改进常用7种工具
质量改进常用的七种工具

质量改进常用的七种工具1.因果图(石川馨图)1953年由日本东京大学教授石川馨第一次提出。
a.因果图的作用:导致过程或产品问题的原因可能有很多因素通过对这些因素进行全面系统地观察和分析,可以找出其因果关系。
b.绘制因果图的方法和注意事项利用逻辑推理法;利用发散整理法。
注意事项:确定时应通过大家集思广益,充分发扬民主,以免疏漏;确定原因尽可能具体;质量特性有多少,就要绘制多少张因果图;质量特性和因素尽可能量化;验证。
因果图又叫鱼刺图,用来罗列问题的原因,并将众多的原因分类、分层的图形。
2.排列图(柏拉图)a.排列图的概念和种类质量问题是以质量损失(缺陷项目和成本)的形式表现出来的,大多数损失往往是由几种缺陷引起的,而这几种缺陷往往又是少数原因引起的。
因此,一旦明确了这些“关键的少数”就可以消除这些特殊原因,避免由此引起的大量损失。
排列图可分为二种:1)分析现象用排列图;2)分析原因用排列图。
b.排列图的作图步骤1)确定所要调查的问题以及如何收集数据;2)设计一张数据表;3)将数据填入表中,并合计;4)作排列图用数据表,表中有各项缺陷数、累计缺陷数、各项缺陷所占百分比,以及累计百分比;5)按数量从大到小顺序填入表中,其它项的数据由许多小项目的数据合并在一起,不必计较他的大小排在最后;6)画两根横轴和纵轴。
左边纵轴标上件数(频数)右边纵轴标上比率(频率)最大为100%。
横轴标上各因素。
7)由大到小依次排出各项;8)在横轴上按频数的大小画出直方图;9)在每个直方柱的右上方标出累计值(累计频数和累计频率百分数)描点,用实点连线,画累计频数折线(巴雷特曲线)。
10)在图上记入有关必要事项,如排列图缺陷名称,数据,单位,作图人姓名以及采集数据的时间,主题,数据合计数等。
排列图又叫帕累托图,它是将各个项目从最主要到最次要的顺序进行排列的一种工具。
3.直方图a.直方图的概念:直方图法是从总体中随机抽取样本,将从样本中获得的数据进行整理,根据这些数据找出质量波动规律,预测工序质量好坏,估算工序不合格率的一种工具。
质量改进的七种工具与技术
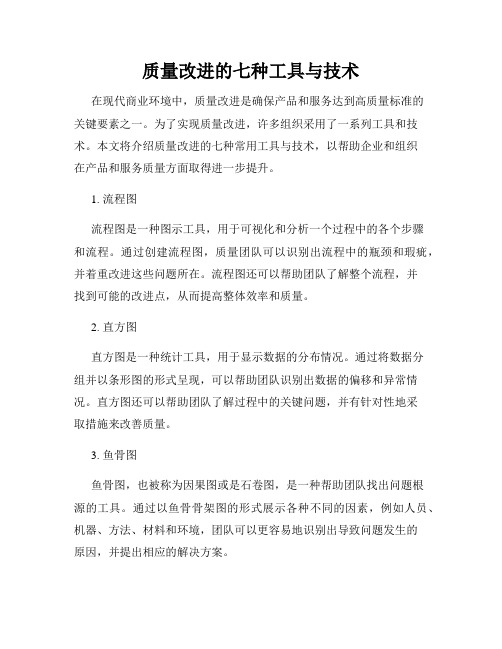
质量改进的七种工具与技术在现代商业环境中,质量改进是确保产品和服务达到高质量标准的关键要素之一。
为了实现质量改进,许多组织采用了一系列工具和技术。
本文将介绍质量改进的七种常用工具与技术,以帮助企业和组织在产品和服务质量方面取得进一步提升。
1. 流程图流程图是一种图示工具,用于可视化和分析一个过程中的各个步骤和流程。
通过创建流程图,质量团队可以识别出流程中的瓶颈和瑕疵,并着重改进这些问题所在。
流程图还可以帮助团队了解整个流程,并找到可能的改进点,从而提高整体效率和质量。
2. 直方图直方图是一种统计工具,用于显示数据的分布情况。
通过将数据分组并以条形图的形式呈现,可以帮助团队识别出数据的偏移和异常情况。
直方图还可以帮助团队了解过程中的关键问题,并有针对性地采取措施来改善质量。
3. 鱼骨图鱼骨图,也被称为因果图或是石卷图,是一种帮助团队找出问题根源的工具。
通过以鱼骨骨架图的形式展示各种不同的因素,例如人员、机器、方法、材料和环境,团队可以更容易地识别出导致问题发生的原因,并提出相应的解决方案。
4. 散点图散点图是一种用于比较两个变量之间关系的图表。
通过在坐标轴上显示不同变量的值,并观察数据点的分布情况,团队可以发现可能存在的相关性或模式。
散点图可以帮助团队识别出可能影响产品质量的关键因素,并针对性地进行改进。
5. 控制图控制图是一种统计工具,用于监控过程中的变异性。
通过绘制数据点的时间序列,并与控制限范围进行比较,团队可以检测出任何异常模式或趋势。
控制图可以帮助团队实时监测过程,并及时采取纠正措施,以确保产品和服务的稳定质量。
6. 五力分析五力分析是一种用于评估市场竞争的工具,并找出企业的竞争优势所在。
通过分析供应商、买家、潜在竞争者、替代品和竞争对手等因素,团队可以更好地了解市场环境,并选择适当的策略来提高产品和服务的质量以增加竞争力。
7. 问卷调查问卷调查是一种用于收集客户反馈和意见的工具。
通过设计有效的调查问卷,并将结果进行统计和分析,团队可以了解客户對产品和服务的满意度及改进建议。
质量改进新七种工具教材介绍
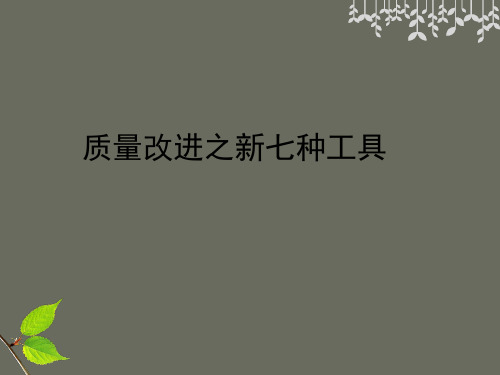
设想资料
× ● ● ◎
• 3.将语言资料制成卡片
– 将收集的语言资料按内容进行逐个分类,并用 独立、简洁的语言写在卡片上。 – 不要用抽象的语言表述、尽量用形象生动、大 家都能理解的语言来表示。否则,这些卡片在 下一阶段就会失效应有的作用。
• 4.整理综合卡片
