注射模设计说明
支撑板注射模的设计

中 图 分 类 号 :G124 T 6. 文献 标识 码 : A
1设计 背 景及 目的 如 图所 示为 支撑 板 的 三维 视 图 ,材 料 为 P C, 度 等级 为 一 般 精 度 ( 级 精 度 )生 产 V 精 5 , 批 量为 大艺 性分 析 . 零 件壁 厚基 本 均匀 ,所 有 厚度 都 大于 塑 件 的最 小 壁厚 0 m . m,注 射成 型 时 应该 不 会 8 出现填 充不 足现 象 。 塑件 侧壁 有两 个 型孔 , 故 注射 成 型模 应具 有侧 抽 芯机 构 。 2 初选 注射 成型 机 的型 号和 规格 . 2 初 选 额 定 注 射 量 在 15 以上 的 卧 式 注 2 射成 型 机型 号 X — Y 15 S Z 一 2 23注射 成 型的基 本 过程 . 注 射成 型是 把 塑料 原 料 ( 一般 为 经过 造 粒、 色、 染 加入 添 加 剂 等 处 理后 的颗 粒 料 ) 防 入料 筒 中 , 过 加热 熔化 , 之 成 为高 粘度 的 经 使 流体 一 为“ 体 ”用柱 塞或 螺 杆作 为 加压 工 称 熔 , 具 ,使熔 体 通过 喷 嘴 以较 高 的压力 注 入模 具 的型 腔 中 , 过 冷却 、 固 阶段 , 经 凝 而后 从 模 具 中脱 出 , 为塑 料制 品 。 成 2 确定 模具 的基 本 结构 . 4 经 过分 析 可知 ,该 塑件 成 型 是必 须采 用 侧 向外 抽芯 , 能适 合 的模 具 结构 有 两种 , 可 即 单 分 型 面 注射 成 型 模 和 双 分 型 面 注 射 成 型 模。 方 案 一 :单 分 型 面注 射 成型 模 型腔 在 定 模上 ; 流道 设在 定模 一 侧 , 流道 设在 分 主 分 型面上 ,开 模后 塑 件 和浇 注 系统 流道 内的凝 料 一起 留在 动模 一 侧 ; 上设 有 顶 出机 构 , 动模 用 以顶 出 塑料 和 流道 里 的凝 料 ,可能 的浇 口 形 式有 : 接浇 口 、 直 侧浇 口 、 形浇 口 、 扇 重叠 式 浇 口和潜伏 式 浇 口等 。该 类模 具 采用 的侧 抽 芯机 构一 般是 斜 导柱 抽芯 机 构 ( 斜导 柱 在定 模, 滑块 在 动模 )斜滑 块抽 芯 机构 、 销 抽芯 、 弯 机构 和斜 导槽 抽芯 机构 。 单 型 腔注 射模 的优点 :塑件 的形 状 和尺 寸始终 一致 ,如生 产 的塑 件要 求 很小 的尺寸 公 差 时 , 用单 型 腔注 射模 具 也许 更 适合 ; 采 单 型腔 注射模 具 只须 根 据一 个 塑件 调整 成 型工 艺条 件 , 以工 艺参 数 易 于控 制 ; 型腔 注射 所 单 模 具 的推 出 机构 、冷 却 系统 和分 型 面 的技术 要求 ,在 大 多数情 况 下均 能 满足 而 不必 综合 考 虑 ; 型腔 注射 模 的制造 成本 低 , 短 。 单 周期 方案 二 : 型 面注射 成 型模 。 双分 它从 不 同 的分 型 面分 别 取 出 塑件 和 流 道 内 的凝 料 , 又
5号电池充电器外壳的塑件注射模毕业设计说明书
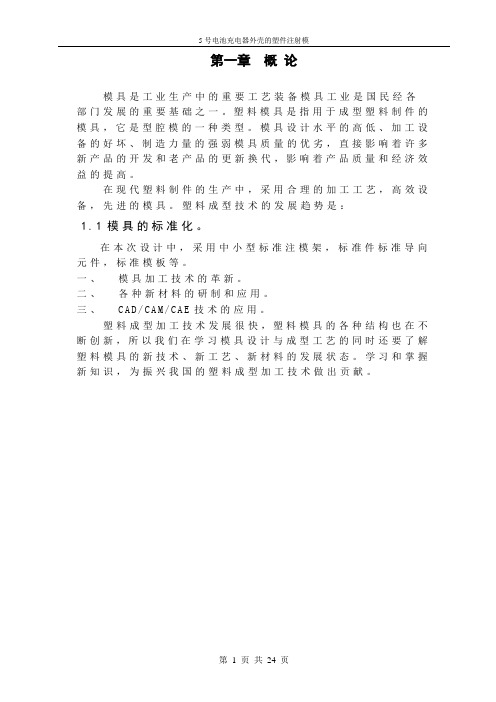
第一章概论模具是工业生产中的重要工艺装备模具工业是国民经各部门发展的重要基础之一。
塑料模具是指用于成型塑料制件的模具,它是型腔模的一种类型。
模具设计水平的高低、加工设备的好坏、制造力量的强弱模具质量的优劣,直接影响着许多新产品的开发和老产品的更新换代,影响着产品质量和经济效益的提高。
在现代塑料制件的生产中,采用合理的加工工艺,高效设备,先进的模具。
塑料成型技术的发展趋势是:1.1模具的标准化。
在本次设计中,采用中小型标准注模架,标准件标准导向元件,标准模板等。
一、模具加工技术的革新。
二、各种新材料的研制和应用。
三、C A D/C A M/C A E技术的应用。
塑料成型加工技术发展很快,塑料模具的各种结构也在不断创新,所以我们在学习模具设计与成型工艺的同时还要了解塑料模具的新技术、新工艺、新材料的发展状态。
学习和掌握新知识,为振兴我国的塑料成型加工技术做出贡献。
第 1 页共24 页第二章设计任务书2.1设计题目本次设计的题目是5号电池充电器外壳的注射模设计。
2.2设计任务书1.一套产品零件图;2.模具总装配图一张(A1图纸);3.所有非标准件图纸;4.模具主要成型零件的加工工艺(凹模、凸模、型芯);5.说明书一份。
说明:所有图纸和说明书一律用计算机打印,严格按照要求完成设计。
第2页共24 页第三章产品零件的工艺分析3.1塑件分析初步了解毕业设计的内容——5号电池充电器外壳。
分析零件的产品图,研究其尺寸、公差、技术要求等。
初步拟订设计方案。
此产品是充电器外壳,所以在设计时要注意其表面的粗糙度,要使表面光滑,达到效果。
零件采用三向侧抽芯成型。
塑件的尺寸精度要求一般。
由于塑件表面光滑度较高,因此塑件采用潜伏浇口。
此塑件的零件图如下图(图1—1)图1—13.2 塑件的成型特性3.2.1 对零件的分析得塑件材料取A B S(丙烯腈-丁二-苯乙烯共聚物)。
第 3 页共24 页3.2.2ABS的基本特性1 ABS良好的综合力学性能,耐化学腐蚀性及表面硬度、韧性强,有良好的加工性和染色性能。
注塑模具设计说明书

数码相机盖模具设计说明书班级:10材料专业:材料成型及控制工程姓名:刘树飞学号:100118019指导老师:引言 (2)一.产品工艺性分析 (3)1.1设计产品概述 (3)1.2产品工艺性分析 (3)二、注塑机的选择 (3)1、塑件的质量、体积计算 (4)2、浇注系统凝料体积的初步估算 (4)3、注射容量与锁模力校核 (4)(1)注射容量校核 (4)(2)锁模力的校核 (4)4.利用UG软件,设置工件尺寸。
(4)三、分型设计 (5)四、标准模架的选用 (6)(1)先定系列。
(6)(2)看型芯固定方式是否需要加支撑板。
(6)(3)确定模板尺寸。
(6)(4)模架厚度 (6)五、模具滑块设计 (6)(1)抽芯距离和抽芯力的计算 (6)(2)斜导柱设计 (7)①斜导柱倾斜角的确定 (7)②斜导柱的直径计算 (7)③斜导柱长度的计算 (7)④滑块其他零部件设计 (7)六、导向与顶出机构设计 (8)(1)顶出机构设计 (8)①脱模力计算 (8)②推出零件尺寸计算 (8)③创建顶管 (8)④创建拉料杆 (8)(2)导向机构的设计 (8)①导柱的选取 (8)②复位杆的选取 (9)七、浇注系统设计 (9)1.浇注系统整体方案确定 (9)2.主流道设计 (9)3、分流道、浇口和冷料穴设计 (9)八、冷却系统设计 (10)1、冷却水道的尺寸计算 (11)(1)计算单位重量的塑料熔体在凝固时所放出的热量Q1(kJ/kg) (11)(2)求冷却水的体积流量qv(m³/min) (11)(3)查表使冷却水处于紊流状态,取d (11)九、画模具装配图 (12)引言虽然受到全球金融危机影响,但是我国模具整体实力还是得到进一步加强。
近两年来中国的模具制造技术水平又有了新的提高。
从模具产品进出口的地域来看,华东地区的江苏、浙江、上海、山东均位列中国进口和出口模具的十大省市之中。
长江三角地区在模具制造整体水平的数量和质量上均已在国内处于行业重要位置。
多腔注塑模具设计说明
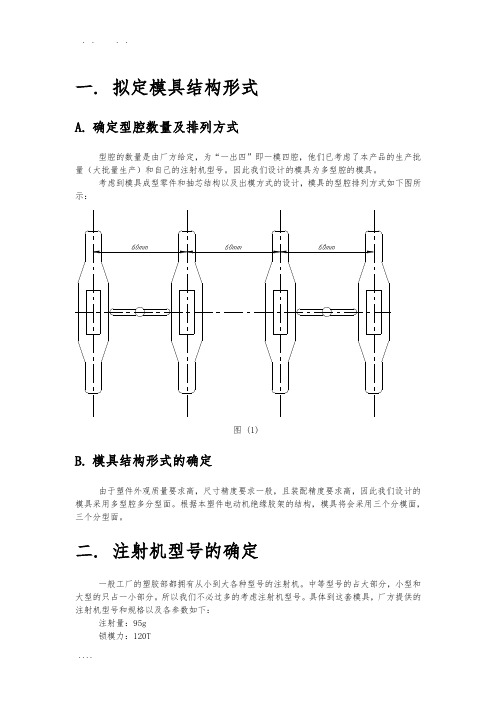
一.拟定模具结构形式A.确定型腔数量及排列方式型腔的数量是由厂方给定,为“一出四”即一模四腔,他们已考虑了本产品的生产批量(大批量生产)和自己的注射机型号。
因此我们设计的模具为多型腔的模具。
考虑到模具成型零件和抽芯结构以及出模方式的设计,模具的型腔排列方式如下图所示:图 (1)B.模具结构形式的确定由于塑件外观质量要求高,尺寸精度要求一般,且装配精度要求高,因此我们设计的模具采用多型腔多分型面。
根据本塑件电动机绝缘胶架的结构,模具将会采用三个分模面,三个分型面。
二.注射机型号的确定一般工厂的塑胶部都拥有从小到大各种型号的注射机。
中等型号的占大部分,小型和大型的只占一小部分。
所以我们不必过多的考虑注射机型号。
具体到这套模具,厂方提供的注射机型号和规格以及各参数如下:注射量:95g锁模力:120T模板大小:400×550开模距离:推出形式:推出位置:推出行程:三.分型面位置的确定如何确定分型面,需要考虑的因素比较复杂。
由于分型面受到塑件在模具中的成型位置、浇注系统设计、塑件的结构工艺性及精度、嵌件位置形状以及推出方法、模具的制造、排气、操作工艺等多种因素的影响,因此在选择分型面时应综合分析比较,从几种方案中优选出较为合理的方案。
选择分型面时一般应遵循以下几项原则:1)分型面应选在塑件外形最大轮廓处。
2)便于塑件顺利脱模,尽量使塑件开模时留在动模一边。
3)保证塑件的精度要求。
4)满足塑件的外观质量要求。
5)便于模具加工制造。
6)对成型面积的影响。
7)对排气效果的影响。
8)对侧向抽芯的影响。
其中最重要的是第5)和第2)、第8)点。
为了便于模具加工制造,应尽是选择平直分型面工易于加工的分型面。
如下图所示,采用A-A这样一个平直的分型面,前模(即定模)做成平的就行了,胶位全部做在后模(即动模),大简化了前模的加工。
A-A分型面也是整个模具的主分模面。
下图中虚线所示的B-B和C-C分型面是行位(即滑块)的分型面。
模具毕业设计58瓶盖注射模设计说明书

塑料模设计说明书系别:机械工程系专业:模具设计与制造班级:姓名:学号:指导老师:12月13日一、塑件工艺特性1、塑件所使用的材料的种类及工艺特性的分析:聚苯乙烯是通用热塑性塑料。
聚苯乙烯树脂是无色、透明并有光泽的非结晶型线型结构的高聚物。
其原料来源广泛,石油工业的发展促进了聚苯乙烯大规模的生产。
目前,它的产量仅次于聚乙烯和聚氯乙烯,居于第三位。
2、塑件的成型特点分析:聚苯乙烯成型性能优良,其吸水性小,成型前可不进行干燥;收缩小,制品尺寸稳定;比热容小,可很快加热塑化,且塑化量较大,故成型速度快,生产周期短,可进行高速注射;流动性好,可采用注射、挤出、真空等各种成型方法。
但注射成型时应防止淌料;应控制成型温度、压力和时间等工艺条件,以减少内应力。
3、塑件结构分析:从塑件外型看,总体为一个圆形阶梯壳体零件,表面要求光滑,并带圆弧,有较细长的排气孔和装配孔。
二、塑件的体积与质量的计算该产品材料为ps,查资料得知其密度为1.054 g/cm3,收缩率为0.6%~0.8%。
利用PRO/E计算得塑件的体积V=4.894cm3塑件质量:M=Vρ=1.054g/cm3×4.894cm3≈5.158g三、注塑机的确定根据原材料和塑料制件的各种参数,初定注射机的型号为:G54-S200/400,其有关参数如下:(参照教材表4.2)注塑机的最大注塑量:200~400cm3;螺杆直径:55mm注射压力:109MPa ;注射行程:160mm注射方式:螺杆式;锁模力:2540KN最大成型面积:645 cm3;最大开合模行程:260cm最大模厚:406mm ;最小模厚:165mm喷嘴圆弧半径:R18mm ;喷嘴孔直径:Ф4mm注塑机拉杆空间:290×368mm 动、定模固定尺寸:532×634mm四、注射模设计1、型腔的确定该塑料结构简单,采用的是一模两腔,为了实现各型腔均匀进料和达到同时充满型腔的目的,采用平衡式布局。
