关于双齿轮齿圈消隙结构传动装置的理论计算
重型机床齿轮箱消隙原理
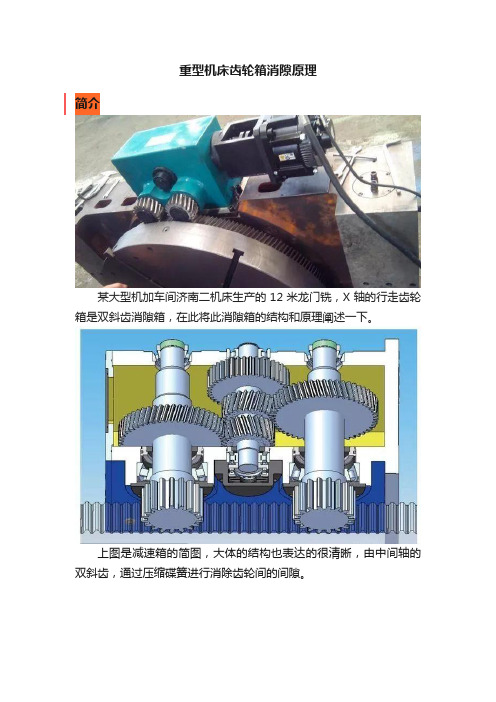
重型机床齿轮箱消隙原理
简介
某大型机加车间济南二机床生产的12米龙门铣,X轴的行走齿轮箱是双斜齿消隙箱,在此将此消隙箱的结构和原理阐述一下。
上图是减速箱的简图,大体的结构也表达的很清晰,由中间轴的双斜齿,通过压缩碟簧进行消除齿轮间的间隙。
双齿轮消隙
[1]1)如图1所示,输入轴2上的两个斜齿轮齿数、模数等参数相同旋向相反,轴1和轴3上的两个齿轮齿数、模数等参数相同而斜齿旋向相反,分别与轴2上的两个斜齿轮啮合。
齿轮4,6相同。
运动由轴2输入,通过两对斜齿轮分别传给轴1和轴3,然后由齿轮4和6传动齿条5。
如果在轴2上施加轴向力F,其上的两个斜齿轮产生微量轴向移动,这时轴1和轴3便以相反的方向转过微小的角度,使齿轮4和6分别与齿条的两相反齿而贴紧,消除间隙。
由于齿轮4,6分别与齿条的两相反齿而贴紧,当需要齿条反向运动时,齿轮4或6能马上驱动齿条换向,从而使反向双齿轮消隙。
双齿轮齿条消隙结构的改进设计
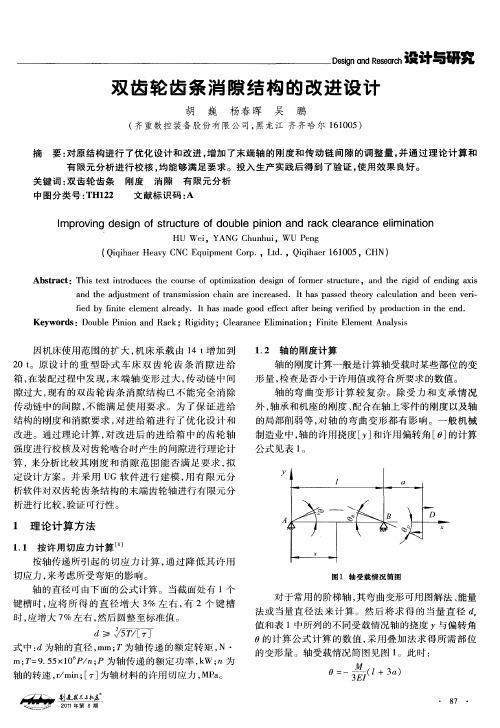
‘ao H P P
决 了现场 间隙过 大 , 能完 全消 隙的难题 ; 对末端 轴 不 针
变形 大 , 过加 粗末 端齿 轮 轴 轴 径 , 增加 刚度 , 小 通 来 减
其 中 : 小 齿轮 的分 度 圆直 径 ; m 为端 面模 数及 d为 m, 法 向模 数 ; 。 Z 为小 齿 轮 齿数 ; , 为 齿 宽 系数 ; 。咖 , 为齿数 比 ; 为 复 合 齿 形 系数 ;' 为 许 用 接 触 应力 , Op H N m 近似 取 O p i 5 O m 为试验 齿 轮 的接 / m( r : i ' i H / ;H 触疲 劳极 限应力 ; 为按 接触 强度 计 算 的最 小 安全 J s 系数 , 可取 s 1 1Op i . ;' 为许 用弯 曲应 力 ,/ m , > I F N r 简 a 化 O p 朋/ i O E " H I r 为齿 轮 材料 的弯 曲疲 劳 强 度基 s ;F
许 用挠 度 [ ] y
般用途 的轴
[ … ] 0 003~ .0 ) y ≤( .0 0 005 L [ ] .0 L Y ≤O 0 02 [ ] 00 0 0 ) Y ≤( . 1— . 3 m 许用偏转角 [ ] rd 0 /a
≤0 0 1 .0
度
y
2 原进给箱体 技术参数及使用情况
箱, 在装 配过程 中发 现 , 端 轴 变 形 过 大 , 动 链 中间 末 传
隙过大 , 现有 的双 齿 轮齿 条 消 隙结 构 已不 能 完 全 消 除 传 动链 中 的间隙 , 能 满 足 使 用 要 求 。为 了保 证 进 给 不
外, 轴承 和机 座 的刚度 、 合在 轴上 零件 的刚度 以及轴 配 的局 部 削弱等 , 轴 的弯 曲变 形 都 有影 响 。一般 机 械 对 制造 业 中 , 的许 用挠 度 [ ] 轴 Y 和许 用偏 转 角 [ ] 0 的计 算
浅谈数控双齿轮消隙减速机的研制
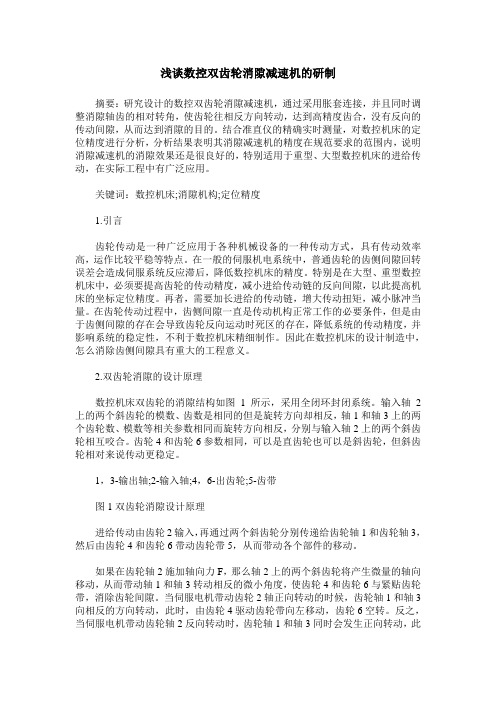
浅谈数控双齿轮消隙减速机的研制摘要:研究设计的数控双齿轮消隙减速机,通过采用胀套连接,并且同时调整消隙轴齿的相对转角,使齿轮往相反方向转动,达到高精度齿合,没有反向的传动间隙,从而达到消隙的目的。
结合准直仪的精确实时测量,对数控机床的定位精度进行分析,分析结果表明其消隙减速机的精度在规范要求的范围内,说明消隙减速机的消隙效果还是很良好的,特别适用于重型、大型数控机床的进给传动,在实际工程中有广泛应用。
关键词:数控机床;消隙机构;定位精度1.引言齿轮传动是一种广泛应用于各种机械设备的一种传动方式,具有传动效率高,运作比较平稳等特点。
在一般的伺服机电系统中,普通齿轮的齿侧间隙回转误差会造成伺服系统反应滞后,降低数控机床的精度。
特别是在大型、重型数控机床中,必须要提高齿轮的传动精度,减小进给传动链的反向间隙,以此提高机床的坐标定位精度。
再者,需要加长进给的传动链,增大传动扭矩,减小脉冲当量。
在齿轮传动过程中,齿侧间隙一直是传动机构正常工作的必要条件,但是由于齿侧间隙的存在会导致齿轮反向运动时死区的存在,降低系统的传动精度,并影响系统的稳定性,不利于数控机床精细制作。
因此在数控机床的设计制造中,怎么消除齿侧间隙具有重大的工程意义。
2.双齿轮消隙的设计原理数控机床双齿轮的消隙结构如图1所示,采用全闭环封闭系统。
输入轴2上的两个斜齿轮的模数、齿数是相同的但是旋转方向却相反,轴1和轴3上的两个齿轮数、模数等相关参数相同而旋转方向相反,分别与输入轴2上的两个斜齿轮相互咬合。
齿轮4和齿轮6参数相同,可以是直齿轮也可以是斜齿轮,但斜齿轮相对来说传动更稳定。
1,3-输出轴;2-输入轴;4,6-出齿轮;5-齿带图1双齿轮消隙设计原理进给传动由齿轮2输入,再通过两个斜齿轮分别传递给齿轮轴1和齿轮轴3,然后由齿轮4和齿轮6带动齿轮带5,从而带动各个部件的移动。