– 卡片汇在一起,展开,反复阅读。 – 将内容相似或比较接近的卡片汇总在一起,编 成一组,并命名。 – 整理卡片时,将无法归入任何一组的卡片,独 立地编为一组。
D1 图4-1
D2
D3
Dn
4.3 PDPC法的思维方法
•(2)逆向思维法
说明:●常用 ◎使用
① .直接观察法
• 含义:
– 指亲自到现场去听、看、亲手去摸,直接掌握 情况,增强感性认识。
• 重要程度:
– 质量管理是根据事实进行管理,而亲和图更强 调掌握事实的重要性,所以用直接观察法收集 语言资料是非常重要的。
②.文献调查法和面谈阅读法
• 包括:
– 这两种方法包括查阅文献资料、直接征求别人 的意见以及启发多数人新构思的集体创造性思 考方法。
• 5.制图
• 卡片编组整理后,将它们的总体结构用容易理解的 亲和图来表示。
• 6.应用
• 绘制出亲和图后,可以反复观看,也可以采用小组 的形式在组内轮流讲解,还可以就亲和图写一些报 告,在这些活动中,就逐步达到了使用亲和图的目 的。
3.2
亲和图的主要用途(目的)
» 对未知事物或领域,认真收集实际资料,并从杂乱无意的资料中整 理出事物的相互关系和脉络,就某件事情达成共识。
– 这种方法是针对某一问题,充分收集各种经验、知识、 创意和意见等语言、文字资料,并按其相互亲和性归 纳整理这些资料,使问题明确起来,求得统一认识和 协调工作,以利于问题解决的一种方法。
质量管理的七种工具

质量管理的七种工具是指一组被广泛应用于质量管理和问题解决过程中的工具和技术。
这些工具可以帮助分析问题、找出根本原因并采取适当的改进措施。
以下是七种常用的质量管理工具:
1. 流程图:用于展示和分析工作流程,揭示流程中的瓶颈和改进潜力。
2. 因果图(鱼骨图):通过将问题因素分类为人员、方法、机器、材料和环境等方面,揭示问题的多方面原因和关联性。
3. 直方图:用来以可视化的方式表示数据的分布情况,帮助分析数据的特征和异常情况。
4. 控制图:用于监控和分析过程的稳定性和可预测性,及时检测并纠正异常情况。
5. 矩阵图(优先级矩阵):用于评估和优先排序问题或改进方案,将不同因素按照重要性和紧迫性进行分类和分析。
6. 散点图:用于显示两个变量之间的相互关系,帮助识别可能的关联和趋势。
7. 流程控制图:用于分析流程中的关键控制点和变量,确保流程在可控范围内运行。
这些质量管理工具可以帮助团队更好地理解问题,找出潜在的改进机会,并采取适当的措施。
根据实际情况,选择和应用适当的工具将有助于提高质量管理和问题解决的效果。
质量改进的七种工具与技术
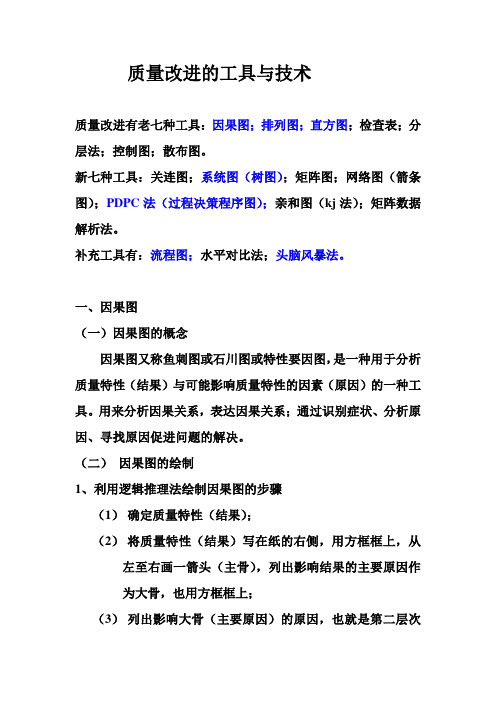
质量改进的工具与技术质量改进有老七种工具:因果图;排列图;直方图;检查表;分层法;控制图;散布图。
新七种工具:关连图;系统图(树图);矩阵图;网络图(箭条图);PDPC法(过程决策程序图);亲和图(kj法);矩阵数据解析法。
补充工具有:流程图;水平对比法;头脑风暴法。
一、因果图(一)因果图的概念因果图又称鱼刺图或石川图或特性要因图,是一种用于分析质量特性(结果)与可能影响质量特性的因素(原因)的一种工具。
用来分析因果关系,表达因果关系;通过识别症状、分析原因、寻找原因促进问题的解决。
(二)因果图的绘制1、利用逻辑推理法绘制因果图的步骤(1)确定质量特性(结果);(2)将质量特性(结果)写在纸的右侧,用方框框上,从左至右画一箭头(主骨),列出影响结果的主要原因作为大骨,也用方框框上;(3)列出影响大骨(主要原因)的原因,也就是第二层次原因,作为中骨;用小骨列出第三层次原因,以此类推;(4)将认为对质量特性(结果)有显著影响的重要原因标出来;(5)在图上记录必要的有关信息(如产品、工序或小组名称、参加人员、日期等)。
它是用逻辑推理法去确定第一层次原因(大骨),第二层次原因(中骨),第三层次原因(小骨)与结果之间的关系,故称“逻辑推理法”。
2、利用发散整理法绘制因果图的步骤(1)确定质量特性;(2)尽可能找出所有可能会影响结果的因素;(3)找出各原因之间的关系,在因果图上以因果关系箭头联接起来;(4)将认为对结果有显著影响的重要因素标出来;(5)在因果图上标上必要的信息。
它的特点是开放式的查找原因(最有效的方法是“头脑风暴法”),然后根据对结果的影响从小骨到中骨再到大骨系统地整理这些原因,形成因果图形状,故称为“发散整理法”。
(三)因果图的注意事项1、绘制因果图的注意事项(1)确定原因应集思广益,以免疏漏;(2)确定原因应尽可能具体;(3)有多少质量特性,就要绘制多少张因果图;(4)验证原因必须要细化,直至能采取措施为止,如分析出的原因不能采取措施,说明原因分析尚未到位。
PDCA的八个步骤七大工具

PDCA的八个步骤七大工具PDCA(Plan-Do-Check-Act)是一种持续改进的管理循环方法,通过不断地策划、执行、检查和调整,实现组织的持续改善和优化。
