斯伦贝谢泵工况说明
Zoeller 840、841和842型潜水研磨泵组说明书

Model Number: ______________Date Code: _______________☐ Simplex ☐ Duplex☐ Packaged System☐ Field Assembled SystemJob Name: ____________________________________________Distributor: ____________________________________________Date of Purchase: _________ Zoeller S/O No.: ______________Contractor: ____________________________________________Date of Installation: ____________________________________System Readings During Start-up: Voltage _____ Amps _____OWNER’S MANUALOwner’s InformationTable of ContentsSafety Instructions .......................................................................................1Limited Warranty and Application ...............................................................2Preinstallation Checklist ..............................................................................3General Information......................................................................................4Pump Wiring Instructions ............................................................................5Typical Indoor Prepackaged System ...........................................................6Indoor Prepackaged Installation Instructions ............................................7Typical Outdoor Prepackaged System ........................................................8Outdoor Prepackaged Installation Instructions ..........................................9Operation .....................................................................................................10Cutter Maintenance ....................................................................................11Service Checklist . (12)FM21680621Supersedes0320NOTICE TO INSTALLER: Instructions must remain with installation.Product information presented here reflects conditions at time of publication. Consult factory regarding discrepancies or inconsistencies.MAIL TO : P.O. BOX 16347 • Louisville, KY 40256-0347SHIP TO : 3649 Cane Run Road • Louisville, KY 40211-1961TEL : (502) 778-2731 • 1 (800) 928-PUMP • FAX : (502) 774-3624Visit our website:Register your Zoeller Pump Company Product on our website:/CSA 22.2 No. 108 StandardsGeneral InformationGRINDER PUMP DESCRIPTION1. Pumps are constructed of cast iron protected with powder coated epoxy for long life when pumping sewage in submersible applications. The cutter assembly is comprised of stainless steel components hardened to a value of 55-60 on the Rockwell C scale; a star shaped cutter and a precision ground flat disk. Cutting action takes place with the rotation of the star cutter at 3450 RPM against the stationary cutter plate (see page 11).2. The cutter mechanism on the model 840 is bidirectional, enabling it to cut in either direction. A control panel with the reversing feature will alternate the pump’s rotational direction with each duty cycle. The cutter mechanism on the model 841 and 842 is single directional.3. Pump motors are available in single and three phase design. Single phase motors require a Zoeller approved starting relay, starting capacitor and a run capacitor, which are mounted in a control panel (ref. page 8).4. The 840, 841 and 842 Grinder Pumps are dual seal and have seal leak probes. Single phase units have an internal thermal overload. Three phase pumps have a thermal sensor.5. Three phase pumps require overload protection in the control panel.6. A Grinder Pump is an intermittent duty pump designed for pumping sanitary sewage. It is not a dewatering or trash pump.FIELD ASSEMBLED INSTALLATION1. Installation and piping instructions are included with the control panel, rail system and basin instructions. If pump is being retrofitted to an existing rail system, accessory parts may be required. Consult the factory and advise make and model of rail system being used.2. Refer to the appropriate Indoor/Outdoor prepackaged instructions on pages 6-9 for more information on system installation.3. All electrical connections including pump to control box and power supply to control panels must comply with the “National Electrical C ode” and applicable local codes. C onduit and panel enclosure openings must have a gas and watertight seal. Installation of electrical panels, conduit and connections should be made by a qualified licensed electrician. A UL Listed potting kit, P/N 10-2350, is available from Zoeller C ompany.4. A properly sized disconnect switch, supplied by others, shall be installed on the service side of the pump and control panel.5. When installing a pump with a check valve, or a rail system with a check valve, you must give the pump case time to fill to help prevent air lock when lowering the unit into the liquid. The pump case has an air vent located behind the discharge. This air vent is across the pump housing mounting surface and must be cleaned before each reinstall. An extra air vent hole (3/16") may be drilled in discharge pipe below the check valve to help prevent air lock. This drilled hole must be cleaned before each reinstall. After the pump is installed, run the unit submerged to assure the pump case is filled (Water should come out of 3/16" diameter hole).FIGURE 1.016532HEAD CAPACITY CURVE MODEL 840/841/8424080120160200240706050403020101048121620130706050403020FLOW PER MINUTEGALLONS LITERST O T A L D Y N A M I C H E A D80902824M E T E R SF E E T1001101203236840841842TOTAL DYNAMIC HEAD/FLOWPER MINUTE SEWAGEMODELFeet Shut-off Head:840Meters Gal.Liters 51020309.16.13.01.54445167170104 ft (31.7 m)60504090807011010012012.215.218.321.324.427.430.533.536.64236301141361592316103861873--------11125 ft (38.1 m)841Gal.Liters 4517045170125 ft (38.1 m)95251342076491534322934343434129121110129129129129842Gal.3434129129Liters 5249185197433628106136163191141542725420454204542045420454204SOLID FIBERGLASS COVERFOAM TAPEUL LISTED EPOXY SEALER#10-2350 POTTING KIT APPLIES TO INSIDE AND OUTSIDE INSTALLATIONSCONDUIT1WIRES ORPUMP CABLES 1/4" TO 1/2"(25 mm)(6 mm TO 12 mm)SK1661LOCATION VARIES WITH BASIN DEPTHOperationGENERALZoeller pumps are lubricated and tested at the factory prior to shipment and require minimum pre-start-up maintenance.Maximum operating temperature of pump liquid for grinder pumps must not exceed 130 °F (54 °C).These units are designed for intermittent duty sanitary sewage applications. If pump is used to dewater areas or pump liquids with heavy or abrasive materials, the warranty will be voided. NAMEPLATE DATAThe nameplate, located on the side of the pump, indicates specific information about the construction of the pump. The model number and date code information should be recorded on the front page in the “Owner’s Information” section of this manual.SHORT TERM STORAGEDo not install pump until electrical power is available and system is operational. When not in use, the pump should be stored and the following is advised:• Store p ump i nside w henever p ossible o r c over w ith s ome t ype o f p rotective covering.• Tape or seal in plastic bag the terminal ends of wire leads.• Spray coat unpainted surfaces with rust inhibiting oil.• The impeller should be rotated every six months in order to keep the seals lubricated and not develop a permanent set.If panel is to be stored, the following is advised:• Store the panel inside whenever possible and leave in the shipping box.• All openings shall be sealed.• Store in an upright position.• Do not stack anything on top of panel.START-UP PROCEDUREBefore placing the equipment into operation the following should be checked:• Clean pit.• Pump, float switches, electrical cables and junction box are dry and properly installed.• Electrical boxes dry, sealed and securely installed.• Floats positioned properly.• Discharge valves open.• 3/16" vent hole drilled in pipe between check valve and pump. Once the above has been verified proceed with the following checks:• Pump power cables and control floats properly installed and voltage verified.• Conduit connections to panel and junction box are properly sealed.• After installing the pump into the containment area, with adequate submergence, open the discharge valve fully. Start the unit using manual controls. If flow is appreciably less than rated performance, pump may be air locked. To expel trapped air, jog the unit several times, using the manual controls.• Have a qualified electrician take voltage and current measurements with the pump running. Record these readings in the space provided in the “Owner’s Information” section on page 1 of this manual for future reference.ADJUSTMENT PROCEDUREPumps: No adjustments are required.Floats: Refer to the system drawing or to the panel wiring schematic for the desired location of each float switch setting. Valves: Discharge valves should be placed in the fully open position.Systems should not be operated for extended periods of timewith the discharge valves partially closed due to damagingthe valve.SHUTDOWN PROCEDURESIf a system is shutdown for more than six months, the following is recommended:Pumps: If pit is to remain dry, then the pump can remain in the pit.With the pump in the pit, it should be operated for five minutesonce every three months. If the pit is to remain wet, the pumpshould be removed and stored as noted above. Panels: The panel should have all openings sealed to prevent moisture and dust from entering the enclosure. Prior to restarting system,the panel should be inspected for presence of moisture and anyloose connections.Valves: Consult the valve/actuator supplier for information concerning these systems components.Cutter MaintenanceTo remove star cutter: Remove guard ring then heat thecenter bolt to 350 °F to loosen Loctite® thread sealant.Grind the Star Cutter and Disc seen here to a 32 microfinish.Surfaces must be flat to within 0.001" T.I.R. Gap must be between 0.004" and 0.008" on these parts.1.All p ower c ircuits m ust b e d isconnected a nd l ocked o ut b efore a ny a ttempts are made at servicing. The star cutter and disc can be removed and sharpened by grinding the cutting faces. Both star cutter and disc must be removed from the pump. Removal of these parts can be accomplished in the field by removing pump from the sump and positioning horizontally to access the intake of the pump. If seals or other repairs are required, the pump must be totally removed and serviced in a shop by a qualified pump technician or authorized service center.2.Remove the three countersunk screws on the plastic guard ring and remove the ring.3. Thoroughly clean the star cutter and disc assembly. Tilt pumpback to the vertical position to make certain the end play has been removed. Check and record the clearance between the star cutter and disc with a feeler gage. The correct running clearance is between 0.004" and 0.008".4.With pump in horizontal position, heat the hex head bolt in the center of the star cutter with a propane torch. The bolt must be heated to 350 °F to soften the thread lock sealer on the bolt for ease of removal. Remove the bolt by turning in a counterclockwise rotation. It will be necessary to use a wood block to prevent the star cutter from turning while removing the bolt. Pull star cutter from the shaft and remove the spacer shims located behind the star cutter.5. Remove the three cap screws holding the disc and remove discfrom the pump.6. The disc and star cutter can be replaced with new service parts or resurfaced by grinding. Resurfacing is accomplished by surface grinding both disc and star cutter to a 32 micro finish. Do not attempt grinding in the field. Send parts to a qualified machine shop for repair. The disc, star cutter and shims are a matched set. Keep parts together. Measure disc before and after resurfacing with micrometer and record measurements.7. After resurfacing, the disc and star cutter must be flat within 0.001". If the disc has been surface ground, it will be necessary to remove shims to compensate for the material removed from the disc. As a starting point, remove shims of the same thickness as the amount machined from the cutter disc (step 6 above). Final running clearance must be between 0.004" and 0.008". Be sure pump is in vertical position and all end play has been removed before measuring.8. Clean bottom of pump where disc is located and replace disc and retainer screws. Torque to 63-67 in-lbs. Replace star cutter with the correct shims. Install washer and torque hex head bolt to 71-75 in-lbs. apply Loctite 262 thread-lock sealant or equal to bolt threads prior to insertion. Check running clearance with pump in vertical position to remove end play. Clearance must be between 0.004" and 0.008" to obtain efficient grinding when pump is put back in service.9. Replace plastic guard ring and its three screws.10. Check the oil in the motor housing before reinstalling. Contact thefactory if the oil has a milky appearance or burnt smell. The level should be even with the fill plug when pump is in the upright position. Add oil if required. Use insulating oil supplied by the factory.FIGURE 7.(Model 840 components shown)If the above checklist does not uncover the problem, consult the factory. Do not attempt to service or otherwise disassemble pump. Service must be performed by Zoeller Authorized Service Stations. Go to /servicestations to find the Authorized ServiceStation in your area.。
斯伦贝谢 Total Flow 提供精确的多相流量剖面,引导油井修整规划说明书

Total Flow example well sketch. Total Flow locates and quantifieswellbore and reservoir flow, and reveals the relationship between the two.Delivered by our True Flow system with Chorus and Cascade technology, Total Flow provides the clarity and insight needed to manage well system performance more effectively.Total Flow is commonly used to diagnose unexpected or undesirable well system behavior, but it can also be usedproactively to ensure the well system is working properly.Customer: AGL Energy Ltd Field: ChurchieWell type: Gas producerCase benefits — L ocated and quantified production from all current reservoir zones— Evaluated the fracture job on the well — Identified gas-producing intervals in a tight reservoir— Located water inflow intervals behind casing— Provided useful insights for future workover and stimulation tasksthe relative contributions of gas from each layer. Water production was also an issue and can be a critical problem in a gas well. The second challenge was, therefore, toidentify where water was entering the well in order to plan a workover operation.The tubing installed in this gas producer well extends below the bottom perforation interval, which means that conventionalproduction logging tool surveys cannot help with evaluation.provides the clarity and insight operators need to manage well-system performance more effectively. Total Flow is commonly used to diagnose unexpected or undesirable well-system behaviour, but it can also beused proactively to ensure that a well system is working properly.In this case, the combination of Cascade flow modelling and Chorus acoustic sensing enabled TGT analysts to generate anaccurate multiphase flow profile for the wellThe maximum survey depth during the flowing regime was X204 m, which means that the bottom perforated interval (X207–X209 m) was not surveyed. The TFM curve shown in the TEMPERATURE track is the modelled flowing temperature profile. It is matched with TEMP_F1D1 down to the maximum surveyed depth and shows the assumed temperature behaviour below this depth. and provide the operator with a clear pictureof what was happening behind the casingand below the survey interval.ResultThe temperature simulation and flowmodelling results from TGT’s Cascadeplatform identified the main inflow zonesand showed that 48% of total gas and 44% oftotal water were entering the well from thebottom perforated interval. This indicatedthat about 93% of the total gas flow rate and100% of the water was from the bottom-zoneWallabella Sandstone Formation. The upperfractured zone (the Tinowon reservoir) wasnot making a significant contribution to gasproduction, thus the well could not reach itsplanned production performance.The operators can apply these insights todevelop an effective plan for future workoverand stimulation tasks.The small volume of gas produced fromthe Lower Tinowon Sandstone Formationis the result of behind-casing channelling,which would not have been identified byconventional production logging tools.2,623 boepdCHORUS FLOWING30.1kHz95110 dB SPL。