如果在齿轮轴2施加轴向力F,那么轴2上的两个斜齿轮将产生微量的轴向移动,从而带动轴1和轴3转动相反的微小角度,使齿轮4和齿轮6与紧贴齿轮带,消除齿轮间隙。
齿轮齿条设计计算公式

齿轮齿条设计计算公式齿轮和齿条是机械传动中常见的元件,用于传递动力和转速。
齿轮齿条的设计计算是设计师在进行齿轮齿条设计时所必须掌握的知识。
本文将介绍齿轮齿条设计计算的一些基本公式和原理。
一、齿轮设计计算公式1. 齿数计算公式齿数是齿轮设计中最基本的参数之一,可以通过以下公式计算:N = (π * D) / m其中,N为齿数,D为齿轮直径,m为模数。
2. 齿轮间距计算公式齿轮间距是指两个相邻齿轮之间的中心距离,可以通过以下公式计算:P = (N1 + N2) / 2 * m其中,P为齿轮间距,N1和N2分别为两个相邻齿轮的齿数,m为模数。
3. 齿轮传动比计算公式齿轮传动比是指两个相邻齿轮的转速之比,可以通过以下公式计算:i = N2 / N1其中,i为传动比,N1和N2分别为两个相邻齿轮的齿数。
4. 齿轮模数计算公式齿轮模数是指齿轮齿数和齿轮直径之间的比值,可以通过以下公式计算:m = D / N其中,m为模数,D为齿轮直径,N为齿数。
二、齿条设计计算公式1. 齿条模数计算公式齿条模数是指齿条齿数和齿条长度之间的比值,可以通过以下公式计算:m = L / N其中,m为模数,L为齿条长度,N为齿数。
2. 齿条传动比计算公式齿条传动比是指齿条的移动距离与齿轮转动角度之间的比值,可以通过以下公式计算:i = L / (π * D)其中,i为传动比,L为齿条的移动距离,D为齿轮的直径。
3. 齿条齿数计算公式齿条齿数是指齿条上的齿数,可以通过以下公式计算:N = L / m其中,N为齿数,L为齿条长度,m为模数。
三、齿轮齿条设计计算实例假设有一对齿轮,其中一个齿轮的齿数为20,直径为40mm,另一个齿轮的齿数为40,直径为80mm,模数为2mm。
我们可以通过上述公式进行计算。
根据齿数计算公式,可得第一个齿轮的齿数为20,第二个齿轮的齿数为40。
根据齿轮间距计算公式,可得齿轮间距为(20+40)/2*2=60mm。
齿轮齿条传动过程中是怎么计算的
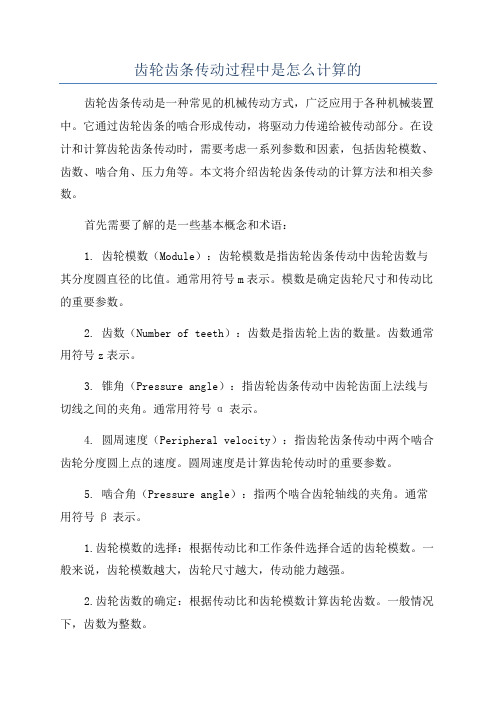
齿轮齿条传动过程中是怎么计算的齿轮齿条传动是一种常见的机械传动方式,广泛应用于各种机械装置中。
它通过齿轮齿条的啮合形成传动,将驱动力传递给被传动部分。
在设计和计算齿轮齿条传动时,需要考虑一系列参数和因素,包括齿轮模数、齿数、啮合角、压力角等。
本文将介绍齿轮齿条传动的计算方法和相关参数。
首先需要了解的是一些基本概念和术语:1. 齿轮模数(Module):齿轮模数是指齿轮齿条传动中齿轮齿数与其分度圆直径的比值。
通常用符号m表示。
模数是确定齿轮尺寸和传动比的重要参数。
2. 齿数(Number of teeth):齿数是指齿轮上齿的数量。
齿数通常用符号z表示。
3. 锥角(Pressure angle):指齿轮齿条传动中齿轮齿面上法线与切线之间的夹角。
通常用符号α表示。
4. 圆周速度(Peripheral velocity):指齿轮齿条传动中两个啮合齿轮分度圆上点的速度。
圆周速度是计算齿轮传动时的重要参数。
5. 啮合角(Pressure angle):指两个啮合齿轮轴线的夹角。
通常用符号β表示。
1.齿轮模数的选择:根据传动比和工作条件选择合适的齿轮模数。
一般来说,齿轮模数越大,齿轮尺寸越大,传动能力越强。
2.齿轮齿数的确定:根据传动比和齿轮模数计算齿轮齿数。
一般情况下,齿数为整数。
3.齿轮副的选择:根据工作条件和传动要求选择合适的齿轮副类型,如直齿轮副、斜齿轮副、锥齿轮副等。
不同类型的齿轮副具有不同的应用特点和适用范围。
4.齿轮啮合角和压力角的计算:根据齿轮模数、齿数和齿轮副类型计算齿轮的啮合角和压力角。
这两个参数影响着齿轮传动的平稳性和传动效率。
5.齿轮啮合的计算:根据齿轮齿数、模数、啮合角等参数计算齿轮的几何尺寸,包括齿高、齿根径等。
6.齿轮传动的力学计算:根据预定的传动功率、转速和工作条件计算齿轮的传动力学参数,如转矩、齿轮强度等。
7.齿轮传动的动力学计算:根据齿轮的几何参数和运动条件进行动力学计算,包括速度、加速度、振动等。
齿轮啮合间隙计算公式
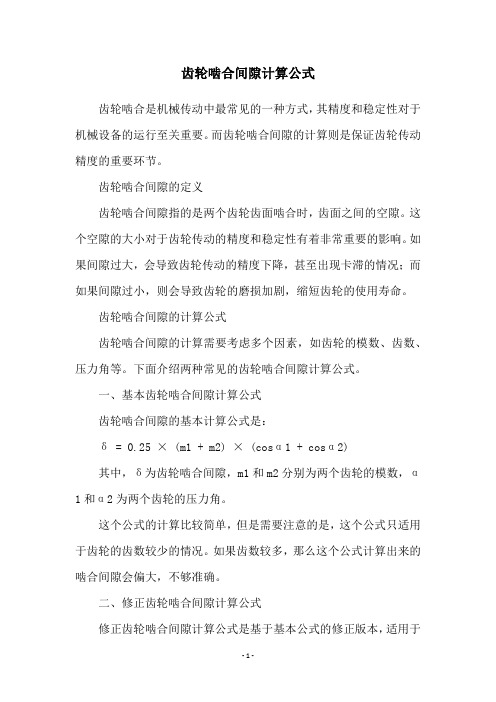
齿轮啮合间隙计算公式齿轮啮合是机械传动中最常见的一种方式,其精度和稳定性对于机械设备的运行至关重要。
而齿轮啮合间隙的计算则是保证齿轮传动精度的重要环节。
齿轮啮合间隙的定义齿轮啮合间隙指的是两个齿轮齿面啮合时,齿面之间的空隙。
这个空隙的大小对于齿轮传动的精度和稳定性有着非常重要的影响。
如果间隙过大,会导致齿轮传动的精度下降,甚至出现卡滞的情况;而如果间隙过小,则会导致齿轮的磨损加剧,缩短齿轮的使用寿命。