在PDCA的循环中,使用七大工具帮助收集和分析数据,以便做出准确的决策和改进措施。
本文将介绍PDCA的八个步骤以及其对应的七大工具。
一、计划(Plan)在PDCA循环的第一个阶段,需要进行充分的计划和准备工作。
在这个阶段,组织需要确立目标,并制定详细的计划来实现这些目标。
在计划阶段,以下工具被广泛应用:1. SWOT分析(SWOT Analysis)SWOT分析通过对组织的优势(Strengths)、劣势(Weaknesses)、机会(Opportunities)和威胁(Threats)进行评估,帮助组织确定发展战略。
2. SMART目标(SMART Goals)SMART目标是指具体(Specific)、可衡量(Measurable)、可实现(Attainable)、相关(Relevant)和具有时限(Time-Bound)的目标。
制定SMART目标帮助组织更加明确地确定行动计划。
二、执行(Do)在PDCA循环的第二个阶段,组织开始根据制定的计划执行相应的工作。
在实施阶段,以下工具常被用到:3. 流程图(Flowchart)流程图是通过图形化的方式描述工作流程,清晰地展示每个步骤的先后关系和工作流程。
流程图有助于组织成员理解整个工作流程,并发现潜在的问题和改进的空间。
4. PDPC图(Process Decision Program Chart)PDPC图是在流程图基础上进一步完善和细化的工具,用于预测和管理潜在的风险。
通过PDPC图,组织可以预先制定应对措施,降低不确定性和风险。
三、检查(Check)在PDCA循环的第三个阶段,组织需要对执行过程进行检查和评估,以确保过程的有效性和效果。
以下工具可帮助组织进行检查:5. 控制图(Control Chart)控制图是一种统计工具,用于监控和分析过程的稳定性和可控性。
总结一下质量管理传统7种工具的原理及应用范围。

总结一下质量管理传统7种工具的原理及应用范围。
质量管理传统7种工具指的是流程控制图、因果图、直方图、散点图、控制图、帕累托图和检验表。
这些工具可以帮助企业进行质量管理,提高产品的质量和客户满意度。
下面将对这些工具的原理及应用范围进行总结。
1. 流程控制图流程控制图是一种图形化的方法,用于显示生产或业务流程的步骤和其间的关系。
通过绘制流程控制图,可以帮助企业优化流程,减少浪费和错误,提高生产效率和产品质量。
应用范围包括生产线、服务行业、办公室等。
2. 因果图因果图是一种图形化的方法,用于分析问题和确定问题的根本原因。
通过绘制因果图,可以将问题分解为各个因素,并找出导致问题的根本原因。
应用范围包括生产线、服务行业、办公室等。
3. 直方图直方图是一种图形化的方法,用于表示数据的分布情况。
通过绘制直方图,可以了解数据的集中趋势和分散程度,进而确定采取何种措施来改进质量。
应用范围包括生产线、服务行业、办公室等。
4. 散点图散点图是一种图形化的方法,用于表示两个变量之间的关系。
通过绘制散点图,可以了解两个变量之间的关系,进而确定采取何种措施来改进质量。
应用范围包括生产线、服务行业、办公室等。
5. 控制图控制图是一种图形化的方法,用于监控过程的稳定性和控制过程的变异。
通过绘制控制图,可以及时发现过程的变异,并采取相应措施来控制过程的稳定性,保证产品质量。
应用范围包括生产线、服务行业、办公室等。
6. 帕累托图帕累托图是一种图形化的方法,用于分析问题的优先级,并确定采取何种措施来改进质量。
通过绘制帕累托图,可以了解哪些问题最为严重,进而优先解决这些问题。
应用范围包括生产线、服务行业、办公室等。
7. 检验表检验表是一种记录数据的表格,用于统计产品的质量指标。
通过记录数据,可以了解产品的质量状况,并采取相应措施来改进质量。
应用范围包括生产线、服务行业、办公室等。
总之,质量管理传统7种工具可以帮助企业提高产品质量和客户满意度,应用范围广泛,包括生产线、服务行业、办公室等。
质量改进的七种工具卡片
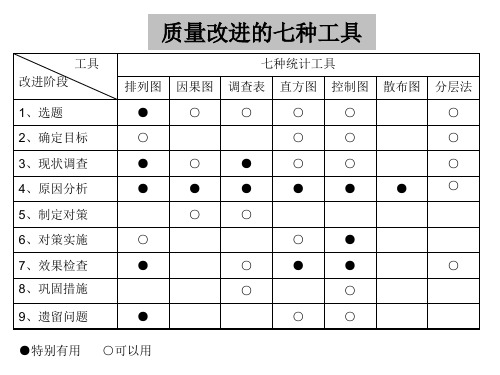
常见的典型直方图
平顶型:几种平均值不 同的分布混在一起,或 过程种某种要素缓慢劣 化时常会出现这种形状
锯齿型:分组过多或测 量方法有问题、读错测 量数据
偏峰型:不良的加工习 惯“轴大孔小”,或单 项公差(如形位公差)
常用的分层标志
人员:年龄、性别
机器:类型、新旧程度、不同夹具、不同生产线 料:产地、批号、生产厂 方法:工艺要求、操作参数、操作方法、生产速度 测量:测量设备、测量方法、测量人员、测量取样 时间:不同班次 环境 :温度、湿度、清洁度
分层法常与直方图、排列图、控制图、散布图和调查表使用。
工具之六:散布图
质量改进的七种工具
