阐述车刀各角度的功用和选择原则
刀具角度选用原则
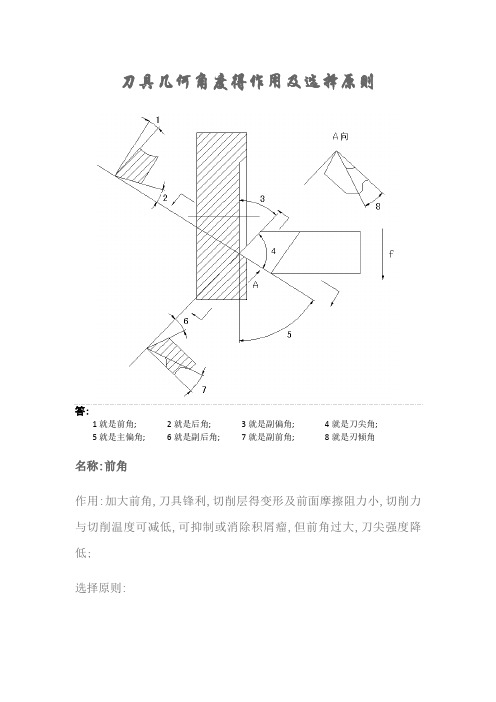
刀具几何角度得作用及选择原则答:1就是前角; 2就是后角; 3就是副偏角; 4就是刀尖角;5就是主偏角; 6就是副后角; 7就是副前角; 8就是刃倾角名称:前角作用:加大前角,刀具锋利,切削层得变形及前面摩擦阻力小,切削力与切削温度可减低,可抑制或消除积屑瘤,但前角过大,刀尖强度降低;选择原则:小得前角;加工特硬材料(如淬硬钢、冷硬铸铁等)甚至可取负得前角(2)刀具材料得抗弯强度及韧性高时,可取较大得前角(3)断续切削或精加工时,应取较小得前角,但如果此时有较大得副刃倾角配合,仍可取较大得前角,以减小径向切削力(4)高速切削时,前角对切屑变形及切削力得影响较小,可取较小前角(5)工艺系统钢性差时,应取较大得前角名称:后角作用:减少刀具后面与工件得切削表面与已加工表面之间得摩擦。
前角一定时,后角愈锋利,但会减小楔角,影响刀具强度与散热面积。
选择原则:(1)精加工时,切削厚度薄,磨损主要发生在后刀面,宜取较大后角;粗加工时,切削厚度大,负荷重,前、后面均要发生磨损、宜取较小后角(2)多刃刀具切削厚度较薄,应取较大后角(3)被加工工件与刀具钢性差时,应取较小后角,以增大后刀面与工件得接触面积,减少或消除振动较小得后角;但对加工硬材料得负前角刀具,后角应稍大些,以便刀刃易于切入工件;(5)定尺寸刀具(如内拉刀、铰刀等)应取较小后角,以免重磨后刀具尺寸变化太大;(6)对进给运动速度较大得刀具(如螺纹车刀、铲齿车刀等),后角得选择应充分考虑到工作后角与标注后角之间得差异;(7)铲齿刀具(如成形铣刀、滚刀等)得后角要受到铲背量得限制,不能太大,但要保证侧刃后角不小于2°。
名称:主偏角作用:(1)改变主偏角得大小可以调整径向切削分力与轴向切削分力之间得比例,主偏角增大时,径向切削分力减小,轴向切削分力增大;(2)减小主偏角可减小削厚度与切削刃单位长度上得负荷;同时主切削刃工作长度与刀尖角增大,刀具得散热得到改善,但主偏角过小会使径向切削分力增加,容易引起振动。
简要说明刀具的主要角度及其选用原则

简要说明刀具的主要角度及其选用原则刀具,这个东西,看似简单,实则里面的学问可大着呢!要说到刀具的主要角度,首先得从“切”这个动作说起。
你想,刀具不就是为了帮助我们切得又快又好嘛?不过别以为这事儿很简单,刀具角度可讲究了,不同的角度对应不同的切削效果,不是随便调一调就行的。
话说回来,刀具的角度主要有几个重要的,比如主切削角、前角、后角、侧角等。
这些角度的选用和调整,直接关系到切削的效率和刀具的使用寿命,关系到你切得快不快、刀刃磨得快不快,甚至刀具能不能“吃得住”硬材料。
所以说呀,选刀具角度可得当心,别瞎选,否则刀具很可能“生病”,不但切不好东西,磨得还特别快,浪费可就大了!首先说说主切削角吧,这个角度就像是刀具的“个性”,它决定了刀具切入材料时的态势。
主切削角越小,刀具的切入角度越大,越容易切进去,工作时感觉特别轻松,不会太费劲。
但是呢,主切削角也不能小得过头,不然刀具容易变钝,切削时材料不容易被带走,刀具负担加重,热量产生也会增多,刀具的寿命可就大打折扣了。
你知道的,刀具这种东西,不能嫌它重也不能嫌它轻,最讲究的就是一个“合适”字。
再说了,主切削角也不是越小越好,越大反而越容易磨损,刀具就容易变得“不听话”了。
所以这角度要选得恰到好处,得看你切的是啥材料,硬度如何,得结合实际情况。
再来看看前角。
这个角度直接影响刀具的锋利程度,前角大,刀具就会锋利,切得也快,顺畅无比。
要是前角太小,切削时材料就不容易被带走,刀具就像是被困住了,切得慢,费力还不省事儿。
前角一般都得大一些,尤其是当我们切的是一些软材料时,前角越大,切削更容易,省力省时。
不过也得小心,如果前角过大,刀具的强度就会降低,容易崩刃,后果可不堪设想。
所以,前角和主切削角一样,得精挑细选,不是随便选一个大的角度就好。
再来说说后角,听起来很简单,其实影响也不小。
后角决定了切削的稳定性,影响着刀具的摩擦情况。
后角大,刀具和工件的接触面小,摩擦就小,切削过程顺畅,刀具也不会那么快磨损。
刀具几何角度的作用及选择原则

刀具几何角度的作用及选择原则刀具的几何角度对加工质量、切削力和切削温度等有很大的影响,正确的选择刀具几何角度可以提高切削效率和工件表面质量。
本文将从切削角、主偏角、切削刃前角和切削刃后角四个方面来探讨刀具几何角度的作用及选择原则。
一、切削角切削角是刀具主切削面与工件切削表面的夹角,一般分为正的和负的两种情况。
