主生产计划和物料需求计划逻辑计算(数据略有变化:提供演算例题结果,有助于理解计算过程)20150106NEW
一文厘清MRP物料需求计划和计算逻辑
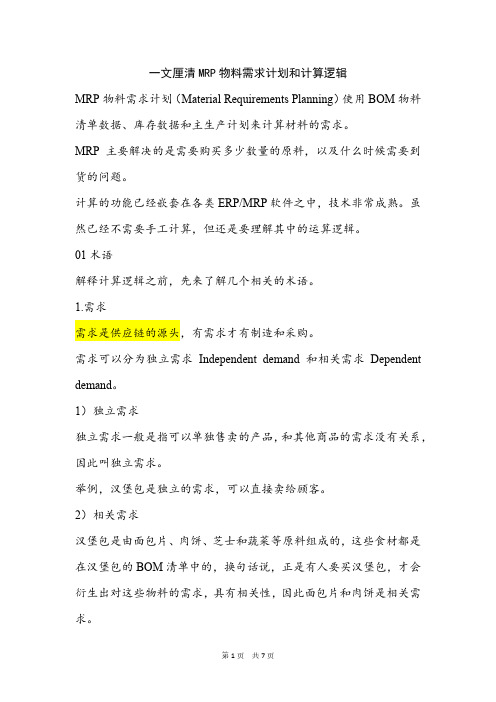
一文厘清MRP物料需求计划和计算逻辑MRP物料需求计划(Material Requirements Planning)使用BOM物料清单数据、库存数据和主生产计划来计算材料的需求。
MRP主要解决的是需要购买多少数量的原料,以及什么时候需要到货的问题。
计算的功能已经嵌套在各类ERP/MRP软件之中,技术非常成熟。
虽然已经不需要手工计算,但还是要理解其中的运算逻辑。
01术语解释计算逻辑之前,先来了解几个相关的术语。
1.需求需求是供应链的源头,有需求才有制造和采购。
需求可以分为独立需求Independent demand和相关需求Dependent demand。
1)独立需求独立需求一般是指可以单独售卖的产品,和其他商品的需求没有关系,因此叫独立需求。
举例,汉堡包是独立的需求,可以直接卖给顾客。
2)相关需求汉堡包是由面包片、肉饼、芝士和蔬菜等原料组成的,这些食材都是在汉堡包的BOM清单中的,换句话说,正是有人要买汉堡包,才会衍生出对这些物料的需求,具有相关性,因此面包片和肉饼是相关需求。
需要预测的是独立需求的商品,而相关需求是根据BOM计算出来的,因此不需要预测。
需要注意的是,同一件商品可以既是独立需求,又是相关需求。
当汉堡包是单品时,是独立需求,在套餐中,汉堡包与可乐和薯条搭配在一起销售,就变成相关需求。
因此,商品的需求属性可以转换。
2.订单1)计划订单Planned Order若把快餐店看作一家工厂,在这里生产的物品有汉堡包、薯条和其他小食,经过加热和油炸等工艺把食材加工成食品。
用于生产的原料都是由供应商提供,快餐店要管理好采购订单,确保始终有足够的原材料。
MRP的一个重要任务就是用来计算采购量和到货时间,然后输出系统建议的订货计划,这就是Planned Order,也叫计划订单。
计划订单是系统建议的订单数量、发布日期和到货日期。
若情况发生变化,在后续处理过程中,系统可以修改或取消订单。
已发布订单Released Order是指已经给供应商发布的采购订单Purchase order。
主生产计划、主需求计划与物料需求计划
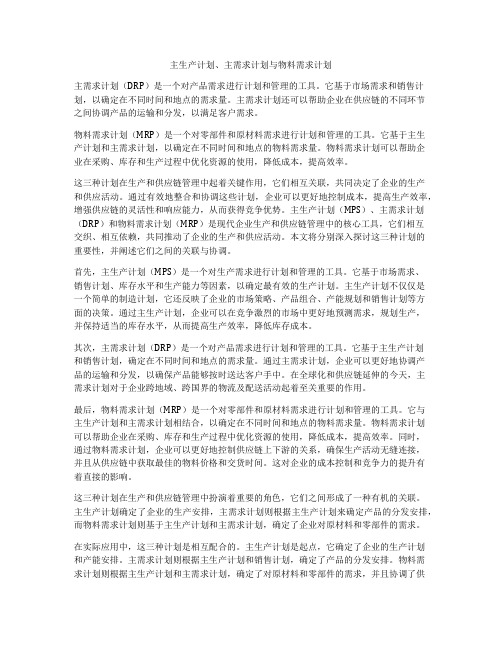
主生产计划、主需求计划与物料需求计划主需求计划(DRP)是一个对产品需求进行计划和管理的工具。
它基于市场需求和销售计划,以确定在不同时间和地点的需求量。
主需求计划还可以帮助企业在供应链的不同环节之间协调产品的运输和分发,以满足客户需求。
物料需求计划(MRP)是一个对零部件和原材料需求进行计划和管理的工具。
它基于主生产计划和主需求计划,以确定在不同时间和地点的物料需求量。
物料需求计划可以帮助企业在采购、库存和生产过程中优化资源的使用,降低成本,提高效率。
这三种计划在生产和供应链管理中起着关键作用,它们相互关联,共同决定了企业的生产和供应活动。
通过有效地整合和协调这些计划,企业可以更好地控制成本,提高生产效率,增强供应链的灵活性和响应能力,从而获得竞争优势。
主生产计划(MPS)、主需求计划(DRP)和物料需求计划(MRP)是现代企业生产和供应链管理中的核心工具,它们相互交织、相互依赖,共同推动了企业的生产和供应活动。
本文将分别深入探讨这三种计划的重要性,并阐述它们之间的关联与协调。
首先,主生产计划(MPS)是一个对生产需求进行计划和管理的工具。
它基于市场需求、销售计划、库存水平和生产能力等因素,以确定最有效的生产计划。
主生产计划不仅仅是一个简单的制造计划,它还反映了企业的市场策略、产品组合、产能规划和销售计划等方面的决策。
通过主生产计划,企业可以在竞争激烈的市场中更好地预测需求,规划生产,并保持适当的库存水平,从而提高生产效率,降低库存成本。
其次,主需求计划(DRP)是一个对产品需求进行计划和管理的工具。
它基于主生产计划和销售计划,确定在不同时间和地点的需求量。
通过主需求计划,企业可以更好地协调产品的运输和分发,以确保产品能够按时送达客户手中。
在全球化和供应链延伸的今天,主需求计划对于企业跨地域、跨国界的物流及配送活动起着至关重要的作用。
最后,物料需求计划(MRP)是一个对零部件和原材料需求进行计划和管理的工具。
主生产计划、物料需求计划和能力需求计划的概念和基本计算

主生产计划、物料需求计划和能力需求计划的概念和基本计算主生产计划(Master Production Schedule, MPS)是制造企业根据市场需求和销售预测而制定的生产计划。
它确定了特定时间段内所需的产品数量和生产时间表,以满足客户需求。
MPS通常基于销售预测、库存水平、生产能力和其他相关因素进行制定。
基本计算方法:1. 确定销售预测:首先需要通过市场调研、历史数据等来预测销售量,这是MPS 的基础。
2. 考虑库存水平:结合当前库存水平和规定的库存目标,确定实际需要生产的数量。
3. 考虑生产能力:考虑到企业的生产能力,确定每个时间段内可用的生产资源和设备。
4. 制定生产计划:根据销售预测、库存水平和生产能力,制定出每个时间段内需要生产的产品数量和时间表。
物料需求计划(Material Requirements Planning, MRP)是一种计划方法,用于确定所需物料的数量和时间,以支持主生产计划的执行。
MRP基于MPS的要求,根据物料清单、库存信息、供应商交货时间等因素,计算出所需的原材料和零部件的采购和生产计划。
基本计算方法:1. 确定物料清单:建立产品的物料清单,包括所需的原材料、零部件和组装工序等。
2. 确定库存水平:根据当前库存和库存目标,确定实际需要采购的物料数量。
3. 考虑供应商交货时间:考虑供应商的交货时间和可靠性,确定采购订单的时间表。
