金属加工的润滑工艺
MQL 加工技术(微量润滑加工技术)
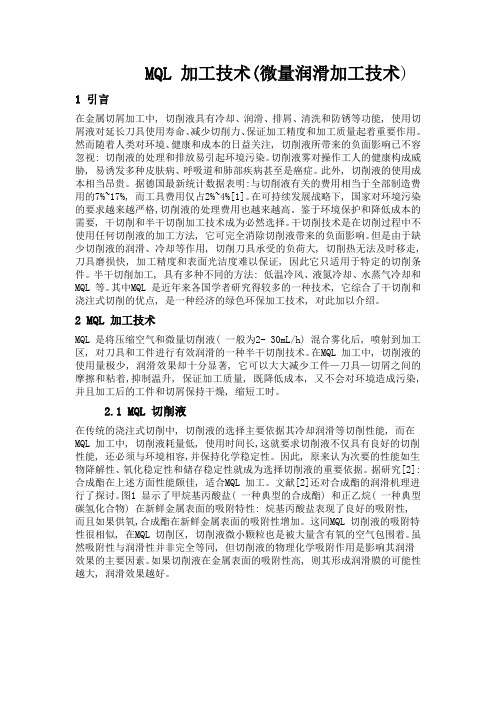
MQL 加工技术(微量润滑加工技术) 1 引言在金属切屑加工中, 切削液具有冷却、润滑、排屑、清洗和防锈等功能, 使用切屑液对延长刀具使用寿命、减少切削力、保证加工精度和加工质量起着重要作用。
然而随着人类对环境、健康和成本的日益关注, 切削液所带来的负面影响已不容忽视: 切削液的处理和排放易引起环境污染。
切削液雾对操作工人的健康构成威胁, 易诱发多种皮肤病、呼吸道和肺部疾病甚至是癌症。
此外, 切削液的使用成本相当昂贵。
据德国最新统计数据表明:与切削液有关的费用相当于全部制造费用的7%~17%, 而工具费用仅占2%~4%[1]。
在可持续发展战略下, 国家对环境污染的要求越来越严格,切削液的处理费用也越来越高。
鉴于环境保护和降低成本的需要, 干切削和半干切削加工技术成为必然选择。
干切削技术是在切削过程中不使用任何切削液的加工方法, 它可完全消除切削液带来的负面影响。
但是由于缺少切削液的润滑、冷却等作用, 切削刀具承受的负荷大, 切削热无法及时移走, 刀具磨损快, 加工精度和表面光洁度难以保证, 因此它只适用于特定的切削条件。
半干切削加工, 具有多种不同的方法: 低温冷风、液氮冷却、水蒸气冷却和MQL 等。
其中MQL 是近年来各国学者研究得较多的一种技术, 它综合了干切削和浇注式切削的优点, 是一种经济的绿色环保加工技术, 对此加以介绍。
2 MQL 加工技术MQL 是将压缩空气和微量切削液( 一般为2- 30mL/h) 混合雾化后, 喷射到加工区, 对刀具和工件进行有效润滑的一种半干切削技术。
在MQL 加工中, 切削液的使用量极少, 润滑效果却十分显著, 它可以大大减少工件—刀具—切屑之间的摩擦和粘着,抑制温升, 保证加工质量, 既降低成本, 又不会对环境造成污染,并且加工后的工件和切屑保持干燥, 缩短工时。
2.1 MQL 切削液在传统的浇注式切削中, 切削液的选择主要依据其冷却润滑等切削性能, 而在MQL 加工中, 切削液耗量低, 使用时间长,这就要求切削液不仅具有良好的切削性能, 还必须与环境相容,并保持化学稳定性。
浅谈金属压力加工中的摩擦与润滑
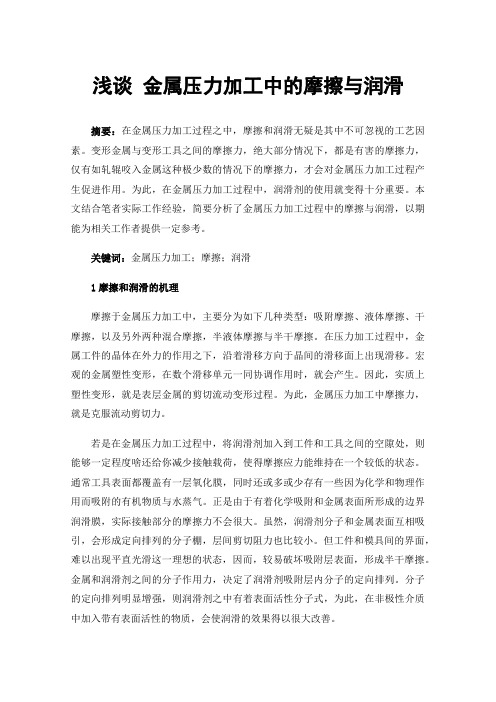
浅谈金属压力加工中的摩擦与润滑摘要:在金属压力加工过程之中,摩擦和润滑无疑是其中不可忽视的工艺因素。
变形金属与变形工具之间的摩擦力,绝大部分情况下,都是有害的摩擦力,仅有如轧辊咬入金属这种极少数的情况下的摩擦力,才会对金属压力加工过程产生促进作用。
为此,在金属压力加工过程中,润滑剂的使用就变得十分重要。
本文结合笔者实际工作经验,简要分析了金属压力加工过程中的摩擦与润滑,以期能为相关工作者提供一定参考。
关键词:金属压力加工;摩擦;润滑1摩擦和润滑的机理摩擦于金属压力加工中,主要分为如下几种类型:吸附摩擦、液体摩擦、干摩擦,以及另外两种混合摩擦,半液体摩擦与半干摩擦。
在压力加工过程中,金属工件的晶体在外力的作用之下,沿着滑移方向于晶间的滑移面上出现滑移。
宏观的金属塑性变形,在数个滑移单元一同协调作用时,就会产生。
因此,实质上塑性变形,就是表层金属的剪切流动变形过程。
为此,金属压力加工中摩擦力,就是克服流动剪切力。
若是在金属压力加工过程中,将润滑剂加入到工件和工具之间的空隙处,则能够一定程度啥还给你减少接触载荷,使得摩擦应力能维持在一个较低的状态。
通常工具表面都覆盖有一层氧化膜,同时还或多或少存有一些因为化学和物理作用而吸附的有机物质与水蒸气。
正是由于有着化学吸附和金属表面所形成的边界润滑膜,实际接触部分的摩擦力不会很大。
虽然,润滑剂分子和金属表面互相吸引,会形成定向排列的分子棚,层间剪切阻力也比较小。
但工件和模具间的界面,难以出现平直光滑这一理想的状态,因而,较易破坏吸附层表面,形成半干摩擦。
金属和润滑剂之间的分子作用力,决定了润滑剂吸附层内分子的定向排列。
分子的定向排列明显增强,则润滑剂之中有着表面活性分子式,为此,在非极性介质中加入带有表面活性的物质,会使润滑的效果得以很大改善。
2金属压力加工中摩擦的特点和影响因素2.1摩擦的特点(1)压力高且接触面积大。
金属压力加工过程中的单位压力,通常是500兆帕。
切削液不得不知的基本知识

切削液不得不知的基本知识金属加工液在金属加工过程中,为了降低切削时的切削力,及时带走切削区内产生的热量以降低切削温度,提高刀具耐用度,从而提高生产效率,改善工件表面粗糙度,保证工件加工精度,达到最佳的经济效果,通常使用金属加工液。
金属加工液在金属加工过程中具有润滑、冷却、清洗、防锈等作用;其中核心作用是:一方面通过冷却作用降低加工过程中的变形热,另一方面通过润滑作用来减少金属加工过程中的磨擦热,从而来提高金属加工质量,延长刀具的使用寿命等。
1、冷却性能:冷却作用是通过乳化液和因切削而发热的刀具、切屑和工件间的对流和汽化作用把切屑热从固体(刀具、工件)处带走,从而有效地降低切削温度,减少工件和刀具的热变形,保持刀具硬度提高加工精度和刀具耐用度。
2、润滑性能:润滑作用就是其减少前刀面与切屑、后刀面与已加工表面间的摩擦形成部分润滑膜的作用,以防止刀具与切屑或工件间的粘着,所以良好的润滑可以减少功能消耗、刀具磨损和良好的表面光洁度。
3、清洗性能:在金属加工过程中,切屑、铁粉、磨屑、油污、沙粒等常常粘附在工件、刀具或砂轮表面及缝隙中,同时沾污机床和工件,不易清洗,使刀具或砂轮切屑刃口变钝,影响切削效果。
所以要求乳化液有良好的清洗作用。
乳化液的清洗性能就是指乳化液防止这些细颗粒粘结和利用液流的机械冲洗作用将其冲走的能力。