工具 改进阶段 1、选题 2、确定目标 3、现状调查 4、原因分析 排列图 ● ○ ● ● ○ ● ● ● 因果图 ○ 七种统计工具 调查表 ○ 直方图 ○ ○ ○ ● 控制图 ○ ○ ○ ● ● 散布图 分层法 ○ ○ ○ ○
5、制定对策
6、对策实施 7、效果检查 8、巩固措施 9、遗留问题 ●特别有用 ● ○可以用 ○ ●
20 9.5 90.0
12 5.7 95.7
9 4.3 100.0
识别质量改进的主要项目:输出端漏油
Percent
质量工具之二:因果图
因果图是一种用于分析质量特性(结果)与可能影响质量特性的因素(原因)的 一种工具,又称石川图、鱼刺图。主要用于:
1、分析因果原因;
2、表达因果关系; 3、通过识别症状、分析原因,寻找措施以促进问题的解决;
济上考虑不值得消除,例如机床开动时的轻微振动等。异因则非过程固
有,有时存在,有时不存在,对质量影响大,但不难除去,例如车刀磨 损。 偶因引起质量的偶然波动。
质量改进老七工具教材

B孔垂直度超差
95.84
7
其他
% 100
75 百
50 分 率
25
0
2024/10/16
图例1-3 第9工序不合格项目排列图
34
• 从上图可直观地看出第9工序产生不合格品 的问题是:
• (1)A孔直径超差,占第9工序不合格品的62.5%。 • (2)孔距超差,占第9工序不合格品的30.36%。
• 该两个项目的不合格占了第9工序不合格品 的92.86%。
51
B孔垂直度超 差
5
其他
7
总计
168
百分比 (%)
62.50 30.36
2.98
4.16 100.00
累计百 分比 (%) 62.50 92.86
95.84
100.00
2024/10/16
备注
返33回
(件) 168
126
不
105
合 格 84
品
数
42
62.5 51
92.86
0
A孔直径超差
5
孔距超差
• 可按班(组)、 个人、熟练程 度、性别、年 龄等进行分层。
2024/10/16
17
• (1)操作人员
• (2)机器设备
• (3)作业方法 • (4)原材料、零部件 • (5)时间 • (6)测量、检查 • (7)环境 • (8)缺陷
• 可按型号、机 (台)号、结 构、新旧程度、 工夹模具等进 行分层。
• 2.引起质量问题的因素会很多,分析主要原因经常 使用排列图。根据现象制作出排列图,确定了要解 决的问题之后,必然就明确了主要原因所在,这就 是“关键的少数”。
• 3.利用排列图不仅可以找到一个问题的主要原因, 而且可以连续使用,找出复杂问题的最终原因。
改进常用7种工具
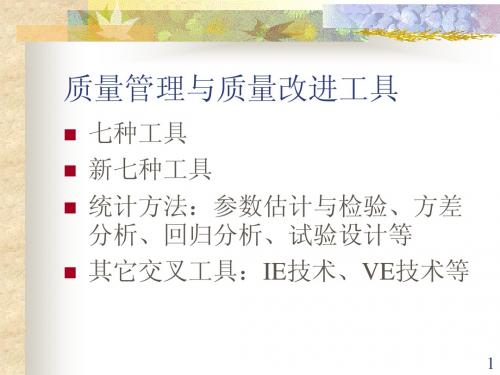
22
排列图的分类
分析现象用排列图
分析原因用排列图
23
分析原因用排列图
分析原因用排列图,与过程有关 操作者:班次、组别、性别、年龄、经 验等 机器:设备、工具等 材料:供应商、批次等 作业方法:作业安排、方法等 作业环境:温度、湿度、光线、噪声等
24
作排列图的步骤
17
QM七种工具
分 散 控 检 直 排 因 层 布 制 查 方 列 果 法 图 图 表 图 图 图
18
排列图
质量问题是以质量损失(缺陷项目和 损失金额)的形式来体现的。大多数损失 是由少数几种的缺陷引起的( Pareto原则) , 而这这几种缺陷又是由少数原因引起的。 因此,只要明确这些“关键的少数”,就 可以消除这些特殊原因,避免由些引起的 大量损失。用排列图法,可以实现这一目 的。
10
因果图作图步骤
选题,分析对象,确定质量特性。 组织讨论,找出所有可能会影响结果的 因素。 找出各因素之间的因果关系,在图上以 因果关系的箭头表示出来。 根据对结果影响的重要程度,将认为对 结果有显著影响的重要原因标示出来。 在因果图上标出有关信息。
11
因果图示例
机床
主轴松动 轴承磨损 机床精度不够 夹具磨损 漏油
小组名称: 组长: 成员: 日期:
轴 颈 有 刀 痕
材 料
工艺方法
14
因果图作图步骤
选题,分析对象,确定质量特性。 组织讨论,找出所有可能会影响结果的 因素。 找出各因素之间的因果关系,在图上以 因果关系的箭头表示出来。 根据对结果影响的重要程度,将认为对 结果有显著影响的重要原因标示出来。 在因果图上标出有关信息。
新旧七种质量管理常用七种工具对比
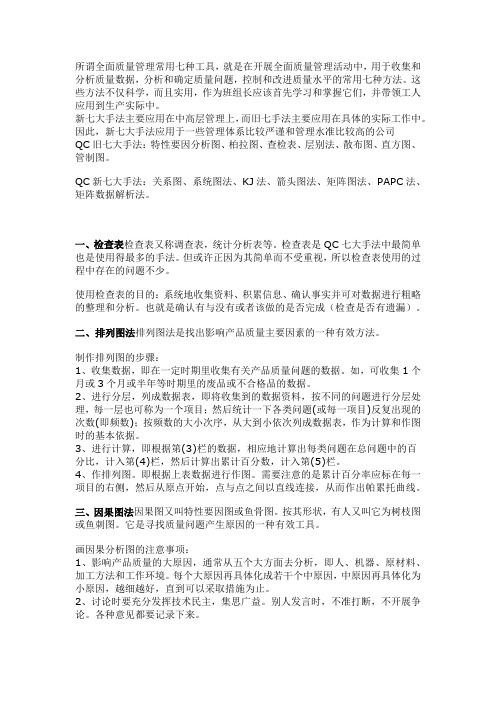
所谓全面质量管理常用七种工具,就是在开展全面质量管理活动中,用于收集和分析质量数据,分析和确定质量问题,控制和改进质量水平的常用七种方法。
这些方法不仅科学,而且实用,作为班组长应该首先学习和掌握它们,并带领工人应用到生产实际中。
新七大手法主要应用在中高层管理上,而旧七手法主要应用在具体的实际工作中。
