达到约737.6万t/a,同比增长4.5%(见表1);中国石化集团的PTA产能达到258.4万t/a,居第二位。
恒力石化采用英威达P8技术建设两套PTA装置
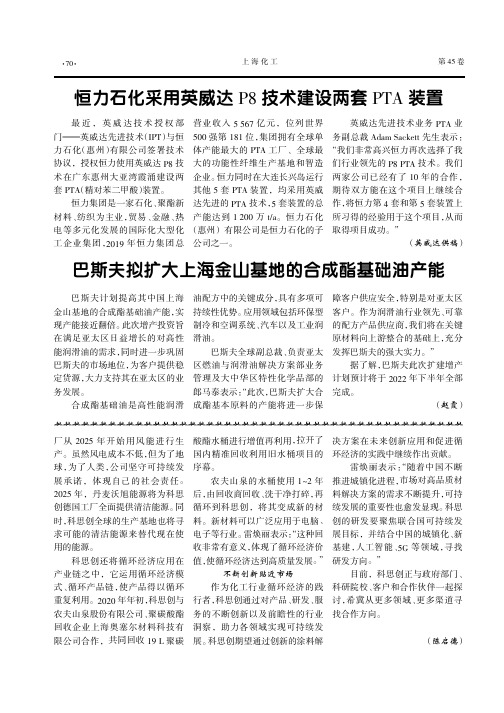
恒力石化采用英威达P8技术建设两套PTA装置最近,英威达技术授权部门———英威达先进技术(IPT)与恒力石化(惠州)有限公司签署技术协议,授权恒力使用英威达P8技术在广东惠州大亚湾霞涌建设两套PTA(精对苯二甲酸)装置。
恒力集团是一家石化、聚酯新材料、纺织为主业,贸易、金融、热电等多元化发展的国际化大型化工企业集团,2019年恒力集团总营业收入5567亿元,位列世界500强第181位,集团拥有全球单体产能最大的PTA工厂、全球最大的功能性纤维生产基地和智造企业。
恒力同时在大连长兴岛运行其他5套PTA装置,均采用英威达先进的PTA技术,5套装置的总产能达到1200万t/a。
恒力石化(惠州)有限公司是恒力石化的子公司之一。
英威达先进技术业务PTA业务副总裁Adam Sackett先生表示:“我们非常高兴恒力再次选择了我们行业领先的P8PTA技术。
我们两家公司已经有了10年的合作,期待双方能在这个项目上继续合作,将恒力第4套和第5套装置上所习得的经验用于这个项目,从而取得项目成功。
”(英威达供稿)厂从2025年开始用风能进行生产。
虽然风电成本不低,但为了地球,为了人类,公司坚守可持续发展承诺,体现自己的社会责任。
2025年,丹麦沃旭能源将为科思创德国工厂全面提供清洁能源。
同时,科思创全球的生产基地也将寻求可能的清洁能源来替代现在使用的能源。
科思创还将循环经济应用在产业链之中,它运用循环经济模式、循环产品链,使产品得以循环重复利用。
2020年年初,科思创与农夫山泉股份有限公司、聚碳酸酯回收企业上海奥塞尔材料科技有限公司合作,共同回收19L聚碳酸酯水桶进行增值再利用,拉开了国内精准回收利用旧水桶项目的序幕。
农夫山泉的水桶使用1~2年后,由回收商回收、洗干净打碎,再循环到科思创,将其变成新的材料。
新材料可以广泛应用于电脑、电子等行业。
雷焕丽表示:“这种回收非常有意义,体现了循环经济价值,使循环经济达到高质量发展。
综述PTA生产工艺发展历史及现状的演变过程知识讲解
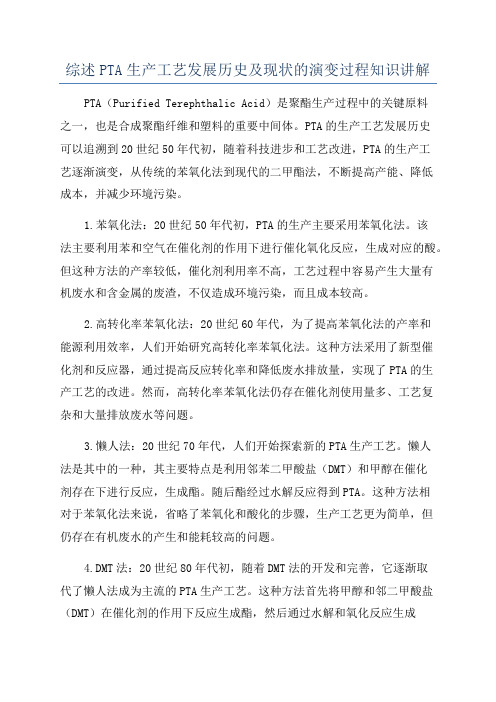
综述PTA生产工艺发展历史及现状的演变过程知识讲解PTA(Purified Terephthalic Acid)是聚酯生产过程中的关键原料之一,也是合成聚酯纤维和塑料的重要中间体。
PTA的生产工艺发展历史可以追溯到20世纪50年代初,随着科技进步和工艺改进,PTA的生产工艺逐渐演变,从传统的苯氧化法到现代的二甲酯法,不断提高产能、降低成本,并减少环境污染。
1.苯氧化法:20世纪50年代初,PTA的生产主要采用苯氧化法。
该法主要利用苯和空气在催化剂的作用下进行催化氧化反应,生成对应的酸。
但这种方法的产率较低,催化剂利用率不高,工艺过程中容易产生大量有机废水和含金属的废渣,不仅造成环境污染,而且成本较高。
2.高转化率苯氧化法:20世纪60年代,为了提高苯氧化法的产率和能源利用效率,人们开始研究高转化率苯氧化法。
这种方法采用了新型催化剂和反应器,通过提高反应转化率和降低废水排放量,实现了PTA的生产工艺的改进。
然而,高转化率苯氧化法仍存在催化剂使用量多、工艺复杂和大量排放废水等问题。
