各家PTA工艺技术对比评析
国内苯乙烯抽提装置工艺技术对比
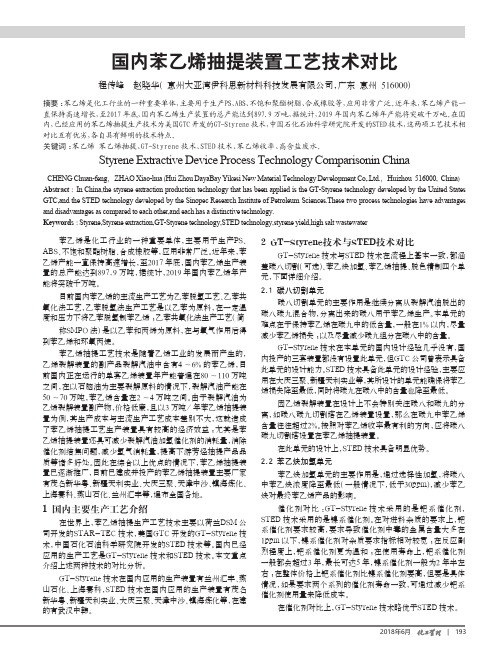
国内苯乙烯抽提装置工艺技术对比程传峰 赵晓华( 惠州大亚湾伊科思新材料科技发展有限公司,广东 惠州 516000)摘要:苯乙烯是化工行业的一种重要单体,主要用于生产PS、ABS、不饱和聚酯树脂、合成橡胶等,应用非常广泛。
近年来,苯乙烯产能一直保持高速增长,至2017年底,国内苯乙烯生产装置的总产能达到897.9万吨,据统计,2019年国内苯乙烯年产能将突破千万吨。
在国内,已经应用的苯乙烯抽提生产技术为美国GTC开发的GT-Styrene技术,中国石化石油科学研究院开发的STED技术,这两项工艺技术相对比互有优劣,各自具有鲜明的技术特点。
关键词:苯乙烯 苯乙烯抽提、GT-Styrene技术、STED技术、苯乙烯收率、高含盐废水。
Styrene Extractive Device Process Technology Comparisonin ChinaCHENG Chuan-feng,ZHAO Xiao-hua(Hui Zhou DayaBay Yikesi New Material Technology Development Co,.Ltd.,Huizhou 516000, China) Abstract:In China,the styrene extraction production technology that has been applied is the GT-Styrene technology developed by the United States GTC,and the STED technology developed by the Sinopec Research Institute of Petroleum Sciences.These two process technologies have advantages and disadvantages as compared to each other,and each has a distinctive technology.Keywords:Styrene,Styrene extraction,GT-Styrene technology,STED technology,styrene yield,high salt wastewater苯乙烯是化工行业的一种重要单体,主要用于生产PS、ABS、不饱和聚酯树脂、合成橡胶等,应用非常广泛。
PTA装置工艺介绍1

中温氧化工艺以BP-Amoco工艺、Invista工艺和日本三井油化工艺 为代表,氧化反应温度在190-205℃。日本三井油化工艺经过不断的 优化,采用高催化剂操作,目前反应温度已降至185℃,使醋酸和PX 的消耗大大降低。
Invista工艺使装置操作更稳定,能耗和物耗更低,单套装置生产能 力更大,使其更具有竞争力。近期国内新建装置所选择的专利技术大 部分为Invista工艺。
中国石化扬子石油化工有限公司化工厂
主要内容
PTA产品介绍 PTA生产原理 PTA工业化生产方法 PTA生产工艺技术发展情况 扬子石化化工厂PTA生产装置介绍
PTA产品介绍
PTA是精对苯二甲酸(Pure Terephthalic Aicd)的 英文缩写,常温下是白色晶体,常压下在300℃以上 升华,无毒、无味,是重要的大宗化工原料之一。
PTA生产工艺技术发展情况
当今PTA技术发展以降低投资、减少物耗能耗、提高产 品质量、最终增强竞争力为核心。明显的技术发展趋势 是生产系列大型化、工艺流程简化、装置布局紧凑,工 艺操作低温、低压,以及强化环保设施等。
PX氧化生产方法
在空气氧化过程中,占空气体积分数79% 的氮气只作为反应的惰性气体, 不参加反应,空气中氮气分压是氧气分压的3.76倍,由于惰性气体的存在 增加了氧化反应器的气相负荷,同时也增加了冷凝器和尾气处理等设备的 操作负荷,能耗相应增加,降低了氧化反应器等设备的生产强度。 20世纪90年代以来,Amoco等国外公司对Co-Mn-Br催化剂进行了改进, 添加了少量的过渡金属或稀土金属可溶性盐类化合物 ,可改善催化剂的性 能,提高了主反应的活性,抑制副反应,改善设备腐蚀状况。
PTA工业化生产方法
低温氧化工艺
PTA生产工艺的发展趋势
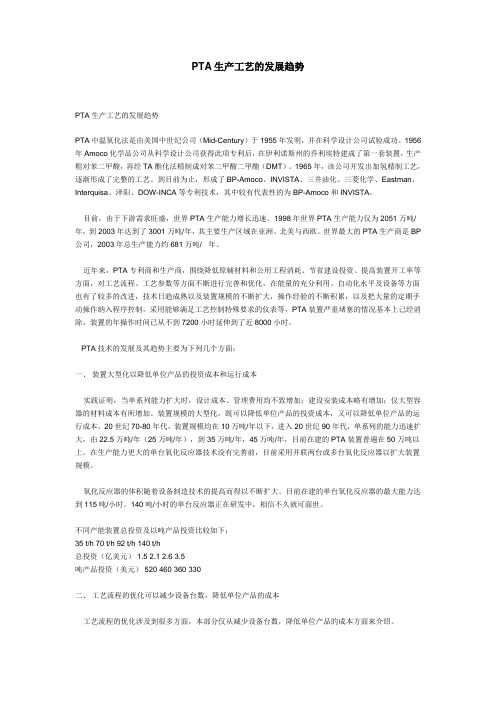
PTA生产工艺的发展趋势PTA生产工艺的发展趋势PTA中温氧化法是由美国中世纪公司(Mid-Century)于1955年发明,并在科学设计公司试验成功。
1956年Amoco化学品公司从科学设计公司获得此项专利后,在伊利诺斯州的乔利埃特建成了第一套装置,生产粗对苯二甲酸,再经TA酯化法精制成对苯二甲酸二甲酯(DMT)。
1965年,该公司开发出加氢精制工艺,逐渐形成了完整的工艺。
到目前为止,形成了BP-Amoco、INVISTA、三井油化、三菱化学、Eastman、Interquisa、泽阳、DOW-INCA等专利技术,其中较有代表性的为BP-Amoco和INVISTA。
目前,由于下游需求旺盛,世界PTA生产能力增长迅速。
1998年世界PTA生产能力仅为2051万吨/年,到2003年达到了3001万吨/年,其主要生产区域在亚洲、北美与西欧。
世界最大的PTA生产商是BP 公司,2003年总生产能力约681万吨/ 年。