KRT 40至700废水用潜水电动泵说明书
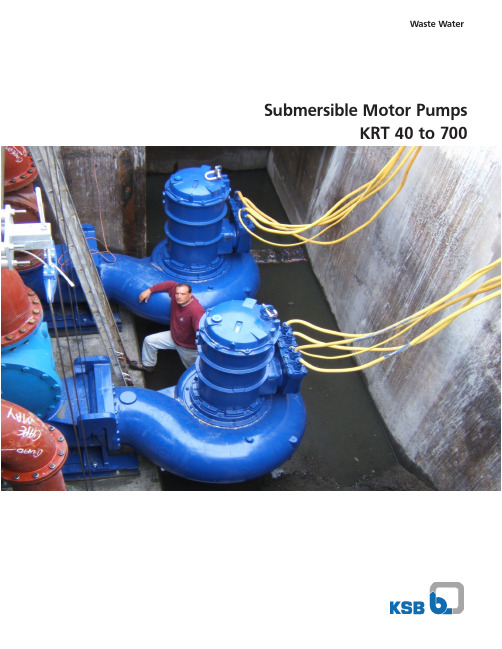
Waste Water Submersible Motor PumpsKRT 40 to 700Three (3) 161 hp Dry-Pit Pumps with cooling jacketKRT Submersible motor pumps for Versatile ApplicationsAdvantages and technical features:• economical installation• wet installation submersible motor pumps operate submerged in the pump sump• low building costs, eliminating intermediate shaft, drainage pump and superstructure• pump stations below ground do not spoil the landscape, traffic areas remain unchanged when sumps are located under roads • the compact pump/motor sets require less space and are easier to install• with the double pump guides the pump can be installed at any installation depth and withdrawn without difficulties • no need to enter the pump sump to carry out inspection and maintenance work• smaller inspection opening on duplex pump sets• small pump sump due to high permissible switching frequency • stationary and portable applications possible, see types of installations• permanent dry well installation possible where the pump is exposed to the danger of occasional flooding • minimum assembly and maintenance work• no coupling to be aligned since KRT pump and motor have a common shaft• no sealing or flushing water required or leakage outlet • motor cooled by the medium• high operation safety (dry running possible)• quiet operationKRT submersible motor pumps are highly efficient in the handling of:- raw sewage containing solid and long fibrous mixtures - contaminated liquids with a high gas and air content - liquids containing sludge and solid substances - concentrated sludge (KRT with agitator) for circulating and mixing the medium prior to pumping - floating sludge and debris such as vegetable wastes, wood chips and similar waste (KRT as a vacuum suction pump on a pontoon)- dirty water and storm water - raw and activated sludge - flume and wash water - pulp- slaughter house wastes - water/product suspensions - sand/cement/water mixtures - plastic granules in liquid - textile effluent- industrial effluent and wash water as well as media in production plants, e.g. flume water, scale wastes, cutting oil and other media containing abrasive components.- chemical and waste disposal effluent with pH-values 2 to 12- effluent containing acid- seawater and brackish water as well as other media with chlorine.Type of construction:KRT submersible motor pumps are submerged, single stage close-coupled pump sets. Depending on the liquid to be pumped and the size of the pump different impel -ler shapes are used: K - Closed non-clogging 2 or 3 vane impeller E - Single vane impeller F - Vortex impellerS - Cutting or Grinding impellerD - Open single vane impellerFields of application:Two (2) 148 hp Submersible Pumps with cooling jacket.1 - Reliable Motor - specifically designed for submersible pumps with air filled housings, explosion proof ratings, continuous duty cycles and automatic monitoring of winding temperature and moisture.2 - Water Tight Cable Entry - power cables with grommet and washer. Cable entry further epoxy sealed to insure no liquid gets inside the motor even if the cables are severed below water level.3 - Non-proprietary silicon carbide faced mechanical seals mounted in tandem in an oil bath.4 - Pump and motor shafts of stainless steel or Gr 1045 carbon steel protected and isolated by stainless steel shaft sleeves.5 - Flexible Hydraulic System - enclosed 1, 2 and 3 vane, recessed, grinder or open single vane impellers available to allow a hydraulic selection ideally suited for a particular application.6 - Major castings of ASTM A 48 Class 35 B cast iron, duplex stainless steel and wear resistant chromium white iron to Brinell 1000 available.7 - Automatic discharge connections with a positive seal between pump and elbow insures zero leakage.8 - Hard metal wear rings maintain hydraulic efficiency.The Safe and Reliable SolutionMotors smaller than ~80 hp :Motors 5 hp and below :9 - Major castings of ASTM A 48 Class 40 B cast iron, duplex stainless steel and wear resistant chromium white iron to Brinell 1000 available.10 - Plug in cable entry for a simple, polarized connection, fast pump installation and removal.11 - All-in-one bearing, seal, and gasket kits that areinterchangeable for all pump sizes, reducing spare parts costs.• 12 •• 3• 4• 5• 7• 910 •• 1• 4• 5• 6• 7• 3• 82 •The right impeller design for cost effective and reliable operationSince no one type of impeller is equally suitable for all applica -tions, KSB offers the KRT series of submersible motor pump with various types of impellers according to specific requirements. Our range of vortex, single vane and non-clogging impellers allows thebest impeller to be selected for the product with due consideration of operating parameters such as flow rate, head, efficiency, solidsize, wear behavior and gas content.Flexible installationsStationary guide wire installationStationary guide rail installationTransportable installationDryinstallationStationary guide wire or guide rail installation - for installation in the pump sump with suspension device ensuring automatic pres -sure-tight coupling of the pump.Transportable installation - with base stand and flange connection for pipework or hose connection (e.g. with rigid coupling)Dry installation - for installation in a separate dry well.The Pump That Keeps Cool1 - Cable Entry - absolutely water tight even in the event of damage to the cable sheath and core insulation there is no possibility of mositure entering the motor chamber along the strands due to capillary action.2 - Thermal Motor Protection - extensive sensor technology for permanent monitoring to ensure trouble-free operation.3 - High Efficiency Motor - all motors FM approved for Class I, Division 1 Group C & D hazardous locations.4 - OPTIONAL Closed-loop Cooling System - optimal cooling in all operating conditions with no external cooling required, perfect for dry-well installations .5 - Non- proprietary silicon carbide faced mechanical seals mounted in tandem in an oil bath.6 - Major Casting of ASTM A 48 Class 35 B Cast iron, Duplex Stainless steel and wear resistant Chromium White Iron.7 - Heat exchanger and separate coolant circulating impeller for optional cooling jacket.8 - Enclosed 1, 2 and 3 vane or recessed impellers available to allow a hydraulic selection ideally suited for a particular application.9 - Wear rings in hard metal to insure continued high efficiences and long impeller life.10 - Pump and motor shafts of stainless steel or Gr 1045 carbon steel protected and isolated by stainless steel shaft sleeves.11 - Temperature monitoring available for lower bearing12 - Float sensor in separate leakage collection chamber. Prevents leakage from reaching motor or lower bearing.* Motors larger than ~80 hp:• 1• 2• 3• 4• 6• 8• 910 •11 •12 •• 5• 7* For certain models, 30, 40, 50, 56, and 74 HP motors with cooling jacket are also available.06Installations and Technical DataThree (3) 12“ discharge, 161 hp closed-loop cooling dry-pit pumps with stainless steel Jacket in existing pumping station.Dry Well InstallationsTwo (2) large 24“ discharge, 148 hp Submersible Pumps with stainless steel cooling jacket on KSB guide rail system for an effluent waste water treatment pumping station.Wet Well Installations Three (3) 10“ discharge, 194 hp closed-loop cooling dry-pit pumps with stainless steel Jacket in existing pumping station.Two (2) large 24“ discharge, 251 hp Submersible Pumps and one (1) 12“ discharge, 80 hp on KSB guide cable system for a stormwater station.Technical DataOperating Data Pump Size - DN 2” - 30”Capacity - Q (gpm)up to 45,000Head - H (ft)up to 330Liquid Temperature - t (°F)up to 140Motor Rating - P (hp)up to 1,080Material Options Cast Iron A 48 Class 35 B Wear Resistant Chromium White IronA 532 II C 15% CrMo-HcDuplex Stainless Steel A 743 CD 4 MCU Part Designation GG1G2GHHC1C2Pump Casing A 48 Class 35 BA532 II C 15% CrMo-Hc A 743 CD 4 MCU Intermediate Casing A 48 Class 35 BA 532 II C 15% CrMo-HcA 743 CD 4 MCU Shaft A 276 Type 420;A 576 Gr. 1045 w/shaft protection sleeve A 276 S 31803/A 576 Gr. 1045ImpellerA 48 class 35B A 743 CD 4 MCU A 532 IIC 15% CrMo-HcA 276 S 31803/A 576 Gr. 1045Motor Casing A 48 Class 35 BA 743 CD 4 MCU Discharge Elbow A 48 Class 35 BA 532 II C 15% CrMo-HcA 743 CD 4 MCUPower/Control CableNeopreneKSB, Inc.4415 Sarellen Road Henrico, VA 2553.031/2-14 / 02.10 © K S B I n c 2008Your local KSB representative:S u b j e c t t o t e c h n i c a l m o d i f i c a t i o n w i t h o u t p r i o r n o t i c e。
斯伦贝谢-高级完井技术

完井工具-封隔器
机械坐封式封隔器
SOT-1 10K Omega SFB1
液压坐封式封隔器
Hydro - 5 Hydro-6
插管式封隔器
L ,QL,B
HSP
Omegamatic
Hydro-12
Omegatrieve
SR-1 ,SR-2
Compression
XHP, MRP, HQL
Quantum
封隔器的 ISO14310 资格认证
–安全阀与封隔器
•气井完井在中国的应用 •先进的完井技术
–流动控制阀 –Sensa光纤分布式温度系统
•多分支井技术 •我们的计划
斯伦贝谢完井技术在中国的气井中的应用
• 中石油塔里木油田牙哈30口高压气井完井项目; • 中石油塔里木西气东输克拉2高压气井完井项目
–克拉205井、克拉2 气田一期4口高压气井项目 ;
• 中石化西北分公司雅-大凝析油气田; • 中石化中原高新注气井项目; • 中石油-北京市政府大港储气库项目 ; • 中石油吐哈油田温米注气项目 ; • 中海油渤中26-2项目 ; • BP-ARCO三亚崖城131高压气田项目 ;
牙哈气田
• 10,000Psi(70MPa); • CO2 、H2S; • 永久式封隔器; • 13Cr; • 气密封扣; • 温度130 DegC。
–流动控制阀 –Sensa光纤分布式温度系统
•多分支井技术 •我们的计划
井眼产出物的检测和控制
检测和控制水和气的 进入 气
水
油藏监测和控制
油藏和井的响应
控制流出物或注入 优化
电力和数据传输
监控压力、 温度和产量
数据传输
更新模型和井动态
Fybroc Series 1500 高性能纤维glas 抗腐性泵说明书
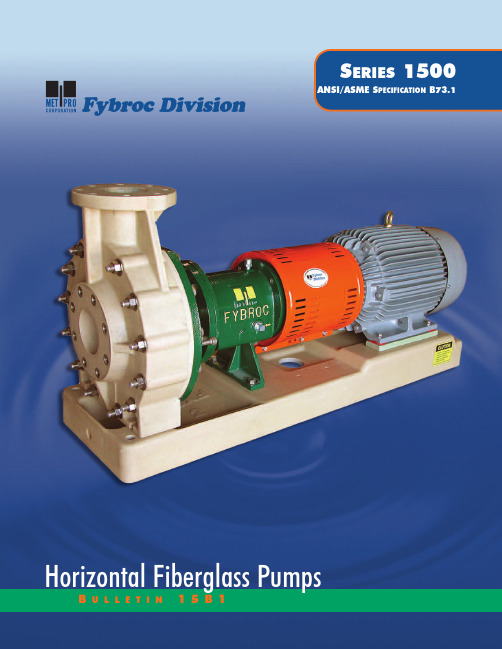
Fybroc DivisionS ERIES 1500ANSI/ASME S PECIFICATION B73.1BU L L E T I N15B 1Horizontal Fiberglass PumpsFYBROC – THE LEADER IN CORROSION-RESISTANT FIBERGLASS PUMPING EQUIPMENTFybroc is an advanced technology pump manufacturer specializing in reinforced composite centrifugal pumps, designed to handle corrosive liquids. Fybroc, the pioneer in the fiberglass pump field, con-tinues its position of leadership with its Series 1500 pump. This line is the culmination of many years of experience in producing high quality, corrosion-resistant pumps.The Series 1500 combines an extensive knowledge of materials and production techniques to provide exception-al structural integrity, excellent corrosion resistance, and dependable service in difficult operating environments.2MATERIALS OF CONSTRUCTION ARE AVAILABLEFOR A WIDE RANGE OF CORROSIVE LIQUIDSOnly Fybroc has the flexibility in materials selection tosolve your difficult corrosive or abrasive pump problems.•VR-1, vinyl ester resin: used for the vast majority ofcorrosive applications including most acids,caustics, brines, sea water, and wastewater.•VR-1 BPO-DMA, vinyl ester resin with BPO-DMAcure system: used to accommodate applications forspecific corrosion resistance to bleaches such assodium hypochlorite (NaOCl) and hydrogenperoxide (H2O2).•VR-1A, vinyl ester resin with abrasive resistantmaterial: used for pumping liquids with lowconcentration highly abrasive fines such asfly ash, diatomaceous earth or titaniumdioxide.•VR-1V,vinyl ester resin with synthet-i cveil: protection used specifically forfluoridic applications such ashydrofluoric acid (HF) and fluosilicicacid (H2SiF6).•EY-2, epoxy resin: offers outstand-ing chemical resistance for aggres-sive chemical/compounds, acids,and solvents. Ideal for high concen-trations of sulfuric acid (up to98%).FDA COMPLIANCEThe Dow DERAKANE series epoxy vinyl ester resinutilized by Fybroc, when properly formulated and cured,will comply with the U.S. Food, Drug, and Cosmetic Act,as amended, and applicable FDA regulations (21 CFR177.2420). These resins may be used as articles or com-ponents of articles intended forrepeated use in contact with food,subject to certain limitationsdescribed in that regulation.For further information on corro-sion resistance to specificchemicals, please refer tothe Fybroc website at.FYBROC SERIES 1500THERMOSET CONSTRUCTION RESIN TRANSFER MOLDING (RTM) PROCESS FOR SUPERIOR STRENGTH AND CORROSION RESISTANCEThermoset fiberglass reinforced plastic (FRP) pumps are increasingly being used in the pump industry due to their low weight, durability, and tailor-made properties. A ther-moset is a material that cures or hardens (sets) into a given shape, generally through the reaction with a cata-lyst. Curing is an irreversible chemical reaction in which permanent connections (cross-links) are made between a material’s molecular chains. The cross-links give the cured polymer a three-dimensional structure, as well as a higher degree of rigidity than it possessed prior to curing. It is important to note that a thermoset material will not re-melt or otherwise regain the processibility it had before being cured. Thermoset materials outperform other materials (thermoplastics, for example) in a number of areas, including the following: mechanical properties, chemical resistance, thermal stability, and overall durability.The fiberglass components in the Series 1500 Series pumps, as well as Fybroc’s complete line of centrifugal pumps, utilize the Resin Transfer Molding process. This process allows for the controlled placement of continu-ous-strand fiberglass mat in high stress areas.Specifically, sheets of contin-uous-strand fiberglassmat are die cut intospecific shapes andthen loaded intomatched-metal diemolds. After load-ing, the molds areclosed and theninjected with cat-alyzed resin into a sin-gle inlet port withnumerous vent ports toensure complete air displace-ment. After the resin gels, the part is removed and allowed to cure at ambient temperature, and then the part is post-cured in a controlled heat operation. The major advantage of the RTM process, unlike a compression molded process that inherently utilizes randomly oriented pieces of chopped fiberglass leadingto comparatively lower strength, is that the carefully ori-ented continuous-strand fiberglass mat provides com-ponents with excellent physical strength and properties.In addition, the process allows for the design of thinner-walled structures, thereby permitting the use of nearlypure resin systems for optimum corrosion resistance.The bottom line is that RTM is a manufacturing tech-nique that optimizes both strength and corrosion resist-ance.Critical components such as the single-piece casing, withits heavily gusseted suction and discharge flanges, bene-fit from the reinforcing properties of the RTM process. Thispermits the handling of normal pipe loads under full working pressures. Furthermore, this method of rein-forcement in the impeller extends the life of this compo-nent and provides unparalled strength without degrada-tion in corrosive environments.With more than thirty years of composite pump designand manufacturing experience, Fybroc has the expertiseto provide you with a composite pump line of the highestquality and durability for your specific service or applica-tion. Remember, FRP pumps are our ONLY business! By controlling the entire manufacturing process in-house,Fybroc is able to offer flexibility with special customer requirements while boasting the best lead times in the industry.3CORROSION-RESISTANT FIBERGLASS BASEPLATESFybroc manufactures fiberglass baseplates since chem-ical pumps are often used and installed in environ-ments where external corrosion can be a serious prob-lem. The baseplates are constructed of fiberglass-rein-forced vinyl ester resin utilizing continuous-strand rein-forcement for maximum strength and stiffness. In addi-tion, they accommodate ANS I/ASME dimensioned pumps (and NEMA/I EC motors) with an integral, sloped drip pan under the pump, a tapped drain con-nection, and a provision for a grouted foundation. Refer to page 13 for additional baseplate information and specifications.DESIGN FEATURES OF THE SERIES 1500 PUMPThe Fybroc Series 1500 pump is designed for broadcorrosion-resistance through the use of high quality1213 materials and state-of-the-art engineering. I ts simplicityand versatility make it the ideal choice for all demandingpumping requirements.The fiberglass components are manufactured utilizing theResin Transfer Molding technique which enables completecontrol of the fiberglass reinforcement in high stressareas. Metallic pump components are NOT in contactwith process fluids.1411109 41.ANSI/ASME B73.1 CONFOR-MANCE ensures maximum interchange-ability with existing metal ANSI pumps,thereby eliminating any need for piping or foundation changes when up-grading an installation to Fybroc Series 1500pumps.2.SMOOTH HYDRAULIC PASSAGES