3.懒人法:20世纪70年代,人们开始探索新的PTA生产工艺。
懒人法是其中的一种,其主要特点是利用邻苯二甲酸盐(DMT)和甲醇在催化剂存在下进行反应,生成酯。
随后酯经过水解反应得到PTA。
这种方法相对于苯氧化法来说,省略了苯氧化和酸化的步骤,生产工艺更为简单,但仍存在有机废水的产生和能耗较高的问题。
4.DMT法:20世纪80年代初,随着DMT法的开发和完善,它逐渐取代了懒人法成为主流的PTA生产工艺。
这种方法首先将甲醇和邻二甲酸盐(DMT)在催化剂的作用下反应生成酯,然后通过水解和氧化反应生成PTA。
DMT法利用了二甲酯的化学反应来实现一步生成PTA,相比于懒人法,它更具经济效益和环境友好。
5.现代的二甲酯法:20世纪90年代以后,随着科技的进步和工艺的改进,PTA的生产工艺进一步发展,并逐渐向现代的二甲酯法演变。
现代的二甲酯法首先将对二甲苯和甲醇催化反应生成二甲酯,然后通过水解和氧化反应得到PTA。
PTA生产工艺比较

PTA生产工艺比较PTA生产工艺在发展过程中,形成了Amoco、三井、ICI、Eastman 4种主要的专利技术。
这4种技术的共同点是均采用Amoco-MC液相催化氧化方法,催化剂为钴-锰-溴体系,溶剂为醋酸,不同之处是各种工艺的氧化反应温度不同(从205 ℃到160 ℃) ,相应的工艺条件、反应器形式、流程设计也有所不同。
ICI和Amoco反应温度最高,三井-Amoco温度居中,而Eastman最低,一些文献上分别称为高温氧化、中温氧化和低温氧化工艺。
高温氧化的反应速率快、单位容积生产能力高,所以在相同产量条件下,反应釜体积小, CTA 晶体粒径大,含水量高,采用搅拌器来强化釜内物料的传质和混合。
不足之处是醋酸和PX消耗比低温氧化高,设备造价也高,因为氧化釜处于高温高压条件,还需要有搅拌器等动设备,配置的空气压缩机造价也很高。
低温工艺单位容积生产能力较低,采用鼓泡塔即可满足传质要求,反应器属于静设备,制造容易。
不足之处是脱水负荷大,需要增加脱水设备,晶体粒径小,浆料还需要进行二次氧化。
中温工艺介于高温和低温二者之间。
从工艺流程方面,Amoco、三井、ICI都是氧化后的CTA通过加氢工序获得PTA 产品。
Eastman的PTA生产工艺则有相当大的不同。
氧化反应器出来的浆料经洗涤处理后直接进入二次氧化反应器, 进行晶体深度氧化, 然后通过几级结晶精制,最后经熟化后得到聚合级(膜、瓶级)的对苯二甲酸产品(市场上也称为EPTA)。
通过比较得知, Eastman工艺与现有的PTA 生产工艺(英威达、BP-Amoco、三井等)有4点显著的不同: 1)较低的PX氧化温度; 2)鼓泡而不带搅拌器的反应器;3)不用加氢精制而采用二次氧化、重结晶以及熟化的工艺; 4)母液除杂质流程。
Eastman生产的PTA与其他公司生产的PTA的产品品质指标有所差异。
从产品品质指标看,杂质总量相差不多。
一个是4-CBA含量高,一个是PT酸含量高,平均粒径差距较大。
PTA合成工艺简介

PTA生产技术及工艺流程简述目前世界PTA生产厂家采用旳技术虽有差别,但归纳起来,大体可分为如下两类:(1)精PTA工艺此工艺采用催化氧化法将对二甲苯(PX)氧化成粗TA,再以加氢还原法除去杂质,将CTA精制成PTA。
这种工艺在PTA生产中居主导地位,代表性旳生产厂商有:英国石油(BP)、杜邦(Dupont)、三井油化(MPC)、道化学-因卡(Dow-INCA)、三菱化学(MCC)和因特奎萨(Interquisa)等。