4、防锈性能:在金属加工过程中,工件要与环境介质如水、氧、硫、二氧化硫、二氧化碳、硫化氢、氯离子、游离酸碱和乳化液分解或氧化变质所产生的油泥等腐蚀性介质接触而受到腐蚀,机床部件与乳化液接触的部分会产生腐蚀。
因此要求乳化液有一定的防锈能力。
金属加工液除了应具有良好的冷却性、润滑性、清洗性、防锈性外,还应具有防腐蚀性、抗菌性、防垢性、抗泡性、热稳定性、无毒、无害、无刺激性气味、不污染环境、使用方便等条件。
金属加工液可分为纯油性切削液和水溶性切削液两种。
金属加工液应具有如下作用:1、改善加工表面,提高表面光洁度;2、提高加工件尺寸的精密度;3、延长切削工具的寿命;4、随时排除切削屑末,洗净加工面;5、防止加工件腐蚀或生锈;6、提高切削加工效率;7、随时冷却加工件表面和加工刀具。
金属压力加工中的摩擦与润滑
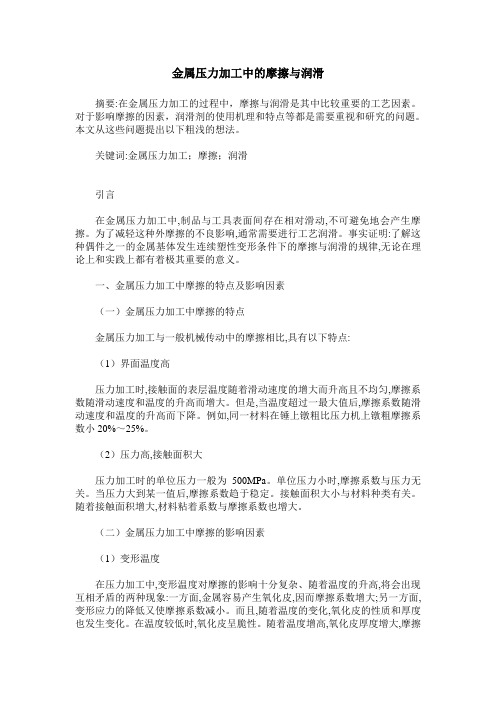
金属压力加工中的摩擦与润滑摘要:在金属压力加工的过程中,摩擦与润滑是其中比较重要的工艺因素。
对于影响摩擦的因素,润滑剂的使用机理和特点等都是需要重视和研究的问题。
本文从这些问题提出以下粗浅的想法。
关键词:金属压力加工;摩擦;润滑引言在金属压力加工中,制品与工具表面间存在相对滑动,不可避免地会产生摩擦。
为了减轻这种外摩擦的不良影响,通常需要进行工艺润滑。
事实证明:了解这种偶件之一的金属基体发生连续塑性变形条件下的摩擦与润滑的规律,无论在理论上和实践上都有着极其重要的意义。
一、金属压力加工中摩擦的特点及影响因素(一)金属压力加工中摩擦的特点金属压力加工与一般机械传动中的摩擦相比,具有以下特点:(1)界面温度高压力加工时,接触面的表层温度随着滑动速度的增大而升高且不均匀,摩擦系数随滑动速度和温度的升高而增大。
但是,当温度超过一最大值后,摩擦系数随滑动速度和温度的升高而下降。
例如,同一材料在锤上镦粗比压力机上镦粗摩擦系数小20%~25%。
(2)压力高,接触面积大压力加工时的单位压力一般为500MPa。
单位压力小时,摩擦系数与压力无关。
当压力大到某一值后,摩擦系数趋于稳定。
接触面积大小与材料种类有关。
随着接触面积增大,材料粘着系数与摩擦系数也增大。
(二)金属压力加工中摩擦的影响因素(1)变形温度在压力加工中,变形温度对摩擦的影响十分复杂、随着温度的升高,将会出现互相矛盾的两种现象:一方面,金属容易产生氧化皮,因而摩擦系数增大;另一方面,变形应力的降低又使摩擦系数减小。
而且,随着温度的变化,氧化皮的性质和厚度也发生变化。
在温度较低时,氧化皮呈脆性。
随着温度增高,氧化皮厚度增大,摩擦系数也增大。
达到一定温度时,氧化皮开始软化,摩擦系数达到峰值。
温度再升高时,氧化皮的塑性增大到一定限度,摩擦系数减小。
含碳量对摩擦的影响,主要在于氧化皮性质不同。
(2)变形速度在压力加工中,变形速度对摩擦系数的影响也很大。
变形速度增大时,摩擦系数降低。
钢冷轧工艺润滑及冷轧油相关知识
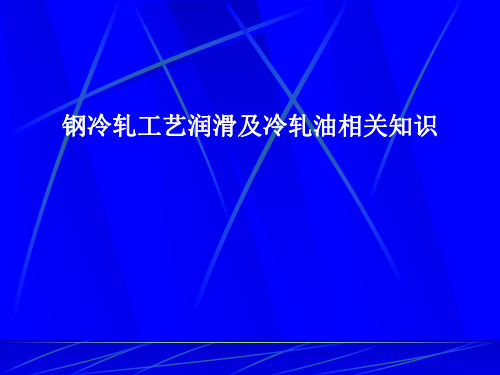
3、乳化液的热分离性
当乳化液喷射到轧辊或变形金属表面上时,由于 受热,乳化液的稳定状态被坏,分离出来的油吸附金 属表面上,形成润滑油膜,起防黏减摩作用。而水则 起冷却轧辊的作用。乳化液正是通过这种热分离性来 达到润滑冷却的目的。即冷轧乳化液的两大主要功能 为润滑和冷却。
乳化液的热分离性除了乳化液本身性质外,基础 油的黏度、添加剂、乳化液中油滴尺寸及分布,乳化 液的使用温度和时间都会影响乳化液的热分离性,进 而影响乳化液的使用效果。
镀锡钢板最早于14世纪在德国问世,首先是锻造方法,到18 世纪才改为轧制生产。1790年开始热轧,由于镀锡板需求增加, 促进了宽带冷轧机发展。但是,由于矿物油等润滑问题未解决, 使生产受到限制。由于轧制速度不断提高,变形量很大,因而迫 切要求同时解决轧辊的润滑与冷却问题,于是,出现了冷却性能 良好的乳化液润滑以代替纯油润滑。
亲油基端 亲油基端
油
乳化剂 油
搅拌
水 水
亲水基端
油 水
根据乳化液中分散相所带电荷性质,乳化液可分为:
(1) 阴离子型乳化剂。阴离子型乳化剂具有乳化效率高、 润滑性能好、清洗性和防锈性强以及破乳容易等特点, 同时也是目前使用较为广泛的轧制润滑乳化液。但是, 其对水质要求较高,易腐败变质,使用寿命短。
1.2、乳化剂
由于两种互不相溶的液相,如油和水混合时不能 形成稳定的平衡体系,故需加入表面活性剂,也即乳 化剂。乳化剂具有独特的分子结构,其分子一端为亲 油基,而分子的另一端为亲水基。这样,通过乳化剂 把油和水结合起来形成稳定的油水平衡体系。乳化剂 结构及乳化液形成过程示意图如下:
乳化剂结构及乳化液形成过程示意图
轧制示意图
2、轧制工艺润滑剂的基本功能 一种工艺润滑剂除了要满足其工艺要求外,往往还要求其实
第三章 切削加工润滑

因此,切削过程中三个变形区所产生的热量 除分别由切屑、工件、刀具和周围介质如空气传 出外,还应采用切削液将切削区的热量迅速带走。 切削液的冷却效果有两个方面:即通过润滑对切 削机理的影响所体现的冷却及直接冷却。 由于切削液的自身冷却能力,其直接冷却作 用不但可以降低切削温度,减少刀具磨损,延长 刀具寿命,而且还可以防止工件热膨胀,翘曲对 加工精度的影响,以及冷却已加工表面抑制热变 质层的产生。
冷却作用通常是指切削液将热量从它产生的地 方迅速带走的能力。在金属切削时,靠对流、汽化 吸收传出大量的热。切削液的冷却作用大小,取决 于热导率、比热容、汽化热、汽化速度、流量及流 速 ( 流速与粘度、压力有关 ) 等。通常水的热导率、 比热容,汽化热比油大,粘度比油小所以一般水的 溶液的冷却性能最好,油类较差,乳化液介于二者 之间,接近于水。
③改善加工面,降低工件表面粗糙度值;④随时 排除碎切屑,洗净加工面;⑤迅速均匀地冷却加工 的刀具、工件和机床有关部件;⑥防止工件和机 床腐蚀或生锈;⑦提高切削加工效率;⑧降低能 耗和生产成本。 切削液的基本功能:冷却、润滑、清洗、防锈。