齿轮啮合间隙的计算公式齿轮啮合间隙的计算需要考虑多个因素,如齿轮的模数、齿数、压力角等。
下面介绍两种常见的齿轮啮合间隙计算公式。
一、基本齿轮啮合间隙计算公式齿轮啮合间隙的基本计算公式是:δ = 0.25 × (m1 + m2) × (cosα1 + cosα2)其中,δ为齿轮啮合间隙,m1和m2分别为两个齿轮的模数,α1和α2为两个齿轮的压力角。
这个公式的计算比较简单,但是需要注意的是,这个公式只适用于齿轮的齿数较少的情况。
如果齿数较多,那么这个公式计算出来的啮合间隙会偏大,不够准确。
二、修正齿轮啮合间隙计算公式修正齿轮啮合间隙计算公式是基于基本公式的修正版本,适用于齿数较多的齿轮。
修正公式如下:δ = 0.25 × (m1 + m2) × (cosα1 + cosα2) + (x1 + x2) 其中,x1和x2分别为两个齿轮的修正值。
修正值可以根据齿轮的齿数、齿形等参数进行计算。
修正值的计算比较复杂,需要根据具体情况进行分析。
齿轮啮合间隙的影响因素齿轮啮合间隙的大小受到多个因素的影响,下面介绍几个影响因素。
1. 齿轮的模数:齿轮的模数越大,齿面间的空隙越小,啮合间隙也会随之减小。
2. 齿数:齿数越多,啮合间隙也会随之增大。
3. 压力角:压力角越大,齿面间的空隙也会随之增大。
4. 齿形:齿形的不同也会影响齿轮啮合间隙的大小。
5. 加工精度:齿轮的加工精度越高,齿面间的空隙也会越小。
各种齿轮参数计算公式大全

各种齿轮参数计算公式大全齿轮是机器、仪器中使用最多的传动零件,齿轮是一个较复杂的几何体,对单个齿轮的齿廓加工误差国家标准规定了17种控制参数,根据齿轮使用要求的不同,对以上17个参数控制的要求也不同。
如何确定齿轮的精度等级以及依据其精度等级确定相关控制参数的公差值,是齿轮设计的关键所在。
齿轮的基本参数:齿轮的组成结构一般有轮齿、齿槽、端面、法面、齿顶圆、齿根圆、基圆和分度圆。
(1)齿数:一个齿轮的轮齿总数叫齿数,用Z表示。
小齿轮的齿数可取为z1=20~40。
开式(半开式)齿轮传动,由于轮齿主要为磨损失效,为使齿轮不致过小,故小齿轮不亦选用过多的齿数,一般可取z1=17~20。
(2)模数由于齿轮的分度圆直径 d 可由其周长 zp 确定,即d = zp/π。
为便于设计、计算、制造和检验,令p/π= m ,m 称为齿轮的模数,并已标准化。
它是决定齿轮大小的主要参数。
分度圆直径d=mZ,所以m=d/z。
(3)压力角α 即分度圆压力角,并规定其标准值为α=20°。
它是决定齿轮齿廓形状的主要参数。
分度圆直径d=mZ/cosβ压力角rb=rcosα=1/2mzcosα在两齿轮节圆相切点P处,两齿廓曲线的公法线(即齿廓的受力方向)与两节圆的公切线(即P点处的瞬时运动方向)所夹的锐角称为压力角,也称啮合角。
对单个齿轮即为齿形角。
标准齿轮的压力角一般为20”。
在某些场合也有采用α=14.5° 、15° 、22.50°及25°等情况。
(4)齿顶高系数和顶隙系数:h*a 、C*两齿轮啮合时,总是一个齿轮的齿顶进入另一个齿轮的齿根,为了防止热膨胀顶死和具有储成润滑油的空间,要求齿根高大于齿顶高。
为次引入了齿顶高系数和顶隙系数。
正常齿:h*a =1; C*=0.25 短齿:h*a =0.8; C*=0.3一对相互啮合的齿轮,模数、压力角必须相等。
标准齿轮的压力角(对单个齿轮而言即为齿形角)为20°齿轮参数计算公式大全:1. 内齿模数齿轮2. 直齿模数齿轮3. 斜齿模数齿轮4. 伞齿模数齿轮5. 变位模数齿轮6. 直齿径节齿轮7. 斜齿径节齿轮8. 齿条。
齿轮各部分计算公式

齿轮各部分计算公式
齿轮是一种常见的机械传动装置,由于其结构复杂,设计计算也相对繁琐。
下面将介绍齿轮各部分的计算公式,包括齿数计算、模数计算、齿廓曲线计算等。
一、齿数计算公式:
齿数是齿轮设计中最基本的参数之一、一般情况下,要求输入齿轮中心距、模数和齿数,通过计算可以得到另一个齿轮的齿数。
1.齿数计算公式:
n=(πd)/m
其中,n为齿数,d为齿轮的规定直径,m为模数。
2.齿轮中心距计算公式:
a=m(z1+z2)/2
其中,a为齿轮中心距,m为模数,z1、z2为两个齿轮的齿数。
二、模数计算公式:
模数是齿轮设计中重要的参数之一,是决定齿轮尺寸的关键。
1.模数计算公式:
m=d/z
其中,m为模数,d为齿轮的规定直径,z为齿数。
三、齿廓曲线计算公式:
齿廓曲线是描述齿轮齿形的曲线,常用的齿廓曲线有圆弧、渐开线等。
1.圆弧齿廓曲线计算公式:
y = r - (r' + r' tanα)
其中,y为齿廓偏差,r为齿轮基圆半径,r'为齿轮分度圆半径,α
为压力角。
2.渐开线齿廓曲线计算公式:
x = (r + r α) cosθ + m tanθ - m tanα
其中,x为齿廓偏差,r为齿轮基圆半径,α为压力角,θ为齿廓角。
以上仅是齿轮计算中的一部分公式,实际的齿轮设计计算还需要考虑
到材料强度、结构刚度等因素。
此外,齿轮的传动特性、工作精度也需要
在设计时进行综合考虑。