promote increased pump efficiency.3.SINGLE ONE-PIECE GUSSETED CASINGeasily withstands the rigors of normal plant piping loads.4.IMPELLER PUMP-OUT VANES and relief holes minimize axial unbalance and lower stuffing box pressure.5.ALLOY INSERT (integrally molded with impeller) with rounded edges carries impeller torque loads with low stress.6.VERSATILE CASING COVER is suit-able for use with most single outside or double inside mechanical seals without modifications. See page 7 for some of the most frequently used configurations and page 8 for seal flush considera-tions.7.CONTINUOUS-STRAND FIBER-GLASS CONSTRUCTION for all wet-ted parts in either vinyl ester or epoxy resin provides maximum corrosion resist-ance for a wide range of difficult liquids.8.CASING THROUGH-BOLTS maintain casing o-ring seal integrity under all hydraulic operating conditions.9.INTEGRAL SHAFT SLEEVE design eliminates gaskets and o-rings andprotects the pump shaft from exposure to the process fluid.10.LARGE-CAPACITY BEARINGS ensure operating life well in excess of the minimum specified by ANSI/ASME B73.1.11.EXTERNAL IMPELLER ADJUST-MENT allows field setting of impeller-to-casing clearance.12.HEAVY -DUTY SHAFT minimizesdeflec-tion to maximize mechanical seal life.13.POLYESTER THERMOSETTINGPOWDER COATED POWER FRAME components prevent external corrosion.14.LABYRINTH OIL SEALS nickel plated-bronze for longer life. Improved oil containment.876543215The Series 1500 pumps have been designed to maximize the life of bearings and mechanical seals which can deteriorate because of shaft deflection resulting from radial thrust. Radial thrust is the force acting on the side of an impeller as a result of the non-uniform distribution of pressure around the pump casing at off-peak opera-tion.The magnitude of this thrust varies with the flow, but the amount of radial thrust can roughly be cut in half by uti-lizing a double volute casing. The solid line in the chart to the right depicts the typical radial thrust characteristic of a single volute casing. The dotted line portrays the use of a double volute casing and the resulting reduction in radial thrust.The drawing at lower right shows the location of the “cutwater” in volute casings. The cutwater is the close clearance extension of the casing located at the base of the volute. Also, shown in orange, is the second cutwater or “splitter” used in the double volute casing, which channels half of the flow to the pump discharge. The split-ter reduces the pressure imbalance in the casing during off-peak flows and reduces both radial thrust and its resulting shaft deflection. Fybroc uses double volute cas-ings in eleven of its larger pump sizes where, typically,radial thrust loadings are higher. See chart on page 9,Casing Data, Volute.MATERIALS OF CONSTRUCTION10090807060504030201000102030405060708090100110120130140% OF DESIGN FLOW% O F M A X I M U M R A D I A L T H R U S TDouble VoluteSingle VoluteSplitterCutwaterConsult Factory for materials availability for your specific pump size.6DESIGN PROVIDES FOR MAXIMUM SEAL AND BEARING LIFECOMPONENTMATERIALSCasing VR-1, VR-1 BPO-DMA, VR-1A, VR-1V , EY-2Impeller VR-1, VR-1 BPO-DMA, VR-1A, VR-1V , EY-2Cover VR-1, VR-1 BPO-DMA, VR-1A, VR-1V , EY-2Gland VR-1, VR-1 BPO-DMA, EY-2Shaft 303SS (Optional 316SS)Bearing Hsg.Polyester Thermosetting Powder Coated Iron Adapter Polyester Thermosetting Powder Coated Iron Hardware 303SS (Optional hardware is available)O-RingsViton A (Optional elastomers are available)Fybroc Series 1500 pumps are available with a wide variety of mechanical seal arrangements. For corro-sive fluid handling, single outside and double inside seals are recommended. The single outside seals have non-metallic wetted parts and all metal components located outside the pump. The double inside mechan-ical seals have metallic parts that are exposed to buffer fluid only and are designed to limit the process fluid contact to non-metallic components.The following illustrations outline some commonly used sealing arrangements. See page 8 for seal flush con-siderations. Additional mechanical seal configurations (for example, cartridge designs) are available as options.C RANE 8B2F LOWSERVE RACC RANE T YPE 8-1T F LOWSERVE RXO7MECHANICAL SEALINTEGRAL IMPELLER AND•“ONE-PIECE” impeller and shaft sleeve •“NO” shaft sleeve o-rings required•Semi-open type with pump-out vanes and bal-ance holes designed to minimize axial unbalance and lower stuffing box pressureAll mechanical seals require flushing to lubricate the seal faces and maintain normal operating temperatures. Seals are normally flushed with either a clean external fluid or by the liquid being pumped. Fybroc Series 1500 pumps are furnished, as standard, with tapped glands for connection to the flush liquid or with theoptional configurations shown below.INTERNAL COVER FLUSHFybroc’s Internal Cover Flush option eliminates the need for external flushing of single mechanical seals from the pump discharge, which also eliminates the possible breakage of external tubing and fittings.This option removes seal heat by circulating high pressure liquid internally through the drilled cover to the seal chamber and then recirculating this liquid back to the low pressure side of the pump.FYBROC’S OPTIONAL FLUSH ASSEM BLY PACKAGEThe flush assembly* consists of the following items:1)Shut off valve and pressure gauge mounted on epoxy-coat-ed steel bracket. Inlet side.2)Solenoid valve and flow meter/metering valve mounted onepoxy-coated steel bracket. Outlet side.3)Necessary tubing and fittings to pipe system to seal gland.*Note:The assembly is intended for use on pumps with double inside mechanical seals (Crane 8-1T, Flowserve RXO). Consult Factory for additional “special” configurations.The system is designed to operate as follows:1)Flush water is brought to the inlet side of the system andpiped away to a suitable drain on the outlet side.2)The normally closed solenoid valve is wired into the motorstarter controls and opens when the motor is energized.3)The inlet shut-off valve would remain open at all times andwould be used only when the system needed to be isolatedfor maintenance purposes.4)The flow meter/metering valve would be adjusted as neces-sary to obtain a reading of 1/4 - 1/2GPM.When properly installed and operated as referenced above, the flush system will ensure that the mechanical seal is operating in the proper environment and is being cooled and lubricated as required.LowPressureLiquid High PressureLiquid8SEAL FLUSHING ARRANGEMENTSDIMENSIONS SHOWN ARE IN INCHES AND(MILLIMETERS )L 3/D 4* – T HE LOWER THE NUMBER , THE STIFFER THE SHAFT(ANDTHEREFORE LESS SHAFT DEFLECTION AND IMPROVED MECHANICAL SEAL LIFE ).9I MPELLER F RONT .015.020.025(.38)(.51)(.64)C LEARANCEB ACK.045.040.035(1.04)(1.02)(.89)C ASING T HICKNESS (M IN ).500.750.625.75.625 1.125.750 1.250 1.375(12.70)(19.05)(15.90)(19.05)(15.90)(28.60)(19.05)(31.75)(35.00)V OLUTES INGLED OUBLE S INGLED OUBLE S INGLED OUBLED IA . AT I MPELLER .750 1.250 1.500(19.05)(31.75)(38.10)D IA . U NDER S LEEVE 1.125 1.750 2.500(28.60)(44.45)(63.50)D IA . AT B EARINGS IB/OB 1.375/1.375 1.968/1.771 2.755/2.755(35.00/35.00)(50.00/45.00)(70.00/70.00)D IA . B ETWEEN B EARINGS1.6252.2503.250(41.30)(57.15)(82.55)B EARING S PAN 3.7907.09010.250(96.30)(180.10)(260.35)D IA . AT C OUPLING.875 1.125 2.375(22.22)(28.60)(60.32)B EARING N O . I NBOARD 307MZC3310MZC36314ZC3B EARING N O . O UTBOARD 5207AZC35309EZC35314ZC3M AX . S HAFT HP (KW) PER 100 RPM1.14(.85 KW)4.00(2.98 KW)14.80(11.04 KW)L-10 L IFE M INIMUM 3 Y EARS (26,280 H OURS )L 3/D 4*1524632B EARING F RAME G ROUP I II IIIO IL C APACITY , P INTS (l ).375(.18 l ) 2.000(.95 l )5.000(2.37 l )S LEEVE (O.D.) 1.375 2.125 2.875(35.00)(54.00)(73.00)S TUFFING B OX B ORE2.000 2.8753.750(50.80)(73.02)(95.25)M AX . D EPTHOFB OX2.7503.250 3.500(69.85)(82.55)(88.90)P ACKING S IZE 5/16 x 5/163/8 x 3/87/16 x 7/16(7.94 x 7.94)(9.52 X 9.52)(11.11 X 11.11)D ISTANCE T O 3.140 3.980 4.870F IRST O BSTRUCTION(79.76)(101.10)(123.70)ENGINEERING INFORMATION –1 x 1.5 x 61.5 x 3 x 62 x3 x 61 x 1.5 x 81.5 x 3 x 82 x3 x 83 x4 x 81 x2 x 101.5 x 3 x 102 x3 x 103 x4 x 104 x 4 x 104 x 6 x 102 x3 x 133 x4 x 134 x 6 x 136 x 8 x 138 x 10 x 1510 x 12 x 16PUMP IMPELLER DIAMETERX SUCTION X DISCHARGEANSI DESIGNATION AA AB –AA A50A60A70A05A50A60A70–A80A30A40A80A90A120–MAX. SPHERE SIZE .375.500.313.625 1.000.188.375.625.750 1.000.313.500 1.0001.1251.7501.375(9.53)(12.70)(7.95)(15.90)(25.40)(4.78)(9.53)(15.90)(19.05)(25.40)(7.95)(12.70)(25.40)(28.60)(44.45)(35.00)C A S I N GD A T AB O X D A T AS H A F T A N D B E A R I N G D A T A1150 RPM60 HERTZ1750 RPM60 HERTZ3500 RPM60 HERTZNOTE:For specific performancecurves refer to curve book or .1X11/2X611/2X3X62X3X63X4X82X3X811/2X3X81X11/2X81X2X102X3X1311/2X3X102X3X103X4X104X4X104X6X103X4X134X6X136X8X138X10X1510X12X16123510152030406080100150200CUBIC METERS PER HOUR1020305010015020030050010002000400060003005007001000150015010080605040302010535302520151052T O T A L H E A D I N M E T E R S123510152030406080100150200CUBIC METERS PER HOUR10203050100150200300500100020004000600030050070010001500250200150100806050403020107060504030252015105T O T A L H E A D I N M E T E R S1X11/2X611/2X3X62X3X63X4X82X3X811/2X3X81X11/2X81X2X102X3X1311/2X3X102X3X103X4X104X4X104X6X103X4X134X6X136X8X138X10X15123510152030406080CUBIC METERS PER HOUR51020304050100150200300500100020001001502003006005004003002001501008060504030201501201008060504030252015108T O T A L H E A D I N M E T E R S1X11/2X611/2X3X62X3X63X4X811/2X3X81X11/2X81X2X1011/2X3X102X3X103X4X104X4X102X3X8T O T A L H E A D I N F E E TT O T A L H E A D I N F E E TT O T A L H E A D I N F E E TUS GALLONS PER MINUTEUS GALLONS PER MINUTEUS GALLONS PER MINUTE10FYBROC SERIES 1500 – THE INDUSTRY’S MOST EXTENSIVE FIBERGLASS CORROSION-RESISTANT COVERAGESHAFT HORSEPOWER (KW)PRESSURE–TE M PERATURE RAT-1450 RPM50 HERTZ2900 RPM50 HERTZ751020304050TEMPERATURE - °C607080901001101205025-10-180100125150175200225250K I L O P A S C A L – k PaTEMPERATURE - °FGROUP II *GROUP III (Except 10x12x16)10x12x16M A X I M U M W O R K I N G P R E S S U R E – P S I 025507510012515017520022525015030045060075090010501200135015001650GROUP I* Standard flat faced flanges (ANSI/ASME B16.5 Class 150)NOTE: Refer to Chemical Compatibility Guide for specific application ratings.11RPM 35002900175014501150Group I 40 HP 33 HP 20 HP 17 HP 13 HP (30 KW)(25 KW)(15 KW)(12 KW)(9.8 KW)Group II 140 HP 116 HP 70 HP 58 HP 46 HP (104 KW)(88KW)(52 KW)(43 KW)(34 KW)Group III *——260 HP 215 HP 170 HP (194 KW)(160 KW)(127 KW)* 1150 RPM maximum for 10x12x16PUMP DIMENSIONS FOR SERIES 1500CPFYV XDE 1E2øHUDIMENSIONS SHOWN ARE IN INCHES AND (MILLIMETERS)*CF—Consult Factory (FRP baseplate available up to 365T frame)121 x 1.5 x 61.5 x 3 x 62 x3 x 61 x 1.5 x 81.5 x 3 x 82 x3 x 83 x4 x 81 x2 x 101.5 x 3 x 102 x3 x 103 x4 x 104 x 4 x 104 x 6 x 102 x3 x 133 x4 x 134 x 6 x 136 x 8 x 138 x 10 x 1510 x 12 x 16PUMP IMPELLERX SUCTION X DISCHARGEANSI DESIGNATION AA AB –AA A50A60A70A05A50A60A70–A80A30A40A80A90A120–ISO/DIN F LANGE A VAILABILITY ––✔––✔✔✔–✔✔✔✔–✔✔✔✔✔JIS F LANGE A VAILABILITY––✔––✔✔✔–✔✔✔✔–✔✔✔✔✔CP 171/2231/2337/8351/8(445)(597)(860)(892)D 51/481/410141/218(133)(210)(254)(368)(457)X 61/281/291/21181/291/211121/2131/2111/2121/2131/2161926(165)(216)(242)(280)(216)(242)(280)(318)(343)(292)(318)(343)(406)(483)(660)F 71/4121/2183/4173/4(184)(318)(476)(541**)2E 1693/41622(152)(248)(406)(559)2E 2071/4914(0)(184)(229)(356)H 5/87/81(16)(22)(25)U 7/811/823/8(22.23)(28.58)(60.33)KEYWAY 3/16x 3/321/4x 1/85/8x 5/16(4.76 x 2.38)(6.35 x 3.18)(15.88 x 7.94)V 225/84(51)(67)(102)Y 467(102)(152)(178)M OTOR F RAME 143T-184T143T-145T254T-365TB ASEPLATE M ODEL #1T 25M OTOR F RAME 213T-215T182T-286T404TS-445T*CFB ASEPLATE M ODEL #2T 26M OTOR F RAME 254T-256T324T-405TS—B ASEPLATE M ODEL #13—Mount your pump on a corrosion-resistant fiberglass baseplate from Fybroc.•Corrosion resistanceFybroc fiberglass baseplates are designed specifically for use in corrosive environments, providing the same corro-sion-resistance as our time-proven Fybroc fiberglass pumps.•High strengthA high percentage of continuous-strand fiberglass mat reinforces the corrosion-resistant resin, thereby giving the baseplate an exceptional degree of strength.•Integral drip pan with rim constructionEach Fybroc fiberglass baseplate incorporates an integral,sloped drip pan, eliminating expensive alloy drip pans and/or rimmed baseplates.• EconomyFybroc fiberglass baseplates resist corrosion indefinitely,thus eliminating the operational and maintenance costs of replacing corroded baseplates.•ANSI/ASME dimensionsEvery Fybroc fiberglass baseplate is pre-drilled to accept all ANSI/AMSE pumps and NEMA/IEC frame motors.•Optional Baseplate DesignsConsult Factory for modified FRP baseplates as well as other materials such as polymer concrete (composite)and steel baseplate designs.HEHEHAC3/4 NPTDrainHGHBHF HLHM11/4 (32)øHHDIMENSIONS SHOWN ARE IN INCHES AND (MILLIMETERS)*Note: Dimension varies with pump model†Model 4 base13BASEPLATE DIMENSIONSBASE PLATE HA HB HE HF HG HH HL HM CMODEL 1T 10(254)35(890)4(102)321/2(825)25/8(67)3/4(19)41/2(114)33/8(86)111/16(43)2T 12(305)39(990)41/2(114)361/2(927)27/8(73)3/4(19)41/2(114)27/8(73)115/16(49)112(305)45(1140)41/2(114)421/2(1080)33/4(95)3/4(19)41/2(114)23/4(70)17/8(47)215(381)52(1320)6(152)491/2(1257)33/4(95)3/4(19)41/2(114)33/4(95)17/8(47)318(457)58(1475)71/2(191)551/2(1410)4(102)1(25)41/2(114)4(102)17/8(47)†418(457)60(1525)71/2(191)571/2(1460)4(102)1(25)*NOTE 4(102)N/A 522(559)68(1727)91/2(241)651/2(1664)41/2(114)1(25)61/2(165)41/2(114)11/2(38)622(559)80(2032)91/2(241)771/2(1969)41/2(114)1(25)61/2(165)41/2(114)11/2(38)14OPTIONS DESIGNED TO ELIMINATE ALIGNMENT PROBLEMSCLOSE-COUPLED PUMPS•Capacities to 1500 GPM (345 m 3/hr)•Heads to 400 Ft (125 m)•C-faced JM extension motors up to 50 HP (37 KW)•Sixteen sizes (all Fybroc Series 1500 Group I and Group II pumps)•Available with all materials of construction (page 2)•Available for mounting on FRP baseplates •Lightweight/space efficient design•Anti-spin-off device (segment key/locking ring) incorpo-rated on the back end of the impeller sleeve to help protect against potential reverse rotation damage.•Available on all Fybroc Series 1500 Group I and Group II pumpsGroup I – motor frame sizes up to 256TC Group II – motor frame sizes up to 365TSC •Designed to simplify pump/motor installation and alignment•Reduces routine maintenanceC-FACEINTERCHANGEABILITYEXTENSIVE INTERCHANGEABILITY SIMPLIFIES SPARE PARTS STOCKING REQUIREMENTS.G ROUP I P UMPSG ROUP II P UMPSG ROUP II P UMPS15©COPYRIGHT 2004 MET Fybroc Division IS A REGISTERED TRADEMARK OF MET -PRO CORPORATION TOLL-FREE: 1-800-FYBROC-1, Phone: (215) 723-8155, FAX: (215) 723-2197EY-2 EPOXY RESIN (FRP)PUMPS•Identical construction (thermoset) and molding process (RTM) as pumps manufactured utilizing vinyl ester resin (VR-1)•Available in all pump configurations: centrifugal (ANSI /ASME dimensioned), close-coupled, self-priming,mag-drive, vertical sump, cantilever•Excellent corrosion resistance with aggressive, solvent-based chemicals•Ideal for concentrated sulfuric acid (98%)•Higher maximum temperature capabilities, in certain applications, compared to vinyl ester resin (VR-1)•Typical markets include pharmaceutical, petrochemical,fertilizer, and pesticide. Also, EY-2 allows expanded opportunities for Fybroc pumps in existing markets such as electronics, chemical process, and metal finishing.。
斯伦贝谢POWER-V
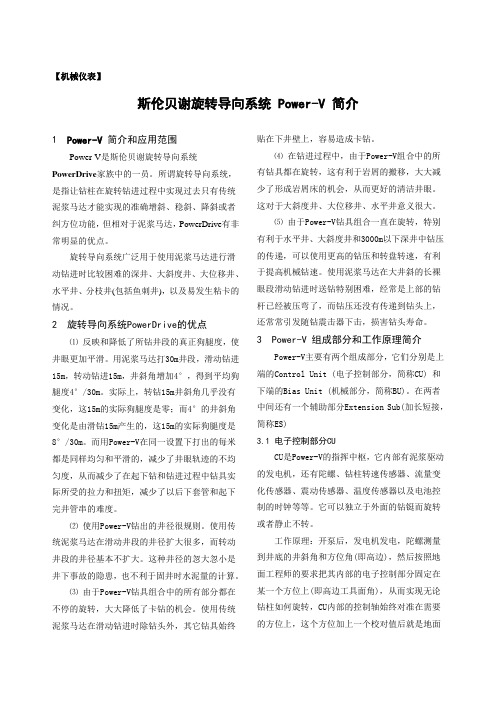
【机械仪表】斯伦贝谢旋转导向系统 Power-V 简介1 Power-V 简介和应用范围Power-V是斯伦贝谢旋转导向系统PowerDrive家族中的一员。
所谓旋转导向系统,是指让钻柱在旋转钻进过程中实现过去只有传统泥浆马达才能实现的准确增斜、稳斜、降斜或者纠方位功能,但相对于泥浆马达,PowerDrive有非常明显的优点。
旋转导向系统广泛用于使用泥浆马达进行滑动钻进时比较困难的深井、大斜度井、大位移井、水平井、分枝井(包括鱼刺井),以及易发生粘卡的情况。
2 旋转导向系统PowerDrive的优点⑴反映和降低了所钻井段的真正狗腿度,使井眼更加平滑。
用泥浆马达打30m井段,滑动钻进15m,转动钻进15m,井斜角增加4°,得到平均狗腿度4°/30m。
实际上,转钻15m井斜角几乎没有变化,这15m的实际狗腿度是零;而4°的井斜角变化是由滑钻15m产生的,这15m的实际狗腿度是8°/30m。
而用Power-V在同一设置下打出的每米都是同样均匀和平滑的,减少了井眼轨迹的不均匀度,从而减少了在起下钻和钻进过程中钻具实际所受的拉力和扭矩,减少了以后下套管和起下完井管串的难度。
⑵使用Power-V钻出的井径很规则。
使用传统泥浆马达在滑动井段的井径扩大很多,而转动井段的井径基本不扩大。
这种井径的忽大忽小是井下事故的隐患,也不利于固井时水泥量的计算。
⑶由于Power-V钻具组合中的所有部分都在不停的旋转,大大降低了卡钻的机会。
使用传统泥浆马达在滑动钻进时除钻头外,其它钻具始终贴在下井壁上,容易造成卡钻。
⑷在钻进过程中,由于Power-V组合中的所有钻具都在旋转,这有利于岩屑的搬移,大大减少了形成岩屑床的机会,从而更好的清洁井眼。
这对于大斜度井、大位移井、水平井意义很大。
⑸由于Power-V钻具组合一直在旋转,特别有利于水平井、大斜度井和3000m以下深井中钻压的传递,可以使用更高的钻压和转盘转速,有利于提高机械钻速。
斯伦贝谢的马达手册.

