数控电火花加工实训要点
数控电火花实习报告

数控电火花实习报告一、填空题1、电火花加工又称放电/电蚀加工,是利用工具电极和工件电极之间的脉冲性的火花放电将金属腐蚀从而将工件逐步加工成型的方法。
2、电火花加工机床主要由主机部分、脉冲电源、自动进给调节系统、工作液及其循环过滤系统和数控系统组成的。
3、电火花线切割采用的加工极性一般是负极性加工,其加工极性也就是钼丝应当接电源的负极,工件接电源的正极。
电火花成型机采用的加工极性一般是性加工。
4、快走丝的加工效率以mm²/min 来衡量.表面粗糙度以Ra 表示,快走丝一般能达到的表面最佳粗糙值为063~1.25um 。
5、FW系统控制分四大模式,分别是手动模式、自动模式、编辑模式和CAD和CAM 模式。
要完成一个零件的装夹找正,需在手动模式下进行,要完成一个零件的加工,需在自动模式下进行,要修改一个程序或手编一个程序,需在编辑模式下进行,要自动编程,需在CAM 模式下进行。
6、偏移是为了补偿丝径和放电间隙带来的尺寸变化。
若按顺时针切一个凸模,需采用左偏移,若按顺时针切一个凹模需采用右偏移。
7、电火花线切割根据移动速度分为快走丝机床和慢走丝机床。
8、电火花加工主要应用线切割加工和成型加工。
二、简答题1、注释下面指令含义I0:圆弧在X轴上,圆心相较于起点坐标差为0J-10000:圆弧在Y轴上,圆心相对于起点坐标差为-10000X10000:圆弧在X轴终点坐标为10000Y0:圆弧在Y轴终点坐标为0G02:顺时针圆弧插补2、什么是特种加工,它有哪些分类?答:特种加工是指利用电能、化学能、光能、声能、热能及其机械能的组合等形式对工程材料进行加工的各种工艺方法的总称。
分类:1、电能热能:电火花加工电子束加工等离子弧加工;2、电能机械能:离子束加工3、电能化学能:电解加工电解抛光4、光能热能:激光加工5、化学能:化学加工化学抛光6、声能机械能:超声加工7、机械能:磨料喷射加工磨料流加工液体喷射加工3、实现电火花加工的条件有哪些?答:1、必须使用脉冲电源来保证瞬时的脉冲放电,以确保放电产生的热量集中在被加工材料的微小区域内,使微小区域内的材料产生熔化、气化而达到电蚀除的目的。
数控电火花机床实训报告

一、实训背景随着现代制造业的快速发展,数控电火花机床作为一种高精度、高效率的加工设备,在模具制造、航空航天、汽车制造等领域得到了广泛应用。
为了提高学生的实际操作能力和工程素质,我校特组织数控电火花机床实训课程。
本次实训旨在使学生了解数控电火花机床的基本原理、操作方法、加工工艺,掌握编程技巧,提高学生的实际操作技能。
二、实训目的1. 使学生了解数控电火花机床的基本结构、工作原理和加工工艺;2. 使学生掌握数控电火花机床的操作方法,包括开机、关机、参数设置、加工等;3. 使学生学会编程技巧,能独立编写简单的数控程序;4. 培养学生的团队协作能力和创新能力。
三、实训内容1. 数控电火花机床基本知识(1)机床概述:介绍数控电火花机床的组成、工作原理、特点及应用领域。
(2)机床结构:讲解机床各部件的功能、作用和安装要求。
(3)加工工艺:分析电火花加工的基本原理、加工参数、加工效果等。
2. 数控电火花机床操作(1)开机操作:讲解机床开机前的准备工作、开机步骤、注意事项等。
(2)参数设置:介绍机床参数设置的方法、技巧和注意事项。
(3)加工操作:讲解加工过程中的操作步骤、注意事项、故障排除等。
3. 编程技巧(1)编程基础:讲解数控编程的基本知识,如坐标系、指令、程序结构等。
(2)编程实例:分析典型零件的编程方法,如模具、刀具路径、加工参数等。
(3)编程技巧:介绍编程过程中的技巧,如简化编程、提高效率等。
四、实训过程1. 理论学习:教师讲解数控电火花机床的基本知识、操作方法和编程技巧。
2. 实践操作:学生分组进行机床操作、编程和加工实践。
3. 故障排除:学生自行分析故障原因,尝试排除故障。
4. 交流讨论:学生分享实训心得,讨论解决实际问题的方法。
五、实训成果1. 学生掌握了数控电火花机床的基本原理、操作方法和编程技巧。
2. 学生的实际操作能力得到提高,能独立完成简单零件的加工。
3. 学生的团队协作能力和创新能力得到锻炼。
电火花成形加工实训

电火花成形加工实训实训四电火花工具电极找正1、实训目的掌握电火花工具电极的找正方法。
2、实训项目电火花工具电极的找正。
3、实训器材NH7135NC数控电火花成形机床、工具电极、精密刀口角尺、百分表。
4、实训内容(1)、型腔模工艺分析电火花加工中,工具电极的装夹尤其重要。
撞击方法可用钻夹头装夹,也可用专用夹具装夹,还可用瑞典3R夹具装夹。
工具电极的找正是要确保工具电极与工件的垂直,找正的方法主要有用精密刀口角尺找正、用百分表找正、用电火花放电找正和用工件模板找正。
(2)、工具电极的装夹①、用钻夹头装夹工具电极先用内六角头扳手将装在主轴夹具上的内六角螺钉旋松,然后将装夹工具电极的钻夹头固定在主轴夹具上。
主轴夹具的装夹部分为900靠山的结构,可将钻夹头稳固地贴在靠山上,最后再用内六角扳手将主轴夹具上的内六角螺钉旋紧,完成工具电极的装夹(图1)。
②、用专用夹具装夹工具电极还可以采用电火花线切割加工出电极扁夹,作为专用的夹具来装夹工具电极,电极扁夹用于装夹某些尺寸比较小的扁状电极。
③、用瑞典3R夹具装夹工具电极采用瑞典3R夹具装夹工具电极时,3R夹具与工具电极固定在一起,在数控机床上加工,加工后再一同装夹到主轴上。
这样的方法解决了工具电极拆装后的重复定位问题。
图1 用钻夹头装夹工具电极(3)工具电极的找正①、用精密刀口角尺找正工具电极工具电极装夹完毕后,必须对工具电极进行找正,确保电极的轴线与工件保持垂直,图2所示为用精密刀口角尺找正工具电极。
具体校准方法如下:图2 用精密刀口角尺找正工具电极图3 用百分表找正工具电极a.按下手控盒上的“Z-”按钮,将工具电极缓缓放下,使工具电极慢慢靠近工件,在与工件之间保持一段间隙后,停止下降工具电极。
b.沿X轴方向工具电极找正。
沿X轴方向将精密刃口角尺放置在工件(凹模)上,使精密刃口角尺的刀口轻轻与工具电极接触,移动照明灯置于精密刃口角尺的后方,通过观察透光情况来判断工具电极是否垂直。
电火花实训报告