4. 计算物料需求:根据MPS的要求和物料清单,通过逐层爆炸式计算,确定每个物料的需求量和时间表。
能力需求计划(Capacity Requirements Planning, CRP)是根据MPS和MRP的结果,以及企业的生产能力和资源情况,制定出适当的生产计划和资源调度。
CRP 主要关注生产设备、人力资源和其他生产资源的需求和利用情况,以确保生产计划的可行性。
基本计算方法:1. 确定生产设备和资源:根据产品的生产工艺和流程,确定所需的生产设备和资源。
主生产计划与物料需求计划

主生产计划与物料需求计划主生产计划(Master Production Schedule,MPS)和物料需求计划(Material Requirements Planning,MRP)是制造企业中非常重要的两个计划。
它们的制定和执行对于企业的生产运营和物料管理至关重要。
本文将分别介绍主生产计划和物料需求计划的概念、作用、制定过程和执行方法。
主生产计划是指制造企业在一定时间内生产产品的计划安排,它是根据市场需求、生产能力和物料供应情况等因素制定的。
主生产计划的主要作用是平衡市场需求和生产能力,确保企业能够按时交付产品,并且在生产过程中尽可能地减少成本。
主生产计划一般由销售部门提供市场需求信息,生产部门提供生产能力信息,物料部门提供物料供应信息,综合考虑这些因素来制定最合理的生产计划。
主生产计划的制定过程一般包括以下几个步骤:首先是收集市场需求信息,包括产品的销售量、交付时间等;然后是评估生产能力,包括设备、人力、时间等资源的可用性;接着是确定生产计划,根据市场需求和生产能力确定生产计划的数量和时间安排;最后是与物料需求计划和库存管理相结合,确保生产计划的执行。
物料需求计划是指根据主生产计划和物料库存情况,对所需物料进行计划和安排的过程。
物料需求计划的主要作用是确保企业能够按时生产所需产品,同时尽可能地减少库存成本。
物料需求计划一般由生产计划部门根据主生产计划和物料库存情况来制定。
物料需求计划的制定过程一般包括以下几个步骤:首先是收集主生产计划和物料库存信息,包括产品的生产数量和时间安排,以及所需物料的库存情况;然后是根据生产计划和物料库存情况,确定所需物料的数量和时间安排;接着是与供应商进行沟通,确保所需物料能够按时供应;最后是与生产计划和库存管理相结合,确保物料需求计划的执行。
主生产计划和物料需求计划是相互关联的,它们的制定和执行对于企业的生产运营和物料管理至关重要。
在制定主生产计划和物料需求计划时,企业需要充分考虑市场需求、生产能力、物料供应等因素,确保生产计划的合理性和可行性。
主生产计划与物料需求计划

主生产计划与物料需求计划摘要主生产计划(Master Production Schedule,简称MPS)和物料需求计划(Material Requirement Planning,简称MRP)是现代企业生产管理中的重要工具。
MPS和MRP能够帮助企业有效地组织生产活动,合理安排材料和资源,实现生产计划的准确执行。
本文将详细介绍主生产计划和物料需求计划的概念、流程以及在企业运作中的作用。
1. 主生产计划主生产计划是企业根据市场需求和生产能力制定的一份计划,用于指导企业的生产活动。
主生产计划通常是以时间段为单位(如月度、季度、年度)进行制定,并根据销售预测、库存状况、生产能力等因素进行调整。
主生产计划的制定需要综合考虑市场需求、生产能力和库存水平,以确保生产计划的准确性和可行性。
主生产计划的制定流程包括以下几个步骤: - 销售预测:根据市场需求和销售数据,预测未来一段时间内的销售情况。
- 库存分析:分析当前库存水平,确定是否存在库存过剩或缺货的情况。
- 生产能力评估:评估企业的生产能力,包括设备、人员和工时等方面的考虑。
- 制定生产计划:根据销售预测、库存分析和生产能力评估,制定合理的生产计划。
主生产计划的制定需要综合考虑多个因素,如市场需求的波动、生产能力的约束以及供应链的稳定性等。
在制定主生产计划时,需要进行综合权衡和调整,以确保生产计划的可行性和效益。
2. 物料需求计划物料需求计划是基于主生产计划,对所需物料进行合理安排和调配的计划。
物料需求计划通过分析主生产计划中所需产品数量和所需物料的关系,以及当前的库存状况和供应链的情况,确定采购和生产物料的时间和数量。
物料需求计划能够帮助企业准确地控制和管理物料的供应,以避免库存过剩或缺货的情况。
物料需求计划的制定流程包括以下几个步骤: - 列出所需物料:根据主生产计划,列出所需物料及其数量。
- 库存分析:分析当前库存水平,确定是否需要采购物料。
物料需求计划计算例题物料需求计划(MRP)的基本计算模型
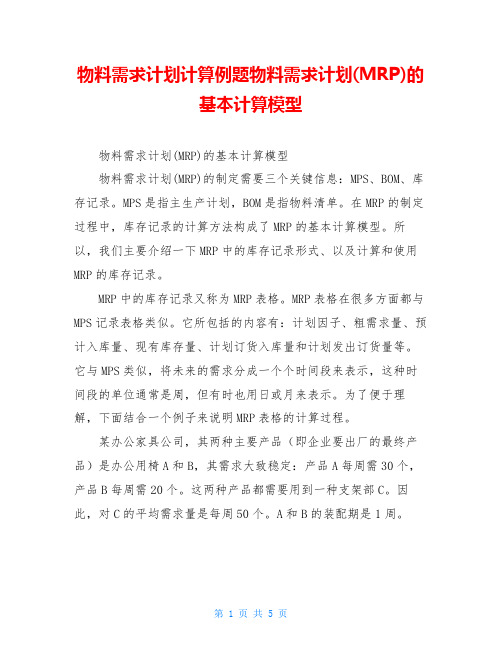
物料需求计划计算例题物料需求计划(MRP)的基本计算模型物料需求计划(MRP)的基本计算模型物料需求计划(MRP)的制定需要三个关键信息:MPS、BOM、库存记录。
MPS是指主生产计划,BOM是指物料清单。
在MRP的制定过程中,库存记录的计算方法构成了MRP的基本计算模型。
所以,我们主要介绍一下MRP中的库存记录形式、以及计算和使用MRP的库存记录。
MRP中的库存记录又称为MRP表格。
MRP表格在很多方面都与MPS记录表格类似。
它所包括的内容有:计划因子、粗需求量、预计入库量、现有库存量、计划订货入库量和计划发出订货量等。
它与MPS类似,将未来的需求分成一个个时间段来表示,这种时间段的单位通常是周,但有时也用日或月来表示。
为了便于理解,下面结合一个例子来说明MRP表格的计算过程。
某办公家具公司,其两种主要产品(即企业要出厂的最终产品)是办公用椅A和B,其需求大致稳定:产品A每周需30个,产品B每周需20个。
这两种产品都需要用到一种支架部C。
因此,对C的平均需求量是每周50个。
A和B的装配期是1周。
下图1是办公椅A和B的主生产计划表格以及部C的库存记录表格(尚未完成)。