Anadrill PowerPak Steerable Motor Handbook1.0 介绍1.1 钻井马达的发展1.2 PowerPak马达的设计和测试1.3 应用2.0 PowerPak马达描述2.1 顶部接头2.2 动力部分2.3 传动部分2.4 轴承部分和驱动轴2.5 弯壳部分和连接扣型3.0 作业3.1 常用参数3.2 狗腿严重度限制3.3 工作准备3.4 马达的现场操作3.5 空气钻井3.6 短半径钻井3.7 打捞马达4.0 地质导向系统5.0 操作参数6.0 司钻手册1。
2 PowerPak 的设计和测试PowerPak马达是根据DD的要求而设计的,特别需要强调的是,粗糙,朴素,已证明的技术已经转变为了在工作现场占优势的,可信赖的作业。
Anadrill 遵循使井底系统接近最小的噪音对MWD测量数据的干扰,以及确保PowerPak马达不会限制排量和其它的钻井作业的原则。
为期18个月的系统分析和部件测试计划开始于1990年。
这项综合计划包括全尺寸的的功率计和钻机操作测试,利用位于Texas Sugar Land 的Anadrill的先进的测试设备。
已设计一项工程维修计划,包括时间表和部件跟踪。
从早在1992年的采用开始,PowerPak马达已经连续地达到或接近设计目标,为了它的可靠性,操作和维修成本,而且,对于改进效率和降低钻井成本,已经建立了一个新的标准。
PowerPak马达特性●PowerPak导向马达设计有标准组件,以使它们能够在对MWD干扰最小的情况下适应更广泛的定向井作业。
可以通过马达部件的选择,优化其在任何一种钻井条件下的作业。
●PowerPak马达的泥浆润滑轴承特性适合恶劣的钻井环境。
●多种多样的定转子形状允许PowerPak马达可用于低速高扭和高速低扭这两种情况。
●地面可调节弯壳体(SAB)改进了效率,增加了在现场的钻井控制能力。
●锻钢驱动轴提高了马达的强度。
●密封的传动组合阻止泥浆损害,从而提高了马达寿命。
斯伦贝谢PVTi参考手册---工作流程
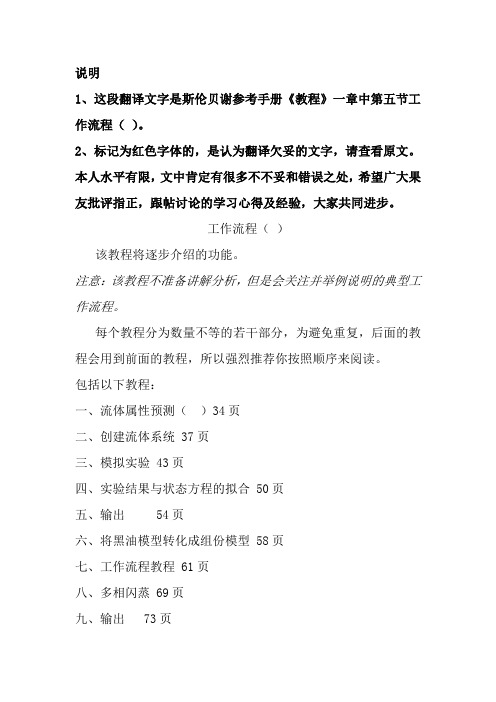
说明1、这段翻译文字是斯伦贝谢参考手册《教程》一章中第五节工作流程()。
2、标记为红色字体的,是认为翻译欠妥的文字,请查看原文。
本人水平有限,文中肯定有很多不不妥和错误之处,希望广大果友批评指正,跟帖讨论的学习心得及经验,大家共同进步。
工作流程()该教程将逐步介绍的功能。
注意:该教程不准备讲解分析,但是会关注并举例说明的典型工作流程。
每个教程分为数量不等的若干部分,为避免重复,后面的教程会用到前面的教程,所以强烈推荐你按照顺序来阅读。
包括以下教程:一、流体属性预测()34页二、创建流体系统 37页三、模拟实验 43页四、实验结果与状态方程的拟合 50页五、输出 54页六、将黑油模型转化成组份模型 58页七、工作流程教程 61页八、多相闪蒸 69页九、输出 73页十、资料(或数据)分析与质量控制 77页十一、排除样品污染 84页十二、调用旧工程用于当前工程 87页一、流体属性预测()该节教程阐明的是如何使用模块进行流体属性预测()。
该教程中的数据可按照标准安装路径如下:$2007.1在使用该节教程之前,你必须先将该文件拷贝到你自己的本地文件夹中。
该教程分为以下几个部分:1.介绍 34页2.基本信息 34页3.闪蒸计算 36页4.结论 36页1、介绍流体属性预测能够提供一种快速查看井场所提供的属性表的功能。
饱和压力(泡点或者露点压力)连同油藏组成已经足够输入并提供快速查看功能,给予一个初始的流体性质预测以方便实验室中的全流体分析。
完成该节教程的学习之后,你应该能够使用这个数值模拟工具来进行流体属性预测。
2、基础信息1、启动(如果你不知道如何启动,请查看31页“启动”)。
2、输入作为新工程的文件名。
提示:当在中建立一个新的、空的工程时,窗口会自动打开。
如果想在其它任何时候打开窗口,可选择:。
窗口允许你输入最少的信息是至少能创建一个完整的状态方程模型。
3、点击“”复选框。
提示:你在实验室报告中看到的摩尔百分数来源于组份的质量百分数和摩尔质量。
Steritest 泵控制器说明书

Avec la fonction Temporisateur l'écran principal.Appuyer surpour ouvrir la têtede pompe.pour sélectionnerle Mode Standard.le Mode Standard.Installer l'unité Steritest™ sur la pompe.Appuyer sur pour fermer la tête de pompe.de la pompe.fixer la valeur du temporisateur .Remarque : Non accessible lorsque la pompe est en fonctionnement.Configurer la pompeMode Régulation de la pressionSans la fonction Temporisateurpour arrêter la pompe avant la fin du temps prédéfini.Utilisation en Mode Stan dardGuide rapide de l'interface utilisateurde la pompe Steritest™ SymbioUtilisation en Mode Méthodes de testà l'écran principal.Remarque : Ce mode n'est accessible que si des méthodes de test ont été préalablement chargées dans la pompeà l'aide du logiciel Steritest™ Symbio.à l'écran précédent..Appuyer surpourouvrir la tête de pompe.à l'étape précédente.à l'écran précédent.Remarque : Pour télécharger le Guide l'utilisateur de la pompe Steritest™ Symbio complet, rendez-vous sur /steritest-symbio.© 2019 Merck KGaA, Darmstadt, Allemagne et/ou ses sociétés affiliées. Tous droits réservés.Merck , Steritest, Sigma-Aldrich et Millipore sont des marques de Merck KGaA, Darmstadt, Allemagne, ou d'une société affiliée. Toutes les autres marques citées appartiennent à leurs propriétaires respectifs. Des informations détaillées sur les marques sont disponibles via des ressources accessibles au public. PF16602FR Version 3.0 01/2019L'activité Life Science de Merck KGaA, Darmstadt, Allemagne opère sous le nom de MilliporeSigma aux États-Unis et au Canada.Appuyer sur pour fermer la tête de pompe.Une fois la dernière étape de la méthode de test terminée, appuyer sur pour ouvrir la tête de pompe.Suivre les instructions de l'étape. Puis appuyer surpour passer à l'étape suivante.。
斯伦贝谢连续油管工艺技术简介

– 压裂设备操 作员
连续油管压裂(CoilFRAC)车
适合不同要求 – 2" 至 2 7/8"连续油管 – 100,000# 拉力注入头 – 远程控制防喷器 – 支架(提高稳定性) 效率 – 二人即可操作 – 7.06" 防喷器 – 7.06" RISER
Slide 15
连续油管压裂(CoilFRAC)技术的应用
连续油管悬重
C ilC T o A
T b gF rc s u in o e
100 40 100 20
A ra e Wig t ve g d e h P p icku S cko la ff
连续油管悬重 –通过数据对比, 及时发现并诊断 井下的异常状况
100 00 80 00 60 00 40 00 A ra e 0 0ig t - lb ve g 2W h f d 0e 0 -2 0 00 0 20 00 40 00 C rre dD p - ft o cte e th
0.150 1.25 2.125 3.125
0.200
0.250
*喷射液压孔设计 *喷射头大小 *除垢速率 *防止损伤油管
Nozzle Dia (in)
100 90 80 70 60 50 40 30 20 10 0 0.000
Nozzle Power (Hp)
0.050
0.100 0.150 0.200 Nozzle Dia (in) Circulating Pressure Drop 4500 4000 3500 3000 2500 2000 1500 1000 500 0 0.000 0.050 0.100
Slide 16
Schlumberger连续油管井下工具 –PETRO-TECH公司
Watson-Marlow Bredel 科学用泵产品说明书
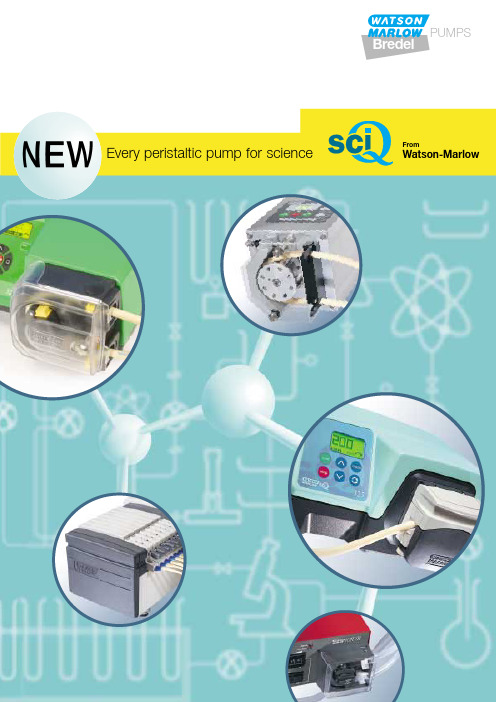
and operate. Each pump is flexible and can be quickly adjusted to perform your exact instruction.Quality has always been a feature of Watson-Marlow pumps and the Sci-Q range enhances this with features like brushless DC drives and precision gearboxes. Reliability, accuracy and long life ensure best value for your 60070ml /mi n –10.4l i t r e /m i n 5000.02ml /mi n –3.5l i t r e /m i n 401µl /m in–730ml /m i n3002µl /m in–2.2l i t 2000.6µl /m i n–22m l /m i n1001µl /m i n–53m l /m i nD i s p e n s i n g0.54m l /m i n –8.5l i tr e/m i nBrushless DC motor means zero Choice of control options – manual,8MC X•••18MC •••4MC X•••14MC•••314D2•••••314X•••••314D•••••13D2•••••313X•••••313D•••••323323S 32323323S 32323323S 32323323S 32323323S 32323323S 32323323U32323323U32323323U32323323U32624Di/Lhas the same long life as Marprene but complies with USP Class VI,resistance, long life and very high burst pressures. Chem-Sure is USP Class VI performance and low gas permeability. FDA approved for use with food and isPhysical compatibilityTemperatureThe chart shows the temperature range of each tubing type when suction and delivery pressures are negligible. Operating temperatures ofBioprene, Marprene, Chem-Sure, Sta-Pure and silicone tubing are limited to 80C, but all may be autoclaved up to 135C.-4F32F70F105F140F175FMarprene/BiopreneSiliconeNeopreneChem-SurePVCSta-Pure-20C0C20C40C60C80CPressureChoose the smallest bore size of tubing which will give the required flow rate.Marprene/BiopreneSiliconeNeopreneChem-SurePVCSta-PureLow Pressure capability HighSuctionAs with pressure, choose the smallest bore of tube which will produce the required flow rate. Equally important, however, is therestitutional power of the tubing material:Marprene/BiopreneSiliconeNeopreneChem-SurePVCSta-PureLow Restitutional Power HighPermeabilityMarprene/BiopreneSiliconeNeopreneChem-SurePVCSta-PureHigh Permeability Low 26Tube life102R tube life range (hours)No pressure. 32rpm. Clockwise rotation. 4.8mm (3/16") bore silicone tubing.Platinum silicone900313 and 314 pumphead tube life range (hours)No pressure. 110rpm. 6.4mm bore tubing.Marprene/Bioprene 10000Platinum silicone 230Sta-Pure10000520R pumphead tube life range (hours): clockwise rotationNo pressure. 220rpm. Clockwise rotation. 6.4mm bore tubing, except Marprene which was 4.8mm bore.Marprene/Bioprene 10000Neoprene 40Platinum silicone 200Chem-Sure 6000Sta-Pure 10000PVC90620R tube life range (hours)Conditions: Zero pressure. 100rpm. Clockwise rotation. 12.7mm bore tubing.Marprene/Bioprene 6000Neoprene 60Platinum silicone 230Chem-Sure 5000Sta-Pure 6000PVC9005001000500010000ViscosityThe flow rates given in this catalogue are valid for fluids with viscosities in the range 1 to 100 centipoise.Increased fluid viscosity will result in decreased flow rate. Choose a tubing with as large a wall thickness as possible, which could, for instance, mean using a 600 series pump which user greater wall thickness tubing, rather than a 500 series pump. Following this guidance will allow fluids with viscosities up to 2500centipoise to be satisfactorily handled.Contact Watson-Marlow or its local distributor for advice on specific applications.27T u b e l i f e•Flow rates from 1µl to 610 ml/min•Precision multi-roller pumpheads for accurate flows •Single channel 102R pumphead for use with Silicone or Marprene tubing•Digital and analogue process signal control •Flow rates from 10 µl/min to 4.4 litre/min•Manual, analogue and digital RS232/RS485 control•ATEX rated, three phase and pneumatic drives •Seven pumpheads options including low-pulse high accuracy 505L• Dosing and dispensing pump for +/- 0.5% accuracy•Flow rates from 50ml/min to 18.3 litre/min •Manual, auto and digital control•Close coupled pumps for the three phaseoperation including pneumatic and ATEX options •One minute maintenance LoadSure elements •Flow rates from 1.6 litre/min to 2,000 litre/ hour •Single or twin channel operation•Driven roller pumphead extends tube life•LoadSure elements ensure correct tube loading every time •Fixed or variable speed drives•Flow rates 2 litre/min to 8,000 litre/hour•Full Clean-In-Place and Steam-In-Place capability •Extensive motor/gearbox control options•Flow rates to 0.3 litre/min 80 cubic metres/hour •Reinforced hoses enable pressures up to 16 bar •Fixed and mechanically or electronically variable speed drives including ATEX versions•Flow rates from 1µl/min to 53ml/min •Rapid and simple tube loading•Manual, auto and digital TTL control100200300600700800500SPX520S /R623S /R 825323E /D205S /C A101F /RS P 10 a n d 15400401U /D 1S P 25704U /R E a n d 704S /R E 624S /R E 520U /R 401U /D M 3323S /D 205U /C A101U /R •Flow rates from 0.6µl/min to 22ml/min per channel •Precise flow control for each individual channel •Manual, auto and digital TTL controlWatson-Marlow Bredel pumps bring you…NEWSingle or multi-channel benchtop pumps with manual, remote,analogue, RS232 control and accurate dispensing.NEWSuperb range of IP31 and IP66 rated pumps for science and industry as well as fixed and variablespeed close-coupled pumps.IP55 mid-flow process pumps with full clean-in-place and steam-in-place capability.Industrial cased and baseplate mounted pumps for use withcontinuous tubing or new LoadSure elements. Three phase motors, ATEX rated drives or pneumatic.High-flow hygienic pumping using USP Class VI Bioprene tubing or STA-PURE tubing.High flow high-pressure industrial pumps with unique patented direct coupled design. Duplex and CIP models available.Low flow single channel pumps.Fixed and manual/auto control variable speed.Near pulseless, multi-channel cassette pumps with up to 32 channels.NEWUltra-compact scientific pumps for low flow single or multi-channel applications.2bar2bar 2bar 2bar 2bar 4bar 2bar 7bar 16bar840•Accurate and repeatable flow rates•Contamination free pumping - ideal for shear-sensitive fluids, viscous sludges or slurries, and aggressive acids and caustics•Flow rates from 0.01µl/min to 33 litre/min •Single and multi-channel pumpheads•Synchronous, DC, induction, shaded-pole or stepper motors•Optional Eurocard pcb enables full controllabilityOEM100300A wide range of instrument quality and industrial OEM pumpheads for fitting to users own drives, or with faceplate-mounted motor options.12bar•Twelve tubing materials in bore sizes 0.13mm to 25.4mm•Autoclavable Marprene, Bioprene, STA-PURE, Chem-Sure and Pumpsil Silicone (platinum-cured) with LaserTraceability •Four hose materials including Natural Rubber, Nitrile NBR,Hypalon and EPDM from 10mm to 100mmTubing HosesM a r p r e n e B i o p r e n e Extensive range of tubing ensures chemical compatibility. USP Class VI and FDA approvals. Precision machined, re-inforced hosesprovide flow stability and excellent suction performance.•Easy to install, operate and maintain •Virtually maintenance free - no expensive seals, valves, diaphragms or rotors to leak,clog or corrode•Flow rates from 2µl/min to 3 litre/min•High visibility digital display with membrane keypad •Single channel or up to ten separate channels •Zero maintenance brushless DC motors•New 323Dz general purpose dispensing pump704U /R a n d 704S /RS P X 32701F /R701P B /R624U /R E624D i /L621F /R621V I /R E621F X /R E520D u /R520S N /R 2520U N /R 2520D u N /R 2521F /R 2403U /R 1403U /U L 2405U /R 1405U /L403U /V M 2621D V /R E521V I /R 2621P /R E 520D i /L 403U /V M 4S P X 40•Designed for continuous duty - 24 hours/7 days •Pumps act as their own check-valves400500S i l i c o n eS t a -P u r e600P V C700N e o p r e n eF l u o r e lC h e m -S u r eH o s e s•Self-priming up to 9 metres (30 feet) and dry running •Reversible flow directionS P X 50S P X 65S P X 80S P X 100S P X D U P L E X 323U /D323D u /D323D z /D314M CDrive F Fixed speed S Manual control variable speed U Manual/auto control variable speed Du Digital/analogue control variable speed Dz Dispenser Di Precision dispenser, RS232 control VI Varmeca controlled FX Fixed speed duplex drive DF ATEX EExd T4 fixed speed P PneumaticDVB ATEX Exd T4, mechanical variable speed PB Pneumatic, baseplate mounted SN/UN/DuN (N) denotes IP66 protectionPumphead R Single channel pumphead R2Single channel pumphead for 2.4mm wall tubing RE Single channel pumphead for LoadSure elements CA High precision multi-channel cassette pumphead D1Single channel, four roller pumphead D Single channel, three or four roller, 'flip-top' pumphead DM2-3Three channel pumphead for three bridge manifold tubing R1Single channel, four roller pumphead L2Two channel, four roller pumphead L Precision 'low pulse' pumpheadVM2-4Precision low flow multi-channel pumphead for two bridge manifold tubingCode descriptionseg: 101U /R = Manual/auto control variable speed with single channel pumphead403U /R701F /R E701P B /R E700 E l e m e n t K i tWolf Laboratories LimitedTel:01759301142Fax:****************************.ukUse the above details to contact us if this literature doesn't answer all yourquestions.Pricing on any accessories shown can be found by keying the part numberinto the search box on our website.The specifications listed in this brochure are subject to change by the manufacturer and therefore cannot be guaranteed to be correct. If there are aspects of the specification that must be guaranteed, please provide these to our sales team so that details can be confirmed.。
KISHOR PUMPS VERSA系列处理泵产品说明说明书

