超硬材料烧结制品简答
烧结制品
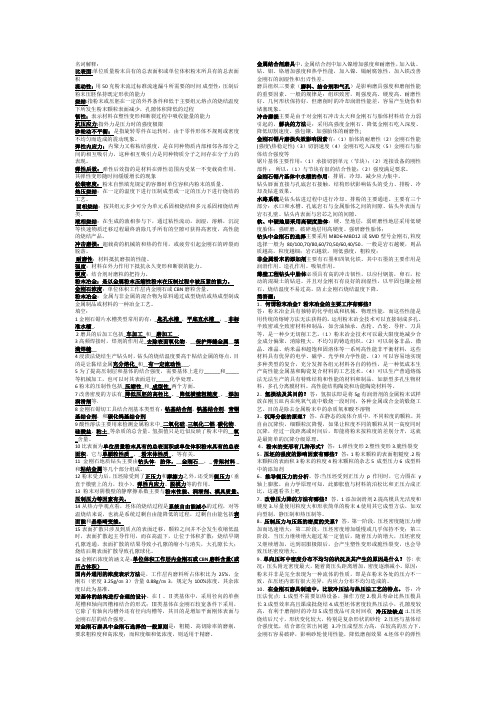
名词解释:比表面:单位质量粉末具有的总表面积或单位体积粉末所具有的总表面积流动性:用50克粉末流过标准流速漏斗所需要的时间成型性:压制后粉末压胚保持既定形状的能力烧结:指粉末或压胚在一定的外界条件和低于主要组元熔点的烧结温度下所发生粉末颗粒表面减少,孔隙体积降低的过程韧性:表示材料在塑性变形和断裂过程中吸收能量的能力抗压应力:指外力是压力时的强度极限砂轮动不平衡:是指旋转零件在运转时,由于零件形体不规则或密度不均匀而造成的震动现象。
弹性内应力:内聚力又称粘结强度,是在同种物质内部相邻各部分之间的相互吸引力,这种相互吸引力是同种物质分子之间存在分子力的表现。
弹性后效:弹性后效指的是材料在弹性范围内受某一不变载荷作用,其弹性变形随时间缓缓增长的现象松装密度:粉末自然填充规定的容器时单位容积内粉末的质量。
热压烧结:在一定的温度下进行压制成型或一定的压力下进行烧结的工艺。
固相烧结:按其组元多少可分为单元系固相烧结和多元系固相烧结两类。
液相烧结:在生成的液相参与下,通过粘性流动,润湿,溶解,沉淀等快速物质迁移过程最终消除几乎所有的空隙可获得高密度,高性能的烧结产品。
冲击磨损:超载荷的机械的和热的作用,或疲劳引起金刚石的碎裂而脱落。
耐磨性:材料抵抗磨损的性能。
强度:材料在外力作用下抵抗永久变形和断裂的能力。
硬度:结合剂对磨粒的把持力。
粉末冶金:是以金属粉末压缩性粉末在压制过程中被压紧的能力。
金刚石浓度:单位体积工作层内金刚石或CBN磨粒含量。
粉末冶金:金属与非金属的混合物为原料通过成型烧结或热成型制成金属制品或材料的一种冶金工艺。
填空:1金刚石锯片水槽类型常用的有:_匙孔水槽_,平底直水槽__,_ 非标准水槽_.2磨具的后加工包括_车加工_和__磨加工__.3高频焊接时,焊剂的作用是_去除表面氧化物、__保护焊缝金属__填满焊缝__4浸渍法烧结生产钻头时,钻头的烧结温度要高于粘结金属的熔点,目的是让黏结金属充分熔化_和__有一定流动性___.5为了提高压制层和基体的结合强度,需要基体上进行______和_____等机械加工,也可以对其表面进行_____化学处理。
关于金属结合剂超硬材料制品的“烧结工艺优化”问题的对话
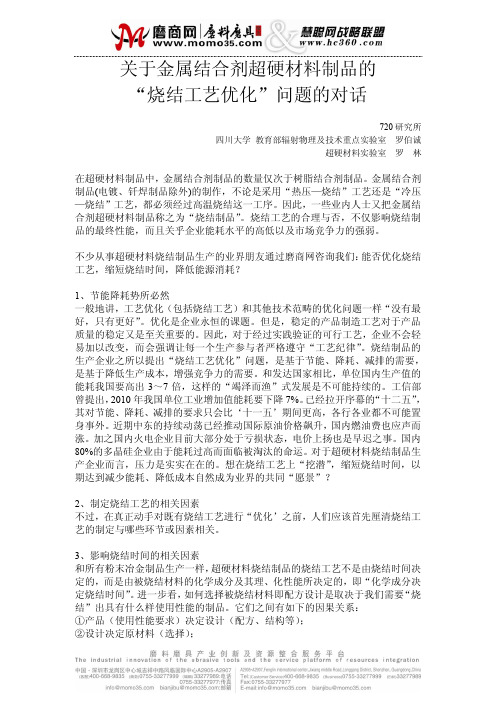
关于金属结合剂超硬材料制品的“烧结工艺优化”问题的对话720研究所四川大学教育部辐射物理及技术重点实验室罗伯诚超硬材料实验室罗林在超硬材料制品中,金属结合剂制品的数量仅次于树脂结合剂制品。
金属结合剂制品(电镀、钎焊制品除外)的制作,不论是采用“热压—烧结”工艺还是“冷压—烧结”工艺,都必须经过高温烧结这一工序。
因此,一些业内人士又把金属结合剂超硬材料制品称之为“烧结制品”。
烧结工艺的合理与否,不仅影响烧结制品的最终性能,而且关乎企业能耗水平的高低以及市场竞争力的强弱。
不少从事超硬材料烧结制品生产的业界朋友通过磨商网咨询我们:能否优化烧结工艺,缩短烧结时间,降低能源消耗?1、节能降耗势所必然一般地讲,工艺优化(包括烧结工艺)和其他技术范畴的优化问题一样“没有最好,只有更好”。
优化是企业永恒的课题。
但是,稳定的产品制造工艺对于产品质量的稳定又是至关重要的。
因此,对于经过实践验证的可行工艺,企业不会轻易加以改变,而会强调让每一个生产参与者严格遵守“工艺纪律”。
烧结制品的生产企业之所以提出“烧结工艺优化”问题,是基于节能、降耗、减排的需要,是基于降低生产成本,增强竞争力的需要。
和发达国家相比,单位国内生产值的能耗我国要高出3~7倍,这样的“竭泽而渔”式发展是不可能持续的。
工信部曾提出,2010年我国单位工业增加值能耗要下降7%。
已经拉开序幕的“十二五”,其对节能、降耗、减排的要求只会比‘十一五’期间更高,各行各业都不可能置身事外。
近期中东的持续动荡已经推动国际原油价格飙升,国内燃油费也应声而涨。
加之国内火电企业目前大部分处于亏损状态,电价上扬也是早迟之事。
国内80%的多晶硅企业由于能耗过高而面临被淘汰的命运。
对于超硬材料烧结制品生产企业而言,压力是实实在在的。
想在烧结工艺上“挖潜”,缩短烧结时间,以期达到减少能耗、降低成本自然成为业界的共同“愿景”?2、制定烧结工艺的相关因素不过,在真正动手对既有烧结工艺进行“优化’之前,人们应该首先厘清烧结工艺的制定与哪些环节或因素相关。
超硬材料及制品的基本知识

超硬材料及制品基本知识一、超硬材料概念:对于超硬材料的含义至今没有一个公认为满意的解释。
1981 年国际硬物质科学会议认为,硬度大于 1000HV 的物质均可称为硬物质,这就自然包括了金刚石和立方碳化硼。
后来对这个定义进行了补充,认为能加工诸如硬质合金(硬度 1600—1800HV )、刚玉(—2000HV)、碳化硅(—2200HV)等这一类物质的材料称为超硬材料。
目前由于金刚石和立方氮化硼等材料有其极高的硬度,所以统称为超硬材,具有硬度高、耐磨和热传导性能好、热膨胀系数低等优异性能。
二、超硬材料的分类:分为单晶超硬材料和聚晶超硬材料(也称为“复合超硬材料”)及 3.金刚石薄膜三类。
单晶超硬材料和聚晶超硬材料的主要区别为:单晶金刚石/立方氮化硼材料的特点为硬度更高、耐热性更好,但尺寸较小,多用于制造锯片等切割工具;聚晶金刚石/立方氮化硼是指以金刚石和立方氮化硼微粉等单晶超硬材料为主要原料,添加金属或非金属粘结剂通过超高压高温烧结工艺制成的聚晶复合材料。