1.正切削角:也称为刀具顶角,是指刀具主切削面与工件切削表面夹角大于90°的情况。
正切削角有利于降低切削力和切削温度,减少刀具磨损。
因此,在切削硬材料或脆性材料时,一般选择正切削角。
但是正切削角也会增大刀具与工件接触面积,增加切削力,从而需要更大的功率投入。
2.负切削角:也称为刀具反角,是指刀具主切削面与工件切削表面夹角小于90°的情况。
负切削角能降低切削力和切削温度,提高切削稳定性和切削质量。
因此,在切削软材料或难切削材料时,一般选择负切削角。
然而,负切削角的刀具易产生振动,增加切削噪声,且不易控制切削深度。
在实际应用中,切削角的选择应根据材料的性质、切削目标和加工条件综合考虑,一般需要通过试切试验来确定最佳切削角。
二、主偏角主偏角是刀具俯仰角,是指刀具主切削面与铣削切削方向之间的夹角。
主偏角的大小会直接影响刀具的切削力和切削质量。
1.大主偏角:大主偏角可以降低刀具的切削力和切削温度,提高切削稳定性和切削质量。
大主偏角适用于切削精度要求高、切削深度相对较小、切削速度相对较低的情况。
2.小主偏角:小主偏角可以提高刀具的切削效率和切削速度,适用于切削深度相对较大、切削速度相对较高的情况。
然而,小主偏角容易导致切屑的卡刀现象,增加刀具磨损和加工表面粗糙度。
主偏角的选择应结合切削效率和切削质量的要求,同时考虑刀具的刚度和加工条件等因素。
三、切削刃前角切削刃前角是刀具切削刃前的锥度角,主要影响刀具的切削稳定性和切削质量。
1.大切削刃前角:大切削刃前角可以增加切削深度和切削范围,提高切削效率和切削速度。
车刀的主要角度及其作用

车刀的主要角度及其作用车刀的主要角度有前角(γ0)、后角(α0)、主偏角(Kr)、副偏角(Kr’)和刃倾角(λs)。
为了确定车刀的角度,要建立三个坐标平面:切削平面、基面和主剖面。
对车削而言,如果不考虑车刀安装和切削运动的影响,切削平面可以认为是铅垂面;基面是水平面;当主切削刃水平时,垂直于主切削刃所作的剖面为主剖面。
(1)前角γ0在主剖面中测量,是前刀面与基面之间的夹角。
其作用是使刀刃锋利,便于切削。
但前角不能太大,否则会削弱刀刃的强度,容易磨损甚至崩坏。
加工塑性材料时,前角可选大些,如用硬质合金车刀切削钢件可取γ0=10~20,加工脆性材料,车刀的前角γ0应比粗加工大,以利于刀刃锋利,工件的粗糙度小。
(2)后角α0在主剖面中测量,是主后面与切削平面之间的夹角。
其作用是减小车削时主后面与工件的摩擦,一般取α0=6~12°,粗车时取小值,精车时取大值。
(3)主偏角Kr在基面中测量,它是主切削刃在基面的投影与进给方向的夹角。
其作用是:1)可改变主切削刃参加切削的长度,影响刀具寿命。
2)影响径向切削力的大小。
小的主偏角可增加主切削刃参加切削的长度,因而散热较好,对延长刀具使用寿命有利。
但在加工细长轴时,工件刚度不足,小的主偏角会使刀具作用在工件上的径向力增大,易产生弯曲和振动,因此,主偏角应选大些。
车刀常用的主偏角有45°、60°、75°、90°等几种,其中45°多。
(4)副偏角Kr’在基面中测量,是副切削刃在基面上的投影与进给反方向的夹角。
其主要作用是减小副切削刃与已加工表面之间的摩擦,以改善已加工表面的精糙度。
在切削深度ap、进给量f、主偏角Kr相等的条件下,减小副偏角Kr’,可减小车削后的残留面积,从而减小表面粗糙度,一般选取Kr′=5~15°。
(5)刃倾角入λs 在切削平面中测量,是主切削刃与基面的夹角。
其作用主要是控制切屑的流动方向。
刀具角度的功用与选择

角度功用选择原则(1)根据工件材料选择前角。
加工塑性材料时,特别是硬化严重的材料(如不锈钢等),为了减小切削变形和刀具磨损,应选用较大的前角;加工脆性材料时,由于产生的切屑为崩碎切屑,切削变形小,因此增大前角的意义不大,而这时刀屑间的作用力集中在切削刃附近,为保证切削刃具具有足够的强度,应采用较小的前角。
工件强度和硬度低时,切削力不大,为使切削刃锋利,可选用较大的甚至很大的前角。
工件材料强度高时,应选用较小的前角;加工影响切削变形和切削力的特别硬的工件材料(如淬火钢)时,应选用很大小、刀具耐用度和加工表面的小的前角,甚至选用负前角。
因为工件的强度、质量。
增大前角能使刀刃变得锋硬度愈高,产生的切削力愈大,切削热愈多,利,使切削更为轻快,可以减小为了使刃具有足够的强度和散热,防止崩刃和切削变形和摩擦,从而减小切削磨损,应选用较小的前角。
前角o力和切削功率,切削热也少,加(2)根据刀具材料选择前角。
刀具材料工表面质量高。