电火花实训报告电火花加工是一种现代制造业中常见的金属加工方法,通过高频电火花放电所产生的热能,使工件表面产生局部高温并迅速融化,然后通过电解液中的离子传递和冷却,形成所需的形状和孔洞。
本次报告将详细介绍电火花加工的原理、设备以及实际操作过程,并总结实训中的一些心得体会。
一、电火花加工原理电火花加工的原理是利用金属导电性和电火花放电的特性,实现对工件进行精细加工。
具体来说,电火花加工主要包括以下几个步骤:1. 工作电极和工件之间形成间隙:将工作电极和工件安装在工作台上,通过调整间隙距离保持适当的放电效果。
2. 电极放电产生电弧:在间隙中加入电解液,通电后会形成电弧,由电极放电方式决定。
3. 电火花放电:电弧放电过程中产生高温,使工件上的金属瞬间融化。
4. 电解液冷却:通过电解液中的离子传递热量,将融化的金属冷却固化,形成加工后的形状和孔洞。
二、电火花加工设备电火花加工设备主要包括数控电火花加工机床、电极和电解液等。
数控电火花加工机床是实现电火花加工的核心设备,具有高精度、高稳定性和高自动化水平的特点。
电极是电火花放电的载体,通常由铜、钼等材料制成,形状根据加工要求而定。
电解液是实现电火花放电和冷却的介质,一般采用蜡状或油状电解液。
三、电火花实训操作在实训操作中,我们使用了数控电火花加工机床进行加工试验。
具体操作步骤如下:1. 设定加工参数:根据工件材料和加工要求,设定加工参数包括放电电压、放电电流、放电时间等。
2. 加工工艺准备:将工作电极、电解液安装在机床上,并根据工件要求进行定位、夹紧等操作。
3. 编程设置:通过数控系统,进行加工路径的编程设置,并确认无误后进行下一步。
4. 开始加工:根据设定的参数和编程路径,启动电火花加工机床,实施加工操作。
5. 加工过程监控:注意观察加工过程中的放电状态、加工质量和加工时间等,及时调整参数,确保加工效果。
6. 加工完成及后续处理:加工完成后,进行工件的清洁和后续处理,如去除电解液、清理残渣等。
电火花实训报告

电火花实训报告一、引言电火花加工是一种常用的金属加工方法,通过电弧放电产生的高温高压能够将金属材料融化或蒸发,并在工件表面形成微小的电火花坑。
电火花加工具有加工精度高、加工效率高和广泛适用于各种金属材料等优点,在工业生产中有着重要的应用。
本报告旨在介绍电火花实训的过程与结果,以及所获得的经验和教训。
二、实训目标通过电火花实训,达到以下目标:1. 理解电火花加工的原理和工艺流程;2. 掌握电火花加工的操作技巧;3. 熟悉电火花加工设备的使用及相关安全知识;4. 根据实训要求完成一定数量的电火花加工工件。
三、实训准备1. 实验设备:电火花加工机床、电极、工作液等;2. 实验材料:金属工件(如钢、铝等);3. 实验环境:通风良好、没有明火等危险物品。
四、实训过程1. 实验前准备a. 检查实验设备是否正常工作,确保安全使用;b. 检查实验材料是否符合要求;c. 穿戴个人防护装备,如防护眼镜、手套等。
2. 实验操作a. 根据实训要求选择适当的电极材料,并装夹到机床上;b. 调整机床参数,如电极电压、放电电流、脉冲时间等;c. 在工作液中浸泡待加工的工件,并将其安装在机床上;d. 启动机床,进行电火花加工,注意操作过程中的安全事项;e. 根据实验要求进行多次加工,获取加工数据。
3. 实验结果分析a. 观察加工后的工件表面,记录电火花坑的数量、形状和尺寸等数据;b. 使用测量仪器检测加工后的工件精度,如直径、表面粗糙度等;c. 对实验结果进行分析,比较不同参数对加工效果的影响。
五、实训总结1. 实训成果a. 成功掌握电火花加工的基本操作技巧;b. 完成了一定数量的电火花加工工件;c. 了解了电火花加工的原理和特点。
2. 实训经验a. 注意安全:电火花加工过程涉及高温、高压等危险因素,操作时需严格按照操作规程,并注意防护措施;b. 熟悉设备:掌握电火花加工机床的使用方法和参数调整技巧,以确保加工效果;c. 多练习:通过多次实验,积累经验,提高加工水平。
电火花加工实训报告

电火花加工实训报告实训报告:电火花加工一、实训背景和目的电火花加工是一种非接触式的金属加工技术,通过电火花放电的方式,在金属工件表面形成微小的放电坑,以达到加工工件的目的。
本次实训旨在使学生了解电火花加工的原理、设备和操作方法,并进行实际操作,掌握电火花加工技术。
二、实训内容1. 学习电火花加工原理和设备- 电火花加工原理:了解电火花加工的原理和基本概念。
- 电火花加工设备:学习电火花加工设备的组成和工作原理。
2. 实际操作电火花加工设备- 设备调试:了解电火花加工设备的使用方法和步骤,进行设备的调试和操作准备。
- 加工试验:选择合适的工件和加工参数,在电火花加工设备上进行加工试验。
- 加工控制:掌握电火花加工过程中的加工控制方法,如放电电流、脉冲间隔等参数的调整。
3. 检验和评估- 加工后工件测量与评估:使用测量工具对加工后的工件进行尺寸测量,评估加工质量。
- 实训总结与报告:对本次实训进行总结和报告,包括实际操作的心得体会和对电火花加工技术的理解。
三、实训过程和结果1. 学习电火花加工原理和设备在实训前,通过课堂学习和相关资料的阅读,了解了电火花加工的基本原理和设备。
2. 实际操作电火花加工设备实训时,首先进行了电火花加工设备的调试,包括电源的连接、电极的安装和工作台的调整等。
然后选择了一块金属工件,并根据加工要求调整了放电电流和脉冲间隔等参数。
经过多次试验和调整,最终得到了满意的加工效果。
3. 检验和评估使用测量工具对加工后的工件进行了尺寸测量,发现工件尺寸与设计要求基本一致,表明电火花加工的加工质量良好。
4. 实训总结与报告通过本次实训,我对电火花加工的原理、设备和操作方法有了更深入的了解,掌握了电火花加工技术。
在实际操作中,我也学会了调整加工参数和控制加工质量。
同时,我也体会到了电火花加工的优点和局限性,在实际应用中需要根据具体情况加以考虑。
四、实训心得与建议本次实训使我对电火花加工有了更深入的了解,通过亲自操作和加工实践,使我对电火花加工技术有了更深刻的认识。
电火花成形加工实训指导

电火花成形加工实训指导一、实训目的1、电火花成形机床的组成、工作原理和操作方法。
2、掌握电极材料的选择、结构形式及电极尺寸计算。
3、掌握电极和工件的装夹及校正定位。
4、掌握加工中电规准的选择及加工参数对被加工型腔质量的影响。
二、实训设备及材料1、电火花机车一台。
2、工具电极一根(材料为铜、石墨、或钢)3、工件材料为常用模具钢。
三、实训内容及步骤在实训教师的指导下,了解电火花加工机车的主要构成,机车和控制板上各旋钮及按键的功用,工件的装夹、平动量的调节及加工操作过程。
1、功能键的介绍(F1~F10)F1:手动放电。
在单节放电时使用即一段加工结束后机车停止。
F2:自动放电。
当有多段程序时,前一段放电结束F3:程序编制。
进行程序的编制。
F4:位置归零。
设定加工的起始点。
F 5:位置设定。
设定加工型腔的平面位置。
F6:找中心点。
当型腔位置在中心是用F6。
F7:EDM参数。
在加工过程中要改变参数是使用。
F8:机械参数。
厂家设定,没有必要不做改动。
F9:计时器归零。
加工时记下加工的时间,在加工开始时要归零。
F10:参数自动匹配。
一些主要加工参数可以在程序编制的时候编制好,但是如脉冲间隔、放电间隙等一些辅助参数可以在编制程序的时候编制好,也可以利用自动匹配的方法自动设定。
四、操作面版介绍在介绍控制面板前,要先将放电条件介绍给大家。
只有熟记放电条件的涵义,才能合理的编制程序并对放电过程中出现的问题加以解决。
B P:高压电流。
设置值大,电流大,火花大,加工的速度快,但表面的质量低,间隙大,设置值小则反之。
一般在粗加工时使用。
A P:低压电流。
设定范围在0~90之间,设定值大火花大,加工速度快,但表面的质量低,间隙大。
设置值小则表面质量高,间隙小。
在使用过程中要注意,电流大于9A时要浸油加工,以防止失火。
P A:脉宽。
与电流配合来决定表面粗糙度,一般是电流的20~30倍。
P B:脉宽间隔。
设定值小,效率高,但容易造成排渣不畅,在加工过程中一般要视电极的材料而定。
电火花实训报告总结