近年来,PTA专利商和生产商,围绕降低原辅材料和公用工程消耗、节省建设投资、提高装置开工率等方面,对工艺流程、工艺参数等方面不断进行完善和优化,在能量的充分利用、自动化水平及设备等方面也有了较多的改进,技术日趋成熟以及装置规模的不断扩大,操作经验的不断积累,以及把大量的定期手动操作纳入程序控制,采用能够满足工艺控制特殊要求的仪表等,PTA装置严重堵塞的情况基本上己经消除,装置的年操作时间已从不到7200小时延伸到了近8000小时。
PTA技术的发展及其趋势主要为下列几个方面:一、装置大型化以降低单位产品的投资成本和运行成本实践证明,当单系列能力扩大时,设计成本、管理费用均不致增加;建设安装成本略有增加;仅大型容器的材料成本有所增加。
装置规模的大型化,既可以降低单位产品的投资成本,又可以降低单位产品的运行成本。
20世纪70-80年代,装置规模均在10万吨/年以下,进入20世纪90年代,单系列的能力迅速扩大,由22.5万吨/年(25万吨/年),到35万吨/年,45万吨/年,目前在建的PTA装置普遍在50万吨以上。
PTA生产工艺及技术研究探究
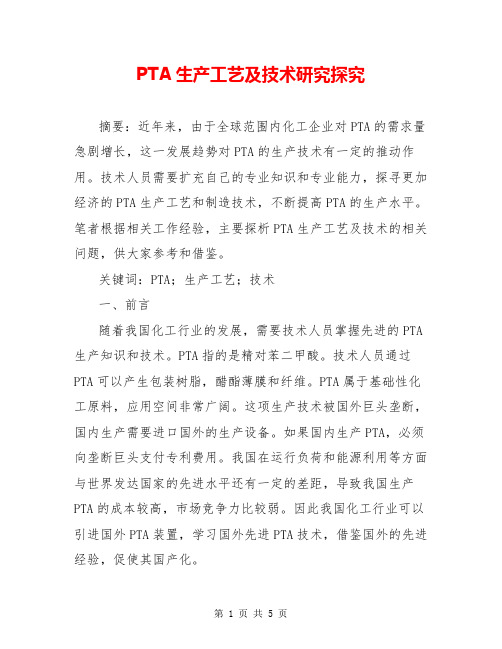
PTA生产工艺及技术研究探究摘要:近年来,由于全球范围内化工企业对PTA的需求量急剧增长,这一发展趋势对PTA的生产技术有一定的推动作用。
技术人员需要扩充自己的专业知识和专业能力,探寻更加经济的PTA生产工艺和制造技术,不断提高PTA的生产水平。
笔者根据相关工作经验,主要探析PTA生产工艺及技术的相关问题,供大家参考和借鉴。
关键词:PTA;生产工艺;技术一、前言随着我国化工行业的发展,需要技术人员掌握先进的PTA 生产知识和技术。
PTA指的是精对苯二甲酸。
技术人员通过PTA可以产生包装树脂,醋酯薄膜和纤维。
PTA属于基础性化工原料,应用空间非常广阔。
这项生产技术被国外巨头垄断,国内生产需要进口国外的生产设备。
如果国内生产PTA,必须向垄断巨头支付专利费用。
我国在运行负荷和能源利用等方面与世界发达国家的先进水平还有一定的差距,导致我国生产PTA的成本较高,市场竞争力比较弱。
因此我国化工行业可以引进国外PTA装置,学习国外先进PTA技术,借鉴国外的先进经验,促使其国产化。
二、PTA生产工艺分析PTA生产需要专业性和综合性较强的生产工艺。
同时也需要技术人员掌握先进的知识和生产工艺,在生产过程中按照工艺要求和操作规范进行操作,在此基础上才能保证生产过程各项操作工艺符合标准要求。
1)EPTA工艺分析。
EPTA和PTA产品质量指标有一定的差异,但是二者在应用方面并没有太大的差异。
技术人员在生产非纤用聚酯时,可以将PTA用EPTA代替。
EPTA的工艺主要分为三个方面,主要包括回收催化剂,聚合级对苯二甲酸生产和粗对苯二甲酸生产等,再利用液相催化氧化反应去除贫溶剂杂质。
在后氧化单元中,CTA可以提纯为EPTA,这样苯二甲酸中的杂质会消除,悬浮固体可以作为残渣被分离出去,技术人员利用流化床焚烧炉对残渣进行处理,从滤液中可以去除可溶性杂质,经过溶解后的催化剂可以循环利用。
这一工艺需要的操作步骤比较少,因此需要的操作费用较少。
苯乙烯工艺技术对比

摘要 : 概 述 了 国 内外苯 乙烯 生产技 术 的研 究进展 及 工 艺原 理 , 对各 工 艺技 术 的制 备 流 程及 工 艺 特 点进 行 了详 细介 绍 , 同时对 比 阐明 了各 生产 工艺 的优缺 点 。 关 键词 : 苯 乙烯 ; 技 术对 比 ; 反 应
d o i : 1 0 . 3 9 6 9 / j . i s s n . 1 0 0 8 — 1 2 6 7 . 2 0 1 7 . 0 3 . 0 1 4
式为反应 提供 能量 , 反 应 器 型 式 主 要 采 用 绝 热 式
固定 床 反应 器 。
1 鲁姆斯技术
自2 0世 纪 7 0年 代 , 苯 乙烯 工 艺 得 到快 速 的 发 展, 反 应 器发 展 经 历 了单 级 轴 向反 应 器 _ 双 级 轴 向 反 应 器 一 双级 径 向 反 应 器 一 双 级 径 向 反 应 器 的 各 种 组 合优 化 的多 种 反应 器 , 反应 器 操 作 压力 经 历 了
第3 1 卷第
津
化
工
Vo l _ 3l No . 3 Ma v . 2 01 7
T i a n j i n C h e mi c a l I n d u s t r y
苯 乙烯 工 艺 技 术 对 比
韩龙 , 陈君 君
( 天 津大沽化 工股份 有限公 司环氧丙烷分厂 , 天津3 0 0 4 5 5 )
收稿 日期 : 2 0 1 7 一 O 1 —1 6 作 者简介 : 韩龙 ( 1 9 8 9 一 ) , 男, 本科学 历 , 助理 工程师 , 主要负责 环氧 丙 烷生产的工艺改造和工艺管理工作 。
中互有参杂 的情况发生 。因此 在分包成本控制及 分包质量控制方 面 , 出现 了互 有 牵 制 , 互 有 影 响 的 情况 。这种局 面的出现需要联 合体双方本着合作 为先 的原则 , 互相信任 , 互相监督 。 珠海项 目在实 际运 作 中 , 派 遣 联 合 设 计 团 队驻 守 在 施 工 现场 , 任
综述PTA生产工艺发展历史及现状的演变过程知识讲解
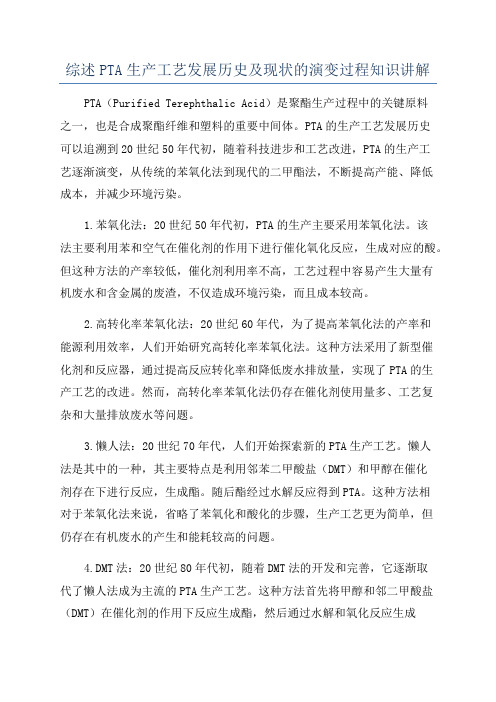
综述PTA生产工艺发展历史及现状的演变过程知识讲解PTA(Purified Terephthalic Acid)是聚酯生产过程中的关键原料之一,也是合成聚酯纤维和塑料的重要中间体。
PTA的生产工艺发展历史可以追溯到20世纪50年代初,随着科技进步和工艺改进,PTA的生产工艺逐渐演变,从传统的苯氧化法到现代的二甲酯法,不断提高产能、降低成本,并减少环境污染。
1.苯氧化法:20世纪50年代初,PTA的生产主要采用苯氧化法。