但增大前角会使的抗弯强度和冲击韧性较低时应选较小的前刀刃和刀尖强度下降,刀具散热角。
通常硬质合金车刀的前角在−5°~体积减小,影响刀具的耐用度。
+20°,高速钢刀具比硬质合金刀具的合理前前角的大小对表面粗糙度、排屑角约大5°~10°,而陶瓷刀具的前角一般取及断屑等也有一定影响。
−5°~−15°。
(3)根据加工性质选择前角。
粗加工时,特别是断续切削或加工有硬皮的铸、锻件时,不仅切削力大,切削热多,而且承受冲击载荷,为保证切削刃有足够的强度和散热面积,应适当减小前角。
精加工时,为使切削刃锋利、减小切削变形和获得较高的表面质量,前角应取得较大一些。
数控机床、自动机床和自动线用刀具,为保证刀具工作的稳定性,使其不易发生崩刃和破损,一般选用较小的前角。
减小后刀面与工件的摩擦(1)根据切削厚度选择后角。
合理后角和后刀面的磨损,其大小对刀具大小主要取决于切削厚度(或进给量),切削耐用度和加工表面质量都有很厚度hD愈大,则后角应愈小;反之亦然。
怎样选择车刀的几何角度

怎样选择车刀的几何角度合理选择车刀几何角度,有利于改善加工条件,提高被加工工件质量,延长刀具与设备的使用寿命,本文从车刀几何角度对切削力、切削热和刀具耐用度影响等角度,分析车刀几何角度选择的一般原则。
车刀几何角度是指车刀切削部分各几何要素之间,或它们与参考平面之间构成的两面角或线、面之间的夹角。
它们分别决定着车刀的切削刃和各刀面的空间位置。
根据“一面二角”理论可知,车刀的独立标注角度有六个,它们分别是:确定车刀主切削刃位置的主偏角Kr和刃倾角λs;确定车刀前刀面Ar与后刀面Aa的前角ro和后角ao;确定副切削刃及副后刀面Aa′的副偏角Kr′和副后角ao′。
这些几何角度对车削过程影响很大,其中尤其以主偏角Kr、前角ro、后角ao和刃倾角λs的影响更为突出,科学合理地选择车刀的几何角度,对车削工艺的顺利实施起着决定性作用。
下面就从车刀几何角度对切削力、切削热和刀具的耐用度的影响分析着手,本着使切削轻便、质量稳定,延长刀具使用寿命的宗旨,确定科学的车刀几何角度的一般性原则。
一、车刀几何角度对切削力的影响在金属切削时,刀具切入工件,将多余材料从工件上切除会产生强烈的力的作用,这些力统称为切削力。
切削力主要来源于被加工材料在发生弹性和塑性变形时的抗力和刀具与切屑及工件表面之间的摩擦作用。
根据切削力产生的作用效果的不同,可将切削力分解成三个相互垂直方向的分力。
它们分别是:主切削力Fz,进给抗力Fx和切深抗力Fy,其中Fz是切削总力Fr沿主运动切向分解而得,是计算车刀强度,设计机床零件,确定机床功率的主要依据;Fx也叫轴向力,它是Fr沿工件轴向的分力,是设计进给机构,计算车刀进给功率所必需的;Fy也叫径向力,它是Fr沿着工件径向的分力,它不消耗机床功率,但是当机床或工艺系统刚度不足时,易引起振动。
(一)前角ro对切削力的影响前角ro增大,剪切角Φ随着增大,金属塑性变形减小,变形系数ξ减小,沿前刀面的摩擦力减小,因此切削力减小。
车刀种类和角度选择原则详解

? ③、选择后角的原则:
? 在不产生摩擦的条件下,应适当减小后角。
? 3.主偏角、副偏角的选择
? (1)主偏角的选择
? A、主偏角κr的增大或减小对切削加工有利的一 面
? 硬质合金可转位(不重磨)车刀在现代机械加工中广泛应用,其刀片用机械 夹固式装夹在刀杆上,当刀片一个刀刃磨钝后,只需将刀片转过一个角度,即 可用新的切削刃进行切削,从而大大缩短了换刀和磨刀时间,提高了刀杆的利 用率,节约了成本。
二.刀具材料
? 1、刀具材料应具备的性能
? (1)高硬度和好的耐磨性
常用车刀
本课内容
? 一.常用车刀的种类和用途
?二.刀具材料
?三.车刀组成
?四.车刀的安装
了解
?五.车刀的刃磨
? 六.车刀角度及切削参数的选择
了解
一.常用车刀的种类和用途
1.传统焊接刀具
直头车刀
弯头车刀
75°强力车刀
90°偏刀
切断刀或切槽刀
扩孔刀(通孔)
扩孔刀(不通孔)
螺纹车刀
2.硬质合金可转位(不重磨)车刀
? 前刀面:切削时,切屑流出所经过的表面。 ? 主后刀面:切削时,与工件加工表面相对的表面。 ? 副后刀面:切削时,与工件已加工表面相对的表面。 ? 主切削刃:前刀面与主后刀面的交线。它可以是直线或曲线,担负着主
要的切削工。 ? 副切削刃:前刀面与副后刀面的交线。一般只担负少量的切削工作。 ? 刀尖:主切削刃与副切削刃的相交部分。为了强化刀尖,常磨成圆弧形
? 粗加工时,一般取较小的前角;
简介车刀几何角度及功用

⑶ 正交平面:过切削刃选定点,同时垂直
于基面与切削平面的平面。
三个坐标平面相互垂直,构成一个空间直角坐标系。