模具毕业设计20电器盒盖注射模设计说明书

一、塑件的成型工艺分析Ⅰ、塑件成型工艺性分析1.塑件(电器盒盖)分析1).塑件如图1-1所示。
2).塑件原图中有四处不详,如图所示:图1—1与指导老师商议后,将①处改为13.9mm;将②处增加一个尺寸取0.56mm;将③处增加两个尺寸取2.15mm(侧壁厚);将④处增加一个尺寸取1mm(底厚)。
3).塑件名称ABS(丙烯腈-丁二烯-苯乙烯共聚物)。
4).色调不透明,微黄色,成型的塑件有较好的光泽,经过调色可配成任何颜色。
5).生产纲领中等批量(20万件/年)。
6).塑件的结构及成型工艺性分析⑴结构分析如下①该塑件为电器盒盖,外表面要求光滑(采用一模一腔,在塑件外表面浇口处会有明显的注射痕迹)。
塑件属于薄壁类,成型时注射压力要求较高。
②该塑件外形是一长方形盒盖类零件,在一侧短边壁有长方形通孔。
⑵成型工艺分析如下①精度等级。
采用一般精度5级(塑件的精度取自由精度。
塑料制件的尺寸公差可依据SJ1372—78塑件公差数值标准进行设计。
查塑件公差数值表,可取该塑件的精度等级为5级。
由于模具尺寸精度比塑件尺寸精度高2—3级。
查标准公差值表,取模具尺寸精度为IT11级)。
②脱模斜度。
该塑件本身设计有脱模斜度,其内外表面的脱模斜度为1度。
查参考文献《中国模具设计大典》,脱模斜度合理。
Ⅱ.热塑性塑料(ABS)的注射成型过程及工艺参数1.注射成型过程⑴成型前的准备。
对ABS的色泽、细度和均匀度等进行检验。
由于ABS易于吸水,成型前应进行充分的干燥,干燥至水分含量<0.3%。
干燥条件:真空度为9.3×105MPa,烘箱温度为70度-80度左右。
料层厚度<25mm,干燥时间8h-12h。
⑵注射过程。
塑料在注射机料筒内经过加热、塑化达到流动状态后,由模具的浇注系统进入模具型腔成型,其过程可以分为充模、压实、保压、倒流和冷却5个阶段。
⑶塑件的后处理。
采用调湿处理,其热处理条件查参考文献《中国模具设计大典》中的表8.7-10有处理介质为油;处理温度为120℃;处理时间为15min。
塑料模具设计说明书【范本模板】

湖南工学院课程设计设计课题注塑模具设计设计学院机械工程学院设计班级成型1001班设计者姓名原育民设计时间2013 年 12月目录1. 塑件的工艺分析 (4)1。
1塑件的成型工艺性分析 (4)1。
1.1 塑件材料ABS的使用性能 (5)1.1。
2 塑件材料ABS的加工特性 (5)1.2 塑件的成型工艺参数确定 (6)2 模具的基本结构及模架选择 (6)2。
1 模具的基本结构 (6)2.1.1 确定成型方法 (6)2。
1。
2 型腔布置 (7)2.1.3 确定分型面 (7)2.1。
4 选择浇注系统 (8)2。
1。
5 确定推出方式 (8)2。
1.6 侧向抽芯机构 (9)2.1。
7选择成型设备 (9)2.2 选择模架 (11)2.2.1 模架的结构 (11)2。
2。
2 模架安装尺寸校核 (11)3 模具结构、尺寸的设计计算 (12)3.1 模具结构设计计算 (12)3。
1.1 型腔结构 (12)3.1.2 型芯结构 (12)3。
1.3 斜导柱、滑块结构 (12)3.1。
4 模具的导向结构 (12)3。
2 模具成型尺寸设计计算 (13)3。
2.1 型腔径向尺寸 (13)3。
2。
2 型腔深度尺寸 (13)3.2。
3 型芯径向尺寸 (14)3.2.4 型芯高度尺寸 (14)3。
3 模具加热、冷却系统的计算 (15)3。
3。
1 模具加热 (15)3.3.2 模具冷却 (15)4. 模具主要零件图及加工工艺规程 (16)4。
1 模具定模板零件图及加工工艺规程 (16)4.2 模具侧滑块零件图及加工工艺规程....... 错误!未定义书签。
4.3 模具动模板(型芯固定板)零件图及加工工艺规程 (17)5 模具总装图及模具的装配、试模.......................... 错误!未定义书签。
5。
1 模具的安装试模。
.。
.。
.。
..。
...。
..。
.。
...。
.。
.。
.。
.。
.。
.。
..。
..。
.。
.。
185.2。
模具毕业设计86瓶塞注射模设计说明书

第十一部分设计小结
通过这次系统的注射模的设计,我更进一步的了解了注射模的结构及各工作零部件的设计原则和设计要点,了解了注射模具设计的一般程序。
进行塑料产品的模具设计首先要对成型制品进行分析,再考虑浇注系统、型腔的分布、导向推出机构等后续工作。
通过制品的零件图就可以了解制品的设计要求。
对形态复杂和精度要求较高的制品,有必要了解制品的使用目的、外观及装配要求,以便从塑料品种的流动性、收缩率,透明性和制品的机械强度、尺寸公差、表面粗糙度、嵌件形式等各方面考虑注射成型工艺的可行性和经济性。
模具的结构设计要求经济合理,认真掌握各种注射模具的设计的普遍的规律,可以缩短模具设计周期,提高模具设计的水平。
第十二部分参考文献
参考资料:
1.屈华昌主编.塑料成型工艺与模具设计.北京:机械工业出版社,
1995
2.黄毅宏、李明辉主编模具制造工艺.北京:机械工业出版社,1999.6
3. 何忠保,陈晓华,王秀英主编.典型零件模具图册.北京:机械工业出版社,2000.9
4. 李绍林,马长福主编.实用模具技术手册.上海:上海科学技术文献出版社,2000.6
5. 王树勋主编.注塑模具设计与制造实用技术.广州:华南理工大学出版社,199
6.1
6. 李绍林主编.塑料·橡胶成型模具设计手册. 北京:机械工业出版社,2000.9。
模具毕业设计46支承管注射模具设计说明书

编号:毕业设计(论文)说明书题目:支承管注射模具设计院(系):机电工程学院专业:机械设计制造及其自动化学生姓名:学号:指导教师单位:机电工程学院姓名:职称:讲师题目类型:☐理论研究☐实验研究☑工程设计☐工程技术研究☐软件开发2014年5月1日摘要模具作为一种成型工具,其设计、制造水平的高低,直接关系到产品的质量与更新换代,是衡量一个国家产品制造水平的重要标志。
支撑管弯头体积较小、内部结构复杂,因而对注射成型模具和成型工艺的要求极高。
支撑管弯头注射模设计制造的最大难点在于成型部件、浇注系统、脱模机构的设计。
然后用Solidworks进行三维实体建模,再进行实体分析,确定出型腔数目,初选出成型设备,确定塑件的摆放位置,然后进行分型面的确定,浇口的确定,确定结构草图,再搭配Solidworks的moldflow可以非常有效的进行模架设计,然后进行抽芯机构,推出机构,复位机构的设计,冷却系统的设计,最后在Solidworks下进行机构模拟分析和校核。
在这过程中经常发现不合理或者干涉的情况,然后分析这些状况产生的原因,然后进行修改,直到最后确定比较合理的方案。
方案出来以后,再利用Solidworks的有限元分析功能对模具的受力部分进行强度校核,这也是Solidworks比较强大的功能之一。
当完全确定没有问题的时候,就进行二维图形的绘制。
在绘制二维图形的时候,运用目前机械行业最有有效的二维图纸绘制方法---由三维转成二维。
这不但在设计的过程思维更加清晰, 把大量经历用于机构的优化和完善,最重要的是大大提高的绘图速度和准确性,这在目前的经济时代是非常重要的。
这套模具最重要的是通过传统和现代二种思维方法来设计的,可以亲身体会出二种方法各自的优缺点,取长补短。
可以让传统工业焕发出新的活力,也提高了大家学习兴趣。
关键词:注塑模具;支撑管弯头;浇注系统;装配工艺;AbstractDie as a tool for molding, its design, manufacture level are of direct bearing on the quality of products and replacement, an important indicator to measure a country's level of manufacturing.Support elbow is of small size and complex internal structure, thus demanding a highly molding technique and injection die. The most difficult parts of Support elbow injection mould design and manufacture are the design of molding part, injection system, stripping structures. after demonstrated, I choose low-pressure polyethylene as the stuff. Second, I use Solidworks to do the three-dimensional sculpting for the entity for the sake of deciding the number of swage, equipment of injection, and the place of produce. Third, I choose the parting line, the gate, the sketch of the machinery, and arranged in pairs or groups imoldflow of Solidworks (in this way, we can design the mold’s carrier with effectively). Next, the machine of take out, fetch, return, and the cool system. The end, I use Solidworks to simulate the machine, besides analyses and check it. In the process, I always find the phenomenon of inconsequence and interference, when this phenomenon happened, I must analyses what’s wrong happened and why. Until I fine the whys, I must modify it. The end, I should decide the rational project. After the project is putted forward, I checked the intension of the pressed part of the mold with FEA of Solidworks. FEA is one of the power