消隙齿轮传动机构回差分析与计算
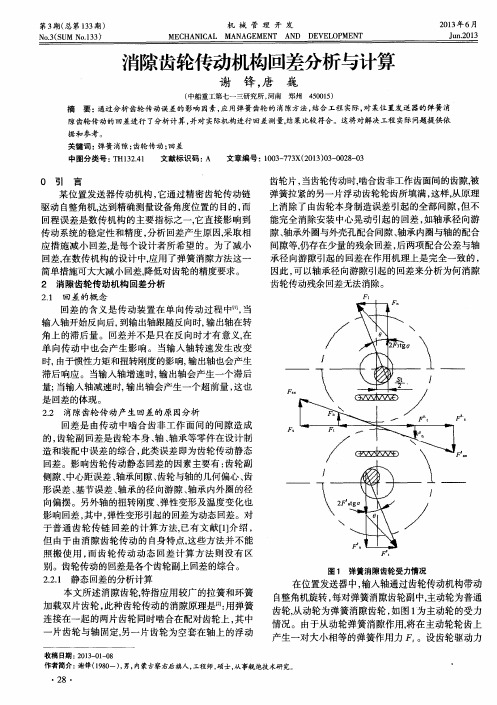
B=B + B ±3 .
( 8 )
3 某位置发送器消隙齿轮传动回差计算 某位置发送器消隙齿轮传动构造 , 如图 2 。 已知齿轮轴径均为 7 m m, 轴承径向游隙公差均为 1 0 m, 弹簧力 与传动力 比值为 / F =2, 传递载荷 力矩 0 . 0 0 6 N・ m, 系统要求在 自整角机轴 4 处测得 的 回差不 大 于 6 。
第3 期( 总第l 3 3 期)
N o . 3 ( S U M N o . 1 3 3 )
机 械 管 理 开 发
M E C HA N I C A L MA N A G E M E N T A N D D E V E L O P ME N T
2 0 1 3 年 6月
J u n . 2 01 3
2 . 1 回差 的概 念
齿轮片, 当齿轮传动时, 啮合齿非工作齿面间的齿隙, 被 弹簧拉 紧 的另 一 片浮动 齿 轮轮齿 所 填满 , 这 样, 从原 理 上消除了由齿轮本身制造误差引起的全部间隙, 但不 能完全消除安装 中心晃动引起的回差 , 如轴承径向游 隙、 轴承外圈与外壳孑 L 配合间隙 、 轴承内圈与轴的配合 间隙等, 仍存在少量的残余回差 , 后两项配合公差与轴 承径 向游隙引起的回差在作用机理上是完全一致 的, 因此 , 可以轴承径 向游隙引起的回差来分析为何消隙 齿轮传动残余 回差无法消除。
一
图 1 弹簧消隙齿轮 受力情况
在位置发送器 中, 输入轴通过齿轮传动机构带动 自整角机旋转 , 每对弹簧消隙齿轮副 中, 主动轮为普通 齿轮, 从动轮为弹簧消隙齿轮 , 如图 1 为主动轮的受力 情况 。由于从动轮弹簧 消隙作用, 将在主动轮轮齿上 产生一对大小相等 的弹簧作用力 。设齿轮驱动力
齿轮系数计算公式资料

齿轮系数计算公式(国标齿轮压力角普遍为cos20°)名称代号计算公式齿数Z齿数模数m m=p/πm=齿距/π分度圆直径 d d=mz(齿中径) d=模数X齿数压力角cosαcosα=(W1-W)/3.14mW =跨K个齿的公法线长度W1=跨K+1个齿的公法线长度基圆直径d b d b= d X cosα(两齿轮运行中形成的线)d b=分度圆直径X压力角齿顶圆直径da da=(Z+2)mda=(齿数+2)X模数齿根圆直径df df= (Z-2.5)mdf= (齿数-2.5)X模数齿顶高ha ha=ha*mha=ha*模数(常用ha*=1)(短齿ha*=0.8)顶隙 c c=c*mc=c*模数(常用c*=0.25)(短齿c*=0.3)齿根高hf hf=ha+c=(ha*+c*)m=1.25m齿高h h=ha+hf=m+1.25m=2.25m齿距P P=mπP=模数Xπ齿厚S槽宽e S=e=P/2中心距(与齿轮副合配)a a=d1/2+d2/2=(Z1+Z2)m/2(d1代表一个齿轮的分度圆直径,d2代表另一个齿轮的分度圆直径)(Z1代表一个齿轮的齿数,Z2代表另一个齿轮的齿数)(m代表齿轮模数)模数选择优先选择(1 1.25 1.5 2 2.5 3 4 5 6 8 10 12 14 16 20 2532 40 50)可以选用(1.75 2.25 2.75 3.5 4.5 5.5 7 9 14 18 22 28 26 45)尽可能不用(3.25 3.75 6.5 11 30)压力角选择米制:20°14.5°15°17.5°22.5°25°28°30°英制:20°14.5°15°其次16°17°17.5°22.5°25°cos20=0.9397 cos30=0.866 cos45=0.7071美标与日标跟国标一样的,可能他们比较多的采用“节径”这个概念,我们相应来说比较多的用的是“模数”。
双齿轮齿条消隙结构的实验研究

・60・ 齐 齐 哈 尔 大 学 学 报 2012年(6). The compound 3 was isolated from this plant for the first time.Key word: Portulaca oleracea L.;DL-epiloliolide;sitosterol双齿轮齿条消隙结构的试验研究1 试验装置工艺实施措施试验装置工艺实施措施:(1)齿条的安装调试。
采取与CK611250E×70/18J-1工艺文件中齿条安装工艺略有不同的方法。
为保证齿条安装精度,调整齿条背面。
把紧齿条,使把合面0.03塞尺不入。
将头2块齿条卸下,在工装上将它们对接,并对它们施加一定预紧力,用牙条样板检查对接处的齿间距,若不能满足要求,刮研两接头处,使对接处合格,将它们作为第1,2节。
按同样方法将第2,3节齿条的接头处调刮,使之合格,以下依次进行,并标出顺序号。
齿条全部调刮后,按顺序号再将在床身上把紧一端第1节齿条,钻铰销钉孔并装销钉,轻微松开第2节到最后一节的把合螺钉,从最后一节齿条对齿条施加预紧力,施加预紧力为该机床最大轴向驱动力,使齿条对接紧密接触,把紧各个齿条,并在最后一节齿条上装上销钉。