5
2.2车刀切削部分结构—三面二刃一刀尖
(1) 前刀面:切屑流过的表面。 (2) 后刀面:与工件上的过渡表面相对着。
(3) 副后刀面:与工件上的已加工表面相对着。
(4) 主切削刃:前刀面与后刀面的交线。 (5) 副切削刃:前刀面与副后刀面的交线。 (6) 刀尖:主切削刃与副切削刃连接的地方。
1.1车刀角度基础要点
1
角度参考平面
2
角度参考系
3
切削部分的构成要素:三面二刃一刀尖
4
五个基本角度、两个派生角度
2.1车刀角度参考平面
⑴ 基面:过切削刃选定点,垂直于切削速 度方向和切削平面。 ⑵ 切削平面:过切削刃选定点,与过渡表 面相切,并垂直于基面的平面。它 也是切削刃与切削速度方向构成的 平面。
简介车刀几何角度及功用
王存龙 1 2016.8.26
目录
2 3 车刀简介 车刀切削部分结构 车刀几何角度 车刀几何角度的合理选择 车刀几何角度测量
4
5
1.车刀简介
任何刀具=刀头+刀柄 刀头用于切削,刀柄用于装夹。 虽然切削加工的刀具种类繁多,但刀具切削部分的组成有许多共同 点。车刀的切削部分可看作是各种刀具切削部分的最基本形态。
3.1车刀几何角度—投影到基面上的角度
主偏角(κr):主切削刃与进给运动方向的 夹角。一般在30°~ 90°之间。
副偏角(κr′):副切削刃与进给运动反方向
的夹角。副偏角一般为正值。 刀尖角(εr):主切削刃与副切削刃的夹角, 它是派生角度。
三者之和为180o。
车刀的主要几何角度及选择原则解析

1)前角(γ0 ) 选择的原则前角的大小主要解决刀头的坚固性与锋利性的矛盾。
因此首先要根据加工材料的硬度来选择前角。
加工材料的硬度高,前角取小值,反之取大值。
其次要根据加工性质来考虑前角的大小,粗加工时前角要取小值,精加工时前角应取大值。
前角一般在-5°~25°之间选取。
通常,制作车刀时并没有预先制出前角(γ0),而是靠在车刀上刃磨出排屑槽来获得前角的。
排屑槽也叫断屑槽,它的作用大了去了折断切屑,不产生缠绕;控制切屑的流出方向,保持已加工表面的精度;降低切削抗力,延长刀具寿命。
2)后角(α0 )选择的原则首先考虑加工性质。
精加工时,后角取大值,粗加工时,后角取小值。
其次考虑加工材料的硬度,加工材料硬度高,主后角取小值,以增强刀头的坚固性;反之,后角应取小值。
后角不能为零度或负值,一般在6°~12°之间选取。
3)主偏角(Kr ) 的选用原则首先考虑车床、夹具和刀具组成的车削工艺系统的刚性,如系统刚性好,主偏角应取小值,这样有利于提高车刀使用寿命、改善散热条件及表面粗造度。
其次要考虑加工工件的几何形状,当加工台阶时,主偏角应取90°,加工中间切入的工件,主偏角一般取60 °。
主偏角一般在30°~90°之间,最常用的是45°、75 °、90 °。
4)副偏角(Kr’ )的选择原则首先考虑车刀、工件和夹具有足够的刚性,才能减小副偏角;反之,应取大值;其次,考虑加工性质,精加工时,副偏角可取10°~15°,粗加工时,副偏角可取5°左右。
5)刃倾角(λS)的选择原则主要看加工性质,粗加工时,工件对车刀冲击大,取λS ≤ 0°,精加工时,工件对车刀冲击力小,取λS ≥ 0°;通常取λS =0°。
刃倾角一般在-10°~5°之间选取。
车刀角度分析
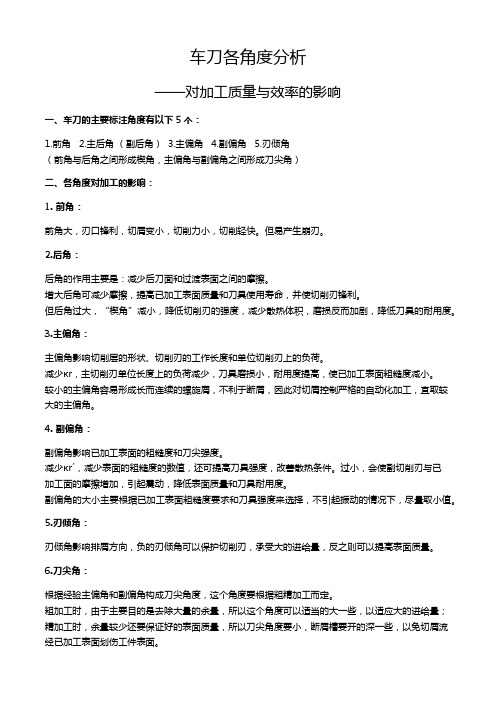
车刀各角度分析——对加工质量与效率的影响一、车刀的主要标注角度有以下5个:1.前角2.主后角(副后角)3.主偏角4.副偏角5.刃倾角(前角与后角之间形成楔角,主偏角与副偏角之间形成刀尖角)二、各角度对加工的影响:1. 前角:前角大,刃口锋利,切屑变小,切削力小,切削轻快。
但易产生崩刃。
2.后角:后角的作用主要是:减少后刀面和过渡表面之间的摩擦。
增大后角可减少摩擦,提高已加工表面质量和刀具使用寿命,并使切削刃锋利。
但后角过大,“楔角”减小,降低切削刃的强度,减少散热体积,磨损反而加剧,降低刀具的耐用度。
3.主偏角:主偏角影响切削层的形状、切削刃的工作长度和单位切削刃上的负荷。
减少κr,主切削刃单位长度上的负荷减少,刀具磨损小,耐用度提高,使已加工表面粗糙度减小。
较小的主偏角容易形成长而连续的螺旋屑,不利于断屑,因此对切屑控制严格的自动化加工,宜取较大的主偏角。
4. 副偏角:副偏角影响已加工表面的粗糙度和刀尖强度。
减少κr´,减少表面的粗糙度的数值,还可提高刀具强度,改善散热条件。
过小,会使副切削刃与已加工面的摩擦增加,引起震动,降低表面质量和刀具耐用度。