电火花实训报告总结电火花实训是一种重要的工业技术培训方式,通过实际操作和实地实训,提升学员对电火花加工技术的理解和应用能力。
本文将对我在电火花实训过程中所学到的知识和体会进行总结和归纳,以便更好地记忆和应用。
一、实训内容电火花加工是一种常见的工艺,它利用电火花放电的特性在工件表面加工出所需的形状和尺寸。
通过实训,我们学习了电火花加工的基本原理、设备操作和工艺参数的设定,具体包括:1. 电火花放电的原理和机理:电火花放电是一种通过电极间高频脉冲放电产生的能量释放而实现的加工方式。
我们深入学习了电火花放电的原理和机理,理解了电火花加工的物理过程。
2. 电火花加工设备和工具的使用:我们接触了电火花加工设备,学习了操作方法和注意事项。
熟悉了电极的选择和更换,了解了不同工件材料和形状对电火花加工的影响。
3. 工艺参数的设定与调整:电火花加工的效果受到工艺参数的影响,我们学习了如何根据工件的要求来设定和调整工艺参数,包括放电电流、放电时间和脉冲间隔等。
4. 实际操作与案例分析:在实训中,我们进行了一系列的实际操作,包括简单形状的加工和复杂形状的加工。
通过实际操作,我们进一步了解了电火花加工的工艺性能和加工效果。
二、实训收获通过电火花实训,我个人获得了以下方面的收获:1. 知识提升:通过学习电火花加工的理论和实践,我对电火花放电的原理和机理有了更深入的理解。
同时,我熟悉了相关设备和工具的使用,对工艺参数的设定和调整也有了更深刻的认识。
2. 技能提高:在实训中,我亲自操作了电火花加工设备,学会了正确使用电极和调整工艺参数的技巧。
通过不断的实践,我的操作技能和加工水平得到了提升。
3. 团队合作:实训中,我们以小组为单位进行实际操作和案例分析。
通过与同学们的合作,我学会了与他人协作、沟通和共享经验。
这对我今后的团队合作能力和组织协调能力有着积极的影响。
4. 实践能力:电火花实训是一种真实的实践活动,在操作中体验了真正的电火花加工过程。
数控电火花线切割机床基本操作实训
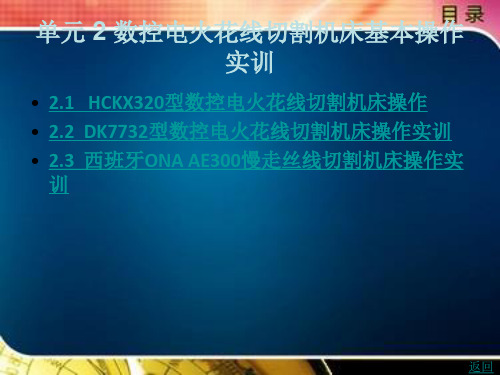
2.1 HCKX320型数控电火花线切割机 床操作
• 2.1.2 HCKX320 型 数控电 火花线切割 机床基本操作 • 1. 机床开 、 关机操作 • (1) 开机
其操作方法为 : ① 接通总电源 ( 打开总电源空气开关 )。 ② 打开数控脉冲电源控制柜左侧开启 开关 。 • ③ 拔出 “ 红色蘑菇头 ” 按钮 ( 急停按钮 )。 ④ 按下绿色启 动按钮 , 总电源启 动 , 电源柜内各个开关接通 。 ⑤ 稍等片刻 , 显示器上出 现计算机自 检信息 , 之后进入主菜单 。 ⑥ 启 动系统后 , 要成功地将各轴移到负极限以便建立机床坐标 。 • (2) 关机 将工作台移至 X、 Y 轴中 间 位置 , 然后按下 “ 红色蘑菇头 ” 按钮 • 关掉电源 , 再关闭 数 控 脉 冲 电 源 控 制 柜 左 侧 空 气 开 关 , 最 后 关掉 总 电 源开关 。
上一页 下一页 返回
2.1 HCKX320型数控电火花线切割机 床操作
• (2) 键盘输入移动 ① 在主菜单下移动光条选择 “ 手动 ” 中的 “ 移动 ” 功能 。 ② 从 “ 移动 ” 菜单中选择 “ 快速定位 ” 子功能 。 ③ 通过按键盘上的键输入数据 。 ④ 按 “Enter” ( 回车 ) 键 , 工作台开始移动 。
• 3. 工作台 移动 该机床移动工作台的方法有两种 : 手控盒移动和输入坐标移动 。 (1) 手控盒移动 ① 在主菜单下移动光条选择 “ 手动 ” 中的 “ 手控盒 ” 功能 。 ② 通过手控盒上的移动速度选择开关选择移动速度 ( 有点动 、 低速 、 中 速 、 快速四挡 )。
• ③ 按下要移动的轴所对应的键就可以实现工作台移动 。
• 2.2.1 DK7732 型数控电火花线切割机床电源柜 控制面板
数控电火花切割实习报告

一、实习目的本次实习旨在让我们深入了解数控电火花切割机床的工作原理、操作流程以及加工工艺,提高我们对特种加工技术的认识和应用能力。
通过实际操作,我们希望掌握以下内容:1. 熟悉数控电火花切割机床的结构及工作原理。
2. 掌握数控电火花切割机床的操作方法和加工工艺。
3. 学会编制数控电火花切割程序,并对加工过程进行优化。
4. 了解电火花切割在模具制造、航空航天、汽车制造等领域的应用。
二、实习内容1. 机床结构及工作原理数控电火花切割机床主要由床身、工作台、电极丝、脉冲电源、控制系统等部分组成。
机床的工作原理是:利用连续移动的细金属丝(电极丝)作为工具电极,在工件与电极丝之间施加脉冲电流,产生电火花放电,从而对工件进行切割。
2. 操作方法(1)开机前检查:检查机床各部件是否完好,工作液是否充足,电极丝是否完好。
(2)设置加工参数:根据工件材料、形状、尺寸等要求,设置合适的加工参数,如脉冲宽度、脉冲间隔、走丝速度等。
(3)装夹工件:将工件放置在工作台上,并调整其位置和角度,确保加工精度。
(4)装夹电极丝:将电极丝装夹在储丝筒上,调整电极丝张力。
(5)启动机床:打开脉冲电源,启动控制系统,开始切割加工。
(6)监控加工过程:观察工件加工情况,及时调整加工参数和电极丝张力。
(7)关闭机床:完成加工后,关闭脉冲电源,停止机床运行。
3. 加工工艺(1)加工参数的选择:根据工件材料、形状、尺寸等要求,选择合适的加工参数,如脉冲宽度、脉冲间隔、走丝速度等。
(2)电极丝的选择:根据工件材料、形状、尺寸等要求,选择合适的电极丝材料,如钼丝、铜丝等。
(3)加工顺序:按照一定的顺序进行加工,如先切割粗加工轮廓,再切割精加工轮廓。
(4)加工精度控制:通过调整加工参数、电极丝张力等手段,控制加工精度。
三、实习心得通过本次实习,我对数控电火花切割技术有了更深入的了解,以下是我的一些心得体会:1. 数控电火花切割技术具有加工精度高、加工速度快、加工范围广等优点,在模具制造、航空航天、汽车制造等领域具有广泛的应用前景。
电火花成形加工实训