该法主要利用苯和空气在催化剂的作用下进行催化氧化反应,生成对应的酸。
但这种方法的产率较低,催化剂利用率不高,工艺过程中容易产生大量有机废水和含金属的废渣,不仅造成环境污染,而且成本较高。
2.高转化率苯氧化法:20世纪60年代,为了提高苯氧化法的产率和能源利用效率,人们开始研究高转化率苯氧化法。
这种方法采用了新型催化剂和反应器,通过提高反应转化率和降低废水排放量,实现了PTA的生产工艺的改进。
然而,高转化率苯氧化法仍存在催化剂使用量多、工艺复杂和大量排放废水等问题。
3.懒人法:20世纪70年代,人们开始探索新的PTA生产工艺。
懒人法是其中的一种,其主要特点是利用邻苯二甲酸盐(DMT)和甲醇在催化剂存在下进行反应,生成酯。
随后酯经过水解反应得到PTA。
这种方法相对于苯氧化法来说,省略了苯氧化和酸化的步骤,生产工艺更为简单,但仍存在有机废水的产生和能耗较高的问题。
4.DMT法:20世纪80年代初,随着DMT法的开发和完善,它逐渐取代了懒人法成为主流的PTA生产工艺。
这种方法首先将甲醇和邻二甲酸盐(DMT)在催化剂的作用下反应生成酯,然后通过水解和氧化反应生成PTA。
DMT法利用了二甲酯的化学反应来实现一步生成PTA,相比于懒人法,它更具经济效益和环境友好。
5.现代的二甲酯法:20世纪90年代以后,随着科技的进步和工艺的改进,PTA的生产工艺进一步发展,并逐渐向现代的二甲酯法演变。
现代的二甲酯法首先将对二甲苯和甲醇催化反应生成二甲酯,然后通过水解和氧化反应得到PTA。
PTA国产化技术简析

PTA国产化技术简析1.PTA过程开发思路PX氧化涉及气液固一系列自由基反应、化学吸收、反应结晶、强放热与蒸发移热,机理十分复杂。
氧化流程涉及反应、精馏、蒸发、吸收、结晶、过滤、换热、干燥、能量回收等多个单元,系统结构也十分复杂。
过程的开发包括两部分工作:一是氧化反应器的开发,二是氧化流程的最优设计,前者采用化学反应工程的规范方法进行研究,后者采用过程系统工程的方法进行模拟和优化。
整个开发工作包括以下步骤:1)热模实验:开发了专门的实验技术,系统考察了温度、PX浓度、催化剂浓度与配比、气相氧浓度、含水量各种因素对液相各步主反应速率、燃烧副反应速率、TA结晶速率与杂质含量的影响,获得了全新的氧化机理认识与动力学模型,能够准确预测工业条件下各种工艺参数变化对反应过程的影响。
2)冷模实验:建立了大型冷模实验装置考察反应器流动与传递规律,考察了流型、搅拌功率、操作气速、固含率等因素对反应器混合、固体悬浮、气含率、气液传质速率的影响,获得了有关的流动图象与传递数据。
3)数学模拟:针对搅拌釜和鼓泡塔两类反应器以及高温、中温、低温四种主流氧化工艺,分别建立了反应器数学模型和相关的工程数据库。
模型全面描述了工业反应器中的氧化反应、气液传质、相平衡、放热与移热、成核与结晶多种过程;数据库包括六类基础数据:反应动力学数据、结晶动力学与热力学数据、冷模传递数据、气液平衡数据、热物性数据、反应器结构与操作数据。
模型模拟结果与各种工况下的工业现场数据相符。
4)新型氧化反应器开发:在对各类氧化工艺与氧化反应器透彻剖析的基础上,浙江大学开发了新型的鼓泡塔式氧化装置,反应器由上部精馏塔与下部鼓泡塔组成,可直接利用反应热进行溶剂脱水,有利节能(专利2003101078895,200320108899.6,200510048977.1,200520100244.3)。
新型氧化反应器结构简单,造价低廉,具有深厚的研究开发基础,能够满足氧化反应、气液传质、混合、固体悬浮等多方面的要求。
精对苯二甲酸(PTA)行业分析报告
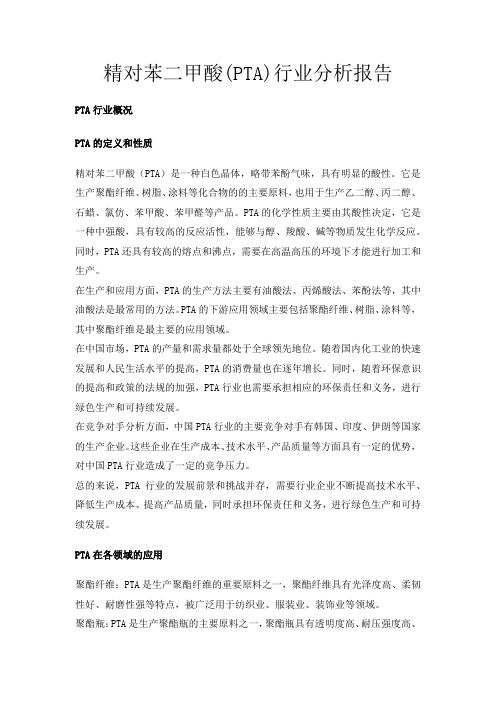
精对苯二甲酸(PTA)行业分析报告PTA行业概况PTA的定义和性质精对苯二甲酸(PTA)是一种白色晶体,略带苯酚气味,具有明显的酸性。
它是生产聚酯纤维、树脂、涂料等化合物的的主要原料,也用于生产乙二醇、丙二醇、石蜡、氯仿、苯甲酸、苯甲醛等产品。
PTA的化学性质主要由其酸性决定,它是一种中强酸,具有较高的反应活性,能够与醇、羧酸、碱等物质发生化学反应。
同时,PTA还具有较高的熔点和沸点,需要在高温高压的环境下才能进行加工和生产。
在生产和应用方面,PTA的生产方法主要有油酸法、丙烯酸法、苯酚法等,其中油酸法是最常用的方法。
PTA的下游应用领域主要包括聚酯纤维、树脂、涂料等,其中聚酯纤维是最主要的应用领域。
在中国市场,PTA的产量和需求量都处于全球领先地位。
随着国内化工业的快速发展和人民生活水平的提高,PTA的消费量也在逐年增长。
同时,随着环保意识的提高和政策的法规的加强,PTA行业也需要承担相应的环保责任和义务,进行绿色生产和可持续发展。
在竞争对手分析方面,中国PTA行业的主要竞争对手有韩国、印度、伊朗等国家的生产企业。
这些企业在生产成本、技术水平、产品质量等方面具有一定的优势,对中国PTA行业造成了一定的竞争压力。
总的来说,PTA行业的发展前景和挑战并存,需要行业企业不断提高技术水平、降低生产成本、提高产品质量,同时承担环保责任和义务,进行绿色生产和可持续发展。
PTA在各领域的应用聚酯纤维:PTA是生产聚酯纤维的重要原料之一,聚酯纤维具有光泽度高、柔韧性好、耐磨性强等特点,被广泛用于纺织业、服装业、装饰业等领域。
聚酯瓶:PTA是生产聚酯瓶的主要原料之一,聚酯瓶具有透明度高、耐压强度高、耐化学性能好等特点,被广泛用于食品、饮料、化妆品等领域的包装容器。
涤纶短纤维:PTA是涤纶短纤维的重要原料之一,涤纶短纤维具有柔软、光泽、强度高等特点,被广泛用于纺织业、地毯业等领域。