它的特点是硬度、耐热性略逊于单晶材料,但是由于聚晶超硬材料是内部结构紧密的金刚石致密体,可以增加工具的切割面积,同时克服了单晶超硬材料由于粘结面积小造成的轻易从锯片表面脱落的弊端,具有更高的耐磨性。
金刚石薄膜是用化学气相沉积(CVD)法或其它方法在非金刚石衬底上制备出的超硬薄膜。
它不仅可用于制作各种金刚石刀具,还可作为功能材料用于制作声传感器、扬声器振动膜、红外窗口、X 光检测窗口等,应用领域十分广泛。
国际上从七十年代初开始进行金刚石薄膜的试制并迅速掀起金刚石薄膜研究开发热潮。
我国从八十年代中期开始此项研究,并已列入国家“863 计划”,现已能制备出 80mm、厚 2mm 的金刚石薄膜,并在应用研究方面取得了不少成果,但目前总体上仍处于研制阶段,尚未达到工业化应用阶段。
有人预计,金刚石薄膜将是 21 世纪金刚石工业的主要材料,各国科学家都在为使金刚石薄膜产业化而不懈努力。
不锈钢烧结组件
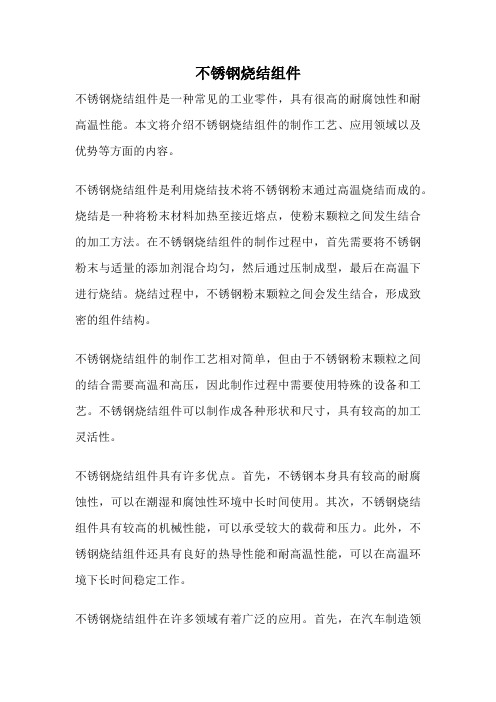
不锈钢烧结组件不锈钢烧结组件是一种常见的工业零件,具有很高的耐腐蚀性和耐高温性能。
本文将介绍不锈钢烧结组件的制作工艺、应用领域以及优势等方面的内容。
不锈钢烧结组件是利用烧结技术将不锈钢粉末通过高温烧结而成的。
烧结是一种将粉末材料加热至接近熔点,使粉末颗粒之间发生结合的加工方法。
在不锈钢烧结组件的制作过程中,首先需要将不锈钢粉末与适量的添加剂混合均匀,然后通过压制成型,最后在高温下进行烧结。
烧结过程中,不锈钢粉末颗粒之间会发生结合,形成致密的组件结构。
不锈钢烧结组件的制作工艺相对简单,但由于不锈钢粉末颗粒之间的结合需要高温和高压,因此制作过程中需要使用特殊的设备和工艺。
不锈钢烧结组件可以制作成各种形状和尺寸,具有较高的加工灵活性。
不锈钢烧结组件具有许多优点。
首先,不锈钢本身具有较高的耐腐蚀性,可以在潮湿和腐蚀性环境中长时间使用。
其次,不锈钢烧结组件具有较高的机械性能,可以承受较大的载荷和压力。
此外,不锈钢烧结组件还具有良好的热导性能和耐高温性能,可以在高温环境下长时间稳定工作。
不锈钢烧结组件在许多领域有着广泛的应用。
首先,在汽车制造领域,不锈钢烧结组件可以用于制作发动机和变速器零件,具有较高的耐磨性和耐腐蚀性,可以提高汽车的性能和寿命。
其次,在化工和医药领域,不锈钢烧结组件可以用于制作容器和管道等设备,可以抵抗腐蚀性介质的侵蚀。
此外,不锈钢烧结组件还广泛应用于航空航天、冶金和能源等领域。
不锈钢烧结组件是一种具有较高耐腐蚀性和耐高温性能的工业零件。
通过烧结技术制作而成,具有较高的机械性能和热导性能。
不锈钢烧结组件在汽车制造、化工、医药等领域有着广泛的应用。
其制作工艺相对简单,但制作过程中需要使用特殊设备和工艺,以确保制品的质量和性能。
随着科技的进步和工艺的改进,不锈钢烧结组件的应用领域将会越来越广泛。
超硬材料的制备与性能研究

超硬材料的制备与性能研究随着现代工业的发展,对材料的性能要求也越来越高,为了满足这种需求,科学家们研究出了一种新型的材料——超硬材料。
超硬材料具有极高的硬度、抗磨损性、耐腐蚀性和高温稳定性等特点,在工业生产中得到了广泛的应用。
本文将探讨超硬材料的制备与性能研究。
一、超硬材料的基础知识超硬材料是指硬度高于天然金刚石的材料,主要有金刚石、立方氮化硼、碳化钨等。
其中,金刚石是最早被发现和应用的超硬材料,由于它具有非常高的硬度和热导率等特点,广泛用于切削、打孔等工业领域。
立方氮化硼是一种新型的超硬材料,优于天然金刚石的地方在于它的热稳定性比金刚石更高,可用于高温环境下的切削和磨削。
碳化钨也是一种常用的超硬材料,它的硬度高于钢材、铸铁等常规材料,应用于切削、钻孔和磨削等领域。
二、超硬材料的制备方法超硬材料的制备方法主要有高温高压合成法、化学气相沉积法、热压法和爆炸合成法等。
高温高压合成法是一种常用的超硬材料制备方法,其原理是通过高温高压下,让粉末原料发生化学反应,形成超硬材料。
该方法制备的产品质量较高,但是制备过程比较复杂,需要高压高温设备,成本较高。
化学气相沉积法是利用化学气相沉积技术制备超硬材料的一种方法。
该方法需要使用反应气体,在高温条件下,让反应气体在基底上沉积出超硬材料膜。
该方法所制备的超硬材料膜均匀、致密,具有很好的金属附着力,但是成本较高,适用于小批量生产。
热压法是将粉末原料放入模具中,在高温高压下进行热压成型,制成超硬材料。
该方法制备出的超硬材料成型精度高,但成本相对较高。
爆炸合成法是通过爆炸反应产生超高压和超高温条件,使原料发生同位素反应,产生超硬材料。
该方法成本较低,可批量生产,但制备过程不稳定,也有一定几率出现批次不一致的情况。
三、超硬材料的性能研究超硬材料主要是以其硬度和抗磨损性为主要特点研究的。
硬度是超硬材料的重要性能参数之一,硬度的高低决定了超硬材料在切削、磨削等领域的应用范围。
烧结工艺知识点总结大全

烧结工艺知识点总结大全一、烧结原理1. 烧结是指将粉末材料在一定温度下加热,使其颗粒间发生结合,形成致密的块状产品。
烧结的基本原理是固相扩散,即热力学上的固相之间的扩散过程。
2. 烧结过程中主要有三种力学过程,分别为颗粒间的原子扩散、颗粒间的表面扩散和颗粒间的体扩散。
这三种扩散方式相互作用,共同促进颗粒间发生结合。
3. 烧结过程中温度、时间和压力是影响烧结效果的重要因素。
通过控制这些参数,可以使烧结过程更加均匀和有效。
二、烧结设备1. 烧结设备主要包括热处理炉、烧结炉、烧结机等。