电火花成形加工实训实训五电火花自动多步加工1、实训目的掌握电火花自动多步加工的方法。
2、实训项目①、多孔加工的定位方法;②、电火花自动多步加工的设定方法。
3、实训器材数控电火花成形机床、工具电极、工件电极、精密刀口角尺、百分表。
4、实训内容(1)、工艺分析多孔加工定位主要采取绝对定位方式,先根据加工工件的要求,确定工件的基准孔,然后按工件各孔之间的间距完成其余各孔的电火花加工。
电火花自动多步加工是编制电规准程序,实现自动完成从粗加工到精加工的全过程。
(2)、多孔加工的定位方法①、工具电极的装夹与找正将工具电极装夹在主轴上,找正方法同实训四。
工具电极采用边长为10mm的方形电极。
②、工件电极的装夹与定位工件电极的外形尺寸长为lOOmm,宽为70mm,厚为5mm。
工件电极上需要加工9个孔,孔的尺寸为lOmmXlOmm,每个孔的加工深度为4mm,加工工件如图1所示。
a.工件电极的装夹。
b.工件上需要加工9个孔,左下角的孔为定位孔,绝对坐标的原点在工件的左下角。
c.工件电极已知定位同实训四。
图1多孔加工工件d.其他各孔的位置可按图纸要求,以第一孔位置为基准,分别计算出各孔距第一孔位置的绝对坐标值。
各孔的坐标值分别为:l(0,0)、2(20,0)、3(40,0)、440,20)、5(40,40)、6(20,40)、7(0,40)、8(0,20)、9(20,20)。
(3)、单电极多孔加工①、设置孔1的电加工规准。
②、手动加工孔1。
第一个点加工完成后,退出手动加工模式,③、将工具电极移到第二个点位置,同②步骤一样加工孔2。
④、经8次重复步骤,完成其他各孔的加工。
⑤、关闭油泵,去除工作液,拆除工件电极,清理工作台面,并涂抹上机油。
电火花加工实训报告
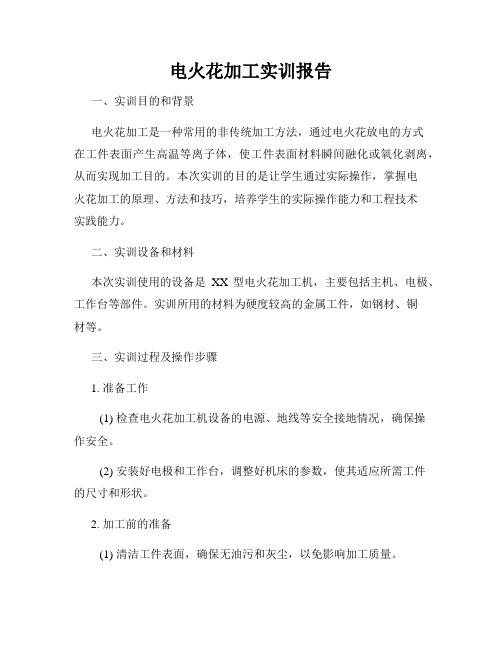
电火花加工实训报告一、实训目的和背景电火花加工是一种常用的非传统加工方法,通过电火花放电的方式在工件表面产生高温等离子体,使工件表面材料瞬间融化或氧化剥离,从而实现加工目的。
本次实训的目的是让学生通过实际操作,掌握电火花加工的原理、方法和技巧,培养学生的实际操作能力和工程技术实践能力。
二、实训设备和材料本次实训使用的设备是XX型电火花加工机,主要包括主机、电极、工作台等部件。
实训所用的材料为硬度较高的金属工件,如钢材、铜材等。
三、实训过程及操作步骤1. 准备工作(1) 检查电火花加工机设备的电源、地线等安全接地情况,确保操作安全。
(2) 安装好电极和工作台,调整好机床的参数,使其适应所需工件的尺寸和形状。
2. 加工前的准备(1) 清洁工件表面,确保无油污和灰尘,以免影响加工质量。
(2) 根据所需加工的工件形状和尺寸,选择合适的电极形状和尺寸。
(3) 将工件固定在工作台上,调整好工作台的位置和方向。
3. 加工操作(1) 启动电火花加工机,进行电极放电参数的设置。
(2) 调整电极与工件之间的间隙,保证电极正常放电,避免过大过小的间隙导致加工质量下降。
(3) 根据所需加工的形状、尺寸和深度,进行相应的程序设置,以实现加工要求。
(4) 开始加工,在机床运行状态下,观察加工过程中的放电现象和工件表面的变化情况,如需调整可及时暂停并进行调整。
4. 加工后的处理(1) 加工完成后,关闭电火花加工机,清理加工现场,将电极和工作台进行清洁和保养。
(2) 取下加工后的工件,进行表面质量的检查,如有不符合要求的地方可进行后续修整处理。
四、实训结果和心得体会通过本次电火花加工的实训,我对电火花加工的原理和操作流程有了更深入的了解。
在实际操作过程中,我不仅掌握了电火花加工机的调试和操作技巧,还学会了如何根据工件的形状、材料和要求进行电极的选择和参数的设置。
此外,我也发现了加工过程中一些常见问题的处理方法,例如电极和工件之间的间隙调整、放电现象的观察等。
电火花加工实训报告

电火花加工实训报告一、实训背景随着制造业的发展,电火花加工技术在金属加工领域中扮演着重要的角色。
为了提高学生对电火花加工的理论与实践操作能力,本次实训旨在让学生熟悉电火花加工设备的使用和工艺参数的调整,以及加工过程中的注意事项和操作规范。
二、设备概述本次实训所用设备为XXX品牌的电火花加工机。
该设备采用了先进的放电控制系统,具备高精度的加工能力和较大的工作范围。
设备主要由放电发生器、工作台、操纵系统、液体供给系统等组成。
三、实训目标1. 掌握电火花加工的基本原理和工艺流程;2. 学习电火花加工设备的正确操作方法;3. 熟悉加工过程中的关键参数的调整与优化;4. 提高对加工材料性能的把握和分析能力。
四、实训过程1. 设备检查和准备在进行实训前,首先需要检查设备的工作状况,包括电源连接是否正常、液体供给系统是否畅通等。
对于第一次使用或长时间未使用的设备,还需要进行清洁和润滑。
2. 实训操作流程1) 启动设备:按照设备说明书的要求,正确启动电火花加工机。
2) 刀具加工准备:选择合适的刀具,并根据加工要求进行装夹和校准。
3) 工件装夹:根据加工要求,将待加工工件固定在工作台上,保证工件的稳定性和精度要求。
4) 加工参数设置:根据材料性质和加工要求,合理设置加工参数,包括放电电流、脉冲时间、电极形状等。
5) 进行加工:按照操作要求,进行电火花加工过程,同时注意监控加工质量和处理异常情况。
6) 工件拆卸与清洁:加工完成后,将工件从工作台上拆卸下来,进行清洁和检查。
3. 实训经验总结通过本次实训,我们进一步了解了电火花加工的原理和操作过程,锻炼了实际操作能力。
在实际操作过程中,我们也总结了一些实用经验,供今后参考:- 在选择刀具时,要综合考虑材料的硬度、加工要求、工件形状等因素。
- 加工过程中,定期检查液体供给系统和滤网的工作状态,保持正常的液体流动。
- 不同材料对应不同的加工参数,需要根据实际情况进行调整。
电火花实训报告