二、冷却作用
切削热是由切削过程中金属变形和摩擦所消耗 的功转变而来。图3-1所示的三个变形区就是产生 切削热的热源:即被加工材料的弹、塑性变形所 消耗的功转变的热和刀具前刀面与切屑底层摩擦 所产生的热以及刀具后刀面与加工表面摩擦所产 生的热。 产生这些热量除去以辐射的形式散出去的部 分外,均用于加热刀具、切屑及加工表面,使之 温度升高:加剧了刀具的磨损、缩短了刀具寿命、 在已加工表面生成热变形。
矿物油在流体润滑状态下,有良好的润滑性 能,但不适用边界润滑。通常矿物油只作为切削 油的基础油,加入一定量的油性剂或极压剂,以 保证切削过程中边界润滑时有较低的摩擦系数和 磨损。 渗透性好的低粘度矿物油,除了用于黄铜、 易切削钢等的轻切削加工外,还可以用于轻合金 的研磨(抛光)、珩磨、和精加工。
金属拉丝油标准-概述说明以及解释
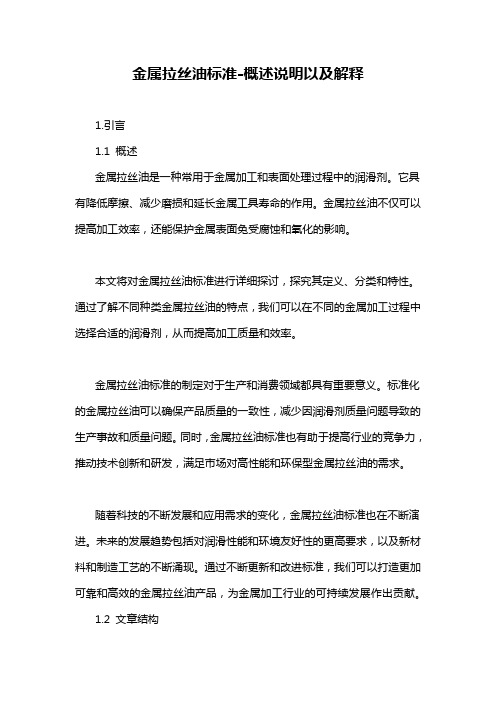
金属拉丝油标准-概述说明以及解释1.引言1.1 概述金属拉丝油是一种常用于金属加工和表面处理过程中的润滑剂。
它具有降低摩擦、减少磨损和延长金属工具寿命的作用。
金属拉丝油不仅可以提高加工效率,还能保护金属表面免受腐蚀和氧化的影响。
本文将对金属拉丝油标准进行详细探讨,探究其定义、分类和特性。
通过了解不同种类金属拉丝油的特点,我们可以在不同的金属加工过程中选择合适的润滑剂,从而提高加工质量和效率。
金属拉丝油标准的制定对于生产和消费领域都具有重要意义。
标准化的金属拉丝油可以确保产品质量的一致性,减少因润滑剂质量问题导致的生产事故和质量问题。
同时,金属拉丝油标准也有助于提高行业的竞争力,推动技术创新和研发,满足市场对高性能和环保型金属拉丝油的需求。
随着科技的不断发展和应用需求的变化,金属拉丝油标准也在不断演进。
未来的发展趋势包括对润滑性能和环境友好性的更高要求,以及新材料和制造工艺的不断涌现。
通过不断更新和改进标准,我们可以打造更加可靠和高效的金属拉丝油产品,为金属加工行业的可持续发展作出贡献。
1.2 文章结构文章结构部分的内容可以是:文章结构部分旨在简要介绍整篇文章的组织结构和各个章节的内容。
通过清晰的结构,读者可以更好地理解和掌握文章的主题和要点。
本文的结构分为引言、正文和结论三个部分。
引言部分主要包括概述、文章结构和目的三个子部分。
首先,概述部分将对金属拉丝油标准的背景和重要性进行简要介绍,引起读者的兴趣。
接下来,文章结构部分将详细描述本文的组织结构,包括引言、正文和结论三个主要部分,以及各个部分的内容和目的。
最后,目的部分将明确本文的写作目的和对读者的价值,使读者对文章有一个清晰的期待。
正文部分是本文的核心内容,其中包括金属拉丝油的定义和作用以及金属拉丝油的分类和特性两个主要部分。
在2.1节,将详细解释金属拉丝油的定义和作用,说明其在金属加工中的重要性和应用领域。
在2.2节,将对金属拉丝油进行分类和特性的介绍,探讨不同类型的金属拉丝油的特点和适用范围,帮助读者更好地选择和使用合适的产品。
冷挤压磷皂化工艺

冷挤压磷皂化工艺是一种金属冷加工中的润滑工艺,主要包括磷化处理和皂化处理两个步骤。
磷化处理是指通过化学和电化学反应形成磷酸盐化学转化膜的过程,这种转化膜称为磷化膜,主要目的是在一定程度上保护金属不受腐蚀,并用于涂装前的底漆,以提高漆膜的附着力和耐腐蚀性,同时也可起到金属冷加工中的减摩润滑作用。
皂化处理工艺是在毛坯磷化处理后进行,毛坯表面已具有一定润滑能力的磷酸盐多孔膜,但磷酸盐膜的摩擦系数并不是很低,主要起支承层的作用,与之配合使用的最佳组合是硬脂酸钠为主要成分的皂类润滑剂,如C10~C20的饱和或不饱和脂肪酸钠、钾和/或三乙醇胺盐等组成的碱金属皂。
金属材料的润滑性和加工

金属材料的润滑性和加工1.1 润滑性的定义:润滑性是指金属材料在摩擦过程中,减少摩擦阻力、降低磨损和散热的能力。
1.2 润滑性的重要性:润滑性对于金属材料的加工过程至关重要,良好的润滑性能有效降低加工过程中的摩擦阻力,延长工具的使用寿命,提高加工效率,降低能耗,减少磨损和污染。
1.3 润滑性的影响因素:(1)金属材料的种类和状态(如晶粒度、晶体结构等);(2)温度和压力;(3)润滑剂的种类和性质(如粘度、极性、化学稳定性等);(4)表面 roughness 和形状误差等。
二、金属材料的加工2.1 金属材料的加工方法:(1)铸造:通过熔融金属浇铸成型的方法,制成所需的形状和尺寸的零件;(2)锻造:通过对金属材料施加压力,使其产生塑性变形,从而获得所需的形状和尺寸的零件;(3)焊接:通过加热或加压,使金属材料局部熔化,并冷却凝固成整体的方法;(4)切削加工:利用切削工具将金属材料切除,获得所需形状和尺寸的零件;(5)磨削加工:利用磨削工具对金属表面进行磨削,以提高表面粗糙度和尺寸精度;(6)电加工:利用电能对金属材料进行加工的方法,包括电火花加工、激光加工等。
2.2 金属材料加工过程中的润滑和冷却:(1)润滑:通过润滑剂减少摩擦阻力,降低磨损,提高加工效率和工件质量;(2)冷却:通过冷却液降低金属材料的温度,减少热应力,防止变形和裂纹。
2.3 金属材料加工中的质量控制:(1)控制加工过程中的温度和压力,以保证材料的塑性变形和加工质量;(2)控制润滑剂的种类和性质,以保证良好的润滑性能;(3)控制表面 roughness 和形状误差,以满足工件的使用要求。
以上是关于金属材料的润滑性和加工的知识点介绍,希望对您有所帮助。
习题及方法:1.习题:润滑性对金属材料的加工过程有何影响?方法:润滑性能够减少金属材料在加工过程中的摩擦阻力,降低磨损,提高加工效率和工件质量。
因此,在实际加工过程中,应选择合适的润滑剂,以提高润滑性能。