因此,新七大手法应用于一些管理体系比较严谨和管理水准比较高的公司QC旧七大手法:特性要因分析图、柏拉图、查检表、层别法、散布图、直方图、管制图。
QC新七大手法:关系图、系统图法、KJ法、箭头图法、矩阵图法、PAPC法、矩阵数据解析法。
一、检查表检查表又称调查表,统计分析表等。
检查表是QC七大手法中最简单也是使用得最多的手法。
但或许正因为其简单而不受重视,所以检查表使用的过程中存在的问题不少。
使用检查表的目的:系统地收集资料、积累信息、确认事实并可对数据进行粗略的整理和分析。
也就是确认有与没有或者该做的是否完成(检查是否有遗漏)。
二、排列图法排列图法是找出影响产品质量主要因素的一种有效方法。
制作排列图的步骤:1、收集数据,即在一定时期里收集有关产品质量问题的数据。
如,可收集1个月或3个月或半年等时期里的废品或不合格品的数据。
2、进行分层,列成数据表,即将收集到的数据资料,按不同的问题进行分层处理,每一层也可称为一个项目;然后统计一下各类问题(或每一项目)反复出现的次数(即频数);按频数的大小次序,从大到小依次列成数据表,作为计算和作图时的基本依据。
3、进行计算,即根据第(3)栏的数据,相应地计算出每类问题在总问题中的百分比,计入第(4)栏,然后计算出累计百分数,计入第(5)栏。
4、作排列图。
即根据上表数据进行作图。
需要注意的是累计百分率应标在每一项目的右侧,然后从原点开始,点与点之间以直线连接,从而作出帕累托曲线。
三、因果图法因果图又叫特性要因图或鱼骨图。
按其形状,有人又叫它为树枝图或鱼刺图。
它是寻找质量问题产生原因的一种有效工具。
质量改进常用的七种工具
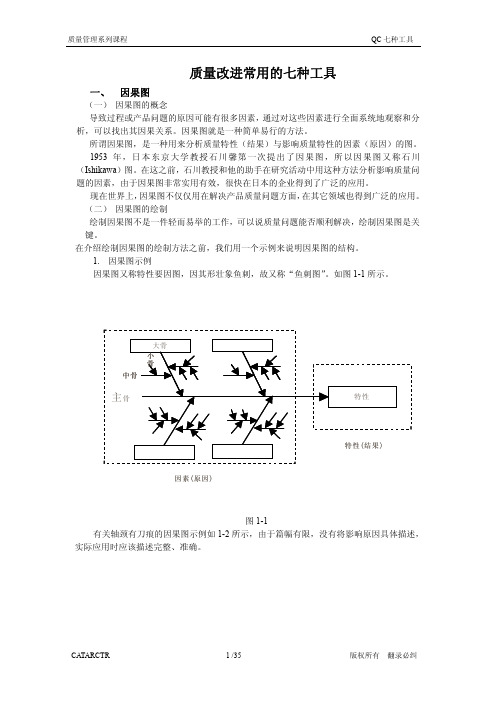
质量改进常用的七种工具一、 因果图(一) 因果图的概念导致过程或产品问题的原因可能有很多因素,通过对这些因素进行全面系统地观察和分析,可以找出其因果关系。
因果图就是一种简单易行的方法。
所谓因果图,是一种用来分析质量特性(结果)与影响质量特性的因素(原因)的图。
1953年,日本东京大学教授石川馨第一次提出了因果图,所以因果图又称石川(Ishikawa)图。
在这之前,石川教授和他的助手在研究活动中用这种方法分析影响质量问题的因素,由于因果图非常实用有效,很快在日本的企业得到了广泛的应用。
现在世界上,因果图不仅仅用在解决产品质量问题方面,在其它领域也得到广泛的应用。
(二) 因果图的绘制绘制因果图不是一件轻而易举的工作,可以说质量问题能否顺利解决,绘制因果图是关键。
在介绍绘制因果图的绘制方法之前,我们用一个示例来说明因果图的结构。
1.因果图示例因果图又称特性要因图,因其形壮象鱼刺,故又称“鱼刺图”。
如图1-1所示。
图1-1有关轴颈有刀痕的因果图示例如1-2所示,由于篇幅有限,没有将影响原因具体描述,实际应用时应该描述完整、准确。
轴承磨损机床精度不够图1-22.利用逻辑推理法绘制因果图的步骤第一步,确定质量特性(结果),因果图中的“结果”可根据具体需要选择。
第二步,将质量特性写在纸的右侧,从左至右画一箭头(主骨),将结果用方框框上。
接下来,列出影响结果的主要原因作为大骨,也用方框框上。
第三步,列出影响大骨(主要原因)的原因,也就是第二层次原因,作为中骨;接着,用小骨列出影响中骨的第三层次的原因,如此类推。
第四步,根据对质量特性影响的重要程度,将认为对质量特性有显著影响的重要因素标出来。
第五步,在因果图上记录必要的有关信息。
一开始使用这种方法可能感到比较困难,这时,最好的方法就是看一看质量特性有没有波动,如果数据表明存在波动,就要想想为什么会存在波动。
当要画某个缺陷的因果图时,比如,可能会从数据中发现每周内不同的日期里,这种缺陷发生的次数有所不同,如果这种缺陷在星期一发生的次数比其它日期次多,就可以换个角度考虑,“为什么会产生缺陷?”,“为什么这种缺陷在星期一发生的次数比其它日期多?”,这样可以找出星期一与其它日期不同的原因,最终发现产生缺陷的原因。
企业质量改进的八步法和七工具
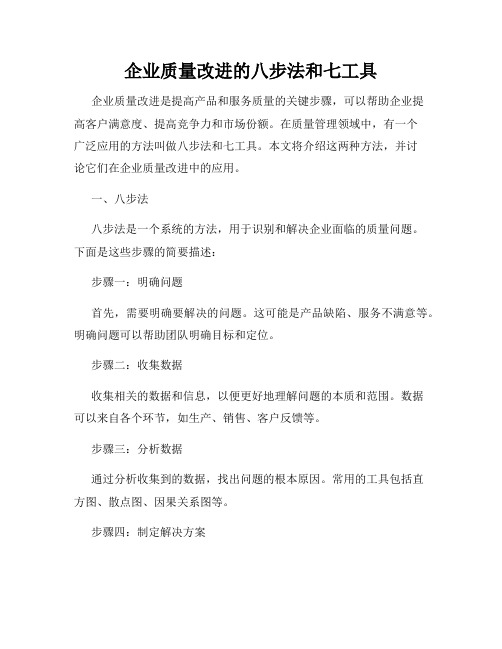
企业质量改进的八步法和七工具企业质量改进是提高产品和服务质量的关键步骤,可以帮助企业提高客户满意度、提高竞争力和市场份额。
在质量管理领域中,有一个广泛应用的方法叫做八步法和七工具。
本文将介绍这两种方法,并讨论它们在企业质量改进中的应用。
一、八步法八步法是一个系统的方法,用于识别和解决企业面临的质量问题。
下面是这些步骤的简要描述:步骤一:明确问题首先,需要明确要解决的问题。
这可能是产品缺陷、服务不满意等。
明确问题可以帮助团队明确目标和定位。
步骤二:收集数据收集相关的数据和信息,以便更好地理解问题的本质和范围。
数据可以来自各个环节,如生产、销售、客户反馈等。
步骤三:分析数据通过分析收集到的数据,找出问题的根本原因。