副偏角的大小主要根据已加工表面粗糙度要求和刀具强度来选择,不引起振动的情况下,尽量取小值。
5.刃倾角:刃倾角影响排屑方向,负的刃倾角可以保护切削刃,承受大的进给量,反之则可以提高表面质量。
6.刀尖角:根据经验主偏角和副偏角构成刀尖角度,这个角度要根据粗精加工而定。
粗加工时,由于主要目的是去除大量的余量,所以这个角度可以适当的大一些,以适应大的进给量;精加工时,余量较少还要保证好的表面质量,所以刀尖角度要小,断屑槽要开的深一些,以免切屑流经已加工表面划伤工件表面。
硬质合金车刀几何角度选择原则

●硬质合金车刀合理前角、后角的参考值(1)前角的选择增大前角,可减小切削变形,从而减小切削力、切削热,降低切削功率的消耗,还可以抑制积屑瘤和鳞刺的产生,提高加工质量。
但增大前角,会使楔角减小、切削刃与刀头强度降低,容易造成崩刃,还会使刀头的散热面积和容热体积减小,使切削区局部温度上升,易造成刀具的磨损,刀具耐用度下降。
选择合理的前角时,在刀具强度允许的情况下,应尽可能取较大的值,具体选择原则如下:1)加工塑性材料时,为减小切削变形,降低切削力和和切削温度,应选较大的前角,加工脆性材料时,为增加刃口强度,应取较小的前角。
工件的强度低,硬度低,应选较大的前角,反之,应取较小的前角。
用硬质合金刀具切削特硬材料或高强度钢时,应取负前角。
2)刀具材料的抗弯强度和冲击韧性较高时,应取较大的前角。
如高速钢刀具的前角比硬质合金刀具的前角要大;陶瓷刀具的韧性差,其前角应更小。
3)粗加工、断续切削时,为提高切削刃的强度,应选用较小的前角。
精加工时,为使刀具锋利,提高表面加工质量,应选用较大的前角。
当机床的功率不足或工艺系统的刚度较低时,应取较大的前角。
对于成形刀具和在数控机床、自动线上不宜频繁更换的刀具,为了保证工作的稳定性和刀具耐用度,应选较小的前角或零度前角。
(2)后角的选择增大后角,可减小刀具后刀面与已加工表面间的摩擦,减小磨损,还可使切削刃钝圆半径减小,提高刃口锋利程度,改善表面加工质量。
但后角过大,将削弱切削刃的强度,减小散热体积使散热条件恶化,降低刀具耐用度。
实验证明,合理的后角主要取决于切削厚度。
其选择原则如下:1)工件的强度、硬度较高时,为增加切削刃的强度,应选较小后角。
工件材料的塑性、韧性较大时,为减小刀具后刀面的摩擦,可取较大的后角。
加工脆性材料时,切削力集中在刃口附近,应取较小的后角。
2)粗加工或断续切削时,为了强化切削刃,应选较小的后角。
精加工或连续切削时,刀具的磨损主要发生在刀具后刀面,应选用较大的后角。
刀具角度的功用与选择
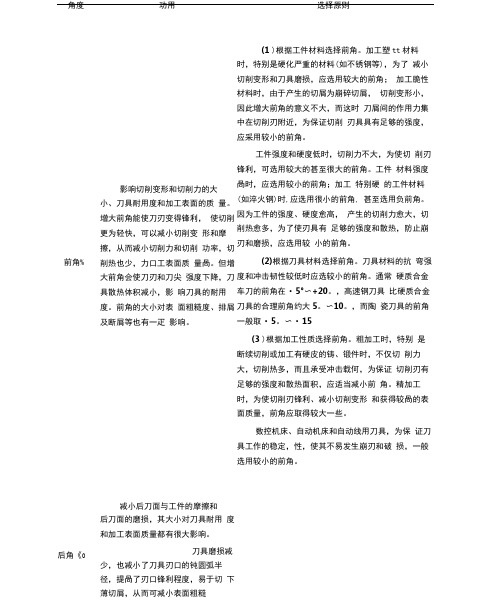
(1 )根据工件材料选择前角。
加工塑tt 材料 时,特别是硬化严重的材料(如不锈钢等),为了 减小切削变形和刀具磨损,应选用较大的前角; 加工脆性材料时,由于产生的切屑为崩碎切屑, 切削变形小,因此增大前角的意义不大,而这时 刀屑间的作用力集中在切削刃附近,为保证切削 刃具具有足够的强度,应采用较小的前角。
工件强度和硬度低时,切削力不大,为使切 削刃锋利,可选用较大的甚至很大的前角。
工件 材料强度咼时,应选用较小的前角;加工 特别硬 的工件材料(如淬火钢)时,应选用很小的前角, 甚至选用负前角。
因为工件的强度、硬度愈高, 产生的切削力愈大,切削热愈多,为了使刃具有 足够的强度和散热,防止崩刃和磨损,应选用较 小的前角。
(2)根据刀具材料选择前角。
刀具材料的抗 弯强度和冲击韧性较低时应选较小的前角。
通常 硬质合金车刀的前角在・5°〜+20。
,高速钢刀具 比硬质合金刀具的合理前角约大5。
〜10。
,而陶 瓷刀具的前角一般取・5。
〜・15 (3 )根据加工性质选择前角。
粗加工时,特别 是断续切削或加工有硬皮的铸、锻件时,不仅切 削力大,切削热多,而且承受冲击载何,为保证 切削刃有足够的强度和散热面积,应适当减小前 角。
精加工时,为使切削刃锋利、减小切削变形 和获得较咼的表面质量,前角应取得较大一些。
数控机床、自动机床和自动线用刀具,为保 证刀具工作的稳定,性,使其不易发生崩刃和破 损,一般选用较小的前角。
角度功用 选择原则 减小后刀面与工件的摩擦和 后刀面的磨损,其大小对刀具耐用 度和加工表面质量都有很大影响。
后角《0刀具磨损减 少,也减小了刀具刃口的钝圆弧半 径,提咼了刃口锋利程度,易于切 下薄切屑,从而可减小表面粗糙 前角%影响切削变形和切削力的大 小、刀具耐用度和加工表面的质 量。
增大前角能使刀刃变得锋利, 使切削更为轻快,可以减小切削变 形和摩擦,从而减小切削力和切削 功率,切削热也少,力口工表面质 量咼。