这种表格没有标准格式,该例所用的是一种常见格式。
如上图示,在这种格式中,左上方通常要标出产品名称及其性质(如上图中,表明C是支架部),右上方表示计划因子,通常包括三项:生产批量、生产周期和安全库存量。
在本例中,C的批量是230个,生产周期为2周,安全库存量为50个。
这些计划因子的量都需要预先选定。
当这些值发生变化以后,管理人员必须及时更新库存记录。
下面首先来看库存记录的内容和确定方法。
一、库存记录要素及其计算1、粗需求量。
上例中未来8周的粗需求量如图1所示。
其需求量是根据C的最终产品A和B的主生产计划所决定的,但有时候需要加上一些作为配(更换)使用的量。
对C的需求之所以比MPS中A、B的时间提前1周,是因为MPS中所表示的各周的量实际上是指当周应该完成的量。
ERP系统的主生产计划与物料需求计划
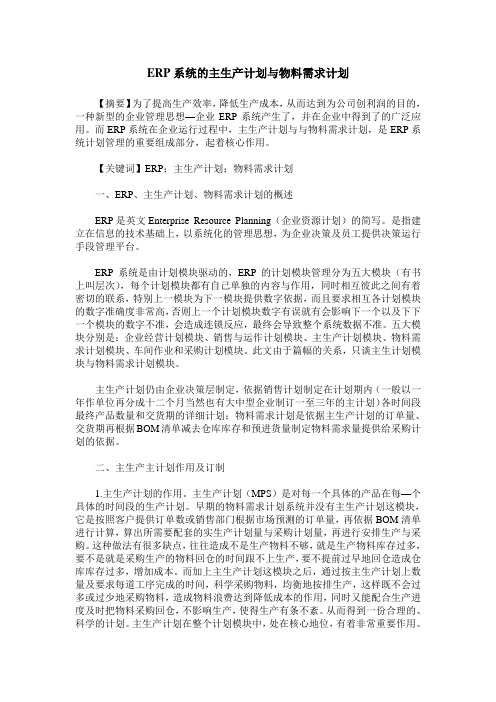
ERP系统的主生产计划与物料需求计划【摘要】为了提高生产效率,降低生产成本,从而达到为公司创利润的目的,一种新型的企业管理思想—企业ERP系统产生了,并在企业中得到了的广泛应用。
而ERP系统在企业运行过程中,主生产计划与与物料需求计划,是ERP系统计划管理的重要组成部分,起着核心作用。
【关键词】ERP;主生产计划;物料需求计划一、ERP、主生产计划、物料需求计划的概述ERP是英文Enterprise Resource Planning(企业资源计划)的简写。
是指建立在信息的技术基础上,以系统化的管理思想,为企业决策及员工提供决策运行手段管理平台。
ERP系统是由计划模块驱动的,ERP的计划模块管理分为五大模块(有书上叫层次),每个计划模块都有自己单独的内容与作用,同时相互彼此之间有着密切的联系,特别上一模块为下一模块提供数字依据,而且要求相互各计划模块的数字准确度非常高,否则上一个计划模块数字有误就有会影响下一个以及下下一个模块的数字不准,会造成连锁反应,最终会导致整个系统数据不准。
五大模块分别是:企业经营计划模块、销售与运作计划模块、主生产计划模块、物料需求计划模块、车间作业和采购计划模块。
此文由于篇幅的关系,只谈主生计划模块与物料需求计划模块。
主生产计划仍由企业决策层制定,依据销售计划制定在计划期内(一般以一年作单位再分成十二个月当然也有大中型企业制订一至三年的主计划)各时间段最终产品数量和交货期的详细计划;物料需求计划是依据主生产计划的订单量、交货期再根据BOM清单减去仓库库存和预进货量制定物料需求量提供给采购计划的依据。
二、主生产主计划作用及订制1.主生产计划的作用。
主生产计划(MPS)是对每一个具体的产品在每—个具体的时间段的生产计划。
早期的物料需求计划系统并没有主生产计划这模块,它是按照客户提供订单数或销售部门根据市场预测的订单量,再依据BOM清单进行计算,算出所需要配套的实生产计划量与采购计划量,再进行安排生产与采购。
主生产计划和计划计算
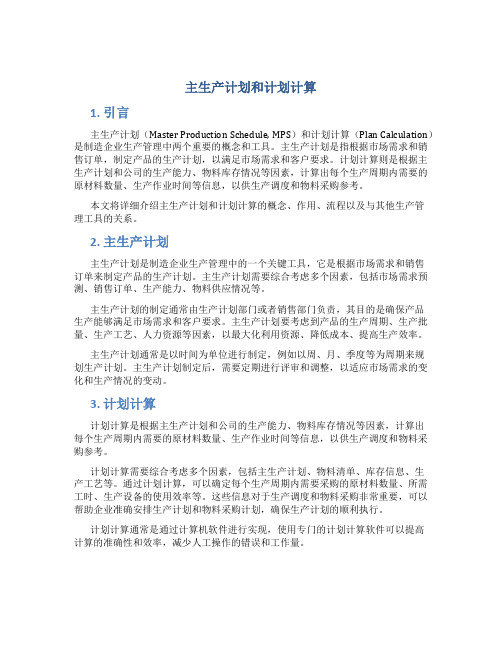
主生产计划和计划计算1. 引言主生产计划(Master Production Schedule, MPS)和计划计算(Plan Calculation)是制造企业生产管理中两个重要的概念和工具。
主生产计划是指根据市场需求和销售订单,制定产品的生产计划,以满足市场需求和客户要求。
计划计算则是根据主生产计划和公司的生产能力、物料库存情况等因素,计算出每个生产周期内需要的原材料数量、生产作业时间等信息,以供生产调度和物料采购参考。
本文将详细介绍主生产计划和计划计算的概念、作用、流程以及与其他生产管理工具的关系。
2. 主生产计划主生产计划是制造企业生产管理中的一个关键工具,它是根据市场需求和销售订单来制定产品的生产计划。
主生产计划需要综合考虑多个因素,包括市场需求预测、销售订单、生产能力、物料供应情况等。
主生产计划的制定通常由生产计划部门或者销售部门负责,其目的是确保产品生产能够满足市场需求和客户要求。
主生产计划要考虑到产品的生产周期、生产批量、生产工艺、人力资源等因素,以最大化利用资源、降低成本、提高生产效率。
主生产计划通常是以时间为单位进行制定,例如以周、月、季度等为周期来规划生产计划。
主生产计划制定后,需要定期进行评审和调整,以适应市场需求的变化和生产情况的变动。
3. 计划计算计划计算是根据主生产计划和公司的生产能力、物料库存情况等因素,计算出每个生产周期内需要的原材料数量、生产作业时间等信息,以供生产调度和物料采购参考。
计划计算需要综合考虑多个因素,包括主生产计划、物料清单、库存信息、生产工艺等。
通过计划计算,可以确定每个生产周期内需要采购的原材料数量、所需工时、生产设备的使用效率等。
这些信息对于生产调度和物料采购非常重要,可以帮助企业准确安排生产计划和物料采购计划,确保生产计划的顺利执行。
计划计算通常是通过计算机软件进行实现,使用专门的计划计算软件可以提高计算的准确性和效率,减少人工操作的错误和工作量。
生产计划与物料需求计划实务讲义
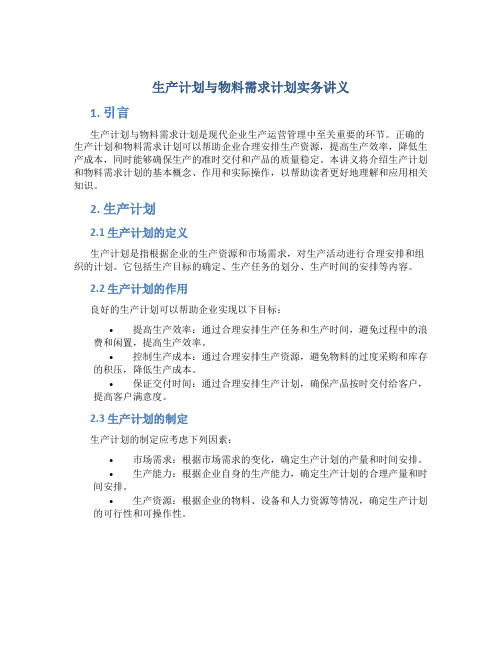
生产计划与物料需求计划实务讲义1. 引言生产计划与物料需求计划是现代企业生产运营管理中至关重要的环节。
正确的生产计划和物料需求计划可以帮助企业合理安排生产资源,提高生产效率,降低生产成本,同时能够确保生产的准时交付和产品的质量稳定。
本讲义将介绍生产计划和物料需求计划的基本概念、作用和实际操作,以帮助读者更好地理解和应用相关知识。
2. 生产计划2.1 生产计划的定义生产计划是指根据企业的生产资源和市场需求,对生产活动进行合理安排和组织的计划。
它包括生产目标的确定、生产任务的划分、生产时间的安排等内容。
2.2 生产计划的作用良好的生产计划可以帮助企业实现以下目标:•提高生产效率:通过合理安排生产任务和生产时间,避免过程中的浪费和闲置,提高生产效率。