常用的工具包括直方图、散点图、因果关系图等。
步骤四:制定解决方案基于问题的根本原因,制定解决方案。
解决方案应该具体、可行,并能够解决问题的根本原因。
步骤五:实施解决方案将制定的解决方案付诸实施。
这需要协调各个部门和团队的合作,确保解决方案得以有效执行。
步骤六:监控结果在解决方案实施后,对结果进行监控和评估。
这可以通过收集反馈和数据来进行。
步骤七:标准化解决方案如果解决方案有效,可以将其标准化并应用到其他类似问题上。
这有助于提高工作效率和质量水平。
步骤八:不断改进质量改进是一个持续的过程,需要不断反思和改善。
企业应该建立学习型组织,鼓励员工提出改进建议,并不断完善业务流程。
二、七工具七工具是用于分析和解决质量问题的常用方法和工具。
它们包括:1. 流程图:用于显示工作流程和关键环节,有助于改进工作流程和减少错误。
2. 直方图:用于显示数据的分布情况,帮助分析问题原因和优化流程。
3. 散点图:用于显示两个变量之间的关系,有助于找出变量之间的因果关系。
4. 因果关系图:用于分析问题的根本原因,帮助制定解决方案。
5. 控制图:用于监控过程的稳定性和控制过程的变异性,有助于及时发现并解决问题。
6. 甘特图:用于项目管理和进度控制,帮助合理安排资源和任务。
质量改进的七种工具与技术

质量改进的七种工具与技术在现代化的生产制造过程中,质量是企业成功的关键。
为了提高产品和服务的质量水平,企业可以运用各种工具和技术来进行质量改进。
本文将介绍七种常用的质量改进工具与技术,并探讨它们的应用场景和效用。
1. 流程图流程图是一种图形化的工具,用于描述和分析工作流程及其各个环节之间的关系。
通过绘制流程图,企业可以更直观地了解工作流程中存在的问题和瓶颈,并提出改进措施。
流程图不仅可以帮助企业识别和消除无效的流程环节,还能够改进流程的效率和准确性。
2. 鱼骨图鱼骨图,又称因果图或石墨图,是一种用于问题分析和决策的图形化工具。
它通过将问题与可能的原因一一对应,以鱼骨的形式展示出来,帮助企业理清问题的根本原因。
鱼骨图可以帮助企业明确问题所在,并集中于解决问题的根本原因,从而实现质量的改进。
3. 直方图直方图是一种用来显示数据分布情况的图形工具。
通过绘制直方图,企业可以直观地了解数据的分布情况,发现潜在的问题和异常情况。
直方图能够帮助企业在质量改进过程中更准确地定位问题,并调整产品和服务的参数,以提高质量水平。
4. 散点图散点图是一种显示两个变量之间关系的图形工具。
企业可以通过绘制散点图,分析两个变量之间的相关性,并找出其中的规律和趋势。
散点图在质量改进中的应用广泛,可以用于分析产品质量与生产工艺参数之间的关系,以便优化生产流程和改进产品质量。
5. 控制图控制图是一种用于监控和评估过程稳定性的图形工具。
通过绘制过程数据的控制图,企业可以判断过程是否处于稳定状态,并及时采取措施防止过程偏离目标。
控制图能够帮助企业实现过程的持续改进,确保产品和服务的一致性和稳定性。
6. 5W1H分析法5W1H分析法是一种用于分析问题和确定解决方案的方法。
5W代表了What(是什么)、Where(在哪里)、When(何时)、Why(为什么)和Who(谁),1H代表了How(如何)。
通过回答这些问题,企业可以深入分析问题的根本原因,并找到解决问题的最佳途径。
质量管理新七工具

质量管理新七工具摘要:一、引言二、新七工具的概念与意义三、新七工具的具体内容1.流程图2.直方图3.帕累托图4.检查表5.散点图6.控制图7.因果图四、新七工具在质量管理中的应用五、新七工具的优势与局限六、企业如何有效运用新七工具提高质量管理七、结论正文:质量管理新七工具是一种在质量管理中常用的方法,旨在帮助企业更有效地进行质量管理,提高产品和服务的质量。
新七工具是在旧七工具的基础上进行改进和拓展,使其更符合现代企业的需求。
新七工具包括流程图、直方图、帕累托图、检查表、散点图、控制图和因果图。
一、引言质量管理是企业持续发展的重要保障,新七工具作为质量管理的重要手段,可以帮助企业更好地实现质量管理的各项任务。
新七工具不仅有助于提高产品和服务的质量,还能提升企业整体运营效率,降低成本,增强竞争力。
二、新七工具的概念与意义新七工具是在旧七工具的基础上,根据现代企业质量管理的需求和发展趋势,进行改进和拓展后形成的一套工具。
新七工具不仅保留了旧七工具的基本功能,还增加了更多实用功能,使其更符合现代企业的实际需求。
三、新七工具的具体内容新七工具包括以下七种工具:1.流程图:通过图形化展示流程,帮助企业发现流程中的问题,优化流程,提高效率。
2.直方图:用于展示数据分布情况,分析数据波动,发现质量问题。
3.帕累托图:用于显示各种因素对质量问题的影响程度,帮助企业集中精力解决关键问题。