刀具角度选用原则

刀具角度选用原则Document serial number【UU89WT-UU98YT-UU8CB-UUUT-UUT108】刀具几何角度的作用及选择原则答:1是前角; 2是后角; 3是副偏角; 4是刀尖角;5是主偏角; 6是副后角; 7是副前角; 8是刃倾角名称:前角作用:加大前角,刀具锋利,切削层的变形及前面摩擦阻力小,切削力和切削温度可减低,可抑制或消除积屑瘤,但前角过大,刀尖强度降低;选择原则:(1)工件材料的强度、硬度低,塑性好时,应取较大的前角;反之应取较小的前角;加工特硬材料(如淬硬钢、冷硬铸铁等)甚至可取负的前角(2)刀具材料的抗弯强度及韧性高时,可取较大的前角(3)断续切削或精加工时,应取较小的前角,但如果此时有较大的副刃倾角配合,仍可取较大的前角,以减小径向切削力(4)高速切削时,前角对切屑变形及切削力的影响较小,可取较小前角(5)工艺系统钢性差时,应取较大的前角名称:后角作用:减少刀具后面与工件的切削表面和已加工表面之间的摩擦。
前角一定时,后角愈锋利,但会减小楔角,影响刀具强度和散热面积。
选择原则:(1)精加工时,切削厚度薄,磨损主要发生在后刀面,宜取较大后角;粗加工时,切削厚度大,负荷重,前、后面均要发生磨损、宜取较小后角(2)多刃刀具切削厚度较薄,应取较大后角(3)被加工工件和刀具钢性差时,应取较小后角,以增大后刀面与工件的接触面积,减少或消除振动(4)工件材料的强度、硬度低、塑性好时,应取较大的后角,反之应取较小的后角;但对加工硬材料的负前角刀具,后角应稍大些,以便刀刃易于切入工件;(5)定尺寸刀具(如内拉刀、铰刀等)应取较小后角,以免重磨后刀具尺寸变化太大;(6)对进给运动速度较大的刀具(如螺纹车刀、铲齿车刀等),后角的选择应充分考虑到工作后角与标注后角之间的差异;(7)铲齿刀具(如成形铣刀、滚刀等)的后角要受到铲背量的限制,不能太大,但要保证侧刃后角不小于2°。
车刀角度的作用及选用原则
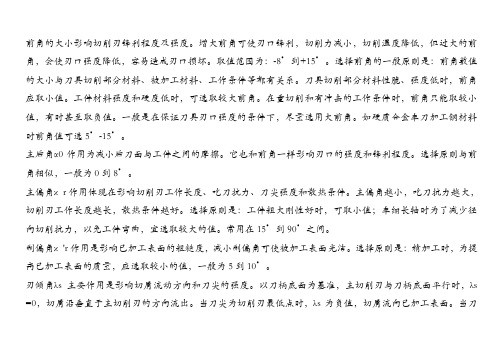
前角的大小影响切削刃锋利程度及强度。
增大前角可使刃口锋利,切削力减小,切削温度降低,但过大的前角,会使刃口强度降低,容易造成刃口损坏。
取值范围为:-8°到+15°。
选择前角的一般原则是:前角数值的大小与刀具切削部分材料、被加工材料、工作条件等都有关系。
刀具切削部分材料性脆、强度低时,前角应取小值。
工件材料强度和硬度低时,可选取较大前角。
在重切削和有冲击的工作条件时,前角只能取较小值,有时甚至取负值。
一般是在保证刀具刃口强度的条件下,尽量选用大前角。
如硬质合金车刀加工钢材料时前角值可选5°-15°。
主后角α0作用为减小后刀面与工件之间的摩擦。
它也和前角一样影响刃口的强度和锋利程度。
选择原则与前角相似,一般为0到8°。
主偏角κr作用体现在影响切削刃工作长度、吃刀抗力、刀尖强度和散热条件。
主偏角越小,吃刀抗力越大,切削刃工作长度越长,散热条件越好。
选择原则是:工件粗大刚性好时,可取小值;车细长轴时为了减少径向切削抗力,以免工件弯曲,宜选取较大的值。
常用在15°到90°之间。
副偏角κ'r作用是影响已加工表面的粗糙度,减小副偏角可使被加工表面光洁。
选择原则是:精加工时,为提高已加工表面的质量,应选取较小的值,一般为5到10°。
刃倾角λs主要作用是影响切屑流动方向和刀尖的强度。
以刀柄底面为基准,主切削刃与刀柄底面平行时,λs =0,切屑沿垂直于主切削刃的方向流出。
当刀尖为切削刃最低点时,λs为负值,切屑流向已加工表面。
当刀尖为主切削刃最高点时,λs为正值,切屑流向待加工表面。
一般刃倾角λs取-5°到+10°。
精加工时,为避免切屑划伤已加工表面,应取正值或零。
粗加工或切削较硬的材料时,为提高刀头强度可取负值。
车刀的主要角度及其作用来源:本站浏览次数:289车刀的主要角度有前角(γ0)、后角(α0)、主编角(Kr)、副偏角(Kr’)和刃倾角(λs)。
车刀的几何角度

车刀的几何角度及选择原则一.为了决定车刀刃口的锋利程度及其在空间的位置,必须建立一个坐标系,该坐标系由三个基准平面构成。
下面以外圆车刀为例,介绍车刀的几何角度。
如图7-5所示.。
基面:过主切削刃选定点的平面,此平面在主切削刃为水平时包含主刀刃并与车刀安装底面即水平面平行,此平面主要作为度量前刀面在空间位置的基准平面。
切削平面:过主切削刃选定点与主切削刃相切,并与基面相垂直的平面。
此平面主要作为度量主后刀面在空间位置的基准面。
主剖面:过主切削刃选定点并同时垂直于基面和主切削平面的平面。
