塑胶件PFMEA 样例
注塑PFMEA范本
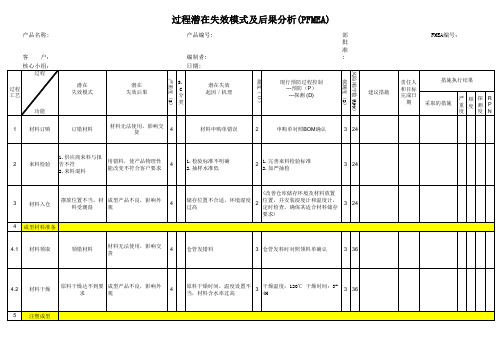
长,保压压力过大 4.模温过低,注射速度过 3
快,注射压力过大 5.注射速度过快,注射压力
过大 6.保压时间不合理,注射压
力不合理(第二段) 7.原材料中含有一定阻燃
剂,导致模具发红
1.升高料温,加大注射压力,延 长保压时间
2.加大注射剂量,加大注射压力 3.加强锁模力,降低料温,减小 注射压力,缩短保压时间,减小
1.制作参数参 照表;提高调 机员的技术水
平 2.经常性清洗 及更换模具配
件
7
2
3 42
5.3 首件确认
外观不良 产品尺寸超差
客户投诉,退货
4
客户投诉,退货
5
2
2 16
未按成型工艺参数表设定
按成型工艺参数表重新设定参数
2
3 30
产品名称:
客 户: 核心小组:
过程 过程 工艺
功能
6 生产自检
潜在 失效模式
责任人 和目标 完成日
期
措施执行结果
采取的措施
严频探 R 重度测 P 度 度N
4
成型条件不稳定
2
对设备进行维修或,使用备用机 台
3
24
7
IPQC 制程检 验
外观不良 产品尺寸超差
客户投诉,退货
4
客户投诉,退货
4
成型条件不稳定 成型条件不稳定
2
对设备进行维修或,使用备用机 台
3
24
2
对设备进行维修或,使用备用机 台
频度(O)
严重度(S)
过程潜在失效模式及后果分析(PFMEA)
产品编号:
编制者: 日期:
塑胶件PFMEA

5
组装
偏位 顾客抱怨 6
素材未卡緊
4
治具松动 作業環境易與產品發 生碰撞 刮伤 外观不良, 造成客訴 4 人員操作不标准
3
5
6
泰德兴精密电子(昆山)有限公司
潛在失效模式及效果分析-过程FMEA
组装站 2014.2.25 版 日 次 期
1.0
2014.2.17
ห้องสมุดไป่ตู้
审核 作版
现行过程控制-预防
現行过程控制-探测
4
48
1.机台点检
4
100
1.对作业人员进行教育训练.
4
100
治具做防呆
96 4 72
治具點檢 對流水臺與作業臺表面加防 護,降低碰刮傷機率
80 4 96
1.作業人員目視全檢 加强对作业人员教育,改正作 2.檢驗人員2H/次/4PCS 业手法,SOP中定義輕拿輕 放,堆放不可超過5pcs,且堆 放時需以包裝袋作依托
袁桃丽
改善結果 严 探 R 频 重 测 P 度 度 度 N
泰德兴精密电子(昆山)有
專案名称: MC32 机种 57-110158-02/57-110158-02/57110158-02/57-110158-02/57零件名称: 110158-02 小組成员: 袁桃丽.骆小峰.陆华龙.刘明进. 陈华.董淑涛. 过程责任: 组装站 关键日期: 2014.2.25
潛在失效模式及效果分析-过
严 过程功能 潜在失效 重 潜在失效模式 要求 后果 度 S
分 發 類 潜在失效原因/机 生 等 度 理 级 O
1.产线线速过快,人 員來不及 2.作业员手法不熟练
漏件
影响组装功 能
4
3
塑胶射出PFMEA样本
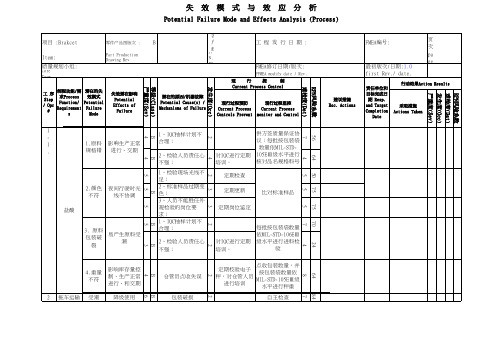
126
98
2 2 3 2
9 8 6 4
7
2
7
112 90 32
受潮 包材储存 数量不 够 受潮 4 拖车运输 包装破 损
降级使用 B 4 B 4 影响生产 B 4 降级使用 原料撒落 B 3 B 3 4 2 2 2 2 2
112 40 32 42 42 48
7 5 4 7 7 8
失
效
模
式
与
效
应
分
析
64
B 4 B 6
2
8
84
包装破损
2
7
失
效
模
式
与
效
应
分
析
Potential Failure Mode and Effects Analysis (Process)
项目 :Brakcet Item: 质量规划小组:
Core Team
零件产品图版次 :
B
客户料号:
P/N.number
工 程 发 行 日 期 :
失
效
模
式
与
效
应
分
析
Potential Failure Mode and Effects Analysis (Process)
项目 :Brakcet Item: 质量规划小组:
Core Team
零件产品图版次 :
B
客户料号:
P/N.number
工 程 发 行 日 期 :
FMEA编号:
页次 page
Part Production Drawing Rev
严重度(Sev)
发生度(Occ)
难检度(Det)
RPN风险系数
PFMEA范例
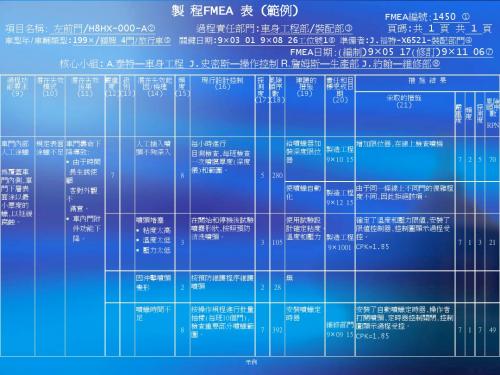
適中的
適度高的 高的 非常高的 幾乎確定
5
4 3 2 1
製程管制方法幾乎可以確定查出失效模式。
製 程 FMEA 填 寫 說 明
19.風險優先數 風險優先數是嚴重度(S)、發生度(O)、和難 檢度(D)的乘積。 RPN=(S)(O)(D) 是一項設計風險的指標。當RPN較高時,設計
小組應提出矯正措施來降低RPN數。一般實務上,
1 in 400
1 in 2,000 1 in 15,000 1 in 150,000 <=1 in 1,500,000
≧1.00
≧1.17 ≧1.33 ≧1.50 ≧1.67
5
4 3 2 1
“可能失效的比率”是根據製程執行中預計發生的失效來確定的。 “失效的機率”用文字描述適合任何類似製程的歷史數據進行主觀評價。
9
8 7 6 5
非常低的
次要的 非常次要的 沒有
4
3 2 1
製 程 FMEA 填 寫 說 明
13.等級 這個欄位用來區分任何 對零件、子系統、或系統將 要求附加於製程管制的特殊 產品特性(如:關鍵的、主要 的、重要的)。如果在製程 FMEA被認定等級,通知設計 負責工程師,這將影響工程 文件相關管制項目的認定。 14.潛在失效原因/機理 在盡可能的範圍里列出所有 可能想像得到的失效原因: ○不當的扭力。 ○不適當的焊接,電流、時間、 壓力。 ○不精確的量具。 ○熱處理不正確-時間、溫度澆 口/通風不正確。 ○不適當或沒有潤滑。 ○缺少零件或放錯。 需要考慮諸如試驗設計之類的方法,來明確那些根本原因起主要作用, 哪些原因容易得到控制。