High T echnology T ailor-Made PumpsExperience our ExperienceVERSAProcessPumpsSeriesWith four decades of experience and expertise, KISHOR PUMPS has been partnering industry majors across the world in the successful execution of projects with its leading age Chemical Process Pumping Solutions. VERSA, our innovative range of Process Pumps caters to numerous critical operations in the process industries like transfer of various kinds of acids, alkalis & solvents and handling of various corrosive liquids. Highly efficient and advanced technology, solution engineering, lifelong performance and excellent service support made us the most accomplishing system partner. Industry majors’ preferred choice and India's renowned consultants' approvals stand testimony to the fact that our Chemical Process Pumps are widely accepted for quality and value for investments.••••••••A trusted name in fluid handling for 45 yearsA company with high-tech solutions for fluid handlingA wide range of products to serve every segment of industry T ailor-made pumping solutionsApproved by all major consultants / inspection agencies State of the art manufacturing and testing facilities Wide spectrum of material to suit all liquidsA wide spread network to reach all geographical locationsThe KISHOR AdvantagesCapacity :Upto 1500 cumph Head:Upto 150 mlc No. of Sizes:46Installation Depth :Upto 10 m (For VerticalExtended Shaft Execution) _T emperature :30°C to + 200°C Viscosity :Upto 20 cst Sp. Gravity :Upto 2T est Pressure:Upto 16 kg / sq.cm.Range••••••••Cast Iron Ductile Iron Alloy Cast Iron Stainless Steels Super Alloys Nickel Alloys BronzesRubberlining( Special materials other than above available on request. )Material of Hydraulic PartsApplicationsIdeal choice for aggressive process chemicals of corrosive and abrasive nature like:• Acids • Alkalies • Solvents • Slurries • Hydrocarbons • Crystallizing Liquids • Chemical Effluents • Hot Oils • Sea WaterUser Industries•••• • ••• ••• • • • • •Chemicals Refineries Power Mining T extile Paper and Pulp PharmaceuticalsWater Treatment Petrochemicals Fertilizers Steel Plastics & Rubber Paints and Dyes Sugar Automobile Bulk DrugsKISHOR PUMPSChemical Process Pumps Series (VERSA)Vertical Execution Standard Features••••••Centrifugal, Single StageBottom axial suction, tangential delivery Glandless executionGrease lubricated deep groove ball bearings Closed impellersRectangular support plateOptional Features•••••••••Variety of wear ringsSemi-open impellersShaft Sealing by gland packing or a variety of standard mechanical sealsWet bearing lubrication by pumped liquid / water / grease for higher installation depthsSupport plate of various shapes, sizes and standardsSteam jacketing for special liquids like molten sulphur or lead Cantilever design for slurry applicationsRubber lining for casing, column pipe & delivery pipe for corrosive liquidsSandwich design for hard materials like Ni-Hard,Hard Chrome IronVersions: Vertical ExecutionVERSA-ES: VERSA-EG: VERSA-EV: VERSA-EJ: VERSA-EC: VERSA-EL: VERSA-ED:Standard Glandless VersionVapor Sealing ( Gland Packed) VersionVapor Sealing ( Mech. Seal )VersionSteam Jacketed Version for Crystallizing Liquids Cantilever VersionRubber lined VersionDual Delivery VersionAdvantages• • •••Priming not necessary since pump casing is submerged upto the lowest pumping levelNo cavitation since casing and impeller are submerged under liquidNo need of suction pipingExpert services for pump and motor shaft alignment not required since vertical flange mounted motorcan be easily fitted to the concentrically machined motor stoolliberally designed shaft, coupling and wet bearingsLonger trouble free working cycle with(Typical Dual Delivery Version)VERSA - EDVERSA - EJVERSA - EL3/98% H SO : Capacity : 1300 m 24Vertical Submerged Pump for hrSince we have introduced the Vertical Submerged Pumps in India, KISHOR PUMPS has become a preferred choice for import substitution for critical applications. Multifaceted Research and Development activities, immensely updated and advanced technology and commitment to international standards earned us this reputation.Preferred choice for Import SubstitutionThe entire series is designed with modular units and pumps of all sizes are built by these modular units offering the best possible interchangeability.The pumps are hydraulically designed for maximum efficiency. Every pump passes through stringent process and quality control plans and is designed to give longer life with consistent performance and trouble free service. This makes our Process Pumps…. Lifelong Performers!ReliabilityInterchangeabilityAlgeria Australia Bangladesh Belgium Egypt Malaysia Nepal Singapore The Netherlands••••••••• Sri Lanka Saudi Arabia Thailand raine France Germany Indonesia ••••• • • • Japan Lithuania Congo Zambia Nigeria Kuwait Qatar Russia• • • •••••Exporting Excellence OverseasRecognition that makes a difference•••••••• Engineers India Ltd.UHDE India Ltd.Kvaerner Power Gas Ltd.TCE Consulting EngineersFitchner Consulting Engineers M. N. Dastur & Co.Technip Consulting Engineers Jacobs H & GL&T Chiyoda Ltd. Tecnimont ICB Ltd. Toyo Engineering Lurgi India Co Pvt. Ltd. DESEINMECON D. C. L., KolkataSNC Lavlin Engg.••••••••• Apex Division• Manufacturing Divisions• Trading Division• Support DivisionsCMD : Corporate Management Division, Pimpri, Pune.IPD : Industrial Pumps Division, Pimpri, Pune.EPD : Enviro Pumps Division, Kuruli, Pune.SPD : Standard Pumps Division, Satara. TPD : Trading Products Division, Kuruli, Pune.CSD : Customer Support Division, Pune. IBD : International Business Division, Pune.• Sales and Service Offices in India • Service Centres in IndiaMumbai, Delhi, Chennai, Kolkata, Pune,Bangalore, Vadodara, Hyderabad, Coimbatore. Pune, Chennai, Ambala, Kolkata.Customer Support Division : 22, Barve Complex, 11710/1, J. M. Road, Shivajinagar, Pune - 411 005, INDIA.Tel: +91-20 25535449 / 459, Fax : +91-20 25535129, E-mail:****************************InternationalBusinessDivision:E-mail:*****************************KISHOR PUMPS PVT . LTD.The world counts on us also for...• Industrial Water Pumps •Thermic Fluid Pumps •Hygienic Liquid Pumps •Submersible Sewage Pumps •Submersible Wastewater Pumps •Submersible Dewatering PumpsK P / P L / V - 10 / H / 2000Due to constant Research & Development, the above information is subject to change without prior notice. Colours do not signify materials.Paradigm Plus。
20110329 斯伦贝谢电潜泵介绍
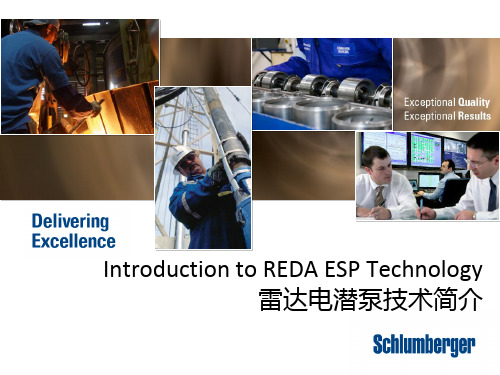
Protector Type
电机保护器种类
Labyrinth Protectors 沉淀式保护器
The labyrinth design uses the difference in specific gravity of the well fluid and the motor oil to keep them apart even though they are in direct contact. 迷宫式保护器是利用井液与电机油比重的不同来实现 保护的作用。
A licensed technology from IFP (Institut Francais du Petrole) TOTAL and STATOIL IFP (Institut Francais du Petrole) ,TOTAL 和STATOIL专利
Protector
电机保护器
Poseidon is the Axial Flow Pump installed between Intake or Gas Separator and the main pump capable of handling up to 75% free gas.
Poseidon可以使泵在75%的自由气情况下正常工作。其安装 在泵与吸入口之间。
Protector Type
电机保护器种类
Using the Modular System, the Protector can be designed to meet specific application requirements without unnecessary and expensive duplication of parts 模块式保护器可以根据不 同的应用需要而设计。
SOGEVAC SV28 BI单阶油封闭旋钮泵操作指南和零件列表说明书

Part Numbers 960 270 - 960 273960 276 - 960 278and their variantsSOGEVAC ®SV28 BISingle-stage, oil-sealed Rotary Vane PumpOperating Instructions 300270050_002_C0and Spare Parts list2300270050_002_C0 - 11/2016 - © Leybold1 General Instructions 31.1 Safety Instructions 31.2 Application range 51.3 Principle of operation 51.4 Technical characteristics 61.5 A ccessories81.6 Transport and Packing91.7 Mounting orientation and storage 91.8 Lubricants92 Installation 102.1 Setting-up 102.2 Inlet connection102.3 Connection to exhaust side 102.4 Oil filling102.5 Electrical connection 102.6 Operating advices 112.7 Shutdown113 Maintenance 123.1 Oil level 123.2 Oil change123.3 Exhaust filters replacement 133.4 Gas ballast valve cleaning 133.5 Inlet flange sifter cleaning 133.6 Anti-suckback valve checking 133.7 Fan cover cleaning133.8 Checking the float valve 134 Breakdown analysis 135Spare parts146 Information 14EC Conformance Declaration Declaration of contamination Spare Parts listSales and ServicePage Installation and operating instructionsThese installation and operating instructions are valid for the SOGEVAC ® pumps SV28 BI in their standard version.Special versions to these pumps are delivered with an additive document, which prevails over the standard instructions.The SOGEVAC ® vacuum pumps have been manufactured according to the latest technical standards and safety regulations. If not installed properly or not used as directed, dangerous situations or damage could occur. It is mandatory that these operating instructions be read and understood prior to vacuum pump installation and start-up.3300270050_002_C0 - 11/2016 - © Leybold 1 General Instructions1.1 Safety instructionsIn this paragraph, the most important safety and usage instructions for the SOGEVAC ® pumps are listed. Ahead of each following paragraph of the manual, the numbers of the applicable safety instructions will be listed. Indicates procedures that must be strictly observed to prevent hazards to persons.Indicates procedures that must be strictly observed to prevent damage to, or destruction of the product.Emphasizes additional application information and other useful information provided within these Operating Instructions.The Leybold Sogevac ® has been designed for safe and efficientoperation when used properly and in accordance with these Operating Instructions. It is the responsibility of the user to carefully read and strictly observe all safety precautions described in this section and throughout the Operating Instructions. The Sogevac ® BI must only be operated indoor in the proper condition and under the conditions described in the Operating Instructions. If not, the protection provided by the equipment may be impaired. It must be operated and maintained by trained personnel only. Consult local, state, and national agencies regarding specific requirements and regulations. Address any further safety, operation and/or maintenance questions to our nearest office.Failure to observe the following precautions could result in serious personal injury!1.1.1SOGEVAC ® pumps are not designed:. for pumping of aggressive, corrosive, flammable or explosive gases or gases mixtures ;. for pumping of oxygen or other highly reactive gases with a greater concentration than atmospheric concentration (>20%) ; . for working in flammable or explosive environment.For all these cases, special materials must be used. In case of doubt, please contact Leybold.See also the limits of use indicated in the EC Declaration of Conformity. 1.1.2Liquid and solid particles must not enter the pump. Install the adequate filters, separators and/or condensers. In case of doubt consult Leybold. Do not allow the ingestion of any objects (screws, welding beads, nuts, washers, pieces of wire, fittings etc.) through the intake port of the pump.Objects falling into the pump can cause severe damage.WarningWarning Caution Note4300270050_002_C0 - 11/2016 - © Leybold1.1.3The intake line of the pump must never be connected to a device with over atmospheric pressure. Size of the exhaust line so that no pressure higher than 1,15 bar abs. (0,15 bar rel.) or depression of 15 mbar (0,15 bar rel.) can occur1.1.4Operating of the pump without oil or operating with incorrect sense of rotation can destroy the pump.1.1.5Never expose part of the body to the vacuum. There is a danger of injury. Never operate the pump with an open and thus accessible inlet. Vacuum connections as well as oil filling and oil draining openings must not be opened during operation of the pump.1.1.6Caution : hot surface !in normal operation, the pump surface temperature can reach 85°C (185°F). There is a risk of burning. Switch off the pump and let it cool down before any intervention or take appropriate precautions.It is recommended to use an oil casing or pump touching protection at high ambient temperatures. As a touching protection, you can use the noise enclosure P/N 960331NENC. The noise enclosure is an accessory not included in the pump delivery.All work on a pump which is "still warm from operation" should be done only whilst wearing protective gloves. Handle the pump only while vented and after having let it cool down.Never remove the oil-fill or oil-drain plugs while the pump is running.There exists the risk of suffering burns. Always wear protective gloves and protective goggles also for protection against the oil.1.1.7Depending on the process involved, dangerous substances and oil may escape from the pump. Take the necessary safety precautions ! Clean oil traces off the pump or floor !1.1.8Observe the safety regulations !Never use discarded seals. Always assemble using new seals.Respect the instructions concerning environment protection when discarding used oil or exhaust filters !1.1.9High electric voltages ! When touching parts at high electric voltages, there is the risk of suffering severe injuries by an electric shock ! Covers marked with this symbol must only be opened by trained electricians after having reliably deenergised (lockout/tagout) the equipmentAlways operate the pump with a properly connected protective earthconductor and make sure that the motor connection box is closed.Lay the connecting lines so that these cannot be damaged. Protect the lines against humidity and contact with fluids. Avoid thermally stressing the lines byunfavourable laying. Provide strain relief for the connecting lines so that theWarningCautionCautionplugs and the line connectors are not subjected to excessively high mechanicalstresses.Lay electric feed lines so that there is no risk of tripping over these.1.2 Application rangeSee prescriptions chapters 1.1.1. and 1.1.2.SOGEVAC® pumps are designed for pumping of inert gases in the range ofmedium vacuum, between atmospheric pressure and ultimate pressure of thepump. Pumps with single phase motors shall not operate in continuous dutyover 50 mbar abs. Please advise Leybold if you are in such a case or if thechamber volume exceeds 50 l.Indoor use up to 2000 m altitude and rel. humidity ≤ 95 % withoutcondensation.Ambiant temperature 1 ph. pumps 16 ... 40°CAmbiant temperature 3 ph. pumps 12 ... 