(1)、前角前刀面与基面的夹角,在主剖面中测量。
前角的大小影响切削刃锋利程度及强度。
增大前角可使刃口锋利,切削力减小,切削温度降低,但过大的前角,会使刃口强度降低,容易造成刃口损坏。
取值范围为:-8o到+15o。
选择前角的一般原则是:前角数值的大小与刀具切削部分材料、被加工材料、工作条件等都有关系。
刀具切削部分材料性脆、强度低时,前角应取小值。
工件材料强度和硬度低时,可选取较大前角。
在重切削和有冲击的工作条件时,前角只能取较小值,有时甚至取负值。
一般是在保证刀具刃口强度的条件下,尽量选用大前角。
如硬质合金车刀加工钢材料时前角值可选5o-15o。
(2)、主后角主后刀面与切削平面间的夹角,在主剖面中测量。
其作用为减小后刀面与工件之间的摩擦。
它也和前角一样影响刃口的强度和锋利程度。
选择原则与前角相似,一般为0o到8o。
(3)、主偏角主切削刃与进给方向间的夹角,在基面中测量。
其作用体现在影响切削刃工作长度、吃刀抗力、刀尖强度和散热条件。
主偏角越小,吃刀抗力越大,切削刃工作长度越长,散热条件越好。
选择原则是:工件粗大刚性好时,可取小值;车细长轴时为了减少径向切削抗力,以免工件弯曲,宜选取较大的值。
常用在15o到90o之间。
(4)、副偏角副切削刃与进给反方向间的夹角,在基面中测量。
其作用是影响已加工表面的粗糙度,减小副偏角可使被加工表面光洁。
硬质合金车刀几何角度选择原则
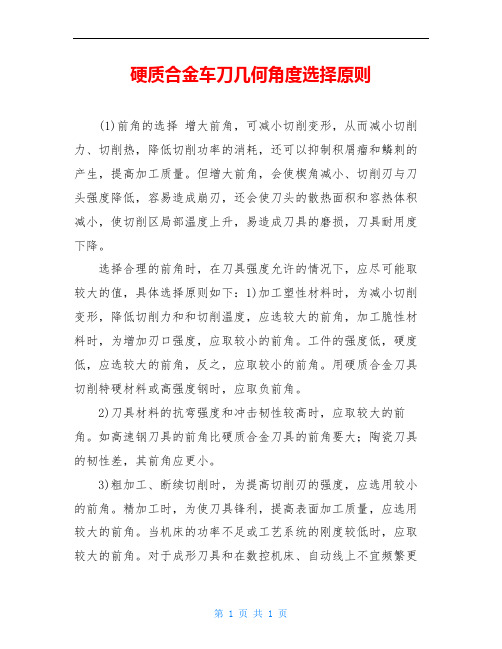
硬质合金车刀几何角度选择原则(1)前角的选择增大前角,可减小切削变形,从而减小切削力、切削热,降低切削功率的消耗,还可以抑制积屑瘤和鳞刺的产生,提高加工质量。
但增大前角,会使楔角减小、切削刃与刀头强度降低,容易造成崩刃,还会使刀头的散热面积和容热体积减小,使切削区局部温度上升,易造成刀具的磨损,刀具耐用度下降。
选择合理的前角时,在刀具强度允许的情况下,应尽可能取较大的值,具体选择原则如下:1)加工塑性材料时,为减小切削变形,降低切削力和和切削温度,应选较大的前角,加工脆性材料时,为增加刃口强度,应取较小的前角。
工件的强度低,硬度低,应选较大的前角,反之,应取较小的前角。
用硬质合金刀具切削特硬材料或高强度钢时,应取负前角。
2)刀具材料的抗弯强度和冲击韧性较高时,应取较大的前角。
如高速钢刀具的前角比硬质合金刀具的前角要大;陶瓷刀具的韧性差,其前角应更小。
3)粗加工、断续切削时,为提高切削刃的强度,应选用较小的前角。
精加工时,为使刀具锋利,提高表面加工质量,应选用较大的前角。
当机床的功率不足或工艺系统的刚度较低时,应取较大的前角。
对于成形刀具和在数控机床、自动线上不宜频繁更换的刀具,为了保证工作的稳定性和刀具耐用度,应选较小的前角或零度前角。
(2)后角的选择增大后角,可减小刀具后刀面与已加工表面间的摩擦,减小磨损,还可使切削刃钝圆半径减小,提高刃口锋利程度,改善表面加工质量。
但后角过大,将削弱切削刃的强度,减小散热体积使散热条件恶化,降低刀具耐用度。
实验证明,合理的后角主要取决于切削厚度。
其选择原则如下:1)工件的强度、硬度较高时,为增加切削刃的强度,应选较小后角。
工件材料的塑性、韧性较大时,为减小刀具后刀面的摩擦,可取较大的后角。
加工脆性材料时,切削力集中在刃口附近,应取较小的后角。
2)粗加工或断续切削时,为了强化切削刃,应选较小的后角。
精加工或连续切削时,刀具的磨损主要发生在刀具后刀面,应选用较大的后角。
车刀角度的作用及选用原则
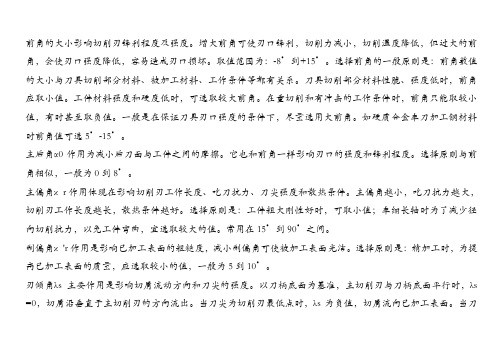
前角的大小影响切削刃锋利程度及强度。
增大前角可使刃口锋利,切削力减小,切削温度降低,但过大的前角,会使刃口强度降低,容易造成刃口损坏。
取值范围为:-8°到+15°。
选择前角的一般原则是:前角数值的大小与刀具切削部分材料、被加工材料、工作条件等都有关系。
刀具切削部分材料性脆、强度低时,前角应取小值。
工件材料强度和硬度低时,可选取较大前角。
在重切削和有冲击的工作条件时,前角只能取较小值,有时甚至取负值。
一般是在保证刀具刃口强度的条件下,尽量选用大前角。
如硬质合金车刀加工钢材料时前角值可选5°-15°。
主后角α0作用为减小后刀面与工件之间的摩擦。
它也和前角一样影响刃口的强度和锋利程度。
选择原则与前角相似,一般为0到8°。
主偏角κr作用体现在影响切削刃工作长度、吃刀抗力、刀尖强度和散热条件。
主偏角越小,吃刀抗力越大,切削刃工作长度越长,散热条件越好。