•控制生产成本:通过合理安排生产资源,避免物料的过度采购和库存的积压,降低生产成本。
•保证交付时间:通过合理安排生产计划,确保产品按时交付给客户,提高客户满意度。
2.3 生产计划的制定生产计划的制定应考虑下列因素:•市场需求:根据市场需求的变化,确定生产计划的产量和时间安排。
•生产能力:根据企业自身的生产能力,确定生产计划的合理产量和时间安排。
•生产资源:根据企业的物料、设备和人力资源等情况,确定生产计划的可行性和可操作性。
3. 物料需求计划3.1 物料需求计划的定义物料需求计划是指根据生产计划和库存情况,对所需物料的数量和时间进行计划和跟踪的过程。
它可以帮助企业合理安排物料采购和库存管理,确保生产需求的顺利实现。
3.2 物料需求计划的作用物料需求计划的实施可以带来以下益处:•减少库存成本:通过合理计划和控制物料的采购和库存,避免过度采购和积压,降低库存成本。
•避免生产中断:通过及时跟踪和计划物料需求,避免因物料缺失而导致的生产中断。
•提高供应链效率:通过合理安排物料需求计划,提高供应链的运作效率,减少不必要的等待和延误。
3.3 物料需求计划的方法物料需求计划的制定可以采用以下方法:•MRP(物料需求计划):基于物料的需求和库存情况,通过计算和分析,确定物料的采购和使用计划。
主生产计划(MPS)和物料需求计划(MRP)逻辑计算(练..

主生产计划(主生产计划(MPS MPS MPS)和物料需求计划()和物料需求计划()和物料需求计划(MRP MRP MRP)逻辑计算(练习题))逻辑计算(练习题)已知某独立需求物料的有关数据如下表1,现有库存量为120120,安全库存,安全库存量为2020,生产批量为,生产批量为160160,批量增量为,批量增量为160160,提前期为,提前期为1个时段。
库存初值为120120。
预测量和订单量如下表。
预测量和订单量如下表1所示。
试根据相关的法则完成该独立需求物料MPS 计算过程,并将相应数据填入下表中。
计算过程,并将相应数据填入下表中。
表1 MPS 报表时区时区 当期当期 需求时区需求时区 计划时区计划时区 预测时区预测时区 时段时段 1 2 3 4 5 6 7 8 9 10 预测量预测量 70 70 70 70 70 80 80 80 80 80 订单量订单量 100 90 80 60 70 90 50 100 90 70 毛需求量毛需求量 PAB 初值初值 120 净需求量净需求量 计划产出量计划产出量 PAB 计划投入量计划投入量 ATP已知某独立需求物料(最终产品)已知某独立需求物料(最终产品)ZXC ZXC 的BOM 结构如图1所示。
每个ZXC 由2个物料A 和1个物料B 组成,每个物料B 由1个物料C 和2个物料D 组成。
图1 最终产品最终产品ZXC 的BOM 结构图结构图最终产品ZXC 的MPS 如表2前三行所示(即最终产品ZXC 的装配提前期为1时段,表2中第2行和第3行分别给出其最终产品ZXC 计划产出量和计划产出量的有关数据)。
表2还同时给出其他物料A 、B 、C 、D 有关数据。
其中物料A 的有关属性是:计划接收量为140140,,PAB 初值为5050,订货批量为,订货批量为140140,安全库存量为,安全库存量为3030,,提前期为1个时段。
物料B 的有关属性是:计划接收量为9090,,PAB 初值为4040,,订货批量为9090,安全库存量为,安全库存量为2525,提前期为,提前期为1个时段。
ERP主生产计划编制和MRP物料需求计算逻辑

/3
MRP II计划层次
层次
能力
计划期 时段 复核期 计划对象
计划内容 工作量
决 策 1经营规划 层
2 销售与运作规划 (SOP)
企业资源 资源计划
3-7年 年 1-3 年 月
产品的品种及市场定位、预期的市场
年
¥2亿
占有率、产品的年销售额、年利润额 。生产率、生产能力ห้องสมุดไป่ตู้划、职工队伍
小
建设
1.把经营规划的货币目标转化为用产
月
产品系列
品系列的产量表达。 2.制订均衡的月产率,均衡利用资
源,维持稳定生产。
3 主生产计划 计 ( MPS ) 划 层
4 物料需求计划 ( MRP )
执
行 5 生产作业控制
层
( SFC/PAC )
粗能力计划 (RCCP)
3-18 周 周-季 周-季
最终成品
按时间段计划企业应生产的最终产品 的数量和交货期,并且在生产需求和 可用资源之间作出平衡。
订货点(警戒点) 安全库存量5
消耗天数=3
消耗加快 订货点上移
消耗天数=2
消耗天数=2
订货提前期T=2
订货提前期T=2
订货提前期T=2
消耗减慢 订货点下移
D0
订货点=安全库存量+单位 时段消耗量*订货提前期
D2
D4
D3=订货点日 订货点=5+2x2=9 消耗量=2x3(天)=6 实际库存量=15-6=9 订购量=10,订货提前期=2
➢ 或者通过经验方法进 行估算:LT=2N (工序 数)+6
影 排队时间 响 加 工 准备时间 提 前 加工时间 期 各 类 等待时间 因 素 传送时间
ERP系统的主生产计划与物料需求计划
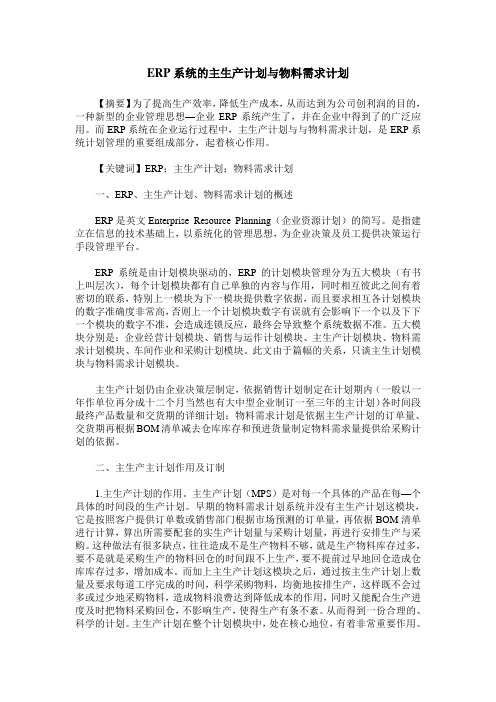
ERP系统的主生产计划与物料需求计划【摘要】为了提高生产效率,降低生产成本,从而达到为公司创利润的目的,一种新型的企业管理思想—企业ERP系统产生了,并在企业中得到了的广泛应用。
而ERP系统在企业运行过程中,主生产计划与与物料需求计划,是ERP系统计划管理的重要组成部分,起着核心作用。
【关键词】ERP;主生产计划;物料需求计划一、ERP、主生产计划、物料需求计划的概述ERP是英文Enterprise Resource Planning(企业资源计划)的简写。
是指建立在信息的技术基础上,以系统化的管理思想,为企业决策及员工提供决策运行手段管理平台。