不同的烧结设备适用于不同的烧结材料和工艺要求。
2. 烧结设备的主要部件包括燃烧室、加热炉、炉膛、热风循环系统、控制系统等。
这些部件共同作用,实现对粉末材料的加热和烧结作用。
3. 热处理炉是常见的烧结设备之一,主要通过电阻加热、气体燃烧等方式对粉末材料进行加热处理,适用于各种金属和非金属材料的烧结工艺。
三、烧结工艺控制1. 烧结工艺控制是烧结过程中的关键环节,可以通过控制温度、时间、压力等参数,实现对烧结过程的精确控制。
2. 烧结工艺控制的主要方法包括PID控制、自适应控制、模糊控制等。
这些控制方法通过对烧结过程中的各个参数进行实时监测和调整,以实现对烧结过程的精确控制。
3. 在实际生产中,烧结工艺控制可以通过计算机控制系统实现自动化,提高生产效率和产品质量。
四、烧结材料选型1. 烧结工艺适用于各种粉末材料,包括金属粉末、陶瓷粉末、粉末冶金材料等。
根据不同的材料性质和要求,选择合适的烧结工艺和设备。
2. 烧结材料的选型考虑因素包括原料种类、粒度、成分、形状等。
根据不同的要求,选择合适的烧结材料,可以有效提高产品质量和生产效率。
3. 在烧结材料选型过程中,也需要考虑成本、资源利用率和环境保护等方面的因素,以实现经济、环保和可持续发展。
五、烧结工艺的应用1. 烧结工艺广泛应用于金属、陶瓷、粉末冶金、电子材料等行业。
在金属制品生产中,烧结工艺可以用于制造各种粉末冶金制品、焊接材料、钎焊材料等。
烧结金属材料

烧结金属材料烧结金属材料是一种常见的金属加工材料,具有高强度、耐磨、耐腐蚀等优良性能,广泛应用于机械制造、航空航天、汽车制造等领域。
烧结金属材料的制备工艺、性能特点及应用领域备受关注。
烧结金属材料的制备工艺主要包括原料准备、混合、压制、烧结等工序。
首先,选用适合的金属粉末作为原料,经过精细加工和混合,确保金属粉末的均匀性和纯度。
然后,将混合后的金属粉末放入模具中,进行压制成型,以确保产品的密度和形状。
最后,将成型的金属坯体进行烧结,通过高温处理使金属颗粒结合成整体,形成烧结金属材料。
烧结金属材料具有优异的性能特点,主要包括高强度、硬度大、耐磨损、耐腐蚀、导热性能好等。
这些性能使得烧结金属材料在机械制造领域得到广泛应用,如汽车发动机零部件、航空航天发动机叶片、工程机械耐磨件等。
同时,烧结金属材料还具有良好的加工性能,可进行切削、焊接、表面处理等工艺,满足不同领域的需求。
烧结金属材料的应用领域广泛,涉及机械制造、航空航天、汽车制造、能源设备等多个领域。
在机械制造领域,烧结金属材料可用于制造高强度、耐磨损的零部件,提高机械设备的使用寿命和可靠性。
在航空航天领域,烧结金属材料可用于制造高温、高压下工作的零部件,如涡轮叶片、涡轮盘等,提高发动机的工作效率和可靠性。
在汽车制造领域,烧结金属材料可用于制造发动机零部件、传动零部件、刹车系统零部件等,提高汽车的性能和安全性。
在能源设备领域,烧结金属材料可用于制造耐磨、耐腐蚀的零部件,提高设备的使用寿命和可靠性。
总的来说,烧结金属材料具有制备工艺简单、性能优异、应用领域广泛等特点,是一种重要的金属加工材料。
随着科技的发展和工艺的改进,烧结金属材料将在各个领域发挥更加重要的作用,推动相关行业的发展和进步。
超硬材料烧结,金属烧结考试试题答案版
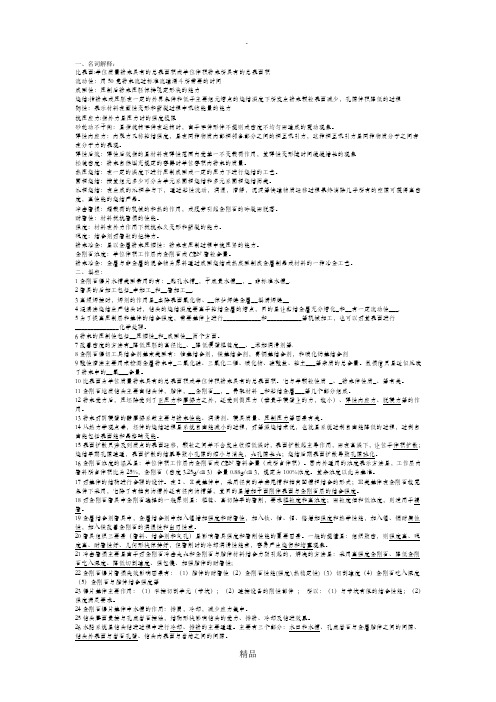
一、名词解释:比表面:单位质量粉末具有的总表面积或单位体积粉末所具有的总表面积流动性:用50克粉末流过标准流速漏斗所需要的时间成型性:压制后粉末压胚保持既定形状的能力烧结:指粉末或压胚在一定的外界条件和低于主要组元熔点的烧结温度下所发生粉末颗粒表面减少,孔隙体积降低的过程韧性:表示材料在塑性变形和断裂过程中吸收能量的能力抗压应力:指外力是压力时的强度极限砂轮动不平衡:是指旋转零件在运转时,由于零件形体不规则或密度不均匀而造成的震动现象。
弹性内应力:内聚力又称粘结强度,是在同种物质内部相邻各部分之间的相互吸引力,这种相互吸引力是同种物质分子之间存在分子力的表现。
弹性后效:弹性后效指的是材料在弹性范围内受某一不变载荷作用,其弹性变形随时间缓缓增长的现象松装密度:粉末自然填充规定的容器时单位容积内粉末的质量。
热压烧结:在一定的温度下进行压制成型或一定的压力下进行烧结的工艺。
固相烧结:按其组元多少可分为单元系固相烧结和多元系固相烧结两类。
液相烧结:在生成的液相参与下,通过粘性流动,润湿,溶解,沉淀等快速物质迁移过程最终消除几乎所有的空隙可获得高密度,高性能的烧结产品。
冲击磨损:超载荷的机械的和热的作用,或疲劳引起金刚石的碎裂而脱落。
耐磨性:材料抵抗磨损的性能。
强度:材料在外力作用下抵抗永久变形和断裂的能力。
硬度:结合剂对磨粒的把持力。
粉末冶金:是以金属粉末压缩性:粉末在压制过程中被压紧的能力。
金刚石浓度:单位体积工作层内金刚石或CBN磨粒含量。
粉末冶金:金属与非金属的混合物为原料通过成型烧结或热成型制成金属制品或材料的一种冶金工艺。
二、填空:1金刚石锯片水槽类型常用的有:_匙孔水槽_,平底直水槽__,_ 非标准水槽_.2磨具的后加工包括_车加工_和__磨加工__.3高频焊接时,焊剂的作用是_去除表面氧化物、__保护焊缝金属__填满焊缝__4浸渍法烧结生产钻头时,钻头的烧结温度要高于粘结金属的熔点,目的是让黏结金属充分熔化_和__有一定流动性___.5为了提高压制层和基体的结合强度,需要基体上进行____________和___________等机械加工,也可以对其表面进行______________化学处理。