选择原则是:工件粗大刚性好时,可取小值;车细长轴时为了减少径向切削抗力,以免工件弯曲,宜选取较大的值。
常用在15°到90°之间。
副偏角κ'r作用是影响已加工表面的粗糙度,减小副偏角可使被加工表面光洁。
选择原则是:精加工时,为提高已加工表面的质量,应选取较小的值,一般为5到10°。
刃倾角λs主要作用是影响切屑流动方向和刀尖的强度。
以刀柄底面为基准,主切削刃与刀柄底面平行时,λs =0,切屑沿垂直于主切削刃的方向流出。
当刀尖为切削刃最低点时,λs为负值,切屑流向已加工表面。
当刀尖为主切削刃最高点时,λs为正值,切屑流向待加工表面。
一般刃倾角λs取-5°到+10°。
精加工时,为避免切屑划伤已加工表面,应取正值或零。
粗加工或切削较硬的材料时,为提高刀头强度可取负值。
车刀的主要角度及其作用来源:本站浏览次数:289车刀的主要角度有前角(γ0)、后角(α0)、主编角(Kr)、副偏角(Kr’)和刃倾角(λs)。
刀具前角、后角和主、副偏角的功用及其选择

刀具前角、后角和主、副偏角的功用及其选择刀具前角、后角和主、副偏角的功用及其选择分类:机械切削一、前角的功用及合理前角值的选择从金属切削的变形规律可知,前角(γ。
)是切削刀具上重要的几何参数之一,它的大小直接影响切削力、切削温度和切削功率,影响刃区和刀头的强度、容热体积和导热面积,从而影响刀具使用寿命和切削加工生产率。
选择合理的前角,是刀具设计的重要问题。
1.前角的主要功用(1)影响切削区域的变形程度:若增大刀具前角,可减小前刀面挤压切削层时的塑性变形,减小切屑流经前刀面的摩擦阻力,从而减小了切削力、切削热和功率。
第四章图4—14所示,为前角γ。
对三个切削分力的影响,当前角增大时,Fc、Fp、Ff力均显著减小,这是增大前角的有利方面。
(2)影响切削刃与刀头的强度、受力性质和散热条件:增大刀具前角,会使切削刃与刀头的强度降低,刀头的导热面积和容热体积减小;过份加大前角,有可能导致切削刃处出现弯曲应力,造成崩刃。
这些都是增大前角的不利方面。
(3)影响切屑形态和断屑效果:若减小前角,可以增大切屑的变形,使之易于脆化断裂。
(4)影响已加工表面质量:前角与表面质量的关系,在第九章已有论述。
值得法意的是,前角大小同切削过程中的振动现象有关,减小前角或者采用负前角时,振幅急剧增大,如图10—5所示。
2.合理前角的概念从上述前角的作用可知,增大或减小前角,各有其有利和不利两方面的影响。
例如,从切削热的产生和散热来说,增大前角,可以减小切削热的产生,切削温度不致太高;但如果前角太大,则因刀头导热面积和容热体积减小,切削温度反而升高。
在切削很硬的材料时,应用较小的前角,甚至选用适宜的负前角,以加强切削刃,并改善刀头容热和散热条件;但若是前角太小,或取很大的负前角,则因切削变形严重,产生热量多,来不及散逸,结果还会使切削温度上升。
可见,在一定的条件下,前角有一个合理的数值。
图10—6为刀具前角对使用寿命影响的示意曲线。
- 1、下载文档前请自行甄别文档内容的完整性,平台不提供额外的编辑、内容补充、找答案等附加服务。
- 2、"仅部分预览"的文档,不可在线预览部分如存在完整性等问题,可反馈申请退款(可完整预览的文档不适用该条件!)。
- 3、如文档侵犯您的权益,请联系客服反馈,我们会尽快为您处理(人工客服工作时间:9:00-18:30)。
阐述车刀各角度的功用和选择原则
车刀是数控车床上常用的加工工具,它具有以下多方面的功用和选择
原则。
1. 功能实用
车刀主要用于车削工艺中,能够完成粗、精、超精细车削等多种加工
工艺。
此外,车刀还可以进行纵向和横向的镗孔、内外螺纹加工、面铣、棒材端面加工等工艺。
综合以上种种加工工艺,车刀为车床的加
工效率和加工精度提供了有力保障。
2. 材质选择
车刀的材质包括硬质合金、高速钢、陶瓷等。
其中,硬质合金车刀耐
磨性好,适合加工硬质材料;高速钢车刀强度高,适合普通材料加工;陶瓷车刀温度稳定,适合加工高温材料。
根据加工工件类型和工艺要求,可进行合理选择。
3. 形状特征
车刀的形状特征包括刀身长度、刀身断面形状、刀尖形状等。
不同形
状的车刀可适应不同的加工需求。
例如,针对大直径粗车和粗车加精
车可以采用U型车刀,针对横向镗孔可以采用V型车刀等。
4. 刃口类型
车刀的刃口类型包括单刃、双刃、三刃、四刃等。
单刃车刀适合小型工件的高效加工;双刃车刀适合中型工件的加工;三刃和四刃车刀适合大型工件加工,能够提高工件加工效率和加工精度。
综上,根据不同的工件需求和加工工艺,可选择不同材质、形状特征和刃口类型的车刀,以提高车床加工效率和加工质量。