化学品生产:PTA还可作为化学品生产的起点原料,生产用于塑料加工的邻苯二甲酸、苯乙烯、聚酯树脂及其他化学产品。
PTA各质量指标对聚酯生产的影响
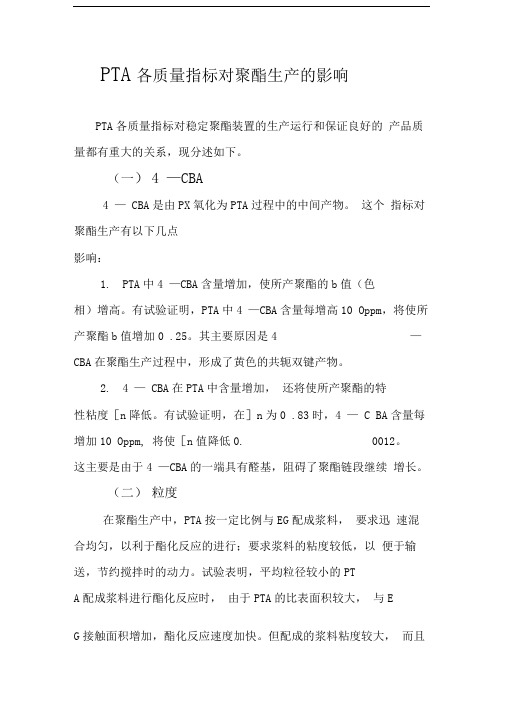
PTA各质量指标对聚酯生产的影响PTA各质量指标对稳定聚酯装置的生产运行和保证良好的产品质量都有重大的关系,现分述如下。
(一)4 —CBA4 —CBA是由PX氧化为PTA过程中的中间产物。
这个指标对聚酯生产有以下几点影响:1.PTA中4 —CBA含量增加,使所产聚酯的b值(色相)增高。
有试验证明,PTA中4 —CBA含量每增高10 Oppm,将使所产聚酯b值增加0 .25。
其主要原因是4 —CBA在聚酯生产过程中,形成了黄色的共轭双键产物。
2. 4 —CBA在PTA中含量增加,还将使所产聚酯的特性粘度[n降低。
有试验证明,在]n为0 .83时,4 — C BA含量每增加10 Oppm, 将使[n值降低0. 0012。
这主要是由于4 —CBA的一端具有醛基,阻碍了聚酯链段继续增长。
(二)粒度在聚酯生产中,PTA按一定比例与EG配成浆料,要求迅速混合均匀,以利于酯化反应的进行;要求浆料的粘度较低,以便于输送,节约搅拌时的动力。
试验表明,平均粒径较小的PTA配成浆料进行酯化反应时,由于PTA的比表面积较大,与EG接触面积增加,酯化反应速度加快。
但配成的浆料粘度较大,而且在风送时,阻力也较大。
生产实践表明,PTA的平均粒度保持不变,至为重要。
例如,在实际生产中曾遇到这样的现象,原来一直使用平均粒径为10 0 左右的PTA,后来改用另一厂家生产的PTA,在平均粒径相近时,酯化反应的温度、停留时间等工艺参数都未改变,产品质量等各方面均能符合要求。
但PTA平均粒径下降到9 7.7 ym时,上述酯化工艺参数仍未加改变,反应速度明显增加,物料酯化率偏高,导致后来进入最终缩聚反应器的物料的端羧基偏低,以致在最终缩聚过程中,帮助物料脱去EG和活性官能团减少,仅靠催化剂本身的催化作用,要达到所要求的聚合度,就比较困难。
必须采取提高真空度,延长停留时间等强化反应条件的措施,才能保证产品的粘度。
如果预先知道PTA的平均粒径,可通过改变酯化工艺参数,如降低酯化温度、缩短停留时间,就可以防止物料酯化过度或者酯化不足。
PTA装置基本知识培训和主流工艺介绍

设计产能 150 130 99 180 60 130 60 40 150 87 32.5 32.5 10 7.5
1173.5
地点 福建厦门 江苏南京 江苏仪征市 浙江绍兴
宁波 宁波 上海 上海金山 珠海 辽宁辽阳 河南洛阳 天津市 山东济南 新疆乌鲁木齐
PTA的成本核算:以07年11月22日的数据为例
3、 概述(1) 氧化工序生产的粗对苯二甲酸(CTA)由于杂质含量高而不适合生
产聚酯产品,主要杂质是来自对二甲苯氧化反应的中间产物包括羧基苯醛、 对甲苯酸和有色物质。纯度为99.7%的粗TA必须提纯到99.98%的精对苯二甲 酸才适合作为聚酯的原料,加氢精制工艺的基本反应完全是根据对二甲苯氧 化反应的逆反应原理进行的。
主要的杂质4-CBA,在加氢反应后生成对甲基苯甲酸(PT酸),由于对甲基 苯甲酸(PT酸)在水中的溶解度要比对苯二甲酸(TA)在水中的溶解度大 得多,当TA从水溶液中成晶体析出时,对甲基苯甲酸(PT酸)仍然溶解在水中 ,所以在148℃左右的温度下 ,通过离心分离,就能够很容易地把PT酸从对 苯二甲酸中分离出去,这实际上就间接地除掉了产品中的4-CBA。
一、进料准备和预热
CTA粉末从CTA干燥机M1-423A/B进到CTA料仓F1-1201A/B, F1-1201的单 个容积为3000 M3, 正常贮存量为2340吨,最大贮存量2640吨。每个CTA料 仓都有两条下料线,CTA固体通过旋转阀、下料螺旋进入进料打浆罐F11206用工艺打浆水打浆,浆料浓度为36%,温度97 ℃ ,浆料浓度是通过 密度计控制旋转阀电机的转速实现的,共有两个密度计,一个在高压溶 解器进料泵G1-1209的入口,一个在低压溶解进料泵G1-1207A/B的回流管 线上。 CTA料仓F1-1201A/B的放空物流在CTA料仓放空气体洗涤器F11202A/B中洗涤气体中夹带的CTA粉末,洗涤液回收到F1-1206,气体进入 CTA料仓放空气体除尘器F1-1205A/B用碱液喷淋洗涤后排放到大气。
PTA生产技术与工艺流程介绍
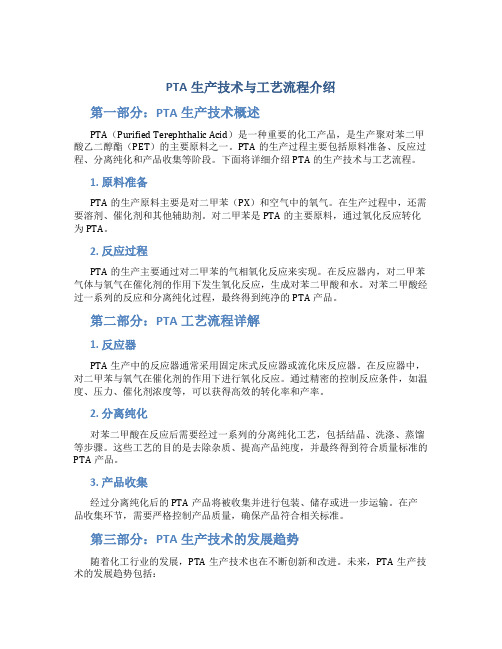
PTA生产技术与工艺流程介绍第一部分:PTA生产技术概述PTA(Purified Terephthalic Acid)是一种重要的化工产品,是生产聚对苯二甲酸乙二醇酯(PET)的主要原料之一。
PTA的生产过程主要包括原料准备、反应过程、分离纯化和产品收集等阶段。
下面将详细介绍PTA的生产技术与工艺流程。
1. 原料准备PTA的生产原料主要是对二甲苯(PX)和空气中的氧气。
在生产过程中,还需要溶剂、催化剂和其他辅助剂。
对二甲苯是PTA的主要原料,通过氧化反应转化为PTA。
2. 反应过程PTA的生产主要通过对二甲苯的气相氧化反应来实现。
在反应器内,对二甲苯气体与氧气在催化剂的作用下发生氧化反应,生成对苯二甲酸和水。
对苯二甲酸经过一系列的反应和分离纯化过程,最终得到纯净的PTA产品。
第二部分:PTA工艺流程详解1. 反应器PTA生产中的反应器通常采用固定床式反应器或流化床反应器。
在反应器中,对二甲苯与氧气在催化剂的作用下进行氧化反应。
通过精密的控制反应条件,如温度、压力、催化剂浓度等,可以获得高效的转化率和产率。
2. 分离纯化对苯二甲酸在反应后需要经过一系列的分离纯化工艺,包括结晶、洗涤、蒸馏等步骤。