金属加工过程及其润滑剂

轧制油的作用:
➢ 减少摩擦,延长轧辊使用寿命 ➢ 冷却轧辊以控制辊型及防止粘辊现象 ➢ 保护板面及轧机牌坊
30
轧制油类型 普碳钢轧制油(M1713、M1714)
1.按用途可分为
热轧油 冷轧油
16
1.3.2、 磨削
M0019
M0016-高速强力磨削、防钴渗出
M0056-磨速快、加工精度高 、硬质合金
M1021 M1028 M2013-中低负荷、长寿命 M2052 M2058-多功能通用型 M3012-清洗性、磨削沉降性
M3018A M3019-轧棍 M3080 M3094-防钴渗出
17
金属加工 过程及其润滑剂
阎勇 上海研发中心 中国石化润滑油公司
2008.5.8
1
金属加工是通过成型、切削、热处理、 是焊金指属接用加、于工铸金润造属滑过及剂其程国合来外金叫制在m造切et零a削lw件、or、研kin磨机g 、f器lu冲i和d,压构 、件轧,制并、包拉括拔一等各定种的加防工锈过处程理中工所使艺用过的程液。
硅钢轧制油(M1715)
普不碳锈钢钢轧板制热油(轧M0轧786制、 油M0781、 M不078锈2)钢板热轧轧制油
1.3.3、 钻孔
M0019 M0088-高速深孔、合金钢、不锈钢 M2011 M3080
18
1.3.4、 补充
钛 铝 铜
线切割
M0047 M3026 (M1021、M1028、 M2058) M3094B(M0019、M1021、 M2058)
M0252、M1210
19
M0006
轧钢安全技术工艺润滑介绍(二篇)
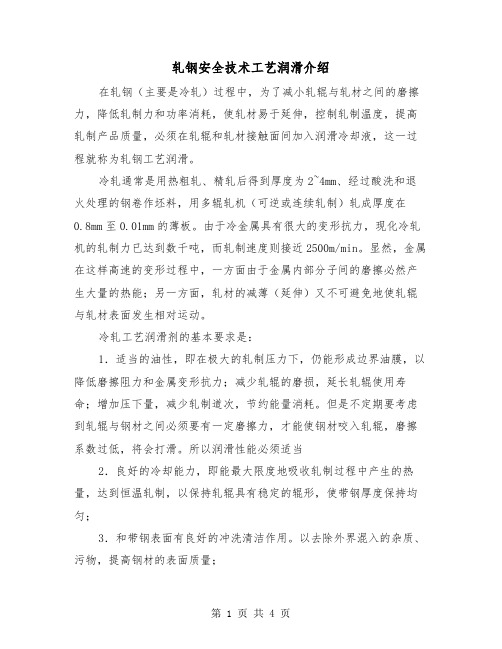
轧钢安全技术工艺润滑介绍在轧钢(主要是冷轧)过程中,为了减小轧辊与轧材之间的磨擦力,降低轧制力和功率消耗,使轧材易于延伸,控制轧制温度,提高轧制产品质量,必须在轧辊和轧材接触面间加入润滑冷却液,这一过程就称为轧钢工艺润滑。
冷轧通常是用热粗轧、精轧后得到厚度为2~4mm、经过酸洗和退火处理的钢卷作坯料,用多辊轧机(可逆或连续轧制)轧成厚度在0.8mm至0.01mm的薄板。
由于冷金属具有很大的变形抗力,现化冷轧机的轧制力已达到数千吨,而轧制速度则接近2500m/min。
显然,金属在这样高速的变形过程中,一方面由于金属内部分子间的磨擦必然产生大量的热能;另一方面,轧材的减薄(延伸)又不可避免地使轧辊与轧材表面发生相对运动。
冷轧工艺润滑剂的基本要求是:1.适当的油性,即在极大的轧制压力下,仍能形成边界油膜,以降低磨擦阻力和金属变形抗力;减少轧辊的磨损,延长轧辊使用寿命;增加压下量,减少轧制道次,节约能量消耗。
但是不定期要考虑到轧辊与钢材之间必须要有一定磨擦力,才能使钢材咬入轧辊,磨擦系数过低,将会打滑。
所以润滑性能必须适当2.良好的冷却能力,即能最大限度地吸收轧制过程中产生的热量,达到恒温轧制,以保持轧辊具有稳定的辊形,使带钢厚度保持均匀;3.和带钢表面有良好的冲洗清洁作用。
以去除外界混入的杂质、污物,提高钢材的表面质量;4.良好的理化稳定性。
在轧制过程中,不与金属起化学反应,不影响金属的物理性能;5.退火性能好。
现代冷轧带钢生产,为了简化工艺,提高劳动生产率,降低成本,在需要进行中间退火时,采用了不经脱脂清洗而直接退火的生产工艺。
这就要求润滑剂不因其残留在钢材表面而发生退火腐蚀现象(即在钢材表面产生斑点);6.过滤性能好。
为了提高钢材表面质量,某些轧机采用高精度的过滤装置(如硅藻土)来最大限度地去除油中的杂质。
此时,要避免油中的添加剂被吸附掉或被过滤掉,以保持油品质量;7.搞氧化安定性好,使用寿命长;8.防锈性好。
微量润滑在金属加工中的应用
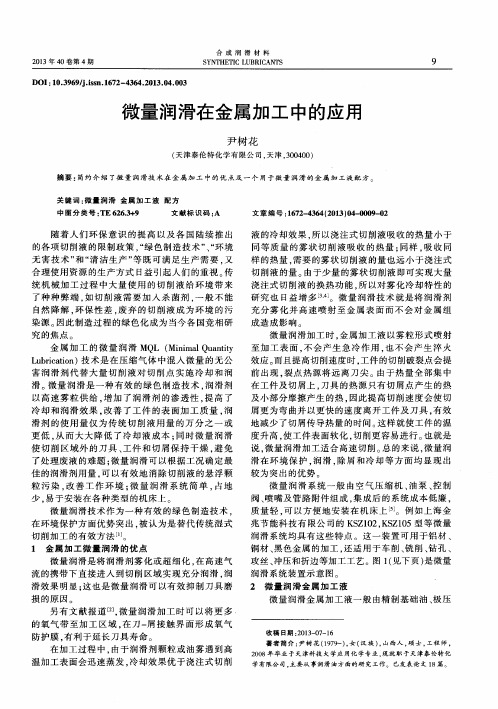
随 着人 们 环 保 意 识 的 提 高 以及 各 国 陆续 推 出 的各项 切削 液 的限制 政策 , “ 绿 色 制造 技 术 ” 、 “ 环 境 无 害 技术 ” 和“ 清 洁 生产 ” 等 既 可满 足 生 产 需要 . 又 合 理使用 资 源 的生产 方式 日益 引起 人们 的重 视 。 传 统 机 械加 工 过 程 中大 量 使 用 的切 削 液 给 环 境 带来 了种种 弊 端 , 如切 削 液需 要 加 入 杀 菌 剂 . 一 般 不 能 自然 降解 , 环保 性 差 , 废 弃 的切 削液 成 为 环 境 的 污 染源 。 因此制 造过 程 的绿色 化成 为 当今各 国竞 相研 究 的焦点 。 金 属加 工 的微 量 润滑 MQ L( Mi n i m a l Q u a n t i t y L u b r i c a t i o n ) 技 术 是 在压 缩 气 体 中混入 微 量 的无 公 害 润滑 剂 代 替 大量 切 削 液 对切 削 点 实 施 冷却 和润 滑。 微 量 润滑 是 一种 有 效 的绿 色 制造 技 术 , 润 滑剂 以 高速 雾 粒 供 给 , 增 加 了润 滑 剂 的渗 透 性 . 提 高 了 冷却 和 润 滑 效果 . 改 善 了工 件 的 表 面加 工 质 量 . 润 滑剂 的使 用 量仅 为 传 统 切 削液 用 量 的 万 分 之一 或 更低 。 从 而大 大 降 低 了冷 却 液 成本 ; 同时 微量 润滑 使切 削 区域 外 的刀 具 、 工 件 和 切 屑保 持 干 燥 . 避 免 了处理 废 液 的难 题 : 微量 润 滑 可 以根据 工况 确定 最 佳 的润滑 剂用 量 , 可 以有 效 地 消除 切削 液 的悬 浮颗 粒污染 , 改善工作 环境 ; 微量 润滑系统简单 , 占地 少, 易于安 装在 各种 类 型 的机 床 上 。 微 量 润滑技 术 作为 一种 有 效 的绿色 制 造技 术 , 在环境 保 护方 面优 势 突出 , 被认 为是 替 代传 统湿 式 切削加 工 的有效 方 法 】 ] 。 1 金 属加 工微 量润 滑 的优点