超硬材料烧结制品简答

1.酸不溶物测定粉末化学成分的原理是什么?对青铜测定时有什么特殊性? 答:(1)原理:金属粉末中2SiO ,32O Al ,碳化硅,硅酸盐、粘土等杂质均不溶于酸,为此,可将粉末试样用某种无机酸(铜用3HNO ,铁用HCl )溶解,滤出沉淀物于900--1000℃下煅烧至恒重,即可计算出粉末中酸不溶物杂质相对含量。
(2)对青铜粉末测定时,由于2SnO 不溶于硝酸,应该扣除该部分含量。
在硝酸不溶物中加入NH4I 于坩埚中加热到425--475℃,煅烧15min ,碘挥发,2SnO 被还原为能溶于硝酸的SnO ,加2--3ml 硝酸使其完全溶解,此时残留物与粉末的质量之比的百分数即为酸的不溶物含量。
2.金属粉末性能测定中利用的沉降天平测粒度分布,其原理是什么?3.答:在静态的流体介质中,不同粒度的颗粒,其自由沉降的速率不同,粗颗粒沉降快,细颗粒沉降慢。
如果让粒度不等的颗粒从同一起点高度同时沉降,经过一定距离或时间后,即能将粉末按粒度的差别分开。
用沉降天平测总重量随沉降时间的变化,得到总重量与沉降时间的实际沉降曲线。
在该曲线上取若干个点,分别作曲线的切线,量出切线的纵截距值,再由各点对应的沉降时间按沉降公式计算粒径,最后,计算所取若干粒级内粉末的百分含量,就可作成粒度分布曲线。
3.松装对粉末的压制性和烧结性影响。
答:对压制性的影响:粉末的压制性包括压缩性和成型性。
颗粒形状越规则,结构越细致,粒度越粗,则松装密度越高,压缩性越好。
一般来说,压缩性好的粉末,其成型性往往较差。
对烧结性影响:烧结过程是粉末体由高能位转变的过程,粉末颗粒越细,形状和结构越复杂,则松装密度越低,有利于扩散和合金均匀,如果粉末粒度形状简单,表面平滑,松装密度高,烧结性差。
4.氢损法测定金属粉末的含氧量的原理。
该方法适用于怎样的金属?为什么说它测定的一般不是全部的氧含量?答:原理:氢损法是将5g 有润滑剂的金属粉末试样放在刚玉舟皿内在纯氢气流中煅烧一段时间,煅烧时,粉末中的洋河请结合生成水汽排出使得粉末总重减少,减少值占粉末试样重量的百分数即为氢损值。
烧结基础知识

烧结基础知识烧结是把粉状物料转变为致密体,是一个传统的工艺过程。
那么你对烧结了解多少呢?以下是由店铺整理关于烧结知识的内容,希望大家喜欢!烧结的定义宏观定义:在高温下(不高于熔点),陶瓷生坯固体颗粒的相互键联,晶粒长大,空隙(气孔)和晶界渐趋减少,通过物质的传递,其总体积收缩,密度增加,最后成为具有某种显微结构的致密多晶烧结体,这种现象称为烧结。
微观定义:固态中分子(或原子)间存在互相吸引,通过加热使质点获得足够的能量进行迁移,使粉末体产生颗粒黏结,产生强度并导致致密化和再结晶的过程称为烧结。
烧结的方法及测量将试条放入烘箱内,在105~110℃下烘干至恒重。
在干燥器内冷却至室温后备用。
在天平上称取干燥后的试样重。
称取饱吸煤油后在煤油中试样重。
饱吸煤油后在空气中的试样重。
将称好重量的试样放入105~110℃烘箱内排除煤油,直至将试样中的煤油排完为止。
按编号顺序将试样装入高温炉中,装炉时炉底和试样之间撒一层薄薄的煅烧石英粉或Al2O3粉。
装好后开始加热,并按升温曲线升温,按预定的取样温度取样。
在每个取样温度点保温15min,然后从电炉内取出试样迅速地埋在预先加热的石英粉或Al2O3粉中,以保证试样在冷却过程中不炸裂。
冷至接近室温后,将试样编号,取样温度记录于表中,检查试样有无开裂、粘砂等缺陷。
然后放入105~110℃烘箱中烘至恒重。
取出试样放入干燥器内,冷却至室温。
将试样分成两批,900℃以下为第一批,测定其饱吸煤油后在煤油后在空气中重,900℃以上的试样为第二批,测定其饱吸水后在水中重及饱吸水后在空气重。
按公式算出各温度点的结果后,以温度为横坐标,气孔率和收缩率为纵坐标,画出收缩率和气孔率曲线,并从曲线上确定烧结温度和烧结温度范围。
烧结的意义烧结时的温度称为烧结温度,烧结温度和开始过烧温度之间的温度范围称为烧结温度范围,在烧结过程中若不确定烧结温度和烧结温度范围继续升温,则坯体开始变形、软化、过烧膨胀,造成烧结事故。
《超硬材料烧结制品》课程设计指导书本
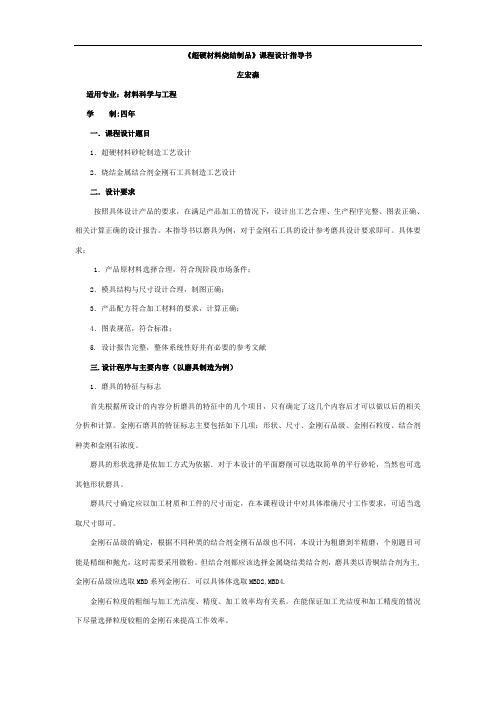
《超硬材料烧结制品》课程设计指导书左宏森适用专业:材料科学与工程学制:四年一.课程设计题目1.超硬材料砂轮制造工艺设计2.烧结金属结合剂金刚石工具制造工艺设计二.设计要求按照具体设计产品的要求,在满足产品加工的情况下,设计出工艺合理、生产程序完整、图表正确、相关计算正确的设计报告。
本指导书以磨具为例,对于金刚石工具的设计参考磨具设计要求即可。
具体要求:1.产品原材料选择合理,符合现阶段市场条件;2.模具结构与尺寸设计合理,制图正确;3.产品配方符合加工材料的要求,计算正确;4.图表规范,符合标准;5. 设计报告完整,整体系统性好并有必要的参考文献三.设计程序与主要内容(以磨具制造为例)1.磨具的特征与标志首先根据所设计的内容分析磨具的特征中的几个项目,只有确定了这几个内容后才可以做以后的相关分析和计算。
金刚石磨具的特征标志主要包括如下几项:形状、尺寸、金刚石品级、金刚石粒度、结合剂种类和金刚石浓度。
磨具的形状选择是依加工方式为依据.对于本设计的平面磨削可以选取简单的平行砂轮,当然也可选其他形状磨具。
磨具尺寸确定应以加工材质和工件的尺寸而定,在本课程设计中对具体准确尺寸工作要求,可适当选取尺寸即可。