(2)纵向大刀架的安装调试。
将大刀架与导轨合研,大刀架与导轨接触的滑动面(A面)研点12点/25 mm×25mm,刮研斜铁。
用0.03塞尺检验各滑动面,插入深度不大于15mm,并使大刀架下底(E面)垂直于床身斜齿条把合面(0.01mm),示意图见图1。
(3)溜板箱的安装调试。
将溜板箱用垫铁、千斤顶支起找中,推紧溜板箱使小齿轮与齿条紧密接触,反号大刀架螺孔。
先将大刀架与溜板箱把紧,在双齿轮齿条没有预紧力的情况下,检查2个小齿轮与齿条的接触情况。
若接触面不均匀,调刮溜板箱与大刀架的把合面,使小齿轮与齿条接触面保持均匀接触,溜板箱与大刀架连接紧固,并装销钉。
保证滑动面0.03塞尺插入深度不超过15mm,结合面0.03塞尺不入。
双齿轮消隙工作原理
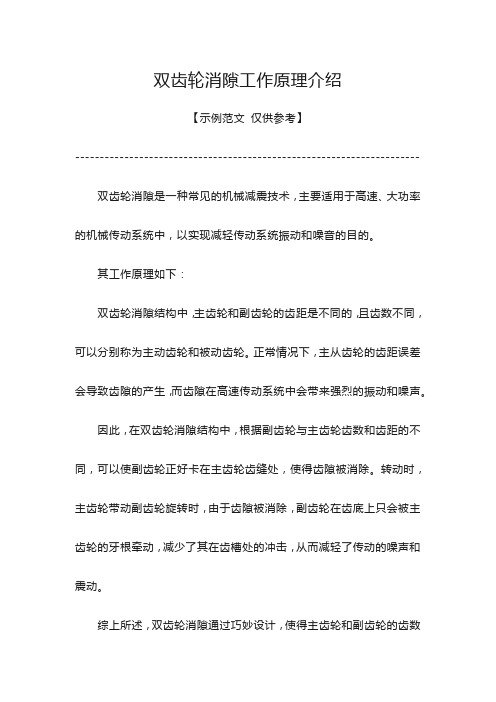
双齿轮消隙工作原理介绍
【示例范文仅供参考】
---------------------------------------------------------------------- 双齿轮消隙是一种常见的机械减震技术,主要适用于高速、大功率的机械传动系统中,以实现减轻传动系统振动和噪音的目的。
其工作原理如下:
双齿轮消隙结构中,主齿轮和副齿轮的齿距是不同的,且齿数不同,可以分别称为主动齿轮和被动齿轮。
正常情况下,主从齿轮的齿距误差会导致齿隙的产生,而齿隙在高速传动系统中会带来强烈的振动和噪声。
因此,在双齿轮消隙结构中,根据副齿轮与主齿轮齿数和齿距的不同,可以使副齿轮正好卡在主齿轮齿缝处,使得齿隙被消除。
转动时,主齿轮带动副齿轮旋转时,由于齿隙被消除,副齿轮在齿底上只会被主齿轮的牙根牵动,减少了其在齿槽处的冲击,从而减轻了传动的噪声和震动。
综上所述,双齿轮消隙通过巧妙设计,使得主齿轮和副齿轮的齿数
和齿距产生差异,使得在副齿轮在齿底的时候,在主齿轮齿缝处压紧,消除齿隙,从而减小传动系统的噪声和振动问题。
两齿轮产生的轴向力相互抵消
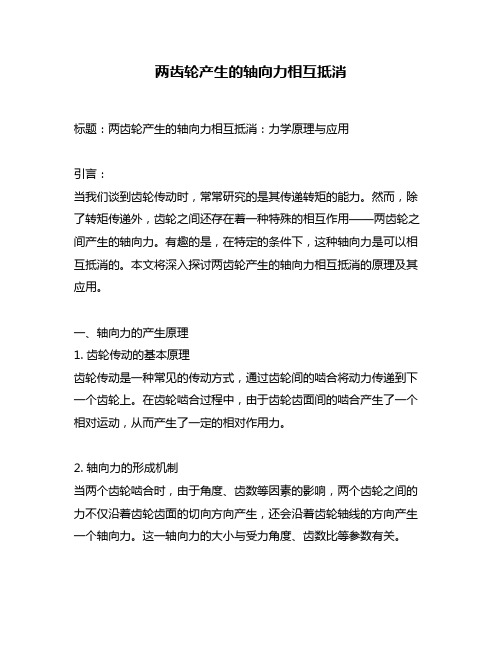
两齿轮产生的轴向力相互抵消标题:两齿轮产生的轴向力相互抵消:力学原理与应用引言:当我们谈到齿轮传动时,常常研究的是其传递转矩的能力。
然而,除了转矩传递外,齿轮之间还存在着一种特殊的相互作用——两齿轮之间产生的轴向力。
有趣的是,在特定的条件下,这种轴向力是可以相互抵消的。
本文将深入探讨两齿轮产生的轴向力相互抵消的原理及其应用。
一、轴向力的产生原理1. 齿轮传动的基本原理齿轮传动是一种常见的传动方式,通过齿轮间的啮合将动力传递到下一个齿轮上。
在齿轮啮合过程中,由于齿轮齿面间的啮合产生了一个相对运动,从而产生了一定的相对作用力。
2. 轴向力的形成机制当两个齿轮啮合时,由于角度、齿数等因素的影响,两个齿轮之间的力不仅沿着齿轮齿面的切向方向产生,还会沿着齿轮轴线的方向产生一个轴向力。
这一轴向力的大小与受力角度、齿数比等参数有关。
二、轴向力的击打效应1. 轴向力的影响在传动过程中,轴向力的存在会引起两个齿轮之间的轴向击打效应。
这种击打会产生很大的冲击力和噪声,严重影响齿轮传动的稳定性和寿命。
2. 问题的解决然而,通过设计合理的齿轮配对和使用合适的基座支撑结构,我们可以使得两齿轮之间产生的轴向力相互抵消,从而解决轴向击打的问题。
在实际的工程设计中,我们常常使用多齿轮级联传动和预紧轴承等方式来实现这一目的。
三、轴向力抵消的应用1. 工业传动系统中的应用轴向力抵消技术在工业传动系统中有着广泛的应用。
汽车变速器、工业机械设备等都会采用这种技术以提高传动的可靠性和稳定性。
2. 精密仪器中的应用在一些对传动精度要求较高的领域,如数控机床、精密仪器等,轴向力抵消技术也起到了重要的作用。
对于这些领域,通过轴向力的相互抵消,可以减少传动过程中的振动和摩擦,提高传动精度和寿命。
四、个人观点与理解作为一种重要的传动技术,两齿轮产生的轴向力相互抵消不仅解决了传动过程中的问题,还提高了传动的可靠性和性能。
通过对轴向力产生原理的深入研究和应用的不断探索,我们可以进一步优化齿轮传动系统的设计和运行,以满足不同领域的需求。
两齿轮啮合节圆计算
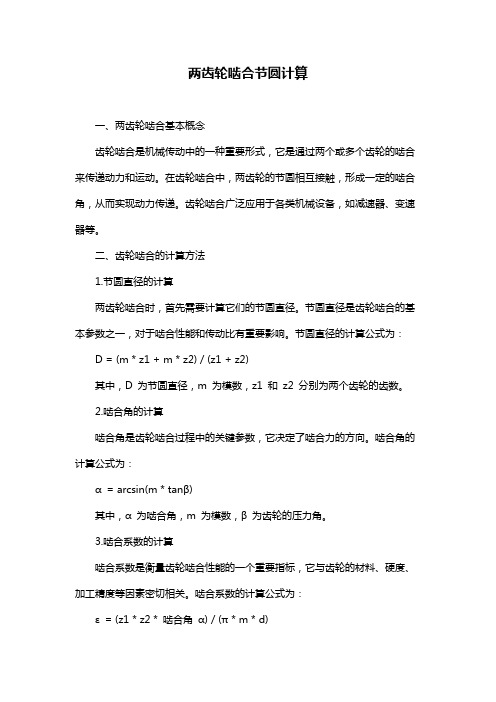
两齿轮啮合节圆计算一、两齿轮啮合基本概念齿轮啮合是机械传动中的一种重要形式,它是通过两个或多个齿轮的啮合来传递动力和运动。
在齿轮啮合中,两齿轮的节圆相互接触,形成一定的啮合角,从而实现动力传递。
齿轮啮合广泛应用于各类机械设备,如减速器、变速器等。
二、齿轮啮合的计算方法1.节圆直径的计算两齿轮啮合时,首先需要计算它们的节圆直径。
节圆直径是齿轮啮合的基本参数之一,对于啮合性能和传动比有重要影响。
节圆直径的计算公式为:D = (m * z1 + m * z2) / (z1 + z2)其中,D 为节圆直径,m 为模数,z1 和z2 分别为两个齿轮的齿数。
2.啮合角的计算啮合角是齿轮啮合过程中的关键参数,它决定了啮合力的方向。