functions of Solidworks. After raveling out all problems, I should draw the planar chart. In the process of drawing——transform the three-dimensional chart to planar. In this way, my thinking became very in focus in the process of design, so I spend mostly energy to optimize and consummate the machine, the top-drawer is that we can heighten speed and veracity of drawing. At present, this is very important.In the process of the design, I used traditionary technique and unconventional ways. Compared them, I found their s strongpoint and disadvantage, so I can learn from other’s strong points to offset one's weakness. Improving the traditionary technique, besides improve our’s interest to study machine.Key Words: Injection mold;Support elbow;Pouring system;Assembly process;目录1. 绪论------------------------------------------------------------------------------------------------------------------ 1 1.1国内外发展状况 ----------------------------------------------------------------------------------------------------- 1 1.1.1模具工业的概况-------------------------------------------------------------------------------------------------- 1 1.1.2我国塑料模具工业和技术状况及地区分布 ---------------------------------------------------------- 2 1.1.3我国塑料模具工业和技术的今后的主要发展方向------------------------------------------------ 5 1.1.4注塑模具CAD发展概况及趋势 ---------------------------------------------------------------------------- 5 1.2研究内容---------------------------------------------------------------------------------------------------------------- 7 1.2.1支撑管弯头外形设计 ------------------------------------------------------------------------------------------ 7 1.2.2分析最佳成型工艺 ---------------------------------------------------------------------------------------------- 7 1.2.3模具结构分析和确定 ------------------------------------------------------------------------------------------ 71.2.4模具开合模运动仿真 ------------------------------------------------------------------------------------------ 72.支撑管弯头设计及其成型工艺分析------------------------------------------------------------------ 8 2.1制品结构和形状的设计 ------------------------------------------------------------------------------------------ 8 2.2制品材料的选择 ----------------------------------------------------------------------------------------------------- 9 2.2.1丙烯腈—丁二烯—苯乙烯三元共聚物(ABS) ----------------------------------------------------- 9 2.2.2聚苯乙烯(PS)-------------------------------------------------------------------------------------------------- 9 2.2.3双酚A型碳酸脂(PC)------------------------------------------------------------------------------------- 10 2.3注射工艺选择------------------------------------------------------------------------------------------------------- 12 2.3.1 ABS塑料的干燥------------------------------------------------------------------------------------------------ 12 2.3.2注射压力 ---------------------------------------------------------------------------------------------------------- 12 2.3.3注射温度 ---------------------------------------------------------------------------------------------------------- 12 2.3.4模具温度 ---------------------------------------------------------------------------------------------------------- 132.3.5料量控制 ---------------------------------------------------------------------------------------------------------- 133.模具设计-------------------------------------------------------------------------------------------------------------- 14 3.1型腔数量的确定 --------------------------------------------------------------------------------------------------- 14 3.2注塑机选型 ---------------------------------------------------------------------------------------------------------- 15 3.2.1注射量计算------------------------------------------------------------------------------------------------------- 15 3.2.2注射机型号确定------------------------------------------------------------------------------------------------ 16 3.2.3注射压力校核 --------------------------------------------------------------------------------------------------- 16 3.2.4锁模力校核------------------------------------------------------------------------------------------------------- 17 3.2.5开模行程和模板安装尺寸校核 -------------------------------------------------------------------------- 17 3.3模具浇注系统设计------------------------------------------------------------------------------------------------ 18 3.3.1主流道设计------------------------------------------------------------------------------------------------------- 18 3.3.2分流道-------------------------------------------------------------------------------------------------------------- 183.3.3浇口设计 ---------------------------------------------------------------------------------------------------------- 19 3.4注射模具成型零部件设计------------------------------------------------------------------------------------- 