(2)优质聚合级对苯二甲酸(QTA、EPTA)工艺此工艺采用催化氧化法将PX氧化成粗TA,再用进一步深度氧化措施将粗TA精制成聚合级TA。
此工艺路线旳代表生产厂商有三菱化学(MCC)、伊斯特曼(Eastman)、杜邦(Dupont)、东丽(Toray)等。
生产能力约占PTA 总产能旳16%。
两种工艺路线差别在于精制措施不同,产品质量也有所差别。
即两种产品所含杂质总量相称,但杂质种类不同样。
PTA 产品中所含PT酸较高(200ppm左右),4-CBA较低(25ppm左右),而QTA(或EPTA)产品中所含杂质与PTA相反,4-CBA较高(250ppm 左右),PT酸较低(25ppm如下)。
两种工艺路线旳产品用途基本相似,均用于聚酯生产,最后产品长短丝、瓶片旳质量差别不大。
目前,钴-锰-溴三元复合体系是PX氧化旳最佳催化剂,其中钴是最贵旳,因此目前该方面旳始终进行减少氧化催化剂能耗旳研究。
PTA生产过程中所用TA加氢反映催化剂为Pd/C,目前研究旳重要问题是如何延长催化剂旳使用寿命。
工业化旳精对苯二甲酸制备工艺诸多,但随着生产工艺旳不断发展,对二甲苯高温氧化法成为制备精对苯二甲酸旳最重要旳生产工艺,这种工艺在对苯二甲酸旳制备工艺中占有绝对优势。
对二甲苯高温氧化工艺是在高温、高压下进行旳,副反映较多;并且由于温度高、压力大对设备自身旳规定就高。
因此工艺改善重要就集中在减少氧化反映温度和减少氧化反映旳压力两个方面。
PTA生产技术与工艺流程介绍
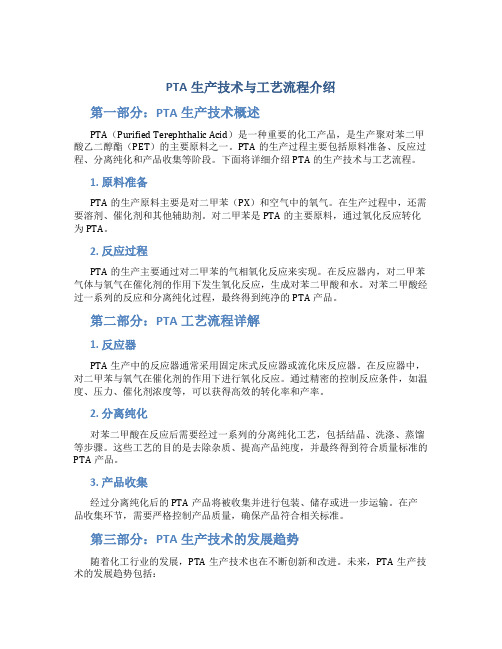
PTA生产技术与工艺流程介绍第一部分:PTA生产技术概述PTA(Purified Terephthalic Acid)是一种重要的化工产品,是生产聚对苯二甲酸乙二醇酯(PET)的主要原料之一。
PTA的生产过程主要包括原料准备、反应过程、分离纯化和产品收集等阶段。
下面将详细介绍PTA的生产技术与工艺流程。
1. 原料准备PTA的生产原料主要是对二甲苯(PX)和空气中的氧气。
在生产过程中,还需要溶剂、催化剂和其他辅助剂。
对二甲苯是PTA的主要原料,通过氧化反应转化为PTA。
2. 反应过程PTA的生产主要通过对二甲苯的气相氧化反应来实现。
在反应器内,对二甲苯气体与氧气在催化剂的作用下发生氧化反应,生成对苯二甲酸和水。
对苯二甲酸经过一系列的反应和分离纯化过程,最终得到纯净的PTA产品。
第二部分:PTA工艺流程详解1. 反应器PTA生产中的反应器通常采用固定床式反应器或流化床反应器。
在反应器中,对二甲苯与氧气在催化剂的作用下进行氧化反应。
通过精密的控制反应条件,如温度、压力、催化剂浓度等,可以获得高效的转化率和产率。
2. 分离纯化对苯二甲酸在反应后需要经过一系列的分离纯化工艺,包括结晶、洗涤、蒸馏等步骤。
这些工艺的目的是去除杂质、提高产品纯度,并最终得到符合质量标准的PTA产品。
3. 产品收集经过分离纯化后的PTA产品将被收集并进行包装、储存或进一步运输。
在产品收集环节,需要严格控制产品质量,确保产品符合相关标准。
第三部分:PTA生产技术的发展趋势随着化工行业的发展,PTA生产技术也在不断创新和改进。
未来,PTA生产技术的发展趋势包括:1.节能减排:PTA生产过程中的能源消耗和排放是行业关注的重点,未来将致力于提高能源利用率,减少排放量,实现绿色生产。