金刚石品级的确定,根据不同种类的结合剂金刚石品级也不同,本设计为粗磨到半精磨,个别题目可能是精细和抛光,这时需要采用微粉。
但结合剂都应该选择金属烧结类结合剂,磨具类以青铜结合剂为主,金刚石品级应选取MBD系列金刚石.可以具体体选取MBD2,MBD4.金刚石粒度的粗细与加工光洁度、精度、加工效率均有关系。
在能保证加工光洁度和加工精度的情况下尽量选择粒度较粗的金刚石来提高工作效率。
金刚石浓度的确定主要考虑三个方面:其一是结合剂对金刚石有较高的把持力:其二是不增加金刚石磨具的成本。
一般常用浓度在75%一125%之间。
2.模具结构、尺寸和技术要求模具的设计部分包括模具的结构设计和尺寸设计(计算)。
模具结构设计与产品生产时特别是成型时的成型方式有直接关系,比如单向成型、双向成型等,在结构设计中还要考虑成型后的卸模方式。
超硬材料烧结,金属烧结考试试题答案版教学文案

超硬材料烧结,金属烧结考试试题答案版一、名词解释:比表面:单位质量粉末具有的总表面积或单位体积粉末所具有的总表面积流动性:用50克粉末流过标准流速漏斗所需要的时间成型性:压制后粉末压胚保持既定形状的能力烧结:指粉末或压胚在一定的外界条件和低于主要组元熔点的烧结温度下所发生粉末颗粒表面减少,孔隙体积降低的过程韧性:表示材料在塑性变形和断裂过程中吸收能量的能力抗压应力:指外力是压力时的强度极限砂轮动不平衡:是指旋转零件在运转时,由于零件形体不规则或密度不均匀而造成的震动现象。
弹性内应力:内聚力又称粘结强度,是在同种物质内部相邻各部分之间的相互吸引力,这种相互吸引力是同种物质分子之间存在分子力的表现。
弹性后效:弹性后效指的是材料在弹性范围内受某一不变载荷作用,其弹性变形随时间缓缓增长的现象松装密度:粉末自然填充规定的容器时单位容积内粉末的质量。
热压烧结:在一定的温度下进行压制成型或一定的压力下进行烧结的工艺。
固相烧结:按其组元多少可分为单元系固相烧结和多元系固相烧结两类。
液相烧结:在生成的液相参与下,通过粘性流动,润湿,溶解,沉淀等快速物质迁移过程最终消除几乎所有的空隙可获得高密度,高性能的烧结产品。
冲击磨损:超载荷的机械的和热的作用,或疲劳引起金刚石的碎裂而脱落。
耐磨性:材料抵抗磨损的性能。
强度:材料在外力作用下抵抗永久变形和断裂的能力。
硬度:结合剂对磨粒的把持力。
粉末冶金:是以金属粉末压缩性:粉末在压制过程中被压紧的能力。
金刚石浓度:单位体积工作层内金刚石或CBN磨粒含量。
粉末冶金:金属与非金属的混合物为原料通过成型烧结或热成型制成金属制品或材料的一种冶金工艺。
二、填空:1金刚石锯片水槽类型常用的有:_匙孔水槽_,平底直水槽__,_非标准水槽_.2磨具的后加工包括_车加工_和__磨加工__.3高频焊接时,焊剂的作用是_去除表面氧化物、__保护焊缝金属__填满焊缝__4浸渍法烧结生产钻头时,钻头的烧结温度要高于粘结金属的熔点,目的是让黏结金属充分熔化_和__有一定流动性___.5为了提高压制层和基体的结合强度,需要基体上进行____________和___________等机械加工,也可以对其表面进行______________化学处理。
硬质合金烧结原理

硬质合金烧结原理硬质合金烧结原理所谓烧结就是将粉末压坯加热到一定温度(烧结温度)并保持一定的时间(保温时间),然后冷却下来,从而得到所需性能的材料,这种热处理工艺叫做烧结。
烧结使多孔的粉末压坯变为具有一定组织和性能的制品,尽管制品性能与烧结前的许多工艺因素有关,但是在许多情况下,烧结工艺对最终制品组织和性能有着重大的甚至是决定性的影响。
硬质合金的烧结过程是比较复杂的,但是这些基本知识又是必须掌握的。
4.1烧结过程的分类烧结过程的分类方法很多,按烧结制品组元的多少可以分为单元系烧结和多元系烧结,如钨、钼条烧结属于单元系烧结,硬质合金绕结则属于多元系烧结。
按烧结时组元中相的状态分为固相烧结和液相烧结,如钨钼的烧结过程中不出现液相,属于固相烧结,硬质合金制品在烧结过程中会出现液相,属于液相烧结。
按工艺特征来分,可分为氢气烧结、真空烧结、活化烧结、热等静压烧结等。
许多烧结方法都能用于硬质合金的烧结。
此外,还可以依烧结材料的名称来分,如硬质合金烧结,钼顶头烧结。
从学习烧结过程的实质来说,将烧结过程分为固相烧结和液相烧结两大类是比较合理的,但在生产中多按烧结工艺特点来进行分类。
4.2烧结过程的基本变化硬质合金压坯经过烧结后,最容易观察到的变化是压块体积收缩变小,强度急剧增大,压块孔隙度一般为50%,而烧结后制品已接近理论密度,其孔隙一般应小于0.2%,压块强度的变化就更大了,烧结前压坯强度低到无法用一般方法来测定,压坯只承受生产过程中转移时所必备的强度,而烧结后制品却能达到满足各种苛刻工作条件所需要的强度值,显然制品强度提高的幅度较之密度的提高要大得多。
制品强度及其他物理机械能的突变说明在烧结过程中压块发生了质的变化。
在压制过程中,虽然由于外力的作用能增加粉末体的接触面,而颗粒中表面原子和分子还是杂乱无章的,甚至还存在有内应力,颗粒间的联结力是很弱的,但烧结后颗粒表面接触状态发生了质的变化,这是由于粉末接触表面原子﹑分子进行化学反应,以及扩散、流动、晶粒长大等物理化学变化,使颗粒间接触紧密,内应力消除,制品形成了一个强的整体,从而使其性能大大提高。
超硬材料烧结制品课程设计烧结金刚石串珠绳的制作大学论文