20 3.4.1成型零部件尺寸分析 ---------------------------------------------------------------------------------------- 20 3.4.2塑件收缩率的影响 -------------------------------------------------------------------------------------------- 20 3.4.3成型零件的设计------------------------------------------------------------------------------------------------ 21 3.4.3.1型腔-------------------------------------------------------------------------------------------------------------- 21 3.4.3.2侧型芯 ---------------------------------------------------------------------------------------------------------- 22 3.4.4成型零部件强度校核计算 --------------------------------------------------------------------------------- 23 3.4.5型芯与型腔配合------------------------------------------------------------------------------------------------ 23 3.5脱模机构设计------------------------------------------------------------------------------------------------------- 24 3.6侧向抽芯设计------------------------------------------------------------------------------------------------------- 26 3.6.1机构设计 ---------------------------------------------------------------------------------------------------------- 26 3.6.2确定抽芯距------------------------------------------------------------------------------------------------------- 26 3.6.3抽芯力的计算 --------------------------------------------------------------------------------------------------- 27 3.6.4斜导柱设计------------------------------------------------------------------------------------------------------- 28 3.7导柱导向机构------------------------------------------------------------------------------------------------------- 29 3.7.1结构形式 ---------------------------------------------------------------------------------------------------------- 29 3.7.2导柱结构和技术要求 ---------------------------------------------------------------------------------------- 29 3.7.3导套 ----------------------------------------------------------------------------------------------------------------- 30 3.8模具温度调节系统------------------------------------------------------------------------------------------------ 303.9模具材料-------------------------------------------------------------------------------------------------------------- 314.模具装配工艺 ----------------------------------------------------------------------------------------------------- 33 4.1塑料模具的装配基准 -------------------------------------------------------------------------------------------- 33 4.2塑料模具的总装配程序 ---------------------------------------------------------------------------------------- 33 4.3塑料模具装配时注意事项------------------------------------------------------------------------------------- 34 4.4空心球柄模具装配工艺 ---------------------------------------------------------------------------------------- 34 结语--------------------------------------------------------------------------------------------- 错误!未定义书签。
塑料仪表盖注射模设计说明书
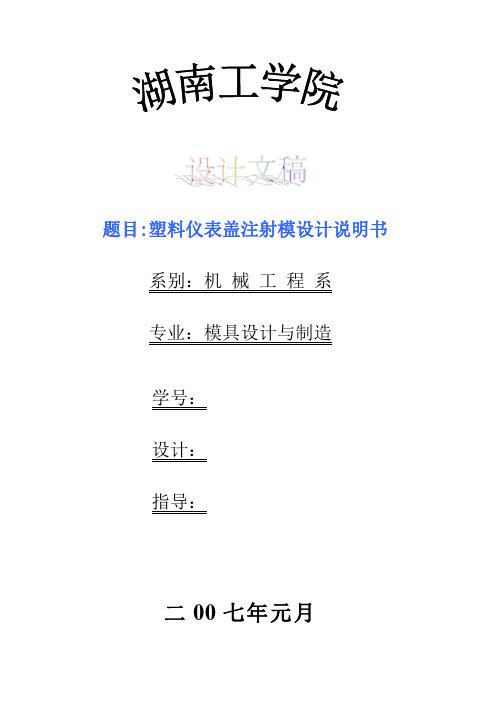
题目:塑料仪表盖注射模设计说明书系别:机械工程系专业:模具设计与制造学号:设计:指导:二00七年元月目录一零件的工艺分析二模具结构设计三成型零部件四侧向分型与推出机构的设计五模具零件的加工六参考文献七心得体会一.零件的工艺分析1.塑件的有关分析结构特点:该塑件大体是一个2mm厚的壳体,由于该塑件较小,采用一模多腔比较合适。
塑件的体积 =2.8cm³塑件的密度 =1.02~1.05kg/cm³塑件的重量 =3g所用材料:丙烯腈——丁二烯——苯乙共聚物(ABS)工程材料2.ABS塑料基本特性:ABS是由丙烯腈、丁二烯、苯乙烯共聚而成的。
这三种组分的各自特性,使ABS 具有良好的综合力学性能。
丙烯腈使ABS有良好的耐化学腐蚀性及表面硬度,丁二烯使ABS坚韧,苯乙烯使它有良好的加工性和染色性能。
ABS无毒、无味,呈微黄色,成形的塑料件有较好的光泽。
密度为1.02~1.05g/cm³。
ABS有极好的抗冲压强度,且在低温下也不迅速下降。
有良好的机械强度和一定的耐磨性、耐油性、耐水性、化学稳定性和电气性能。
ABS有一定的硬度和尺寸稳定性,易于成型加工。
经过调色可配成任何颜色。
其缺点是耐热性不高,连续工作温度为70°C左右,热变形温度为93°C 左右。
耐气候性差,在紫外线作用下变硬变脆。
主要用途:ABS广泛用于水表壳、纺织器材、电器零件、文教体育用品、玩具等。
成型特点:ABS在升温时粘度增高,所以成型压力比较高,塑料上的脱模斜度宜稍大,ABS易吸水,成型加工前应进行干燥处理;易产生熔接痕,模具设计时应注意尽量减少浇口对流道的阻力;在正常的成型条件下,壁厚、熔料温度及收缩率影响极小。
要求塑件精度高时,模具温度可控制在50~60°C,要求塑件光泽和耐用时,应控制在60~80°C。
(具体参数见下页)3. 产品工艺性与结构分析(1) 尺寸的精度塑件的尺寸公差推荐值参考《模具设计与制造手册》的2-17,塑件的精度等级参考表2-18。
注塑模具设计说明书

绪论模具作为重要的生产工艺装备,在现代工业的规模生产中日益发挥着重在作用;通过模具进行产品生产具有优质、高效、节能、节材、成本低等显著特点,在汽车、机械、电子、轻工、家电、通信、军事和航空航天等领域获得了广泛应用,对塑料模具的需求越来越大,对产品质量要求越来越高,用不可代替;塑料模具是当今工业生产中利用特定的形状,通过一定的方式来成型塑料制品的工艺装配或工具,它属于型腔模的范畴;通常情况下,塑件质量的优劣及生产效率的高低,其模具的因素约占80%,然而模具的质量好坏又直接与模具的设计与制造有很大的关系随着国民经济的领域的各个部门对塑件的品种和产量需求愈来愈大,产品更新换代周期也和质量提出了更高的要求,这就促使塑料模具设计和制造技术不断向前发展,从而也推动了塑料工业以及机械加工工业的告诉发展,可以说,模具技术,特别是设计与制造大型,精密,长寿命的模具技术便成为衡量一个国家机械制造水平的重要标志;模具在世界上占有的比列大,我作为一个学模具专业的学生,应在学完所学的知识之后来很好的进行模具设计;我们进行设计之前,不许具备机械制图,公差与技术测量,机械原理及零件,模具材料及热处理,模具制造技术,塑料制品成型工艺及模具设计等方面必要的基础知识和专业知识,并且通过教学和生产实习,初步了解塑料制品的生产过程,熟悉多种塑料模具的典型结构;近几年来,我国模具工业的技术水平已取得了很大的进步,但总体上与工业发达的国家相比仍有较大的差距;例如,精密加工设备还很少,许多先进的技术如CAD/CAE/CAM技术的普及率还不高,特别是大型、精密、复杂和长寿命模具远远不能满足国民经济各行业的发展需要;纵观发达国家对模具工业的认识与重视,我们感受到制造理念陈旧则是我国模具工业发展滞后的直接原因;模具技术水平的高低,决定着产品的质量、效益和新产品开发能力,它已成为衡量一个国家制造业水平高低的重要标志;目前,我国模具工业的当务之急是加快技术进步,调整产品结构,增加高档模具的比重,质中求效益,提高模具的国产化程度,减少对进口模具的依赖;现代模具技术的发展,在很大程度上依赖于模具标准化、优质模具材料的研究、先进的设计与制造技术、专用的机床设备,更重要的是生产技术的管理等;21世纪模具行业的基本特征是高度集成化、智能化、柔性化和网络化;追求的目标是提高产品的质量及生产