电火花实训报告[日期][实训名称][实训时间][实训地点]一、实训概述本次实训旨在让学员通过实际操作,掌握电火花加工技术的相关知识和技能,提高其在工业制造领域的应用能力。
在实训过程中,我们深入学习了电火花加工的原理、设备的使用方法、预防安全事故的措施等内容。
二、实训内容1. 电火花加工原理电火花加工是一种利用电弧放电的高温高能量特性进行金属加工的方法。
通过在工件表面形成电火花放电,使工件材料在瞬间受到高温高压作用,熔化或气化,最终实现对工件的加工目的。
2. 设备操作与调试在实训过程中,我们首先学习了电火花加工设备的基本组成和功能,包括主轴、电极、电源等部件的作用和使用方法。
然后,通过调试设备,我们学会了选择合适的放电参数、设置加工路径和切削速度等操作技巧。
3. 加工实例演练为了更好地掌握电火花加工技术,我们还进行了一系列的加工实例演练。
通过实际操作,我们学会了如何选择合适的加工电极、加工工艺和参数等,并在实验过程中不断调整和改进,使加工效果达到最佳状态。
三、实训成果经过一段时间的学习和实践,我们在电火花加工技术方面取得了显著的进步和成果。
以下是我们在实训中取得的几个关键成果:1. 掌握了电火花加工的基本原理和操作技巧,能够独立完成一般工件的加工。
2. 学会了根据加工要求选择合适的电极材料和形状,提高了加工效果和工件质量。
3. 能够熟练操作电火花加工设备,并能够根据加工需求进行参数设置和调试。
4. 实践中探索和应用了一些创新的加工方法和技巧,提高了工作效率和质量。
四、实训感悟通过这次电火花实训,我们不仅掌握了相关知识和技能,还深刻体会到了实践的重要性。
以下是我们在实训中所得到的几点感悟:1. 实践是掌握技能的关键。
只有通过实际操作,我们才能真正理解和掌握电火花加工的技术要点。
2. 安全第一,严格遵守操作规程和安全标准。
电火花加工是一项高风险的工作,我们必须时刻保持警惕,确保自身和他人的安全。
3. 不断学习和探索创新是提高加工水平的关键。
电火花加工实训指导书.docx

电火花加工实训指导书一、目的及要求通过对数控电火花加工的实际观看与上手操作,使学生深刻理解电火花的加工原理,熟悉数控电火花设备构成及其技术范围,了解电火花加工工件的过程和进行初步操作。
要求如下:1、止确阐述电火花加工的原理;2、熟悉数控电火花设备各组成部分,了解如何使用和操作;3、了解所用电火花设备的技术规范;4、了解电极材料的选择和如何考虑电极损耗;5、初步掌握工件与电极的装夹定位方法;6、了解基本数控操作。
二、实训内容1、了解SPI型数控电火花成形机由哪些部分组成,各部分的用途及操作方法;2、了解各种电极材料的加工性能、各种电极结构、粗/精加工电极的获得以及平动电极加工;3、了解电极的加工与修复;4、了解设备粗、中、精加工电规准情况和选用方法;5、了解设备各项技术规范;6、了解工作液的选用、工作液过滤循环装置;7、动手操作并初步掌握对工件和电极的装夹与定位;8、动手操作并初步掌握工件加工方法。
三、实训课时:6学时四、电火花设备操作步骤现以加工某冲压级进模的卸料板的凸模固定台阶孔为例(后附卸料板零件图)。
操作步骤:1、读图,充分理解零件加工要求。
该工件事先已加工穿通2—①8.0孔,要求采用电火花加工该处两个台阶孔2—①10.8深3.5;2、明确电极采用紫铜材料。
分粗、精两步加工;粗加工放电一次,精加工放电3次(要求较高的可放电6次以上);3、确定粗、精加工电规准条件;图1操纵面板显示的半精加工电规准案例图2操纵面板显示的精加工电规准案例4、 正确安装工件。
擦拭干净工作台面、工件各基准面及加工表面后,把工件 放置在工作台上。
进行工件的X 向、Y 向找止,在此过程中利用百分表 并结合铜棒轻轻敲击,找止工件位置。
找止完毕,将工件牢固固定;5、 正确安装电极。
初步安装电极后,作电极X 向、Y 向垂直找正,即工具 电极与工作台的垂直找止。
令方分表触头沿着电极Z 向移动,旋动工具 电极夹具旋钮进行微量调整,找止后将电极锁紧固定;6、 找正加工基准。
电火花加工实训报告

电火花加工实训报告电火花加工是现代制造业中的重要加工技术,因其高精度、高效率、大批量加工和可加工任何导电材料的优势而被广泛应用。
在本次实训之前,我对电火花加工只是听过一些概念和看过一些图片,对于具体操作流程和技术原理并不了解。
通过本次实训,我深入了解了电火花加工的操作流程、操作控制、应用范围以及影响加工质量的因素。
1. 实训操作流程第一步,下载加工图纸和NC程序,导入加工机床中。
通过加工机床的操作系统进行参数配置、工装装夹、刀具安装等操作。
第二步,通过底部辅助电极进行工件的定位和磁性吸附。
第三步,进行初始点、等高线和加工路径的设置,以及放电参数的配置。
第四步,开始加工,控制电极和工件之间的距离,通过电极和工件之间的放电产生电火花进行加工,通过喷水冷却来降低加工温度。
第五步,加工完成后,将工件卸载并进行清洁。
2. 实训操作控制在实际操作中,加工工艺参数的控制非常重要。
例如,加工深度、电极和工件之间的距离、放电脉冲持续时间、喷水量等因素都会影响加工质量和效率。
在操作过程中,需要不断调整这些参数,以达到最佳的加工效果。
同时,加工过程中还需要进行机床的数控程序调整、工件的定位和磁性吸附、电极的选择等操作。
3. 实训应用范围电火花加工是一种高精度、高效率、可以加工特殊材料的金属切削技术,因此在制造业中有着广泛的应用范围。
例如,电子元器件、精密仪器、模具等领域都需要使用电火花加工技术进行生产。
此外,汽车、航空航天等行业也需要利用电火花加工技术进行高精度加工。
4. 实训影响加工质量的因素在实际操作中,如果处理不当,会影响加工质量和效率。
例如,电极的选择、清洁度、磨损情况、放电状态和冷却状态、工件和加工机床的磁性吸附等因素都可能影响加工质量和效率。
因此,在操作过程中需要密切关注这些因素,及时调整操作参数和操作方式,以获得最佳的加工效果和最高的加工质量。
综上所述,电火花加工是现代制造业中不可或缺的一环,掌握电火花加工技术对于提高现代制造业的生产质量和效率非常重要。
数控电火花加工实训要点