金属加工上油工艺流程
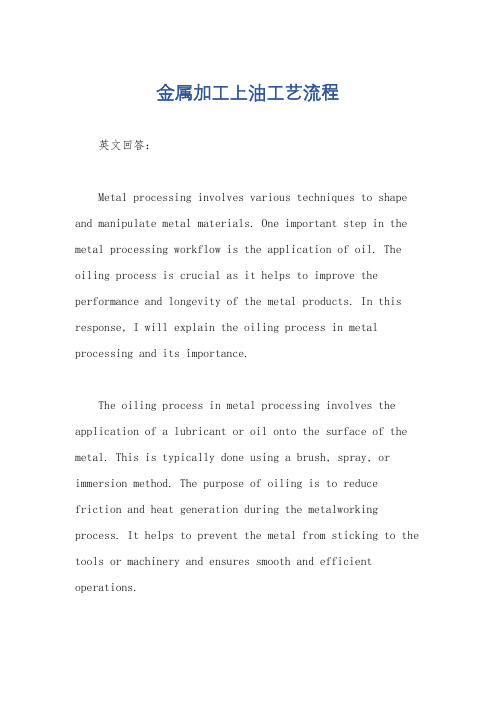
金属加工上油工艺流程英文回答:Metal processing involves various techniques to shape and manipulate metal materials. One important step in the metal processing workflow is the application of oil. The oiling process is crucial as it helps to improve the performance and longevity of the metal products. In this response, I will explain the oiling process in metal processing and its importance.The oiling process in metal processing involves the application of a lubricant or oil onto the surface of the metal. This is typically done using a brush, spray, or immersion method. The purpose of oiling is to reducefriction and heat generation during the metalworking process. It helps to prevent the metal from sticking to the tools or machinery and ensures smooth and efficient operations.There are several types of oils that can be used in metal processing, including cutting oils, forming oils, and rust preventives. Cutting oils are used during machining operations to lubricate the tool and workpiece, reducing friction and heat. Forming oils are used in processes such as bending, stamping, and drawing to facilitate smooth metal deformation. Rust preventives are applied to protect the metal surface from corrosion during storage or transportation.The oiling process is essential for several reasons. Firstly, it helps to improve the tool life and performance. By reducing friction and heat, the oiling process minimizes tool wear and extends the lifespan of cutting tools. This results in cost savings for the metal processing industry as there is less frequent need for tool replacement.Secondly, oiling enhances the surface finish of the metal products. The lubricating properties of the oil prevent scratching or gouging of the metal surface during processing. This ensures that the final product has a smooth and polished appearance, which is important forindustries such as automotive, aerospace, and electronics.Thirdly, oiling helps to prevent rust and corrosion. Metal materials are prone to oxidation when exposed to moisture or air. By applying rust preventives during the oiling process, a protective layer is formed on the metal surface, preventing the formation of rust and extending the product's lifespan.Lastly, the oiling process also plays a role in improving the overall efficiency of metal processing operations. By reducing friction and heat, the