效率,缩短设计及制造周期,降低生产成本,最大限度地提高模具行业的应变能力,满足用户需要;在科技发展中,人是第一因素,因此我们要特别注重人才的培养,实现产、学、研相结合,培养更多的模具人才,搞好技术创新,提高模具设计制造水平;在制造中积极采用多媒体与虚拟现实技术,逐步走向网络化、智能化环境,实现模具企业的敏捷制造、动态联盟与系统集成;模具类型塑料模具分类的方法很多,按照塑料制作的成型方法不同可分为以下几类:注射模,压缩模,挤出模,压注模;本次设计主要是注射模,又叫注塑模,注射成型是根据金属压铸成型原理发展起来的,首先将粒状或粉末状的塑料原料加入到注射机的料筒中,经过加热熔融成粘流态,然后在柱塞或螺杆的推动下,以一定的流速通过料筒前端的喷嘴和模具的浇注系统,注射入闭合的模具型腔中,经过一定的时间后,模具在模内硬化成型,近几年来,热固性塑料注射成型的应用也在逐渐增加;塑料制件主要是靠成型模具获得的,而它的质量是靠模具的正确结构和模具成型零件的正确形状,精确尺寸及较低的表面粗糙度来保证的;由于塑料成型工艺的飞速发展,模具的结构也日益趋于多功能和复杂化,这对模具的设计工作提出了更高的要求;虽然模具制作的质量与许多因素有关,但合格的塑料制作首先取决于模具的设计与制造的质量,其次取决与合理的成型工艺;塑料成型加工技术发展很快,塑料模具的各种结构也在不断的创新,我们在学习成型的同时,还应注意了解塑料模具的新技术、新工艺和新材料的发展动态,学习和掌握新知识,为振兴我国的塑料成型加工技术做出贡献;塑料成型工艺分析1、制品的分析制品的设计要求本次设计制品的用途是线盒盖,该制品结构形状较简单,形状尺寸小,壁厚均匀,基本对称,精度要求中等;制品的生产批量本制品为大批量生产,为了缩短周期,提高生产率,制品使用一模四腔和全自动化生产,浇口形式可采用侧浇口;该塑件很小,壁不厚,因此只采用一个点进料,都可以满足充满型腔,利用模具的顶出机构,将制品推出模腔,再利用拉料杆和二次脱模机构使制品流道凝料脱落;为了提高生产率,制品在模具中直接成型;制品成型设计该制品使用二次分型机构,采用点浇口形式,虽然其他的浇口形式还有直接浇口、侧浇口、扇形浇口、薄片式浇口、环行浇口、轮辐浇口、爪形浇口、潜伏浇口、护耳浇口等,但他们都不容易在开模时实现自动切断,而点浇口就具有这个优点,而且其留于塑件的疤痕较小,不影响塑件外观;2、注射成型工艺的设计塑料制品分析本制品采用ABS为原料苯乙烯—丁二烯—丙烯氰共聚物;ABS主要技术指标:表1-1 热物理性能表1-2 力学性能表1-3 电气性能1无定性料,流动性中等,比聚苯乙烯、AS差,但比聚氯乙烯好,溢边值为0.04 mm左右;2吸湿性强,必须充分干燥,表面要求光泽的塑料须经长时间的预热干燥;3成型时宜取高料温,但料温过高易分解分解温度≥250℃,对精度较高的塑料,模温宜取50~60℃,对光泽要求较高的耐热塑料模温宜取注射压力高于聚苯乙烯;用柱塞式注射机成型时,料温为60~80℃,180~200℃,注射压力为1000~1400MPa,用螺杆式注射机成型时,料温为160~220℃,注射压力为700~1000×10MPa;4 ABS的其他成型工艺参数注射机类型:螺杆式制品收缩率:~%预热温度:80~85℃时间:2~3 h料筒温度:后段 150~170℃中段 165~180℃前段180~200℃喷嘴温度:170~180℃模具温度:50~80℃注射压力:60~100 MPa成型时间:注射时间20~90 s 保压时间0~5 s冷却时间20~120 s 总周期50~220 s螺杆转速:30 r/min适用注射机类型:螺杆、柱塞均可后处理方法:红外线灯、鼓风烘箱温度70℃时间2~4 h制品成型方法及工艺流程本制品采用注射成型,工艺流程包括模前准备,模塑成型和后处理及二次加工工艺流程步骤如下:1预热ABS吸湿性强,必须充分干燥,表面要求光泽的塑料须经长时间的预热干燥;2注射注射过程包括加料、塑化、注射冷却和脱模几个步骤;加料由于注射成型是一个间歇过程,因而须定量加料,以保证操作稳定,塑料塑化均匀,最终获得良好的塑件;加料过多;受热的时间过长等容易引起物料的热降解,同时注射及功率损耗增多;加料过少,料筒内缺少传压介质,型腔中塑料融化压力降低,难于补料,容易引起塑件出现收缩、凹陷、空洞等缺陷;塑化加入的塑料在料筒中进行加热,由固体颗粒转化成粘流态,并且受到良好的剪切力作用;通过料筒对物料加热,使聚合物分子松弛,出现由固体向液体转变;一定的温度使塑料得到变形、熔融和塑化的必要条件,螺杆的剪切作用能在塑料中产生更多的摩擦热,促进了塑料的塑化,因而螺杆式注射机对塑料的温度尽量均匀一致,还有使热分解物的含量达到最小值,并且能提供上述质量的足够的熔融塑料以保证产生连续并顺利的进行,这些要求与塑料的特性、工艺条件的控制及注射机的塑化装置的结构等密切相关;注射不论何种形式的注射机,注射的过程可分为充模,保压倒流,浇口冻结后的冷却和脱模等几个阶段;塑件的后处理注射成型的塑件经脱模或机械加工之后,常需要进行适当的后处理以消除存在的内应力,改善塑件的性能和提高尺寸稳定性;其主要方法是退火和调湿处理;退火处理是将注射塑件在定温的加热液体介质或热烘箱中静置一段时间,塑料制件的氧化,加快吸湿平衡速度的一种处理方法,其目的是使制作的颜色、性能以及尺寸得到稳定;本次设计采用退火后处理;工艺流程图解:成型工艺条件注射成型的核心问题,就是采用一切措施得到塑化良好的塑料;熔体,并把它注射到型腔中去,在控制条件下冷却定型,使塑件;达到所要求的质量,影响注射成型工艺的重要参数是塑化流动和;冷却的温度、压力以及影响的各个作用时间;1注射成型过程需要控制的温度有料筒温度,喷嘴温度和模具温度等;前两个温度主要影响塑件的塑化和流动,而后一个温度主要是影响塑件的流动和冷却,料筒温度的选择与各种塑料的特性有关;每种塑料都具有不同的粘流态温度,为了保证塑件溶体的正常流动不使物料发生质分解,料筒最合适的温度范围应在粘流态温度和热分解温度之间;柱塞式和螺杆式柱塞注射机由于其塑化过程不同,因而选择料筒也不同,通常后者选择的温度低一点,料筒温度在70~93℃之间,喷嘴温度稍低于料筒温度,在65~90℃之间,模温在要求塑件光泽时控制在60~80℃之间;2压力包括塑化压力和注射压力两种,他们直接影响塑料的塑化和塑料质量;塑化压力是指背压,是指采用螺杆式注射机时,螺杆头部熔体在螺杆转动后退时所受到的压力,塑化压力在保证塑件质量的前提下越低越好,其具体数值时随所用塑料的品种而异的,但通常很少超过20MP,注射压力是指柱塞式螺杆头部对塑件熔体所施加的压力;在注射机上常用表压指示注射压力的大小,一般在40~130MP之间;其作用式克服塑料熔体从料筒流向型腔的流动阻力,给予熔体一定的充型速率以及对熔体进行压实等;3完成一次注射成型过程所需要的时间称成型周期,成型周期直接影响到劳动生产率和注射机使用率,因此在生产中,在保证质量的前提下,尽量缩短成型周期中各个阶段的有关时间,一般生产中,充模时间为3~5S,保压时间为20~25S,冷冲压时间一般在30~120S;3 注射机的选用注射机的选用包括两方面的内容:一是要确定注射机的型号,使塑料、塑件、注射模、注射工艺等所要求的注射机的规格参数点在所选注射机的规格参数可调范围之内,即要满足所需的参数在额定的范围之内;二是调整注射机的技术参数至所需的参数点;注射机的两种类型的优缺点采用卧式注射机的优点是注射部分和锁模部分在同一水平线上,工作位置低,操作方便,稳定性好,顶出后塑件可以自动脱落,是应用广泛的注射机,适用于大、中、小个各型注射机,但唯一的缺点是占地面积大;采用立式注射机的优点是占地面积小,缺点是操作位置高,对于注射量大的注射机,势必使注射机高度增加,操作台升高,操作不方便,注射机的工作稳定性也减小;因此,立式注射机多限于小型注射机;选用注射机按流量选择注塑机,选择SZ—40/32立式注射机,表为该注射机的技术参数;模具结构的设计1、塑件成型位置及分型面的选择分型面即打开模具取出塑件或取出浇注系统凝料的面,分型面的位置影响着成型零部件的结构形状,型腔的排气情况也与分型面的开设密切相关;分型面的选择应注意以下几点:1不影响塑件外观,尤其是对外观有明确要求的制品;2有利于保证塑件的精度要求;3有利于模具加工,特别是型腔的加工;4有利于浇注系统、排气系统、冷却系统的设计;5便于制件的脱模,尽量使塑件开模时留在动模一边.6分型面应有利于侧向抽心;7分型面应取塑件尺寸最大处;8拔模斜度小或塑件较高时,为了便于脱模,可将分型面选在塑件的中间部位;2、型腔的排列形式及流道布局的确定型腔数目确定方法常见的有四种:1根据经济性确定型腔树木2根据注射机的额定锁模力确定型腔树木3根据注射机的最大注射量确定型腔数目4根据制品精度确定型腔数目对于高精度制品,由于多型腔模具难以使各型腔的成型条件均匀一致;故通常推荐型腔数目不超过6个,本设计为四型腔注射模;型腔数量的确定该制品精度要求不高,属于小零件,又要大量的生产,为了考虑生产效率和模具制造费用低点,给公司带来更多的效益,因此本设计初步拟定于一模八腔模具的形式生产;根据注射机的最大注射量确定型腔数目,即只要满足下式,就符合要求 210.8G W n W -≤ 式中:n —型腔数目G —注射机的最大注射量,g ;W 1—单个制品的质量,g ;W 2—浇注系统的质量,g ;210.8G W W -0.8600.910.64 1.421.4228.36⨯⨯-⨯⨯== 28.36>4,因此一模四腔符合要求;型腔的排列在设计时要注意以下几点1尽可能采用平衡式排列确保制品的质量的均一和稳定2型腔布置与浇口开设部位应力求对称,以便防止模具承受偏载而产生溢料现象,尽量使型腔排的紧凑,以便减少模具的外形尺寸;该塑件侧面有一个梯形槽,需要有侧向抽心,为了便于抽心及节省流道凝料,因此采用下列的型腔排列及流道布局;型腔的排列及流道布局3、 浇注系统的设计浇注系统通常由主流道 分流道 浇口料穴等组成;浇注系统是塑料容体由注射机的喷嘴向模具型腔的流动通道;因此它应该保证容体迅速顺利有序地充满型腔各处,获得外观清晰,内在优良的塑料件;对于浇注系统设计的具体要求有:①重点考虑型腔布局;②热量及压力损失要小,为此浇注系统流程应尽可能短,截面尺寸应尽可能大,弯折尽量少,表面粗糙度要低;③均衡进料,即分流道尽可能采用平衡式布置;④塑料耗量要少,满足各型腔充满的前提下,浇注系统容积尽量小,以减少塑料耗.