河南工业大学课程设计课程设计名称:超硬材料烧结制品专业班级:学生姓名:学号:指导老师:何方课程设计时间:《超硬材料烧结制品》课程设计任务书目录第一章设计目的及产品说明…………………第二章设计产品的尺寸与形状………………第三章配方设计……………………………§3.1 结合剂的选择…………………………§3.2 结合剂中各成分的选择………………§3.3 结合剂中各成分的用量计算…………第四章工艺流程………………………………§4.1 工艺流程图的绘制……………………§4.2 烧结工艺………………………………第五章原材料的确定…………………………§5.1 基体……………………………………§5.2 金刚石…………………………………§5.3 金属粉末………………………………§5.4 润湿剂和临时粘结剂…………………第六章压制成型模具的设计…………………§6.1 模具结构………………………………§6.2 模具各部分尺寸的设计………………第七章设备的选择……………………………§7.1混料设备选择§7.2压机的选择………………………………§7.3烧结设备选择§7.4其它设备选择……………………………第八章操作流程………………………………§8.1 压制成型操作…………………………§8.2 热压成型操作…………………………§8.3 装炉与冷却出炉………………………第九章产品的后加工……………………第十章质量检测………………………………参考文献作为一种常用的现代工程结构建材料,混凝土在房屋.桥梁、隧道。
机场矿井等方面应用极其广泛。
随着混凝土的广泛应用,混凝土的切割也成为一个庞大的产业,特别是二战以后界各国经济快速发展,在房屋建筑道路桥梁等行业投入巨资建设,混凝土的切割技术也随之快速发展并逐渐成熟起来。
超硬材料和硬质合金的固体特征(5)

通常情况下,由于间隙周边的原子之间的化学键强度更弱且有更多 的间隙位置,因此间隙扩散比空位扩散更快。 更小的能量势垒。 原子半径更小的原子(例如,C, H,O等)能够匹配进入间隙位置。
扩散原子的流量(J)
单位时间单位面积上的原子数量[atoms/(m2s)]
原子在开放的晶格或方向扩散地更快
扩散:微观结构的作用
金的自扩散系数依赖于扩散路径:晶界和表面具有更少的限制
影响扩散的因素
温度- 扩散率随着温度的增加而迅速地增加 扩散机理 – 间隙扩散通常比空位扩散更快 微观结构 – 由于沿晶界和位错的更快扩散率,原子在 多晶中比在单晶中的扩散速率更快。
R0 = attempt frequency proportional to vibration frequency
如何计算激活扩散?
1. 在邻近晶格位置发现空位的几率
乘与
2. 原子热波动的几率
Q P Const.exp v k T B
E R j R0 exp m k T B
重要的概念
扩散的应用 扩散激活能
扩散的机理
菲克第一定律和第二定律 影响扩散的因素
扩散的应用
陶瓷热障涂层被广泛地用于保护高负荷燃气涡轮机部件免受过热; 超硬材料涂层硬质合金刀具。
2
更重要的应用:硬质合金的烧结
烧结过程的几个阶段
• 固相烧结阶段 (800℃~共晶温度):所谓共晶温度是指缓慢升温时, 烧结体中开始出现共晶液相的温度,对于WC-Co合金,在平衡烧结 时的共晶温度为1340℃。烧结体中的某些固相反应加剧,扩散速度 增加,颗粒塑性流动加强,使烧结体出现明显的收缩。 • 液相烧结阶段 (共晶温度~烧结温度):当烧结出现液相后,烧结体 收缩很快完成,碳化物晶粒长大并形成骨架,从而奠定了合金的基 本组织结构。 • 冷却及热处理阶段:在这一阶段,合金的组织和枯结相成分随冷 却条件的不同而产生某些变化。冷却后,得到最终组织结构的合金。
金刚石烧结制品重点

简答题:1.什么叫做比表面?比表面与颗粒的哪些性质有关?2.论述影响松装密度、流动性和压制性的因素及之间的关系.3..叙述压坯密度与压制压力之间的变化规律.4.叙述再结晶与晶粒长大的动力学过程.5.为什么金属结合剂的金刚石制品常常采用热压烧结?6.叙述液相烧结过程.7.简述结合剂的组成性能与加工材质和加工方式的关系.8.叙述金属结合剂的对金刚石烧结制品使用性能的影响。
9.需制造某种磨具5片,已知磨具的单片质量为530克,所选用的结合剂成分配比(质量分数%)为Cu78Sn12Ag7Zn3,外加石墨1%。
求各种粉末的用量。
(设投料系数为1.05)10.如何判断混合结合剂后,其是否混合均匀?11.结合剂贮存应注意什么?12.磨具产品的测试主要有哪些内容?13.简要列出配方设计的试验工作的一般程序。
14.已知非金刚石层体积和金刚石层体积分别为:Vi=13.56cm3,V=12.35cm3。
采用冷压成型工艺,结合剂成型密度的γ=7.5g/cm3,金刚石浓度为100%。
求金刚石用量和结合剂用量(包括非金刚石层的结合剂用量)。
15.叙述热压法工艺特点为。
16.冷压烧结过程中500℃的保温阶段坯体内主要发生什么变化?为什么此阶段十分重要?17.冷压烧结时,冷却阶段对最终产品的性能有什么影响?18.如果金刚石磨具出现废品时,通过镜下观察发现其组织结构不均匀,在实际生产中,我们应从哪几个方面分析其产生的原因。
19.叙述金刚石在切割过程中磨损情况。
20.根据切割工件材料特点对选择金刚石和结合剂有什么要求。
21.对于长为40mm,高为5mm,厚为4mm的节块,计算1000个节块金刚石用量、金刚石层结合剂用量、过渡层料的用量。
假设成型密度为8.89g/cm3,金刚石的浓度按50%计算。
22.选择焊料一般要满足什么样的要求。
23.写出一般金刚石锯片制造工艺流程24.叙述锯片开刃过程。
25.在制造金刚石钻头时,调整胎体硬度的方法主要有哪些?26.为什么说钻头胎体的硬度选择在使用过程中起着重要的作用。