2.自动化智能化:未来PTA生产将更加智能化,引入先进的控制系统和自动化设备,提高生产效率和品质稳定性。
3.高效环保技术:未来PTA生产技术将重点研究环保工艺,如废水处理、固体废弃物处理等方面的技术,实现资源循环利用和零排放目标。
成本大揭秘!恒力石化、嘉兴石化、独山能源的PTA装置成本对比!

成本大揭秘!恒力石化、嘉兴石化、独山能源的PTA装置成本对比!PTA产品是连接着石化和化纤两大产业的重要纽带,其生产技术成熟稳定,投资门槛较低,被行业所公认。
但是平头哥发现,PTA龙头企业却能以较低的投资成本快速扩张,以迅速抢占市场为动机,他们是如何做到的?本文,平头哥将通过几个代表性PTA企业的成本对比,为大家揭秘规模化企业的成本构成。
图1:PTA产业链流程图截至2018年末,我国超过100万吨产能的PTA生产企业主要包括逸盛集团、福海创、恒力石化、三房巷海伦石化、珠海BP、桐昆嘉兴、江苏虹港石化、华彬石化、扬子石化、台化宁波、江阴汉邦和仪征石化,主要产能集中在华东、华南、东北地区,其中华东地区约占据国内总产能的45.76%,华南地区约占据国内总产能23.99%,东北地区约占据总产能的26.91%,其他地区约占据总产能的3.34%附近。
图2:中国PTA企业分布图目前PTA行业产能最大的两家企业是逸盛和恒力,其两家企业产能共约占全国总产能的40%,考虑到实际装置运行情况,尤其是2018年年底福海创的复产,逸盛与恒力两家企业的运行产能占全国正常运行PTA总产能的48%左右。
2020年开始,国内的PTA项目投资在沉寂了两年之后,又再度火热起来——2020年预计投放产能达到1200万吨、2021年预计也将有1020万吨之多。
PTA投资的主体主要有两类:一类是传统的PTA巨头——以逸盛、恒力为代表,投资的核心诉求是巩固市场份额、增强规模优势;另一类是各地的聚酯龙头——以桐昆、新凤鸣与福建百宏为代表,这类企业投资PTA项目的诉求是保障PTA供应、延长产业链稳定风险。
图3:2019年及之后新增PTA产能1、恒力石化PTA装置成本分析恒力石化的PTA装置一直以来都是采用的INVISTA的技术,在新增的#4、#5两套250万吨/年的装置上也不例外。
根据环评文件,恒力石化PTA#4、#5的投资均不到30亿人民币,尽管都是采用了INVISTA-P8技术,但是由于罐区与相关的公共工程投资更少,因而总投资相比嘉兴石化二期也有进一步的下降,同时,在PX的单耗上略有降低(从652kg/tPTA降至650kg/tPTA)。
PTA的生产技术进展

PTA的生产技术进展
发表日期: 2003-1-22 17:00:50
PTA由对二甲苯在醋酸溶剂中进行液相氧化制取,采用醋酸钴催化剂。
氧化反应条件大体是:温度185~200℃,压力0.98~1.5MPa,在立式罐反应器内进行气液相鼓泡反应。
BP和杜邦公司拥有专有技术,三菱化学、依斯曼化学和三井化学公司也开发有竞争性工艺。
BP公司最近还开发了环保型PTA生产工艺,可使废水和气体污染排放减少3倍,固体废物减少一半,挥发性有机化合物(VOC)排放基本消除。
该工艺应用于我国珠海和台湾的PTA装置,以及美国新建的70万吨/年PTA装置中。
英国诺丁汉(Nottinghom)大学与杜邦聚酯技术公司合作,开发了在超临界水(ScH2O)中从对二甲苯生产对苯二甲酸的连续法绿色工艺。