这些工艺的目的是去除杂质、提高产品纯度,并最终得到符合质量标准的PTA产品。
3. 产品收集经过分离纯化后的PTA产品将被收集并进行包装、储存或进一步运输。
在产品收集环节,需要严格控制产品质量,确保产品符合相关标准。
第三部分:PTA生产技术的发展趋势随着化工行业的发展,PTA生产技术也在不断创新和改进。
未来,PTA生产技术的发展趋势包括:1.节能减排:PTA生产过程中的能源消耗和排放是行业关注的重点,未来将致力于提高能源利用率,减少排放量,实现绿色生产。
2.自动化智能化:未来PTA生产将更加智能化,引入先进的控制系统和自动化设备,提高生产效率和品质稳定性。
3.高效环保技术:未来PTA生产技术将重点研究环保工艺,如废水处理、固体废弃物处理等方面的技术,实现资源循环利用和零排放目标。
“中国制造”最大PTA装置双突破

据 了解 , 与 同期 引进 装 置相 比 , 采 用 昆 仑公 司 工
中 国 昆仑 工程 公 司 ( 原 中 国纺 织 工业 设 计 院 ) 介绍, 艺包 建设 的P TA 装置 万吨 产 品投资 节省4 0 %, 产 品 质 为摆 脱P TA技 术桎 梏 , 2 0 0 2年 , 昆仑 公司 组织 产学 研 量优 于国标优级 品指标 , 成果 整体达到 国际先进水 平 , 联合攻 关 , 开 发具 有 自主知 识产权 的大 型P T A 装置 工 其 中P X消耗等 主要技术 经济指标处于 国际领先水 平 。 艺 技术 和 成套 装 备 , 这 一项 目先后 获 得财 政 部 、 国家 此 次建 设 的 国产化P TA装 置规 模 达 1 5 0万 吨/年 , 已
产化上 又有新突破 。 万 吨/年P T A 国产化 示范 工程 , 成 功打破 国外 在该 技 术领 域的垄断 。
P TA是 聚酯 ( P E T) 工 业的 主要 原料 。 P T A装 置
集技 术密集 、 资金密集 于一体 , 是典型 、 复杂 的高温 、 高
此 次 装 置竣 工 的 虹 港P TA项 目合 同于2 0 1 1 年6
置机械 竣 工。 这是 采用 中国昆仑 工程 公司 自主P T A 工 机组 , 南京 宝钛研 制 的P X氧 化反 应器 , 中国二 重和 南
艺建 设的产 能规模 最大 的P T A装置, 8 O % 以上的 国产 化机 研制的加 氢精制 反应器 , 锦西化 机研制 的C TA和 设 备也使该 装置成 为 国产 化率最 高的P T A 装置 , 标 志 P T A 干燥机等 。 2 0 0 9年 , 昆仑公 司与蓬成石化 合作 , 采 着 我国 自主 技术P T A 装置在 工艺技 术、 规 模和装备 国 用 自主 研发 的工 艺技术 及成 套装 备 , 建成 国内首套 9 0
苯乙烯生产工艺技术对比

苯乙烯生产工艺技术对比苯乙烯是一种重要的化工原料,广泛应用于塑料、橡胶和合成纤维等行业。
目前,苯乙烯的生产工艺技术主要有烟气法和催化裂化法两种。
烟气法是传统的苯乙烯生产工艺技术之一,它的原料是乙苯和空气。
首先,将乙苯和空气混合,并通过燃烧反应生成苯乙烯。
然后,将产生的混合气体通过冷凝器冷却,得到液体苯乙烯。
这个过程的主要优点是简单、成本低,但是也存在一些不足之处。
首先,烟气法的反应温度较高,容易产生副产物和有毒物质,对环境造成污染。
其次,烟气法的乙苯利用率较低,约为70%,对资源的浪费较为严重。
此外,烟气法的产品纯度较低,需要经过进一步的提纯处理。
催化裂化法是目前最常用的苯乙烯生产工艺技术之一。
催化裂化法主要通过在催化剂的作用下,将乙苯分解为苯和乙烯,再将乙烯加氢生成苯乙烯。
催化裂化工艺的优点包括反应温度较低、产品纯度高、乙苯利用率高等。
此外,催化裂化法还可以通过改变催化剂的组成和反应条件,调整产品的比例,满足不同行业的需求。
然而,催化裂化法的成本较高,需要进行催化剂的再生和废气处理等工序,增加了工艺的复杂性。
同时,催化裂化法还面临着催化剂的选择和设计的问题,需要不断改进和优化。
综上所述,烟气法和催化裂化法是目前苯乙烯生产工艺技术的两种主要方法。
烟气法简单、成本低,但对环境造成污染并且乙苯利用率低;催化裂化法反应温度低,产品纯度高,乙苯利用率高,但成本较高并且工艺较为复杂。
随着环保意识的增强和技术的进步,一些新的苯乙烯生产工艺技术也在不断涌现,如光电催化法和电解法等。
未来,随着科学技术的进步和工艺技术的不断改进,苯乙烯的生产工艺将会变得更加环保、高效和经济。
PTA装置中离心机与压力过滤机的技术分析对比
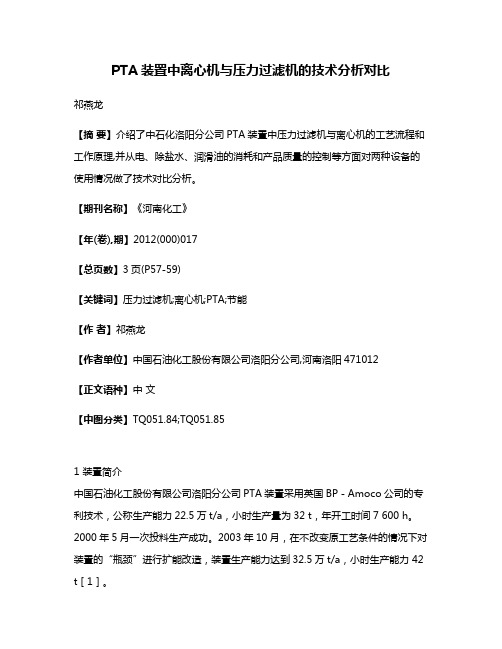
PTA装置中离心机与压力过滤机的技术分析对比祁燕龙【摘要】介绍了中石化洛阳分公司PTA装置中压力过滤机与离心机的工艺流程和工作原理,并从电、除盐水、润滑油的消耗和产品质量的控制等方面对两种设备的使用情况做了技术对比分析。
【期刊名称】《河南化工》【年(卷),期】2012(000)017【总页数】3页(P57-59)【关键词】压力过滤机;离心机;PTA;节能【作者】祁燕龙【作者单位】中国石油化工股份有限公司洛阳分公司,河南洛阳471012【正文语种】中文【中图分类】TQ051.84;TQ051.851 装置简介中国石油化工股份有限公司洛阳分公司PTA装置采用英国BP-Amoco公司的专利技术,公称生产能力22.5万t/a,小时生产量为32 t,年开工时间7 600 h。
2000年5月一次投料生产成功。
2003年10月,在不改变原工艺条件的情况下对装置的“瓶颈”进行扩能改造,装置生产能力达到32.5万t/a,小时生产能力 42 t[1]。