项目26 数控电火花加工26.1任务描述在工件上加工一个矩形腔,如图26-1所示。
底面和侧面的表面粗糙度要求为Ra2.0µm,工件材料为45钢,电极材料为纯铜,要求加工时损耗、效率兼顾。
图26-1 方孔形工件26.2 知识链接26.2.1 数控电火花加工简介1.数控电火花加工原理电火花加工的原理是基于工具电极和工件(正、负电极)之间脉冲性火花放电时的电腐蚀现象来蚀除多余的金属,以达到对零件的尺寸、形状及表面质量预定的加工要求。
如图26-2所示,工具电极与工件分别与高频脉冲电源的两输出端相连接,主轴进给机构使工具电极与工件间经常保持一很小的放电间隙,且工具电极与工件间充满工作液。
当脉冲电压加到两极之间,便在当时条件下相对某一间隙最小处或绝缘强度最低处击穿介质,在该局部产生火花放电,瞬时高温使电极和工件表面都蚀除掉一小部分金属,各自形成一个小凹坑。
脉冲放电结束后,经过一段间隔时间(即脉冲间隔),使工作液恢复绝缘后,第二个脉冲电压又加到两极上,又会在当时极间距相对最近或绝缘强度最弱处击穿放电,又电蚀出一个小坑。
这样随着相当高的频率,连续不断地重复放电,工具电极不断地向工件进给,就可将工具电极的形状复制在工件上,加工出所需要的零件,整个加工表面将由无数个小凹坑所组成。
图26-2 电火化加工的基本原理2.数控电火花成型机床的组成数控电火花成型机床主要由机床主体部分、脉冲电源、自动进给调节系统、工作液净化及循环系统等几部分组成。
如图26-3所示为北京阿奇夏米尔SE 系列数控电火花机床的外观及其各部分的构成。
图26-3 机床的外观图及其组成3.数控电火花加工的特点与应用 1)数控电火花加工的特点电火花加工是一种直接利用电能和热能进行加工的新工艺,具有以下优点和缺点: (1)电火花加工的优点①电火花加工是靠放电的电热作用实现的,其加工性主要取决于材料的热学性能,如熔点、比热容、热导率等。
因此不受工件材质的硬度及韧性限制,只要导电就可以加工,如淬火钢、硬质合金钢、耐热合金钢等。
数控电火花实习报告
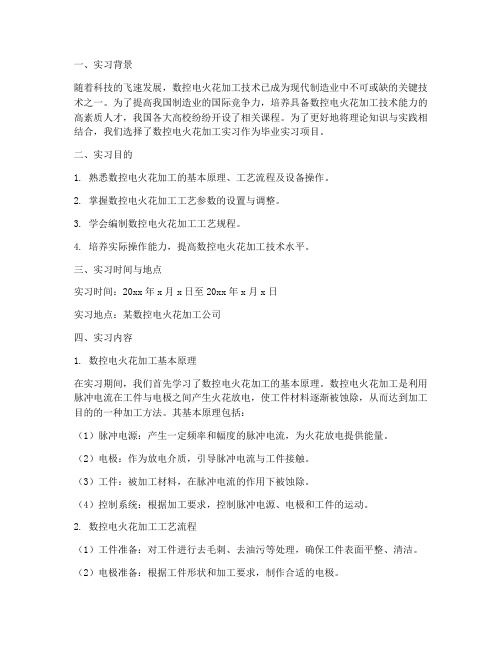
一、实习背景随着科技的飞速发展,数控电火花加工技术已成为现代制造业中不可或缺的关键技术之一。
为了提高我国制造业的国际竞争力,培养具备数控电火花加工技术能力的高素质人才,我国各大高校纷纷开设了相关课程。
为了更好地将理论知识与实践相结合,我们选择了数控电火花加工实习作为毕业实习项目。
二、实习目的1. 熟悉数控电火花加工的基本原理、工艺流程及设备操作。
2. 掌握数控电火花加工工艺参数的设置与调整。
3. 学会编制数控电火花加工工艺规程。
4. 培养实际操作能力,提高数控电火花加工技术水平。
三、实习时间与地点实习时间:20xx年x月x日至20xx年x月x日实习地点:某数控电火花加工公司四、实习内容1. 数控电火花加工基本原理在实习期间,我们首先学习了数控电火花加工的基本原理。
数控电火花加工是利用脉冲电流在工件与电极之间产生火花放电,使工件材料逐渐被蚀除,从而达到加工目的的一种加工方法。
其基本原理包括:(1)脉冲电源:产生一定频率和幅度的脉冲电流,为火花放电提供能量。
(2)电极:作为放电介质,引导脉冲电流与工件接触。
(3)工件:被加工材料,在脉冲电流的作用下被蚀除。
(4)控制系统:根据加工要求,控制脉冲电源、电极和工件的运动。
2. 数控电火花加工工艺流程(1)工件准备:对工件进行去毛刺、去油污等处理,确保工件表面平整、清洁。
(2)电极准备:根据工件形状和加工要求,制作合适的电极。
(3)工艺参数设置:根据工件材料、加工精度、加工表面粗糙度等要求,设置合适的加工参数。
(4)装夹工件与电极:将工件和电极安装到数控电火花加工机上。
(5)编程与调试:编写数控程序,对加工过程进行调试。
(6)加工:启动数控电火花加工机,进行加工。
(7)检验:对加工后的工件进行检验,确保加工精度和表面质量。
3. 数控电火花加工工艺参数设置与调整在实习过程中,我们学习了如何设置和调整数控电火花加工工艺参数。
主要包括:(1)脉冲宽度:控制火花放电时间的长短,影响加工速度和表面质量。
数控电火花实验报告
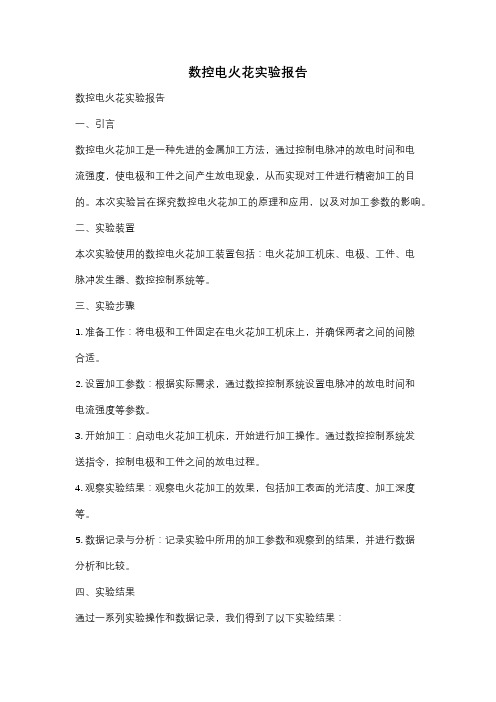
数控电火花实验报告数控电火花实验报告一、引言数控电火花加工是一种先进的金属加工方法,通过控制电脉冲的放电时间和电流强度,使电极和工件之间产生放电现象,从而实现对工件进行精密加工的目的。
本次实验旨在探究数控电火花加工的原理和应用,以及对加工参数的影响。
二、实验装置本次实验使用的数控电火花加工装置包括:电火花加工机床、电极、工件、电脉冲发生器、数控控制系统等。
三、实验步骤1. 准备工作:将电极和工件固定在电火花加工机床上,并确保两者之间的间隙合适。
2. 设置加工参数:根据实际需求,通过数控控制系统设置电脉冲的放电时间和电流强度等参数。
3. 开始加工:启动电火花加工机床,开始进行加工操作。
通过数控控制系统发送指令,控制电极和工件之间的放电过程。
4. 观察实验结果:观察电火花加工的效果,包括加工表面的光洁度、加工深度等。
5. 数据记录与分析:记录实验中所用的加工参数和观察到的结果,并进行数据分析和比较。
四、实验结果通过一系列实验操作和数据记录,我们得到了以下实验结果:1. 放电时间对加工效果的影响:在一定范围内,放电时间的延长可以增加加工深度,但过长的放电时间可能导致加工表面的烧伤和变形。
2. 电流强度对加工效果的影响:适当增加电流强度可以提高加工速度和效率,但过高的电流强度可能引起电极和工件的烧蚀和损坏。
3. 电极材料的选择:不同材料的电极对加工效果有一定影响。
例如,铜电极适用于加工硬度较低的材料,而钼电极适用于加工硬度较高的材料。
4. 工件材料的选择:不同材料的工件对加工效果也有一定影响。
例如,对于硬度较高的工件,需要选择合适的加工参数和电极材料,以确保加工质量。
五、实验讨论根据实验结果,我们可以得出以下结论和讨论:1. 数控电火花加工是一种高精度、高效率的金属加工方法,广泛应用于模具制造、航空航天等领域。
2. 在进行数控电火花加工时,需要根据实际情况选择合适的加工参数,以确保加工质量和效率。
3. 电极和工件的选择对加工效果有重要影响,需要根据材料的硬度和特性选择合适的电极和工件材料。
实训3数控电火花慢走丝线切割加工.doc
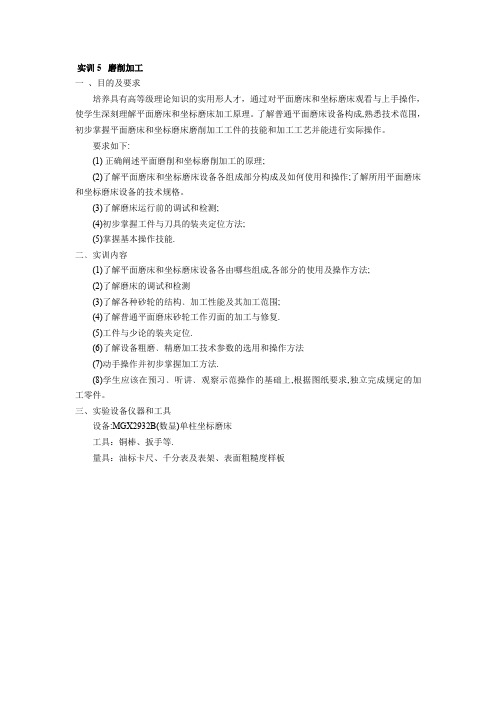