对二甲苯先被氧部分氧化,氧就地从过氧化氢在预热器中分解产生,在ScH2O中和400℃下,再用溴化锰进行催化,可高产率地得到对苯二甲酸,选择性超过90%。
与现有工艺相比,该反应路线可大大提高能效和减少废物。
在常规的对二甲苯在醋酸中氧化生产对二甲苯的路线中,水的存在降低了溴化锰催化剂的活性。
新工艺路线在ScH2O中进行反应,因为超临界流体的极性低于液体水的极性,催化剂不会有太大的失活。
PTA装置建设趋向于大型化,新建75万吨/年PTA装置的每吨生产成本可比新建30万吨/年PTA装置低150美元。
预计今后5年内将兴建80万吨/年或更大的PTA装置。
PTA生产技术及工艺流程

PTA生产技术及工艺流程PTA(对苯二甲酸 terephthalic acid)是合成聚酯纤维(聚酯纤维和聚酯菱苯酸纤维)的重要原料。
下面将介绍PTA的生产技术及工艺流程。
PTA生产技术主要有两种,一种是间位:通过对二甲苯进行氧化反应得到间苯二甲酸,再经过脱羧获得PTA。
另一种是对位:通过对甲苯进行三步反应,首先进行甲苯硝化反应得到硝基甲苯,然后还原得到对甲苯,最后通过氧化反应得到对苯二甲酸,再经过脱羧获得PTA。
PTA的工艺流程大致分为原料处理、反应过程以及PTA的脱羧过程。
首先,原料处理。
这个过程包括对原材料的处理和准备,主要包括对二甲苯、苯、空气、反应剂等的净化过程,以确保反应的纯度和稳定性。
其次,是反应过程。
反应过程包括苯和二甲苯的氧化过程,主要有间位和对位两种生产工艺流程。
如果选择的是间位工艺,首先将二甲苯蒸汽与空气加热至适当温度后送入氧化器,通过催化剂的作用进行氧化反应,生成间苯二甲酸,然后将得到的间苯二甲酸通过脱羧得到PTA。
如果选择的是对位工艺,首先对甲苯进行硝化反应,生成硝基甲苯,然后进行还原反应,得到对甲苯,最后通过氧化反应得到对苯二甲酸,再通过脱羧得到PTA。
最后,是PTA的脱羧过程。
脱羧过程是将得到的苯二甲酸(包括间苯二甲酸和对苯二甲酸)进行脱羧反应,生成PTA。
脱羧过程主要有两种方法,一种是熔融法,即将苯二甲酸加热至高温,使其发生脱羧反应,生成PTA;另一种是溶液法,即将苯二甲酸溶解在溶剂中,在催化剂的作用下进行脱羧反应,生成PTA。
综上所述,PTA的生产技术及工艺流程包括原料处理、反应过程以及PTA的脱羧过程。
通过科学的生产技术和合理的工艺流程,可以高效地生产出优质的PTA,确保聚酯纤维的质量和稳定性。
- 1、下载文档前请自行甄别文档内容的完整性,平台不提供额外的编辑、内容补充、找答案等附加服务。
- 2、"仅部分预览"的文档,不可在线预览部分如存在完整性等问题,可反馈申请退款(可完整预览的文档不适用该条件!)。
- 3、如文档侵犯您的权益,请联系客服反馈,我们会尽快为您处理(人工客服工作时间:9:00-18:30)。
各家PTA工艺技术对比评析
【更新时间:2010-11-6 13:20:44 文章录入:中国PTA行业网站】
前言
精对苯二甲酸(purified terephthalic acid简称PTA)是生产聚酯的重要原料,对苯二甲酸是无色针状结晶或无定型粉末(外观为白色粉末),无毒、有刺激性,粉尘具有爆炸性,在常温下与空气混合达到一定质量浓度时会发生爆炸,其最低爆炸浓度为0.05克/升。
分子量166.13,密度1.510克/厘米3,比热0.2873卡/克·度,升华热23.5千卡/克分子,熔点(在封管中)425℃,升华点402℃,能溶于碱溶液,稍溶于热乙醇,微溶于水。