2 工艺流程2.1 离心机工艺流程离心机和压力过滤机属于PTA装置中精制单元的一级分离设备。
其工艺原理为在0.46 MPa、152℃的条件下,根据对苯二甲酸(PTA)与对甲基苯甲酸(PT酸)在水中溶解度的不同将PT酸除去,从而达到精制的目的。
BP-Amoco的专利技术采用三台离心机并联操作,2003年扩能后又增上了一台离心机。
自第五结晶器BD605来的浆料经离心机进料泵BG605加压后送入四台离心机BM701A/B/C/D,分离后的含水量10%~20%的滤饼通过除盐水打浆后进入再打浆罐BD702进行后续工艺处理。
被分离的富含PT酸的母液进入母液罐BD703,然后经冷却送入下游污水厂。
2.2 压力过滤机工艺流程2011年装置经过改造增上一台压力过滤机BM701,用以取代先前的四台离心机。
自第五结晶器来的浆料由BG605送入压力过滤机进料罐BD701,然后由压力过滤机进料泵BG701将浆料送入压力过滤机BM701,部分浆料溢流回BD701,其余浆料在转鼓表面形成滤饼后经过再打浆送入BD702,富含PT酸的母液被送入BD703。
各家PTA工艺技术对比评析

各家PTA工艺技术对比评析精对苯二甲酸(purified terephthalic acid 简称PTA)是生产聚酯的重要原料,对苯二甲酸是无色针状结晶或无定型粉末(外观为白色粉末),无毒、有刺激性,粉尘具有爆炸性,在常温下与空气混合达到一定质量浓度时会发生爆炸,其最低爆炸浓度为0.05克/升。
分子量166.13,密度1.510克/厘米3,比热0.2873卡/克·度,升华热23.5千卡/克分子,熔点(在封管中)425℃,升华点402℃,能溶于碱溶液,稍溶于热乙醇,微溶于水。
我国聚酯工业的超速成长,极大地刺激了PTA投资的快速增长,从而加快了PTA项目的工艺引进,上述成果也不同程度地在新建或改建的PTA装置中得到了应用。
我国从20世纪70年代中期开始引进PTA生产装置,目前已形成相当的生产规模。
但我国PTA装置建设的关键技术仍然依靠进口,基础研究薄弱,能耗水平与国际先进水平比较还有相当大的差距。
我国PTA装置的生产规模已经与国际接轨,在大型化方面取得了长足的进展,但在工艺优化方面,特别是基础研究方面仍然有待开发。
下面将各家PTA生产工艺技术进行对比,来分析各个工艺的优缺点。
工艺技术各专利商都拥有工业化生产PTA的专利技术,拥有近期采用最新技术的专利工厂,并生产出合格的PTA产品。
都采用回收氧化反应副产蒸汽和反应尾气用于空压机驱动等节能措施,并将尾气用于中间产品CTA和成品PTA输送。
溶剂回收:多数厂家为共沸蒸馏,优于常压蒸馏,筛板塔逐渐改为填料塔。
催化剂回收:工艺技术(二)的回收技术较简单,其他几家公司流程较复杂。
精制母液回收:工艺技术(六)无精制母液回收,脱盐水消耗量大, PTA损失量大,其他几家都有。
工艺条件氧化反应温度、压力趋于降低。
工艺技术(一)(二) (三) (五) (六)为高温氧化工艺,工艺技术(四)为中温氧化工艺。
高温氧化反应温度曾先后采用230 ℃→209 ℃→196 ℃→191 ℃;中温186 ℃。
PTA生产工艺比较

PTA生产工艺比较PTA生产工艺在发展过程中,形成了Amoco、三井、ICI、Eastman 4种主要的专利技术。
这4种技术的共同点是均采用Amoco-MC液相催化氧化方法,催化剂为钴-锰-溴体系,溶剂为醋酸,不同之处是各种工艺的氧化反应温度不同(从205 ℃到160 ℃) ,相应的工艺条件、反应器形式、流程设计也有所不同。
ICI和Amoco反应温度最高,三井-Amoco温度居中,而Eastman最低,一些文献上分别称为高温氧化、中温氧化和低温氧化工艺。
高温氧化的反应速率快、单位容积生产能力高,所以在相同产量条件下,反应釜体积小, CTA 晶体粒径大,含水量高,采用搅拌器来强化釜内物料的传质和混合。
不足之处是醋酸和PX消耗比低温氧化高,设备造价也高,因为氧化釜处于高温高压条件,还需要有搅拌器等动设备,配置的空气压缩机造价也很高。
低温工艺单位容积生产能力较低,采用鼓泡塔即可满足传质要求,反应器属于静设备,制造容易。
不足之处是脱水负荷大,需要增加脱水设备,晶体粒径小,浆料还需要进行二次氧化。
中温工艺介于高温和低温二者之间。
从工艺流程方面,Amoco、三井、ICI都是氧化后的CTA通过加氢工序获得PTA 产品。
Eastman的PTA生产工艺则有相当大的不同。
氧化反应器出来的浆料经洗涤处理后直接进入二次氧化反应器, 进行晶体深度氧化, 然后通过几级结晶精制,最后经熟化后得到聚合级(膜、瓶级)的对苯二甲酸产品(市场上也称为EPTA)。
通过比较得知, Eastman工艺与现有的PTA 生产工艺(英威达、BP-Amoco、三井等)有4点显著的不同: 1)较低的PX氧化温度; 2)鼓泡而不带搅拌器的反应器;3)不用加氢精制而采用二次氧化、重结晶以及熟化的工艺; 4)母液除杂质流程。
Eastman生产的PTA与其他公司生产的PTA的产品品质指标有所差异。
从产品品质指标看,杂质总量相差不多。
一个是4-CBA含量高,一个是PT酸含量高,平均粒径差距较大。
PTA产品技术简介
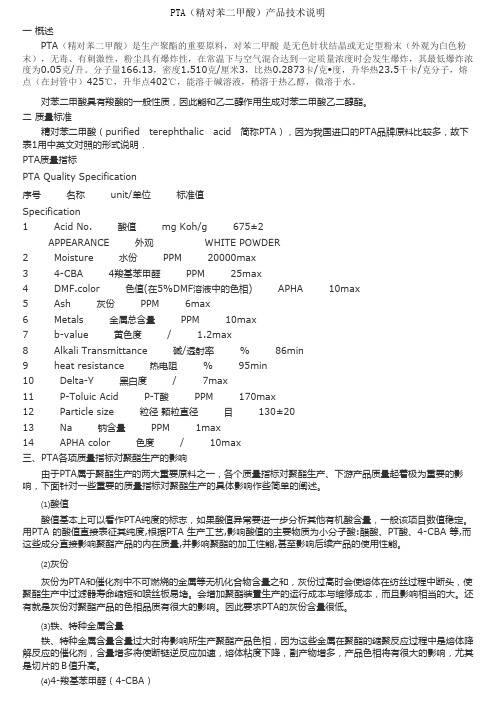
PTA(精对苯二甲酸)产品技术说明一概述 PTA(精对苯二甲酸)是生产聚酯的重要原料,对苯二甲酸是无色针状结晶或无定型粉末(外观为白色粉末),无毒、有刺激性,粉尘具有爆炸性,在常温下与空气混合达到一定质量浓度时会发生爆炸,其最低爆炸浓度为0.05克/升。