啮合角的计算公式为:α= arcsin(m * tanβ)其中,α为啮合角,m 为模数,β 为齿轮的压力角。
3.啮合系数的计算啮合系数是衡量齿轮啮合性能的一个重要指标,它与齿轮的材料、硬度、加工精度等因素密切相关。
啮合系数的计算公式为:ε= (z1 * z2 * 啮合角α) / (π * m * d)其中,ε为啮合系数,z1 和z2 为两个齿轮的齿数,α 为啮合角,m 为模数,d 为齿轮的径向距离。
4.接触比的计算接触比是齿轮啮合过程中另一个重要参数,它反映了齿轮啮合的平稳性。
接触比的计算公式为:ε" = (z1 * 啮合角α") / (π * m * d")其中,ε" 为接触比,z1 为齿轮的齿数,α" 为啮合角,m 为模数,d" 为齿轮的径向距离。
三、两齿轮啮合的应用齿轮啮合在机械传动中具有广泛的应用,如减速器、变速器、齿轮箱等。
通过合理设计齿轮啮合参数,可以实现平稳、高效、低噪音的传动性能。
四、总结与展望两齿轮啮合计算是齿轮传动设计中的基础内容,掌握啮合计算方法对于提高齿轮传动的性能至关重要。
在实际工程应用中,还需考虑齿轮的材料、加工精度、载荷等多种因素,以实现优质齿轮啮合。
有关齿轮传动比的原理、计算方法及其分配原则

传动比原理机构中瞬时输入速度与输出速度的比值称为机构的传动比.机构中两转动构件角速度的比值,也称速比。
构件a和构件b的传动比为Ⅰ=ωa/ ωb=na/nb,式中ωa和ωb分别为构件a和b的角速度(弧度/秒);na和nb分别为构件a和b的转速(转/分)(注:ω和n后的a 和b为下脚标)。
当式中的角速度为瞬时值时,则求得的传动比为瞬时传动比。
当式中的角速度为平均值时,则求得的传动比为平均传动比。
对于大多数齿廓正确的齿轮传动和摩擦轮传动,瞬时传动比是不变的对于链传动和非圆齿轮传动,瞬时传动比是变化的。
对于啮合传动,传动比可用a和b轮的齿数Za和Zb表示,i=Zb/Za;对于摩擦传动,传动比可用a和b轮的直径和b表示,i=b/a。
这时传动比一般是表示平均传动比。
在液力传动中,液力传动元件传动比一般指的是涡轮转速和泵轮转速B的比值,即=/B。
液力传动元件也可与机械传动元件(一般用各种齿轮轮系)结合使用,以获得各种不同数值的传动比(轮系的传动比见轮系)。
传动比计算方法传动比=使用扭矩÷9550÷电机功率×电机功率输入转数÷使用系数传动比=主动轮转速与从动轮的比值=它们分度圆直径的反比。
即:i=n1/n2=D2/D1i=n1/n2=z2/z1(齿轮的)单级与多级传动单级传动指的是没有变速的,传动比是恒定的。
多级是传动比可调的,具有多级变速比得传动方式。
对于多级齿轮传动1、每两轴之间的传动比按照上面的公式计算2、从第一轴到第n轴的总传动比按照下面公式计算: 总传动比ι=(Z1/Z2)×(Z3/Z4)×(Z5/Z6)……=(n2/n1)×(n4/n3)×(n6/n5)…… 与齿轮半径没有关系传动比分配原则多级减速器各级传动比的分配,直接影响减速器的承载能力和使用寿命,还会影响其体积、重量和润滑。
传动比一般按以下原则分配:使各级传动承载能力大致相等;使减速器的尺寸与质量较小;使各级齿轮圆周速度较小;采用油浴润滑时,使各级齿轮副的大齿轮浸油深度相差较小。
双电机消隙
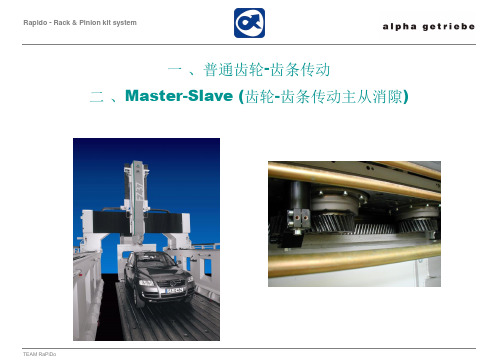
F2S
equal flank
F
S
TP Ei A Mn
2io R
a Pn i D o k
i t s y s t e m
Master-Slave
2. 原理与运行模式—图形 Master
Load direction Slave
F2M
Contra flank
F2S
Change over with backlash
s, v, a
TP Ei A Mn R o a Pn i D o k
举 例 :i C a si et
Master-Slave
2.原理与运行模式— 张力计算
s 1y s :t e Fm
a
= 0 N F
2ห้องสมุดไป่ตู้M
= + 1 0 0 N ; F
2 S
=
Vorlagen Nr.: 1097-D005821 Rev.: 02
TP Ei A Mn R o a Pn i D o k
i
i t s y s t e m
Master-Slave
4. 优缺点
G 无间隙 (消除了齿面之间的间隙) G 更高的刚性 ( 2 x 单个刚性) G 更好的动态性能 (两个驱动单元同时工作) G 更高的精度 (因为更好的刚性和零间隙 ) G 可选用更小的减速箱、电机、齿轮齿条 H 成本更高 (2套驱动单元) H 更大的体积 ( 2x 电机 2x 齿轮箱) H 更长的调试时间
经验值 => 最大张力 大约. 40 % 系数 c = 1,4
=> 通常张力 大约. 10 %
系数 c = 1,1
Vorlagen Nr.: 1097-D005821 Rev.: 02
驱动双齿轮啮合齿条的计算
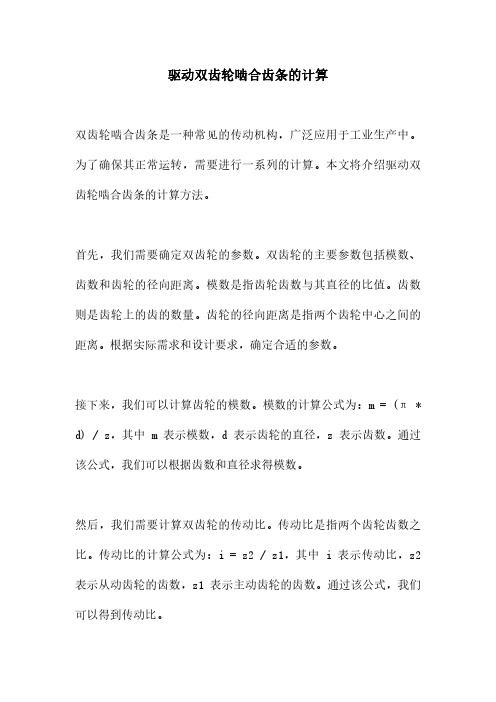