我国聚酯工业的超速成长,极大地刺激了PTA投资的快速增长,从而加快了PTA项目的工艺引进,上述成果也不同程度地在新建或改建的PTA装置中得到了应用。
我国从20世纪70年代中期开始引进PTA 生产装置,目前已形成相当的生产规模。
但我国PTA装置建设的关键技术仍然依靠进口,基础研究薄弱,能耗水平与国际先进水平比较还有相当大的差距。
我国PTA装置的生产规模已经与国际接轨,在大型化方面取得了长足的进展,但在工艺优化方面,特别是基础研究方面仍然有待开发。
下面将各家PTA生产工艺技术进行对比,来分析各个工艺的优缺点。
各家PTA工艺技术比较
工艺技术
各专利商都拥有工业化生产PTA的专利技术,拥有近期采用最新技术的专利工厂,并生产出合格的PTA 产品。
都采用回收氧化反应副产蒸汽和反应尾气用于空压机驱动等节能措施,并将尾气用于中间产品CTA 和成品PTA输送。
溶剂回收:多数厂家为共沸蒸馏,优于常压蒸馏,筛板塔逐渐改为填料塔。
催化剂回收:工艺技术(二)的回收技术较简单,其他几家公司流程较复杂。
精制母液回收:工艺技术(六)无精制母液回收,脱盐水消耗量大, PTA损失量大,其他几家都有。
工艺条件
氧化反应温度、压力趋于降低。
工艺技术(一)(二) (三) (五) (六)为高温氧化工艺,工艺技术(四)为中温氧化工艺。
高温氧化反应温度曾先后采用230 ℃→209 ℃→196 ℃→191 ℃;中温186 ℃。
高低温氧化温度相差约50 ℃,压力相差约0. 6 MPa,主要为减少副反应,降低原料消耗。
不同的氧化反应温度,相应的反应压力、催化剂配比及反应器型式均有所不同。
设备配置
空压机:高温、中温工艺均可采用"空压机+蒸汽轮机+尾气膨胀机+电机",正常生产时,电机用来发电。
氧化反应器:高温工艺均为单台带搅拌反应釜;中温为塔式反应器,底部带搅拌、顶部带精馏段;中温工艺氧化反应器产能较小。
氧化反应器进料罐: 2000年之后引进的技术,大多采用静态混合器,取消进料混合罐。
CTA结晶:采用1段或3段结晶。
5种高温氧化工艺均采用3段结晶;中温氧化工艺仅采用1 段结晶,粒径较小。
分离及干燥: CTA均采用RVF 1道分离; PTA均采用2道分离,干燥机为列管式。
产品品质指标
各工艺技术产品品质指标没有大的差异,产品品质相近。
物耗能耗
各工艺技术均注重节能及环保。
氧化反应副产蒸汽用于蒸汽轮机和脱水塔再沸器;精制结晶闪蒸蒸汽用于浆料预热;凝液闪蒸蒸汽用于预热或伴热;氧化尾气用于尾气膨胀机驱动空压机和CTA /PTA 输送;增加氧化母液循环率,减少催化剂损失,减少除盐水消耗。
"三废"排放及治理
废气:几种专利技术排放量接近。
安全阀排放气体汇集后进入洗涤塔, 保护环境; 采用高压焚烧(HPCCU) 、低压焚烧(LPCCU)或再生热氧化(RTO)装置处理尾气,改善环境。
废水:工艺技术(一) (五)废水量较少,其余较多。
废水经过处理达到国家排放标准要求。
废渣:按照残渣中同样含水量计,废渣排放量应相近。
废渣治理大多采用焚烧或生化处理,工艺技术
(六)废渣外售。
结语
(1)各专利商都拥有工业化生产PTA的专有技术,拥有近期采用最新技术的专利工厂,均能生产出合格的产品。
引进技术应"货比三家",择优选取。
可能情况下,宜考虑技术多元化。
(2)目前,国内已引进多家PTA 专利技术, PTA装置单系列产能迅速扩大;工艺流程进一步优化;物耗、能耗显著降低;安全、环保措施进一步完善;整体技术水平显著提高。