分子量166.13,密度1.510克/厘米3,比热0.2873卡/克•度,升华热23.5千卡/克分子,熔点(在封管中)425℃,升华点402℃,能溶于碱溶液,稍溶于热乙醇,微溶于水。
对苯二甲酸具有羧酸的一般性质,因此能和乙二醇作用生成对苯二甲酸乙二醇酯。
二质量标准 精对苯二甲酸(purified terephthalic acid 简称PTA),因为我国进口的PTA品牌原料比较多,故下表1用中英文对照的形式说明.PTA质量指标PTA Quality Specification序号名称 unit/单位标准值Specification1 Acid No. 酸值 mg Koh/g 675±2APPEARANCE 外观 WHITE POWDER2 Moisture 水份 PPM 20000max3 4-CBA 4羧基苯甲醛 PPM 25max4 DMF.color 色值(在5%DMF溶液中的色相) APHA 10max5 Ash 灰份 PPM 6max6 Metals 金属总含量 PPM 10max7 b-value 黄色度 / 1.2max8 Alkali Transmittance 碱/透射率 % 86min9 heat resistance 热电阻 % 95min10 Delta-Y 黑白度 / 7max11 P-Toluic Acid P-T酸 PPM 170max12 Particle size 粒径颗粒直径目 130±2013 Na 钠含量 PPM 1max14 APHA color 色度 / 10max三、PTA各项质量指标对聚酯生产的影响 由于PTA属于聚酯生产的两大重要原料之一,各个质量指标对聚酯生产、下游产品质量起着极为重要的影响,下面针对一些重要的质量指标对聚酯生产的具体影响作些简单的阐述。
pta生产工艺方案比较

pta生产工艺方案比较
本文将比较pta生产工艺中的两种方案,并对其进行评估。
两种方案分别是:
1. 纯氧气法生产工艺:该方案使用纯氧气作为氧化剂,通过氧化反应将二甲醚转化为pta。
2. 空气氧法生产工艺:该方案使用空气中的氧气作为氧化剂,通过氧化反应将二甲醚转化为pta。
以下是两种方案的比较和评估:
纯氧气法生产工艺
- 优点:
- 可以得到高纯度的pta产品。
- 氧化反应速度较快,生产效率高。
- 缺点:
- 需要纯氧气供应,成本较高。
- 氧气的使用增加了安全风险。
空气氧法生产工艺
- 优点:
- 不需要纯氧气供应,成本较低。
- 可以使用环境中的氧气作为氧化剂,更加环保。
- 缺点:
- 得到的pta产品质量相对较低。
- 由于氧化反应速度较慢,生产效率较低。
根据以上比较,两种生产工艺方案各有优缺点。
如果追求高纯度的pta产品和较高的生产效率,纯氧气法生产工艺是一个很好的选择。
然而,如果成本和环保性是更重要的考虑因素,空气氧法生产工艺可能更适合。
请注意,本文所提供的信息仅供参考,具体实施方案需根据实际情况进行评估和决策。
PTA合成工艺简介

PTA合成工艺简介PTA生产技术及工艺流程简述目前世界PTA生产厂家采用的技术虽有差异,但归纳起来,大致可分为以下两类:(1)精PTA工艺此工艺采用催化氧化法将对二甲苯(PX)氧化成粗TA,再以加氢还原法除去杂质,将CTA精制成PTA。
这种工艺在PTA生产中居主导地位,代表性的生产厂商有:英国石油(BP)、杜邦(Dupont)、三井油化(MPC)、道化学-因卡(Dow-INCA)、三菱化学(MCC)和因特奎萨(Interquisa)等。
(2)优质聚合级对苯二甲酸(QTA、EPTA)工艺此工艺采用催化氧化法将PX氧化成粗TA,再用进一步深度氧化方法将粗TA精制成聚合级TA。
此工艺路线的代表生产厂商有三菱化学(MCC)、伊斯特曼(Eastman)、杜邦(Dupont)、东丽(Toray)等。
生产能力约占PTA总产能的16%。
两种工艺路线差异在于精制方法不同,产品质量也有所差异。
即两种产品所含杂质总量相当,但杂质种类不一样。
PTA产品中所含PT酸较高(200ppm左右),4-CBA较低(25ppm 左右),而QTA(或EPTA)产品中所含杂质与PTA相反,4-CBA 较高(250ppm左右),PT酸较低(25ppm以下)。
两种工艺路线的产品用途基本相同,均用于聚酯生产,最终产品长短丝、瓶片的质量差异不大。
目前,钴-锰-溴三元复合体系是PX氧化的最佳催化剂,其中钴是最贵的,所以目前该方面的一直进行降低氧化催化剂能耗的研究。
PTA生产过程中所用TA加氢反应催化剂为Pd/C,目前研究的主要问题是如何延长催化剂的使用寿命。
工业化的精对苯二甲酸制备工艺很多,但随着生产工艺的不断发展,对二甲苯高温氧化法成为制备精对苯二甲酸的最主要的生产工艺,这种工艺在对苯二甲酸的制备工艺中占有绝对优势。
对二甲苯高温氧化工艺是在高温、高压下进行的,副反应较多;而且由于温度高、压力大对设备本身的要求就高。
因此工艺改进主要就集中在降低氧化反应温度和降低氧化反应的压力两个方面。
精对苯二甲酸(PTA)生产工艺风险分析与控制的研究的开题报告

精对苯二甲酸(PTA)生产工艺风险分析与控制的研究的开题报告一、研究背景与意义随着化学工业的快速发展,精对苯二甲酸(PTA)作为一种重要的有机合成原料得到了广泛应用,尤其是在涤纶纤维、饮料瓶、聚对苯二甲酸乙二酯等行业的生产中。
然而,PTA的生产过程中存在多种危险及风险源,并且这些风险在操作者的偏差、设备故障、原辅料质量波动、突发事件等不确定因素的干扰下,可能演变成事故,给工作人员、设备和环境带来不可预估的损失。
为此,建立PTA生产过程风险分析与控制体系,可有效地降低安全事故发生的概率,实现生产的可持续发展。