energy consumption and heat generation during the metalworking process are minimized. This leads to improved productivity and reduced operating costs for metal processing facilities.In conclusion, the oiling process is an important stepin metal processing. It helps to improve tool life, enhance surface finish, prevent rust and corrosion, and increase overall efficiency. By understanding the significance of oiling and using the appropriate oils for different metalworking processes, manufacturers can ensure high-quality metal products that meet customer requirements.中文回答:金属加工涉及各种技术来塑造和操纵金属材料。
我国铝板带箔冷轧生产及其工艺润滑剂的现状与发展

2021 June 第金属加工油:创新争先,服务制胜金属加工油(液)是根据金属加工工艺过程的特点和要求,在加工过程中使用的润滑材料或工作介质。
金属加工油(液)主要分为四大类,即切削油(液)、成型油(液)、防锈油和热处理油。
金属加工油产品的质量和性能,对保证工件质量、提高加工效率具有极为重要的意义,同时,快捷、高效的技术服务,对于解决产品在现场应用时出现的技术问题,也必不可少。
2021年3月,我国颁布了《中华人民共和国国民经济和社会发展第十四个五年规划和2035年远景目标纲要》,提出推动制造业优化升级,推动集成电路、航空航天、船舶与海洋工程装备、机器人、先进轨道交通装备、先进电力装备、工程机械、高端数控机床、医药及医疗设备等产业创新发展;改造提升传统产业,完善绿色制造体系,鼓励企业应用先进适用技术、加强设备更新和新产品规模化应用。
随着我国制造业向更高阶段迈进,预计金属加工油市场需求将保持持续增长的势头,产业化、规模化程度将进一步提升,并呈现出用油多样化、个性化的特点。
我国金属加工油市场庞大,机遇与挑战并存。
如何进一步提升技术能力和服务能力,提高核心竞争力和品牌形象,扩大金属加工油市场占有率,是每一个金属加工油产品开发者和市场竞争利益相关者需要精心作答的重要考卷。
本期双月策划的3篇文章,分别对金属加工油细分领域相关产品的市场现状及趋势、系列新产品的研发及典型应用服务案例进行了介绍,以作为未来我国金属加工油产品和服务升级的先导。
44三期项目2016年2017年2018年2019年2020年产量/(×104 t)902 1 030 1 123 1 136 1 185铝板带增幅/%14.29.0 1.2 4.3产量/(×104 t)318365390400415铝箔增幅/%14.7 6.8 2.6 3.8精制、分馏切割而得的不同馏分的基础油。
其中,如果不饱和烃以及硫、氮等非烃类物质的脱除程度越高,则基础油的稳定性能和清净性能就越好[6]。
金属加工的润滑工艺

剪切前产生显著的塑性变形,可使乳化液变成绿 色。 如选油剂要有过滤设备。
7
加工材料的性质
铜:
粘韧,切削时产生微细卷曲的屑,可使乳化液变成 绿色,影响乳化液的稳定。 如选用油剂要配备过滤设备。
可锻铸铁 :
切削时产生大量微细的具有化学活性的磨蚀性屑。 如使用油剂,必须用离心机或过滤器把铁屑除去。
13
使用和维护
配制(稀释)
稀释: 确定稀释的比例和所需乳化液的体积。
算出所用切削液(原液)量和水量。选取洁净 的容器,将所需的全部水倒入容器内,在低 速搅拌下加入切削液原液。配制乳化液时, 原液的加入速度以不出现未乳化原液为准。 切削液原液和水的加入程序不能颠倒。不要 在机床的油池(槽)内直接调配乳液。
切削类型
选用的切削液
低速重负荷切削 选用极压切削油剂
高速浅层切削 选用水基切削液
重负荷切削
选用极压乳化液
12
使用和维护
配制(稀释)
只有水基切削液需要配制,即按一定比 例加水稀释。水基切削液特别是乳化型的, 在用水稀释时要注意 : 水质:
不宜使用硬度超过400的水配制乳化液 的水的适宜硬度为50~200。
16
使用和维护
切削液的使用
3.油嘴形状: 油嘴的形状应适合被加工件的形状和大小,
以及刀具种类帮操作程序。良好的油嘴应使 切削液一直保持液流平坦,使加工件各部分 充分浴于液体内。油嘴形状要按实际效果来 调整,基本要求是使最需要冷却和润滑之处 得到足够的冷却液。
17
使用和维护
切削液的使用
4.泡沫 : 水基切削液和净切削油在使用中会发生泡沫 过多的问题。
5.机床的密封:
检查机床的轴封(特别是用乳化液作为 冷却剂时),防止切削液串入机床齿轮箱、 床头箱或其它密封的传动机构内。乳化液 如果进入矿物油润滑系统将使机床磨损。 含极压剂的净切削油串入机床传统或液压 系统,危害较小。
金属加工用油相关产品介绍

4.金属加工用油相关产品
低硫、低芳烃、无毒、无异味
KLR系列不锈钢轧制油性能特点
适中的粘度
良好的极压抗磨性
良好的抗氧化性
良好的退火清净性
4.金属加工用油相关产品
KLR9302不锈钢冷轧油-与国外产品性能对比
实测
项 目 美孚速明达AH70 昆仑KLR9302
40℃运动粘度,mm2/s
开口闪点, ℃ 倾 点, ℃
退火清净性
不合格
合格
合格
合格
合格