⑤消除冷料,浇注系统应能收集温度较低的“冷料”;⑥排气良好;⑦防止塑件出现缺陷,避免熔体出现充填不足或塑件出现气孔、缩孔、残余应力;⑧保证塑件外观质量;⑨较高的生产效率;⑩塑料熔体流动特性;4、主流道的设计主流道是指连接注射机喷嘴与风流道或型腔的进料通道;负责将塑料溶体从喷嘴引入模具,其形状,大小直接影响塑料的流速及填充时间;主流道是塑料容体进入模具型腔时经过的部分,它将注射机的喷嘴注出的塑料容体导入分流道或型腔;其形状为圆锥形,便于容体顺利地向前流动,开模时主流道凝料又能顺利拉出来;主流道的尺寸直接影响到塑料容体的流动速度和充填时间;由于主流道要与高温塑料和喷嘴反复接触和碰撞,通常不直接开在定模板上,而是将它单独设计成主流道衬套镶入定模板内;主流道的尺寸①半锥角一般在1°~3°内选取,主流道带锥度是为了在模具打开时使主流道凝料容易脱离定模;本设计选取锥度为3°;②主流道径向尺寸的小端与喷嘴连接的一端应大于喷嘴口孔径~㎜;当主流道与喷嘴同轴度有偏差时,可以防止主流道凝料不易从定模一侧拉下来;D=d+~1㎜式中:d—注射机喷嘴口直径D—浇口套进料口直径③凹球面半径R应比喷嘴球径1R大1~2㎜,可以;保证注射过2程中喷嘴与模具紧密接触,防止两球面之间产生间隙而使容体充入这间隙中,妨碍主流道凝料顺利从定模上拉出;④主流道内壁的表面粗糙度R在以下,主流道的长度L一般根据a模板的厚度而定,为了减少压力损失和物料损耗;应尽可能减少主流道的长度,一般控制在60mm以内;主流道出口处的圆角半径较小,一D般取r=18⑤主流道上开设浇口套;将主流道开设在一个专用零件主流道衬套上而不是直接加工在定模板上的方法较好,因为主流道的表面粗糙度和硬度要求一般都比定模板高,可以选用较好的钢材;损坏后也容易更换,一般选用T8或T10制作,淬火硬度为50~55HRC,浇口套的形式如下图a b c e f g浇口套的形式(a)是浇口套和定位圈做成一体,仅适用于小型模具;(b)采用螺钉将定位圈和定模座板连接,防止浇口套受容体的反压力而脱出,是常用结构;(c)用定位圈的凸肩将其压在注射机的固定板下,当浇口套端面尺寸较小时,仅靠注射机喷嘴的推力就能将浇口套压紧,也是常用结构;(d)通过浇口套上挖出凹坑来减少主流道的长度;(e)直接在定模座板上开主流道,适用用于小型模具的小批生产,上述几种情况适用与注射机为球面的情况;(f)用于喷嘴头为平面的结构,优点是接触面积大,密封好容体不外溢,缺点是对注射机的精度要求很高;本设计采用b图的结构5、分流道的设计分流道是指主流道与模具型腔浇口之间的一段流道,在多型腔或单型腔多浇口塑件尺寸大时应设置分流道,分流道是指主流道末端与浇口之间这一段塑料熔体的流动通道;它是浇注系统中熔融状态的塑料由主流道流入型腔前,通过截面积的变化及流向变换以获得平稳流态的过渡段;因此分流道设计应满足良好的压力传递和保持理想的充填状态,并在流动过程中压力损失尽可能小,能将塑料熔体均衡地分配到各个型腔;分流道的布置常用塑料的分流道直径列于下表,由表可见,对于流动性极好的塑料,当分流道很短时,其直径可小到2mm左右;对于流动性差的塑料,分流道直径可以大到13mm;大多塑料所用分流道的直径为6mm~10mm;在多型腔模具中分流道的布置中有平衡式和非平衡式;平衡式布置是指分流道到各型腔浇口的长度、断面形状、尺寸都相等的布置形式;它要求各对应部分的尺寸相等,这种布置可实现均衡送料和同时充满型腔的目的,使成型的塑件力学性能基本一致;但是这种布置使分流道较长;非平衡式布置是指分流道到各个型腔浇口的长度相等的布置;这种布置使塑料进入各个型腔有先后顺序,因此不利于均衡送料,但对型腔数量多的模具,为不使流道过长,也常采用;为了达到同时充满型腔的目的,各个浇口的断面尺寸要制作得不相同,在试模的时候要多修改才能实现;a b分流道的平衡布置示意图分流道的非平衡布置示意图本设计中为了成型的塑件力学性能基本一致,采用图a结构,分流道的平衡布置;6、浇口的设计浇口亦称进料口,是连接分流道与型腔的通道,除直接浇口外,它是浇注系统中截面最小的部分,但却是浇注系统的关键部分,浇口的位置、形状及尺寸对塑件性能和质量的影响很大;浇口的主要作用:➢型腔充满后,熔体在浇口处首先凝结,防止其倒流;➢易于切除浇口尾料;➢对于多型腔模具,用以控制熔接痕的位置;当塑料熔体通过浇口时,剪切速率增高,同时熔体的内摩擦加剧,使料流的温度升高,黏度降低,提高流动性能,有利于充型,但是浇口尺寸过小会使压力增大,凝料加快,补缩困难,甚至形成喷射现象, 影响塑件质量;浇口类型的选择浇口是典型的矩形截面浇口,有以下优点:①浇口的位置一般都在分型面上,从塑件的外侧进料;②塑件容易形成熔接纹、缩孔,凹陷等缺陷,注射压力损失较大,对壳体件排气不良;③截面形状简单,加工方便;④位置选择灵活,去除浇口方便,痕迹小;⑤广泛用于两板式多型腔模具以及断面尺寸较小的塑件;本设计采用侧浇口的结构形式;浇口位置的选择模具设计时,浇口的位置及尺寸要求比较严格,初步试模后还需进一步修改浇口尺寸,无论采用何种浇口,其开设位置对塑件成型性能及质量影响很大,因此合理选择浇口的开设位置是提高质量的重要环节,同时浇口位置的不同还影响模具结构;总之要使塑件具有良好的性能与外表,一定要认真考虑浇口位置的选择,通常要考虑以下几项原则:①避免制件上产生喷射等缺陷②浇口应开设在塑件截面最厚处;③有利于塑件熔体流动;④有利于型腔排气;⑤考虑塑件使用时的载荷状况;⑥减少或避免塑件的熔接痕;⑦考虑分子取向对塑件性能的影响;⑧考虑浇口位置和数目对塑件成型尺寸的影响;⑨防止将型芯或嵌件挤歪变形;下图为本设计塑所选的浇口位置浇口位置浇注系统的平衡对于中小型塑件的注射模具己广泛使用一模多腔的形式,设计应尽量保证所有的型腔同时得到均一的充填和成型;一般在塑件形状及模具结构允许的情况下,应将从主流道到各个型腔的分流道设计成长度相等、形状及截面尺寸相同型腔布局为平衡式的形式,否则就需要通过调节浇口尺寸使各浇口的流量及成型工艺条件达到一致,这就是浇注系统的平衡;显然,我们设计的模具是平衡式的,即从主流道到各个型腔的分流道的长度相等,形状及截面尺寸都相同;7、冷料穴的设计冷料穴的作用是储存因两次注射间隔而产生的冷料头以及塥体流动的前锋冷料,以防止溶体冷料进入型腔;冷料穴一般设在主流道的末端,冷料穴底部常作成曲折的钩行或下陷的凹槽,使冷料穴兼有分模时将主流道衬套中拉出,并留在动模一侧的作用;在完成一次注射循环的间隔,考虑到注射机喷嘴和主流道入口这一小段熔体因辐射散热而低于所要求的塑料熔体的温度,从喷嘴端部到注射机料筒以内约10-25mm的深度有个温度逐渐升高的区域,这时才达到正常的塑。
机械类塑料模注射模具设计说明书

二设计要求:1.绘制产品零件图2.绘制模具装配图3.绘制整套模具零件图(除标准件外)4.编写设计说明书三设计要求:1.模具结构设计合理,工艺性好。
设计计算正确,参数选用正合理。
2.模具绘图布局合理,视图完整、清晰,各项要求符合规范。
3.模具装配图采用CAD绘制并打印(0号图打印)4.绘制全套模具零件图,除标准件(模架选择标准的也要出图)5.设计说明书内容完整,分析透彻,语言流畅,参考资料应注明出处,字数在20000左右,统一采用A4Z纸、5号宋体打印。
图量一般要求为2张半0号。
第二部分塑件分析1.制品图如图2-1:图2-12.制品分析:该制品结构简单,形状尺寸小,壁厚均匀,使用PA制造。
公差等级为MT5,该制品采用了凸起来增加制品的料制品及成型略地估计分流道的直径。
常用塑料的分流道直径推荐值如〈塑料制品成型及模具设计〉表4-3。
对于壁厚小于3mm,质量在200—以下的塑件可以用以下经验公式确定分流道的直径;D=0.2654m4l式中;M-流径分流道的塑料量L-分流道长度〈mm〉D-分流道直径,对于粘度叫大的塑件,可用上式算得的D值再以1.2~1.25的系数,据表4——3查得尼龙类分流道的直径为1.6~9.5 取D=4。
〈3〉分流道的布置:分流道采用平衡布置,多型腔模具应尽量均衡布置型腔,使熔融塑料几乎同时到达每个型腔的进料口,这样,塑料到每个型腔的压力和温度是相同的,塑件的品质理应相同图4—2D 浇口的设计〈1〉浇口又称进料口,是分流道与型腔之间的狭窄部分,也是浇注系统中最短小的部分,他使塑料溶体的流速产生加速度,有利于迅速充满型腔,同时还起封闭型腔防止溶体倒流的作用,并在成型后使浇口凝料与塑件易于分离。
浇口的设计与塑料性能,塑件形状,截面尺寸模具结构及注射工艺参数等有关。
总的要求是使溶料以较快的速度进入并充满型腔,同时在充满后能适时冷却封闭,因此浇口的截面要小,长度要短,这样可以增大料流速度,快速冷却封闭,且便于塑件与凝料分离,不留明显的浇口痕迹,保证塑件外观质量。
注塑(简单)家用台灯灯罩注射模设计设计说明书

注塑(简单)-家用台灯灯罩注射模设计-设计说明书江苏财经职业技术学院综合毕业实践说明书(论文)标题: 家用台灯灯罩注塑模设计系别:机电工程系专业: 模具设计与制造学号:0810403229 姓名: 王岚指导教师: 陈青云2011年5月15日摘要本课题主要是针对台灯上小夜灯灯罩的模具设计,通过对塑件进行工艺的分析和比较,最终设计出一副注射模。
该课题从产品结构工艺性,具体模具结构出发,对模具的成型零部件、合模导向机构、浇注系统、侧向分型与抽芯机构、推出机构、加热和冷却系统、排气系统、支承零部件、注射机的选择及有关参数的校核、都有详细的设计,同时并简单的编制了模具的加工工艺。
通过整个设计过程表明该模具能够达到此塑件所要求的加工工艺。
根据题目设计的主要任务是灯罩注射模的设计。
也就是设计一副注射模具来生产灯罩塑件产品,以实现自动化提高产量。
关键词:灯罩;注射模;模具结构;加工工艺目录摘要1引言 51塑料成型工艺性分析 31.1塑件结构工艺分析 31.2塑件的性能分析 31.2.1塑件材料的选择 31.2.2材料基本特性 31.2.3材料综合性能 31.3 PS注射成型过程及工艺参数 41.3.1成型特点 41.3.2注射成型过程 41.33注射工艺参数42 模具的结构形式分析52.1分型面位置的确定 52.2型腔数量和排列方式的确定 52.2.1 型腔数量的确定52.2.2 腔排列形式的确定72.3注射机型号的确定 72.3.1 注射量的计算232.3.2浇注系统凝料体积的初步估算23 2.3.3选择注射机233浇注系统的设计243.1主流道的设计243.1.1主流道尺寸243.1.2浇口套的形式253.2分流道的设计253.3浇口的设计263.4冷料穴的设计274成型零件的结构设计及计算27 4.1成型零件的结构设计274.1.1凹模的结构设计 274.1.2凸模型芯的结构设计274.2 成型零件钢材的选用284.3成型零件的尺寸计算284.3.1型腔尺寸计算284.3.2型芯尺寸的计算 294.4型腔壁厚和底板厚度计算30 5模架的确定315.1各模板尺寸的确定 315.2模架各尺寸的校核 326排气系统设计327推出机构的设计327.1 推出机构的组成337.2 设计原则337.3 脱模力的计算 338温度调节系统的设计 348.1冷却系统的作用348.2 设计冷却系统时应考虑的因素 358.3冷却介质359导向与定位结构的设计359.1导柱导向机构的作用359.2 导柱导套的设计原则359.3导柱导套的设计3610总装配图37结束语38致谢39参考文献40家用台灯灯罩注射模设计引言随着中国当前的经济形势的日趋好转,在“实现中华民族的伟大复兴”口号的倡引下,中国的制造业也日趋蓬勃发展;而模具技术已成为衡量一个国家制造业水平的重要标志之一,模具工业能促进工业产品生产的发展和质量提高,并能获得极大的经济效益,因而引起了各国的高度重视和赞赏。
注塑模具设计说明书