- 1、下载文档前请自行甄别文档内容的完整性,平台不提供额外的编辑、内容补充、找答案等附加服务。
- 2、"仅部分预览"的文档,不可在线预览部分如存在完整性等问题,可反馈申请退款(可完整预览的文档不适用该条件!)。
- 3、如文档侵犯您的权益,请联系客服反馈,我们会尽快为您处理(人工客服工作时间:9:00-18:30)。
1. 酸不溶物测定粉末化学成分的原理是什么?对青铜测定时有什么特殊性?答:(1)原理:金属粉末中,,碳化硅,硅酸盐、粘土等杂质均不溶于酸,为此,可将粉末试样用某种无机酸(铜用,铁用HCl)溶解,滤出沉淀物于900--1000℃下煅烧至恒重,即可计算出粉末中酸不溶物杂质相对含量。
(2)对青铜粉末测定时,由于不溶于硝酸,应该扣除该部分含量。
在硝酸不溶物中加入NH4I于坩埚中加热到425--475℃,煅烧15min,碘挥发,被还原为能溶于硝酸的,加2--3ml硝酸使其完全溶解,此时残留物与粉末的质量之比的百分数即为酸的不溶物含量。
2. 金属粉末性能测定中利用的沉降天平测粒度分布,其原理是什么?3. 答:在静态的流体介质中,不同粒度的颗粒,其自由沉降的速率不同,粗颗粒沉降快,细颗粒沉降慢。
如果让粒度不等的颗粒从同一起点高度同时沉降,经过一定距离或时间后,即能将粉末按粒度的差别分开。
用沉降天平测总重量随沉降时间的变化,得到总重量与沉降时间的实际沉降曲线。
在该曲线上取若干个点,分别作曲线的切线,量出切线的纵截距值,再由各点对应的沉降时间按沉降公式计算粒径,最后,计算所取若干粒级内粉末的百分含量,就可作成粒度分布曲线。
3. 松装对粉末的压制性和烧结性影响。
答:对压制性的影响:粉末的压制性包括压缩性和成型性。
颗粒形状越规则,结构越细致,粒度越粗,则松装密度越高,压缩性越好。
一般来说,压缩性好的粉末,其成型性往往较差。
对烧结性影响:烧结过程是粉末体由高能位转变的过程,粉末颗粒越细,形状和结构越复杂,则松装密度越低,有利于扩散和合金均匀,如果粉末粒度形状简单,表面平滑,松装密度高,烧结性差。
4. 氢损法测定金属粉末的含氧量的原理。
该方法适用于怎样的金属?为什么说它测定的一般不是全部的氧含量?答:原理:氢损法是将5g有润滑剂的金属粉末试样放在刚玉舟皿内在纯氢气流中煅烧一段时间,煅烧时,粉末中的洋河请结合生成水汽排出使得粉末总重减少,减少值占粉末试样重量的百分数即为氢损值。
适用:(1)粉末金属氧化物中氧能被还原的金属(2)高熔点的金属(不易挥发的金属)氢损值只是近似反映粉末中的氧含量,因为在煅烧过程中,粉末中SiO2,Al2O3,MgO,CaO等含氧杂质不能被还原,而一些非氧杂质C,S等却能与氢生成挥发性化合物排出,同时,粉末表面吸附的气体杂质和粉末中低共熔点金属Zn,Cd,Pb等也挥发排出,因此给准确测量氧含量带来了困难。
5、金属粉末中常见的杂质类型?如何减少这些杂质?答:(1)与主金属结合形成固溶体或化合物的金属或非金属元素(2)原材料和粉末生产过程中带进的机械夹杂(3)粉末颗粒表面的杂质(4)制粉工艺带来的杂质减少杂质的方法:(1)通过避免或控制P、T等参数实现(2)改进加工设备(3)对粉末做真空保护(4)提升制作工艺水平。
6、影响粉末松装密度的因素?答:松装密度取决于粉末材料的密度、颗粒的形状、表面状态、颗粒的孔隙、粉末粒度及粒度组成。
7、粉末流动性的影响因素?1、粉末颗粒形状,颗粒越复杂流动性越差2、粉末粒度及组成,粒度越细其流动性越差,细粉末占得比例越大,流动性越差3、颗粒表面杂质,表面氧化吸附杂质以及添加润湿剂等会降低流动性4、松装密度,松装密度大,流动性好5、材料粉末密度,材料粉末密度高、流动性好8、金刚石钻头的胎体硬度的调整方法?1、胎体硬度的调整方法主要有:1、改变胎体骨架的成型密度,密度大,硬度高,反之低;2、改变胎体的骨架的成分,比如骨架成分中硬质材料成分多时硬度高,反之则低,3、改变粘结金属的成分,除此之外,三种方法综合运用也可以获得不同胎体的硬度。
9.金刚石地质表锒钻头的金刚石分布遵守的原则。
(1)金刚石均匀分布满胎体表面,刻取岩石表面重叠,不能有空隙(2)便于冲洗液排除岩粉不冲坏(3)充分冷却金刚石10.液相烧结组织结构与润湿性有什么关系?液相烧结在烧结温度下结合剂熔融成为液相,若液相润湿性好,则胚体组织均匀,致密度高,稳定性好。
润湿角等于零完全润湿,液体均匀分布在颗粒周围组织致密均匀,几乎无水隙。
润湿角在零到九十度之间润湿结合剂也能填充在颗粒孔隙处,有一定的孔隙,但孔隙率很小,组织较均匀,润湿角大于九十度不润湿,结合剂只是很少量分布在颗粒的孔隙处,组织不均匀,孔隙率大。
11.金刚石焊接锯片的结块结构有哪些,有何优点?答:1.通用型节块(截面形状呈矩形)优点:制造方便快捷,使用寿命长,适用于一般大理石和软花岗岩加工)2.夹心节块 优点:切割效率较高,稳定性好,切片厚薄均匀,基体也不易变形,保证了复焊次数)3.台阶形结块 优点:切割效率较高,功耗小,锯片不易变形,保证了石材的加工厚度和平直厚度。
12.高频焊接钎料的选择原则是什么?1. 焊料的熔化温度低于节块的热压烧结温度,一般低100~200度左右。
2. 焊料对节块和钢基体的可焊接性较好3. 焊料熔融后流动性要好,表面张力要小4. 经济性好,货源充足5. 符合环保要求13、分析影响压制过程的因素答:原材料的影响:(1)粉末颗粒的材质(2)粉末颗粒的形状(3)粉末的粒度及粒度组成(4)润滑剂和成型机压制成型条件的影响:(1)压制方式(2)加压速度(3)保压时间(4)成型磨具的性能(5)压机性能14、圆柱形压坯单双向成型时内部各区域密度情况及原因答:(1)单向压制时:在单向压制的压坯中,各层的平均密度沿高度方向从上至下降低,最底层密度最低,在横截面上,上层的密度中间小边缘远大,下层的密度分布则相反。