该产品可等效替换嘉实多的RN90,好富顿1231C、美孚的真力士26,AL70、出光50K以及ESSO的速明达N60产品。
4.金属加工用油相关产品
KLR9305铜材轧制油与国内外同类产品摩擦学性能对比
国外某品牌铜材轧制油
昆仑KLR9305铜材冷轧油
国内某品牌铜材轧制油
KLR系列不锈钢冷轧油应用
太钢
KLR9302不锈钢冷轧油已成为太钢的指定工艺用油, 2009年,太钢两条生产线实现了整体全部换油(工艺 油一般不更换,全为补加方式),后经过连续四个月 的产品质量跟踪,最终油品品质得到了用户的认可, 太钢90%以上冷轧油品采用昆仑的油品,年用量在 1000吨以上。
其它钢厂
4.金属加工用油相关产品
KLR9305铜材轧制油与进口油退火清净性能对比:TGA试验
4.金属加工用油相关产品
KLR9305铜材轧制油与进口油退火清净性能对比:模拟现场退火炉 试验(无保护气体) 进口油1
进口油2
KLR9305
酸洗前
4.金属加工用油相关产品
KLR9305铜材轧制油
适用场合:
专用于生产铜及铜合金冷轧薄板,轧速为800m/min以内,轧件宽度在 500 —1320mm,厚度为0.03-3.0mm的四辊、六辊、八辊、十二辊、 十四辊及二十辊轧机轧制过程的工艺润滑。主要喷淋在轧辊和轧板表面 起到润滑和冷却作用。
先进制造—微量润滑技术

先进制造微量润滑加工技术在金属切削加工过程中,通常都要使用切削液。
切削液在切削加工中主要起冷却、润滑、排屑和防锈的作用,有助于提高刀具耐用度,减少工件热变形,保证工件已加工表面质量等。
但是切削液的大量使用也造成了很多负面影响,不仅导致生产成本大大增加,还给环境和人体健康带来了巨大的潜在危害。
据有关统计数据表明:与切削液有关的费用相当于全部制造费用的7~17%,而工具费用仅占2~4%。
面对降低生产成本,改善生产条件和实施可持续发展对环境保护的要求,更迫于有关法律的压力,合理利用制造资源、废弃物少、环境污染小、安全性高、可进行良性循环的“绿色切削”技术是新时期机械制造技术领域的主要发展趋势之一。
其中微量润滑(Minimum Quantity Lubrication,简称MQL)技术是一种具有极大发展潜力和广阔应用前景的绿色加工技术。
MQL的概念和优点微量润滑技术亦称为半干式切削或准干式切削,是将压缩气体(空气、氮气、二氧化碳等)与极微量的润滑油混合汽化后,形成微米级的液滴,喷射到加工区进行有效润滑的一种切削加工方法。
微量润滑的主要作用是润滑,借此起到减小摩擦、降低切削热和改善切屑的流动。
切削液的用量一般仅为0.03~0.2L/h(传统湿法切削的用量为20~100L/min),可有效减小刀具与工件、刀具与切屑之间的摩擦,防止粘结,延长刀具寿命,提高加工表面质量。
MQL切削技术大大降低了冷却液成本,使切削区域外的刀具、工件和切屑保持干燥,改善了工作环境,避免了处理废液的难题,应用优势明显,适用范围广阔,国内外关于MQL的研究包含了几乎所有的切削工艺,如钻削、铣削、车削和磨削等。
MQL的方式微量润滑技术主要包括气雾外部润滑和气雾内部冷却两种方式。
①气雾外部润滑方式:将切削液送人高压喷射系统并与气体混合雾化,然后通过一个或多头喷嘴将雾滴尺寸达毫、微米级的气雾喷射到加工刀具表面,对刀具进行冷却和润滑;②气雾内冷却方式:通过主轴和刀具中的孔道直接将冷却气雾送至切削区域,进行冷却和润滑。
切削液的一些基本知识

切削液的一些基本知识金属加工液金属及其合金在切削、成形、处理和保护等过程忠使用的工艺润滑油统称为金属加工液,又名切削液。
在金属加工过程中,为了降低切削时的切削力,及时带走切削区内产生的热量以降低切削温度,提高刀具耐用度,从而提高生产效率,改善工件表面粗糙度,保证工件加工精度,达到最佳的经济效果,通常使用金属加工液。
金属加工液在金属加工过程中具有润滑、冷却、清洗、防锈等作用;其中核心作用是:一方面通过冷却作用降低加工过程中的变形热,另一方面通过润滑作用来减少金属加工过程中的磨擦热,从而来提高金属加工质量,延长刀具的使用寿命等。
1、冷却性能:冷却作用是通过乳化液和因切削而发热的刀具、切屑和工件间的对流和汽化作用把切屑热从固体(刀具、工件)处带走,从而有效地降低切削温度,减少工件和刀具的热变形,保持刀具硬度提高加工精度和刀具耐用度。
2、润滑性能:润滑作用就是其减少前刀面与切屑、后刀面与已加工表面间的摩擦形成部分润滑膜的作用,以防止刀具与切屑或工件间的粘着,所以良好的润滑可以减少功能消耗、刀具磨损和良好的表面光洁度。
3、清洗性能:在金属加工过程中,切屑、铁粉、磨屑、油污、沙粒等常常粘附在工件、刀具或砂轮表面及缝隙中,同时沾污机床和工件,不易清洗,使刀具或砂轮切屑刃口变钝,影响切削效果。
所以要求乳化液有良好的清洗作用。
乳化液的清洗性能就是指乳化液防止这些细颗粒粘结和利用液流的机械冲洗作用将其冲走的能力。
4、防锈性能:在金属加工过程中,工件要与环境介质如水、氧、硫、二氧化硫、二氧化碳、硫化氢、氯离子、游离酸碱和乳化液分解或氧化变质所产生的油泥等腐蚀性介质接触而受到腐蚀,机床部件与乳化液接触的部分会产生腐蚀。
因此要求乳化液有一定的防锈能力。
金属加工液除了应具有良好的冷却性、润滑性、清洗性、防锈性外,还应具有防腐蚀性、抗菌性、防垢性、抗泡性、热稳定性、无毒、无害、无刺激性气味、不污染环境、使用方便等条件。
金属加工液可分为纯油性切削液和水溶性切削液两种。
- 1、下载文档前请自行甄别文档内容的完整性,平台不提供额外的编辑、内容补充、找答案等附加服务。
- 2、"仅部分预览"的文档,不可在线预览部分如存在完整性等问题,可反馈申请退款(可完整预览的文档不适用该条件!)。
- 3、如文档侵犯您的权益,请联系客服反馈,我们会尽快为您处理(人工客服工作时间:9:00-18:30)。