40°C1.3. Principle of operationThe SOGEVAC® pumps SV28 BI are single-stage oil sealed rotary vanevacuum pumps. The rotor, having three slots in which the vanes are sliding, iseccentrically installed in a pump cylinder (stator).The vanes separate the interior space into 3 chambers. The volume of thesechambers varies with the rotation of the rotor.The gas sucked into the inlet chamber is compressed and then pushed out atthe exhaust valve.The oil injected in the inlet chamber guarantees the air-tightness, the lubricationand cooling of the pump. It is dragged off by the compressed gases and roughlyseparated by gravity when entering in the oil sump. A fine separation is thenoperated in the exhaust filter. The exhaust filter retains > 99,9% of the aerosols.An internal transfer pushes the collected oil back into the vacuum generator, thetransfer is operated by a float valve to avoid atmospheric air coming from the oilcasing to the inlet of the pump when no oil is present in the recovery system.The oil circulation functions by differential pressure.Depending on catalog numbers, the pumps are equipped with a gas ballast valvefor pumping condensable vapours.The anti suckback valve at the inlet flange avoids oil coming back into the inletline when the pump is stopped. This is valid for working pressures below 100mbar and under the condition that the valve is kept clean and in good condition.The anti suck-back valve is not a safety valve. If oil back flowing is to be avoidedby all means, it is necessary to mount a separate safety valve on the pump inlet.The pumps P/N 960 276 and 960 277 and their variants are certified accordingStd. EN 61010-1 (2004).This product has been tested to the requirements of CAN/CSA-C22.2 No61010-1, second edition, including Amendment 1, or a later version of the samestandard incorporating the same level of testing requirements.37 A @ 240 V AC300270050_002_C0 - 11/2016 - © Leybold5General Instructions6300270050_002_C0 - 11/2016 - © Leybold7300270050_002_C0 - 11/2016 - © LeyboldS i n g l e p h a s e p u m p .P l e a s e c o n t a c t L e y b o l d f o r 3 p h a s e p u m p s8300270050_002_C0 - 11/2016 - © Leyboldwithout gas ballastwith gas ballastat 60Hzat 50HzPumping speed curves1.5 AccessoriesFor the accessories, please refer to the Leybold General Catalogue chapters C01 and C13.Kit anti suck back valve 9 714 62 600Gas ballast kit 9 714 62 640Gas ballast obturator EK971473010Set of seals 9 714 62 670Float valve kit 9 714 62 660Rubber feet kit9 714 62 6503 phase motor flange kit 9 714 62 630Stator kit9 714 62 620Complete oil casing 0.5 l 9 714 49 400Complete oil casing 1.5 l 9 714 54 140Repair kit9 714 62 690Vacuum generator three phase pump 9 714 62 620Vacuum generator single phase pump 9 714 62 630Oil level switchupon requestno retrofit possible Noise enclosure960331NENC300270050_002_C0 - 11/2016 - © Leybold910300270050_002_C0 - 11/2016 - © Leybold2 Installation (see chapter 1.1)It is essential to observe the following instructions step by step to ensure safe start-up. Start-up may only be conducted by trained specialists.2.1 Setting-upThe pump must be set up or mounted horizontally on a flat surface. Special mounting is not required.The following ambient operating environment must be observed : . Ambient temperature: 15°C to 40°C (59°F to 104°F), . Ambient pressure = Atmospheric pressure.In order to avoid over-heating of the pump, an undisturbed fresh airflow to the pump is necessary.The pump must be kept clean (no dust deposit)2.2 Inlet connection (see chapter 1.1)The inlet flange can be connected with a vacuum-tight flexible hose and/or pipe. The pipes should cause no stresses on the pump’s flanges. If necessary, compensators must be installed.Restriction of the pipes must be avoided in order not to decrease thepumping speed of the pump. The nominal diameter of the pipes has to be at least the same as the diameter of pump inlet flange.When removing condensable vapours, a gas ballast valve must be installed or open.The inlet pressure must not be above atm. pressure.2.3 Connection to exhaust sideNo isolation or restricting devices should be installed in the exhaust line of the pump. If an exhaust line is installed, it must at least have the same diameter as the exhaust flange. It should be installed in a manner so that no condensate can enter the pump (siphon, slope).Pump exhaust to be connected if oil mist or process gases are to be avoided in the pump area.Warning: The maximum exhaust pressure must neither exceed 1.15 bar absolute (0.15 bar relative), nor fall under atmospheric pressure minus 15 mbar.Corresponding pressure regulating devices to be installed by the user.2.4 Oil filling (see chapter 1.1.4)The necessary oil is supplied in a can beside the pump. To fill in the oil, unscrew the oil fill plug and fill in until the oil level reaches the “MAX” mark beside the oil sight glass.2.5. Electrical connection (see chapters 1.1.4 and 1.1.5) The electrical installation may only be conducted by a specialist. Local regulations have to be followed. Disconnect the power supply before any work in the motor connection box !. Voltage and frequency mentioned on the motor nameplate must correspond to the supply voltage and frequency.. The drive motor must be protected against overloads according to local regulations and IEC 60204-1 & IEC 61010-1WarningWarning11300270050_002_C0 - 11/2016 - © Leybold 2.5.1 Single phase motorsSingle phase motors are equipped with a C14 or C20 socket (depending of their rated voltage) and a C13 or C19 plug for user's mains cord.The motor integrates a motor over-load protection device (red knob on motor connection box) to be manually reset after an overload trip, and an ON/OFF switch.The power socket and cord are disconnection elements which must remain accessible to the users.2.5.2 Three phase motorsA motor protection breaker is to be used to protect the motor against over-currents. The breaker tripping current must be set in accordance with the rated current marked on the motor nameplate.To check the direction of rotation of pumps, flick pump on. If the direction of rotation is not identical to the one indicated by the arrow sticking on the motor hood, then inverse any two of the 3 electrical phases in the terminal box. Looking at the motor fan cover, the direction of rotation has to be counter-clockwise.2.6 Operating advices (See chapters 1.1.1, 1.1.2, 1.1.3 and 1.2)When removing condensable vapours, a gas ballast valve must be installedor opened.The vacuum pump must be run for 30 minutes prior to operation with the inlet connection closed, in order to reach the operating temperature of about 75°C. Only up from this operating temperature, condensable vapours can be transported. After use, the pump has to be left running for an additional 30 minutes with the inlet connection closed and open gas ballast, to clear the oil of condensate.Use ear protection in case of operation at high inlet pressures2.7 ShutdownThe inlet flange of the SOGEVAC ® pumps contains an anti-suck back valve. It closes the inlet flange when the pump is voluntarily or accidentally shut down, thus maintaining the vacuum in the connected system and preventing oil from being sucked back into the system.Except the indications in chapter 2.6 (operating advices) there are no particular precautions for the shutdown of the pump.If the pump must be stopped for a longer period, see chapter 1.7. Close the gas ballast3-phase connection diagramWarningMaintenance Before refastening the oil drain plug, control the O-ring and if necessaryreplace it. Open the oil fill plug and pour in clean oil ; refasten the oil fill plug.The pump has to be rinsed out if there is considerable pollution. Thereforepour in clean oil up to the low edge of the oil-level glass, let the pump runbriefly (for a few minutes) then drain the oil again.3.3 Exhaust filters replacement (see chapters 1.1.6 and 1.1.8)Oil mist escaping from the exhaust during operation indicates that the filteris probably clogged. Increased energy intake by the motor could also be theresult of a soiled exhaust filter. Open the exhaust hood, take out the filterand replace it. Also check the gasket of the exhaut flange and change it ifnecessary.3.4 Gas ballast valve cleaning (see safety prescriptions chapter)Consult Leybold3.5 Inlet flange sifter cleaningSee safety prescriptions chapters 1.1.2., 1.1.6. and 1.1.8.To clean the inlet flange sifter, disconnect the inlet connection and clean thesifter with blast air or an appropriate solvent.3.6 Anti-suck back valve checkingSee safety prescriptions chapters 1.1.2., 1.1.6. and 1.1.8.The anti-suck back valve should be checked at the same time as the inletflange sifter and if dirty, be cleaned with an appropriate solvent. Remove theinlet flange, check if there is no damage on the sealing part of the valve.3.7 Fan cover cleaningSoiling of the fan cover may lead to overheating of the motor and the pump.Put off the cover and clean it with blast air. Before starting the pump again,be sure that the cover has been reassembled.3.8 Checking the float valve (see chapters 1.1.6 and 1.1.8)When replacing the exhaust filter, check the cleanliness and the properoperation of the float valve. After having disassembled the exhaust flangeand fan cover, remove the screw using a 4mm Allen Key. Pull on the floatvalve, clean the nozzle and check that the float itself oscillates free aroundits axle and that the valve is tight. Clean the float chamber of the oil casing.Reassemble in the reverse sequence.4 Breakdown analysisIf you have a breakdown, please contact the Leybold service station and/orask us, to send you the guide: “breakdown analysis”.300270050_002_C0 - 11/2016 - © Leybold13Spare parts5 Spare partsTo guarantee safe operation of the Leybold vacuum pump, only originalspare parts and accessories should be used. When ordering spare parts andaccessories, always state pump type and serial number. You can find partnumbers in the spare parts list.Consumables and main spare parts kits for SOGEVAC® pumps are usuallyavailable on stock at Leybold’s service centers. The list of these parts isgiven hereafter and in the spare part table where the contents of each kit isdetailed.. Exhaust demisters. Oil (Special oils please refer to the specific notice of the pump or contactLeybold).. Service kit. Set of seals. Repair kitWe recommend to use these kits which have been defined to allow anoptimal maintenance or repair. Individual spare parts may need longerdelivery time.Return to Leybold service stationIf the pump has to be returned to Leybold service station for repairing, youhave to attach the form “Declaration of Contamination of Vacuum Equipmentand Components”.The Service of Leybold will send it to you on simple request (specimen on theend of this manual).Leybold will return to the sender’s address any material received without thisdeclaration.For the transport, the pump and its components must be packaged in sucha way, that it will not be damaged during shipping, and that no harmfulsubstances can escape from the package.6 InformationWe would be happy to supply further information as required:Available are :. Technical description of the SOGEVAC® vacuum pumps. Technical description of special oil types for vacuum pumps. Declaration of Contamination of Vacuum Equipment and Components.14300270050_002_C0 - 11/2016 - © Leybold300270050_002_C0 - 11/2016 - © Leybold15Declaration of contamination Declaration of Contamination of Compressors, Vacuum Pumps and Components16300270050_002_C0 - 11/2016 - © Leybold17300270050_002_C0 - 11/2016 - © Leybold Spare parts list18300270050_002_C0 - 11/2016 - © LeyboldSpare parts listNotes 300270050_002_C0 - 11/2016 - © Leybold19Headquarter Leybold GmbH Bonner Strasse 498D-50968 Cologne T: +49-(0)221-347-0F: +49-(0)221-347-1250****************GermanyLeybold GmbHSales, Service, Support Center (3SC)Bonner Strasse 498D-50968 Cologne T: +49-(0)221-347 1234F: +49-(0)221-347 31234*****************Leybold GmbH Sales Area North Branch Office Berlin Industriestrasse 10b D-12099 Berlin T: +49-(0)30-435 609 0F: +49-(0)30-435 609 10********************Leybold GmbH Sales Office South Branch Office MunichKarl-Hammerschmidt-Strasse 34D-85609 Aschheim-Dornach T: +49-(0)89-357 33 9-10F: +49-(0)89-357 33 9-33******************************************Leybold Dresden GmbHService Competence Center Zur Wetterwarte 50, Haus 304D-01109 Dresden Service:T: +49-(0)351-88 55 00F: +49-(0)351-88 55 041*******************EuropeBelgiumLeybold Nederland B.V .Belgisch bijkantoorLeuvensesteenweg 542-9A B-1930 Zaventem Sales:T: +32-2-711 00 83F: +32-2-720 83 38********************Service:T: +32-2-711 00 82F: +32-2-720 83 38**********************FranceLeybold France S.A.S.Parc du Technopolis, Bâtiment Beta 3, Avenue du Canada F-91940 Les Ulis cedex Sales and Service:T: +33-1-69 82 48 00F: +33-1-69 07 57 38*****************************************Leybold France S.A.S.Valence Factory 640, Rue A. Bergès B.P . 107F-26501 Bourg-lès-Valence Cedex T: +33-4-75 82 33 00F: +33-4-75 82 92 69************************Great BritainLeybold UK LTD.Unit 9Silverglade Business Park Leatherhead Road Chessington Surrey (London)KT9 2QL Sales:T: +44-13-7273 7300F: +44-13-7273 7301********************Service:T: +44-13-7273 7320F: +44-13-7273 7303**********************ItalyLeybold Italia S.r.l.Via Trasimeno 8I-20128 Mailand Sales:T: +39-02-27 22 31F: +39-02-27 20 96 41********************Service:T: +39-02-27 22 31F: +39-02-27 22 32 17**********************NetherlandsLeybold Nederland B.V .Floridadreef 102NL-3565 AM Utrecht Sales and Service:T: +31-(30) 242 63 30F: +31-(30) 242 63 31******************************************SwitzerlandLeybold Schweiz AG, Pfäffikon Churerstrasse 120CH-8808 PfäffikonWarehouse and shipping address:Riedthofstrasse 214CH-8105 Regensdorf Sales:T: +41-44-308 40 50F: +41-44-302 43 73********************Service:T: +41-44-308 40 62F: +41-44-308 40 60**********************SpainLeybold Spain, S.A.C/. Huelva, 7E-08940 Cornellà de Llobregat (Barcelona)Sales:T: +34-93-666 43 11F: +34-93-666 43 70********************Service:T: +34-93-666 46 11F: +34-93-685 43 70**********************AmericaUSALeybold USA Inc.5700 Mellon RoadUSA-Export, PA 15632T: +1-724-327-5700F: +1-724-325-3577*******************Sales:T: +1-724-327-5700F: +1-724-333-1217Service:T: +1-724-327-5700F: +1-724-325-3577BrazilLeybold do BrasilRod. Vice-Prefeito Hermenegildo Tonolli,nº. 4413 - 6B Distrito Industrial Jundiaí - SPCEP 13.213-086Sales and Service:T: +55 11 3395 3180F: +55 11 99467 5934******************************************AsiaP . R. ChinaLeybold (Tianjin)International Trade Co. Ltd.Beichen EconomicDevelopment Area (BEDA),No. 8 Western Shuangchen Road Tianjin 300400ChinaSales and Service:T: +86-22-2697 0808F: +86-22-2697 4061F: +86-22-2697 2017******************************************IndiaLeybold India Pvt Ltd.No. 82(P), 4th Phase K.I.A.D.B. PlotBommasandra Industrial Area Bangalore - 560 099IndienSales and Service:T: +91-80-2783 9925F: +91-80-2783 9926********************************************JapanLeybold Japan Co., Ltd.HeadquartersShin-Yokohama A.K.Bldg., 4th floor 3-23-3, Shin-Yokohama Kohoku-ku, Yokohama-shi Kanawaga 222-0033Japan Sales:T: +81-45-471-3330F: +81-45-471-3323********************Leybold Japan Co., Ltd.Tsukuba Technical Service Center 1959, Kami-yokobaTsukuba-shi, Ibaraki-shi 305-0854Japan Service:T: +81-29 839 5480F: +81-29 839 5485***********************MalaysiaLeybold MalaysiaLeybold Singapore Pte Ltd.No. 1 Jalan Hi-Tech 2/6Kulim Hi-Tech Park Kulim, Kedah Darul Aman 09000MalaysiaSales and Service:T: +604 4020 222F: +604 4020 221******************************************South KoreaLeybold Korea Ltd.3F . Jellzone 2 Tower Jeongja-dong 159-4Bundang-gu Sungnam-si Gyeonggi-doBundang 463-384, Korea Sales:T: +82-31 785 1367F: +82-31 785 1359********************Service:623-7, Upsung-Dong Cheonan-SiChungcheongnam-Do Korea 330-290T: +82-41 589 3035F: +82-41 588 0166**********************SingaporeLeybold Singapore Pte Ltd.8 Commonwealth Lane #01-01Singapore 149555SingaporeSales and Service:T: +65-6303 7030F: +65-6773 0039******************************************TaiwanLeybold Taiwan Ltd.No 416-1, Sec. 3Chunghsin Rd., Chutung Hsinchu County 310Taiwan, R.O.C.Sales and Service:T: +886-3-500 1688F: +886-3-583 3999******************************************Sales and ServiceL V _13786_2016 10.16。