塑料模课程设计水杯盖注塑模具设计学院机电与建筑工程学院专业材料成型及控制工程姓名李瑞朝学号指导老师杨俊杰余五新目录1前言 (1)2设计任务书 (1)3塑件的结构工艺性分析 (1)4分型面及浇注系统的设计.............................5模具设计方案论证 (1)6主要零部件的设计计算 (1)7成型设备的校核计算 (1)8设计小结 (1)9参考文献 (1)1前言水杯盖在我们生活中随处可见,几乎每家每户都会用到。
市场上也有各种各样的杯盖,有时候一个灵巧鲜艳的造型便能吸引消费者的眼球,为生产厂家创造利润。
所以一个貌似简单的盖子也蕴含着无尽的商机,引人深思。
本次设计的顶盖结构非常简单,主要展现出一个最普通的生活用品的注塑成型过程,希望能有助于人们对身边事物的了解。
2设计任务书(1)塑料制品名称:水杯盖。
(2)成型方法:注塑成型。
(3)塑料原料:ABS。
(4)收缩率:0.4%~0.7%。
(5)生产批量:10万件。
3塑件的结构工艺性分析3.1塑件的几何形状分析本塑件为圆形的顶盖,尺寸中等,结构简单。
考虑到该制件精度要求较低,结合其材料性能,故选一般精度等级为:MT5。
3.2塑件原材料的成型特性分析ABS是目前产量最大,应用最广的工程塑料。
ABS是不透明非结晶型聚合物,无毒,无味,密度为1.02~1.05g/cm 3。
ABS具有突出的力学性能,坚韧,坚固;易于成型和机械加工,成型塑料油较好的光泽,经过调色可配成任何颜色。
ABS可采取注射,挤塑,吹塑,真空成型机表面涂饰等多种成型加工方法。
ABS成型性能如下:(1)易吸水,成型加工前需进行干燥处理,表面光泽要求高的塑件需长时间预热干燥。
(2)比热容低,塑化效率高,凝固也快,故成型周期短。
(3)顶出力过大或机械加工时塑件表面会留下白色痕迹,脱模斜度宜取2°以上。
(4)易产生熔接痕,模具设计是应注意尽量减少浇注系统对料流的阻力。
(5)宜采用高料温,高模温,高注射压力成型。
一模四腔透盖注射模具课程设计说明书
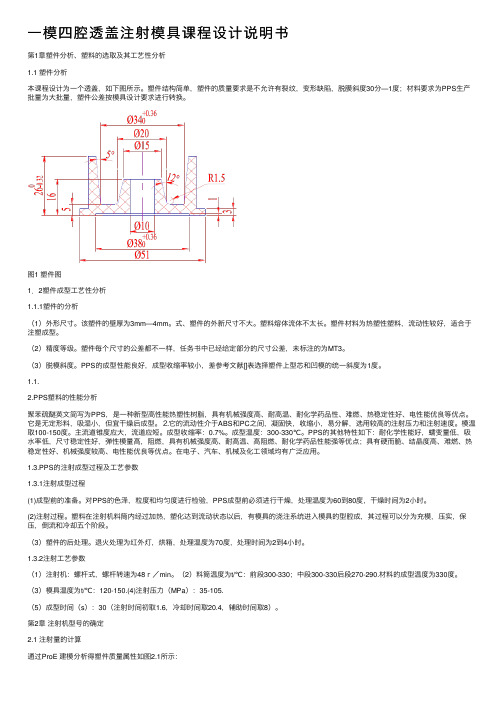
⼀模四腔透盖注射模具课程设计说明书第1章塑件分析、塑料的选取及其⼯艺性分析1.1 塑件分析本课程设计为⼀个透盖,如下图所⽰。
塑件结构简单,塑件的质量要求是不允许有裂纹,变形缺陷,脱膜斜度30分—1度;材料要求为PPS⽣产批量为⼤批量,塑件公差按模具设计要求进⾏转换。
图1 塑件图1.2塑件成型⼯艺性分析1.1.1塑件的分析(1)外形尺⼨。
该塑件的壁厚为3mm—4mm。
式、塑件的外新尺⼨不⼤。
塑料熔体流体不太长。
塑件材料为热塑性塑料,流动性较好,适合于注塑成型。
(2)精度等级。
塑件每个尺⼨的公差都不⼀样,任务书中已经给定部分的尺⼨公差,未标注的为MT3。
(3)脱模斜度。
PPS的成型性能良好,成型收缩率较⼩,差参考⽂献[]表选择塑件上型芯和凹模的统⼀斜度为1度。
1.1.2.PPS塑料的性能分析聚苯硫醚英⽂简写为PPS,是⼀种新型⾼性能热塑性树脂,具有机械强度⾼、耐⾼温、耐化学药品性、难燃、热稳定性好、电性能优良等优点。
它是⽆定形料,吸湿⼩,但宜⼲燥后成型。
⒉它的流动性介于ABS和PC之间,凝固快,收缩⼩,易分解,选⽤较⾼的注射压⼒和注射速度。
模温取100-150度。
主流道锥度应⼤,流道应短。
成型收缩率:0.7%。
成型温度:300-330℃。
PPS的其他特性如下:耐化学性能好,蠕变量低,吸⽔率低,尺⼨稳定性好,弹性模量⾼,阻燃,具有机械强度⾼、耐⾼温、⾼阻燃、耐化学药品性能强等优点;具有硬⽽脆、结晶度⾼、难燃、热稳定性好、机械强度较⾼、电性能优良等优点。
在电⼦、汽车、机械及化⼯领域均有⼴泛应⽤。
1.3.PPS的注射成型过程及⼯艺参数1.3.1注射成型过程(1)成型前的准备。
对PPS的⾊泽,粒度和均匀度进⾏检验,PPS成型前必须进⾏⼲燥,处理温度为60到80度,⼲燥时间为2⼩时。
(2)注射过程。
塑料在注射机料筒内经过加热,塑化达到流动状态以后,有模具的浇注系统进⼊模具的型腔成,其过程可以分为充模,压实,保压,倒流和冷却五个阶段。
注射模具毕业设计说明书
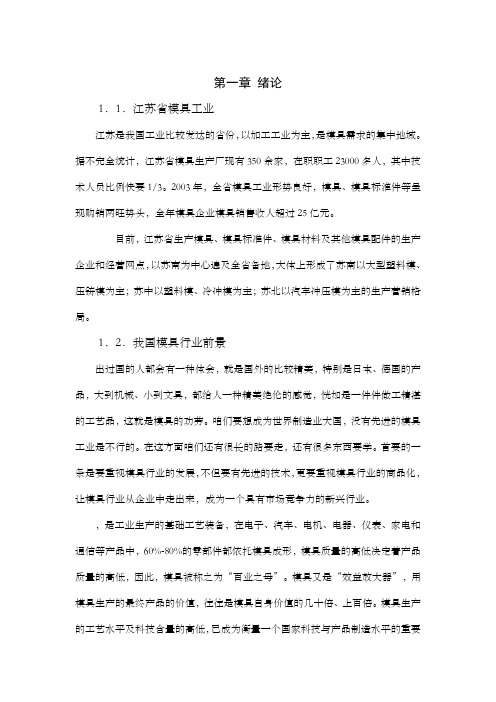
第一章绪论1.1.江苏省模具工业江苏是我国工业比较发达的省份,以加工工业为主,是模具需求的集中地域。
据不完全统计,江苏省模具生产厂现有350余家,在职职工23000多人,其中技术人员比例快要1/3。
2003年,全省模具工业形势良好,模具、模具标淮件等呈现购销两旺势头,全年模具企业模具销售收人超过25亿元。
目前,江苏省生产模具、模具标准件、模具材料及其他模具配件的生产企业和经营网点,以苏南为中心遍及全省备地,大体上形成了苏南以大型塑料模、压铸模为主;苏中以塑料模、冷冲模为主;苏北以汽车冲压模为主的生产营销格局。
1.2.我国模具行业前景出过国的人都会有一种体会,就是国外的比较精美,特别是日本、德国的产品,大到机械、小到文具,都给人一种精美绝伦的感觉,恍如是一件件做工精湛的工艺品,这就是模具的功劳。
咱们要想成为世界制造业大国,没有先进的模具工业是不行的。
在这方面咱们还有很长的路要走,还有很多东西要学。
首要的一条是要重视模具行业的发展,不但要有先进的技术,更要重视模具行业的商品化,让模具行业从企业中走出来,成为一个具有市场竞争力的新兴行业。
,是工业生产的基础工艺装备,在电子、汽车、电机、电器、仪表、家电和通信等产品中,60%-80%的零部件都依托模具成形,模具质量的高低决定着产品质量的高低,因此,模具被称之为“百业之母”。
模具又是“效益放大器”,用模具生产的最终产品的价值,往往是模具自身价值的几十倍、上百倍。
模具生产的工艺水平及科技含量的高低,已成为衡量一个国家科技与产品制造水平的重要标志,它在很大程度上决定着产品的质量、效益、新产品的开发能力,决定着一个国家制造业的国际竞争力。
改革开放以来,我国模具工业发展迅猛。
1996至2001年间,我国模具工业的产值年平均增加14%左右。
目前,全国共有模具生产厂点万个,从业人员50多万人。
2001年全国模具工业总产值达300亿元人民币,我国模具年产值已位居世界第四。
模具毕业设计16接触器座注射模设计说明书1

本科毕业论文(设计)题目: 接触器座注射模设计学院:工学院姓名:学号:专业:机械设计制造及其自动化年级:指导教师:职称:高级实验师二0一四年五月摘要塑料成型产品是塑料材料的加工产品为主要结构,也称为塑料零件,塑料部件。
塑料成型产品广泛应用,尤其是在电子仪器、机电设备、通信工具、生活用品、等,获得大量的应用。
各种受力不大的壳体、结构、装饰、等;用于各种塑料异型材、板和门窗,塑料中空容器与塑料制品和各种各样的生活用塑料制品等。
塑料零件以塑料成型加工为主要加工方法。
塑料成型各种塑料原材料(粉、粒状、熔化或分散)塑化的要求或加热熔融塑料的状态,在一定的压力下,要求形状模具或填充到模具型腔形状,等待冷却定型后,获得所需的形状和大小几个塑料零件生产过程。
其特点是生产的产品形状尺寸很稳定,可实现连续生产,一模多件,生产效率高。
常用的塑料注射成型工艺有注塑成型、压缩成型,吹塑等,注塑是一种主要塑料模塑成型方法。
注塑技术出现了许多新工艺方法,如热固性塑料注射成型、排气注射成型、反应注射成型以及各种塑料注塑。
关键词:塑料制件注塑成型Abstract:(Times New Roman)Plastic molding products are widely used, especially in electronics, electrical equipment, communication tools, daily necessities, such as a large number of applications. Such as the big shell, frame, base, structural parts, decorative parts; All kinds of plastic pipe used in construction, metal plate and profile doors and Windows; Hollow plastic containers and plastic products, such as life.The Main processing plastic processing methods of plastic parts. Plastic molding is the various types of plastic raw materials (powder, granular, melting or spread) of plastics melt or heat conform to the requirements of the country, under a certain pressure after shape mould requirement or request mold - filled cavity, stereotype is the shape, size, quantity after cooling requirements of plastic parts production process properties. Stability in the shape of production on the size of products, can realize continuous production, more than one mode of production, high productivityCommon plastic molding process is injection molding, compression molding, blow molding, injection molding is a main forming method. Injection molding technology has a lot of new technical methods, such as material non - condensate injection flow, thermosetting plastic injection molding, exhaust injection molding, reaction injection molding, and the total number of all kinds of plastic injection moldingKey words:(Times New Roman)Plastic parts Injection molding目录摘要 (2)前言 (5)1、设计课题及设计目的 (6)1.1、设计内容 (6)1.2、设计目的 (6)2、模具设计 (7)2.1、产品工艺性分析 (7)2.2、注射机的选择 (8)2.3、确定模具基本结构 (10)2.4、模具结构设计 (10)2.5、模具整体设计 (16)总结 (19)参考文献 (20)致谢 (21)前言模具是一种广泛应用于工业生产的设备,采用模具生产的产品和部件,具有市场效率高、节省原材料、低成本、确保质量等一系列的优点,是现代工业生产的重要手段和主要发展方向。