实训5 磨削加工一、目的及要求培养具有高等级理论知识的实用形人才,通过对平面磨床和坐标磨床观看与上手操作,使学生深刻理解平面磨床和坐标磨床加工原理。
了解普通平面磨床设备构成,熟悉技术范围,初步掌握平面磨床和坐标磨床磨削加工工件的技能和加工工艺并能进行实际操作。
要求如下:(1) 正确阐述平面磨削和坐标磨削加工的原理;(2)了解平面磨床和坐标磨床设备各组成部分构成及如何使用和操作;了解所用平面磨床和坐标磨床设备的技术规格。
(3)了解磨床运行前的调试和检测;(4)初步掌握工件与刀具的装夹定位方法;(5)掌握基本操作技能.二﹑实训内容(1)了解平面磨床和坐标磨床设备各由哪些组成,各部分的使用及操作方法;(2)了解磨床的调试和检测(3)了解各种砂轮的结构﹑加工性能及其加工范围;(4)了解普通平面磨床砂轮工作刃面的加工与修复.(5)工件与少论的装夹定位.(6)了解设备粗磨﹑精磨加工技术参数的选用和操作方法(7)动手操作并初步掌握加工方法.(8)学生应该在预习﹑听讲﹑观察示范操作的基础上,根据图纸要求,独立完成规定的加工零件。
三、实验设备仪器和工具设备:MGX2932B(数显)单柱坐标磨床工具:铜棒、扳手等.量具:油标卡尺、千分表及表架、表面粗糙度样板四﹑坐标磨床实习步骤(一)坐标磨床的认识1﹑坐标磨床外观及构成坐标磨床适用于具有高精度坐标孔距离要求,并经淬火后的直孔锥孔平面的磨削加工。
坐标磨床的主要系统:传动系统;定位测量系统;润滑系统;电气系统.2﹑数显表盘3﹑技术数据表1MGX2932B(数显)单柱坐标磨床主要技术数据。
表14、操作规程(1)被加工零件、所需的测量工具等应预先放于恒温室内等温,然后才能够加工:(2)被加工零件不要直接与工作台面接触,以防损坏工作台面;(3)磨头所用润滑油必须经过精细的过滤.(4)磨削工作进行前,热补偿电源接通补得少于4小时.热补偿电源需要长期通电;(5)当使用高速磨头磨削时,应使用防护罩板并特别注意安全.(二)、上机操作步骤1、开机操作机床在启动时,首先应将电气箱上的电源纵开拔至接通位置,此时信号灯亮,然后打开气源,并调整压力至规定的数值。
- 1、下载文档前请自行甄别文档内容的完整性,平台不提供额外的编辑、内容补充、找答案等附加服务。
- 2、"仅部分预览"的文档,不可在线预览部分如存在完整性等问题,可反馈申请退款(可完整预览的文档不适用该条件!)。
- 3、如文档侵犯您的权益,请联系客服反馈,我们会尽快为您处理(人工客服工作时间:9:00-18:30)。
项目26 数控电火花加工26.1任务描述在工件上加工一个矩形腔,如图26-1所示。
底面和侧面的表面粗糙度要求为Ra2.0µm,工件材料为45钢,电极材料为纯铜,要求加工时损耗、效率兼顾。
图26-1 方孔形工件26.2 知识链接26.2.1 数控电火花加工简介1.数控电火花加工原理电火花加工的原理是基于工具电极和工件(正、负电极)之间脉冲性火花放电时的电腐蚀现象来蚀除多余的金属,以达到对零件的尺寸、形状及表面质量预定的加工要求。
如图26-2所示,工具电极与工件分别与高频脉冲电源的两输出端相连接,主轴进给机构使工具电极与工件间经常保持一很小的放电间隙,且工具电极与工件间充满工作液。
当脉冲电压加到两极之间,便在当时条件下相对某一间隙最小处或绝缘强度最低处击穿介质,在该局部产生火花放电,瞬时高温使电极和工件表面都蚀除掉一小部分金属,各自形成一个小凹坑。
脉冲放电结束后,经过一段间隔时间(即脉冲间隔),使工作液恢复绝缘后,第二个脉冲电压又加到两极上,又会在当时极间距相对最近或绝缘强度最弱处击穿放电,又电蚀出一个小坑。
这样随着相当高的频率,连续不断地重复放电,工具电极不断地向工件进给,就可将工具电极的形状复制在工件上,加工出所需要的零件,整个加工表面将由无数个小凹坑所组成。
图26-2 电火化加工的基本原理2.数控电火花成型机床的组成数控电火花成型机床主要由机床主体部分、脉冲电源、自动进给调节系统、工作液净化及循环系统等几部分组成。
如图26-3所示为北京阿奇夏米尔SE 系列数控电火花机床的外观及其各部分的构成。
图26-3 机床的外观图及其组成3.数控电火花加工的特点与应用 1)数控电火花加工的特点电火花加工是一种直接利用电能和热能进行加工的新工艺,具有以下优点和缺点: (1)电火花加工的优点①电火花加工是靠放电的电热作用实现的,其加工性主要取决于材料的热学性能,如熔点、比热容、热导率等。
因此不受工件材质的硬度及韧性限制,只要导电就可以加工,如淬火钢、硬质合金钢、耐热合金钢等。
②其加工是非接触式加工,只是电能的作用,故加工中无明显的作用力。
当然不能忽略在加工面积较大时,由冲油以及抬刀形成的液压力。
③可以加工特殊及复杂形状的零件。
一是由于加工中无切削力,可以加工低刚度工件及主轴进给伺服机构 (伺服机构)脉冲电流高频脉冲电源加工槽工作液 (危险物)电极工作台 机床本体工件 供电盘电柜主轴箱 滑枕床身液槽手控盒键盘底座油箱微细加工,如各种小孔、深孔、窄缝零件(尺寸可以是几微米);二是由于可以简单地将工具电极的形状复制到工件上,因此特别适用于复杂表面形状工件的加工,如复杂型腔模具的加工;另外,数控电火花加工可以用简单形状的工具电极加工复杂形状的零件。
④工艺灵活性大。
本身有“正极性加工”和“负极性加工”之分;可与其他工艺结合,形成复合加工,如与电解加工结合;可以改革工件结构,多种型腔可整体加工,提高零件的加工精度,降低工人劳动强度;可在淬火后进行,免去了工件热变形的修正问题。
⑤便于实现加工过程自动控制。
⑥利用数控功能可显著扩大应用范围。
如水平加工、锥度加工、多型腔加工,采用简单电极进行三维型面加工,利用旋转主轴进行螺旋面加工。
⑦加工表面微观形貌圆滑,工件的棱边、尖角处无毛刺、塌边。
(2)电火花加工的缺点①一般只能加工金属等导电材料。
②加工速度一般较慢,效率较低。
③存在电极损耗。
④电蚀产物在排除过程中与工具电极距离太小时会引起二次放电,形成加工斜度,影响加工精度。
⑤最小角部半径有限制。
一般电火花加工能得到的最小角部半径等于加工间隙(通常为0.02~0.03mm),若电极有损耗或采用平动加工、摇动加工,则角部半径还要增大。
2)数控电火花加工的应用①加工模具。
如冲模、锻模、塑料模、拉伸模、压铸模、挤压模、玻璃模、胶木模、陶土模、粉末冶金烧结模、花纹模等等。
②航空、宇航等部门中高温合金等难加工材料的加工。
例如喷气发动机的涡轮叶片和一些环形件上,大约需要一百万个冷却小孔,其材料为又硬又韧的耐热合金,电火花加工是合适的工艺方法。
③微细精密加工,通常可用于0.01~1mm范围内的型孔加工,如化纤异型喷丝孔、发动机喷油嘴等。