潮流北美漂浮池水泵系统操作说明及零件手册说明书
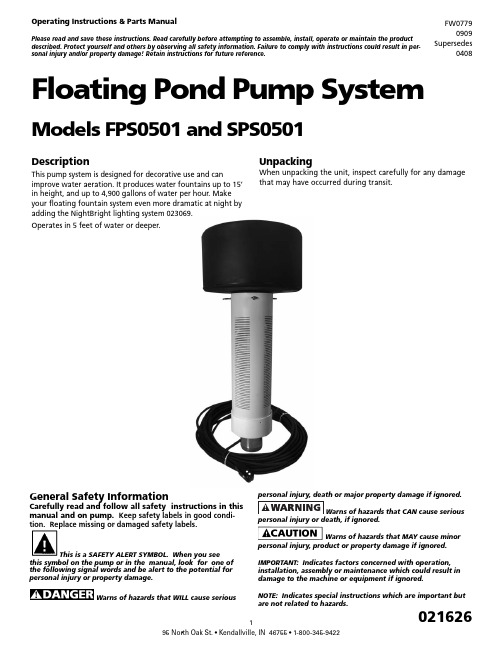
DescriptionThis pump system is designed for decorative use and canimprove water aeration. It produces water fountains up to 15’ in height, and up to 4,900 gallons of water per hour. Make your floating fountain system even more dramatic at night by adding the NightBright lighting system 023069.Operates in 5 feet of water or deeper.UnpackingWhen unpacking the unit, inspect carefully for any damage that may have occurred during transit.Floating Pond Pump SystemModels FPS0501 and SPS0501Operating Instructions & Parts ManualPlease read and save these instructions. Read carefully before attempting to assemble, install, operate or maintain the product described. Protect yourself and others by observing all safety information. Failure to comply with instructions could result in per-sonal injury and/or property damage! Retain instructions for future reference.FW07790909 Supersedes0408General Safety InformationCarefully read and follow all safety instructions in this manual and on pump. Keep safety labels in good condi-tion. Replace missing or damaged safety labels.This is a SAFETY ALERT SYMBOL. When you seethis symbol on the pump or in the manual, look for one of the following signal words and be alert to the potential for personal injury or property damage.Warns of hazards that WILL cause seriouspersonal injury or death, if ignored.Warns of hazards that MAY cause minorpersonal injury, product or property damage if ignored.IMPORTANT: Indicates factors concerned with operation, installation, assembly or maintenance which could result in damage to the machine or equipment if ignored.NOTE: Indicates special instructions which are important but are not related to hazards.Never enter the watereither wading, swimming or in a boat with thepump power on, as this may result in severecarefully. Failure to follow could result in serious bodilyinjury and/or property damage.shall be in accordance with National ElectricCode (NEC) and all applicable local codesand ordinances. A licensed electrician shouldperform installation.“NO SWIMMING” ANDOR WARNING SIGNS SHOULD BE POSTED PERSTATE AND LOCAL CODES.Please affix included warning label to powerreceptacle or junction box.100ft power cord with three prong GFI plug. –Must connect to properly grounded receptacleof grounding type. Do not remove groundpin on plug. Do not extend the cord length by splicing orTHIS UNIT, WITH THE GFI, TO A PROPERLYGROUNDED RECEPTACLE MAY RESULT INto a circuit equipped with a fuse or circuitbreaker of ample capacity.Always disconnect powersource before performing any work on ornear the motor or its connected load. If thepower disconnect point is out-of-sight, lock itin the open position and/or tag it to prevent unexpectedapplication of power. Failure to do so could result in fatalelectrical shock or bodily injury.DO NOT handle pump withwet hands or when standing in water asfatal electrical shock could occur. Disconnectmain power supply before handling systemfor any reason.from coming in contact with sharp objects,oil, grease, hot surfaces or chemicals. DONOT kink the power cable. If damagedbox, fused disconnect switch, or covers open(either partially or completely) when notbeing worked on by a competent electricianor repairman.Always use caution whenoperating electrical controls in damp areas.If possible, avoid all contact with electricalequipment during thunderstorms or extremedamp conditions.equipment in protected area to preventmechanical damage which could produce seriouselectrical shock and/or equipment failure.DO NOT use this system topump flammable liquids such as gasoline, fueloil, kerosene, etc. Failure to follow the abovewarning could result in property damage and/or personal injury.Do not pump water above 120 degreesFahrenheit.Water leaving nozzle is at high velocityand can cause bodily injury if contact is made.in swimming pool areas.!to the State of California to cause cancer and birth defects orother reproductive harm.!coming out the bottom and protected from direct rainfall.INSTALLATION INSTRUCTIONS1. Only install this system in ponds where no swimming,wading, boating or fishing is allowed while fountain isoperating. Disconnect power to pump before fishing orentering the water.2. Post appropriate warning signs per local and state codes.3. Inspect pump system for damage before installing inpond. Check that all bolts and screws are tight. Check forany bent prongs or a cracked case on the GFI.4. The unit ships with one spray nozzle attached. To changeto one of the other 2 nozzles, remove the 4 screws fromthe nozzle then replace with desired nozzle. Refer toFigures 1, 2 & 3 for spray pattern appearance. Nozzlesare marked “This side up.” Make sure the o-ring isseated in groove before installing nozzle. Tighten screwsuntil seated, approximately 10 to 12 in-lbs.5. Attach nylon anchor ropes to 3 eyebolts located at topof screen. Secure (make sure rope is tight) to weightsplaced on pond floor or stakes on pond shore. Whenusing weights to anchor the pump, place weightsapproximately 10 feet from unit. Alternately, two anchorropes placed 180 degrees apart can be used, but 3 ropeswill provide the best stability.6. Before connecting the unit to the power receptacle,check to insure there is no leakage to ground. This canbe done by using an ohm meter and setting the scale toits highest setting (i.e. Rx100K). Connect one ohmmeter lead to the unit power cord ground (round prong) and to one of the flat prongs. It should read infinite or at least 2 mega ohms. Repeat with the other prong. If reading is below 2 mega ohms on either prong contact Customer Service Help Line listed at bottom of page.7. Do Not Operate System on an Extension Cord. If no power is accessible at the pond, contract a licensed electrician to install the proper power supply in accordance with National Electric Code and all applicable local codes and ordinances.8. After installing the unit, checking ground andconnecting power to the unit, the unit can be powered up. Check operation of the GFI by pushing the “Test” button, the unit should stop. Pushing the “Reset” button should restart the unit. If pressing the “test” button does not stop the unit, immediately shut off power to unit and contact Customer Service Help Line listed at bottom of page.NOZZLE PATTERNST h is s id eu p Figure 1: Water Lily - An eye-catching combination spray. Item #2AT h i s s id eu pFigure 2: Sky Cannon - A dramatic single plume of water. Item #2BT h i s s id eu pFigure 3: Water Trumpet - A symmetrical inverted bell shape.Item #2CFigure 4: Typical InstallationINSTALLATION CHECK LIST☐ Read installation instructions and warnings ☐ Post appropriate warning signs ☐ Install desired spray nozzle ☐ Install and anchor unit in pond☐ Check insulation resistance to ground ☐ Power up unit☐ Test operation of GFI by pressing the “Test” Button.☐ File instructions for future reference REQUIRED TOOLS & SUPPLIES• #2 Phillips screwdriver • Nylon rope to anchor unit• Stakes or weights for anchoring unit• Ohm meter to check insulation resistance to groundWINTER STORAGE• Rinse unit with clean water to remove any build-up on unit.• Check unit for any damage.• Store unit in heated space in freezing climates.The pump motor is water lubricated and is factory filledwith an antifreeze solution. During operation the antifreeze may exchange, thru the filtered check valve, with the pond water. In climates where freezing may occur, the unit must be stored in a heated storage space to prevent damage to the motor.TROUBLESHOOTING GUIDE PROBLEM POSSIBLECAUSESCORRECTIVE ACTIONUnit won’t run Circuit break-er trippedReset circuit breaker GFI Tripped Reset GFINo or low spray Blockedscreen ornozzle, miss-ing or dam-aged o-ring,or incorrectlyinstallednozzleDisconnect power. Clean screenand/or nozzle. Check that o-ring isundamaged and seated in groove.Check that nozzle is installed prop-erly (nozzles are marked “This sideup”). Check depth of pond. If lessthan 5 feet deep, move to deepersection. Restart unit.GFI Trips Electricalstorm can tripGFIReset GFIShort in sys-tem Disconnect power and check cord for damage. If cord is damaged contact Customer Service Help Line listed at bottom of page for replacement.Unit spins Anchor ropeloose Check anchor rope and re-attach if necessaryItem #Qty Part No.Description16021624Screw - #10 x 3/4 Pan Head High-Low 2A1021617Nozzle - Water Lily2B1021618Nozzle - Sky Cannon2C1021619Nozzle - Water Trumpet31021622O-Ring - AS568A - 041 (3” ID x 3/18” OD) 44021628Bolt - SS 1/4-20 x 3/454021629Lockwasher - 1/4”61021707Mounting Flange71021534Float81021713Pump End91021740Motor 1/2 HP 115V104127021Locknut - SS 5/16-24111021715100 ft. power cord with GFI11A1021614GFI123021609Eye Bolt - SS 1/4-20 x 2-1/2133021623Locknut - SS 1/4--20141021608Screen151021611Screen Cap161021613Strain Relief172021625Warning DecalFlow (GPH)Spray Height(Ft.)PatternImagePatternName 490015Thissi de upIL053Thissi de upThissi de upWater Lily- 2A 330015Sky Cannon- 2B 270013WaterTrumpet - 2C15161112(A/B/C)345671710911131214811A。
Hayward T-Series 浴池泵说明书

Pumps by Hayward"T" SERIESIMMERSIBLE PUMPOWNER'S MANUALINSTALLATION, OPERATION, MAINTENANCE, PARTSModelsT2 T4 T5 T6 T7 T8Hayward Flow ControlHayward Flow ControlPLEASE READ THE FOLLOWING INFORMATION PRIOR TO INSTALLING AND USING WEBSTER BY HAYWARD T-SERIES PUMPS. FAILURE TO FOLLOW THESE INSTRUCTIONS MAY RESULT IN PRODUCT DAMAGE, PROPERTY DAMAGE, PERSONAL INJURY, OR EVEN DEATH. 1. Hayward Flow Control (Hayward), a division of Hayward Industries, guarantees its products against defective material and workmanship only. Hayward assumes no responsibility for property damage or personal injury resulting from improper installation, misapplication, or abuse of any product.2.Hayward assumes no responsibility for property damage or personal injury resulting from chemical incompatibility between its products and the process fluids to which they are exposed. Determining whether a particular PVC or CPVC product is suitable for an application is the responsibility of the user. Chemical compatibility charts provided in Hayward literature are based on ambient temperatures of 70°F and are for reference only.3.Hayward products are designed for use with non-compressible liquids.damage due to the water hammer effect.5. Piping systems must be designed and supported to prevent excess mechanical loading on Hayward products due to system misalignment, weight, shock, vibration, and the effects of thermal expansion and contraction.6.The effect of temperature on plastic piping systems must be considered when the systems are initially designed. The pressure rating of plastic systems must be reduced with increasing temperature. Maximum operating pressure is dependent upon material selection as well as operating temperature. Before installing any Hayward product, consultHayward product literature for pressure vs. temperature curves to determine any operating pressure or temperature limitations.7.PVC and CPVC plastic products become brittle below 40°F. Use caution in their installation and operation below this temperature.8.Due toDIRECT INSTALLATION OF PLASTIC PRODUCTS INTO METAL PIPING SYSTEMS IS NOT RECOMMENDED . Wherever installation of plastic products into metal piping systems is necessary, it is recommended that at least 10 pipe diameters in length of plastic pipe be installed upstream and downstream of the plastic product to compensate for the factors mentioned above.9. Published operating specifications are based on testing of new products using clean water at 70°F. Pump performance is affected by many factors including fluid chemistry, viscosity, specific gravity, and temperature. These should be considered when sizing pumps.10.Fluid handling systems should always be depressurized and drained prior to installing or maintaining any Hayward product. Electrical systems should be shut off and disconnected prior to installing or maintaining any Hayward product.READ AND FOLLOWSAFETY INSTRUCTIONS!This is the safety-alert symbol. When you see this symbol on your pump or in this manual, look for one of the following signal words and be alert to the potential for personal injury:DANGER warns about hazards that will cause serious personal injury, death or majorproperty damage if ignored.WARNING warns about hazards that can cause serious personal injury, death or majorproperty damage if ignored.CAUTION warns about hazards that will or can cause minor personal injury or propertydamage if ignored.NOTICE indicates special instructions which are important but not related to hazards.Carefully read and follow all safety instructions in this manual and on pump.Keep safety labels in good condition. Replace missing or damaged safety labels.T2 T4 T5 T6 T7 T8SERIES IMMERSIBLE PUMPSTo avoid performance issues, prevent possible injuries, and extend the life ofyour pump, READ THIS MANUAL CAREFULLY!!Webster by Hayward T-Series Immersible Pump Features:Easy to install and operate.No bearings or shaft seals immersed in the fluid being pumped.Can handle moderately abrasive liquids.Designed to run dry without damage.Virtually maintenance free.TABLE OF CONTENTSSAFETY INSTRUCTIONS (2)INSTALLATION ……………………………………………………………………….. 4-5OPERATION (6)MAINTENANCE ………………………………………………………………………. 7-9REPAIR PARTS LIST ….