製 程 FMEA 填 寫 說 明 追蹤確認
製程責任工程師應負責確認所有的建議措施均已
注塑产品PFMEA表

FME A 编产品名称/Product:J ETTA 内框过程职责第页关键日期编制人:刘红FMEA (原2014.5.8控制预防Control and Prevention 发生度Occur 控制探测Control and Detection 探测度Dete 采取的措施/完成日期Measures/C 严重度S 发生度O 探测度D RPN 10 原料采购及时延期影响生产5没合理安排库存设最低库存,及时跟踪2按月订单量的一半设最低库存330包装破包影响产品外观7运输过程损坏专人验收6全检142颗粒大小均匀颗粒连并、偏大影响注塑加工6供应商生产造成抽检2两包/批44810-2 原料入库指定位置,批次分开批次混放发料时混发2作业员未按规定分区,加强管理4专人检查32410-3 配料先进先出混料影响产品品质稳定6作业员未按规定加强员工培训、管理,做好原料标识3专人发放原料,建立原料台账236设定温度过高材料结块6F 作业员疏忽现场放置作业指导书3每小时检查1~2次236设定温度过低材料干燥不充分6F作业员疏忽现场放置作业指导书3每小时检查1~2次47220-2 模具安装安全碰擦、伤害人员受伤、耽误生产6作业员疏忽加强培训、严格按安全作业标准操作2现场管控,季度考核224调试工艺时间长耽误生产进度4工艺员业务水平不够加强培训3月度考核336外观尺寸不合格返工或报废5F 工艺调整不合理制作工艺表,并及时更新,检验员及时跟进5做好首件确认37520-4 注塑成型稳定产品容易出现缺陷报废产品多,产量不够3设备不稳定加强设备保养3设备保养维修记录32720-5 取产品、修边、自检无缩痕、无明显熔接痕、无变形、缺料、拉丝、卡爪断裂缺陷产品容易混进包装返工5F作业员疏忽、质量意识不强定期对员工进行培训、做好标准样品参考5自检记录、月度考核375外观符合要求(如上)缺陷产品容易漏检返工、客诉、退货7F 检验员抽检比率太小或漏抽严格按标准要求每箱抽取两个4产品入库检验记录384尺寸合格尺寸偏差报废7F工艺不合理做好首件确认4加强巡检力度384包装箱无损坏使用不合格纸箱产品损坏、客户退货6作业员疏忽加强作业员培训、管理3按作业指导书操作236数量准确多装或少装客诉、退货6作业员疏忽加强作业员培训、管理4电子称复检372搬运过程损坏客诉、退货6作业员野蛮搬运加强作业员培训、管理3专人负责354码放太高产品损坏、纸箱损坏4作业员不按规定实施作业加强作业员培训、管理3专人负责检查112RPN 建 议 措施Suggestio n Measure 职责和目标完成日期Duties and target completion干燥温度85±5°快速、合理20-1 原料干燥20-3 工艺调试30 检验40 包装50 入库失效潜在原因Potential causes of failure 现行过程 Current Process 实施结果Results of theimplementation 过程Process步骤Step 功能要求Request 分类Clas sify 轻拿轻放、最高堆放5层潜在失效模式Potential FailureMode失效潜在影响The potential impact of failure 严重度Seve rity 10-1 检验 注塑产品PFMEA表潜在失效模式与影响分析Failure mode and effects analysis(过程FMEA/Process FMEA )车型年/项目/Model year/Project:JETTA 1.4T 核心小组/Core Group:项目小组。
完整实用的过程PFMEA实例(注塑企业)
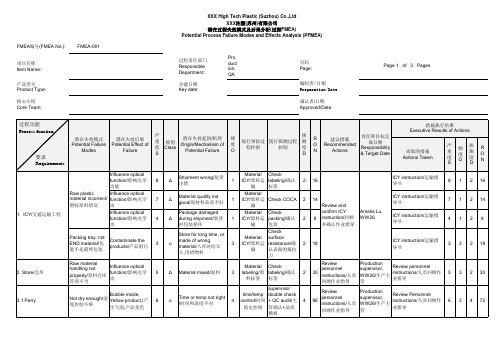
过程责任部门 Responsible Department:
Pro duct ion, QA
关键日期 Key date:
页码 Page:
编制者/日期 Preparation/Date
确认者/日期 Approved/Date
Page 1 of 3 Pages
பைடு நூலகம்
过程功能
Process function 要求
Imaging lens Dia.,
Dim 1: 5.78±0.03 Influence out of spec./镜头 assembly/影响装配
3
直径尺寸超规
Review PM mould
Order start
Production personnel instruction,
o
Wrong insert/嵌入错误
Contaminate the products/产品脏污
3
2. Store/仓库
Raw material handling not properly/原料仓库 管理不当
Influence optical function/影响光学 功
5
3.1 Perry
Not dry enough/湿 度控制不够
1
release
Dim check/尺
plan/订单开 寸确认
2
6
PM mould /点检 磨具
supervisor, incoming inspection WW26/生产主 optical inserts/人员回顾
时包装损坏
输
包装
并确认作业指导
ICY instruction/运输指 导书
ICY instruction/运输指 导书
塑胶产品易开裂物料 PFMEA 模板-(1

清理完成后技术员对清理工 作确认,用无尘布擦拭,无 脏污即可(详见换料作业指
导书进行作业) 技术员开机前对材料进行核 对确认是否按照规范做业。
技术员对加料人员设定的干 燥温度及时间进行确认,选
用设备进行确认.