④加工各种成形刀具、样板、工具、量具、螺纹等成形零件。
1201.电火花加工的主要工艺指标1)加工速度加工速度是指在单位时间内,工件被蚀除的体积或重量,也称为加工生产率,一般用体积表示。
若在时间t内,工件被蚀除的体积为V,则加工速速U W为U W=V/t在规定的表面粗糙度、规定的相对电极损耗下的最大加工速度,是衡量电加工机床工艺性能的重要指标。
一般情况下,生产厂家给出的加工速度是以最大加工电流,在最佳加工状态下所能达到的最高加工速度。
因此,在实际加工时,由于被加工件尺寸与形状的千变万化,加工条件、排屑条件等与理想状态相差甚远,即使在粗加工时,加工速度也往往大大低于机床的最大加工速度指标。
影响加工速度的主要因素有脉冲宽度、脉冲间隔、峰值电流、排屑条件、加工面积、电极材料及加工极性等因素。
2)电极损耗在电火花加工中,工具电极损耗直接影响加工精度,特别对于型腔加工,电极损耗这一工艺指标较加工速度更为重要。
电极损耗分为绝对损耗和相对损耗。
绝对损耗最常用的是体积损耗V e 和长度损耗V eh 两种方式,他们分别表示在单位时间内,工具电极被蚀除的体积和长度,即V e =V /t V eh =H /t相对损耗是工具电极绝对损耗与工件加工速度的百分比。
通常采用长度相对损耗比较直观,测量也比较方便。
电火花加工中,工具电极的不同部位,其损耗的速度也不相同。
一般尖角的损耗比钝角快,角的损耗比棱快,棱的损耗比面快,而端面的损耗比侧面快,端面的侧缘损耗比端面的中心部位快。
对工具电极损耗的影响因素有脉冲宽度、脉冲间隔、峰值电流、加工极性、加工面积、冲油或抽油的大小、电极材料、工作液等。
3)表面粗糙度表面粗糙度是指加工表面上的微观几何形状误差。
对电加工表面来讲,即加工表面放电痕——坑穴的聚集。
由于坑穴表面会形成一个加工硬化层,而且能存润滑油,其耐磨性比同样粗糙度的机加表面要好,所以加工表面允许比要求的粗糙度大些。
而且在相同粗糙度的情况下,电加工表面比机加工表面亮度低。
工件的电火花加工表面粗糙度直接影响其使用性能,如耐磨性,配合性质,接触刚度,疲劳强度和抗腐蚀性等。
尤其对于高速、高洁、高压条件下工作的模具和零件,其表面粗糙度往往是决定其使用性能和使用寿命的关键。
影响表面粗糙度的主要因素有脉冲宽度、峰值电流、电极的材料及加工极性等。
4)表层变化电火花加工过程中,在火花放电局部的瞬时高温高压下,煤油中分解的炭颗粒渗入工件表层,又在工作液的快速冷却下,材料的表面层发生了很大变化,可粗略地把它分为熔化凝固层和热影响层,如图26-4所示。
另外,还会在熔化层(白层)内出现显微裂纹,当脉冲能力很大时,显微裂纹也会扩展到热影响层,而影响零件的耐磨性、耐疲劳性等。
5)加工精度电火花加工精度主要包括尺寸精度和形状精度。
尺寸精度是指电火花加工完成后各部位尺寸值的准确程度,如加工深度的尺寸精度。
形状精度是指电火花加工完成部位的形状与加工要求形状的符合情况。
影响加工精度的主要因素有脉冲宽度、峰值电流、电压及加工的稳定性等。
2.数控电火花加工的工艺方法数控电火花加工工艺方法的内容较多,主要有单电极直接成形工艺、多电极更换成形工艺、分解电极成形工艺、数控摇动成形工艺、数控多轴联动成形工艺等。
选择时要根据工件1图26—4 电火花加工的工件表面层放大图 1、熔化凝固层 2、热影响层 3、未受影响基体层132成形的技术要求、复杂程度、工艺特点、机床类型及脉冲电源的技术规格、性能特点而定。
3.电极材料的选择在电火花加工中,工具电极是一项非常重要的因素,电极材料的性能将影响电极的电火花加工性能(材料去除率、工具损耗率、工件表面质量等),因此,正确选择电极材料对于电火花加工至关重要。
电火花加工用工具电极材料应满足高熔点、低热胀系数、良好的导电导热性能和力学性能等基本要求,从而在使用过程中具有较低的损耗率和抵抗变形的能力。
现在广泛使用的电极材料主要有以下几种:1)纯铜:纯铜是目前在电加工领域应用最多的电极材料。
具有塑性好、电极成形容易(可机械加工成形、锻造成形、电铸成形、电火花线切割成形等)、加工稳定性好、加工表面质量高等优点,但其熔点低(1083°C)、热膨胀系数较大等缺点。
适合较高精度模具的电火花加工,如加工中、小型型腔,花纹图案,细微部位等。
2)石墨:石墨也是电火花加工中常用材料,其具有价格较便宜、密度小、、良好的机械加工性能和导电性能好、熔点高(3700°C)、加工效率高、在大电流的情况下仍能保持电极的低损耗等优点;但在精加工中放电稳定性较差,容易过渡到电弧放电,只能选取损耗较大的加工条件来加工;加工微细面表面粗糙度略差,在加工中容易脱落、掉渣,不能用于镜面加工。
适合加工蚀除量较大的型腔,如大型的塑料模具、锻模、压铸模等。
另外,其热变形小,特别适合加工精度要求高的深窄缝条。
3)钢:钢电极使用的情况较少,在冲模加工中,可以直接用冲头作电极加工冲模。
但与纯铜及石墨电极相比,加工速度、电极消耗率等方面均较差。
4)铜钨、银钨合金:用铜钨(Cu-W)及银钨(Ag-W)合金电极加工钢料时,特性与铜电极倾向基本一致,但由于价格很高,所以大多只用于加工硬质合金类耐热性材料。
除此之外还用于在电加工机床上修整电极用,此时应用正极性。
4.数控电火花加工电参数的确定电火花加工的主要电参数为脉冲峰值电流、脉冲宽度和脉冲间隔三大电参数,这三大电参数决定了放电加工的能量,对加工生产率、表面粗糙度、放电间隙、电极损耗、表面变质层、加工稳定性等各方面的工艺效果有重要影响,如表26-1所示。
表26-1 三大电参数对工艺指标的影响数控电火花机床一般都有用于各种加工的成套电参数,并将一组电参数用一个条件号来表示,因此选用电参数时可以直接调用条件号。
下面以北京阿奇夏米尔SE系列数控电火花机床为例讲解条件号和工艺留量的确定方法:(1)确定第一个加工条件可根据投影面积的大小和工艺组合,由加工参数表26-2、表26-3和表26-4来选择第一个加工条件。
查表时要区分工艺要求是低损耗,还是标准,还是高效率的要求分别查表26-2、表26-3和表26-4。
表26-2 铜打钢—最小损耗参数表表26-3铜打钢—标准型参数表表26-4 铜打钢—最大去除率型参数表(2)确定最终加工条件根据最终表面粗糙度要求Ra查表26-2、表26-3和表26-4确定最终加工条件。
(3)确定中间加工条件全选第一个加工条件至最终加工条件间的全部加工条件。
(4)确定每个加工条件的底面留量最后一个加工条件之前的底面留量按所选加工条件的安全间隙M的一半留取,最后一个加工条件按本条件的放电间隙的一半留取。