ERP系统是由计划模块驱动的,ERP的计划模块管理分为五大模块(有书上叫层次),每个计划模块都有自己单独的内容与作用,同时相互彼此之间有着密切的联系,特别上一模块为下一模块提供数字依据,而且要求相互各计划模块的数字准确度非常高,否则上一个计划模块数字有误就有会影响下一个以及下下一个模块的数字不准,会造成连锁反应,最终会导致整个系统数据不准。
五大模块分别是:企业经营计划模块、销售与运作计划模块、主生产计划模块、物料需求计划模块、车间作业和采购计划模块。
此文由于篇幅的关系,只谈主生计划模块与物料需求计划模块。
主生产计划仍由企业决策层制定,依据销售计划制定在计划期内(一般以一年作单位再分成十二个月当然也有大中型企业制订一至三年的主计划)各时间段最终产品数量和交货期的详细计划;物料需求计划是依据主生产计划的订单量、交货期再根据BOM清单减去仓库库存和预进货量制定物料需求量提供给采购计划的依据。
二、主生产主计划作用及订制1.主生产计划的作用。
主生产计划(MPS)是对每一个具体的产品在每—个具体的时间段的生产计划。
早期的物料需求计划系统并没有主生产计划这模块,它是按照客户提供订单数或销售部门根据市场预测的订单量,再依据BOM清单进行计算,算出所需要配套的实生产计划量与采购计划量,再进行安排生产与采购。
主生产计划、主需求计划与物料需求计划
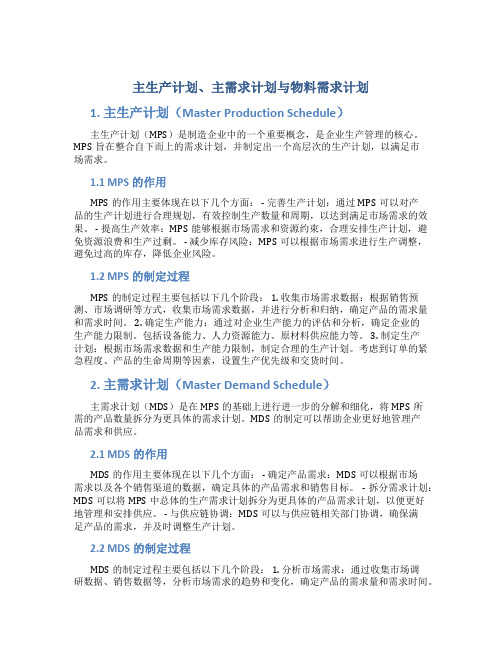
主生产计划、主需求计划与物料需求计划1. 主生产计划(Master Production Schedule)主生产计划(MPS)是制造企业中的一个重要概念,是企业生产管理的核心。
MPS旨在整合自下而上的需求计划,并制定出一个高层次的生产计划,以满足市场需求。
1.1 MPS的作用MPS的作用主要体现在以下几个方面: - 完善生产计划:通过MPS可以对产品的生产计划进行合理规划,有效控制生产数量和周期,以达到满足市场需求的效果。
- 提高生产效率:MPS能够根据市场需求和资源约束,合理安排生产计划,避免资源浪费和生产过剩。
- 减少库存风险:MPS可以根据市场需求进行生产调整,避免过高的库存,降低企业风险。
1.2 MPS的制定过程MPS的制定过程主要包括以下几个阶段: 1. 收集市场需求数据:根据销售预测、市场调研等方式,收集市场需求数据,并进行分析和归纳,确定产品的需求量和需求时间。
2. 确定生产能力:通过对企业生产能力的评估和分析,确定企业的生产能力限制。
包括设备能力、人力资源能力、原材料供应能力等。
3. 制定生产计划:根据市场需求数据和生产能力限制,制定合理的生产计划。
考虑到订单的紧急程度、产品的生命周期等因素,设置生产优先级和交货时间。
2. 主需求计划(Master Demand Schedule)主需求计划(MDS)是在MPS的基础上进行进一步的分解和细化,将MPS所需的产品数量拆分为更具体的需求计划。
MDS的制定可以帮助企业更好地管理产品需求和供应。
2.1 MDS的作用MDS的作用主要体现在以下几个方面: - 确定产品需求:MDS可以根据市场需求以及各个销售渠道的数据,确定具体的产品需求和销售目标。
- 拆分需求计划:MDS可以将MPS中总体的生产需求计划拆分为更具体的产品需求计划,以便更好地管理和安排供应。
- 与供应链协调:MDS可以与供应链相关部门协调,确保满足产品的需求,并及时调整生产计划。
主生产计划和MRP计划计算概述

主生产计划和MRP计划计算概述1. 引言主生产计划(Master Production Schedule,简称MPS)和物料需求计划(Material Requirements Planning,简称MRP)是制造企业中常用的计划管理工具。
MPS主要用来确定生产计划的整体需求,而MRP则用来根据MPS计划和库存状况,计算出具体的物料需求和采购计划。
本文将对主生产计划和MRP计划的概念进行介绍,并探讨它们在制造业中的重要性和应用。
2. 主生产计划(MPS)主生产计划是制造业中用于确定生产计划整体需求的工具。
它基于销售和市场需求,以及企业内部的产能和生产能力,制定出一份长期的产品生产计划。
MPS计划通常根据销售预测和市场需求计划进行制定,旨在确保产品能够按时交付给客户。
主生产计划的制定需要考虑多个因素,包括市场需求、销售预测、现有库存、生产能力等。
它的制定需要与销售、生产和采购等部门进行紧密的合作和协调,以确保计划的准确性和可行性。
MPS计划通常是一个长期的计划,一般覆盖3个月或更长的时间范围。
它提供了一个基准,用于确定产品的生产数量、交付时间以及所需的物料。
这对于企业的生产和供应链管理至关重要。
3. MRP计划物料需求计划是根据MPS计划和库存状况,计算出具体的物料需求和采购计划的工具。
MRP系统通过分析MPS计划中所需的物料,结合当前库存水平和供应商交货时间等信息,计算出每个物料的需求量,并生成相应的采购订单或生产计划。
MRP系统一般包括以下几个关键步骤:•根据MPS计划和销售订单等信息,确定所需物料的数量和时间。
•分析当前库存水平,计算出需要采购或生产的物料数量。
•根据供应商的交货时间和采购 lead time,确定采购计划的时间表。
•生成物料清单、采购订单、生产计划等相关文档。
MRP计划的核心目标是确保物料的准时供应,以满足生产计划的需求。
它能够帮助企业提高生产效率、降低库存成本,提升客户满意度。
主生产计划主需求计划与物料需求计划
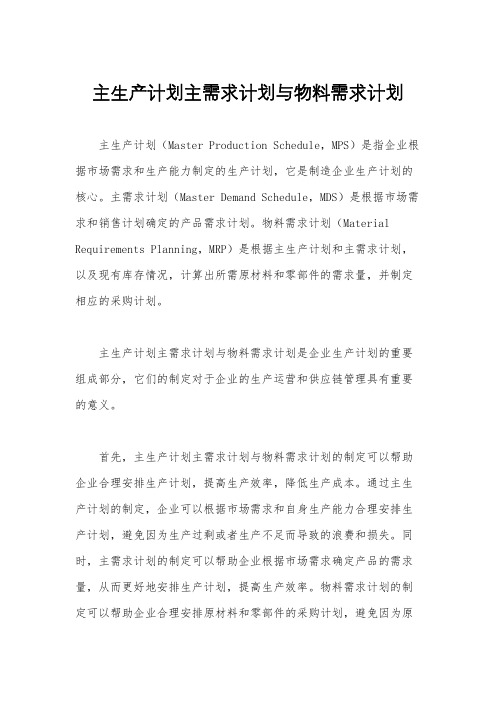
主生产计划主需求计划与物料需求计划主生产计划(Master Production Schedule,MPS)是指企业根据市场需求和生产能力制定的生产计划,它是制造企业生产计划的核心。
主需求计划(Master Demand Schedule,MDS)是根据市场需求和销售计划确定的产品需求计划。
物料需求计划(Material Requirements Planning,MRP)是根据主生产计划和主需求计划,以及现有库存情况,计算出所需原材料和零部件的需求量,并制定相应的采购计划。