………………………………………………………… 10-12Hayward Flow ControlHayward Flow ControlINSTALLATIONInstall pump inside tank (See Figure 1).Mount pump vertically with motor above highest liquid level in the tank. Be sure that highest liquid level in tank is below ‘Maximum Immersion’ line (molded into body) located below weep hole on pump body column (See Figure 1).Pump inlet opening must always be at least one foot above tank bottom.CAUTION: tolerate piping stress. To prevent damage or deformation of pump body and damage to pump, be sure any piping attached to pump is properly aligned and supported.Mount pump in tank so that pump inlet opening is at least one foot above tank bottom. Be sure that any foot valve or other hardware on inlet pipe will not stick closed or partially closed. Restricting flow can starve inlet, causing cavitation, which can damage pump.To be sure of priming on restart, install an inlet foot valve and discharge check valve, orBe sure that fluid level covers discharge port after shutoff (see Fig. 1).When a foot valve is installed, manually prime pump for initial start-up.With both foot valve and discharge check installed, pump should not need priming for restart even if liquid level in tank falls below discharge port.CAUTION: the pump body and contacting the base of the motor on shutoff, discharge check valve must be installed between 1 to 3 feet of the pump discharge port.Fig. 1Hayward Flow ControlELECTRICALGround motor before connecting to electrical power supply! Failure to ground motor can cause severe or fatal electrical shock hazard! Do not ground to a gas supply line!To avoid dangerous or fatal electrical shock, turn OFF power to motor before working on electrical connections.Motor wiring and supply voltage must match exactly to prevent poor performance and motor damage. Running the motor at the wrong voltage will void the warranty.MOTOR FUSE AND WIRING DATASee Table 1 for motor fuse and wiring dataROTATIONMotor shaft rotation is counterclockwise (CCW) viewed from suction end of pump. Running pump backwards may loosen impeller and will reduce performance.Single Phase Motors: Pre-wired for correct rotation and highest nameplate voltage. For lower voltage operation, follow motor manufacturer's instructions inside wiring access cover or on motor.Three Phase Motors: Follow directions on motor nameplate to connect for desired voltage and rotationHayward Flow ControlOPERATIONWebster pumps will handle temperatures from –20ºF to +260ºF and a wide range of chemicals (depending on pump materials of construction; see product catalog, or reference Hayward website for data).CAUTION: Liquid within impeller will cause heavy side loading and may cause motor bearing failure and pump damage. To prevent liquid from rising high enough to fill impeller:1. Use a liquid level control on sump installations.2. Set liquid level control to start pump when sump liquid level is between discharge port centerline and `Maximum Immersion' line on pump flange.3. Pump should shut off before liquid level has reached bottom of pump inlet.CAUTION: Webster pumps are designed to allow dry running. However, do not run pump partially dry; that is,1. Do not operate pump with impeller only partially submerged and2. Do not operate pump with impeller alternately submerged and dry. Operating under these conditions will put shock loads on the pump which can cause early motor bearing or pump failure.WARNING: If pump runs dry, NEVER allow pumping chamber to refill while pump is running! To avoid shock loading of impeller, stop pump while liquid level rises into pumping chamber.START-UP1. Manually prime pump before starting for the first time.2. Close pump discharge.3. Start pump.4. Open discharge to desired flow rate.5.With both foot valve and discharge check installed and operating correctly, pump will not need priming for restart even if liquid level in tank drops below discharge port. (Figure 2)Fig. 2MAINTENANCE: Series T2To avoid danger of injury from electrical shock or from motor unexpectedly starting, disconnect power to motor before working on pump.Disassembly:1. Use a screwdriver to pry retainer ring (6) toward suction port and out of its groove.2. Pull end cover (4) out of pump body (2). Move end cover from side to side while pulling to loosen it. Do not remove end cover o-ring (5) unless you are replacing it.3. Remove impeller by holding motor shaft via the motor fan blades and unscrewing the impeller (3B) counterclockwise until it fully disengages from shaft threads and lift out of pump body.4. Check impeller shaft seal (3A) for damage and replace as necessary. (Note: Impeller shaft seal may stay assembled in end of impeller sleeve upon impeller removal.)5. Remove four main pump body bolts (7) and washers (8). Lift body (2) off of motor (1).6. For pump motor maintenance, consult factory.NOTICE: Disassembly of motor will void motor manufacturer's warranty.Assembly:1. Orient discharge port as desired and place flange of body (2) against face of motor (1) with bolt holes of body flange aligned with tapped holes in motor face.2. Install four main pump body bolts (7) and washers (8). Tighten bolts in an alternating crossing pattern to ensure that body flange is tightened evenly to motor face.3. Check impeller shaft seal (3A) for damage and replace as necessary. Insert shaft seal (3A) into top of sleeve of impeller (3B) and push seal into counterbore in top of impeller sleeve.4. Position impeller (3B) over shaft of motor (1) and holding motor shaft in place by engaging motor fan blades thread impeller (3B) onto threaded end of the motor shaft (1). Note that as the impeller (3B) is threaded onto the motor shaft (1), the shaft seal (3A) will be compressed and will form a seal between the impeller and a shoulder on the motor shaft. Notice: Do not over-tighten impeller.5. Make sure impeller (3B) spins freely and that there is no interference between the impeller (3B) and the inside surfaces of body (2).6. Push end cover (4) into bore in end of pump body (2) until end cover o-ring (5) and bottom face of end cover clear the groove in the end of the pump body.7. Install the retainer ring (6) into the groove in the end of the pump body. Make sure that retainer ring fully snaps into the groove.4Hayward Flow ControlSeries T4 through T8To avoid danger of injury from electrical shock or from motor unexpectedly starting, disconnect power to motor before working on pump.Disassembly:1. Use a screwdriver to pry retainer ring (6) toward suction port and out of its groove.2. Pull end cover (4) out of pump body (2). Move end cover from side to side while pulling to loosen it. Do not remove end cover o-ring (5) unless you are replacing it.3. Remove nosepiece (3D) by holding motor shaft via the motor fan and unscrewing nosepiece counterclockwise.4. While continuing to hold motor shaft in place by engaging motor fan blades, unscrew impeller (3B) counterclockwise until it fully disengages from shaft threads and lift out of pump body.5. Check impeller shaft seal (3A) for damage and replace as necessary. (Note: Impeller shaft seal may stay assembled in end of impeller sleeve upon impeller removal.)6. Remove four main pump body bolts (7) and washers (8). Lift body (2) off of motor (1).7. For pump motor maintenance, consult factory.NOTICE: Disassembly of motor will void motor manufacturer's warranty.Hayward Flow ControlSeries T4 through T8To avoid danger of injury from electrical shock or from motor unexpectedly starting, disconnect power to motor before working on pump.Assembly:1. Orient discharge port as desired and place flange of body (2) against face of motor (1) with bolt holes of body flange aligned with tapped holes in motor face.2. Install four main pump body bolts (7) and washers (8). Tighten bolts in an alternating crossing pattern to ensure that body flange is tightened evenly to motor face.3. Check impeller shaft seal (3A) for damage and replace as necessary. Insert shaft seal (3A) into top of sleeve of impeller (3B) and push seal into counterbore in top of impeller sleeve.4. Position impeller (3B) over shaft of motor (1) and holding motor shaft in place by engaging motor fan blades thread impeller (3B) onto threaded end of the motor shaft (1). Note that as the impeller (3B) is threaded onto the motor shaft (1), the shaft seal (3A) will be compressed and will form a seal between the impeller and a shoulder on the motor shaft. Notice: Do not over-tighten impeller.5. Make sure impeller (3B) spins freely and that there is no interference between the impeller (3B) and the inside surfaces of body (2).6. Insert nosepiece o-ring (3C) over threaded end of nosepiece (3D) and thread nosepiece into end of motor shaft (1).7. Using a wide flat screwdriver, tighten nosepiece (3D).8. Push end cover (4) into bore in end of pump body (2). Push end cover until end cover o-ring (5) and bottom face of end cover clear the groove in the end of the pump body.9. Install the retainer ring (6) into the groove in the end of the pump body. Make sure that retainer ring fully snaps into the groove.WEBSTER® Seal-less Immersible PumpT2 SERIES – Parts List● Not illustrated.** Not available separately. Order Impeller Kit.*** Entire liquid end; includes all parts except Motor (1).NOTE ON PART NUMBERS:For CPVC parts: use listed part number, no suffix added.For PVDF parts: use listed part number plus -2 suffix; for example 4654-2For Polypropylene parts: use listed part number plus - 3 suffix: for example 4654-3.Hayward Flow ControlWEBSTER® Seal-less Immersible PumpT4, T5 SERIES – Parts List● Not illustrated.** Not available separately. Order Impeller Kit.*** Entire liquid end; includes all parts except Motor (1).NOTE ON PART NUMBERS:For CPVC parts: use listed part number, no suffix added.For PVDF parts: use listed part number plus -2 suffix; for example 4654-2For Polypropylene parts: use listed part number plus - 3 suffix: for example 4654-3.Hayward Flow ControlHayward Flow ControlWEBSTER ® Seal-less Immersible PumpT6, T7, T8 SERIES – Parts List● Not illustrated. ** Not available separately. Order Impeller Kit. *** Entire liquid end; includes all parts except Motor (1). NOTE ON PART NUMBERS: For CPVC parts: use listed part number, no suffix added. For PVDF parts: use listed part number plus -2 suffix; for example 4664-2 For Polypropylene parts: use listed part number plus -3 suffix: for example 4664-3.。
浸润式生物污水泵型号NS说明书
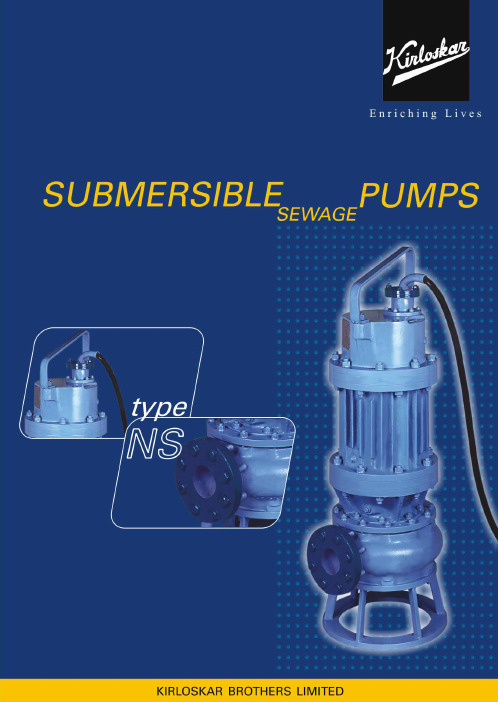
A specially designed cable, 1.1 kV grade having annealed tinned copper conductor, insulated with Electron Beam Irradiated crosslinked elastomeric compound (compatible for continuous operation at 1200 C) cores laid up with a proof cotton binder tape and sheathed overall with Electron Beam Irradiated Cross-linked HD HOFR elastomeric compound and generally conforming to IS 9968 Part l. The cable with this unique combination of insulating and sheathing material offers best resistance to acidic or alkaline sewage medium and to the effluent gases coming out of the sump. The cable is more flexible than PVC cable making coiling and handling easier and light in weight compared to PVC cable of the same size.
II 65 50 65 50 1030 135 491 256 309 225 55 460 165 125 4/18 320 260 200 150 24 560 450 70 320 900 I 80 65 84 65 1030 140 542 312 309 225 55 460 185 145 4/18 330 270 225 175 24 570 475 80 340 900
Steritest Symbio泵操作手册说明书
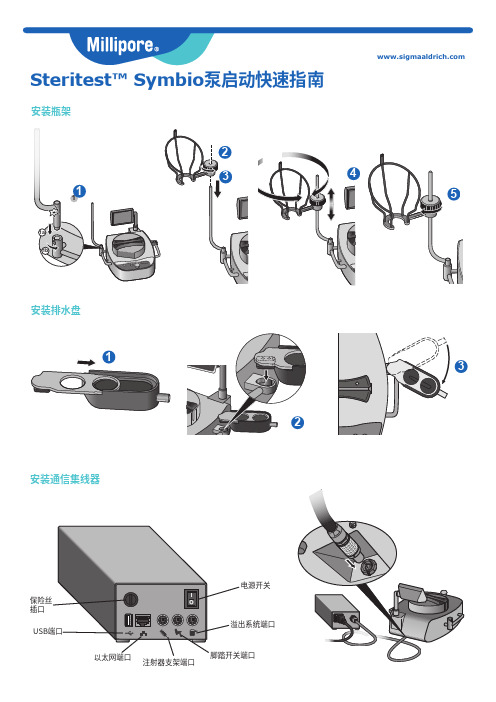
安装瓶架泵控制面板概览开动泵按电源开关开动或关停泵。
按打开/关闭按钮打开或关闭泵头。
按后退或下一步按钮执行各种操作。
旋转和按控制按钮执行各种操作。
按电源开关(位置1)打开通讯集线器。
按住 按钮几秒钟开动泵。
这时画面上将显示Steritest™装置,然后显示欢迎画面。
第一次启动泵时,在泵证书激活前,即会接着显示泵证书画面。
注:激活证书后,在欢迎画面之后将显示自动测试(Autotest )画面。
如果 泵已安装好且已准备好接受资格认证,则 和 以回答“是”。
根据指示激活泵证书。
在此之后,时间开始倒计时,倒计时时间为12个月,倒计时结束时即是下一次校准的时间。
如果 泵尚未准备好接受资格认证,则 和 以回答“否”。
这时将显示自动测试(Autotest )画面,并继续从工厂的校准日期开始倒计时至下一次校准时间。
当自动测试程序结束时,将显示辅件和数据来源画面。
复选框中的符号表示辅件或数据来源已连接到通讯集线器。
按动。
这时将显示主画面。
从主画面,您可以:•进入标准模式,可以手动模式使用泵。
•进入测试方法模式,在该模式下,可以预定的程序使用泵。
•进入配置菜单,以配置泵参数及其辅件,并将测试方法上传到泵。
© 2019年版权归德国达姆施塔特默克集团(Merck KGaA )及/或其附属公司所有。
保留一切权利。
Merck ,Steritest , 西格玛·奥德里奇(Sigma-Aldrich )和密理博(Millipore )是德国达姆施塔特默克集团(Merck KGaA )的商标。
所有其他商标均归相应所有者所有。
商标的详细信息可通过公众可得的资源了解。
PF16601ZH 版本3.0 01/2019德国达姆施塔特默克集团的生命科学业务在美国和加拿大的公司名称为MilliporeSigma 。
- 1、下载文档前请自行甄别文档内容的完整性,平台不提供额外的编辑、内容补充、找答案等附加服务。
- 2、"仅部分预览"的文档,不可在线预览部分如存在完整性等问题,可反馈申请退款(可完整预览的文档不适用该条件!)。
- 3、如文档侵犯您的权益,请联系客服反馈,我们会尽快为您处理(人工客服工作时间:9:00-18:30)。
18 Initials
*: Mark of Schlumberger
2.9 存储卡数据下载
- 点击”Read Module” -点击”Load Trend”
Schlumberger Private Schlumberger Private
19 Initials
*: Mark of Schlumberger
Schlumberger Private Schlumberger Private
*: Mark of Schlumberger
2.5 Uniconn操作-查看泵工况数据
Schlumberger Private Schlumberger Private
12 Intouch #4057132 1/2/2012
格式化/设置 存储卡
15 Initials
状态显示
*: Mark of Schlumberger
2.7.2 Uniconn操作 – 存储卡设置/格式化
格式化存储卡
Schlumberger Private Schlumberger Private
16 Initials
一旦选择yes,系统将删除存储卡以前的内容
Schlumberger Private Schlumberger Private
Adobe Acrobat Document
20 Intouch #4057132 1/2/2012
*: Mark of Schlumberger
3. 基本故障诊断
1. 2. 3. 4. PIC Fault – 需要进行PIC卡检测,井下绝缘监测
*: Mark of Schlumberger
2.7.3 Uniconn操作 – 存储卡设置/格式化
选择需要的参数添加到存 储卡,在以后的正常工作 中存储卡将按照所添加的 参数进行数据存储
Schlumberger Private Schlumberger Private
一旦选取“wrap data”在一段时间后新数据将复盖老数据
*: Mark of Schlumberger
2.7 Uniconn操作 – 存储卡设置/格式化
存储卡 1. 2. 3.
读卡器 (USB)
电脑
Star View
Schlumberger Private Schlumberger Private
将存储卡插入读卡器, 读卡器连接到电脑 打开桌面stariew软件 选择File目录下Uniconn Memberger Private Schlumberger Private
动力电缆
电机
泵工况 5 Intouch #4057132 1/2/2012
*: Mark of Schlumberger
1.4 井下设备
泵工况 0.56M, 法兰 4.5” 底部扣型:2-3/8 EUE BOX
keypad
Schlumberger Private Schlumberger Private
模拟/数值输入输出
DataCard Slot
9 Intouch #4057132 1/2/2012
4个扩展卡插槽
*: Mark of Schlumberger
2.3 Uniconn 扩展卡
Schlumberger Private Schlumberger Private
Schlumberger Private Schlumberger Private
斯伦贝谢电泵工况监测系统 泵工况监测系统
要点
1. 系统的组成和安装
Schlumberger Private Schlumberger Private
2. 操作事宜 3. 故障诊断
2 Intouch #4057132 1/2/2012
*: Mark of Schlumberger
1.2测量参数
参数
在地面设备上的英文显示
范围
准确度
吸入口压力 排出口压力 吸入口温度 电机绕组温度 震动 电流漏失
Pi Pd Ti Tm Vib Cl-a & Cl-p
0~400Bar (5800psi) 0~400Bar (5800psi) 0~125 ℃ 0~175 ℃ 0~15g 0~25mA
供电110vdc
Schlumberger Private Schlumberger Private
变频器输出
井口接线盒
变压器输出
7 Intouch #4057132 1/2/2012
*: Mark of Schlumberger
2.1 Uniconn 正视图
2 lines x 40 LED 显示屏 状态指示灯
14 Intouch #4057132 1/2/2012
*: Mark of Schlumberger
2.7.1 Uniconn操作 – 存储卡设置/格式化
数据库记录
显示数据卡内容
Schlumberger Private Schlumberger Private
加载所选数据库 转换数据库到文件 读取存储卡内容 读取存储卡文件 将数据内容转 换成曲线图 进度条 完成 / 退出 停止
通讯卡
泵工况功能卡
PIC 卡
10 Intouch #4057132 1/2/2012
*: Mark of Schlumberger
2.4 组件
扼流板
PIC卡
通讯卡 SCADA (RS232/485) 存储卡 读卡器 (USB) DB-9 数据线 StarView
11 Intouch #4057132 1/2/2012
Schlumberger Private Schlumberger Private
语言选择键
返回键 停止键
功能键 DB9 数据线接口
8 Intouch #4057132 1/2/2012
存储卡插槽及其退出按键
*: Mark of Schlumberger
2.2 Uniconn – 侧视图及后视图
保险
Schlumberger Private Schlumberger Private
百事可乐
22 Intouch #4057132 1/2/2012
*: Mark of Schlumberger
Schlumberger Private Schlumberger Private
Tool Open – 检查扼流板保险丝,以及相关的电缆连接 Tool ok – 正常状态 Tool short – 检查井下绝缘和相间值阻
21 Intouch #4057132 1/2/2012
*: Mark of Schlumberger
Schlumberger Private Schlumberger Private
压力传输管线 100FT OD 1/4” Jam nut 连接
传压接头 0.24M 3.5” EUE
OD 5’’
6 Intouch #4057132 1/2/2012
*: Mark of Schlumberger
1.6 地面设备
2.11 泵工况操作注意事项
1. 2. 3.
4.
由于泵工况的地面设备与控制柜内的高压电缆相连接,因此在对地面 设备进行工作之前一定要停泵并且断开控制柜的电源。 为了安全,泵工况在运行的时候不要打开地面设备箱。 在对井下电缆进行绝缘测试之前一定要将接到控制柜内的三条红色高 压线与井下电缆的连接断开。否则会导致地面设备的损坏。在测绝缘 时,测试电压不应该大于2500Vdc,推荐用1000Vdc来进行测量。将- VE接到电缆,+VE接地。如果测到井下电缆绝缘为0,一定要倒换表 笔再测一次,这样才能确定井下绝缘是否存在问题。 不要打火花放电。这样可能会导致井下泵工况内二极管的损坏。
*: Mark of Schlumberger
1.1 系统的组成
传压接头
压力管线
Schlumberger Private Schlumberger Private
动力电缆 ISU
供电110V 110V 供电110V
高压扼流板 Uniconn
信号反馈 4-20mA
泵工况 扶正器
3 Intouch #4057132 1/2/2012
*: Mark of Schlumberger
2.6 Uniconn操作 - RSR 快速取样模式
RSR 快速采样模式:只针对吸入口压力参数进行一秒钟采集一次,同时其他参数处于暂停状态
Schlumberger Private Schlumberger Private
13 Intouch #4057132 1/2/2012
17 Initials
*: Mark of Schlumberger
2.8 存储卡下载数据
- 将存储卡从Uniconn上弹开 ;
注意: 点击 “退出” 按钮,等待数秒当屏幕显示 “Ready to unplug”
Schlumberger Private Schlumberger Private
- 将存储卡插入到读卡器并连接到电脑的USB接口 - 运行star view 软件 - 选择File 目录下的“Uniconn Mem Module”
0.7bar (10psi) 0.7bar (10psi) 1% 1% 1% 0.05%
Schlumberger Private Schlumberger Private
4 Intouch #4057132 1/2/2012
*: Mark of Schlumberger
1.3 原理
显示面板
变频器
ISP/Uniconn 输出110vdc 经过扼流板(高低压隔离), 加载到井下电泵的动力电缆, 直达电机底部的星点,提供泵 工况工作电压。 泵工况得电,正常工作,并且 将产生的模拟信号通过接地反 馈到地面ISU/Uniconn