材料在炮筒停留时间适 当,生产出外观、功能 合格的产品
成型机台与实际零件重量不匹 配,导致材料降解
7 材料在炮筒停留时间过长
成型周期设置不合理,导致生产 7 材料在炮筒停留时间过长 周期过长,导致材料降解
生产设备性能稳定可 靠,产品一致性好,支 持批量生产
螺杆磨损造成储料不稳定或驱动 曲臂磨损造成锁模不稳定,机台 稳定性差,产品一致性不好,可 能出现小概率的不良品
8
注塑机台维护不到位
模温符合理、正确,生 实测多点模温偏低,导致熔接线 8 实测模具温度不够高,致零件内
产出外观、功能合格的 位置强度下降、开裂
应力偏大
产品
注塑压力合理、正确, 注塑压力过大,使产品内应力大 8 注塑压力过大
生产出外观、功能合格
的产品
速度过快会导致材料温度上升而 8 小浇口情况下,注塑速度过快
5
设备维护不到位
生产前5模样品需废弃, 生产前10模内注塑机参数还不稳 5 生产过程控制不完善
10模后注塑趋于稳定, 定,产品一致性不好,不良率高
产品一致性好
8 零件清洗工艺缺失、或不彻底 金属镶件有油污,跟塑胶材料不
兼容
清洗外观、油污的溶剂跟塑胶材 8 清洗剂选择错误 料不兼容
8 模具上模前保养不规范 顶针油、润滑油等模具用油接触
过大,导致材料降解;背压过 小,导致熔胶内气体量过大,材 料易局部降解,产品易产生气 泡,开裂。
注塑产品_PFMEA案例

共 4页 编制
最初编 制日期
FMEA 编号
201
FMEA 版本号
A
电话号码
FMEA 最新 更改日期
过程
要求
潜在失效模式 潜在的失效后果
严
重 等 潜在的失效原因/
度级
机理
S
控制预防
产品表面缩水
产品外观不合格 顾客抱怨
产品尺寸偏大 与相关零件不匹配,
或偏小
使顾客不满意
4、注塑成型
通过注塑机和模 产品表面烧焦 具成型生产出颜 色、外观、尺寸 、性能合格的产
2
《成型条件表》每班 次点检
4
48
2/16
编号: 总成
零件名称/零件号/工 序名称
产品编号:
CFT小组成 员:
分总成
潜在的失效模式及后果分析-PFMEA
零件
设 计/ 过 程 责 任 部 门
制 造 部
关键日期:(要求PFMEA编制完成日及预计生产开始日期)
Hale Waihona Puke PFMEA编制预定完成日:
预计生产开始日:8
9/16
2013-01
A/0
措施结果 R
ODP N
10/16
2013-01
A/0
措施结果 R
ODP N
11/16
2013-01
A/0
措施结果 R
ODP N
12/16
2013-01
A/0
措施结果 R
ODP N
13/16
2013-01
A/0
措施结果 R
ODP N
14/16
2013-01
A/0
不正确
作业
7
注塑产品 PFMEA案例

零件名称/零件号/工序名称设计/过程责任部门编制电话号码制造部产品编号:最初编制日期FMEA 最新更改日期CFT小组成员:控制预防发生度O控制探测探测度D采取的措施S1、来料检验少检验不合格品进入公司影响产品质量7抽样数量错误做成抽样标准,根据标准要求数量抽样2检验记录表班长确认456漏判不合格品进入公司影响产品质量7检验员能力不够对检验员岗前进行培训,并进行能力考核2456误判合格品判为不合格,导致不能及时投入生产影响产品纳期6检验员抽样过于集中对检验员岗前进行抽检方法培训,并进行能力考核2448 7料粒色泽不均匀,有杂质根据颜色样本进行检验2投料前确认、记录456 9ROHS测试不合格该产品原材料属于顾客提供,根据供应商提供材料保证书、检测报告判定261082、生产领料根据出料单正确出料原材料出库错误产品特性不能满足顾客要求,顾客投诉8领料员未依据生产任务通知单进行实物确认对领料员、仓库管理员进行岗前教育2投料前确认、记录232要求按照检验规定进行抽样,并正确判定来料品质潜在的失效原因/机理关键日期:(要求PFMEA编制完成日及预计生产开始日期)PFMEA编制预定完成日: 预计生产开始日:8FMEA 编号FMEA 版本号RPN2等级措施结果共 4 页现行过程责任目标/完成日期建议措施过程潜在失效模式潜在的失效后果严重度S原材料不符合要求顾客不满意总成分总成零件零件名称/零件号/工序名称设计/过程责任部门编制电话号码制造部产品编号:最初编制日期FMEA 最新更改日期CFT小组成员:控制预防发生度O控制探测探测度D采取的措施S要求潜在的失效原因/机理关键日期:(要求PFMEA编制完成日及预计生产开始日期)PFMEA编制预定完成日: 预计生产开始日:8FMEA 编号FMEA 版本号RPN2等级措施结果共 4 页现行过程责任目标/完成日期建议措施过程潜在失效模式潜在的失效后果严重度S总成分总成零件零件名称/零件号/工序名称设计/过程责任部门编制电话号码制造部产品编号:最初编制日期FMEA 最新更改日期CFT小组成员:控制预防发生度O控制探测探测度D采取的措施S要求潜在的失效原因/机理关键日期:(要求PFMEA编制完成日及预计生产开始日期)PFMEA编制预定完成日: 预计生产开始日:8FMEA 编号FMEA 版本号RPN2等级措施结果共 4 页现行过程责任目标/完成日期建议措施过程潜在失效模式潜在的失效后果严重度S总成分总成零件零件名称/零件号/工序名称设计/过程责任部门编制电话号码制造部产品编号:最初编制日期FMEA 最新更改日期CFT小组成员:控制预防发生度O 控制探测探测度D 采取的措施S要求潜在的失效原因/机理关键日期:(要求PFMEA编制完成日及预计生产开始日期)PFMEA编制预定完成日: 预计生产开始日:8FMEA 编号FMEA 版本号R P N2等级措施结果共 4 页现行过程责任目标/完成日期建议措施过程潜在失效模式潜在的失效后果严重度S 总成分总成零件首件检查、PQC巡检、自检影响顾客装配顾客抱怨根据生产工艺卡,成型工艺监控8具成型生产出颜色、外观、尺寸、性能合格的产品产品缺胶零件名称/零件号/工序名称设计/过程责任部门编制电话号码制造部产品编号:最初编制日期FMEA 最新更改日期CFT小组成员:控制预防发生度O控制探测探测度D采取的措施S要求潜在的失效原因/机理关键日期:(要求PFMEA编制完成日及预计生产开始日期)PFMEA编制预定完成日: 预计生产开始日:8FMEA 编号FMEA 版本号RPN2等级措施结果共 4 页现行过程责任目标/完成日期建议措施过程潜在失效模式潜在的失效后果严重度S总成分总成零件零件名称/零件号/工序名称设计/过程责任部门编制电话号码制造部产品编号:最初编制日期FMEA 最新更改日期CFT小组成员:控制预防发生度O控制探测探测度D采取的措施S要求潜在的失效原因/机理关键日期:(要求PFMEA编制完成日及预计生产开始日期)PFMEA编制预定完成日: 预计生产开始日:8FMEA 编号FMEA 版本号RPN2等级措施结果共 4 页现行过程责任目标/完成日期建议措施过程潜在失效模式潜在的失效后果严重度S总成分总成零件零件名称/零件号/工序名称设计/过程责任部门编制电话号码制造部产品编号:最初编制日期FMEA 最新更改日期CFT小组成员:控制预防发生度O控制探测探测度D采取的措施S要求潜在的失效原因/机理关键日期:(要求PFMEA编制完成日及预计生产开始日期)PFMEA编制预定完成日: 预计生产开始日:8FMEA 编号FMEA 版本号RPN2等级措施结果共 4 页现行过程责任目标/完成日期建议措施过程潜在失效模式潜在的失效后果严重度S总成分总成零件不合格品进入公司做成抽样标准,根据标准零件名称/零件号/工序名称设计/过程责任部门编制电话号码制造部产品编号:最初编制日期FMEA 最新更改日期CFT小组成员:控制预防发生度O控制探测探测度D采取的措施S要求潜在的失效原因/机理关键日期:(要求PFMEA编制完成日及预计生产开始日期)PFMEA编制预定完成日: 预计生产开始日:8FMEA 编号FMEA 版本号RPN2等级措施结果共 4 页现行过程责任目标/完成日期建议措施过程潜在失效模式潜在的失效后果严重度S总成分总成零件。