主生产计划主需求计划与物料需求计划是企业生产计划的重要组成部分,它们的制定对于企业的生产运营和供应链管理具有重要的意义。
首先,主生产计划主需求计划与物料需求计划的制定可以帮助企业合理安排生产计划,提高生产效率,降低生产成本。
通过主生产计划的制定,企业可以根据市场需求和自身生产能力合理安排生产计划,避免因为生产过剩或者生产不足而导致的浪费和损失。
同时,主需求计划的制定可以帮助企业根据市场需求确定产品的需求量,从而更好地安排生产计划,提高生产效率。
物料需求计划的制定可以帮助企业合理安排原材料和零部件的采购计划,避免因为原材料和零部件的短缺而导致的生产停滞和延误,从而降低生产成本,提高生产效率。
其次,主生产计划主需求计划与物料需求计划的制定可以帮助企业更好地管理供应链,提高供应链的灵活性和响应速度。
通过主生产计划的制定,企业可以更好地与供应商和客户沟通,建立稳定的供应链关系,提高供应链的稳定性和可靠性。
主需求计划的制定可以帮助企业更好地了解市场需求,及时调整生产计划,提高供应链的灵活性和响应速度。
物料需求计划的制定可以帮助企业更好地管理库存,降低库存成本,提高供应链的效率和响应速度。
最后,主生产计划主需求计划与物料需求计划的制定可以帮助企业更好地应对市场变化,提高企业的竞争力。
通过主生产计划的制定,企业可以更好地了解市场需求,及时调整生产计划,提高企业的市场反应能力。
物料需求计划计算例题 [物料需求计划(MRP)的基本计算模型]
![物料需求计划计算例题 [物料需求计划(MRP)的基本计算模型]](https://img.taocdn.com/s3/m/9ac6c662daef5ef7bb0d3c23.png)
《物料需求计划计算例题 [物料需求计划(MRP)的基本计算模型]》摘要:物计划(R)制定要三关键信息、B、库存记录,所以我们主要介绍下R库存记录形式、以及如何计算和使用R库存记录,、粗量物计划(R)基计算模型物计划(R)制定要三关键信息、B、库存记录是指主生产计划B是指物清单R制定程库存记录计算方法构成了R基计算模型所以我们主要介绍下R库存记录形式、以及如何计算和使用R库存记录R库存记录又称R表格R表格很多方面都与记录表格类似它所包括容有计划因子、粗量、预计入库量、现有库存量、计划订货入库量和计划发出订货量等它与类似将分成段表示这种段单位通常是周但有也用日或月表示了便理下面结合例子说明R表格计算程某办公具公司其两种主要产品(即企业要出厂终产品)是办公用椅和B其致稳定产品每周30产品B每周0这两种产品都要用到种支架部件因对平量是每周50和B装配期是周下图是办公椅和B主生产计划表格以及部件库存记录表格(尚完成)这种表格没有标准格式该例所用是种常见格式如上图示这种格式左上方通常要标出产品名称及其性质(如上图表明是支架部件)右上方表示计划因子通常包括三项生产批量、生产周期和安全库存量例批量是30生产周期周安全库存量50这些计划因子量都要预先选定当这些值发生变化以管理人员必须及更新库存记录下面首先看库存记录容和确定方法、库存记录要素及其计算、粗量上例8周粗量如图所示其量是根据终产品和B主生产计划所定但有候要加上些作配件(更换件)使用量对所以比、B提前周是因所表示各周量实际上是指当周应该完成量但由生产或装配是要周期因该生产指令发出必须给出这部分提前量该例周50其装配周期周故周应发出生产订单开始装配上图表格表示是考虑了生产周期生产订单发出和生产量样R库存记录粗要量是指当周应准备量例如了周装完50周必须准备50、预计入库量(l r简称R)它是指订单已发出、但货尚收到量对外购件它现可能处几种状态买方刚发出订单供应商正加工;正从供应商至卖方途;已到买方、买方正验货等对加工件它现可能状态包括正生产现场被加工;等待他原材和零件到达;正机床前排队等待加工;正从工序移至下工序等周50其生产周期周故至少周前已发出了该生产订单但通常不会比提前周更早地发出订单3、现有库存量()其概念与概念相指每周被满足手头仍有库存量该记录随着每周进货或出货情况而更新各周则可计算德出其计算公式式周末; R周预计入库量; R周计划订货入库量; GR周粗;可见上式与计算方式是致即R+R相当量GR相当x()这里不存预测值或订单值选择因是相关、确定上面图只给除了前周周只剩7少所要50安全库存量这是要生产信即要增加R信、计划订货入库量(l r简称R)其含义是计划订货或生产、但订单尚发出订货量这量义是要保持量不低安全库存(考虑安全库存保持非即可)对某些不要安全库存物则如其义是要保持非库存记录所表示R量应包括这两种情况R确定方法如下()出现短缺(或值或安全库存量)当周制订R量其值应是等安全库存;()继续计算其各周当又出现短缺制订下R量这两步骤反复进行直至整计划期记录和R记录格都填满5、计划发出订货量(l rr rl简称R)它实际上是要说明订单发出或开始生产所以将其称“╳╳量”是因这种对说明库存记录是通将该订单量记入相应栏说明该基计算式是到货减生产周期利用这项可容易地导出构成某项物B下层物粗摘《生产与运作管理》(刘丽著)。
主生产计划和MRP计划计算

主生产计划和MRP计划计算主生产计划(Master Production Schedule,MPS)和物料需求计划(Material Requirements Planning,MRP)是生产计划和控制的两个重要工具。
MPS是一个制定生产计划的目标表,而MRP是一个根据MPS确定所需物料的计划。
主生产计划是一个公司制定的计划,用于确定一定时间范围内所需生产的产品数量和时间。
它基于销售预测、库存目标和其他生产要求确定。
MPS将销售和运营规划转化为一个具体的生产计划。
它能够提供给其他生产计划和控制系统一个稳定的时间框架。
在制定MPS时,需要考虑一些因素,如销售预测、库存水平、产品生命周期、生产资源和制造能力等。