不宜使用硬度超过400的水配制乳化液 的水的适宜硬度为50~200。
a
13
使用和维护
配制(稀释)
稀释: 确定稀释的比例和所需乳化液的体积。
算出所用切削液(原液)量和水量。选取洁净 的容器,将所需的全部水倒入容器内,在低 速搅拌下加入切削液原液。配制乳化液时, 原液的加入速度以不出现未乳化原液为准。 切削液原液和水的加入程序不能颠倒。不要 在机床的油池(槽)内直接调配乳液。
如选油剂要有过滤设备。
青铜:
剪切前产生显著的塑性变形,可使乳化液变成绿 色。
如选油剂要有过滤设备。
a
7
加工材料的性质
铜:
粘韧,切削时产生微细卷曲的屑,可使乳化液变成 绿色,影响乳化液的稳定。
如选用油剂要配备过滤设备。
可锻铸铁 :
切削时产生大量微细的具有化学活性的磨蚀性屑。
如使用油剂,必须用离心机或过滤器把铁屑除去。
及时排除循环路线的金属屑、金属粉末、霉菌粘液、 切削液本身的分解物、砂轮屑,以免造成堵塞。
2.抑菌
可采用定期投入杀菌剂和用超微过滤等手段抑 制细菌的繁殖。
3.切削液的净化
a
19
使用和维护
切削液内所含的固体粉末的危害:
(1) 悬浮于冷却液内的粒子损坏泵的密封,增 大刀具磨损,损害人的皮肤,影响加工质量;
铅及其合金 :
易切削,可生成铁皂,破坏乳化液的稳定。
如使用油剂,对油剂有稠化倾向,要防止使用含
大量脂肪的油剂。
a
8
加工材料的性质
镁:
切削时产生细屑,可燃。 可采用低粘度油作为切削液。
镍及高镍合金:
切削时局部产生高热,切屑可能烧结。 可选用重负荷乳化液或非活性硫化油。
a
燃的切削,易发生加工硬化现象。 应用重负荷乳化油或极压油剂。
油基切削液指含添加剂的矿物油。 水基切削液指乳液、合成液及化学溶液。
切削类型
选用的切削液
低速重负荷切削 选用极压切削油剂
高速浅层切削 选用水基切削液
重负荷切削
选用极压乳化液
a
12
使用和维护
配制(稀释)
只有水基切削液需要配制,即按一定比 例加水稀释。水基切削液特别是乳化型的, 在用水稀释时要注意 :
a
16
使用和维护
切削液的使用
3.油嘴形状: 油嘴的形状应适合被加工件的形状和大小,
以及刀具种类帮操作程序。良好的油嘴应使 切削液一直保持液流平坦,使加工件各部分 充分浴于液体内。油嘴形状要按实际效果来 调整,基本要求是使最需要冷却和润滑之处 得到足够的冷却液。
a
17
使用和维护
切削液的使用
4.泡沫 : 水基切削液和净切削油在使用中会发生泡沫 过多的问题。
3.合成液体:含油或不含油,以溶于水的高 分子有机物为主要润滑剂。
4.化学溶液:不含油。是不含矿物油的水溶
液。
a
4
切削液的选择,首先要避免 使用那些对机床、刃具和加工材 料有害的液体。通常,不含游离 硫的硫化油适用于加工钢材和铜 材。而有些铜合金和高镍合金, 在硫剂(特别是含游离硫)作用下 会产生暗色斑痕。
a
3
金属切削液的成分
主要成分如下 : 1.油或油基液体:习惯称为切削油(也称切削 油),主体为矿物油,含或不含添加剂。
2.乳液:有时称为溶解油。根据矿物油含量 和油滴粒度可分为3种:
粗乳液:含油65%~80%,油滴粒度 2~10μm; 微乳液:含油40%~50%,油滴粒度<1μm;半合 成乳液:含油5%~40%,油滴粒度约0.1μm
a
14
使用和维护
切削液的使用
1.循环液体总量: 机加工过程中循环使用的切削液因飞溅、
雾化、蒸发以及加工材料和切屑携带,不断 地消耗。为了维持机床油槽原有切削液的体 积,每月需补加切削液量。
a
15
使用和维护
切削液的使用
2.切削液的流量: 一般的机加工应保证压力、大流量。镗
深孔和空心杆刀具可采用高压喷射冷却液, 以利于把切屑冲刷出来。有些中低碳钢和钛 材的钻孔加工采用脉冲式注射冷却液更有利, 但要注意适合油泵的性能。苛刻的加工所使 用的氯净切削油,要加大流量。
金属加工的 润滑工艺
a
1
金属的机械加工类型及选用的润滑剂
金属的去除
靠刃具把金属从被加工件上除掉, 一般习惯地把金属去除作业所用的润滑剂称为切 削液。
金属的变形
用模具使金属在应力下塑性变形,如轧、拉拔、 冲压、挤压等, 把金属变形用的润滑剂称为金属加工工艺液体。
a
2
金属切削液的品种
金属切削液的品种繁多,ASTMD2881把 金属加工用的液体划分为以下三类: 1。油和油基液体 2。水基乳液及分散体 3。化学溶液(真溶液及胶体溶液)
a
5
加工材料的性质
被加工的材料物理化学性质各 异,反映在切削操作上就会有切削 的难易和与切削液相容性等新问题。 对较难加工的材料及其与切削液的 相容性分别简略介绍如下。
a
6
加工材料的性质
铝:
质软,切割易粘切具。
应选用专用乳化液或石蜡基矿物油作冷却润滑剂。
黄铜:
切削时产生大量细屑,易使乳化油变绿。
5.机床的密封:
检查机床的轴封(特别是用乳化液作为
冷却剂时),防止切削液串入机床齿轮箱、
床头箱或其它密封的传动机构内。乳化液
如果进入矿物油润滑系统将使机床磨损。
含极压剂的净切削油串入机床传统或液压
系统,危害较小。
a
18
使用和维护
切削液的维护
冷却液、切削液的维护工作主要包括: 1.确保液体循环路线的畅通
(2) 固体沉淀在油池底部,与有机物聚结,形 成一层有大量气孔的沉淀层,为微生物繁殖提供了 有利条件,而霉菌的细丝更稳定了沉淀的固体;
(3) 切削液中的金属粉末具有很高的化学活性,
可使切削液中的某些成分失效。菌污染使切削液酸
败分解,霉菌的繁殖产生粘稠物,导致管路和喷嘴
堵塞。
a
20
锌:
切削面不规整,难以取得良好的光洁度,与乳化液 生成锌皂,使乳化液分离。 应选用专用乳化液。
a
10
加工工况
在低速加工(螺纹切削、扩孔和齿面切削) 时,切削润滑剂的主要任务是缩小推进面与 屑的粘结,作为边界润滑剂。
在高速切削加工时,切削液的主要作用 是降低摩擦热,带走热量。
a
11
油基和水基的特点