注塑成型PFMEA分析范例

4
96
2 校准成绩书判定
2 24
2
《成型条件表》每班 次点检
4
48
1/8
总成 零件名称/零件号/工序名称 注塑产品 产品编号:
CFT小组成员:
分总成
潜在的失效模式及后果分析PFMEA
零件
设计/过程责任部门
制造部
关键日期:(要求PFMEA编制完成日及预计生产开始日期)
PFMEA编制预定完成日:
预计生产开始日:8
2 检验记录表班长确认 4 56
漏判
不合格品进入公司 影响产品质量
7
检验员能力不够
对检验员岗前进行培训, 并进行能力考核
2
4 56
按照检验规定进 行抽样,并正确 误判
判定来料品质
合格品判为不合格, 导致不能及时投入生 6 产影响产品纳期
7
原材料不符合 要求
顾客不满意
9
2、生产领料
根据出料单正确 原材料出库错 产品特性不能满足顾
度级
机理
S
控制预防
发
探
生 度
控制探测
测 度
O
D
5、料把修理
胶口修理过高 或修伤 对料把进行修理
胶口漏修
影响顾客装配
影响顾客装配 顾客抱怨
6
作业员修理方法 按照产品《作业指导书》
不正确
作业
7
PQC巡检、操作员 100%检验
2
6
作业员操作方法 按照产品《作业指导书》
不正确
作业
7
PQC巡检、操作员 100%检验
总成 零件名称/零件号/工序名称 注塑产品 产品编号:
CFT小组成员:
分总成
汽车塑料部件成型PFMEA分析范例

A
B
C
Responsibility Recommended & Target Action's)建议的措 Completion 施 Date责任&目标 完成日期
Actions Taken方案
10.Receiving Raw Material , Requirements paint 原材料,涂料的接收 1.Raw material & Batch No. as per PO 接收的材料,批号与定单一致 10 a Raw Material received 原材料的接收 2. Correct packing and Labeling 正确的包装与标签 Wrong Material supplied against Invoice. 供应商发错料 Not able to plan for production. 无法按计划生产 8 Supplier not aware of specification & grade 供应商未分清材料与等级 2 Standard packing is provided to supplier 提供包装规范 Material specification & Grade is provided on PO 订单上注明材料规范与等 级 Visual inspection 目测检查 7 112
7
Transit damage 运输损坏
2Байду номын сангаас
Visual inspection / qty cross check on weigh balance 目视检查/称重检查 Material specification & Grade is provided on PO 订单上注明材料规范与等 级 Visual inspection 目测检查
塑胶行业PFMEA案例
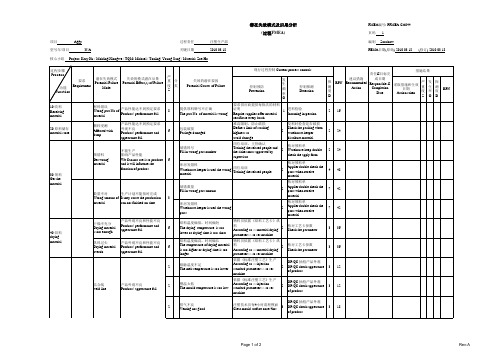
Aggy
过程责任
注塑生产部
型号年/项目
N/A
关键日期
2010.03.18
核心小组 Project: Kary Xu / Molding:Xiongwe / TQM: Michael / Tooling: Young Jiang / Material: Zoe Hu
潜在失效模式及后果分析 (过程FMEA)
Incoming inspection
certificate every batch
2 16
包装破损 Package damaged
堆高限制,防止破损 Define a limit of stacking highness to avoid damage
发料时检查是否破损
2
Check the packing when warehouse keeper
can not finished on time
干燥不充分 Drying material is not enough
产品外观不良和性能不良 Products' performance and appearance fail
6
烘料过头
产品外观不良和性能不良
Drying material Products' performance and 6
□ 注塑工艺原因 8 ◇ Caused by moulding parameter
setting
influence assembly
□ 原料变化原因 8 ◇ Caused by raw material
试模人员试模时发现问题,解 IPQC每4小时检查1shot
决问题 Solve problem on time once
PFMEA 模板参考

Delivery Delay 不能按期交貨
7
Inaccuracy of Measurement
Equipment
1
儀器精度不够
Incorrect Measurement Method 測量點錯誤
2
Poor Workmanship
未對樣板,圖紙
2
Poor Workmanship 未按貨品原規劃區域進行擺 2 放
Maintenance/Material
Controller Instruction
4
24
每月乾燥機检點/加料员
指引
Temp., Time,
Poor Workmanship 用電腦操作時,輸入錯誤,打錯 5 來料標識
Warehouse Working
Instruction
按<<膠料倉工作指引>>執 2
60
行
Material cannot be found- No Material for Produciton 7 找不到料生產,延 誤交期
Sev 嚴重 性 (S)
Clas Potential s Cause(s)/Cause(s)
分类 /Mechanism(s)of Failure 潛在的失效原因
Occur 可能性 (O)