驱动双齿轮啮合齿条的计算双齿轮啮合齿条是一种常见的传动机构,广泛应用于工业生产中。
为了确保其正常运转,需要进行一系列的计算。
本文将介绍驱动双齿轮啮合齿条的计算方法。
首先,我们需要确定双齿轮的参数。
双齿轮的主要参数包括模数、齿数和齿轮的径向距离。
模数是指齿轮齿数与其直径的比值。
齿数则是齿轮上的齿的数量。
齿轮的径向距离是指两个齿轮中心之间的距离。
根据实际需求和设计要求,确定合适的参数。
接下来,我们可以计算齿轮的模数。
模数的计算公式为:m=(π* d)/z,其中m表示模数,d表示齿轮的直径,z表示齿数。
通过该公式,我们可以根据齿数和直径求得模数。
然后,我们需要计算双齿轮的传动比。
传动比是指两个齿轮齿数之比。
传动比的计算公式为:i=z2/z1,其中i表示传动比,z2表示从动齿轮的齿数,z1表示主动齿轮的齿数。
通过该公式,我们可以得到传动比。
接着,我们可以计算双齿轮的啮合角。
啮合角是指相对于齿轮的齿廓曲线,两个相邻齿之间的夹角。
啮合角的计算公式为:α= cos^(-1)((r1+r2)/c),其中α表示啮合角,r1和r2分别表示主动齿轮和从动齿轮的半径,c表示两个齿轮中心之间的距离。
通过该公式,我们可以得到啮合角。
最后,我们可以计算双齿轮的传动速比。
传动速比是指从动齿轮转速和主动齿轮转速之比。
传动速比的计算公式为:v=(n2/n1)* (d1/d2),其中v表示传动速比,n1和n2分别表示主动齿轮和从动齿轮的转速,d1和d2分别表示主动齿轮和从动齿轮的直径。
通过该公式,我们可以得到传动速比。
综上所述,驱动双齿轮啮合齿条的计算涉及参数的确定,包括模数、齿数和齿轮的径向距离。
然后,根据这些参数,计算齿轮的模数、传动比、啮合角和传动速比。
这些计算对于确保双齿轮啮合齿条的正常运转非常重要。
齿轮齿条的传动计算

齿轮齿条的传动计算
齿轮与齿条传动特点
齿轮作回转运动,齿条作直线运动,齿条可以看作一个齿数无穷多的齿轮的一部分,这时齿轮的各圆均变为直线,作为齿廓曲线的渐开线也变为直线。
齿条直线的速度v 与齿轮分度圆直径d 、转速n 之间的关系为
v=(/)60
dn mm s π
式中 d ——齿轮分度圆直径,mm ; n ——齿轮转速,min r 。
其啮合线12N N 与齿轮的基圆相切1N ,由于齿条的基圆为无穷大,所以啮合线与齿条基圆的切点2N 在无穷远处。
齿轮与齿条啮合时,不论是否标准安装(齿轮与齿条标准安装即为齿轮的分度圆与齿条的分度圆相切),其啮合角'α恒等于齿轮分度圆压力角α,也等于齿条的齿形角;齿轮的节圆也恒与分度圆重合。
只是在非标准安装时,齿条的节线与分度线不再重合。
齿轮与齿条正确啮合条件是基圆齿距相等,齿条的基圆齿距是其两相邻齿廓同侧直线的垂直距离,即cos cos b P P m απα==。
齿轮与齿条的实际啮合线为12B B ,即齿条顶线及齿轮齿顶圆与啮合线12N N 的交点2B 及1B 之间的长
度。
齿轮齿条传动的几何尺寸计算 齿轮与齿条传动的尺寸计算见表 表 齿轮齿条传动的几何尺寸计算
齿条的主要特点:
(1)由于齿条齿廓为直线,所以齿廓上各点具有相同的压力角,且等于齿廓的倾斜角,此角称为齿形角,标准值为20°。
(2)与齿顶线平行的任一条直线上具有相同的齿距和模数。
(3)与齿顶线平行且齿厚等于齿槽宽的直线称为分度线(中线),它是计算齿条尺寸的基准线。
- 1、下载文档前请自行甄别文档内容的完整性,平台不提供额外的编辑、内容补充、找答案等附加服务。
- 2、"仅部分预览"的文档,不可在线预览部分如存在完整性等问题,可反馈申请退款(可完整预览的文档不适用该条件!)。
- 3、如文档侵犯您的权益,请联系客服反馈,我们会尽快为您处理(人工客服工作时间:9:00-18:30)。
关于双齿轮齿圈消隙结构传动装置的理论计算
双齿轮齿圈及消隙结构主要应用在双柱立式车、铣、钻、镗加工中心的工作台分度机构上,本文以我公司(齐重数控装备股份有限公司)CXH5250F×40/50L 型数控双柱立式加工中心为例,研究其工作台分度双齿轮齿圈消隙结构进给传动装置的理论计算。
CXH5250F×40/50L型数控双柱立式加工中心采用西门子840D数控系统,X、Z、C轴三轴联动,。
该机床精度要求高,工作台分度机构允差±8″,工作台的径向跳动和钻削主轴的径向跳动按国家标准的允差值压缩30%。
一、工作台分度进给传动装置的理论计算
工作台分度进给结构是该机床的关键结构,首先根据图纸,分析工作台分度机构的结构、传动原理并进行传动链传动误差的理论计算。
1、传动链误差传递规律计算
双齿轮消隙传动装置系统,在传动链中,传动误差由动力输入环节向着末端执行元件传递和累积,最后集中反映到末端件上,使主轴产生运动误差。
传动误差的计算,相似于运动位移的计算。
运动位移是在啮合过程中由主动件传给被动件的,并且只沿瞬时啮合点处的公法线方向传递。
由于两传动件在公法线方向上的瞬时速度分量相等,所以两传动件在啮合点处的公法线方向上的瞬时位移量也应相等,误差传递也是这样。