作用在粉末各处的压制压力是不一致的,在压头附近,坯体密度最大,随着离压头距离的增加,密度逐渐减小,特别是在模壁处。
(2)双向压制时:密度分布上下对称,接近压头层的密度高,坯体中间部分的密度最低。
在压坯中存在几乎不移动的“中立层”,是压坯密度最小的部分。
单向压制时中立层在最底部,双向压制时中立层在中间部位,中立层的位置可以反映压坯密度分布的均匀程度。
15.试分析金刚石青铜磨具中锡含量对磨具力学性能及磨削性能的影响?答:当含锡量小于6%时,锡青铜塑性很大,且随着含锡亮的增加,塑性和强度都增大。
当含锡量大于6%时,由于合金中出现硬脆的相,塑性急剧下降,硬度提高,此时强度继续提高,当含锡量大于20%后,合金组织中有大量的δ相,使得合金变得很脆,强度由最高峰值急剧下降。
锡含量在10%-25%间的锡青铜,不仅强度、硬度高,而且有较高的脆性,磨削性能较好,适合做磨具结合剂。
16.金属粉末成型密度与压力之间关系的变化规律答:粉末成型料在压力作用下,随着颗粒的位移和变形,压坯密度出现有规律的变化,大致分为三个阶段:第一阶段(滑移阶段),压坯密度随着压力而迅速增加,这是因为粉末的拱桥现象在不大的压力作用下迅速消除,粉末颗粒位移距离较大,使孔隙急剧减小。
第二阶段(保持阶段),压坯密度增加缓慢或几乎保持不变,这是由于大量的孔隙已在第一阶段消除,压坯密度已经达到一定值,继续增大压力的结果是使颗粒发生弹性变形,粉末颗粒的位移小。
第三阶段(变形阶段),当压力继续增加超过某一定值后,随着压力的增加,压坯密度又继续增加,粉末颗粒在此压力下产生塑性变形或脆性断裂。
颗粒塑性变形的方向指向压坯的孔隙,因此材料填入孔隙,导致压坯密度增大。
18金属粉末压坯成型密度随成型压力的变化规律①第一阶段:滑移阶段,压坯密度随压力的增大而迅速增大。
这是因为粉末的拱桥现象,在不大的压力作用下迅速消除,粉末颗粒移动距离较大,使空隙急剧减小。
②第二阶段,保持阶段,压坯谜底增加缓慢或几乎保持不变,这是由于大量空隙已在第一阶段消除,压坯密度已达到一定值,粉末体出现了一定的压缩阻力,继续增大压力的结果是使颗粒发生弹性形变。
③第三阶段,变形阶段,当压力继续增加超过某一定值后,随着压力的增加,压坯密度又继续增加,这是因为压力的增加可能达到粉末材料的屈服极限和强度极限,粉末颗粒产生塑性形变,或脆性断裂,颗粒的脆性断裂,断裂碎块填入空隙,压坯密度也会增大。
19、在磨具成型中为何要加入添加剂?(1)降低内外摩擦力 (2)降低脱模力 (3)降低磨具磨损(4)防止粉末损失(5)改善压坯的密度、密度分布和压坯强度20、影响压坯弹性后效的因素?(1)粉末成型料成分 弹性后效随硬度提高而增加(2)粉末粒度 不同的金属粉末,粉末粒度对弹性后效的影响程度不一样,电解铜粉在成型压力100~300MPa时,粒度越细,弹性后效越小。
但对于还原铁粉,粒度越细,弹性后效越大。
(3)颗粒的表面形状和成型压力 粉末成型的压制压力越大,通常弹性后效值随着增大。
(4)模具的材质和结构 对于相同的压坯来说,组合筒阴模所引起的弹性后效比单层厚壁阴模小,硬质合金阴模比钢模所引起的弹性后效小,阴模刚性差则变形大,弹性后效也大。
21、改善单向成型坯体密度均匀性的措施。
答:降低压坯的高径比 降低模壁的粗糙度 添加润滑剂 改变压制方式22、试推导出粉末成型时的侧压力与正压力的关系P侧=ξP(P侧为侧压力,P为正压力)。
答:对于Y轴方向上正压力P的作用使其膨胀ΔLy1=γP/EX轴上侧压力也使其膨胀ΔLy2=γP/EY轴方向上的侧压力使其收缩ΔLy3=P侧/P则在Y轴方向上的膨胀值等于收缩值,即ΔLy1+ΔLy2=P侧/PγP/E+γP/E=P侧/PγP/E=P侧/P*(1-γ)P侧/P=ξ=γ/(1-γ)P侧=ξP γ:材料的泊松比E:弹性模量ξ:测压系数 23. 成型添加剂的功能有哪些?(1) 减小内外摩擦,减低单位压制压力;(2) 降低脱模力;(3) 防止压坯和模套啮合,减少模套磨损;(4) 防止粉末的装模损失。
24. 金属粉末烧结机构有哪些?他们主要起作用的外界环境。
答:烧结机构:扩散、流动、再结晶和晶粒长大。
主要起作用的外界环境:坯体成型压力、烧结温度、烧结时间。
25. 扩散传质的方式,各有什么特点。
(1) 蒸发与凝聚 特点:可以使烧结颈长大,但并不引起颗粒间的距离收缩;(2) 表面扩散特点:它只涉及到质点的表面迁移,只能促进孔隙表面光滑和孔隙球化,对孔隙的消失和烧结体的收缩不产生影响;(3) 体积扩散 特点:空位有烧结颈曲面出发,经由颗粒内部像空位阱扩散,体积扩散可以使闭孔收缩;(4) 晶界扩散 特点:晶界扩散的结果是烧结颈长大,颗粒互相靠近。
27.单元系固相烧结的三个温度段中各发生的变化答:单元系固相烧结是指纯金属,有固定化学成分的化合物或均相预合金粉末的烧结,烧结过程中不产生新的物相和凝聚状态的改变,故也称单项烧结。
(1)低温预烧结阶段( 《0.25T熔 )这一阶段主要发生金属回复,吸附气体和水份挥发,添加剂的分解和排除,金属的回复消除了坯体内的残余应力,使颗粒接触相对减少,体积有所增加,挥发份的排除是坯体产生微小收缩,总体来说,本阶段坯体体积基本上不会发生变化,例外非金属颗粒接触转化为金属颗粒接触,使坯体的导电有所增加。