Current Process Controls Prevention 預防方法
Current Process Control Detection 當前檢測控制方法
Instruction
按<<膠料倉工作指引>>執 5
30
行
Warehouse Working
Instruction
注塑成型PFMEA范例
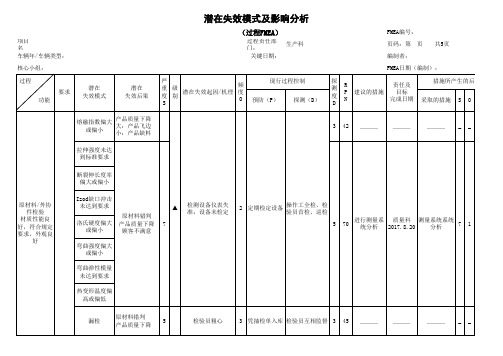
包装
6
产品变形、表 面擦毛
产品性能、外观 质量下降,顾客
不满意
6
纸箱偏大或偏小
4
纸箱进货检验
操作工自检,检 验员巡检
2
48
___
产品无内包装
3
作业指导书规 操作工自检,检
定
验员巡检
2
36
___
___ ___
___ _ _ ___ _ _
半成品入库贮 存
打孔 孔位准确到位
打孔 孔位准确到位
产品变形
产品性能下降, 顾客不满意
注塑成型
产品表面无不 良缺陷,注塑
尺寸精确
产品质量下降:
●表面油漆附着 5
力下降,漆面经
过长时间后脱
产品表面银丝
落,使顾客对外 观不满意
●涂装后产品表 面容易产生裂
5
纹,外观质量使
顾客不满意
时间计电器失准, 导致材料干燥时间 不够
3
计电器定期校 操作工自检,检
准
验员首检、巡检
3
45
___
___
温度表失准,导致 干燥温度过高或过 低
2
24
___
___
___ _ _
涂装工艺不对
3
制定涂装工艺 操作工自检,检
卡
验员巡检
4
48
___
___
___ _ _
涂装
产品表面无划 伤、颗粒、发 花等不良现象 油漆附着力符 合海南马自达
6
孔位偏移 四周飞边
产品装配不良, 使顾客不满意
5
外观质量下降, 使顾客对外观不 4
满意
堆放层数过高 夹具松动 电钻迟钝
注塑PFMEA实例

XXX High Tech Plastic(Suzhou)Co.,LtdXXX注塑(苏州)有限公司潜在过程失效模式及后果分析(过程FMEA)Potential Process Failure Modes and Effects Analysis(PFMEA)FMEA编号(FMEA No.): 项目名称Item Name:产品型号Product Type:核心小组Core Team: FMEA-001过程责任部门ResponsibleDepartment:关键日期Key date:Production, QA编制者/日期Prepartion/Date确认者/日期Approved/DatePage 1 of 3 Pages过程功能Process function要求Requirements1. IQC潜在失效模式PotentialFailureModes潜在失效后果Potential EffectofFailure严重度S级别Class(★,Δ,o)潜在失效起因/机理Origin/MechanismofPotential Failure频度O现行预防过程控制现行探测过程控制探测度D22222RPN1614818建议措施RecommendedActionsReview andconfirm IQCinstruction责任和目标完成日期Responsibility& TargetDate措施执行结果Excutive Results ofActions探测度D222RPN1614采取的措施 ActionsTakenIQC instructionIQC instructionIQC instruction严重度S874频度O111Amela Lu,WW26页码Page:2. Store3.1 Predry 3.2 Moulding Raw plasticmaterialincorrectPacking tray:not ESDmaterialRaw materialhandling notproperlyNot dryenoughImaging lensDia.,Dim 1: 5.78±0.03 out ofspec.Influence opticalfunctionInfluence opticalfunctionInfluence opticalfunctionContaminate theproductsInfluence opticalfunctionBuble inside,Yellow product,Influence assy8743563ΔΔΔoΔooShipment wrongMaterial quality notgoodPackage damagedduring shipmentStore for long time,or made of wrongmaterialMaterial mixedTime or temp not rightWrong insert1113341MaterialIQCMaterialIQCMaterialIQCMaterialIQCMateriallabellingtime/tempcontrolOrderstartreleaseplanChecklablingCheckCOCCheckpackingChecksurfaceresistanceChecklablingsupervisordoublecheck +QC auditDim check423966ReviewpersonnelinstructionsReviewpersonnelinstructionsPM mouldProductionsupervisor,WW26Productionsupervisor,WW26Productionsupervisor,WW26IQC instructionReview personnelinstructionsReview PersonnelinstructionsReview PM mouldpersonnelinstruction,incominginspection opticalinserts3563333122428183726过程功能Process function要求Requirements3.2 Moulding潜在失效模式PotentialFailureModesImaging lensthickness,Dim 2: 1.93±0.03 mm outof spec.Total heightDim.4: 5.05±0.05, out ofspec.Distance, Dim5: 14.54± 0.03out of spec.Distance,Dim.6: 7.86±0.03 out ofspec.Distance,Dim.9: 1.60±0.05 out ofspec.Overall width,Dim 12: 39.5±0.1 out ofspec.Diameter,Dim13: 42±0.1mm out ofspecThickness,Dim 16: 6±0.1mm out ofspec.