对应于转角误差△φ1的线性误差△s1为:
△S1=△φ1×r1
△φ1—齿轮的转角误差
r1—齿轮的回转半径
与齿轮1相啮合的齿轮2
也同时产生等值的线性位移,
即△S2=△S1
同理△S2=△φ2 ×r2
△φ2 =△S2/ r2=△φ1×r1 / r2
=△φ1×I 1
△S2—齿轮2的线性误差
△φ2—齿轮2的回转半径
I 1 —第一对啮合齿轮的传动比
同理:
△φ3=△φ2=△φ1×I 1
△S3=△φ3×r3=△φ1×I 1×r3
△S4=△S3=△φ1×I 1×r3=△φ4×r4
△φ4=△S4 / r4=△φ1×I 1×r3 / r4=△φ1×I 1×I 2
由此可见,各个运动件的误差都按一定的传动比依次传递。
因此,整个传动链中各传动件的误差反映到末端件(主轴)上总的转角误差为:
式中:I m—末端传动副的传动比
△φm—末端传动件的转角误差
根据以上原理及公式,双齿轮消隙传动装置传动链总的转角误差为:
△φ1为电机轴上的同步带轮转角误差,△φ2、△φ3…△φ9分别为各级齿轮转角误差。
由上面的原理及公式得出,传动链中越靠近末端的齿轮对传动链的精度影响越大。
为此我们只计算传动链末端两级传动齿轮的转角误差。
我们知道,其中,△S可以近似认为齿轮周节累积误差,r为齿轮回转半径,即齿轮分度园半径。
双齿轮消隙传动装置上传动链末端齿轮计算数据见表(一)
表(一)
将以上数据代入公式得出:
(rad)
故φ = 0.000306 ×=0.01750=1'03"
因此,双齿轮消隙传动装置传动链中各传动件的误差反映到末端工作台转角误差近似为1'03"。
由于以上计算△S取各齿轮传动件最大周节累积误差,因此传动装置传动链中各传动件的误差反映到末端工作台转角误差要小于1'03"。
2、双齿轮消隙传动装置传动链消隙油缸压力计算
双齿轮消隙传动装置消隙原理为:通过Ⅳ轴上两个旋向相反齿轮,使传动链分成两个相同的传动链,即两个相同的传动链末端的齿轮同时与大齿圈相啮合, Ⅳ轴轴端设有油缸,通过油缸压力油,使Ⅳ轴带动两个旋向相反齿轮向下移动,进而使与大齿圈相啮合的齿轮产生方向相反微小转动,这样消除传动链的间隙。
工作台主轴箱中两个传动链末端齿轮与齿圈接触的示意图见图2:
图2齿轮与齿圈接触示意图
图中F1、F2分别为两个齿轮对齿圈的作用力,F1与F1′、F2与F2′是作用力与反作用力,F为切削时作用于工作台主轴上的力。
在没有切削力作用的情况下,F1=F2是消隙油缸压力传递到齿轮产生的。
切削力作用后,F2增大F1减小。
切削力达到最大时,为保证工作台的分度精度,要使第一个齿轮和齿圈间的接触力F1>0,即第一个齿轮与齿圈保持接触不产生间隙。
下面求消隙油缸压力P:
巳知该机构最大扭矩为50KN·m,根据传动系统图我们可以得出消隙油缸Ⅳ轴上齿轮1的最大力矩,而消隙油缸压力应克服此时最大力矩所产生的轴向力。
齿轮1是螺旋角为β斜齿轮,由轴向力F导出切向力P'。
P'=F=P×S
设齿轮1的半径为R1,作用在齿轮1的力矩为N,则有:
P×S×R1/ tgβ=N
N= 50KN·m /I
其中:P——消隙油缸压力
S——消隙油缸面积S=×0.1252=0.0122 m2
I——Ⅳ轴上的齿轮至工作台齿圈的传动比I=50/30×70/30=35/9
β——斜齿轮1的螺旋角β= 2507'30"
R1——齿轮1的半径R=0.0994m
将以上数据代入得出:P=4.9 MPa
消隙油缸的压力最大为4.9MPa
3.双齿轮消隙传动装置消隙油缸行程计算
由前文我们得知,传动装置传动链转角误差最大为1'03", 消隙油缸行程,由消隙油缸压力与面积及行程的乘积与工作台转矩与转角的乘积相等求得。
设消隙油缸压力为P,齿轮1的半径为R1,则有:
P×S×L = P×S / tgβ×R1×I×θ
其中:P×S / tgβ——齿轮1所受的切向力
P×S ——齿轮1所受的轴向力
S——消隙油缸面积
I——Ⅳ轴上的齿轮至工作台齿圈的传动比I=50/30×70/30=35/9
β——斜齿轮1的螺旋角β= 2507'30"
L——消隙油缸行程
θ——工作台转角θ=0.000306(rad)
R1——齿轮1半径R1=0.09940(m)
因此消隙油缸行程L= R1×I×θ/ tgβ
=0.0994××0.000306/ tg25.125
=2.5×10-4(m)= 0.25mm
二、结论
通过计算得知,按各齿轮传动件最大周节累积误差计算,双齿轮消隙传动链中各传动件的误差反映到末端工作台转角误差最大为1'03"。
这与机床实际要求±8"相差很大,为达到机床的要求,必须控制传动链齿轮的加工精度。
按工作台最大转角误差1'03"计算,传动装置消隙油缸行程最大为0.25mm,机床C轴传动装置消隙油缸行程图纸设计给定为10mm。
双齿轮消隙传动装置没施加预紧力时,机床工作台主轴的分度精度变化很大。
施加一定预紧力并通过数控系统进行反向间隙补偿后,可满足设计要求,应用于产品生产。
注:文章内所有公式及图表请以PDF形式查看。