4.检查表:用于记录和统计数据,便于分析和改进。
5.散点图:用于展示两个变量之间的关系,分析其对质量的影响。
6.控制图:用于监控过程质量,发现异常情况,及时采取措施。
7.因果图:用于分析问题根本原因,制定针对性的改进措施。
四、新七工具在质量管理中的应用新七工具在质量管理中的应用十分广泛,企业可以根据实际情况选择合适的工具进行质量管理。
例如,企业可以通过流程图优化生产流程,提高生产效率;利用直方图分析产品质量,发现潜在问题;利用帕累托图确定改进的重点等。
- 1、下载文档前请自行甄别文档内容的完整性,平台不提供额外的编辑、内容补充、找答案等附加服务。
- 2、"仅部分预览"的文档,不可在线预览部分如存在完整性等问题,可反馈申请退款(可完整预览的文档不适用该条件!)。
- 3、如文档侵犯您的权益,请联系客服反馈,我们会尽快为您处理(人工客服工作时间:9:00-18:30)。
f i u f i ui S h fi fi
2 i
2
8 x 25 3 25.24 7.92524 100 2 300 8 S 3 5.19 0.00519 100 100
19
排列图的分类
分析现象用排列图
分析原因用排列图
20
排列图的分类
分析现象用排列图
分析原因用排列图
21
分析现象用排列图
分析现象用排列图,与不良结果有关 质量:缺陷、故障、顾客抱怨、退货或 维修等 成本:损失金额或费用等 交货期:存货短缺或交货期拖延等 安全:发生事故或出现差错等
选题:产品尺寸缺陷 分析问题:用因果图分析 采取对策,进行改进 改进前后比较
34
产品尺寸缺陷因果图
操作者
疲劳 注意力 健康 精神 疾病 教育培训 心情 经验
形状 成分 原料质量 贮存 排列
机 器
稳定 操作 不平衡 变形 磨损 夹具和工具
产品尺寸缺陷
位置 装配
拧紧程度
定位 顺序
尺寸
角度 程序 动作
பைடு நூலகம்速度
零件和原料
作业方法
35
影响产品尺寸缺陷因素排列图
36
排列图和因果图结合使用
选题 分析问题 采取对策,进行改进 改进前后比较
37
改进后影响产品不合格因素排列图
9月1日至10月31日
38
排列图和因果图结合使用
选题 分析问题 采取对策,进行改进 改进前后比较
39
改进前后不良品排列图比较
6月1日至7月31日
9月1日至10月31日
总改进效果
改进效果
40
QM七种工具
分 散 控 检 直 排 因 层 布 制 查 方 列 果 法 图 图 表 图 图 图
41
直方图
直方图是从工序中随机抽取样 本,将从数据中获取的数据进行整 理,绘成图,从中找到质量波动规 律,预测工序质量的一种工具。
轴 颈 有 刀 痕
材 料
工艺方法
12
因果图作图步骤
选题,分析对象,确定质量特性。 组织讨论,找出所有可能会影响结果的 因素。 找出各因素之间的因果关系,在图上以 因果关系的箭头表示出来。 根据对结果影响的重要程度,将认为对 结果有显著影响的重要原因标示出来。 在因果图上标出有关信息。
29
排列图和因果图结合使用
选题 分析问题 采取对策,进行改进 改进前后比较
30
案例分析
某厂为降低产品不良品率
31
影响产品不合格因素排列图
6月1日至7月31日
32
排列图和因果图结合使用
选题:产品尺寸缺陷 分析问题 采取对策,进行改进 改进前后比较
33
排列图和因果图结合使用
计算组距h,即组与组之间的间隔 La S m h k 38 13 h 2.5 3 10
计算第一组上下界限值,一般用下面的公式 确定:
h Sm 2 h Sm 13 1.5 14.5 ~ 11.5 2
47
直方图的画法与举例(续)
计算各组的上下界和中心值(xi) 记录各组数据,整理成频数分布表 统计落入各组的尺寸频数fi
操作者
无作业标准 油压不稳 工作纪律松驰 未经培训 油中有气泡 薪金低 日夜加班 没有积极性 疲劳 情绪 缺乏作业技能
环境
光线弱 光线 气温高 光线过强
冷却液不标准 浓度不当 材质不当
上道工序加工不良 中心孔位 置不正确
切削速度 用错刀具 转速高 进给量大 刀具管理不善
小组名称: 组长: 成员: 日期:
质量管理与质量改进工具
七种工具 新七种工具 统计方法:参数估计与检验、方差 分析、回归分析、试验设计等 其它交叉工具:IE技术、VE技术等
1
QM七种工具
分 散 控 检 直 排 因 层 布 制 查 方 列 果 法 图 图 表 图 图 图
2
QM七种工具
分 散 控 检 直 排 因 层 布 制 查 方 列 果 法 图 图 表 图 图 图
特
性
特性(结果)
因素(原因) 5
因果图作图步骤
选题,分析对象,确定质量特性。 组织讨论,找出所有可能会影响结果的 因素。 找出各因素之间的因果关系,在图上以 因果关系的箭头表示出来。 根据对结果影响的重要程度,将认为对 结果有显著影响的重要原因标示出来。 在因果图上标出有关信息。