潜在失效后果Potential EffectofFailurePoor imagequality,Influence TOPInfluenceimagingfunctionImpactillumination,spot positionImpactillumination,spot positionImpact TOPInfluenceproductassembly严重度S766676级别Class(★,Δ,o)★★ΔΔ★潜在失效起因/机理Origin/MechanismofPotential FailureIncorrect stackheight after PMmouldMolding processor mold dim. Ormould temp.Molding processor mold dim. Ormould temp.Molding processor mold dim. Ormould temp.Molding processor mold dim. Ormould temp.Mould dimensionwrongMould dimensionwrongMould dimensionwrong频度O155511现行预防过程控制Orderstartreleaseplan+IPQCIPQCOrderstartreleaseplanOrderstartreleaseplanIPQC现行探测过程控制Dim checkDim checkDim checkDim checkDim 2, 3, 4arecontrolledduringprocessDim check探测度D322232RPN2166621建议措施RecommendedActionsPM mouldPM mould,checkmouldingparameterregularlyPM mould,checkmouldingparameterregularlyPM mould,QC checkmouldingparameterregularlyPM mould,checkmouldingparameterregularlyPM mouldPM mould责任和目标完成日期Responsibility& TargetDateXu ZhenglinXu Zhenglin/AmelaXu Zhenglin/AmelaXu Zhenglin/AmelaXu Zhenglin/Amela措施执行结果Excutive Results ofActions采取的措施 ActionsTakenReview PMmouldpersonnelinstructionReview PM mouldpersonnelinstruction, checkmouldingparameterregularlyReview PM mouldpersonnelinstruction, checkmouldingparameterregularlyReview PM mouldpersonnelinstruction, checkmouldingparameterregularlyReview PM mouldpersonnelinstruction, checkmouldingparameterregularlyReview PMmouldpersonnelinstructionReview PM严重度S766676频度O155511探测度D322232RPN2166621Thickness, Dim 17: 10.36± 0.1 out of spec. Distance, Dim18:3.51±0.03mm out of spec. Thickness,Dim 19:1.3±0.1 out of spec. InfluenceproductassemblyInfluenceproductassemblyConflict with clipon productImpactillumination,spot position66666★★★★Δ★Mould dimensionwrongMould dimensionwrongMould dimensionwrong11151OrderstartreleaseplanOrderstartreleaseplanOrderstartreleaseplanOrderstartreleaseplanOrderstartreleaseplanOrderstartreleaseplanDim checkDim checkDim checkDim checkDim check2222212121212612PM mouldPM mouldPM mouldPM mouldXu ZhenglinXu ZhenglinXu ZhenglinXu ZhenglinXu ZhenglinFangGuozhu /XuZhenglinmouldpersonnelinstructionReview PMmouldpersonnelinstructionReview PMmouldpersonnelinstructionReview PMmouldpersonnelinstruction66661115612222212121212612过程功能Process function要求Requirements3.2 Moulding潜在失效模式PotentialFailureModesImaging lensshape changeImaging lenstransmittancetoo lowImaging lensoptical axisshift versusmech. AxisBiginclusions inlensFlowlines,defects etc.Warpage ofproductTOPContamination潜在失效后果Potential EffectofFailurePoor imagequality, TOP outof spec.Reduced imagequalityPoor imagequalityReduced imagequalityReduced imagequalityInfluenceimagingfunctionInfluenceimagingfunctionReduced image严重度S5555566级别Class(★,Δ,o)ΔooΔΔ★★潜在失效起因/机理Origin/MechanismofPotential FailureMouldingprocessparameter,ormould designmarginallyCavity cleanlinessWrong mouldImpurities orburned materialduringmouldingMoulding processparameterMouldingprocessparameter, orwrong mold dimMouldingprocessparameter, orwrong mold dimParticle generationduring