销售预测是制定MPS的重要依据,它是基于市场需求和销售历史数据等进行预测的。
库存水平是为了满足客户需求和减少生产停滞而要考虑的因素。
产品生命周期是指产品从研发到生产、销售和淘汰的整个过程,需要在不同阶段进行不同的生产计划。
生产资源和制造能力是指企业的生产设备和员工能够处理的产量。
一旦MPS制定完成,接下来就是根据MPS进行物料需求计划。
物料需求计划是根据MPS和库存目标,计算所需的原材料和其他物料的数量和时间。
MRP通过分析产品结构(Bill of Materials,BOM)和现有库存,计算每个物料的需求量,并生成物料采购和生产订单。
在MRP计算中,需要考虑一些因素,如物料的供应周期、批量优惠、订单的交付时间等。
供应周期是指从下达订单到供应商将物料交货给企业所需的时间。
批量优惠是指在一次订单中采购更大数量的物料所能获得的折扣。
订单的交付时间是根据客户需求和销售订单的要求确定的。
对于每个物料,MRP计算包括四个主要步骤:净需求计算、批量调整、可用性计算和订单生成。
净需求计算是根据MPS和现有库存计算物料的需求量。
批量调整是根据供应商的批量优惠和企业的经济批量计算最优的采购数量。
可用性计算是判断物料是否足够,如果不足则生成相应的采购或生产订单。
主生产计划和物料需求计划逻辑计算(数据略有变化:提供演算例题结果,有助于理解计算过程)20150106NEW
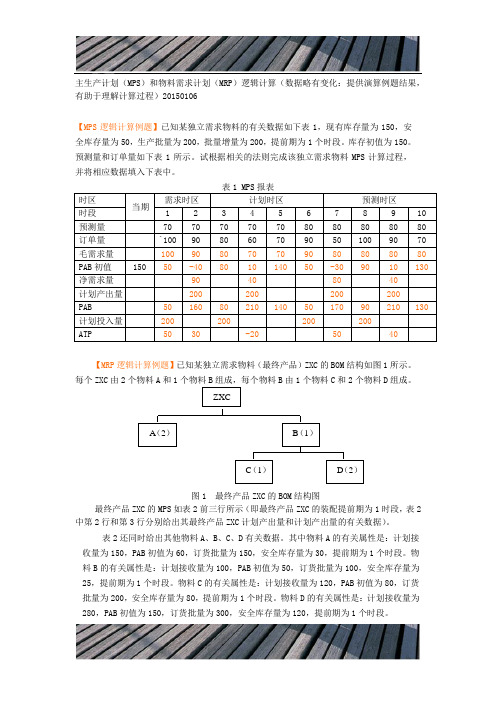
主生产计划(MPS )和物料需求计划(MRP )逻辑计算(数据略有变化:提供演算例题结果,有助于理解计算过程)20150106【MPS 逻辑计算例题】已知某独立需求物料的有关数据如下表1,现有库存量为150,安全库存量为50,生产批量为200,批量增量为200,提前期为1个时段。
库存初值为150。
预测量和订单量如下表1所示。
试根据相关的法则完成该独立需求物料MPS 计算过程,并将相应数据填入下表中。
【MRP 逻辑计算例题】已知某独立需求物料(最终产品)ZXC 的BOM 结构如图1所示。
每个ZXC 由2个物料A 和1个物料B 组成,每个物料B 由1个物料C 和2个物料D 组成。
图1 最终产品ZXC 的BOM 结构图最终产品ZXC 的MPS 如表2前三行所示(即最终产品ZXC 的装配提前期为1时段,表2中第2行和第3行分别给出其最终产品ZXC 计划产出量和计划产出量的有关数据)。
表2还同时给出其他物料A 、B 、C 、D 有关数据。
其中物料A 的有关属性是:计划接收量为150,PAB 初值为60,订货批量为150,安全库存量为30,提前期为1个时段。
物料B 的有关属性是:计划接收量为100,PAB 初值为50,订货批量为100,安全库存量为25,提前期为1个时段。
物料C 的有关属性是:计划接收量为120,PAB 初值为80,订货批量为200,安全库存量为80,提前期为1个时段。
物料D 的有关属性是:计划接收量为280,PAB 初值为150,订货批量为300,安全库存量为120,提前期为1个时段。
试根据相关的法则完成物料A、B、C、D的MRP计算过程,并将相应数据填入下表中。
表2 最终产品ZXC 的MRP 计算表When you are old and grey and full of sleep,And nodding by the fire, take down this book, And slowly read, and dream of the soft look Your eyes had once, and of their shadows deep; How many loved your moments of glad grace,And loved your beauty with love false or true,But one man loved the pilgrim soul in you,And loved the sorrows of your changing face; And bending down beside the glowing bars, Murmur, a little sadly, how love fledAnd paced upon the mountains overheadAnd hid his face amid a crowd of stars.The furthest distance in the worldIs not between life and deathBut when I stand in front of youYet you don't know thatI love you.The furthest distance in the worldIs not when I stand in front of youYet you can't see my loveBut when undoubtedly knowing the love from both Yet cannot be together.The furthest distance in the worldIs not being apart while being in loveBut when I plainly cannot resist the yearningYet pretending you have never been in my heart. The furthest distance in the worldIs not struggling against the tidesBut using one's indifferent heartTo dig an uncrossable riverFor the one who loves you.。
物料需求计划(MRP)计算
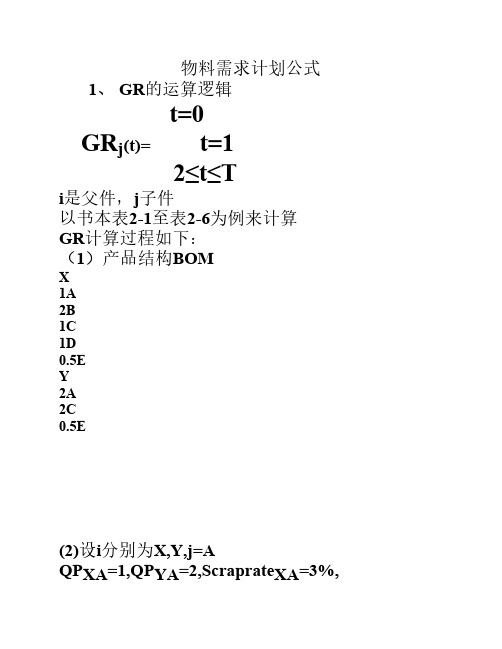