二、研究内容和思路1. 理解PTA生产中的危险和风险源通过系统调研与采集相关文献,深入了解PTA生产过程中可能出现的危险和风险源,包括化学反应危险、高温高压危险、火灾爆炸危险、设备失效危险等。
2. 分析PTA生产中的安全风险在对PTA生产过程中的危险和风险源进行全方位的了解之后,进行安全风险分析,采用常用的风险评估方法,如HAZOP,FMECA等方法,评估各个环节的安全风险,确定最严重的环节和可能引发事故的原因、条件等。
3. 制定安全风险控制和管理措施根据安全风险评估结果,针对性地提出相应的风险控制和管理措施,包括完善PTA生产过程安全规范、强化操作员安全教育培训、加强设备维护管理等方面的措施。
4. 建立PTA生产安全管理体系针对PTA生产中可能发生的安全风险,建立PTA生产安全管理体系,包括制定安全技术规范与操作规程、建立风险应急预案、设置安全监测装置、实施安全检查与评估等方面的内容。
5. 案例分析通过对PTA生产企业的现状,利用研究成果中提出的方法和措施,提高企业安全管理水平,加强安全生产工作。
三、研究目标和意义1. 确定PTA生产过程中最重要的风险源,采取有效的风险防控措施,提升企业生产安全水平,减少因为安全事故产生的经济损失和声誉损害。
2. 建立完整的PTA生产过程安全管理体系,为企业高效、可靠的生产提供技术手段与保障。
- 1、下载文档前请自行甄别文档内容的完整性,平台不提供额外的编辑、内容补充、找答案等附加服务。
- 2、"仅部分预览"的文档,不可在线预览部分如存在完整性等问题,可反馈申请退款(可完整预览的文档不适用该条件!)。
- 3、如文档侵犯您的权益,请联系客服反馈,我们会尽快为您处理(人工客服工作时间:9:00-18:30)。
各家PTA工艺技术对比评析
精对苯二甲酸(purified terephthalic acid 简称PTA)是生产聚酯的重要原料,对苯二甲酸是无色针状结晶或无定型粉末(外观为白色粉末),无毒、有刺激性,粉尘具有爆炸性,在常温下与空气混合达到一定质量浓度时会发生爆炸,其最低爆炸浓度为0.05克/升。
分子量166.13,密度1.510克/厘米3,比热0.2873卡/克·度,升华热23.5千卡/克分子,熔点(在封管中)425℃,升华点402℃,能溶于碱溶液,稍溶于热乙醇,微溶于水。
我国聚酯工业的超速成长,极大地刺激了PTA投资的快速增长,从而加快了PTA项目的工艺引进,上述成果也不同程度地在新建或改建的PTA装置中得到了应用。
我国从20世纪70年代中期开始引进PTA生产装置,目前已形成相当的生产规模。
但我国PTA装置建设的关键技术仍然依靠进口,基础研究薄弱,能耗水平与国际先进水平比较还有相当大的差距。
我国PTA装置的生产规模已经与国际接轨,在大型化方面取得了长足的进展,但在工艺优化方面,特别是基础研究方面仍然有待开发。
下面将各家PTA生产工艺技术进行对比,来分析各个工艺的优缺点。
工艺技术
各专利商都拥有工业化生产PTA的专利技术,拥有近期采用最新技术的专利工厂,并生产出合格的PTA产品。
都采用回收氧化反应副产蒸汽和反应尾气用于空压机驱动等节能措施,并将尾气用于中间产品CTA和成品PTA输送。
溶剂回收:多数厂家为共沸蒸馏,优于常压蒸馏,筛板塔逐渐改为填料塔。
催化剂回收:工艺技术(二)的回收技术较简单,其他几家公司流程较复杂。
精制母液回收:工艺技术(六)无精制母液回收,脱盐水消耗量大, PTA损失量大,其他几家都有。
工艺条件
氧化反应温度、压力趋于降低。
工艺技术(一)(二) (三) (五) (六)为高温氧化工艺,工艺技术(四)为中温氧化工艺。
高温氧化反应温度曾先后采用230 ℃→209 ℃→196 ℃→191 ℃;中温186 ℃。
高低温氧化温度相差约50 ℃,压力相差约0. 6 MPa,主要为减少副反应,降低原料消耗。
不同的氧化反应温度,相应的反应压力、催化剂配比及反应器型式均有所不同。
设备配置
空压机:高温、中温工艺均可采用"空压机+蒸汽轮机+尾气膨胀机+电机",正常生产时,电机用来发电。
氧化反应器:高温工艺均为单台带搅拌反应釜;中温为塔式反应器,底部带搅拌、顶部带精馏段;中温工艺氧化反应器产能较小。
氧化反应器进料罐: 2000年之后引进的技术,大多采用静态混合器,取消进料混合罐。
CTA结晶:采用1段或3段结晶。
5种高温氧化工艺均采用3段结晶;中温氧化工艺仅采用1 段结晶,粒径较小。
分离及干燥: CTA均采用RVF 1道分离; PTA均采用2道分离,干燥机为列管式。
产品品质指标
各工艺技术产品品质指标没有大的差异,产品品质相近。
物耗能耗
各工艺技术均注重节能及环保。
氧化反应副产蒸汽用于蒸汽轮机和脱水塔再沸器;精制结晶闪蒸蒸汽用于浆料预热;凝液闪蒸蒸汽用于预热或伴热;氧化尾气用于尾气膨胀机驱动空压机和CTA /PTA 输送;增加氧化母液循环率,减少催化剂损失,减少除盐水消耗。
"三废"排放及治理
废气:几种专利技术排放量接近。
安全阀排放气体汇集后进入洗涤塔, 保护环境; 采用高压焚烧(HPCCU) 、低压焚烧(LPCCU)或再生热氧化(RTO)装置处理尾气,改善环境。
废水:工艺技术(一) (五)废水量较少,其余较多。
废水经过处理达到国家排放标准要求。
废渣:按照残渣中同样含水量计,废渣排放量应相近。
废渣治理大多采用焚烧或生化处理,工艺技术
(六)废渣外售。
结语
(1)各专利商都拥有工业化生产PTA的专有技术,拥有近期采用最新技术的专利工厂,均能生产出合格的产品。
引进技术应"货比三家",择优选取。
可能情况下,宜考虑技术多元化。
(2)目前,国内已引进多家PTA 专利技术, PTA装置单系列产能迅速扩大;工艺流程进一步优化;物耗、能耗显著降低;安全、环保措施进一步完善;整体技术水平显著提高。