- 1、下载文档前请自行甄别文档内容的完整性,平台不提供额外的编辑、内容补充、找答案等附加服务。
- 2、"仅部分预览"的文档,不可在线预览部分如存在完整性等问题,可反馈申请退款(可完整预览的文档不适用该条件!)。
- 3、如文档侵犯您的权益,请联系客服反馈,我们会尽快为您处理(人工客服工作时间:9:00-18:30)。
一塑件原材料选用与性能分析1分析制件材料的使用性能ABS属热塑性非结晶型塑料,不透明。
ABS由丙烯晴、丁二烯、苯乙烯共聚而成的,这三种组分各自的特性,使ABS具有良好的综合力学性能。
ABS无毒、无味,呈微黄色,成型的制件有较好的光泽,密度为1.02~1.05g/cm3。
ABS有极良好的机械强度和一定的耐磨性、耐寒性、耐油性、化学稳定性和电气性能。
ABS有一定的硬度和尺寸稳定性,易于成型加工,经过调色可配成任何颜色。
2 分析塑料成型工艺性能ABS属于无定形塑料,流动性中等;升温时黏度增高,所以成型压力较高,故制件的脱模斜度宜稍大;ABS易吸水,成型加工前应进行干燥处理,预热干燥80~100℃,时间2~3h;ABS易产生熔接痕,模具设计时应注意尽量减小浇注系统对料流的阻力。
该产品为某电工产品外壳,要求具有一定的强度、刚度、耐热和耐磨损等性能,中等精度,外表面无瑕疵、美观、性能可靠,同时还必须满足绝缘性。
采用ABS材料,产品的使用性能基本能满足要求,但在成型时,要注意选择合理的成型工艺。
二塑件结构与质量分析1 塑件的尺寸精度分析从零件图上分析,该零件总体形状为长方形,该零件重要尺寸如:等的尺寸精度为MT2~MT3级(查GB/T 14486-2008中常用材料模塑件尺寸公差登等级选用表),未标注公差的尺寸为自由尺寸,可按MT5级塑料件精度查取公差值(可查GB/T 14486-2008中模塑件尺寸公差表)。
2 塑件表面质量分析该塑件是某电工产品外壳,要求外表美观、光洁无毛刺、无缩痕,表面粗糙度可取Ra0.8,而塑件部没有较高的粗糙度要求,模具制造和成型工艺容易保证。
3 塑件结构工艺性分析此塑件外形为方形壳类零件,腔体为25mm深,壁厚均匀2mm,外形尺寸适中,塑件成型性能良好,脱模斜度选为1°;4 侧孔和侧凹该塑件在宽度/长度方向有三个通孔,因此模具设计时必须设置侧向分型抽芯机构。
5 塑件的体积和质量计算根据零件的三维模型,利用三维软件直接可查询到塑件的体积为:V=31.180cm3故塑件的质量W=V·ρ=32.115g(ABS塑料密度按1.03g/cm3)三注塑成型机的选择初选注射机规格通常依据注射机允许的最大注射量、锁模力及塑件外观尺寸等因素确定。
1 依据最大注射量初选设备①单个塑件体积 V=31.180cm3②由于塑件尺寸不大,结合模具设计要求,采用一模两腔,加上浇注系统凝料体积(初步估算约为34cm3)③塑件成型每次需要注射量:2V+34=96 (cm3)④根据注射量,查附表一选择XS-ZY-130型号的螺杆式注射机,满足注射量小于或等于注射机允许的最大注射量的80%。
3依据最大锁模力初选设备当熔体充满模腔时,注射压力在模腔所产生的作用力会使模具沿分型面胀开,为此,注射机的锁模力必须大于模腔熔体对动模的作用力,以避免发生溢料和胀模现象。
①单个塑件在分型面上投影面积A1。
A1≈128*85=10880 (mm2)②成型时熔体塑料在分型面上投影面积A。
初步估算凝料在分型面上投影面积约2500mm2A=2*A1+2500=24260(mm2)③成型时塑料熔体对动模的作用力F=Ap=829.7 KN式中:p是塑料熔体对型腔的平均成型压力,成型ABS塑件型腔所需的平均成型压力p=34.2Mpa。
④根据锁模力必须大于模腔熔体对动模的作用力的原则,查附录一选择XS-ZY-130型号的螺杆式注射机。
四塑件工艺参数的确定ABS成型性能较好,成型温度围宽,通常在160℃以上即可成型,在270℃以上才开始出现分解,塑件注射成型工艺参数如下表所示:五模具分型面的选择该塑件外形要求美观、光洁无毛刺和缩痕,表面质量要求较高。
在选择分型面时,根据分型面的选择原则——便于脱模,分型面应设置在塑件外形最大轮廓处,为保证塑件表面质量要求分型面不在塑件的壁部,而是端部。
六浇注系统的设计1 主流道设计查注射机喷嘴球半径SR0=10mm,喷嘴孔直径d0=φ4mm。
根据模具主流道与喷嘴的关系:SR= SR0+(1~2)mm,d= d0+0.5mm取主流道球面半径:SR=11mm,球面深度取3mm(3~5mm)。
取主流道的小端直径:d=4.5mm为了便于将凝料从主流道拔出,将主流道设计成圆锥形,如图所示,其锥角为α=4°(2~4°),表面粗糙度Ra≤0.4μm。
为了使熔料顺利进入分流道,在主流道出料端设计r=3mm(1~3mm)的圆弧过渡。
主流道长度由定模板厚度确定,一般不超过60mm(初步确定L=50mm)。
2 分流道设计分流道的形状与尺寸与塑件的体积、壁厚、形状的复杂程度、注射速率等因素有关。
该塑件的体积不大,形状较为简单,且壁厚均匀,塑件外表面不允许设置浇口,可以考虑采用潜伏式浇口。
分流道的截面形状有圆形、半圆形、U形、矩形及梯形等形状。
为使流道中热量和压力损失最小,并且便于加工,采用截面形状为U形的分流道,分流道长度取40mm,为利于熔体的流动及填充,分流道与浇口处的连接采用r=1.2mm的圆角过渡。
参考《实用模具设计简明手册》,对于熔体粘度较小,壁厚小于3mm,质量在200g以下的塑件,其分流道直径按下式计算:D=42654.0L W式中 W —流经分流道的塑料质量(g ) L —分流道的长度(mm ) D=42654.0L W =440115.322654.0=0.2654×5.667×2.5148 =3.7823mm查表5-9得知:ABS 分流道截面直径经验值为4.8~9.5mm ,再根据塑件尺寸,选定分流道的尺寸如下图所示:分流道表面粗糙度Ra 取1.6μm ,这样流道外层流速较低,容易冷却而形成固定表皮层,有利于流道保温。
3 浇口设计由于该塑件外观质量要求较高,浇口的位置不允许设置在塑件的外表面,因此可选择侧潜伏式浇口,如下图所示:依次初步设计浇口尺寸为 1.6、50°、15°4 冷料穴设计选用“Z ”字形拉料杆的冷料穴。
七 模具顶出系统的设计1 脱模力的计算脱模力F 可以粗略的用下式计算: F=F Z +F Q式中:F Z ——塑料收缩产生的对型芯的抱紧力造成的抽芯阻力,N ; F Q ——真空负压造成的抽芯阻力,N。
F Z =pA (μcos α-sin α)μ——塑料与钢的摩擦系数,PC 、POM 取0.1~0.2,其余取0.2~0.3; p ——塑件对型芯的单位面积上的包紧力,一般情况下,模外冷却的塑件p=(2.4~3.9)*107Pa ,模冷却的塑件p=(0.8~1.2)*107Pa ;A ——塑件包围型芯的面积,mm2 α——脱模斜度,取0.5°~1.5° F Q =0.1A 1式中:A 1——垂直于抽芯方向的投影面积,mm 2。
2 推出机构方式的选择选用推杆推出机构结构简单,使用方便,根据脱模力大小,推杆选用直径可根据压杆稳定公式计算:412nE FL K d ⎪⎪⎭⎫⎝⎛= 式中 d ——推杆的直径 L ——推杆的长度 F ——塑件的脱模力E ——弹性模量(推杆选用T10A ,E=2.06*105Mpa )n ——推杆数量,根据塑件和型腔或型芯的结构和尺寸确定; K ——安全系数,取K=1.5。
推杆直径确定后,还应进行强度校核,其计算公式为[]⎪⎪⎭⎫⎝⎛≥ σπn F 4d式中 [ σ]——推杆材料的需用压应力,工作端面为圆形。
尾部采用台肩固定,推杆台阶部分的直径d 1=2d 。
推杆部分与模板上推杆孔的配合常采用H8/f8,推杆与推杆孔的配合长度取L=(2~3)d ,推杆工作端配合部分的粗糙度Ra ≤0.8μm 。
八 模具的冷却系统设计1 冷却水体积流量ABS 塑料的模具平均工作温度为60℃,用常温20℃的水作为模具冷却介质,其出口温度为30℃,每次注射质量为100g ,注射周期150s 。
ABS 注射成型固化时单位质量放出热量Δh=3.5*105J/kg 。
冷却水的体积流量计算如下:()21p t -t C 60hnm Vρ∆=式中:n ——每小时注射的次数ρ——冷却水在使用状态下的密度,1000kg/m 3 Cp ——冷却水的比热容,4187J/(kg •℃); t 1——冷却水出口温度,30℃t 2——冷却水入口温度,20℃ 2 冷却管道直径的确定及结构设计根据冷却水体积流量查表可初步确定冷却水管道直径;一般水孔的直径可根据塑件的平均壁厚来确定。
平均壁厚为2mm 时,水孔直径可取8~10mm ,平均壁厚为2~4mm 时,水孔直径可取10~12mm ,平均壁厚为4~6mm 时,水孔直径可取10~14mm 。
3 冷却回路所需的总表面积A()w m t -t 3600hnm Aα∆=式中:α——冷却水的表面传热系数, W/(m 2K) t m ——模具成型表面的温度 t w ——冷却水的平均温度 4 冷却回路的总长度 dAL π=模具的冷却分为两部分,一部分是型腔的冷却,另一部分是型芯的冷却 型腔的冷却水道结构。
型腔的冷却是由定模板(中间板)上的两条直径为 的冷却水道完成的;型芯冷却水道结构。
型芯部开有φ mm 的冷却孔,中间用隔水板隔开,冷却水由支撑板上的φ mm冷却水孔进入,型芯与支撑板之间用密封圈密封。
九模具模架的选择1 该模具采用一模两腔左右分布,分流道长度为40mm,所以型腔在分型面上投影尺寸为296mm*85mm,即l=296mm根据表7-3模板的侧壁厚度经验公式可得:S=0.2l+17mm=76.2mm由于l>100mm,实际模板的壁厚为(0.85~0.9)S,即(64~69)mm,初选取66mm。
支撑板厚度查表7-4,由于b=85mm<102mm,所以支撑板厚度:h=(0.12~0.13)l=(0.12~0.13)*296=(35.32~38.48)mm2 计算型腔模板周界整体式模板尺寸可以确定如下:型腔模板的长度: L=296+2S=448.4mm型腔模板的宽度: N=85+2S=237.4mm3 模板周界尺寸根据上面计算尺寸,查GB/T 4169.8-2006标准模板的尺寸,将计算出的数据向标准尺寸靠拢修整。
确定模板周界尺寸为250mm*450mm4 确定模板厚度该制件为薄壳形塑件,塑件高度为25mm,型腔设计在定模一侧,型腔深度取60mm即可5 选择模架类型根据已经确定下来的模具周边尺寸,配合模板所需厚度,查GB/T 12556-2006标准模板规格:九注射机有关参数的校核1 模具闭合高度的确定根据标准模架各模板尺寸及模具设计的其他零件尺寸:定模座板H定= 型腔板(定模板)H型= 型芯固定板H固=支撑板H支=垫板高度H垫=模脚H脚=模具闭合高度H1=H定+H型+H固+H支+H垫+H脚模具闭合高度和压力机的模具厚度关系应满足:H min≤Hm≤H max(H max=550,H min=250)2模具安装部分的校核该模具外形尺寸为L×B,XS-ZY-130型注射机模板最大安装尺寸为715mm*715mm,故能满足模具安装要求。