packing频度O11134652现行预防过程控制IPQCIPQCIPQCIPQCIPQCIPQC现行探测过程控制TOPmeasurementMeasureimageresolutionVisualinspection100%Visualinspection100%WapagemeasurementTOPmeasurementVisual探测度D3322233RPN1515134189建议措施RecommendedActionsCheckmouldingparameterregularlyPM mouldPM mouldMouldingprocessoptimizationMouldingprocessoptimizationMouldingprocessoptimizationPM mould,MouldingprocessoptimizationHandling withfinger cots,ionized aircleaning,ESD packingmaterial责任和目标完成日期Responsibility& TargetDateAmela LuXu ZhenglinXu ZhenglinFangGuozhu /XuZhenglinFangGuozhu /XuZhenglinFangGuozhu /XuZhenglinFangGuozhu /Xu措施执行结果Excutive Results ofActions采取的措施Actions TakenCheck mouldingparameter regularlyPM mouldpersonnelinstructionPM mouldpersonnelinstructionPM mouldpersonnelinstruction, setprocess window严重度S5555566频度O1113465探测度D3322233RPN15151341894 Packing quality 5ΔIPQCinspection100%22ZhenglinProductionsupervisorPersonnel instruction 52 22Sheet-2002-0Kept by: DCC Keep period: production requirement + 1 year。
注塑成型PFMEA完整版
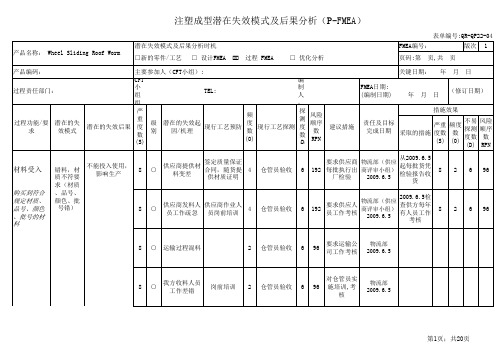
注塑成型潜在失效模式及后果分析(P-FMEA)
表单编号:QR-QP22-04
客户要求,造成退
客户要求,造成退
增加,成本增
风险顺序数(RPN)=(S)*(O)*(D) RPN值超过100需做改善行动. SC表示客户指定特殊特性. T 表示公司自己识别的特性
风险顺序数(RPN)=(S)*(O)*(D)
严重度数(S) 级别 频度数(O) 不易探测度数 (D) 无警告的严重危害 10 严重 ! 很 高 失效率≥1/10 Cpk〈0.33 10 绝对不肯定 10 有警告的严重危害 9 关键 ● 很 高 失效率 1/20 Cpk≥0.33 9 很微小 9 很 高 8 重要 ○ 高 失效率 1/50 Cpk≥0.51 8 微小 8 高 7 一般 --- 高 失效率 1/100 Cpk≥0.67 7 很小 7 中 等 6 客户指定特殊特性, 中 等 失效率 1/500 Cpk≥0.83 6 小 6 低 5 用客户的符号 中 等 失效率 1/2000 Cpk≥1.00 5 中等 5 很 低 4 中 等 失效率 1/10000 Cpk≥1.17 4 中上 4 轻 微 3 低 失效率 1/100000 CPK≥1.33 3 高 3 很 轻 微 2 很 低 失效率 1/1000000 Cpk≥1.50 2 很高 2 FMEA小组成员签署:。
PFMEA 案例
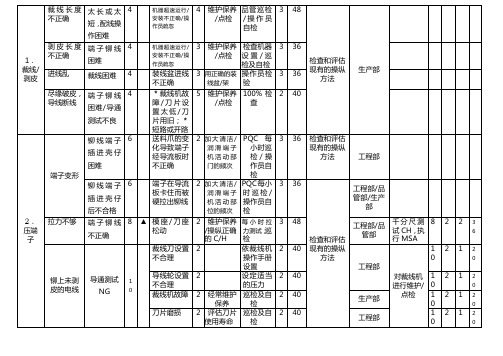
36
检查和评估现有的操纵方法
工程部
铆线端子插进壳仔后不合格
6
端子在导流板卡住而被硬拉出铆线
2
加大清洁/润滑端子机活动部位的频次
PQC每小时巡检/操作员自检
3
36
检查和评估现有的操纵方法
工程部/品管部/生产部
拉力不够
端子铆线不正确
8
▲
模座/刀座松动
2
维护保养/操纵正确的C/H
每小时拉力测试;巡检
3
48
2
36
检查和评估现有的操纵方法
生产部
6
机器设置咨询题
2
定期维护保养
依照注胶机操作讲明
2
24
工程部
6﹑
缠胶布
胶布缠错位置或胶布尺寸不正确
线束装进车辆时困难或安装失败/妨碍电线包扎尺寸
5
操作员不了解图面要求的缠胶布位置
2
培训操作人员并重点标注图面要求
依照图面规定操作/100%外看检验
3
30
检查和评估现有的操纵方法
5
操作员作业疏忽
2
培训作业员
作业员自检/FQC全检
2
20
生产部
11﹑
产品包装
包错纸箱
发错产品到客户;
客户投诉
6
操作员作业疏忽
2
培训作业员
严格依照作业指导书/操作员自检/QA100%检验
2
24
检查和评估现有的操纵方法
生产部/品管部
贴错LABLE
6
2
2
24
包错数量
6
2
2
24
注胶壳仔粘在一起
粘在一起分不开
- 1、下载文档前请自行甄别文档内容的完整性,平台不提供额外的编辑、内容补充、找答案等附加服务。
- 2、"仅部分预览"的文档,不可在线预览部分如存在完整性等问题,可反馈申请退款(可完整预览的文档不适用该条件!)。
- 3、如文档侵犯您的权益,请联系客服反馈,我们会尽快为您处理(人工客服工作时间:9:00-18:30)。
设计/过程责任部门 制造部 关键日期:(要求PFMEA编制完成日及预计生产开始日期) PFMEA编制预定完成日: 预计生产开始日:
严 重 度 S 6
现行过程
等 级 潜在的失效原因/机理 控制预防 发 生 度 O 7
包装箱规格使 造成产品擦伤,导致顾客投诉 用错误
未依据《作业指导书》的包 装要求执行
依据《作业指导书》实施
现行过程
等 级 潜在的失效原因/机理 控制预防 发 生 度 O 2
Байду номын сангаас过程
要求
潜在失效模式
潜在的失效后果
少检验 根据出货检验标准正 漏判 确判定是否可以出货 误判
不合格品进入公司 影响产品质量 不合格品流出公司 顾客投诉 合格品判为不合格, 影响纳期 顾客抱怨
7
抽样数量错误 检验员能力不够
做成抽样标准,根据标准要求数量抽 样 对检验员岗前进行培训,并进行能力 考核 对检验员岗前进行抽检方法培训,并 进行能力考核
现行过程
等 级 潜在的失效原因/机理 控制预防 发 生 度 O 3 模温监控、 成型工艺监控、 3 3 做成生产工艺卡, 根据工艺卡调机 4 3 3 根据生产工艺卡, 模温监控、 成型工艺监控 4 7 3 根据生产工艺卡, 成型工艺监控 根据生产工艺卡, 成型工艺监控 模具定期保养、维护 开机前清洗模具 按照产品《作业指导书》作业 3 3 4 4 3 7
样品 预生产 量产
零件名称/零件号/工序名称 产品编号: CFT小组成员:
严 重 度 S 6 6
设计/过程责任部门 制造部 关键日期:(要求PFMEA编制完成日及预计生产开始日期) PFMEA编制预定完成日: 预计生产开始日:
现行过程
等 级 潜在的失效原因/机理 控制预防 发 生 度 O 7 7
过程
8
领料员未依据生产任务通知 单进行实物确认 烘干箱温度不准确
对领料员、仓库管理员进行岗前教育
2
做成原材料干燥指导书
4
3、注塑烘料
烘干原材料,生产出 颜色、外观、尺寸、 性能合格的产品
产品外观不合格 烘干温度偏差 顾客抱怨
6 测温仪故障 测温仪定期外部校准 2
烘干时间偏差
产品外观不合格 顾客抱怨
6
烘干时间设定错误
6
对检查员进行教育,并考核
2
将不合格品判定为合格品,造成不良 品出货,导致顾客投诉
6
检验员能力不够
对检查员进行教育,并考核
2
产品包装数量 顾客抱怨 不正确 产品标签标识 不符合顾客要 顾客抱怨 求
4 5
作业员工作失误 作业员工作失误 包装材料质量问题
对检查员进行教育,并考核 做成《作业指导书》,根据规程作业 IQC来料检验
潜在失效模式及后果分析 Failure Mode and Effect Analysis (过程FMEA)
样品 预生产 量产
零件名称/零件号/工序名称 产品编号: CFT小组成员:
严 重 度 S
设计/过程责任部门 制造部 关键日期:(要求PFMEA编制完成日及预计生产开始日期) PFMEA编制预定完成日: 预计生产开始日:
3 2
7、包装
依据产品《操作/包装 封箱不密实 指示》,对产品进行 包装封箱、打包,粘 贴标签
周转过程中包装出现破损,造成产品 伤、污影响产品质量
5
封箱方式不正确 依据产品《作业指导书》实施 作业员漏封 作业员一次填写多种产品标 签 作业员方法不正确 作业员一次写一种标签,依据产品《 作业指导书》 依据《作业指导书》实施
排气不良 6 模具表面温度过高 注射位置设置不当 注射压力小 8
*
注射速度慢 保压过高
脱模不良
5 模具表面光洁度不够 6 4 模具表面有油 操作工操作不当
产品外观不合格 顾客抱怨 产品产品碰伤 产品外观不合格 、划伤 顾客抱怨 产品表面油污
2/10
潜在失效模式及后果分析 Failure Mode and Effect Analysis (过程FMEA)
O
D
PQC巡检、操作员100%检验 PQC巡检、操作员100%检验
84 84
6
72
6 PQC巡检 、FQC、操作员100%自 检
72
3 3
36 30 45 45 45 98 90
入库前包装检验
3 3
入库前包装检验 3 入库前包装检验 入库前包装检验 2 6
8/10
共 编制
页
FMEA 编号 FMEA 版本号 电话号码 FMEA 最新更改日期
现行过程
等 级 潜在的失效原因/机理 控制预防 发 生 度 O 2
过程
要求
潜在失效模式
潜在的失效后果
1、来料检验
少检验 漏判
不合格品进入公司 影响产品质量 不合格品进入公司 影响产品质量 合格品判为不合格,导致不能及时投 入生产影响产品纳期
7
抽样数量错误 检验员能力不够
做成抽样标准,根据标准要求数量抽 样 对检验员岗前进行培训,并进行能力 考核 对检验员岗前进行抽检方法培训,并 进行能力考核
7
2
按照检验规定进行抽 样,并正确判定来料 误判 品质
6
检验员抽样过于集中
2
7 原材料不符合 顾客不满意 要求
料粒色泽不均匀,有杂质
根据颜色样本进行检验 产品原材料属于顾客提供,根据供应 商提供材料保证书、检测报告判定
2
9
ROHS测试不合格
2
2、生产领料
根据出料单正确出料
原材料出库错 产品特性不能满足顾客要求,顾客投 误 诉
行过程
控制探测 探 测 度 D 4 开机设定确认, 首件检查、PQC巡检、自检 4 4 开机设定确认, 检验员首检、末检,对产品关键装 配尺寸进行检查 3 3 2 开机设定确认, 首件检查、PQC巡检、自检 2 2 3 4 首件检查、PQC巡检、自检 4 首件检查、PQC巡检、自检 首件检查、PQC巡检、自检 首件检查 自检 4 3 2 3 96 80 80 36 84 R P N 建议措施 责任目标/完成 采取的 日期 措施 S
最初编制日期
产开始日:
行过程
控制探测 探 测 度 D 2 R P N 建议措施 责任目标/完成 采取的 日期 措施 S
措施结果 R P N
O
D
入库前包装检验
84
9/10
共 编制
页
FMEA 编号 FMEA 版本号 电话号码 FMEA 最新更改日期
最初编制日期
产开始日:
行过程
控制探测 探 测 度 D 4 R P N 建议措施 责任目标/完成 采取的 日期 措施 S
4/10
潜在失效模式及后果分析 Failure Mode and Effect Analysis (过程FMEA)
样品 预生产 量产
零件名称/零件号/工序名称 产品编号: CFT小组成员:
严 重 度 S
设计/过程责任部门 制造部 关键日期:(要求PFMEA编制完成日及预计生产开始日期) PFMEA编制预定完成日: 预计生产开始日:
措施结果 R P N
O
D
72 72 72 84 63 72 48 84 54 96
7/10
共 编制
页
FMEA 编号 FMEA 版本号 电话号码 FMEA 最新更改日期
最初编制日期
产开始日:
行过程
控制探测 探 测 度 D 2 2 R P N 建议措施 责任目标/完成 采取的 日期 措施 S
措施结果 R P N
过程
要求
潜在失效模式
潜在的失效后果
注射压力小 产品表面缩水 产品外观不合格 顾客抱怨 6 冷却时间短 模具温度高 产品尺寸偏大 与相关零件不匹配, 或偏小 使顾客不满意
7
◇
注射压力过低或过高 冷却时间过长或过短 注塑速度快
4、注塑成型
产品外观不合格 通过注塑机和模具成 产品表面烧焦 顾客抱怨 型生产出颜色、外观 、尺寸、性能合格的 产品 产品缺胶 影响顾客装配 顾客抱怨 产品变形、拉坏 影响外观
3
标签与实物不 顾客抱怨 符 包装箱或产品 顾客抱怨 内异物
7 5
7 3
3/10
潜在失效模式及后果分析 Failure Mode and Effect Analysis (过程FMEA)
样品 预生产 量产
零件名称/零件号/工序名称 产品编号:
依据产品《操作/包装 CFT 小组成员: 指示》,对产品进行 7 、包装 包装封箱、打包,粘 贴标签 过程 要求 潜在失效模式 潜在的失效后果
投料前确认、记录 验证确认供应商提供的材料证明或 第三方提供的/RoHS 测试报告
4
56
6
108
投料前确认、记录
2
32
《成型条件表》每班次点检
4
96
校准成绩书判定
2
24
《成型条件表》每班次点检
4
48
6/10
共 编制
页
FMEA 编号 FMEA 版本号 电话号码 FMEA 最新更改日期
最初编制日期
产开始日:
7
5/10
共 编制
页
FMEA 编号 FMEA 版本号 电话号码 FMEA 最新更改日期
最初编制日期
产开始日:
行过程
控制探测 探 测 度 D 4 R P N 建议措施 责任目标/完成 采取的 日期 措施 S
措施结果 R P N
O
D
检验记录表班长确认 检验记录表班长确认
56
4
56
检验记录表班长确认
4
48
8、OQC检验
7
2
6
检验员能力不够