6
42
直方图的作用
展示用表格难以说明的大量数据 显示各种数值出现的相对频率 揭示数据的中心、波动及形状 快速阐明数据的潜在分布 为预测过程提供有利信息 可以发现“过程是否能满足顾客要求”
43
直方图的绘制步骤
明确衡量过程的特性值 收集数据 计算极差 数据分组 作频数分布表 画直方图 在图上记录有关资料
明确问题以及如何收集数据 设计数据记录表(检查表),记录数据 将数据从大到小排列,并累计计算 画排列图 在图上画累计频数折线 在图上记入必要事项
25
排列图示例
某厂对产品缺陷作排列图分析
26
排列图示例
例:某厂随机调查4月1日至7月1日的 产品共5000件,对其逐一检查,进行缺陷 分析,得到缺陷种类及数据如下:
操作者
无作业标准 油压不稳 工作纪律松驰 未经培训 油中有气泡 薪金低 日夜加班 没有积极性 疲劳 情绪 缺乏作业技能
环境
光线弱 光线 气温高 光线过强
冷却液不标准 浓度不当 材质不当
上道工序加工不良 中心孔位 置不正确
切削速度 用错刀具 转速高 进给量大 刀具管理不善
小组名称: 组长: 成员: 日期:
45
直方图的画法与举例(续)
收集数据
一般取100个左右,找出其最大值La和最小值Sm
把100个数据分成若干组,一般用下表经验数值确定
数据的数量 N 50~100 100~250 250 以上
适当的分组数 k 6~10 7~12 10~20
一般使用的组数 k 10
46
直方图的画法与举例(续)
13
因果图示例
机床
主轴松动 轴承磨损 机床精度不够 夹具磨损 漏油
操作者
无作业标准 油压不稳 工作纪律松驰 未经培训 油中有气泡 薪金低 日夜加班 没有积极性 疲劳 情绪 缺乏作业技能
环境
光线弱 光线 气温高 光线过强
冷却液不标准 浓度不当 材质不当
上道工序加工不良 中心孔位 置不正确
切削速度 用错刀具 转速高 进给量大 刀具管理不善
10
因果图作图步骤
选题,分析对象,确定质量特性。 组织讨论,找出所有可能会影响结果的 因素。 找出各因素之间的因果关系,在图上以 因果关系的箭头表示出来。 根据对结果影响的重要程度,将认为对 结果有显著影响的重要原因标示出来。 在因果图上标出有关信息。
11
因果图示例
机床
主轴松动 轴承磨损 机床精度不够 夹具磨损 漏油
因果图作图步骤
选题,分析对象,确定质量特性。 组织讨论,找出所有可能会影响结果的 因素。 找出各因素之间的因果关系,在图上以 因果关系的箭头表示出来。 根据对结果影响的重要程度,将认为对 结果有显著影响的重要原因标示出来。 在因果图上标出有关信息。
7
因果图示例
机床
主轴松动 轴承磨损 机床精度不够 夹具磨损 漏油
轴 颈 有 刀 痕
材 料
工艺方法
8
因果图作图步骤
选题,分析对象,确定质量特性。 组织讨论,找出所有可能会影响结果的 因素。 找出各因素之间的因果关系,在图上以 因果关系的箭头表示出来。 根据对结果影响的重要程度,将认为对 结果有显著影响的重要原因标示出来。 在因果图上标出有关信息。
15
因果图示例
机床
主轴松动 轴承磨损 机床精度不够 夹具磨损 漏油
操作者
无作业标准 油压不稳 工作纪律松驰 未经培训 油中有气泡 薪金低 日夜加班 没有积极性 疲劳 情绪 缺乏作业技能
环境
光线弱 光线 气温高 光线过强
冷却液不标准 浓度不当 材质不当
上道工序加工不良 中心孔位 置不正确
切削速度 用错刀具 转速高 进给量大 刀具管理不善
22
排列图的分类
分析现象用排列图
分析原因用排列图
23
分析原因用排列图
分析原因用排列图,与过程有关 操作者:班次、组别、性别、年龄、经 验等 机器:设备、工具等 材料:供应商、批次等 作业方法:作业安排、方法等 作业环境:温度、湿度、光线、噪声等
24
作排列图的步骤
小组名称: 组长: 成员: 日期:
轴 颈 有 刀 痕
材 料
工艺方法
14
因果图作图步骤
选题,分析对象,确定质量特性。 组织讨论,找出所有可能会影响结果的 因素。 找出各因素之间的因果关系,在图上以 因果关系的箭头表示出来。 根据对结果影响的重要程度,将认为对 结果有显著影响的重要原因标示出来。 在因果图上标出有关信息。
9
造成轴颈有刀痕的所有可能因素
工人疲劳、机床油压不稳、机床、工人有情绪、中 心孔位置不正确、工作纪律松驰、作业环境不好、机床 夹具磨损、冷却液浓度不当、机床漏油、材质不当、上 道工序加工不良、机床轴承磨损、工作无积极性、切削 时进给量太大、工人缺乏作业技能、机床精度不够、用 错刀具、工人日夜加班、工艺方法有问题、切削速度不 当、冷却液不标准、切削速度太快、机床主轴松动、工 人未经培训、气温高、光线不良、光线过强、刀具管理 有问题、光线过弱、材料和冷却液有问题、操作无作业 标准、油中有气泡、工人薪水低