物料需求计划公式1、 GR的运算逻辑t=0GR j(t)= t=12≤t≤Ti是父件,j子件以书本表2-1至表2-6为例来计算GR计算过程如下:(1)产品结构BOMX1A2B1C1D0.5EY2A2C0.5E(2)设i分别为X,Y,j=AQP XA=1,QP YA=2,Scraprate XA=3%,Scraprate YA=5%t=0时,父件X,Y的POR都等于0POR x(0)=0,PORy(0) =0,indmd x(0)=0, indmd y(0)=0GR A(0)= 0t=1时,父件X,Y的POR分别为POR x(1)=200,POR y(1) =200,indmd x(1)=0, indmd y(1)=0GRA(1)= (200×1)/(1-3%)+(200×2)/(1-5%)+0+0=627.2t=2时, 父件X,Y的POR分别为POR x(2)= 0,POR y(1) =150,indmd x(1)=0, indmd y(1)=0GR A(2)= ( 0×1)/(1-3%)+(150×2)/(1-5%)+0=315.8 2.SR的来源T=0的逾期量SR j(0)是应到未到量,T≥1的SR j(t)为排定在未来t时段将会取得的“已订未交量”3、 POH的运算逻辑OH j+SR j(1)+SR j(0)-AL j-GR j(1) t=1POH j(t)=PAB j(t-1)+SR j(t)-GR j(t) 2≤t≤TOH A=300,SR A(1)=500,SR A(0)=0,AL A=200,GR A(1)=627(1) 还是以上面的例子来计算t=1时,j=APOH A(1)= OH A+ SR A(1)+ SR A(0)- AL A-GR A(1)=-27t=2时,j=APOH A(2)=PAB A(1)+SR A(2)-GR A(2)=473+0-315.8=157.24、 NR的运算逻辑NR j(t)=IF{POH j(t)≥SS j,0,} 1≤t≤T以上面的例子,j=APOH A(1)=-27, SS A=10,Yield A=100%NR A(1)= IF{POH A(1)≥SS A,0,}=IF{-27≥10,0,37}=37NR A(2)=05、 PORC的运算逻辑PORC j(t)=F(NR j(t),LSR) 1≤t≤T(1) 最小订购量法,即一旦有净需求,订购量最少应为某基准量LSPORC j(t)=IF(NR j(t)>0,max{NR j(t),LS j},0) 1≤t≤T(2) 定量批量法,即一旦有净需求,订购量始终为某基准量LS整数倍PORC j(t)=IF(NR j(t)>0,CEILING{NR j(t),LS j},0)1≤t≤T以上面例子为例j=A时NR A(1)=37, LS A=500,A的批量法则LSR为最小订购量法,所以用公式(1)PORC A(1)=IF(NR A(1)>0,max{ NR A(1),LS A},0)=500PORC A(2)=06、 PAB的运算逻辑PAB j(t)=POH j(t)+PORC j(t) 1≤t≤T以上面例子为例当t=1,j=A时POH A(1)= -27,PORC A(1)=500PAB A(1)=-27+500=4737、 POR的运算逻辑t=0POR j(t)= PORC j(t+LT j) 1≤t≤T-LT j0 T- LT j<t≤T以上面例子为例当t=0时,j=A,因此LT j=2POR A(t)=PORC A(1)+PORC A(2)=500+0=500当t=1时, j=A,因此LT j=2计算PORC A(3)案例MRP计算步骤如下:(1)首先计算第1阶MRP物料A和B全部期别的毛需求(2)随机选取A或B,此处假设选A,按{POH(t)→NR(t)→PORC(t)→PAB(t)}的顺序依次计算第1至第9期数据。
- 1、下载文档前请自行甄别文档内容的完整性,平台不提供额外的编辑、内容补充、找答案等附加服务。
- 2、"仅部分预览"的文档,不可在线预览部分如存在完整性等问题,可反馈申请退款(可完整预览的文档不适用该条件!)。
- 3、如文档侵犯您的权益,请联系客服反馈,我们会尽快为您处理(人工客服工作时间:9:00-18:30)。
主生产计划(MPS)和物料需求计划(MRP)逻辑计算(数据略有变化:提供演算例题结果,有助于理解计算过程)20150106
【MPS逻辑计算例题】已知某独立需求物料的有关数据如下表1,现有库存量为150,安全库存量为50,生产批量为200,批量增量为200,提前期为1个时段。
库存初值为150。
预测量和订单量如下表1所示。
试根据相关的法则完成该独立需求物料MPS计算过程,并将相应数据填入下表中。
【MRP逻辑计算例题】已知某独立需求物料(最终产品)ZXC的BOM结构如图1所示。
每个ZXC由2个物料A和1个物料B组成,每个物料B由1个物料C和2个物料D组成。
图1 最终产品ZXC的BOM结构图
最终产品ZXC的MPS如表2前三行所示(即最终产品ZXC的装配提前期为1时段,表2中第2行和第3行分别给出其最终产品ZXC计划产出量和计划产出量的有关数据)。
表2还同时给出其他物料A、B、C、D有关数据。
其中物料A的有关属性是:计划接收量为150,PAB初值为60,订货批量为150,安全库存量为30,提前期为1个时段。
物料B的有关属性是:计划接收量为100,PAB初值为50,订货批量为100,安全库存量为25,提前期为1个时段。
物料C的有关属性是:计划接收量为120,PAB初值为80,订货批量为200,安全库存量为80,提前期为1个时段。
物料D的有关属性是:计划接收量为280,PAB初值为150,订货批量为300,安全库存量为120,提前期为1个时段。
试根据相关的法则完成物料A、B、C、D的MRP计算过程,并将相应数据填入下表中。
表2 最终产品ZXC的MRP计算表。